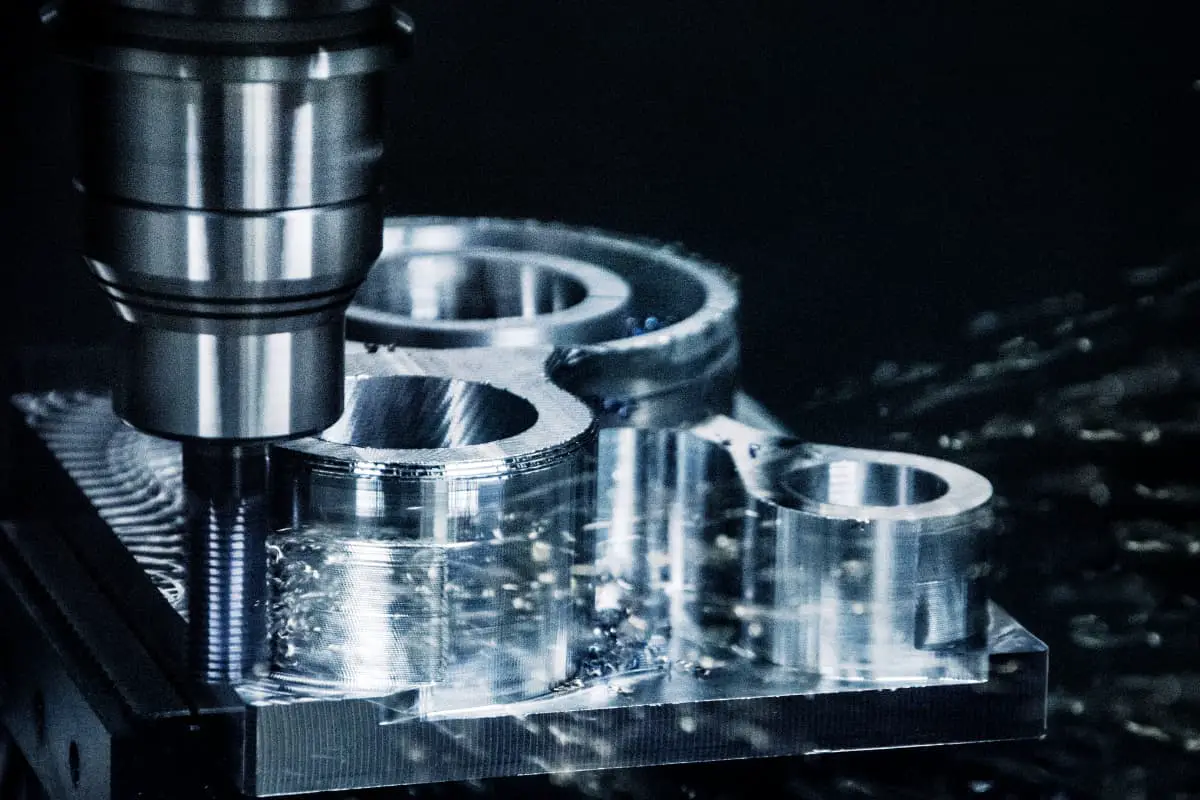
Saldatura per fusione
La saldatura per fusione è un metodo di saldatura in cui il metallo di base nel punto di saldatura viene fuso (spesso con l'aggiunta di metallo d'apporto) senza applicare pressione, formando un cordone di saldatura.
L'essenza della saldatura per fusione è un processo di fusione e fusione su piccola scala, che comporta la fusione e la cristallizzazione del metallo. Quando la temperatura raggiunge il punto di fusione del materiale, il metallo di base e il filo di saldatura si fondono per formare un bagno fuso, che si cristallizza in cristalli colonnari. Il bagno fuso esiste per breve tempo, ha una temperatura elevata, si raffredda rapidamente e, dopo la cristallizzazione, forma facilmente cristalli colonnari grossolani.
Per ottenere un buon giunto di saldatura, è necessario disporre di una fonte di calore adeguata, di una buona protezione del bagno fuso e di un metallo d'apporto per il cordone di saldatura. Questi sono i tre elementi essenziali della saldatura per fusione.
(1) Fonte di calore:
L'energia deve essere concentrata e la temperatura elevata per garantire una rapida fusione del metallo e ridurre al minimo la zona colpita dal calore. Le fonti di calore adatte sono, tra le altre, l'arco elettrico, l'arco al plasma, il calore delle scorie elettriche, il fascio di elettroni e il laser.
(2) Protezione del bacino fuso:
La protezione dalle scorie, la protezione dai gas e una combinazione di protezione dalle scorie e dai gas possono essere utilizzate per prevenire l'ossidazione ed effettuare la deossigenazione, la desolforazione e la disfosforazione, trasferendo gli elementi di lega al cordone di saldatura.
(3) Metallo di riempimento:
In questo modo si garantisce il riempimento del cordone di saldatura e l'introduzione di elementi di lega vantaggiosi, ottenendo le proprietà meccaniche richieste e altri requisiti di prestazione. I tipi principali sono l'anima di saldatura e il filo di saldatura.
I metodi più comuni di saldatura per fusione includono la saldatura a gas e la saldatura ad arco di bastone, saldatura ad arco sommerso, saldatura ad arco di argon, saldatura a CO2 saldatura a gas, saldatura elettrica a scoria, saldatura al plasma, saldatura a fascio elettronico e saldatura laser.
Saldatura ad arco sommerso
La saldatura ad arco sommerso è un metodo in cui il filo di saldatura viene alimentato automaticamente e continuamente e l'arco brucia sotto uno strato di flusso per la saldatura. Il flusso granulare sostituisce il rivestimento delle barre di saldatura e il filo di saldatura alimentato automaticamente sostituisce l'anima delle barre. Poiché i processi di accensione dell'arco, alimentazione del filo e avanzamento dell'arco sono tutti eseguiti da macchine, si ottiene un'elevata produttività e qualità della saldatura.
(1) Il processo di saldatura ad arco sommerso
Come illustrato nella Figura 4-18, il principio della saldatura ad arco sommerso prevede la copertura del giunto di saldatura con uno strato di flusso granulare di circa 30-50 mm di spessore. La testa di saldatura automatica alimenta il filo di saldatura continuo a forma di bobina nella zona dell'arco, mantenendo una certa lunghezza d'arco. Il filo di saldatura, la giunzione del pezzo e parte del flusso si fondono, formando scorie e una pozza fusa, con conseguenti reazioni metallurgiche.
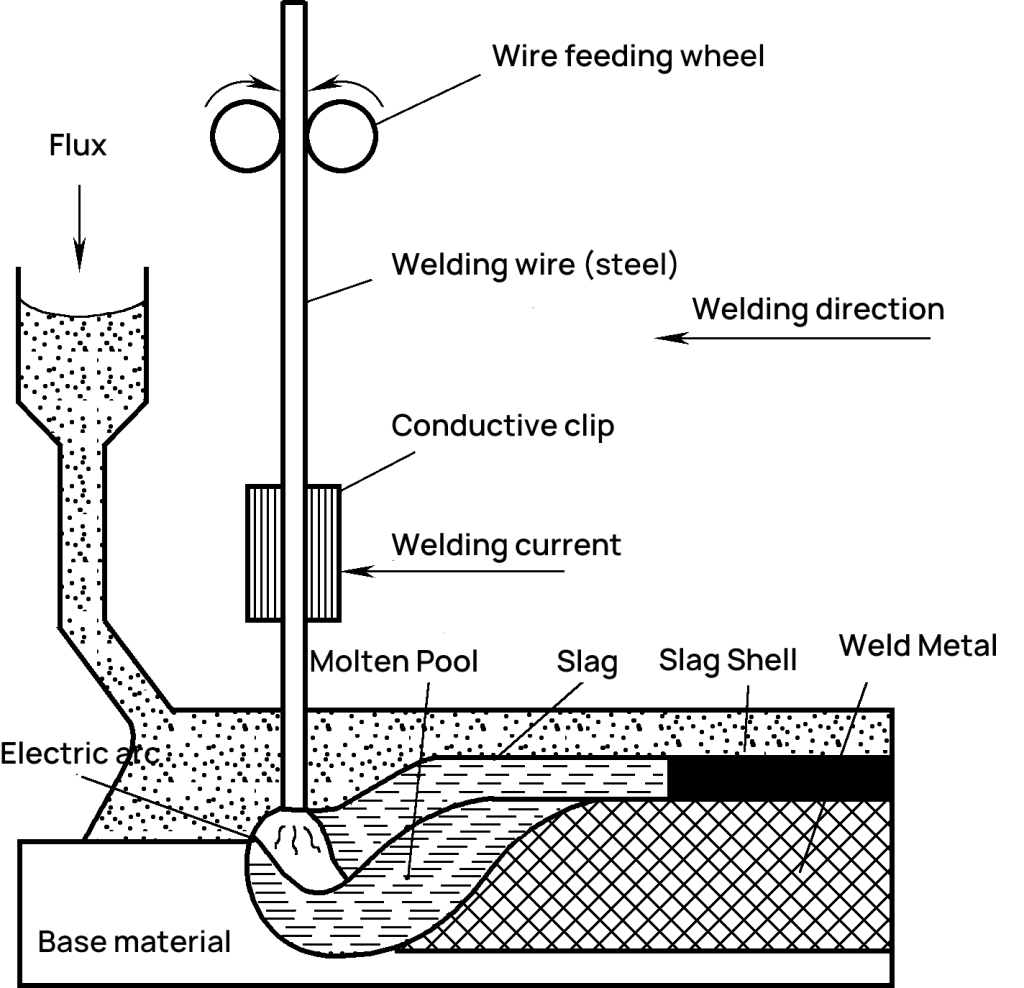
Una parte del flusso e del metallo evapora formando dei gas. Il gas, con una certa pressione, spinge via la scoria che circonda l'arco, formando una bolla di scoria chiusa. Ha una certa viscosità e può sopportare una certa pressione. Il metallo fuso, racchiuso nella bolla di scoria, viene isolato dall'aria, evitando schizzi di metallo, riducendo la perdita di calore e impedendo la dispersione della luce dell'arco.
Mentre la saldatrice automatica avanza (o la macchina rimane ferma mentre il pezzo si muove a una velocità uniforme), il metallo madre e il filo di saldatura sotto l'arco vengono continuamente riscaldati e fusi, formando un comune bagno di fusione. Il metallo dietro la piscina si raffredda e si solidifica in un cordone di saldatura. Le scorie che galleggiano sulla superficie della piscina si condensano in scorie di saldatura e il flusso non fuso può essere riciclato e riutilizzato dopo il recupero.
