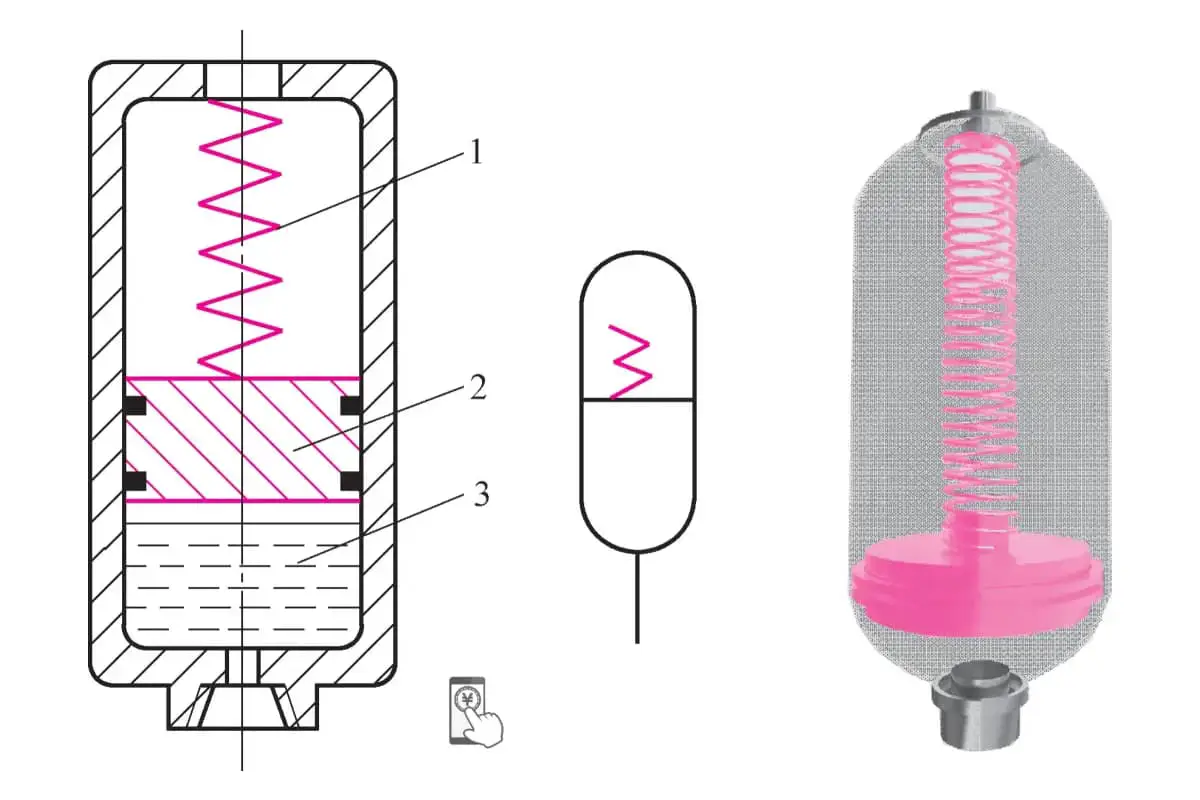
1.ファイル・フィッティング・プロセス
2つ以上の一致する部品を、指定された技術要件に適合させるためにファイリング方法を使用する操作は、ファイルフィッティングと呼ばれています。
(1) ファイル・フィッティングのための基準部品の選定
1) ファイル・フィッティングのための基準部品の定義
ヤスリ合わせの基準部品とは、すべてのヤスリ合わせ部品の中で、ヤスリ合わせ前に工程分析によって選択された「テンプレート部品」を指す。この部品は、加工後、測定テンプレートとして使用することができ、他の適合部品のファイリング調整時に測定ツールと協力し、他の適合部品のファイリング精度を共同で測定および管理することにより、必要なファイルを正確かつ迅速に完成させることができます。 フィッティング 精度が高い。
2) 基準部品選定の原則
基準部品は、他の適合部品よりも、ヤスリがけによって要求される寸法精度、形状・位置精度、表面粗さ値を達成しやすいはずである。
凸部が基準部品として好まれるのは、凹部に比べて凸部が測定しやすい、すなわち測定による精度管理がしやすいからである。凹面部品は内面があるため、測定工具が入りにくく、測定作業が難しい。測定しやすい凹型部品であれば、凸型部品にヤスリをかけるための基準部品として使うこともできる。
(2) ファイル・フィッティング・プロセス
1) 参考部品のファイリング
ファイル装着工程は、一般に個別ファイリング工程とファイリング調整工程に分けられる。個別のヤスリがけ方法は、前述のとおりである。通常、ヤスリ掛け工程は、まず基準部品をヤスリ掛けする。基準部品が要求される寸法精度、形状精度、位置精度、表面粗さ(基準部品の表面粗さは、通常、図面の技術要求より1ランク高い)を満たしたら、加工を終了する。その後のファイル・フィッティングでは、テンプレート部品としての基準部品は加工できなくなる。
