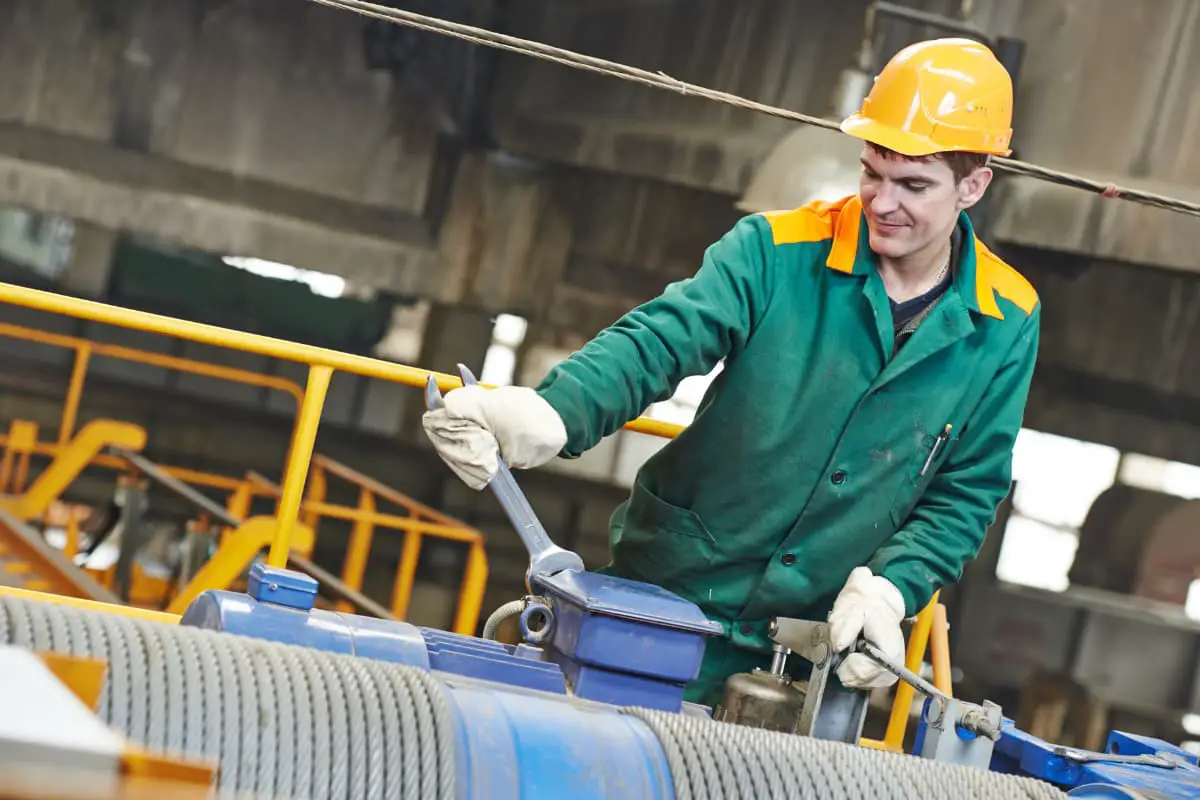
生産設備は、組立フィッターの仕事の道具です。その使い方やメンテナンス方法を知ることで、効果的な活用や長寿命化を図るとともに、人身事故や設備事故を未然に防ぐことができます。
この章では、組立工が使用する一般的な機器の操作手順から始める。まず、ドリルプレス、電動工具、研削盤、クレーン、その他の工具や機器の操作と使用方法を紹介する。これらは習熟すべき基本的な内容である。次に、組立工の一般的な設備の構造、使用方法、メンテナンスについて紹介し、実習で習得することを求めている。科学技術の絶え間ない発展に伴い、設備の高度化・自動化レベルは大幅に向上し、設備メンテナンスの基準も変化していく。
I.組立工が使用する一般的な機器の操作手順
トレーニングの目的組立フィッターが使用する一般的な機器の操作手順を習得する。
1.ドリルプレスの操作手順
(1) 掘削
1) 穴あけ時に手袋を着用することは厳禁である。袖はきつく結び、女性労働者は作業帽を着用すること。作業者は、切屑やドリル・ビットが誤ってそれらに引っ掛かることによる事故を防止するため、綿糸その他の織物または織布を手に持ってはならない。
2) 穴あけ中に手や布切れで切りくずを取り除いたり、口で吹き飛ばしたりしないこと。切りくずの除去には必ずブラシを使用すること。短冊状の切りくずは、フックで折るか、速やかに切断し、機械が停止しているときに取り除くようにする。
3) 運転中は、危険を避けるため、作業者の頭を回転しているスピンドルに近づけすぎないこと。また、逆回転でブレーキをかけないでください。
4) 穴あけ加工では、特に小さなワークピースに大きな直径の穴をあける場合、ワークピースをしっかりとクランプしなければならない。クランプは確実に行ってください。
5) 穴あけ時のドリルビットの切れ味と送り力は適切であること。特に貫通穴をあける場合は、貫通しそうになったら送り力を弱め、急激な送りの増加によるワークの飛び出しなどの事故を防ぐ。
6) 機械の運転中にワークを取り付けたり、取り外したりすることは厳禁です。ワークの点検や主軸回転数の変更は、機械が停止している時に行ってください。
7) ドリルプレスを掃除するときや潤滑油を入れるときは、必ず電源を切ってください。
8) 送り速度の調整は、機械が停止しているときに行ってください。自動送りの場合は、ドリルビットの直径と被削材の種類に応じて送り速度を調整し、トラベルリミットブロックを固定してください。
9) ドリルプレスの作業中、特に動力送りを使用しているときは、移動限界の超過による設備事故を防止するため、オペレータの離席は厳禁である。
10) ドリルビット移行テーパスリーブを取り外すときは、標準的なくさびを使用してください。スピンドルの損傷を防ぐため、ハンマー、鉄棒、その他の不適切な工具でこじることは厳禁です。
11) ラジアル・ドリル・プレスを使用する場合、アームを下降させるときは、ドリル・ビットをワークや作業台から離さなければならない。操作ミスや装置の破損につながる装置の故障やスライディングを防ぐため、作業者は集中して慎重に操作してください。穴あけ中にスピンドルボックスを上下させないでください。
12) 穴あけ径がラジアル・ドリル・プレスの最大限界に近づいた場合は、被加工物をコラム側に近づけ、クランプした状態で作業する。
(2) ワークをクランプする
1) 薄い板や直径8mmを超える小さなワークに穴をあける場合は、ベンチバイスまたは小型のマシンバイスを使用してワークを保持する必要があります。ワークを直接手で持って穴を開けないでください(図1a)。
