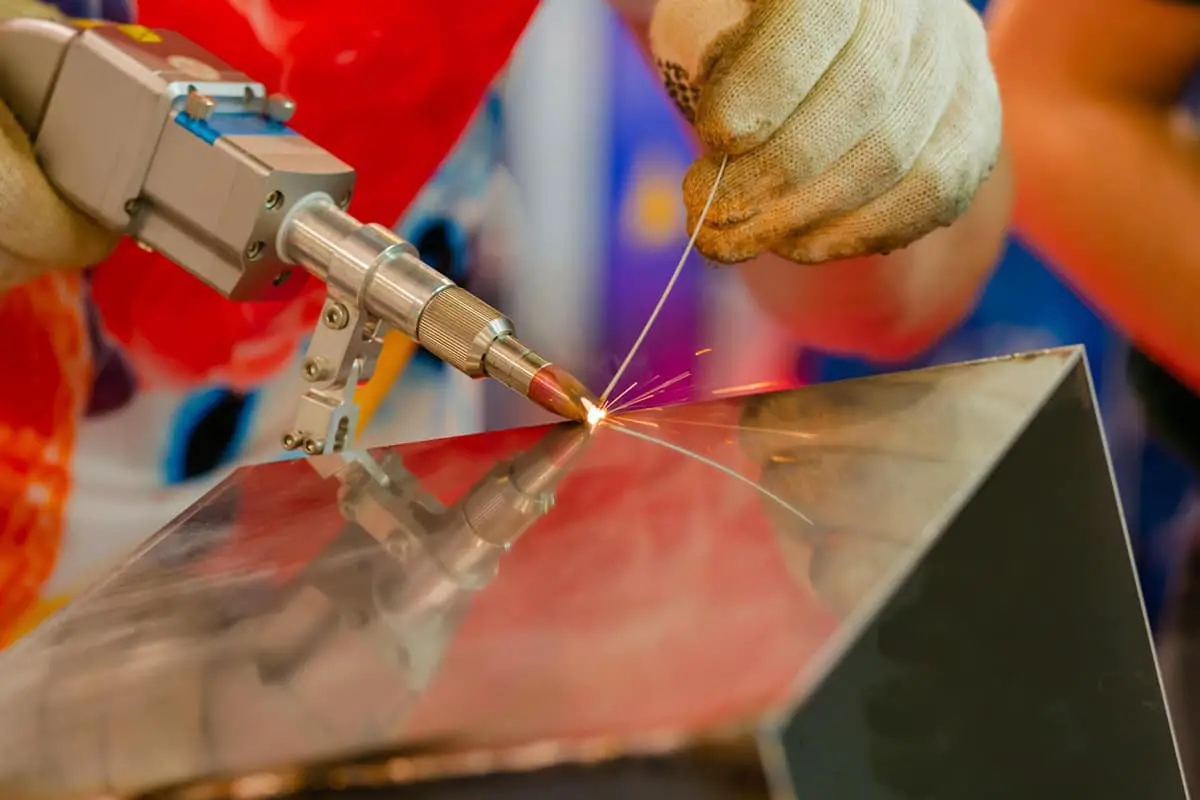
اللحام بالليزر هو تقنية ربط عالية الدقة تستخدم أشعة ليزر مركزة وعالية الطاقة لدمج المواد، وخاصة المعادن، بدقة وكفاءة استثنائية. تشتهر هذه العملية المتقدمة بإنتاج لحامات قوية مع تقليل التشوه الحراري في المناطق المجاورة. ويتوقف نجاح عمليات اللحام بالليزر على التحكم الدقيق في المعلمات الحرجة، وعلى رأسها سُمك قطعة العمل وسرعة اللحام. يتم تحسين هذه المتغيرات بدقة لضمان أقصى قدر من قوة اللحام وسلامته مع تعزيز الإنتاجية التشغيلية.