(2) Tecnica di saldatura ad arco sommerso
1) Preparazione prima della saldatura.
La saldatura ad arco sommerso comporta una corrente di saldatura elevata e una fusione profonda, pertanto i pezzi con uno spessore di 20-25 mm o inferiore non necessitano di una scanalatura. Tuttavia, nella produzione reale, per garantire la piena penetrazione del pezzo, è necessario tagliare una scanalatura a forma di Y quando lo spessore della piastra è di 14-22 mm. Quando lo spessore della piastra è di 22-50 mm, è possibile tagliare una scanalatura doppia a Y o a U.
L'angolo per le scanalature a Y e a doppia Y è di 50-60 gradi. La distanza tra i cordoni di saldatura deve essere uniforme. Quando si salda un cordone dritto, è necessario installare una tavola di partenza e una tavola di uscita (Figura 4-19f) per evitare che difetti come pori, inclusioni, cavità da ritiro e allentamenti causati dall'impatto e dall'estinzione dell'arco entrino nel cordone di saldatura del pezzo, compromettendo la qualità della saldatura.
2) Saldatura di testa della piastra piana.
Come illustrato nella Figura 4-19, per la saldatura di testa delle lamiere piane si adotta in genere la saldatura su due lati. Si possono saldare entrambi i lati senza lasciare spazi vuoti direttamente, oppure si può scegliere di eseguire la saldatura alla radice o a tampone. Per migliorare la produttività, è possibile utilizzare piastre di rame raffreddate ad acqua per la saldatura su un solo lato con formazione di un doppio lato.
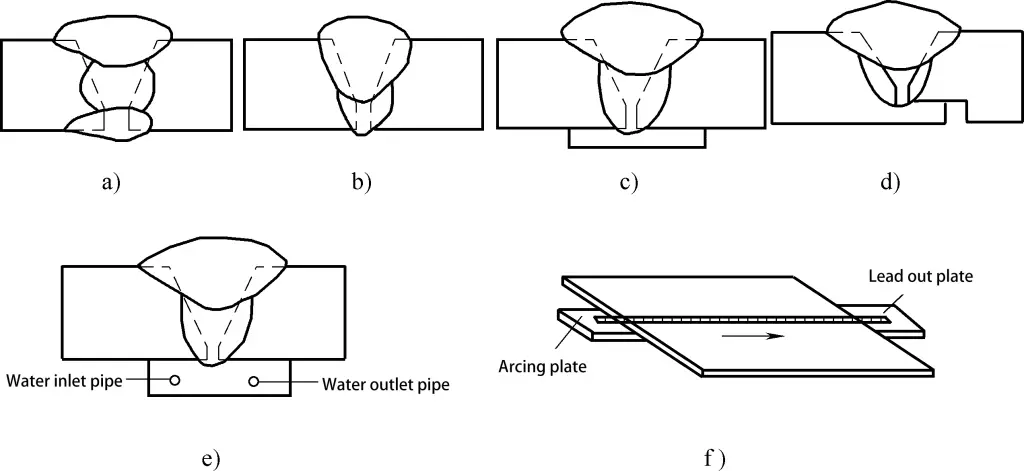
a) Saldatura su entrambi i lati
b) Saldatura a strappo
c) Utilizzo di una piastra di supporto
d) Utilizzando una scanalatura retrograda
e) Piastra di rame raffreddata ad acqua
f) Utilizzo di una piastra di riscontro e di una piastra di deflusso
3) Saldature circolari.
Quando si saldano cordoni circolari, il punto di partenza del filo di saldatura deve trovarsi a una certa distanza "e" dalla linea centrale del cerchio (Figura 4-20) per evitare che il metallo fuso del bagno fluisca. In genere, e=20-40 mm. I cordoni di saldatura circolari di componenti con diametro inferiore a 250 mm non vengono generalmente saldati con il metodo della saldatura ad arco sommerso.
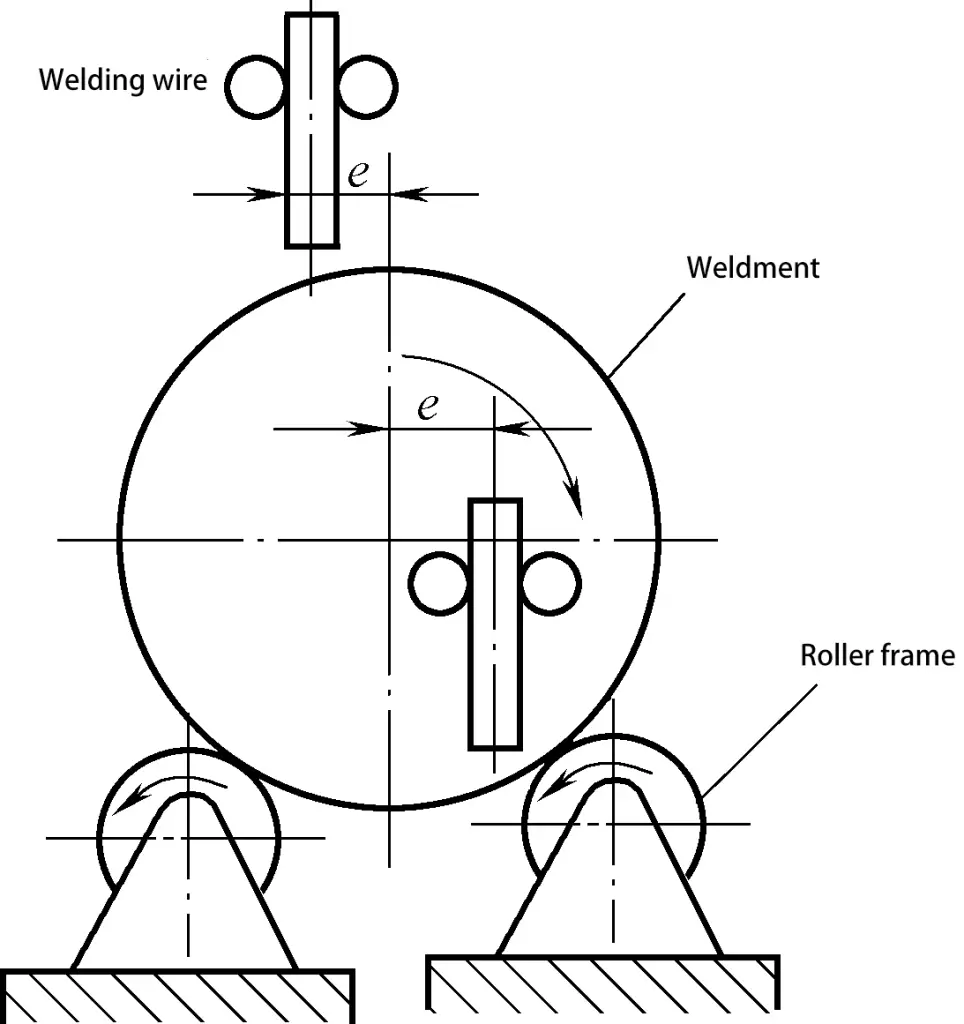
(3) Caratteristiche e applicazioni della saldatura ad arco sommerso
Rispetto alla saldatura ad arco metallico schermato, la saldatura ad arco sommerso presenta i seguenti vantaggi:
1) Alta produttività.
La corrente nella saldatura ad arco sommerso supera spesso i 1000A, 6-8 volte superiore a quella della saldatura ad arco con metallo schermato. Pertanto, la profondità di fusione è maggiore e la velocità di saldatura è più elevata. Non è necessario cambiare il filo di saldatura, si risparmia tempo e la produttività è 5-10 volte superiore a quella della saldatura ad arco metallico schermato.
2) Qualità di saldatura elevata e stabile.
Il processo di saldatura è automatico e i parametri di processo sono stabili. Il bagno fuso rimane liquido più a lungo, rendendo il processo metallurgico più completo. I gas e le scorie escono facilmente e la composizione chimica del metallo saldato è uniforme. Allo stesso tempo, grazie all'ampio flusso, la zona dell'arco è ben protetta, con conseguente formazione di una bella saldatura e una qualità di saldatura stabile.
3) Risparmia materiali metallici e ha bassi costi di produzione.
Il pezzo per la saldatura ad arco sommerso può non avere bisogno di scanalature o averne meno, risparmiando i materiali metallici e i materiali di saldatura consumati a causa della scanalatura. Inoltre, non vi è alcuna perdita di bacchetta per saldatura come nella saldatura ad arco di metallo schermato, e meno spruzzi di gocce fuse, con conseguenti minori costi di produzione.
4) Buone condizioni di lavoro.
La meccanizzazione e l'automazione del processo di saldatura ad arco sommerso riducono significativamente l'intensità di lavoro degli addetti. Inoltre, poiché l'arco è sepolto sotto il flusso, la luce dell'arco non è visibile e il fumo di saldatura è minore, migliorando le condizioni di lavoro.
La saldatura ad arco sommerso è adatta solo per la saldatura in piano, per cuciture diritte lunghe e per cuciture circolari di grande diametro. Non è adatta a lamiere sottili e alla saldatura di cordoni curvi. Inoltre, presenta requisiti più elevati per il preassemblaggio del pezzo.
La saldatura ad arco sommerso è applicabile all'acciaio al carbonio, all'acciaio strutturale a bassa lega, all'acciaio inossidabile, all'acciaio resistente al calore, ecc. Viene utilizzata principalmente per la saldatura di cordoni circonferenziali e rettilinei di recipienti a pressione, per la saldatura di cordoni lunghi e rettilinei di pareti di raffreddamento di caldaie, scafi di navi e sottomarini, gru, macchinari metallurgici (corpo dell'altoforno) e così via.
Saldatura ad arco di argon
(1) Classificazione della saldatura ad arco di argon
La saldatura ad arco con argon è un metodo di saldatura ad arco che utilizza il gas argon per proteggere l'arco e l'area di saldatura. In quanto gas inerte, l'argon non si scioglie nel metallo liquido e non reagisce con il metallo.
Una volta acceso, l'arco di argon è molto stabile. A seconda del tipo di elettrodo utilizzato, la saldatura ad arco di argon si divide in due tipi: saldatura ad arco di argon con elettrodo consumabile e saldatura ad arco di argon con elettrodo non consumabile (nota anche come saldatura ad arco di argon con elettrodo di tungsteno).
1) Saldatura ad arco ad argon con elettrodo consumabile.
Questo tipo di saldatura utilizza come elettrodo un filo alimentato in continuo che, dopo la fusione, serve anche come metallo d'apporto nella saldatura a gas inerte schermato, comunemente nota come saldatura MIG, come mostrato nella Figura 4-21a.
