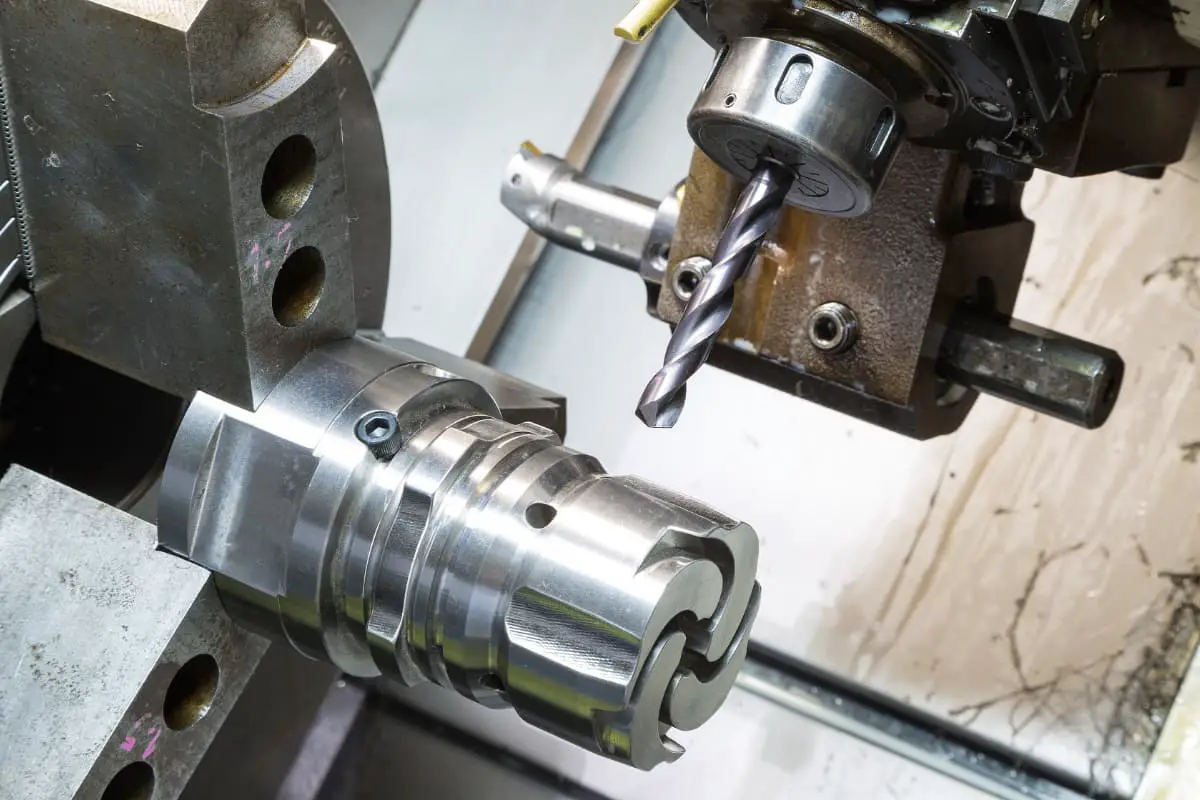
I. تكوين ومبدأ عمل مراكز المعالجة الآلية
مركز التشغيل الآلي هو عبارة عن معدات معالجة مؤتمتة للغاية تم تطويرها من ماكينات التفريز بنظام التحكم الرقمي. إنها أداة ماكينة بنظام التحكم الرقمي مزودة بمخزن أدوات ومبادل أدوات أوتوماتيكي (ATC)، وتُعرف أيضًا باسم أداة ماكينة بنظام التحكم الرقمي ذات التغيير الآلي للأدوات أو أداة ماكينة بنظام التحكم الرقمي متعددة العمليات.
بعد تشبيك قطعة العمل مرة واحدة، يمكن لنظام التحكم الرقمي باستخدام الحاسب الآلي التحكم في الماكينة لتحديد الأدوات وتغييرها تلقائيًا وفقًا لعمليات مختلفة؛ وتغيير سرعة المغزل ومعدل التغذية ومسار حركة الأداة بالنسبة لقطعة العمل تلقائيًا، بالإضافة إلى الوظائف المساعدة الأخرى؛ وإكمال التشغيل الآلي متعدد العمليات على عدة أسطح لقطعة العمل بالتسلسل.
وهذا يقلل من وقت تشبيك الشغل والقياس وتعديل الماكينة، ويقلل من وقت تخزين الشغل والمناولة ويحسن من كفاءة الإنتاج واستخدام الماكينة. مراكز التصنيع هي معدات لا غنى عنها في المعالجة الآلية وهي أيضًا الماكينات الأساسية في أنظمة التصنيع المرنة (FMS). ولتحسين وظائف مراكز الماكينات، ظهرت مراكز الماكينات المزودة بتغيير مخزن الأدوات تلقائيًا وتغيير رأس المغزل تلقائيًا وتغيير صندوق المغزل تلقائيًا.
تتميز مراكز الماكينات المزودة بتغييرات مخزن العِدَّة الأوتوماتيكية بسعات أكبر لمخازن العِدَّة، مما يسهل التصنيع متعدد العمليات للقِطع المعقدة من النوع الصندوقي. يمكن لمراكز الماكينات المزودة بتغييرات تلقائية لرأس عمود الدوران إجراء التفريز الأفقي والتفريز الرأسي والطحن والتفريز القابل للفهرسة. بالإضافة إلى مخزن العِدَّة، يحتوي هذا النوع من مراكز الماكينات أيضًا على مخزن رأس المغزل، والذي يتم تغييره بواسطة الروبوتات الصناعية أو الأيدي الميكانيكية.
عادةً ما تحتوي مراكز الماكينات المزودة بتغيير صندوق المغزل الأوتوماتيكي على صناديق مغزل للتشغيل الآلي الخام وصناديق مغزل للتشغيل الآلي الدقيق لتحسين دقة التشغيل الآلي ونطاقه. والفرق الرئيسي بين مراكز الماكينات وأدوات الماكينات بنظام التحكم الرقمي العادية هو أنها يمكن أن تكمل العمل على ماكينة واحدة يتطلب ماكينات متعددة.
في الوقت الحالي، تتمتع مراكز الماكينات حاليًا بسعات متزايدة لمخازن الأدوات، وأوقات تغيير أدوات أقصر، ودقة تصنيع أعلى، ووظائف محسّنة. بالإضافة إلى مراكز التصنيع الآلي المطورة من ماكينات التفريز بنظام التحكم الرقمي (مراكز التفريز والتثقيب الآلي)، ظهرت أيضًا مراكز تصنيع آلات الخراطة المطورة من مخارط بنظام التحكم الرقمي.
1. تكوين مراكز الماكينات
منذ أن وُلد أول مركز تصنيع آلي في العالم في عام 1958، ظهرت أنواع مختلفة من مراكز التصنيع الآلي بهياكل خارجية مختلفة، ولكنها تتألف بشكل عام من الأجزاء الرئيسية التالية
(1) جسم أداة الماكينة
يشير هيكل مركز الماكينات إلى كيان هيكله الميكانيكي، الذي يتكون من نظام المحرك الرئيسي، ونظام محرك التغذية، والسرير، والعمود، ومنضدة الشُّغْلَة.
وتشمل هذه المكونات أجزاء الحديد الزهر والهياكل الفولاذية الملحومة. إنها الهيكل الأساسي لمركز التشغيل الآلي ويجب أن تتحمل الحمل الساكن لمركز التشغيل الآلي بالإضافة إلى حمل القطع المتولد أثناء التشغيل الآلي، لذلك يجب أن تتمتع بالصلابة الكافية.
(2) نظام CNC
نظام التحكم الرقمي باستخدام الحاسب الآلي هو مركز التحكم في مركز الماكينات وروحه. ويتكون بشكل أساسي من نظام التحكم الرئيسي، ووحدة التحكم المنطقي القابلة للبرمجة (PLC)، وواجهة الإدخال/الإخراج، ولوحة المفاتيح، والشاشة. يتكون نظام التحكم الرئيسي بشكل أساسي من وحدة المعالجة المركزية، والذاكرة، ووحدة التحكم.
تتمثل عناصر التحكم الرئيسية في نظام التحكم الرقمي باستخدام الحاسب الآلي في الكميات الميكانيكية مثل الموضع والزاوية والسرعة، بالإضافة إلى الكميات الفيزيائية مثل درجة الحرارة والضغط والتدفق. يمكن تقسيم طرق التحكم الخاصة به إلى فئتين: التحكم في معالجة عملية البيانات والتحكم المنطقي المتسلسل.
تقوم وحدة الاستيفاء في وحدة التحكم الرئيسية بقراءة برنامج الجزء، ومعالجته من خلال فك التشفير والتجميع، وإجراء حسابات استيفاء مسار الأداة المقابلة، والتحكم في إزاحة كل محور إحداثي لأداة الماكينة من خلال المقارنة مع إشارات التغذية المرتدة للموضع والسرعة لكل نظام مؤازر إحداثي.
عادةً ما يتم إجراء التحكم المنطقي المتسلسل بواسطة PLC، الذي ينسق الإجراءات المطلوبة في عملية التصنيع الآلي لأداة الماكينة، ويصدر أحكامًا منطقية بناءً على إشارات الكشف المختلفة، ويتحكم في التشغيل المنظم لمختلف أجزاء أداة الماكينة.
(3) نظام المؤازرة
نظام المؤازرة هو وصلة المحرك الكهربائي بين نظام التحكم الرقمي باستخدام الحاسب الآلي وجسم أداة الماكينة. ويتكون بشكل أساسي من محركات مؤازرة، وأنظمة التحكم في المحرك، وأجهزة الكشف عن الموضع والتغذية الراجعة. المحرك المؤازر هو المكون المنفذ للنظام، في حين أن نظام التحكم في القيادة هو مصدر الطاقة للمحرك المؤازر.
تتم مقارنة إشارة الأوامر الصادرة من نظام التحكم الرقمي باستخدام الحاسب الآلي مع إشارة التغذية الراجعة للموضع وتستخدم كأمر إزاحة. بعد تضخيم الطاقة بواسطة نظام المحرك، فإنه يدفع المحرك للدوران، والذي بدوره يدفع طاولة العمل أو حامل الأداة للتحرك من خلال أجهزة النقل الميكانيكية.
(4) الأجهزة المساعدة
تتضمن الأجهزة المساعدة بشكل أساسي مبادل الأدوات الأوتوماتيكي (ATC)، ومبادل المنصات الأوتوماتيكي (APC)، وآلية تشبيك وتحرير الشُّغْلَة وآلية تحريرها، ومنضدة الشُّغْلَة الدوارة وأجهزة التشحيم والتبريد، ونظام إزالة البُرادة الأوتوماتيكي، والنظام الهيدروليكي, نظام هوائيوالنظام الكهربائي، وأجهزة التحميل الزائد والحماية، إلخ. وهي تلعب دورًا في ضمان كفاءة العمل، ودقة التصنيع، وموثوقية السلامة لمركز الماكينات.
2. مبدأ عمل مراكز المعالجة الآلية
لتصنيع القِطع على مركز الماكينات، أولاً، بناءً على رسم الجزء المصمم وبعد تحليل وتصميم عملية التصنيع الآلي، يتم إجراء العمليات المختلفة المطلوبة أثناء عملية التصنيع الآلي، مثل بدء/إيقاف تشغيل المغزل، وتغيير سرعة المغزل، ومعلمات القطع، ومسار التغذية, سائل القطع تتم كتابة الإمداد والإزاحة النسبية بين الأداة وقطعة العمل في برنامج الماكينات باستخدام أكواد CNC محددة بتنسيق معين.
بعد ذلك، يتم نقل المعلومات إلى نظام التحكم الرقمي باستخدام الحاسب الآلي من خلال لوحة مفاتيح أو أجهزة إدخال أخرى. يقوم الكمبيوتر في نظام التحكم الرقمي باستخدام الحاسب الآلي بمعالجة وحساب تعليمات البرنامج المستلمة، ويرسل الأوامر إلى نظام المؤازرة ودوائر التحكم المساعدة الأخرى، مما يجعلها تقوم بإجراء التشغيل الآلي وفقًا لتسلسل العمل المحدد، ومسار حركة الأداة، ومعلمات عملية القطع في البرنامج. عند اكتمال تصنيع الجزء، تتوقف الماكينة.
عندما يكمل مركز الماكينات إدخال البرنامج وتصحيح الأخطاء والقطع التجريبي للقطعة الأولى ويدخل في إنتاج الدفعات، يحتاج المشغل عمومًا فقط إلى تحميل وتفريغ قطع العمل، ثم الضغط على زر بدء الدورة الأوتوماتيكية للبرنامج، ويمكن لمركز الماكينات إكمال عملية التشغيل الآلي بالكامل تلقائيًا.
II. تصنيف واستخدامات مراكز المعالجة الآلية
1. تصنيف مراكز الماكينات
هناك العديد من أنواع مراكز الماكينات ذات الأشكال المختلفة، وهناك طرق تصنيف متعددة.
وفقًا لدقة التصنيع، يمكن تقسيمها إلى مراكز تصنيع عادية ومراكز تصنيع عالية الدقة؛ ووفقًا لعدد محاور الإحداثيات القابلة للتحكم ومحاور الإحداثيات المرتبطة بها، يمكن تقسيمها إلى مراكز تصنيع ثلاثية المحاور ثلاثية الوصلات، وأربع محاور ثلاثية الوصلات، وخمسة محاور رباعية الوصلات، وخمسة محاور رباعية الوصلات، وستة محاور خماسية الوصلات؛ ووفقًا لعدد ووظيفة طاولات العمل، يمكن تقسيمها إلى مراكز تصنيع آلي أحادية طاولة العمل، ومراكز تصنيع آلي مزدوجة طاولة العمل، ومراكز تصنيع آلي متعددة طاولات العمل، إلخ.
تعتمد طريقة التصنيف الشائعة على هيكل الماكينة، وتنقسم عمومًا إلى مراكز الماكينات العمودية، ومراكز الماكينات الأفقية، ومراكز الماكينات الجسرية، ومراكز الماكينات ذات الخمسة أوجه.
(1) مركز الماكينات العمودية
يشير مركز الماكينات العمودي إلى مركز تصنيع آلي مزود بمغزل مضبوط عموديًا، يحتوي بشكل عام على ثلاثة محاور إحداثيات وقادر على الربط ثلاثي المحاور. يمكن لبعض مراكز الماكينات إجراء تحكم خماسي المحاور أو سداسي المحاور، مما يسمح بتصنيع القِطع الأكثر تعقيدًا.
يوضح الشكل 1 المنظر الخارجي لمركز الماكينات العمودية. غالبًا ما يكون هيكلها من نوع العمود الثابت، مع طاولة عمل مستطيلة بدون وظيفة دوران الفهرسة، وهي مناسبة لتصنيع القِطع من نوع القرص والكم واللوح. يمكن تركيب طاولة دوارة ذات محور أفقي بنظام التحكم الرقمي باستخدام الحاسب الآلي على طاولة العمل لمركز الماكينات العمودية لتصنيع القِطع الحلزونية.