2) その他の適合部品のファイリング
他の合わせ部品は、形状、位置の精度と表面粗さの要求を満たすようにヤスリをかけるが、ヤスリをかけるためのトリミング代は残しておく。凹面部品が合わせ部品である場合、一般に、凹面部品の内面を加工する際の加工精度の管理を容易にするために、凹面部品の関連する外面を測定基準として選択することが望ましい。したがって、凹面部品の外形基準面は、より高い形状精度と位置精度を達成しなければならない。
3) 調整プロセス
基準部品を使用して、他の適合部品を比較し、試着する。ライト・ギャップ法または染色スメア法を使用して適合部品を測定し、適合部品のファイリング領域を決定する。次に、測定具を組み合わせて適合部品を測定し、トリミング代を決定し、必要なはめあい精度を達成するために徐々に加工する。
(3) 非接触フィッティングについて
非接触フィッティングでは、基準部品(測定用テンプレート)を使ってマッチング部品を直接測定することができないため、要求されるフィッティング精度を達成するためには、綿密な測定作業によってすべてのフィッティング部品の寸法精度や形状・位置精度を管理するしかない。
ヤスリ掛け作業をより効果的にするためには、形状や位置の誤差が機能寸法に与える影響を総合的に分析し、できるだけ基準部品を比較作業のテンプレートとして使用する必要がある。入念な観察と正確な測定を通じて、適合部品の調整と試着が行われる。
さらに、非接触で満足のいくフィッティングを行うには、試着時の観察力と手の感度が必要である。シャープなノギスを使うテクニックは、ファイルフィッティング時の修正に大いに役立つ。これらの技術は、探求とまとめと経験の積み重ねが必要である。
(4) ファイリングにおける対称性の測定と管理について
加工後のフィッティング部品は、外形の真直度と平坦度が一定の精度要求を満たす必要がある。
