Proses pemotongan logam mengacu pada proses di mana pahat memotong lapisan logam berlebih dari benda kerja melalui gerakan pemotongan, membentuk serpihan dan permukaan mesin. Serangkaian fenomena terjadi selama proses ini, seperti pembentukan chip, pembangkitan gaya pemotongan, panas pemotongan dan suhu pemotongan, serta keausan pahat.
I. Koefisien Deformasi, Chip, dan Tepi yang Dibangun
1. Koefisien Deformasi dan Jenis Chip
(1) Koefisien Deformasi
Logam pada lapisan pemotongan membentuk serpihan setelah pemotongan, dengan panjang yang memendek dan ketebalan yang bertambah dibandingkan dengan logam pada lapisan pemotongan, yang mengindikasikan bahwa logam pada lapisan pemotongan telah berubah bentuk, seperti yang ditunjukkan pada Gambar 1.
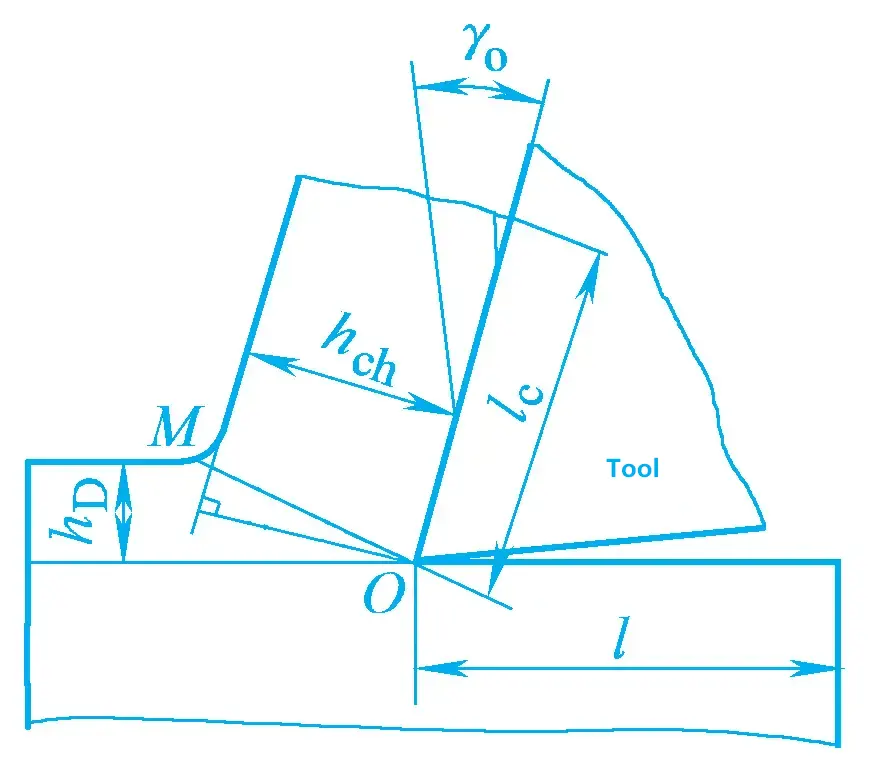
Derajat deformasi dapat diukur secara kasar dengan koefisien deformasi ξ. Koefisien deformasi sama dengan rasio ketebalan chip terhadap ketebalan logam pada lapisan pemotongan, dan juga sama dengan rasio panjang logam pada lapisan pemotongan terhadap panjang chip.
ξ = l/lc=hch/hD>1
Dapat dilihat bahwa semakin besar nilai koefisien deformasi, semakin parah deformasi pemotongan.
(2) Jenis Keripik
Menurut bentuk keripik yang berbeda-beda, biasanya keripik dibagi ke dalam empat jenis berikut ini:
1) Keripik Pita
Bentuknya seperti pita, dengan permukaan bawah yang halus dan tidak ada retakan yang kentara di bagian belakang, menunjukkan bentuk yang agak bergerigi. Jenis chip ini sering dibentuk ketika mengerjakan logam plastik, seperti baja non-paduan, baja paduan, tembaga, aluminium, dan bahan lainnya.
2) Keripik Tersegmentasi
Permukaan bawah chip relatif halus, dan permukaan belakangnya retak secara lokal menjadi bintil-bintil. Jenis chip ini mudah diperoleh ketika memotong kuningan atau memotong baja pada kecepatan rendah.
3) Keripik granular
Chip pecah menjadi butiran yang seragam di sepanjang arah ketebalan. Jenis chip ini dapat diperoleh ketika memotong timah atau memotong baja pada kecepatan yang sangat rendah.
4) Keripik yang terfragmentasi
Ketika memotong logam yang rapuh seperti besi tuang dan perunggu, lapisan pemotongan hampir tidak mengalami deformasi plastis dan patah secara rapuh, sehingga menghasilkan chip berbutir halus yang tidak beraturan. Tabel 1 menunjukkan faktor-faktor yang memengaruhi morfologi chip dan dampaknya terhadap gaya potong.
