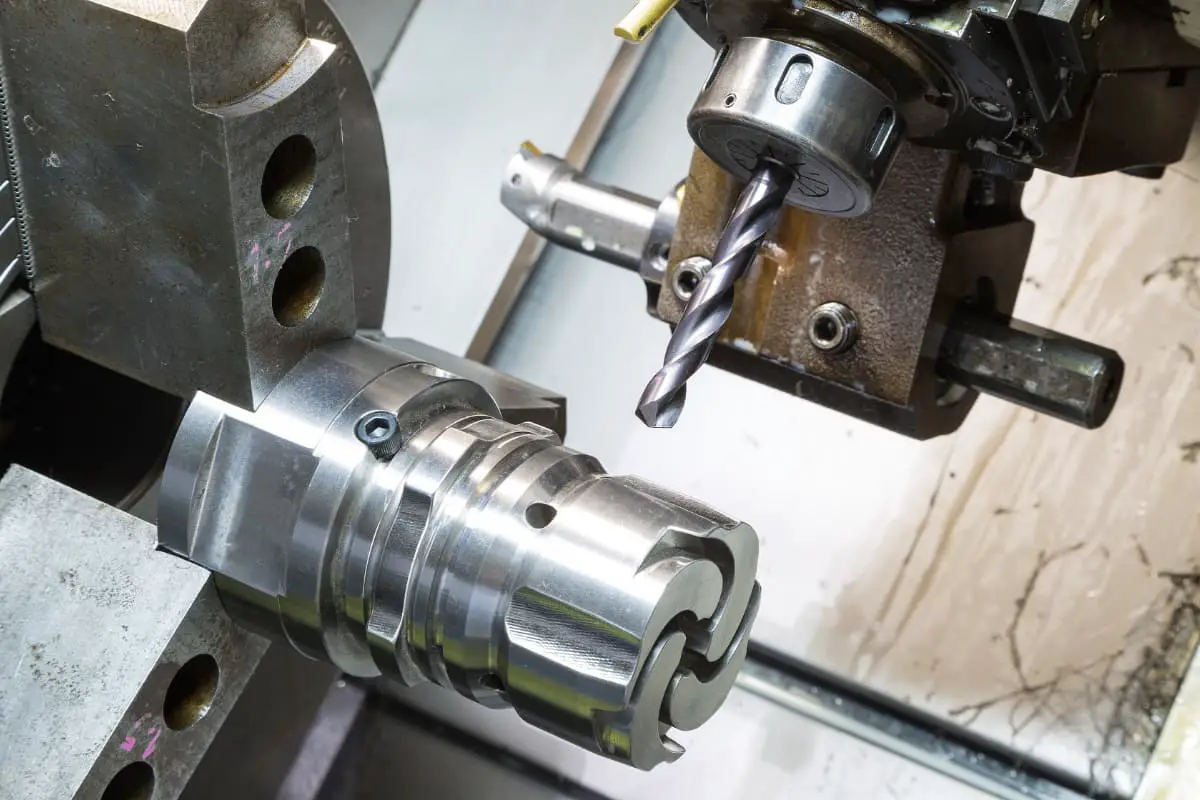
I.マシニングセンタの構成と動作原理
マシニングセンタは、CNCフライス盤から発展した高度に自動化された加工装置である。工具マガジンと自動工具交換装置(ATC)を備えたCNC工作機械で、自動工具交換CNC工作機械やマルチプロセスCNC工作機械とも呼ばれる。
ワークが一旦クランプされた後、CNCシステムはマシンを制御して、異なるプロセスに応じて工具を自動的に選択・交換し、主軸速度、送り速度、ワークに対する工具の動作軌跡、およびその他の補助機能を自動的に変更し、ワークの複数の面を順番に多工程加工することができる。
これにより、ワークのクランプ、測定、機械の調整時間が短縮され、ワークの保管とハンドリング時間が短縮され、生産効率と機械の稼働率が向上する。マシニングセンタは、自動加工に欠かせない設備であり、また、次のような分野の中核をなす機械でもある。 フレキシブル生産システム (FMS)である。マシニングセンタの機能性を向上させるために、ツールマガジンの自動交換、主軸ヘッドの自動交換、主軸ボックスの自動交換などを備えたマシニングセンタが登場している。
ツールマガジンの自動交換が可能なマシニングセンタは、ツールマガジンの容量が大きく、複雑な箱型部品の多工程加工が容易です。主軸頭自動交換タイプのマシニングセンタは、横フライス加工、立フライス加工、研削加工、割出フライス加工が可能である。このタイプのマシニングセンタには、ツールマガジンの他に、主軸ヘッドマガジンがあり、このマガジンの交換は 産業用ロボット または機械的な手。
主軸箱自動交換機能を持つマシニングセンタは、加工精度と加工範囲を向上させるため、一般的に粗加工用主軸箱と微細加工用主軸箱を備えている。マシニングセンタと一般的なCNC工作機械との大きな違いは、複数の機械が必要な加工を1台の機械で完結できることです。
現在、マシニングセンタは、ツールマガジンの大容量化、ツール交換時間の短縮、加工精度の向上、高機能化などが進んでいる。CNCフライス盤から発展したマシニングセンタ(フライス・中ぐりマシニングセンタ)に加え、CNC旋盤から発展したターニングマシニングセンタも登場している。
1.マシニングセンタの構成
1958年に世界初のマシニングセンタが誕生して以来、さまざまなタイプのマシニングセンタが登場し、外観構造も異なるが、おおむね次のような主要部品で構成されている。
(1) 工作機械本体
マシニングセンタのボディとは、主駆動システム、送り駆動システム、ベッド、コラム、ワークテーブルで構成される機械構造の実体を指す。
これらの部品には、鋳鉄部品や溶接鋼構造物などがある。マシニングセンタの基本構造であり、マシニングセンタの静的荷重や加工時に発生する切削荷重に耐える必要があるため、十分な剛性が求められます。
(2) CNCシステム
CNCシステムはマシニングセンタのコントロールセンターであり、その魂である。主に主制御システム、プログラマブルロジックコントローラ(PLC)、入出力インターフェース、キーボード、モニターで構成される。主制御システムは主にCPU、メモリ、コントローラで構成される。
CNCシステムの主な制御対象は、位置、角度、速度などの機械量と、温度、圧力、流量などの物理量である。その制御方式は、データ演算処理制御と逐次論理制御に分けられる。
主制御装置内の補間モジュールは、部品プログラムを読み込み、デコードとコンパイルによって処理し、対応する工具経路の補間計算を行い、各座標サーボシステムの位置と速度のフィードバック信号と比較して工作機械の各座標軸の変位を制御する。
シーケンシャルロジック制御は通常、PLCが行う。PLCは工作機械の加工プロセスで必要な動作を調整し、各種検出信号に基づいて論理的な判断を行い、工作機械の各部の動作を整然と制御する。
(3) サーボシステム
サーボシステムは、CNCシステムと工作機械本体の間の電気駆動リンクである。主にサーボモーター、駆動制御システム、位置検出装置、フィードバック装置から構成される。サーボモータはシステムの実行部品であり、駆動制御システムはサーボモータの動力源である。
CNCシステムによって発行されたコマンド信号は、位置フィードバック信号と比較され、変位コマンドとして使用されます。駆動システムによる電力増幅の後、モーターを回転駆動し、機械的な伝達装置を介してワークテーブルまたはツールホルダーを移動させます。
(4) 補助装置
補助装置は主に自動工具交換装置(ATC)、自動パレット交換装置(APC)、ワークのクランプとリリース機構、回転ワークテーブル、潤滑と冷却装置、自動切屑除去システム、油圧システムを含む、 空気圧システム電気系統、過負荷装置、保護装置など。マシニングセンタの作業効率、加工精度、安全信頼性を確保する役割を担っています。
2.マシニングセンタの動作原理
マシニングセンタで部品を加工するには、まず、設計された部品図面に基づいて、加工プロセスの分析と設計を行った後、主軸の始動/停止、主軸速度の変更、切削パラメータ、送り経路など、加工プロセス中に必要なさまざまな操作を行います、 切削油剤 工具の供給量、工具とワーク間の相対変位は、指定されたCNCコードを使用して、一定のフォーマットで加工プログラムに書き込まれる。
そして、キーボードなどの入力装置を通じてCNCシステムに情報を送信する。CNCシステム内のコンピュータは、受信したプログラム命令を処理・計算し、サーボシステムやその他の補助制御回路に指令を送り、プログラム内の指定された動作シーケンス、工具の動作軌跡、切削加工パラメータに従って自動加工を行わせる。部品加工が完了すると、機械は停止する。
マシニングセンタは、プログラム入力、デバッグ、最初のピースの試し切りが完了し、バッチ生産に入ると、一般的にオペレータはワークのロードとアンロードを行い、プログラム自動サイクルスタートボタンを押すだけで、マシニングセンタは自動的に全加工プロセスを完了することができる。
II.マシニングセンタの分類と用途
1.マシニングセンタの分類
マシニングセンタには様々な形状のものがあり、分類方法も複数ある。
加工精度によって、通常のマシニングセンタと高精度マシニングセンタに分けられ、制御可能な座標軸と連動座標軸の数によって、3軸3連動、4軸3連動、5軸4連動、6軸5連動マシニングセンタに分けられ、ワークテーブルの数と機能によって、シングルワークテーブルマシニングセンタ、ダブルワークテーブルマシニングセンタ、マルチワークテーブルマシニングセンタなどに分けられる。
一般的な分類方法は機械の構造に基づいており、一般的に立形マシニングセンタ、横形マシニングセンタ、門形マシニングセンタ、五面加工マシニングセンタに分けられる。
(1) 立形マシニングセンター
立形マシニングセンタとは、主軸が垂直に設置されたマシニングセンタのことで、一般的に3つの座標軸を持ち、3軸リンクが可能である。マシニングセンタの中には、5軸制御や6軸制御が可能なものもあり、より複雑な部品の加工も可能である。
図1に立形マシニングセンタの外観を示す。その構造は多くの場合、固定コラムタイプで、インデックス回転機能を持たない長方形のワークテーブルを持ち、ディスク、スリーブ、プレートタイプの部品の加工に適している。立形マシニングセンタのワークテーブル上に水平軸CNCロータリーテーブルを設置し、スパイラルタイプの部品を加工することもできる。
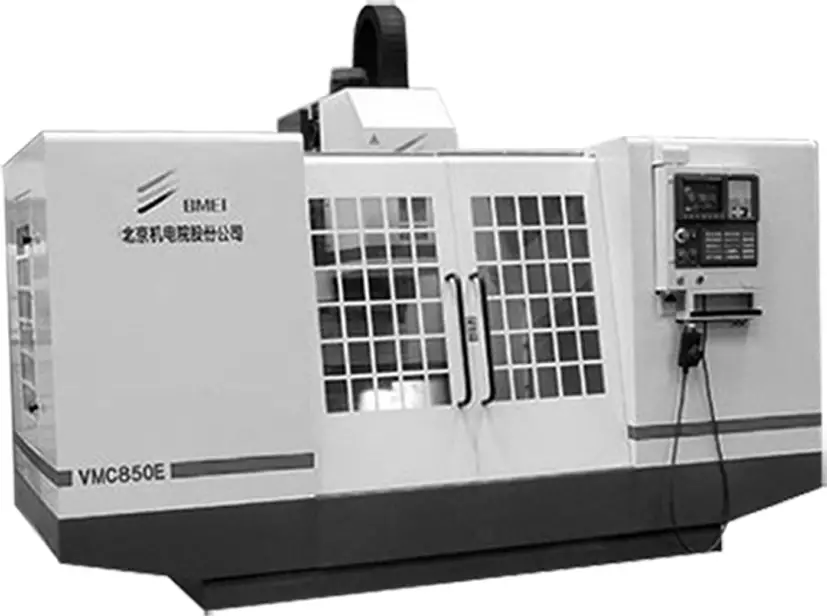
