
قطع المعادن هي عملية إزالة المعادن الزائدة من الأجزاء باستخدام أداة قطع في حركة نسبية مع قطعة العمل، مما يؤدي إلى تكوين برادة وسطح مشغول.
تتضمن عملية قطع المعادن تشوه القص للطبقة المعدنية التي يتم قطعها تحت تأثير أداة القطع. ويصاحب هذه العملية ظواهر فيزيائية مثل تشوه المعدن وقوى القطع وحرارة القطع وتآكل الأداة. ترتبط جميع المشاكل التي تحدث في عملية الإنتاج، مثل النتوءات والحواف المتراكمة والاهتزازات وتجعد البُرادة وتكسرها بعملية القطع.
I. عملية القطع
1. عملية تشكيل البُرادة
أثناء القطع، تحت تأثير القطع من حافة القطع وحركة الدفع من وجه أشعل النار، تخضع الطبقة المعدنية التي يتم قطعها إلى القصوالانزلاق والتشوه، وأخيرًا الانفصال عن قطعة العمل لتصبح برادة. تسمى هذه العملية عملية القطع.
تظهر عملية تشكيل الرقاقة في الشكل 1.

تشوه المنطقة I: منطقة تشوه القص في طبقة القطع بالقرب من حافة القطع.
تخضع الطبقة المعدنية التي يتم قطعها أولاً لتشوه مرن تحت قوة الضغط أمام أداة القطع. عندما يصل الحد الأقصى لإجهاد القص إلى حد خضوع المادة، يحدث انزلاق القص. ومع اقتراب وجه أداة القص تدريجيًا، يزداد التشوه البلاستيكي مصحوبًا بتصلب الإجهاد، حتى يتوقف الانزلاق، وتنفصل الطبقة المعدنية المقطوعة عن جسم الشُّغْلَة لتصبح برادة تتدفق على طول وجه أداة القص.
تشوه المنطقة II: منطقة التشوه في طبقة البُرادة الملامسة لوجه أشعل النار.
تخضع البُرادة المتكونة عن طريق انزلاق القص في منطقة التشوه الأولى لاحتكاك شديد مع وجه أشعل النار أثناء تدفقها للخارج، مما يتسبب في حدوث تشوه قص ثانٍ يبطئ تدفق طبقة رقيقة من المعدن في أسفل البُرادة. تسمى هذه الطبقة من المعدن بطيء التدفق الطبقة الراكدة. تكون درجة التشوه في الطبقة الراكدة أكبر بعدة مرات أو حتى عشرات المرات من تلك الموجودة في الطبقة العليا من البُرادة.
تشوه المنطقة III: منطقة التشوه في الطبقة السطحية المشغولة آلياً بالقرب من حافة القطع.
يشير التشوه في منطقة التشوه الثالثة إلى المنطقة التي يخضع فيها سطح الشُّغْلَة والطبقة المعدنية السطحية المشغولة آليًا لتشوه بلاستيكي بسبب الضغط والاحتكاك من الجزء الحاد من حافة القطع ووجه الجناح. يتسبب هذا في تليف وتصلب الشغل للطبقة المعدنية السطحية وينتج بعض الضغوط المتبقية. سيؤثر التشوه المعدني في هذه المنطقة على جودة السطح وأداء قطعة العمل.
2. أنواع الرقائق
أثناء قطع المعادن، نظرًا للاختلافات في مواد الشُّغْلَة وهندسة الأداة ومعلمات القطع، يكون للبُرادة المشكلة أشكال مختلفة. هناك بشكل عام أربعة أنواع أساسية (انظر الشكل 2).

أ) الرقائق المتصلة
ب) الرقائق المجزأة
ج) رقائق العناصر
د) الرقائق المتقطعة
(1) الرقائق المتصلة
(انظر الشكل 2أ) تتشكل الرقائق في شريط متصل. ويكون السطح الداخلي للرقائق المتصلة أملس، بينما يكون السطح الخارجي غير واضح. وتحت المجهر، يمكن رؤية العديد من التصدعات المستوية للقص على الجانب. تتشكل هذه الرقائق بسهولة عند قطع المطيل المعادن مع سماكة قطع صغيرة، وسرعة قطع عالية، وزاوية أشعل النار كبيرة للأداة.
وتتمثل مزايا تشكيل هذا النوع من البُرادة في عملية القطع المستقرة، والتذبذب الصغير في قوة القطع، والجودة السطحية العالية لقطعة الشُّغْلَة. العيب هو أن البُرادة المستمرة الطويلة للغاية يمكن أن تلتف حول قطعة العمل والأداة، مما يؤثر على التشغيل والسلامة. لذلك، يجب اتخاذ تدابير كسر البُرادة.
(2) الرقائق المجزأة
(انظر الشكل 2 ب) السطح الخارجي لهذه الرقائق مسنن، والسطح الداخلي به شقوق. ويرجع ذلك إلى أن إجهاد القص المحلي بالداخل يصل إلى حد قوة المادة أثناء القطع.
عند قطع المعادن القابلة للسحب، يتم الحصول على هذه البُرادة بسهولة مع سُمك قطع أكبر وسرعة قطع أقل وزاوية أشعل النار أصغر. أثناء تكوين هذه البُرادة تتذبذب قوة القطع بشكل كبير، وتكون عملية القطع أقل استقرارًا، وتميل إلى التسبب في سطح مشغول أكثر خشونة على قطعة العمل.
(3) رقائق العناصر
(انظر الشكل 2ج) إذا انكسرت الرقائق إلى هياكل كتل غير منتظمة أكبر أثناء القطع، تسمى هذه الرقائق بالرقائق العنصرية. ويرجع السبب في تكوين هذه الرقائق إلى أن إجهاد القص داخل الرقاقة يتجاوز حد قوة المادة، مما يتسبب في كسر الرقاقة على طول مقطع عرضي معين، مما يمنع تكوين رقائق متصلة. بشكل عام,
عند قطع المعادن القابلة للسحب، يتم الحصول على هذه البُرادة بسهولة مع سُمك القطع الكبير، وسرعة القطع المنخفضة، وزاوية أشعل النار في الأداة الصغيرة. عند تشكيل هذه الرقائق، تتذبذب قوة القطع بشكل كبير، وتكون عملية القطع غير مستقرة للغاية، وتكون البُرادة المشكّلة خشونة السطح لقطعة العمل عالية. لذلك، يجب تجنب تكوين هذه البُرادة أثناء التصنيع الآلي، خاصةً في عمليات التشطيب.