対称嵌め合い部品の場合、通常は回転嵌め合いが必要となる。個々の加工で対称性の要求が満たされないと、嵌合後の外形平坦度が要求精度を満たすことが難しくなり、特に図1に示すように、回転後の外形平坦度が保証できなくなる。したがって、加工順序を合理的に配置し、測定によって対称性を管理する必要がある。
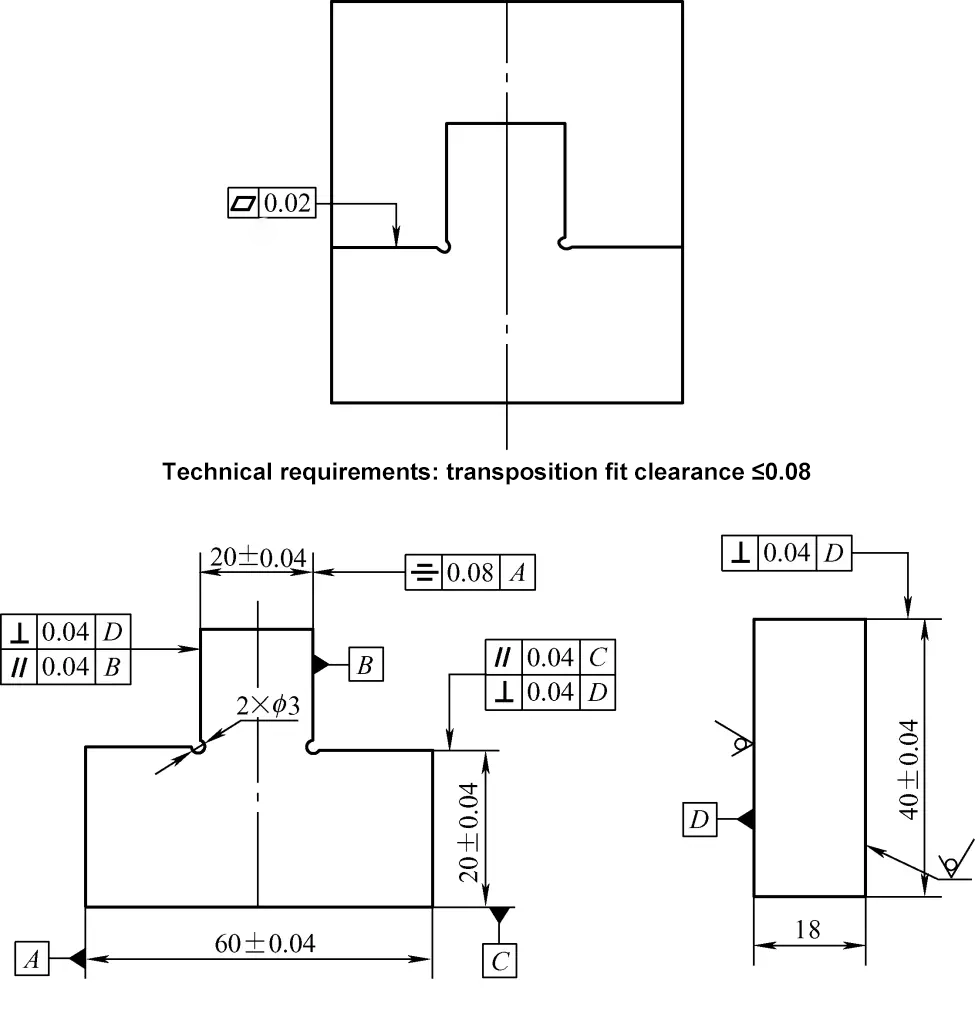
1) 注文の処理
図1に示すように、ボス(寸法20)の基準A(図1参照)との対称性を確保するため、加工はボスの両側からすべての材料を鋸で切り取るのではなく、片側の材料を残すべきである(図2参照)。寸法 L が要件(後述)を満たしたら、この側の残 り材を鋸で切り落とし、同時にヤスリ掛け面 II を (20±0.04)mm に管理する。
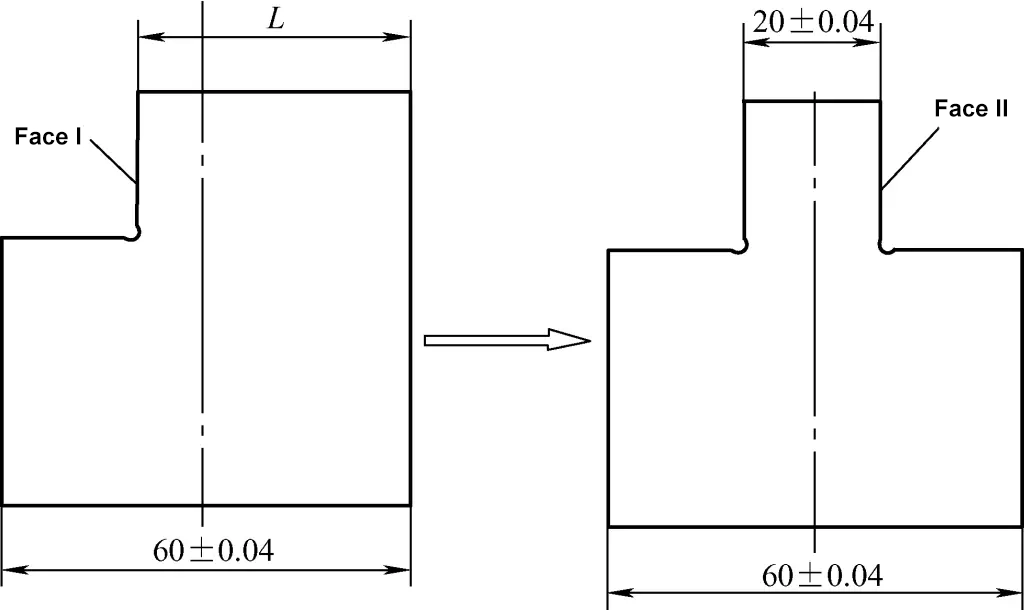
2) 対称性誤差の測定
対称性誤差とは、ファイリング加工の観点から、2つの加工面の中心面とファイリング加工後の理論的な中心面とのずれを指す。
図1に示すように、ワークの場合、軸基準Aに対するボス(20±0.04)mmの対称公差は0.08mmである。図3に示すように、この対称性の要求を保証するためには、寸法Lの間接測定によって保証する必要がある。
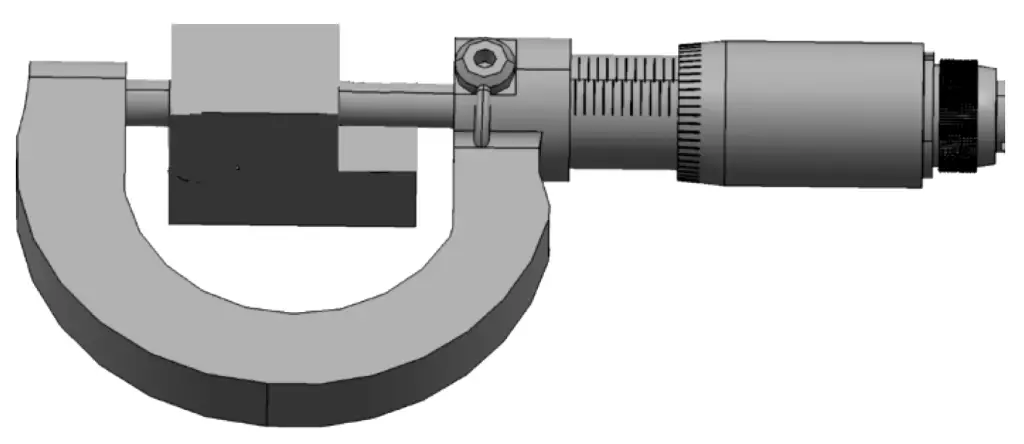
最大制御寸法 Lマックス.
図4に示すように、ボス寸法ファイリングの管理下では、下限偏差は19.96mmであり、その結果、元の中央左のオフセットは0.02mmとなった。現在の対称公差は0.08mmである。対称公差の概念によれば、ボス中心面の最大許容左オフセットは(0.02+0.02)mmである。したがって、制御寸法Lマックス = 40.02mm。
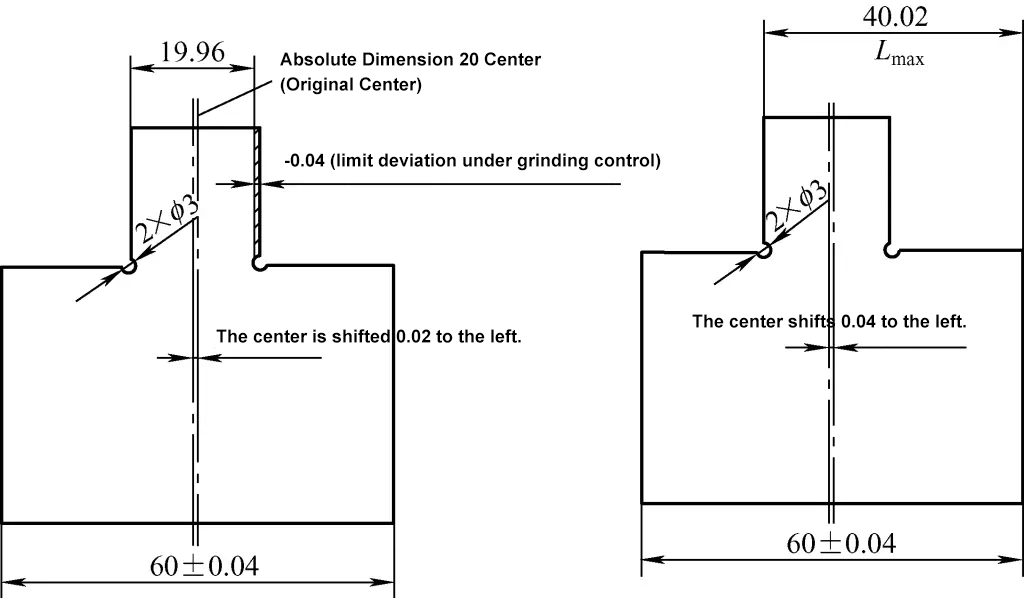
最小制御寸法 L分.