立形マシニングセンタは、ワークのクランプに便利で、観察、操作、プログラムのデバッグが容易である。また、立形マシニングセンタはシンプルでコンパクトな構造で、設置面積が小さく、価格も比較的安いため、広く使用されている。
しかし、コラムの高さと工具交換装置の制限により、立形マシニングセンタは非常に背の高いワークを加工することができない。キャビティや凹面を加工する場合、切りくずの排出が難しく、工具や加工面に深刻な損傷を与え、加工の円滑な進行に影響を及ぼす可能性がある。
(2) 横型マシニングセンター
横型マシニングセンタとは、主軸が水平に設置されたマシニングセンタのことである。図2に横形マシニングセンタの外観を示す。
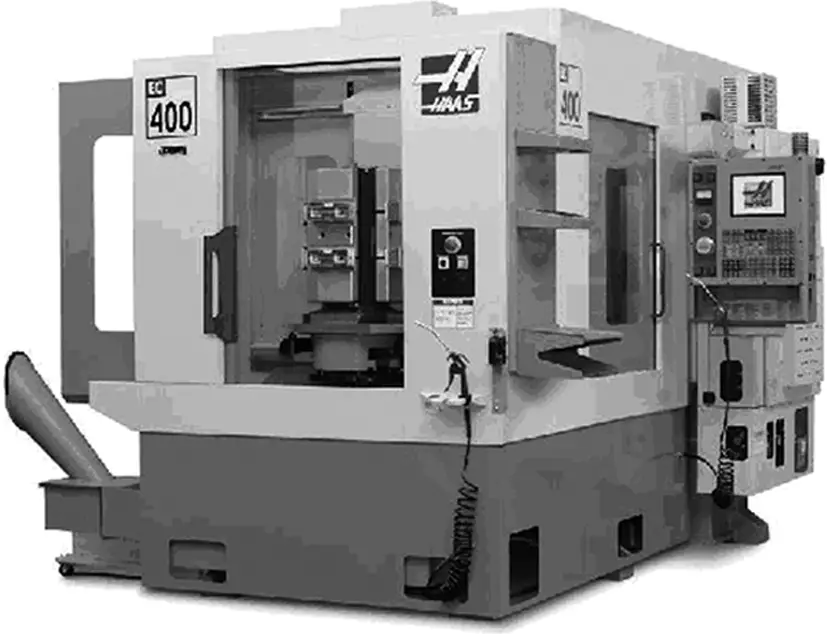
横型マシニングセンタは一般的に3~5軸の座標軸を持ち、一般的には3軸の直線運動座標軸に1軸の回転運動座標軸を加えたもので、ワークの取り付け面と上面を除く4面をワンクランプで加工することができる。立形マシニングセンタに比べ、箱形部品、特に穴と基準面の位置決めや穴間の相対位置精度が要求される箱形部品の加工に適しており、加工精度の確保が容易である。
横型マシニングセンタは、プログラムのデバッグや試切削時の観察、加工中のモニタリングに不便である。ワークのクランプや計測も不便だが、加工中の切りくず排出は容易で、加工には有利だ。
立形マシニングセンタに比べ、横形マシニングセンタはツールマガジンの容量が大きく、全体構造が複雑で、容積と床面積が大きく、価格が高いなどの特徴がある。横形マシニングセンタは、マシニングセンタの中で最も広く使用されている。
(3) ガントリー型マシニングセンター
ガントリータイプのマシニングセンタの形状はガントリーフライスに似ており、主軸は通常垂直に設置される。自動工具交換装置に加え、交換可能な主軸頭アタッチメント、包括的なCNC機能を備え、多目的に使用できる。特に、図3に示すような大型ワークや複雑な形状のワークの加工に適している。
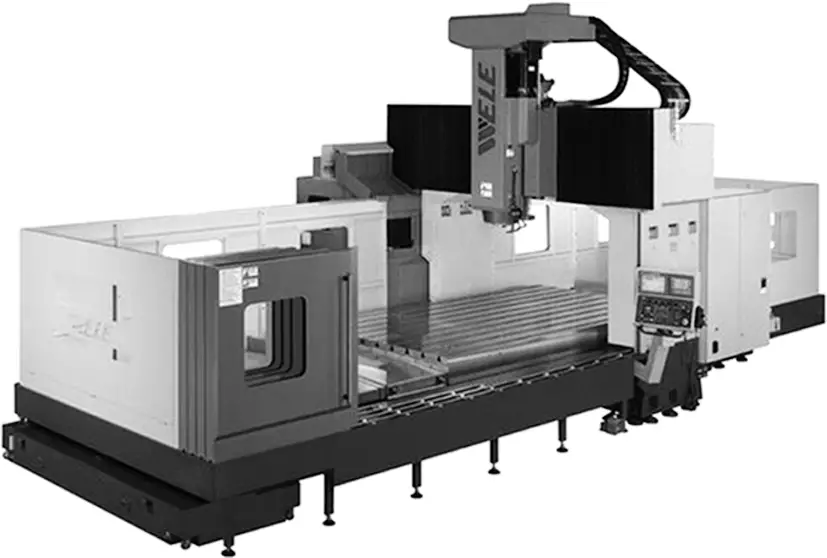
(4) 五面加工機
五面加工機は、図4に示すように、立形マシニングセンタと横形マシニングセンタの機能を併せ持つマシニングセンタ、すなわち立形と横形の複合マシニングセンタである。
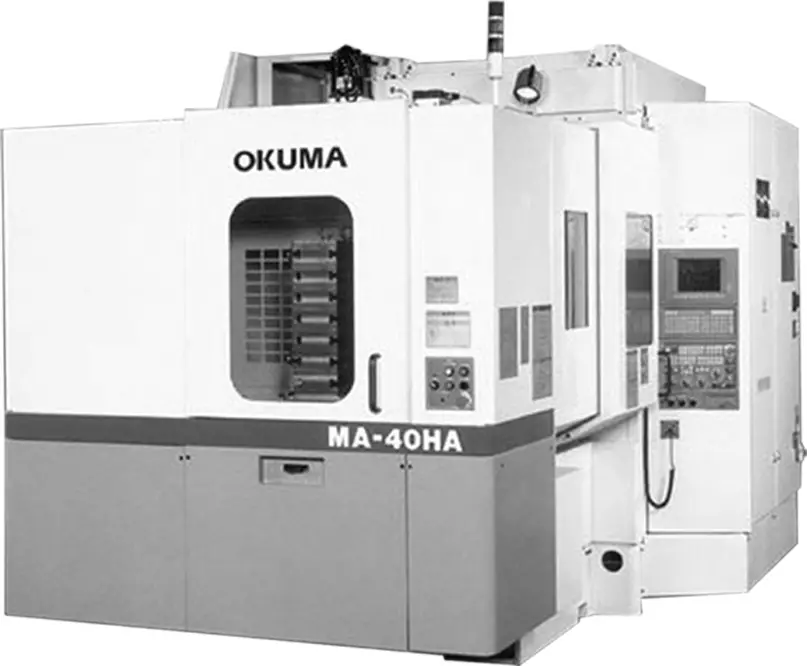
五面加工機は、一度のワーク取り付けで、取り付け面を除く5面すべての加工を完了することができ、加工精度と生産効率を大幅に向上させ、経済的なメリットも大きい。
一般的な五面加工機には、主軸が90°回転して垂直・水平加工を行うタイプと、主軸は回転しないがCNC回転作業台がX軸に沿って90°回転し、ワークを90°回転させて5面の加工を行うタイプがある。
2.マシニングセンタの用途
マシニングセンタは高価で、初期投資も大きく、部品加工コストも高く、質の高いオペレーターが要求される。そのため、マシニングセンタでの加工に適した部品を、形状や要求精度などさまざまな角度から総合的に検討する必要がある。
一般的にマシニングセンタは、複雑な形状、高い精度が要求される部品、複数の工程を要する部品、複数の種類の従来型工作機械や多数の工具・治具を必要とし、何度もセットアップや調整を行わなければ完成しない部品に適している。
(1) 箱型部品
箱型部品とは、一般に、複数の穴があり、一定の内部空洞を持ち、長さ、幅、高さが一定の比率を持つ部品を指す。これらの部品は、機械、自動車、航空宇宙などの産業で一般的で、自動車エンジンブロック、ギヤボックスハウジング、工作機械ヘッドストック、スピンドルボックス、ディーゼルエンジンブロック、ギヤポンプハウジングなどがある。
箱型部品は一般的に、多位置穴加工システムと平面加工を必要とするため、マシニングセンタの主要な加工対象の1つとなっている。
公差要件、特に幾何公差要件は比較的厳しく、通常、フライス加工、ボーリング加工、ドリル加工、リーマ加工、面取り加工、タッピング加工などの工程が必要となる。従来の工作機械が必要とする60%~95%の加工内容を、1回の段取りで完了させることができるため、安定した部品精度、安定した品質、生産サイクルの大幅な短縮、コスト削減を実現します。
加工位置が複数あり、完成までにワークテーブルを何回転もさせる必要がある部品には、一般的に横型マシニングセンタが選択される。加工位置が少なく、スパンが大きくない場合は、一端から加工する立型マシニングセンタを選択することができる。
(2) ディスク、スリーブ、プレートタイプ部品
例えば、フランジ付きシャフトスリーブ、キー溝付きシャフト、角型ヘッドなど。さらに、複数の穴加工が施された板状の部品、例えば各種モーターカバーなどがある。
ディスク、スリーブ、プレートタイプの部品で、穴が分散しているものや端面が曲面になっているものには立形マシニングセンタが適しており、ラジアル穴のものには横形マシニングセンタを選ぶことができる。
(3) 複雑な構造形状や高精度が要求される部品
複雑な構造形状を持つ部品は、複雑な曲面で構成された複数の加工面を持つことが多く、通常、従来の工作機械では一般的に困難か不可能な多座標リンク加工を必要とする。
航空機や自動車のプロファイル面、インペラ、プロペラ、各種曲面成形金型などの複雑な曲面は、機械製造業、特に航空宇宙、自動車、造船、防衛産業において重要な位置を占めている。マシニングセンタは、一般的にこれらのタイプの部品を加工するために選択され、通常のCNC工作機械の主な加工対象でもある。
代表的な部品には、カム式部品、一体型インペラ式部品、金型式部品などがある。高精度が要求される中・小ロット部品の加工にマシニングセンタを選択することで、寸法精度や形状位置精度が良く、寸法安定性が高く、安定した品質が得られます。
複雑な曲面を加工する場合、加工干渉帯や死角がなければ、ボールエンドミルカッタを3座標リンク加工に使用することができる。この場合、加工精度は高くなりますが、効率は比較的低くなります。加工物に加工干渉帯や死角がある場合は、4座標または5座標リンクの工作機械の使用を検討する必要がある。
マシニングセンタの自動工具交換の利点は、複雑な曲面の加工では十分に生かされない。複雑な曲面の加工は一般的に、荒フライス加工から(中)仕上げフライス加工までのステップを経るため、特に金型のような単一ピースの加工では、少ない工具で加工できる。
(4)不定形部品
異形部品とは、外形が不規則な部品のことで、ブラケット、ベース、テンプレート、治具など、点、線、面を複数の位置で混在して加工する必要があるものが多い。一般に異形部品は、剛性が低く、クランプが複雑で、切削時に変形しやすく、加工精度の確保が難しい。
従来の工作機械による加工では、工程が多く、治具が複数あり、加工時間が長く、加工品質の確保が難しい。このような場合、マシニングセンタの工程集約機能をフルに活用し、適切な工程対策を採用することで、1~2回の段取りで加工内容のほとんど、あるいはすべてを比較的短時間で完了させることができる。
異形部品を加工する場合、形状が複雑で要求精度が高ければ高いほど、マシニングセンタの優位性が発揮され、活用される。マシニングセンタで部品を加工する場合、工程の準備やプログラムの編集に費やす時間は、作業時間全体に占める割合が大きい。そのため、部品の循環バッチ生産では、同じプログラムを何度も繰り返し使用することで、生産サイクルを大幅に短縮することができる。