(4) الرقائق المتقطعة
(انظر الشكل 2 د) عند قطع المعادن الهشة (مثل الحديد الزهر والنحاس الأصفر)، يتم ضغط الطبقة المعدنية التي يتم قطعها وتكسيرها بشكل هش مع تشوه بلاستيكي ضئيل للغاية تحت تأثير دفع الأداة. وهذا يشكل برادة مجزأة غير منتظمة بأحجام مختلفة، تسمى برادة متقطعة.
عند تشكيل هذه البُرادة تختلف قوة القطع اختلافًا كبيرًا، وتكون خشونة سطح الشُّغْلَة الميكانيكية عالية جدًا. كلما كانت زاوية أشعلت الأداة أصغر وزادت سماكة القطع، زادت احتمالية إنتاج هذه البُرادة.
3. الحافة المبنية
(1) تشكيل الحافة المبنية
في ظل ظروف معينة، عند قطع المعادن القابلة للسحب، تلتصق قطعة صغيرة من المعدن ذات صلابة أعلى بالقرب من طرف الأداة، كما هو موضح في الشكل 3. تسمى هذه القطعة المعدنية بالحافة المتراكمة. ولها تأثير كبير على عملية القطع وجودة السطح المشغول آليًا.
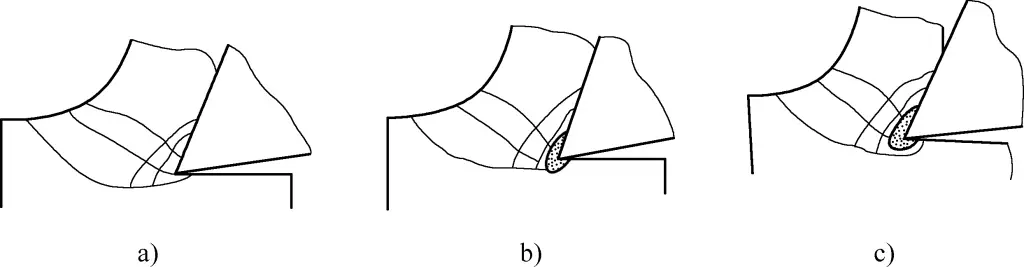
يتطلب تكوين الحافة المتراكمة ظروفًا وأسبابًا معينة. أولاً، يحدث ذلك عند قطع المعادن القابلة للسحب، وثانيًا، عند سرعات القطع المتوسطة (5-60 م/دقيقة). عند قطع الفولاذ العام أو مواد مطيلة أخرى، يتم إجبار الطبقة المعدنية التي يتم قطعها على الانفصال عن المادة الأصلية تحت تأثير القطع بحافة القطع للأداة. تتدفق الطبقة السفلية على طول وجه الأداة، مما يسبب احتكاكًا بين طبقة القطع ووجه أداة القطع.
وفي الوقت نفسه، أثناء عملية القطع، ينتج عن حركة دفع وجه الأداة على البُرادة ضغط هائل أثناء عملية القطع. ويتسبب الضغط والاحتكاك الهائل في أن تكون سرعة تدفق المعدن في الطبقة السفلية من البُرادة أبطأ بكثير من الطبقة العلوية، مما يؤدي إلى تشوه كبير على طول وجه البُرادة المعروف باسم تدفق الركود.
عندما يصل الضغط ودرجة الحرارة بين البُرادة ووجه أشعل النار إلى مستوى معين، يحدث اللحام البارد. وتبقى الطبقة السفلية من المعدن المقطوع التي خضعت للحام البارد على وجه الشق على وجه الشق على البارد، مما يشكل طبقة من الحافة المتراكمة. وتتسبب هذه الطبقة من الحافة المتراكمة في تعرض طبقة المعدن الملامسة لها لتشوه بلاستيكي كبير وتراكمها فوقها.
من خلال التراكم المستمر، تنمو الحافة المتراكمة تدريجيًا بشكل أكبر. عندما تصل إلى ارتفاع معين، فإنها تشكل حافة مبنية كاملة وتحل محل حافة القطع في عملية القطع. يؤدي وجود الحافة المتراكمة إلى تغيير زاوية أشعل النار للأداة.
عندما تكون سرعة القطع منخفضة للغاية (أقل من 5 م/دقيقة)، يكون الضغط ودرجة الحرارة بين وجه الأداة وطبقة القطع منخفضة، مما لا يفي بشروط تشكيل حافة مبنية. عندما تكون سرعة القطع عالية جدًا، تكون درجة حرارة الطبقة السفلية من المعدن عالية جدًا. تزداد سيولة معدن الطبقة السفلية، وينخفض معامل الاحتكاك بشكل كبير، مما يمنع أيضًا تكوين حافة مبنية.
(2) تأثير الحافة المبنية على القطع
1) يحمي الأداة.
تبلغ صلابة الحافة المدمجة حوالي 2-4 أضعاف صلابة مادة قطعة العمل. يتم لحامها في مقدمة الأداة، ويمكنها أن تحل محل حافة القطع في القطع، مما يحمي حافة القطع ووجه أشعل النار، ويقلل من تآكل الأداة. الحافة المدمجة لها تأثير إيجابي على التشغيل الآلي الخشن.
2) يزيد من زاوية أشعل النار الفعالة.
يمكن لأداة الخراطة المزودة بحافة مدمجة أن تزيد من زاوية أشعل النار الفعالة إلى 30°-35°، مما يقلل من تشوه البُرادة ويقلل من قوى القطع، كما هو موضح في الشكل 4.

3) يؤثر على دقة أبعاد قطعة العمل وجودة السطح.