Tabel 1 Faktor-faktor yang memengaruhi morfologi chip dan dampaknya terhadap gaya potong
Klasifikasi morfologi chip | Keripik granular | Keripik nodular | Keripik pita | |
Diagram skematik morfologi chip | ![]() | ![]() | ![]() | |
Faktor-faktor yang memengaruhi morfologi chip dan transformasi timbal baliknya | 1. Sudut penggaruk alat 2. Laju pemakanan (ketebalan pemotongan) 3. Kecepatan potong | Kecil ↔ Besar Besar (tebal) ↔ Kecil (tipis) Rendah ↔ Tinggi | ||
Dampak morfologi chip pada proses pemotongan | 1. Fluktuasi gaya pemotongan 2. Stabilitas proses pemotongan 3. Kekasaran permukaan nilai permukaan mesin 4. Efek pemecahan chip | Besar ↔ Kecil Buruk ↔ Baik Besar ↔ Kecil Baik ↔ Buruk |
2. Tepi yang dibangun
(1) Konsep tepi yang dibangun
Dalam kisaran tertentu dari kecepatan potongSaat pemesinan baja, logam non-besi, dan material plastik lainnya, sepotong logam dengan kekerasan tinggi muncul pada permukaan rake di dekat mata potong. Logam ini mengelilingi mata potong dan menutupi sebagian permukaan rake, yang berfungsi sebagai pengganti mata potong untuk melakukan operasi pemotongan pada benda kerja. Bagian logam ini, dengan kekerasan sekitar 2 sampai 3 kali lipat dari material benda kerja, disebut built-up edge, seperti yang ditunjukkan pada Gambar 2.
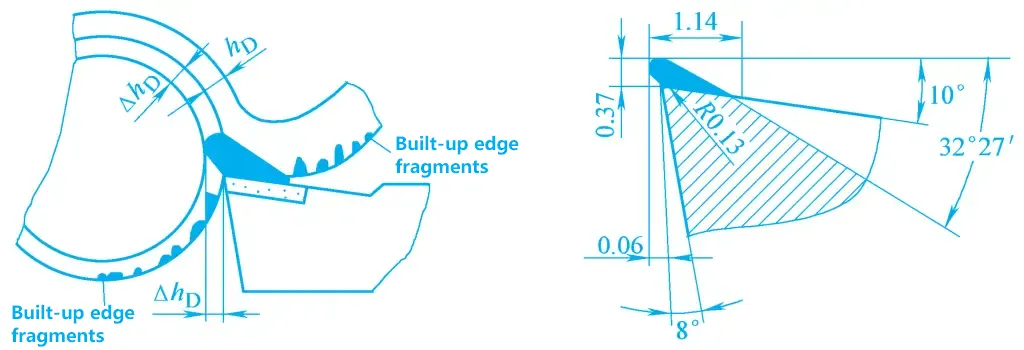
(2) Pembentukan dan Pertumbuhan Tepi Terbangun
Ada banyak penjelasan untuk pembentukan built-up edge, yang secara umum diyakini disebabkan oleh perlekatan chip pada rake face. Dalam kondisi pemesinan tertentu, saat suhu dan tekanan antara chip dan permukaan rake meningkat, gesekan juga meningkat, menyebabkan laju aliran lapisan deformasi pada chip di dekat permukaan rake melambat, sehingga menghasilkan fenomena "stagnasi". Semakin dekat lapisan logam ke permukaan penggaruk, semakin rendah laju alirannya.
Ketika suhu dan tekanan meningkat sampai batas tertentu, logam bawah di lapisan stagnasi akan melekat pada permukaan penggaruk. Ketika tegangan geser pada logam dasar chip melebihi batas kekuatan luluh geser logam, laju aliran logam dasar menjadi nol dan terpotong, melekat pada permukaan penggaruk.
Lapisan perekat ini mengalami deformasi plastis yang parah, sehingga meningkatkan kekerasannya. Selama pemotongan yang berlanjut, lapisan perekat yang keras menggunting lapisan logam lunak, menumpuk lapis demi lapis, dan secara bertahap bertambah tinggi, membentuk tepi yang terbentuk. Oleh karena itu, adhesi dan pengerasan kerja merupakan kondisi yang diperlukan untuk pertumbuhan built-up edge.
(3) Pelepasan dan Hilangnya Tepi yang Dibangun
Tepi built-up yang tumbuh dapat mengalami fraktur atau pelepasan lokal akibat kekuatan atau getaran eksternal. Apabila suhu dan tekanannya sesuai, built-up edge mulai terbentuk dan tumbuh lagi. Pembentukan, pertumbuhan, dan pelepasan built-up edge adalah proses dinamis yang periodik.
Eksperimen menunjukkan bahwa faktor yang menentukan pembentukan built-up edge adalah suhu pemotongan. Pada suhu pemotongan yang sangat rendah dan sangat tinggi, built-up edge tidak mudah terbentuk. Pada kisaran suhu sedang, misalnya, ketika memotong baja karbon sedang pada suhu pemotongan 300-380 ° C, terjadi adhesi yang parah, dan built-up edge mencapai ketinggian yang signifikan. Selain itu, faktor-faktor seperti tekanan antara pahat dan chip, kekasaran permukaan rake, dan kekuatan rekat juga memengaruhi ukuran built-up edge.
(4) Keuntungan dan Kerugian dari Tepi yang Dibangun
Keuntungan dari built-up edge dalam pemotongan adalah bahwa ia menutupi sebagian permukaan rake dan mata potong, menggantikan mata potong dalam pekerjaan, sehingga melindungi mata potong dan meningkatkan sudut kerja rake yang sebenarnya dari pahat.