マシニングセンタマシニングセンタの加工特性と適用範囲
1.マシニングセンタの加工特性
従来のCNC工作機械と比較して、マシニングセンタには次のような優れた特徴がある。
(1) プロセス集中
マシニングセンタは、工具マガジンと自動工具交換装置を備えている。1つのワークをセットアップした後、CNCシステムは機械を制御して、異なるプロセスに応じて工具を自動的に選択・交換し、機械主軸速度、送り速度、ワークに対する工具の移動軌跡、およびその他の補助機能を自動的に変更することができる。カム、ハウジング、ブラケット、カバープレート、金型などの複雑な表面部品の加工に適しています。
(2) 高い加工精度
マシニングセンタは、他のCNC工作機械と同様、加工精度が高いという特徴がある。また、マシニングセンタは加工工程が集中しているため、長い工程フローを避けることができ、人の干渉を減らすことができるため、さらに高い加工精度と安定した加工品質を実現することができます。
(3) 機械加工における強力な適応性
マシニングセンタは、加工対象への強い適応性、すなわち高い柔軟性を持っている。マシニングセンタの生産柔軟性は、特殊な要求への迅速な対応だけでなく、バッチ生産を迅速に実現する能力にも反映され、市場競争力を向上させる。
(4) 労働強度の低減と労働条件の改善
マシニングセンタは、あらかじめプログラムされたルーチンに従って自動的に部品を加工し、部品加工を完了する。オペレーターは、操作盤の操作、ワークの着脱、工具のセット、主要工程の中間検査、機械の動作観察などを行うだけで、重い手作業を繰り返す必要がない。これにより、労働強度や緊張感が大幅に軽減され、作業環境も改善される。
(5) 高い生産効率
マシニングセンターには、ツールマガジンと自動工具交換装置が装備されている。マシニングセンタの中には、自動ワークステーション交換機能を備えたものもある。複数の工程を1台の機械に集中させることができるため、ワークのセットアップ、測定、機械の調整時間が短縮され、半製品の搬送、ハンドリング、保管の時間も短縮されるため、補助時間が大幅に短縮され、生産効率が向上する。
(6) 優れた経済効果
マシニングセンタで部品を加工する場合、各部品に割り当てられる設備費は高額になる。しかし、生産効率が高く、加工精度が高く、加工が安定しているため、スクラップ率が低く、加工設備費が低いため、生産コストが大幅に削減され、経済効果が高い。
(7) 生産管理の近代化の促進
マシニングセンタによる部品加工は、部品加工時間の正確な計算を可能にし、検査、工具・治具管理、半製品管理を効果的に簡素化し、生産管理の近代化に寄与する。
マシニングセンタには上記のような利点があるが、高価で、技術的に複雑で、メンテナンスが困難で、加工コストが高く、質の高い管理・運営要員が必要である。したがって、企業にとって最良の経済的利益を得るためには、さまざまな要素を総合的に考慮する必要がある。
2.マシニングセンタの適用範囲
マシニングセンタは、高能率、高精度、高度自動化など、一般の工作機械にはない多くの利点を備えた工作機械である。現在、マシニングセンタの応用範囲は拡大の一途をたどっている。マシニングセンタのメリットを最大限に引き出すためには、以下のような特徴を持つ部品の加工に適している。
(1) 多品種少量生産部品
マシニングセンタの生産柔軟性は、特殊部品加工への迅速な対応だけでなく、バッチ生産を迅速に実現し、市場シェアを迅速に獲得する能力にも反映されている。
(2) 複雑な形状や構造を持つ部品
部品によっては複雑な形状や構造を持ち、従来の工作機械で加工すると高価な加工装置が必要になる。CNCフライス盤を使用する場合でも、工具や治具を何度も交換する必要があるが、マシニングセンターを使用すれば、フライス加工、ドリル加工、中ぐり加工、タップ加工などの複数の工程を1回の段取りで実現できる。
(3) 高価な高精度部品
一部の部品は需要が少ないが高価で、廃棄できない重要な部品である。高い精度と短い生産時間が要求される。従来の工作機械で加工すると、複数の機械が連携して作業する必要があり、人的要因による不良品が出やすい。
加工にマシニングセンターを使用することで、生産工程をすべてプログラムで制御し、工程の流れに干渉する要因を排除することで、高い生産効率と安定した品質を実現している。
(4) 繰り返し生産される部品
製品によっては周期的、季節的な市場需要がある。専用の生産ラインを使えば採算が合わない。通常の設備では加工効率が悪く、品質も安定しない。しかし、マシニングセンターを使えば、1個目の切削に成功した後、プログラムと関連情報を保持することができる。次回の生産時には、最小限の準備時間で生産を開始することができる。
(5) 頻繁な修正を必要とする部品
加工対象が変わっても、加工プログラムを修正し、工具パラメータを調整するだけで、新しい部品を加工できる。これにより、生産準備サイクルが大幅に短縮され、新製品開発、製品改良、改造の近道となる。
(6) 測定が困難な部品
測定が困難な部品については、マシニングセンタ自体の高精度特性をフルに活用することで、部品の加工精度を確保することができる。
IV.マシニングセンタの主要構造と技術パラメータ
1.スピンドル部品
主軸部品はマシニングセンタの重要な部品の一つである。その剛性と回転精度はワークの加工品質に直接影響する。主軸部品は主に主軸ボックス、主軸モーター、主軸、主軸軸受から構成される。
マシニングセンタの主軸モータには、主にDC主軸モータとAC主軸モータが使用され、主動作の無段階変速を実現している。主軸の起動、停止、変速動作はすべてCNCシステムによって制御され、切削加工は主軸に取り付けた工具を通して行われる。
2.サポート体制
(1) ベッド
ベッドは工作機械の基礎であり、十分に高い静的・動的剛性と精度保持が要求される。全体的な設計要件を満たしながら、合理的な構造、適切なリブ配置を実現し、良好な冷間・熱間加工技術を確保する努力が必要である。
ターニングマシニングセンタでは、一般的に剛性を向上させるために傾斜ベッドが使用される。傾斜ベッドは切削時の力状態を改善することができ、断面は閉じた空洞構造を形成することができる。その内部には減衰材として泥芯やコンクリートを充填することができ、振動時の相対摩耗によって振動エネルギーを消散させる。
(2)コラム
マシニングセンタのコラムは、主に主軸箱を支持し、主軸のZ軸移動を収容する。コラムは剛性と熱安定性に優れていなければならない。マシニングセンタでは、コラムの曲げやねじりに対する耐性を向上させるため、内部に傾斜板を配置した密閉箱型構造を採用している。構造全体は鋳造によって実現される。
(3) ガイド
ほとんどのマシニングセンタは、リニアローリングガイドを使用しています。ローリングガイドは摩擦係数が非常に低く、静摩擦係数と動摩擦係数の差が小さい。這うことなくスムーズな低速移動を実現し、高い位置決め精度を実現します。
しかし、この精度を達成するには、ベースが正しい状態でなければならない。そうでなければ、垂直方向の支持高さの誤差が構造的な横方向の歪みを引き起こし、移動範囲全体にわたって摩擦抵抗が変化し、位置決め精度の誤差が生じることになる。
従来、スライドガイドを使用する場合、ガイドの合わせ面を削って微調整する必要があった。組み立て時にガイドの歪みを検出し、調整によって修正することができた。ローリングガイドの場合、修正工程がないため、取り付けによるベッドの歪みやトラックの歪みを避けることが難しい。そのため、3点支持ベースを使用する必要がある。