يكون تكوين الحافة المتراكمة متقطعًا ومتفاوتًا في الحجم وغير مستقر إلى حد كبير. أثناء عملية القطع، يتم حمل بعض الحواف المتراكمة بعيدًا بواسطة البُرادة بينما يتم تضمين البعض الآخر في السطح الميكانيكي لقطعة العمل، مما يؤدي إلى تكوين بقع ونتوءات صلبة، مما يزيد من قيمة خشونة السطح، كما هو موضح في الشكل 5.

عندما تنمو الحافة المتراكمة بشكل أكبر من حافة القطع، يتغير الموضع الفعلي لطرف الأداة، مما يتسبب في تغيير عمق القطع، مما يؤثر على دقة أبعاد الشُّغْلَة. لذلك، في التصنيع الآلي النهائي، يمكن تجنب تشكيل الحافة المتراكمة عن طريق تغيير معلمات القطع الثلاثة.
(3) العوامل الرئيسية التي تؤثر على الحافة المبنية
العوامل الرئيسية التي تؤثر على الحافة المبنية هي مادة الشغل وسرعة القطع ومعدل التغذية و سائل القطع. من بينها، سرعة القطع لها التأثير الأكبر على تكوين الحافة المتراكمة. بالإضافة إلى ذلك، تؤثر زاوية أشعل الأداة وسُمك القطع أيضًا على تشكيل الحافة المتراكمة.
تقلل زاوية أشعل النار الأكبر من تشوه البُرادة مما يساعد على منع تكون الحافة المتراكمة. تؤدي زيادة سُمك القطع أيضًا إلى زيادة طول التلامس بين البُرادة ووجه أشعل النار، مما يزيد من إمكانية تكوين الحافة المتراكمة.
4. تشديد العمل
تُسمى الظاهرة التي تزداد فيها قوة السطح وصلابة المعادن القابلة للسحب بينما تقل اللدونة بعد التشغيل الآلي بالتصلب الشغلي، والمعروف أيضًا باسم تصلب الإجهاد. وسبب تصلب الإجهاد هو التشوه البلاستيكي للمواد المعدنية أثناء عملية التشغيل الآلي.
كلما زاد التشوه البلاستيكي، زادت شدة تصلب الإجهاد السطحي. يمكن أن تصل صلابة الطبقة المتصلبة إلى 1.2-2 أضعاف صلابة قطعة العمل، بعمق طبقة متصلبة من 0.07-0.5 مم. وهذا يخلق صعوبات في التصنيع الآلي اللاحق، ويزيد من تآكل الأداة، ويؤثر على جودة سطح قطعة العمل. ويرافق حدوث تصلب الإجهاد إجهاد متبقي وتشققات دقيقة، مما يقلل من خصائص المواد لسطح قطعة العمل.
على الرغم من أن تصلب الإجهاد له بعض الآثار السلبية، إلا أن له أيضًا جوانب مفيدة. على سبيل المثال، في ظل الظروف التي تكبح الإجهاد المتبقي، خاصةً الشقوق الدقيقة، يمكن أن يؤدي استخدام الصقل بالأسطوانة لإنتاج تصلب العمل إلى تحسين صلابة السطح المشغول وقوته ومقاومته للتآكل.
ثانياً. قوة القطع
تسمى القوة التي تبذلها أداة القطع على قطعة العمل أثناء القطع قوة القطع F r التي تؤثر على قطعة العمل. وتسمى مقاومة مادة قطعة العمل ضد حركة القطع بالأداة مقاومة القطع F'' r التي تعمل على الأداة.
قوة القطع F r ومقاومة القطع F' r قوتان متساويتان في المقدار ومتضادتان في الاتجاه تؤثران على جسمين مختلفين، كما هو موضح في الشكل 6.

تؤثر مقاومة القطع تأثيرًا كبيرًا على عمر الأداة، واستهلاك طاقة الماكينة، وجودة معالجة الشُّغْلَة أثناء عملية القطع.
1. مصادر مقاومة القطع
أثناء القطع، لا تتعرض الأداة لمقاومة التشوه (F₀، F₁، F₂، F₃، F₃) الناتجة عن التشوه اللدن والمرن للمعدن المقطوع والرقائق والطبقة السطحية لقطعة العمل، ولكن أيضًا لمقاومة الاحتكاك (f₄، f₅) بين وجه أشعل النار والرقائق، وبين وجه الجناح وسطح قطعة العمل. مقاومة القطع هي القوة المحصلة (المجموع الاتجاهي) لهذه القوى، كما هو موضح في الشكل 7.

2. تحلل مقاومة القطع
مقاومة القطع F'₀ هي متجه مكاني، وليس من السهل قياس مقدارها واتجاهها. ولتسهيل تحليل تأثير مقاومة القطع وقياسها، ولحساب مقدار قوة القطع، عادةً ما تتحلل مقاومة القطع F'₁ إلى ثلاثة مكونات متعامدة متبادلة: مقاومة القطع الرئيسية F'₂، والمقاومة الشعاعية F'y، والمقاومة المحورية F'x (انظر الشكل 8).

عندما تكون قيم القُوى الثلاث المكوِّنة معروفة، يمكن حساب قيمة القوة المحصلة F'₀ باستخدام المعادلة التالية:

(1) مقاومة القطع الرئيسية F'₀
وهي عمودية على مستوى القاعدة ومتسقة مع اتجاه سرعة القطع v₀. إنها أكبر القوى المكونة، وتستهلك أكبر قدر من الطاقة، حيث تمثل حوالي 95% إلى 99% من إجمالي طاقة الماكينة. سوف يتسبب F'₁ في ثني ساق الأداة. لذلك، عند تركيب الأداة، يجب تمديد ساق الأداة لأقصر فترة ممكنة.
(2) المقاومة الشعاعية F'y
تكون في المستوى الأساسي وموازية لاتجاه التغذية الشعاعية. لا تستهلك طاقة الماكينة. ومع ذلك، تعمل قوة القطع الشعاعية التفاعلية على قطعة العمل شعاعيًا، مما يؤدي إلى ثني قطعة العمل. عندما تكون الشُّغْلَة نحيلة ويفتقر النظام التكنولوجي إلى الصلابة، فمن السهل إنتاج تشوه واهتزازات الانحناء، مما يؤثر على دقة التصنيع وخشونة السطح.
