
I.基本的なプロセス知識
1.スクレイピングの原理と機能
図1に示すように、スクレーピングとは、加工面の精度をさらに向上させるために、スクレーパーを使用して加工物の表面から金属のごく薄い層を除去する操作のことである。
スクレーピングの基本的な方法は相互スクレーピングであり、標準的な工具またはスクレーピングされた表面に一致するワークピースを使用して、加工表面のより高い金属層の位置と分布を示します。作業者は、スクレーパーに圧力と押し付け力を加え、これらの高次金属層を除去し、要求される加工精度が得られるまで、相互スクレーピングを継続的に微調整する。
スクレイピングは一般的に、粗いスクレイピング、細かいスクレイピング、精密なスクレイピングの3段階に分けられる。要求される加工精度を達成するためには、多くの場合、相互の擦り合わせと微細化が繰り返される。削り出しによって、加工面の形状精度、位置精度、接触精度がさらに向上し、表面粗さが小さくなり、アッセンブリの油保持性やシール性が大幅に向上する。
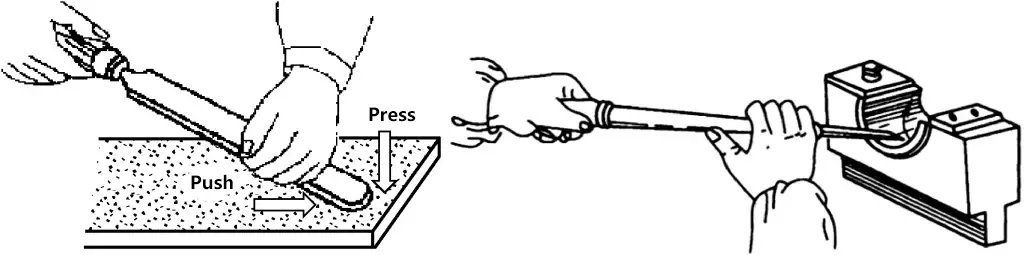
2.スクレイピングツール
(1) 開発者
相互擦過の前に、ワークピースの誤差の大きさと位置を把握するために、擦過する表面に着色塗料を薄く均一に塗布する必要がある。図2に示すように、相互削り取りによって、盛り上がった部分が示され、スクレーパーで除去される。
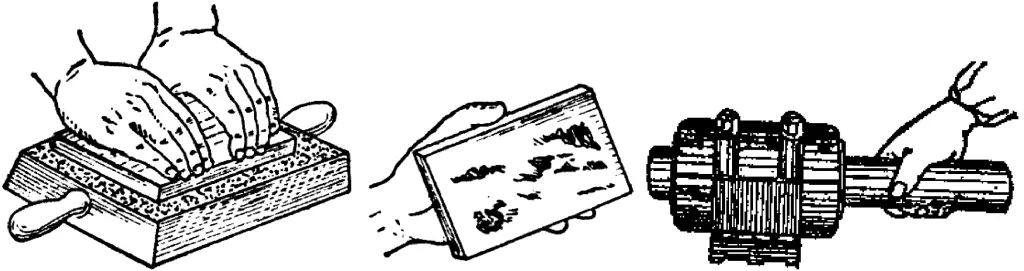
一般的な現像剤には赤鉛粉とプルシアンブルーがある。赤鉛粉の場合は、機械油や獣脂と混合する。この現像液は光を反射せず、斑点がはっきり見える。プルシアンブルーオイルは、プルシアンブルーの粉末にひまし油とマシン油を混ぜて作られる。濃い青色で小さな斑点がはっきり見えるので、精密な削り出しや非鉄金属部品に最適です。
(2) 一般的なスクレイピング・ラッピング・検査工具
(表1参照)
表1:一般的なスクレイピング・ラッピング・検査工具
名称 | イラスト | 機能 | |
スクレイピングと検査ツール | 標準平板 | ![]() | 主に平坦面を削る際の基準ラッピングツールとして使用され、0級と1級の平板が一般的に使用される。 |
![]() | ラッピングツールとして使用される。 | ||
![]() | 平坦度検査用 | ||
ブリッジ・ストレートエッジ | ![]() | 細長い平面を削る際に、着色ポイントの基準となるラッピングツールとして使用。 | |
I字型ストレートエッジ | ![]() | 1) 細長い平面を削る際に、着色ポイントの基準となるラッピングツールとして使用; 2) 細長いガイドの真直度チェック用 | |
角度定規 | ![]() | 角度のついた(アリ溝など)細長い平面を削る際に、着色ポイントの基準となるラッピングツールとして使用。 | |
検査棒 | ![]() | 主に工作機械の主軸スリーブやその他の部品のラジアル振れ、軸方向移動、同軸度、平行度の検査に使用されます。 |
(3) スクレーパー
1) フラットスクレーパー
フラット・スクレーパーの種類
一般的なフラット・スクレーパーには、一体型スクレーパーとはめ込み式ヘッド・スクレーパーがある。一体型スクレーパーは、一般的に合金工具鋼(9SiCrなど)またはバネ鋼から作られ、前刃は焼入れされています。はめ込み式ヘッドスクレーパーは、スクレーパー本体の前端に超硬チップをはめ込んだものです。
また、図3に示すように、一般的に使用されている平スクレーパーは、形状によって、手押し平スクレーパー、スタンドスクレーピング平スクレーパー、ベントヘッド平スクレーパーに分けることができる。
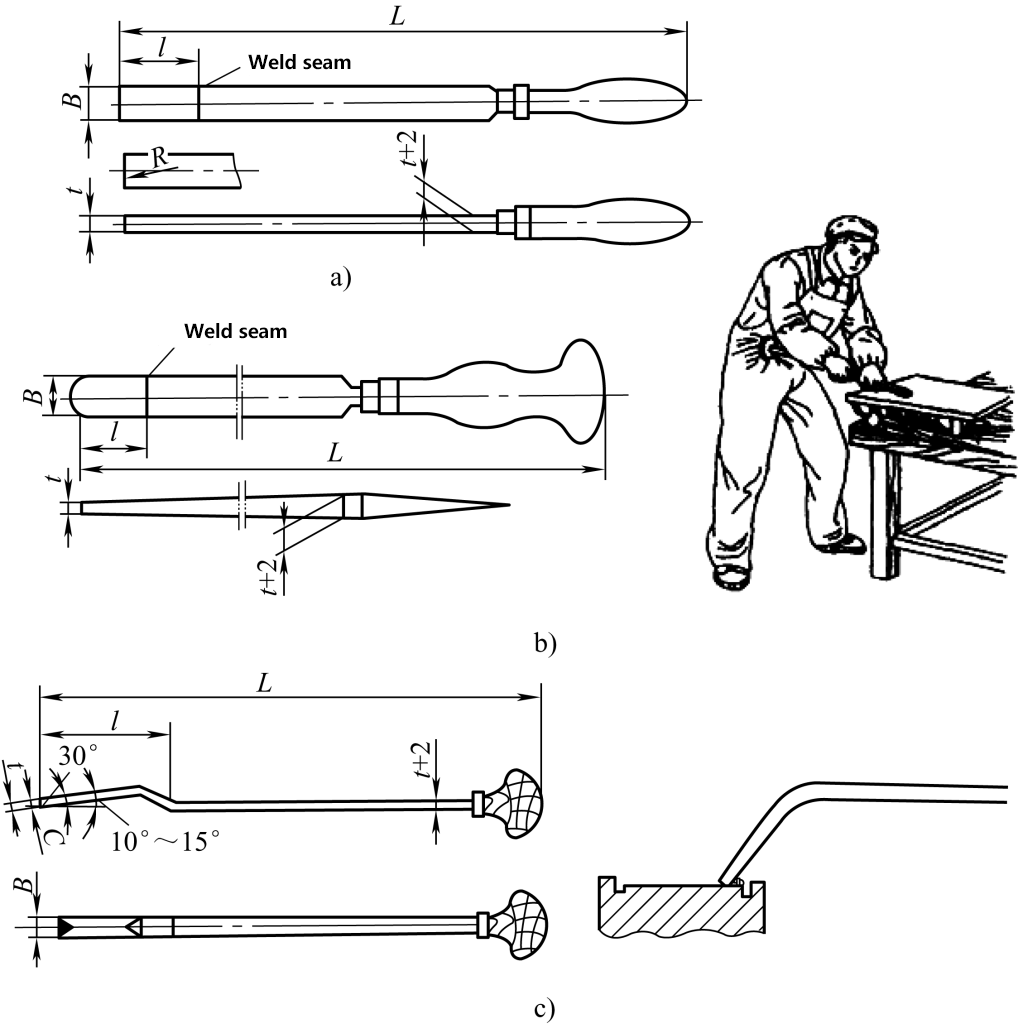
a) ハンド・プッシュ・フラット・スクレーパー
b) スタンドスクレーピング・フラットスクレーパー
c) ベントヘッド・フラット・スクレーパーとステップ・プル・スクレーピング
プレーン・スクレーパーのカッティング・ヘッドの形状とくさび角度
プレーン・スクレーパーのカッティング・ヘッドの形状とくさび角を図4に示す。
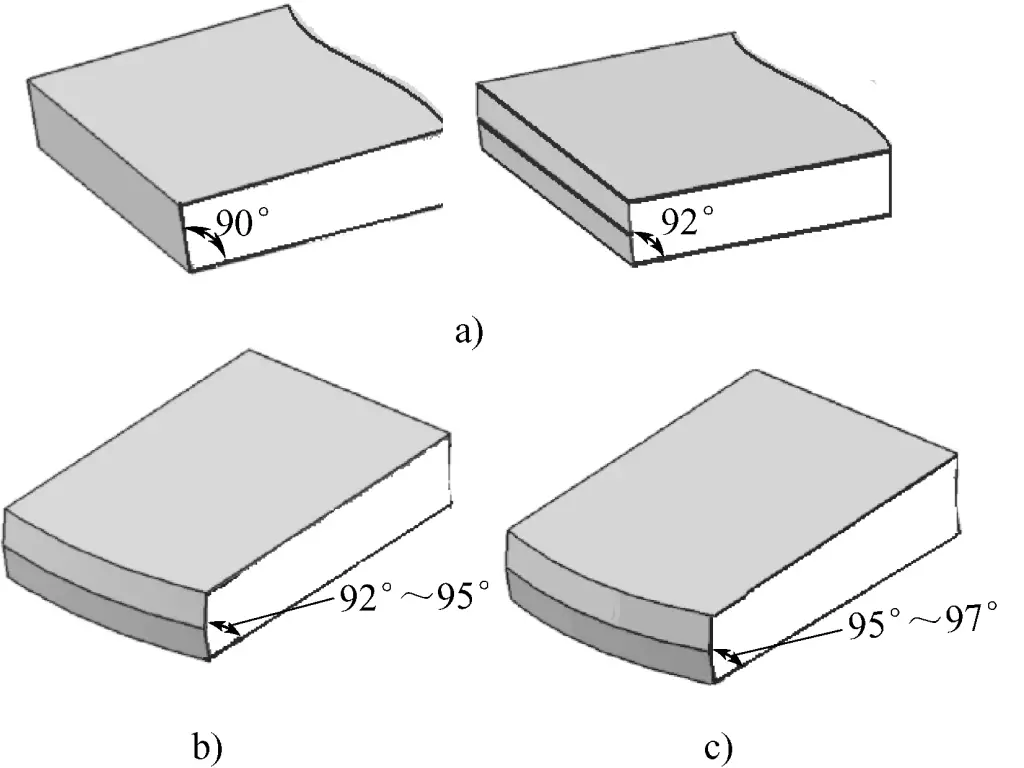