3.サーボシステム
(1) スピンドルサーボシステム
CNC技術の発展に伴い、最新のCNC工作機械は、主軸変速機に対する要求がますます高くなっている。例えば、広い範囲で連続的に調整可能な回転数、広い範囲の定電力、4象限駆動能力などが要求される。マシニングセンタの自動工具交換や特定の加工技術のニーズを満たすためには、主軸の高精度な姿勢制御が必要である。
一つは歯車分割式無段変速のスピンドルモーターで、もう一つは同期歯付ベルトまたは伝動ベルトを介してスピンドルを駆動するスピンドルモーターである。後者のタイプのスピンドルモーターは、ワイドレンジモーターまたは重切削モーターとも呼ばれ、一定出力の範囲が広いことが特徴である。
主軸の方向制御は、機械的方向制御と電気的方向制御に分けられる。現在、国内外の中級機から高級機までのCNCシステムは、すべて電気的配向制御を採用している。
1) DCスピンドル駆動方式。
DCスピンドルドライブでは、サイリスタ速度制御方式が多用される。DCフィードサーボ方式は、DCスピンドルモータの電機子電圧を制御する速度ループと電流ループからなる2重ループ制御方式である。スピンドルモーターは、励磁巻線と電機子巻線が独立した個別励磁モーターを使用しています。
モータ速度の最小値から定格値まで、励磁電流は一定のままであり、定トルク制御に属する電圧制御速度制御を実現します。定格値から最大値まで、励磁電流は減少し、磁束制御速度制御を実現し、定電力制御に属します。
2) ACスピンドル駆動方式。
交流速度制御技術の発展に伴い、CNC工作機械の主軸駆動装置には、周波数変換器を用いた主軸モータの制御方式が多く採用されるようになった。パワーグリッド側のインバータは、6個のサイリスタからなる三相ブリッジ完全制御整流回路で構成されている。この回路は整流状態で動作し、中間回路に直接電力を供給することができ、またインバータ状態でも動作し、パワーグリッドへのエネルギーフィードバックのタスクを完了することができます。
負荷側インバータは、逆並列フリーホイールダイオードを備えた6個のパワートランジスタで構成されている。磁界コンピュータの制御により、負荷側インバータは三相正弦波パルス幅変調(PWM)電圧を出力し、モータが必要なトルク電流と励磁電流を得ることを可能にする。
出力三相PWM電圧振幅範囲は0~430Vで、周波数調整範囲は0~300Hzです。回生制動時、モータエネルギーはコンバータの6つのフリーホイールダイオードを介してコンデンサを充電する。コンデンサの電圧が600Vを超えると、レギュレータとグリッド側インバータの制御により、コンデンサのエネルギーが電力網に戻されます。
(2) フィードサーボシステム
1) パルス幅変調フィードサーボシステム。
パルス幅変調速度制御方式は、パルス幅変調器を用いてハイパワートランジスタのスイッチング時間を制御する方式である。速度制御信号を一定周波数の矩形波電圧に変換し、DCサーボモータの電機子端子に印加する。矩形波の幅を制御することで、電機子端子の平均電圧を変化させ、サーボモータの速度制御の目的を達成する。
CNCシステムのCPUは、補間器を通して一連のパルス信号を出力する。これらのパルスは、指令乗算器CMRを通過した後、位置フィードバックパルスと比較される。結果の差は誤差レジスタに送られ、位置ゲイン補正とオフセット補正で計算され、パルス幅変調のためにPWMに送られる。その後、D/Aまたはアナログ電圧に変換され、速度制御信号VCMDとして速度制御ユニットに送られます。
パルスエンコーダからのパルスは、断線検出器によって信号が断線していないことが確認された後、位相検出器に送られ、2つのパルス群PAとPBを調べることによってモータの回転方向を決定する。
位相検出器からの一方の信号はF/V変換を受けて速度フィードバック信号TSAとなり、もう一方の出力は検出乗算器DMRを通過して位置フィードバック信号となる。基準点カウンタと1回転信号PCは、グリッド方式の基準点復帰動作に使用されます。
2) ACフィードドライブサーボシステム。
DCフィードサーボシステムは優れた速度調整機能を持つが、使用されるモーターは摩耗しやすいブラシと整流子を持つ。また、整流時に発生するスパークがモータの最高回転数を制限する。
さらに、DCモーターは構造が複雑で製造が難しく、銅や鉄の材料を大量に消費し、製造コストが高い。しかし、ACモーターにはこのような欠点はない。
過去20年間で、新しいハイパワー電子デバイスの出現、新しい周波数変換技術のブレークスルー、現代的な制御理論、実用的なアプリケーションにおけるマイコンデジタル制御技術は、ACフィードサーボ技術の急速な発展を促進した。ACフィードサーボシステムは完全にDCフィードサーボシステムに取って代わりました。
ACサーボモーターはAC永久磁石同期モーターを使用しているため、ACフィード駆動装置は本質的に電子整流DCモーター駆動装置である。
4.ツールマガジンと自動工具交換装置
マシニングセンタでは、ツールマガジンを使用した工具交換が主流となっている。ツールマガジンを使用することで、機械は工具を保持するための固定スピンドルを1つ持つだけでよくなり、スピンドルの剛性を向上させるのに有益である。
独立したツールマガジンは、工具の保管容量を大幅に増加させ、機械の機能拡張に有益であり、加工精度に影響を与える様々な要因をより良く切り分けることができる。
ツールマガジンを使用する工具交換は、機械アームを使用するかどうかで2つのカテゴリーに分けることができます:機械アームを使用する工具交換と機械アームを使用しない工具交換です。機械アームを使用する工具交換では、1つの機械アームが完成工具を主軸から取り外し、同時にもう1つの機械アームが待機工具を工具マガジンから取り出します。その後、2つのアームは位置を交換し、工具交換を完了します。
機械アームを使用しない工具交換では、マガジン内の工具はスピンドルと平行に収納され、工具はスピンドルからアクセス可能な位置に配置されます。工具交換中、主軸頭はマガジンの上の工具交換位置に移動します。主軸のZ軸移動を利用して、完成した工具をマガジンの必要な空き位置に挿入する。その後、マガジン内の待機工具が待機位置まで回転する。主軸はZ方向に移動し、マガジンから待機工具を取り出し、主軸に挿入する。
メカニカルアームを使用するシステムは、ツールマガジンの構成、主軸に対する相対位置、ツール数の点で柔軟性が高く、ツール交換時間が短い。メカニカルアームを使用しない方式は、構造はよりシンプルですが、工具交換時間が長くなります。
(1) マシニングセンターの工具マガジンの種類
ツールマガジンには様々な種類があり、マシニングセンターで最も一般的に使用されているのはディスクタイプとチェーンタイプである。
ディスク構造(図5参照)では、工具はスピンドル軸に沿って、放射状に、または斜めに収納することができる。工具の軸方向設置は最もコンパクトであるが、工具交換をスピンドルに合わせるために、マガジンの一部の工具を工具交換位置で90°回転させる必要がある。
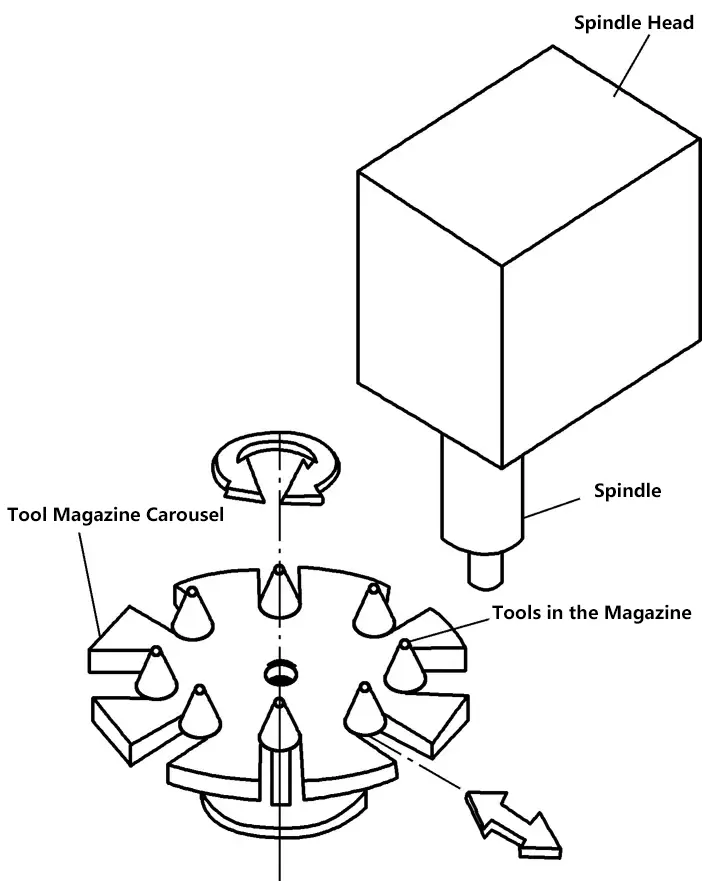
大容量のツールマガジンを使用する場合、コンパクトな構造を維持しながら収納・取り出しが容易なドラム式構造を採用することができる。現在、多くのツールマガジンは、マシンコラムの上部または側面に設置されており、ツールマガジンの回転による振動を隔離するために、別の土台に設置されているものもある。
