
I.一般的なブランキング方法とその応用
板金加工に使われる材料の形状には、主に板材、形鋼、パイプ材などがある。板金部品に要求される形状などを加工するためには、まず原材料を必要に応じてブランクに切断する必要がある。この工程はブランキングと呼ばれ、板金加工の最初のステップとなることが多い。
ブランキングには多くの方法がある。生産に使われる主なものには、剪断、打ち抜き、切断、機械加工などがある。表1に一般的なブランキング方法とその用途を示す。
表1 一般的なブランキング方法とその用途
分類 | 方法 | 設備 | 申し込み |
シャーリング | 手動シャーリング | ハンド鋏、ハンドヘルド振動鋏、手動ギロチン鋏 | 低炭素鋼、アルミニウムおよびその合金、銅およびその合金、厚紙、ベークライト、厚さt≦4mmのプラスチックシートなどの板材の直線および曲線加工に使用される。加工部品の精度や生産効率は低いが、コストは低い。 |
マシンストレートシャーリング | ギロチン鋏 | 低炭素鋼、アルミニウムおよびその合金、銅およびその合金、段ボール、ベークライト、プラスチックシートなどの材料のせん断に使用されます。剪断力が強く、生産性が高く、板材の直線形状加工に使用される。 | |
斜め鋏 | 低炭素鋼、アルミニウムとその合金、銅とその合金、段ボール、ベークライト、プラスチックシートなどの材料のせん断に使用されます。剪断力が弱く、中・大型の直線形状、大きな円弧、板材の面取りなどに適しており、剪断厚さは40mmまで。 | ||
小段シャーリング | 振動鋏 | 低炭素鋼、アルミニウムとその合金、銅とその合金、厚紙、ベークライト、プラスチックシートなどのせん断に使用。複雑なカーブ、ミシン目、ノッチに適しており、チタン合金のせん断も可能。 | |
ディスクローリング鋏 | 直円ローリング鋏 | 低炭素鋼、アルミニウムとその合金、銅とその合金、段ボール、ベークライト、プラスチックシートなどの材料のせん断に使用。比較的精度の低いストリップ、直線、円弧のせん断に適しています。切り口にはバリがあり、小・中型部品の小ロット生産に適し、剪断厚さは30mmまで。 | |
斜め下ローリング鋏 | 直線と円弧(Rは小さい)を、比較的低精度で、切り口にバリをつけながら、最大30mmの厚さで剪断する。 | ||
フルスラント・ローリング・シャー | 複雑なカーブで比較的精度が低く、切断端にバリがあり、剪断厚さは最大20mm、精度は±1mm。 | ||
パンチング | パンチング | プレス | 一般的にt≤10mmのシート材やプロファイルのブランキング、パンチング、切断、ノッチングに使用されます。高精度(ブランキングIT10、パンチングIT9)、高生産性、中規模および大規模バッチ生産に適しています。 |
カッティング | フレームカット | ガス切断機、トーチ | 純鉄、低炭素鋼、中炭素鋼、および一部の低合金鋼でできた板や形材のブランキングとトリミングに使用でき、精度は±1mm、コストは低い。 |
プラズマ切断 | 切断機、トーチ | 炭素鋼、ステンレス鋼、高合金鋼、チタン合金、アルミニウムおよびその合金、銅およびその合金、非金属材料などの形状切断に使用され、切断幅は狭く、厚さは200mmまで、精度は±0.5mmで、水中切断も可能。 200mm、精度±0.5mm、水中切断も可能。 | |
カーボンアークガウジング | DC溶接機、ガウジング用トング | 高合金鋼、アルミニウムおよびその合金、銅およびその合金などの材料の切断、トリミング、面取り、大きなバリの除去に使用。 | |
放電ワイヤー切断 | 放電ワイヤー切断機 | 様々な導電性材料の精密切断に使用され、切断厚さは300mmを超え、精度は±0.01mm。平坦な曲線や側壁勾配30°以下のあらゆる形状の切断が可能で、特にプレス金型製造に適している。 | |
レーザー切断 | レーザー切断機 | 様々な材料の精密切断、切断厚さ10mm以上、切断幅0.15~0.5mm、精度0.1mm以下、しかし高価な設備。 | |
高圧水切断 | 超高圧 (≥400MPa) ウォータージェット切断機 | 様々な用途に使用可能 金属 非金属(ガラス、セラミック、岩石など)、人工砥粒を装備することができ、高精度、10mm以上の厚さのセラミックを切断することができます。 | |
カッティング | 手動操作 | ボウソーマシン | 様々なプロファイル、ロッド、パイプ、プレート、およびその他の金属/非金属材料の切断に使用され、溝や硬い材料を見ることができます。 |
ハンドヘルド・パワー・ソー、ハンドコントロール・ソー | 非硬化金属および非金属の各種プロファイル、ロッド、パイプ、シートの加工に使用。 | ||
電動パイプ切断機 | 直径φ200~φ1000mmの金属およびプラスチックパイプの加工に使用されます。 | ||
パイプ切断フレーム | 小・中口径パイプの加工 | ||
手動砥石切断機 | 各種金属、非金属(非鉄金属、ゴム、プラスチック材料を除く)の形材、棒材、管材の加工 | ||
工作機械の操作 | 鋸盤 | 非硬化金属のプロファイル、ロッド、パイプ材、プラスチック、木材の加工、高生産性 | |
エッジフライス盤、プレーナー | 非硬化金属の形材、棒材、パイプ材、プラスチック、木板などの切断、トリミング、面取り、その他の加工に使用。 | ||
板金フライス盤、フライス盤 | 非硬化金属のプロファイル、ロッド、パイプ材、プラスチックや木製の板材を高精度で切断およびトリミングするために使用され、複雑な曲線を切断することができます。 | ||
旋盤、中ぐり盤 | 様々な材質の棒材やパイプ材の切断、面取り、トリミングに使用され、加工精度が高い。 |
切断方法は、会社の既存の加工設備、生産能力、加工される板金部品の精度要件、生産バッチ、加工経済性に応じて選択されるべきであることに留意すべきである。
上記の一般的な切断方法のうち、生産現場で最もよく使用されているのは以下の方法である。 剪断機パンチング、オキシアセチレン火炎切断、プラズマ切断、レーザー切断、およびいくつかの切断加工。図1aおよび1bは、手動切断に使用される一般的な手持ち空気鋸および砥石切断機を示す。図2は、一般的な工作機械による弓のこ切断機である。
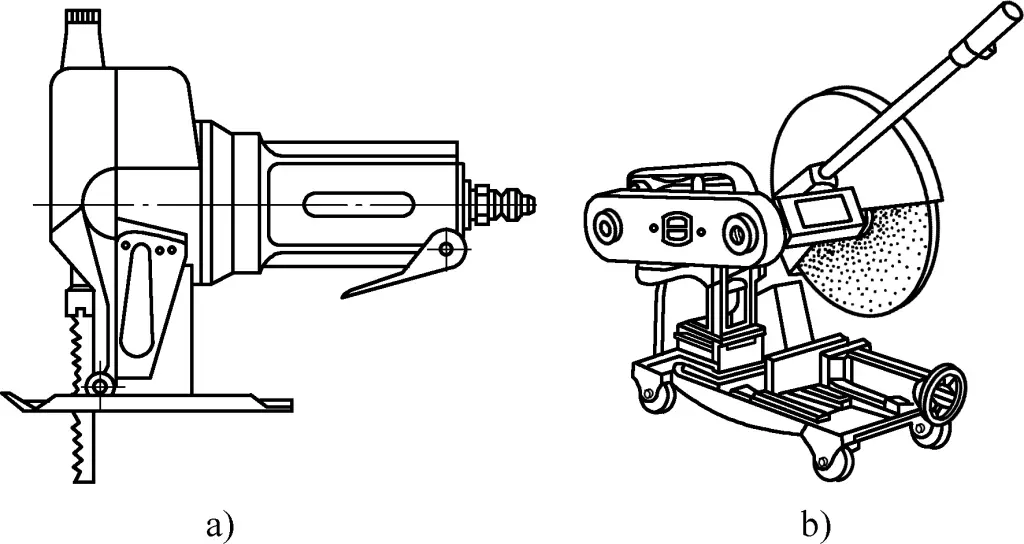
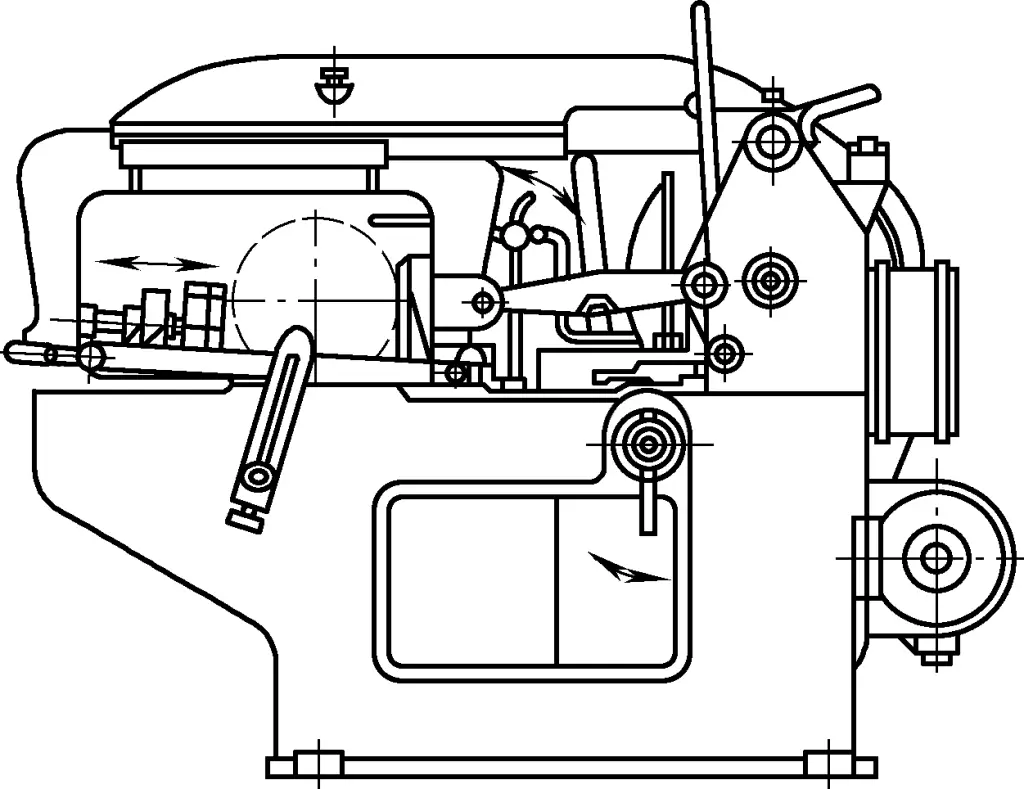
II.シャーリング
シャーリングとは、専用のシャーリング装置や工具を用いて、板材、形材、棒材などをあらかじめ決められた直線や曲線に沿って切り離し、様々な直線や曲線の外形(場合によっては内形)を得る加工方法である。焼入れ鋼や硬脆性材料(鋳鉄、セラミックス、ガラス、超硬合金など)を除くあらゆる材料に適している。
1.手作業による剪断技術
手作業による剪断は、送り、余分な材料の除去などを含む板金技術の重要な部分である。薄板部品のほとんどすべての形状を手動でシャーリングすることができます。手作業によるシャーリングは、ほとんど制約がなく、柔軟で便利です。
(1) 手動シャーリング用工具
手作業で剪断するための道具には、直線鋏、曲線鋏、空気圧式直線鋏、空気圧式パンチング鋏などがある(図3参照)。

a) ストレートシザース
b) カーブドシザーズ
c) 空気圧式直線はさみ
d) 空気圧パンチングシャー
ストレートシザーは、刃先が直線状になっている手動の鋏で、板材の外形を直線状に切断するのに使用され、厚さ1.5mmまでのアルミ板、厚さ1mmまでの鋼板を切断することができる。カーブシザーズは、刃先がカーブしており、板材の外形をカーブさせながら切断するもので、厚さ2mmまでのアルミ板、厚さ0.8mmまでの鋼板を切断できる。ポータブル・ニューマチック・シアーは、半機械化されたハンド・シャーで、2.5mm厚まで切断できる。
(2) 手動シャーリング作業
1) 手動シャーリングの技術
一般に、薄い板を手で剪断する場合、右手で鋏を持ち、左手で材料を持つのが通例である。図4はハサミの正しい持ち方を示したもので、ハサミの柄は手のひらからあまり長く出さない方が力を入れやすく、また、右手で握るのに不便にならないように尾端は手のひらの内側に入れないようにする。
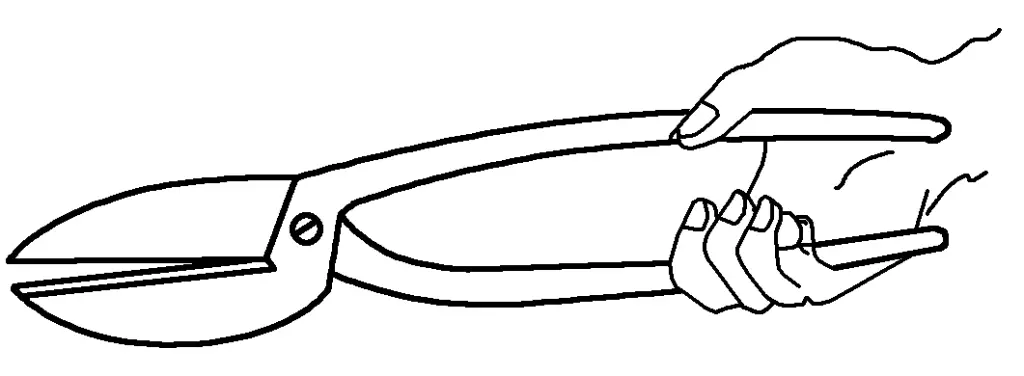
左手は材料を持ち、剪断方向へ送り、上刃を剪断線(直線または曲線の接線)に合わせる。剪断の際、上刃は材料を強く押さえる必要があり、図5のように力を入れやすいように刃の角度を調整する。
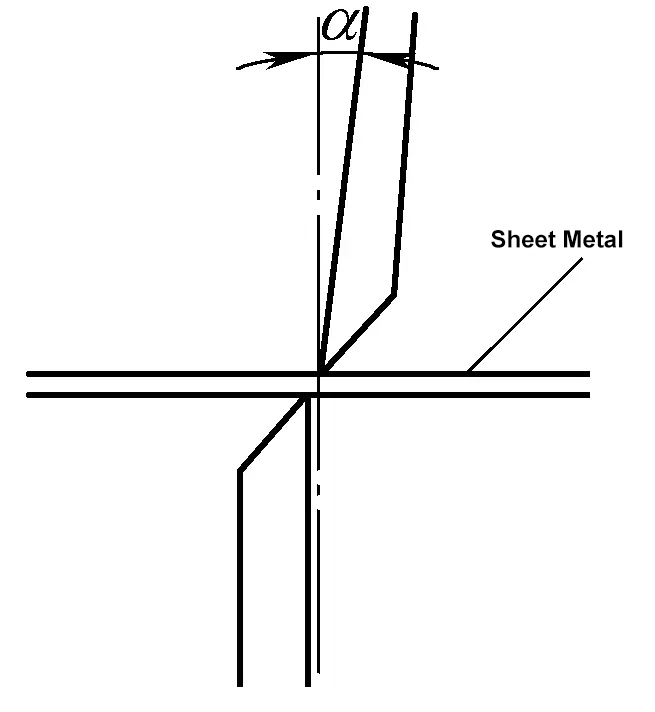
剪断の始めは、2枚の刃が刃渡りの3/4までしか開かないようにする。各カットの終わりには、刃は完全に閉じず、刃の長さの1/4を残す。言い換えれば、ハサミは、図6に示すように、刃渡りの1/4の位置から3/4の位置まで部分的にしか開閉せず、各切断の長さは刃渡りの約1/2とする。
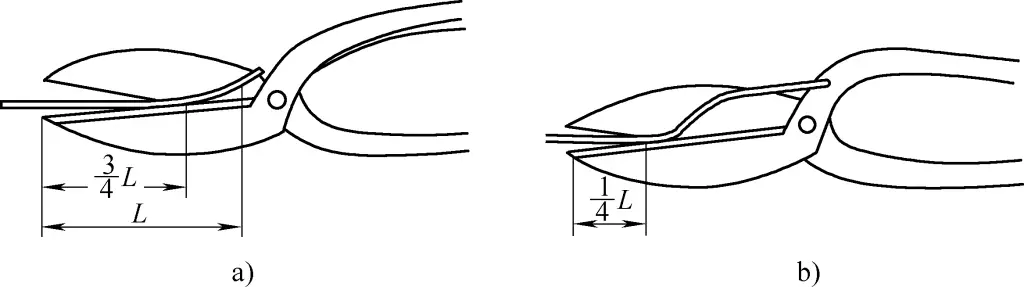
a) シャーリング開始
b) せん断端
刃を閉じる際には、切断線に沿って圧力をかけ続け、刃先が重なるようにする。図7に示すように、2枚の刃の間には0~0.2mmのギャップを維持し、薄い材料ほど小さく、厚い材料ほど大きくする。
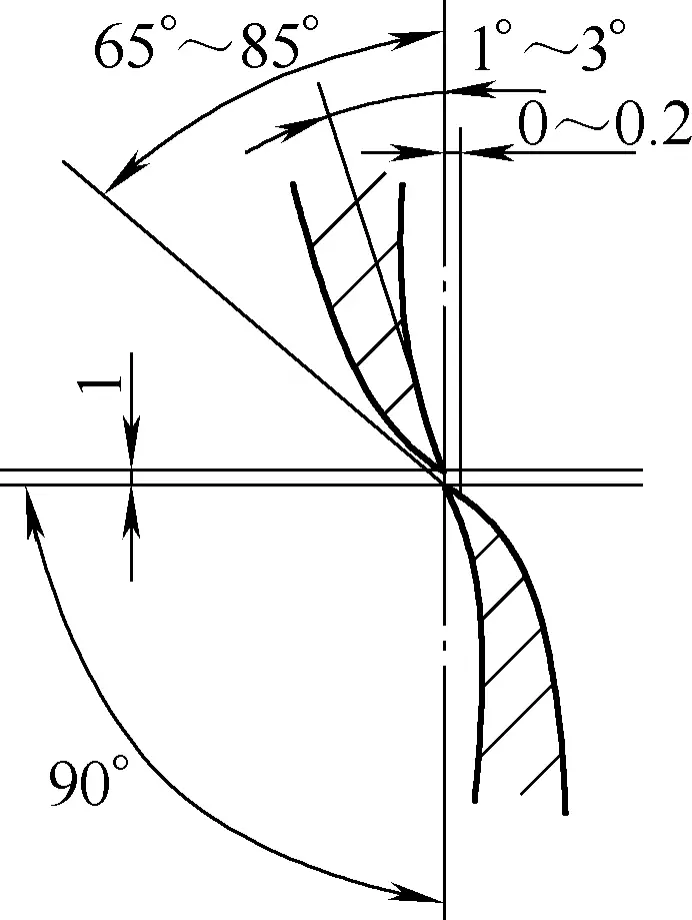
2) 直線の切断方法
図8aと図8bはそれぞれ、直線を切る際の正しい方向と間違った方向を示している。
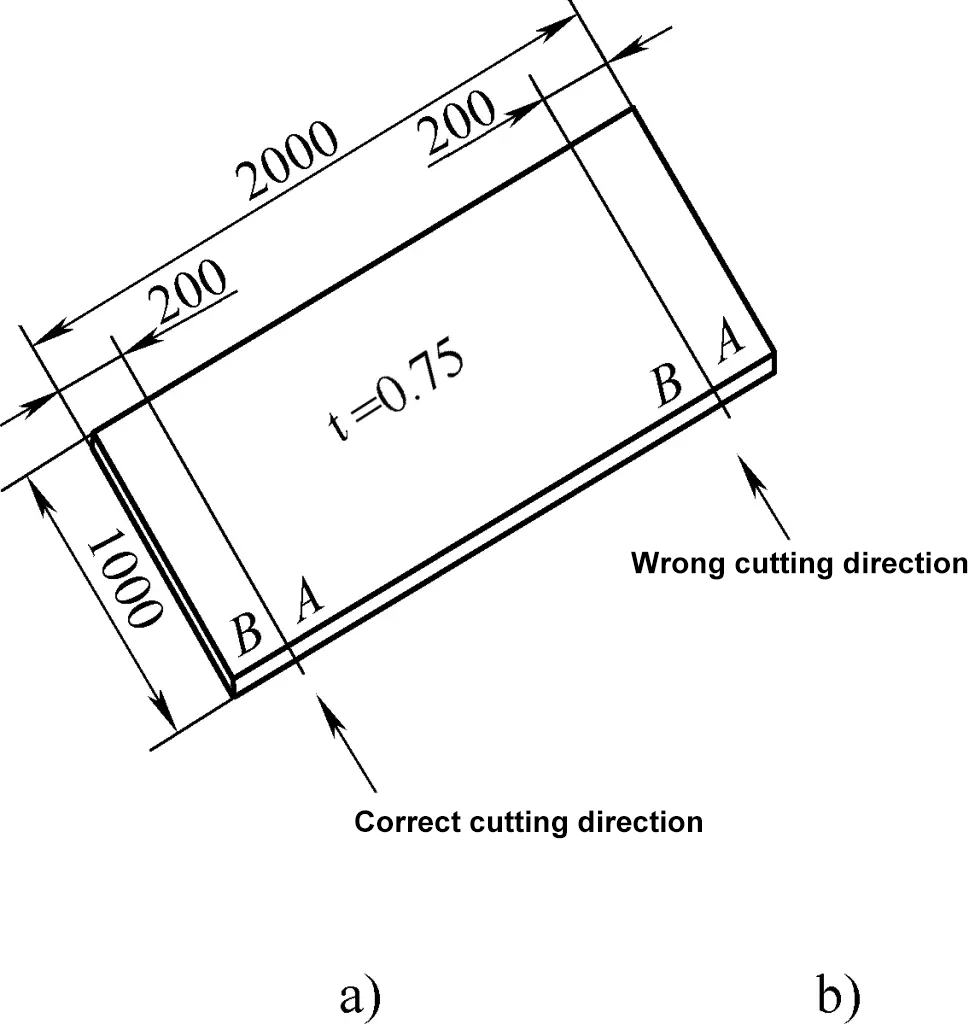
図8aは正しい方向を示している。切断中、右手はハサミ本体を持ち、右足はA点を踏み、左手はB点を持つ。切り口が深くなるにつれて、左手を持ち上げて切断点を引き裂くのを補助し、下のハサミ本体を置くスペースを作る。プレートBは小さいので簡単に持ち上げることができ、正しい方向となる。一方、図8bでは、B点の面積と重量が大きいため、材料を持ち上げにくく、深く切ることが難しいため、正しくない方向となる。
3) 凹角材と角材の切断方法
板金上の切断線がワークピースに対して凹形状、いわゆる凹角を形成する場合、凹型の切断線の交点に割れ止め穴を開けるか、一定の距離を切り残さなければならない。
クラックストップ穴を開ける目的は、切断時に両側の切断線の端部位置がクラックストップ穴の上に収まるようにすること、あるいは一定の距離を切り残し、剪断端がワークの交差部に跡を残さないようにして応力集中点を防ぐことである。
一般的には、切断線の交点に一定の距離を切り残 し、その接続部分を手で切断し、最後にヤスリで必要な 形状と寸法に仕上げる。斜め形状の部品を切断する場合は、図9に示すように、まず根元をノコギリで切断し、その後、ハサミでラインを切断することができる。
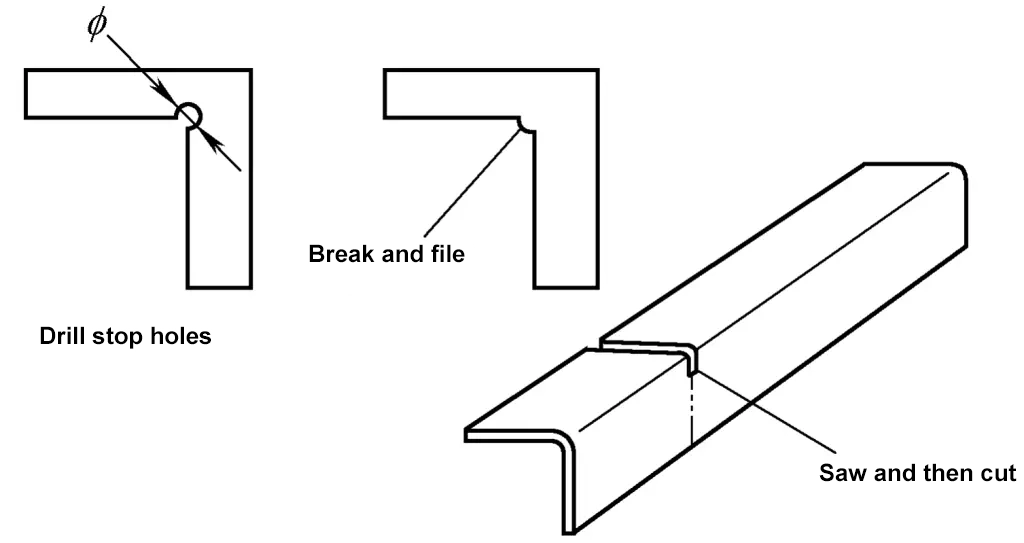
4) カーブのカット方法
切断線が曲線の場合、ハサミの移動方向は、図10に示すように、作業者が上刃を曲線に接するようにコントロールできるように、切断線を覆わずに曲線に沿わせる。
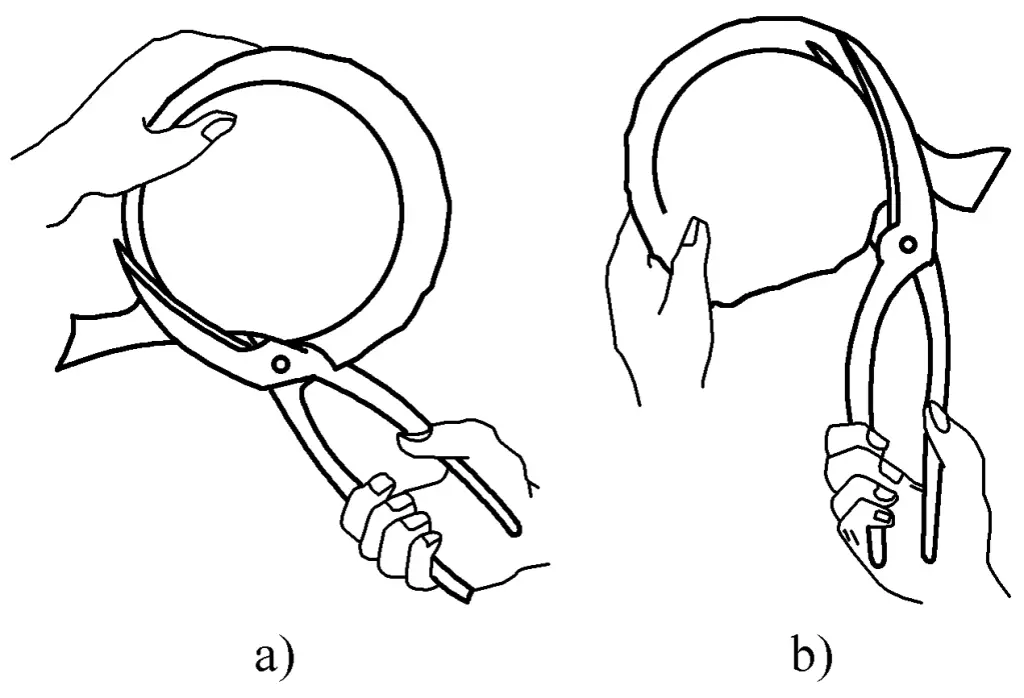
a) 時計方向
b) 反時計回り方向
内孔の切断方法は、まず板金に加工孔を開け、切断線に沿って湾曲したハサミで螺旋状に徐々に拡大していく。大きな内孔の場合は、振動せん断切断が望ましい。
(3) よくある切断不良とその対策
板金の切断作業では、不完全な切断、寸法の狂い、切断線の途切れや非直線性、切り口、過度のバリなどの問題がしばしば発生します。以下では、これらの問題を分析し、対応する解決策を提供します。
1) 不完全な板金切断
不完全切断の主な理由は以下の通りである:
上ブレードと下ブレードの隙間が大きすぎる。板金の厚みによって適した隙間は異なります。隙間が小さすぎると刃の摩耗や切削力の増加につながり、逆に隙間が大きすぎると材料がめくれたり、切削が不完全になったりします。解決策は、ブレードの隙間を適切に調整することです。
図11はギャップを調整する方法を示す。図11aでは、間隙を狭める方法は、リベット・ヘッドの端を叩き、鋏の凸ワッシャに圧力を加え、いくらかの金属を下方に移動させ、刃の間隙を狭めることである。過剰な力を使わないでください。通常、縁の周りを2~3回軽く叩くだけで十分です。
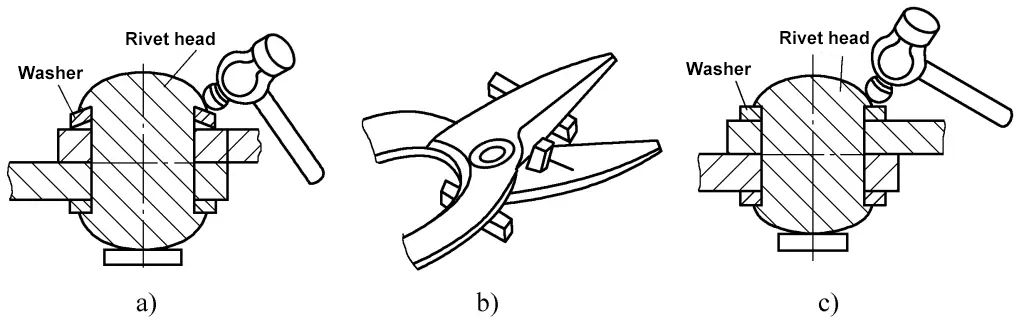
図11bの場合、隙間を広げる方法は、片方の刃とハンドルの下に固定サポートを置き(ピボットに近いほど良い)、もう片方の刃を叩く(これもピボットに近いほど良い)。力を入れすぎず、通常は2~3回軽く叩くだけで十分です。
凸型ワッシャーが平らになっている場合(図11cに示すように)、いくらハンマーで叩いても隙間は調整できない。この場合の解決策は、リベットと凸ワッシャを交換することである。
刃が鈍い。刃を研げば解決する。
板金が厚く、手切りの範囲を超える。
2) 切削加工における寸法偏差
寸法の狂いの主な原因は、ハサミの上刃がシートメタルの切断線と合っていないことです。直線的な切断線の場合は、上刃を合わせ、線に沿って押さえる必要がある。曲線の場合、ハサミは引かれた線を覆わないようにし、上刃は板金を押し、切断中は線に接するようにする。
3) 中断線と非直線切断線
これが原因だ:
連続カット中にハサミとシートメタルの接続が緩くなる。上刃をラインに合わせ続けることで、この現象を防ぐことができる。
長期間の使用により刃が曲がり、外向きまたは内向きに湾曲する。刃をまっすぐにするか、ハサミを交換することで解決する。
4) カット
切断不良の主な理由は以下の通りである:
ワークの凹角部にクラック・ストップ・ホールを開けなかったり、せん断がラインを超えてしまい、切り残しが応力集中点となり、最終的に様々なクラックにつながる。唯一の解決策は、クラック・ストップ穴を開けるか、必要に応じてファイリング・マージンを残すことである。
上刃と下刃の隙間が小さすぎて、切断中に刃全体が閉じて部品を挟んでしまう。解決策としては、ブレードギャップを調整し、切断中にブレードが完全に閉じないようにし、ブレードの長さの1/4を残してさらに切断することです。
5) 過度のバリ
バリ過多の主な原因は以下の通りである:
ブレードのギャップが不適切で、大きすぎたり小さすぎたりして、大きなバリが発生している。ギャップを調整し、何度かテストカットして最適なギャップを見つけるのが解決策。
刃のくすみ。刃がくすんでいるとバリが出やすくなるため、定期的に刃を研ぐことで品質や加工効率が向上します。
(4)切断作業時の注意事項
板金の切断時には、以下の点に注意すること:
1) 薄いシートメタルの手動切断では、ブレードを最も効果的な切断位置に維持するため、ブレードの切断面をシート表面に対して垂直に保つ必要があります。切断面をシート表面に対して傾けることは、過度のバリや不完全な切断、あるいはブレードのピボット面の間にワークピースを挟み込む原因となるため、禁止されています。
2) 刃が被切断物に加える切断力は、連続的で滑らかでなければならない。厚いシートを切断する場合、切断力を上げるためにハサミの背をハンマーで叩くと、刃先が傷ついたり、カーブが折れ線に変わったりして、切断品質に影響するので避ける。代わりに、スチールパイプを取り付けるなどしてハサミの柄の長さを長くし、切断力を高める。
2.手作業による鑿打ち技術
