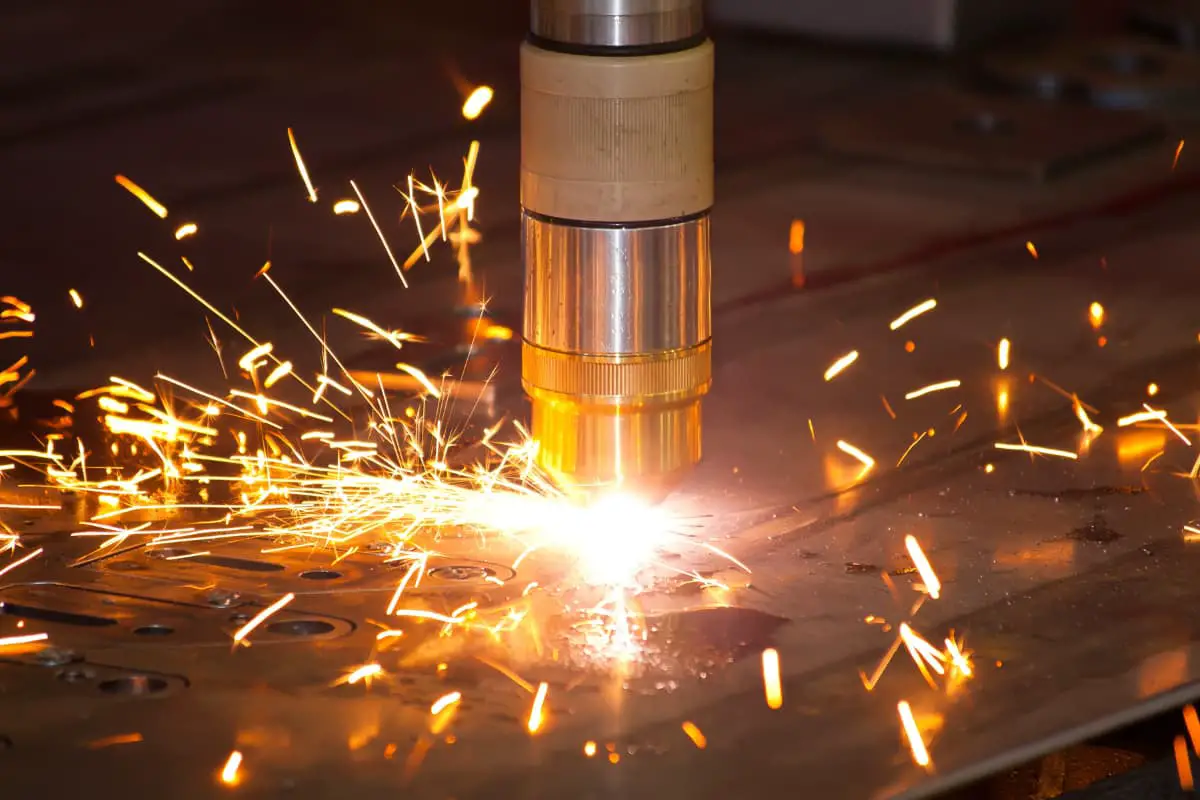
القطع بالبلازما

القطع بالبلازما هو عملية قطع حرارية عالية الدقة تستخدم كثافة طاقة عالية وقوسًا مقيدًا وتدفق بلازما عالي السرعة لصهر المعدن وطرده، مما يؤدي إلى قطع نظيف ومستمر. تعمل هذه التقنية المتقدمة على تأيين الغاز لتكوين البلازما، والتي يتم توجيهها بعد ذلك من خلال فوهة نحاسية دقيقة لتركيز الطاقة.
توفر عملية القطع بقوس البلازما العديد من المزايا مقارنة بالطرق التقليدية:
- السرعة: يحقق سرعات قطع أسرع بكثير من القطع بالوقود الأوكسيلي، خاصةً للمواد التي يقل سمكها عن 25 مم.
- الحد الأدنى من المنطقة المتأثرة بالحرارة: نظرًا لطاقته المركزة وعمل القطع السريع، فإن القطع بالبلازما يُدخل حرارة أقل في قطعة العمل، مما يؤدي إلى تقليل التشوه الحراري وتحسين جودة القطع.
- متعدد الاستخدامات: مناسبة لقطع مجموعة واسعة من الموصلات المعادن، بما في ذلك الفولاذ والألومنيوم والفولاذ المقاوم للصدأ والسبائك الأخرى.
- الدقة: قادرة على إنتاج شقوق ضيقة العرض والحفاظ على تفاوتات دقيقة، خاصةً مع دمج التحكم العددي بالكمبيوتر (CNC).