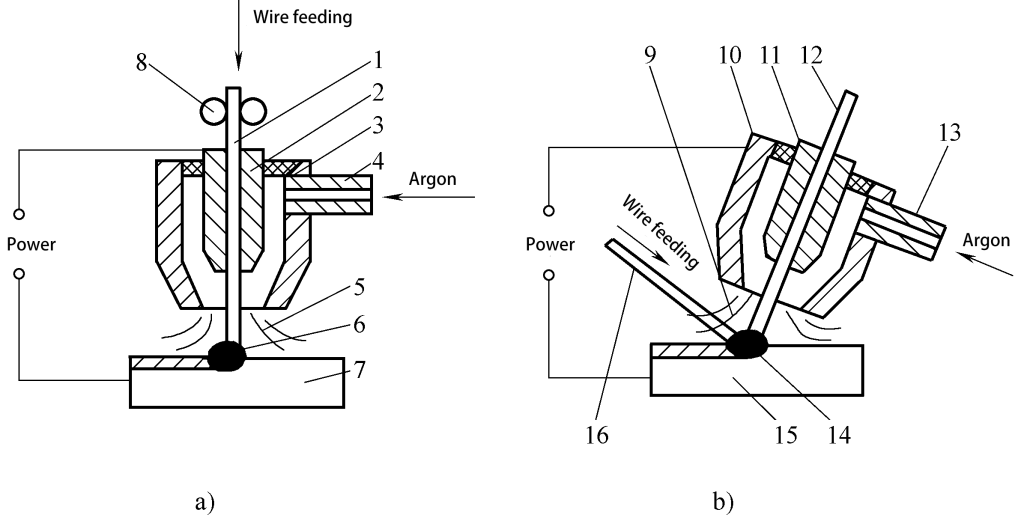
1,16-Filo di saldatura
2,11-Ugello conduttivo
3,10 ugelli
4,13-Tubo di aspirazione dell'aria
5, 9 Flusso di gas
6,14-Arco elettrico
7,15 pezzi
Ruota di alimentazione a 8 fili
Asta di tungsteno 12
Le gocce di filo entrano tipicamente nel bagno di saldatura attraverso un sottile "passaggio di spruzzatura". La corrente utilizzata per la saldatura è relativamente alta, la produttività è elevata ed è adatta alla saldatura di lamiere di spessore medio e inferiore a 25 mm. Per la saldatura dell'alluminio e delle sue leghe, si utilizza spesso la corrente continua a polarità inversa (pezzo collegato all'elettrodo negativo) per migliorare la stabilità dell'arco.
Allo stesso tempo, gli ioni argon di grande massa vengono utilizzati per bombardare la superficie del bagno fuso, rompendo la pellicola di ossido ad alto punto di fusione che si forma facilmente sulla superficie del bagno fuso, a vantaggio della fusione della saldatura e garantendo la qualità della saldatura. Questo effetto è noto come "pulizia del catodo" (chiamato anche "atomizzazione del catodo").
Poiché il filo di saldatura funge sia da elettrodo che da materiale d'apporto, è necessario un meccanismo di alimentazione del filo dedicato.
2) Saldatura ad arco ad argon con elettrodo non consumabile.
Questo tipo di saldatura utilizza una barra di tungsteno puro o in lega di tungsteno con un elevato punto di fusione come elettrodo nella saldatura con gas inerte, comunemente nota come Saldatura TIG. Durante la saldatura, l'elettrodo di tungsteno non fonde e serve solo come elettrodo per la conduzione elettrica. Il filo di saldatura viene introdotto nel bagno di saldatura dalla parte anteriore dell'elettrodo di tungsteno (Figura 4-21b).
Quando si saldano parti in acciaio, si utilizza spesso l'elettrodo positivo a corrente continua (pezzo collegato all'elettrodo positivo), altrimenti l'elettrodo di tungsteno si brucia facilmente. Quando si saldano parti colorate metalli come l'alluminio, il magnesio e le loro leghe, è possibile utilizzare la saldatura ad arco di argon in corrente continua a polarità inversa o in corrente alternata.
Quando il pezzo si trova in corrispondenza dell'elettrodo negativo o durante il semiciclo negativo della sorgente di alimentazione alternata, è possibile utilizzare l'effetto "pulizia del catodo". Per ridurre la bruciatura dell'elettrodo di tungsteno, la corrente di saldatura che attraversa l'elettrodo non deve essere troppo elevata e la profondità della saldatura è bassa, per cui la saldatura ad arco di argon con elettrodo non consumabile viene solitamente utilizzata per la saldatura di lamiere sottili con uno spessore inferiore a 6 mm.
(2) Caratteristiche e applicazioni della saldatura ad arco di argon
1) Qualità di saldatura superiore.
Il gas inerte fornisce una schermatura efficace, che consente di ottenere cordoni di saldatura puri ed esteticamente gradevoli.
2) Zona termicamente alterata e deformazione minima.
Il processo di saldatura ad arco di argon è caratterizzato da un arco di energia stabile e concentrato (grazie alla costrizione dell'arco), che rende il processo di saldatura facile da controllare.
3) Facilita la meccanizzazione e l'automazione.
Con la saldatura ad arco aperto, la formazione del cordone di saldatura è facile da osservare; la rimozione della scoria post-saldatura non è necessaria.
La saldatura ad arco di argon presenta alcuni svantaggi: il gas argon è costoso, il costo dell'attrezzatura è elevato, è necessaria una rigorosa pulizia pre-saldatura e il gas argon non ha effetti di deossigenazione e deidrogenazione. La saldatura ad arco di argon è adatta alla saldatura di metalli non ferrosi facilmente ossidabili, acciai legati e altri materiali, come alluminio, magnesio, titanio e loro leghe, acciai resistenti al calore, acciai inossidabili e altri ancora.
CO2 Saldatura a gas schermata
CO2 saldatura a gas schermata, comunemente chiamata CO2 è un tipo di saldatura a gas inerte metallico (MIG) che utilizza la CO2 per schermare l'arco e l'area di saldatura. Questo metodo di saldatura utilizza un filo di saldatura ad alimentazione continua come elettrodo, affidandosi all'arco generato tra il filo e il pezzo da saldare per fondere il metallo di base e il filo, consentendo una saldatura automatica o semi-automatica.
Una volta acceso l'arco, l'estremità del filo di saldatura, l'arco e il bagno fuso sono circondati da CO2 che protegge il metallo ad alta temperatura dagli effetti nocivi dell'aria. Il principio e l'attrezzatura sono simili a quelli della saldatura a gas inerte metallico (MIG), con la differenza del gas di protezione utilizzato. Il filo di saldatura comunemente utilizzato è H08Mn2SiA.
Caratteristiche della CO2 Saldatura a gas schermata:
1) Alta produttività. Grazie all'alimentazione automatica del filo, all'elevata densità di corrente e al calore concentrato dell'arco, la velocità di saldatura è elevata. Non si formano scorie dopo la saldatura, con conseguente risparmio di tempo per la rimozione delle scorie. La produttività è da 1 a 4 volte superiore a quella della saldatura ad arco a bastone.
2) Buona qualità di saldatura. Grazie alla protezione della CO2 Il filo di saldatura ha un basso contenuto di idrogeno e un alto contenuto di manganese, con un conseguente effetto di desolforazione significativo. Inoltre, poiché l'arco brucia sotto il flusso di gas compresso, il calore si concentra, la zona colpita dal calore è piccola e il giunto saldato ha una buona resistenza alle cricche.
3) Buone prestazioni operative. CO2 La saldatura a gas schermato è un processo di saldatura ad arco aperto, che consente di identificare facilmente i problemi di saldatura e di risolverli tempestivamente. È inoltre adatto alla saldatura in varie posizioni, offrendo un funzionamento flessibile.
4) Basso costo. CO2 Il gas è poco costoso e il filo di saldatura è un filo nudo a forma di disco, il cui costo è pari a circa 40% quello della saldatura ad arco sommerso e della saldatura a bastone.
CO2 La saldatura a gas ha anche i suoi svantaggi, come schizzi significativi, scarsa formazione della saldatura e tendenza a creare sacche di gas. Inoltre, i metalli e gli elementi in lega sono soggetti a ossidazione e bruciatura, il che la rende inadatta alla saldatura di metalli non ferrosi facilmente ossidabili e acciai altamente legati.
CO2 La saldatura a gas schermata è adatta alla saldatura di acciaio a basso tenore di carbonio e di acciai strutturali generici a bassa lega con livelli di resistenza non elevati, utilizzati principalmente per la saldatura di lamiere sottili.
Saldatura a elettroscoria
La saldatura a elettroscoria è un metodo di saldatura per fusione che sfrutta il calore resistivo generato dal passaggio della corrente elettrica attraverso la scoria liquida.
Il processo di saldatura a elettroerosione è illustrato nella Figura 4-22. I due pezzi sono posizionati verticalmente (in un cordone di saldatura verticale), a una distanza di 20-60 mm l'uno dall'altro, con cursori di rame raffreddati ad acqua su entrambi i lati, una piastra di avvio dell'arco in basso e una piastra di uscita in alto. All'inizio della saldatura, il filo di saldatura entra in cortocircuito con la piastra di avvio dell'arco per innescare l'arco.