手作業による切断と同様、手作業によるチゼリングも板金切断の重要な技能であり、一般的に3mm以上の厚板を切断する際に使用される。チゼリングは、チゼル工具とスレッジハンマーを使って行われる。
チゼリングは、チゼル刃の切削運動を利用してワークを加工する。手動チゼリングの最大の特徴は、作業位置や部品の形状に制限されず、操作が簡単で柔軟性があることです。
(1) 手工具
よく使われる 手工具 - 図12に示すように、上ケジと下ケジに分けられる。このうち下ケジは通常、鋏の刃の廃材や鉄のレールを加工して作られる(図12b参照)。
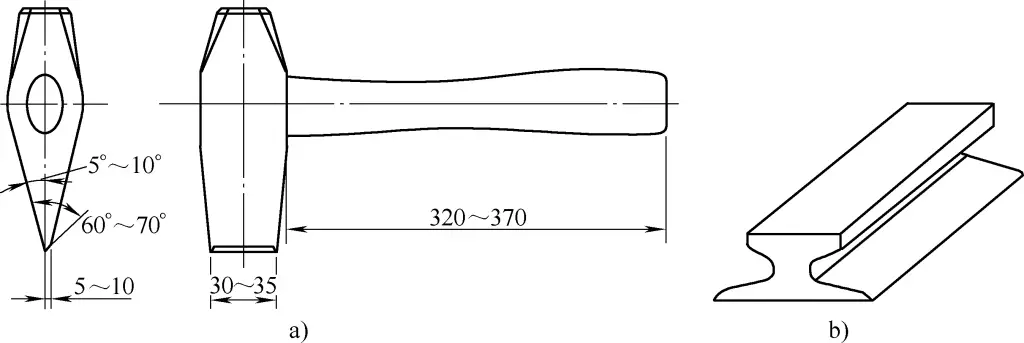
a) アッパー・ケジの寸法
b) 下のケジ
上ケジの刃部は左右非対称のくさび形をしている。切断時、刃先の左側(図12a参照)がブランクの部分となり、右側が屑の部分となる。上部のハンマリング力により、ケジの刃先はケジ軸に沿って部品材料に食い込む。
ブレードの先端が板金のほとんどに食い込むと、非対称のくさび形ブレードの屑側の大きな絞り力により、ブレードの先端が板金の底に到達する前に、板金はブレードの先端線に沿って引き裂かれ、材料が分離する。
図12aに見られるように、ケージの刃先の断面は一般的な工具とは異なっている。厚く広い刃先は、ケジが大きな衝撃力を受けても変形したり折れたりしないようにし、硬くて脆い材料に刃先が食い込んで折れたり飛び出したりして怪我をするのを防ぎます。これは主に、材料(特にシートメタル)を分離するというケージの機能を保証するものです。
(2) ハンド・カット・テクニック
ワークピースにハンド・カッティングを施す前に、まず部品図に慣れ、ワークピースの形状と寸法を理解する必要がある。選ぶケジは、図12aに示すように、柄の長さが約320~370mm、刃の厚さが約5~10mmのものである。
手切りをするときは、手のひらを下に向け、ケジ柄の端から30~40mmほど離して持つ。
裁断は2人で行う。ケジの柄を持つ人が両手でしっかりと握り、ケジを少し斜めにする。刃先を板金の線に合わせたら、ケジをまっすぐにし、少し直立させ、刃先に集中する。そして、もう一人がハンマーでケジの上部を打ち、打撃がまっすぐで正確であることを確認する。台の上で印のついた鋼板を切るときは、ケジの柄を持つ人はしゃがみ、やや前傾姿勢になるが、頭はまっすぐに保ち、やや後ろに下がる。
前傾姿勢は、柄を垂直に安定させるのに役立ち、頭を少し後ろに下げることで、ラインの観察、アライメントを容易にし、ハンマーの使い手による偶発的なミシットを避けることができる。左足は、図13に示すように、ふくらはぎを地面に対して垂直にし、大腿部を両腕の間に挟むようにして、わずかに前に踏み出す。
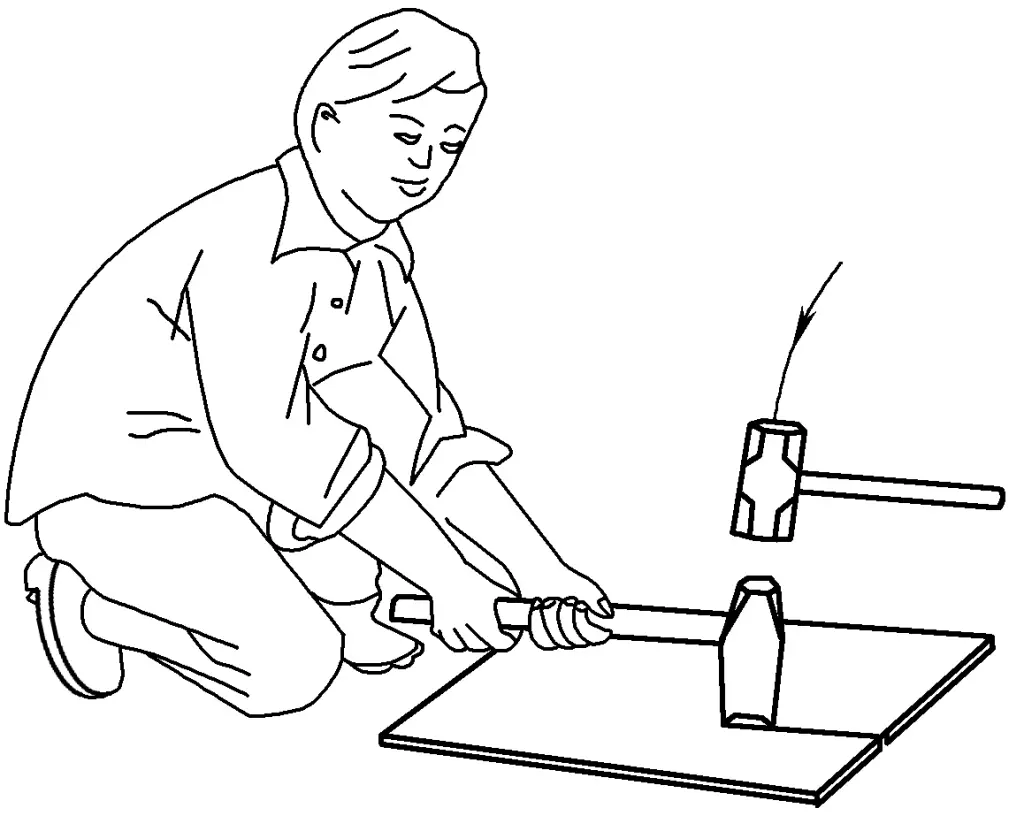
切断中、ケジがシート・メタルに完全に押し込まれないようにしながら、ケジ・ブレードの前端を作業ラインに合わせる。切断はシートメタルの端から開始し、ケジ刃の1/3がシート端からはみ出し、下側のケジ刃と位置が合うようにする。
シートの端が切断されたら、刃をラインに合わせ、下に向かって切断を続ける。この時、刃の後端を10°~15°上方に傾けることで、図14に示すように、ラインの観察が容易になり、ケジの前部に打ち込み力が集中し、シートの連続切断が確実になる。
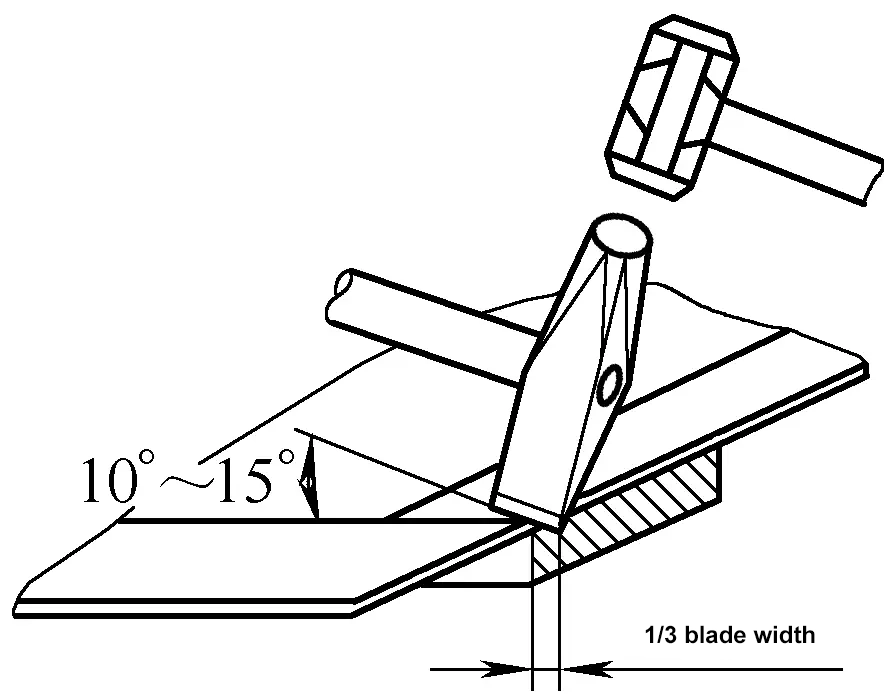
ケジの上部をハンマーで叩いた後、刃の後端を素早く上方に傾け、刃の前端を切断溝に沿って後方にスライドさせ、切断線が完全に終わるようにする。カットが終わりに近づいたら、刃や台の表面を傷つけないよう、やさしくハンマーで叩く。
切断の際、刃先側の作用で板金が横方向に曲がったり、局部的な押し出しで反ったりするので、切断後の板金には平らに修正する必要がある。
切断作業終了後は、速やかに作業場を清掃してください。
(3) ハンドカッティングの手順と方法
切断する板金部品は多種多様であるが、切断工程のステップと方法は一般的に同じである。以下、一例を通して、手切断のステップと方法を詳細に説明する。
図15に示すワークは、厚さ4mmのQ235A鋼板から作られている。切断後、内孔の角が割れてはならない。切断の手順と方法は以下の通りである:
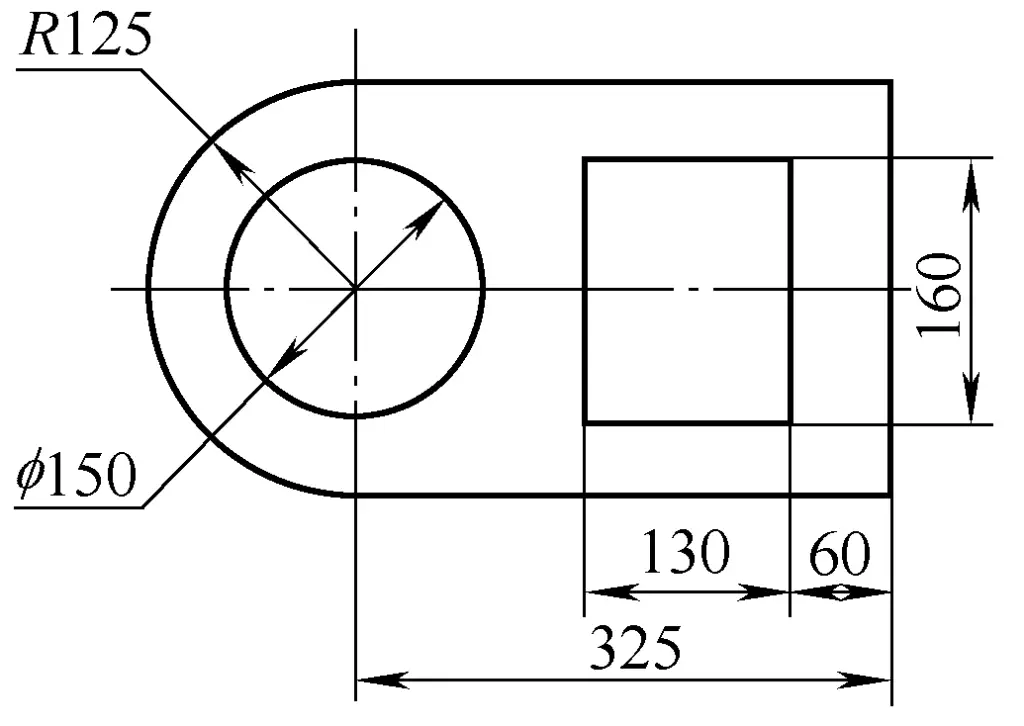
1) マーキング
加工するシートメタルを準備し、マーキング用のテンプレートを使用するか、シートメタルに1:1の縮尺でパターンを直接描く。正確な位置合わせを容易にするため、まず切断開始点を決め、図16に示すように、板金の端に開始線を引き、下ケジ刃に合わせる。
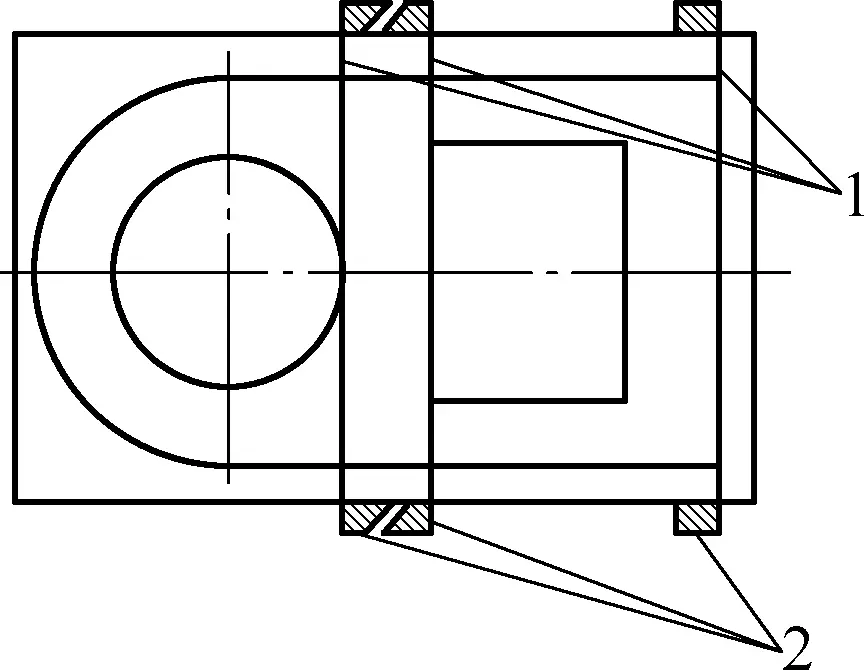
1-スタートライン
2-下ケジブレード
2) カット順序の決定
ワークのパターンを分析し、切断順序を決定する。一般に、切断順序は、外形が先で、次に内孔、直線が先で、次に曲線、部品全体が先で、次に断面である。図15のワークの切断順序は、図17のように配置される。
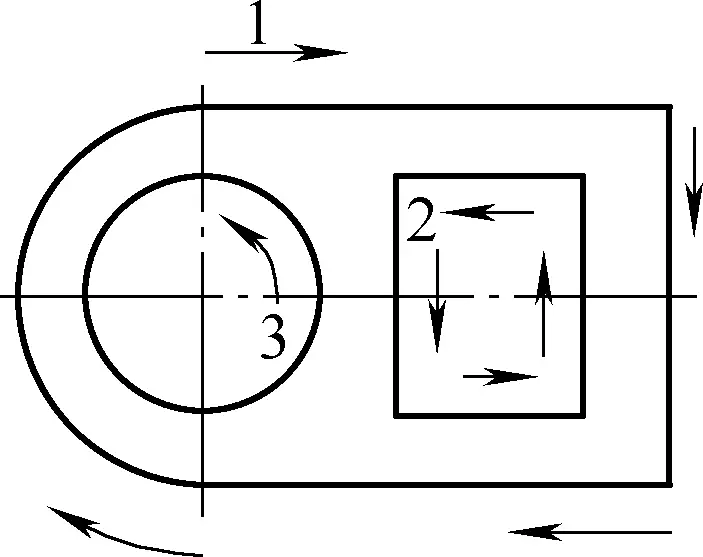
3) 直線部の切断
直線部分の切断方法は以下の通り:
カットを開始します。
余分な材料がカッティング・エッジからはみ出るようにして、シートを下側のカッティング・エッジに平らに置き、カッティング・ラインが下側のエッジと一致するように正確に合わせる。カッターの位置と角度は図14の通り。
切り始めの打ち込み力は、切り始めが正確でない場合に調整できるよう軽めにし、刃先の衝突による損傷を防ぎます。スタート・カットが正確であることを確認したら、下側のカッターの刃先に沿って、段階的に直線的なカットを進めます。
カッティング。
カッティング・プロセスでは、シートのカッティング・ラインが下側のエッジと一直線になるようにし、上側のカッターで適切な角度を保ち、2 つのエッジを近づけます。これを怠ると、図 18 に示すように、切断が不完全になったり、曲げ変形が生じたりすることがあります。
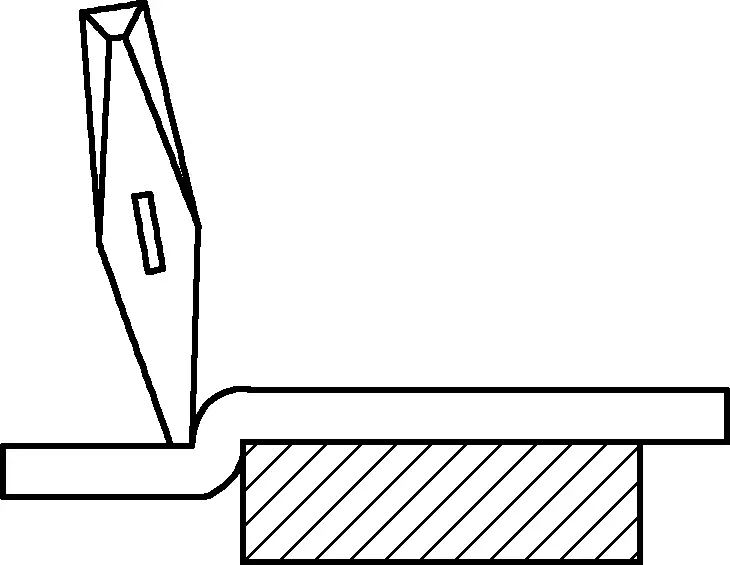
切断時の品質を向上させるには、常に偏差を修正し、ハンマーの力を調整する必要があります。このため、オペレーターは常に観察し、カッターホルダーの指示にハンマーが従うよう、綿密に調整する必要があります。
4) 曲線の切断
曲線部分の切断方法は
カットを開始します。
切断が曲線部に達する場合は、干渉を避けるため、まず完成した直線部から余分な材料を切り落とす。変形を最小限に抑えるため、円形部分を下端に置き、常に下端の端を切削に使用しながら、ワークを連続的に回転させる(図19参照)。
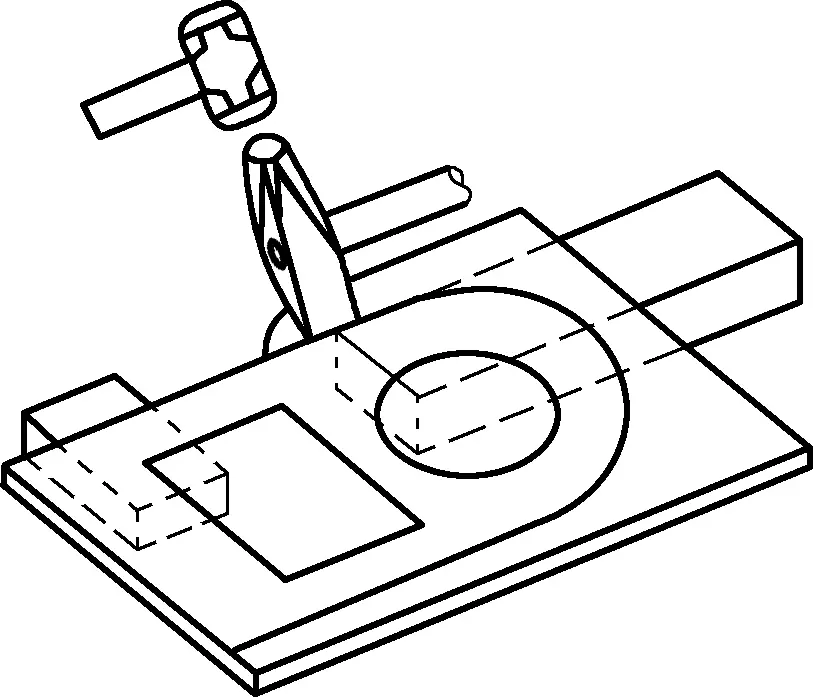
カッティング。
カーブをカットする場合、上辺も下辺も直線であるため、各カットで作成されるのはセグメントのみである。曲線の切断の本質は、曲線の接線に沿ってまっすぐなセグメントを切り出し、曲線に近い多角形を形成することである。セグメントが短ければ短いほど、曲線に近くなる。
カーブのカットに必要なのは、1回のカットを最小限にとどめ、シートを頻繁に回転させることである。
5) 内部角穴の切断
内角穴の正確な開口部を確保するため、図 20 のように位置合わせを行う。カットを開始するには、シートとの接点で上端を軽く叩く。最初のカットがエッジ幅の2~3倍に達したら、上エッジを平らにし、完全に切り抜く(図21参照)。開口後の切断方法は、直線部と同じである。
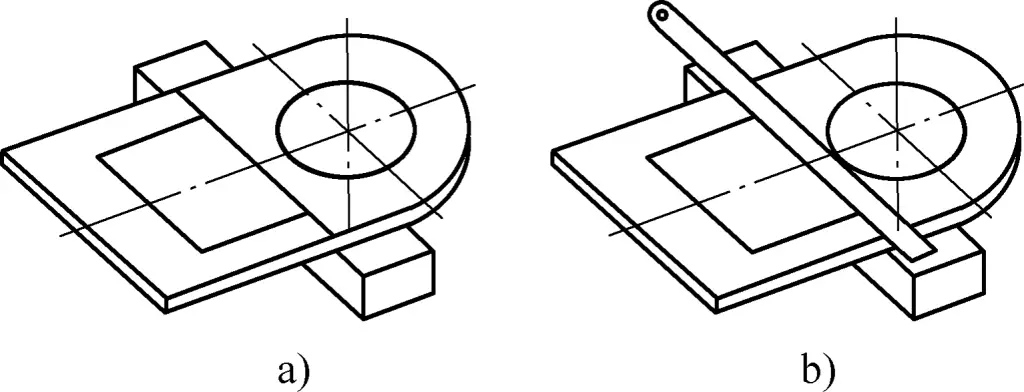
a) スクライブラインによる位置合わせ
b) ストレート・エッジ・オーバー・ラインによる位置合わせ
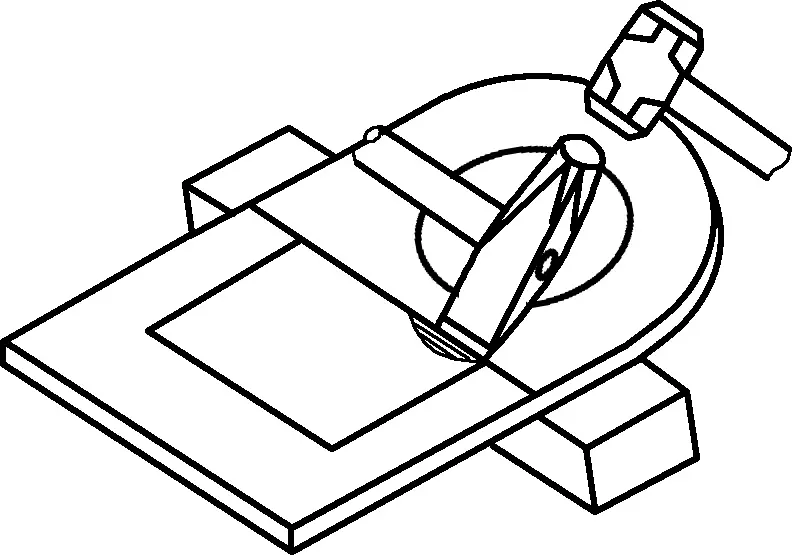
6) 内丸穴加工
内部円形穴の切断では、まず開始点を選ぶ。切断を開始しやすいように、クランプしやすい点を選択し、この点の接線を下端に合わせる(図22参照)。切断方法は曲線部と同様である。
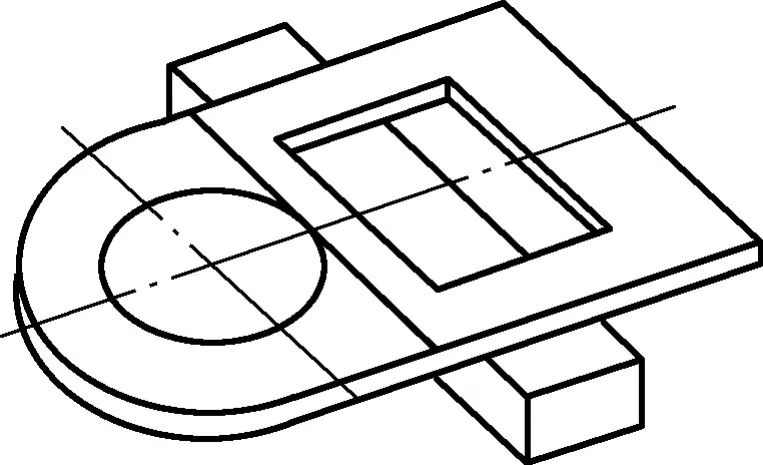
(4) 手動切断作業における注意事項
手作業による裁断では、もう一人の人間がカッターの上部をスレッジハンマーで叩くことで裁断力を加える。ハンマーがカッターに接触する瞬間、ハンマーとカッターの中心線がシートの平面に対して一直線になり、垂直になるようにする。
ハンドルホルダーの姿勢は正しく、グリップは安定し、カッターの位置合わせは素早く正確でなければならない。ハンマー打ちは、両者が集中し、協調しながら、まっすぐ正確に打たなければならない。
切断中に歩行者がいないか周囲を確認する。精度と安定性が確保されるまでハンマーの高さを低くして開始し、その後ハンマーの高さと力を上げる。
手袋を着用すると触覚フィードバックが低下し、グリップを失い、事故につながる恐れがある。怪我を避けるため、バリ取り、ワークピースの取り扱い、余分な材料の取り扱いには手袋を着用すること。
スレッジハンマーとカッターの締め付けを頻繁にチェックし、長時間の使用によるハンドルの緩みを防ぐため、ハンドルがくさびで固定されていることを確認する。また、ハンマーによる破片の飛散による怪我を防ぐため、カッターの先端を研ぎ、バリを取り除く。
ワークピースが折れそうになったら、刃先や表面を傷つけないように、そっと切るか、ハンドハンマーを使用してください。
3.機械的剪断技術
メカニカル・シャーリングは、特殊な装置を使用してシートを切断・分離するもので、その高い効率と精度のためにシートメタル切断に広く使用されている。
(1) 機械式シャーリング装置
機械式剪断装置には、ギロチン剪断機、振動剪断機、回転剪断機などがある。
ギロチン・シャーは、主にシートを直線に切断するために使用され、上下の剪断刃に直線刃を使用する原理で作動する。
図 23 はギロチンシャー原理図である。上刃(8)は刃ホルダー(1)に、下刃(7)はテーブル(4)に固定されている。ボール(6)がシートの移動を容易にし、後部ゲージ(9)は位置決めピン(10)によって位置決めされる。
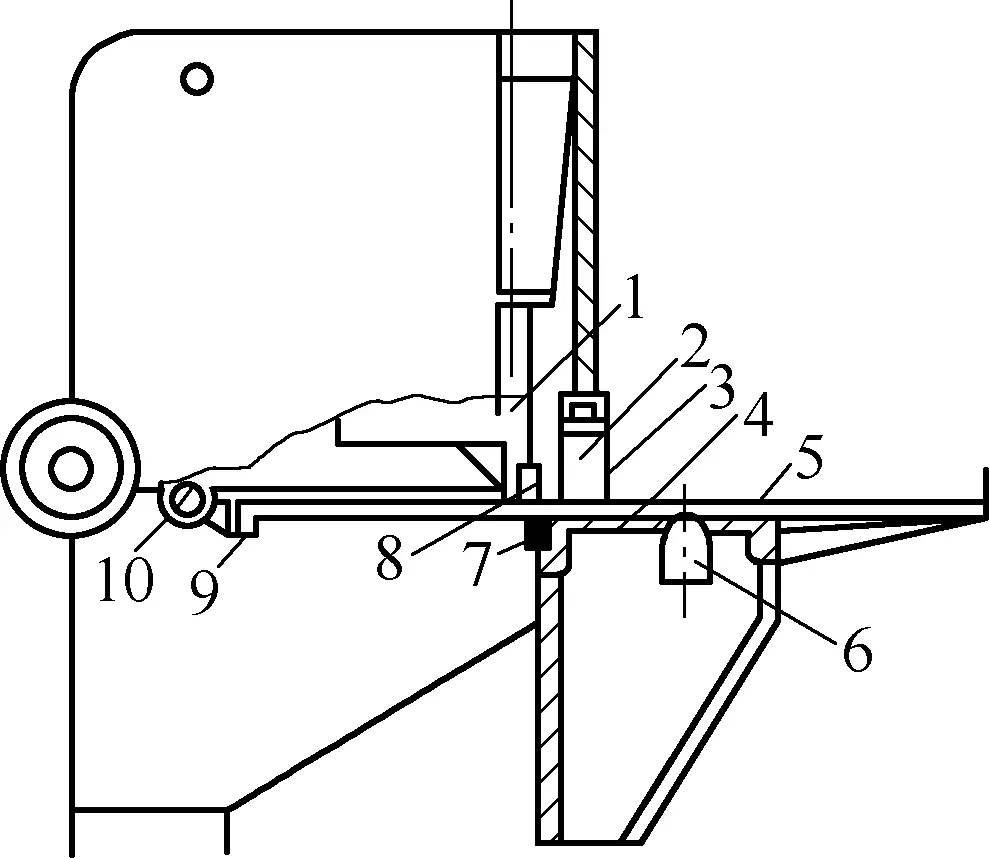
1ブレードホルダー
2-油圧クランプシリンダー
3カバープレート
4テーブル
5シート
6ボール
7-下ブレード
8アッパーブレード
9-リアゲージ
10ポジション・ピン
油圧加圧シリンダー2はシートを加圧するためのもので、剪断時にシートがめくれるのを防ぐ。保護板3は、労働災害を防止するための安全装置です。運転中は、クランクシャフトが剪断スライダーを駆動し、上下の剪断刃の相対運動で材料を切断します。
シャーリングマシンは、伝動方式により機械伝動式シャーリングマシンと油圧伝動式シャーリングマシンに分類される。板厚10mm未満のシャーリングマシンは機械式伝動構造が多く、板厚10mm以上のシャーリングマシンは油圧式伝動構造が多い。
振動剪断機は、一般的に線やテンプレートに基づいて切断するために使用され、一般的に厚さ2mm未満のシートを処理するために使用されます。その動作原理は、機械的な伝達によって下刃に対する上刃の高速往復運動を発生させ、シートを小さなセグメントに切断することです。そのため、曲率半径の大きい曲線状の外形や内形の切断にも使用できる。その構造と作動原理を図24に示す。
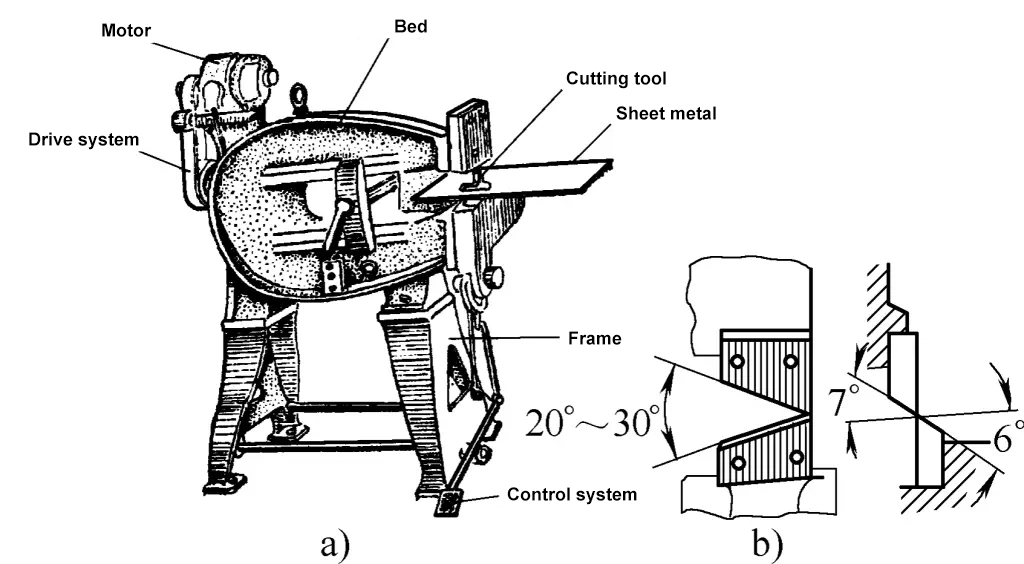
a) 外観
b) 上ブレードと下ブレード
ローリングシャーは、直線的な剪断や曲線に沿った剪断が可能です。ローリングシャーは、円形または曲線形状を切断できるという特性を生かし、パンチダイに代わって大型の切断やトリミングを行うことができます。 プレス部品 剪断品質と生産性は高くないが、小ロット生産に適している。ローリング・シャー・マシンは、反対方向に回転する一対の円形ブレードを使ってシートを剪断する。
図25aは、ローリングシャー・マシンの構造と作動原理を示し、図25b、c、dは、円形ブレードのいくつかの構成を示す。
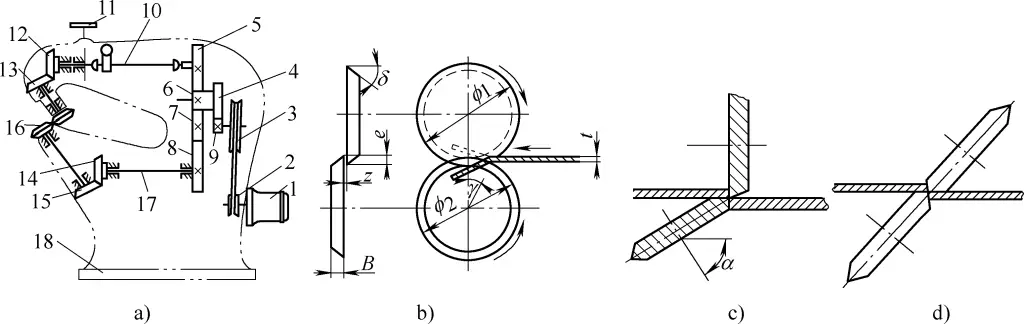
a) 圧延シャーマシンの構造
b) 円形ブレードの直線構成
c) 円形ブレードの傾斜直線構成
d) 円形ブレードの傾斜配置
1モーター
2、3プーリー
4-9-ギア
10シャフト
11-操作ハンドル
12-15-ベベルギア
16-円形ブレード
17-ドライブシャフト
18ベース
(2) シャーリングマシンによる剪断の基本的方法
シャーリングマシンは、上刃と下刃の組み方の違いにより、平刃シャーリングと傾斜刃シャーリングに分けられる。傾斜刃シャーリングは平刃シャーリングに比べ省力化が図れ、幅の広い薄板のシャーリングに多く使用される。図26aに傾斜刃による剪断の模式図を示す。
傾斜刃シャーリングは、シャーリング力を大幅に低減することができます。傾斜刃シャーリングマシンでは、下刃は水平で、上刃は下刃に対してある角度で傾斜している。上刃が傾斜しているため、剪断時に刃と材料が接触する長さがシートの幅よりはるかに小さくなり、ストロークが大きく、剪断力が小さく、動作が滑らかになるため、薄板や幅広シートの剪断に適している。
一般的に、上刃の傾斜角φは1°~6°である。板厚3~10mmではφ=1°~3°、板厚12~35mmではφ=3°~6°。γはすくい角で、せん断中の材料の回転を抑える効果があります。αは逃げ角で、刃と材料の摩擦を抑える効果があります。γは一般に15°~20°、αは一般に1.5°~3°である。
図26bは、平刃剪断機による平刃剪断の模式図である。平刃剪断の特徴は、平行な上刃と下刃の間で剪断することである。βは一般に0°~15°である。ストロークが小さいが剪断力が大きく、厚板や狭幅板の剪断に適している。
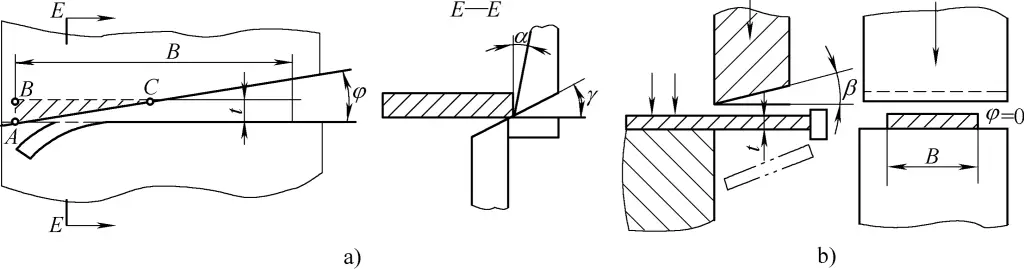
a) 傾斜ブレードシャーリング
b) フラット・ブレード・シャーリング
(3) シャーリングマシンの運転方法
シャーリングマシンは、上下の直線刃でシートブランクを剪断する。ブランクを一定の形状やサイズに切断するため、シャーリングマシンには、フロントストッパー、リアストッパー、サイドストッパー、特殊な角度ストッパーからなるストッパー装置が装備されています。
前後左右のストッパープレートは、シャーリングマシンのワークテーブルやベッドフレームに設置・固定でき、調整機構により前後左右の位置調整が可能です。角度ストッパープレートは、一般的にテーブル面のT溝に設置され、切断するシートの形状に合わせてテーブル上の異なる位置に設置・固定することができます。
一部のストッパープレート(リアストッパープレートなど)の自動位置決め制御と表示を実現し、一定の長さのブロックやストリップの剪断を大幅に容易にしたデジタルディスプレイやCNC剪断機は数多くあるが、より複雑な形状の剪断には、依然として各種ストッパープレートの手動調整が必要である。
複雑な形状の切断には、通常、テンプレートを使用した手作業による調整方法が採用される。切断作業で重要なことは、剪断機に設置された各種ストッパープレートの位置を調整し、幅や形状の異なるストリップやブロックの剪断を完了させ、品質を確保・管理することである。ストッパー・プレートを用いた剪断を図 27 に示す。

a) リアストッパープレートの使用