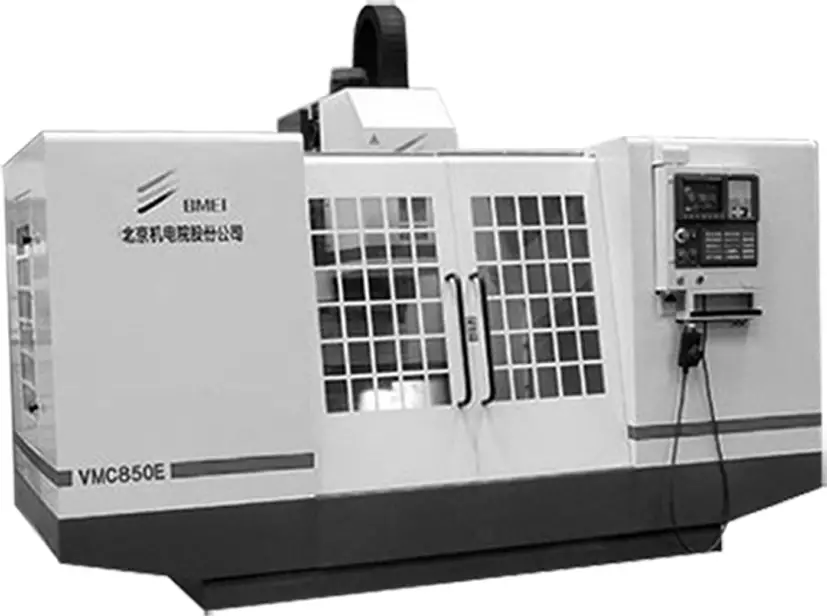
تعتبر مراكز الماكينات العمودية ملائمة لتثبيت الشُّغْلَة وسهلة المراقبة والتشغيل وتصحيح البرامج. بالإضافة إلى ذلك، تتميز مراكز الماكينات العمودية بهيكل بسيط ومضغوط، وبصمة صغيرة، وسعر منخفض نسبيًا، لذلك تم استخدامها على نطاق واسع.
ومع ذلك، نظرًا للقيود المفروضة على ارتفاع العمود وجهاز تغيير الأدوات، لا يمكن لمراكز الماكينات العمودية تشغيل قطع العمل الطويلة جدًا. عند تصنيع التجاويف أو الأسطح المقعرة، تكون إزالة البُرادة صعبة، مما قد يؤدي إلى تلف الأدوات والأسطح الميكانيكية بشكل خطير، مما يؤثر على التقدم السلس للقطع.
(2) مركز تصنيع آلي أفقي
يشير مركز الماكينات الأفقي إلى مركز تصنيع آلي مزود بمغزل مضبوط أفقيًا. يوضح الشكل 2 المنظر الخارجي لمركز الماكينات الأفقي.
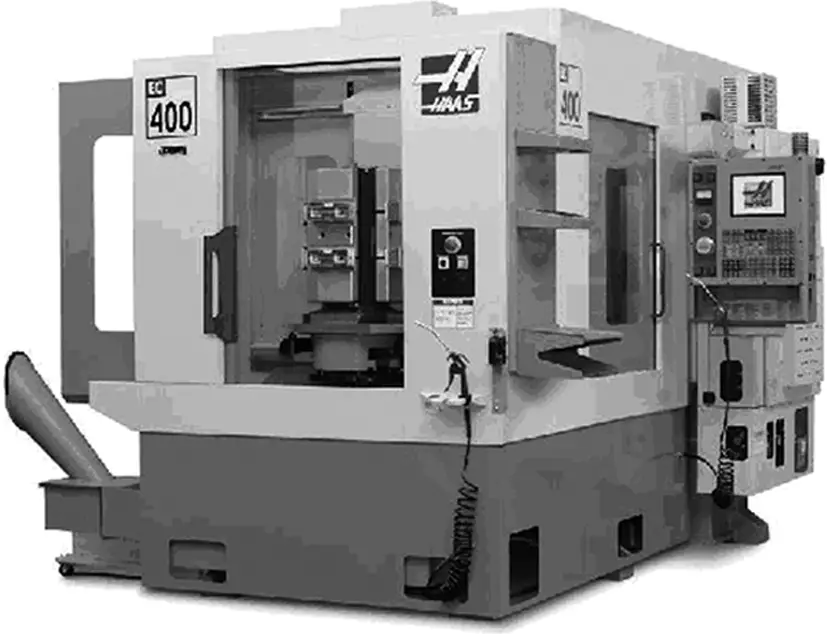
تحتوي مراكز الماكينات الأفقية عمومًا على 3 إلى 5 محاور إحداثيات، وعادةً ما تحتوي على ثلاثة محاور إحداثيات للحركة الخطية بالإضافة إلى محور إحداثيات حركة دوّارة واحدة، مما يسمح لقطعة العمل بإكمال التشغيل الآلي على أربعة جوانب باستثناء سطح التركيب والسطح العلوي بعد تثبيت واحد. مقارنةً بمراكز الماكينات العمودية، فهي أكثر ملاءمة لتصنيع القِطع من النوع الصندوقي، وخاصةً القِطع من النوع الصندوقي مع متطلبات دقة الموضع النسبي بين الثقوب وتحديد موقع أسطح المسند أو بين الثقوب، مما يسهل ضمان دقة التصنيع.
مراكز الماكينات الأفقية غير ملائمة للمراقبة أثناء تصحيح أخطاء البرنامج والقطع التجريبي، وللمراقبة أثناء التشغيل الآلي. كما أن تشبيك وقياس الشُّغْلَة غير ملائم أيضًا، ولكن إزالة البُرادة سهلة أثناء التصنيع الآلي، وهو أمر مفيد للمعالجة.
مقارنةً بمراكز الماكينات العمودية، تتميز مراكز الماكينات الأفقية بميزات مثل سعة مخزن الأدوات الأكبر، والهيكل العام الأكثر تعقيدًا، والحجم الأكبر ومساحة الأرضية الأكبر، والسعر الأعلى. مراكز الماكينات الأفقية هي أكثر أنواع مراكز الماكينات استخدامًا على نطاق واسع.
(3) مركز تصنيع آلي من النوع الجسرية
يتشابه شكل مركز الماكينات من النوع الجسرية مع ماكينة التفريز الجسرية، حيث يتم ضبط المغزل عادةً بشكل عمودي. بالإضافة إلى جهاز تغيير الأداة الأوتوماتيكي، فإنه يحتوي أيضًا على ملحقات رأس مغزل قابلة للتبديل، ووظائف شاملة للماكينات بنظام التحكم الرقمي CNC، ويمكن استخدامه لأغراض متعددة. وهي مناسبة بشكل خاص لمعالجة قطع العمل الكبيرة أو المعقدة الشكل، كما هو موضح في الشكل 3.
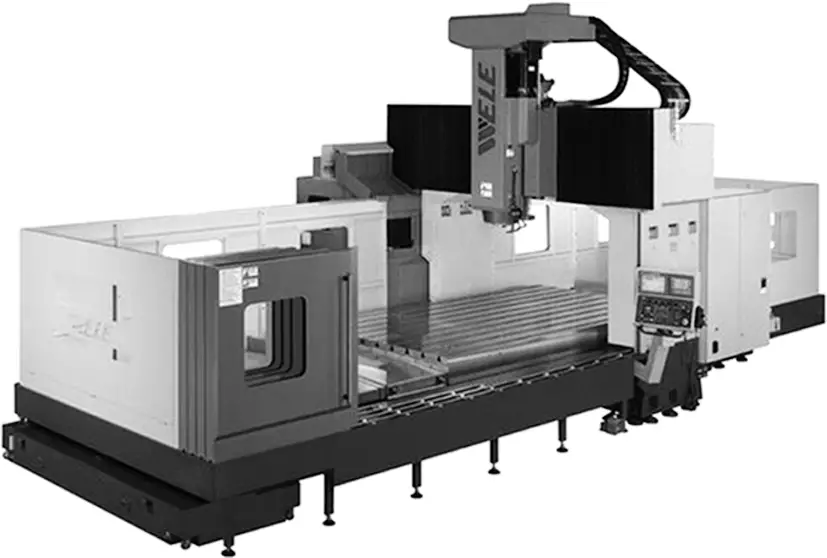
(4) مركز التصنيع الآلي خماسي الأوجه
مركز الماكينات خماسي الأوجه هو مركز تصنيع آلي يجمع بين وظائف مراكز الماكينات الرأسية والأفقية، أي مركز تصنيع آلي مركب للاستخدام الرأسي والأفقي على حد سواء، كما هو موضح في الشكل 4.
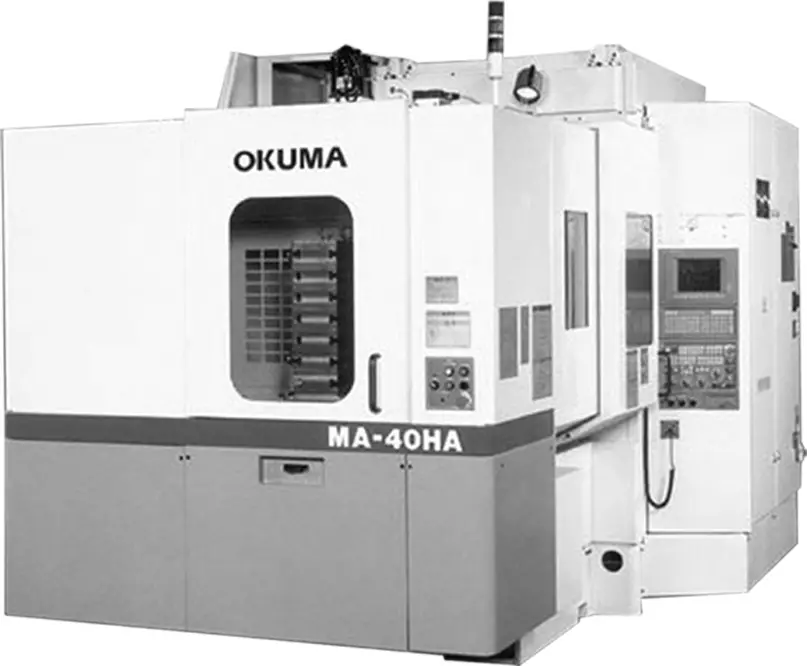
يمكن لمركز الماكينات خماسي الأوجه إكمال تصنيع جميع الجوانب الخمسة باستثناء سطح التركيب بعد تركيب واحد لقطعة العمل، مما يحسن بشكل كبير من دقة التصنيع وكفاءة الإنتاج، مع فوائد اقتصادية كبيرة.
هناك نوعان شائعان من مراكز الماكينات خماسية الأوجه: أحدهما حيث يمكن للمغزل أن يدور 90 درجة لتحقيق التصنيع الآلي الرأسي والأفقي؛ والآخر حيث لا يغير المغزل اتجاهه، ولكن تدور طاولة العمل الدوارة بنظام التحكم الرقمي بنظام التحكم الرقمي 90 درجة على طول المحور X، وبالتالي تدور الشُّغْلَة 90 درجة لإكمال تصنيع خمسة أسطح من الشُّغْلَة.
2. تطبيقات مراكز الماكينات
مراكز التصنيع الآلي باهظة الثمن، وتتطلب استثمارًا أوليًا كبيرًا، وتكاليف معالجة القطع عالية، وتتطلب مشغلين ذوي جودة عالية. ولذلك، من الضروري النظر بشكل شامل في الأجزاء المناسبة للمعالجة على مراكز الماكينات من جوانب مختلفة مثل الشكل ومتطلبات الدقة.
بشكل عام، تعد مراكز التصنيع الآلي مناسبة للقطع ذات الأشكال المعقدة والمتطلبات العالية الدقة والعمليات المتعددة وتلك التي تتطلب أنواعًا متعددة من أدوات الماكينات التقليدية والعديد من الأدوات والتركيبات ولا يمكن إكمالها إلا بعد عدة إعدادات وتعديلات.
(1) أجزاء من نوع الصندوق
تشير الأجزاء من النوع الصندوقي عمومًا إلى الأجزاء التي تحتوي على أكثر من نظام ثقب واحد، وتجويف داخلي معين، ونسبة معينة في الطول والعرض والارتفاع. هذه الأجزاء شائعة في صناعات مثل الماكينات والسيارات والفضاء، مثل كتل محركات السيارات، وأغطية علب التروس، وأغطية علب التروس، وأغطية رؤوس أدوات الماكينات، وصناديق المغزل، وكتل محركات الديزل، وأغطية مضخات التروس، إلخ.
تتطلب القِطع من النوع الصندوقي عمومًا نظام ثقب متعدد المواضع وتشغيل آلي مستوٍ، مما يجعلها أحد عناصر التشغيل الآلي الأساسية لمراكز الماكينات.
متطلبات التفاوت المسموح به، وخاصة متطلبات التفاوت الهندسي صارمة نسبيًا، وعادةً ما تتطلب عمليات طحن، وثقب، وحفر، وتوسيع، وشطب، وشطب، واستدقاق وعمليات أخرى. يمكن لإعداد واحد أن يكمل 60% إلى 95% من محتوى العملية لأدوات الماكينات التقليدية، مما يؤدي إلى دقة القطعة المتسقة والجودة المستقرة ودورات الإنتاج المختصرة إلى حد كبير وانخفاض التكاليف.
بالنسبة للقِطع ذات مواضع الماكينات المتعددة التي تتطلب دورانًا متعددًا لمنضدة الشغل لإكمالها، يتم اختيار مراكز الماكينات الأفقية بشكل عام؛ عندما يكون هناك عدد أقل من مواضع الماكينات ولا يكون الامتداد كبيرًا، يمكن اختيار مراكز الماكينات العمودية للتصنيع من طرف واحد.
(2) الأجزاء من نوع القرص والكم واللوح
الأجزاء مثل الأقراص أو الأكمام أو الأعمدة ذات مسارات مفاتيح أو ثقوب شعاعية، أو ذات أنظمة ثقوب موزعة أو أسطح منحنية على الوجه النهائي، على سبيل المثال، أكمام الأعمدة ذات الحواف، والأعمدة ذات مسارات مفاتيح أو رؤوس مربعة، إلخ. وبالإضافة إلى ذلك، هناك أجزاء من نوع الألواح ذات ثقوب متعددة الآلات، مثل أغطية المحركات المختلفة.
بالنسبة للقطع ذات الأقراص والأكمام والألواح ذات أنظمة الثقوب الموزعة أو الأسطح المنحنية على الوجه النهائي، تكون مراكز الماكينات العمودية مناسبة، بينما يمكن اختيار مراكز الماكينات الأفقية لتلك التي تحتوي على ثقوب شعاعية.
(3) الأجزاء ذات الأشكال الهيكلية المعقدة ومتطلبات الدقة العالية
غالبًا ما تحتوي القِطع ذات الأشكال الهيكلية المعقدة على أسطح تشغيل آلي متعددة تتكون من أسطح منحنية معقدة، وعادةً ما تتطلب تشغيل آلي متعدد الإحداثيات للربط، وهو أمر يصعب أو يستحيل تحقيقه بشكل عام على أدوات الماكينات التقليدية.
تحتل الأسطح المنحنية المعقدة مثل الأسطح الجانبية للطائرات والسيارات والمراوح والمراوح وقوالب تشكيل الأسطح المنحنية المختلفة مكانة مهمة في صناعة التصنيع الميكانيكي، خاصة في صناعات الطيران والسيارات وبناء السفن والدفاع. يتم اختيار مراكز الماكينات بشكل عام لمعالجة هذه الأنواع من الأجزاء، والتي تُعد أيضًا أجسام الماكينات الرئيسية لأدوات الماكينات بنظام التحكم الرقمي العادي.
تشمل القِطع النموذجية القِطع من نوع الكامة والقِطع من نوع المكرهة المتكاملة والقِطع من نوع القالب. يمكن أن يؤدي اختيار مراكز الماكينات لمعالجة القِطع المتوسطة والصغيرة ذات متطلبات الدقة العالية إلى تحقيق دقة أبعاد جيدة ودقة موضع الشكل، مع اتساق أبعاد جيد وجودة مستقرة.