図5に示すように、ボス寸法を上限偏差20.04mmまでファイリングした後、元の中央右のオフセットは0.02mmである。現在の対称公差は0.08mmである。対称公差の概念によれば、ボス中心面の最大許容右オフセットは(0.02+0.02)mmである。したがって、制御寸法Lmin=39.98mmとなる。
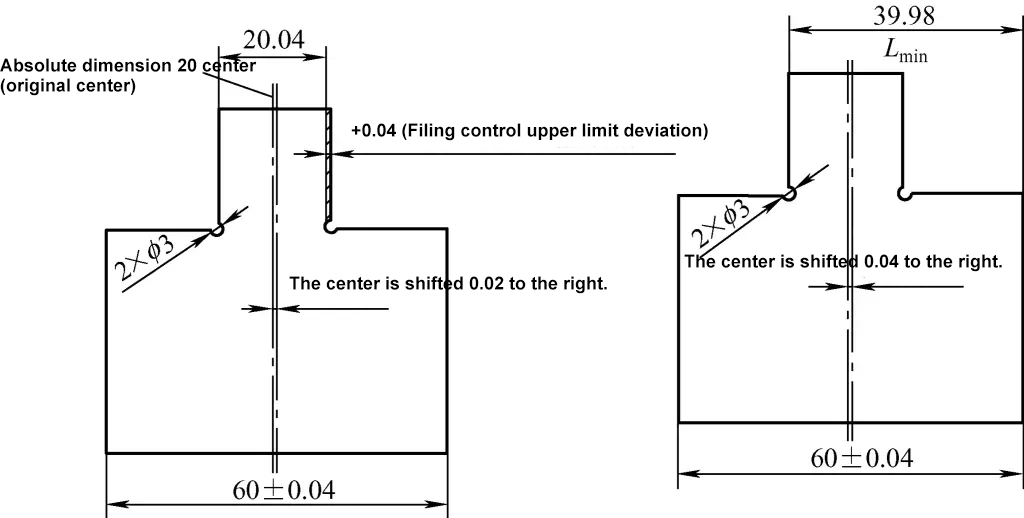
2.部品のファイリングとフィッティングの分析例 - 前編
図6a、図6bに示すように、モータのメンテナンス時にステータとロータのギャップを測定するための測定器(フィーラゲージともいう)で、その構造は次のように説明されている:
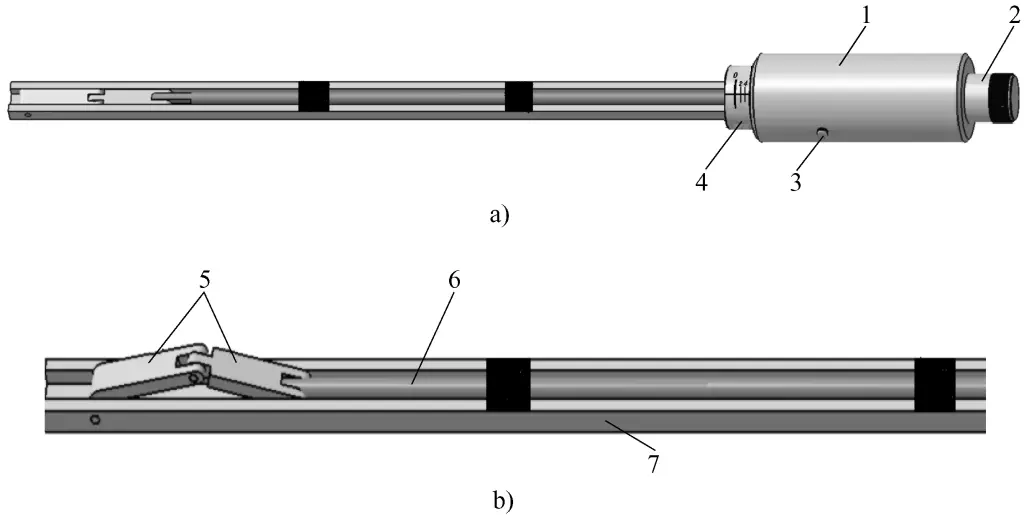
1-可動式スリーブ
2-微調整装置
3-可動ピンシャフト
4-固定スリーブ
5-計測ブロック
6-可動式測定ロッド
7定規ボディ
1) 可動スリーブと可動測定棒の尾端はネジ(ネジ仕様はM10×1mm)で接続されています。
2) 2つの測定ブロックと可動測定ロッドは可動ヒンジで連結されている。
フィーラーゲージの動作原理は以下の通り:
可動スリーブが回転していないとき、固定スリーブ上のゼロマークは可動スリーブ上のゼロラインと一致します(図6a参照)。可動スリーブを反時計回りに回転させると、可動ピン軸は固定スリーブの円形スロットに沿って円を描くように回転します。螺旋伝達の原理により、可動測定ロッドは左方向に移動する(図6に示すように)。一方、2つの測定ブロックは上昇し(図6b参照)、上昇した高さは可動スリーブに表示することができます。