Kerugiannya adalah bahwa tepi yang terpasang meningkatkan dimensi lateral alat, menyebabkan pemotongan yang berlebihan. Ketika built-up edge terlepas, maka akan membawa partikel logam dari rake face, sehingga mempercepat keausan rake face. Proses pembentukan built-up edge menyebabkan fluktuasi gaya potong, sehingga mempengaruhi akurasi pemesinan dan kekasaran permukaan benda kerja. Oleh karena itu, built-up edge bermanfaat untuk pemesinan kasar tetapi merugikan untuk pemesinan akhir.
(5) Langkah-langkah untuk Mengurangi atau Menghindari Tepi yang Terbangun
- Hindari pemotongan pada kecepatan yang menghasilkan built-up edge (lihat Gambar 3), yaitu, gunakan pemotongan kecepatan rendah atau kecepatan tinggi. Namun demikian, pemesinan kecepatan rendah memiliki efisiensi yang rendah, sehingga pemotongan kecepatan tinggi sering digunakan.
- Gunakan alat dengan sudut penggaruk yang besar untuk mengurangi tekanan kontak antara alat dan chip.
- Mengurangi plastisitas material benda kerja, meningkatkan kekerasan benda kerja, dan mengurangi kecenderungan pengerasan kerja.
- Langkah-langkah lain termasuk mengurangi laju pengumpanan, mengurangi kekasaran permukaan permukaan penggaruk, dan menggunakan memotong cairan dengan tepat.
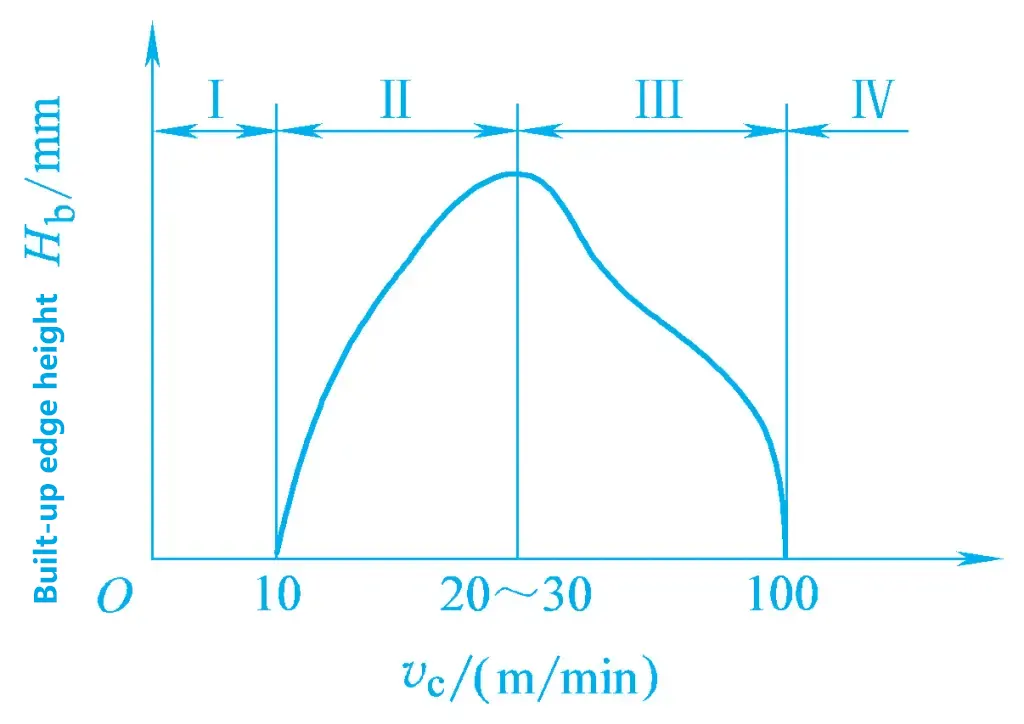
II. Gaya Pemotongan
Gaya interaksi antara pahat dan benda kerja selama pemotongan disebut gaya potong, dan pekerjaan yang dilakukan oleh gaya potong adalah pekerjaan pemotongan.
1. 1. Sumber Gaya Pemotongan
Sumber gaya pemotongan berasal dari dua aspek: resistensi deformasi yang dihasilkan oleh deformasi logam pada lapisan pemotongan dan resistensi gesekan yang dihasilkan oleh gesekan antara chip, benda kerja, dan pahat.
2. Penguraian Gaya Pemotongan
Besar dan arah gaya pemotongan tidak mudah diukur secara langsung. Untuk memenuhi kebutuhan desain dan analisis proses, gaya pemotongan pada umumnya diuraikan, dan akan sangat berarti untuk mempelajari komponen-komponennya pada arah tertentu.
Seperti yang ditunjukkan pada Gambar 4 dan 5, gaya potong F dapat diuraikan menjadi tiga komponen yang saling tegak lurus F c , F p dan F f .