عند تشكيل الأسطح المنحنية المعقدة، إذا لم تكن هناك مناطق تداخل في التشغيل الآلي أو نقاط عمياء، يمكن استخدام قواطع التفريز ذات الأطراف الكروية للتشغيل الآلي ثلاثي الإحداثيات. ينتج عن ذلك دقة تصنيع عالية ولكن بكفاءة منخفضة نسبيًا. إذا كانت هناك مناطق تداخل بالقطع أو بقع عمياء في الشُّغْلة، فمن الضروري التفكير في استخدام أدوات ماكينة الربط ذات الإحداثيات الأربعة أو الخمسة.
لا يمكن الاستفادة من ميزة تغيير الأدوات الأوتوماتيكي في مراكز الماكينات بشكل كامل عند تصنيع الأسطح المنحنية المعقدة، حيث إن تصنيع الأسطح المنحنية المعقدة يمر عمومًا بخطوات من التفريز الخشن إلى التفريز النهائي (شبه النهائي)، باستخدام عدد أقل من الأدوات، خاصةً في التصنيع الآلي للقطعة الواحدة مثل القوالب.
(4) أجزاء غير منتظمة الشكل
القِطع غير منتظمة الشكل هي مكونات ذات أشكال خارجية غير منتظمة، ويتطلب معظمها تصنيعًا آليًا مختلطًا في مواضع متعددة بنقاط وخطوط وأسطح مثل الأقواس والقواعد والقوالب والرقصات. تتميز الأجزاء غير المنتظمة الشكل عمومًا بصلابة ضعيفة وتثبيت معقد، وهي عرضة للتشوه أثناء القطع، ومن الصعب ضمان دقة التصنيع الآلي.
إذا تم استخدام أدوات الماكينات التقليدية في التصنيع الآلي، فهناك العديد من العمليات، والتركيبات المتعددة، وأوقات المعالجة الطويلة، ومن الصعب ضمان جودة التصنيع. في هذه الحالة، يمكن الاستفادة بشكل كامل من ميزة تركيز العملية لمراكز الماكينات في مراكز الماكينات، مع اعتماد تدابير عملية مناسبة لإكمال معظم أو كل محتوى الماكينات في إعداد واحد أو اثنين في وقت قصير نسبيًا.
عند تصنيع القِطع غير المنتظمة الشكل، كلما كان الشكل أكثر تعقيدًا وكلما زادت متطلبات الدقة، كلما زادت مزايا مراكز الماكينات والاستفادة منها. عند استخدام مراكز الماكينات لتصنيع القِطع، يمثل الوقت المستغرق في إعداد العملية وتحرير البرنامج نسبة كبيرة من إجمالي وقت العمل. لذلك، بالنسبة للإنتاج الدفعي الدوري للقِطع، يمكن استخدام نفس البرنامج مرارًا وتكرارًا عدة مرات، مما يقلل من دورة الإنتاج بشكل كبير.
ثالثًا. خصائص التصنيع ونطاق تطبيق مراكز التصنيع الآلي
1. خصائص التصنيع لمراكز التصنيع الآلي
مقارنةً بأدوات الماكينات بنظام التحكم الرقمي التقليدية، تتميز مراكز الماكينات بالخصائص البارزة التالية.
(1) تركيز العملية
مراكز الماكينات مزودة بمخازن أدوات وأجهزة تغيير الأدوات تلقائيًا. بعد إعداد قطعة عمل واحدة، يمكن لنظام التحكم الرقمي باستخدام الحاسب الآلي التحكم في الماكينة لتحديد الأدوات وتغييرها تلقائيًا وفقًا لعمليات مختلفة، وتغيير سرعة مغزل الماكينة تلقائيًا، ومعدل التغذية، ومسار حركة الأداة بالنسبة لقطعة العمل، والوظائف المساعدة الأخرى. يمكنها تنفيذ عمليات متعددة بشكل مستمر مثل التفريز، والحفر، والتوسيع، والتثقيب، والثقب، والثقب، والثقب على أسطح التشغيل المختلفة لقطعة العمل تلقائيًا، وهي مناسبة لتصنيع القِطع السطحية المعقدة مثل الكامات، والمبيتات، والأقواس، وألواح الغطاء، والقوالب.
(2) دقة تشغيل آلي عالية
مثل أدوات ماكينات التصنيع باستخدام الحاسب الآلي الأخرى، تتميز مراكز الماكينات بخاصية دقة التصنيع العالية. وعلاوة على ذلك، نظرًا لتركيز عمليات التصنيع، تتجنب مراكز الماكينات تدفقات العمليات الطويلة وتقلل من التدخل البشري، مما يؤدي إلى دقة تصنيع أعلى وجودة تصنيع أكثر استقرارًا.
(3) قدرة قوية على التكيف في التشغيل الآلي
تتمتع مراكز التصنيع الآلي بقدرة قوية على التكيف مع أغراض التصنيع، أي مرونة عالية. لا تنعكس مرونة الإنتاج في مراكز الماكينات ليس فقط في الاستجابة السريعة للمتطلبات الخاصة ولكن أيضًا في القدرة على تحقيق الإنتاج على دفعات بسرعة، وبالتالي تحسين القدرة التنافسية في السوق.
(4) تقليل كثافة العمالة وتحسين ظروف العمل
تقوم مراكز الماكينات بمعالجة القِطع تلقائيًا وفقًا لإجراءات مبرمجة مسبقًا، وإكمال تصنيع القِطع. يحتاج المشغلون فقط إلى تشغيل لوحة التحكم، وتحميل وتفريغ قطع العمل، وضبط الأدوات، وإجراء عمليات الفحص الوسيطة للعمليات الرئيسية، ومراقبة تشغيل الماكينة، دون الحاجة إلى عمليات يدوية متكررة ثقيلة. وهذا يقلل كثيرًا من كثافة العمالة والتوتر، ويحسن أيضًا من ظروف العمل.
(5) كفاءة إنتاج عالية (5)
مراكز الماكينات مجهزة بمخازن أدوات وأجهزة تبديل آلي للأدوات. تحتوي بعض مراكز التصنيع الآلي أيضًا على إمكانيات تبديل آلي لمحطة العمل. يمكن تركيز عمليات متعددة على ماكينة واحدة، مما يقلل من وقت إعداد الشُّغْلَة والقياس ووقت ضبط الماكينة، بالإضافة إلى تقليل وقت نقل المنتجات شبه المصنعة ومعالجتها وتخزينها، مما يقلل بشكل كبير من الوقت الإضافي ويحسن كفاءة الإنتاج.
(6) فوائد اقتصادية جيدة
عند استخدام مراكز المعالجة الآلية لمعالجة الأجزاء، تكون تكلفة المعدات المخصصة لكل جزء باهظة الثمن. ومع ذلك، فإن كفاءتها الإنتاجية العالية، ودقة التصنيع العالية، والتشغيل الآلي المستقر، تقلل من معدل الخردة، وتؤدي تكاليف معدات المعالجة المنخفضة إلى انخفاض تكاليف الإنتاج بشكل كبير، وبالتالي تحقيق فوائد اقتصادية جيدة.
(7) يسهل تحديث إدارة الإنتاج
يسمح استخدام مراكز التصنيع الآلي لمعالجة القِطع بحساب دقيق لوقت معالجة القِطع، ويبسط بشكل فعال الفحص وإدارة الأدوات والتركيبات وإدارة المنتجات شبه المصنعة، مما يساعد على تحديث إدارة الإنتاج.
على الرغم من أن مراكز التصنيع الآلي تتمتع بالمزايا المذكورة أعلاه، إلا أنها باهظة الثمن ومعقدة تقنيًا وصعبة الصيانة وذات تكاليف معالجة عالية وتتطلب إدارة عالية الجودة وموظفي تشغيل. لذلك، ينبغي النظر في عوامل مختلفة بشكل شامل لتحقيق أفضل الفوائد الاقتصادية للمؤسسة.
2. نطاق تطبيق مراكز التصنيع الآلي
مراكز الماكينات هي أدوات ماكينات عالية الكفاءة وعالية الدقة ومؤتمتة للغاية مع العديد من المزايا التي لا يمكن لأدوات الماكينات العادية أن تضاهيها. في الوقت الحالي، يتوسع نطاق تطبيق مراكز الماكينات باستمرار. لاستغلال أفضل مزايا مراكز الماكينات بشكل كامل، فهي أكثر ملاءمة لمعالجة الأجزاء ذات الخصائص التالية.
(1) أجزاء إنتاج متعددة الأصناف وصغيرة الحجم
تنعكس مرونة الإنتاج في مراكز الماكينات ليس فقط في الاستجابة السريعة لمعالجة القطع الخاصة ولكن أيضًا في القدرة على تحقيق إنتاج الدُفعات بسرعة والاستحواذ على حصة سوقية سريعة.
(2) الأجزاء ذات الأشكال والهياكل المعقدة
تحتوي بعض القِطع على أشكال وهياكل معقدة تتطلب معدات معالجة باهظة الثمن عند تشكيلها على أدوات الماكينات التقليدية. حتى أن استخدام ماكينات التفريز بنظام التحكم الرقمي يتطلب تغييرات متعددة للأدوات والتركيبات، في حين أن استخدام مركز الماكينات يمكن أن يحقق عمليات متعددة مثل التفريز والحفر والثقب والتثقيب والاستدقاق في إعداد واحد.
(3) قطع غالية الثمن وعالية الدقة
بعض الأجزاء منخفضة الطلب ولكنها باهظة الثمن، وهي مكونات حرجة لا يمكن التخلص منها. وهي تتطلب دقة عالية ووقت إنتاج قصير. إذا تم استخدام أدوات الماكينات التقليدية في المعالجة، تحتاج ماكينات متعددة لتنسيق العمل، ومن السهل إنتاج منتجات معيبة بسبب العوامل البشرية.
باستخدام مراكز التصنيع الآلي للمعالجة، يتم التحكم في عملية الإنتاج بالكامل من خلال البرامج، مما يؤدي إلى تجنب العوامل المتداخلة في تدفق العملية، مما يؤدي إلى كفاءة إنتاج عالية وجودة مستقرة.
(4) أجزاء الإنتاج المتكررة دوريًا
بعض المنتجات لها طلبات دورية وموسمية في السوق. إذا تم استخدام خطوط إنتاج متخصصة، فسيكون ذلك غير مربح. يؤدي استخدام المعدات العادية إلى كفاءة معالجة منخفضة وجودة غير مستقرة. ومع ذلك، باستخدام مركز التصنيع الآلي، بعد قطع القطعة الأولى بنجاح، يمكن الاحتفاظ بالبرنامج والمعلومات ذات الصلة. في المرة التالية التي يتم فيها إنتاج المنتج، يمكن أن يبدأ الإنتاج بأقل وقت تحضير.
(5) الأجزاء التي تتطلب تعديلات متكررة
عندما يتغير كائن المعالجة، يجب فقط تعديل برنامج المعالجة وتعديل معلمات الأداة لمعالجة الأجزاء الجديدة. وهذا يقلل إلى حد كبير من دورة إعداد الإنتاج ويوفر اختصارًا لتطوير المنتجات الجديدة وتحسين المنتج والتعديلات.
(6) الأجزاء صعبة القياس
بالنسبة لبعض القِطع التي يصعب قياسها، يمكن الاستفادة من الخصائص عالية الدقة لمركز الماكينات نفسه بشكل كامل لضمان دقة معالجة القِطع.
رابعًا. الهيكل الرئيسي والمعايير الفنية لمراكز المعالجة الآلية
1. مكونات عمود الدوران
يعد مكون المغزل أحد الأجزاء المهمة في مركز الماكينات. تؤثر صلابته ودقة دورانه بشكل مباشر على جودة معالجة الشُّغْلَة. يتكون مكون عمود الدوران بشكل أساسي من صندوق عمود الدوران، ومحرك عمود الدوران، وعمود الدوران، ومحامل عمود الدوران.
يستخدم محرك عمود الدوران لمركز الماكينات بشكل أساسي محركات عمود الدوران DC ومحركات عمود الدوران AC لتحقيق تغيير السرعة بدون خطوات للحركة الرئيسية. يتم التحكم في جميع إجراءات بدء تشغيل المغزل وإيقافه وتغيير سرعته بواسطة نظام التحكم الرقمي باستخدام الحاسب الآلي، ويتم إجراء القطع من خلال الأدوات المثبتة على المغزل، وهو عنصر إخراج الطاقة لعمليات القطع.
2. نظام الدعم
(1) سرير
السرير هو أساس أداة الماكينة، مما يتطلب صلابة ثابتة وديناميكية عالية بما فيه الكفاية والاحتفاظ بالدقة. أثناء تلبية متطلبات التصميم الإجمالية، ينبغي بذل الجهود لتحقيق هيكل معقول، وترتيب مناسب للأضلاع، وضمان تقنية معالجة باردة وساخنة جيدة.
بالنسبة لمراكز الخراطة الميكانيكية، يتم استخدام سرير مائل بشكل عام لتحسين الصلابة. يمكن للسرير المائل تحسين حالة القوة أثناء القطع، ويمكن أن يشكل المقطع العرضي هيكل تجويف مغلق. يمكن ملء الجزء الداخلي منه بنوى الطين والخرسانة كمواد تخميد، والتي تبدد طاقة الاهتزاز من خلال التآكل النسبي أثناء الاهتزاز.
(2) العمود
يدعم عمود مركز الماكينات بشكل أساسي صندوق عمود الدوران ويستوعب حركة المحور Z للمغزل. يجب أن يتمتع العمود بصلابة جيدة وثبات حراري. تستخدم مراكز الماكينات هيكل صندوقي مغلق، مع ألواح مائلة داخلية لتحسين مقاومة العمود للانحناء والالتواء. يتم تحقيق الهيكل بأكمله من خلال الصب.
(3) أدلة إرشادية
تستخدم معظم مراكز التصنيع الميكانيكي موجهات دحرجة خطية. تتميز الموجهات الدوارة بمعاملات احتكاك منخفضة للغاية واختلافات صغيرة بين معاملات الاحتكاك الثابتة والديناميكية. وهي توفر حركة سلسة منخفضة السرعة دون زحف، وبالتالي تحقق دقة عالية في تحديد المواقع.
ومع ذلك، يجب أن يعتمد تحقيق هذه الدقة على الحالة الصحيحة للقاعدة. وإلا، فإن أخطاء ارتفاع الدعم الرأسي ستؤدي إلى تشويه جانبي هيكلي، مما يؤدي إلى تغيرات في مقاومة الاحتكاك في جميع أنحاء نطاق الحركة، مما يؤدي إلى أخطاء في دقة تحديد المواقع.
في الماضي، عندما كان يتم استخدام الموجهات المنزلقة في الماضي، كانت أسطح التزاوج بين الموجهات تتطلب الكشط والضبط الدقيق. أثناء التجميع، يمكن اكتشاف تشوه الموجه وتصحيحه من خلال الضبط. مع الموجهات الدوارة، لا توجد عملية تصحيح، مما يجعل من الصعب تجنب تشوه السرير أو تشوه المسار الناجم عن التثبيت. لذلك، يجب استخدام قاعدة دعم ثلاثية النقاط.
3. نظام مؤازر
(1) نظام مؤازرة عمود الدوران
مع تطور تكنولوجيا الماكينات بنظام التحكم الرقمي، أصبحت أدوات الماكينات بنظام التحكم الرقمي الحديثة ذات متطلبات عالية بشكل متزايد لنقل المغزل. على سبيل المثال، فهي تتطلب سرعة قابلة للتعديل باستمرار على نطاق واسع، ونطاق واسع من الطاقة الثابتة، وقدرة على الدفع الرباعي. لتلبية احتياجات التغيير التلقائي للأدوات وتقنيات معالجة معينة في مراكز الماكينات، يلزم التحكم في التوجيه عالي الدقة للمغزل.