a) 粗面スクレーパーのくさび角
b) ファインプレーン・スクレーパーのくさび角
c) 精密平面スクレーパーのくさび角
- 図4aに示すように、粗面スクレーパーのくさび角(スクレーパーの前面と後面のなす角)は90°~92°であり、刃先は直線である。
- 図4bに示すように、ファインプレーン・スクレーパーのくさび角は一般に95°前後で、刃先はわずかに弧を描いている。
- 図4cに示すように、精密平面スクレーパーのくさび角は概ね97°前後であり、刃先円弧の曲率は微細スクレーパーよりも大きい。
平面スクレーパーの切断角度
図5に示すように、スクレーピング工程では、すくい角γは一般に-15°から35°の間で変化し、逃げ角αは一般に20°から40°の間で変化する。スクレーパーのすくい角が小さいため、スクレーパーは被加工物の表面を押したり研磨したりする効果を発揮し、それによって加工面の表面粗さ値が低下する。
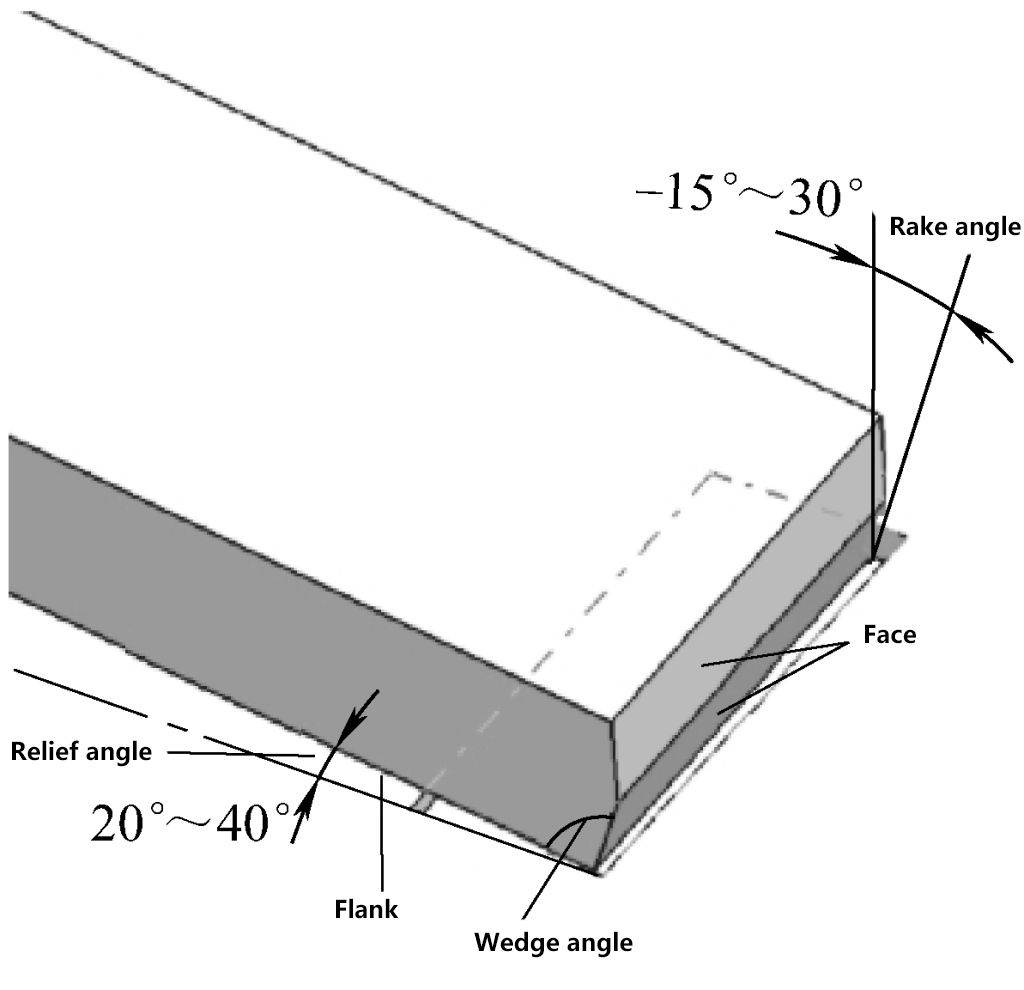
2) 曲面スクレーパー
曲面スクレーパーは、主に各種すべり軸受などの内側曲面を削るために使用されます。また、穴内部のバリを削り取るために使用されることもある。
曲面スクレーパーの種類
三角スクレーパーとスネークヘッドスクレーパー。三角スクレーパーとスネークヘッドスクレーパーは、主に一般的な内側曲面のスクレーピングと穴開口部のバリ取りに使用される。図6にその構造形式を示す。
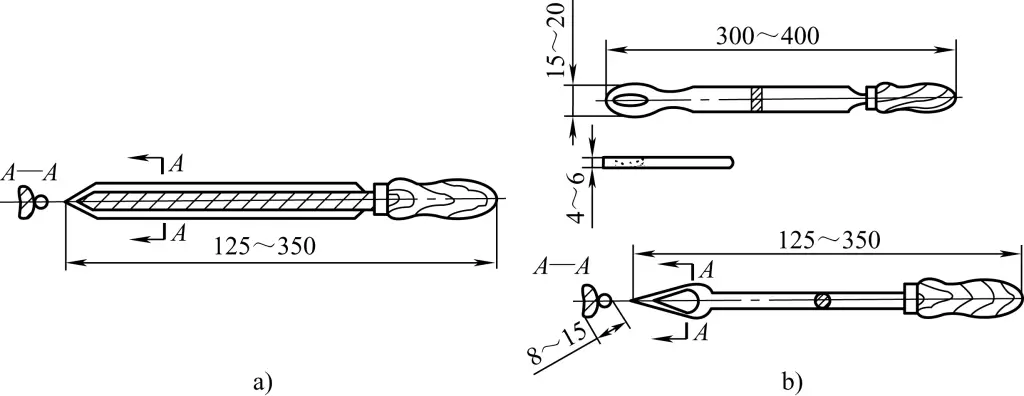
a) 三角スクレーパーの構造形式
b) スネークヘッドスクレーパーの構造形式
半円形ヘッドスクレーパー。図7に示すように、半円ヘッドスクレーパーの刃先部分は半円形であるため、掻き取り時に角点が出にくい。割れたベアリングなどを削るのに適している。半円ヘッドスクレーパの刃先サイズRは、削る曲面の半径サイズに合わせて研削することができます。
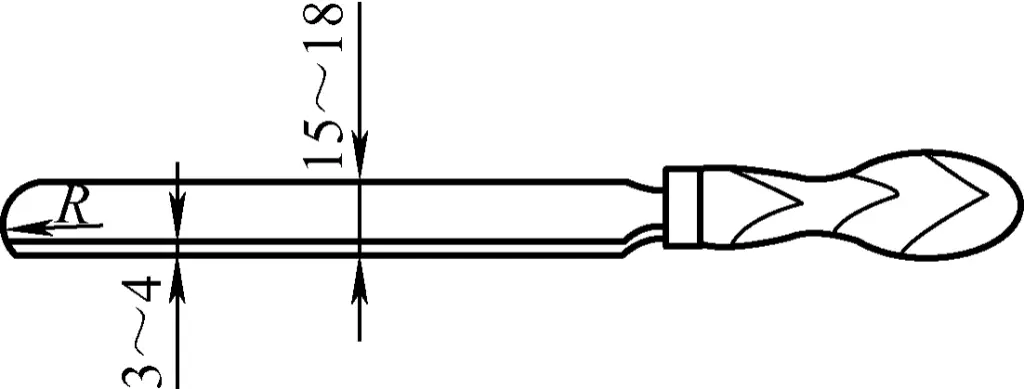
柳の葉スクレーパー。図8に示すように、柳の葉スクレーパーには2つの刃があり、先端は細かく削るためのもので、後方は激しく削るためのものである。銅スリーブやスプリットベアリングを削るのに適している。
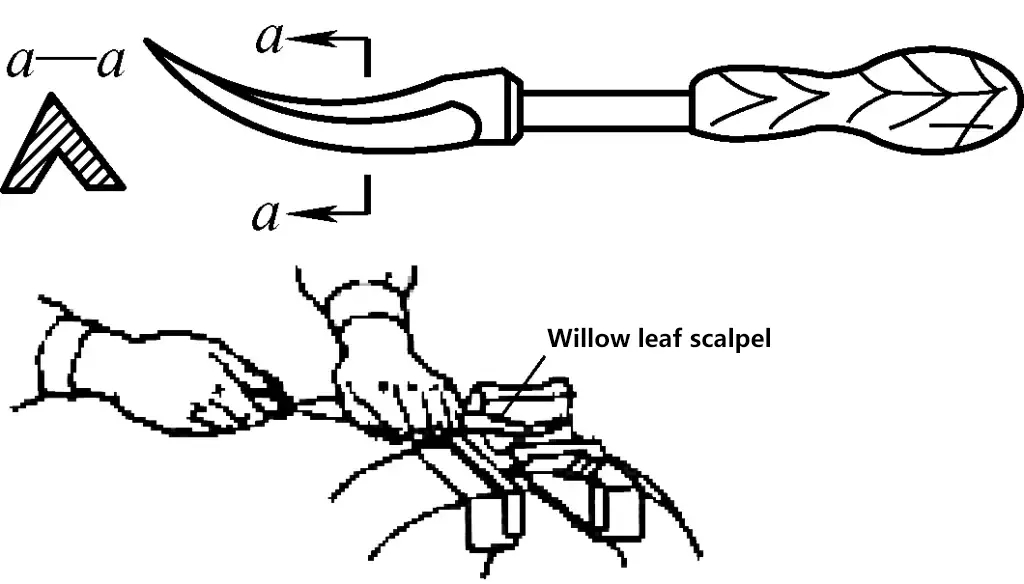
カーブド・スクレーパーのカット・レーキ角度。図9は、カーブド・スクレーパーの切削形態を示す。ポジティブレーキまたはニュートラルレーキで削ると、切りくずが厚くなり、ツールマークが深くなるので、荒削りや軟質バビットメタルなどの軟質軸受合金の削りに適している。
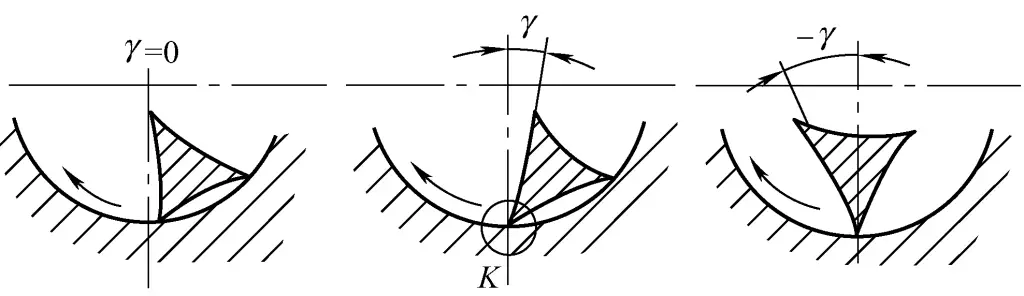
ネガすくいを使用して削ると、切り屑が薄くなるため、削り取り時のビビリ跡が少なくなり、加工面の面粗さ値を下げることができる。しかし、刃先の押し出し削り現象が激しいため、錫基軸受合金のような低硬度材の削りでは、工具の噛み込みや削り跡が発生しやすい。そのため、通常は高硬度の銅基軸受合金や、最終の微細な削り出し時の仕上げに使用される。
低硬度ベアリングの内側曲面の仕上げ削りにネガすくいを使用する場合は、スクレーパーにかかるラジアル方向の圧力を最小にする必要があります。
II.基本操作スキル
1.スクレーパーブレードの研磨
(1) プレーン・スクレーパー・ブレードの研磨
1) プレーン・スクレーパー・ブレードの研磨に必要な条件
プレーン・スクレーパーの刃を研磨するための全体的な条件は以下の通り:
- スクレーパーの刃の2つの後面は、凸凹のない平らで滑らかなものでなければならない。
- スクレーパーの刃の2つの前面と刃先は、中心軸に対して対称で、平らで、滑らかで、凸凹の凹凸がなく、刃の厚み方向に円弧面がないこと。
- さまざまな用途に応じて、スクレーパーブレードのくさび角を正しく研磨してください。
- 工具鋼製のスクレーパーの刃を砥石で研削する場合は、研削中に刃を水に浸して冷却する。 研削工程 ブレードヘッドの焼きなましを防ぐため。超硬チップのスクレーパー刃の場合、刃先の割れを防ぐため、研磨中に超硬部分を水につけないこと。
2)プレーン・スクレーパーの刃の研磨方法