チェーン式ツールマガジンの基本構造を図6に示す。通常、ディスク式マガジンに比べて工具容量が大きく、フレキシブルな構造になっている。工具マガジンの容量は、チェーンを延長することで増やすことができ、またチェーンを折り畳んだり巻き戻したりすることで、スペースの利用率を向上させることができる。非常に大きな工具容量が必要な場合は、複数のチェーン構造を採用することもできる。
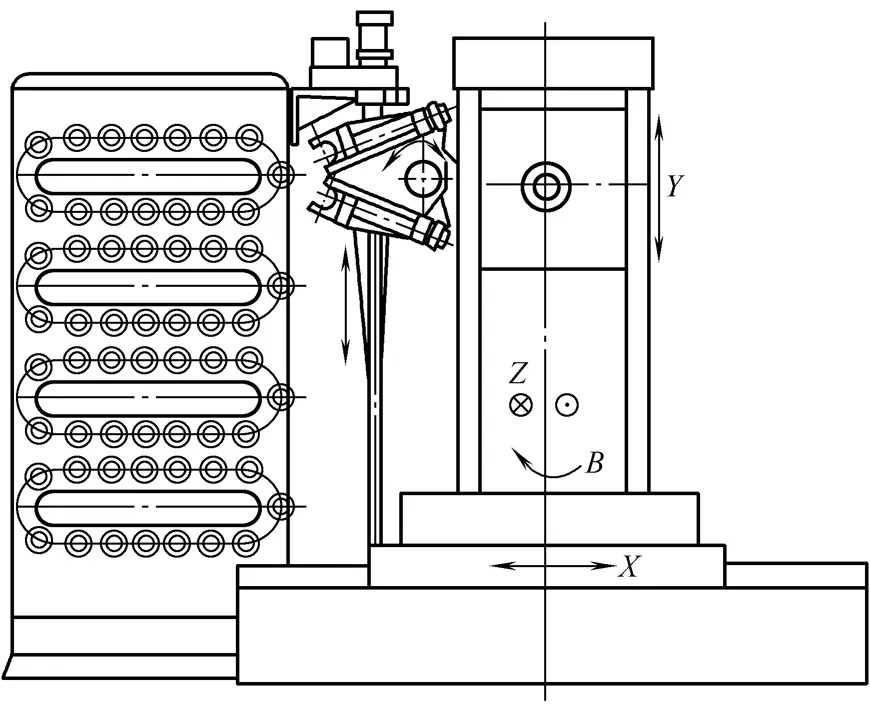
(2) マシニングセンター用自動工具交換装置
自動工具交換装置は、タレット式、180°回転式、回転挿入式、2軸回転式、主軸直結式の5つの基本形式に分けられる。自動工具交換用の工具は専用の工具ホルダーに固定することができ、工具を交換するたびに工具ホルダーを主軸に直接挿入する。
1) タレット式ツールチェンジャー。
工具交換にタレットを使用するのは、自動工具交換の最も初期の形態である。図7に示すように、タレットはフライス盤のパワーヘッド(スピンドルボックス)に接続された複数のスピンドルで構成されている。プログラムを実行する前に、工具がスピンドルに取り付けられ、特定の工具が必要になると、タレットが対応する位置まで回転する。
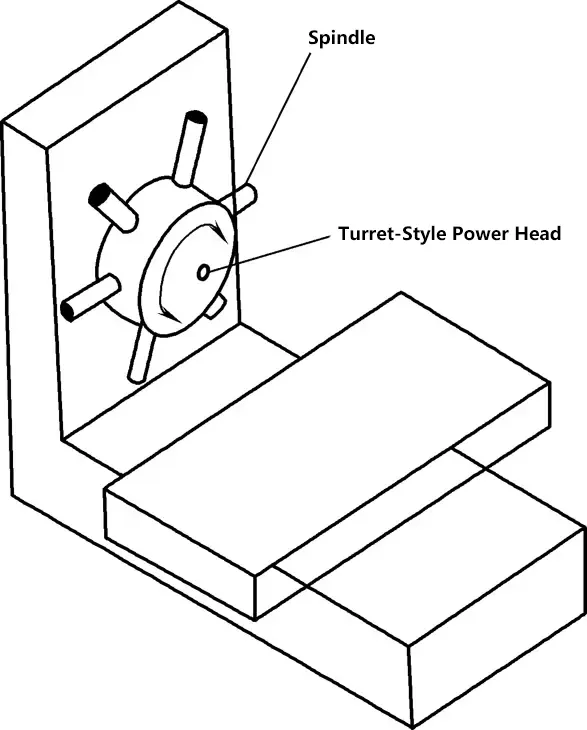
この装置の欠点は、スピンドルの数に制限があることである。スピンドル数以上の工具を使用する場合、作業者は使用済みの工具を取り外し、次のプログラムに必要な工具を取り付けなければならない。タレット式の工具交換は、工具を分解するのではなく、工具と工具ホルダーを一緒に交換するため、工具交換のスピードが速い。現在もNCボール盤などでは、タレット式の工具マガジンが使われている。
2) 180°回転式ツールチェンジャー。
最も単純な工具交換装置は、図8に示すような180°回転タイプの工具交換装置である。
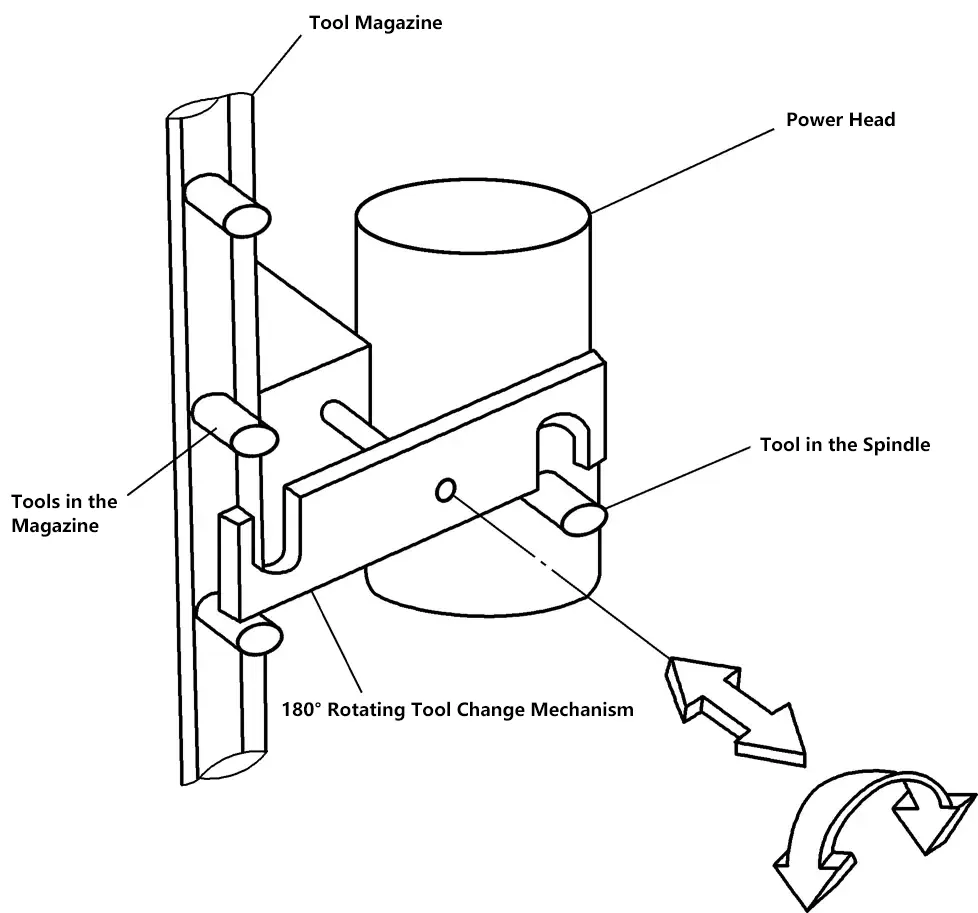
工具交換コマンドを受信すると、機械制御システムは主軸を指定された工具交換位置に移動させ、同時に工具マガジンは適切な位置に移動し、工具交換装置は主軸と工具マガジン内の工具の両方に回転して係合する。
ドローバーは主軸から工具を離し、ツールチェンジャーはそれぞれの位置から工具を取り外す。ツールチェンジャーは180°回転し、主軸工具とツールマガジン工具を取り外す。
ツールチェンジャーが回転すると、ツールマガジンはスピンドルから取り外した工具を受け取るためにその位置を再調整する。次に、ツールチェンジャーは新しい工具をスピンドルに取り付け、取り外した工具をツールマガジンに取り付ける。
この時点で工具交換は完了し、プログラムは引き続き実行される。このツールチェンジャーの主な利点は、構造がシンプルで、動作が少なく、工具交換が速いことである。主な欠点は、工具を主軸と平行な平面に収納しなければならないこと、サイドマウントやリアマウントのツールマガジンに比べて、切りくずや切削液がツールホルダー内に入りやすいため、工具の追加保護が必要なことである。
ツールホルダのテーパ面に付着した切り屑は、工具交換ミスの原因となり、ツールホルダやスピンドルを損傷する可能性さえあります。マシニングセンタの中には、トランスファーバーを使用し、ツールマガジンをサイドに配置するものもあります。
ツールチェンジコマンドが呼び出されると、トランスファーバーはツールマガジンからツールを取り出し、機械の前面に回転し、ツールチェンジャーと噛み合うように位置決めする。180°回転タイプのツールチェンジャーは、横型機にも縦型機にも使用できる。
3) 回転挿入式ツールチェンジャー。
これは最も一般的に使用される形式の一つで、ロータリー式ツールチェンジャーの改良版である。回転挿入機構は、工具交換装置とトランスファーバーを組み合わせたものである。図9に、横型マシニングセンターに適用される回転挿入式工具交換装置の動作原理を示す。この工具交換装置の構造設計は、180°回転式工具交換装置と基本的に同じである。
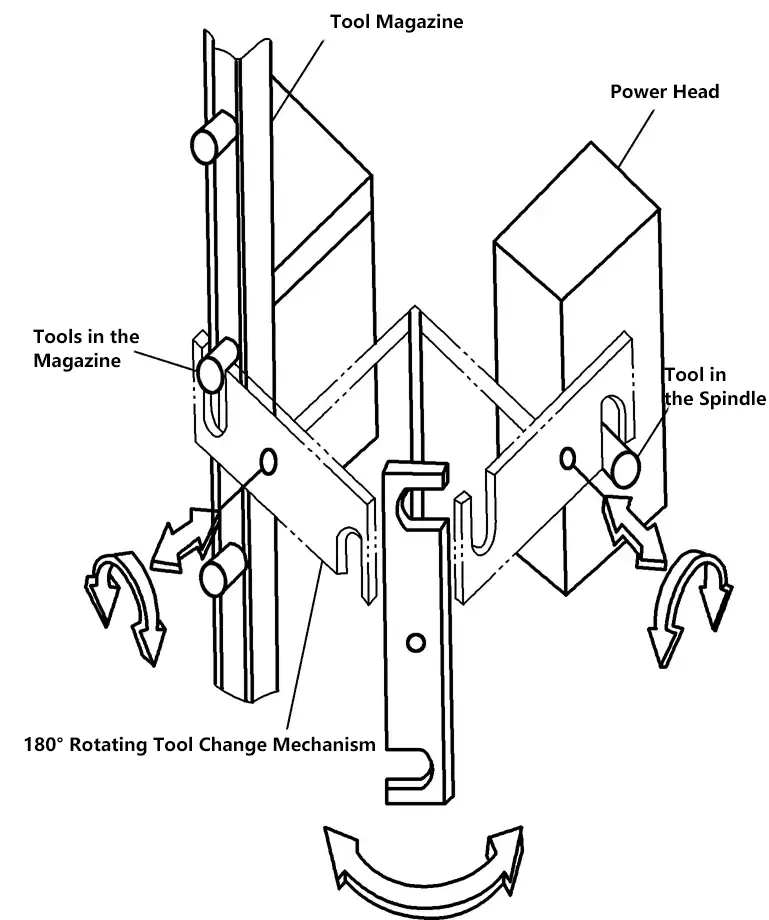
工具交換コマンドを受信すると、主軸が工具交換ポイントまで移動し、工具マガジンが適切な位置まで回転し、工具交換装置がそのスロットから目的の工具を取り出すことができる。工具交換装置が回転し、機械の側面にある工具マガジンから工具を取り出すと、工具交換装置は機械の前面まで回転し、そこで主軸から工具を取り外し、180°回転して新しい工具を主軸に取り付ける。
一方、工具マガジンは、主軸から取り外された工具を受け取る適切な位置に移動し、工具交換装置は機械の側方に回転し、主軸から取り外された工具を工具マガジンのスロットに入れる。
この装置の主な利点は、工具が機械の側面に収納されるため、切り屑がスピンドルやツールホルダーを傷つける可能性がないことです。180°回転タイプの工具交換装置と比較すると、工具交換時の動作が多くなり、工具交換時間が長くなるという欠点がある。
4) 2軸回転式ツールチェンジャー。
図 10 に、2 軸回転式工具交換装置の動作原理を示す。このツールチェンジャは、工具マガジンを横置きまたは後置きにすることができ、その構造上の特徴は立形マシニングセンタに最適である。
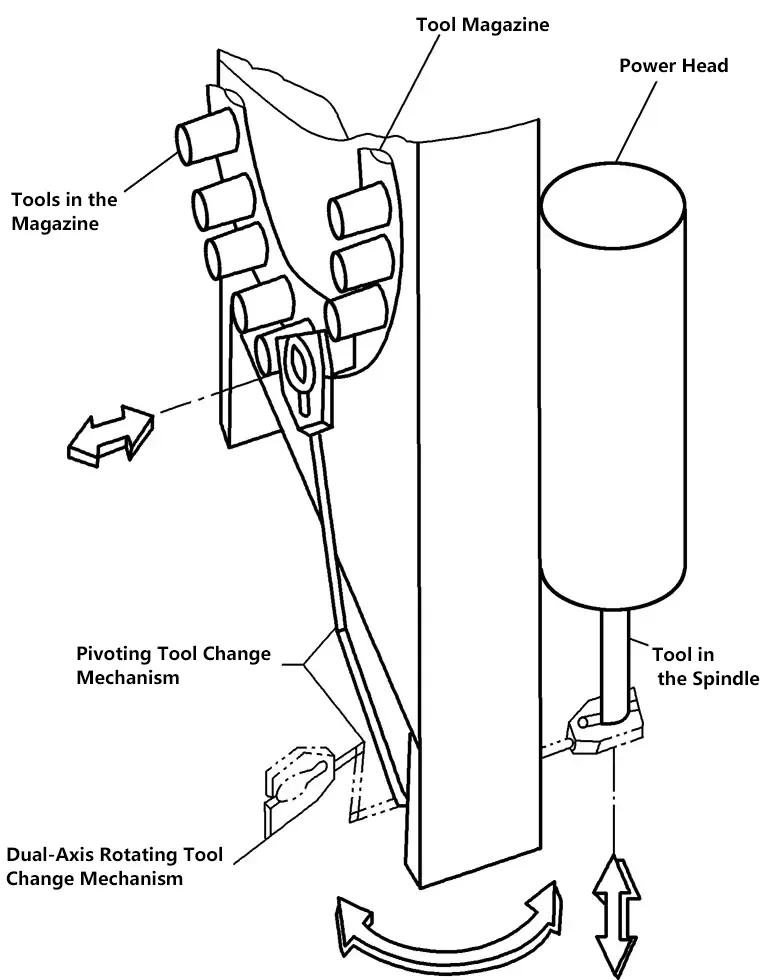
工具交換コマンドを受信すると、工具交換機構は「待機」位置から移動を開始し、主軸内の工具を把持して取り外し、工具マガジンまで回転して工具を工具マガジンに戻し、工具マガジンから目的の工具を取り出し、主軸に向かって回転して工具を主軸に取り付け、最後に「待機」位置に戻って工具交換を完了する。
この装置の主な利点は、ツール・マガジンが機械の側面または後部にあり、工具を最大限に保護できることである。欠点は、工具の移動や移動が多くなることである。立形マシニングセンタのこの装置は、180°回転タイプやダイレクトスピンドルタイプのツールチェンジャーに徐々に取って代わられました。
5)ダイレクトスピンドル式ツールチェンジャー
ダイレクトスピンドル式工具交換装置は、他の形式の工具交換装置とは異なる。この装置では、工具マガジンが主軸位置に直接移動するか、主軸が工具マガジンに直接移動する。図11に、横形マシニングセンタにおけるダイレクトスピンドル式工具交換装置の適用例を示す。
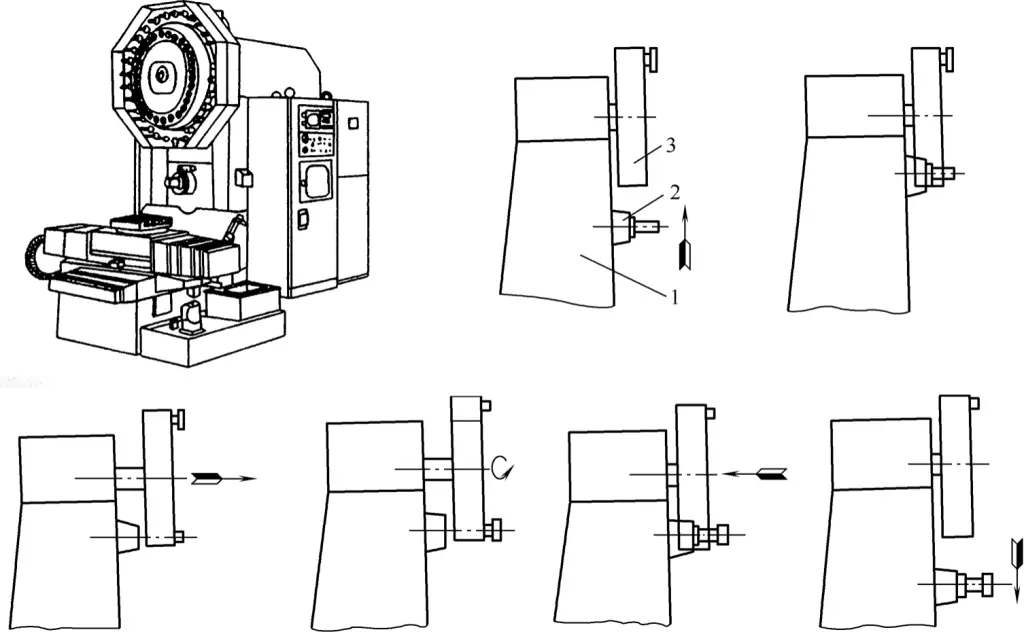
1-メインカラム
2スピンドルボックス
3ツールマガジン
工具交換時には、主軸が工具交換位置まで移動し、ディスク式工具マガジンが必要な工具スロットの位置まで回転し、主軸に装着された工具ホルダと噛み合いながら、工具を「待機」位置から工具交換位置まで移動させる。
ドローバーがツールホルダーから後退し、ツールマガジンが前方に移動して工具を取り外し、次にツールマガジンが回転して必要な工具をスピンドルに合わせ、後方に移動して工具をスピンドルに挿入して固定し、最後にツールマガジンがスピンドルから離れ、上方に移動して「待機」位置に戻り、工具交換が完了する。
立形マシニングセンタの場合、小型のものはツールマガジンを移動させることで工具交換を行うのが一般的だが、一部の大型機では、工具交換工程が上記とは異なり、ツールマガジンが大きすぎて便利に移動できないため、主軸を移動させて工具の脱着を行うか、ロボットアームを使用して工具交換を行う。