(3) المقاومة المحورية F'x
تكون في المستوى الأساسي وموازية لاتجاه التغذية الطولية. يستهلك فقط 1% إلى 5% من إجمالي طاقة الماكينة. نظرًا لأنها موازية لمحور الشُّغْلة، فإنها تميل إلى انحراف أداة المخرطة في الاتجاه المعاكس للتغذية. لذلك، عند تركيب أداة المخرطة، يجب قفلها بإحكام لتجنب تخريد الشُّغْلَة بسبب حركة الأداة.
3. العوامل المؤثرة في مقاومة القطع
(1) مادة قطعة العمل
تؤثر كل من الصلابة والقوة والتشوه البلاستيكي والاحتكاك بين البُرادة وأدوات مادة قطعة العمل على مقاومة القطع. كلما زادت صلابة أو قوة مادة قطعة العمل، زادت مقاومة القطع.
كلما زادت مرونة أو صلابة مادة الشغل، زادت مقاومة التشوه وقوة الاحتكاك، وزادت مقاومة القطع. إن قوة وتشوه الفولاذ أكبر من قوة وتشوه الحديد الزهر، وبالتالي فإن مقاومة القطع عند قطع الفولاذ أكبر منها عند قطع الحديد الزهر (حوالي 0.5 إلى 1 مرة أعلى).
(2) معلمات القطع
من بين معلمات القطع، تتمثل العوامل الرئيسية في عمق القطع ومعدل التغذية، والتي تؤثر على مقاومة القطع من خلال التأثير على مساحة القطع. عمق القطع له التأثير الأكبر على مقاومة القطع، يليه معدل التغذية.
ستؤدي زيادة عمق القطع ومعدل التغذية إلى زيادة سمك القطع وعرض القطع على التوالي، وبالتالي زيادة مساحة القطع. ونتيجة لذلك، تزداد مقاومة التشوه ومقاومة الاحتكاك، مما يؤدي إلى زيادة مقاومة القطع.
عندما يتضاعف عمق القطع، تتضاعف أيضًا مقاومة القطع الرئيسية؛ ولكن عندما يتضاعف معدل التغذية، تزداد مقاومة القطع الرئيسية بمقدار 0.75 إلى 0.9 مرة فقط. لذلك، فإن استخدام معدل تغذية أكبر يكون أكثر كفاءة في استهلاك الطاقة من استخدام عمق قطع أكبر.
تؤثر سرعة القطع على مقاومة القطع من خلال التأثير على درجة تشوه البُرادة ولكن ليس لها تأثير على مساحة القطع. لذلك، لا يكون تأثير سرعة القطع على مقاومة القطع بنفس أهمية تأثير عمق القطع ومعدل التغذية. عند قطع المعادن الهشة، يكون التشوه والاحتكاك صغيرًا نسبيًا، ولا تتغير قوة القطع كثيرًا عندما تتغير سرعة القطع.
(3) زوايا أداة المخرطة
1) زاوية التدوير.
كلما كانت زاوية أشعل النار أكبر، كان تشوه البُرادة أصغر، وانخفضت مقاومة القطع بشكل كبير.
2) زاوية الاقتراب.
عند قطع المعادن البلاستيكية، إذا كانت زاوية الاقتراب أقل من 60 درجة إلى 75 درجة، فإن زيادة زاوية الاقتراب ستقلل من مقاومة القطع الرئيسية؛ وعندما تكون زاوية الاقتراب أكبر من 60 درجة إلى 75 درجة، فإن زيادة زاوية الاقتراب ستزيد من مقاومة القطع الرئيسية بسبب تأثير نصف قطر أنف الأداة. عند قطع المعادن الهشة، لا تتغير مقاومة القطع الرئيسية بشكل أساسي مع تغير الزاوية عندما تكون زاوية الاقتراب أكبر من 45 درجة.
3) زاوية الميل.
عندما تختلف زاوية الميل من 10 درجات إلى 45 درجة، تظل مقاومة القطع الرئيسية دون تغيير بشكل أساسي. ومع ذلك، عندما تنخفض زاوية الميل، تزداد مقاومة القطع الشعاعي، وتنخفض قوة التغذية.
4) الأرض السالبة.
عندما يتم طحن الأداة بأرض سالبة، تصبح حافة القطع غير حادة، ويزداد تشوه البُرادة وتزداد مقاومة القطع أيضًا.
5) نصف قطر أنف الأداة.
مع زيادة نصف قطر أنف الأداة أو الحافة الانتقالية، يزداد طول حافة القطع المشاركة في القطع، ويزداد تشوه البُرادة وقوة الاحتكاك، وتزداد أيضًا مقاومة القطع.
ثالثًا. حرارة القطع ودرجة حرارة القطع
حرارة القطع هي الحرارة المتولدة أثناء عملية القطع بسبب تشوه المعدن والاحتكاك. وتؤثر حرارة القطع ودرجة حرارة القطع الناتجة بشكل مباشر على تآكل الأداة وعمر الخدمة، وتؤثر على دقة تصنيع الشُّغْلَة وجودة السطح، خاصةً في القطع عالي السرعة.
1. مصادر حرارة القطع وتبديدها
هناك ثلاثة مصادر لحرارة القطع: أولًا، التشوه المرن واللدائن لطبقة القطع المعدنية؛ ثانيًا، الاحتكاك بين البُرادة ووجه الشدّة؛ ثالثًا، الاحتكاك بين قطعة العمل ووجه الجناح. أثناء عملية القطع، يتم تحويل معظم الطاقة المستهلكة بواسطة التشوه والاحتكاك أعلاه إلى طاقة حرارية.
يتم تبديد حرارة القطع من خلال البُرادة وقطعة العمل والأداة والوسط المحيط. وقد أظهرت التجارب أن نسبة حرارة القطع المنقولة إلى الأجزاء المختلفة تكون أعلى بشكل عام في البُرادة.