يعتمد تغير سرعة محرك عمود الدوران حاليًا بشكل أساسي على شكلين: أحدهما هو محرك عمود الدوران مع تغير السرعة غير المتدرج المقسم بالتروس؛ والآخر هو محرك عمود الدوران الذي يقود عمود الدوران من خلال حزام مسنن متزامن أو حزام نقل. يُطلق على النوع الأخير من محرك عمود الدوران أيضًا اسم المحرك واسع النطاق أو محرك القطع الثقيل، ويتميز بنطاق واسع من الطاقة الثابتة.
ينقسم التحكم في توجيه عمود الدوران إلى توجيه ميكانيكي وتوجيه كهربائي. في الوقت الحالي، تعتمد جميع أنظمة الماكينات بنظام التحكم الرقمي المحلية والأجنبية المتوسطة إلى المتطورة على التحكم في التوجيه الكهربائي.
1) نظام محرك عمود الدوران بالتيار المستمر.
غالبًا ما تستخدم محركات مغزل التيار المستمر طرق التحكم في سرعة الثايرستور. نظام مؤازرة التغذية بالتيار المستمر هو نظام تحكم ثنائي الحلقة يتكون من حلقة سرعة وحلقة تيار للتحكم في جهد المحرك لمحرك عمود الدوران DC. ويستخدم محرك عمود الدوران محركًا مثارًا بشكل منفصل، مع لف الإثارة ولف المحرك بشكل مستقل عن بعضهما البعض.
من القيمة الصغرى إلى القيمة المقدرة لسرعة المحرك، يظل تيار الإثارة ثابتًا، مما يحقق التحكم في السرعة المنظمة للجهد، والتي تنتمي إلى التحكم في عزم الدوران الثابت. من القيمة المقدرة إلى القيمة القصوى، يتناقص تيار الإثارة، مما يحقق التحكم في السرعة المنظمة بالتدفق المغناطيسي، والذي ينتمي إلى التحكم في القدرة الثابتة.
2) نظام محرك عمود الدوران بالتيار المتردد.
مع تطور تكنولوجيا التحكم في سرعة التيار المتردد، يعتمد محرك عمود الدوران لأدوات الماكينات بنظام التحكم الرقمي CNC الآن في الغالب طريقة التحكم في محرك عمود الدوران مع محول التردد. يتكون العاكس الموجود على جانب شبكة الطاقة من دائرة مقوم ثلاثي الأطوار يتم التحكم فيها بالكامل مكونة من ستة ثايرستور. يمكن أن تعمل هذه الدائرة في حالة التصحيح، وتوفر الطاقة مباشرةً إلى الدائرة الوسيطة، ويمكنها أيضًا العمل في حالة العاكس، لتكمل مهمة التغذية المرتدة للطاقة إلى شبكة الطاقة.
يتألف العاكس من جانب الحمل من ستة ترانزستورات طاقة مع ثنائيات ثنائية حرة مضادة للتوازي. من خلال التحكم في كمبيوتر المجال المغناطيسي، يقوم العاكس من جانب الحمل بإخراج جهد تعديل عرض النبضات الجيبية ثلاثية الأطوار (PWM)، مما يمكّن المحرك من الحصول على تيار عزم الدوران المطلوب وتيار الإثارة.
يتراوح نطاق سعة جهد PWM الناتج ثلاثي الأطوار PWM من 0-430 فولت، مع نطاق ضبط التردد من 0-300 هرتز. أثناء الكبح المتجدد، تقوم طاقة المحرك بشحن المكثف من خلال الثنائيات الستة للمحول. عندما يتجاوز الجهد على المكثف 600 فولت، يتم إرجاع الطاقة على المكثف إلى شبكة الطاقة من خلال التحكم في المنظم وعاكس جانب الشبكة.
(2) نظام مؤازرة التغذية
1) نظام مؤازرة تغذية عرض النبضات المعدل النبضي.
تتحكم طريقة التحكم في سرعة تعديل عرض النبضة في وقت تبديل الترانزستورات عالية الطاقة باستخدام مُعدِّل عرض النبضة. يقوم بتحويل إشارة التحكم في السرعة إلى جهد موجة مربعة بتردد معين، والذي يتم تطبيقه على أطراف المحرك لمحرك سيرفو التيار المستمر. من خلال التحكم في عرض الموجة المربعة، يتم تغيير متوسط الجهد عند أطراف المحرك، وبالتالي تحقيق الغرض من التحكم في سرعة المحرك المؤازر.
تقوم وحدة المعالجة المركزية لنظام التحكم الرقمي باستخدام الحاسب الآلي بإخراج سلسلة من إشارات النبضات من خلال المحوِّل البيني. تتم مقارنة هذه النبضات، بعد مرورها عبر مضاعف الأوامر CMR، مع نبضات التغذية الراجعة للموضع. يتم إرسال الفرق الناتج إلى سجل الخطأ، ثم يتم حسابه مع كسب الموضع وتعويض الإزاحة، وإرساله إلى PWM لتعديل عرض النبضة. بعد ذلك، يتم تحويله إلى D/A أو جهد تناظري وإرساله إلى وحدة التحكم في السرعة كإشارة التحكم في السرعة VCMD.
يتم إرسال النبضات من أداة تشفير النبضات، بعد التأكد من عدم وجود فصل للإشارة بواسطة كاشف الفصل، إلى كاشف الطور لتحديد اتجاه دوران المحرك من خلال فحص مجموعتي النبضات PA و PB.
تخضع إحدى الإشارتين من كاشف الطور لتحويل F/V لتصبح إشارة التغذية المرتدة للسرعة TSA؛ ويمر الخرج الآخر عبر مضاعف الكشف DMR ليصبح إشارة التغذية المرتدة للموضع. يتم استخدام عداد النقطة المرجعية وإشارة PC ذات الدورة الواحدة لعملية إرجاع النقطة المرجعية لطريقة الشبكة.
2) نظام مؤازرة محرك التغذية بالتيار المتردد.
على الرغم من أن أنظمة مؤازرة التغذية بالتيار المستمر تتمتع بوظائف ممتازة لتنظيم السرعة، إلا أن المحركات المستخدمة تحتوي على فرش ومبدلات للسرعة معرضة للتآكل. وعلاوة على ذلك، فإن الشرر الناتج أثناء التبديل يحد من السرعة القصوى للمحرك.
بالإضافة إلى ذلك، فإن محركات التيار المستمر لها هياكل معقدة، ويصعب تصنيعها، وتستهلك كميات كبيرة من النحاس ومواد الحديد، ولها تكاليف تصنيع عالية. لكن محركات التيار المتردد لا تعاني من هذه العيوب.
في السنوات العشرين الماضية، مع ظهور أجهزة إلكترونية جديدة عالية الطاقة، عززت الإنجازات في تكنولوجيا تحويل الترددات الجديدة، ونظرية التحكم الحديثة، وتكنولوجيا التحكم الرقمي للحاسبات الدقيقة في التطبيقات العملية التطور السريع لتكنولوجيا أجهزة تغذية التيار المتردد. وقد حلت أنظمة مؤازرة التغذية بالتيار المتردد محل أنظمة مؤازرة التغذية بالتيار المستمر تمامًا.
نظرًا لأن المحركات المؤازرة بالتيار المتردد تستخدم محركات متزامنة ذات مغناطيس دائم للتيار المتردد، فإن جهاز محرك التغذية بالتيار المتردد هو في الأساس جهاز محرك بمحرك تيار مستمر مبدل إلكترونيًا.
4. مخزن الأدوات وجهاز تغيير الأدوات الأوتوماتيكي
تستخدم مراكز الماكينات مخازن الأدوات لتحقيق تغيير الأدوات، وهي طريقة تغيير الأدوات المستخدمة حاليًا على نطاق واسع في مراكز الماكينات. مع مخزن الأدوات، تحتاج الماكينة إلى عمود دوران ثابت واحد فقط لحمل الأدوات، وهو أمر مفيد لتحسين صلابة عمود الدوران.
يزيد مخزن الأدوات المستقل من سعة تخزين الأدوات بشكل كبير، وهو أمر مفيد لتوسيع وظائف الماكينة ويمكنه عزل العوامل المختلفة التي تؤثر على دقة التصنيع بشكل أفضل.
يمكن تقسيم عملية تغيير العِدَّة باستخدام مخزن العِدَّة إلى فئتين بناءً على ما إذا كان هناك ذراع ميكانيكي في العملية: تغيير العِدَّة بذراع ميكانيكي وتغيير العِدَّة بدون ذراع ميكانيكي. في عملية تغيير العِدَّة بذراع ميكانيكي، يزيل أحد الذراعين الميكانيكيين العِدَّة المنتهية من عمود الدوران، بينما يزيل ذراع ميكانيكي آخر في نفس الوقت العِدَّة المنتظرة من مخزن العِدَّة. بعد ذلك، يتبادل الاثنان المواضع لإكمال عملية تغيير العِدَّة.
لتغيير العِدَّة بدون ذراع ميكانيكي، يتم تخزين الأدوات في المخزن بشكل موازٍ لعمود الدوران، ويتم وضع الأدوات في موضع يمكن الوصول إليه بواسطة عمود الدوران. أثناء تغيير الأدوات، يتحرك رأس عمود الدوران إلى موضع تغيير الأدوات فوق المخزن. باستخدام حركة المحور Z لعمود الدوران، يتم إدخال الأداة النهائية في الموضع الفارغ المطلوب في المخزن. بعد ذلك، تدور الأداة المنتظرة في المخزن إلى وضع الاستعداد. يتحرك عمود الدوران في الاتجاه Z لاسترداد الأداة المنتظرة من المخزن وإدخالها في عمود الدوران.
الأنظمة ذات الأذرع الميكانيكية أكثر مرونة من حيث تكوين مخزن الأدوات، والوضع النسبي لعمود الدوران، وعدد الأدوات، مع أزمنة تغيير أدوات أقصر. تتميز الطريقة التي لا تحتوي على أذرع ميكانيكية بهيكل أبسط ولكن أزمنة تغيير الأدوات أطول.
(1) أنواع مخازن أدوات مركز التشغيل الآلي
هناك أنواع مختلفة من مخازن العِدَّة، حيث أن النوع القرصي ونوع السلسلة هما الأكثر استخدامًا في مراكز الماكينات.
في هيكل القرص (انظر الشكل 5)، يمكن تخزين الأدوات على طول محور عمود الدوران أو شعاعيًا أو بزاوية. التثبيت المحوري للأدوات هو الأكثر إحكامًا، ولكن لتغيير الأدوات لمحاذاة عمود الدوران، يجب تدوير بعض الأدوات في المخزن بزاوية 90 درجة في موضع تغيير الأدوات.
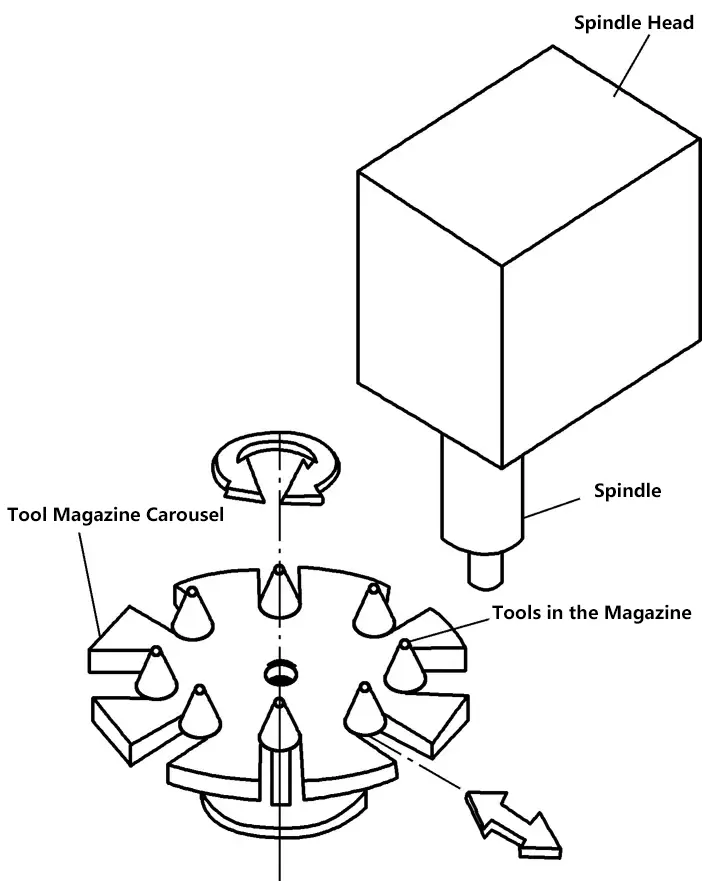
بالنسبة للقدرات الكبيرة لمخازن الأدوات، يمكن اعتماد هيكل من نوع الأسطوانة لتسهيل التخزين والاسترجاع مع الحفاظ على هيكل مضغوط. في الوقت الحالي، يتم تركيب العديد من مخازن الأدوات على الجزء العلوي أو الجانبي من عمود الماكينة، وبعضها مثبت على أساسات منفصلة لعزل الاهتزازات الناجمة عن دوران مخزن الأدوات.
يظهر الهيكل الأساسي لمخزن الأدوات من نوع السلسلة في الشكل 6. وعادة ما يكون لها سعة أدوات أكبر من مخزن الأدوات من النوع القرصي وهيكل أكثر مرونة. يمكن زيادة سعة مخزن الأدوات عن طريق تمديد السلسلة، أو يمكن تحسين استخدام المساحة عن طريق طي السلسلة وإعادة لفها. بالنسبة لمتطلبات سعة الأدوات الكبيرة جدًا، يمكن أيضًا اعتماد هياكل متعددة السلاسل.
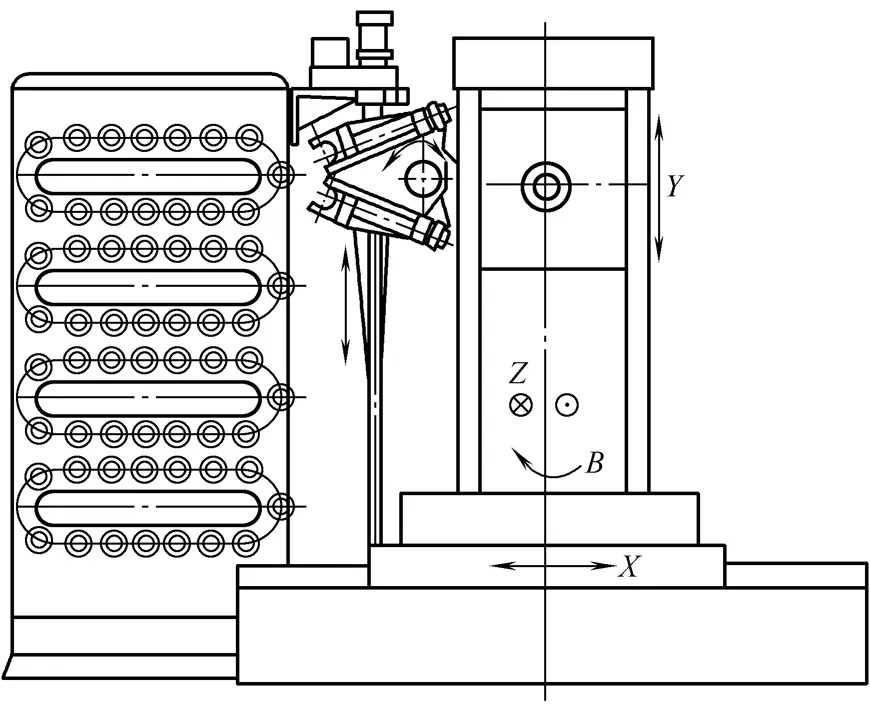
(2) مبادل العِدَّة الأوتوماتيكي لمراكز الماكينات
يمكن تقسيم مبادلات الأدوات الأوتوماتيكية إلى خمسة أشكال أساسية: نوع البرج الدوّار، ونوع الدوران 180 درجة، ونوع الإدخال الدوّار، ونوع الدوران ثنائي المحور، ونوع المغزل المباشر. يمكن تثبيت الأدوات الخاصة بالتغيير التلقائي للأدوات في حوامل أدوات خاصة، وفي كل مرة يتم فيها تغيير الأداة، يتم إدخال حامل الأدوات مباشرةً في عمود الدوران.