يعمل مخطط شامل لسماكة وسرعة اللحام بالليزر كأداة مرجعية لا غنى عنها لفنيي اللحام ومهندسي التصنيع. ويوفر بيانات مهمة لاختيار معلمات اللحام المثلى بناءً على خصائص المواد وتكوين الوصلة ومتطلبات التطبيق المحددة. من خلال الضبط الدقيق للمتغيرات الرئيسية مثل طاقة الليزر ووضع الحزمة (مستمر أو نابض) وموضع النقطة البؤرية وسرعة اللحام، يمكن للمشغلين التحكم بدقة في عمق اختراق اللحام وهندسة الحبة وجودة اللحام بشكل عام. تسهِّل الطبيعة الفريدة للحام بالليزر الحصول على نسبة عرض إلى عرض عالية (العمق إلى العرض) في شكل اللحام، مما يؤدي إلى لحام ضيق وعميق الاختراق مع الحد الأدنى من المنطقة المتأثرة بالحرارة (HAZ). تحافظ مدخلات الطاقة الموضعية هذه على الخواص الميكانيكية والبنية المجهرية للمادة الأساسية، مما يحافظ على السلامة الهيكلية للمكونات الملحومة.
وعلاوة على ذلك، غالباً ما تشتمل أنظمة اللحام بالليزر الحديثة على ميزات المراقبة في الوقت الحقيقي والتحكم التكيفي، مما يسمح بالتعديل الديناميكي لمعلمات اللحام للتعويض عن الاختلافات في خصائص المواد أو تركيب الوصلة. تتيح هذه القدرة المتقدمة، إلى جانب المرونة المتأصلة في اللحام بالليزر، تطبيق العملية بفعالية في مجموعة واسعة من الصناعات، بدءاً من صناعة السيارات والفضاء إلى الإلكترونيات وتصنيع الأجهزة الطبية.
مخطط قوة اللحام بالليزر وسماكته وسرعته
اللحام بالليزر هو تقنية ربط دقيقة توفر لحامات عالية السرعة وعالية الجودة لمختلف سماكات المعادن. إن العلاقة بين طاقة الليزر وسُمك المادة وسرعة اللحام أمر بالغ الأهمية لتحقيق أفضل النتائج. إليك مخطط شامل يوضح بالتفصيل هذه المعلمات للمواد الشائعة:
المواد | 1000 واط | 1500 واط | 2000 واتس |
---|---|---|---|
SUS (فولاذ مقاوم للصدأ) | 0.5 مم - 3 مم | 0.5 مم - 4 مم | 0.5 مم - 5 مم |
الحديد (Fe) | 0.5 مم - 3 مم | 0.5 مم - 4 مم | 0.5 مم - 5 مم |
الذكاء الاصطناعي (ألومنيوم) | 0.5 مم - 2 مم | 0.5 مم - 3 مم | 0.5 مم - 4 مم |
النحاس (النحاس الأصفر) | 0.5 مم - 3 مم | 0.5 مم - 6 مم | 0.5 مم - 8 مم |
صفيحة مجلفنة | 0.5 مم - 3 مم | 0.5 مم - 4 مم | 0.5 مم - 5 مم |
الفولاذ الكربوني | 0.5 مم - 3 مم | 0.5 مم - 4 مم | 0.5 مم - 5 مم |
الفولاذ المقاوم للصدأ
الفولاذ المقاوم للصدأ | طاقة الليزر (W) | الطاقة (W) | السرعة (ملم/ثانية) | التردد (كيلو هرتز) | التركيز (مم) |
---|---|---|---|---|---|
1 مم | 500 | 26 | 800 | 5 | 2 |
1.5 مم | 500 | 340 | 750 | 5 | 2 |
2 مم | 1000 | 600 | 800 | 5 | 2 |
2.5 مم | 1000 | 730 | 700 | 5 | 2 |
3 مم | 1000 | 860 | 720 | 5 | 3 |
ألومنيوم
ألومنيوم | طاقة الليزر (W) | الطاقة (W) | السرعة (ملم/ثانية) | التردد (كيلو هرتز) | التركيز (مم) |
---|---|---|---|---|---|
1 مم | 500 | 480 | 700 | 20 | 1 |
1.5 مم | 1000 | 560 | 800 | 20 | 1 |