図12はロボットアームとグリッパーの構造を示し、図13はロボットツール交換の作業工程を示す。
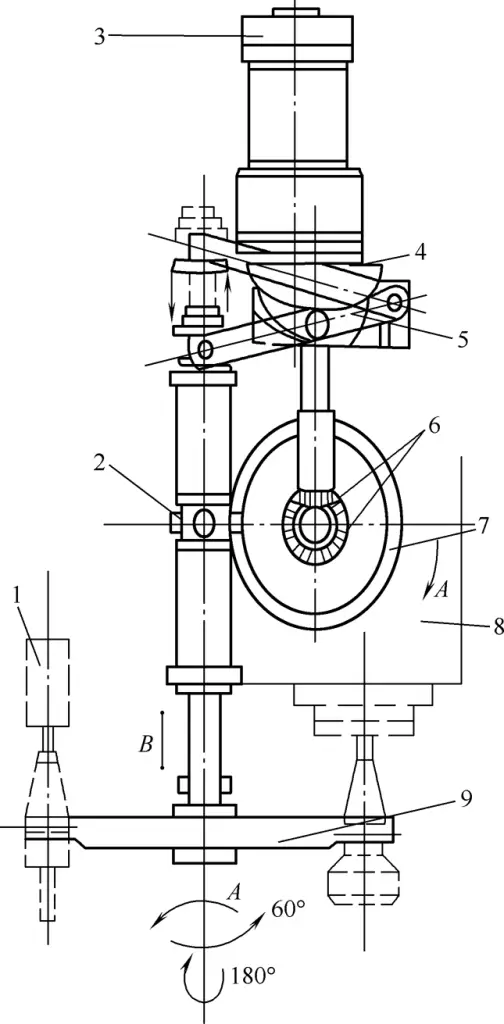
1-ツールホルダー
2-クロスシャフト
3モーター
4-円筒形スロットカム(アーム上下式)
5-レバー
6段ギア
7カムローラー(アーム回転)
8スピンドルボックス
9-ツールチェンジアーム
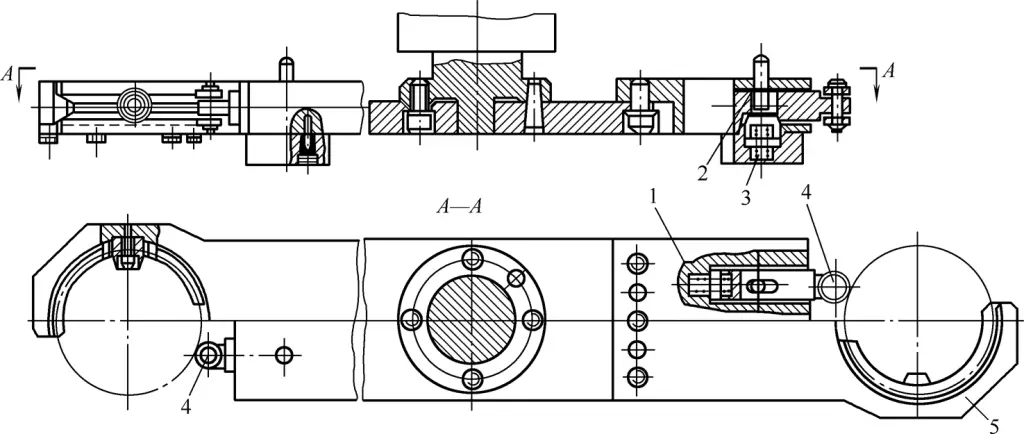
1,3-スプリング
2-ロックピン
4-アクティブ・ピン
5-グリッパー
V.CNCシステムの主な機能
マシニングセンタ用CNCシステムの機能は、CNCフライス盤と多くの類似点があるが、マシニングセンタ用に構成されたCNCシステムは、CNCフライス盤と比較して、より豊富で包括的な機能とコマンドを持っている。
マシニングセンタに搭載されるCNCシステムは、メーカーによってさまざまだが、基本的な機能はほぼ同じ。マシニングセンタでは、ファナック製やシーメンス製が広く使われている。これらのマシニングセンタは、工具交換を除けば、基本的にCNCフライス盤と同じプログラミングと操作が可能である。
CNCシステムの機能には、一般に基本機能とオプション機能がある。基本機能とは、CNCシステムに必要不可欠な機能であり、オプション機能とは、ユーザーが機械の特性や目的に応じて選択する機能である。CNCシステムによって機能は異なる。以下にファナックシステムを例にいくつかの機能を簡単に説明する。
1.マルチ座標制御機能
制御システムが制御できる座標軸の数は、CNCシステムが制御できる座標軸の最大数を指し、直線軸と回転軸を含む。基本的な直線座標軸はX軸、Y軸、Z軸であり、基本的な回転座標軸はA軸、B軸、C軸である。同時軸数とは、加工要求に応じてCNCシステムが制御して同時に動かすことができる座標軸の数を指す。
制御機能とは、CNC装置が制御でき、同時に制御できる軸の数を指す。制御機能はCNC装置の主な性能指標の一つである。
制御軸には、移動軸と回転軸、基本軸と追加軸がある。制御できる軸が多ければ多いほど、特に同時に制御できる軸が多ければ多いほど、CNC装置の機能は強くなり、CNC装置は複雑になり、プログラミングは難しくなる。
2.工具補正機能
工具補正機能には、工具長補正と工具半径補正がある。工具長補正はさらに、工具形状補正と工具摩耗補正を含む。
(1) 工具長補正機能
工具長補正とは工具の軸方向補正のことで、実際の工具の軸方向の位置を、プログラムされた値と比較してオフセット値だけ増減させます。この機能は、切削面の高さを自動的に変更するだけでなく、軸方向の工具設定誤差を低減します。
(2) 工具摩耗補正機能
工具は使用中に摩耗するため、工具摩耗補正が適時に行われないと、ワークの加工精度の低下につながります。工具形状補正はそのままに、工具摩耗補正を調整することで、間接的に工具長補正を修正し、ワークの加工精度を確保します。
(3) 工具半径補正機能
この機能を使用すると、工具中心がワークの輪郭から自動的に工具半径1つ分オフセットされるため、プログラミング中にワークの実際の輪郭寸法に従って計算し、プログラミングするのに便利で、フライスカッターの中心軌跡に基づいて計算し、プログラミングする必要はありません。
この機能は、工具半径補正値を変更することで、フライスカッターの製造精度不足を補正し、工具径の選択範囲や工具再研磨の許容誤差を拡大することもできる。
工具半径補正値を変更する方法は、同じ加工プログラムで積層フライス加工や粗加工と微細加工を実現したり、部品の加工精度を向上させたりする場合にも利用できる。さらに、工具半径補正値の正負の符号を変えることで、同じ加工プログラムで、合わせる必要のあるワーク同士を加工することもできる。
3.固定サイクル機能
固定サイクルとは、あらかじめプログラムされた一連の典型的な加工操作をメモリに保存したもので、必要なときにGコードを使用して呼び出すことができます。固定サイクル機能を使用することで、プログラムの準備を大幅に簡素化することができます。固定サイクルには、穴あけサイクル、中ぐりサイクル、ねじ切りサイクルなどがあります。
4.ミラー加工機能
ミラー加工は軸対称加工とも呼ばれる。座標軸に対して対称なワークの場合、ミラー加工機能を使用すると、プログラムの1象限または2象限を記述するだけで、他の象限の輪郭をミラー加工で実現することができる。
5.回転機能
この機能は、プログラムされた加工プログラムを加工面内で任意の角度だけ回転させて実行することができる。
6.サブプログラム
加工部品によっては、幾何学的に同一の加工経路が現れることが多く、加工プログラムを記述する際に、固定されたシーケンスや繰り返しパターンを持つプログラムセグメントが複数のプログラムに現れることがある。
プログラミングを簡単にするため、固定シーケンスや繰り返しパターンを持つこれらの典型的な加工プログラムセグメントは、一定のフォーマットでサブプログラムとしてプログラムし、メモリに入力することができる。
メイン・プログラムが実行中に特定のサブプログラムを必要とする場合、特定の形式のサブプログラム・コール命令によってそのサブプログラムを呼び出すことができる。サブプログラムが実行された後、メイン・プログラムに戻り、次のプログラム・セグメントを実行し続ける。
7.マクロプログラム機能
ユーザマクロとは、変数を含むサブプログラムのことである。ユーザーマクロプログラムは、変数、算術演算、論理演算、条件転送を使用することができ、同じ加工動作のプログラムをより便利に、より簡単に記述することができる。加工プログラムでは、ユーザマクロ命令という簡単な命令でユーザマクロプログラムを呼び出すことができる。
8.準備機能
Gファンクションとしても知られる準備ファンクションは、CNCフライス盤の動作モードを指定するために使用される。Gファンクション命令は、アドレスコードGの後に2桁の数字が続く。
9.補助機能
補助機能はCNC加工に不可欠な補助操作で、アドレスコードMの後に任意の2桁の数字が続くことで表される。システムによって、Mファンクションが異なる場合があります。補助ファンクションは、スピンドルのスタート/ストップ、切削油剤のオン/オフなどを指定するために使用されます。
10.フィード機能
Fファンクションとしても知られる送りファンクションは、送り速度を表し、アドレスコードFの後に数桁の数字が続きます。実際の送り速度は、CNC操作パネルの送り速度オーバーライドノブで調整できます。
11.スピンドル機能
マシニングセンタの主軸機能とは、主に主軸回転数(工具回転数)を指定することです。 切断速度)を加工することができます。スピンドル機能は、アドレスコード S の後に数桁の数字が続き、単位は r/min です。例えば、S1000 はスピンドル速度が 1000 r/min であることを示します。
12.グラフィック表示機能
CNC装置は、モノクロまたはカラーCRTを装備することができ、ソフトウェアとインターフェイスを介して文字やグラフィック表示を実装しています。加工プログラム、パラメータ、各種補正値、座標位置、アラーム情報、動的工具運動軌跡などを表示できる。
13.運転制御機能
マシニングセンターは通常、シングルブロック操作、ドライラン、スキップ、マシンロック、グラフィックシミュレーションラン、緊急停止などの機能を備えている。
14.自己診断アラーム機能
