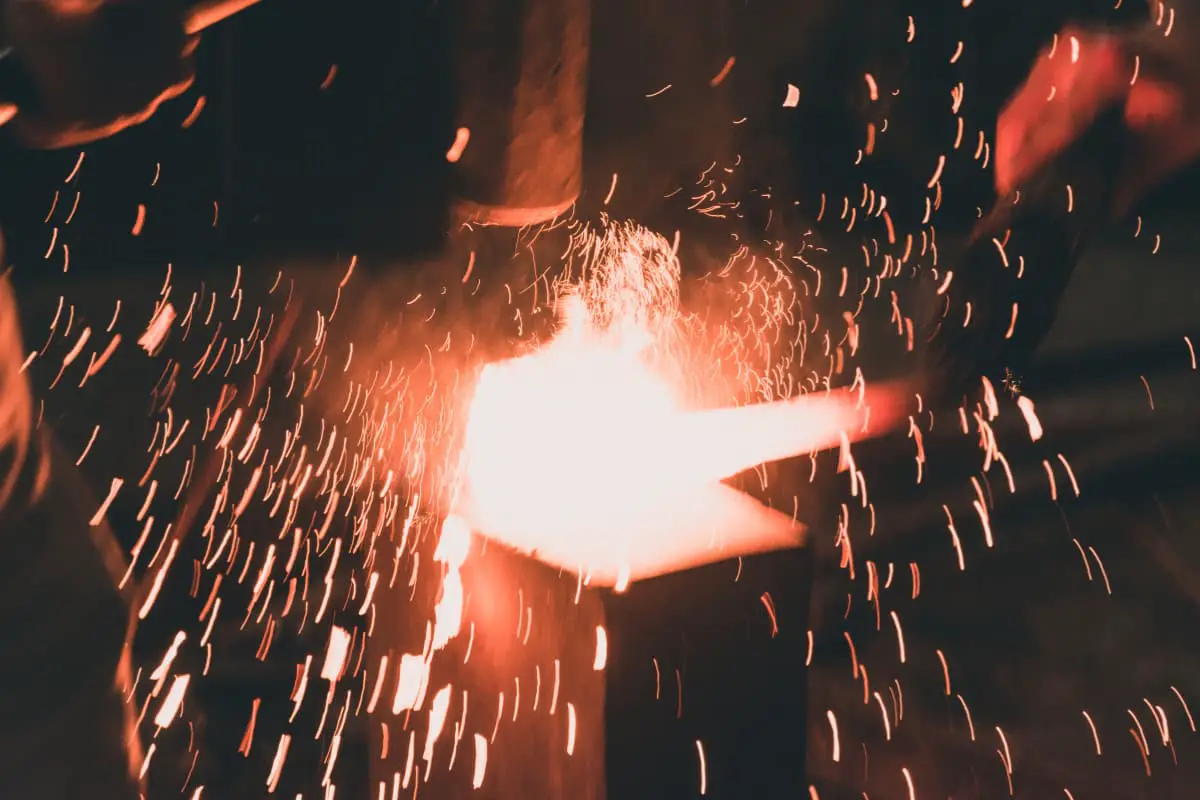
1. الكراك
(1) الشقوق الناجمة عن الاحتراق الزائد على السطح تتوزع هذه الشقوق في الغالب على حواف الزوايا لمطروقات قضبان التوصيل، خاصة في المناطق التي تتعرض لإجهاد الشد أثناء التشكيل. وتتمثل الخصائص في أن الشقوق قصيرة وسميكة وموزعة بكثافة غير منتظمة على سطح المطروقات وتمتد إلى الداخل على طول حدود الحبيبات؛ ويمتلئ الجزء الداخلي من الشقوق بالأكاسيد وإزالة الكربنة الشديدة على كلا الجانبين والحبيبات الخشنة ووجود بنية Widmanstätten.