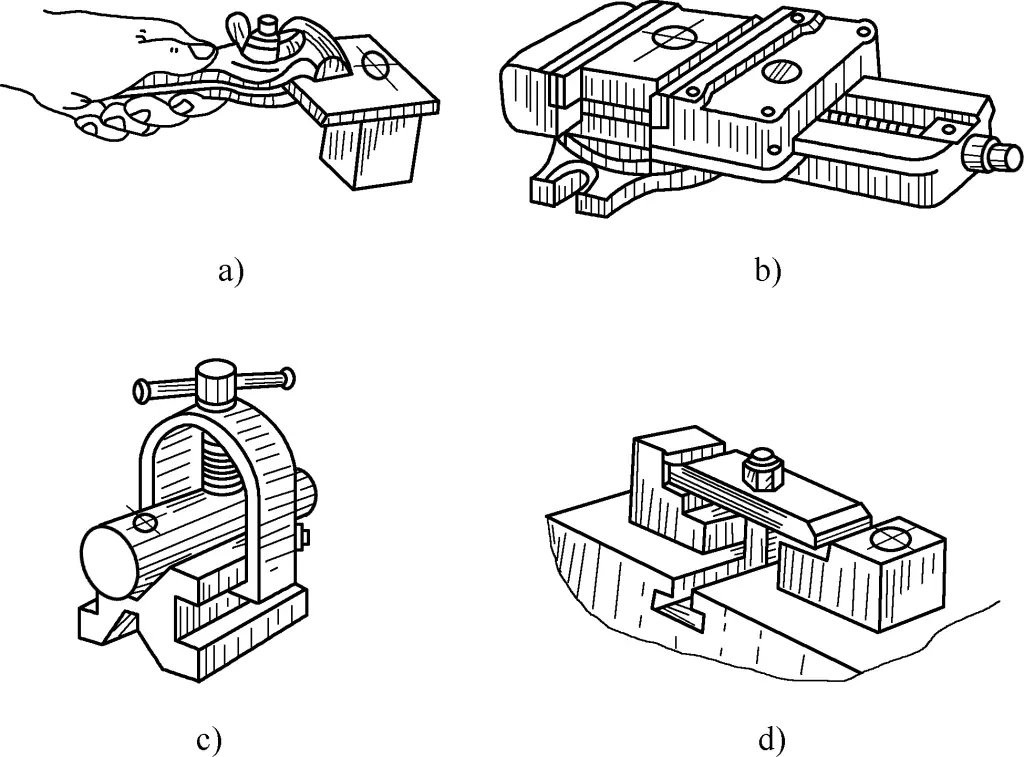
2)長いワークに穴を開ける場合、手で持つこともできるが、ドリルプレスの作業台に固定ネジを追加してワークを支える方が安全で確実である。
3) 平らなワークピースに穴をあける場合、一般にワークをマシンバイスでクランプする(図1b)。クランプするときは、ワークの表面がドリルビットに対して垂直になるようにする。穴あけ径が比較的大きい場合は、マシンバイスをボルトとプレッシャープレートでドリルプレスの作業台に固定する必要があります。貫通穴加工でワークのクランプにマシンバイスを使用する場合は、マシンバイスを傷つけないように、ワークの下にスペーサーを置き、穴あけ部分にスペースを空けてください。
4) 円筒形のワークに穴をあける場合は、ワークが回転しないように、ワークをVブロック(図1c)の上に置く。クランプする際は、ドリルビットの中心線がVブロックの2つの傾斜面の対称面に一致するようにし、ドリル穴の中心線がワークの軸を通るようにします。
5) マシンバイスでクランプするのに不便な大きな穴やワークには、プレッシャープレート、ボルト、スペーサーを使用してドリルプレスの作業台に固定します(図1d)。以下の点に注意してください:
プレッシャー・プレートの曲げ変形を抑えるため、スペーサーはできるだけワークピースに近づけること。
スペーサーは、ワークのクランプ面よりわずかに高く、低くならないようにしてください。そうしないと、ワークをクランプしたとき、プレッシャープレートとワークの間の圧力ポイントがワークの端になります。片方のプレッシャー・プレートのみでワークをクランプすると、ワークが浮き上がります。スペーサーを少し高くすると、プレッシャープレートが多少曲がっても、加圧点がワークの端に来ないようにすることができ、ワークの浮き上がりを防ぐことができる。
ボルトはできるだけワークピースに近づけ、ワークピースにより大きなクランプ力を与え、クランプ中にワークピースが動くのを防ぎます。
ワークのクランプ面が精密加工されている場合は、プレッシャープレートによる圧痕を防ぐため、銅箔などをクッションとして使用してください。切粉の引っ掛かりによる事故を防ぐため、加工面に布などの繊維や織物をクッションとして使用することは厳禁です。
(3) ドリルビットを取り付ける際の注意事項
ストレートシャンクのドリルビットは、ドリルチャックによって保持され、クランプ長さは15mm以上である。テーパーシャンクドリルビットは、シャンクのモールステーパーを利用してドリルプレスのスピンドルスリーブに直接接続します。接続の際は、ドリルビットのテーパーシャンクとスピンドルのテーパー穴をきれいにし、テーパーシャンクの平らな尾をスピンドルの腰型の穴に合わせる必要があります。加速された衝撃力で一気に取り付ける。
ドリルビットのテーパーシャンクがスピンドルのテーパー穴より小さい場合、接続にトランジションスリーブを使用することができます。ドリルビットがドリルプレスのスピンドルにしっかりと接続され、回転中の半径方向の振れ(幾何公差に使用)が最小であることを確認してください。
(4) 穿孔開始後に穿孔位置がずれる場合は修正が必要である。
穴あけ前に、穴のセンター・ポンチ・マークが小さすぎないようにしてください。そうしないと、穴あけ開始時にドリル・ビットのノミ刃がセンター・ポンチ・マークの円錐形の穴に最初に落ちず、穴あけ中にドリル・ビットが中心から外れてしまいます。