1) مبادل أدوات من النوع المدور.
يعد استخدام برج دوّار لتغيير الأدوات هو أول شكل من أشكال تغيير الأدوات تلقائيًا. كما هو موضح في الشكل 7، يتكون البرج الدوّار من عدة أعمدة دوران متصلة برأس طاقة ماكينة التفريز (صندوق عمود الدوران). قبل تشغيل البرنامج، يتم تثبيت الأدوات في أعمدة الدوران، وعندما تكون هناك حاجة إلى أداة معينة، يدور البرج الدوّار إلى الموضع المقابل.
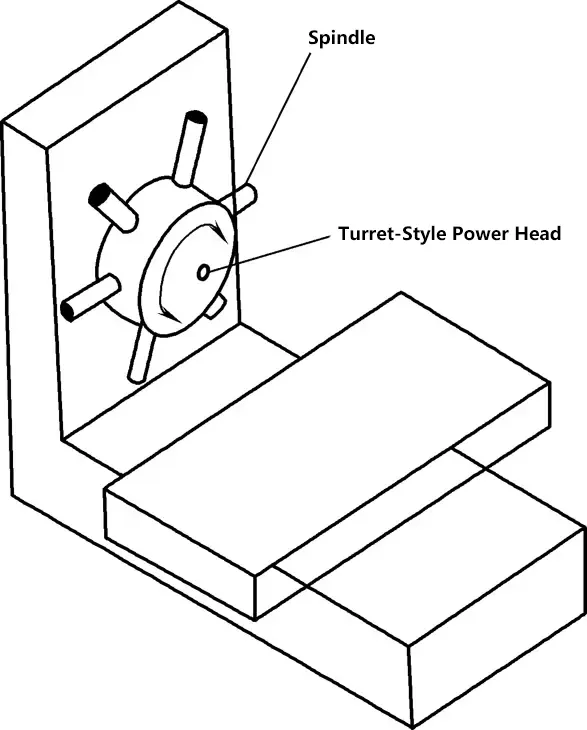
عيب هذا الجهاز هو أن عدد المغازل محدود. عند استخدام عدد أدوات أكثر من عدد أعمدة الدوران، يجب على المشغل إزالة الأدوات المستخدمة وتركيب الأدوات اللازمة للبرامج اللاحقة. لا ينطوي تغيير الأداة من نوع البرج على تفكيك الأداة، بل تغيير الأداة وحامل الأداة معًا، لذا فإن هذه الطريقة لتغيير الأداة سريعة جدًا. في الوقت الحالي، لا تزال ماكينات الحفر NC وغيرها من ماكينات الحفر من النوع الدوّار تستخدم مخازن الأدوات من النوع الدوّار.
2) مبادل أدوات من نوع الدوران 180 درجة.
أبسط مبادل أدوات هو مبادل الأدوات من نوع الدوران 180 درجة، كما هو موضح في الشكل 8.
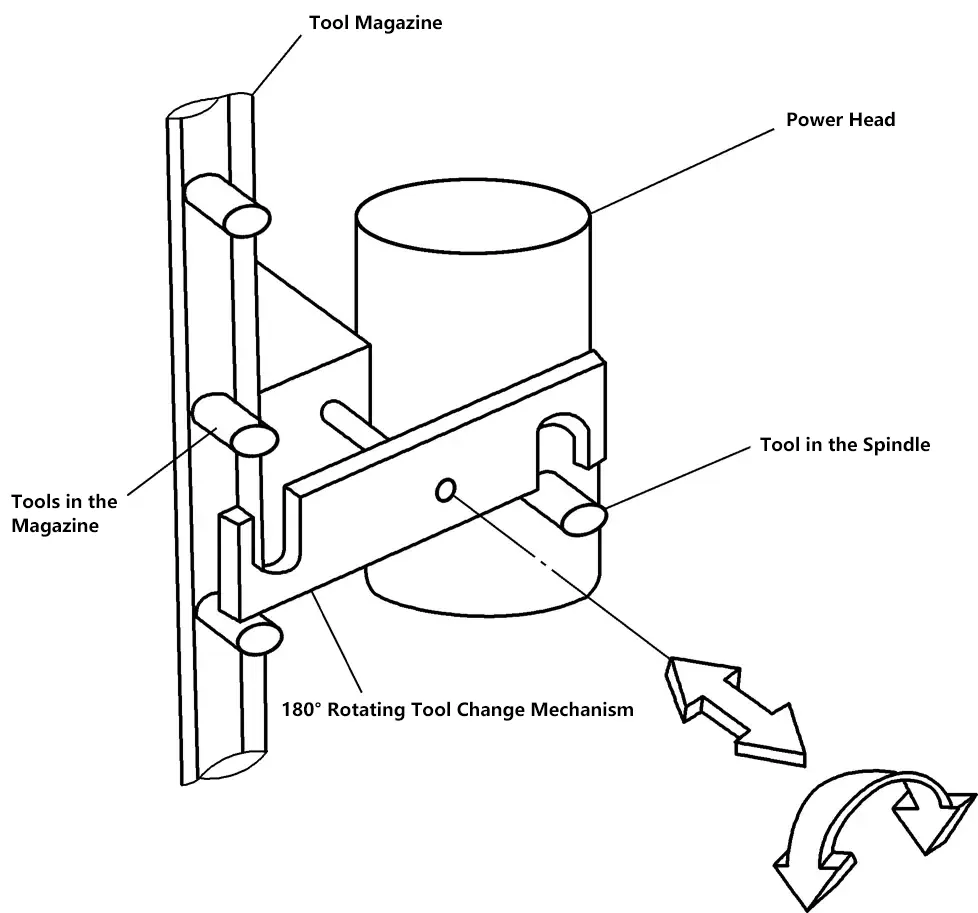
عند تلقي أمر تغيير العِدَّة، يقوم نظام التحكم في الماكينة بتحريك عمود الدوران إلى موضع تغيير العِدَّة المحدد؛ وفي نفس الوقت، يتحرك مخزن العِدَّة إلى الموضع المناسب، ويدور مبادل العِدَّة ويتشابك مع كل من عمود الدوران والعِدَّة في مخزن العِدَّة.
يقوم عمود السحب بتحرير الأداة من عمود الدوران، ويقوم مبادل الأدوات بإزالة الأدوات من مواضعها الخاصة بها؛ يدور مبادل الأدوات 180 درجة ويزيل أداة عمود الدوران وأداة مخزن الأدوات.
أثناء دوران مبادل الأدوات، يقوم مخزن الأدوات بإعادة ضبط موضعه لاستقبال الأداة التي تمت إزالتها من عمود الدوران؛ بعد ذلك، يقوم مبادل الأدوات بتثبيت الأداة الجديدة في عمود الدوران والأداة التي تمت إزالتها في مخزن الأدوات؛ وأخيرًا، يعود مبادل الأدوات إلى وضعه الأصلي "الاستعداد".
عند هذه النقطة، يكتمل تغيير الأداة، ويستمر البرنامج في التشغيل. تتمثل الميزة الرئيسية لمبادل الأدوات هذا في هيكله البسيط، وحركات أقل، وتغيير الأدوات بسرعة؛ أما العيب الرئيسي فهو أنه يجب تخزين الأدوات في مستوى موازٍ لعمود الدوران، وبالمقارنة مع مخازن الأدوات المثبتة على الجانب أو الخلف، يمكن أن تدخل البُرادة وسائل القطع بسهولة إلى حامل الأدوات، لذلك من الضروري توفير حماية إضافية للأدوات.
يمكن أن تتسبب البُرادة على السطح المستدق لحامل العِدَّة في حدوث أخطاء في تغيير العِدَّة بل ومن المحتمل أن تتلف حامل العِدَّة وعمود الدوران. تستخدم بعض مراكز الماكينات عمود نقل وتضع مخزن الأدوات على الجانب.
عندما يتم استدعاء أمر تغيير العِدَّة، يزيل عمود النقل العِدَّة من مخزن العِدَّة، ويدور إلى مقدمة الماكينة، ويضع نفسه في موضعه للتشابك مع مبادل العِدَّة. يمكن استخدام مبادل الأدوات من نوع الدوران 180 درجة لكل من الماكينات الأفقية والرأسية.
3) مبادل أدوات من نوع الإدخال الدوار.
هذا هو أحد الأشكال الأكثر استخدامًا وهو نسخة محسنة من مبادل الأدوات من النوع الدوار. آلية الإدخال الدوارة عبارة عن مزيج من مبادل العِدَّة وقضيب النقل. يوضح الشكل 9 مبدأ عمل مبادل العِدَّة الدوَّار من نوع الإدخال الدوَّار المطبق على مركز الماكينات الأفقي. التصميم الهيكلي لمبادل الأدوات هذا هو في الأساس نفس تصميم مبادل الأدوات من نوع الدوران 180 درجة.
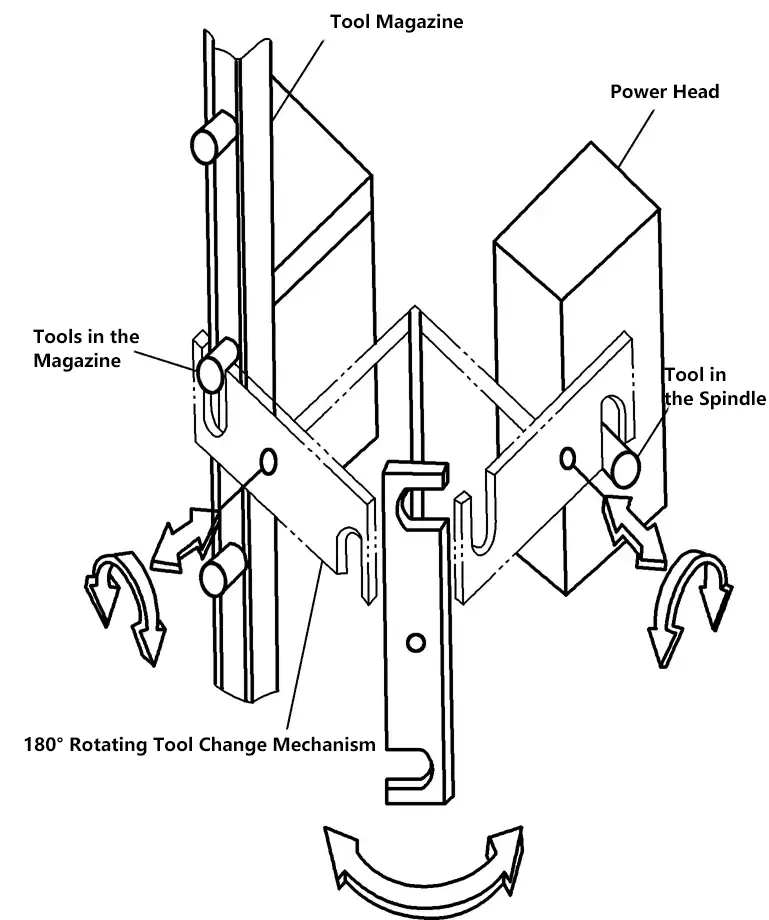
عندما يتم استلام أمر تغيير الأداة، يتحرك عمود الدوران إلى نقطة تغيير الأداة، ويدور مخزن الأدوات إلى الموضع المناسب، مما يسمح لمبادل الأدوات باسترداد الأداة المطلوبة من الفتحة الخاصة بها؛ يدور مبادل الأدوات ويخرج الأداة من مخزن الأدوات الموجود على جانب الماكينة، ويدور مبادل الأدوات إلى مقدمة الماكينة، حيث يزيل الأداة من عمود الدوران، ويدور 180 درجة ويثبت الأداة الجديدة في عمود الدوران.
وفي الوقت نفسه، يتحرك مخزن الأدوات إلى الموضع المناسب لاستقبال الأداة التي تمت إزالتها من عمود الدوران؛ يدور مبادل الأدوات إلى جانب الماكينة ويضع الأداة التي تمت إزالتها من عمود الدوران في الفتحة الموجودة في مخزن الأدوات.
الميزة الرئيسية لهذا الجهاز هي أن الأدوات يتم تخزينها على جانب الماكينة، مما يجنب إمكانية إتلاف البُرادة لعمود الدوران أو حامل الأدوات. بالمقارنة مع مبادل الأدوات من نوع الدوران 180 درجة، فإن عيبه هو أن هناك المزيد من الإجراءات أثناء عملية تغيير الأدوات، مما يؤدي إلى وقت أطول لتغيير الأدوات.
4) مبادل أدوات من نوع الدوران ثنائي المحور.
يوضح الشكل 10 مبدأ عمل مبادل العِدَّة ثنائي المحاور من نوع الدوران. يمكن استخدام مبادل العِدَّة هذا مع مخازن العِدَّة المثبتة على الجانب أو الخلف، وخصائصه الهيكلية هي الأنسب لمراكز الماكينات العمودية.
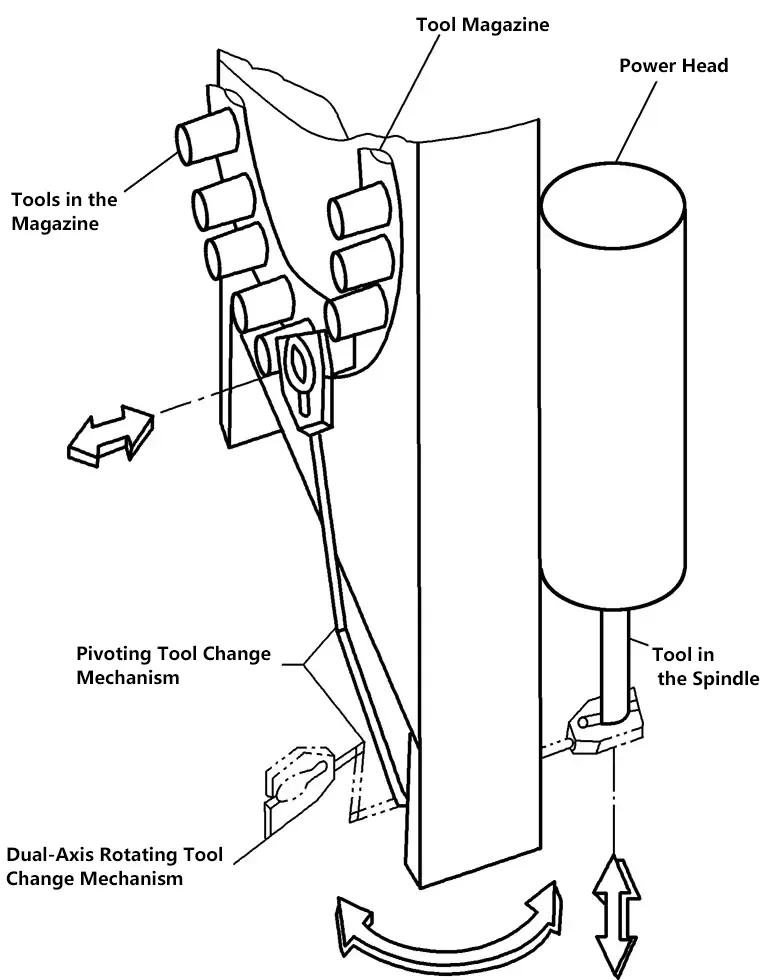
عند تلقي أمر تغيير العِدَّة، تبدأ آلية تغيير العِدَّة في التحرك من وضع "الانتظار"، وتمسك العِدَّة في مخزن العِدَّة وتزيلها، وتدور إلى مخزن العِدَّة، وتعيد العِدَّة إلى مخزن العِدَّة، ثم تسترجع العِدَّة المطلوبة من مخزن العِدَّة، وتدور باتجاه عمود الدوران، وتثبت العِدَّة في عمود الدوران؛ وأخيرًا، تعود إلى وضع "الانتظار"، لتكمل عملية تغيير العِدَّة.