2 مم | 1000 | 780 | 800 | 20 | 2 |
2.5 مم | 1000 | 920 | 800 | 20 | 2 |
3 مم | 1500 | 1150 | 800 | 20 | 2 |
نحاس
نحاس | طاقة الليزر (W) | الطاقة (W) | السرعة (ملم/ثانية) | التردد (كيلو هرتز) | التركيز (مم) |
---|---|---|---|---|---|
1 مم | 1000 | 900 | 600 | 30 | 3 |
1.5 مم | 1500 | 1100 | 600 | 30 | 4 |
2 مم | 1500 | 1350 | 500 | 30 | 4 |
2.5 مم | 2000 | 1600 | 500 | 30 | 5 |
3 مم | 2000 | 1850 | 500 | 30 | 6 |
النحاس
النحاس | طاقة الليزر (W) | الطاقة (W) | السرعة (ملم/ثانية) | التردد (كيلو هرتز) | التركيز (مم) |
---|---|---|---|---|---|
1 مم | 1000 | 650 | 600 | 30 | 0 |
1.5 مم | 1000 | 850 | 600 | 30 | 0 |
2 مم | 1500 | 1100 | 500 | 30 | 0 |
2.5 مم | 1500 | 1400 | 500 | 30 | 0 |
3 مم | 2000 | 1750 | 500 | 30 | 0 |
الفولاذ الطري
الفولاذ الطري | طاقة الليزر (W) | الطاقة (W) | السرعة (ملم/ثانية) | التردد (كيلو هرتز) | التركيز (مم) |
---|---|---|---|---|---|
1 مم | 500 | 300 | 500 | 20 | 0 |
1.5 مم | 500 | 370 | 500 | 20 | 0 |
2 مم | 500 | 480 | 600 | 20 | 1 |
2.5 مم | 1000 | 600 | 600 | 20 | 1 |
3 مم | 1000 | 760 | 700 | 20 | 2 |
صفيحة مجلفنة
صفيحة مجلفنة | طاقة الليزر (W) | الطاقة (W) | السرعة (ملم/ثانية) | التردد (كيلو هرتز) | التركيز (مم) |
---|---|---|---|---|---|
1 مم | 500 | 320 | 600 | 20 | 0 |
1.5 مم | 500 | 460 | 600 | 20 | 1 |
2 مم | 1000 | 600 | 500 | 20 | 2 |
2.5 مم | 1000 | 800 | 700 | 20 | 3 |
3 مم | 1000 | 960 | 650 | 20 | 3 |
أساسيات اللحام بالليزر
أحدث اللحام بالليزر ثورة في الصناعة تقنيات الانضمامتوفر دقة عالية السرعة والقدرة على ربط مجموعة متنوعة من المواد.
عملية اللحام بالليزر
اللحام بالليزر هو تقنية متقدمة وعالية الطاقة لدمج الأشعة تستخدم شعاع ليزر مركز لإنشاء وصلات دقيقة وعالية الجودة. تركز هذه العملية إشعاعاً كهرومغناطيسياً مكثفاً على مساحة صغيرة، يتراوح قطرها عادةً بين 0.2 و13 مم، مما يولد درجات حرارة موضعية تتجاوز 10000 درجة مئوية. يتم امتصاص طاقة الشعاع بسرعة بواسطة مواد قطعة العمل، مما يتسبب في ذوبان فوري، وعند التبريد، يتم دمج الوصلة.
الجوانب الرئيسية:
تركيز الشعاع: يتم تركيز شعاع الليزر بدقة باستخدام أنظمة بصرية لتحقيق كثافة طاقة تتراوح بين 1-10 ميجاوات/سم². ويتيح هذا التركيز إمكانية اللحام بالاختراق العميق أو اللحام بثقب المفتاح، مما يسمح بوصلات أحادية المرور في مواد يصل سمكها إلى 20 مم.
تفاعل المواد: تمتص المواد المختلفة طاقة الليزر بكفاءات متفاوتة. على سبيل المثال, المعادن مثل الفولاذ والتيتانيوم عادةً ما تكون معدلات الامتصاص 30-35% لليزر CO₂ وحتى 80% لليزر الليفي أو القرصي. تخلق الطاقة الممتصة ثقب مفتاح مملوء بالبخار، مما يعزز اقتران الطاقة الفعال والاختراق العميق.