穴あけを始めるときは、まずドリルビットを穴の中心に合わせ、浅い円錐形のピットを作り、最初の浅い円錐形のピットとスクライブした円との同心度を目視で確認し、継続的に修正する。穴の位置が大きくずれている場合は、センター・パンチ・マークを反対方向に修正するか、チゼルを使って浅い円錐ピットに数本の溝を作り、この部分の切削抵抗を減らすことで、ドリル・ビットがずれて修正目的を達成できるようにする(図2)。
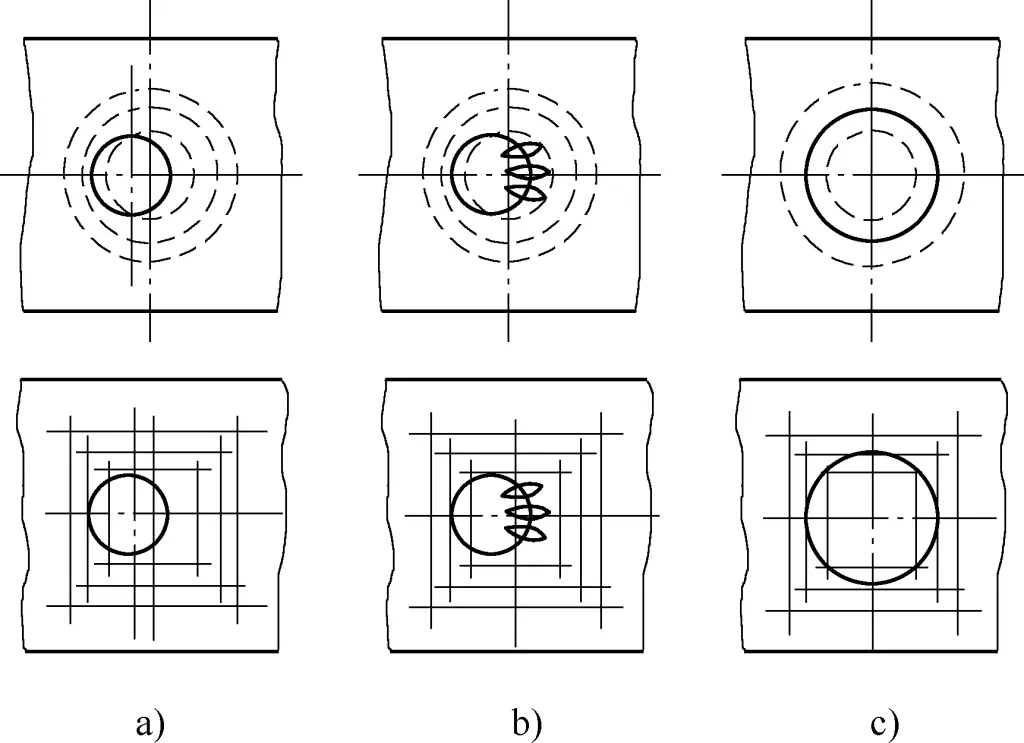
最初の円錐ピットの直径がドリルビットの直径より小さくなる前に、修正プロセスを完了しなければならない。これは穴位置の精度を確保するための重要なステップである。もし、最初の円錐ピットの直径がすでに穴の直径に達しており、穴の位置がまだオフセットしている場合、この時点で修正することは難しく、穴の位置誤差が大きくなり、組立精度に影響します。
手動送りを使用する場合、送り力を大きくし過ぎると、ドリルビットが曲がって変形し(特に細長い穴を加工する場合に顕著)、ドリル穴の軸が斜めになる(図3)。ドリル穴の軸の傾きは、穴の形状、位置精度、組立品質に直接影響する。また、ドリルビットの破損やワークの突き出しを引き起こす危険性もある。
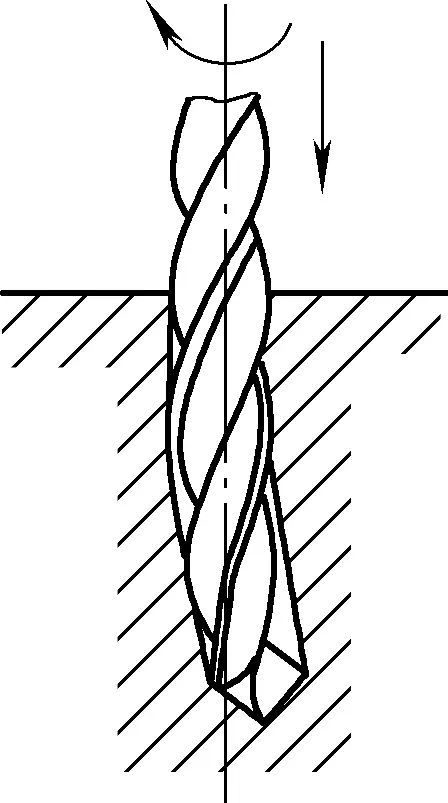
2.手持ち式電気ドリルの操作手順
1) 異なる穴の直径に基づいて適切なハンドヘルド電気ドリルを選択し、保護接地または保護ゼロ接続に注意してください。
2) 電動ドリルを使用する前に、無負荷で回転させ、伝達部の音や回転方向が正常であることを確認してください。ハンドヘルド電動ドリルを使用するときは、力を均等に加え、圧力のコントロールに集中する。圧力は適切なものとし、ドリルビットの軸を加工面に対して垂直に保つ。過度な力が加わらないように、穴を開けようとするときは圧力を下げてください。ドリルビットが急に抵抗にぶつかると、その反力で手首を痛めることがあるので注意する。ドリルビットが穴の中で回転しなくなってから再スタートする場合も同様に注意する。
3) 電動ドリルに過負荷をかけない。ドリルビットの直径がハンドヘルド電動ドリルの最大使用容量に近いか等しい場合は、ドリルの過負荷損傷を防ぐために、印加力を適切に低減する必要があります。
4) 電動レンチの代用として電動ドリルを使用しないでください。手持ち電動ドリルは速度が速いため、締め付け後にボルトを急に止めると、その反力で手首を痛めやすい。
5) 電気ドリルは、定期的にほこりや油分を除去し、適切な換気を行うこと。電気ドリルを可燃性または爆発性の環境で使用したり、湿気の多い環境や腐食性ガスのある環境で保管したりしないこと。損傷を防ぐため、電気ドリルを不用意に引きずったり投げたりしないこと。
6) 新品の電気ドリルや長期間保管していた電気ドリルは、使用前に絶縁抵抗試験を行う。抵抗値は0.5MΩ以上でなければならず、そうでない場合は乾燥処理を行う。
3.電動工具の操作手順
1) 手持ち式電動工具の電源コードを許可なく接続することは禁止されている。電動工具が必要な場合は、電気技師が電線を接続し、金属ケーシングが帯電していないか確認すること。できれば安全保護ソケットを使用し、安全アースをとること。
2) 電源コードが損傷した電動工具を使用することは禁止されています。使用中は、電源コードの保護に注意してください。電源コードを引きずったり、重い物や車輪で押しつぶしたりしないでください。
3) 絶縁保護対策なしに電動工具を使用することは禁止されている。特に比較的湿気の多い環境で使用する場合は、絶縁靴、絶縁手袋を着用し、絶縁ゴムマットや乾燥した木の板の上で作業することが感電防止のために重要である。