ومع ذلك، يمثل القطع بالبلازما بعض التحديات:
- المخاوف البيئية: تولد العملية ضوضاء وأبخرة وجسيمات كبيرة، مما يتطلب تهوية مناسبة وحماية المشغل.
- قيود السُمك: على الرغم من الكفاءة العالية للقطع بالبلازما بالنسبة للمواد الأقل سمكًا، إلا أن القطع بالبلازما يصبح أقل اقتصاديًا مقارنةً بالقطع بالأوكسجين والوقود لألواح الصلب الكربوني التي يتجاوز سمكها 25 مم.
- التكلفة الأولية: تتطلب أنظمة القطع بالبلازما عمومًا استثمارًا مبدئيًا أعلى من معدات وقود الأكسجين.
ومن الجدير بالذكر أن تكنولوجيا البلازما تتجاوز تطبيقات القطع. إن تعدد استخدامات أنظمة قوس البلازما يسمح بعمليات اللحام والرش والرش والصلب والتقطيع، مما يجعلها أداة قيمة متعددة الأغراض في تصنيع المعادن.
ولتحسين أداء القطع بالبلازما والتخفيف من عيوبه، ضع في اعتبارك تنفيذ جداول مائية للحد من الضوضاء والتحكم في الأبخرة، بالإضافة إلى الاستثمار في أنظمة البلازما عالية الوضوح لتحسين جودة القطع وتقليل التأثير البيئي.
خصائص وتصنيف القطع بقوس البلازما وتصنيفه
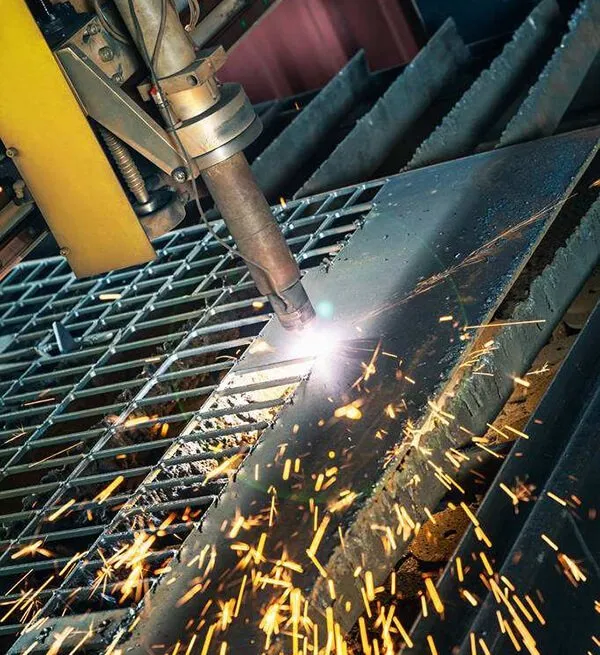
1.1 خصائص قطع القوس بالبلازما
يستخدم القطع بقوس البلازما قوس البلازما قوسًا مضغوطًا بدرجة حرارة عالية بين الكاثود (عادةً ما يكون قطبًا كهربائيًا من التنغستن) وأنود. تنتج هذه العملية نفاثة بلازما تتميز بالتأين العالي وكثافة الطاقة ومعدل التدفق.
تنطوي آلية القطع على دفع القوس والغاز الخامل من خلال فوهة ذات قطر صغير، مما ينتج عنه نفاثة عالية السرعة وساخنة للغاية. تعمل طاقة القوس المركَّزة هذه على إذابة مادة قطعة العمل، في حين أن نفاثة الغاز الممدد ذات درجة الحرارة العالية تطرد المعدن المنصهر عبر الشق.
عند قطع المواد الحديدية مثل الفولاذ الكربوني أو الحديد الزهر، يمكن إضافة الأكسجين إلى تيار الغاز لتوفير طاقة طاردة للحرارة إضافية، مما يعزز عملية القطع.
تشمل المزايا الرئيسية للقطع بقوس البلازما ما يلي:
- متعدد الاستخدامات: يمكن قطع مجموعة كبيرة من المعادن وبعض المواد غير المعدنية التي تمثل تحديًا للطرق التقليدية.
- السرعة: أسرع بكثير من القطع بالأكسجين والوقود الأوكسجيني، خاصةً بالنسبة للمواد الرقيقة (حتى 5-6 مرات أسرع بالنسبة للفولاذ الكربوني الرقيق).
- الجودة: ينتج قطعًا ساطعًا ونظيفًا بأقل قدر من التشويه الحراري، وهو مثالي للقطع الدقيقة.