スクレーパー・ブレードの後面を研磨する(図10参照)。
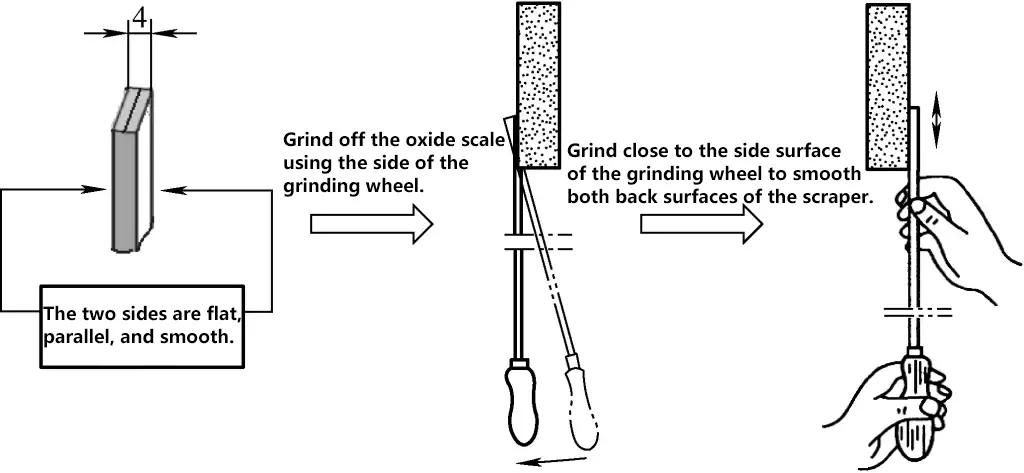
スクレーパーの刃の前面と刃先を粗く研磨する。
図11に示すように、スクレーパーの刃の前面と刃先を荒研ぎするときは、刃先を砥石の端に安定させて置き、その位置は砥石の中心よりやや高くする。
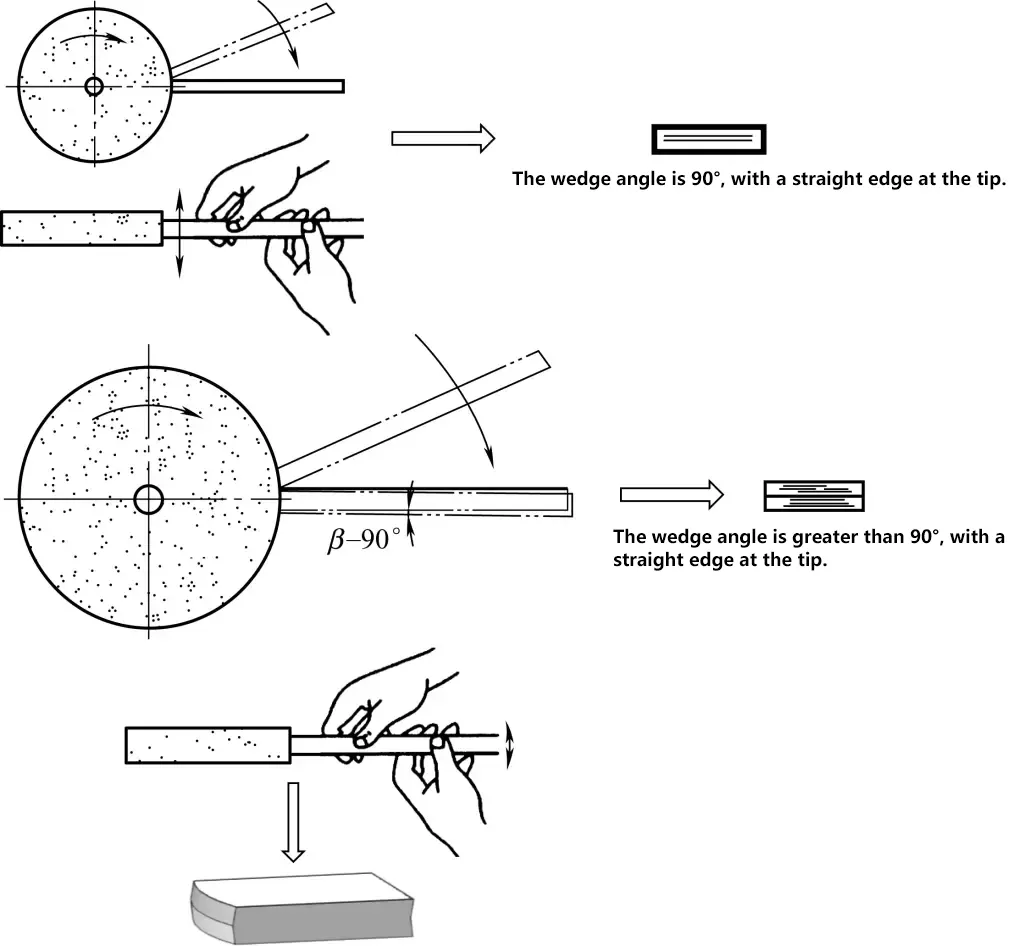
先端が砥石のエッジに接触したときの激しい振動を防ぐには、まずスクレーパーの刃を斜めに傾けて砥石に軽く接触させ、次に刃を上から下へゆっくりと動かして必要な位置にする。必要なくさび角が90°の場合は、ブレードを水平に置きます。必要なくさび角が90°より大きい場合は、研削時にブレードを傾けます。
片面を砥いだら、手前の手(砥石の端に近い方の手)を支点にして刃を180度回転させ、もう片方の面を砥いで両面を対称にする。
先端の刃先を研磨する場合は、刃を左右に滑らかに動かします。直線的な刃先が必要な場合(荒削り用)は、直線に沿って刃を動かします。刃先に丸みが必要な場合(細掻刃、仕上げ掻刃)は、刃先の湾曲に合わせて、刃を少し振って振り量を調整します。
3) プレーン・スクレーパー・ブレードの微研磨
スクレーパーの刃を砥石で粗研磨すると、刃先に微細な凹凸が大きく残る。そのままスクレーピングに使用すると、ツールマークが深くなり、チッピングが発生しやすく、スクレーピングスレッドの原因となる。そのため、スクレーパーの刃は粗研磨の後、オイルストーンの上で精研磨する必要がある。
スクレーパー・ブレードの後面の微研磨
スクレーパーの刃の後面をオイルストーンで微研磨する場合、まずオイルストーンの表面の平坦度をチェックする。オイルストーンの中央に凹凸がある場合は、使用しないでください。オイルストーンにきれいな機械油を塗り、スクレーパーの刃の後面をオイルストーンの表面に強く押し当て、両手で同時にスクレーパーの刃を水平に均等に動かします。一定時間精研磨した後、スクレーパーの刃の裏面が平らに研磨されているか、スチール定規で確認する。
図12に示すように、スクレーパー・ブレードの後面を微研磨するには、図12aが正しい方法である。図12bのように研磨すると、スクレーパー・ブレードの後面が浮き上がったり、水平に傾いたりしやすくなり、後面の研磨が不均一になったり、円弧面になったりする。
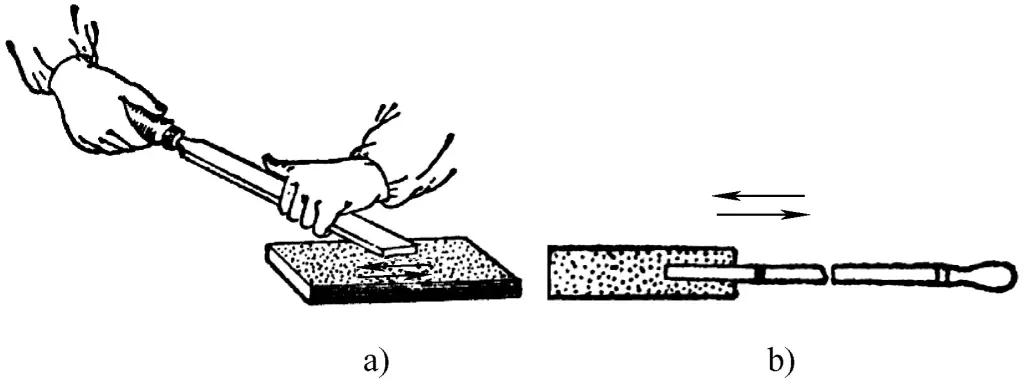
a) リア・フェースの精密研削の正しい方法
b) リア・フェースの微粉砕方法の誤り
スクレーパー刃の正面と刃先の微研磨
スクレーパー刃の前面と刃先の微研磨を図13に示す。
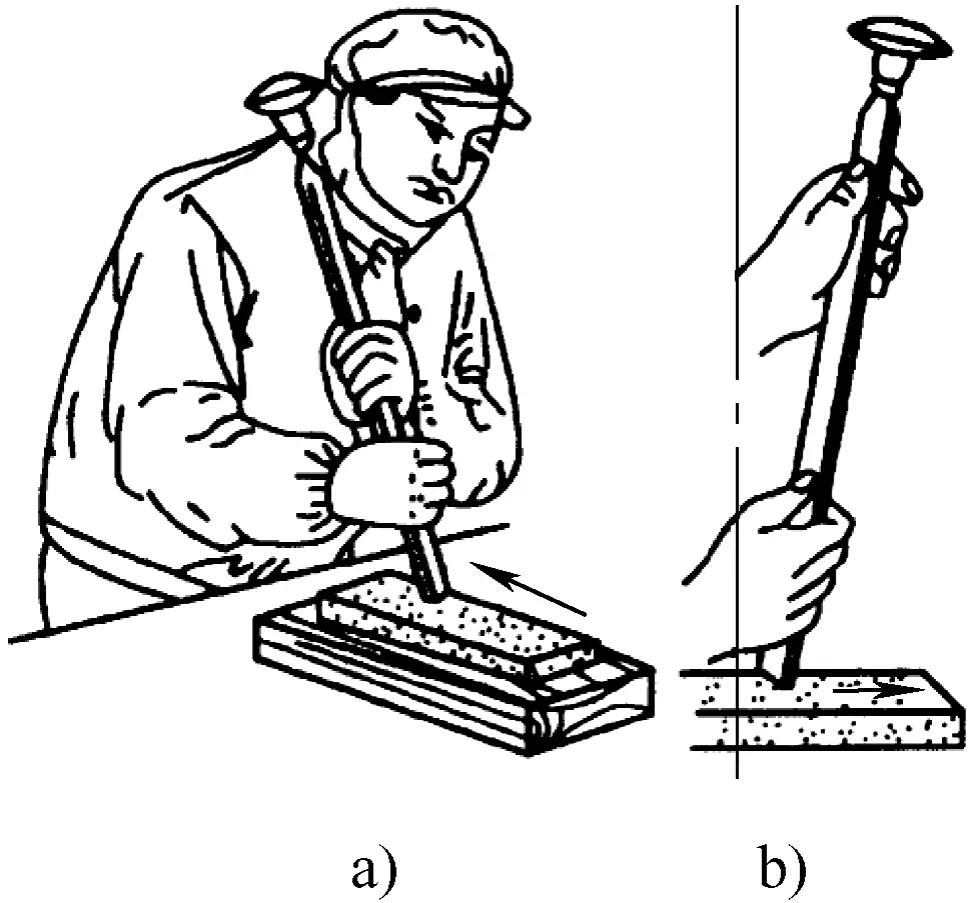
方法1:図13aに示すように、スクレーパー・ブレードの上部を肩で支え、ブレード本体を両手で持ち、スクレーパー・ブレードを手前から奥に動かし、ブレードを少し持ち上げて再び手前から奥に動かす。この作業を繰り返し、前面の平坦度を確認する。
つまり、前面がオイルストーンの表面にしっかりと押し付けられるようにします。微粉砕のくさび角が90°より大きい場合は、それに応じてブレード本体を傾けてください。
方法2:図13bに示すように、ブレード本体を両手で持ち、スクレーパーブレードの前面をオイルストーンの表面に強く押し付ける。スクレーパー・ブレードを前方に押し出しながら下方に圧力をかけ、オイル・ストーンの前端に到達したらスクレーパー・ブレードを少し持ち上げ、その後引き戻す。研磨作業を繰り返す。
上述したように、微研削のくさび角が90°の場合、研削中は刃体をオイルストーンに対して垂直に保つ必要がある。微粉砕のくさび角が90°より大きい場合は、それに応じてブレード本体を傾ける必要があります。
特に強調したいのは、どのような研磨方法であっても、研磨時には両手で同時にスクレーパーの刃を動かすことである。片手を支点にして、もう一方の手でスクレーパーの刃を振らないこと。この方法で研磨すると、スクレーパーの刃の前面に円弧面ができ、刃の切れ味に影響する。
(2) カーブ・スクレーパー・ブレードの研磨
1) カーブ・スクレーパーの粗研磨