بدون استخدام سائل القطع، عند قطع المواد الفولاذية بسرعة قطع متوسطة، يتم نقل 50% إلى 86% من حرارة القطع بواسطة البُرادة بعيدًا، ويتم نقل 10% إلى 40% إلى قطعة العمل، ويتم نقل 3% إلى 9% إلى أداة المخرطة، ويتم نقل حوالي 1% إلى الهواء المحيط.
2. درجة حرارة القطع
ويؤدي توليد حرارة القطع إلى ارتفاع درجة الحرارة في منطقة القطع، ويكون توزيع درجة حرارة القطع في منطقة القطع غير متساوٍ. وعادة ما تشير درجة حرارة القطع إلى متوسط درجة الحرارة في منطقة التلامس بين البُرادة ووجه أشعل النار. يعتمد مستوى درجة حرارة القطع على كمية حرارة القطع وجودة ظروف تبديد الحرارة.
3. العوامل الرئيسية التي تؤثر على درجة حرارة القطع
(1) تأثير مادة قطعة العمل
تؤثر مادة الشُّغْلَة على درجة حرارة القطع من خلال خصائصها المختلفة من حيث القوة والصلابة والتوصيل الحراري. عندما تكون مادة الشُّغْلَة ذات قوة وصلابة أقل، وموصلية حرارية أعلى، تتولد حرارة أقل، مما يؤدي إلى انخفاض درجة حرارة القطع. والعكس صحيح بالنسبة لدرجات حرارة القطع الأعلى.
(2) تأثير معلمات القطع
تؤدي زيادة بارامترات القطع (v₀، f، a₁) إلى زيادة درجة حرارة القطع، حيث يكون لسرعة القطع (v₂) التأثير الأكبر، يليها معدل التغذية (f)، ويكون عمق القطع (a₃) الأقل تأثيرًا.
(3) تأثير زوايا الأداة
1) زاوية التدوير (γ ₀)
يؤثر حجم زاوية أشعل النار على تشوه القطع والاحتكاك، مما يؤثر بشكل كبير على درجة حرارة القطع. مع زيادة زاوية أشعل النار، ينخفض التشوه والاحتكاك، وتتولد حرارة أقل، وتنخفض درجة حرارة القطع. ومع ذلك، إذا كانت زاوية أشعل النار كبيرة جدًا، تنخفض زاوية الإسفين، مما يقلل من حجم طرف الأداة ويزيد من سوء ظروف تبديد الحرارة، مما يتسبب في ارتفاع درجة حرارة القطع قليلاً.
2) زاوية الاقتراب (K₀)
في ظل نفس عمق القطع، تؤدي زيادة زاوية الاقتراب إلى تقصير طول L₀ من حافة القطع الرئيسية المشاركة في القطع، وتقلل من زاوية نقطة الأداة ε₁. يؤدي ذلك إلى تركيز حرارة القطع ويزيد من سوء ظروف تبديد الحرارة، مما يؤدي إلى ارتفاع درجة حرارة القطع، كما هو موضح في الشكل 9.

أ) K₀ صغير، زاوية نقطة أداة كبيرة
ب) كبير K₀، زاوية نقطة الأداة الصغيرة
(4) تأثير العوامل الأخرى
يمكن أن يؤدي الاختيار السليم والاستخدام الكافي لسائل القطع إلى تقليل درجة حرارة القطع بشكل فعال.
4. تأثيرات درجة حرارة القطع على التصنيع بالقطع
تأثيرات درجة حرارة القطع على القطع والتشغيل الآلي ذات طبيعة مزدوجة.
(1) الآثار الضارة لدرجة حرارة القطع على القطع والتشغيل الآلي
1) يؤدي ارتفاع درجة حرارة القطع إلى تسريع تآكل الأداة وتقليل عمر الأداة.
2) بعد التسخين، قد تتعرض الأدوات أو قطع العمل للتمدد الحراري والتشوه بعد التسخين، مما يؤثر على دقة التصنيع، خاصةً عند تصنيع المعادن غير الحديدية أو قطع العمل النحيلة.
3) عندما يتصل سطح قطعة العمل بجناح الأداة، يمكن أن ترتفع درجة الحرارة إلى عدة مئات من الدرجات على الفور، ولكنها تنخفض بسرعة بعد الانفصال عن الجناح. على الرغم من أن هذه العملية قصيرة، إلا أنها قد تسبب إجهاد شد متبقي ضار على سطح قطعة العمل. وفي الحالات الشديدة، قد تتسبب في حرق السطح وظاهرة التلدين على الشُّغْلَة.
(2) التأثيرات المفيدة لدرجة حرارة القطع على القطع والتشغيل الآلي
1) تعمل درجة حرارة القطع على تليين مادة الشُّغْلة، مما يسهل من عملية القطع، وهو أمر مفيد لتصنيع المواد ذات الصلابة العالية ولكن ذات القوة المنخفضة في درجات الحرارة العالية (مثل الفولاذ المروي والمصلد).
2) بالنسبة لبعض مواد الأدوات الهشة ولكنها تتمتع بمقاومة جيدة للحرارة (مثل الكربيدات الأسمنتية والمواد الخزفية)، يمكن أن تؤدي درجات الحرارة العالية المناسبة إلى تحسين صلابة المادة وتقليل ظاهرة التقطيع.
3) درجات حرارة القطع المرتفعة غير مواتية لتكوين حواف متراكمة، مما يقلل من تآكل الأداة ويحسن جودة سطح قطعة العمل.
رابعًا. معايير البلى والتآكل للأداة
سوف تتآكل الأدوات تدريجيًا أثناء عملية القطع. عندما يصل تآكل الأداة إلى مستوى معين، يمكن ملاحظة أن مقاومة القطع تزداد بوضوح، وترتفع درجة حرارة القطع، ويتغير لون البُرادة ويحدث اهتزاز القطع، وتتدهور جودة السطح الميكانيكي بشكل كبير. قد لا تفي أبعاد قطعة العمل بالمتطلبات. عند هذه النقطة، يجب إعادة شحذ الأداة أو استبدالها بأخرى جديدة.
1. أشكال تآكل الأدوات
هناك ثلاثة أشكال من تآكل الأداة: تآكل وجه أشعل النار، وتآكل وجه الجناح، والتآكل المتزامن لوجه أشعل النار ووجه الجناح، كما هو موضح في الشكل 10.