- المرونة: مناسبة لقطع الأشكال والملامح المعقدة.
ومع ذلك، فإن القطع بالبلازما له أيضًا بعض القيود:
- يميل عرض الشق والزاوية المائلة إلى أن يكونا أكبر مقارنة بالطرق الأخرى، على الرغم من أن الفوهات والتقنيات الخاصة يمكن أن تخفف من ذلك بالنسبة للمواد الرقيقة.
- القدرة على قطع الألواح السميكة أقل شأناً من القطع بالأكسجين والوقود.
- ارتفاع تكاليف المعدات واستهلاك الطاقة مقارنةً بأنظمة الوقود الأوكسي.
- مخاوف محتملة تتعلق بالسلامة بسبب الجهد العالي والإشعاع القوسي والدخان والضوضاء.
تتطلب معدات القطع بالقوس البلازما عادةً:
- إمداد الطاقة: 25-200 كيلوواط، مع تيارات قطع تتراوح بين 30-1000 أمبير وجهد عالي عند عدم التحميل.
- إمدادات الغاز: الأرجون أو مخاليط النيتروجين والهيدروجين، حسب الاستخدام.
- شعلة مبردة بالماء لإدارة الحرارة.
تتوفر أنظمة القطع بالبلازما اليدوية والآلية على حد سواء. يتطلب القطع اليدوي مهارات مماثلة للقطع بالوقود الأوكسي ولكن مع تحكم إضافي في المعلمات. توفر الأنظمة المؤتمتة دقة وإنتاجية أعلى، وغالبًا ما تشتمل على طاولات مائية أو سترات للحد من الضوضاء والأبخرة.
في الختام، يوفر القطع بقوس البلازما مزايا كبيرة من حيث السرعة وتعدد الاستخدامات وجودة القطع لمجموعة واسعة من المواد والسماكات. ومع ذلك، يجب الموازنة بين الاعتبارات المتعلقة بتكلفة المعدات ومتطلبات السلامة والقيود المفروضة على المواد السميكة جدًا مقابل هذه المزايا عند اختيار عملية القطع.
1.2 مبدأ عمل القطع بقوس البلازما
ويستخدم القطع بقوس البلازما قوس البلازما قوس بلازما بدرجة حرارة عالية للغاية، تتراوح عادةً بين 10000 درجة مئوية و14000 درجة مئوية، وهو ما يتجاوز بشكل كبير درجة انصهار جميع المعادن واللافلزات المعروفة. وتتيح هذه الحرارة الشديدة قطع مجموعة واسعة من المواد، بما في ذلك معظم المواد المعدنية وغير المعدنية.
تم استخدام القطع بقوس البلازما، الذي تم تطويره في خمسينيات القرن العشرين، في البداية لقطع المواد المعدنية التي كانت تمثل تحديًا للقطع التقليدي بلهب الأكسجين والأسيتيلين، مثل سبائك الألومنيوم والفولاذ المقاوم للصدأ. ومع تطور هذه التقنية، توسعت تطبيقاتها لتشمل الفولاذ الكربوني والفولاذ منخفض السبائك، مما يجعلها طريقة قطع متعددة الاستخدامات في التصنيع الحديث.
يشبه التصميم الأساسي لشعلة القطع بقوس البلازما إلى حد كبير تصميم شعلة اللحام بقوس البلازما. ومع ذلك، يكمن الاختلاف الرئيسي في خصائص تدفق الغاز:
- تطبيق اللحام: يستخدم تدفق غاز مؤين منخفض السرعة لصهر المعدن الأساسي وتشكيل وصلة ملحومة.
- تطبيق القطع: يستخدم تدفق غاز مؤين عالي السرعة لإذابة المعدن الأساسي وطرد المادة المنصهرة بقوة، مما يؤدي إلى إحداث شقوق.
يتم تحديد فعالية قوس البلازما للقطع من خلال عدة عوامل:
- نوع الغاز المتأين
- ضغط الغاز
- الكثافة الحالية
- هندسة قناة الفوهة (نسبة العرض إلى الارتفاع)
- مسافة المواجهة بين الفوهة وقطعة العمل
يوضح الشكل 4.1 الهيكل الأساسي لشعلة القطع بقوس البلازما.
في عمليات القطع بقوس البلازما، يتم تكوين مزود الطاقة حصريًا للقطبية الموجبة للتيار المستمر، مع توصيل قطعة العمل بالقطب الموجب. يضمن هذا الإعداد النقل الأمثل للطاقة وأداء القطع الأمثل.