現在の課題は、2つの測定ブロックをヤスリで削ってはめ込むことだ。
2つの測定ブロックの寸法は図7に示す通りである。
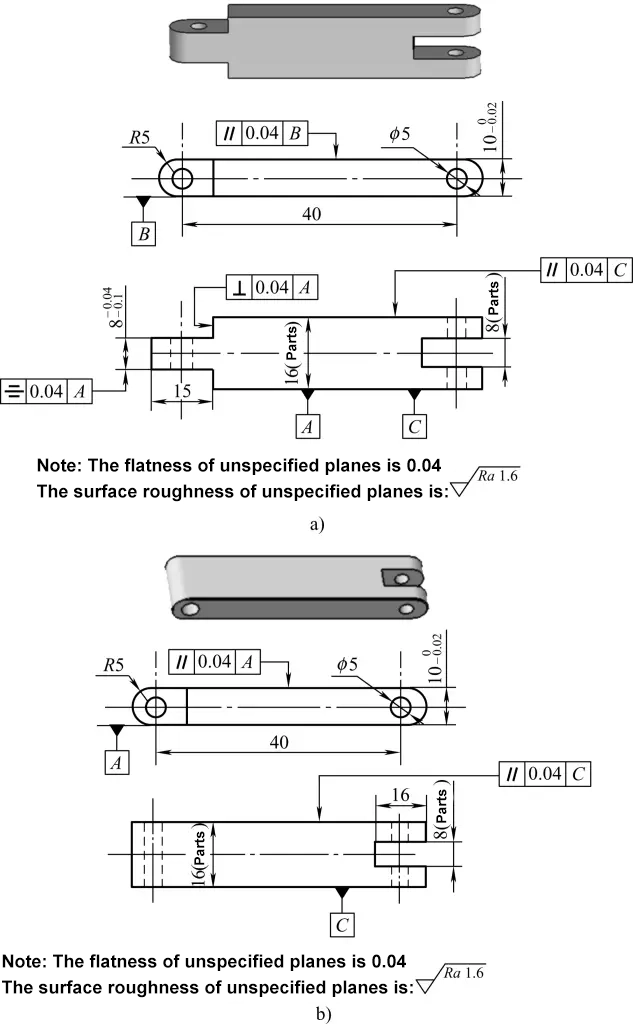
a) 測定ブロック1
b) 測定ブロック2
(1) 出願技術要件
1) 使用上の要求に従って、2つの測定ブロックは定規本体の溝内でスムーズにスライドし、左右にぐらつかないようにする。したがって、2つの測定ブロックをヤスリで削った後、2つの測定ブロックが合わさるようにします:
2つの測定ブロックの側面をヤスリで削った後、図7(測定ブロックと定規本体の溝の内側の2つの側面との嵌め合いに関する要件)に示す寸法精度および形状精度を満たしている必要があります。
つの測定ブロック端部のヒンジ部をヤスリで削った後、図7(測定ブロック端部の凸部と凹部のはめ合いに関する要求事項)に示す寸法精度と形状精度を満たすようにする。
測定ブロック2のヒンジ部と可動測定ロッド端部にヤスリをかけた後、図7(測定ブロック端部の凸部と凹部のはめ合いに関する要求事項)に示す寸法精度と形状精度を満たすようにする。
使用上の要求に従って、2つの測定ブロックの底面は、定規溝の底面とよく接触する必要があります。すなわち、フィーラゲージを使用しないとき(可動スリーブを回転させないとき)、測定ブロックの上面は定規本体の上面と同じ水平面上にあるべきである。従って、ヤスリ掛け後の測定ブロックの上下面は、図7に示す寸法精度および形状精度を満たす必要があります。
ファイリング・ツール
2つのメジャー・ブロックの形と大きさに応じて、ヤスリは10″、6″、4″の平ヤスリを選び、4″の平ヤスリの非作業エッジは研磨する。
出願プロセス