الميزة الرئيسية لهذا الجهاز هي أن مخزن الأدوات يقع على جانب الماكينة أو خلفها، مما يوفر أقصى قدر من الحماية للأدوات. عيبه هو أن هناك المزيد من عمليات نقل الأدوات وحركاتها. وقد تم استبدال هذا الجهاز في مراكز الماكينات العمودية تدريجيًا بمبدلات العِدَّة من نوع الدوران 180 درجة ومبدلات العِدَّة من نوع المغزل المباشر.
5) مبادل الأدوات المباشر من نوع المغزل.
يختلف مبادل الأدوات من نوع عمود الدوران المباشر عن الأشكال الأخرى من مبادلات الأدوات. في هذا الجهاز، إما أن تتحرك مخزن العِدَّة مباشرةً إلى موضع عمود الدوران، أو يتحرك عمود الدوران مباشرةً إلى مخزن العِدَّة. يوضح الشكل 11 تطبيق مبادل العِدَّة من نوع عمود الدوران المباشر في مركز الماكينات الأفقي.
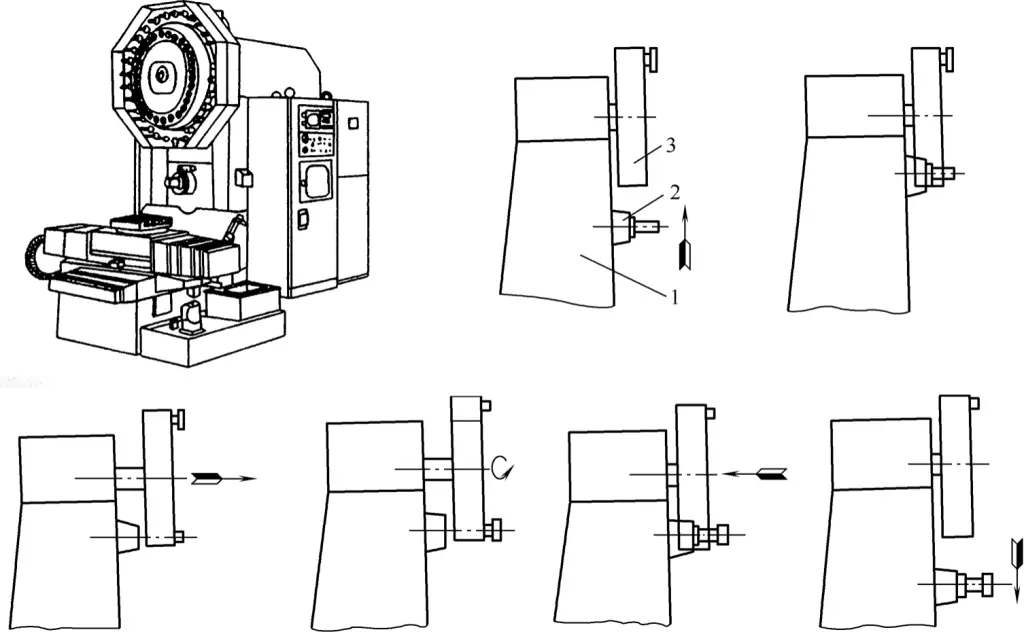
1-العمود الرئيسي
2-صندوق المغزل 2-المغزل
3-مجلة الأدوات 3
أثناء تغيير الأداة، يتحرك عمود الدوران إلى موضع تغيير الأداة، وتدور مخزن الأدوات من النوع القرصي إلى موضع فتحة الأداة المطلوبة، وتنقل الأداة من موضع "الانتظار" إلى موضع تغيير الأداة، وتشتبك مع حامل الأداة المثبت في عمود الدوران.
يتراجع عمود السحب من حامل الأدوات، ويتحرك مخزن الأدوات إلى الأمام ويزيل الأداة؛ ثم يدور مخزن الأدوات لمحاذاة الأداة المطلوبة مع عمود الدوران، ويتحرك للخلف، ويدخل الأداة في عمود الدوران ويثبتها؛ وأخيرًا، يتحرك مخزن الأدوات بعيدًا عن عمود الدوران، ويتحرك لأعلى، ويعود إلى وضع "الانتظار"، ويكمل تغيير الأداة.
بالنسبة لمراكز الماكينات العمودية، تحقق المراكز الأصغر حجمًا بشكل عام تغيير الأدوات عن طريق تحريك مخزن الأدوات؛ وبالنسبة لبعض الماكينات الكبيرة، تختلف عملية تغيير الأدوات عما سبق، حيث إن مخزن الأدوات كبير جدًا بحيث لا يمكن تحريكه بشكل ملائم، لذلك إما أن يتحرك المغزل لإزالة الأدوات وتركيبها، أو يتم استخدام ذراع روبوتية لتغيير الأدوات.
يوضح الشكل 12 هيكل الذراع الروبوتية والقابض، ويوضح الشكل 13 عملية عمل تغيير الأداة الروبوتية.
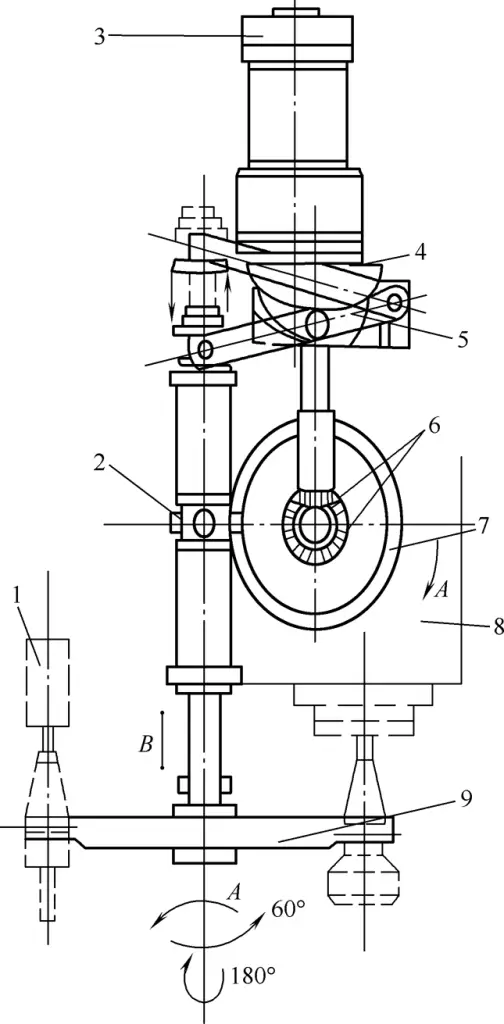
1-حامل الأدوات
2-العمود المتقاطع
3-المحرك
4-كاميرا ذات فتحة أسطوانية (الذراع لأعلى ولأسفل)
5-الحمالة
6-الترس ذو 6 مستويات
7-أسطوانة 7 كاميرا (دوران الذراع)
8-صندوق مغزل 8
9-ذراع تغيير الأدوات 9-ذراع تغيير الأدوات
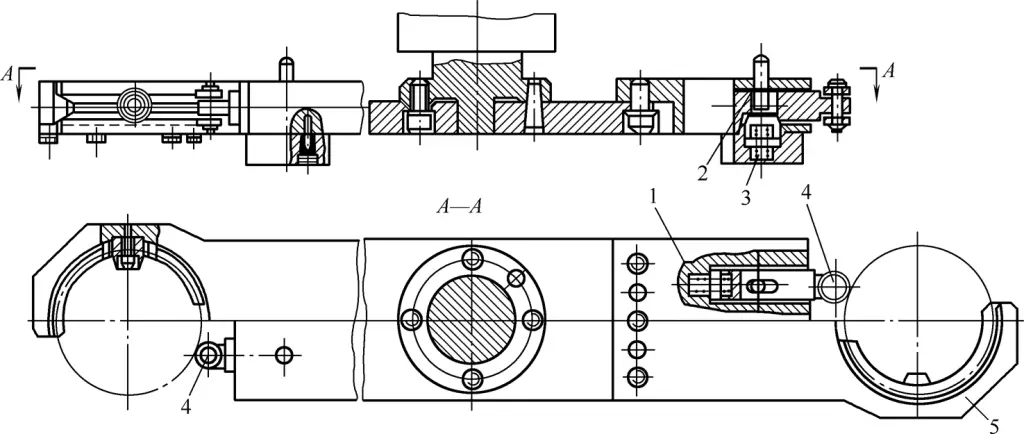
1،3-سبرينغز
2-دبوس القفل
4-الدبوس النشط
5-القابض
V. الوظائف الرئيسية لنظام التحكم الرقمي باستخدام الحاسب الآلي
تتشابه وظائف نظام التحكم الرقمي باستخدام الحاسب الآلي لمراكز الماكينات مع وظائف ماكينات التفريز باستخدام الحاسب الآلي في العديد من أوجه التشابه مع وظائف وأوامر ماكينات التفريز باستخدام الحاسب الآلي، ولكن أنظمة التحكم الرقمي باستخدام الحاسب الآلي المهيأة لمراكز الماكينات لها وظائف وأوامر أكثر ثراءً وشمولاً مقارنةً بماكينات التفريز باستخدام الحاسب الآلي.
تختلف أنظمة الماكينات بنظام التحكم الرقمي المهيأة لمراكز الماكينات التي تنتجها الشركات المصنعة المختلفة، ولكن وظائفها الأساسية متشابهة تقريبًا. تُستخدم مراكز الماكينات المجهزة بأنظمة FANUC وأنظمة SIEMENS على نطاق واسع. وباستثناء تغيير الأداة، فإن برمجة وتشغيل مراكز الماكينات هذه هي في الأساس نفس ماكينات التفريز بنظام التحكم الرقمي.
تتضمن وظائف أنظمة التحكم الرقمي باستخدام الحاسب الآلي بشكل عام وظائف أساسية ووظائف اختيارية. والوظائف الأساسية هي الوظائف الأساسية لنظام التحكم الرقمي باستخدام الحاسوب، بينما الوظائف الاختيارية هي وظائف اختيارية يمكن للمستخدمين اختيارها بناءً على خصائص الماكينة والغرض منها. لأنظمة الماكينات بنظام التحكم الرقمي CNC المختلفة وظائف مختلفة. فيما يلي وصف موجز لبعض الوظائف باستخدام نظام FANUC كمثال.
1. وظيفة التحكم متعدد الإحداثيات
يمكن لنظام التحكم التحكم التحكم في عدد من محاور الإحداثيات، في إشارة إلى الحد الأقصى لعدد محاور الإحداثيات التي يمكن لنظام التحكم الرقمي باستخدام الحاسب الآلي التحكم فيها، بما في ذلك المحاور الخطية والمحاور الدوارة. محاور الإحداثيات الخطية الأساسية هي المحاور X وY وZ؛ ومحاور الإحداثيات الدوارة الأساسية هي المحاور A وB وC. يشير عدد المحاور المتزامنة إلى عدد محاور الإحداثيات التي يمكن لنظام الماكينة بنظام التحكم الرقمي باستخدام الحاسب الآلي التحكم فيها للتحرك في وقت واحد وفقًا لمتطلبات التصنيع الآلي.
تشير وظيفة التحكم إلى عدد المحاور التي يمكن لجهاز ماكينة التحكم الرقمي CNC التحكم بها ويمكنه التحكم بها في وقت واحد. وظيفة التحكم هي أحد مؤشرات الأداء الرئيسية لجهاز ماكينة التحكم الرقمي بنظام التحكم الرقمي.
تشمل محاور التحكم المحاور المتحركة والمحاور الدوارة والمحاور الأساسية والمحاور الإضافية. كلما زاد عدد المحاور التي يمكن التحكم بها، وخاصةً كلما زاد عدد المحاور التي يمكن التحكم بها في وقت واحد، كلما زادت وظائف جهاز الماكينة بنظام التحكم الرقمي CNC، وكلما زاد تعقيد جهاز الماكينة بنظام التحكم الرقمي، وكلما زادت صعوبة البرمجة.
2. وظيفة تعويض الأداة
تتضمن وظيفة تعويض الأداة تعويض طول الأداة وتعويض نصف قطر الأداة. يتضمن تعويض طول الأداة أيضًا تعويض هندسة الأداة وتعويض تآكل الأداة.
(1) وظيفة تعويض طول الأداة
يشير تعويض طول الأداة إلى التعويض المحوري للأداة، والذي يزيد أو يقلل من الموضع الفعلي للأداة في الاتجاه المحوري بقيمة إزاحة مقارنة بالقيمة المبرمجة. لا تقوم هذه الوظيفة بتغيير ارتفاع سطح القطع تلقائيًا فحسب، بل تقلل أيضًا من أخطاء الإعداد المحوري للأداة.
(2) وظيفة تعويض تآكل الأدوات
سوف تتآكل الأدوات أثناء الاستخدام، وإذا لم يتم إجراء تعويض تآكل الأداة في الوقت المناسب، فسوف يؤدي ذلك إلى انخفاض دقة تصنيع قطع العمل. من خلال ضبط تعويض تآكل الأداة مع الحفاظ على تعويض هندسة الأداة دون تغيير، يتم تعديل تعويض طول الأداة بشكل غير مباشر لضمان دقة تصنيع الشُّغْلَة بالقطع.
(3) وظيفة تعويض نصف قطر الأداة
باستخدام هذه الوظيفة، يمكن إزاحة مركز الأداة تلقائيًا عن محيط الشُّغْلَة بمقدار نصف قطر أداة واحدة، مما يجعل من الملائم حساب وبرمجة وفقًا لأبعاد الكفاف الفعلية للشُّغْلَة أثناء البرمجة، دون الحاجة إلى الحساب والبرمجة بناءً على مسار مركز قاطع التفريز.
يمكن استخدام هذه الوظيفة أيضًا لتعويض دقة التصنيع غير الكافية لقواطع التفريز عن طريق تغيير قيمة تعويض نصف قطر الأداة، وتوسيع نطاق اختيار قطر الأداة والخطأ المسموح به لإعادة طحن الأداة.
يمكن أيضًا استخدام طريقة تغيير قيمة تعويض نصف قطر الأداة لتحقيق الطحن متعدد الطبقات والتشغيل الآلي الخشن والدقيق باستخدام نفس برنامج المعالجة، أو لتحسين دقة تصنيع الأجزاء. بالإضافة إلى ذلك، يمكن أيضًا استخدام تغيير العلامات الموجبة والسالبة لقيمة تعويض نصف قطر الأداة لمعالجة بعض قطع العمل التي تحتاج إلى مطابقتها مع بعضها البعض باستخدام نفس برنامج المعالجة الآلية.
3. وظيفة الدورة الثابتة
الدورات الثابتة عبارة عن سلسلة مبرمجة مسبقًا من عمليات التشغيل الآلي النموذجية المخزنة في الذاكرة، والتي يمكن استدعاؤها باستخدام أكواد G عند الحاجة. يمكن أن يؤدي استخدام وظائف الدورات الثابتة إلى تبسيط إعداد البرنامج بشكل كبير. تشمل الدورات الثابتة دورات الحفر، ودورات الثقب، ودورات التثقيب، ودورات اللولبة، وغيرها.
