
タングステン・イナート・ガス(TIG)溶接は、しばしばTIG溶接と呼ばれ、消耗しない電極と被加工物の間に熱を発生させるアーク溶接の一種である。
電極棒、溶接池、アーク、被加工物の加熱領域近 辺はすべて、ガス・シールドによって大気汚染から 隔離されている。このシールドは、定常流のガスまたは混合ガス (通常は不活性ガス)によって供給され、少量の大気 汚染でも溶接ビードを台無しにするため、完全 な保護を提供しなければならない。
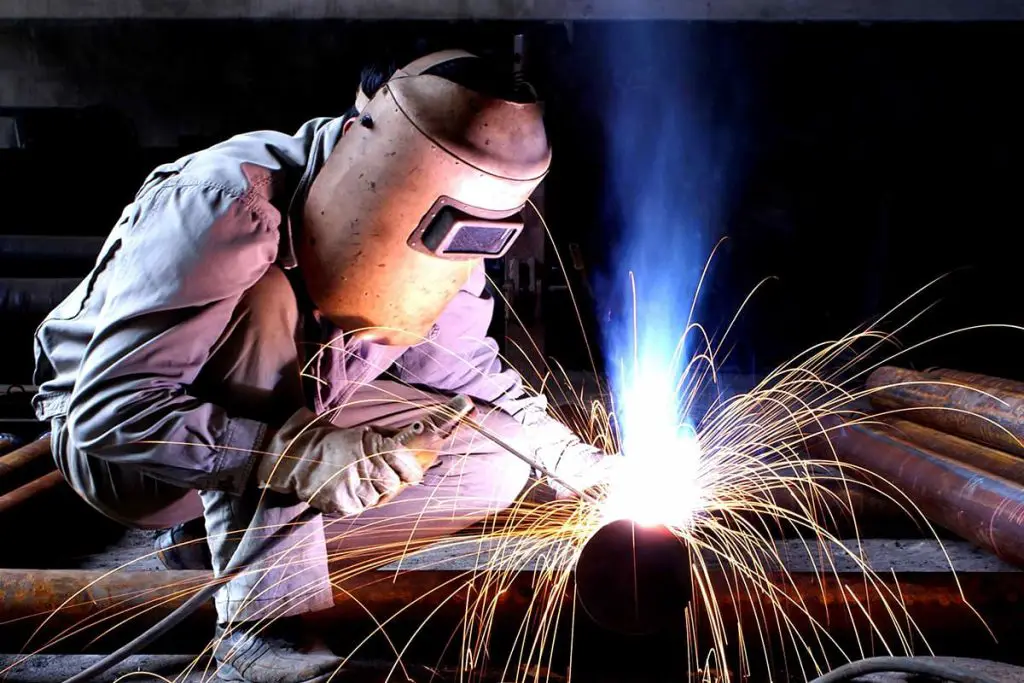
TIG溶接の原理
電極、アークゾーン、溶融金属を保護するためにアルゴンガスを使用し、電極として耐火金属純タングステンまたは活性化タングステン(トリア化タングステン、セリウム化タングステン)を使用するアーク溶接の方法(一般にタングステン不活性ガス(TIG)溶接として知られる)を図5-53に示す。
アルゴンは不活性ガスで、液体金属には溶解しない。溶接中、アークは電極とワークの間で燃焼し、アルゴンガスは金属プール、溶融液滴、タングステン電極チップを空気から隔離する。
TIG溶接の特徴
(1) 利点
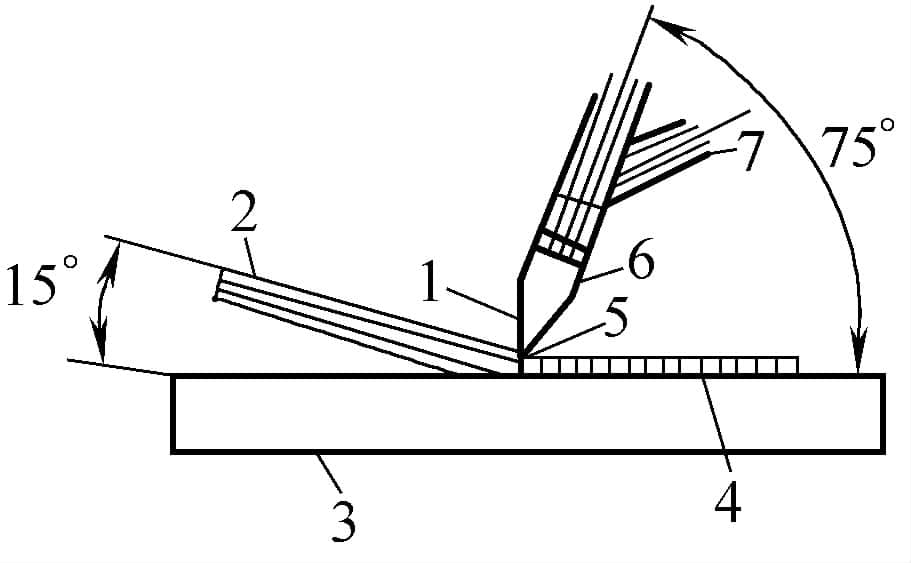
1-タングステン電極 2-溶加材 3-被加工材 4-溶接金属 5-アーク 6-ノズル 7-シールドガス
1)耐火金属タングステンまたは活性タングステン製の電極は、溶接中に溶融しない。アルゴンガスで雰囲気を遮断するため、酸素、窒素、水素などのガスがアークや溶融池に影響を与えず、溶接金属や溶接ワイヤの成分が燃えにくい(ごく一部が燃え落ちる)。
そのため、アーク長を一定に保つのが容易で、溶接プロセスが安定し、溶接品質も良好である。
2) 溶接中、フラックスが不要で、溶接面にスラグが付着しな いため、溶融池や溶接部の観察が容易で、欠陥を速やかに 発見できる。溶接中に適切な対策を講じることで、欠陥をなくすことができる。
3) タングステン・イナート・ガス溶接は安定性に優れ、 溶接電流が10A未満でもアークは安定的に燃焼 する。そのため、特に薄板の溶接に適している。
熱源とフィラー・ワイヤーが別々に制御されるため、熱調整が便利で、溶接部への入熱を制御しやすい。そのため、さまざまな位置での溶接に適しており、両面形成による片面溶接も容易である。
4) アルゴンガスの流れがアークを圧縮するため、熱が集中し、溶融池が小さくなる。シーム部付近のアルゴンガスの冷却効果により、熱影響部が狭くなり、ワークの変形が減少する。
ステンレス鋼を溶接する場合、溶接部の耐食性、 特に粒界腐食に対する耐性が特に優れている。
5) フィラーワイヤは溶接電流を流さないため、溶滴遷移によるアーク電圧と電流の変化に起因するスパッタが発生せず、平滑な溶接面を得るための好条件を提供する。
タングステン・イナート・ガス溶接のアークは明るいアークで、溶接プロセス・パラメーターは安定しており、監視と制御が容易で、機械化された自動溶接に適している。
(2) デメリット
1) タングステン・イナート・ガス溶接は、保護ガス を使用するため、横風に対する抵抗力が弱い。溶け込みが浅く、溶着速度が遅く、生産性が低い。
タングステンの蒸発の少量があり、溶接プールに入るタングステン粒子は、電流が高すぎる場合は特に、タングステン電極のバーンオフが深刻であり、タングステンの介在物は明らかである、溶接品質に影響を与える、タングステンの介在物を引き起こす可能性があります。
2)被覆アーク溶接に比べ、操作が難しく、設備が複雑で、溶接物の洗浄要求が特に高い。製造コストは、被覆アーク溶接よりも高い、 サブマージアーク溶接そしてCO2溶接。
TG溶接の適用範囲