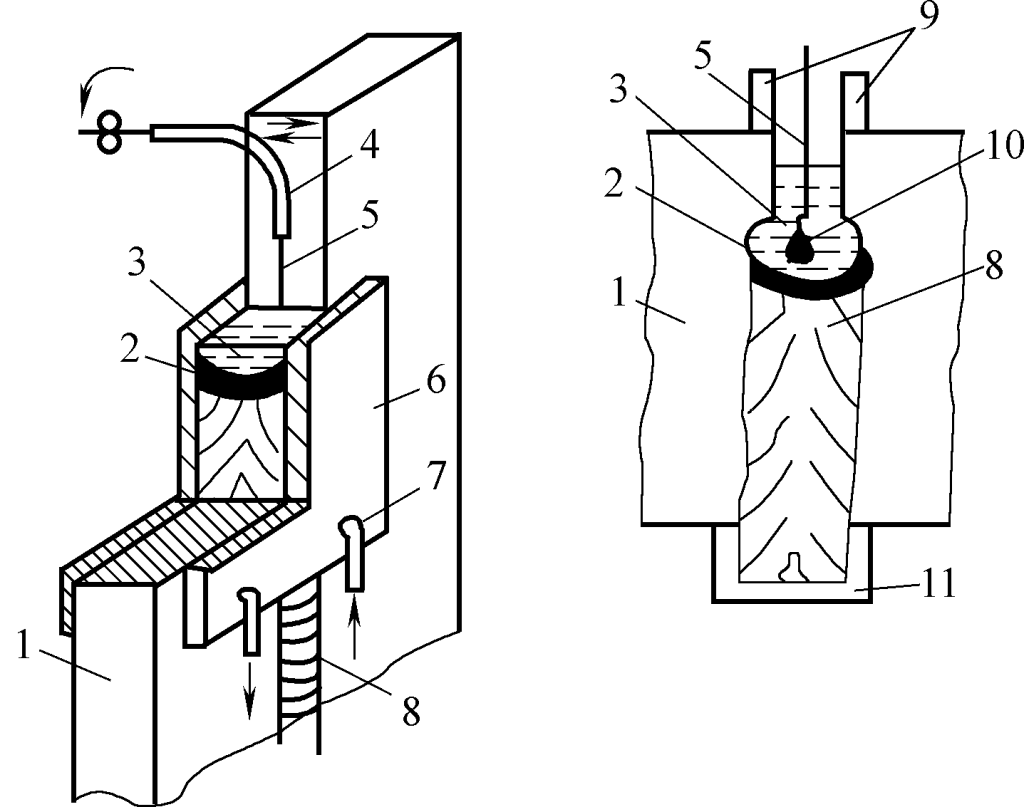
1 pezzo
Piscina a 2 metalli fusi
Piscina a 3 lembi
Ugello a 4 conduttori
5-Filo di saldatura
6 cursori
7-Tubo dell'acqua di raffreddamento
Cucitura a 8 saldature
Piastra a 9 conduttori
10-Filo di saldatura fuso
Piastra iniziale a 11 archi
L'arco fonde il flusso continuamente aggiunto per formare una pozza di scorie. Quando il bagno di scorie raggiunge un certo spessore, l'arco si spegne e il filo di saldatura e il pezzo vengono fusi dal calore resistivo del bagno di scorie.
Con l'aumento della quantità di metallo d'apporto, il bagno di scoria aumenta gradualmente e i cursori raffreddati ad acqua su entrambi i lati salgono con esso. La parte inferiore del cordone di saldatura si solidifica successivamente, formando un cordone di saldatura. A seconda dello spessore del pezzo, si possono utilizzare fili singoli o multipli.
Caratteristiche della saldatura a elettroerosione:
1) Alta produttività. È possibile saldare pezzi di grandi dimensioni in un'unica operazione. Ad esempio, se un singolo filo non oscilla, può saldare spessori di 40-60 mm; se un singolo filo oscilla, può saldare spessori di 60-150 mm.
2) Buona qualità della saldatura. Il metallo liquido del cordone di saldatura ha un tempo di permanenza lungo, che riduce la probabilità di produrre sacche di gas, inclusioni e altri difetti; la scoria copre il bagno di saldatura e fornisce una buona protezione.
3) Alta produttività e basso costo. Non è necessario eseguire scanalature per qualsiasi spessore, è sufficiente lasciare uno spazio di 25-60 mm e la saldatura può essere eseguita in un'unica operazione; i materiali di saldatura e il consumo di energia elettrica sono ridotti.
Lo svantaggio della saldatura a elettroerosione è che il bagno di saldatura rimane a lungo ad alta temperatura, i grani sono grossolani, la zona termicamente alterata è ampia ed è necessaria una ricottura post-saldatura; l'adattabilità della saldatura è scarsa; viene sempre eseguita in modo verticale, non può essere eseguita in piano, non è adatta alla saldatura di pezzi sottili e il cordone di saldatura non deve essere troppo lungo.
La saldatura a elettroerosione è adatta alla saldatura di materiali come l'acciaio al carbonio, l'acciaio legato e l'acciaio inossidabile. Viene utilizzata principalmente per la saldatura di recipienti a pressione a parete spessa, per la saldatura per colata, per la saldatura per fucinatura e per componenti di grandi dimensioni, come la saldatura per giunzione di lamiere spesse. Lo spessore di saldatura deve essere generalmente superiore a 40 mm.
Saldatura al plasma ad arco
La saldatura ad arco plasma è un processo di saldatura che comprime un arco in uno stretto fascio di plasma attraverso effetti di compressione meccanica (contrazione forzata quando l'arco passa attraverso il piccolo foro dell'ugello), effetti di compressione termica (sotto la forte azione del flusso d'aria fredda, le particelle cariche, gli ioni negativi e il flusso di elettroni si concentrano verso il centro della colonna d'arco) ed effetti di contrazione elettromagnetica (le linee di corrente delle particelle cariche nella colonna d'arco sono parallele e il campo magnetico fa sì che le linee di corrente si attraggano e si contraggano).
Il principio è illustrato nella Figura 4-23. La temperatura dell'arco di plasma raggiunge i 24.000-50.000 K, con un'energia altamente concentrata e una densità di energia del 105 a 106W/cm2che può fondere materiali spessi in una sola passata. La saldatura al plasma può essere utilizzata sia per la saldatura che per il taglio.
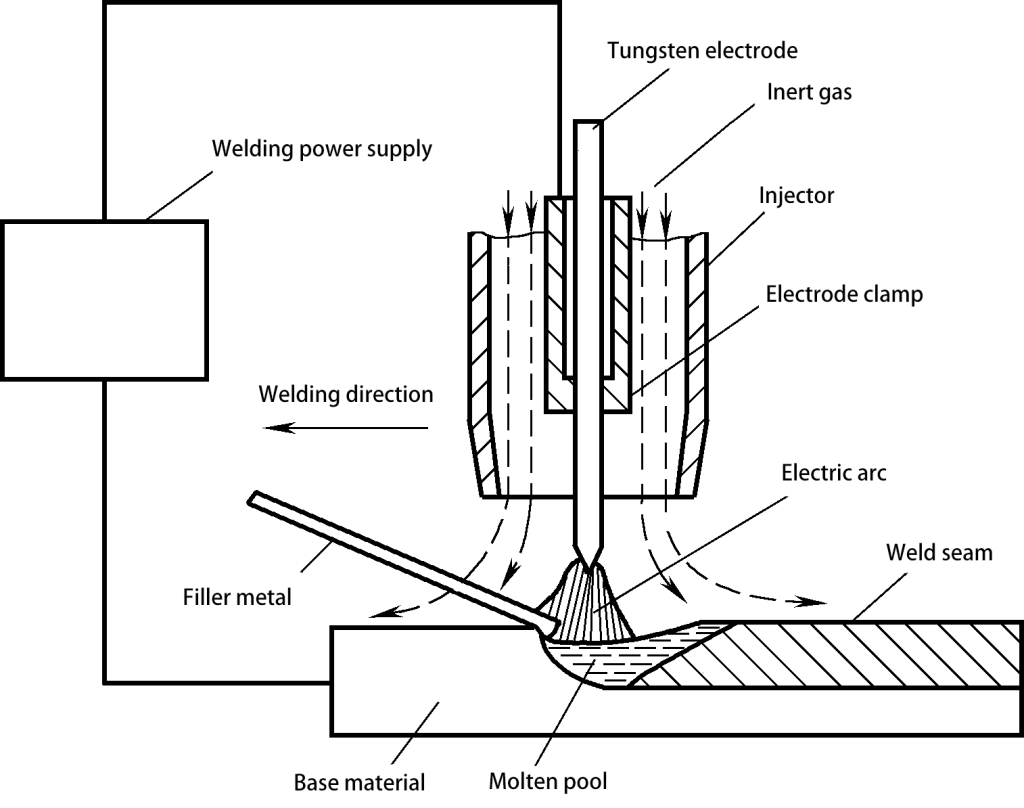
La saldatura al plasma ad arco ha un'alta densità di energia, un'elevata temperatura della colonna d'arco, un forte potere di penetrazione e può saldare acciaio di 10-12 mm in un'unica passata senza smussare, con formazione del doppio lato. Ha una velocità di saldatura elevata, un'alta produttività, una zona termicamente alterata ridotta, una deformazione di saldatura minima e una buona qualità di saldatura.
Quando la corrente è inferiore a 0,1A, l'arco al plasma può ancora bruciare in modo stabile e può saldare piastre ultrasottili di 0,1-2 mm di spessore, come lamine e termocoppie. Tuttavia, l'attrezzatura per la saldatura al plasma è complessa e consuma una grande quantità di gas, il che la rende adatta solo alla saldatura in ambienti chiusi.
Attualmente, la saldatura al plasma ad arco è utilizzata principalmente nell'industria della difesa e nelle tecnologie industriali d'avanguardia per la saldatura di materiali difficili da fondere, facilmente ossidabili e termicamente sensibili, come rame, tungsteno, nichel, molibdeno, alluminio, titanio e le loro leghe, nonché acciaio inossidabile e acciaio ad alta resistenza.
Saldatura a fascio di elettroni
La saldatura a fascio elettronico è un metodo di saldatura per fusione che utilizza un fascio di elettroni accelerato e focalizzato per generare energia termica colpendo i pezzi in lavorazione posti in un ambiente sotto vuoto o non sotto vuoto.
In base al grado di vuoto dell'ambiente in cui si trova il pezzo, la saldatura a fascio elettronico si divide in saldatura a fascio elettronico ad alto vuoto, saldatura a fascio elettronico a basso vuoto e saldatura a fascio elettronico senza vuoto. La Figura 4-24 mostra la saldatura a fascio elettronico ad alto vuoto più utilizzata.