b) フロント・ストッパー・プレートの使用
c) アンギュラープレートとリアストッパープレートの使用
d) 2枚のアングル・ストッパー・プレートの使用
e) リア・ストッパープレートとアングラー・ストッパー・プレートの使用
f) アンギュラープレートとフロントストッパープレートの使用
1) 一般的な幅のストリップのシャーリング
一般的な幅のシートを剪断する場合、位置決めはラインまたはリアストッパプレートで行い、リアストッパプレートの位置をネジで調整する。剪断の際、シートは押え板で強く押えられ、上剪断刃の付いたスライダーが下降し、上剪断刃と下剪断刃が重なることで剪断される。図27aに示すように、剪断された部分は通常、品質を確保するためのさらなる加工を必要としない。
2) 幅の広いストリップのシャーリング
幅の広いストリップをシャーリングする場合、後部ストッパープレートでシートを位置決めすると、張り出し部分がその重さによってたるみます。位置決め誤差は、張り出し長さと板厚の比(B/t)が大きくなるほど大きくなる。したがって、板幅が300~400mmを超える場合は、図27bに示すように、前ストッパー板を使用して位置決めを行う。フロント・ストッパーの位置は、一般的な測定具やテンプレ ートを使って決めることができる。
3) 台形ブロックと三角ブロックのせん断
台形ブロックや三角ブロックのせん断には、サイドストッパープレートを他のストッパープレートと組み合わせて使用し、位置決めを行います。
取り付けの際は、テンプレートをテーブルの上に置き、下刃に合わせ、サイド・ストッパー・プレートを調整して固定する。その後、図27cに示すように、テンプレートを使って後方のストッパー・プレートを調整し、シャーリング時の位置決めにサイド・ストッパー・プレートと後方のストッパー・プレートの両方を使用する。同様に、サイド・ストッパー・プレートと他のストッパー・プレートを使用した他の接合位置決め方法を図27d、e、fに示す。
4) 細い材料を切る。
剪断板が押え装置から離れすぎて押えられない場合、安全かつ円滑に剪断するために、剪断板と同じ厚さの当て板を追加して押え装置で押え剪断することができる。図28に示すように、押え板を厚くすることもできる。薄い板材の場合はパディングは不要で、押え板で直接板材を押えることができる。
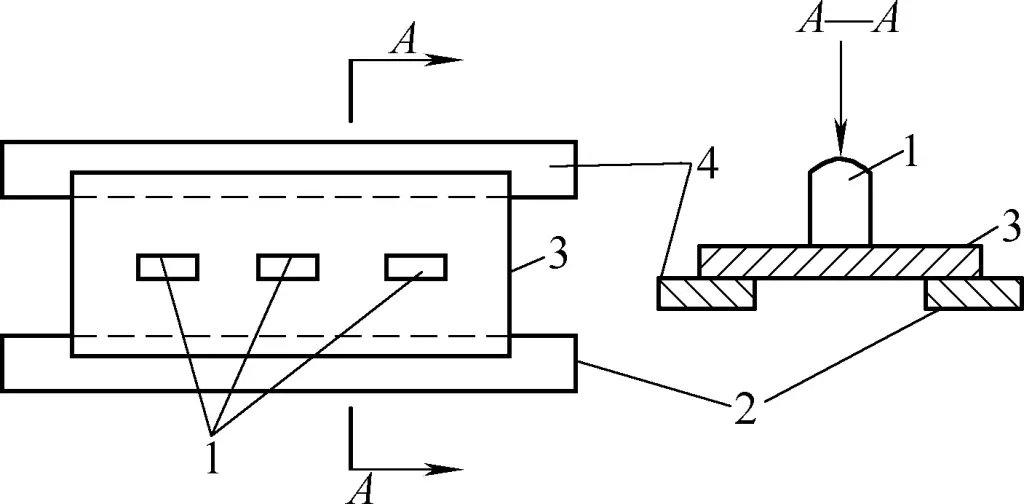
1-圧力装置
2-剪断鋼板
3-プレスボード
4-パッド・ボード
4) シャーリングマシンの動作ステップとアライメント方法
皿の間 剪断作業まず、剪断の安全作業手順を厳守すること。次に、板材の剪断面の真直度と平行度を確保し、材料の歪みを最小限に抑えることで、高品質の部品を実現します。以下に、剪断作業のステップとアライメント方法を詳しく説明するために、例を示します。
図 29 に示すワークは、厚さ 10mm の 25 鋼板から作られている。剪断後の各寸法の公差は±1mmである。門型傾斜剪断機による剪断作業の手順とアライメント方法は以下の通りである:
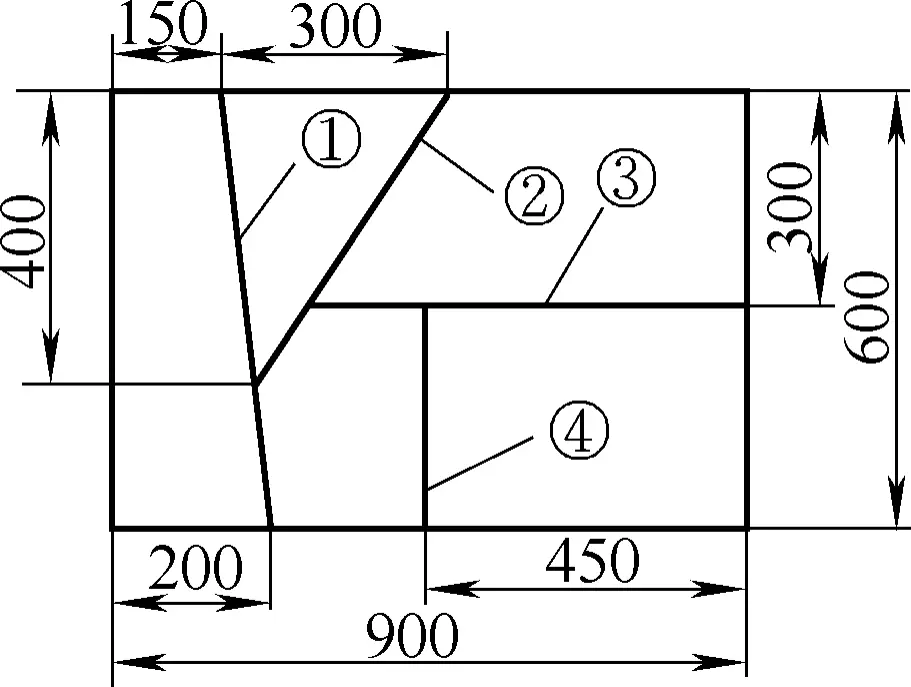
1) シャーリング作業の手順
剪断されるワークピースの構造は大きく異なる可能性があるが、剪断作業の基本的なステップは一般的に同じであり、以下のように行うことができる:
毛刈りに必要な人数を決める。
プレートが大きい場合、シャーリングの際に一人で作業するのは好ましくない。2~3人で連携して作業を行い、1人をリーダーと定め、すべての行動を一貫させ、リーダーの指示に従うようにする。
剪断の順序を決める。
ワークピースには複数のシャーリングラインがあることがよくあります。ガントリー式傾斜シャーリングマシンを使用する場合、シャーリング順序は、各シャーリングが板を 2 つの部分に分離するようにする必要があります。図 29 は、剪断線の順序に従ったワークの剪断順序を示している。
ワークのシャーリングのアライメント方法を分析し、決定する。
ガントリー式傾斜シャーリングマシンにおけるワークのアライメントには複数の方法がある。これらの方法は、ワークの構造解析に基づいて柔軟に適用する必要がある。このワークの場合、アライメント方法としては
- シャーリングライン①の位置合わせは、ダイレクトビジュアルアライメントまたはシャドーアライメントを使用します。
- 剪断線②は、角度ストッパー板を使って位置合わせする。
- シャーリングライン③を背面ストッパー板で揃える。
- シャーリングライン④は、フロントストッパー板を使用して揃える。
剪断する材料の性質と厚さに基づき、剪断刃のギャップを点検・調整してください。シャーリングマシンにシャー刃隙間調整データ表が付属している場合は、そのデータに従って隙間を調整してください。または、表 2 を参照して、シャー刃のギャップを決定してください。
表 2:シャーリングマシンの適正ギャップ範囲(単位:mm)
素材タイプ | ギャップ(t%) |
電磁純鉄 軟鋼(低炭素鋼) 硬鋼(中炭素鋼または高強度鋼) 電気珪素鋼 ステンレス 低合金鋼 硬質アルミニウム、真鍮 防錆アルミニウム | 6~9 6~9 8~12 7~11 7~13 6~10 6~10 5~8 |
注:表中、tは剪断された板の厚さを表す。
剪断刃のギャップをチェックし調整した後、材料をセットする前に機械を無負荷の状態で運転し、正常に動作することを確認してください。材料を投入する前に、板材の表面を清掃し、せん断線が明瞭で正確であることを確認してください。
シャーリングを行う。決められたアライメント方法とシャーリングの手順に従ってください。
品質検査。剪断されたワークのすべての部分の寸法を測定し、設計要件を満たしていることを確認し、剪断されたエッジの品質をチェックします。
2) シャーリングアライメント法の操作
図 28 に示すワークピースに対して、決められたアライメント方法でシャーリング作業を行う。
シャーリングライン①。
板をシャーリング・マシンのテーブルの上に置き、シャーリング開口部 に押し込み、図 30 に示すように、シャーリング線の両端をシャーリング刃の下 端に目視で合わせる。次に、剪断開口部から押え板の外側に手を離し、スイッチを押すか踏み込んで板を剪断する。
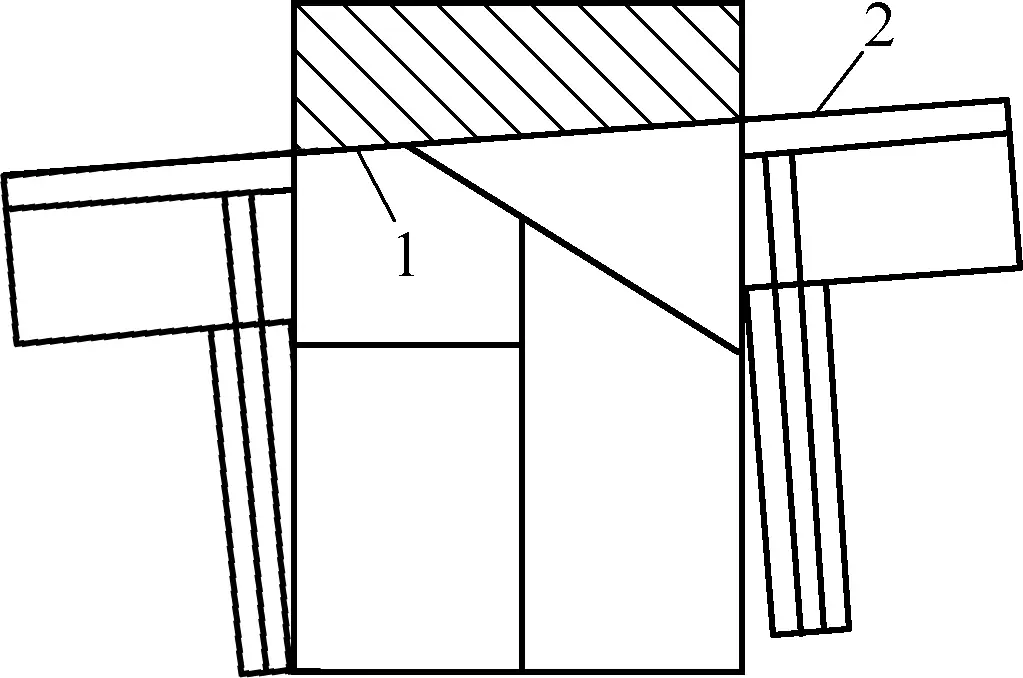
1-剪断線
2-下部シャー刃先
シャーリングライン②。
角度位置決めストッパー板を調整・固定し、ストッパー板を位置決めの基準とし、シャーリングマシンに板を正しく置き、図31に示すようにシャーリングライン②に沿ってシャーリングを行う。
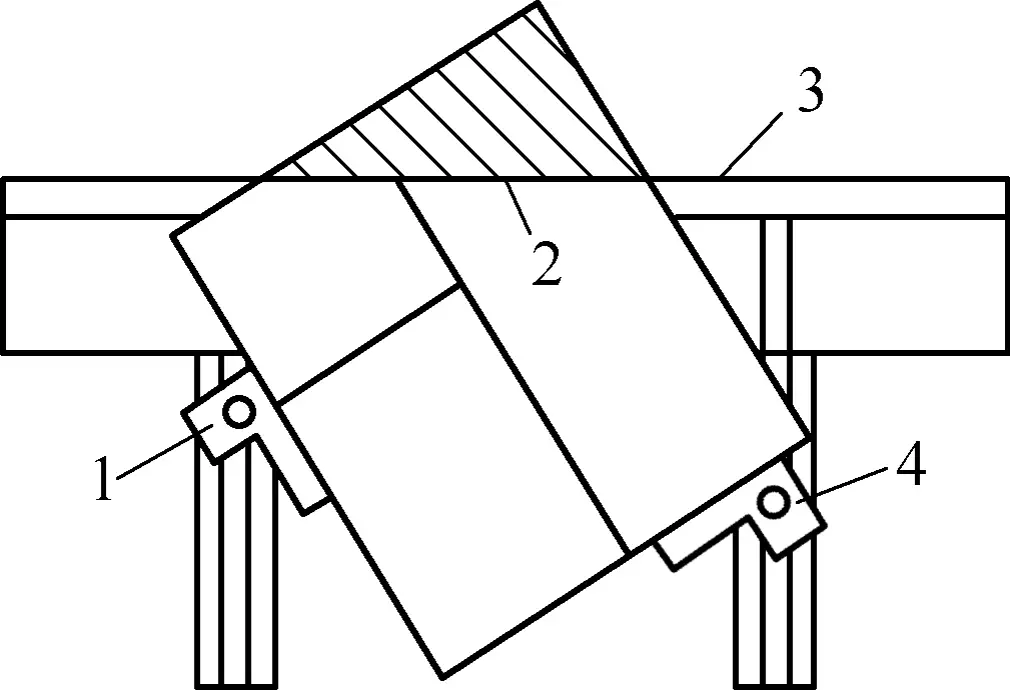
1、4角ストッパーボード
2-カットライン
3-下ブレードエッジ
切断線③。
切断線③をバックゲージで位置決めする場合、バックゲージの位置は2つの方法で決めることができる:ひとつはスチール定規で直接測定する方法で、上刃と下刃の刃先からバックゲージ面までの距離が、切断する材料の幅と等しくなるようにします。バックゲージを固定した後、正確な位置決めのために再度測定する。
第二の方法は、テンプレートの位置決め方法である。切断する材料と同じ幅のテンプレートを下刃の刃先とバックゲージの間に挟むことで、バックゲージの位置を決めることができる。バックゲージの位置が決まれば、図 32 のように切断線③を位置決めして切断することができる。
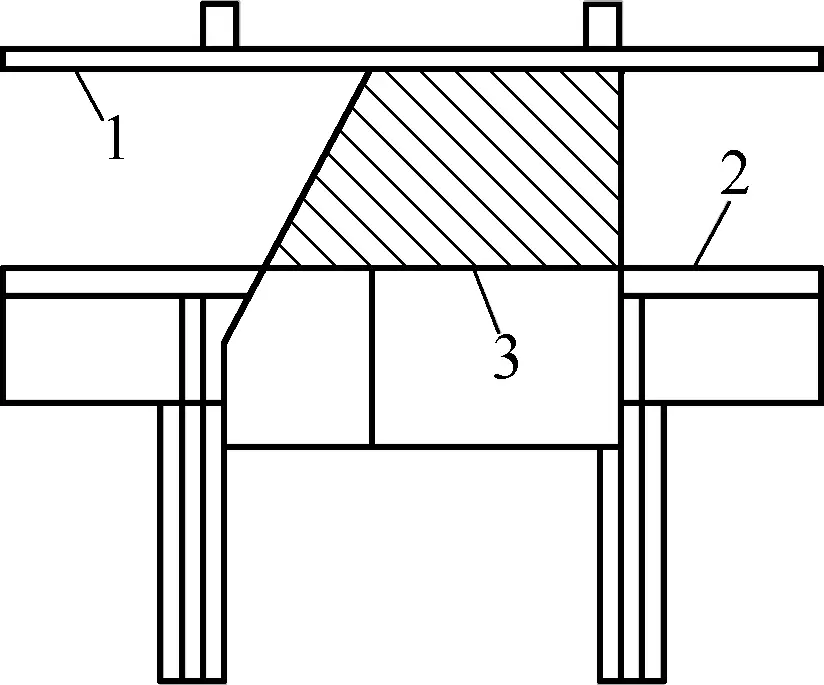
1-バックゲージ
2-下ブレードエッジ
3カットライン
切断線④。
フロントゲージで切断線④を位置決めする場合、フロントゲージの位置の決め方はバックゲージと同じである。フロントゲージの位置決めと切断のシナリオを図 33 に示す。
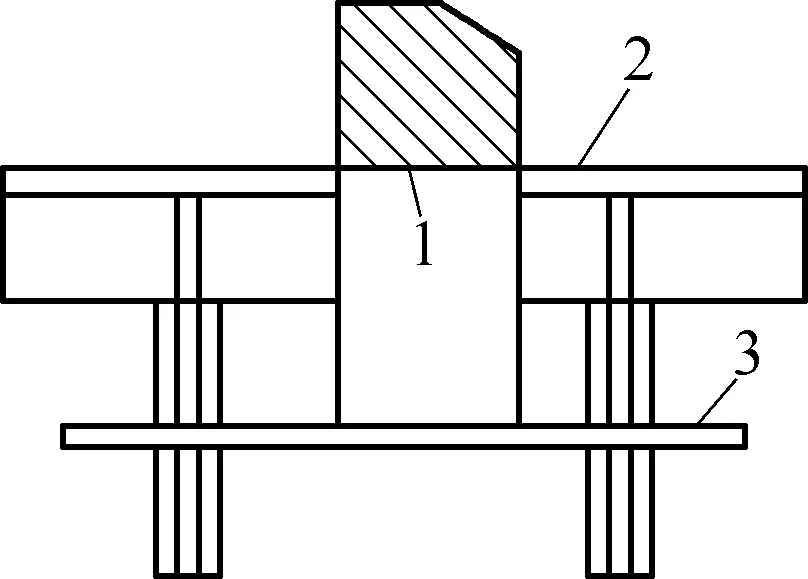
1-切断線
2-下ブレードエッジ
3バックゲージ
(5) シャーリングマシンの運転上の注意事項
比較的、ブランキング加工の作業は技術的な内容は低いが、シャーリングマシンによるブランキング加工は作業事故が発生しやすい。ブランキング加工品の品質とブランキング加工の安全性を確保するために、ブランキング加工時には次のような注意が必要である:
1) 始動前に、シャーリングマシンの操作システム、クラッチ、ブレーキが信頼できる有効な状態にあるか、安全装置が完全で信頼できるものであるかを注意深くチェックしてください。異常が発見された場合は、直ちに必要な処置を行ってください。故障のある装置を運転することは禁じられています。運転中、リジッドクラッチのピンやキーの大きなノック音がないことを確認してください。
2) モーターは負荷がかかった状態で始動してはならない。クラッチを切ってから始動すること。正式運転前に無負荷試運転を行い、プルロッドの動作不良やネジのゆるみがないか確認し、正常であることを確認してから正式運転を行ってください。
3) シャーリング作業中は集中すること。複数人で作業する場合は、指定された人が切断スイッチを操作すること。切断エリアに手を伸ばすことは厳禁である。特に指先の安全を確保するため、送り出し中は集中してください。シート材が端まで切断されている場合、指で材料を下から押さないでください。
4) 刃と刃先は鋭利でなければならない。薄いシートをカットするときは、刃がしっかりとフィットしていなければならない。上刃と下刃を平行に保ち、鈍い刃を使用せず、刃先が滑らかかどうかを確認する。刃の調整後は、手動テストと無負荷テストを行ってください。
5) 小片を切断する場合は、不適切な押圧や事故を防ぐため、押圧パッドを使用する。
6) 作業台の上に他の物や関係のない物を置かないでください。調整や清掃は、必ずマシンを停止させた状態で行ってください。
7) 同じシャーリングマシンで、2 人が同時に 2 枚の異なるシートをシャーリングすることは厳禁です。ワークが整列する前にフットペダルを踏んだり、エアフックを引いたりしないでください。いかなる場合でも、刃の下に頭や手を入れないでください。
8) 現場周辺の作業スペースを整頓し、ワークピースやシートが妨げられることなく垂直に持ち上げられるようにする。
9) 長すぎるワークや厚すぎるワークの加工にシャーリングマシンを使用することは禁止されています。焼入れ鋼、高速度鋼、合金工具鋼、鋳鉄、脆性材料の切断には使用しないでください。
シャーリングマシンの校正の主な仕様は、t×B(tはシャーリングする材料の最大許容厚さ、Bはシートの最大許容幅)です。最大許容剪断幅 B と最大許容板厚 t を超えるワークの加工には使用しないでください。
高強度材(バネ鋼や高合金鋼板など)をせん断する場合は、最大許容せん断厚さ tマックス.これは、シャーリングマシンの設計が一般的に中硬度材(引張強さ500MPa前後、鋼種25~30)を考慮しているためである。したがって、引張強さσb 剪断される材料の最大許容剪断厚さ tマックス は以下の式で計算される:
tマックス=√(500t/σb)
式中
- t - 校正されたシャーリングマシンの最大許容シャーリング厚さ(mm);
- σb - せん断される材料の引張強さ(MPa);
- tマックス - シャーリングマシンの計算された最大許容シャーリング厚さ(mm)。
この式を用いると、計算された最大許容せん断厚さがせん断される材料の厚さより小さい場合、せん断機は使用できません。表 3 にシャーリングマシンの技術仕様を示す。
表 3 シャーリングマシンの技術仕様
パラメータ | モデル | ||||
Q11-1×1000 | QY11-4×2000 | Q11-4×2500 | Q11-12×2000 | Q11Y-16×2500 | |
シート厚 (mm) | 1 | 4 | 4 | 12 | 16 |
シート幅 (mm) | 1000 | 2000 | 2500 | 2000 | 2500 |
剪断角度 | 1° | 2° | 1°30′ | 2° | 1°~4° |
ストローク数(回/分) | 65 | 22 | 45 | 30 | 8~12 |
バックゲージ距離 | 500 | 25~500 | 650 | 750 | 900 |
出力(kW) | 0.6 | 6.5 | 7.5 | 13 | 22 |
構造形式 | メカニカル・アンダードライブ | 油圧式アンダードライブ | メカニカルドライブ | 油圧駆動 |
10)長尺板を切断する場合は、補助支持具を用意する。大型で重い板を切断する場合は、送りを容易にし、切断材表面の摩擦を減らすために、転がり支持具(すなわち、材料を保持するための鋼球を備えた支持具、図34のような構造)を用意する。また、板材を吊り上げるには、十分な補助作業員とともに吊り上げ装置を使用し、補助作業員との連携を確保すべきである。
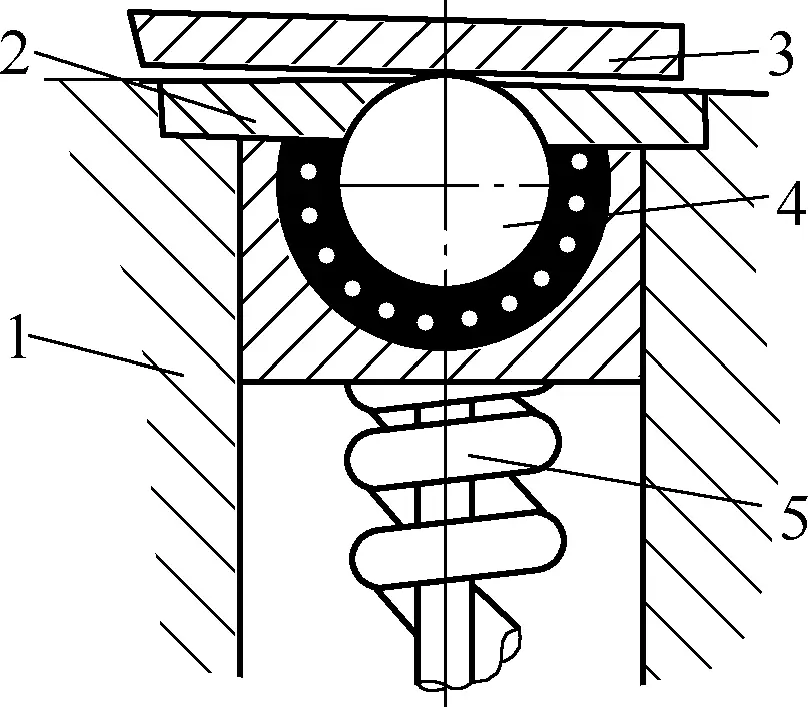
1-サポート
2-プレスカバー
3カットプレート
4-スチールボール
5-スプリング
III.ブランキング
ブランキングは プレス加工 プレスの圧力下でダイを使用し、パンチとダイのエッジの間に配置されたシートまたはストリップ材料の一部を分離し、それによって平らなブランクまたは部品の所望の形状とサイズを得るもの。
シート材から必要な形状を切り出す方法をブランキングと呼ぶ。部品を大量生産する場合、ブランキングは生産効率と製品の品質を向上させることができる。
ブランキングでは、材料はパンチとダイの間に置かれ、外力の作用下でパンチとダイが剪断力を発生させ、剪断力の作用下で材料を分離する(図35参照)。ブランキングの基本原理は剪断と同じであるが、剪断では直線状の刃先であったものが、閉じた円形などの刃先となる。
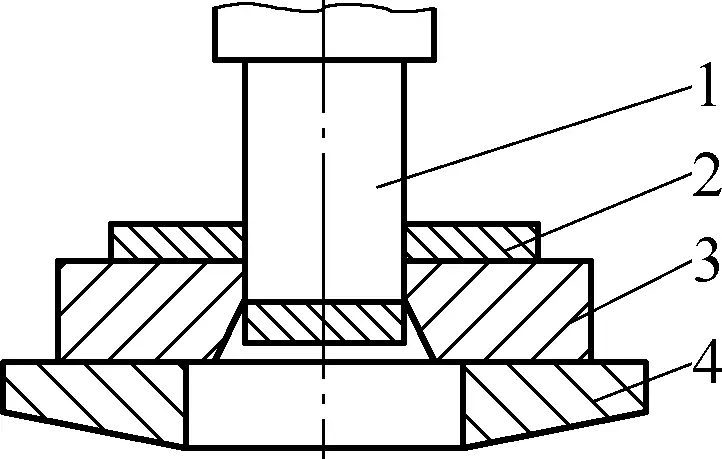
1パンチ
2シート素材
3-ダイ
4プレステーブル
1.ブランキング加工の生産要素
ブランキング加工の原理によれば、ブランキング加工は主にプレス機に取り付けられた金型にシート材を載せることで完了する。したがって、シート材料、ブランキング装置、ブランキング金型がブランキング加工の基本的な生産要素を構成する。
(1) ブランキング用原材料
ブランキングの主な原材料は金属板材で、一部の形材(パイプ)や非金属材料も加工できる。一般的なブランキング用素材を図36に示す。
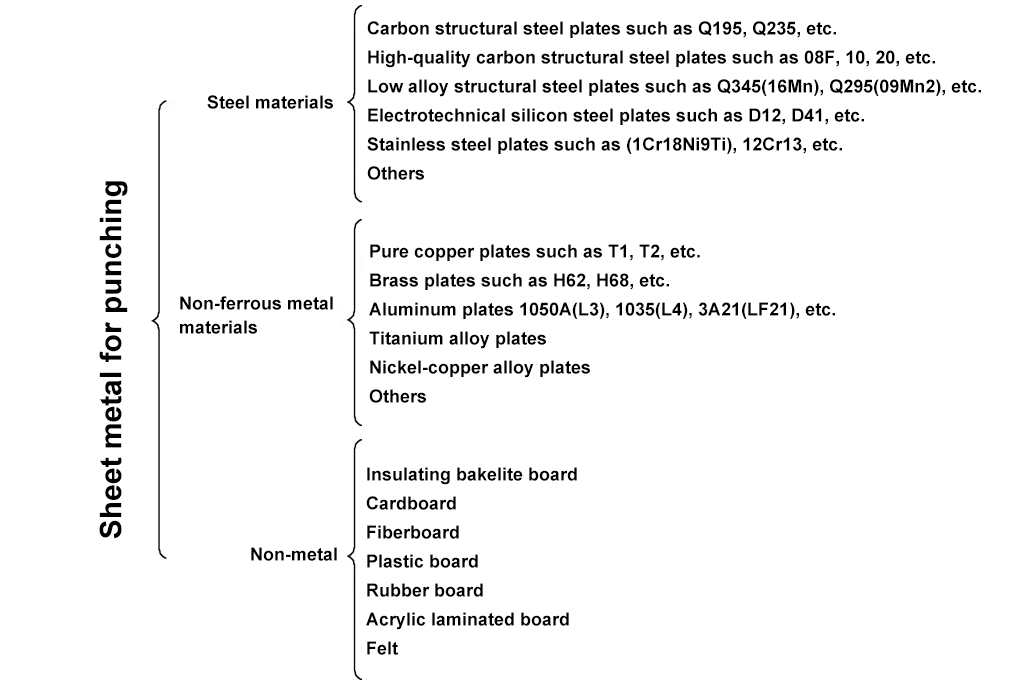
注:括弧内の数字は旧標準グレード。
ブランキングには様々な原材料が使用されるが、全ての原材料がブランキングに適しているわけではない。ブランキングに使用される原材料は、ブランキングプロセスの特性に合った、良好なスタンピング性能、良好な使用性、良好な表面品質を備えていなければなりません。
(2) ブランキング装置
ブランキングの主な設備は、クランク機構によって駆動する鍛造機械であるクランクプレスである。プレスは公称圧力で大、中、小に分類される。小型プレスの呼び圧力は1000kN未満、中型プレスの呼び圧力は1000~3000kN、大型プレスの呼び圧力は3000kN以上である。
プレス機は構造形式によって、オープンプレスとクローズドプレスに分けられる。オープンプレスは、フレームがC型になっており、作業者が前、左、右から作業台に近づくことができ、操作が容易である。しかし、フレームの剛性に限界があるため、オープンプレスは小型・中型プレスにしか適さない。クローズドプレスは、フレームが完全に密閉され、剛性も高いため、中・大型の汎用プレスや高精度の軽プレスに向いている。