4) 中性線と接地線を共用する電動工具の使用は禁止する。電源コードを引っ張ったり、中性線の接触が悪いと、電動工具の金属面に電圧が発生し、感電事故の原因となります。
4.グラインダー操作手順
グラインダーは、電動モーター、グラインダーベース、刃物台、保護カバーで構成され、フィッターの仕事場にある一般的な機器である。主に、ノミ、ドリル・ビット、スクレーパー、その他の切削工具を研いだり、ワークピースや材料からバリ、鋭いエッジ、硬い表面層を除去したりするのに使用される。
グラインダーは、安全上の事故が起こりやすい機器でもある。砥石はもろく、高速で回転する。そのため、グラインダーを使用する際は、安全事故を防ぐため、作業手順を厳守する必要がある。
1) 研削盤を使用する場合は、始動前に砥石と保護カバーの間に異物がないか、砥石に衝撃痕や損傷がないかなどをよく確認してください。問題がないことを確認してから研削盤を始動してください。研削盤を始動したら、砥石が安定して回転するまで待ってから研削を行ってください。砥石のぐらつきが顕著な場合は、直ちに機械を停止して調整してください。
2) 研削盤の刃物台と砥石の間隔は、ワークの挟み込み事故を防ぐため、3mm以内に保つこと。隙間が大きすぎる場合は、使用前に調整してください。ワークや切削工具を研削するときは、無理な力を加えないでください。
3) ソフトに挽かない 金属 アルミニウム、銅、木材のような砥石を使用しないでください。砥石が限界を超えて摩耗している場合は使用しないでください。
4) 研削作業では、砥石が破損した場合に砥石の破片による怪我を避けるため、作業者はグラインダーの側面または対角線上に立つこと。
5) 標準以下の研削砥石は使用しないでください。研削砥石を交換する場合は、研削盤の安全操作手順を参照してください。ひび割れや破損した研削砥石の使用は禁止されています。
6) 砥石を取り付ける際、クランププレートが直接砥石に接触しないようにしてください。クランププレートと砥石の間にペーパーワッシャーを入れること。組み立ては円形で、スムーズに回転するようにする。
7) グラインダーを使用する際は、保護メガネを着用すること。
5.ハンドヘルドグラインダー操作手順
1) 安全ガードや適切なアースがない状態で、ハンドヘルドグラインダーを使用しないでください。使用する前に、砥石に衝撃による損傷や亀裂がないか、金属ケーシングに電気が通っていないか、電源コードに異常がないかを注意深く確認してください。損傷している場合は、使用前に修理してください。ハンドヘルドグラインダーを使用する前に、必ず無負荷テスト運転を行い、正しい回転方向を確認してから使用してください。
2) ハンドグラインダーを使用する際は、十分な集中力が必要です。グラインダーを始動する前に、グラインダー本体をしっかりと握ってください。砥石を地面や工作物に近づけると、グラインダーが始動時の反力で転がり、砥石が飛んで事故になることがありますので、避けてください。
回転しているハンドヘルドグラインダーを地面やワークの上に無造作に置かないでください。砥石が完全に停止してから、指定の安全な場所に置かなければなりません。一時的に使用しないときは、必ず電源を切ってください。
3) 砥石の側面でワークを研削しないでください。手持ちグラインダーを使用する場合は、砥石の面を使用し、グラインダーをしっかりと持ち、ゆっくりとワークに接触させてください。衝撃や急激な圧力は禁物です。作業中は周囲に人が立っていない方がよい。作業者は砥石に直接向かわないようにし、保護メガネなどの必要な保護具を着用すること。