材料を準備する
18mm×10mm×110mmの粗鋼材(20号鋼)のブロックを用意する。
角柱をヤスリで削る(図8参照)
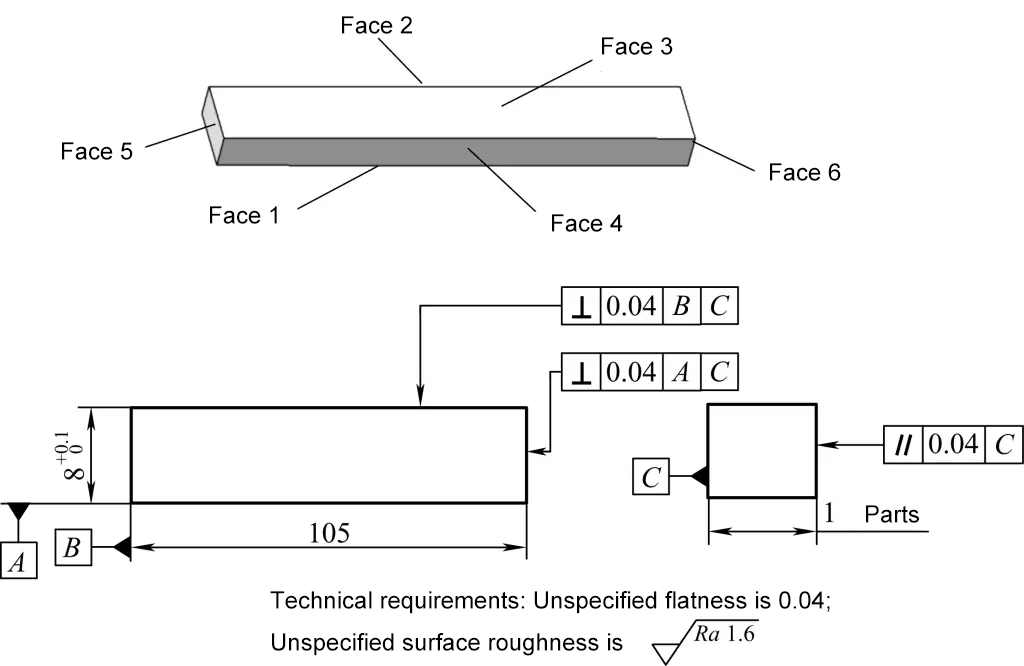
まず表面1を平らにヤスリで削り、ナイフエッジ定規で平坦度を0.04mm以内の精度で管理し、表面1の表面粗さがRa1.6μm以内になるようにする。
図8に示すように、サーフェス1を基準としてサーフェス3の加工境界をマークし、サーフェス3にヤスリをかけてサイズと幾何公差の要件を満たすようにする。
平坦度と表面粗さを表面1と同様に制御した表面2をヤスリで削り、表面2の表面1に対する垂直度を制御する(図8参照)。
図9に示すように、定規の溝の実際のサイズに従って表面4をヤスリで削り、寸法を16mmに制御し、定規の溝と16mmの寸法方向との間のはめあいクリアランスを0.04mmにする。
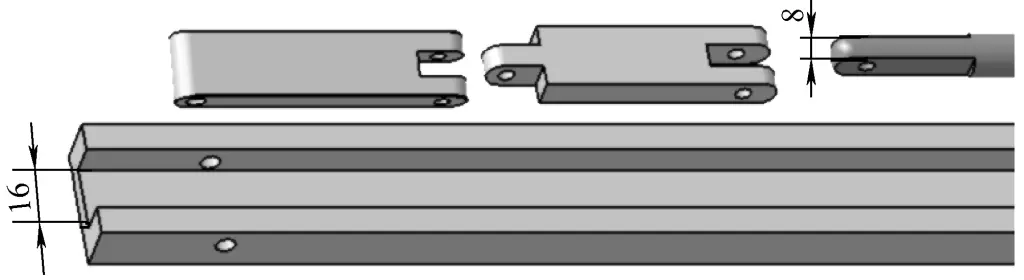
両端面5、6にヤスリをかけ、表面5と表面1、2との直角度、表面6と表面1、2との直角度をコントロールすることに重点を置き、全長を105mmにコントロールする。
図10に示すように、直方体を1部と2部に分割する。
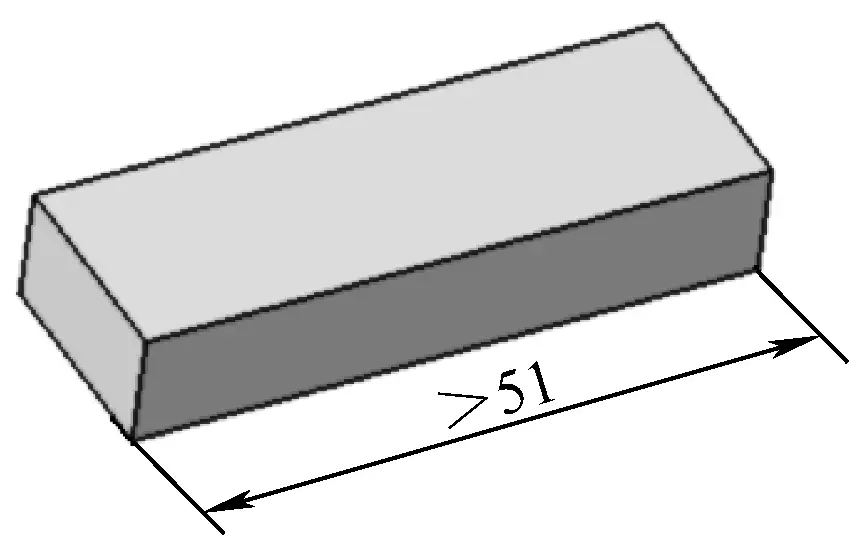
プロセス測定ブロック1
- 8mm×16mmの溝をヤスリで削り(可動式測定ロッド端部のヤスリのはめ込みに従って、図7、図9参照)、可動式測定ロッドと8mm×16mmの溝の側面との間の隙間が0.04mmになるようにする。
- 溝端の外側の円弧をR5mmにヤスリで削り、全長50mmにする。