現在、カーブスクレーパーは基本的に成形スクレーパーである。カーブスクレーパーの粗研磨の主な目的は、摩耗したカーブ内側の溝をトリミングし、円弧面を研磨することで刃先のカーブを連続させ、刃先の欠けをなくすことである。
三角スクレーパーの粗研磨
三角スクレーパーヘッドの円弧面を砥石盤で研削する方法を図14に示す。
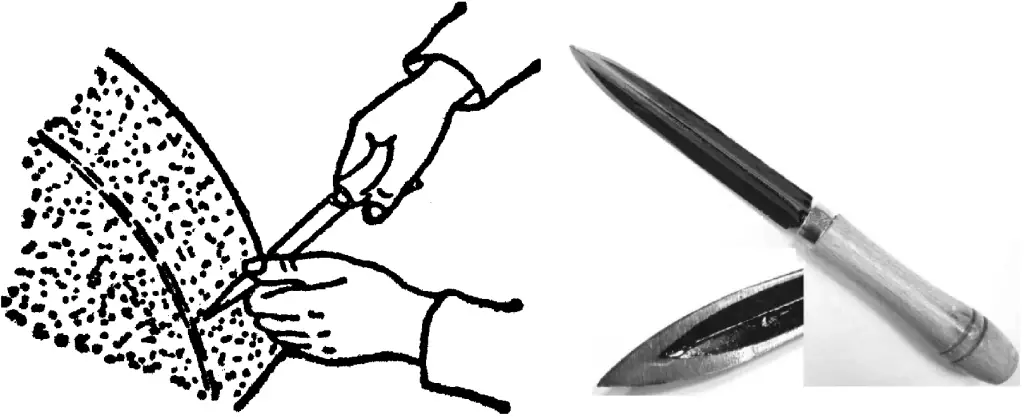
スクレーパーを砥石の外周円弧面に水平に軽く押し付け、刃の円弧に合わせて前後に動かし、3面の交線が円弧状の刃先を形成するようにする。
図15に砥石機による三角スクレーパの内弧溝の研削方法を示す。
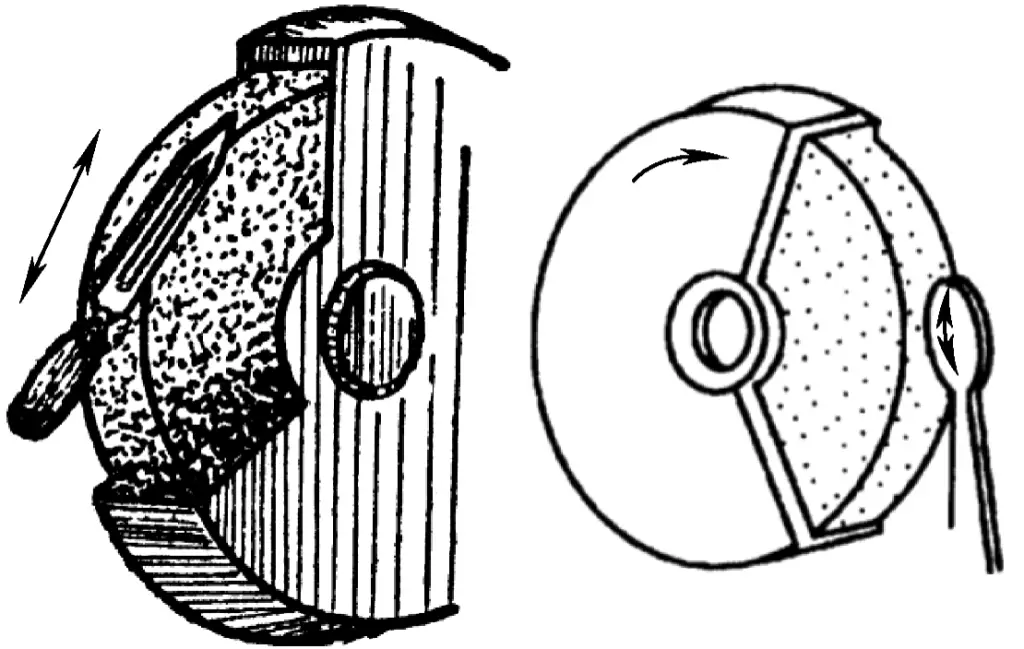
内側円弧溝を研削する場合は、スクレーパー内側円弧溝の中心を砥石の端に置き、上下に動かして溝の長さを調整し、左右に動かして溝の幅を調整する。ナイフの溝は、2枚の刃の中間に位置するようにします。
スネークヘッド・スクレイパーの粗研磨
スネークヘッド・スクレーパーを砥石の中心面に置き、砥石の外側の円弧面に沿って上下に動かし、円弧の形を整える。2~3mmのマージンを残して、砥石の端で溝を研削する。
2) カーブ・スクレーパーの微研磨
図16に示すように、湾曲したスクレーパーの微研磨もオイルストーンの上で行う。精研磨の際には、スクレーパーをオイルストーンの長さに沿って前後に動かし、刃の円弧に合わせて上下に振動させながら、3つの刃先の研磨痕が消え、円弧面が滑らかになり、刃先が鋭利になるまで行う。
より滑らかな円弧面とシャープな刃先のために、研磨ペーストをラッピングプレートに塗布して刃先を研磨することもできる。
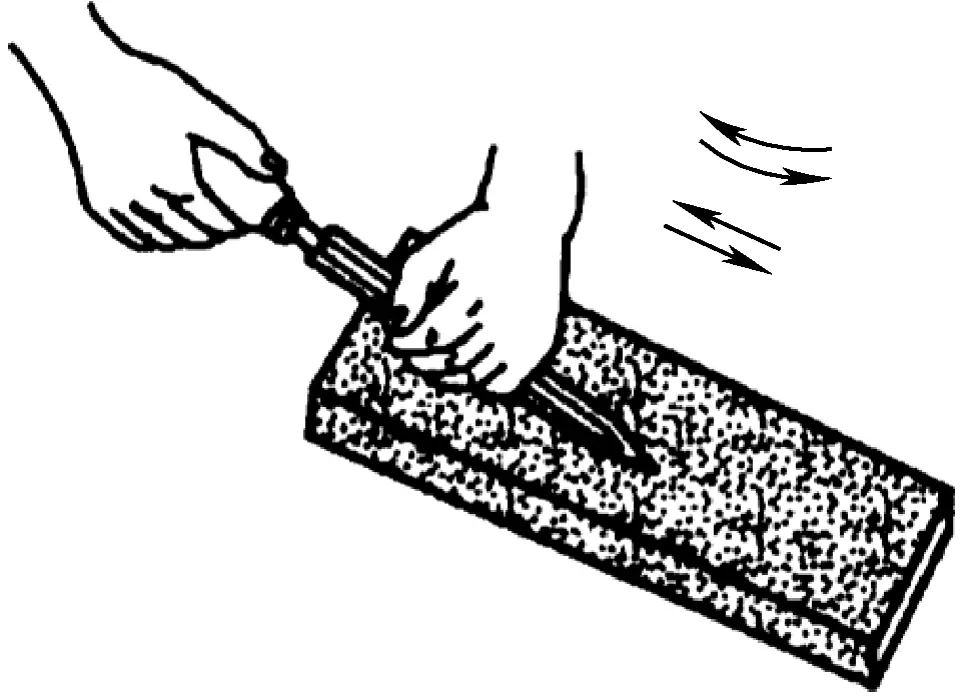
2.スクレイピング・プロセス
(1) プレーン・スクレイピング加工
1) カラーリングとラッピングの要件
前述のように、表面の局所的な高ポイントの位置を表示するには、削る前に削った表面に表示剤を塗布し、標準的な工具または一致する部品で表面をラップする必要がある。高点位置は、表示される黒いマークで判断することができる。
ディスプレイ・エージェントとアプリケーションの要件
ディスプレイ剤の割合は、薄すぎず、濃すぎず、適切でなければならない。薄すぎると油分が多くなり、ラッピングの際に低い部分に黒い跡がつき、真の高点がわかりにくくなる。厚すぎるとラッピング時の抵抗が大きくなり、バウンシング現象が起こり、ラッピングの品質に影響する。通常、荒削りの場合は表示剤を薄く、細かい削りの場合は厚くする。
ディスプレイ剤は厚すぎても薄すぎてもいけない。厚すぎると下の方にも黒い跡がつき、誤った結果につながる。薄すぎると表示されるポイントがはっきりせず、削る際に高いポイントを見つけるのが難しくなる。
表示剤を塗布する前に、ラッピングツールの表面と削り取った表面をきれいに拭き取り、乾燥させておく必要がある。表面に汚染物質があると、ラップ後に黒いマークが現れますが、これは真の高ポイントを示すものではなく、削り取り時の誤った操作につながります。
削り出しが細かい削り出しの段階に達すると、明確で目立つ点が必要になる。この目的のために、ラッピングツールの基準面に表示剤を塗布することができる。
ラッピングポイントの注意点
正しいラッピング方法は、削られた表面の本当の高ポイントを明らかにし、誤ったラッピングポイントを避けることができる。したがって、ラッピングの際、標準工具または適合部品は、ワークピースの長さの3分の1以上、削り取った面の端からはみ出さないようにする。
2) スクレイピング・プロセス
荒削り
図 17 に示すように、ラフスクレーパによる粗研磨の主な目的は、金属表面の酸化被膜を除去し、平坦度の技術 要件を満たすことである。通常、嵌合面(ギアボックスの嵌合面など)や可動サブシステムのガイドウェイ(水平旋盤のガイドウェイなど)では、粗研磨後の平坦度は0.02mm以内でなければならない。マッチングパーツや標準的な検査ツールでラッピングした後、高ポイントが中央に高く、周囲に低い現象がなく、均等に分布している必要があります。
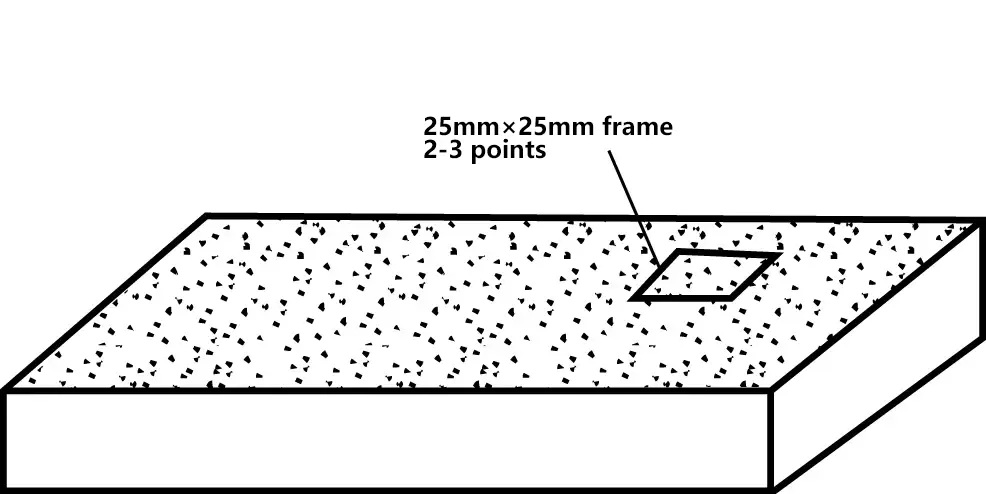