タングステン不活性ガス溶接は、酸化しやすい非鉄金属を溶接することができます。 金属 およびその合金、ステンレス鋼、高温合金、チタンおよびチタン合金、ならびに耐火活性金属(モリブデン、ニオブ、ジルコニウム)など、主に板厚3mm以下の薄板溶接用。
圧力容器やパイプラインのような板厚の大きい重要な構造物には、ルートパス溶接に使用できる。タングステンイナートガス溶接
適用性
タングステン・イナート・ガス(TIG)溶接は、手動で行 うか自動で行うかにかかわらず、連続溶接、断続 溶接(「飛ばし溶接」と呼ばれることもある)、および、溶接の 過程で使用するのに適している。 スポット溶接.その電極が消耗品でないことから、溶加材を加える必要なく、母材を溶かすだけで溶接を行うことができる。しかし、特定の接合部については、特定の必要性に基づいて溶加材が必要となる場合がある。
TIG溶接は汎用性の高い溶接方法で、特に薄板の溶接に適している。
1.溶接用金属
TIG溶接の特性により、ほとんどの金属と合金の溶接に使用できる。TIG溶接が可能な金属には、炭素鋼、合金鋼、ステンレス鋼、耐熱合金、耐火金属、アルミニウム合金、マグネシウム合金、ベリリウム合金、銅合金、ニッケル合金、チタン合金、ジルコニウム合金などがある。
鉛と亜鉛はTIGでの溶接が難しい。これらの金属は融点が低いた め、溶接プロセスの制御が極めて難しい。亜鉛の気化温度は 1663°Fで、アーク温度よりかなり低い。鉛、スズ、亜鉛、カドミウム、アルミニウムで コーティングされた鋼鉄表面や、より高い温度で溶 けるその他の金属は、アーク溶接が可能であるが、 特別な手順が必要である。
被覆金属の溶接継手では、"金属間化合物" の形成により機械的特性が低下することがある。被覆金属の溶接時の金属間化合物形成を防ぐには、 溶接する部分の表面被覆を除去し、溶接後に補修する 必要がある。
2.ベースメタルの厚さ
TIG溶接は、幅広い金属厚に適用できる。アークが高濃度の熱を発生させ、溶接速度が速いため、厚さ3mm未満の溶接物に特に適している。溶加材を使用することで、複数回の溶接パスが可能である。
他の 溶接方法 は通常、6.25mmより厚い母材に使用されるが、 高品質で厚い溶接物では、マルチパス溶接に TIG溶接が必要になる場合がある。例えば、直径8mのロケット・エンジン用の15mm厚のシェルの製造では、フィラー・メタルによるTIG溶接が、複数の縦方向および円周方向の溶接に使用されている。このような厚い金属では、この溶接法の方が溶接速度が遅いが、溶接ビードに高品質が要求されるため、TIG溶接が使用されている。
TIG溶接は、様々な「箔厚」合金の溶接に成功する。薄板溶接には、精密な機器固定が必要である。箔厚の金属では、機械溶接または自動溶接が必要である。「高温イオン・アーク溶接」は、TIG溶接の変種とし て認識されることが多く、薄板溶接により多くの利点を もたらす。
3.ワーク形状
自動溶接を使用する場合、複雑な形状には手動 溶接が必要である。手動操作は、短い溶接ビードを必要とする不規則 な形状の対象物や、手の届きにくい場所の溶接に 適している。手動操作は、全姿勢溶接にも適している。
自動装置は曲面も直線も溶接できる。例えば、波型のチタン電極の両端を部品に当てる場合、特殊な正弦波溶接法が用いられます。このタイプの正弦波溶接では、機械的ガイドユニットが金属テンプレートに従って溶接トーチをガイドします。このような溶接の手動操作には、極めて難しい制御が要求されます。
TIGの基礎