4) 損傷の兆候がある研削砥石は使用しないこと。手動スイッチのないハンドヘルドグラインダーは使用しないでください。ハンディグラインダーの砥石は回転速度が速く、強度が低いため、破損しやすい。研削砥石を取り付ける際は、適切なはめ合いを確認し、レンチでナットを適切に締め付けてください。
5) ハンドグラインダーは乾燥した場所に保管すること。内部絶縁体の損傷を防ぐため、湿気の多い場所や水に触れる可能性のある場所での保管は避けてください。
6.組み立て時の持ち上げ手順
組立工程では、作業者の肉体的負担を軽減し、作業効率を向上させ、製造の安全性を確保するために、より重い部品やコンポーネントには、リフティング機器を使用すべきである。
(1) ジャックの操作手順
ジャッキは、重量物を限られた高さまで持ち上げたり、重量物を移動させたりするのに適している。一般的に使用されるタイプには、スクリュージャッキ、ラック&ピニオンジャッキ、油圧ジャッキなどがある。ジャッキを使用する際は、以下の手順に従ってください:
- ジャッキは重量物の下に垂直に設置し、作業面は沈んだり傾いたりしないようにしっかりと水平にする。
- ラック・ピニオン・ジャッキを使用する場合、逆転防止爪はラチェット・ホイールに密着していなければなりません。
- 油圧ジャッキを使用する場合、調整ねじは伸ばし過ぎないこと。また、メインピストンのストロークが極端な高さマークを超えないようにしてください。
- 安全に使用するため、荷重はジャッキの耐荷重を超えないようにしてください。
- ジャッキを使う場合は、土台がしっかりしていて、設置場所が安定していなければなりません。ゆっくりと持ち上げ、支えを加えながら持ち上げる。重量物を持ち上げるために複数のジャッキを同時に使用する場合、指定された人が、対象物が傾かないように、ジャッキ間の持ち上げ速度と高さを一定に保つように調整する必要があります。事故防止のため、安定した昇降を行いましょう。
(2) クレーン作業手順
1) フック、チェーン、ブレーキなどに欠陥のある手動ホイストは使用しないでください。手動ホイストでワークや重量物を持ち上げる場合、ホイストを支えるフレームは安全で信頼できるものでなければなりません。
2) 手動ホイストに過負荷をかけたり、重いものを無理に持ち上げたりすることは禁止されています。吊り上げる対象物の大きさや重さに応じて、適切な手動ホイストを選択してください。
3) 重量物を長時間宙吊りにすることは禁止されている。吊り荷の下を人が通ったり、その下に留まったりすることは禁止されている。物を吊り上げるときは、確実に固定しなければならない。ロープは許容荷重の範囲内で使用すること。ロープが比較的鋭利なエッジの上を通る場合は、ロープの過度の摩耗や破損を防ぐため、柔らかい素材をパッドとして使用すること。2つ以上のホイストを使用して、同じ対象物を同時に持ち上げる場合は、指定された人が調整しなければならない。昇降はゆっくりと行うこと。
4) 重いものを持ち上げるとき、急いで持ち上げることは厳禁です。まず結束がしっかりしているか、重心の位置が適切かどうかを確認する。そして0.5m持ち上げ、検査で安全が確認された後に吊り上げを続行すること。
5) 機器を設置するときは、合理的に持ち上げる。ロープの長さ、太さは機器の重量に合わせて選びます。まず0.5mほど吊り上げて重量物の重心を確認し、確認後に吊り上げます。装置の変形や精度への影響を避けるため、不適切な吊り上げは厳禁です。