さらに、クランクプレスは、その主な作業軸の構造に基づいて、クランクシャフトプレスと偏心プレスに分けることができる。
1) クランクシャフトプレス
クランクシャフトプレスは,クランクシャフトで形成されたクランク機構を主作動軸とし,力の拡大や運動変換を行うものである.JB23-63クランクオープン傾斜プレスの構造と作動原理を以下に説明する(図37参照)。
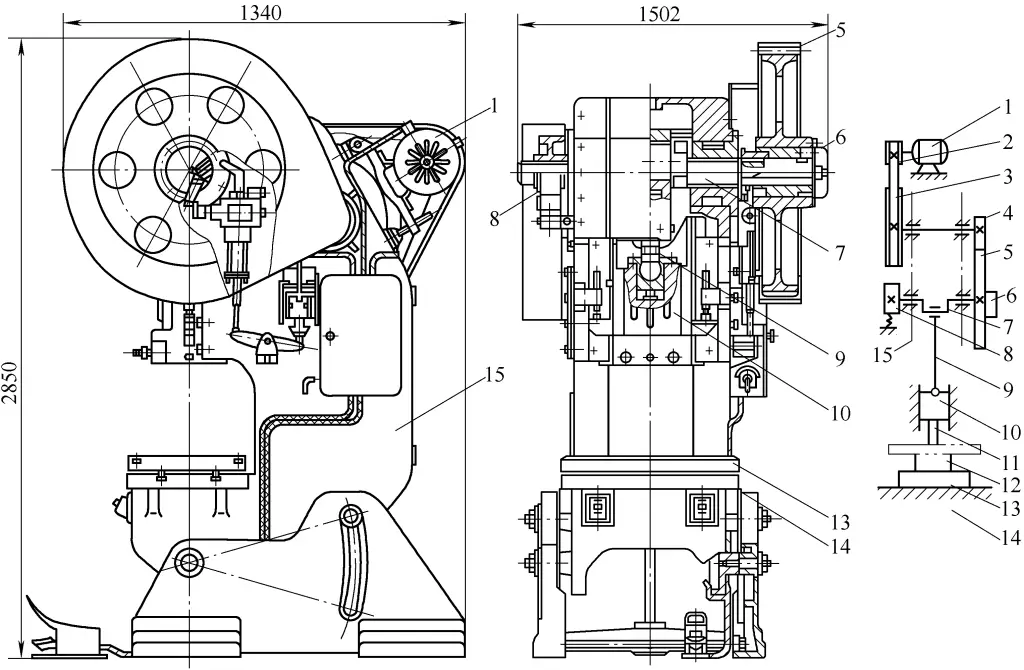
1モーター
2-小型プーリー
3-大型プーリー
4-スモールギア
5-ラージギア
6クラッチ
7-クランクシャフト
8ブレーキ
9-コネクティングロッド
10-スライダー
11-上型
12-下金型
13-バッキングプレート
14-ワークテーブル
15マシンボディ
プレスが作動するとき、モーター1はVベルトを通して大プーリー3に運動を伝え、小ギア4と大ギア5を通してクランクシャフト7に運動を伝えます。コネクティングロッド9の上端はクランクシャフトに取り付けられ、下端はスライダー10に連結され、クランクシャフトの回転運動をスライダーの往復直線運動に変換する。スライダー10の運動の最高位置を上死点と呼び、最低位置を下死点と呼ぶ。
生産工程の要求により、スライダーは動くこともあれば止まることもあるので、クラッチ6とブレーキ8が設置されている。プレス機は各作業サイクル中の稼働時間が非常に短く、ほとんどの時間は無負荷で稼働するため、モーターへの負荷を均一化し、装置のエネルギーを有効に活用するためにフライホイールを設置しています。大型プーリーはフライホイールの役割も果たす。
プレス作業時には、使用済みの金型の上型11をスライダ上に設置し、下型12をワークテーブル14上に直接設置するか、ワークテーブルにバッキングプレート13を追加して適切な閉塞高さにする。このとき、上型と下型の間に材料を挟むことで、打ち抜きなどの成形加工を行い、ワークを製作することができる。
図37からわかるように、スライダ10のストローク(すなわち、スライダの上死点から下死点までの距離)は、クランクシャフト7の偏心量の2倍に等しく、プレスのストロークが大きく調整できないことが特徴である。
しかし、クランクシャフトはプレス上の2つ以上の対称的なベアリングで支えられているため、プレスにかかる負荷はより均一であり、大ストローク、大トンのプレスが製造できる。
2) エキセントリック・プレス
偏心プレスは、偏心主軸を作動主軸として形成されたクランク機構により、力の増幅を完了し、運動形態を変化させるものである。図38に示すように、プレスにおける偏心スリーブ5の位置を調整することにより、プレススライダのストロークを調整することができる。
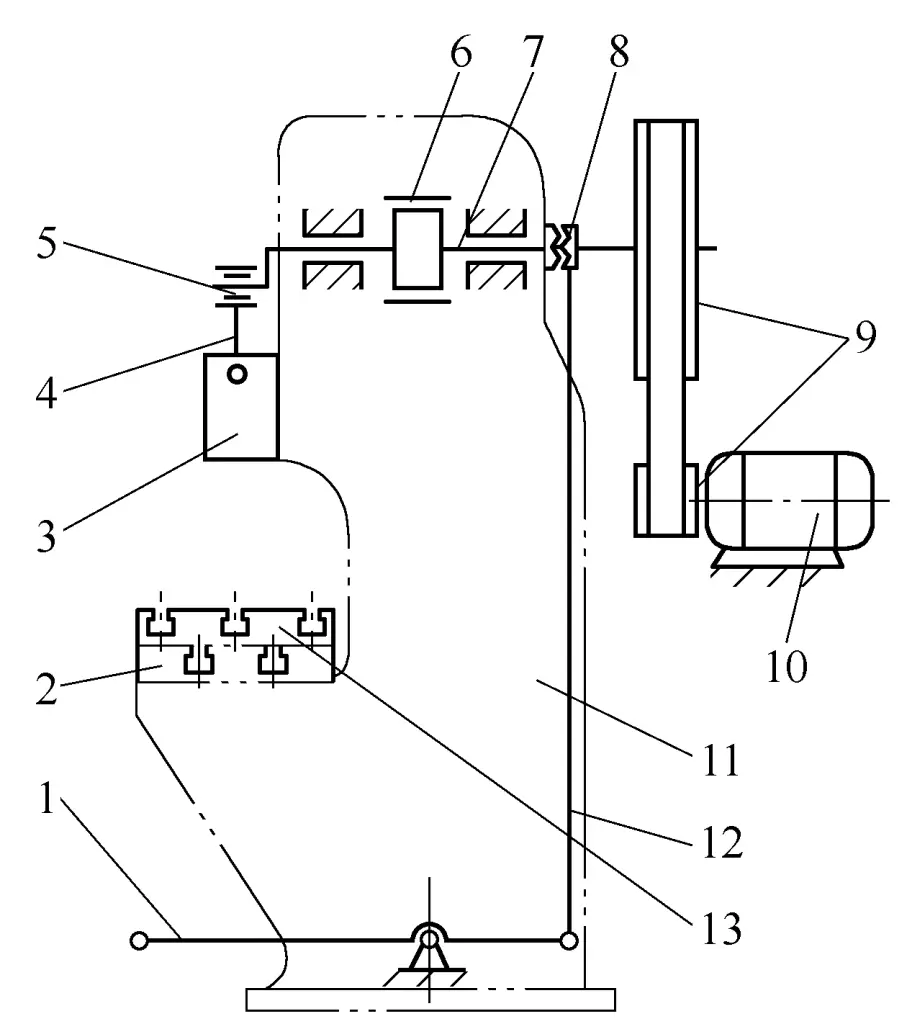
1ペダル
2ワークテーブル
3スライダー
4-コネクティングロッド
5-偏心スリーブ
6ブレーキ
7偏心メインシャフト
8クラッチ
9-プーリー
10モーター
11ベッド
12-コントロールレバー
13-ワークテーブル・バッキング・プレート
このタイプのプレスの特徴は、ストロークは小さいが調整可能であるため、ガイドプレート金型のような大きなストロークを必要としない金型の打ち抜き加工に使用できる。
(3) パンチング・ダイ
一般的に使用されている板金部品用の打ち抜き金型は、プレスの1ストロークで1つの打ち抜き工程(パンチングまたはブランキング)を完了する単工程金型である。打ち抜き工程の違いにより、一般的に使用される板金部品用打ち抜き金型には、パンチング金型、ブランキング金型などがあります。ガイド方法の違いにより、オープン打ち抜き型、ダイセットガイド打ち抜き型、ガイドプレート打ち抜き型などに分けられます。
1) パンチング・ダイ
図39bに示すように、図39aに示す部品の穴加工に使用される抜き型の構造図である。
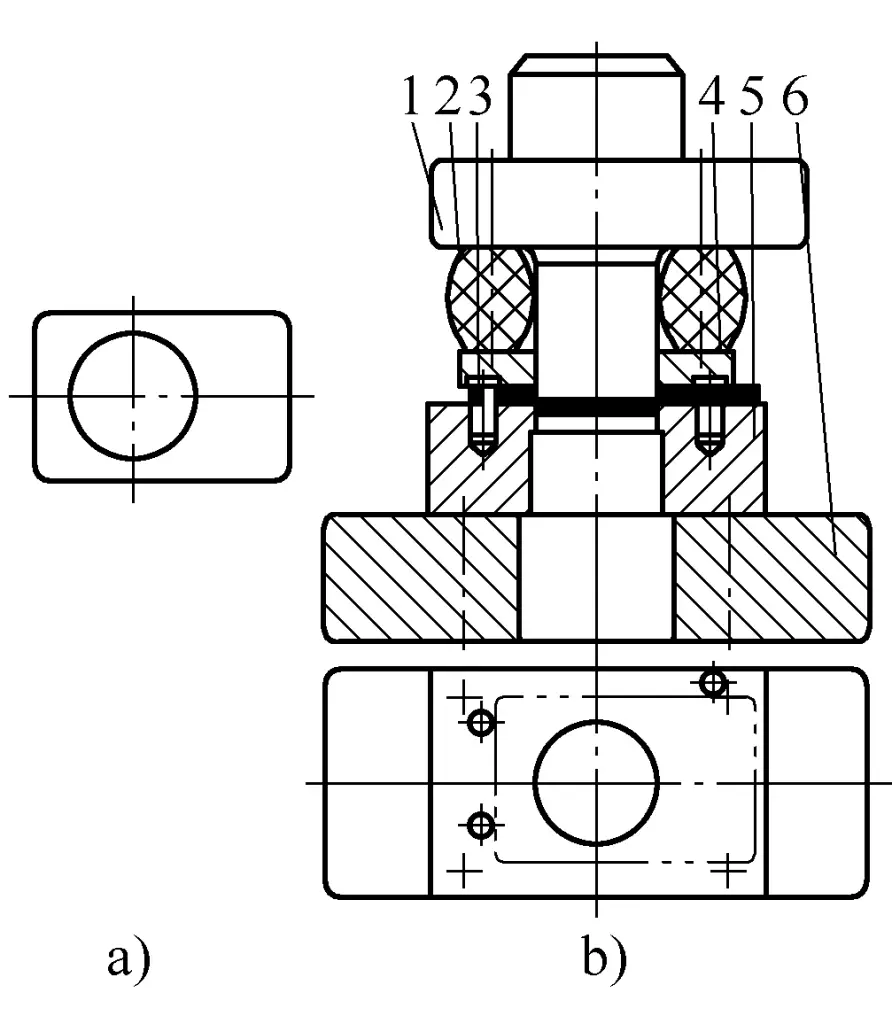
a) 部品構造図
b) 金型構造図
1-上型
2-ゴム弾性体
3ポジション・ピン
4ストリッパー・プレート
5-女性
6-下ダイプレート
この金型は、ガイダンスを持たない単純なオープンタイプの打ち抜き金型である。剪断されたブランクは、メス型5に取り付けられた3本の位置決めピンによって位置決めされます。上型1とメス型5が一体となって丸穴を打ち抜き、圧縮ゴム弾性体2の力でストリッパープレート4が上型パンチでクランプされた部品を押し出す。
このタイプの金型は構造が単純で、製造が容易であり、低コストである。 ダイ・クリアランス 調整が面倒で、打ち抜かれた部品の品質が悪く、作業もあまり安全ではない。主に、精度の要求が低く、形状が単純で、小ロットの部品の打ち抜きに使用される。
2) ブランキング・ダイ
ブランキング・ダイは、ブランキング工程を完成させる単一工程のダイである。ブランキング・ダイには、パンチとダイ間の適度なクリアランス、ダイ内での帯材の正確な位置決め、ブランキングされたパーツの滑らかな落下、ブランキングされたパーツの平坦度、剪断面の良好な品質が要求されます。
図40は、スライド式ガイドポストを備えたブランキングダイを示している。ガイドポストダイセットによってガイドされるブランキングダイは、ガイドポストとガイドスリーブをガイド部品として使用し、互いに嵌合します。動作中、これらは常にH6/h5またはH7/h6のクリアランスで適合し、ダイの作業部品(パンチとダイ)が正しく位置決めされ、ブランク加工された部品の品質が保証されます。
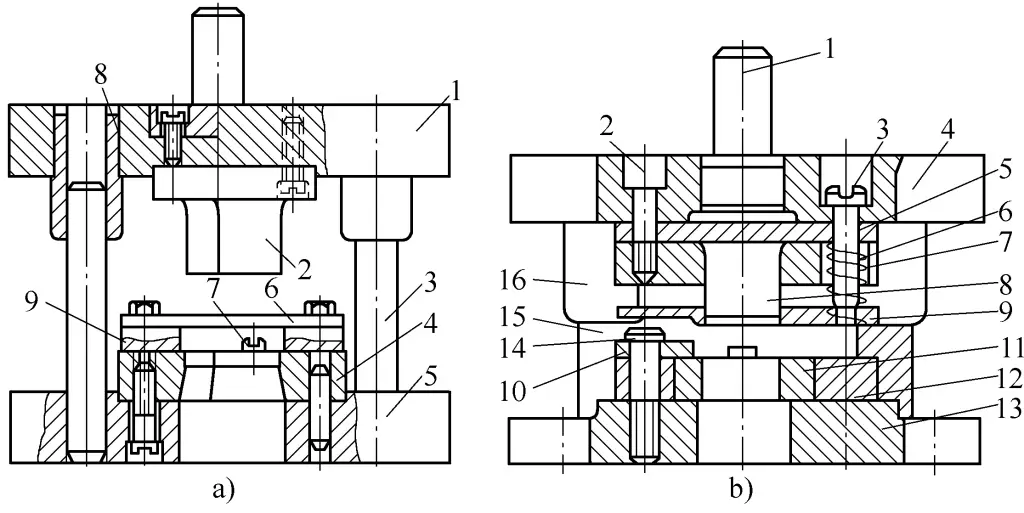
a) 固定ストリッパープレート付きブランキングダイ
b) 弾性ストリッパープレート付きブランキングダイ
a) 図の中:
1-上ダイホルダー
2パンチ
3-ガイドポスト
4-ダイ
5-下ダイホルダー
6-ストリッパープレート
7-位置決めピン
8ガイドスリーブ
9ガイド定規
b) 図の中:
1-ダイシャンク
2-インナー六角穴付きボルト
3-ストリップスクリュー
4-上ダイホルダー
5-バッキングプレート
6パンチ固定プレート
7-スプリング
8パンチ
9-ストリッパープレート
10-ポジショニング・プレート
11-ダイ
12-ダイインサート
13-下ダイホルダー
14-スクリュー
15-ガイドポスト
16ガイドスリーブ
図40aに示すように、固定ストリッパープレートを備えたブランキングダイは、主に厚物(t>0.5mm)で剛性の高い部品のスタンピングに使用されます。ダイの動作中、ストリップ材は左右のガイドルーラー9によって供給され、位置決めピン7によって直接位置決めされ、シート材がダイ上で正しい位置になるようにします。
プレススライドが下降すると、パンチ2とダイ4が徐々にシート材に接触して切断します。スライドが上昇するとパンチ2も上昇し、ガイド定規9に取り付けられたストリッパプレート6がパンチ2に付着したストリップ材を掻き落とす。ブランク部品は、下型ホルダ下のスクラップ穴から直接落下する。
図40bに示すように、弾性ストリッパープレートを備えたブランキングダイは、主に薄い(t<0.5mm)部品のスタンピングに使用され、部品の平坦度を良好に保つことができる。ストリッピングシステムは、ストリッパープレート9、ストリッピングスクリュー3、スプリング7から構成されています。パンチ8がプレスと共に下降してシート材を打ち抜くと、ストリッパープレート9も下降してシート材を押し、スプリング7は圧縮します。
パンチング後、製品は下型ホルダーのスクラップ穴から直接落下し、屑は帯材をパンチ8に強く巻き付けたまま上昇します。スプリング7は、ストリッパープレート9のリセットにより、廃棄物を剥離します。弾性ストリップシステムは、弾性要素としてバネを使用することも、ゴムエラストマー、ゴムなどを使用することもできます。
ダイセットによってガイドされる金型は、ガイド精度が高く、金型寿命が長く、部品の大量生産に適している。
図41cに示すように、図41aに示す円形部品を加工するために、ガイドプレート型ブランキングダイが使用される。図 41b は部品のレイアウトを示す。
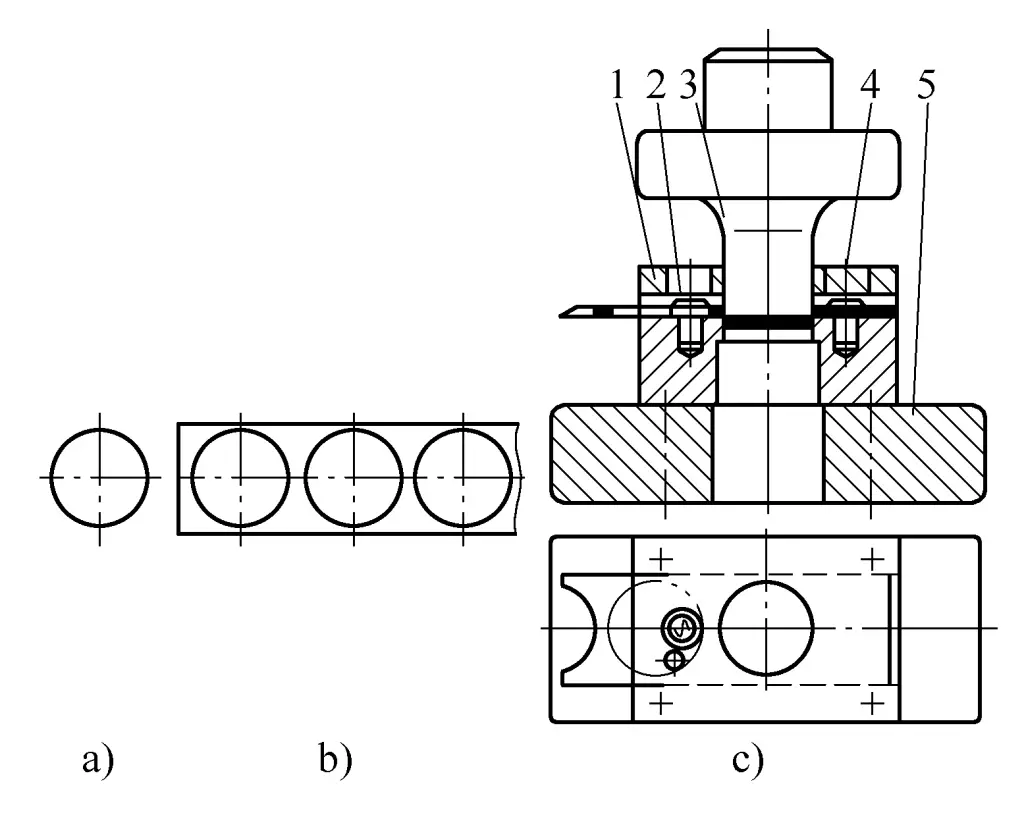
a) 部品構造の概略図
b) 部品レイアウトの概略図
c) 金型構造の概略図
1-ガイドプレート
2-円筒ピン
3-上型
4-ダイ
5-下段テンプレート
このタイプのダイは、ガイドなしのダイよりも精度が高く、製造が複雑ですが、使用がより安全で、取り付けが簡単で、一般的に、板厚t>0.5mmの単純な形状や小さなサイズの単工程ブランキングダイに使用されます。動作中にパンチがガイドプレートから離れないようにするため、小さなプレスストロークが必要です。
複雑な形状や大きな部品には、この種の構造は適しておらず、ガイド用のガイドポストやガイドスリーブを備えた金型構造を使用する方がよい。
ガイドプレート・パンチが作動すると、上型3の作動部とガイドプレート1との間のわずかな隙間をガイドします。0.8mm未満の材料にはH6/h5を、3mm以上の材料にはH8/h7を使用します。
ガイドプレートはストリッパーの役割も果たします。パンチング中、ガイド精度を維持するために、パンチャーがガイドプレートから離れないようにしてください(特に複数または小型のパンチャーの場合)。パンチャーがガイドプレートから離れたり、再びガイドプレートに入ったりすると、パンチャーの鋭利なエッジが容易に損傷し、ガイドプレートのガイド穴が容易にかじられ、パンチャーの寿命やパンチャーとガイドプレート間のガイド精度に影響を与えます。
3) パンチングダイの構造構成
抜き型の構造形式はいろいろあるが、どのような形式であっても、その構造は次のような部分で構成されている。
パンチ&ダイ
これらは材料を直接せん断する部品であり、パンチ金型の核となる部品である。通常、パンチは上型に固定され、ダイは下型に固定される。
位置決め装置。
その機能は、打ち抜かれた部品の金型内での正しい位置を確保することであり、通常、ガイドプレートや位置決めピンなどの位置決め部品で構成され、下側のダイホルダーに固定され、ストリップの送り方向と送り量を制御します。
ストリップ装置
その機能は、シート材または打ち抜かれた部品をダイから分離することであり、通常、硬質または弾性のストリッピングプレートなどの部品で構成されます。打ち抜きが完了し、パンチが上方に移動すると、パンチ上のストリップはストリッピングプレートによってブロックされ、落下します。さらに、ダイ上の下方に拡大したテーパー穴は、打ち抜かれた材料をダイから排出するのに役立ちます。
誘導装置。
その機能は、ダイの上部と下部の間の正しい相対位置を確保することであり、通常はガイドスリーブとガイドピラー、ガイドプレートなどで構成されます。動作中、ガイドはパンチとダイの間の正しい適合を保証します。
クランプと固定装置。
その機能は、金型とプレス、および金型の部品間の強固で信頼性の高い接続を保証することであり、通常、上部テンプレート、下部テンプレート、ダイシャンク、プレッシャープレート、ボルト、およびネジなどの部品で構成されています。これらの部品は、金型のさまざまな部品を組み合わせ、組み立て、プレス機に固定します。
プレス装置。
その機能は、打ち抜かれた部分にしわが寄るのを防ぎ、打ち抜き部の品質を向上させることであり、通常、弾性押さえリングなどで構成される。
2.パンチングの主要パラメータの決定
打ち抜かれた部品の品質を保証するために、打ち抜き工程を策定し、打ち抜き型を設計する際には、以下の工程パラメータを決定する必要があります。
(1) レイアウトの決定
ストリップ上の打ち抜き部品の配置方法はレイアウトと呼ばれる。レイアウトの基本原則は、材料の利用率を向上させること、労働集約度の低い作業員が安全かつ容易に作業できるようにすること、金型構造を単純化することである。レイアウト作業の主な仕事はレイアウト図を設計することであり、そのためにオーバーラップ、ステップ距離などの値を決定しなければならない。
1) オーバーラップ値の決定
レイアウトの際、打ち抜かれた部品と部品の間や、打ち抜かれた部品とストリップの側面の間には、オーバーラップと呼ばれる一定の加工代が残される。
オーバーラップを設定する目的は、打ち抜き時のストリップとガイドプレート間の隙間によるストリップの切断誤差、送り段差誤差、送りスキュー誤差を補正することです。さらに、パンチとダイの刃先が両側からの力に耐えられるようにし、連続送り中のストリップに一定の剛性を与え、角欠けなどの不良品を避け、ダイの寿命と部品断面の品質を向上させます。
オーバーラップが多すぎると材料が無駄になり、少なすぎると本来の目的を果たせません。オーバーラップが不十分だと、ダイの中に入り込みやすくなり、刃先の摩耗が進み、ダイの寿命に影響します。
オーバーラップ値は通常、経験によって決定される。表4に低炭素鋼板のオーバーラップ値を示す。オーバーラップ値が決まれば、レイアウト方法に基づいてシャーリングする板幅を決めることができる。
表4 オーバーラップ値aとa1 低炭素鋼板用(単位:mm)
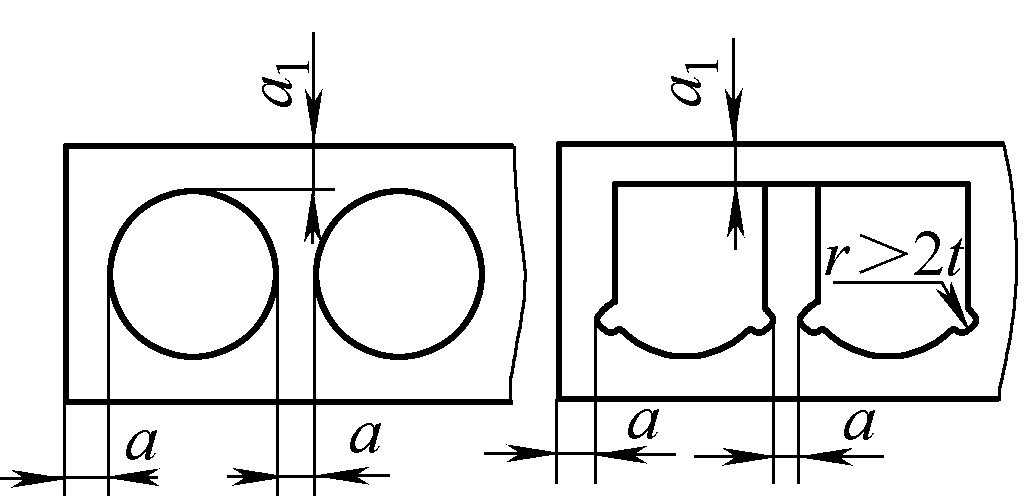
注:
中炭素鋼0.9、高炭素鋼0.8、硬質黄銅1~1.1、硬質アルミニウム1~1.2、軟質黄銅、純銅1.2、アルミニウム1.3~1.4、非金属(皮革、紙、繊維板など)1.5~2。
2) ステップ距離の決定
ストリップがダイ上を毎回前進する距離は、フィード・ステップ距離Aと呼ばれる。
段差距離の計算は、レイアウト方法に関連している。段差距離の大きさは、図 42 に示すように、ストリップ上の対応する 2 つの打ち抜き部分の対応点間の距離である。
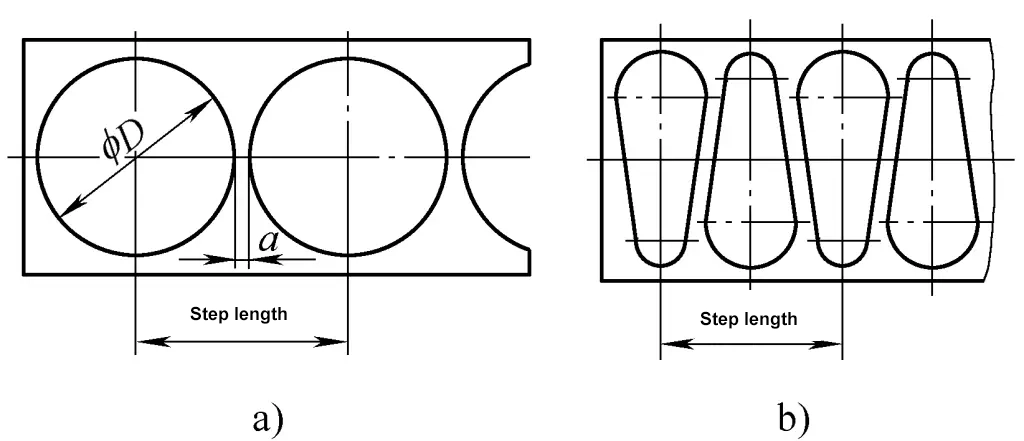
a) 円形部品のレイアウト図
b) 異形部品のレイアウト図
(2) パンチ力の計算
パンチ力 は、適切なプレスを選択するための主要な基礎であり、金型を設計し、金型の強度をチェックするためにも必要なデータである。通常の平打ちの場合、打ち抜き力の計算式は次のようになります:
式中
F=Ltσb
- F - パンチ力(N);
- L - 打ち抜き部分の周囲長(mm);
- t - シートの厚さ(mm);
- σb - 材料の引張強さ(MPa)。
ブランキング工程では、ブランキング力の他に、剥離力、押し出し力、排出力がある。ブランキング後にポンチに付着した材料を除去する力を剥離力といい、Fストリップ金型に詰まった材料を押したり排出したりする力を押す力、排出する力といい、それぞれ Fプッシュ とFイジェクト をそれぞれ表す。これらの力の大きさは、一般にブランキング力Fに係数(0.04~0.12)を乗じたものである。係数の具体的な選択は、関連するスタンピング計算資料から参照できる。
ブランキング時に必要な総ブランキング圧力は、ブランキング力、ストリッピング力、プッシング力、エジェクト力の合計です。プレス機を選ぶ際には、金型の構造によって、これらの力をすべて考慮する必要があるかどうかを検討する必要があります:
- 剛体ストリッピング装置とボトムエジェクション方式を用いたブランキング金型の場合、全ブランキング圧力F合計=Fブランク+Fプッシュ;