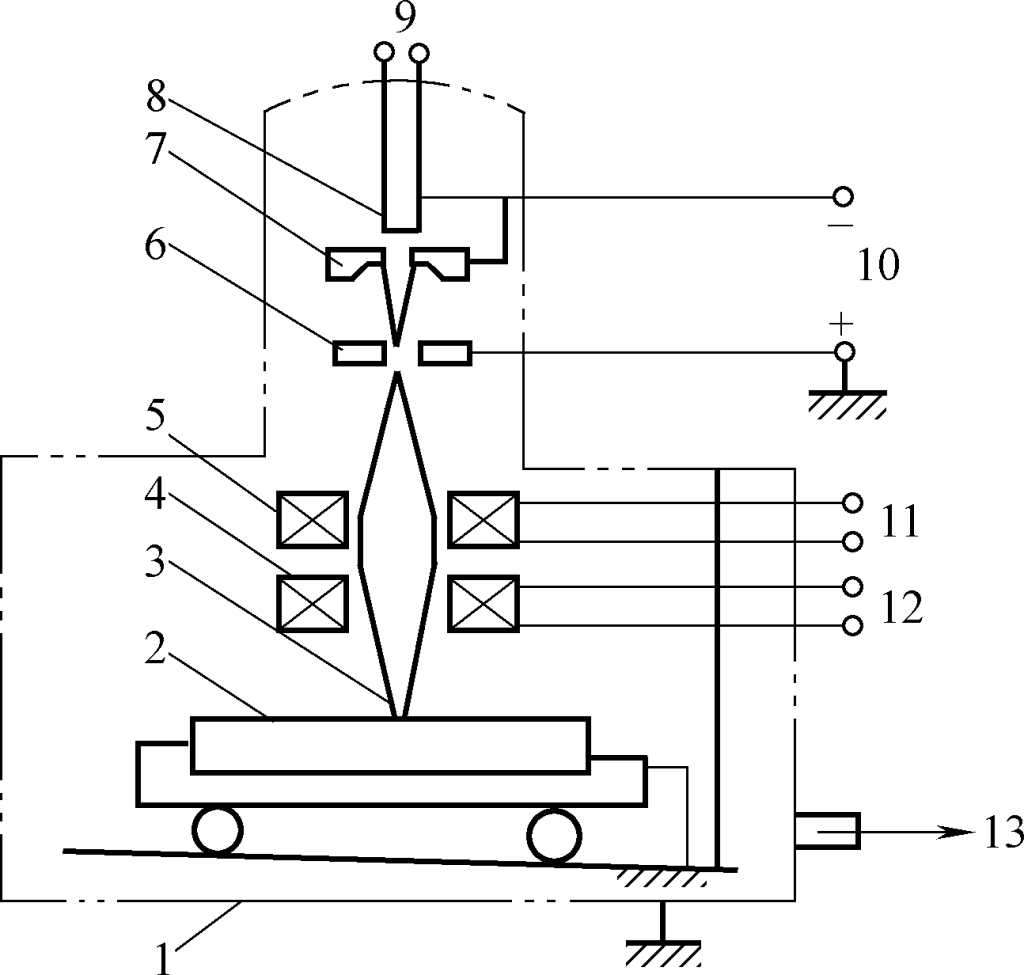
1-Camera di vuoto
2-Sviluppo
Fascio di 3 elettroni
Dispositivo di deviazione a 4 magneti
Obiettivo a 5 punti di messa a fuoco
A 6 nodi
7-Catodo
A 8 filamenti
Alimentazione 9-AC
Alimentatore ad alta tensione 10-DC
11, 12- Alimentazione CC
13-Dispositivo di scarico
Nel vuoto, il catodo del cannone elettronico viene riscaldato elettricamente ad alta temperatura, emettendo un gran numero di elettroni. Questi elettroni vengono accelerati sotto l'influenza di un forte campo elettrico.
Gli elettroni ad alta velocità formano una densità ad alta energia (109W/cm2) attraverso il dispositivo di formazione del fascio (anodo e lente di focalizzazione), colpendo un'area molto piccola del pezzo ad una velocità estremamente elevata (1,6×108m/s). L'energia cinetica si trasforma in energia termica, causando la rapida fusione o addirittura la vaporizzazione dell'area colpita.
Il giunto desiderato può essere ottenuto spostando opportunamente il pezzo in base al suo grado di fusione. In genere, nella saldatura a fascio elettronico non viene aggiunto alcun metallo d'apporto.
La saldatura a fascio elettronico sottovuoto viene eseguita nel vuoto, quindi il metallo non si ossida e non si nitrura, garantendo un'elevata qualità della saldatura. Il calore durante la saldatura è altamente concentrato, con il risultato di una piccola zona colpita dal calore (solo 0,05~0,75 mm), eliminando virtualmente la deformazione della saldatura e rendendola adatta alla saldatura di pezzi dopo una lavorazione di precisione.
La gamma regolabile dei parametri di processo della saldatura a fascio di elettroni è ampia e consente di saldare piastre di diverso spessore (0,1~300 mm). La densità di energia del fascio di elettroni è elevata, la velocità di saldatura è rapida e il rapporto profondità/larghezza della saldatura può raggiungere 20:1 senza la necessità di una scanalatura, con conseguente alta produttività e basso costo.
La saldatura a fascio elettronico sottovuoto è adatta alla saldatura di vari metalli refrattari (come titanio, molibdeno, ecc.), metalli reattivi (escluse le leghe con un elevato contenuto di elementi a basso punto di ebollizione, come stagno, zinco, ecc.
Può essere utilizzato per la saldatura di microstrutture a parete sottile e di strutture a piastra spessa, come i componenti dei circuiti microelettronici, i grandi involucri dei missili, le strutture a parete spessa delle apparecchiature nucleari, i cuscinetti, i gruppi di ingranaggi, ecc.".
Saldatura laser
La saldatura laser è una tecnica che utilizza il calore prodotto da un raggio laser focalizzato che colpisce il pezzo da saldare. Il laser è una forma di luce coerente ad alta intensità, eccellente monocromaticità e buona direzionalità. La densità di energia di un raggio laser focalizzato è estremamente elevata. In un breve lasso di tempo, l'energia laser può essere convertita in energia termica, raggiungendo temperature di oltre 10.000°C.
Durante la saldatura laser (Figura 4-25), il laser viene stimolato per produrre un raggio laser che viene focalizzato in un piccolo punto focale da un sistema di messa a fuoco, concentrando ulteriormente l'energia.
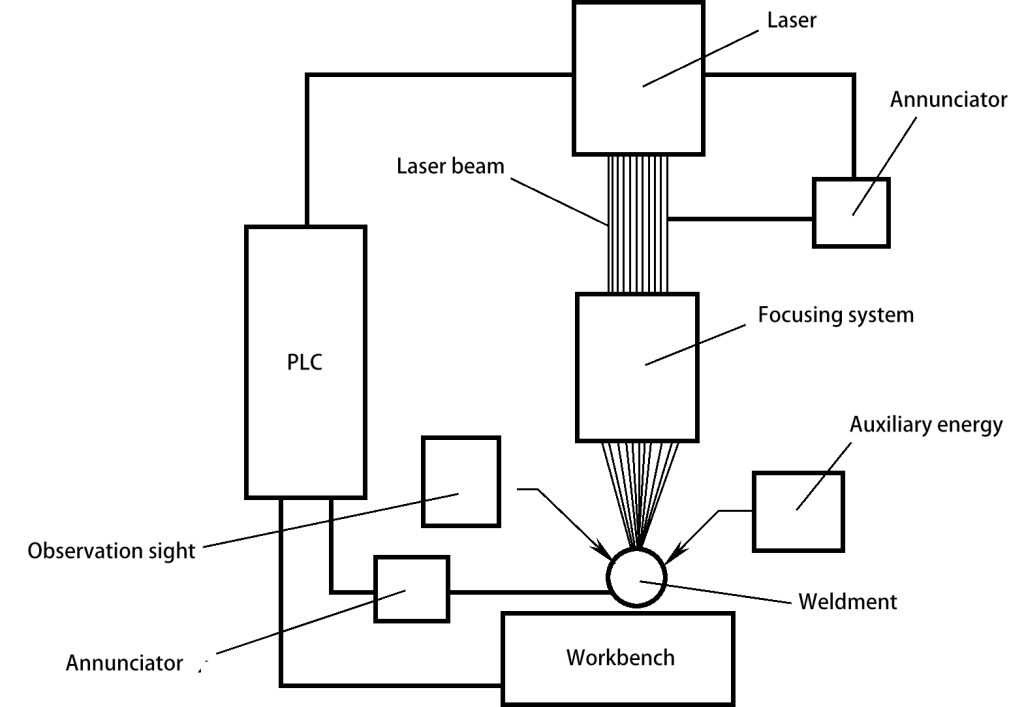
Quando il raggio laser viene focalizzato sulla giuntura del pezzo, l'energia luminosa viene assorbita dal materiale di saldatura e trasformata in energia termica, generando alte temperature in prossimità del punto focale, che causano la fusione istantanea del metallo e la formazione di un giunto saldato al momento del raffreddamento.
La saldatura laser ha un'alta densità di energia e la fonte di calore agisce per un tempo molto breve, con il risultato di una zona minimamente colpita dal calore, una deformazione minima della saldatura e un'elevata precisione delle dimensioni della saldatura. Può essere utilizzata per saldare parti di precisione e materiali sensibili al calore. Inoltre, grazie al processo di saldatura estremamente rapido, il materiale saldato ha una minore probabilità di ossidarsi, consentendo di saldare in atmosfera senza bisogno di vuoto o protezione dal gas.
La saldatura laser è flessibile e può essere diretta verso aree difficili da raggiungere con l'aiuto di prismi di deviazione o fibre ottiche, oppure può essere utilizzata per focalizzare la saldatura attraverso materiali trasparenti.
La saldatura laser è adatta per materiali isolanti, metalli dissimili e saldatura tra metalli e non metalli. Attualmente, viene utilizzata principalmente per la micro-precisione, per i componenti di saldatura densamente disposti e sensibili al calore.
Saldatura a pressione
La saldatura a pressione si riferisce a una categoria di metodi di saldatura che realizzano giunti non separabili riscaldando i metalli allo stato plastico, pressurizzandoli per provocare deformazione plastica, ricristallizzazione e diffusione atomica. In questo modo gli atomi di due superfici separate si avvicinano abbastanza da formare legami metallici (a una distanza reticolare di 0,3~0,5 nm).
Saldatura a resistenza
La saldatura a resistenza è un metodo in cui i pezzi combinati vengono pressurizzati attraverso gli elettrodi e il calore generato dalla resistenza quando una corrente elettrica passa attraverso la superficie di contatto e l'area adiacente del giunto di saldatura viene utilizzato per la saldatura. I tipi più comuni includono saldatura a punti, saldatura a cordone e saldatura di testa.
(1) Saldatura a punti
La saldatura a punti è un metodo di saldatura a resistenza che forma un punto di saldatura fondendo localmente il metallo madre attraverso il calore della resistenza. Questo metodo si ottiene assemblando i pezzi in un giunto a spirale, stretto tra loro. montaggio tra due elettrodi cilindrici, applicando una pressione e facendo passare una corrente elettrica. Il principio è illustrato nella Figura 4-26, e le forme più comuni di spot giunti di saldatura sono mostrati nella Figura 4-27.