(2) الشقوق الناجمة عن درجة الحرارة المنخفضة للغاية أثناء التشكيل أو التحجيم النهائي تتوزع هذه الشقوق في الغالب في مناطق التشكيل التي تتعرض لإجهاد الشد أثناء التشكيل بالقالب أو عند حدود تدفق المعدن. وتتميز بكونها عميقة وطويلة وكثيفة نسبياً.
(3) التشقق (انظر الشكل 6-32) السمة المميزة هي أن الشقوق ضحلة نسبياً وشبيهة بالشبكة موزعة على سطح التشكيل. والأسباب الرئيسية لتكوينها هي كما يلي:
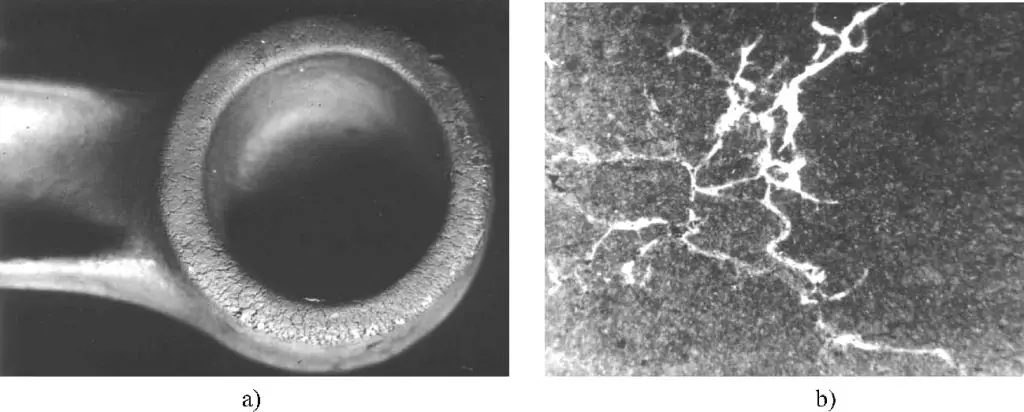
أ) التشقق في الطرف الصغير لقضيب التوصيل ب) النحاس في الفولاذ
1) فصل النحاس والقصدير في المادة الخام، أو المحتوى الزائد من النحاس والقصدير. نظرًا لأن النحاس والقصدير لهما درجات انصهار منخفضة، فإنهما يذوبان أثناء تسخين التشكيل، مما يتسبب في انخفاض اللدونة الموضعية وتكوين الشقوق.
2) المحتوى المفرط من الكبريت في الوقود، خاصةً عند استخدام الغاز أو الغاز الطبيعي كوقود، بسبب عدم اكتمال إزالة الكبريت، يخترق الكبريت الطبقة السطحية للقضبان على طول حدود الحبيبات أثناء التسخين، مكونًا شوائب كبريتيدية عند حدود الحبيبات مما يضعف الاتصال بين الحبيبات ويؤدي إلى التشقق أثناء التشكيل بالقالب.
(4) التشققات الطولية على طول خط الفراق (انظر الشكل 6-33) تحدث هذه التشققات بسبب شوائب غير معدنية. بسبب الشوائب غير المعدنية مثل الكبريت والفوسفور في الفولاذ، وكذلك العيوب مثل الانكماش والمسامية التي لم يتم لحامها أثناء صنع البليت أو التشكيل، يتم ضغطها في الوميض أثناء التشكيل بالقالب، وتظهر الشقوق عند خط الفراق أثناء التشذيب.

1) القضبان التي بها عيوب شديدة، يتم ضغط العيوب إلى الوميض، وتظهر على شكل شقوق على طول السطح المقطوع للوميض، أو ينقسم التشكيل إلى نصفين على طول خط افتراق قالب التشكيل (انظر الشكل 6-34). ونظرًا لوجود انكماش أو مسامية في سبيكة الصلب، والتي تكون ممدودة أثناء السحب أو التشكيل بالدلفة، يتم ضغط حواف الانكماش أو المسامية التي تم ضغطها أثناء التشكيل بالقالب في الوميض، وتظهر هذه العيوب بعد تقليم الوميض.