標準的な25mm×25mmの正方形の枠で検査し、2~3点が表示されるようにする。この削り取り技術的要求を満たすためには、高い点(ラップ後に表示される黒く光沢のある点)を大きく削り取る必要がある。
ラフ・スクレーパーのエッジは一般に直線的で、ロング・スクレーピング法と呼ばれる、スクレーピング痕が重なり合うような、より広く長いスクレーピング痕を作る。何度も削る場合は、削り跡が互いに垂直になるようにする。
ファインスクレーパーによる掻き取り
荒削りを基本に、接触点の数をさらに増やす。削り取り時には、削り跡が短く幅の狭いショート・スクレイピング法を使用する。何度も削る場合は、それぞれの削り方向を一定にし、後の削り跡が前の削り跡と45°~60°交差するようにする。
微細な削り取りの効率を上げるため、削り取り時に高点(黒く光る点)を大きく削り取り、その周囲も削り取ることで高点以下の点を表示する。標準的な25mm×25mmの正方形の枠で検査し、12~15点が表示されるようにする。
細かい削り
ファインスクレーピングを基本に、さらにファインスクレーパーを使用して、加工部品表面の平坦度と合わせ部品の接触精度を向上させる。
細かい削りでは、スクレーパーを高いところに向け、最も大きく明るい点を取り除き、中程度の大きさの明るい点は砕き、小さな点は削らずに残す。削り跡は短く細くなり、削り花の大きさが均一で、きれいに交差していることが要求される。標準的な25mm×25mmの正方形の枠で検査し、20点以上が表示されるようにする。
(2) 曲面削り出し加工
一般機器の製造や主な修理において、曲面削正は主にすべり軸受の削正を指し、最も一般的なものは、一体型ラジアルすべり軸受(スリーブ)、分割型ラジアルすべり軸受(スプリットブッシュ)、内円錐外円筒すべり軸受(旋盤用ブッシュなど)、3分割扇形ブッシュ(グラインダー用ブッシュなど)の削正である。
前述の平面削りと同様であることに加え、曲面削りでも以下の点に注意する必要がある:
1) スクレイピングの準備
スリーブ取付け後のクリアランス要件、スプリットブッシュの取付け要件とシムによるベアリングクリアランスの調整方法、内円錐外円筒すべりブッシュの取付け要件と精度調整方法、扇形ブッシュのアライメント方法など、ベアリングの取付けに関する技術的要件を詳細に理解する。
装置の動作精度要件を理解し、適切な検査ツールを使用して関連する幾何学的精度をチェックし、詳細な記録を作成すること。
装置の運転精度の要求を満たすため、一般にすべり軸受の内外面は研磨され、幾何学的精度(真円度、同軸度、平行度、相対運動部との直角度など)はすでに要求精度に近くなっている。必要な検査を行うことで、削り出しの目的や削り代が明確になり、削り出し計画の立案が容易になります。
2) 道具と機材の準備
スクレーパーや各種精密測定器の準備に加え、曲面削りに必要な治具やクランプツール(金型)の準備にも特に注意を払う必要がある。
特定の状況(ベアリングと対になるシャフトが重かったり、削るのに不便な場所にあったりする場合など)では、ベアリングと同じ直径の標準シャフトを、粗削り時の「ダミーシャフト」として使用することができる。ダミーシャフトは通常、精密研削が施される。ベアリングを削るときは、このダミーシャフトで削ることができる。
平面削正と異なり、ベアリングのクランプ方法は削正品質に直接影響します。掻き取り時にベアリングが適切に配置されていなかったり、クランプされていなかったりすると、ベアリングが変形し、品質に大きな影響を与えます。図18に、一般的に使用されているスクレイピング用治具を示す。
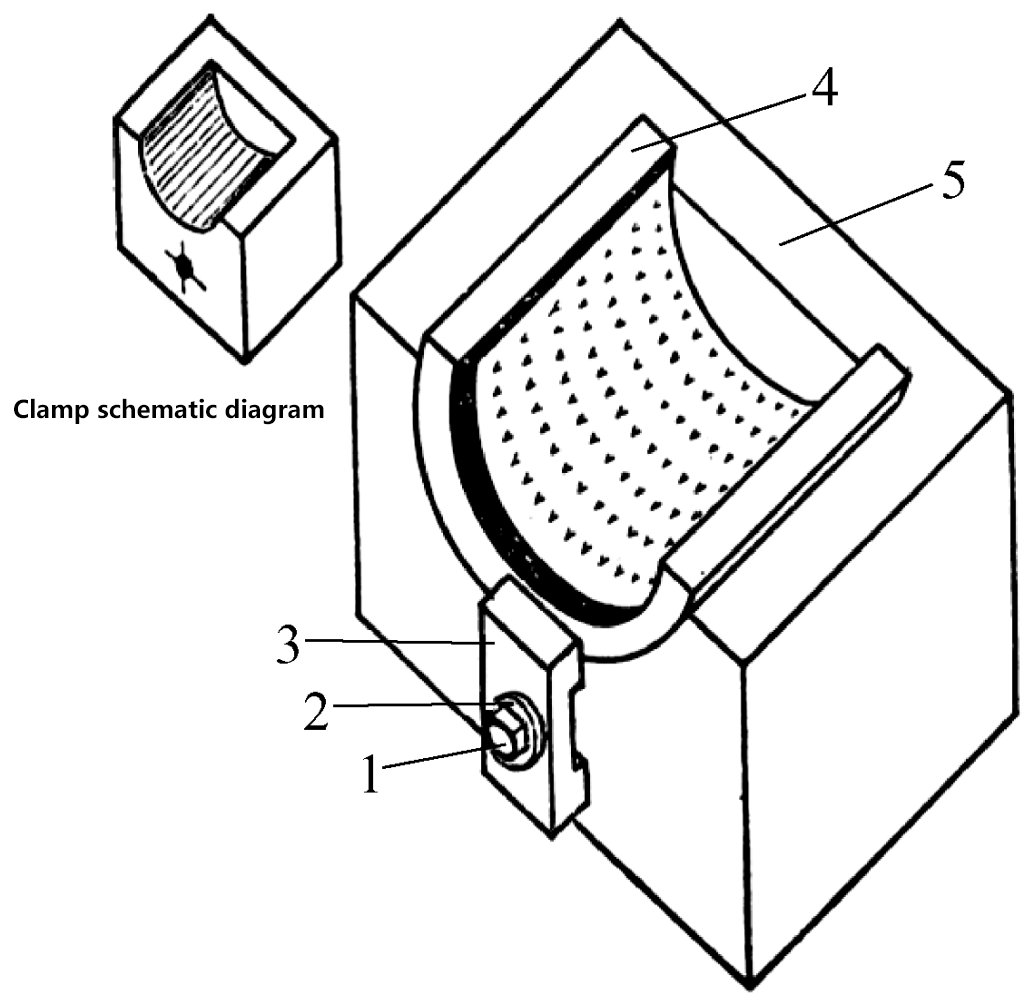
1-スクリュー
2-ワッシャー
3プレッシャープレート
4ワーク
5クランプボディ
3) 典型的なベアリング削り取り工程
分割型ベアリングのスクレーピング工程
分割型すべり軸受の構造を図19に示す。
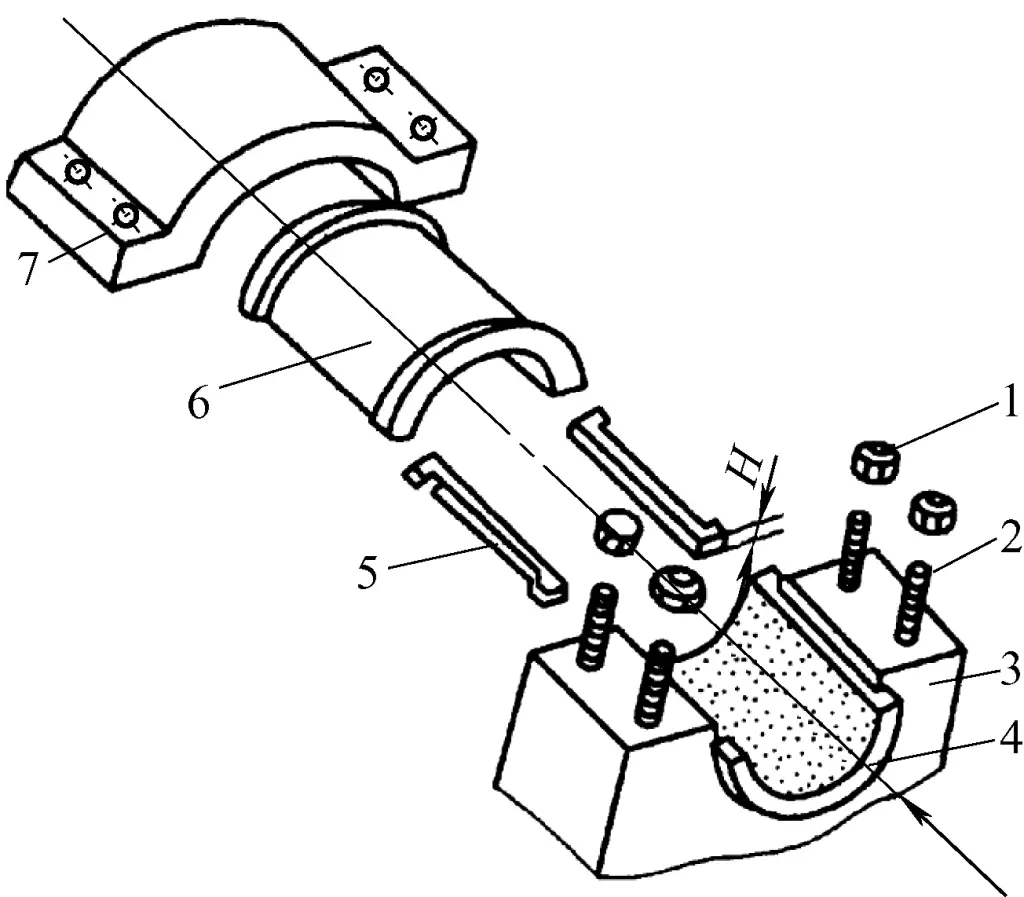
1ナット
2-ダブルエンド・スタッド
3ベアリング・ハウジング
4-下部ベアリング
5-調整シム
6-上部ベアリング
7-ベアリング・キャップ