- 8mm×15mmのエンドアークをR5mmにヤスリで削る。
- 8mm×15mmのエンド・ボスをヤスリで削り、図7に示す寸法と形状の精度を満たす。
プロセス測定ブロック2(図7b、図9参照)
パート1の溝と同じ方法で、8mm×16mmの溝を加工する。パート1のボスとの溝のはめあいクリアランスが0.04mmになるようにコントロールすることに重点を置く。
パート2の左右の端の円弧をR5mmにヤスリで削り、合計50mmの長さにする。
3.パーツ・ファイリング・フィットの分析例 - 前編
図11に示す絶縁体ピン・プーラーは、送電線の保守・工事でよく使われる自作工具である。そのプライヤー本体の製造工程を説明する:
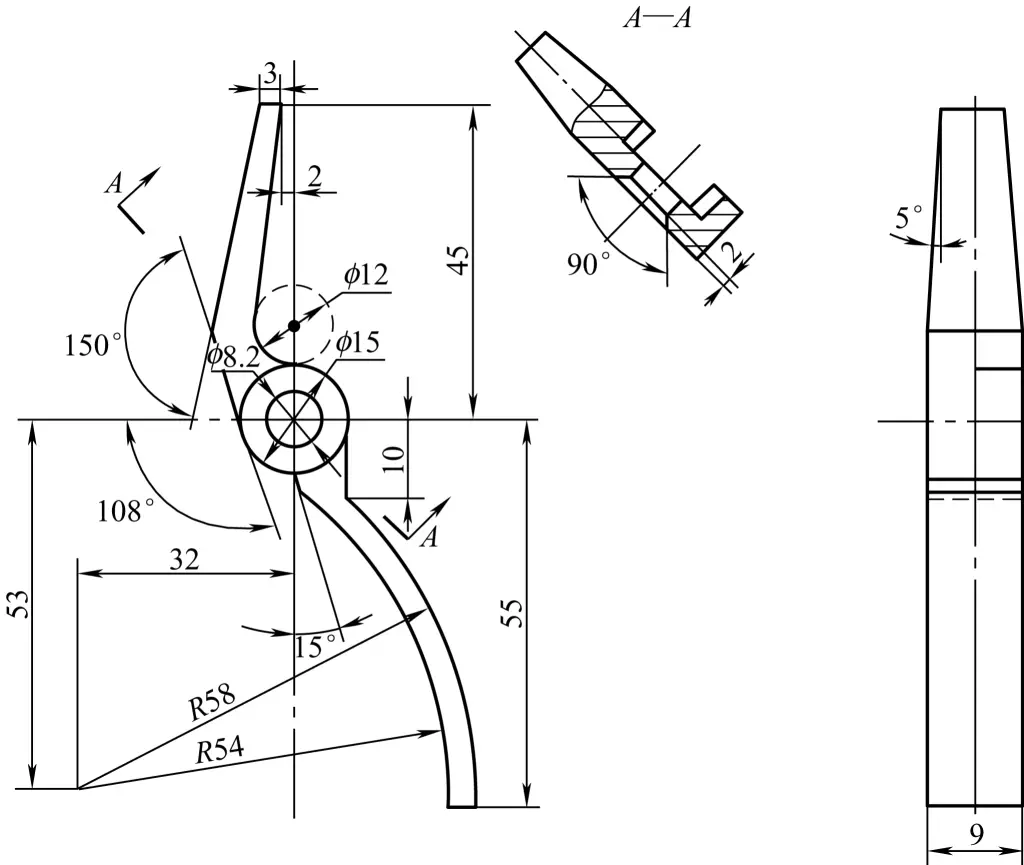
材料を準備する
ストリップ35鋼板の寸法は、図12に示すように、110mm×20mm×10mm(厚さ)である。
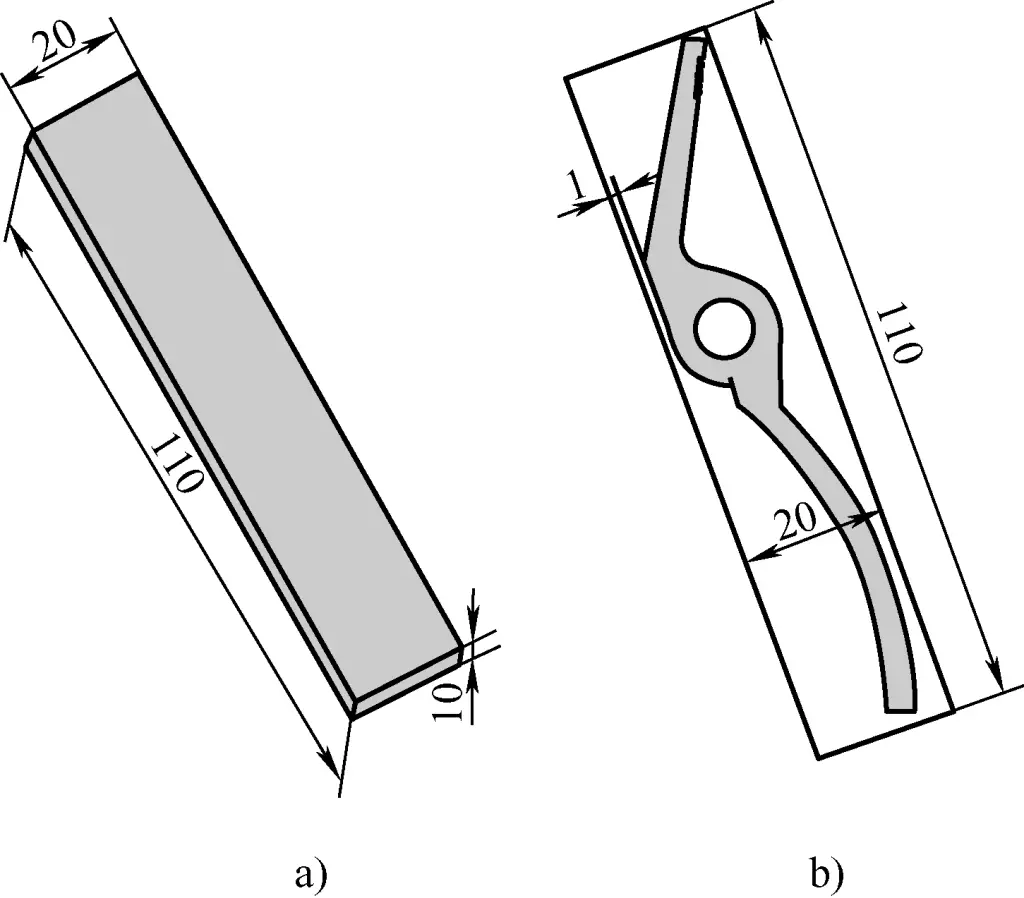
a) ブランク寸法
b) 成形後の形状
(2) ファイリング・ストリップ・プレート・ブランク(図13参照)
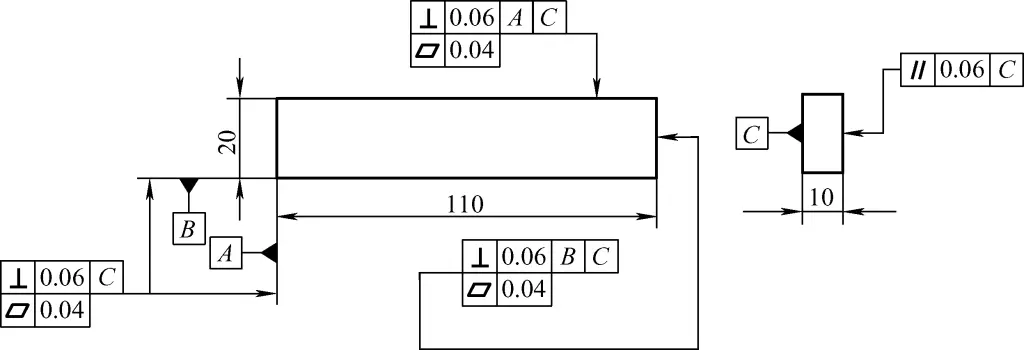
- 帯板のA面をCに垂直に、平坦度0.04mmでヤスリをかける。
- 帯板のB面を、AおよびCに垂直に、平坦度0.04mmでヤスリをかける。
- AとBを基準(スクライビングと測定の両方の基準)とし、基準面AとBの反対側をヤスリで削って、平坦度0.06mmと必要な垂直度を得る。
(3) 穴加工(図14参照)
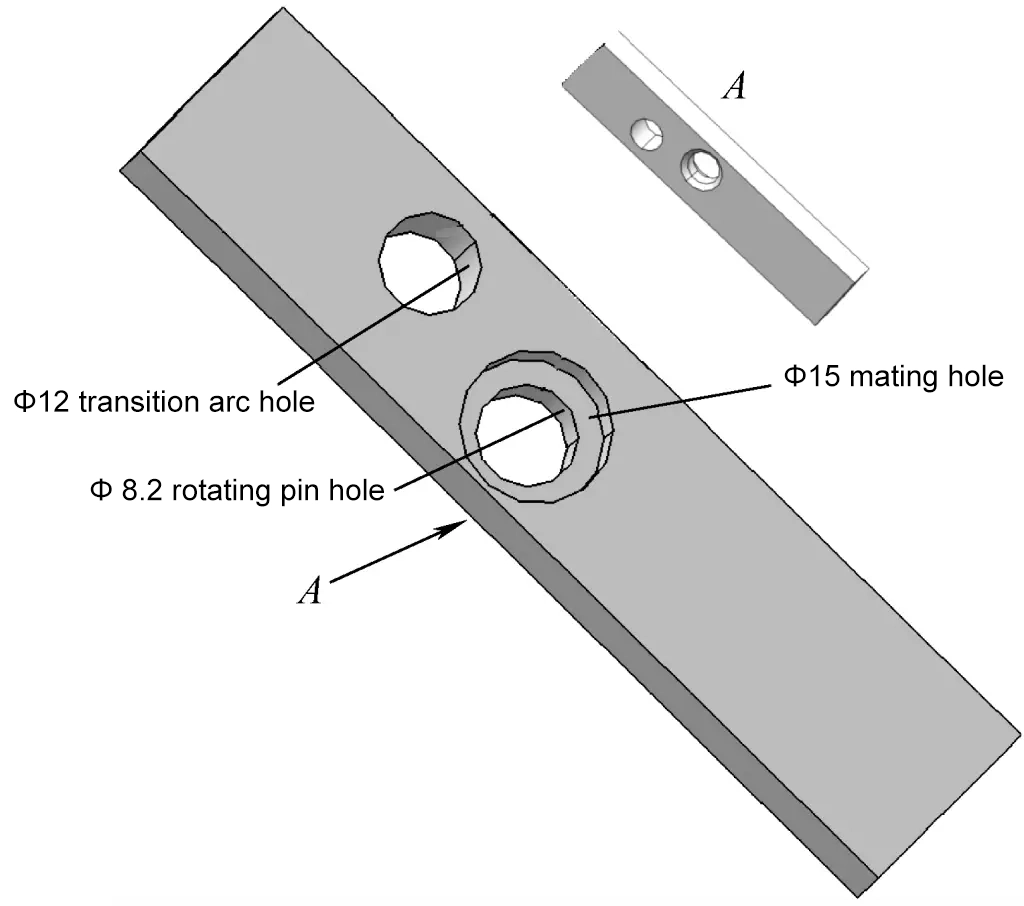