6)摩耗基準を超えるワイヤロープの使用は禁止する。また、ワイヤが切れたり、継ぎ目が破損したワイヤロープの使用も禁止する。
7) 使用中のワイヤーロープは、燃焼や強度の低下を避けるため、生きた金属(電線、溶接機のケーブルなどを含む)に接触してはならない。 ワイヤロープ 熱によるものだ。
8) ワイヤーロープの能力を超えて物を吊り上げることは禁止されています。ワイヤーロープの直径は、吊り上げる対象物の重量に応じて合理的に選択しなければならない。
9) ウィンチを使用する場合は、障害物のない平らな場所に設置する。固定には安全なグラウンドアンカーまたはパイルアンカーを使用してください。固定は、フレームが力を受けて動いたり傾いたりしないよう、信頼できるものでなければならない。
10) ウィンチを使用する場合、走行ロープは直接高い位置ではなく、ガイドプーリーに向かって水平に誘導すること。
11) ウィンチを使用する場合は、ドラムコアの上部からランニングロープの一端を引き出し、熟練者が締め付ける。ロープは通常ドラムコアに4~6回転巻き付ける。
12)吊り上げ作業中、スリングと対象物の間の水平角度は、45°以上であることが望ましい。水平角度が小さすぎる場合、スリングの高さは低くできますが、スリングや機器にかかる水平方向の力は大きくなります。強度が弱い場合、過剰な力は機械の変形や破損を引き起こしやすくなります。
II.共通機器のメンテナンス、使用、ケア
トレーニングの目的一般的なフィッター用具を正しく使用し、メンテナンスとケアができるようになる。
1.ドリルマシンの使用、メンテナンス、ケア
ボール盤は、一般的な穴加工用工作機械である。ボール盤にドリルビット、リーマ、ザグリ、リーマ、ボーリング工具、タップなどの工具を取り付けることで、穴あけ、リーマ、ザグリ、リーマ、ボーリング、ネジ切りなどの加工を行うことができる。ボール盤は、組立工が最もよく使う工作機械のひとつである。
ボール盤は、その構造と適用範囲から、ベンチボール盤(略称:ベンチドリル)、アップライトボール盤(略称:アップライトドリル)、ラジアルボール盤(略称:ラジアルドリル)の3種類に分類される。
(1) ベンチボール盤の構造と動作
ベンチドリルは、作業台の上で使用できる小型のボール盤で、最大穴あけ径は一般に12mmまでである。ベンチドリルの最低主軸回転数は比較的高く、一般に400r/min以下であるため、ザグリ加工、リーマ加工、ネジ切り加工には適さない。ベンチドリルは通常Vベルトトランスミッションを使用し、5段階のテーパプーリで回転数を変える。
ベンチドリルの主軸送りは手動のみで、通常、目盛付きダイヤル、目盛付き定規、固定移動装置など、穴あけ深さを制御する装置が付いている。穴あけ後、スピンドルはスパイラルスプリングの作用で自動的に元の位置に戻ることができます。
1) ベンチボール盤の構造
Z512ベンチドリルは、図4に示すように、組立工がよく使用するシンプルな構造です。
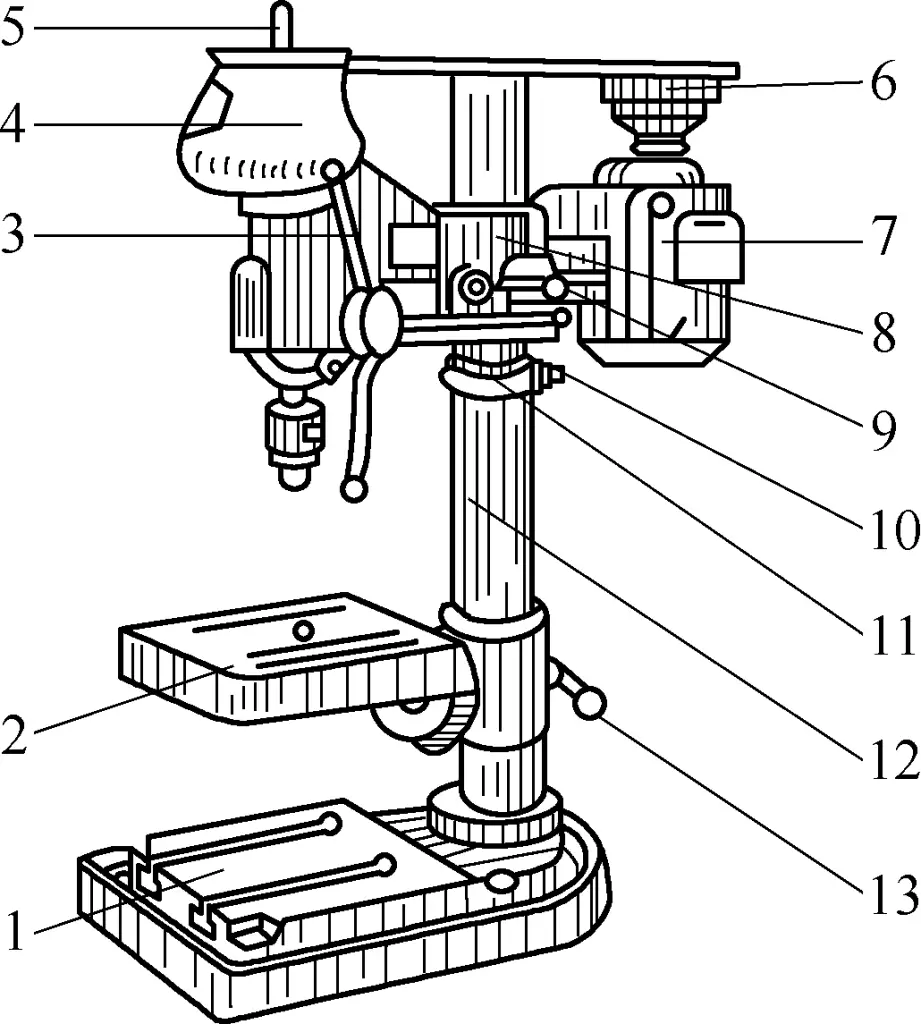
1ベース
2ワークテーブル
3-フィードハンドル
4カバー
5スピンドル
6プーリー
7モーター
8ボディー
9ハンドル
10スクリュー
11-安全リング
12列
13-作業台ロックハンドル
モータ7はプーリ6とVベルトを介してスピンドル5を駆動し、複数の異なる回転速度を実現する。本体8はコラム12に上下動可能に取り付けられており、コラム中心を中心に任意の位置に回転させることができる。適切な位置に調整した後、ハンドル9でロックすることができる。本体を降ろす必要がある場合は、まず安全リング11を適切な位置に調節してネジ10でロックし、次にハンドルを少し緩めて本体を自重で安全リング上に落下させ、ハンドル9をロックする。