装置に要求される性能によって、ベアリングの削り出しに要求される精度は異なる。スピンドルの回転精度が要求される重機の場合、伝達剛性を高め、振動を低減し、伝達の滑らかさを向上させるために、シャフトとベアリングの接触精度が高くなければなりません。さらに、流体力学的な油膜を形成するために、シャフトとベアリングの上部および側面のクリアランスを厳密に確保する必要がある。従って、スクレーピングはシャフトとベアリングの接触精度(接触面積、接触面、接触点数)とクリアランスを考慮する必要があります。
ベアリングの背面をトリミングする。スプリットベアリングの背面は、ベアリングハウジングの穴とよく接触していなければならない。そうでないと、運転中、ジャーナルの力を受けて振動が発生したり、ベアリングが変形したりすることがある。従って、検査で条件を満たさない場合は、ハウジングの穴を基準にして、ベアリングの背面を削り直す必要がある。
ベアリング穴の荒削り。ベアリング穴を荒く削る目的は、ベアリング内孔の変形をなくし、ベアリングとシャフトの接触面積を修正し、接触面積を増やすことである。ベアリング穴を荒削りするときは、柔らかいゴムパッドでベアリングを万力で挟んで削る。また、ベアリングハウジングに組み込んで、マッチングシャフトを使用して削ることもできる。
ベアリングハウジングにベアリングを取り付けてから、シャフトを使用して印を付ける場合の注意事項は以下の通りです:
- 上下のベアリングの内面に現像剤を塗布する。
- 相手シャフト、アッパーベアリング、ダブルエンドスタッド、ベアリングキャップを組み立てる。
- ナットを締める。荒削りの初期は、ナットを締めすぎるとシャフトが回転しにくくなります。そのため、荒削りの初期は、相手シャフトを回転させながらナットを軽く締め、シムの厚みを調整し、シャフトが適切な締まり具合で回転するようにする。
- 平らな面の削り取りと同様に、荒削りな削り取りでは、予備的なマーキングの後、ベアリングの内面に現れる黒っぽく光沢のある部分に焦点を当てる必要があります。
- しばらく荒削りした後、フィーラーゲージでシャフトとベアリングの上面と側面のクリアランスを測定する。接触点の分布が均一(25mm×25mmあたり4~7点)であれば、上面と側面のクリアランスも装置の技術要件に近いはずです。
- 具体的には、重作業機では、主軸の焼き付きを防止するために、主軸の延長端にある下部ベアリングを少し低く削ることができる。
ベアリングの穴を細かく削る。ベアリングの内孔を細かく削る目的は、第一に、シャフトとベアリングの内孔の接触点の数を増やし(25mm×25mmあたり10~15点)、接触点を小さくし、均等に分散させることである。第二に、細かく削った後、フィーラーゲージを使ってシャフトの上面と側面のクリアランスを測定し、装置の指定要件を満たすようにする。
細かい削り取り作業では、上下のベアリングの間のシムの厚さを徐々に薄くし、ベアリングをハウジングの穴に組み込んだ後のナットの締め付け力を徐々に大きくする。ただし、マーキングの際に "偽のポイント "ができないように、締め付け力は過大にならないようにする(シャフトを手動で回転させることができるようにする)。
平らな面を削るのと同様に、削る際にはツールマークを交差させ、濃く光沢のある点は強く削り、高い点の周辺は軽く削って次の高い点がどんどん現れるようにする。
内柱外輪テーパすべり軸受のスクレーピング工程
まず、削る順番だ。
図20aに示すように、内柱外輪テーパーすべり軸受は、工作機械の主軸駆動装置によく使用される。内柱外輪テーパすべり軸受の削り取り修理順序は、まず、マッチングシャフトを治具として使用し、回転精度の要求を満たすように軸受の内孔を削り取り、次に、主軸ボックス孔に合うように軸受の外輪テーパ面を削り取る(新しい軸受の場合は、機械ベース孔を基準として外輪テーパ面を削る)。
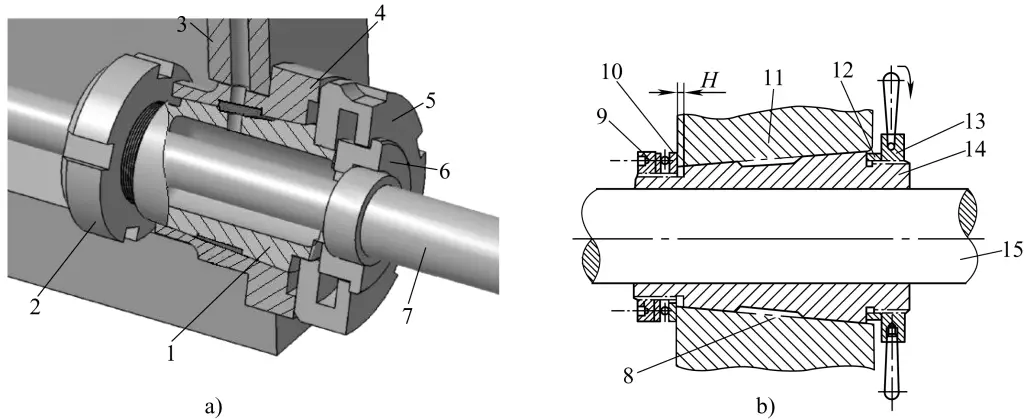
1インナーベアリングスリーブ
2-リアナット
3ベアリングハウジング穴
4アウターベアリングスリーブ
5-フロントナット
6-アジャスト・スリーブ
7シャフト
8-コンタクト・マーク・ポイント
ナインナッツ
10-スラスト玉軸受
11スピンドルボックス
12-ブッシング
13-スパナナット
14-ベアリング
15-メインスピンドル