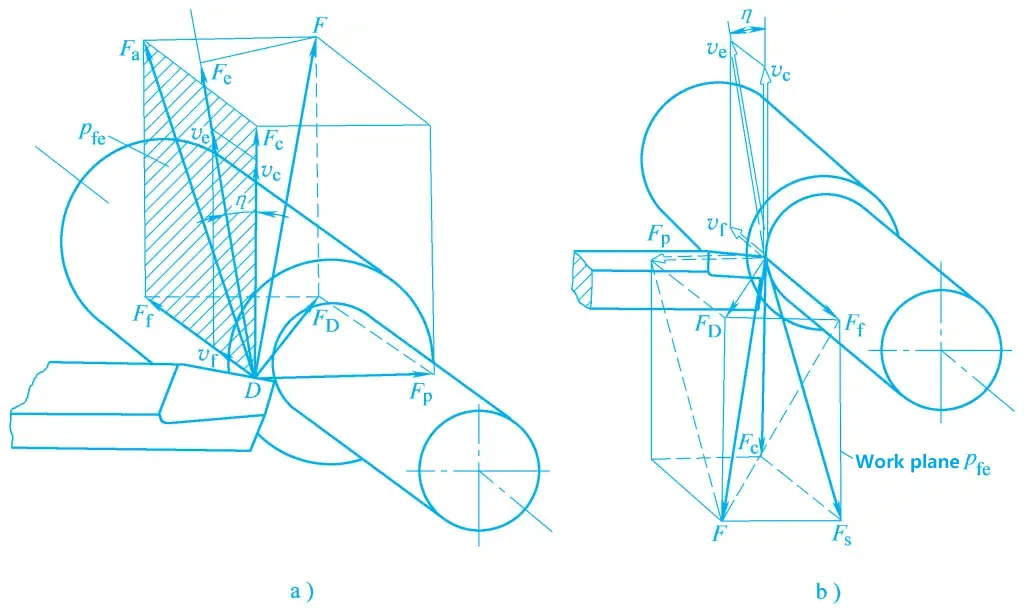
a) Penguraian gaya yang diberikan oleh pahat pada benda kerja
b) Penguraian gaya yang diberikan oleh benda kerja pada alat
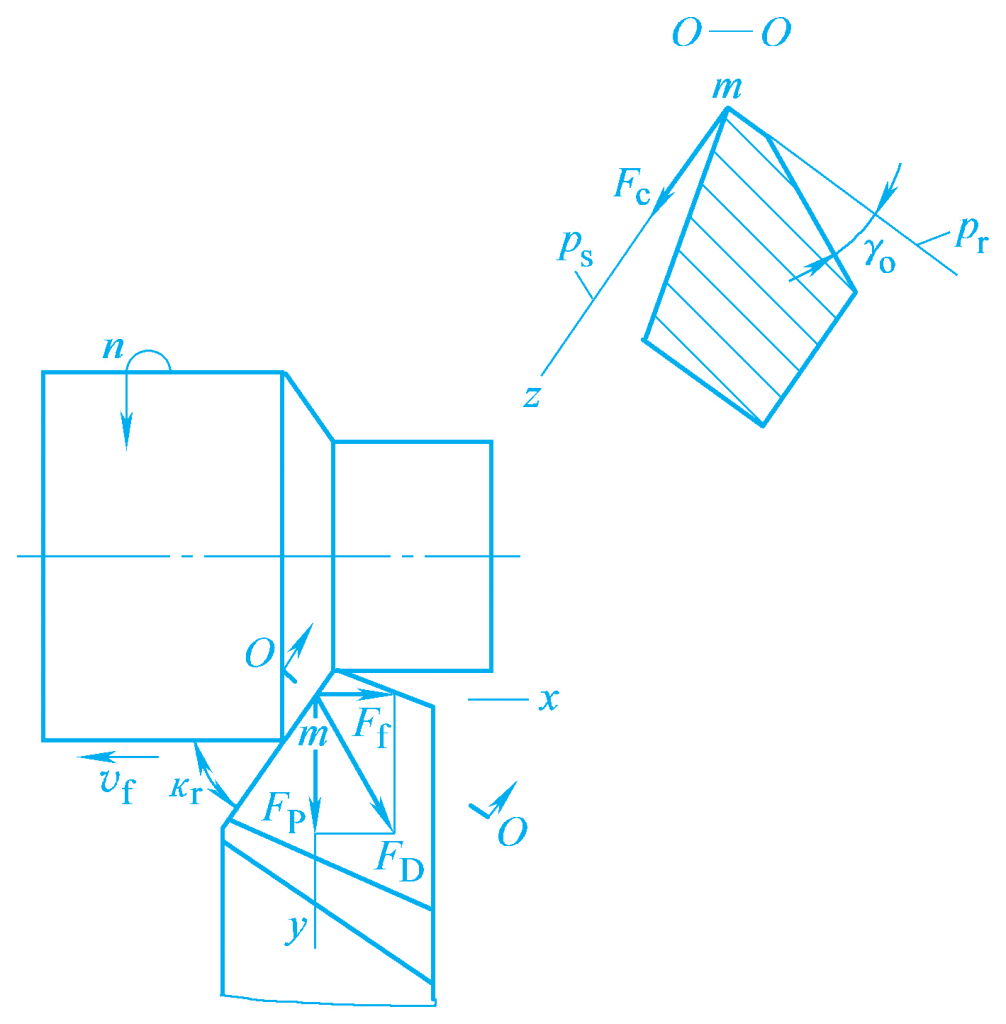
(1) Gaya Pemotongan Utama Fc
Komponen gaya pemotongan pada arah gerakan utama.