- 弾性ストリップ装置とボトムエジェクション方式を用いたブランキングダイの場合、全ブランキング圧力F合計=Fブランク+Fプッシュ+Fストリップ;
- 弾性ストリップ装置とトップエジェクション方式を用いたブランキングダイの場合、全ブランキング圧力F合計=Fブランク+Fプッシュ+Fイジェクト.
ブランキング金型の総ブランキング圧力に基づいてプレスを選択する場合、プレスの公称圧力は、一般的に以下を満たす必要があります:プレスの公称圧力≥1.2F合計.
(3) ブランキングクリアランスの決定
ブランキングクリアランスZは、パンチとダイの間の加工部品の寸法差を意味し、すなわちZ=D采の目-DパンチZはブランキング用の両面クリアランス、D采の目 とDパンチ はそれぞれダイとパンチの刃先寸法である。
ブランキング・クリアランスは、ブランキング工程に大きな影響を与えます。その大きさは、ブランキング部品の品質に直接影響し、金型の寿命にも大きな影響を与えます。ブランキングクリアランスは、適切なブランキングを保証するための最も重要なプロセスパラメータです。実際の生産では、妥当なブランキングクリアランスの値は実験的手法によって決定されます。
妥当なブランキングクリアランスの値は、かなり広い範囲にあり、通常(5%~25%)tである。絶対的に妥当なブランキングクリアランスの値はなく、ブランキングパーツの具体的な要件は業界によって異なるため、各業界、さらには各企業が独自のブランキングクリアランス表を持っている。具体的なブランキングクリアランス値を決定する際には、関連するブランキングクリアランス表を参照することが多い。
一般的に言って、適正なブランキングクリアランスを小さく選ぶとプレス部品の品質が向上し、適正なブランキングクリアランスを大きく選ぶと金型寿命が向上します。したがって、プレス部品の品質を確保することを前提に、合理的なブランキングクリアランスを大きくすることが望ましい。
また、両面ブランキングクリアランスZは、以下の式で計算することができる:
Z=mt
式の中で:
- m - 係数、表5と表6を参照;
- t - シートの厚さ(mm)。
表5 機械製造業と自動車・トラクター産業のm値
材料名 | m値 |
08スチール, 10スチール, 真鍮, 純銅 | 0.08~0.10 |
Q235、25鋼 | 0.1~0.12 |
45スチール | 0.12~0.14 |
(4) パンチとダイの加工部品サイズの決定
ブランキング加工では、ダイの加工部品の寸法と精度が、ブランキング加工された部品の寸法公差等級に影響を与える主な要因です。さらに、ダイの適切なブランキング・クリアランスも、ダイの加工部品の寸法と公差に左右されます。したがって、パンチとダイの加工部品の寸法と製造公差を決定する際には、ブランキング変形の法則、ブランキング部品の公差等級、ダイの摩耗、および製造特性を考慮する必要があります。
表6 電気器具・計器産業のm値
素材タイプ | 材料名 | m値 |
金属材料 | アルミニウム、純銅、純鉄 | 0.04 |
硬質アルミニウム、真鍮、08スチール、10スチール | 0.05 | |
錫リン青銅、ベリリウム合金、クロム鋼 | 0.06 | |
ケイ素鋼板、バネ鋼、高炭素鋼 | 0.07 | |
非金属材料 | 紙クロス、皮革、アスベスト、ゴム、プラスチックハードボード、粘着ボード、粘着クロスボード、雲母シート | 0.02 0.03 |
1) ブランキング用パンチとダイのサイズ計算の基本原則
ブランキング用のパンチとダイのサイズ計算の基本原則は以下の通りである:
穴を開ける場合、穴の直径によってポンチのサイズが決まり、ダイのサイズを大きくすることでブランキングクリアランスが得られる。
ブランキングを行う場合、外形寸法によってダイのサイズが決まり、パンチのサイズを小さくすることでブランキングクリアランスが得られる。
金型の磨耗はブランク部品の寸法を増加させ、パンチの磨耗は打ち抜き部品の寸法を減少させるので、金型の寿命を改善するために、新しい金型を製造する場合、金型のサイズはブランク部品の寸法の下限に向かう傾向があり、パンチのサイズは打ち抜き部品の寸法の上限に向かう傾向がある。
2) ブランキング・クリアランスの確保方法
ブランキング金型を製造する際、適度なブランキングクリアランスを確保するために、一般的に次の2つの方法が用いられる:
そのひとつが分離加工法である。パンチとダイのサイズと公差を別々に指定し、個別に製造する。パンチとダイのサイズと製造公差により、必要なブランキングクリアランスが確保される。この方法で加工されたパンチとダイは互換性があり、製造サイクルが短く、バッチ生産に適しています。
もう一つの方法は、シングルフィット加工法である。この方法では、パンチとダイを個別に合わせ、適度なブランキング・クリアランスを確保する。加工後、パンチとダイは正確に一致させる必要があり、交換することはできません。通常、ブランク加工された部品にはダイが基準ダイとして選ばれ、パンチ加工された部品にはパンチが基準ダイとして選ばれます。
基準ダイの部品図には寸法と公差が記され、適合する非基準ダイの部品図には基準ダイと同じ公称寸法が公差なしで記されます。ブランキング・クリアランスは、基準ダイの実際の寸法に従って合わせられ、ブランキング・クリアランス値がZ分 Zへマックス.シングルフィット加工法は、複雑な形状や小さなブランクリアランスを持つパンチに対して主に使用される。
3) パンチとダイを別々に加工する場合の加工寸法の計算
パンチとダイを別々に加工するための加工寸法とは、パンチとダイの製造偏差を与える寸法を指す。加工寸法の決定は、次の2つの状況で計算できる:
パンチングダイ:
d凸=(d分+xΔ)0-δ凸
d凹=(d凸+Z分)=(d分+xΔ+Z分)+δ凹面0
抜き型:
D凸=(Dマックス-xΔ)+δ凹面0
D凸 = (D凹 - Z分) = (Dマックス - xΔ - Z分)0 - δ凸
式中
- d凸 とd凹 - はそれぞれパンチとダイの公称寸法である;
- D凹 とD凸 - はそれぞれブランキングダイとパンチの公称寸法である;
- d分 - 打ち抜き部分の下限サイズ;
- δ凸 とδ凹 - はそれぞれパンチとダイの製造公差である。パンチ公差は負、ダイ公差は正です。一般的には、部品公差Δの1/3から1/4程度とすることができる。円や四角のような単純な形状の場合、製造が簡単で精度を保証しやすいため、製造公差はIT6~IT8レベルで選択することができます;
- Z分 とZマックス - はそれぞれブランキング金型の初期両面クリアランスの最小値と最大値で、各業界や企業の関連するブランキングクリアランステーブルに従って選択されます;
- Δ - ブランク部分の公差;
- x - 摩耗係数、その値は0.5から1の範囲で、ブランク部品の公差レベルに応じて選択できます。部品公差がIT10以上の場合、x=1とし、部品公差がIT11~IT13の場合、x=0.75とし、部品公差がIT14以下の場合、x=0.5とする。
4) パンチとダイのシングルマッチング加工のステップ
複雑な形状や薄い材質のブランク部品には、シングルマッチング加工法がよく使われる。パンチとダイの公称寸法を決定する原則は、金型加工部品の適格寸法範囲内で最大摩耗量を確保することである。
単一のマッチング加工されたパンチとダイの製造寸法を決定する手順は以下の通りである:
まず基準となる金型を選びます。
基準金型の各寸法が、摩耗後に増加するか、減少するか、あるいは変化しないかを判断する。
この決定に従って、寸法増加とは、部品の上限寸法からxΔを引いた寸法で、パンチとダイの公差を正とし、公差の大きさを寸法公差Δの1/3~1/4とする;サイズの減少は、部品の下限サイズにxΔを加えたもので、パンチとダイの公差はマイナスで、公差のサイズはサイズ公差Δの1/3から1/4として選択されます。
基準金型の外側の寸法は、基準金型の実際の寸法に合わせ、パンチングクリアランスの要件を確保します。
3.パンチ金型取り付け時のプレスの調整
プレスの正しい調整は、打ち抜き金型を設置する際の重要な側面であり、高品質のプレス部品を製造するための重要な前提条件です。プレス調整の主な側面は、プレスストロークとプレスシャットハイトの調整です。金型にストリッパーバーがある場合は、ストリッパーバーの位置も調整する必要があります。
(1) プレスストロークの調整
ほとんどのプレス(クランクプレスなど)のスライダーのストロークは調整できません。一部のプレス機(図43に示すように、プレス機の主軸が偏心軸になっている偏心プレス機など)は、スライダーのストロークが調整可能です。図43aに示すように、偏心シャフトとスリーブ構造の使用により、偏心スリーブの位置を回転させることでストロークを調整することができます。
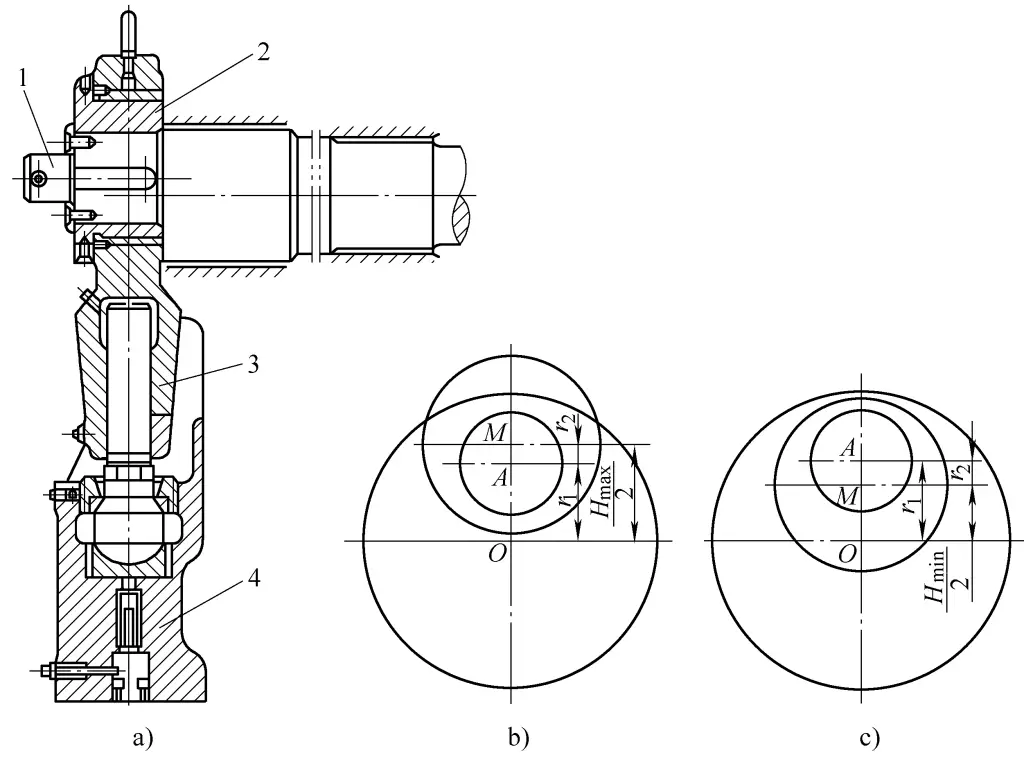
a) ストローク調整機構
b) 最大動作ストローク
c) 最小動作ストローク
1-偏心シャフト
2-偏心スリーブ
3-コネクティングロッド
4スライダー
Oメインシャフト・センター
A-偏心主軸の偏心部中心
M-偏心スリーブの中心
偏心シャフトと偏心スリーブの偏心距離が同じ方向にあるとき、動作ストロークの値は、図43bに示すように最大となる、
Hマックス=2(r1+r2)
どこ
- Hマックス-プレスの最大動作ストローク(mm);
- r1-偏心シャフトの偏心半径(mm);
- r2-偏心スリーブの偏心半径(mm)。
偏心軸と偏心スリーブの偏心距離が逆方向の場合、図43cに示すように、動作ストロークの値は最小となる、
H分=2(r1-r2)
ここでH分-プレスの最小動作ストローク(mm)。
図44は偏心プレスストローク調整機構の概略図である。調整の原理と手順は以下の通りである:
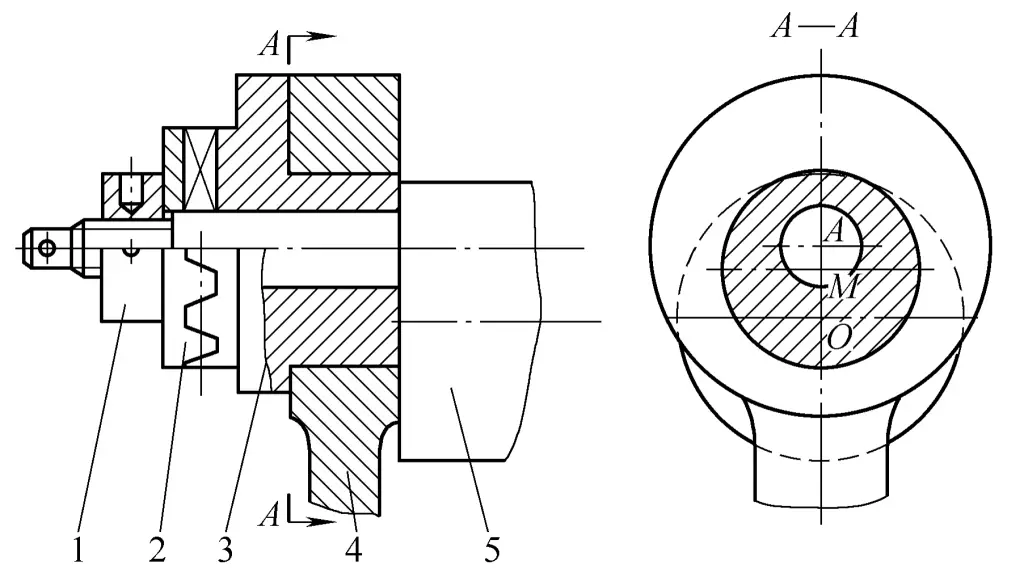
1ナット
2-エンゲージ・スリーブ
3-偏心スリーブ
4-コネクティングロッド
5-偏心主軸
偏心主軸5の前端は偏心部となっており、偏心スリーブ3でスリーブされている。偏心スリーブ3と係合スリーブ2は端歯で噛み合わされ、ナット1でロックされている。コネクティングロッド4は、偏心スリーブ上に自在にスリーブされている。これにより、主軸の回転により偏心スリーブ3の中心Mが主軸の中心Oに沿って円運動し、コンロッド4とスライダーが上下往復運動を行う。
ナット1を緩めて係合スリーブ2の端歯の係合を解除し、偏心スリーブ3を回転させ、偏心スリーブの中心Mからメインシャフトの中心Oまでの距離を調整することにより、スライダのストロークを一定範囲内に調整します。ストロークの調整範囲は (Aは偏心メインシャフトの偏心部の中心、Mは偏心スリーブの中心)。
(2) プレスシャット高さの調整
異なる高さの金型に対応するためには、プレスのダイハイトを調整できなければならない。一般的には、プレスのコネクティングロッドの長さを調整することができます。
プレスのコネクティングロッドの一端はクランクシャフトに接続され、他端はスライダーに接続されています。従って、コネクティングロッドの長さを調整することで、ダイハイト調整の目的を達成することができる。図45に示すJB23-63プレスのクランクスライダ機構は、コネクティングロッドの長さを調整することでダイハイトを調整する。
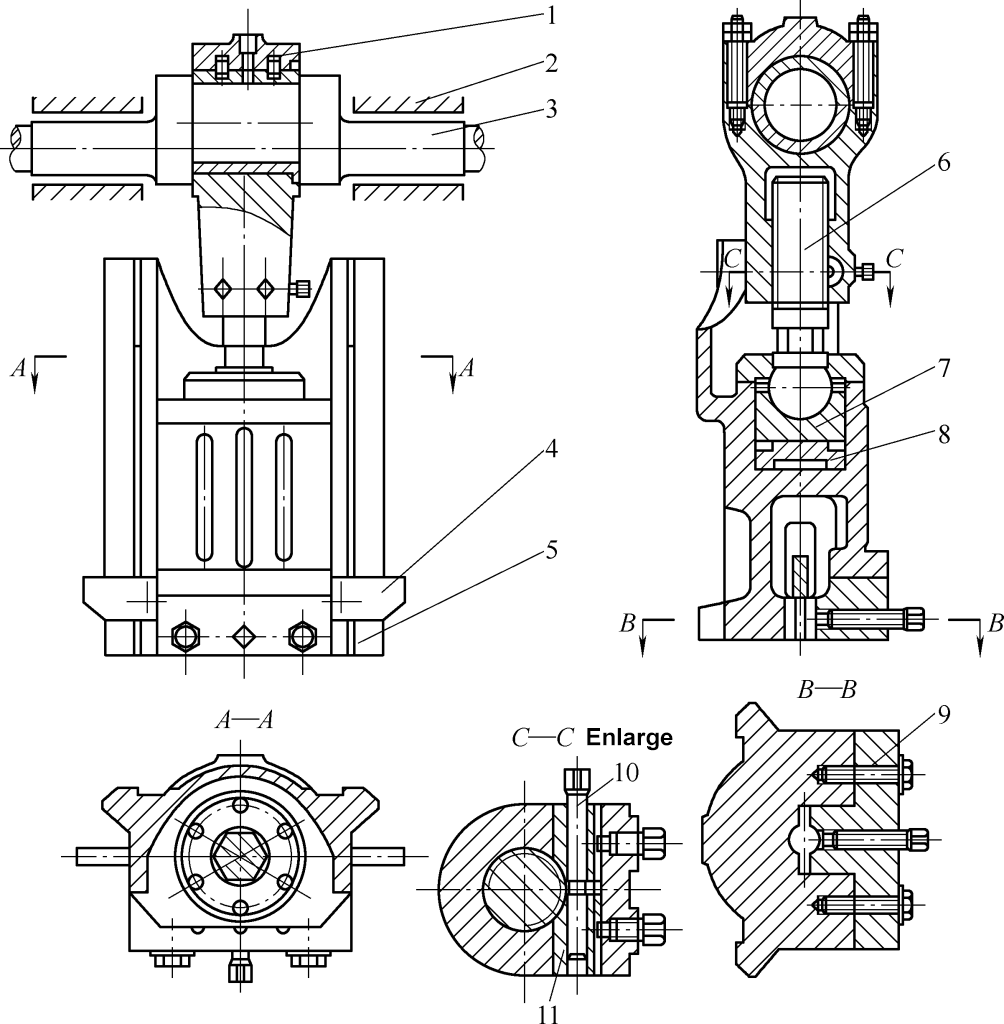
1-コネクティングボディ
2-ベアリングブッシュ
3クランクシャフト
4ストライカー・バー
5スライダー
6-調整ネジ
7-サポートシート
8-安全ブロック
9-ダイホルダークランプブロック
10-ロックネジ
11-ロッキングブロック
図45に見られるように、コネクティングロッドは一体部品ではなく、コネクティングボディ1と調整ネジ6で構成されている。 図44のA-A部に示すように、調整ネジ6の途中には六角部がある。ロックねじ10を緩め、スパナで調整ねじ6の中間にある六角部を回してコネクティングロッドの長さを調整する。大型のプレス機では、モーター、ギヤ、ウォーム・ギヤ機構によってネジを調整する。
スライダーが下死点にあるとき、スライダーの下側の平面とテーブル面との間の距離は、プレスのシャットハイトと呼ばれます。コネクティングロッドを最小の長さに調節すると、シャットハイトは最大値に達し、プレスの最大シャットハイトと呼ばれ、コネクティングロッドを最大の長さに調節すると、シャットハイトは最小値に達し、プレスの最小シャットハイトと呼ばれる。
金型をプレス機に正しく取り付け、金型が正常に作動するようにするため プレス加工プレスの最大閉高さは、プレスの作業面とスライダーの下面との間に金型を設置できるように、金型の閉高さより大きくなければならない。プレスの最小閉高さは、スタンピング中に上下の金型が適切に位置合わせできるように、金型の閉高さより小さくなければならない。
プレスの閉じた高さを調整した後、ロック装置は、プレスの動作中に緩みによってコネクティングロッドの長さが変化し、正常なスタンピング動作に影響を与えないようにロックする必要があります。これは、曲げやエンボスなどの基本的な変形手順における特定のスタンピング工程で特に重要です。
(3) ノックアウト装置の調整
プレス加工の終了後、ワークが金型にはまり込むことがよくあります。ワークピースを押し出すために、プレスには通常、スライダーにセットされたノックアウト装置があります。図46に示すように、剛性の高いノックアウト装置は、スライダーを貫通するノックアウトロッド4と、機械本体に固定されたストップスクリュー3から構成されています。
スライダが下降してプレス加工を行うとき、ワークはスライダのノックアウトロッド4を介して上型のエジェクタロッド7によって押し上げられます。スライダーが上昇し、上死点に近づくと、ノックアウトロッド4の両端は機械本体のストップスクリュー3によって塞がれます。スライダが上昇を続けると、ノックアウトロッド4はスライダに対して下方に移動し、上型のエジェクタロッド7を押してワークを排出します。
ノックアウトロッド4の最大作動ストロークはH-hである。ノックアウトロッド4がストップスクリュー3に早く衝突すると、設備事故の原因となります。したがって、金型の交換やプレスの設置高さを調整する場合は、ストップスクリュー3の位置を適宜調整する必要があります。
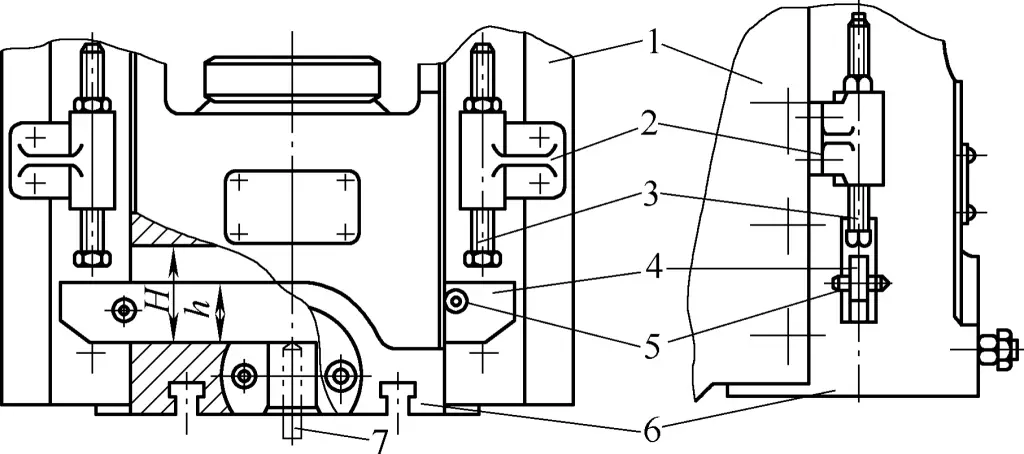
1-マシン本体
2ストップシート
3ストップスクリュー
4ノックアウト・ロッド
5ストップ・ピン
6スライダー
7-エジェクターロッド
図47はプレスノックアウト装置の初期作動状態を示す。
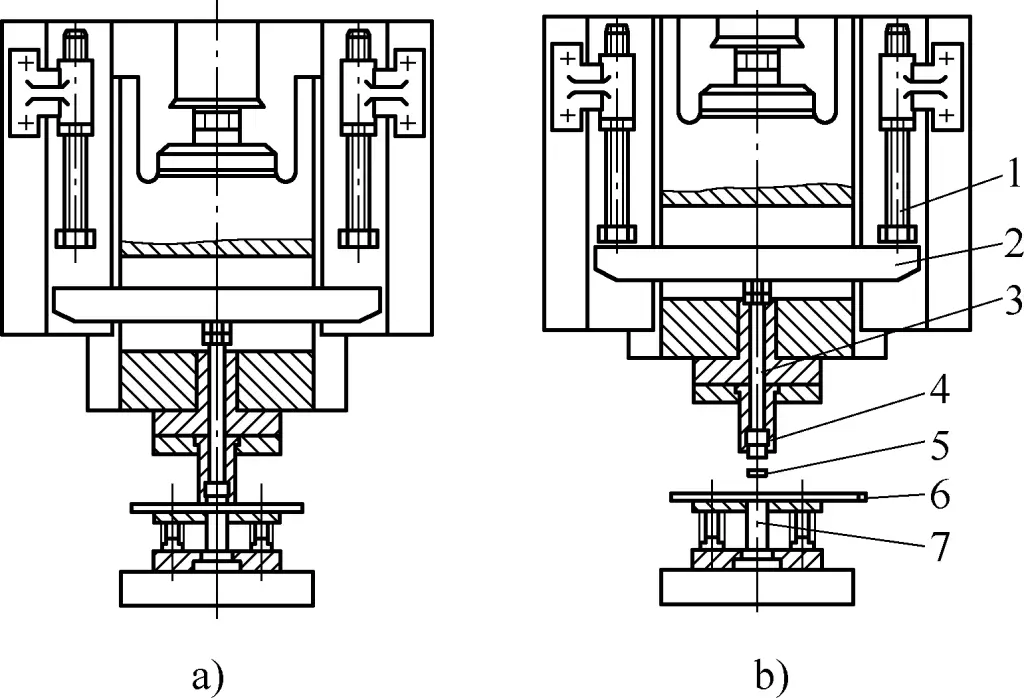
a) ストロークの下死点
b) ストロークの上死点
1-ストップスクリュー
2-ノックアウト・ロッド
3エジェクターロッド
4-女性ダイ
5スタンプ部品
6シート素材
7パンチ
4.ブランキングダイの取り付けと調整
プレス金型の取り付けと調整は、プレス加工の重要な部分です。取り付けと調整の品質は、加工部品の安全性と生産性に直接影響します。取り付けと調整の正確さは、金型、設備、スタンピング作業者の安全性に直接影響します。
(1) ブランキング・ダイの取り付け方法
プレス機への金型の一般的な取り付け方法は、まず上型をプレス機のスライダーに固定し、上型の位置に合わせて下型を調整します。金型の取り付け工程では、プレス機の調整も必要です。