أ) تآكل وجه المجرفة
ب) تآكل وجه الجناح
ج) التآكل المتزامن لوجهي أشعل النار والجناح
(1) تآكل وجه المجرفة (1)
يشير تآكل وجه الأشواك إلى ظهور حفرة على شكل هلال على مقدمة الأداة. عند قطع المعادن البلاستيكية بسرعات قطع أعلى وسماكات قطع أكبر، من المرجح أن تحدث حفر على شكل هلال. سيقلل التمدد التدريجي للتآكل على شكل هلال من قوة حافة القطع، مما يجعل من السهل تشقق الأداة وتلفها.
(2) تآكل وجه الجناح
تحدث منطقة التآكل الرئيسية على وجه الخاصرة. ويحدث ذلك بسبب الضغط الشديد والاحتكاك بين السطح المشغول بالماكينة ووجه جناح الأداة، مما يؤدي إلى تلف وأخاديد بالقرب من حافة القطع على وجه الجناح.
يحدث هذا النوع من التآكل بشكل عام عند قطع المعادن الهشة أو عند قطع المعادن البلاستيكية بعمق قطع صغير (أ p <0.1 مم). قيمة التآكل ممثلة بـ VB.
(3) التآكل المتزامن لوجهي أشعل النار والجناح
هذا هو نوع شامل من التآكل، يشير إلى حدوث حفر على شكل هلال على وجه أشعل النار وأخاديد على وجه الجناح في وقت واحد. عند قطع المعادن البلاستيكية، هذه هي الحالة الأكثر شيوعًا. نادرًا ما يحدث تآكل وجه أشعل النار أو تآكل وجه الجناح.
2. عملية تآكل الأدوات
يمكن تقسيم عملية تآكل الأداة بشكل عام إلى ثلاث مراحل. يظهر منحنى عملية تآكل الأداة في الشكل 11.

عادةً ما يشير تآكل الأداة إلى التآكل على وجه الجناح لأنه في معظم الحالات، يتعرض وجه الجناح للتآكل. ويؤثر حجم التآكل البطيء تأثيرًا كبيرًا على دقة التصنيع وخشونة السطح، كما أنه أكثر ملاءمة للقياس. لذلك، في الوقت الحالي، تُستخدم كمية التآكل على وجه الجناح بشكل عام لتعكس درجة تآكل الأداة.
(1) مرحلة التآكل الأولي (قسم OA)
يكون ميل منحنى التآكل كبيرًا نسبيًا في هذه المرحلة. ونظرًا لصغر مساحة التلامس الفعلية بين وجه جناح الأداة المطحونة حديثًا والسطح المشغول آليًا، يكون الضغط مرتفعًا جدًا، مما يؤدي إلى تآكل سريع.
ويرتبط مقدار التآكل الأولي ارتباطًا وثيقًا بجودة طحن الأداة، وعادةً ما يتراوح بين VB=0.05 إلى 0.1 مم. تتميز الأدوات المطحونة بتآكل أولي أقل وتكون أكثر متانة.
(2) مرحلة التآكل العادي (القسم AB)
بعد التآكل الأولي، يتم تآكل حافة ضيقة على وجه جناح الأداة، مما يقلل من الضغط، وبالتالي تتباطأ الزيادة في التآكل وتصبح أكثر استقرارًا. هذه هي مرحلة التآكل العادي، وهي أيضًا مرحلة العمل الفعال للأداة.
خلال هذه المرحلة، يكون منحنى التآكل في الأساس خطًا مستقيمًا مع ميل تصاعدي صغير، ويمثل ميله شدة تآكل الأداة أثناء التشغيل العادي. تعد شدة التآكل أحد المؤشرات المهمة لمقارنة أداء قطع الأداة.
(3) مرحلة التآكل السريع (قسم BC)
بعد مرحلة التآكل العادي، تصبح حافة القطع غير حادة بشكل كبير، وتزداد قوى القطع، وترتفع درجة حرارة القطع. عند هذه النقطة، تخضع حالة تآكل الأداة لتغيير نوعي وتدخل مرحلة التآكل السريع. يكون منحدر منحنى التآكل في هذه المرحلة كبيرًا جدًا، مما يشير إلى كثافة تآكل عالية.
إذا استمرت الأداة في العمل في هذه المرحلة، فإنها لا يمكن أن تضمن جودة التصنيع فحسب، بل تستهلك أيضًا المزيد من مواد الأداة وقد تفقد قدرتها على القطع تمامًا. لذلك، يجب على الأداة تجنب التآكل السريع وتجنب عمليات القطع في هذه المرحلة.
3. معايير تآكل الأدوات
سيؤثر تآكل الأداة على قوى القطع، ودرجة حرارة القطع، وجودة التصنيع، لذلك يجب تحديد قيمة التآكل القصوى المسموح بها بناءً على ظروف التصنيع. هذه هي معايير تآكل الأداة.
بشكل عام، يوجد تآكل على وجه الجناح للأدوات، والذي له تأثير أكبر على دقة التصنيع وقوى القطع من تآكل وجه أشعل النار. بالإضافة إلى ذلك، فإن تآكل وجه الجناح أسهل في القياس. ولذلك، في إدارة الأدوات وأبحاث قطع المعادن، غالبًا ما يتم وضع معايير التآكل بناءً على أبعاد تآكل وجه الجناح.
يشير ما يسمى بمعايير التآكل عادةً إلى الحد الأقصى المسموح به لمتوسط مقدار التآكل المسموح به في الجزء الأوسط من نطاق تآكل الجناح، معبراً عنه بـ VB.
على سبيل المثال، عند الخراطة الخشنة للفولاذ الكربوني باستخدام أدوات الكربيد، فإن VB = 0.6 ~ 0.8 مم؛ وعند الخراطة الخشنة للحديد الزهر، فإن VB = 0.8 ~ 1.2 مم؛ وعند الخراطة النهائية، فإن VB = 0.1 ~ 0.3 مم تعتبر معايير التآكل.