作業台ロックハンドル13を緩めると、作業台2もコラム12上を上下に移動したり、コラム中心の周りの任意の位置に回転したりすることができる。小さなワークピースに穴を開けるときは、ワークピースをワークテーブルの上に置くことができ、大きなワークピースや背の高いワークピースの場合は、ワークテーブルを回転させて離して固定し、ワークピースをドリルベース1の上に直接置いて穴を開けることができる。
2) ベンチボール盤の操作
主軸回転数の調整。
ドリルビットの直径と加工材料に基づいて適切な速度を選択します。回転数の調整は、ベンチドリルの上部カバー4の内側にあるテーパー付きプーリーで行います。調整時には、スピンドルを停止させておく必要があります。カバーを開け、手動でプーリーを回転させ、まず小さい方のプーリーにVベルトを掛け、次に大きい方のプーリーに掛け、徐々にVベルトを適切なプーリーに掛け、希望の速度になるまで調整する。
作業台の上下左右位置の調整。
左手で作業台を持ち、右手で作業台ロックハンドル13を緩め、作業台2をスイングして希望の位置まで下または上に移動させ、作業台ロックハンドル13を再びロックします。
主軸送り位置の調整。
主軸の送りは、送りハンドル3を回転させることで行います。主軸の伸びは長すぎない方が良いので、穴あけ前にまず主軸を試しに上げ下げし、ワークの設置高さが適切かどうか確認する(ワークテーブルの昇降で調整する)。
3) ベンチボール盤の正しい使い方とメンテナンス
穴あけ加工を行う際は、ワークを加圧板でクランプしてください(手で保持できる大きなワークの小穴加工を除く)。貫通穴をあけるときは、ドリルビットの突き刺しやワークの飛び出しなどの事故を防ぐため、送り力を弱くしてください。
穴あけ中は、工具や測定器などを作業台表面に置かないでください。貫通穴をあける場合は、ドリルビットがワークテーブル面の逃げ穴(またはT溝)を通過できるようにするか、ワークの下にスペーサーブロックを置き、ワークテーブル面を傷つけないようにしてください。
作業台は定期的に清掃してください。使用後は、ベンチドリルの露出した摺動面および作業台面をきれいに拭き取り、摺動面および油穴には潤滑油を塗布してください。
(2)直立ボール盤の構造、使用方法及び保守点検について
直立ボール盤の最大穴あけ直径は、φ25mm、φ35mm、φ40mm、φ50mmなどです。直立ボール盤は自動送りが可能です。主軸回転数と自動送り速度は共に調整範囲が広く、様々な中型ワークのドリル加工、リーマ加工、カウンターボーリング加工、リーマ加工、ネジ切り加工に適しています。高出力、充実した機構により、高能率、高精度加工が可能です。
1) Z535直立ボール盤の構造と性能
Z535直立ボール盤は、図5aに示すように、組立工がよく使うタイプのボール盤である。
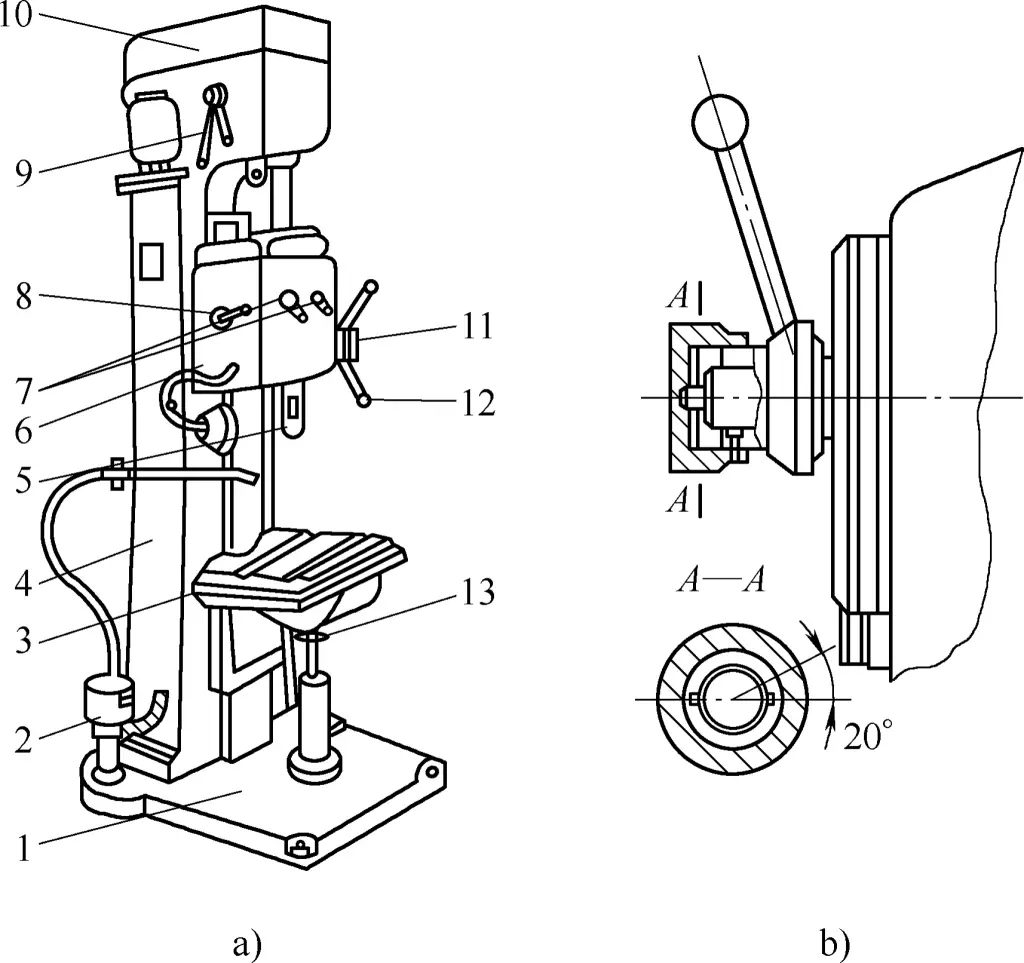
1ベース
2-油圧ポンプ
3ワークテーブル
4列
5スピンドル
6-フィードボックス
7-フィードハンドル
8-前進/後退ハンドル
9段変速ハンドル
10-スピンドル・ボックス
11-エンドカバー
12-操作ハンドル
13-作業台昇降ハンドル