ブランキング・ダイの取り付けは、ノンガイド・ブランキング・ダイとガイド・ブランキング・ダイに分けられる。
1) ノンガイド・ブランキング・ダイの取り付け
ノンガイド・ブランキング・ダイの取り付けは比較的複雑である。その方法は次の通りである:
金型設置の準備金型を取り付ける前に、プレス機と金型を検査する必要があります。主な点検項目は以下の通り:
- 選択したプレスの公称圧力は、金型の加工力の1.2~1.3倍でなければならない。
- 金型の取り付け穴(スロット)の位置は、プレス機の取り付け穴(スロット)の位置と一致していなければならない。
- プレス機の作業テーブル上のスクラップ穴の大きさは、製品やスクラップの大きさより大きくする。ワークやスクラップが作業テーブル上に直接落下した場合、手作業で取り除くためのスペースを確保する必要があります。
- プレスの作業テーブルとスライダーの下面の大きさは、取り付けた金型に合わせ、ある程度のクリアランスが必要です。一般的に、プレスの作業テーブルは、ダイプレートサイズより50~70mm大きくする必要があります。
- ダイのエジェクションロッドの長さと直径は、プレスのノックアウト機構に合わせる必要がある。
さらに、オペレーターは、打ち抜く部品の形状、寸法精度、技術的要求を熟知し、打ち抜く部品の関連工程書類と現行工程の加工内容を理解し、使用する抜き型の種類、構造、作業原理、使用特性を熟知していなければならない。最後に、プレスの金型と作業台を清掃し、プレスの作業状態をチェックする。
金型の設置条件を確認してください。金型の閉じた高さが、プレス機の設置高さに合っていること。金型を取り付ける前に、金型の閉じた高さを測定する必要があります。閉じた高さH0 金型は以下の要件を満たす必要がある:
H分+10mm≦H0≤Hマックス-5mm
フォーミュラ
- H0-金型の閉じた高さ(mm);
- Hマックス-プレスの最大閉じ高さ(mm);
- H分-プレスの最小閉じ高さ(mm)。
金型の閉じた高さが小さすぎて上記の要件を満たさない場合は、図48に示すように、金型を設置する前に、プレスの作業台にグラウンドパッドを追加して上記の要件を満たすことができる。
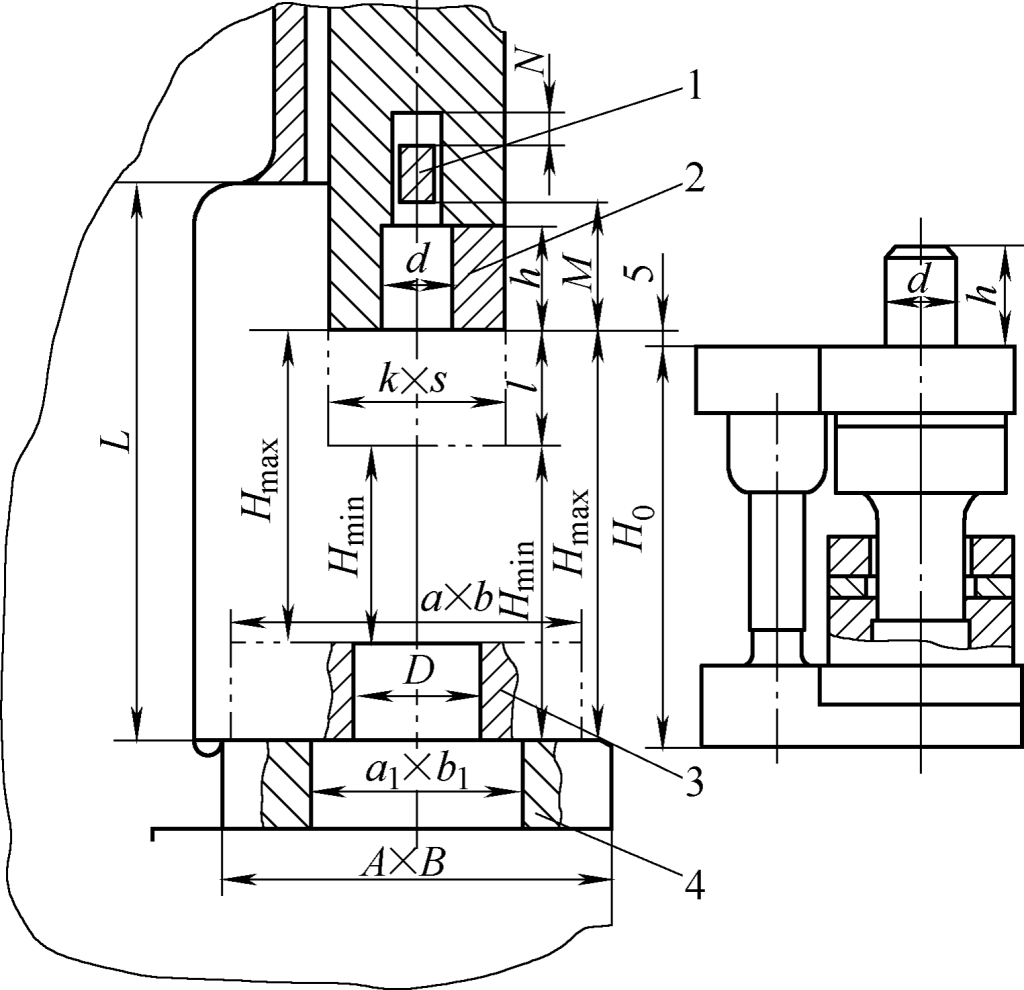
1-射出ビーム
2モールド・ハンドル・クランプ・ブロック
3パッド
4-ワーキングテーブル
図に示された他の寸法の意味は次の通りである:
- N - クロスバーを打つストローク;
- M - ヒッティングクロスバーとスライダー下面との距離;
- h - ダイハンドルの穴の深さまたはダイハンドルの高さ;
- d - ダイ・ハンドルの穴またはダイ・ハンドルの直径;
- k×s - スライダー底面の寸法;
- L - 作業台の表面からスライダーガイドレールまでの距離;
- l - 金型高さの調整量(閉じた状態での高さ調整);
- a×b - バッキングプレートの寸法;
- D - バッキングプレートの穴の直径;
- a1×b1 - 作業台の穴の寸法;
- A×B - 作業台の寸法。
マルチ・ステーション・スタンピングのために、複数の金型セットを同じプレス機械に取り付ける場合、各金型の閉塞高さは同じでなければならない。
金型を取り付ける。各金型の取り付け準備作業が完了したら、以下の手順で金型の取り付けを進めます。
図 49 に示すように、プレス機械の中央に金型を配置する。上型と下型はブロック 3 で支えられます。
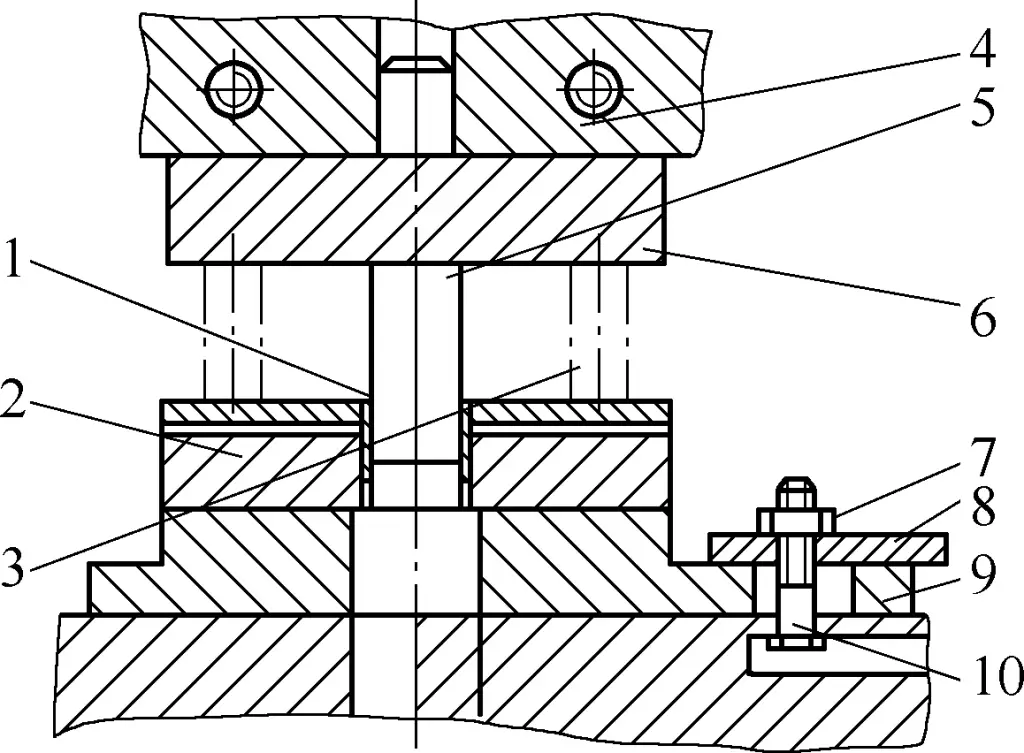
1-硬質ボール紙
2-ダイ
3ブロック
4プレスマシン・スライダー
5パンチ
6-上部テンプレート
セブンナッツ
8-圧力板
9-バッキング・アイアン
10-Tボルト
プレス機スライダー4のナットを緩め、手動またはプライバーでプレス機フライホイールを回し、プレス機スライダー4が上部テンプレート6に接触し、ダイハンドルがプレス機スライダー4のダイハンドル穴に入るまで下降させる。
上記の条件でプレス機スライダー4を最下点に調整しても上型6に接触しない場合は、プレス機コネクティングロッドのネジを調整してプレス機スライダー4を上型6に接触させます。コネクティングロッドを最低位置まで調整してもプレス機スライダー4が上テンプレート6に接触しない場合は、下テンプレートの下部にブロックを追加し、接触するまで下テンプレートを上昇させる。
プレス機スライダー4の高さを調整した後、ダイハンドルをプレス機スライダー4に固定する。
ダイギャップの調整プレス機への金型取り付けが完了したら、パンチとダイの隙間調整、すなわち、パンチとダイの片側隙間値に相当する厚さの硬質ダンボール1または銅板をダイ2の刃先に置き、ライトトンネル法でパンチとダイの隙間が均一になるように調整します。
金型を固定する。隙間調整後、Tボルト10をプレス機テーブルの溝に挿入し、プレッシャープレート8、ブロック9、ナット7を介して下型をプレス機にしっかりと固定します。ボルトは左右対称に交互に締める。
金型の試運転。以上の作業が終了したら、プレス機械を起動して金型の試運転を行います。試運転中に パンチとダイの隙間 調整が必要な場合は、ナット7を少し緩め、パンチとダイの隙間の配分に従って、下型テンプレートを調整方向にハンマーで軽く打ち、隙間が適当になるまで調整します。
正式生産。試運転したワークを自主検査・検査担当者が検査し、合格した後、量産を開始する。
2) ガイド付き抜き型の取り付け方法
ガイド付き切断ダイスの場合、ガイドポストとガイドスリーブのガイドにより、非ガイド付き切断ダイスに比べて、取り付けと調整がより便利で簡単です。取り付けの主なポイントは以下の通りです:
- ノンガイド切断金型の設置要件に従って、金型を設置する前に技術的な準備を行い、金型とプレス機械のテーブルを清掃し、プレス機械を検査する。
- 金型を閉じた状態でプレス機のテーブルに置く。
- 上型と下型に分け、上型を木製のブロックかバッキングアイアンで支える。
- プレス機械のスライダーを下死点まで下げ、図50に示すように、金型上部テンプレートの上面に接触するように調整する。
- 上型と下型を別々にプレス機械のスライダーとプレス機械のテーブルに固定する。ボルトは左右対称に交互に締める。プレス機械スライダーの位置を調整する場合、上死点でパンチがガイドプレートより突出しないか、ガイドスリーブがガイドポストの長さの1/3以上下降しないようにしてください。
- 金型がしっかりと固定されたら試運転を行い、試運転が成功したら正式な生産に移る。
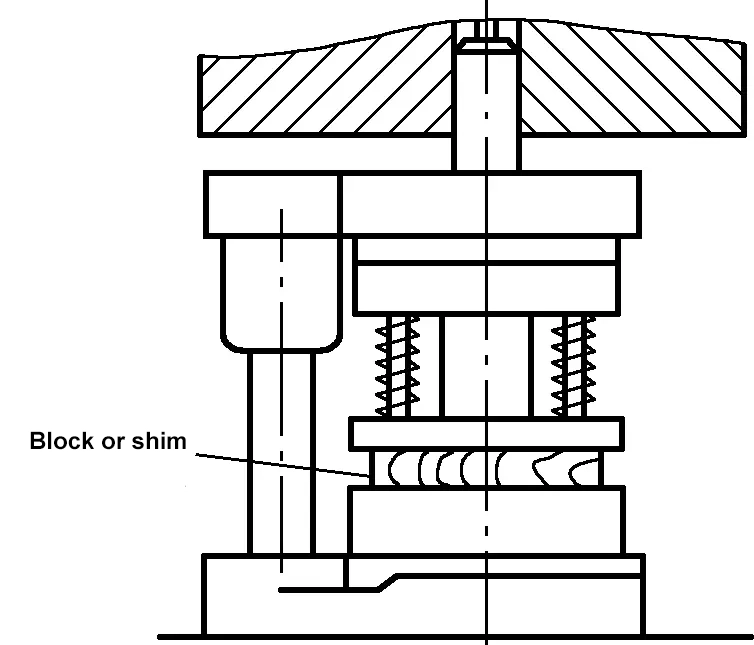
(2) 抜き型調整のポイント
抜き型調整のポイントは以下の通り:
1) パンチとダイのはめ込み深さの調整
カッティング・ダイの上型と下型を調整し、上型と下型の稼動部間のかみ合わせが適切な深さになるようにする。深すぎても浅すぎてもいけない。一般的に、カッティング・ダイは、パンチがダイに入る深さを0.5~1mmにし、硬質合金ダイの場合は0.5mmを超えないようにします。パンチとダイのはめ込み深さは、プレス機械のコネクティングロッドの長さを調整することで実現します。
2) パンチとダイのギャップの調整
カッティング・ダイは、パンチとダイの周囲に均一なギャップを確保しなければなりません。不適切な隙間や不均一な隙間は、プレス部品の品質に直接影響します。
ガイド付き部品切断ダイスの場合、ガイド部品(ガイドポストやガイドスリーブなど)間の嵌め合いが比較的正確で、上型と下型の間の均一な嵌め合いギャップを確保できるため、ガイド部品の移動精度が確保される限り、取り付けと調整は比較的便利である。
ノンガイドカッティングダイの場合、ダイの刃先に純銅箔や硬質ボール紙をライニングして調整することができます(純銅箔や硬質ボール紙の厚みは、パンチとダイの片側隙間に相当します)。プレス品のブランク厚みが1.5mmを超える場合は、ダイギャップが大きくなるため、前述のライニングによる調整が可能です。
より薄いワークピースの型抜きの場合は、プレス作業者が、相手パンチとダイの周囲の隙間の大きさを観察して、ダイを調整することができる。パンチとダイの間の隙間がある方向に比較的大きいことがわかったら、まず上型を固定し、下型を緩めます。そして、ハンマーで下型の側面を、隙間が小さくなる方向に向かって軽く叩く。適切な調整が終わったら、相手パンチとダイの周囲の隙間が均一になるまで観察を繰り返します。
刃先がストレートエッジのブランキング・ダイの場合、光透過法とフィーラーゲージ・テストでギャップを調整することができます。ポンチとダイが中央にあり、ギャップが均一であれば、ねじを使ってダイをプレス機に固定し、試し打ちを行います。
試し打ち後、試し打ちした部品を検査し、バリや切断面の荒れがないか確認する。不適当な場合は、下型を緩め、適正な隙間になるまで前記の方法で調整を続ける。
今後の生産において、ノンガイドブランキングダイの隙間調整を容易にするために、パンチとダイの片側隙間と同じ厚さの純銅板や硬質紙をパンチとともにダイキャビティに圧入する方法を用いることで、ブランキングダイの調整作業を軽減することができる。
3) 位置決め装置の調整
ブランキングダイの位置決め部品には、主に位置決めピン、位置決めブロック、位置決めプレートがあります。ブランキング・ダイを調整する際には、位置決め部品が位置決め要件を満たしているか、また位置決めが確実かどうかを確認する。位置決め部品の位置が適切でない場合は、調整中にトリミングし、必要に応じて交換する。
4) ストリッピング・システムの調整
ストリッピング・システムの調整では主に、ストリッパー・プレートやエジェクターがスムーズに機能するか、ストリッピング・スプリングやゴムの弾性は十分か、ストリッピング・ストロークは適切か、スクラップ・ホールに障害物はないか、パンチ・ロッドやプッシャー・ロッドが部品や廃棄物をスムーズに排出できるかなどをチェックする。不具合が見つかれば調整し、必要であれば交換する。
5.ブランキング作業の注意事項
ブランキングに使用される設備には、主に各種クランクプレスがある。作業にあたっては、まず使用する設備の性能や特性を熟知し、その操作方法をマスターする必要がある。次に、ブランキングに使用する金型の性能や特性を理解し、取り付けや調整ができることも重要である。また、ブランキング作業を行う際には、作業手順を守ることに留意する必要があるが、その主な要件は以下の点である。
(1) 作業前の要件
- 使用する個人用保護具や工具を準備する。
- シフトの引き継ぎ記録をチェックし、前シフトからの未解決の問題に注意を払う。
- 装置の緩みやすい部分が締まっているか確認する。
- 石油・ガスシステムの圧力が適切かどうか、パイプラインに漏れがないかどうかをチェックする。
- 必要に応じて機器に注油する。
- 工程ファイルと製造タスクシートの確認:使用金型とその設置状況の確認、材料仕様とグレードの確認、ブランキングピースの数量、その他工程ファイルに指定されている関連項目の確認。
(2) 作業中の要件
1) 電源を接続し、フライホイールが正常に回転した後、プレスを数回空運転させ、クラッチ、ブレーキ、制御システムが敏感で信頼できるかどうかをチェックする。
2) 数個のワークをテストし、自己検査を行い、検査員にチェックしてもらう。適格である場合のみ、通常の生産に進む。
3) 作業中、プレスの品質問題や異常動作、制御装置の誤動作、クラッチやブレーキの鈍感な反応などが発生した場合は、直ちに機械を停止させること。故障のまま運転することは厳禁です。
(3) 作業終了後の要求事項
- クラッチを切り、電源を切る。
- 作業場を清掃し、プレス機と金型を拭き、必要に応じて保護油を塗布する。
- シフト引継ぎの詳細を注意深く記録する。
6.ブランキングピースの一般的な欠陥とその解決策
ブランキングピースの一般的な欠陥には、大きなバリや表面のゆがみなどがあります。このような欠陥は、ブランキング材の問題、ブランキング金型の調整や問題、操作の過失などが原因として考えられます。欠陥の原因を注意深く分析した上で、解決策を考案すべきである。ブランキング材の一般的な欠陥と解決策については、表7を参照のこと。
表7 ブランキング・ピースの一般的な欠陥と解決策
品質ステータス | 原因 | ソリューション |
剪断された部分は、小さなバリがあるだけで、切断面にはある程度の傾きがある。 | 適度で均一な隙間、パンチとダイの鋭い刃先、重なり合うせん断亀裂。 | これは普通の状況だ。 |
切断面にはクラック、ダブルブライトバンド、バリがあり、打ち抜きサイズは小さくなり、ブランキングサイズは大きくなる。 | 隙間が小さすぎて、パンチとダイの刃先の亀裂が重なっていない。 | パンチとダイの刃先を研ぐ。 |
切断面の傾斜が大きく、バリの破れ、フィレットの拡大、打ち抜きサイズの拡大、ブランキングサイズの縮小が形成される。 | 隙間が大きすぎ、亀裂が重なっていない。 | パンチとダイの刃先を交換する。 |
切断面のバリの分布が不均一で、フィレットが安定しない。 | 1) パンチとダイの軸がずれているか、同軸になっていない。 2) ガイド装置のギャップが大きすぎる。 3) ガイド装置またはパンチが傾いている。 | 1) パンチとダイの相対位置を調整するか、刃先を研ぐ。 2) ガイド装置(ガイドブッシュなど)を交換する。 3) ガイド装置またはパンチを再び取り付ける。 |
打ち抜かれたピースのエッジに大きなバリがあり、ブランク加工されたピースのフィレットが増加している。 | ダイスの刃先が鈍いか、十分に硬くない。 | ダイスを研ぐか交換する。 |
ブランクピースには大きなバリが、パンチピースには大きなフィレットがある。 | パンチの刃先が鈍いか、十分な硬さがない。 | パンチを研ぐか交換する。 |
ブランクもパンチも、大きなバリや大きなフィレットがある。 | パンチもダイも鈍い。 | パンチとダイの両方を研ぐか交換する。 |
ワークピースの平面が凹んでいる。 | 1) ダイの刃先は逆テーパーになっている。 2) エジェクタロッドとワークの接触面積が小さすぎる。 3) ストリッパープレートは固定されている。 4) ダイホールを使ったブランキング | 1) ダイスの刃を研ぐ 2) エジェクターピンの交換 3) 弾性ストリッパー・プレートへの変更 4) 排出機構の改善 |
ワーク内孔のオフセット | 1) 位置決めリングとダイの位置ずれ 2) 材料ストッパーと供給装置のミスアライメント | 1) 位置決めリングの交換 2) 関連部品の再組み立てまたは交換 |
IV.ガス切断
ガス切断は、酸素アセチレン炎または酸素液化ガス炎の熱エネルギーを利用して、被加工物の切断部位を一定の温度に予熱した後、高速の切断ガス流を噴射して金属を燃焼させて熱を放出させ、切断を行う。
ガス切断は、利便性と強力な適応性の利点があります。鋼板や構造用鋼など、あらゆる厚みと種類の炭素鋼の切断を実現できる。さらに、ガス切断は生産コストが低い。
ガス切断は、切断ガスによって発生する火炎の違いによって分類され、酸素アセチレン火炎切断や酸素液化石油ガス切断などがある。操作方法によって、手動ガス切断、半自動ガス切断、CNC自動ガス切断に分けられる。酸素アセチレン手動ガス切断は、最も広く使用されている方法です。 板金加工.