タングステン・イナート・ガス(TIG)溶接では、 電極と被加工物の間に熱が発生し、被加工物の端 を溶かす。適切な融合を実現するためには、凝固時に 溶接池を清浄に保つことが極めて重要である。TIGで高品質の溶接を実現するには、使用する 溶加材だけでなく、すべての表面と隣接する 溶接部位を徹底的に清掃する必要がある。
特に高精度が要求され、被加工物が薄く複雑な形状の場合、溶接される部品の正確で安定した位置決めが、もうひとつの基本的な要件となる。溶加材を使用しない溶接や自動溶接では、特別な固定具が必要になる場合がある。
1.アーク開始
アーク開始」の一般的な方法には、電子放出とガスイオン化のトリガーが含まれる。これは、通電した電極を被加工物から必要なアーク長さまで素早く後退させるか、パイロットアーク、または電極と被加工物の間に高周波スパークを発生させる補助装置を使用することで達成できる。
被加工物から電極を機械的に引き込む方法は、直流溶接機による機械化溶接にのみ使用できる。しかし、パイロット・アーク開始法 は、手動溶接および機械化溶接に使用できるが、直流 溶接機に限定される。高周波スパーク開始法は、交流溶接機でも直流溶接機でも、手溶接に適用できる。多くの溶接機には、アーク開始と安定化のため に高周波スパークを発生させる装置がある。
2.電極棒とフィラーメタルの位置決め
手動タングステン・アーク溶接では、アークが始まったら、 電極棒が被加工物の表面から約75°離れ、溶接方向 を向くように溶接トーチを維持する。溶接開始時、アークは通常、母材が十分に溶融し て適切な大きさの溶融池ができるまで、円形に 移動する。
十分な溶融が達成されたら、溶接トーチをワーク ピース接合部の隣接するエッジに沿って徐々に 移動させる。ワークピースのこの漸進的な融合は、通常、手作業で溶加材を加える場合、ワークピースの表面から約15°の角度を保ち、ゆっくりと溶融プールに入りながら行われる。
金属フィラーを供給する際には、ガスシールドを破壊したり、電極棒に触れてフィラーロッド端部や電極棒の酸化による汚染を引き起こしたりしないように注意しなければならない。溶加棒は、連続的に追加することも、「浸漬」と「引き抜き」を繰り返すこともできる。
溶加材は、溶加棒と溶接経路の直線的な配置を 維持することによって(V字形継手のマルチ・パス継 手でよく使用される)、または溶加棒と溶接トーチ を左右に振って溶加棒を溶融池に送り込むことによって (サーフェシング・プロセスでよく使用される)、連続的 に加えることができる。
溶接を停止する際は、溶加金属を溶融池から引き 抜くが、溶加金属の酸化を防ぐため、一時的にガ ス保護下に置いておく。アークを消す前に、溶接トーチを溶融池の前端 に移動させ、アークを消すのにちょうど良い高さま で溶接トーチを持ち上げるが、クレーターや電極棒の汚 染を引き起こさないようにする。最良の方法は、溶接トーチを持ち上げる必要 はなく、フット・ペダル・コントロールを使用して、 電流を徐々に下げることである。
3.アークの長さ
多くの全自動タングステン・アーク溶接では、使用 するアーク長は電極棒の直径の約1.5倍であるが、 具体的な用途や溶接者の好みによって異なる。
しかし、アーク長 が長いほど、周囲の雰囲気に拡散する熱量が増 加するため、長いアークは溶接の安定した進行 を(ある程度)妨げることが多い。パイプラインの「ソケット・ジョイント」 は例外である。公定軸を使った垂直溶接では、長 いアークの方が短いアークよりも滑らかな隅肉 溶接ができる。
4.手動操作と自動操作
タングステン・イナート・ガス(TIG)溶接には、手動溶接と全自動溶接の区別がある。手動溶接は "溶接工 "によって行われ、自動溶接は "オペレーター "によって行われる。例えば、溶接電流の手動制御やフット・ペダルによる切り替えは、自動化に傾いた初期の開発である。