(2) Gaya punggung Fp
Komponen gaya pemotongan pada arah yang tegak lurus terhadap bidang kerja yang diasumsikan. Bidang kerja yang diasumsikan ditentukan oleh titik yang dipilih pada mata potong, tegak lurus terhadap bidang dasar, dan sejajar dengan arah gerak umpan yang diasumsikan.
(3) Gaya umpan Ff
Komponen gaya pemotongan pada arah gerakan umpan.
Gaya pemotongan F dapat diuraikan menjadi Fc dan FD dan FD dapat diuraikan menjadi Fp dan Ff . Hubungan mereka adalah:

Signifikansi aktual dari masing-masing gaya komponen selama pembubutan adalah sebagai berikut: Gaya potong utama adalah komponen terbesar, mengkonsumsi sekitar 95% dari total daya potong. Gaya ini bekerja pada arah gerak utama dan merupakan dasar utama untuk menghitung kekuatan mekanisme gerak utama alat mesin, kekuatan dudukan pahat dan sisipan, mendesain perlengkapan alat mesin, dan memilih parameter pemotongan.
Gaya belakang tidak mengkonsumsi daya selama pembubutan eksternal. Gaya ini bekerja pada arah di mana kekakuan benda kerja dan alat mesin adalah yang terlemah, sehingga dengan mudah menyebabkan deformasi benda kerja pada bidang horizontal, mempengaruhi akurasi pemesinan, dan dengan mudah menyebabkan getaran. Ini adalah dasar utama untuk memverifikasi kekakuan alat mesin.
Gaya umpan bekerja pada mekanisme gerakan umpan alat mesin, mengkonsumsi sekitar 5% dari total daya. Ini adalah dasar utama untuk memverifikasi kekuatan mekanisme pengumpanan alat mesin.
3. Perhitungan gaya pemotongan
Dalam produksi aktual, rumus eksponensial sering digunakan untuk menghitung gaya pemotongan. Rumus perhitungan spesifik dapat ditemukan dalam materi referensi yang relevan.
4. Faktor-faktor yang mempengaruhi gaya pemotongan
Semakin tinggi kekuatan dan kekerasan material benda kerja, semakin besar gaya pemotongannya. Ketika kedalaman potong digandakan, gaya potong meningkat sekitar satu kali lipat; ketika laju pemakanan digandakan, gaya potong meningkat 70% menjadi 80%. Meningkatkan sudut rake mengurangi gaya potong; sudut mata potong utama Kr mempengaruhi ketiga komponen gaya Fc , Fp dan Ff tetapi memiliki dampak yang lebih besar pada Fp dan Ff .
Menurut rumus sebelumnya, meningkatkan sudut mata potong utama akan mengurangi gaya punggung dan meningkatkan gaya umpan. Dampak dari Kr pada Fc dapat dibagi menjadi dua situasi: ketika Kr bervariasi dalam kisaran 30° hingga 60°, karena Kr meningkat, Fc menurun; ketika Kr bervariasi dalam kisaran 75° hingga 90°, karena Kr meningkat, Fc meningkat.
5. Daya potong
Daya pemotongan mengacu ke daya yang dikonsumsi di zona pemotongan selama pemotongan. Ini adalah jumlah daya yang dikonsumsi oleh gaya pemotongan utama Fc dan gaya umpan Ff . Karena daya yang dikonsumsi oleh gaya umpan Ff sangat kecil, biasanya diabaikan. Oleh karena itu, ketika Fc dan vc diketahui, maka daya pemotongan Pc adalah
Pc = (Fc vc × 10-3 ) / 60
Di mana
- Pc - Daya pemotongan, satuan: kW;
- Fc - Gaya pemotongan utama, unit: N;
- vc – Kecepatan potong, satuan: m/menit.
Daya yang diperlukan dari motor alat mesin PE seharusnya
PE = Pc / η
Dalam rumus di atas, η adalah efisiensi transmisi alat berat, umumnya diambil sebagai η = 0,75 hingga 0,85. Rumus ini merupakan dasar utama untuk memverifikasi dan memilih motor alat mesin.
III. Panas pemotongan dan suhu pemotongan
Fenomena fisik penting lainnya yang terjadi selama pemotongan adalah panas pemotongan dan suhu pemotongan. Panas pemotongan menyebabkan suhu pemotongan meningkat, sehingga mengakibatkan deformasi termal pada benda kerja dan alat mesin, yang mempengaruhi akurasi pemesinan dan kualitas permukaan benda kerja. Temperatur pemotongan adalah faktor utama yang mempengaruhi umur pahat. Oleh karena itu, mempelajari panas pemotongan dan temperatur pemotongan memiliki signifikansi praktis yang penting.
1. Memotong panas
Pekerjaan yang dilakukan oleh deformasi elastis dan plastis logam pada lapisan pemotongan di bawah aksi pahat, dan gesekan antara chip dan permukaan penggaruk, serta antara permukaan mesin benda kerja dan permukaan sisi, semuanya diubah menjadi panas pemotongan. Panas pemotongan dihantarkan oleh chip, benda kerja, pahat, dan media di sekitarnya.