عند قطع المعدن، يتم استخدام قوس منقول. وتعتمد طريقة بدء هذا القوس المنقول على تصميم شعلة القطع المحددة. يمكن تصنيف مشاعل القطع بقوس البلازما إلى نوعين رئيسيين:
- شعلة القطع بالقوس التجريبي (قوس الصيانة)
- شعلة قطع القوس غير التجريبي (القوس غير القابل للصيانة)
يوضح الشكل 4.2 مخطط أسلاك الدائرة الكهربائية لشعلة القطع القوسي التجريبي. تتشابه دائرة شعلة القطع بالقوس غير التجريبي مع دائرة شعلة القطع بالقوس غير التجريبي ولكنها تفتقر إلى الفرع المقاوم الموجود في تكوين القوس التجريبي. يؤثر هذا الاختلاف في التصميم على خصائص بدء القوس وخصائص الاستقرار لكل نوع من أنواع الشعلة.
ويُعد فهم هذه المبادئ وتكوينات المعدات أمرًا بالغ الأهمية لتحسين عمليات القطع بقوس البلازما في التطبيقات الصناعية، مما يضمن إجراء عمليات قطع فعالة وعالية الجودة عبر مجموعة واسعة من المواد.
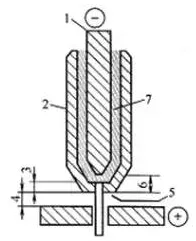
الشكل 1 الهيكل الأساسي لمسدس القطع بقوس البلازما
- 1. قطب كهربائي;
- 2. فوهة ضغط;
- 3. اضغط على طول قناة الفوهة;
- 4. المسافة من الفوهة إلى قطعة العمل;
- 5. اضغط على فتحة الفوهة;
- 6. مسافة سحب القطب الكهربائي;
- 7. غاز لونيك.
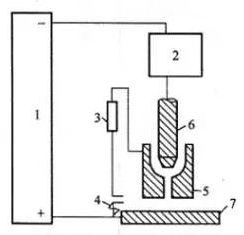
الشكل 2 الدائرة الأساسية لمسدس القطع القوسي للصيانة
- 1. مزود الطاقة;
- 2. مشغل قوس عالي التردد;
- 3. المقاومة;
- 4. جهة الاتصال;
- 5. رذاذ الضغط;
- 6. القطب الكهربائي;
- 7. الشغل.
تتمثل وظيفة المقاوم في الشكل 2 في الحد من تيار صيانة القوس إلى أدنى قيمة يمكن أن تشعل قوس النقل بسلاسة.
يتم استخدام بادئ القوس عالي التردد لإشعال قوس الصيانة.
عندما يصطدم القوس، يتم إغلاق ملامس الملامس، ويولد بادئ القوس عالي التردد ترددًا عاليًا وجهدًا عاليًا لإشعال قوس الصيانة.
بعد أن يتم إشعال قوس الصيانة، عندما يقترب مسدس القطع من قطعة العمل، يلامس لهب البلازما عالي السرعة من الفوهة قطعة العمل لتشكيل مسار بين القطب وقطعة العمل، بحيث يتم نقل القوس بين القطب وقطعة العمل.
وبمجرد إنشاء قوس النقل، يتم إطفاء قوس الصيانة تلقائيًا، ويتم فصل تلامس الملامس تلقائيًا بعد فترة تأخير زمني.
القطع بالليزر
القطع بالليزر هو تقنية قطع متقدمة ومستخدمة على نطاق واسع في معالجة المواد.
وهي طريقة معالجة تستخدم شعاع ليزر عالي الكثافة للطاقة "كأداة قطع" لقطع المواد حرارياً.
يمكن استخدام تكنولوجيا القطع بالليزر لقطع أنواع مختلفة من المعادن والألواح غير المعدنية والمواد المركبة والمواد الصلبة مثل كربيد التنجستن وكربيد التيتانيوم، وقد استخدمت على نطاق واسع في بناء الدفاع الوطني والفضاء والآلات الهندسية وغيرها من المجالات.
Lمبدأ القطع العصري وتصنيفه وخصائصه
2.1 مبدأ القطع بالليزر وتصنيفه
(1) مبدأ القطع بالليزر
القطع بالليزر هو طريقة القطع الحراري الدقيق الذي يستخدم شعاع ليزر عالي الكثافة ومركّز وعالي الطاقة لمعالجة المواد. عندما يشع شعاع الليزر قطعة العمل، فإنه يسخن المادة بسرعة إلى درجة انصهارها أو درجة حرارة التبخير أو نقطة الاشتعال، اعتمادًا على خصائص المادة والنتيجة المرجوة. في الوقت نفسه، يتم توجيه تيار غاز عالي السرعة، عادةً ما يكون النيتروجين أو الأكسجين، بشكل محوري مع شعاع الليزر لطرد المادة المنصهرة من الشق، مما يؤدي إلى قطع نظيف ودقيق.