4. وظيفة التصنيع الآلي بالمرآة
يُعرف التصنيع الآلي بالمرآة أيضًا باسم التصنيع الآلي بالتناظر المحوري. بالنسبة لقطعة عمل متناظرة بالنسبة لمحور الإحداثيات، باستخدام وظيفة المعالجة الآلية بالمرآة، يجب كتابة ربع أو ربعين فقط من البرنامج، ويمكن تحقيق خطوط الأرباع الأخرى من خلال المعالجة الآلية بالمرآة.
5. وظيفة الدوران
يمكن لهذه الوظيفة تدوير برنامج التشغيل الآلي المبرمج بأي زاوية داخل مستوى التشغيل الآلي للتنفيذ.
6. البرنامج الفرعي
في بعض الأجزاء المشغولة آليًا، غالبًا ما تظهر مسارات تشغيل آلي متطابقة هندسيًا، وعند كتابة برامج التشغيل الآلي، توجد مقاطع برامج ذات تسلسلات ثابتة وأنماط متكررة تظهر في برامج متعددة.
لتبسيط البرمجة، يمكن برمجة مقاطع برامج الماكينات النموذجية هذه ذات التسلسلات الثابتة والأنماط المتكررة كبرامج فرعية بتنسيق معين ثم إدخالها في الذاكرة.
إذا احتاج البرنامج الرئيسي إلى برنامج فرعي معين أثناء التنفيذ، فيمكنه استدعاء ذلك البرنامج الفرعي من خلال تعليمات استدعاء برنامج فرعي بصيغة محددة. بعد تنفيذ البرنامج الفرعي، يعود البرنامج الفرعي إلى البرنامج الرئيسي ويستمر في تنفيذ أجزاء البرنامج التالية.
7. وظيفة برنامج الماكرو
تشير برامج ماكرو المستخدم إلى البرامج الفرعية التي تحتوي على متغيرات. تسمح برامج ماكرو المستخدم باستخدام المتغيرات، والعمليات الحسابية والمنطقية، والتحويلات الشرطية، مما يجعل كتابة البرامج لنفس عمليات التشغيل الآلي أكثر ملاءمة وسهولة. في برنامج التشغيل الآلي، يمكن استخدام تعليمات بسيطة، وهي تعليمات ماكرو المستخدم، لاستدعاء برنامج ماكرو المستخدم.
8. الوظيفة التحضيرية
تُستخدم الدالة التحضيرية، والمعروفة أيضًا باسم الدالة G، لتحديد وضع العمل لماكينة التفريز باستخدام الحاسب الآلي. تتكون تعليمات الدالة G من رمز العنوان G متبوعًا برقمين.
9. الوظيفة الإضافية
الدالة المساعدة هي عملية مساعدة أساسية في التصنيع الآلي باستخدام الحاسب الآلي، ويمثلها رمز العنوان M متبوعًا بأي رقمين. قد يكون للأنظمة المختلفة وظائف M مختلفة. تُستخدم الدوال المساعدة لتحديد بدء/إيقاف تشغيل/تشغيل عمود الدوران، وتشغيل/إيقاف تشغيل سائل القطع، إلخ.
10. وظيفة التغذية
تمثل دالة التغذية، والمعروفة أيضًا باسم الدالة F، معدل التغذية ويشار إليها برمز العنوان F متبوعًا بعدة أرقام. يمكن ضبط معدل التغذية الفعلي من خلال مقبض تجاوز معدل التغذية على لوحة تشغيل ماكينة التحكم الرقمي CNC.
11. وظيفة المغزل
تشير وظيفة عمود الدوران لمركز الماكينات بشكل أساسي إلى تحديد سرعة عمود الدوران (الأداة سرعة القطع) أثناء عملية التشغيل الآلي. يتم تمثيل دالة عمود الدوران برمز العنوان S متبوعًا بعدة أرقام، مع كون الوحدة r/دقيقة. على سبيل المثال، S1000 يشير S1000 إلى سرعة عمود الدوران 1000 ص/دقيقة.
12. وظيفة العرض البياني
يمكن تجهيز أجهزة الماكينات بنظام التحكم الرقمي باستخدام الحاسب الآلي بأجهزة CRT أحادية اللون أو ملونة، وتنفيذ شاشات عرض الأحرف والرسوم البيانية من خلال البرامج والواجهات. يمكنها عرض برامج التصنيع الآلي والمعلمات وقيم التعويض المختلفة ومواضع الإحداثيات ومعلومات الإنذار ومسارات حركة الأداة الديناميكية وما إلى ذلك.
13. وظيفة التحكم في التشغيل
تحتوي مراكز الماكينات عادةً على وظائف مثل تشغيل كتلة واحدة، والتشغيل الجاف، والتخطي، وقفل الماكينة، وتشغيل المحاكاة الرسومية، والتوقف في حالات الطوارئ.
14. وظيفة إنذار التشخيص الذاتي
تشير وظيفة إنذار التشخيص الذاتي إلى قدرة نظام التحكم الرقمي باستخدام الحاسب الآلي على التشخيص الذاتي لأعطال البرمجيات والأجهزة. يمكن استخدام هذه الوظيفة لمراقبة ما إذا كانت أداة الماكينة بأكملها وعملية التشغيل الآلي بأكملها طبيعية، والإنذار الفوري في حالة وجود أعطال، وبالتالي تحديد نوع الأعطال وموقعها بسرعة، مما يقلل من وقت التوقف عن العمل الناجم عن الأعطال.
15. وظيفة الاتصال
عادةً ما تكون أنظمة الماكينات بنظام التحكم الرقمي الحديثة مزودة بوجه عام بواجهات RS232C أو واجهات DNC، مما يسمح بنقل الإشارات عالية السرعة مع أجهزة كمبيوتر عالية المستوى. كما يمكن لأنظمة الماكينات بنظام التحكم الرقمي المتطورة أن تتصل بالإنترنت لتلبية متطلبات نظام التصنيع المرن (FMS) ونظام التصنيع المتكامل بالكمبيوتر (CIMS).
سادسًا. تطوير واتجاه تكنولوجيا التصنيع باستخدام الحاسب الآلي
1. عملية تطوير أنظمة التحكم الرقمي باستخدام الحاسب الآلي
نشأت أدوات ماكينات التحكم الرقمي باستخدام الحاسوب لأول مرة في الولايات المتحدة. ومنذ طرح أول ماكينة ثقب وتفريز ثلاثية الإحداثيات بنظام التحكم الرقمي في العالم في عام 1952، مرت أنظمة التحكم الرقمي باستخدام الحاسوب بمرحلتين وستة أجيال من التطوير (انظر الجدول 1).
استخدم الجيل الأول من أنظمة التحكم الرقمي باستخدام الحاسب الآلي مكونات الأنابيب المفرغة من الهواء، والتي كانت كبيرة الحجم، ومنخفضة الموثوقية، ومرتفعة السعر. وكانت تُستخدم بشكل أساسي في الصناعة العسكرية ولم يتم تطبيقها على نطاق واسع، وكانت أحجام إنتاجها منخفضة.
ظهر الجيل الثاني في عام 1961، ويتألف من أنظمة التحكم الرقمي باستخدام الحاسب الآلي القائمة على الترانزستورات، والتي حسّنت الموثوقية وقللت الحجم إلى حد كبير.
وكان الجيل الثالث هو نظام التحكم الرقمي باستخدام الحاسب الآلي ذو الدوائر المتكاملة الذي تم تسويقه في عام 1965، والذي قلل إلى حد كبير من حجم أجهزة التحكم الرقمي باستخدام الحاسب الآلي وحسّن الموثوقية بشكل كبير، مما جعله مقبولاً لدى عامة المستخدمين. شهد كل من حجم الإنتاج وتنوع أدوات الماكينات بنظام التحكم الرقمي تطوراً كبيراً.
كانت الأجيال الثلاثة المذكورة أعلاه من أنظمة التحكم الرقمي باستخدام الحاسب الآلي في الأساس عبارة عن أجهزة كمبيوتر متخصصة، تعتمد بشكل أساسي على الأجهزة لتنفيذ وظائف التحكم المختلفة. وكانت هذه هي المرحلة الأولى، التي تسمى أنظمة التحكم العددي (NC).
في عام 1968، تم تطبيق الحواسيب الصغيرة في أنظمة الماكينات بنظام التحكم الرقمي CNC، ليصبح الجيل الرابع من أنظمة الماكينات بنظام التحكم الرقمي. وأصبح تطبيق المعالجات الدقيقة في عام 1974 الجيل الخامس من أنظمة الماكينات بنظام التحكم الرقمي باستخدام الحاسوب. في عام 1990، أصبحت أنظمة الماكينات بنظام التحكم الرقمي المفتوحة القائمة على منصات الحاسبات الشخصية الجيل السادس من أنظمة الماكينات بنظام التحكم الرقمي.
تنتمي الأجيال الثلاثة الأخيرة إلى المرحلة الثانية التي تسمى أنظمة التحكم العددي بالكمبيوتر (CNC).
الجدول 1 ستة أجيال من تطوير نظام التحكم الرقمي باستخدام الحاسوب الآلي
تاريخ تطوير نظام CNC | سنة الظهور العالمي | سنة الظهور في الصين | |
المرحلة الأولى (أنظمة NC) | الجيل الأول من نظام CNC الأنبوبي الفراغي CNC الجيل الثاني من نظام CNC الترانزستور الرقمي من الترانزستور الجيل الثالث من نظام الدوائر المتكاملة CNC | 1952 1961 1965 | 1958 1964 1972 |
المرحلة الثانية (أنظمة CNC) | الجيل الرابع من نظام الحاسب الآلي الصغير CNC الجيل الخامس من نظام المعالجات الدقيقة CNC الجيل السادس من نظام التحكم الرقمي باستخدام الحاسب الآلي المفتوح (CNC) المفتوح القائم على منصة الكمبيوتر الشخصي (الصناعي) | 1968 1974 1990 | 1978 1981 1992 |
2. اتجاهات تطوير تكنولوجيا التصنيع باستخدام الحاسب الآلي
وفي الوقت الحالي، تمتلك الصين أنظمة ماكينات بنظام التحكم الرقمي باستخدام الحاسوب ذات حقوق ملكية فكرية مستقلة، ولكن الغالبية العظمى من أدوات ماكينات التحكم الرقمي باستخدام الحاسوب التي تعمل بكامل طاقتها لا تزال تستخدم أنظمة ماكينات بنظام التحكم الرقمي باستخدام الحاسوب الأجنبية. من من منظور أداة الماكينة بشكل عام، لا تزال هناك فجوة كبيرة مقارنة بنظيراتها الأجنبية من حيث الموثوقية والدقة ومستوى الأتمتة وكفاءة الإنتاج.
مع تطور العلوم والتكنولوجيا وظهور تقنيات التصنيع المتقدمة في جميع أنحاء العالم، أصبحت متطلبات تكنولوجيا التصنيع باستخدام الحاسب الآلي أعلى بشكل متزايد. ومع تطور التقنيات ذات الصلة، مثل القطع فائق السرعة والتصنيع الآلي فائق الدقة، أصبحت مؤشرات الأداء الأعلى مطلوبة لهياكل أدوات الماكينات ومحركات المغزل وأنظمة الماكينات بنظام التحكم الرقمي وأنظمة المؤازرة لأدوات ماكينات التحكم الرقمي باستخدام الحاسوب، مما يؤدي إلى اتجاهات التطوير السبعة التالية في تكنولوجيا أدوات ماكينات التحكم الرقمي باستخدام الحاسوب.
(1) دقة عالية
تتضمن الدقة العالية لأدوات الماكينات بنظام التحكم الرقمي دقة هندسية عالية لأداة الماكينة ودقة تصنيع عالية. الدقة الهندسية العالية هي الأساس لتحسين دقة التشغيل الآلي. أهم جانب من جوانب الدقة الهندسية هو دقة تحديد المواقع. وقد أدى التحسن في دقة تحديد المواقع، إلى جانب تحسين الخصائص الهيكلية للماكينة والاستقرار الحراري، إلى تحسين دقة التصنيع الآلي لأدوات الماكينات بنظام التحكم الرقمي بشكل كبير.
على سبيل المثال: تحسنت دقة التشغيل الآلي لمراكز التصنيع الآلي من ± 0.01 مم في السابق إلى ± 0.005 مم، أو حتى أعلى من ذلك. لتحقيق أهداف دقة أعلى، يتم اعتماد التدابير التالية بشكل أساسي:
1) نظام محرك سيرفو.
لقد أدى اعتماد أنظمة مؤازرة التيار المتردد الرقمية إلى تحسين أداء المؤازرة بشكل كبير من حيث دقة تحديد المواقع وسرعة التغذية وجوانب أخرى مقارنة بأنظمة المؤازرة التناظرية السابقة ذات التيار المستمر. حتى أنه كان هناك ما يسمى بطرق التغذية المؤازرة الخطية المؤازرة "صفر الإرسال" باستخدام محركات خطية لتشغيل طاولة أداة الماكينة مباشرة، مما أدى إلى تحسين دقة التشغيل الآلي بشكل كبير.
2) تقنية التحكم في التغذية الأمامية.
ضاعفت أنظمة المؤازرة السابقة الانحراف بين موضع الأمر والموضع الفعلي في كسب حلقة الموضع، وتم استخدام الناتج كأمر سرعة للتحكم في سرعة المحرك. كان لهذه الطريقة دائمًا خطأ تأخر في تتبع الموضع، مما أدى إلى تدهور ظروف التشغيل الآلي عند معالجة الزوايا أو الأقواس.
يضيف ما يسمى بالتحكم المعزز ما يسمى بالتحكم المعزز طريقة التحكم في أمر السرعة إلى نظام التحكم الأصلي، مما يقلل بشكل كبير من خطأ تأخر التتبع، وبالتالي تحسين دقة التصنيع الآلي للقطع الزاوية.
3) تقنية التحكم التعويضي غير الخطي للاحتكاك الديناميكي والثابت للأدوات الآلية.
يمكن أن يؤدي عدم خطية الاحتكاك الديناميكي والساكن في أدوات الماكينة إلى زحف السرج. وبالإضافة إلى اتخاذ تدابير لتقليل الاحتكاك الساكن في هيكل الماكينة، فإن أنظمة المؤازرة الرقمية الجديدة لديها وظيفة التحكم في التعويض التلقائي لعدم خطية الاحتكاك الديناميكي والساكن في الأنظمة الميكانيكية.
4) تطوير تكنولوجيا التعويض وتطبيقها على نطاق واسع.
تستخدم أدوات الماكينات بنظام التحكم الرقمي CNC الحديثة وظيفة التعويض البرمجي لأنظمة التحكم العددي بالكمبيوتر لإجراء تعويضات مختلفة على نظام المؤازرة، مثل تعويض خطأ النقطة الثابتة للحركة المحورية، وتعويض خطأ درجة لولب الرصاص، وتعويض رد الفعل العكسي، وتعويض التشوه الحراري، إلخ.
5) مكافئ نبضي عالي الدقة.
يمكن لمكافئ النبض عالي الدقة تحسين دقة تحديد المواقع وقابلية التكرار.
6) اعتماد أجهزة كشف المواقع عالية الدقة.
على سبيل المثال: أجهزة التشفير النبضي عالية الدقة، والدوائر التقسيمية الفرعية المكونة من معالجات دقيقة مدمجة، والتي تحسن الدقة بشكل كبير.