溶接ガンを一定または計画された速度で駆動し、アーク電圧(アーク長)を自動的に調整し、自動的に開始および停止する装置を使用することは、完全自動溶接を構成する。
5.溶接技術
オペレーターの選定と訓練は、主に使用する機器の「自動化の度合い」によって決まる。TIG溶接は多くの場合 金属板の接合 その応用として、溶接工は比較的小さな部品を容易に扱うことができる。
そのため、溶接工はしばしば、清掃、機器の組み合 わせと固定、スポット溶接作業に時間の一部を費やす。良質の溶接ビードを得るためには、高い手先の器用さと忍耐強い訓練が必要であるほか、溶接される部品の適切な組み立てと固定には、機械的な技術が不可欠な場合もある。
ある溶接方法から別の溶接方法に移行する場合、特 定の溶接技術の必要性が変化する。例えば、手動のガス・シールド溶接に熟練した 溶接士がTIG溶接の資格を得るには、さらなる訓練 が必要になる。さらに、消耗品であるバッキング・リングの 配置と溶接、補修溶接など、特殊な技術を必要と する用途もある。
6.検査
TIG溶接の検査には、板金溶接部の表面検査から、厚い溶接部のX線(レントゲン)検査や超音波検査まで、あらゆる非破壊検査法が含まれ、表面下(内部)に潜在的な欠陥がないかをチェックする。
溶接電流
どのような溶接作業においても、「電流」は溶け込み深さに関係するため、最も重要な作業条件である、 溶接速度凝固速度、溶接ビードの品質。
基本的に溶接電流には、(a)直流電極正(DCEP)、(b)直流電極負(DCEN)、(c)交流(AC)の3種類がある。これら3種類の電流に高周波電流を重畳することで、いくつかの所望の効果を得ることができる。
1.直流電極プラス(DCEP)
DCEPは、TIG溶接に最も広く使用されている電流タイプで、一般的に溶接可能なほぼすべての金属および合金で良好な溶接ビードを生成することができる。
DCEP溶接では、電極棒はマイナスで、被加工物金属はプラスであるため、電子の流れは電極棒から被加工物金属に向かう。すべての直流アークにおける熱の70%は、アークの正極または負極端で発生するため、あるサイズの電極棒は、より多くの正電流に耐え、より少ない負電流に耐えることができる。
同様に、特定のサイズの電極棒が最も高温のアークを必要とする場合、DCEPが必要な電流タイプである。
DCEPは、深くて狭い溶接ビードを生成でき、その 「溶け込み」は他の2種類の電流より優れている。しかし、溶接ビードが狭く、溶け込みが深いため、 DCEPによる薄い金属物の溶接は難しい。DCENやACと異なり、DCEPはアルミニウム、 マグネシウム、ベリリウム銅の表面酸化物を除去でき ない。
しかし、アルミニウムをDCEPで 溶接する場合は、溶接前に機械的または化学的洗浄を行 うとともに、特別に改良された溶接方法を使用しなけれ ばならない。DCEP溶接は、高周波安定化交流アーク 溶接に比べて熟練を要するが、その主な理由 は、DCEPがアークを打つ際に高周波誘導 放電を行なわないからである。
したがって、DCEPに高周波電流を重畳するための特別な装置を標準機に追加することができる。
2.直流逆極性
直流逆極性(DCRP)溶接では、電極棒は溶接機のプラス端子に接続され、ワーク金属はマイナス端子に接続される。その結果、電子の流れはワークから電極棒へと移動する。
このプロセスは、電極棒に高い熱を発生させ、被加工物に低い熱を発生させる。同じアンペア数とアーク長であれば、DCRPアークの電圧はDCSPアークよりわずかに高く、その結果、DCRPアークの総エネルギーは大きくなる。