تتضمن العملية عدة آليات رئيسية:
- الامتصاص: تمتص المادة طاقة الليزر وتحولها إلى حرارة.
- الذوبان: تتسبب الحرارة الموضعية في ذوبان المادة في منطقة محصورة.
- التبخير: قد تتبخر بعض المواد جزئياً، خاصةً عند كثافات الطاقة العالية.
- التفاعل الكيميائي: في حالة القطع بمساعدة الأكسجين، يمكن أن يحدث تفاعل طارد للحرارة، مما يعزز عملية القطع.
- قذف الذوبان: يزيل نفاث الغاز المحوري المادة المنصهرة، مما يؤدي إلى إحداث القطع.
يوفر القطع بالليزر العديد من المزايا، بما في ذلك الدقة العالية، والحد الأدنى من المنطقة المتأثرة بالحرارة، والقدرة على قطع الأشكال الهندسية المعقدة، وملاءمة مجموعة واسعة من المواد، من المعادن إلى غير المعادن.
انظر الشكل 3 للاطلاع على تمثيل تخطيطي لمبدأ القطع بالليزر.
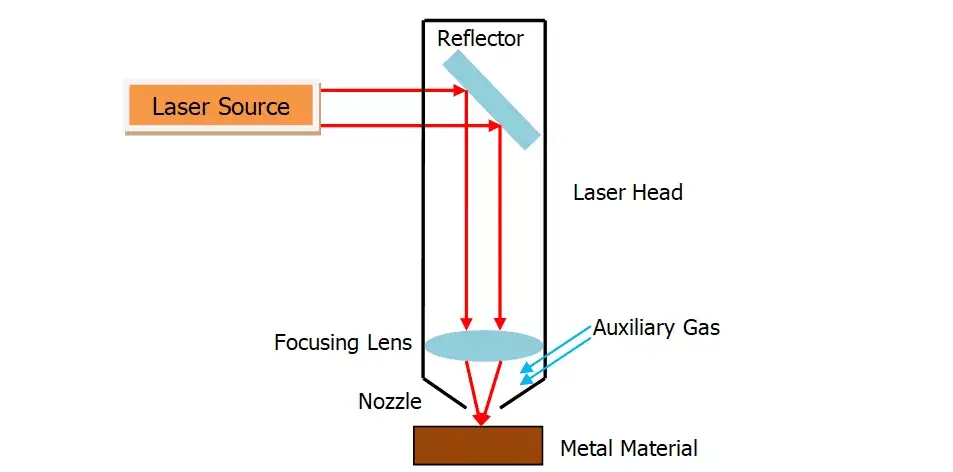
الشكل 3 مبدأ القطع بالليزر
(2) تصنيف القطع بالليزر
يمكن تصنيف القطع بالليزر إلى أربعة أنواع رئيسية: القطع بالتبخير بالليزر، والقطع بالذوبان بالليزر، والقطع بالأكسجين بالليزر، والقطع بالليزر بالأكسجين والقطع بالليزر مع الكسر المتحكم فيه.
1) القطع بالتبخير بالليزر
في هذه العملية، يسخّن شعاع ليزر عالي الكثافة الطاقة قطعة العمل بسرعة، مما يتسبب في وصول درجة حرارة المادة بسرعة إلى نقطة الغليان. ويؤدي ذلك إلى تبخير المادة، مما يؤدي إلى تشكيل نفاثة بخار عالية السرعة. وبينما يتم قذف البخار، فإنه يخلق في الوقت نفسه شقاً في المادة.
ونظراً لحرارة التبخير العالية عادةً للمواد، فإن القطع بالتبخير بالليزر يتطلب طاقة وكثافة طاقة كبيرة. وتستخدم هذه الطريقة في المقام الأول لقطع الصفائح المعدنية الرقيقة للغاية والمواد غير المعدنية مثل الورق والمنسوجات والخشب والبلاستيك والمطاط.
2) القطع بالذوبان بالليزر
يتضمن القطع بالصهر بالليزر استخدام حرارة الليزر لصهر المادة المعدنية. يتم بعد ذلك نفخ غاز غير مؤكسد (مثل Ar أو He أو N2) من خلال فوهة محورية مع الشعاع. يقوم تيار الغاز عالي الضغط بطرد المعدن المنصهر مما يؤدي إلى تكوين شق.