أ) عيوب البليت ب) العيوب التي تم ضغطها على الوميض
2) السبب في تكوّن الشقوق أثناء عملية التشكيل هو اختلاف خشونة السطح للجسور العلوية والسفلية لأخدود الوميض، مما يسبب مقاومة مختلفة عندما يتدفق المعدن في أخدود الوميض، مما يؤدي إلى سهولة توليد إجهاد القص داخل سطح الفراق,
مما يتسبب في تشقق السطح الفاصل وتشققه.
3) اختلال شديد في المحاذاة أثناء تشكيل القالب، مما يتسبب في تمزق سطح الفراق أثناء عملية التشذيب (انظر الشكل 6-35).

يتمزق السطح الفاصل أثناء العملية
2. مقياس مزور في الحدادة
بالإضافة إلى تغيير أبعاد المقطع العرضي وطول البليت وتوزيع المعدن، فإن خطوة الإزعاج في التشكيل بالقالب المطرقي تعمل أيضًا على إزالة القشور. إذا لم يتم تشغيل خطوة الإزعاج وفقًا لمتطلبات العملية، ولم تتم إزالة القشور بالكامل، فسيتم ضغطها في التشكيل أثناء التشكيل النهائي. بعد سقوط الترسبات الكلسية من التشكيل، تتشكل الحفر على السطح، تاركةً قشورًا سوداء على السطح الميكانيكي. يمكن أن يصل عمق الآثار المتبقية بعد التخليل وإزالة القشور من التشكيل إلى 3 مم.
إذا تجاوز هذا العيب الحد المسموح به في التصنيع، فقد يتسبب في إلغاء التشكيل. لذلك، من المهم إزالة القشور بعناية لتجنب حدوث هذا العيب.
تتمثل الأسباب الرئيسية لهذا الخلل في الجودة فيما يلي:
1) تزوير العيوب مثل المسافات البادئة الناجمة عن قشور الأكسيد غير النظيفة في أخاديد القالب أثناء التشكيل. يمكن أن يؤدي الإهمال الطفيف، خاصةً في الأطراف الأمامية والخلفية لأخاديد القالب، إلى زوايا ميتة في النفخ.
2) الأكسدة الحادة أثناء تسخين البليت، حيث لا يمكن تقشير مقياس الأكسيد تمامًا أثناء التشكيل المسبق، مما يتسبب في حدوث ثغرات في التشكيل بسبب التصاق أجزاء من مقياس الأكسيد بالبليت. لحل هذه المشكلة بشكل أساسي، من الضروري التحكم الصارم في جودة التسخين. إذا تم تشكيل مقياس الأكسيد هذا على التشكيل، فسوف يشكل حفرًا وتجاويف على السطح، أو يقلل من حجم المقطع العرضي العامل للجزء.
3) القفز في القالب أثناء عملية التشكيل، مما يتسبب في إدخال قشور الأكسيد في قالب التشكيل النهائي ويؤدي إلى ظهور مسافات بادئة على التشكيل. ولذلك، من الضروري تنظيف قشور الأكسيد من أخاديد القالب بعد قفز القالب قبل الاستمرار في عملية التشكيل.
4) تكوّن الخبث في قاع الفرن، حيث يلتصق مقياس الأكسيد بقوة بالمعدن، مما يجعل من المستحيل التخلص منه أثناء التشكيل بالقالب ولا يمكن تنظيفه أثناء التخليل. وحتى إذا كان من الممكن إزالة هذا النوع من قشور الأكسيد من التشكيل، فغالبًا ما تتقلص أبعاد التشكيل.