DCRPは、平坦で幅が広く、浅い溶接経路を作 る傾向があるため、3種類の電流の中で最も一般 的でない。DCRPでの溶接は、同じ低電流値でより大 きな電極棒を使用する必要があるため、高度な 技能が要求される。そのため、一般的に は使用されない。DCRPは、「最も冷たい」効果的なアークを提供 するが、被加工物の表面から酸化物を除去する際 に優れた特性を持つ。
DCRPによるアルミニウム溶接は、溶融池が電極棒の先端に引き寄せられやすいため、特に難しい。電極はアルミニウムに接触すると汚染される。
しかし、DCRPは薄いアルミニウム板(0.6mm)の接合に効果的に使用できる。一方、マグネシウムはDCRP固有のアーク作用の影響を受けないため、コンタミネーションの問題が発生せず、厚さ3mmまでDCRPを使用して溶接できる。
3.酸化物除去のためのDCRP
DCRPが特定の卑金属の表面から酸化物を除去できる理由は、いくつかの理論で説明できる。一般的に受け入れられている説明は以下の通りである:
電極が正の場合、アルゴンまたはヘリウムイオンが母材表面に向かって移動する。周囲の不活性ガス雲では、アークの作用により荷電ガスイオンが発生する。これらのイオンはかなりの質量を持つため、金属表面に向かって突進する間に多くの運動エネルギーを得る。金属表面と衝突すると、サンドブラストの要領で酸化物粒子を引き剥がし、表面をきれいにします。
この作用により、アークのプラス側よりも母材に発生する熱量が少なくなり、結果として溶け込みが最小限になります。電極棒がマイナスで被加工物がプラスの場合、イオンは電極棒に向かって移動し、被加工物金属にはクリーニング作用はありません。電子による「砲撃」は、被加工金属にかなりの熱と貫入を引き起こす。
ステンレス鋼、炭素鋼、銅などの金属は、タ ングステン・イナート・ガス(TIG)溶接に大 きな影響を与える酸化被膜を形成しない。
4.溶接機の極性の決定
自動TIG溶接では、繰り返し操作のため、誤った極性で溶接作業を開始する危険性がある。手動溶接の場合、機械の端子接続が逆になって極性が変 わることがある。電極への潜在的な損傷(小さな電極棒に逆極性の電流を流した場合に発生する可能性がある)を避けるため、溶接作業を開始する前に極性をテストするのが最善である。
手動棒溶接の場合、電極ホルダーを回路に接続し、極性を テストする。全ポジション手動スティック溶接用のロッド(E6010 グレード)を逆極性で始動します。極性が正の場合、アークは強く、力強いヒューという音を発し ます。真の逆極性 E6010 アークでは、力強いクラッキング音は発生し ません。
5.交流 (AC)
交流は、電流の方向が1秒間に120回変化するDCSPとDCRPの間の連続的な振動と表現できる。交流では、電圧は各周期で正の最大値から負の最大値まで交互に変化し、この変化が起こるたびにアークは消えます。
不活性雰囲気で溶接する場合、従来のアーク 溶接用変圧器では、アーク消滅後にアークを再確立 するのに十分な高電圧を発生させることができない。同様に、十分な固有電圧を持つ変圧器を使用しない限り、各半サイクルで溶接アークを再確立するためには、アークに高周波電流を加えなければならない。
交流は良好な溶け込みを提供し、表面酸化物を 減らす(または戻す)。ACタングステンイナートガス(TIG)溶接で 生成される溶接ビードは、DCSPより広く浅いが、 DCRPより狭く深い。さらに、AC溶接ビードの補強はDCSPやDCRP よりも大きいため、ACはアルミニウム、マグネシ ウム、ベリリウム銅の溶接に適している。
6.交流整流防止
電圧の正と負の半サイクルは、交流アーク中に不均等な電流抵抗を発生させるため、不平衡な電流正弦波となり、整流効果の上昇を引き起こす。この効果は、アークブローや不安定性を引き起こすのに十分な高さの直流電圧の一部を交流アークに発生させる。