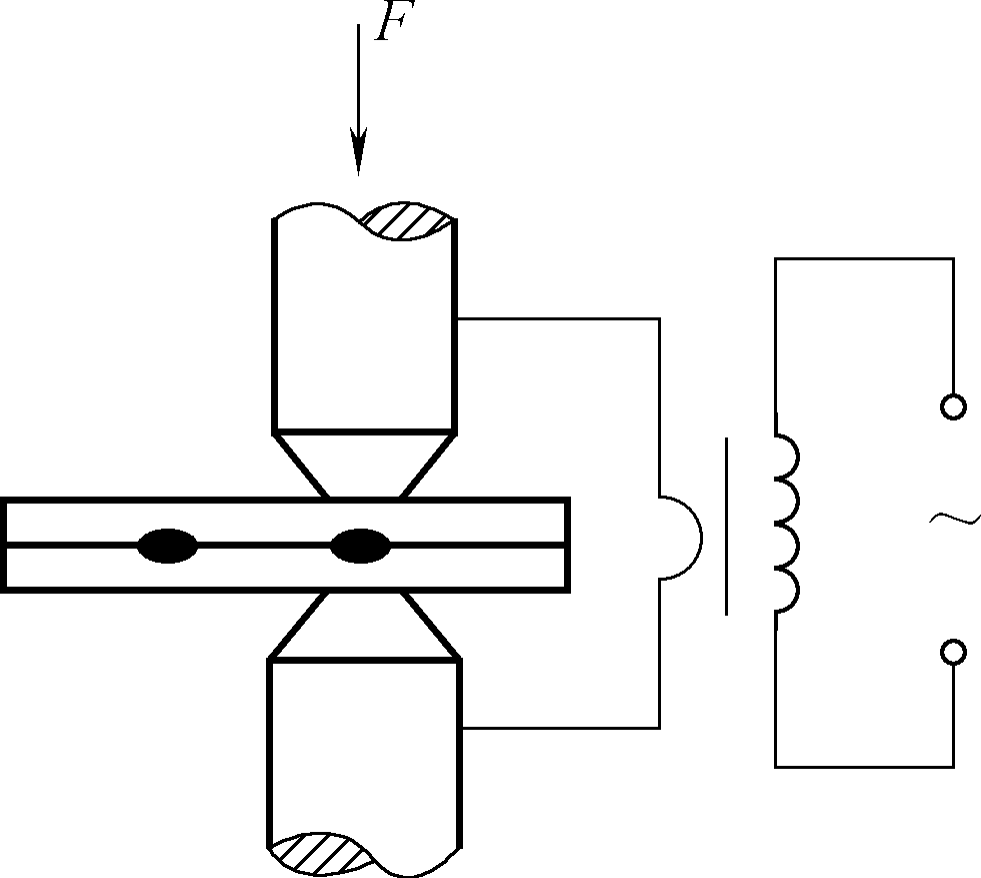
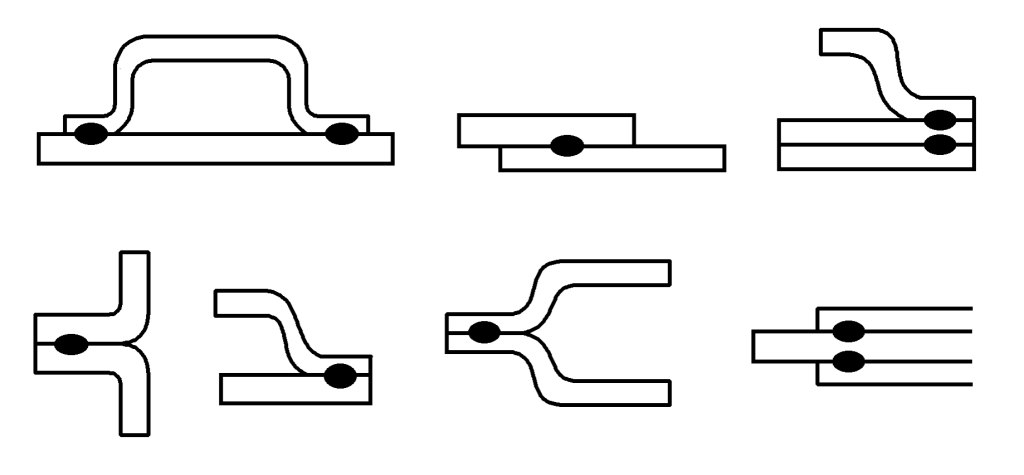
Durante la saldatura a punti, viene dapprima applicata una pressione per garantire lo stretto contatto tra i due pezzi, seguita da un riscaldamento mediante corrente elettrica. Poiché la resistenza nel punto di contatto dei pezzi è elevata, il calore si concentra in quel punto, aumentando rapidamente la temperatura e fondendo il metallo per formare un nucleo fuso di una certa dimensione.
Quando la corrente viene interrotta e la pressione viene rimossa, il nucleo di fusione nel punto di contatto dei due pezzi si solidifica formando un punto di saldatura denso. Prima della saldatura a punti, è fondamentale pulire accuratamente la pellicola di ossido, le macchie di olio, ecc. sulla superficie dei pezzi per evitare di compromettere la qualità della saldatura a punti e la durata degli elettrodi a causa dell'eccessiva resistenza di contatto dei pezzi.
Inoltre, durante la saldatura a punti, una parte della corrente passa attraverso i punti già saldati, riducendo la corrente sul punto di saldatura e causando un fenomeno di shunting. Per ridurre al minimo lo shunting, la distanza di saldatura a punti non deve essere troppo piccola. I principali parametri di processo che influenzano la qualità della saldatura a punti sono la pressione dell'elettrodo, la corrente di saldatura e il tempo di eccitazione.
Se la pressione dell'elettrodo è troppo alta, la resistenza di contatto diminuisce, riducendo il calore e provocando un'insufficiente resistenza del punto di saldatura. Se la pressione dell'elettrodo è troppo bassa, il contatto tra i pezzi è scarso.
Sebbene la fonte di calore sia forte, è instabile e può persino provocare schizzi e difetti di bruciatura. Se la corrente di saldatura è insufficiente, il calore è insufficiente, la profondità di fusione è troppo piccola e può persino causare la mancata fusione; se la corrente è troppo alta, la profondità di fusione è troppo grande e possono verificarsi schizzi di metallo, fino a provocare una bruciatura.
L'influenza del tempo di eccitazione sulla qualità della saldatura a punti è simile a quella della corrente. La saldatura a punti è utilizzata principalmente per la saldatura di lamiere sottili inferiori a 4 mm e di barre di rinforzo.
(2) Saldatura a cordoncino
La saldatura a cordone è un processo di saldatura a punti continuo. Utilizza elettrodi a forma di disco che ruotano in modo continuo al posto di quelli cilindrici, dando luogo a cordoni di saldatura continui e sovrapposti dopo la saldatura, come mostrato nella Figura 4-28.
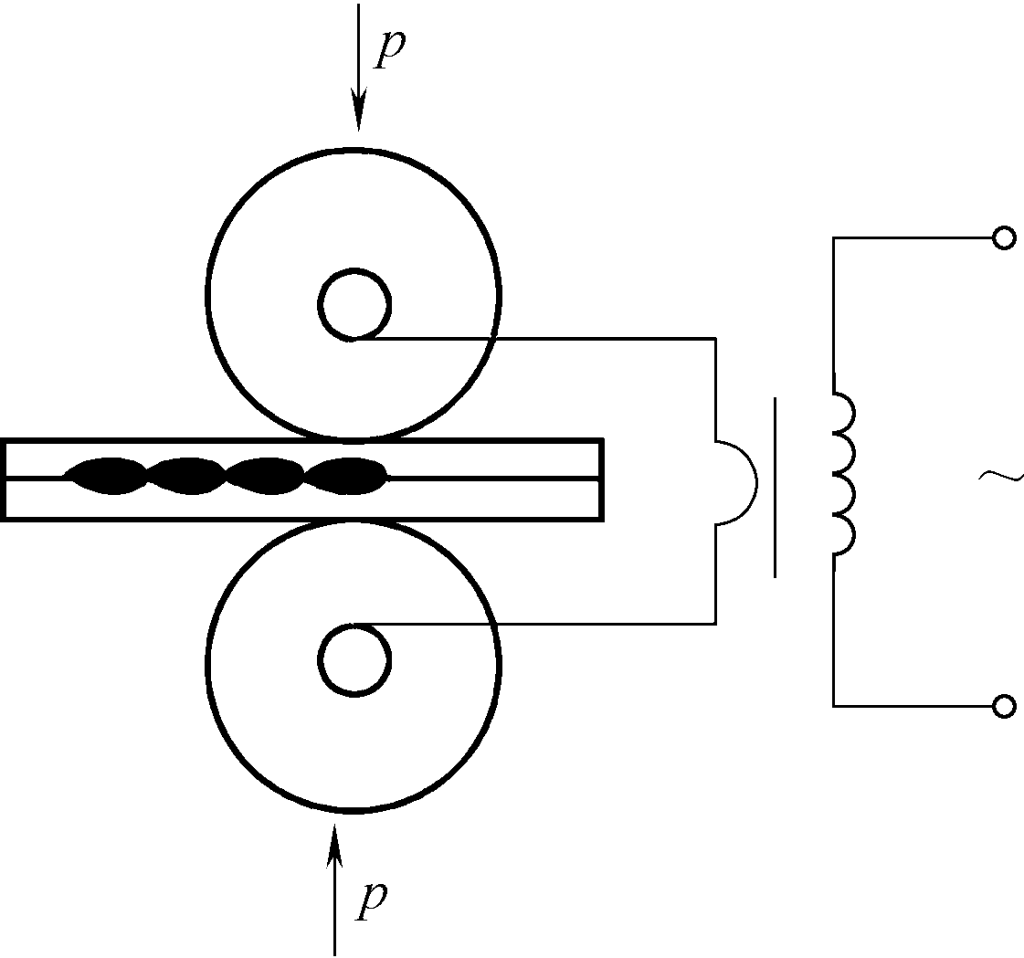
L'elettrodo a forma di disco non solo pressurizza e conduce l'elettricità ai pezzi da saldare, ma fa anche avanzare i pezzi grazie alla propria rotazione per completare la saldatura.
Il fenomeno di smistamento durante la saldatura a cordone è più grave. Quando si saldano pezzi dello stesso spessore, la corrente di saldatura è 1,5~2 volte quella della saldatura a punti. La saldatura a cordone è comunemente utilizzata per la saldatura di contenitori a pareti sottili inferiori a 3 mm che devono essere sigillati, come serbatoi dell'olio, serbatoi dell'acqua, marmitte, ecc.
(3) Saldatura di testa
La saldatura di testa è un metodo di saldatura a resistenza che utilizza il calore resistivo per fondere due pezzi in un giunto di testa, saldando le intere facce finali.
1) Saldatura di testa a resistenza: La saldatura di testa a resistenza prevede l'assemblaggio dei pezzi in un giunto di testa, assicurandosi che le loro facce finali siano a stretto contatto e utilizzando il calore resistivo per riscaldarli fino allo stato plastico. La pressione viene quindi applicata per completare la saldatura. Il principio di questo metodo di saldatura è illustrato nella Figura 4-29a. La saldatura di testa a resistenza ha il vantaggio di avere giunti lisci, bave minime e un processo di saldatura semplice.