Selama pembubutan, sekitar 50% hingga 86% panas pemotongan dihantarkan oleh chip, 10% hingga 40% dihantarkan ke benda kerja, 3% hingga 9% dihantarkan ke pahat, dan 1% dihantarkan ke media di sekitarnya; selama pengeboran, sekitar 28% panas pemotongan dihantarkan oleh chip, 15% dihantarkan ke mata bor, 52% dihantarkan ke benda kerja, dan 5% dihantarkan ke media di sekitarnya.
Meningkatkan kecepatan potong dapat meningkatkan proporsi panas yang terbawa oleh chip, mengurangi panas yang dihantarkan ke benda kerja, dan bahkan lebih sedikit panas yang dihantarkan ke pahat. Oleh karena itu, meskipun suhu pemotongan di zona pemotongan sangat tinggi selama pemotongan kecepatan tinggi, namun tool masih dapat bekerja secara normal.
2. Suhu pemotongan
Temperatur pemotongan umumnya mengacu pada temperatur rata-rata pada area kontak antara chip dan permukaan rake tool. Tingkat suhu pemotongan tergantung pada jumlah panas yang dihasilkan di lokasi tersebut dan laju pembuangan panas. Melalui perhitungan dan pengukuran, diketahui bahwa temperatur rata-rata paling tinggi terdapat pada chip. Temperatur tertinggi pada permukaan rake tidak berada pada mata potong atau mata potong, tetapi pada jarak yang kecil dari mata potong.
3. Faktor-faktor yang mempengaruhi suhu pemotongan
Kecepatan potong memiliki dampak terbesar pada suhu pemotongan; seiring dengan meningkatnya kecepatan potong, maka suhu pemotongan juga meningkat. Laju pemakanan memiliki dampak yang lebih kecil, dan kedalaman pemotongan memiliki dampak yang lebih kecil lagi. Meningkatkan sudut rake akan mengurangi suhu pemotongan, tetapi sudut rake tidak boleh terlalu besar; jika terlalu besar, suhu pemotongan malah akan meningkat. Meningkatkan sudut defleksi utama akan meningkatkan suhu pemotongan.
IV. Keausan Perkakas dan Umur Perkakas
Selama proses pemotongan, alat ini beroperasi di bawah suhu tinggi dan tekanan tinggi. Oleh karena itu, pahat tidak hanya memotong serpihan, tetapi juga menjadi aus. Apabila keausan pahat mencapai tingkat tertentu, kekasaran permukaan benda kerja meningkat, bentuk dan warna serpihan berubah, dan suara yang berat dipancarkan selama proses pemotongan, disertai getaran. Pada titik ini, pahat harus diasah kembali atau diganti dengan yang baru.
1. Keausan Alat
(1) Bentuk Keausan Alat
Keausan pahat mengacu pada fenomena di mana material pahat terkikis oleh serpihan atau benda kerja pada permukaan kontak antara pahat dan benda kerja atau serpihan. Jenis keausan ini disebut keausan normal. Jika ujung pahat patah atau retak karena benturan, getaran, efek termal, dll., maka disebut keausan abnormal. Bentuk keausan normal pahat adalah sebagai berikut:
1) Keausan Sayap
Saat memotong bahan plastik, jika ketebalan pemotongan besar, pola keausan berbentuk bulan sabit akan muncul di belakang mata potong pada permukaan penggaruk pahat (lihat Gambar 6a). Area bulan sabit adalah tempat dengan suhu pemotongan tertinggi. Saat keausan meningkat, area bulan sabit secara bertahap akan semakin dalam dan melebar, dan saat mendekati mata potong, mata potong bisa tiba-tiba putus. Jumlah keausan pada permukaan rake ditunjukkan oleh lebar KB dan kedalaman KT dari area bulan sabit.
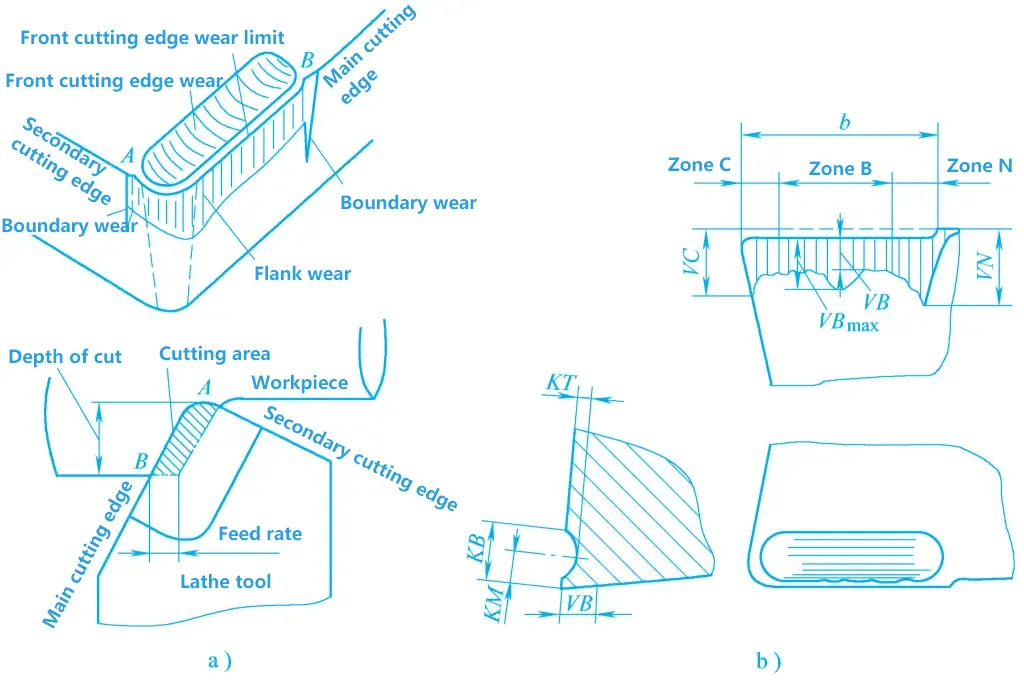
a) Keausan Wajah Sisi dan Rake Face
b) Representasi Jumlah Keausan
2) Keausan Sayap
Hal ini mengacu pada keausan yang terutama terjadi pada sisi muka. Setelah keausan flank, terbentuklah sisi kecil dengan sudut jarak bebas nol derajat. Saat memotong logam plastik dengan ketebalan pemotongan yang kecil atau logam yang rapuh, karena gesekan yang lebih sedikit dan suhu yang lebih rendah pada permukaan rake, keausan terutama terjadi pada permukaan sisi. Jumlah keausan sisi tidak merata.