タングステン・イナート・ガス(TIG)溶接に使用される古いトランスは、最新のバランス波形コンポーネントがないため、整流が起こりやすい。
整流は、電極棒と溶接金属から電子が不均等に放出されるために起こる。整流は、電極先端と被加工物のアーク電流密度(温度を制御するため)、アーク長、使用する保護ガスの影響をある程度受ける。アルミニウム溶接では、整流によって最大12Vの直流電圧成分を発生させることができる。
直流成分が高いと、明るいアルミニウムの溶融池が暗くなり、酸化皮膜が形成されるが、その程度は直流成分の大きさに正比例する。
整流とその有害な影響を排除するために、平衡波 形変圧器を使用することができる。このようなユニットには、溶接回路と直列にコンデ ンサが含まれている。このコンデンサーの静電容量によって、交流 溶接電流の一部を遮断しつつ、効果的な電流を流 すことができる。これらの部品は通常、100~150ボルトの範囲の 開回路電圧を持つように設計されており、アーク 発生に高周波電流を必要とし、アルミニウムやマグネ シウム合金の溶接に広く使用されている。
7.パルス電流溶接
パルス電流タングステン不活性ガス(TIG)溶接は、高 い繰り返しパルス・レートで高い電流上昇率と減衰 率で作動し、精密部品の接合に広く使用され ている。より低速の電流パルス・レートは、機械化さ れたパイプ溶接およびその他の機械化された 溶接用途に使用される。
現在、パルスTIG溶接におけるアーク電圧の自動 精密制御を可能にする回路が開発されている。これらの回路は、高パルス電流を使用してアーク電圧 を発生させ、残りのサイクルの間、制御をロックする。改良された形状のパルス電流溶接機では、以下の 機能が独立して開始される。
パルス電流TIG溶接の利点は以下の通りである:
1.溶接部の「深さ対幅」比の増加:短時間の高電流溶接パルスと小型の純トリウ ム・タングステン電極棒を使用することで、ステンレ ス鋼溶接で発生するアーク力は、溶接部の深さ と幅の比を2:1にする。
2.たるみ」大電流の排除:短時間パルスは、溶融池が十分に膨張して垂れる前に、 溶接部のルートまたは薄いワークピース金属を「貫通」 し、凝固させることができる。
3.熱影響部の最小化:高パルスの高さと持続時間と低パルスの高さと持続時間の適切な比率によって、熱影響部を最小化することができる。低パルスの高さをゼロに設定し、高電流パルス間のギャップを限定的に維持することもある。
4.溶融池の攪拌:大電流パルスによって発生するアークと電磁力は、 定常電流溶接よりもはるかに大きい。これらの大きな力は溶融池を攪拌し、継手底部でのピンホールや不完全融着の可能性を低減する。低電流溶接でパルスが生み出す硬いアークは、 低定常電流で発生する可能性のあるアーク散乱の 不安定性を排除する。
溶接機
タングステン・イナート・ガス(TIG)溶接用の溶接機には、以下のものがある:
(a)直流(DC)出力の変圧器整流器タイプ。
(b) 交流(AC)出力の変圧器タイプ。
(c) 動力駆動発電機-電動機駆動(交流出力のみ)またはエンジン駆動(交流または直流出力)。
変圧器および整流器タイプの溶接機には、動力駆動型発電機と比較して、イニシャル・コストが低い、ウォームアップ時の電流降下がない、運転音が静か、メンテナンスおよび運転コストが低い、可動部品がない、休止時の電力入力が低い、などの利点がある。エンジン駆動発電機の利点は、電源のない場所でも使用できることである。
1.高周波安定化
大型のエア・ギャップまたはチューブ・オシレーターが、アーク開始用、場合によっては連続使用用の溶接トランス回路に接続されている。高周波安定化交流を使用した初期のTIG溶接では、「電波干渉」によってかなりのトラブルが発生した。