図20bに示すように、ケーシングの外側の円錐面と内側の穴を削った後、スパナナットとブッシュを外し、ベアリングをスピンドルボックスの穴に固定し、ベアリングの内側の穴をスピンドルに合うように少し削る。
次に、内孔を削るための技術的要件。
まず、工作機械の高速運転の特性に合わせるため、内孔を削った後、ベアリングの両端の接点は硬く密にし、ベアリング孔の中央の接点は柔らかくまばらにする。こうすることでオイルのくさびができやすくなり、運転中にシャフトを安定させることができる。内孔を精密に削った後、両端25mm以内に14~17個の接触点があるはずである。
第二に、工作機械の重負荷運転の特性に適応するため、軸受負荷面の接触点を適切に密にして耐摩耗性を高め、摩耗後の主軸の沈み込みに一定の余裕を残す必要がある。旋盤の主軸軸受穴を削った後、接触点は通常「ダイヤモンド」分布を呈する。
内孔を削る際の注意点。
- フロントとリアの両方がベアリングブッシュ構造の場合、フロントとリアのベアリングを同時に削り、同軸性を確保しなければならない。
- 接点を削るときは、スピンドルの回転と同じ方向にシャフトを3~5回転させる。その後、シャフトを引き抜き、ベアリングを取り外し、大きな斑点から鎖状に斑点が散らばるまで削る。
- リヤベアリングが転がり軸受の場合は、転がり軸受に代わるセンタリングスリーブとして鉄製スリーブを製作する。
- 最終的にベアリング・ホールを細かく削るときは、隣接するナイフ・マークを2パスごとに交差させて削る。スポットが均一になったら、ナイフマークを徐々に薄く、短くし、スポットは小さな四角形または多角形にして、長い帯状にならないようにする。
3.スクレイピングの基本テクニック
(1) 平面削り
1) 平面削りの基本プロセス
平面を削る基本的な工程には、主にナイフを下ろす、ナイフを押す、ナイフを押す、ナイフを持ち上げるというステップが含まれる。掻き出し動作の完了までの時間は非常に短いため、連続した動作で一気に完了させる必要がある。
スクレイピングの重要なテクニックは、優しくナイフを下ろすこと(振動痕がないこと、下ろす角度が15°~25°であること)、安定して押し付けること(スクレーパーが横方向に傾かないこと、圧力が小さいものから大きいものへと徐々に変化すること)、素早くナイフを持ち上げること(ブレード痕がないこと)である。
図21に示すように、平らな表面を削る際の作用過程である。
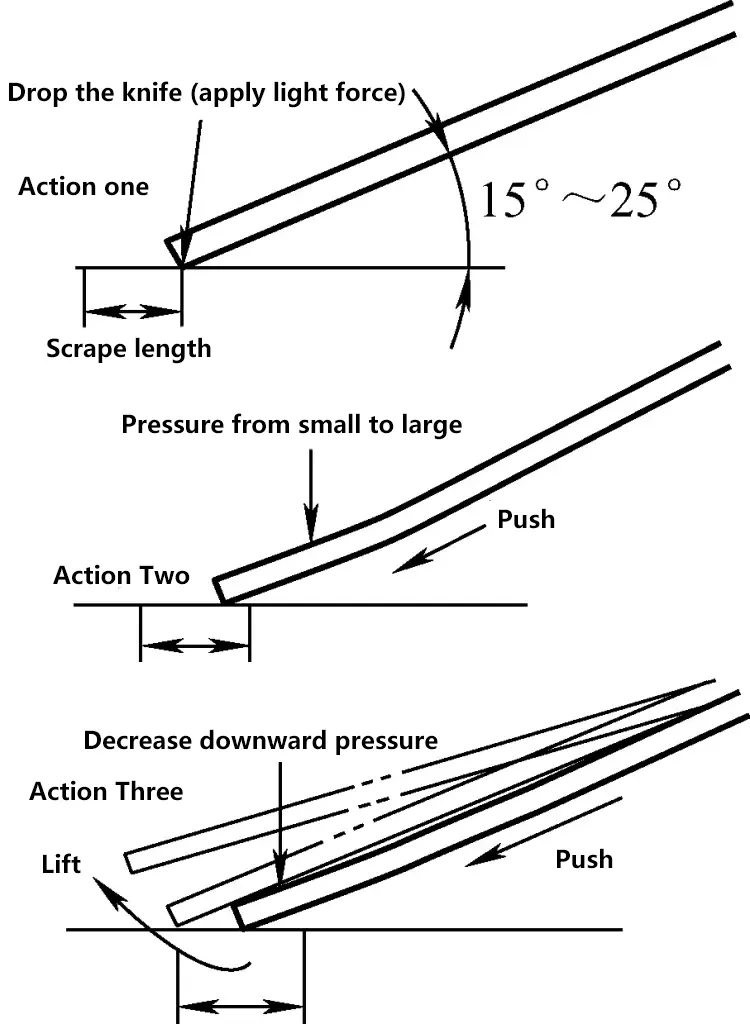
2) 手掻き法と押し掻き法
手で削る方法
図22に示すように、手掻きの基本的な技術である。スクレイピングの際、通常、右手はハンドルを持ち、左手はブレードを握り、手のひらはエッジから約50mmのところでスクレーパーの前端を押す。
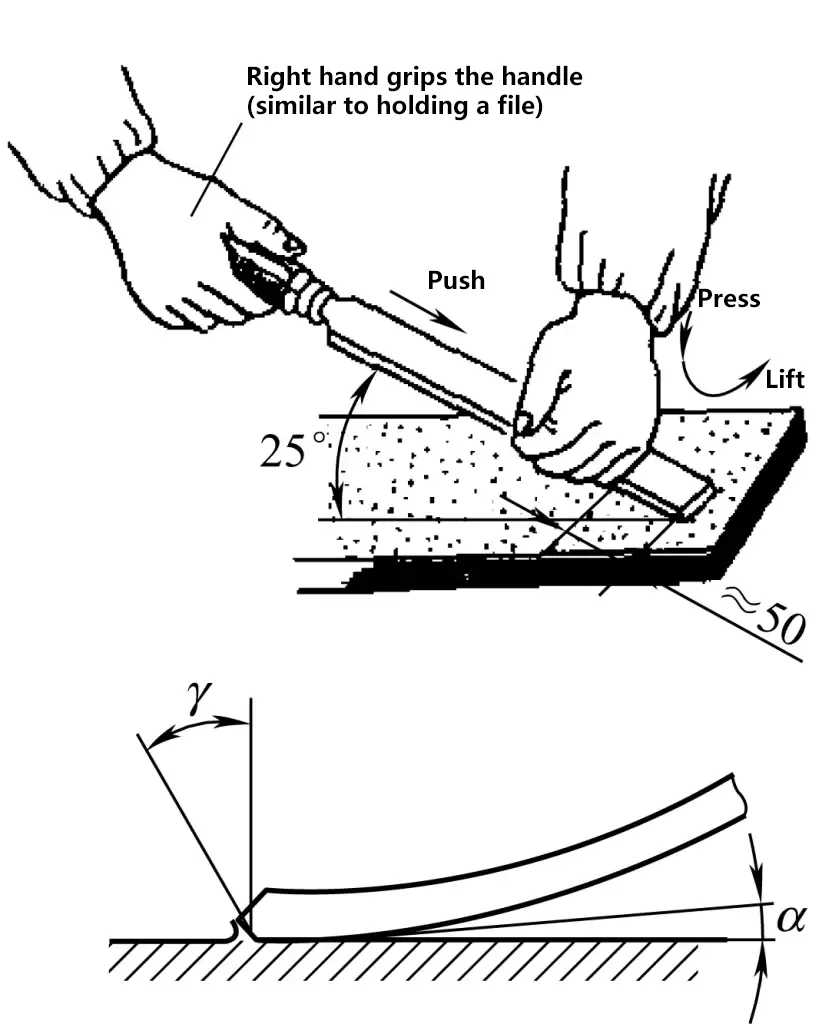
スクレーピングの際は、ブレードをスクレーピングエリアに合わせた後、左手でスクレーパーを押し、ブレードをわずかに曲げ変形させる。その後、両手でスクレーパーを刃渡りの長さだけ前に押し出し、素早くスクレーパーを持ち上げる。押す、押す、持ち上げるの一連の動作が一度に完了する。手掻きの方が力加減や掻き代が少なく、一般的に小さな部品の表面仕上げに適している。
プッシュ・スクレイピング方式
現在の押し掻きの作業では、構えや姿勢はほとんど同じで、スクレーパーの持ち方と手の力の使い方に違いがある。
プッシュ・スクレイピング方式1:
図23に示すように、スクレーパーの柄を腹部の右側の筋肉に当て、両手で刃を持つ。左手は正面、刃先から約80mmの位置にある(この距離は操作者の身長によって調節できる)。スクレーピングの際は、両手でスクレーパーを押し下げ(右手の圧力は弱め)、脚と腰の力を使ってスクレーパーをコンタクトポイントに合わせて前に押し出す。
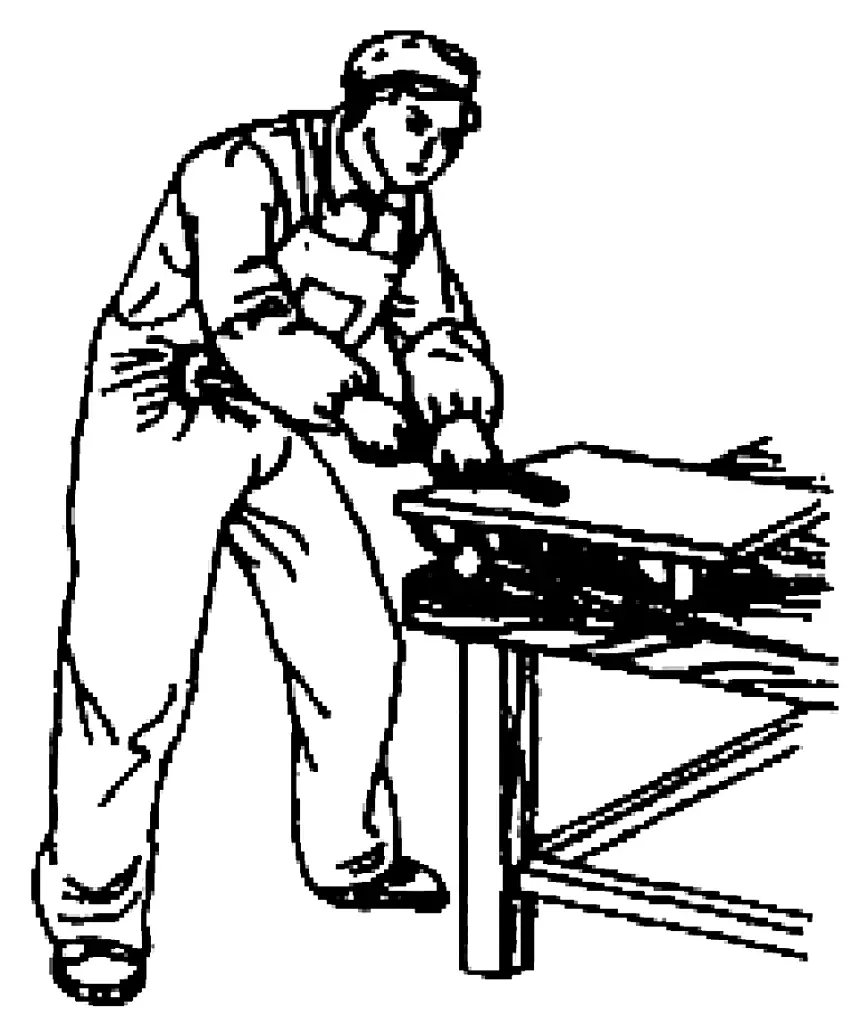
押し進めた瞬間、右手はスクレーパーの方向をガイドし、左手はスクレーパーを素早く持ち上げ、表面から金属の切れ端を取り除き、ワンプッシュの掻き取り動作を完了する。この方法は、主に左手による削り圧のコントロールに頼っており、左手の圧力を調整することで、荒削り、細削り、精密削り時の削り量を調整することができる。
プッシュ・スクレイピング法2:
これは平面のスクレーピングで最も広く使われている作業である。図24に示すように、右手でスクレーパーを持ち、左手を右手の上に置いてスクレーパーを押す方法である。基本的に両手を密着させ、スクレーパーの特定の箇所に力を加えるので、前端が大きく曲がり、切削量が大きくなり、軟らかい素材の荒削りに適している。
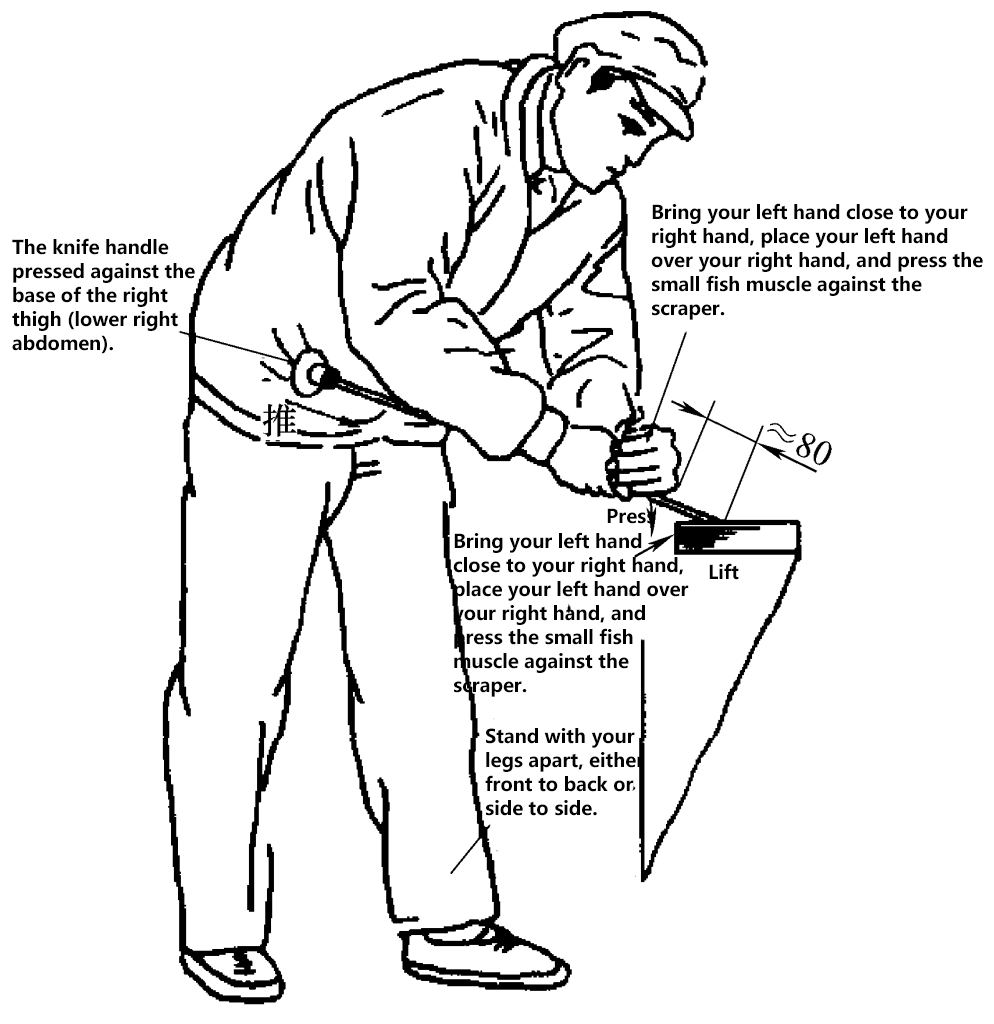
この説明の後、プッシュ・スクレイピングの主なテクニックを以下にまとめる:
足を開いて安定し、腰を前に曲げる;
スクレーパーの柄を腹部(右下側)で持つ;
右手でスクレーパーを操作し、刃を静かに平らに下ろす;
左手で押さえ、腰と脚で前に押し出す;
右手で素早く持ち上げ、瞬時に動作を完了させる。
プッシュ・スクレイピング方式3:
上の2つの動作と似ているが、違いは両手が刃に加える力の変化にある。左手が手前、右手が奥で刃を持ち、スクレーパーの刃先を高い位置に合わせた後、右手はある位置で刃をわずかに持ち上げ、左手はスクレーパーを押し下げることで、掻き出し時に刃の前端にわずかな曲がりを生じさせる方法である。
上記2つの方法と比較して、この掻き取り方法の最大の利点は、穏やかなブレードの下降、迅速なブレードの持ち上げ、短いブレードトレースです。しかし、掻き取り圧力が小さく、より多くの労力を必要とするため、精密な掻き取りに最も適している。
(2) 曲面削りの主なテクニック
図25aに示すように、曲面を削るには両手の協調運動が必要である。
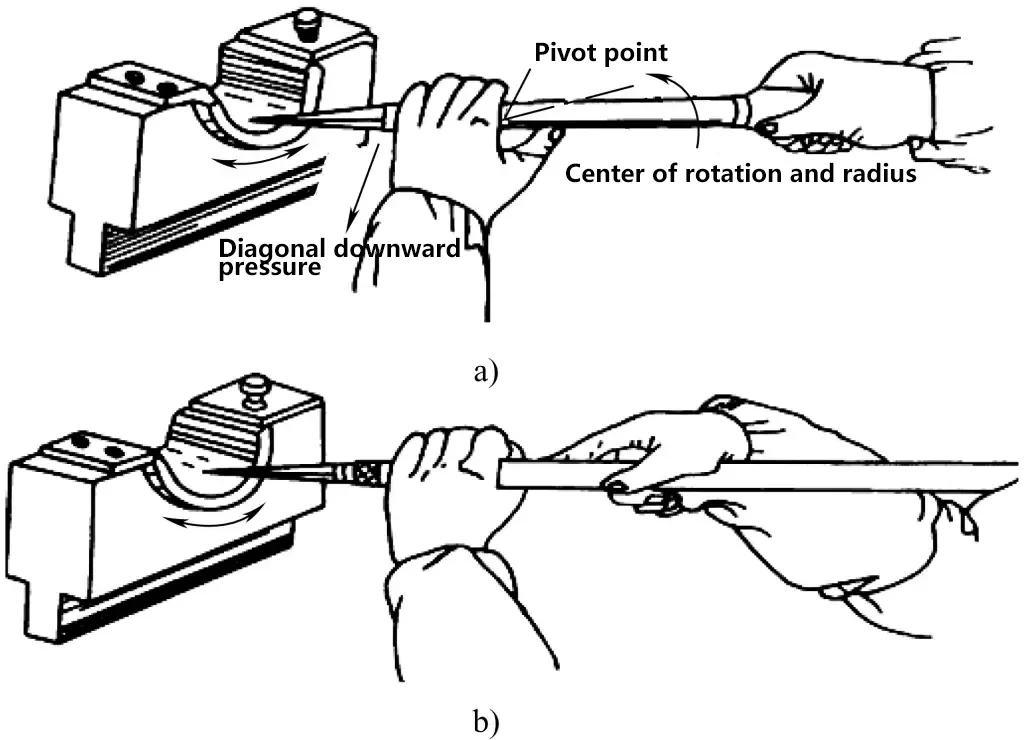
a) 曲面削り取り作業
b) 曲面削り取り作業2
スクレーピングの際、スクレーパーエッジの先端を高い位置に合わせ、右手でハンドルを持ち、左手で内側の円弧の接線に沿って斜めに圧力をかける。左手を円運動の支点として、スクレーパーを内側の円弧に沿って誘導する。
したがって、作用原理の観点から見ると、スクレーパー前縁は、右手によって制御される回転運動(スクレーパー軸を中心としたわずかな回転)と、左手によって制御される内側円弧に沿ったスイング運動の両方を持ち、その結果、スクレーピング中のスクレーパー前縁のらせん運動が生じる。
図25bに示すように、スクレーパーの刃と柄の後部を肩に置き、両手で刃を握って上記と同じ原理で曲面を削る。
平面の掻き取りと同様、曲面の掻き取りにも、刃を静かに下げること、安定した押し付け、素早い刃の持ち上げが要求される。
4.スクレイピング表面の欠陥分析
表2 スクラッピング表面の欠陥分析
欠陥の種類 | 欠陥の原因 |
ピット清掃 | 1) スクレーパーのウェッジ角度が不適切である; 2) スクラップの逃げ角が大きすぎる; 3) 過度の削り圧; 4) 削り跡が長すぎる、スクレーパーの持ち上げが遅すぎる。 |
チャターマークを削る | 1) スクレーパーの落下が重すぎる; 2) 平面スクレーピングでは、ブレードが平らでない、つまりブレードとスクレーピング面の間に角度がある。曲面スクレーピングでは、曲面スクレーパーの角度が正しくない; 3) 掻き取り面の材料分布が不均一である。 |
ナイフで削った跡 糸のような跡が現れる | 1) スクレーパーには切り欠きがある; 2) 高点材料が硬すぎる; 3) スクレーパーの刃に硬いものが付着する; 4) 研磨工具と被研磨物の間に硬いものが挟まっている、または研磨工具の端にバリがある。 |
5.スクレイピングの安全要件
- 削る前に、ワークから鋭利なエッジやバリを取り除く。削る際は、慣性による腕の怪我を避けるため、鋭角付近でのナイフの位置と力に特に注意する。
- 移動したり合わせたりする必要がある大きなワークを削る場合は、持ち上げたり置いたりする際の安全性に注意してください。
- 掻取りの際は、作業者とワークの相対位置を適切に調整してください。高さが不足する場合は、木製の板で支えますが、作業者が安全に掻き出し力を加え、転倒を防止するために、調整後の板が安定していることを確認してください。
- ワークの端まで擦るときは、過剰な力によって人とナイフの両方が誤って前方に突き出されないように、圧力と推力をコントロールする。
- スクレーパーは使用後適切に保管し、プライバーとして使用しないこと。