Seperti yang ditunjukkan pada Gambar 6b, pada ujung pahat (area C), kondisi pembuangan panas dan kekuatannya buruk, sehingga menghasilkan keausan yang lebih besar, yang ditunjukkan oleh VC. Di dekat mata potong yang dekat dengan permukaan benda kerja (area N), karena kulit blank yang keras atau pengerasan kerja, keausan juga lebih besar, yang ditunjukkan oleh VN. Hanya di bagian tengah mata potong (area B) keausan relatif seragam, ditunjukkan dengan VB, dengan jumlah keausan maksimum yang ditunjukkan dengan VBmaks .
3) Memakai Wajah Sisi dan Rake secara bersamaan
Saat memotong logam plastik dengan ketebalan pemotongan sedang, keausan secara simultan pada rake face dan flank face sering terjadi.
Keausan pahat terutama terjadi karena gesekan mekanis dan efek termokimia di bawah suhu dan tekanan tinggi. Umumnya, semakin tinggi suhu pemotongan, semakin cepat keausan pahat.
(2) Proses Keausan Alat
Dalam kondisi keausan normal, jumlah keausan pahat secara bertahap meningkat seiring dengan waktu pemotongan. Mengambil keausan flank sebagai contoh, proses keausan tipikal secara kasar dibagi menjadi tiga tahap seperti yang ditunjukkan pada Gambar 7.
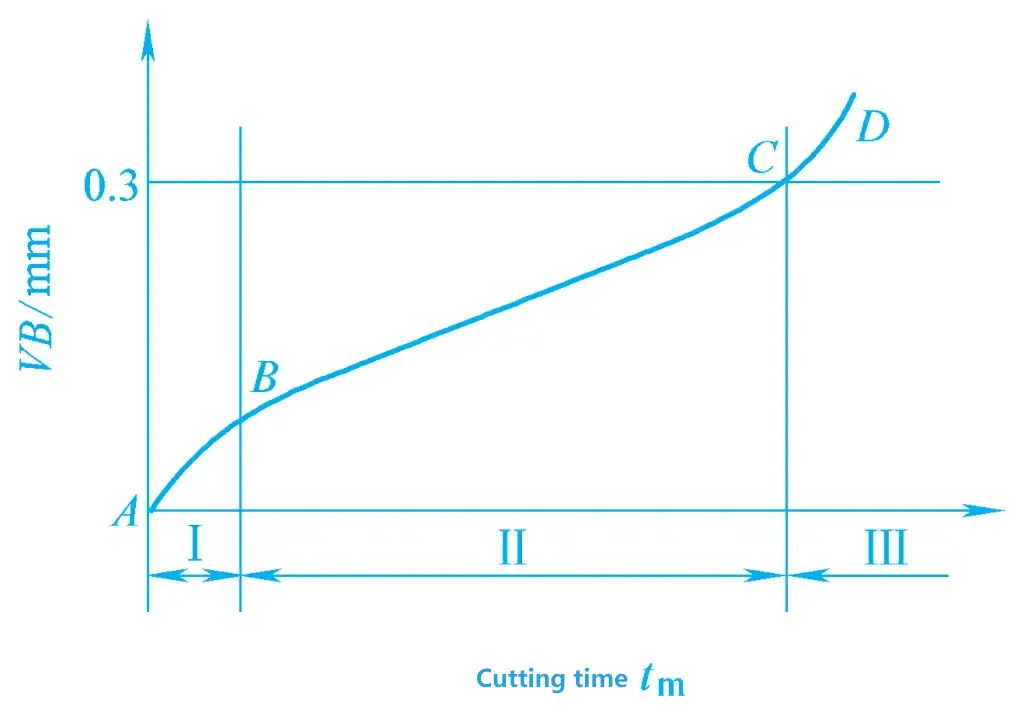
1) Tahap Keausan Awal
(Tahap AB pada gambar) Keausan relatif cepat dalam waktu singkat setelah pahat mulai memotong. Hal ini disebabkan karena kekasaran permukaan permukaan pahat yang tinggi setelah penggerindaan, dan struktur lapisan permukaan tidak tahan aus.