しかし今日では、振動する電気ステーション、「電子管」制動装置、独特の位相を持つ高周波変圧器などが、より弱い火花放電を供給し、「電波干渉」現象を減らしている。
一部の古い変圧器を改造する場合は、接触アーク 発生用に高周波安定化回路を設置する。AC溶接機には、操作用のフット・スイッチを備えた磁気コンタクターを追加することができる。
このセットアップでは、溶接工は電極棒をワーク・カバーの下 の始点に向けて配置し、フット・スイッチを押します。電極棒をワークから離すと、アークが開始される。このプロセスは簡単で、溶接電流を止めるには、溶接者はフット・スイッチを離すだけでよい。
必要な高周波誘導放電の強さは、継手の設計、 電極棒の突出長、最小の高周波誘導電流でアーク を発生させる溶接士の能力によって決まる。深い開先継手で溶接する場合は、高周波電流の強度を低くする必要がある。そうしないと、アークが開先幅を橋渡ししてしまい、継手の付け根に入らないからである。
過度の高周波安定化は、以下のような悪影響を及ぼす可能性がある:
1.操作者が感電する可能性が高くなる。
2.不安定な溶接アーク。
3.金属製ノズルを使用する場合は、ノズルの "電化"。
4.高周波が絶縁体を貫通するため、溶接ケーブルの寿命が短くなる。
5.電波干渉の増加。
溶接電流に高周波回路を追加する場合は、電極棒を取り付 ける前や調整する前、または溶接ヘッドの金属部分に手を 付けたり近づけたりする前に、必ず電源を切ってください。さもないと、特に作業者がワークの近くの暖かい空気に触れると、激しい感電が起こる可能性があります。
高周波安定化交流で溶接すると、アークが消え た後、電極棒がまだ熱いうちに、電極棒の先端に紫 色のハローが現れる。電極棒が冷えるにつれて、紫色のハ ロは劇的に薄れ、ある温度に達すると突然消えます。紫色のハローが見えている間でも、電極棒は被加工物からかなり離れた位置でアークを発生させる可能性があるため、突然のアーク発生や不要な場所でのアーク燃焼を避けるよう注意が必要です。
2.「ホットスタート装置
特定の溶接作業では、可能な限り短い時間遅れで 溶接プロセス(アーク・スタート)を開始するために、 (通常のレベルよりかなり高い)サージ電流を流す 必要がある。これは、自動または半自動溶接で特に有用である。ホット・スタート装置は、この初期電流のサージを供給 するために回路に接続される。この装置は通常、必要な追加電流と所望の持続時間を供給するよう、事前に調整することができる。
3.電力サージの軽減
短時間の大電流と頻繁な始動を伴う溶接作業では、誘導モー ターを溶接機の端子と並列に使用することで、ライン内の電 力サージを緩和することができる。外部負荷のないこのモーターは、溶接機の KVA定格を上回る定格馬力を持つ必要がある。
アークスタート時に短絡による電流サージが発生してライン電圧が低下した場合、回転電機子にはラインに供給される実質的な電力に変換するのに十分な運動エネルギーがあります。線路の急激な電圧降下はモータを減速させ、モータの回転エネルギーは電気エネルギーに変換され、アークスタート時の線路電圧降下を緊急に抑えるために使用されない限り、線路電圧の上昇を維持するのに役立ちます。しかし、このようなセットアップを実施する前に、慎重なコスト分析を行う必要がある。
4.クレーター充填のための電流低減
特定の用途では、溶接クレーター内の消火点 での突然の窪みを避け、溶接経路の終端を対称的 に仕上げる必要がある。アルミニウムとマグネシウム合金の溶接では、仕上 げの直前に溶接電流を下げなければならない。