自己診断アラーム機能とは、CNCシステムがソフトウェアとハードウェアの故障を自己診断する機能を指す。この機能を利用して、工作機械全体と加工プロセス全体が正常かどうかを監視し、異常が発生した場合には速やかにアラームを発することができるため、故障の種類と場所を迅速に特定し、故障によるダウンタイムを短縮することができる。
15.通信機能
最新のCNCシステムは、一般的にRS232CインターフェイスまたはDNCインターフェイスを装備しており、上位コンピュータとの高速信号伝送が可能です。ハイエンドCNCシステムは、FMS(フレキシブル製造システム)やCIMS(コンピュータ統合製造システム)の要件を満たすために、インターネットに接続することもできます。
VI.CNC技術の発展と方向性
1.CNCシステムの開発プロセス
CNC工作機械は、最初にアメリカで生まれた。1952年に世界初のCNC三次元中ぐりフライス盤が登場して以来、CNCシステムは2段階、6世代の発展を遂げてきた(表1参照)。
第一世代のCNCシステムは真空管部品を使用しており、サイズが大きく、信頼性が低く、価格も高かった。主に軍需産業で使用され、生産量も少なく、広く適用されることはなかった。
第2世代は1961年に登場し、トランジスタベースのCNCシステムで構成され、信頼性が向上し、サイズが大幅に縮小された。
第3世代は、1965年に製品化された集積回路CNCシステムで、CNC装置のサイズを大幅に縮小し、信頼性を大幅に向上させ、一般ユーザーにも受け入れられるようになった。CNC工作機械は、生産量、種類ともに大きく発展した。
上記の3世代のCNCシステムは、基本的に特殊なコンピュータであり、主にハードウェアに依存して様々な制御機能を実現していた。これは数値制御(NC)システムと呼ばれる第一段階であった。
1968年、ミニコンピュータがCNCシステムに適用され、CNCシステムの第4世代となった。1974年のマイクロプロセッサの応用は、CNCシステムの第5世代となった。1990年、PCプラットフォームをベースとしたオープンCNCシステムが第6世代のCNCシステムとなった。
後者の3世代は、コンピュータ数値制御(CNC)システムと呼ばれる第2段階に属する。
表1 CNCシステム開発の6世代
CNCシステム開発の歴史 | 世界的台頭の年 | 中国での出現年 | |
ファーストステージ(NCシステム) | 第一世代真空管CNCシステム 第2世代トランジスタCNCシステム 第3世代集積回路CNCシステム | 1952 1961 1965 | 1958 1964 1972 |
第2ステージ(CNCシステム) | 第4世代ミニコンピュータCNCシステム 第5世代マイクロプロセッサーCNCシステム 産業用)PCプラットフォームをベースとした第6世代のオープンCNCシステム | 1968 1974 1990 | 1978 1981 1992 |
2.CNC技術の開発動向
現在、中国には独立した知的財産権を持つCNCシステムがあるが、完全に機能するCNC工作機械の大部分は、依然として外国のCNCシステムを使用している。工作機械全体から見ると、信頼性、精度、自動化レベル、生産効率の面で、外国製と比較してまだかなりの開きがある。
科学技術の発展と世界的な先端製造技術の台頭により、CNC加工技術に対する要求はますます高くなっている。超高速切削加工や超精密加工などの関連技術の発展に伴い、CNC工作機械の工作機械構造、主軸駆動装置、CNCシステム、サーボシステムなどには、より高い性能指標が求められるようになり、CNC工作機械技術には次の7つの発展傾向が見られる。
(1) 高精度
CNC工作機械の高精度には、工作機械の高い幾何学精度と高い加工精度が含まれる。高い幾何学的精度は、加工精度を向上させる基礎となる。幾何学精度の中で最も重要なのは位置決め精度である。位置決め精度の向上は、機械の構造特性や熱安定性の向上とともに、CNC工作機械の加工精度を大きく向上させている。
例えばマシニングセンタの加工精度は、従来の±0.01mmから±0.005mm、あるいはそれ以上に向上している。より高い精度目標を達成するために、主に次のような対策が採られている:
1) サーボドライブシステム。
デジタルACサーボシステムの採用により、従来のアナログDCサーボシステムに比べ、位置決め精度や送り速度などのサーボ性能が大幅に向上した。工作機械のテーブルを直接駆動するリニアモーターを用いた、いわゆる「伝達ゼロ」のリニアサーボ送り方式も登場し、加工精度が大幅に向上している。
2)フィードフォワード制御技術。
従来のサーボシステムでは、指令位置と実際の位置の偏差に位置ループゲインを掛け合わせ、その積を速度指令としてモータの回転数を制御していた。この方式では、常に位置追従の遅れ誤差が発生し、コーナーや円弧の加工時に加工条件が悪化していた。
いわゆるフィードフォワード制御は、本来の制御方式に速度指令制御方式を加えることで、追従遅れ誤差を大幅に低減し、コーナーカットの加工精度を向上させる。
3) 工作機械の動摩擦・静摩擦に対する非線形補償制御技術
工作機械における動摩擦と静摩擦の非線形性は、サドルクローリングの原因となる。新しいデジタルサーボシステムは、機械構造の静止摩擦を低減する対策に加えて、機械システムの動摩擦と静止摩擦の非線形性を自動的に補正する制御機能を備えている。
4) 補償技術の開発と普及。
最近のCNC工作機械は、コンピュータ数値制御システムのソフトウェア補正機能を使用して、軸運動定点誤差補正、リードスクリューピッチ誤差補正、バックラッシ補正、熱変形補正など、サーボシステム上でさまざまな補正を行っている。
5)高精度パルス相当。
高精度のパルス等価により、位置決め精度と再現性を向上させることができる。
6)高分解能位置検出装置の採用。
例えば高分解能パルスエンコーダ、マイクロプロセッサ内蔵の細分化回路、これにより分解能が大幅に向上。
(2) 高速
生産効率の向上は、常に工作機械技術開発の目標の一つであった。CNC工作機械の出現と急速な発展は、従来の工作機械に比べて生産効率がはるかに高いことも一因である。
近年、CNC工作機械の生産効率は、主に切削時間と非切削補助時間の短縮によって著しく向上している。切削時間の短縮は、切削速度の向上、すなわち主軸回転速度の向上によって達成される。
マシニングセンタの主軸回転速度は、10年前の4000~6000r/minから現在の8000~12000r/minに上昇し、最高速度は100000r/minを超えた。CNC旋盤の主軸回転速度も5000~20000r/minに、研削砥石の線速も100~200m/sに向上している。
最新の統計によると、マシニングセンタの切削時間は全作業時間の55%を超えない。したがって、非切削時間を短縮することは、生産効率を向上させる主要な手段である。非切削時間は2つの部分から構成される。1つは急速移動に必要な時間である急速移動時間、もう1つは補助時間であり、主に工具交換時間とワーク交換時間である。
早送り時間を短縮するには、早送り速度を上げる必要がある。現在、一般的な早送り速度は20~24m/minに達しており、30m/min前後のものもある。
特に直動送りサーボモータの登場により、さらなる高速化の可能性が出てきた。また、補助動作の時間を短縮するためには、自動工具交換や自動ワーク交換の時間を短縮する必要がある。
現在、CNC旋盤のタレット回転時間は0.4~0.6秒に達し、マシニングセンタの自動工具交換時間は約3秒に達し、最速は1秒以内に達する。マシニングセンタのパレット交換時間は従来の12~20秒から6~10秒に短縮され、最速では2.5秒に達する。