تتطلب هذه التقنية حوالي 1/10 فقط من الطاقة اللازمة للقطع بالتبخير، حيث إنها لا تستلزم تبخير المواد بالكامل. القطع بالذوبان بالليزر فعال بشكل خاص في قطع المواد التي تقاوم الأكسدة أو المعادن النشطة، بما في ذلك الفولاذ المقاوم للصدأ والتيتانيوم والألومنيوم وسبائكها.
إن كفاءة ودقة القطع بالصهر بالليزر ودقته تجعل منه طريقة مفضلة في العديد من التطبيقات الصناعية، خاصةً عندما تكون عمليات القطع النظيفة والحد الأدنى من المناطق المتأثرة بالحرارة أمرًا بالغ الأهمية.
3) قطع الأكسجين بالليزر
يجمع القطع بالأكسجين بالليزر بين دقة تقنية الليزر والتفاعل الطارد للحرارة للقطع بالأكسجين. وتستخدم هذه العملية شعاع الليزر كمصدر للتسخين المسبق والأكسجين كغاز القطع، مما يخلق تأثيرًا تآزريًا يعزز كفاءة القطع وجودته.
تعمل الآلية على محورين أساسيين:
- تفاعل الأكسدة: يتفاعل تيار الأكسجين عالي الضغط مع سطح المعدن المسخن، مما يؤدي إلى بدء تفاعل أكسدة طارد للحرارة. ويطلق هذا التفاعل كمية كبيرة من الحرارة الإضافية، مما يزيد من كثافة عملية القطع.
- إزالة المواد: ينتج عن الجمع بين التسخين بالليزر والأكسدة معدن مصهور وأكاسيد منصهرة. ثم يطرد نفاث الأكسجين عالي السرعة هذه المواد المنصهرة من الشق، مما يخلق قطعًا نظيفًا وضيقًا.
نظرًا للمساهمة الحرارية الكبيرة من تفاعل الأكسدة، لا يتطلب القطع بالأكسجين بالليزر سوى حوالي 501 تيرابايت 3 تيرابايت من طاقة الليزر اللازمة للقطع بالاندماج النقي. وتُترجم كفاءة الطاقة هذه إلى سرعات قطع أعلى بكثير مقارنةً بطرق القطع بالتبخير بالليزر أو القطع بالاندماج.
القطع بالأكسجين بالليزر فعال بشكل خاص للمواد ذات الأكسجين العالي، مثل:
- الفولاذ الكربوني
- الفولاذ منخفض السبائك
- درجات معينة من الفولاذ المعالج بالحرارة
ومع ذلك، فهي أقل ملاءمة للمواد التي تشكل أكاسيد حرارية أو ذات ميول أكسدة منخفضة، مثل الفولاذ المقاوم للصدأ والتيتانيوم والألومنيوم وسبائكها. بالنسبة لهذه المواد، تكون تقنيات القطع بالليزر الأخرى مثل القطع بالانصهار مع مساعدة الغاز الخامل أكثر ملاءمة.
4) الحك بالليزر والتحكم في الكسر بالليزر
الخربشة بالليزر هي تقنية معالجة دقيقة للمواد تستخدم أشعة الليزر عالية الكثافة للطاقة لإنشاء أخاديد ضحلة يمكن التحكم فيها على سطح المواد الهشة. تتضمن هذه العملية الخطوات التالية:
- يقوم شعاع ليزر مركز، عادةً من ليزر Q-switched أو ليزر CO2، بمسح سطح المادة.
- يؤدي التسخين الموضعي الشديد إلى تبخير سريع، مما يخلق أخدودًا ضيقًا ضحلًا.
- بعد الخربشة، يتم تطبيق الضغط المتحكم به على المادة.
- تنكسر المادة الهشّة على طول الخط المكتوب، مما ينتج عنه كسر نظيف ودقيق.
تستفيد تقنية الكسر المتحكم فيه، وهي تقنية ذات صلة، من التدرجات الحرارية الحادة للحرارة المتولدة أثناء الحك بالليزر لإحداث إجهادات حرارية موضعية في المواد الهشة. هذه الطريقة:
- ينشئ منطقة متأثرة بالحرارة شديدة التأثر بالحرارة على طول الخط المكتوب.
- يولد إجهادات حرارية بسبب دورات التسخين والتبريد السريعة.
- يستغل هذه الضغوط لنشر صدع على طول المسار المطلوب.
- ينتج عنه كسر متحكم به مع الحد الأدنى من فقدان المواد وجودة حافة عالية.
إن كلاً من الحك بالليزر والتكسير المتحكم فيه ذو قيمة خاصة لمعالجة المواد الهشة مثل الزجاج والسيراميك وبعض أشباه الموصلات، مما يوفر مزايا في الدقة والسرعة وتقليل هدر المواد مقارنة بطرق القطع التقليدية.