عند تصنيع قطع الشُّغْلَة الكبيرة، لتجنب تغيير الأدوات في منتصف الطريق، يتم استخدام سرعات قطع أقل بشكل عام لإطالة عمر الأداة. في هذه الحالة، تكون درجة حرارة القطع أقل، وبالتالي يمكن زيادة معايير التآكل بشكل مناسب.
بالنسبة لأدوات التشطيب المستخدمة في الإنتاج الآلي، يتم وضع معايير التآكل بشكل عام بناءً على متطلبات دقة الشُّغْلَة. في مثل هذه الحالات، غالبًا ما يتم استخدام مقدار التآكل الشعاعي NB كمعيار للقياس، كما هو موضح في الشكل 12.

4. عمر الأداة
يُطلق على وقت القطع منذ بدء أداة مطحونة حديثًا في القطع حتى تصل كمية التآكل إلى معايير التآكل عمر الأداة. ويتم تمثيله ب T، وهو وقت القطع الخالص بين عمليتي إعادة طحن. وهو يشير إلى زمن القطع الصافي ولا يشمل زمن القطع غير وقت القطع المستخدم لإعداد الأداة والقياس والتغذية السريعة وضربات التباطؤ وما إلى ذلك.
عمر الأداة هو مجموع الوقت الذي يتم فيه استخدام الأداة من البداية وحتى التخلص منها، أي مجموع العمر الافتراضي بعد كل عملية إعادة طحن. في الإنتاج الحديث، لا يُنصح في الإنتاج الحديث بالسعي الأعمى إلى إطالة عمر الأداة. يجب أن يكون الهدف هو زيادة عمر الأداة إلى أقصى حد مع مراعاة جودة المنتج وكفاءة الإنتاج وتكاليف المعالجة.
V. طرق تقليل خشونة سطح قطعة العمل
تشير خشونة السطح إلى التفاوتات الصغيرة المتباعدة بين القمم والوديان على السطح المشغول آلياً. تكون المسافة بين قمتين أو واديين (الطول الموجي) صغيرة جداً (أقل من 1 مم) ويصعب تمييزها بالعين المجردة، لذا فهي تنتمي إلى أخطاء الشكل الهندسي المجهري. كلما كانت خشونة السطح أصغر، كان السطح أكثر سلاسة. يؤثر حجم خشونة السطح تأثيراً كبيراً على أداء الأجزاء الميكانيكية.
تشمل معلمات التقييم لخشونة السطح المتوسط الحسابي للانحراف الحسابي للشكل الجانبي Ra، وارتفاع المخالفات Rz المكون من عشر نقاط، والارتفاع الأقصى للشكل الجانبي Ry. نظرًا لأن معلمة Ra يمكن أن تعكس بشكل كامل خصائص الشكل الهندسي المجهري للسطح في اتجاه الارتفاع وطريقة القياس الهندسي بسيطة نسبيًا، فهي معلمة التقييم الأساسية الموصى بها كخيار ذي أولوية حسب المعايير.
تُعد خشونة السطح والخصائص الفيزيائية الميكانيكية للطبقة السطحية للسطح المُشَكَّل معايير لتقييم جودة السطح للسطح المُشَكَّل. ولخشونة السطح تأثير كبير على مقاومة التآكل، ومقاومة التآكل، وقوة التعب، و التركيب خصائص الأجزاء. تعد كيفية تقليل خشونة السطح أيضًا أحد المحتويات المهمة في أبحاث مبدأ القطع.
1. العوامل المؤثرة على خشونة سطح قطعة العمل
(1) المساحة المتبقية
يتم تشكيل السطح الميكانيكي على قطعة العمل من خلال قطع حافتي القطع الرئيسية والثانوية للأداة. تسمى مساحة المقطع العرضي للجزء المتروك غير المقطوع على السطح الميكانيكي بواسطة حافتي القطع بالمساحة المتبقية، كما هو موضح في الشكل 13. من الشكل، يمكن ملاحظة أنه كلما كبرت المساحة المتبقية وزاد ارتفاعها، زادت قيمة خشونة السطح.

بالإضافة إلى ذلك، تؤثر خشونة حافة القطع أيضًا على جودة تصنيع سطح قطعة العمل. كلما كانت حافة القطع أكثر سلاسة ووضوحًا، انخفضت قيمة خشونة السطح للسطح المشغول.
أثناء القطع، سيؤدي التشوه البلاستيكي الناجم عن ضغط واحتكاك نصف قطر طرف الأداة ووجه الجناح إلى تشويه المنطقة المتبقية، وبالتالي زيادة قيمة خشونة السطح لسطح قطعة الشُّغْلَة المُشَكَّلَة.
(2) نتوءات تشبه القشور
عند قطع المعادن البلاستيكية بزاوية أشعل الأداة صغيرة جدًا وسرعة قطع منخفضة جدًا، ستظهر شقوق عرضية عمودية تقريبًا على اتجاه سرعة القطع ونتوءات تشبه القشور، والتي تسمى ببساطة نتوءات قشرية، على سطح قطعة العمل. عندما تظهر النتوءات القشرية يمكن أن تزيد من قيمة خشونة السطح.
(3) الحافة المبنية
بعد تكوين حافة مبنية عند قطع المعادن البلاستيكية بسرعات متوسطة، نظرًا لأن الحافة المبنية غير منتظمة وغير مستقرة على حد سواء، فمن ناحية، تحل أجزاؤها غير المنتظمة محل جزء من حافة القطع للقطع، مما يخلق أخاديد متفاوتة الأعماق على سطح قطعة العمل. ومن ناحية أخرى، تصبح بعض الحافة المبنية المنفصلة جزءًا لا يتجزأ من الحافة المبنية المنفصلة في السطح المشغول، مما يشكل نقاطًا ونتوءات صلبة، مما يزيد من قيمة خشونة سطح قطعة العمل.
(4) الاهتزاز
سوف تتسبب الاهتزازات الدورية الناتجة عن الأدوات، وقطع العمل، ومكونات أداة الماكينة في ظهور علامات اهتزاز دورية على سطح الشُّغْلَة المُشَغَّلة، مما يزيد من قيمة خشونة السطح بشكل كبير.