3. سنّ الأسنان
سمة هذا النوع من الخردة هي التلف الميكانيكي. ويحدث التلف الميكانيكي للمطروقات عند إزالتها من أخاديد قالب التشكيل أو أثناء مناولة المطروقات الساخنة؛ أو أثناء التشذيب، عندما تسقط أجسام غير ذات صلة (مثل الصفائح الرقيقة المثقوبة) على قالب التشذيب مسببة تلفاً ميكانيكياً للمطروقات. إذا تجاوز العمق المسموح به للتشذيب، يتم إلغاء الصياغة.
4. تزوير تالف
تلف المطروق بسبب الصدمة قبل وضعه بإحكام في أخدود القالب السفلي أو أثناء تحركه داخل أخدود القالب. أسباب هذا النوع من الخردة هي كما يلي:
1) لم يضع المشغل الفراغ بشكل صحيح في قالب التشكيل النهائي أو في قالب التشذيب، أو أن الصياغة لم تصطدم عندما قفزت من أخدود القالب.
2) مطرقة الحدادة لها ظواهر تأثير متداخلة، أي أن الضغط على الدواسة مرة واحدة يؤدي إلى ضرب المطرقة عدة مرات، وتتم المعالجة أيضًا على قوالب الحدادة وقوالب التشذيب المعيبة.
3) أثناء التشذيب، إذا لم يتم وضع المطروق داخل القالب، فسوف يتلف المطروق أيضًا. إن الضرر الذي يلحق بالحدادة ناتج بشكل أساسي عن إهمال المشغل، والطريقة الوحيدة لمنع تلف المطروق هي العمل بحذر.
5. انسيابية غير صحيحة
وعادةً ما يكون توزيع خط انسياب التشكيل متسقًا مع شكل التشكيل، كما هو موضح في الشكل 6-36.
ومع ذلك، إذا تم تصميم أخدود القالب قبل التشكيل بشكل غير معقول، أو إذا كان العامل يعمل بشكل غير صحيح، أو بسبب تآكل القالب، أو طرق إزعاج البليت غير السليمة، أو وضع البليت في غير موضعه في أخدود القالب، فقد يتسبب ذلك في تدفق معدني غير متساوٍ، مما قد يؤدي إلى انسيابية مضطربة وغير منتظمة.
يمكن أن تؤدي خطوط الانسيابية غير المنتظمة إلى درجات متفاوتة من الانخفاض في مؤشرات الأداء الميكانيكية المختلفة. لذلك، بالنسبة للمطروقات المهمة، هناك متطلبات لتوزيع خطوط الانسيابية.

تنجم عيوب التيارات الدوامة والتدفق العابر واختراق الأضلاع عن نفس أسباب الطي، وكلها ناتجة عن التوزيع غير المعقول للمعدن على المقطع العرضي للقوالب أو تجاوز حجم القالب للمطروقات بنسبة كبيرة، مما يتسبب في تدفق معدني غير متساوٍ شديد أثناء ملء أخدود القالب. وبالنظر إلى أشكال المطروقات المعرضة لهذه العيوب الثلاثة، نجد أن معظمها يحدث في المطروقات ذات المقاطع العرضية على شكل حرف "L" أو "Π" أو "T".
على الرغم من أن هذه العيوب الثلاثة ناتجة عن التدفق المعدني غير المتساوي، إلا أن درجة التفاوت تتفاوت مما يؤدي إلى عواقب مختلفة؛ فالحالات الأخف تشكل تيارات دوامية (انظر الشكل 6-37)، والحالات الأكثر شدة تشكل تدفقاً خلالياً (انظر الشكل 6-38)، والحالات الأكثر شدة تسبب شقوقاً في اختراق الأضلاع.
وغالبًا ما تصاحب التيارات الدوامية والتدفق العابر ظواهر الحبيبات الخشنة، ويرجع ذلك إلى أن المعدن المتدفق بشدة يميل إلى التكتل وإعادة التبلور. تُظهر النتائج التجريبية أن التيارات الدوامية والتدفق العابر لها تأثير ضئيل على قوة الجزء، ولكن لها تأثير كبير على اللدونة، والتأثير الأشد على أداء التعب ومقاومة التآكل.