(2) سرعة عالية
لطالما كان تحسين كفاءة الإنتاج أحد أهداف تطوير تكنولوجيا الأدوات الآلية. ويرجع ظهور أدوات الماكينات بنظام التحكم الرقمي وتطورها السريع جزئياً إلى كفاءتها الإنتاجية الأعلى بكثير مقارنةً بأدوات الماكينات التقليدية.
في السنوات الأخيرة، تحسنت كفاءة إنتاج أدوات ماكينات التحكم الرقمي باستخدام الحاسب الآلي بشكل ملحوظ، وذلك بشكل أساسي عن طريق تقليل وقت القطع والوقت الإضافي غير المتصل بالقطع. يتحقق تقليل وقت القطع عن طريق زيادة سرعة القطع، أي زيادة سرعة المغزل.
زادت سرعة المغزل لمراكز الماكينات من 4000-6000 دورة/دقيقة قبل 10 سنوات إلى 8000-12000 دورة/دقيقة حاليًا، حيث وصلت أعلى سرعة إلى أكثر من 100000 دورة/دقيقة. كما زادت سرعة مغزل المخارط بنظام التحكم الرقمي إلى 5000-20000 دورة/دقيقة، وزادت السرعة الخطية لعجلات الطحن إلى 100-200 م/ثانية.
وفقًا لأحدث الإحصاءات، لا يتجاوز وقت القطع لمراكز الماكينات 55% من إجمالي وقت العمل. لذلك، يعد تقليل وقت عدم القطع وسيلة رئيسية لتحسين كفاءة الإنتاج. يتكون وقت عدم القطع من جزأين: أحدهما هو وقت الاجتياز السريع، وهو الوقت اللازم للحركة السريعة؛ والآخر هو الوقت الإضافي، وهو بشكل أساسي وقت تغيير الأداة ووقت تغيير الشُّغْلَة.
لتقصير وقت الاجتياز السريع، من الضروري زيادة سرعة الحركة السريعة. في الوقت الحالي، وصلت السرعة العامة للحركة السريعة إلى 20 ~ 24 م / دقيقة، وبعضها حوالي 30 م / دقيقة، وأسرعها يمكن أن تصل إلى 60 م / دقيقة.
وقد أتاح ظهور محركات مؤازرة تغذية الحركة الخطية على وجه الخصوص إمكانية زيادة سرعة الحركة بشكل أكبر. بالإضافة إلى ذلك، لتقليل وقت الإجراءات المساعدة، من الضروري تقصير وقت التغيير التلقائي للأداة والتغيير التلقائي لقطعة العمل.
في الوقت الحاضر، وصل وقت دوران البرج الدوّار لمخارط الماكينات بنظام التحكم الرقمي إلى 0.4 إلى 0.6 ثانية، ووصل وقت تغيير الأدوات الأوتوماتيكي لمراكز الماكينات إلى حوالي 3 ثوانٍ، ويمكن أن يصل أسرع وقت إلى 1 ثانية. تم تقليل وقت تغيير المنصة النقالة لمراكز الماكينات من 12 إلى 20 ثانية في الماضي إلى 6 إلى 10 ثوانٍ، وأسرعها يصل إلى 2.5 ثانية.
في الوقت الحالي، يتم اتخاذ التدابير بشكل رئيسي من الجوانب التالية لتحسين مؤشرات السرعة:
1) نظام CNC.
المعالج الدقيق هو المكون الأساسي لأنظمة التحكم الرقمي باستخدام الحاسب الآلي الحديثة. وتستخدم المعالجات الدقيقة ذات البت والتردد الأعلى لتحسين سرعة الحوسبة الأساسية للنظام. وحاليًا، تم الانتقال من وحدات المعالجة المركزية 16 بت إلى وحدات المعالجة المركزية 32 بت، ويتم تطويرها نحو وحدات المعالجة المركزية 64 بت. يتم اعتماد المعالجات الدقيقة 32 بت وهياكل المعالجات الدقيقة متعددة المعالجات لتحسين قدرة النظام على معالجة البيانات، أي لزيادة سرعة ودقة حسابات الاستيفاء.
2) تكوين PLC مدمج قوي وعالي السرعة.
من خلال تحسين سرعة تشغيل المجلس التشريعي المنطقي القابل للبرمجة، فإنه يلبي متطلبات التشغيل الآلي عالي السرعة لأدوات ماكينات التحكم الرقمي باستخدام الحاسب الآلي. تحتوي وحدات التحكم المنطقي القابلة للبرمجة القابلة للبرمجة الجديدة على وحدات معالجة مركزية مخصصة، مع سرعة تنفيذ التعليمات الأساسية التي تصل إلى μs/خطوة، ويمكن توسيع الخطوات القابلة للبرمجة إلى أكثر من 16000 خطوة. تُستخدم وظيفة المعالجة عالية السرعة لوحدة التحكم المنطقي القابلة للبرمجة لتمكين الجمع العضوي بين ماكينة التحكم الرقمي باستخدام الحاسب الآلي ووحدة التحكم المنطقي القابلة للبرمجة، مما يلبي متطلبات التحكم المختلفة في الوقت الحقيقي أثناء تشغيل أدوات الماكينات بنظام التحكم الرقمي.
3) تحسين مستوى التحكم متعدد المحاور.
تتميز جميع أنظمة الماكينات بنظام التحكم الرقمي الجديدة بوظائف تحكم متعددة المحاور، والتي يمكنها استخدام وصلات متعددة المحاور لتحقيق تصنيع آلي للأسطح المعقدة والخاصة، ويمكنها أيضًا اعتماد التصنيع الآلي المتزامن متعدد الأدوات مع التحكم متعدد الأبراج.
4) استخدام أدوات القطع فائقة السرعة.
في الوقت الحالي، تم تطبيق الأدوات المطلية بالماس والأدوات الخزفية في التصنيع الآلي فائق السرعة.
(3) أتمتة عالية
بعد تطوير نظام الماكينات بنظام التحكم الرقمي باستخدام الحاسب الآلي إلى نظام ماكينات بنظام التحكم الرقمي باستخدام الحاسب الآلي القائم على المعالجات الدقيقة، تم توسيع وظائف النظام باستمرار، وبالتالي تم تحسين مستوى أتمتة أدوات الماكينات بنظام التحكم الرقمي باستخدام الحاسب الآلي باستمرار.
بالإضافة إلى التغيير التلقائي للأداة والتبديل التلقائي لقطعة العمل، ظهرت وظائف مثل إدارة عمر الأداة، والاستبدال التلقائي للأدوات الاحتياطية، والقياس والتعويض التلقائي لحجم الأداة والتعويض، والقياس والتعويض التلقائي لحجم قطعة العمل والتعويض، والتعديل التلقائي لمعلمات القطع تباعًا، مما يجعل أتمتة الماكينات الفردية تصل إلى مستوى عالٍ جدًا. كما يتم تحسين وظائف مراقبة تآكل الأدوات والكسر بشكل مستمر.
(4) موثوقية عالية
تعتمد موثوقية تشغيل أداة ماكينة التحكم الرقمي باستخدام الحاسوب بشكل أساسي على موثوقية نظام التحكم الرقمي باستخدام الحاسوب وأنظمة المؤازرة المختلفة. وفي الوقت الحالي، يتم اعتماد التدابير التالية بشكل رئيسي لتحسين الموثوقية:
1) تحسين جودة الأجهزة في نظام التحكم الرقمي باستخدام الحاسب الآلي.
اختيار رقائق دارة تكامل أعلى، وإنشاء وتنفيذ فحص صارم للمكونات، وتصنيع منتج مستقر، واختبار أداء شامل.
2) التوحيد النمطي والتوحيد القياسي والتعميم.
في الوقت الحالي، أصبحت وظائف أنظمة الماكينات بنظام التحكم الرقمي الحديثة قوية بشكل متزايد، مما يتيح لهياكل الأجهزة والبرمجيات الخاصة بالنظام تحقيق النمذجة والتوحيد القياسي والتعميم، مما يسهل تنظيم الإنتاج ومراقبة الجودة وصيانة المستخدم.
(5) وظائف متعددة الوظائف
1) تعتمد أدوات الماكينات بنظام التحكم الرقمي باستخدام الحاسب الآلي على الوظائف المتعددة لتحسين استخدام المعدات.
تعني الوظائف المتعددة الجمع بين وظائف أدوات الماكينات المختلفة في أداة ماكينة واحدة. وممثلوها النموذجيون هم مراكز الماكينات المختلفة المزودة بآليات تغيير الأدوات الأوتوماتيكية (يمكن أن تصل سعة مخزن الأدوات إلى أكثر من 100 أداة)، والتي يمكنها إجراء عمليات متعددة في نفس الوقت مثل الطحن، والثقب، والحفر، والخراطة، والتوسيع، والتوسيع، والاستدقاق وحتى الطحن على نفس أداة الماكينة.
ولتحسين كفاءة العمل بشكل أكبر، اعتمدت أدوات الماكينات بنظام التحكم الرقمي الحديثة (مثل مراكز الماكينات ذات الخمسة أوجه) على القطع متعدد المغزل ومتعدد الأوجه، أي إجراء عمليات قطع مختلفة على أجزاء مختلفة من قطعة العمل في وقت واحد.
بالإضافة إلى ذلك، يتزايد عدد محاور التحكم في أنظمة الماكينات بنظام التحكم الرقمي الحديثة باستمرار، حيث يصل بعضها إلى 31 محورًا، ووصل عدد المحاور المترابطة في وقت واحد إلى 7 محاور. تتميز أدوات الماكينات هذه بدقة تصنيع أعلى ويمكنها تحسين كفاءة العمل بشكل كبير، وتوفير مساحة الأرضية، وتقليل كمية المعدات، وتوفير الاستثمار.
2) وظيفة الحوار الجيد بين الإنسان والآلة.
على أداة ماكينة واحدة، يمكن تنفيذ معالجة القِطع وتحرير البرنامج في وقت واحد، أي أن لها وظيفة التشغيل الأمامي والتحرير في الخلفية. تستخدم أنظمة التحكم الرقمي باستخدام الحاسب الآلي الحديثة CRT الملونة لعرض المسار ثنائي الأبعاد، ويمكن للأنظمة الأفضل منها تحقيق محاكاة رسومية ديناميكية ملونة ثلاثية الأبعاد، وعرض مسار المعالجة الآلية للرمز المبرمج، وتسهيل تصحيح الأخطاء وتعديل برامج الأجزاء، وضمان سلامة عملية المعالجة الفعلية.
3) وظيفة تواصل أقوى.
يتطلب تطوير أدوات الماكينات بنظام التحكم الرقمي من ماكينات بنظام التحكم الرقمي من ماكينات مستقلة إلى FMC (خلية التصنيع المرنة) وFMS (نظام التصنيع المرن) والمزيد من الربط الشبكي لتشكيل نظام التصنيع المتكامل بالكمبيوتر (CIMS) أن تتمتع أنظمة التحكم الرقمي بنظام التحكم الرقمي بوظائف اتصال أقوى.
تحتوي معظم أنظمة التحكم الرقمي باستخدام الحاسب الآلي على واجهات تسلسلية عالية السرعة لمسافات طويلة RS232C و RS422، والتي يمكنها تبادل البيانات المختلفة مع أجهزة كمبيوتر عالية المستوى وفقًا لمتطلبات التنسيق على مستوى المستخدم. يجب أن تحتوي أنظمة الماكينات بنظام التحكم الرقمي CNC المتطورة على واجهات DNC (التحكم العددي الموزع)، والتي يمكنها تحقيق اتصال البيانات بين العديد من أدوات ماكينات التحكم الرقمي CNC، ويمكنها أيضًا التحكم مباشرةً في العديد من أدوات ماكينات التحكم الرقمي CNC.
وللتكيف مع التطور الإضافي لتكنولوجيا الأتمتة وتلبية متطلبات أتمتة المصانع على نطاق واسع بشكل متزايد والحاجة إلى الربط الشبكي بين مختلف الشركات المصنعة وأنواع أدوات ماكينات التحكم الرقمي CNC، اعتمدت أدوات ماكينات التحكم الرقمي الحديثة MAP (بروتوكول أتمتة التصنيع) شبكات التحكم الصناعي. وقد تم الآن تنفيذ الإصدار 3.0 من بروتوكول أتمتة التصنيع (MAP)، مما يهيئ الظروف الملائمة لأدوات الماكينات بنظام التحكم الرقمي الحديث للدخول في نظام إدارة المرافق ونظام إدارة المعلومات الصناعية.
(6) أتمتة البرمجة باستخدام الحاسب الآلي
تُعد البرمجة الآلية للحاسب الآلي CAM حاليًا أكثر طرق برمجة الماكينات بنظام التحكم الرقمي تقدمًا.
حاليًا، يتم استخدام برامج البرمجة التلقائية التفاعلية الرسومية التفاعلية CAD/CAM على نطاق واسع. وهو يستخدم التصميم بمساعدة الحاسوب لإكمال الرسم الحاسوبي للأشكال الهندسية للقطع، ثم من خلال حساب بيانات مسار الأداة الداخلية للحاسوب والمعالجة اللاحقة، يولد تلقائيًا برامج معالجة القطع NC، والتي يتم إرسالها بعد ذلك إلى أدوات الماكينات بنظام التحكم الرقمي باستخدام الحاسب الآلي من خلال واجهات الاتصال لمعالجة التحكم الآلي، وبالتالي تحقيق التكامل بين التصميم بمساعدة الحاسوب/التصنيع بمساعدة الحاسوب وتحقيق التصميم والتصنيع بدون رسومات.
بالإضافة إلى ذلك، مع تطور تكنولوجيا نظام إدارة المعلومات الآلية المتكاملة، ظهرت طريقة برمجة آلية بالكامل تدمج بين CAD/CAPP (تخطيط العمليات بمساعدة الحاسوب)/CAM. ويتمثل الاختلاف الأكبر عن برمجة نظام CAD/CAMP في أن معلمات عملية التشغيل الآلي المطلوبة للبرمجة لا تحتاج إلى مشاركة بشرية ولكن يتم الحصول عليها مباشرةً من قاعدة بيانات CAD/CAPP داخل النظام.
(7) أدخلت أنظمة التحكم الرقمي الحديثة باستخدام الحاسب الآلي (CNC) تقنية التحكم التكيفي.
تتطلب تقنية التحكم التكيفي (AC) التعديل التلقائي لحالة العمل والخصائص التي يتم قياسها أثناء عملية التصنيع في عمليات التصنيع المتغيرة عشوائيًا، وتصحيح معلمات العمل الخاصة بها تلقائيًا وفقًا لمؤشرات تقييم معينة لتحقيق حالة العمل المثلى أو الاقتراب منها.
يمكن لتقنية التحكم التكيفي أن تحقق دقة تصنيع عالية جدًا وأصغر خشونة السطحمع تحسين عمر الأداة وكفاءة إنتاج المعدات في الوقت نفسه.
ينعكس ذكاء أنظمة التحكم الرقمي باستخدام الحاسب الآلي بشكل أساسي في الجوانب التالية:
- الكشف التلقائي عن عمر الأداة واستبدالها تلقائيًا، والتنبيه في الوقت المناسب لخروج قطعة العمل عن التحمّل، أو تآكل الأداة أو كسرها، والتعويض التلقائي أو استبدال الأدوات الاحتياطية.
- التشخيص والإصلاح التلقائي عند حدوث أعطال.
- تعويض في الوقت الحقيقي لتمدد وانكماش البراغي الكروية والمكونات الأخرى بسبب التشوه الحراري أثناء التشغيل الآلي.
- إدخال تقنية التعرف على الأنماط وتطبيق تقنية التعرف على الصور وتقنية التحكم الصوتي، مما يسمح للنظام بالتعرف على الرسومات بنفسه وإجراء التصنيع الآلي باستخدام الحاسب الآلي وفقًا لأوامر اللغة الطبيعية.