السرعة والسُمك: يمكن أن تتراوح سرعات اللحام من 0.5 إلى 10 م/دقيقة، اعتمادًا على سُمك المادة وقوة الليزر. على سبيل المثال، يمكن لطاقة الليزر التي تبلغ 1 كيلوواط من طاقة الليزر أن تلحم عادةً فولاذًا بسمك 1 مم بسرعة 1 متر/دقيقة. يمكن لحام الصفائح الرقيقة، مثل أغلفة مفجر الوسائد الهوائية بسُمك 0.25 مم (0.01 بوصة) بسرعات تصل إلى 50 مم/ثانية (2 بوصة في الثانية) باستخدام ليزر Nd:YAG النبضي.
مزايا العملية:
- الحد الأدنى من المنطقة المتأثرة بالحرارة (HAZ)، مما يقلل من التشوه الحراري
- دقة عالية وإمكانية تكرار عالية، مثالية للأتمتة
- القدرة على لحام المواد غير المتشابهة والأشكال الهندسية المعقدة
- عملية عدم التلامس، مما يقضي على مشاكل تآكل القطب الكهربائي
التطبيقات: يستخدم اللحام بالليزر على نطاق واسع في صناعة السيارات والفضاء والإلكترونيات وصناعات الأجهزة الطبية. وهو مناسب بشكل خاص لربط المقاطع الرقيقة والمكونات الحساسة للحرارة والمواد ذات الموصلية الحرارية العالية مثل الألومنيوم والنحاس.
أنواع الليزر للحام
عند اختيار الليزر للحام، يعتمد الاختيار على خصائص المواد والدقة المطلوبة وكفاءة الإنتاج. إن فهم خصائص أنواع الليزر المختلفة أمر بالغ الأهمية لتحسين عمليات اللحام.
ليزر الموجة المستمرة (CW): ينبعث منها شعاع ليزر ثابت غير متقطع، وهو مثالي للحامات ذات الاختراق العميق ولحام اللحام عالي السرعة. وهي تتفوق في التطبيقات التي تتضمن مواد يصل سمكها إلى 0.25 بوصة (6.35 مم) أو أكثر. أجهزة الليزر CW فعالة بشكل خاص في الإنتاج بكميات كبيرة والمواد ذات التوصيل الحراري العالي.
الليزر النبضي: تبعث طاقة الليزر على دفعات متحكم فيها مما يسمح بالتحكم الدقيق في مدخلات الحرارة وعمق اللحام في المواد الرقيقة أو الحساسة للحرارة. يقلل هذا الإجراء النبضي من المنطقة المتأثرة بالحرارة (HAZ)، مما يجعلها مناسبة لتطبيقات اللحام الدقيق في صناعة الإلكترونيات والأجهزة الطبية.
أنواع الليزر الشائعة في اللحام الصناعي:
ليزر الألياف: يشتهر بتعدد استخداماته وكفاءة الطاقة وجودة الشعاع الفائقة. توفر ليزرات الألياف الليزرية كفاءة عالية في التوصيل الحائطي (حتى 50%) وهي بارعة بشكل خاص في اللحام الدقيق والتطبيقات عالية السرعة. وهي تتفوق في لحام المواد العاكسة مثل الألومنيوم والنحاس، والتي تمثل تحديًا لأنواع الليزر الأخرى.
ليزر ثاني أكسيد الكربون: على الرغم من أن ليزر ثاني أكسيد الكربون تقليدي في لحام المواد السميكة، إلا أنه يتم استبداله بشكل متزايد بليزر الألياف في العديد من التطبيقات. ومع ذلك، فإنها لا تزال تقدم مزايا في اللحام العميق الاختراق للمواد التي يزيد سمكها عن 0.5 بوصة (12.7 مم) وهي فعالة في المواد غير المعدنية مثل البلاستيك والمواد العضوية المركبة.
ليزر Nd:YAG: يوفر توازناً بين خصائص ليزر الألياف وليزر ثاني أكسيد الكربون. وهو مفيد بشكل خاص لـ اللحام الموضعي والتطبيقات التي تتطلب طاقة قصوى عالية. توفر أشعة الليزر القرصية الحديثة، وهي تطور لتقنية Nd:YAG، جودة وكفاءة شعاع محسّنة.