1.ガス切断装置と工具
ガス切断に使用する機器や工具は、使用する可燃性ガスの種類によって若干異なる。図51に示すように、酸素ボンベと酸素レギュレーター、アセチレンボンベとアセチレンレギュレーター、フラッシュバックアレスター、トーチから構成される。
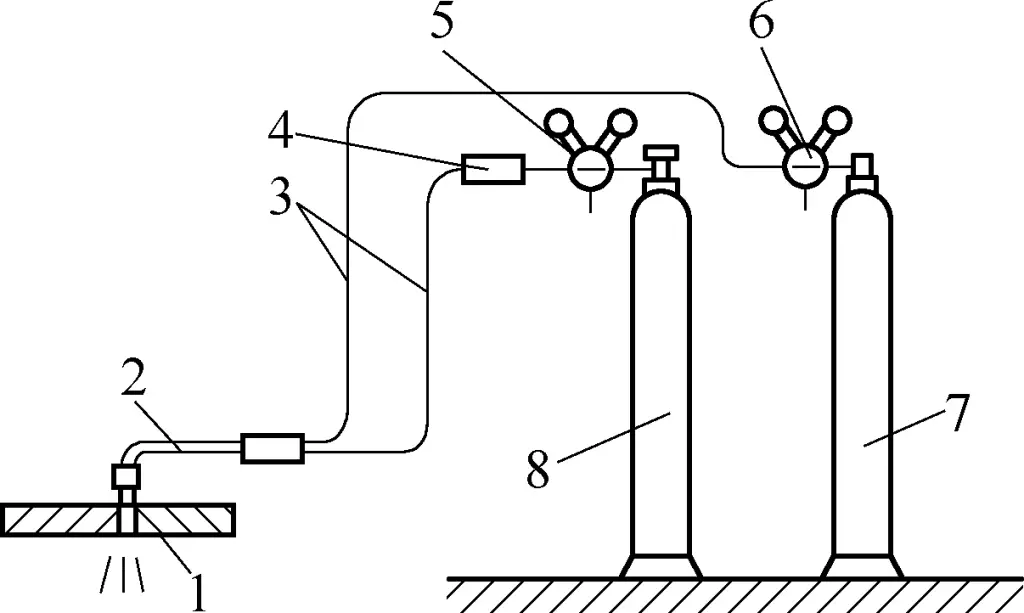
1-ワークピース
2トーチ
3ホース
4-フラッシュバックアレスター
5-アセチレンレギュレーター
6-酸素レギュレーター
7-酸素ボンベ
8-アセチレンボンベ
(1) 酸素ボンベおよびアセチレンボンベ
酸素ボンベは高圧酸素を貯蔵する円筒形の容器で、識別のために水色に塗装されている。最大圧力は16.7MPaで、容積は約40L、ガス容量は約6m3.酸素ボンベは爆発の危険性がある高圧容器であり、使用時には安全上の注意が必要である。激しい振動や衝撃を与えないよう取り扱いに注意し、使用中は裸火や熱源から5m以上離してください。
夏期は酸素ボンベを日光から保護し、冬期は凍結したバルブを火で解凍せず、温水で解凍する。ボンベ内の酸素を完全に使い切ってはならない。他のガスの侵入や爆発の可能性を防ぐため、残圧は98~196kPaに維持する必要がある。
アセチレンボンベは、アセチレンを貯蔵・運搬するための専用容器である。酸素ボンベに似ているが、やや短く(1.12m)、直径が大きい(250mm)。表面は白色で塗装され、赤色で「アセチレン」と表示されている。アセチレンを安定かつ安全に貯蔵するため、シリンダー内にはアセトンを染み込ませた多孔質体が充填されている。
アセチレンボンベは、取り扱い、積み込み、積み下ろし、使用中は直立させ、決して地面に平らに置かないでください。アセチレンの使用には圧力調整器が必要で、直接の使用は禁止されている。
(2) レギュレーター。
レギュレーターは高圧ガスを低圧ガスに減圧する装置です。その機能は、シリンダーからの高圧ガスを所望の使用圧力まで減圧し、圧力の安定性を維持することです。
図52は、単段レギュレーターの構造原理を示しています。調整ねじ1を時計回りに回すと圧力制御弁8が開き、シリンダーからの高圧ガスが高圧室7から圧力制御弁8を通って低圧室12に流れ込みます。ガスは膨張して作動圧力まで減圧され、出口11から排出されます。
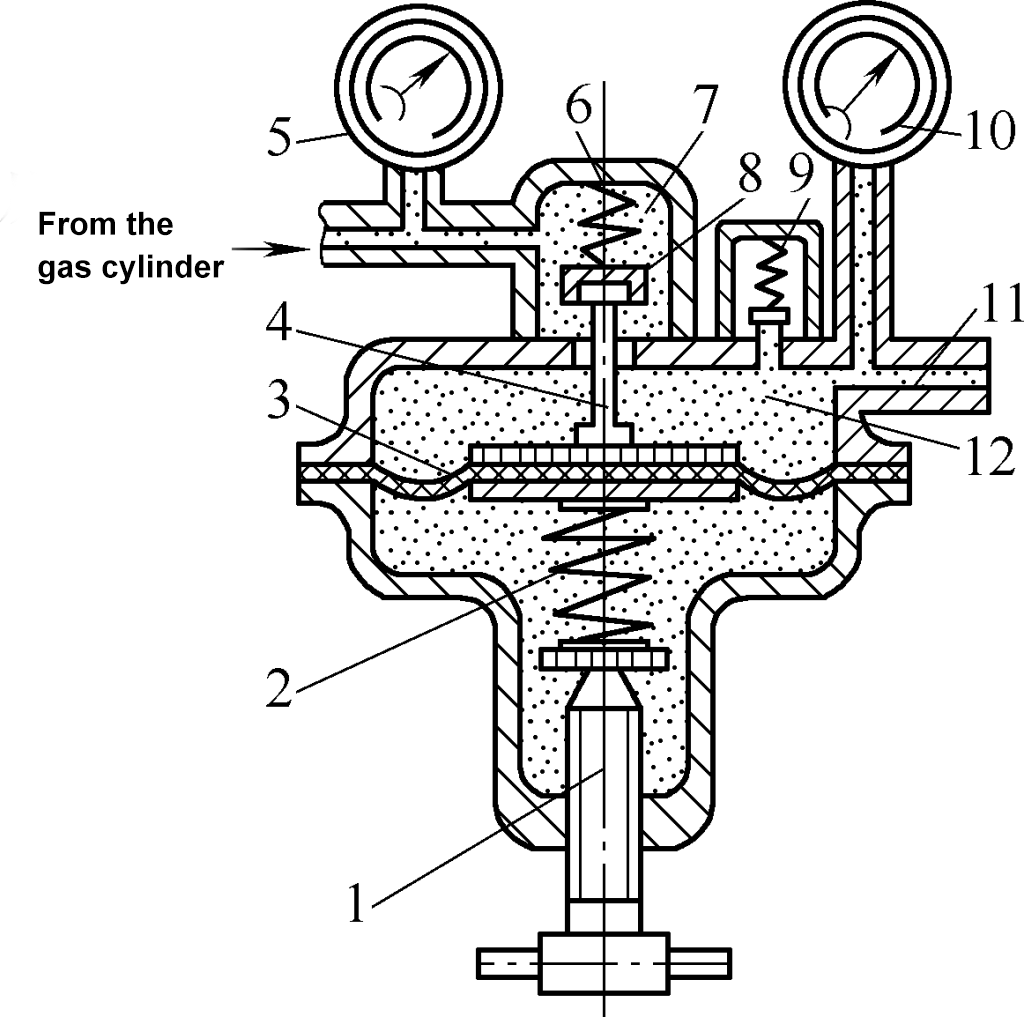
1-調整ネジ
2-スプリング
3-弾性ダイアフラム
4トランスミッション・ロッド
5-高圧ゲージ
6-補助スプリング
7-高圧チャンバー
8-圧力制御弁
9-安全バルブ
10-低圧ゲージ
11アウトレット
12-低圧チャンバー
作動圧力は、調整ねじ1の位置を変えることによって調整されます。 作動ばね2と補助ばね6により、シリンダ圧力が徐々に減少するにつれて圧力制御弁8が自動的に開き、バランスを保つことができ、作動圧力が安定した状態に保たれます。
酸素ガス用レギュレーターと溶存アセチレンガス用レギュレーターは、それぞれのガスの特性に合った専用のレギュレーターでなければならない。
(3) トーチとホース。
トーチの機能は、酸素とアセチレンを適切な割合で混合して予熱炎を形成し、高圧酸素を被切断物に噴射して、酸素噴流中の金属を燃焼させ、吹き飛ばして切り口を形成することである。
切断トーチは、図53に示すように、酸素とアセチレンの混合方法の違いにより、ジェット式と等圧式に分けられる。このうち、ジェット式切断トーチが最も一般的で、低圧または中圧のアセチレンガスに適している。表8にジェット式切断トーチの一般的な機種とパラメータを示す。

a) ジェットタイプの原理と形状
b) 等圧タイプの形状
1-カッティングノズル
2、9-ミキシングチューブ
3ジェットチューブ
4ノズル
5、10-酸素バルブ
6-酸素導管
7-アセチレン導管
8-アセチレンバルブ
表 8 ジェット型切断トーチの一般的なモデルとパラメータ
モデル | カッティングノズル | 低炭素鋼板の厚さ/mm | 切断ノズル酸素孔径/mm | ガス圧/MPa | ガス消費量/(L/min) | |||
番号 | タイプ | 酸素 | アセチレンガス | 酸素 | アセチレンガス | |||
G01-30 | 1 | リング形状 | 3~10 | 0.7 | 0.2 | 0.001~0.1 | 13.3 | 3.5 |
2 | 10~20 | 0.9 | 0.25 | 23.3 | 6.0 | |||
3 | 20~30 | 1.1 | 0.3 | 36.7 | 5.2 | |||
G01-100 | 1 | 梅の花の形 | 10~25 | 1.0 | 0.3 | 36.7~45 | 5.8~6.7 | |
2 | 25~50 | 1.3 | 0.4 | 58.2~71.7 | 7.7~8.3 |
注)型番中のGは切断トーチ、0は手動式、1はジェット式、以下の数字はガス切断用低炭素鋼の最大板厚(mm)を表す。
図53aにジェット式切断トーチを示す。ジェット型切断トーチは、固定ジェット管を使用し、異なる酸素孔径の切断ノズルを交換することにより、異なる厚さのワークの切断ニーズに対応することができる。生産現場で広く使われている。
作業時、予熱酸素は高速で混合室に入り、周囲のアセチレンガスを引き込み、一定の比率の混合ガスを形成し、切断ノズルから噴射される。着火後、予熱炎を形成する。切削酸素は、切削ノズルの中心孔から酸素チューブを通り、高速切削酸素流となる。
図53bは等圧式切断トーチである。等圧式切断トーチのアセチレン、予熱用酸素、切断用酸素はそれぞれ別々のパイプラインを通って切断ノズルに導入される。予熱用酸素とアセチレンは切断ノズル内で混合を開始し、噴射・点火された後、予熱炎を発生します。中圧のアセチレンガスに適しており、炎が安定し、フラッシュバックしにくいのが特徴です。
酸素ガス、アセチレンガス、液化石油ガスなどを切断トーチに供給するゴムホースで、高品質のゴムに織布や綿繊維を組み合わせたもの。酸素ホースの許容使用圧力は1.5MPa、ホース径は8mm、アセチレンホースの許容使用圧力は0.5MPa、ホース径は10mmです。識別しやすいように、酸素ホースは赤色、アセチレンホースは緑色となっている。
2.ガス切断技術
一般的なガス切断は、以下の手順と方法に従って行うことができる:
(1) ガス切断前の準備。
ワーク表面の油汚れや錆を落とし、酸化スラグを排出しやすくするため、ワークの下に一定の隙間を空けて、ワークを一定の高さまで上昇させる。
その後、切断酸素流線の形状を確認する。点検中、切断トーチに点火し、酸素とアセチレンの混合比を調節して予熱炎が中性炎になるようにする。オキシアセチレン火炎の性質を判断する最も簡単で実用的な方法は、その形状を観察することである。
中性の炎の長さは中程度で、炎芯、内炎、外炎の3つの明確な部分がある(図54a参照)。還元性の炎は長く明るく、内炎がより目立つ(図54b参照)。酸化性の炎は短く、内炎と外炎の境界は明らかではなく、明るさは暗い(図54c参照)。

1-炎芯
2-内炎
3-外炎
予熱炎を中立炎に調整した後、切断酸素を繰り返し放出し、混合調整バルブを調整して、切断プロセス中にオキシアセチレン炎が中立を維持できるようにする。切断気流(通称エアライン)の形状をさまざまな角度から観察し、均一で澄んだ円筒形であることを確認する。そうでない場合は、アセチレンと酸素を止め、標準的な切断気流が得られるまで、掃除針を使って切断ノズルを掃除する。
(2) ガス切断。
鋼板の端から切断を始める場合は、まず鋼板の端を予熱する。予熱点がわずかに赤くなったら、予熱炎の中心をエッジの外側に移動させ、切断用酸素バルブをゆっくりと開き、切断部の酸素流とともに酸化した溶融スラグが飛び出すのを観察する。切断が完了したら、図55に示すように、切断トーチをゆっくり動かして切断を続ける。
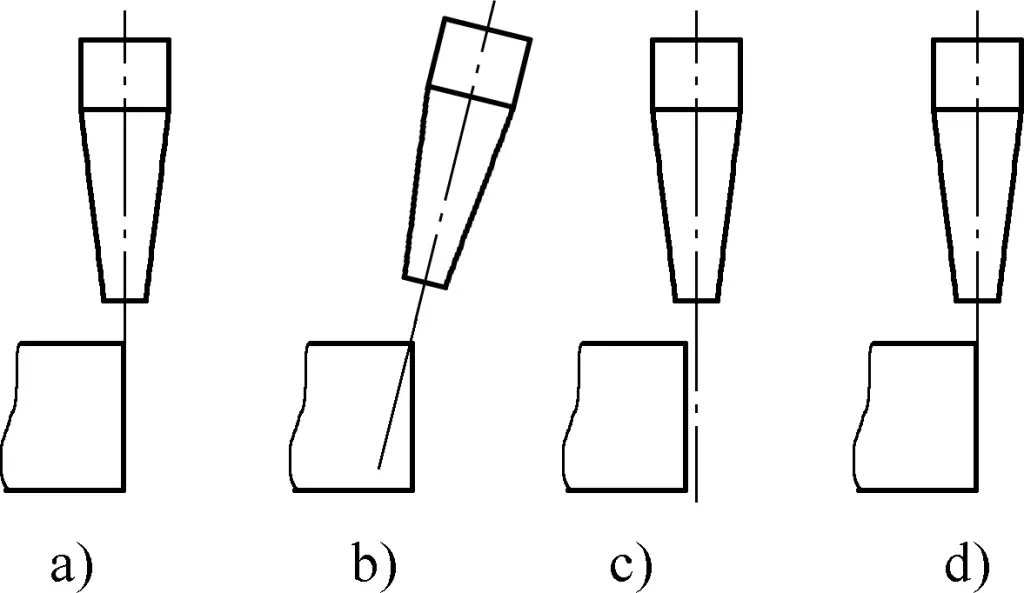
a), b) 予熱
c) 下がって酸素を放出する
d) カットの開始
について 切断速度 鋼板の厚さと切断面の品質要求に応じて決定されるべきである。
実際の作業において、切削速度が適切かどうかを判断する方法は2つある:切断面の筋目を観察する。条線が均一で、バックドラグが少なければ、切断速度が適切であることを示している。切断中、切断気流方向に沿って上部から切断を観察する。切断速度が適切であれば、切断部位の気流は明らかな曲がりのない滑らかなものでなければならない。
予熱炎を十分に利用し、切断時の能率を向上させるために、切断ノズルは、切断する鋼板の厚さに応じて、切断進行方向と反対方向に0°~30°後方に傾斜させることができ、鋼板が薄いほど、図56に示すように角度を大きくすることができる。
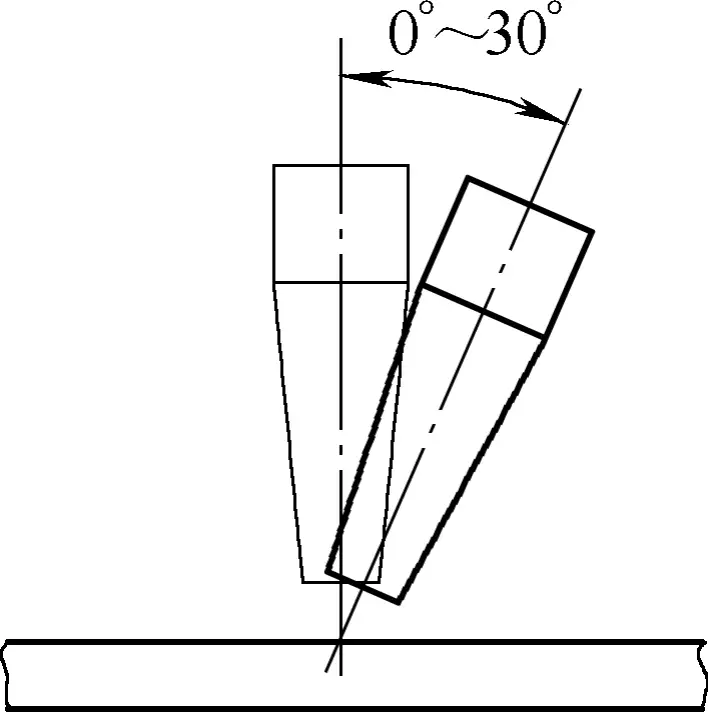
鋼板の中央のある位置に穴をあける必要がある場合は、図57に示すように、切断酸素を開放する際に、飛散したスラグが切断ノズルを塞がないように、切断ノズルの鋼板からの距離と角度を制御することに注意を払う必要がある。
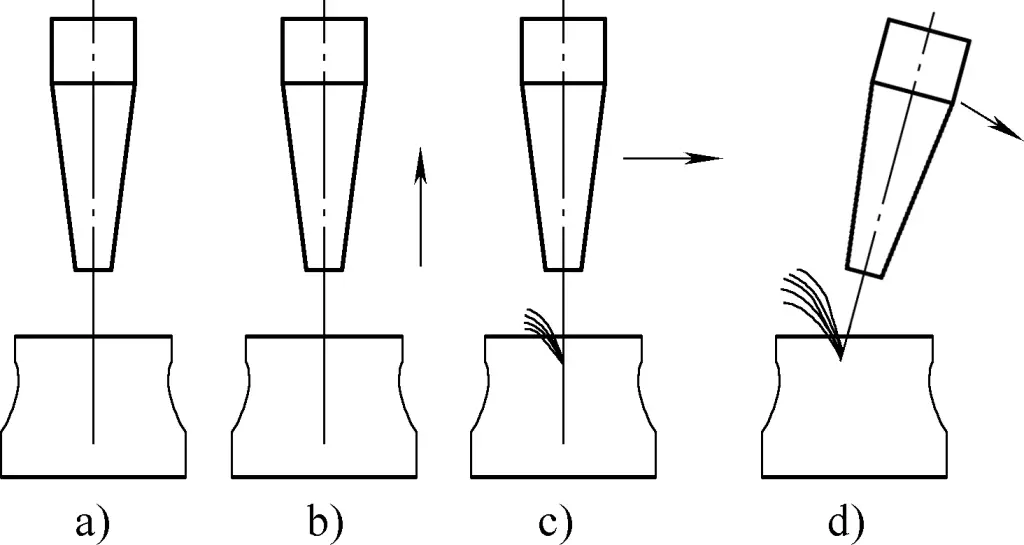
a) 予熱
b) カッティングノズルを持ち上げる
c) 酸素の切断を開始し、トーチを後方に動かす。
d) トーチを傾ける
ガス切断時のトーチの持ち方は、右手でトーチのハンドルを持ち、左手の親指、人差し指、中指で切断用酸素調整弁を支える。立っていても、しゃがんでいても、重心を安定させ、腕の筋肉をリラックスさせ、自然な呼吸をし、トーチを安定させ、切断速度の要求に応じて、または体の動きに合わせて、両腕をゆっくりと動かす。トーチ本体は切断対象物の上面と平行にする。
切断中、酸素やアセチレンガスの供給不足、スラグが切断ノズルを塞いだり、ノズルヘッドが過熱したりするために、しばしば逆火が発生する。この場合、ガス源を緊急に閉じる必要がある。正しい順序は次のとおり:まずアセチレン・ガス・バルブを閉じて可燃性ガス源を遮断し、次に混合ガス・バルブを閉じる。原因を特定し、解決した後、再点火して作業を続けてください。
(3) ガス切断の終了。
終点まで切断したら、切断用酸素バルブを閉じ、同時にトーチを持ち上げる。使用しない場合は、まずアセチレンガスバルブを閉め、最後に混合ガス調整バルブを閉めます。圧力調整器の調整ねじをゆるめ、アセチレンガスと酸素ボンベのバルブを閉じる。作業終了後、トーチ、圧力調整器を取り外して適切に保管し、アセチレンホース、酸素ゴムホースを巻き取り、作業場を清掃する。
3.低炭素鋼のガス切断
酸素アセチレン火炎ガス切断は、主に低炭素鋼や低合金鋼の切断に使用される。鋼板や形鋼の切断、溶接前の材料準備や溶接部の開先加工、様々な複雑形状の板の切断に広く使用されています。
(1) 鋼板のガス切断
酸素アセチレン火炎ガス切断は、異なる厚さの低炭素鋼板を切断することができ、操作方法も異なる。
1) 4~25mm厚鋼板のガス切断。
4〜25mm厚の鋼板をガス切断する場合は、G01-100タイプの切断トーチを選択できます。材料準備の際、切断気流(風切り線)の長さが切断する板厚の1/3以上になるようにする。切断ノズルと切断片の距離は、炎芯の長さに2~4mmを加えた長さにほぼ等しい。切断効率を上げるため、ガス切断時に切断ノズルを20°~30°後方に傾けることができる。
2) 薄鋼板のガス切断。
薄い鋼板をガス切断する場合、G01-30タイプの切断トーチとNo.2切断ノズルがよく選ばれる。より良い結果を得るためには、予熱炎のエネルギーを小さくし、切断ノズルを進行方向と反対方向に傾け、鋼板と25°~45°の角度を形成し、切断ノズルと切断片表面との距離を10~15mmとし、切断速度をできるだけ速くする必要がある。
3) 厚鋼板のガス切断。
厚い鋼板をガス切断する場合、まず切断片の端の角から予熱を開始する(図58a参照)。切断温度まで予熱したら、切断用酸素を徐々に増やし、切断ノズルを切断片に向けて傾ける(図58b参照)。切削片の端が完全に貫通したら、切削酸素の流量を増やし、切削ノズルを切削片の表面に対して垂直にする。同時に、切断ノズルを切断線に沿って移動させる。切断速度は遅くし、切断ノズルは三日月型の横揺れをするようにする(図58c参照)。
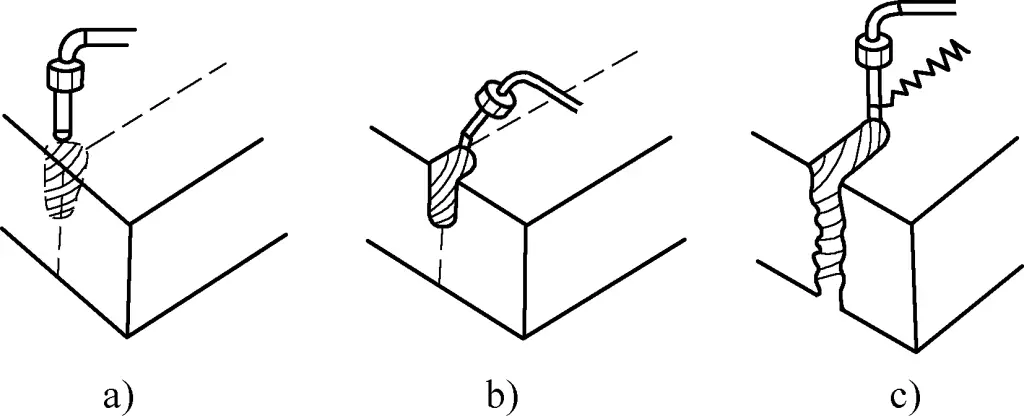
4) 鋼板に穴を開ける。
フランジ・リングタイプの部品をガス切断する場合、鋼板の端から切断を開始することはできないので、切断作業は鋼板の中央から開始しなければならない。鋼板に穴を開けたら、切断線に沿って切断する。