2) Tahap Keausan Normal
(Tahap BC pada gambar) Seiring dengan bertambahnya waktu pemotongan, jumlah keausan meningkat pada kecepatan yang relatif seragam. Hal ini karena lapisan permukaan pahat yang tidak rata dan tidak tahan aus telah terkikis habis, sehingga membentuk daerah yang stabil. Oleh karena itu, kecepatan keausan lebih lambat dari sebelumnya, tetapi jumlah keausan secara bertahap meningkat seiring dengan waktu pemotongan. Tahap ini juga merupakan tahap kerja alat yang efektif.
3) Tahap Keausan Cepat
(Tahap CD pada gambar) Ketika jumlah keausan pahat mencapai nilai tertentu, keausan akan bertambah cepat, dan pahat akan mengalami kegagalan. Hal ini disebabkan oleh waktu pemotongan yang lama, kondisi kontak yang memburuk antara pahat dan benda kerja, gesekan yang berlebihan, peningkatan suhu pemotongan yang tajam, serta berkurangnya kekuatan dan kekerasan pahat. Dalam produksi, untuk menggunakan alat secara wajar dan memastikan kualitas pemrosesan, mata potong harus diasah kembali atau alat diganti sebelum tahap ini tiba.
(3) Standar Tumpul Alat (Batas Keausan)
Standar tumpulnya pahat mengacu pada nilai keausan yang ditentukan di mana pahat harus diasah ulang atau mata potongnya diganti (indexable insert). Jika tidak, maka akan mempengaruhi kualitas pemrosesan, meningkatkan keausan pahat dan roda gerinda selama pengasahan ulang, mengurangi pemanfaatan pahat, dan menambah waktu penggerindaan.
Standar nasional GB/T 16461-2016 menetapkan standar tumpul untuk perkakas baja berkecepatan tinggi, perkakas karbida, dan perkakas keramik sebagai berikut:
- Ketika pita keausan flank di area B berupa keausan normal, lebar rata-rata pita keausan flank VB = 0,3 mm.
- Ketika pita keausan pada area flank face B tidak berupa keausan normal, seperti goresan, terkelupas, dll., maka lebar maksimum pita keausan pada flank face VB maks = 0,6 mm.
- Kedalaman kawah KT = 0,06 + 0,3f.
Selain itu, selama finishing, kriteria tumpulnya pahat sering kali adalah apakah jumlah keausan pahat memengaruhi kekasaran permukaan dan akurasi dimensi.
2. Masa Pakai Alat
(1) Konsep masa pakai alat
Umur pahat T didefinisikan sebagai total waktu pemotongan dari awal pemotongan dengan pahat yang baru diasah hingga mencapai batas keausan pahat, dilambangkan sebagai T, dengan satuan dalam menit.
(2) Faktor-faktor yang mempengaruhi umur alat
1) Dampak kecepatan potong terhadap umur pahat
Meningkatkan kecepatan potong vc akan meningkatkan suhu pemotongan, mempercepat keausan pahat, dan dengan demikian mengurangi umur pahat T. Di antara tiga elemen parameter pemotongan, v c memiliki dampak terbesar pada T.
2) Dampak laju pengumpanan dan kedalaman pemotongan
Meningkatkan f dan ap keduanya mengurangi umur pahat T, tetapi meningkatkan f meningkatkan suhu pemotongan secara lebih signifikan, sehingga memiliki dampak yang lebih besar pada T; sedangkan meningkatkan αp meningkatkan suhu pemotongan lebih sedikit, sehingga memiliki dampak yang lebih kecil pada T.
3) Parameter geometri alat
Pemilihan parameter geometri pahat yang wajar dapat memperpanjang umur pahat. Dalam produksi, umur pahat sering digunakan sebagai ukuran apakah parameter geometri pahat sudah masuk akal.
Meningkatkan sudut penggaruk γo mengurangi suhu pemotongan dan meningkatkan umur pahat, tetapi jika sudut rake terlalu besar, kekuatan pahat berkurang dan pembuangan panas memburuk, yang dapat mengurangi umur pahat. Oleh karena itu, ada nilai optimal untuk sudut rake, yang dapat ditentukan melalui eksperimen pemotongan.
Mengurangi sudut mata potong utama Kr , sudut ujung tombak sekunder kr dan meningkatkan radius hidung pahat rε dapat meningkatkan kemampuan perpindahan panas pahat dan mengurangi suhu pemotongan, yang keduanya dapat memperpanjang usia pakai pahat.
4) Bahan benda kerja
Semakin tinggi kekuatan, kekerasan, dan ketangguhan material benda kerja, dan semakin rendah perpanjangannya, maka semakin tinggi pula temperatur pemotongan selama pemotongan, dan semakin pendek usia pakai pahat.
5) Bahan alat
Material perkakas merupakan faktor penting yang mempengaruhi umur perkakas. Pemilihan material perkakas yang tepat, penggunaan material perkakas yang dilapisi, dan penggunaan material perkakas yang baru merupakan cara yang efektif untuk memperpanjang usia pakai perkakas.