2.2 Cخصائص القطع بالليزر
بالمقارنة مع طرق القطع الحراري الأخرى، يتميز القطع بالليزر بسرعة سرعة القطع وجودة عالية.
يمكن تلخيصها على النحو التالي.
(1) جودة القطع الفائقة
يحقق القطع بالليزر جودة قطع استثنائية نظرًا لصغر البؤرة البؤرية وكثافة الطاقة العالية وسرعة القطع السريعة. توفر هذه التقنية المتقدمة العديد من المزايا الرئيسية:
① الشق الدقيق: يتميز الشق المقطوع بالليزر بأنه رفيع وضيق بشكل استثنائي، مع جوانب متوازية متعامدة على سطح المادة. وتتيح هذه الدقة دقة أبعاد الأجزاء المقطوعة التي تصل إلى ± 0.05 مم (± 0.002 بوصة)، متجاوزة بذلك العديد من طرق القطع التقليدية.
② سطح نقي السطح: يُظهر سطح القطع مظهرًا نظيفًا وممتعًا من الناحية الجمالية. يتم تقليل خشونة السطح إلى بضع عشرات من الميكرونات فقط (عادةً 10-50 ميكرون Ra)، مما يلغي في كثير من الأحيان الحاجة إلى عمليات تشطيب ثانوية. في كثير من الحالات، يمكن استخدام الأجزاء المقطوعة بالليزر مباشرةً دون الحاجة إلى معالجة ميكانيكية إضافية، مما يؤدي إلى تبسيط سير عمل الإنتاج.
③ الحد الأدنى من المنطقة المتأثرة بالحرارة (HAZ): تولد عملية القطع بالليزر منطقة متأثرة بالحرارة ضيقة للغاية. ينتج عن هذه المدخلات الحرارية الموضعية:
- تغيير طفيف في خصائص المواد المجاورة لحافة القطع
- الحد الأدنى من تشوه الشُّغْلة، مع الحفاظ على دقة عالية بشكل عام
- هندسة الشق الممتازة، التي تتميز بمقطع عرضي مستطيل متناسق على طول مسار القطع
إن الجمع بين هذه العوامل - الدقة وجودة السطح والحد الأدنى من التأثير الحراري - يجعل القطع بالليزر خيارًا مثاليًا للتطبيقات التي تتطلب مكونات عالية الدقة، خاصة في صناعات مثل الفضاء وتصنيع الأجهزة الطبية والهندسة الدقيقة.
انظر الجدول 1 للمقارنة بين طرق القطع بالليزر والقطع بالأوكسي أسيتيلين والقطع بالبلازما.
مادة القطع هي صفيحة فولاذية منخفضة الكربون بسماكة 6.2 مم.
الجدول 1 مقارنة بين القطع بالليزر والقطع بالأوكسي أسيتيلين والقطع بالبلازما
طريقة القطع | عرض الشق / مم | عرض المنطقة المتأثرة بالحرارة / مم | شكل الشق | سرعة القطع | تكلفة المعدات |
القطع بالليزر | 0.2~0.3 | 0.04~0.06 | موازٍ | سريع | عالية |
القطع بالأوكسي أسيتيلين | 0.9~1.2 | 0.6~1.2 | متوازي نسبيًا | بطيء | منخفضة |
القطع بالبلازما | 3.0~4.0 | 0.5~1.0 | مصبوب ومائل | سريع | الأوسط |
(2) كفاءة قطع عالية (2)
تتفوق ماكينات القطع بالليزر في الإنتاجية بسبب خصائص النقل الفريدة وأنظمة التحكم المتقدمة. وعادةً ما تشتمل هذه الأنظمة على طاولات عمل متعددة بنظام التحكم العددي الحاسوبي (CNC)، مما يتيح عمليات قطع مؤتمتة بالكامل ويتم التحكم فيها بدقة.
عملية القطع متعددة الاستخدامات وفعالة بشكل ملحوظ. فبمجرد تعديل برنامج الماكينة بنظام التحكم الرقمي، يمكن للمشغلين الانتقال بسرعة بين قطع الأجزاء ذات الأشكال الهندسية المتنوعة. تمتد هذه المرونة إلى كل من تطبيقات القطع ثنائية الأبعاد وثلاثية الأبعاد، مما يستوعب مجموعة كبيرة من متطلبات التصنيع.