しかし、ニッケル基合金やコバルト基合金のような「脈動」に非常に敏感な金属は、アークを消火するために電流を徐々に減少させ、溶融金属フィラーの温度を助ける必要がある(これはまた、水たまりの量を減らすことができる)。
そうしないと、クレーター割れは避けられない。消火後のクレーターの「渇き」や窪みを避けるには、 溶接経路を終点を過ぎても続け、金属が溶融しなくな るレベルまで電流を徐々に下げなければならない。そうしないと、アークが停止したときに被溶接材 に窪みやアーク痕が形成され、こうした痕や微 細な亀裂が腐食の可能性を高めることになる。
5.溶接トーチ
手動タングステン・アーク溶接用の溶接トーチ は、頑丈で軽量、かつ完全に絶縁されていなけれ ばならない。加圧用のハンド・グリップがあり、保護ガス をアーク部分に供給できるものでなければな らない。
さらに、チュー ブ・クランプまたはクランプ・ヘッド、あるいは溶接 電流をタングステン電極棒にしっかりと押し付け、導 くための別の方法が必要である。溶接トーチ・アセンブリには通常、トーチを電源に接続するためのさまざまなケーブル、ホース、カップリング部品、さらにガスや水が含まれている。
図3は、典型的な水冷式手動溶接トーチを示している。保護ガスが通過するシステム全体が気密でなければ ならない。ホースの継ぎ目でガスが漏れると、ガスが著しく損失 し、溶融池の保護が不十分になる可能性がある。ガス・システム内への空気の混入は、しばしば大 きな問題となるため、ガス・システムの気密性を確保す るための入念なメンテナンスが必要である。
タングステン・アーク溶接トーチには、さまざまな サイズと種類があり、重さは数オンスから1ポンド 近くまである。溶接トーチの サイズは、使用できる最大溶接電流によって決ま り、さまざまなサイズの電極棒や、さまざまな タイプとサイズのノズルを装備できる。
電極棒とハンドルの角度も溶接トーチによって異なる。最も一般的な角度は約120°だが、ヘッド角度が90°の溶接トーチや、直線的な溶接トーチ、さらには角度調整可能な溶接トーチもある。溶接トーチによっては、ハンドルに補助スイッチやガスバルブが取り付けられているものもある。
タングステン・アーク溶接トーチの主な違いは、空 冷式か水冷式かである。空冷トーチの冷却の大部分は、ガス・シ ールドによって行なわれる。したがって、より正確な用語は "ガス冷却 "である。真の空冷は、周囲の空気への放射によってのみ達成される。一方、水冷式溶接トーチの冷却の一部は、シールド・ガスによって行われるが、残りはトーチ内を循環する水による追加冷却である。
空冷式溶接トーチは一般に軽量、コンパクトで耐久性があり、水冷式溶接トーチよりも安価である。しかし、一般的に溶接電流は約125アンペア以下に制限され、通常、使用率の低い薄板の溶接に使用される。タングステン電極棒の動作温度は、水冷溶接トーチよりも高く、その結果、純粋なタングステン電極棒を使用したり、定格電流容量の近くで溶接する場合、タングステン粒子が溶融プールに落ちることがあります。
水冷式溶接トーチは連続大電流溶接用に設計されており、最大200アンペアの溶接電流で持続的に作動できる。最大溶接電流500アンペアに対応するものもあり、空冷溶接トーチより重く高価である。
溶接トーチは、水道管や関連コネクターに接続される。通常、溶接機から電極棒に電流を送るケーブルは、水冷システムの出口パイプライン内に収容される。これによりケーブルが冷却され、小口径、軽量、フレキシブルな配線の使用が可能になる。時には、継手、フロー・スイッチ、ヒューズも含まれる。溶接トーチ内の水漏れやガス漏れ、あるいは湿気を 含むシステムは、溶接経路を汚染し、スムーズな操作 を妨げる可能性がある。