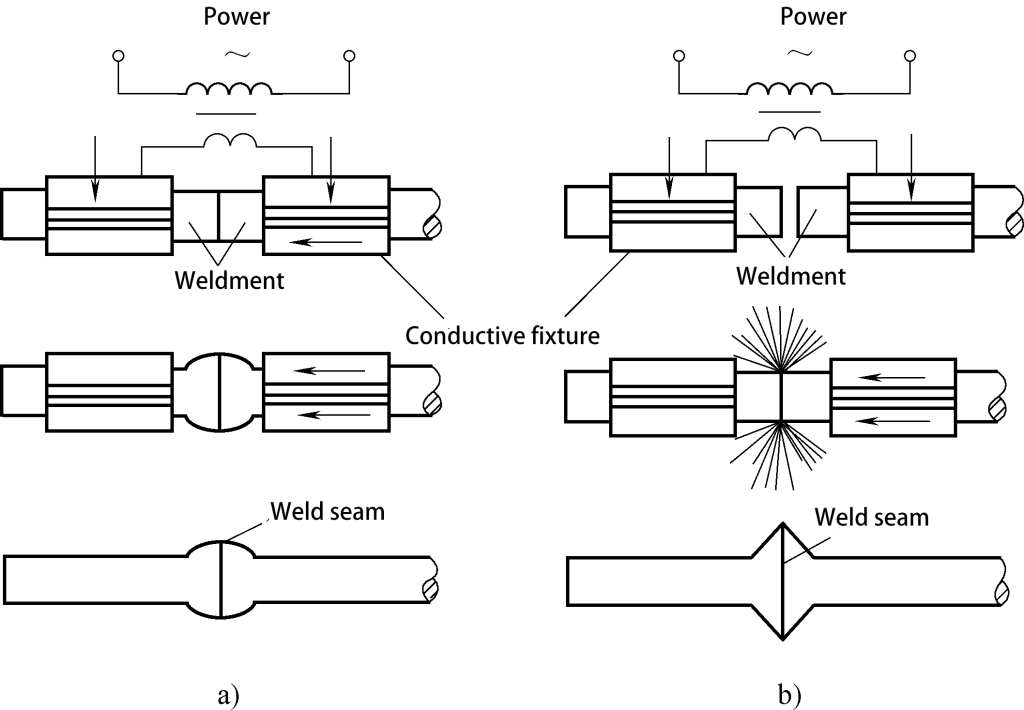
a) Saldatura di testa a resistenza
b) Saldatura di testa a caldo
Tuttavia, le sue giunzioni hanno proprietà meccaniche inferiori e richiedono un'elevata preparazione delle facce del pezzo (è necessaria una rigorosa pulizia pre-saldatura). Viene generalmente utilizzato per giunzioni di testa di profili metallici di piccola sezione (inferiore a 250 mm²).
2) Saldatura di testa: Durante la saldatura, i pezzi vengono bloccati sulla testa di serraggio dell'elettrodo, la fonte di alimentazione viene accesa e i pezzi vengono gradualmente avvicinati. A causa delle facce di contatto ruvide, all'inizio solo pochi punti sono in contatto.
Quando una forte corrente passa attraverso questi pochi punti con un'area di contatto molto piccola, si genera una grande quantità di calore resistivo, che provoca la rapida fusione e persino la vaporizzazione del metallo nei punti di contatto. Il metallo fuso, sotto l'influenza delle forze elettromagnetiche e dell'esplosione di gas, schizza fuori con gli ossidi superficiali, creando un lampo scintillante. Man mano che i pezzi avanzano, il flash si verifica nei nuovi punti di contatto.
Quando un sottile strato di metallo sull'intera superficie di contatto dei pezzi si è fuso, si applica rapidamente la pressione e si interrompe l'alimentazione. I due pezzi si raffreddano e si solidificano sotto pressione, saldandosi insieme. Il principio della saldatura di testa è illustrato nella Figura 4-29b.
Durante il processo di saldatura flash di testa, gli ossidi e le impurità presenti sull'estremità del pezzo vengono espulsi dalle scintille flash o spremuti con il metallo liquido, impedendo l'intrusione di aria. In questo modo, il giunto presenta meno impurità, un'elevata qualità e una maggiore resistenza e plasticità della saldatura. Il requisito della pulizia pre-saldatura della faccia terminale non è elevato.
Viene spesso utilizzata per saldare parti importanti come binari, catene di ancoraggio, tubi, cerchioni e utensili. Può essere utilizzata anche per saldare metalli diversi (come alluminio-rame, rame-acciaio, alluminio-acciaio, ecc.), da fili metallici con un diametro di 0,01 mm a tubi con un diametro di 500 mm, e profili o piastre metalliche con una sezione trasversale fino a 20000 mm².
Tuttavia, la saldatura flash di testa comporta una maggiore bruciatura dei pezzi e le bave devono essere pulite dopo la saldatura".
(4) Caratteristiche della saldatura a resistenza
La saldatura a resistenza vanta un riscaldamento rapido a temperature relativamente basse, che determina un impatto termico e una deformazione minimi del pezzo, facilitando così la creazione di giunti di alta qualità. Non richiede metallo d'apporto o flusso aggiuntivo. Il processo è privo di luce d'arco, genera un rumore minimo e produce meno polvere e gas nocivi, migliorando l'ambiente di lavoro.
Le unità di saldatura a resistenza sono semplici nella struttura, leggere e con una buona tenuta d'aria, il che le rende ideali per la produzione di pezzi di forme complesse. Il processo è facilmente meccanizzabile e automatizzabile, con conseguente elevata produttività.
Tuttavia, i fattori che influenzano la resistenza possono provocare fluttuazioni di calore, con conseguente incoerenza della qualità del giunto. Questo può, in una certa misura, limitare l'applicazione della saldatura a resistenza su alcuni componenti critici. Inoltre, la saldatura a resistenza consuma una quantità significativa di elettricità e le macchine sono complesse e costose.
Saldatura a frizione
Saldatura a frizione è un metodo di saldatura a pressione che utilizza il calore generato dall'attrito tra le superfici dei pezzi per portare le facce finali a uno stato termoplastico, seguito da una rapida applicazione di pressione per completare il processo di saldatura. Come illustrato nella Figura 4-30, il principio della saldatura per attrito prevede che il pezzo 1 sia tenuto in un mandrino rotante e il pezzo 2 in un mandrino che può muoversi assialmente e applicare pressione.
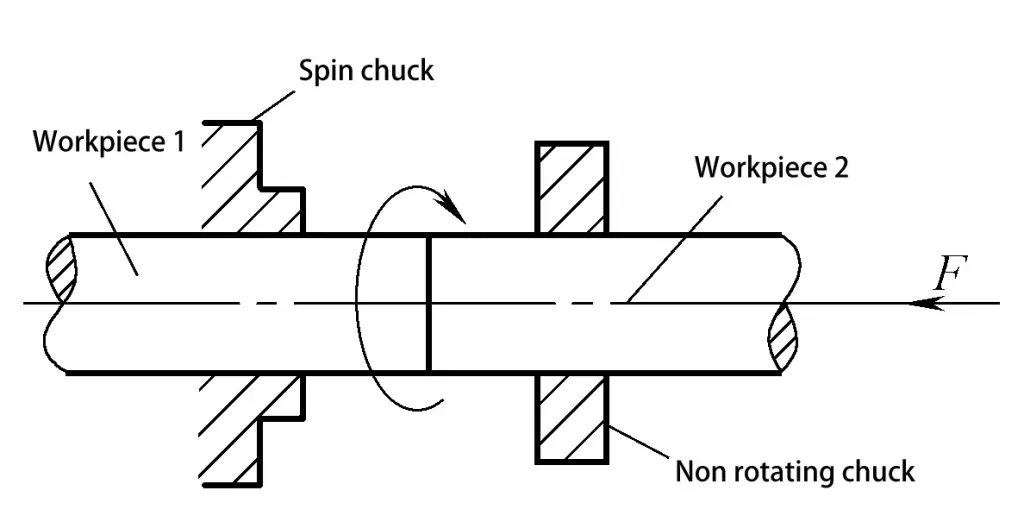
All'inizio della saldatura, il pezzo 1 ruota ad alta velocità mentre il pezzo 2 si muove verso il pezzo 1 ed entra in contatto con esso. L'energia meccanica consumata dalle superfici di attrito viene convertita in calore, portando la temperatura del giunto a un certo livello (stato termoplastico). A questo punto, il pezzo 1 smette di ruotare e viene applicata una pressione superiore a un'estremità del pezzo 2, che si raffredda sotto pressione formando una struttura di giunzione densa.
I giunti di saldatura per attrito sono generalmente di sezione uguale, ma possono anche essere di sezione disuguale, purché una sezione sia un corpo rotante.
(1) Caratteristiche della saldatura per attrito
1) Qualità del giunto buona e stabile. La temperatura di saldatura per attrito è inferiore al punto di fusione del metallo del pezzo, la zona interessata dal calore è piccola e il giunto completa la deformazione plastica e la ricristallizzazione sotto la forza superiore, dando luogo a una struttura densa.
Inoltre, il film di ossido e la contaminazione da olio sulla faccia terminale del pezzo vengono eliminati per attrito, rendendo il giunto meno soggetto a porosità e inclusioni di scorie e migliorando così la qualità del giunto.
2) Elevata produttività di saldatura e costi contenuti. La saldatura per attrito è semplice da utilizzare e non richiede metallo d'apporto, il che la rende facile da automatizzare e porta a una maggiore produttività. Allo stesso tempo, l'attrezzatura è semplice e il consumo energetico è basso, solo 1/10 - 1/5 di quello della saldatura di testa, con conseguente riduzione dei costi.
3) Ampia applicabilità. È adatto non solo per i comuni metalli ferrosi e non ferrosi, ma anche per la saldatura di materiali speciali e materiali dissimili con differenze significative nelle proprietà meccaniche e fisiche a temperatura ambiente.
4) Buone condizioni di produzione. La saldatura ad attrito non produce scintille, archi luminosi o polvere, il che la rende facile da usare e riduce l'intensità di lavoro per gli addetti.
(2) Applicazioni della saldatura per attrito
Come metodo di saldatura a pressione rapido ed efficace, la saldatura per attrito è spesso utilizzata per la saldatura di testa di pezzi rotondi, aste e tubi. Può saldare pezzi solidi con diametri che vanno da 2 a 100 mm, mentre il diametro esterno dei tubi può raggiungere diverse centinaia di millimetri. È stata ampiamente utilizzata nella produzione di utensili, automobili, trattori, aste di trivellazione, centrali elettriche e macchinari tessili.