تشمل المزايا الرئيسية لكفاءة القطع بالليزر ما يلي:
- أوقات إعداد سريعة: الحد الأدنى من تغييرات الأدوات بين المهام
- قطع عالي السرعة: تتحرك أشعة الليزر بسرعات تصل إلى 20-30 م/دقيقة للمواد الرقيقة
- القدرة متعددة المحاور: تتيح الأنظمة ذات 5 محاور إجراء عمليات قطع ثلاثية الأبعاد معقدة في إعداد واحد
- التعشيش التلقائي: يعمل البرنامج على تحسين استخدام المواد، مما يقلل من الهدر
- التشغيل المستمر: تتميز بعض الأنظمة بخاصية التحميل/التفريغ التلقائي للمواد من أجل وقت تشغيل ممتد
تجتمع هذه الميزات لتقليل أزمنة الدورات بشكل كبير وزيادة الإنتاجية وتعزيز إنتاجية التصنيع الإجمالية مقارنةً بطرق القطع التقليدية.
(3) سرعة القطع السريع
يمكن لنظام الليزر عالي الطاقة، الذي يستخدم عادةً مصدر 1200 واط، تحقيق سرعات قطع عالية بشكل ملحوظ لمختلف المواد. وعند معالجة ألواح الفولاذ منخفض الكربون بسماكة 2 مم، يمكن تحقيق سرعات قطع تصل إلى 15000 مم/دقيقة (590 بوصة/دقيقة)، مما يبرز كفاءة تكنولوجيا الليزر في تشغيل المعادن.
تمتد براعة القطع بالليزر إلى المواد غير المعدنية أيضًا. على سبيل المثال، عند قطع صفائح راتنج البولي بروبيلين بسماكة 5 مم، يمكن أن تصل السرعات أيضًا إلى 15000 مم/الدقيقة، مما يدل على قدرة النظام على التكيف عبر أنواع المواد المختلفة وسماكاتها.
تتمثل إحدى المزايا الرئيسية للقطع بالليزر في طبيعته غير التلامسية، مما يلغي الحاجة إلى التثبيت الميكانيكي أو تركيب قطع العمل. لا تقلل هذه الميزة من تكاليف الأدوات وتبسط عملية الإعداد فحسب، بل تقلل أيضًا بشكل كبير من الوقت الإضافي لتحميل المواد وتفريغها. كما أن عدم وجود تلامس مادي يقلل أيضًا من خطر تشوه قطعة العمل، وهو أمر مفيد بشكل خاص للمواد الرقيقة أو الحساسة.
وعلاوة على ذلك، تساهم دقة وسرعة القطع بالليزر في تقليل هدر المواد وتحسين اتساق القطع، مما يعزز كفاءة التصنيع بشكل عام. إن قدرة هذه التقنية على إجراء عمليات قطع معقدة مع الحد الأدنى من المناطق المتأثرة بالحرارة تجعلها مثالية لكل من النماذج الأولية وسيناريوهات الإنتاج بكميات كبيرة في صناعات تتراوح من صناعة السيارات إلى تصنيع الإلكترونيات.
(4) القطع بدون تلامس
يعمل القطع بالليزر بدون تلامس مادي بين آلية القطع وقطعة العمل، مما يقلل من تآكل الأداة ويطيل عمر المعدات. تسمح طبيعة عدم التلامس هذه بإجراء عمليات قطع دقيقة بأقل قدر من التشويه الحراري، وهو أمر مفيد بشكل خاص للمواد الحساسة للحرارة.
إن تعدد استخدامات القطع بالليزر لا مثيل له؛ فمعالجة الأجزاء الهندسية المتنوعة لا تتطلب سوى تعديلات على معلمات الليزر مثل الطاقة والتردد والبُعد البؤري. وتقلل هذه المرونة بشكل كبير من وقت الإعداد وتعزز كفاءة الإنتاج مقارنةً بطرق القطع التقليدية التي تتطلب تغيير الأدوات.
وعلاوة على ذلك، يوفر القطع بالليزر العديد من المزايا البيئية والمريحة:
- انبعاث ضوضاء منخفض، عادةً أقل من 70 ديسيبل، مما يعزز الراحة في مكان العمل
- الحد الأدنى من الاهتزاز، مما يضمن دقة عالية ويقلل من إجهاد المشغِّل
- تلوث يقترب من الصفر، حيث لا ينتج عن العملية أي رقائق وأدنى حد من الأدخنة عند تهويتها بشكل صحيح
تجعل هذه الخصائص من القطع بالليزر خيارًا مثاليًا لبيئات الغرف النظيفة والصناعات ذات المعايير الصارمة للجودة والمعايير البيئية مثل تصنيع الأجهزة الطبية وتطبيقات الفضاء.