ليزر الصمام الثنائي: تكتسب ليزرات الصمام الثنائي الليزر، المعروفة بحجمها الصغير وكفاءتها العالية، شعبية في قطاع السيارات وقطاعات التصنيع الأخرى ذات الحجم الكبير. وهي توفر امتصاصًا ممتازًا للطاقة في المعادن، مما يجعلها مناسبة للحام سبائك الألومنيوم والفولاذ المجلفن.
يجب أن يأخذ اختيار نوع الليزر المناسب في الاعتبار عوامل مثل خصائص المواد وتصميم الوصلة وحجم الإنتاج ومتطلبات التطبيق المحددة لضمان الجودة المثلى للحام وكفاءة العملية.
الاعتبارات المادية
عند الانخراط في اللحام بالليزر، يجب على المرء أن يأخذ في الاعتبار طبيعة المواد التي يتم ربطها والسماكات المختلفة التي تمثلها. وتعتبر هذه الجوانب حاسمة في تحديد معلمات اللحام بالليزر.
المعادن والسبائك
يُعد التفاعل بين طاقة الليزر والمعادن والسبائك المختلفة عاملاً حاسماً في كفاءة وجودة عمليات اللحام بالليزر. تُظهر المواد المختلفة خواص بصرية وحرارية متميزة تؤثر بشكل كبير على خصائص امتصاص طاقة الليزر الخاصة بها، مما يؤثر بشكل مباشر على قابلية اللحام وسلامة الوصلة.
يُظهِر الفولاذ المقاوم للصدأ، بمزيجه الملائم من محتوى الكروم وطبقة أكسيد السطح، خصائص امتصاص ممتازة لطاقة الليزر عبر نطاق واسع من الأطوال الموجية. وهذا يجعله مناسبًا بشكل خاص لتطبيقات اللحام بالليزر، مما يسمح بإجراء عمليات لحام عالية السرعة ودقيقة ومنخفضة التشويه في صناعات مثل صناعة السيارات والفضاء.
وعلى العكس من ذلك، تمثل المواد عالية الانعكاسية مثل الألومنيوم والنحاس تحديات فريدة في اللحام بالليزر بسبب الموصلية الحرارية العالية ومعاملات الامتصاص المنخفضة. وللتغلب على هذه العقبات، يتم استخدام أنواع محددة من الليزر مثل ليزر الألياف عالية الطاقة أو الليزر الأخضر (الذي يعمل بأطوال موجية تبلغ حوالي 515 نانومتر). توفر هذه الليزرات كفاءة اقتران محسنة، مما يتيح اللحام الفعال لهذه المواد. بالإضافة إلى ذلك، يمكن استخدام تقنيات مثل تحضير السطح (مثل الكشط الميكانيكي أو الحفر الكيميائي) لتعزيز امتصاص طاقة الليزر.
يمكن أن يؤدي إدخال إضافات المواد إلى تغيير كبير في خصائص الامتصاص وعملية اللحام بشكل عام. فعلى سبيل المثال:
- يمكن أن تؤدي إضافة التيتانيوم إلى سبائك الألومنيوم إلى تحسين امتصاص الليزر واختراق اللحام.
- يمكن للعناصر الأرضية النادرة مثل الإربيوم أو الإيتربيوم في سبائك الصلب أن تعزز اقتران الطاقة في أطوال موجية ليزرية معينة.
- يؤثر محتوى السيليكون في سبائك الألومنيوم على السيولة ويمكن أن يؤثر على ديناميكيات حوض اللحام.
نطاق سماكة المواد
تؤثر سماكة المادة بشكل مباشر على طاقة الليزر المطلوبة:
- بالنسبة لـ ألواح رقيقة (أقل من 1.0 مم)، فإن طاقة الليزر المنخفضة ضرورية، وتختلف المعلمات بشكل كبير عن تلك المستخدمة للمواد السميكة.