Poiché l'investimento iniziale per una saldatrice ad attrito è elevato, la saldatura ad attrito è adatta alla produzione su larga scala.
Saldatura per esplosione
La saldatura per esplosione è un metodo di saldatura a pressione che utilizza l'onda d'urto ad alta pressione (700 MPa), alta temperatura (3000℃) e alta velocità (500-1000 m/s) prodotta dall'esplosione di esplosivi per agire sul rivestimento, facendolo collidere violentemente con la piastra di base. In questo modo si crea un getto nel punto di contatto, che rimuove gli ossidi superficiali e altre impurità e forma un giunto allo stato solido ad alta pressione.
Come illustrato nella Figura 4-31, è possibile saldare per esplosione qualsiasi metallo che abbia una resistenza e una plasticità sufficienti e che possa sopportare la rapida deformazione richiesta dal processo. Il metodo può essere suddiviso in metodi paralleli e angolari in base ai diversi metodi di assemblaggio.
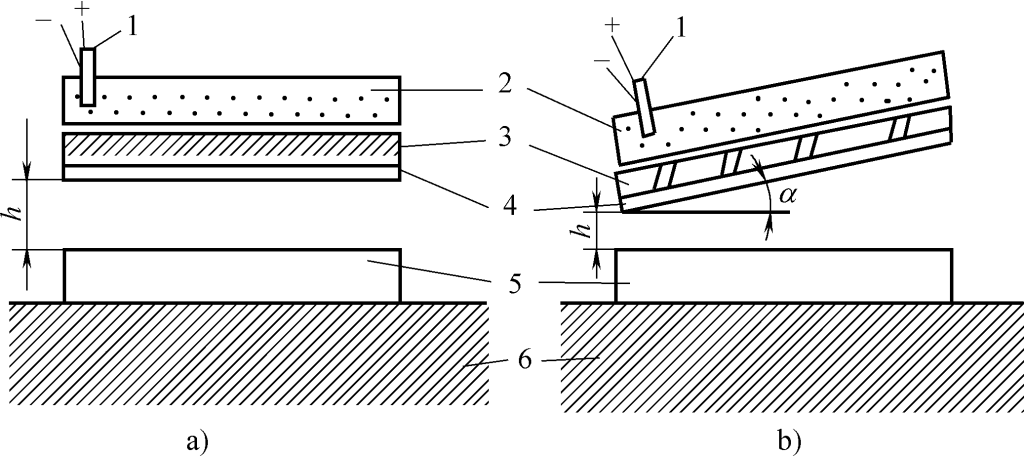
a) Metodo parallelo b) Metodo angolare
1-Detonatore
2-Esplosivo
Strato a 3 buffer
4-Rivestimento
5-Piastra di base 6-Fondazioni
La qualità dei giunti saldati per esplosione è buona, con una piccola zona colpita dal calore. È utilizzata principalmente per la saldatura di grandi piastre e tubi compositi, come alluminio-acciaio-rame, titanio-acciaio e zirconio-niobio, che non sono adatti ad altri metodi di saldatura.
Saldatura a ultrasuoni
La saldatura a ultrasuoni è una forma di saldatura a pressione che utilizza l'energia di oscillazione ad alta frequenza degli ultrasuoni per riscaldare e pulire localmente la giunzione dei pezzi, mentre la pressione viene applicata per ottenere la saldatura, come illustrato nella Figura 4-32.
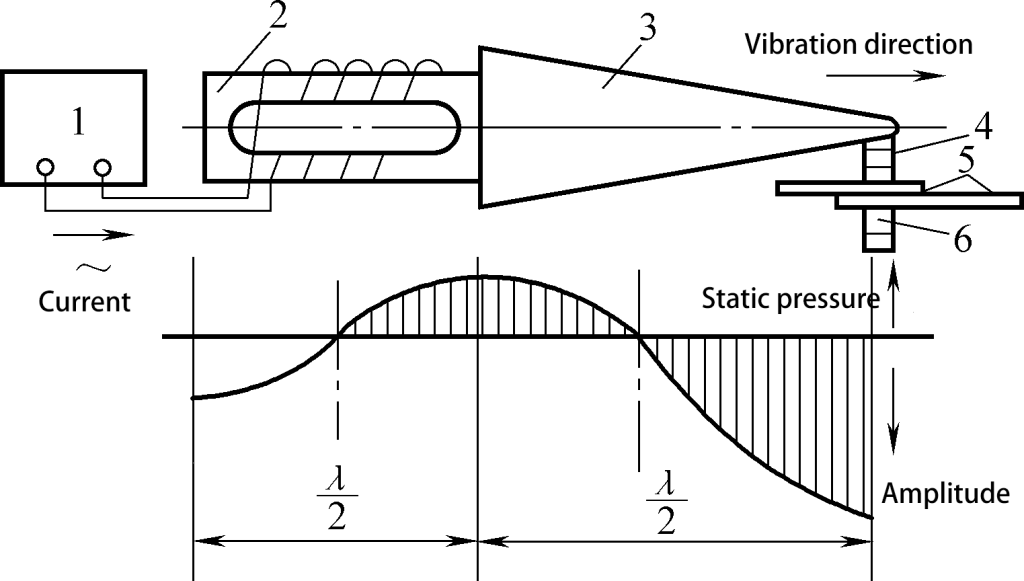
1 - Generatore di ultrasuoni
2 - Trasduttore
3 - Concentratore
4 - Polo sonoro superiore
5 - Saldatura
6 - Polo sonoro inferiore
Durante il processo di saldatura, le onde ultrasoniche generate dal generatore di ultrasuoni raggiungono il polo sonoro superiore attraverso una serie di fasi di conversione e trasmissione dell'energia. Sotto l'influenza dei poli oscillanti, nei punti di contatto locali dei due pezzi si verificano un intenso attrito, un aumento di temperatura e una deformazione che rompono o disperdono contaminanti come gli ossidi e avvicinano gli atomi di metallo puro per formare legami metallurgici.
Nel processo di saldatura a ultrasuoni non c'è corrente che attraversa i pezzi e non c'è l'influenza di fonti di calore come la fiamma o la luce ad arco. È un processo di saldatura che prevede una combinazione di attrito, diffusione e deformazione plastica. La saldatura a ultrasuoni può essere suddivisa in saldatura a punti a ultrasuoni e saldatura a cordoni a ultrasuoni.
La saldatura a ultrasuoni ha un'ampia gamma di materiali saldabili ed è particolarmente indicata per la saldatura di metalli ad alto punto di fusione, ad alta conducibilità termica, difficili da fondere e materiali dissimili, nonché per strutture speciali come quelle con notevoli disparità di spessore e lamine multistrato, come lamine d'oro da 2μm, conduttori di circuiti di dispositivi microelettronici e così via.
Può essere utilizzato anche per saldare materie plastiche come PVC, polietilene, nylon e plexiglass.
Brasatura
La brasatura è un metodo di saldatura che utilizza un materiale d'apporto metallico con un punto di fusione inferiore a quello del materiale di base. Il pezzo e il materiale d'apporto vengono riscaldati a una temperatura superiore al punto di fusione del materiale d'apporto ma inferiore al punto di fusione del materiale di base.
Questo processo utilizza il materiale di riempimento liquido per bagnare il materiale di base, riempire la fessura del giunto e diffondersi reciprocamente con il materiale di base. Una volta raffreddato, si ottiene un collegamento.
La brasatura è considerata un collegamento fisico, noto anche come brasatura. Il flussante utilizzato nella brasatura è chiamato flusso di brasatura, che serve a rimuovere ossidi e altre impurità dalle superfici dei materiali di riempimento e di base.
Ricopre le superfici del pezzo e del materiale d'apporto sotto forma di pellicola liquida, isolandole dall'aria per proteggere il materiale d'apporto liquido e il pezzo dall'ossidazione. Inoltre, migliora la bagnabilità del materiale d'apporto liquido sul pezzo e aumenta la capacità del materiale d'apporto di riempire gli spazi vuoti.
La differenza fondamentale tra la brasatura e gli altri metodi di saldatura è che i pezzi non si fondono durante il processo di saldatura. Il collegamento viene invece realizzato fondendo e riempiendo i pezzi con un materiale d'apporto che ha un punto di fusione inferiore.
Il processo di brasatura è suddiviso in tre fasi: bagnatura, spalmatura e giunzione, come mostrato nella Figura 4-33.

a) Bagnatura
b) Diffusione
c) L'adesione
1. Classificazione della brasatura
La brasatura può essere suddivisa in brasatura dolce e brasatura forte in base al punto di fusione del materiale d'apporto.
(1) Brasatura dolce
La brasatura dolce utilizza materiali d'apporto con punti di fusione inferiori a 450°C, che danno luogo a giunti con una resistenza inferiore, in genere compresa tra 60 e 190 MPa, e sono adatti a temperature di esercizio inferiori a 100°C. Questi materiali d'apporto hanno una forte capacità di penetrare negli interstizi dei giunti e presentano una buona lavorabilità in saldatura.
I comuni riempitivi per brasatura morbida includono leghe di stagno-piombo, note anche come saldature a stagno. Le leghe di brasatura a stagno sono altamente conduttive e vengono utilizzate principalmente per collegare i componenti dei circuiti elettronici. I flussanti utilizzati nella brasatura dolce comprendono principalmente soluzioni di colofonia e cloruro di zinco.
(2) Brasatura dura
La brasatura dura impiega materiali d'apporto con punti di fusione superiori a 450°C, ottenendo giunti con una maggiore resistenza, tutti superiori a 200 MPa, e in grado di sopportare temperature di esercizio più elevate.
I comuni riempitivi per brasatura dura includono leghe a base di alluminio, argento e rame, con disossidanti costituiti principalmente da borace, acido borico, fluoruri e cloruri.
2. Configurazioni dei giunti e metodi di riscaldamento nella brasatura
Le configurazioni di giunzione nella brasatura includono la sovrapposizione di lamiere, l'inserimento di manicotti e altre. Questi giunti sono caratterizzati da ampie superfici brasate, che garantiscono una buona capacità di carico.
I metodi di riscaldamento per la brasatura includono il riscaldamento a fiamma, il riscaldamento a resistenza, il riscaldamento a induzione, il riscaldamento in forno, il riscaldamento a bagno di sale e il riscaldamento con saldatore. La scelta del metodo di riscaldamento può essere determinata in base a fattori quali il tipo di materiale d'apporto, la forma e le dimensioni del pezzo, il numero di giunzioni, i requisiti di qualità e il volume di produzione.
Tra questi, il riscaldamento con il saldatore genera temperature più basse ed è generalmente adatto solo per la brasatura dolce.