2. طرق تقليل خشونة سطح قطعة العمل
في عمليات القطع، إذا تبين أن قيمة خشونة السطح لقطعة العمل لا تفي بمتطلبات الرسم، يجب أولاً ملاحظة وتحليل شكل وسبب زيادة قيمة خشونة السطح بعناية، وتحديد العوامل الرئيسية التي تؤثر على زيادة قيمة خشونة السطح، ثم اقتراح الحلول المستهدفة.
فيما يلي العديد من الظواهر الشائعة التي تسبب ارتفاع قيم خشونة سطح قطعة العمل (انظر الشكل 14).

أ) ارتفاع مرتفع متبقٍ عالٍ
ب) النتوءات السطحية
ج) علامات سحب البُرادة
د) علامات الاهتزاز
(1) الحد من ارتفاع المساحة المتبقية
كما يتضح من الشكل 14، يمكن أن يؤدي تقليل زاوية حافة القطع الرئيسية وزاوية حافة القطع الثانوية ومعدل التغذية، بالإضافة إلى زيادة نصف قطر طرف الأداة، إلى تقليل ارتفاع المساحة المتبقية. عند تنفيذ ذلك، يجب الانتباه إلى الجوانب التالية:
1) بشكل عام، يكون لتقليل زاوية حافة القطع الصغرى تأثير أكثر وضوحًا على تقليل قيم خشونة السطح. ومع ذلك، فإن تقليل زاوية حافة القطع الرئيسية k r سيزيد من المقاومة الشعاعية، مما قد يسبب الاهتزاز إذا كان النظام التكنولوجي يفتقر إلى الصلابة.
2) يمكن أن تؤدي زيادة نصف قطر طرف الأداة بشكل مناسب إلى تقليل قيم خشونة السطح. ومع ذلك، إذا كان نصف قطر طرف الأداة كبيرًا جدًا وكانت أداة الماكينة تفتقر إلى الصلابة، فسوف تزيد المقاومة الشعاعية وتسبب الاهتزاز، مما يزيد بدوره من قيم خشونة السطح.
3) يمكن أن يؤدي تقليل معدل التغذية وزيادة سرعة القطع أيضًا إلى تقليل قيم خشونة السطح.
(2) تجنب الحافة المتراكمة وعلامات الخدش
يمكن كبح تشكيل الحافة المتراكمة عن طريق تغيير سرعة القطع. بالنسبة لأدوات الخراطة الفولاذية عالية السرعة، يجب تقليل سرعة القطع (v c <5 م/دقيقة) وينبغي إضافة سائل القطع؛ أما بالنسبة لأدوات الخراطة المصنوعة من الكربيد، فينبغي زيادة سرعة القطع (تجنب نطاق السرعة المتوسطة حيث من المرجح أن تحدث الحافة المتراكمة، v c = 15 ~ 30 م/دقيقة).
يمكن أن تؤدي زيادة زاوية أشعل النار لأداة الخراطة إلى كبح تشكيل الحافة المتراكمة بشكل فعال، ولكن يجب ضمان القوة الكافية لحافة القطع. بالإضافة إلى ذلك، فإن خشونة السطح العالية لحافة القطع سوف تتسبب أيضًا في ظهور نتوءات على سطح قطعة العمل. ولذلك، يجب بذل الجهود لتقليل خشونة السطح لأوجه أشعل النار والجناح، والحفاظ على حدة حافة القطع في جميع الأوقات.
(3) تجنب البقع المضيئة البالية
عندما تكون الأداة متآكلة بشدة، ستظهر بقع مضيئة أو نقاط مضيئة على السطح المشغول آليًا، وستنتج ضوضاء أثناء القطع. ستقوم حافة القطع البالية بضغط العلامات المضيئة على سطح الشُّغْلة، مما يزيد من قيمة خشونة السطح. في هذه الحالة، يجب إعادة صقل الأداة أو استبدالها على الفور.
(4) منع البُرادة من خدش السطح المشغول آليًا
سوف يظهر سطح قطع العمل المتأثرة بسحب البُرادة بعض الخدوش الضحلة غير المنتظمة على السطح المشغول. يمكن أن يؤدي اختيار أداة القطع بزاوية أشعل النار الموجبة، وتوجيه تدفق البُرادة نحو السطح غير المشكَّل من الشُّغْلة، واعتماد تدابير مناسبة لكسر أخدود البُرادة إلى تجنب هذه الظاهرة ومنعها بشكل فعال.
(5) منع علامات الثرثرة والتخلص منها
يمكن أن تتسبب الاهتزازات الناتجة أثناء الخراطة في ظهور علامات رفرفة عرضية أو طولية دورية على سطح قطعة العمل. لمعالجة ذلك، يجب الانتباه إلى الجوانب التالية:
1) جوانب الأدوات الآلية.
تعزيز ثبات تركيب المخرطة؛ وضبط خلوص عمود الدوران، وتحسين دقة المحمل؛ وضبط خلوص شرائط الانزلاق المتوسطة والصغيرة إلى أقل من 0.04 مم، وضمان حركة سلسة وسهلة.
2) جوانب الأداة.
تحسين صلابة ساق الأداة؛ واختيار معلمات هندسية مناسبة للأداة، والحفاظ بانتظام على حواف قطع نظيفة وحادة.
3) جوانب الشغل.
قم بزيادة صلابة تركيب الشُّغْلَة وتقليل طول الشُّغْلَة المتدلية؛ تغيير طريقة التشبيك؛ استخدام مساند مركزية أو مساند أتباع للدعم عند العمل مع قطع الشُّغْلَة الطويلة والنحيلة.
4) جوانب معلمات القطع.
اختر عمق قطع ومعدل تغذية أصغر، أو قم بتغيير أو تقليل سرعة القطع.
(6) الاختيار المناسب لسائل القطع، مع ضمان التبريد والتشحيم المناسبين
يعد الاختيار السليم لسائل القطع طريقة فعالة للتخلص من الحافة المتراكمة والقشور وتقليل خشونة السطح. يمكن أن يقلل التبريد والتشحيم الملائم من مقاومة القطع، ويقلل من درجة حرارة القطع، ويحسن من عمر الأداة.