- 図面の寸法に基づいて、φ8.2mm のピボット・ピンの穴とφ12mm のトランジション・アークの穴の位置と直径をマークします。
- 図 14 に示すように、ストリップ・プレートのブランクに、φ8.2mm とφ12mm の穴を開けます。
- 図14と図11に示すように、円錐カウンターシンク・ドリルを 使用し、φ8.2mm(ピン取り外しプライヤーに使用)用の上部コ ーンをカウンターシンクします。
- 図 14 に示すように、φ15mm の平底円筒形皿穴を 4.5mm の深さまで皿穴加工するために、φ15mm の平底円筒形皿穴を使用します。
(4) 絶縁体ピン抜きの外形マーキング(図15参照)
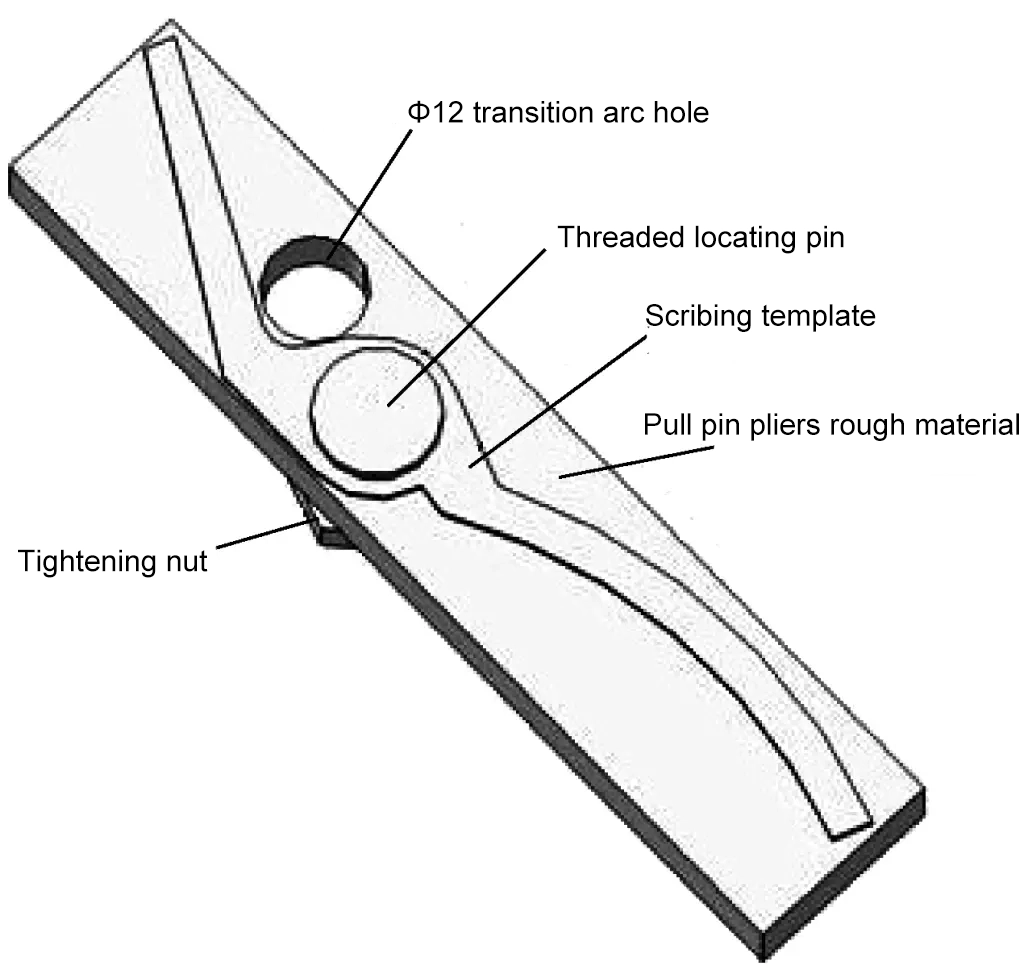
1) テンプレートのφ8.2mm のピボット・ピンの穴を、ストリップ・プレート・ブランクのφ8.2mm の穴と合わせ、ネジの切られた位置決めピンを挿入し、ナットを使ってスクライビング・テンプレートとストリップ・ブランクを一緒に固定します。
2) スクライブを使って、エジェクター・プライヤーの輪郭線をテンプレートに沿ってマークする。
(5) 材料の除去
特にノミを使うとプライヤー本体が変形するので注意すること。
(6) 絶縁体ピン・プライヤーの全体的なヤスリがけ
インシュレーター・ピン・リムーバー・プライヤーの全体的なヤスリがけの加工順序を図16に示す。プライヤーのジョーの内側を加工する場合は、内側 の輪郭がφ12mmの接続円弧に接するようにします。
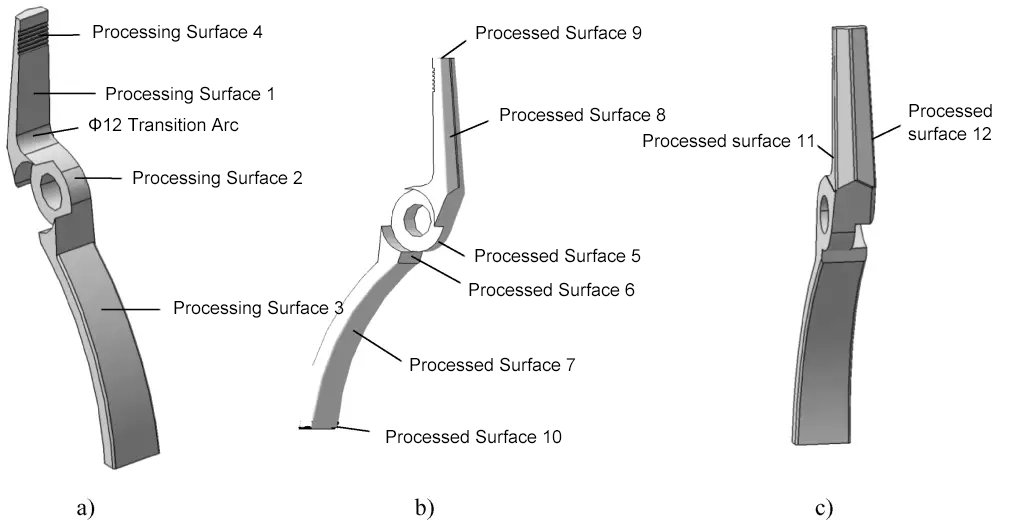
a) ステップ1
b) ステップ2
c) ステップ3