6. تزوير التشوه
يشير التشوه إلى انحراف الخط المركزي ومستوى التشكيل عن الشكل الصحيح على مخطط التشكيل. يمكن أن يحدث هذا العيب أثناء التشكيل بالقالب أو التشذيب بالتثقيب أو النقل أو المعالجة الحرارية. يمكن معالجة التشوه الناتج في هذه الحالات بطرق التصحيح. هناك عمليات تصحيح في العمليات اللاحقة للتشكيل، مثل التصحيح في قالب التشكيل، على مكبس هيدروليكيعن طريق النقش، أو يدوياً.
(1) يمكن توضيح التشوه الناجم عن إزالة القوالب من خلال مقارنتها بعملية إزالة الصب من القالب. يمكن إزالة التشكيل من الصب عن طريق تدمير القالب الرملي، في حين أن عملية إزالة التشكيل من التشكيل يجب أن تتم بشكل مشابه لكيفية إزالة النموذج الخشبي من القالب الرملي أثناء الصب، وذلك باستخراج القطعة المطروقة من تجويف القالب.
لذلك، ولتسهيل عملية إزالة الرمل من المطروقات، من الضروري تطبيق مبدأ "بُعد إزالة الرمل" - وهو البعد المستدق لإزالة الرمل، على جميع جدران القالب المتعامدة على اتجاه ضغط التشكيل، مما يخلق زاوية ميل معينة، تُعرف بزاوية سحب التشكيل (عادةً ما بين 5° و12°).
وبخلاف ذلك، لا يمكن سحب القطعة المطروقة الطرية، التي تم ضغطها في تجويف القالب، إلا بالقوة باستخدام الكماشة، مما قد يؤدي إلى تشويه القطعة المطروقة بالفعل.
تكون بعض قوالب التشكيل سيئة التصميم، مما يتطلب استخدام أداة حادة لنزع القطع المطروقة، مما يتسبب حتمًا في حدوث تشوه. ويتمثل النهج الأفضل في الانتباه إلى مستدق القالب وتقليل عمق تجويف القالب (المساحة الرأسية أعلى وأسفل سطح الفراق) بالنسبة لعرضه، ومن الناحية المثالية أقل من طوله، للسماح للقطعة المطروقة بالقفز للخارج تلقائيًا أو إزالتها بأقل جهد ممكن.
(2) التشوه الناجم عن التثقيب أو التشذيب بسبب عدم دقة لكمات التشذيب أو سوء تصميم القالب، يمكن أن تتشوه التشكيلات المعقدة ذات المقاطع العرضية الرقيقة، وغالبًا ما تنحني المطروقات الطويلة بسبب تشوه التشذيب.
(3) التشوه الناجم عن التبريد بعد التشكيل أو المعالجة الحرارية يمكن أن يتسبب التبريد غير المتكافئ بعد التشكيل أو طرق التسخين والتبريد غير السليمة أثناء المعالجة الحرارية في حدوث تشوه. تشمل التشوهات الشائعة انحناء المطروقات ذات المحاور الطويلة، والتي يمكن تصحيحها عن طريق التقويم.
بالنسبة لمطروقات الفولاذ الكربوني المتوسط والمنخفض الكربون ومطروقات الفولاذ الهيكلي منخفض السبائك، إذا كان الانحناء أقل من 10 مم، فيمكن تصحيحه على البارد؛ أما التشوهات الكبيرة في الفولاذ المطروق أو سبائك الفولاذ المختلفة من الفولاذ، ومطروقات الفولاذ الهيكلي من سبائك الكربون المتوسطة فيجب تصحيحها على الساخن، أو تلدينها بعد الاستقامة لتخفيف الضغط.