現在、速度指標を改善するために、主に以下のような観点から対策が講じられている:
1) CNCシステム。
マイクロプロセッサーは、現代のCNCシステムの中核をなすコンポーネントである。システムの基本的な計算速度を向上させるために、より高いビットと周波数のマイクロプロセッサーが使用されている。現在、16ビットCPUから32ビットCPUに移行し、64ビットCPUに向けて発展している。32ビットマイクロプロセッサとマルチプロセッサ構造は、システムのデータ処理能力を向上させるため、すなわち補間計算の速度と精度を向上させるために採用されている。
2) 高速で強力な内蔵PLCを構成する。
PLCの動作速度を向上させることで、CNC工作機械の高速加工の要件を満たす。新しいPLCは専用CPUを持ち、基本命令実行速度はμs/ステップに達し、プログラム可能なステップは16,000ステップ以上に拡張できる。PLCの高速処理機能を活用することで、CNCとPLCの有機的な結合が可能となり、CNC工作機械運転中の様々なリアルタイム制御の要求に応えることができる。
3) 多軸制御レベルの向上。
新しいCNCシステムはすべて多軸制御機能を備えており、多軸リンクを使用して複雑で特殊なサーフェスの加工を実現し、マルチタレット制御による多工具同時加工を採用することもできる。
4)超高速切削工具の応用。
現在、ダイヤモンドコーティング工具やセラミック工具が超高速加工に応用されている。
(3) 高い自動化
CNCシステムがマイクロプロセッサー・ベースのCNCシステムに発展した後、システムの機能は絶えず拡張され、その結果、CNC工作機械の自動化レベルも絶えず向上してきた。
自動工具交換、自動ワーク交換に加え、工具寿命管理、スペア工具の自動交換、自動工具寸法測定・補正、自動ワーク寸法測定・補正、切削パラメータ自動調整などの機能が次々と登場し、単能機の自動化は非常に高いレベルに達している。工具の摩耗や破損の監視機能も絶えず改善されている。
(4) 高い信頼性
CNC工作機械の動作信頼性は、主にCNCシステムと各種サーボシステムの信頼性に依存する。現在、信頼性向上のために主に次のような対策が採られている:
1) CNCシステムのハードウェア品質を向上させる。
より集積度の高い回路チップを選択し、部品の厳格なスクリーニング、安定した製品製造、総合的な性能テストを確立し、実施する。
2) モジュール化、標準化、普遍化。
現在、最新のCNCシステムの機能はますます強力になり、システムのハードウェアとソフトウェアの構造は、モジュール化、標準化、普遍化を達成することができるようになり、生産組織、品質管理、ユーザーメンテナンスを容易にしている。
(5) 多機能性
1) CNC工作機械は多機能を採用し、設備の稼働率を向上させる。
多機能化とは、異なる工作機械の機能を一つの工作機械に統合することである。代表的なものは、自動工具交換機構(工具マガジンの容量は100本以上にもなる)を備えた各種マシニングセンタで、フライス加工、中ぐり加工、穴あけ加工、旋盤加工、リーマ加工、タップ加工、さらには研削加工など、複数の加工を1台の工作機械で同時に行うことができる。
作業効率をさらに向上させるため、最新のCNC工作機械(各種五面加工機など)では、多軸・多面加工、つまりワークの異なる部分に対して同時に異なる切削加工を行う方法が採用されている。
さらに、最新のCNCシステムの制御軸数は増加の一途をたどっており、最大31軸に達するものもあり、同時連動軸数は7軸に達している。これらの工作機械は加工精度が高く、作業効率を大幅に向上させ、床面積を節約し、設備台数を削減し、投資を節約することができる。
2)人間と機械の対話機能が優れている。
一台の工作機械で、部品加工とプログラム編集を同時に行うことができる。最新のCNCシステムは、二次元軌跡表示のためにカラーCRTを使用し、より優れたものは、カラー三次元ダイナミックグラフィックシミュレーションを実現することができ、プログラムされたコードの加工軌跡を表示し、部品プログラムのデバッグと修正を容易にし、実際の加工プロセスの安全性を確保する。
3) コミュニケーション機能の強化。
CNC工作機械がスタンドアロンマシンからFMC(フレキシブル・マニュファクチャリング・セル)、FMS(フレキシブル・マニュファクチャリング・システム)へと発展し、さらにネットワーク化されてCIMS(コンピュータ統合製造システム)を形成するようになると、CNCシステムにはより強力な通信機能が求められる。
ほとんどのCNCシステムはRS232CとRS422高速長距離シリアルインターフェースを持ち、ユーザーレベルのフォーマット要求に従って、上位コンピュータと様々なデータを交換することができる。ハイエンドのCNCシステムはDNC(分散型数値制御)インターフェースを持つべきで、複数のCNC工作機械間のデータ通信を実現し、また複数のCNC工作機械を直接制御することができる。
オートメーション技術のさらなる発展に適応し、ますます大規模になる工場オートメーションと、異なるメーカーや種類のCNC工作機械をネットワーク化する必要性の要件を満たすために、最新のCNC工作機械は、MAP(Manufacturing Automation Protocol)産業用制御ネットワークを採用しています。MAPバージョン3.0が実装され、最新のCNC工作機械がFMSとCIMSに参入する条件が整った。
(6) CNCプログラミングの自動化
CAM自動プログラミングは、現在最も先進的なCNC加工プログラミング手法である。
現在、CAD/CAMグラフィック対話型自動プログラミングソフトが広く使われている。これは、CADを使用して部品形状のコンピュータ図面を完成させ、コンピュータ内部のツールパスデータ計算と後処理を経て、NC部品加工プログラムを自動的に生成し、通信インターフェースを介してCNC工作機械に送信し、自動制御処理を行うことで、CAD/CAMの統合を実現し、図面なしで設計と製造を実現する。
また、CIMS技術の発展に伴い、CAD/CAPP(Computer-Aided Process Planning)/CAMを統合した完全自動プログラミング手法も登場している。CAD/CAMシステムのプログラミングとの最大の違いは、プログラミングに必要な加工プロセスパラメータを人間が関与することなく、システム内のCAPPデータベースから直接取得することである。
(7) 知能 現代のCNCシステムは適応制御技術を導入している。
適応制御(AC)技術は、ランダムに変化する加工プロセスにおいて、加工プロセス中に測定された加工状態や特性を自動的に調整し、与えられた評価指標に従って自身の作業パラメータを自動的に修正し、最適な作業状態を達成またはそれに近づけることを必要とする。
適応制御技術により、非常に高い加工精度と小型化を実現することができます。 表面粗さまた、工具の寿命や設備の生産効率も向上する。
CNCシステムのインテリジェンスは、主に以下の側面に反映される:
- 工具寿命の自動検出と交換、ワークピースの公差外れのタイムリーなアラーム、工具の摩耗や破損、スペア工具の自動補正または交換。
- 故障発生時の自動診断と修理
- 加工中の熱変形によるボールねじなどの伸縮をリアルタイムで補正。
- パターン認識技術の導入、画像認識と音声制御技術の応用により、システムが自ら図面を認識し、自然言語命令に従って自動CNC加工を行うことができる。