- ألواح أكثر سمكاً تتطلب طاقة ليزر أعلى لتحقيق اختراق وقوة في اللحام. توجد علاقة تناسبية بين السُمك والطاقة:
سُمك المادة | طاقة الليزر التقريبية |
---|---|
< 1.0 مم | طاقة منخفضة |
1.0 مم - 5.0 مم | طاقة متوسطة |
> 5.0 مم | طاقة عالية |
من المهم تعديل معلمات الليزر، مثل عرض التأرجح و سرعة اللحاملمطابقة نطاق السُمك المحدد للحصول على أفضل النتائج.
معلمات اللحام بالليزر
يعد اختيار معلمات اللحام بالليزر أمرًا بالغ الأهمية لتحقيق وصلات عالية الجودة مع القوة والدقة المطلوبة. وتشمل هذه المعلمات طاقة الليزر وسرعة اللحام وسرعة اللحام وموضع التركيز وتدفق غاز التدريع، والتي يجب تحسينها جميعًا بعناية لتتناسب مع خصائص المواد المحددة وتكوين الوصلة والسماكة التي يتم لحامها.
إعدادات طاقة الليزر
تؤثر طاقة الليزر بشكل مباشر على عمق الاختراق وخصائص حبة اللحام. تُستخدم الإرشادات التالية كنقاط مرجعية أولية:
- المواد < 1.0 مم سماكة: 500-1500 وات
- المواد بسماكة 1.0-3.0 مم: 1500-3000 واط
- المواد > سمك 3.0 مم: 3000-6000 واط وما فوق
يعد الضبط الدقيق لإعدادات الطاقة أمرًا بالغ الأهمية لمنع الاحتراق في المواد الرقيقة أو الاختراق غير الكافي في المقاطع السميكة. على سبيل المثال، قد يتطلب لحام الفولاذ المقاوم للصدأ بقطر 1.5 مم حوالي 2000 واط للحصول على أفضل النتائج.
سرعة اللحام
يجب معايرة سرعة اللحام لضمان انصهار متسق وتقليل المنطقة المتأثرة بالحرارة (HAZ):
- نطاق السرعة النموذجي: 1-10 م/دقيقة، حسب المادة والسُمك
- مواد رقيقة (أقل من 1.0 مم): سرعات أعلى، 5-10 م/دقيقة
مواد أكثر سماكة (> 3.0 مم): سرعات أقل، 1-5 م/دقيقة
مثال: بالنسبة للفولاذ الطري عيار 2 مم، غالبًا ما تسفر سرعة 3-4 م/دقيقة عن نتائج جيدة عند إقرانها بإعدادات طاقة مناسبة.
موضع التركيز
يؤثر موضع التركيز البؤري بشكل كبير على هندسة حبة اللحام وجودة اللحام بشكل عام:
- تركيز السطح: مناسبة للمواد الرقيقة، وتنتج لحامات أوسع وأكثر سطحية
- تركيز عميق: مثالي للمواد السميكة، ويخلق لحامات ضيقة وعميقة الاختراق
بالنسبة للفولاذ الهيكلي مثل S235JR، يمكن أن يؤدي تعديل الموضع البؤري بمقدار ± 1 مم إلى تغيير نسبة العمق إلى العرض بنسبة تصل إلى 20%، مما يؤثر على الخواص الميكانيكية والمظهر.
غاز التدريع
يعد الاختيار السليم لغاز التدريع ومعدل التدفق المناسبين ضروريين لحماية حوض اللحام وتحقيق الخصائص المعدنية المطلوبة:
- الأرجون: شائع الاستخدام لمعظم المعادن، معدل التدفق 10-20 لتر/دقيقة
- الهيليوم: يوفر تغلغلًا أعمق، وهو مفيد للمواد العاكسة مثل الألومنيوم، معدل التدفق 20-30 لتر/دقيقة
- النيتروجين: مناسب للفولاذ الأوستنيتي المقاوم للصدأ، معدل التدفق 10-20 لتر/دقيقة
ومن خلال التحسين الدقيق لهذه المعلمات من خلال الاختبار والتحليل المنهجيين، يمكن أن ينتج اللحام بالليزر وصلات عالية القوة والدقة مع الحد الأدنى من التشويه الحراري وضيق منطقة الخطر الحرجة. يمكن لأنظمة مراقبة العمليات المتقدمة وأنظمة التحكم أن تعزز جودة اللحام وقابلية التكرار في التطبيقات الصناعية.