鋼板に穴を開ける方法を図59に示す。まず、鋼板の穴が必要な部分を予熱し、切断ノズルを鋼板に対して垂直に保持し(図59a参照)、切断温度まで加熱したら、切断ノズルを鋼板から約15mm離し(図59b参照)、切断用酸素バルブをゆっくりと開き、切断ノズルをわずかに傾ける(図59c参照)。
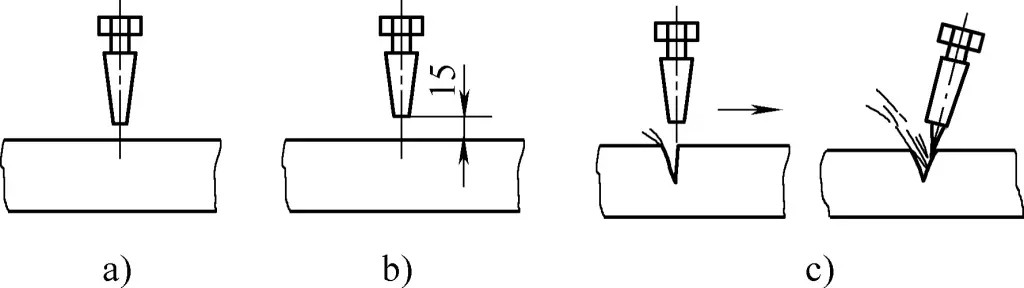
a) 予熱
b) ノズルを持ち上げる
c) 切断用酸素バルブをゆっくりと開く
穴あけ作業中は、飛散したスラグでやけどをしないよう、鋼板の表面に顔を向けないように注意する。
5) 多層鋼板のガス切断。
同じ形状の鋼板を何枚も重ねてガス切断する場合、一度に複数の鋼板の切断を完了させるために、鋼板を重ね合わせることが多い。多層鋼板の切断には、鋼板同士を密着させる必要があるため、プレス装置が必要であり(図60a参照)、鋼板表面の錆や汚れを落とす必要がある。
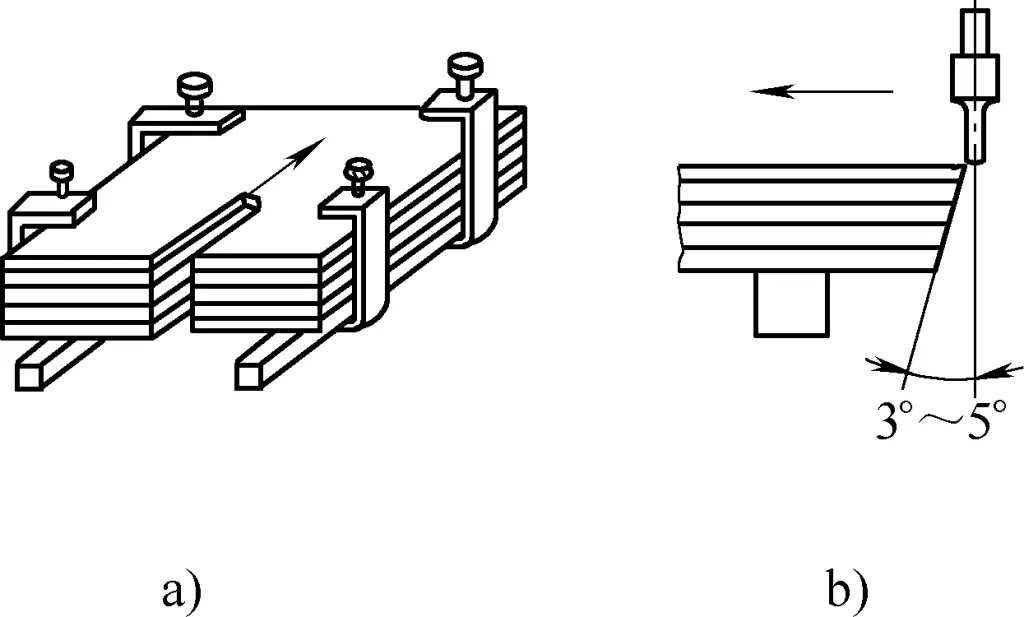
ガス切断を開始しやすくするため、上層の鋼板を少し外側に移動させる(図60b参照)。切断パラメーターは、多層鋼板の合計厚さに応じて決定する。上層鋼板の過度の溶解を避けるため、平らな鋼板を切断用のカバープレートとして使用することができる。
(2) 鋼管のガス切断
鋼管のガス切断では、予熱炎は鋼管の表面に対して垂直にする。完全に切断したら、切断ノズルをパイプ材の接線方向に近づくまで徐々に傾け、切断を続ける。
図 61a は固定鋼管のガス切断を示し、管材の下側から(下から見て)図中 1 で示す方向に予熱を開始する。パイプ材の上部まで切断したら、切断用酸素を閉じ、トーチを再びパイプ材の下側に移動させ、図中2の方向に切断を続ける。
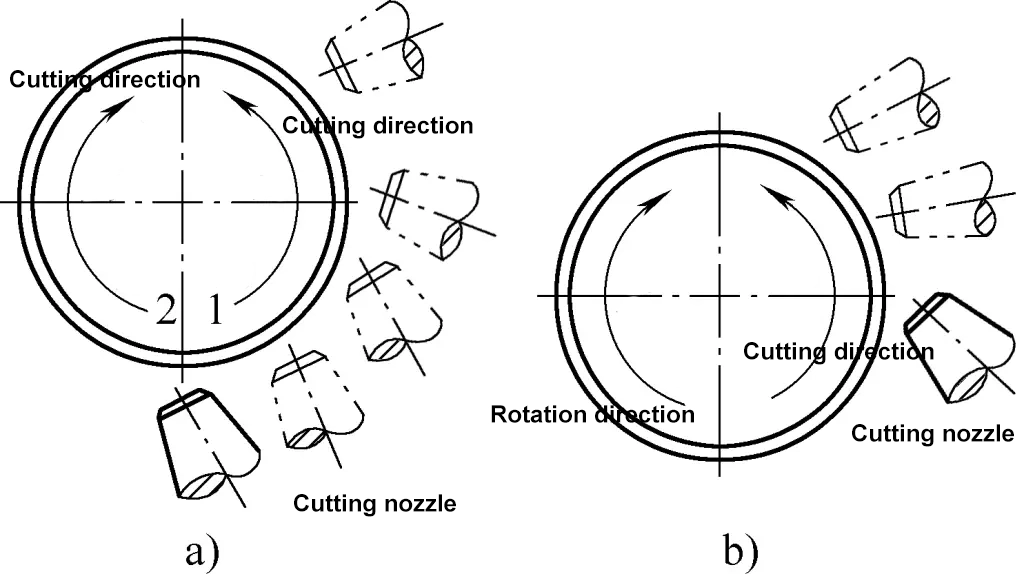
図61bは回転パイプ材のガス切断を示している。鋼管の側面から予熱を開始し、図の切断方向に沿って切断する。一部分を切断したら一時停止し、パイプ材を少し回転させてから切断を続ける。小径のパイプ材は2~3回で切断できるが、大径のパイプ材は複数回切断する必要があるが、少ない方がよい。
(3) 丸鋼のガス切断
丸鋼をガス切断する場合は、丸鋼の片側から予熱を開始する。予熱の炎は丸鋼の表面に対して垂直にする。ガス切断の開始と同時に、切断用酸素バルブを開き、切断ノズルを地面に対して垂直になるように回す。丸鋼を切断したら、切断ノズルを前進させ、わずかに水平に振る。
丸鋼の切断は一度に完了させるのが最善である。丸鋼の直径が大きく、一度で切断できない場合は、図62に示すような分割切断法を用いることができる。図中の数字は丸鋼の分割切断時の切断順序を示す。
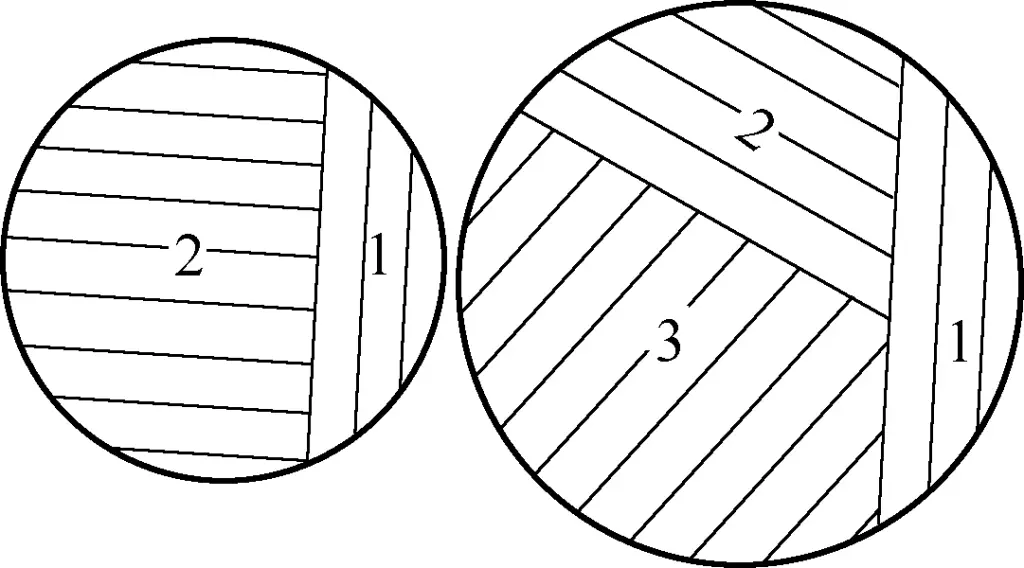
(4) I形鋼のガス切断
ガスでI形鋼を切断する場合、図63に示すように、下から上に向かって切断するのが原則である。こうすることで、残った材料が落下して切断部を傷つけたり、その他の事故を引き起こしたりすることはありません。ガス切断の際、切断ノズルは切断線に対して垂直にする。
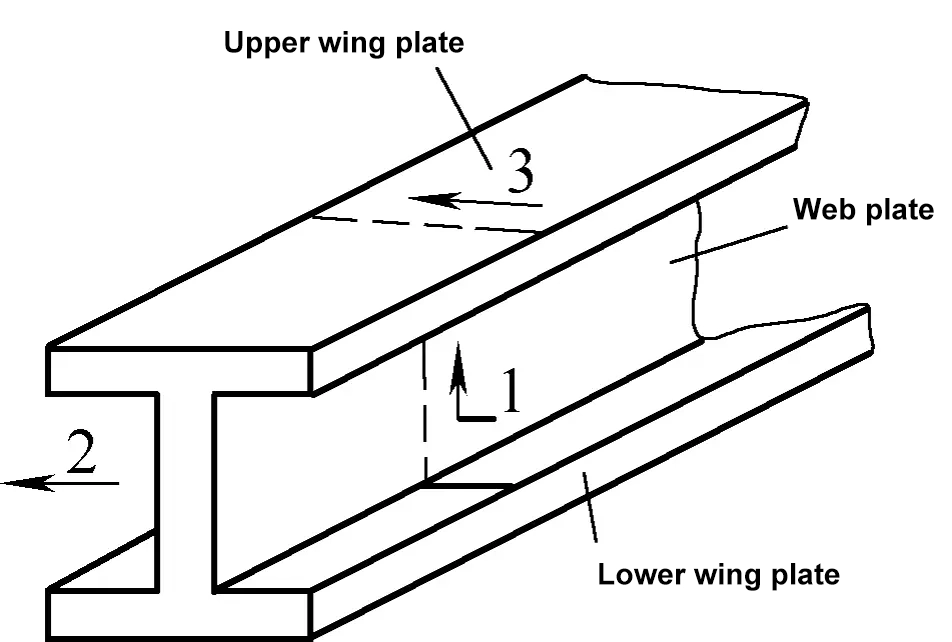
1-下フランジとウェブの片側をワンカットで完成させる。
2-ロアフランジの反対側をガスカットする。
3-最後に、ガスでトップフランジをカットする。
(5) 溝形鋼のガス切断
溝形鋼を直線に沿ってガス切断する場合、切断ノズルは切断面に対して垂直でなければならない(図64a参照)。傾斜切断の場合、ノズルはウェブに垂直であるべきであり、他の2つのフランジの場合、ノズルはウェブ上の傾斜線の方向に沿ってガス切断すべきである(図64b参照)。
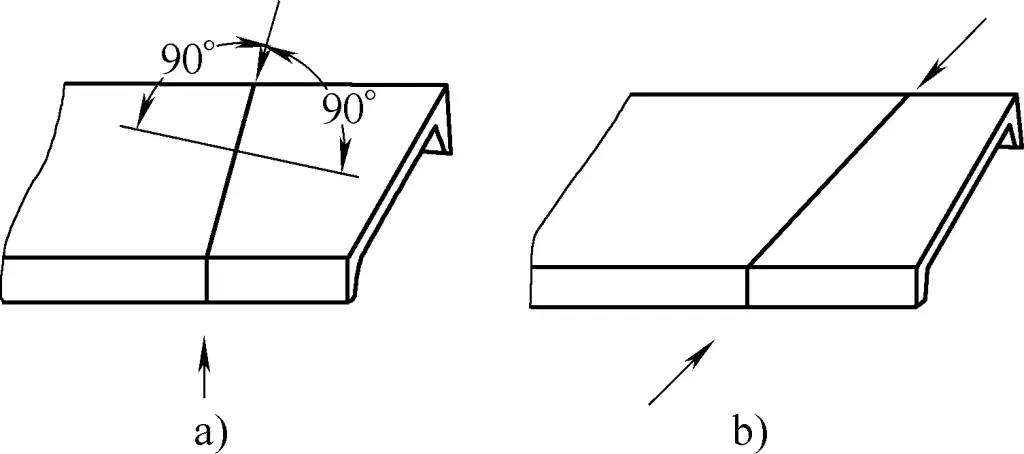
(6) 溶接溝のガス切断
一般的なガス切断に比べ、溶接開先のガス切断はやや速く、予熱火炎出力と切断酸素圧力をやや高くする必要がある。図65aは鋼板や鋼管の開先切断に使われるガス切断の形態を示し、図65bの方法は主に鋼管の開先切断に使われる。
パイプの溝をガス切断するために図65bに示す方法を使用する場合、予熱炎のパワーは図65aに示す方法を使用する場合よりも低く、鈍いエッジの燃焼を防ぐことができる。
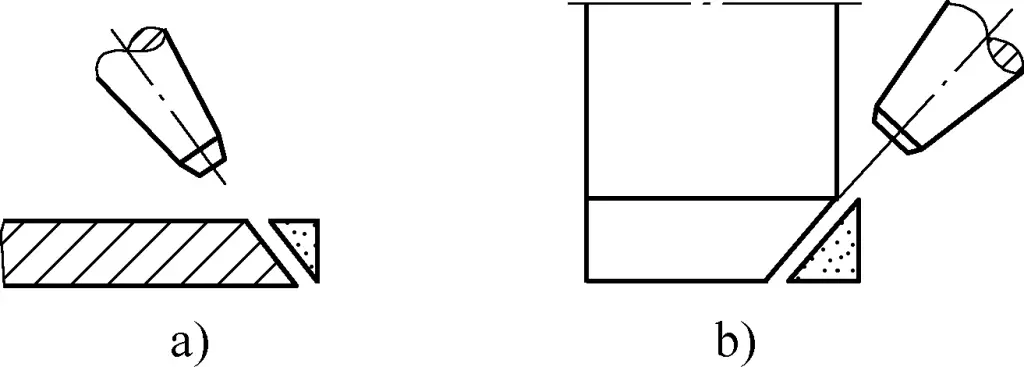
4.ガス切断作業の注意事項
ガス切断に使用されるアセチレンは引火性・爆発性のガスであり、酸素は燃焼補助効果が強く圧力が高いガスです。酸素ボンベ、アセチレンボンベ、アセチレン発生器はいずれも圧力容器であり、輸送、保管、使用時に一定のリスクがあります。
また、ガス切断時には直火を使用するため温度が高く、溶融スラグが大量に飛散し、火災や爆発の危険性が高まる。そのため、ガス切断作業では安全性と文明的生産に特に注意を払う必要がある。
一方、ガス切断における切断部品の品質は、切断工程パラメータの選択と手動操作の姿勢と密接に関係している。切断部品の品質を確保するためには、ガス切断作業中のガス切断プロセス仕様の選択にも注意を払う必要がある。
(1) ガス切断作業の安全に関する注意事項
ガス切断作業中の安全を確保するため、以下の主な注意事項を守ること:
1) ガス切断作業区域は安全要件を満たし、必要な消火設備を備えていなければならない。可燃性物質や爆発性物質がなく、換気がよく、一定の湿度が保たれていること。切削噴流や溶融スラグがセメント表面に直接触れることは厳禁である。アセチレン発生器、アセチレンボンベ、酸素ボンベは、作業エリアから安全な距離(通常10メートル以上)に置かなければならない。
2) 作業場で切断する鋼板または鋼片は、整然と配置し、安定した状態に置くこと。溶融スラグの排出を容易にし、爆発の原因となるアセチレンの蓄積を防止するため、切断場所の後方に一定の空間を確保すること。
切断後に発生するスクラップや残留スラグは、速やかに清掃すること。作業中、逆火防止器、酸素ホース、アセチレンホースは、溶融スラグに引火したり、切断部品に押しつぶされたりしないように、その流通方向を適切にする。
3) ガス切断に使用する安全装置や機器は、安全で信頼できるものでなければならない。例えば、逆火防止器は敏感で効果的であるべきであり、減圧器は正確に表示され、定期的に校正されるべきである。酸素ボンベやアセチレンボンベは、置き場所を固定し、整然と並べ、滑りや転がりを防止するために特殊なブラケットで固定する。
4) 作業者は、ガス切断作業を行う前に訓練を受け、資格を取得しなければならず、ガス切断の安全作業手順を厳守しなければならない。他人によるガス切断工具や機器の無断使用は厳禁です。作業中は、個人用保護具(ガス溶接ゴーグル、作業着、溶接手袋、必要な絶縁靴、ガードなど)を清潔にし、完全な状態にしてください。
(2) ガス切断作業の品質に関する注意事項
ガス切断作業中の切断部品の品質を確保するため、以下の注意事項も守ること:
1) 切断する鋼板や断面の厚さに応じて、適切な仕様の切断トーチとノズルを選択する。
2)ガス切断加工の仕様を正しく選択する。酸素アセチレン炎で切断する場合、ノズルと被加工物表面との距離は3~5mmが一般的で、板厚4mm以下の薄板では10~15mmを選ぶ。手動切断時のガス圧を表9に示す。ワーク表面に対するノズルの傾斜角度を表10に示す。
表 9 手動切断のガス圧
鋼板厚/mm | カッティング・トーチ | ガス圧/MPa | ||
タイプ | ノズル | 酸素 | アセチレン | |
<3 | G01-30 | 12 | 0.3~0.4 | 0.001~0.12 |
3~12 | 12 | 0.4~0.5 | ||
12~30 | 2,3,4 | 0.5~0.7 | ||
30~50 | G01-100 | 3,4,5 | 0.5~0.7 | |
50~100 | 56 | 0.6~0.8 | ||
100~150 | G01-300 | 7 | 0.8~1.6 | |
150~200 | 8 | 1.0~1.4 | ||
200~250 | 9 | 1.0~1.4 |
表10 ワーク表面に対するノズルの傾斜角度
ワーク厚さ/mm | <10 | 10~30 | >30 | ||
傾斜方向 | 後傾 | 後傾 | スタート時の前傾姿勢 | 貫通後垂直 | 最後に後傾 |
傾斜角度 | 0°~30° | 80°~85° | 80°~85° | 0° | 80°~85° |
ガス切断では、酸素圧が低すぎると金属の不完全燃焼を引き起こし、切断速度が低下し、切断間にスラグが付着することがある。一方、酸素圧が高すぎると、過剰な酸素がクーラントとして作用し、切断面が不均一になることがある。
切断用酸素ジェットの最適な長さは約500mmで、輪郭がはっきりしているため、スラグがスムーズに吹き付けられ、シャープなエッジできれいに切断される。そうでないと、深刻なスラグの付着や切断幅の不均一が発生する。
3) 切断には純酸素を使用する。純度が98%を下回ると、酸素中の窒素などの不純物が切断時に熱を吸収し、切断面に他の化合物膜を形成し、金属の燃焼を妨げ、切断速度を低下させ、酸素消費量を増加させます。
4) 被切断板は化学的にスケール除去し、酸化被膜を除去する。
5) 焼入れに敏感な鋼材の場合、ガス切断のエッジは、関連規則に従って表面亀裂検査と硬度試験を受ける必要がある。ガス切断中の環境温度が低い場合は、切断前に切断部位を予熱する。
ガス切断面の品質は、切断面の平坦度、切断痕の深さ、ノッチ間の最小距離に基づいて評価される。また、寸法偏差はガス切断における一般的な品質問題である。表11に、酸素アセチレン火炎切断面の一般的な欠陥とその原因を示す。
表11 酸素アセチレン炎による切断面の欠陥とその原因
欠陥 | 原因 |
ラフすぎる(深く切りすぎる) | 酸素純度が低い、切断酸素圧力が高すぎる、切断速度が速すぎる、予熱火炎出力が高すぎる |
多くのピット | 切断中の中断が多く、切断を再開する際の接続不良、錆を伴う表面の厚い酸化スケール、溝を切断する際の不十分な予熱炎、切断機のガイドレールの汚れによるキャリッジの揺れ。 |
凹面 | 切断酸素圧が高すぎる、切断速度が速すぎる |
傾斜 | 切断トーチが板面に対して垂直でない、切断気流が斜めになっている、切断酸素圧が低すぎる、ノズルサイズが小さい。 |
上端崩壊 | 予熱炎が強すぎる、切断速度が遅すぎる、ノズルが加工物に近すぎる、切断酸素圧が高すぎる |
下端に多くのスラグ | 酸素純度が低い、切断酸素圧が低い、予熱炎が強すぎる、切断速度が速すぎる、または遅すぎる |
浸炭 | ノズルが鋼板に近すぎ、予熱炎が還元炎になっている。 |
大きなドラッグマーク | 切断速度が速すぎる、切断酸素圧が不十分 |
(3) ガス切断の条件
すべての金属をガス切断できるわけではありません。ガス切断に使用する金属は、以下の条件を満たす必要があります:
1) 金属の発火点は融点より低くなければならない。金属の発火点が融点より高いと、発火点に達する前に金属が溶けてしまい、切断条件を満たさない切断ムラのある溶断になったり、まったく切断できなかったりする。
2) 金属酸化物の融点は、金属そのものの融点より低くなければならない。これにより、金属酸化物が時間内に吹き飛ばされ、新しい金属表面が露出し、連続切断が可能になる。そうでない場合、金属酸化物の融点が高く、加熱された金属表面を覆ってしまうと、下地金属と切断酸素との接触を妨げ、ガス切断を困難にする。
金属をガス切断する条件によると、ガス切断は主に炭素鋼と低合金鋼、例えば低炭素鋼、高マンガン鋼、低クロム、低クロムモリブデン、クロムニッケル合金鋼、チタン合金に使用される。高炭素鋼や高強度低合金鋼のガス切断は一般に難しい。鋳鉄、ステンレス鋼、銅、アルミニウムのような材料はガス切断できない。表12は、さまざまな金属のガス切断性能を示している。
表12 各種金属のガス切断性能
メタル | パフォーマンス |
鋼炭素含有量0.4%以下 | 良いカッティング |
スチール炭素含有量0.4%~0.5% | 切れ味が良い。割れを防ぐため、予熱は200℃、切断後は徐冷する。アニール温度は650℃とする。 |
スチール炭素含有量0.5%~0.7% | 切れ味が良い。切断前に700℃に予熱し、切断後にアニールする必要がある。 |
鋼炭素含有量0.7%以上 | カットが難しい |
鋳鉄 | カットが難しい |
高マンガン鋼 | 切れ味は良いが、予熱後の方が良い |
ケイ素鋼 | カット不良 |
低クロム合金鋼 | 良いカッティング |
低クロムおよび低クロム・ニッケルステンレス鋼 | 良いカッティング |
18-8クロム・ニッケルステンレス鋼 | 切断は可能だが、それに対応する運用技術が必要 |
銅および銅合金 | カット不可 |
アルミニウム | カット不可 |