ベッド4はベース1上に固定されている。スピンドルボックス10はベッドの上に固定されている。フィードボックス6はベッドの垂直ガイドレール上に設置され、ガイドレールに沿って上下に移動できる。操作を容易にするため、スピンドルの自重のバランスをとるカウンターウェイトがベッド内部に設置されている。ワークテーブル3は、ベッドの垂直ガイドレールの下部に設置され、高さの異なるワークに対応するため、ガイドレールに沿って上下に移動することができます。
Z535立型ボール盤には冷却装置も装備されています。また 切削油剤 はベースの空洞に収納され、使用時には油圧ポンプ2によって排出される。
Z535立型ボール盤の主な性能・仕様は以下の通り:
最大穴あけ直径ϕ35mm
主軸穴テーパー モース4番
スピンドルトラベル 225mm
主軸回転速度 68~1000 r/min
送り速度 0.11~1.6mm/r
作業台移動325mm
モーター出力4.5kW
2) 垂直ボール盤の操作
主軸回転数の調整。
ドリルビットの直径とワークの材質に基づいてスピンドル速度を決定します。速度の変更は、速度変更レバー9を介して達成される。正逆転レバー8は、スピンドル5の正転、逆転、停止を制御するために使用されます。
作業台昇降装置の調整。
ワークの穴あけ位置の高さに合わせて、ワークテーブルの下に設けたワークテーブル昇降ハンドル13で、ワークテーブルをベッドの垂直ガイドレールに沿って上下に調整する。また、図6に示すように、ワークテーブルが円筒形であり、ベッドを中心に回転しながらワークの穴あけ位置を合わせやすい円筒形ベッドを備えたタイプもある。
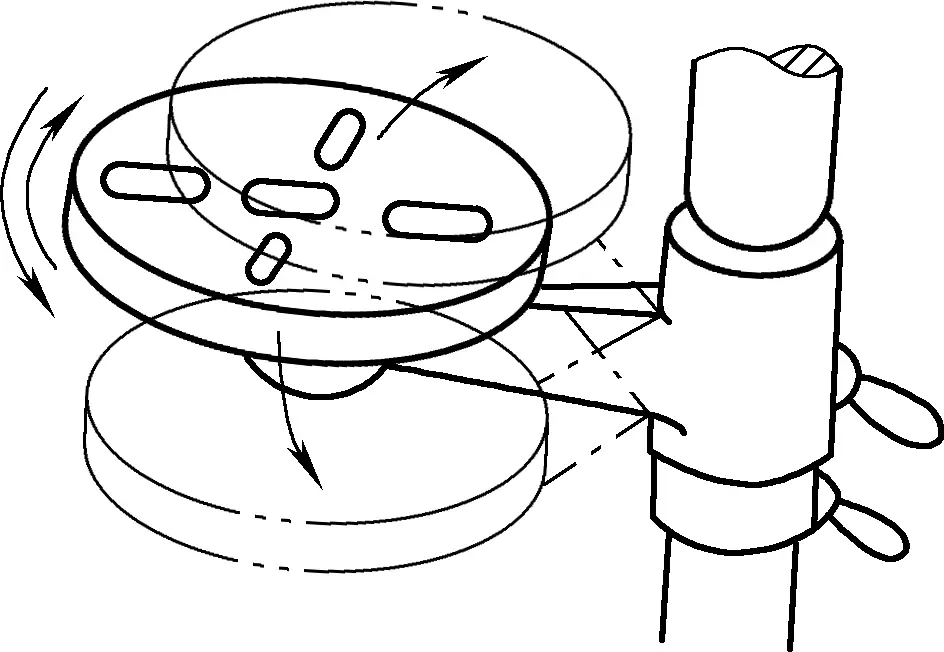
主軸送りの調整
主軸の送りには、自動送りと手動送りの2種類がある。
自動送りの場合、まず2つの送りハンドル7を所望の位置にセットして必要な送り速度を決定し、図5bに示すように、エンドキャップ11を外側に引き、ハンドルに対して時計回りに20°回転させて自動送り位置にする。スピンドルが回転すると、自動送りが可能になる。手動送りの場合は、エンドキャップをハンドルに対して反時計回りに20°回転させ、元の位置まで押し戻すと、自動送り装置が解除される。
手動送りの場合は、エンドキャップをハンドルに対して反時計回りに20°回転させ、元の位置まで押し戻し、その時点で自動送り装置が外れる。送り出しの場合は操作ハンドル12を反時計回りに、引き込みの場合は時計回りに回します。
ネジ山をタッピングする場合は、ハンドルを手送りの位置にする必要があります。まず、手送りを使ってタップを切り込ませます。タップが2~3回転切り込んだら、手動送りを止め、タップのねじ山を頼りに軸圧をかけ、スピンドル送りを駆動させます。タッピングが完了したら、スピンドルを逆転させてタップを引っ込めます。
3) 垂直ボール盤の使用規則
- 作業前に潤滑条件に従って注油し、ハンドル位置が正常かどうか、ガイドレール表面に異物がないかどうかを確認してください。機械を低速で始動し、主軸油窓に油があるか、伝動部に異常現象がないか確認してください。
- 作業中に自動送りを使用しない場合は、エンドキャップを内側に押して自動送り装置を解除する必要があります。
- 作業中は安全に注意してください。ワーク、固定具、工具はしっかりとクランプしてください。貫通穴をあける場合は、ワークの下にバッキング・ブロックを置いてください。鋳物や深い穴をあける場合は、頻繁にドリルを後退させて切りくずを除去してください。切削仕様を超えないこと。
- 切り屑、水、その他のゴミがガイドレールの表面、 モーター、電気ボックスに落ちるのを防ぐ。
- 作業後は、すべてのハンドルを停止位置またはニュートラル位置にセットし、作業台を最下部まで下ろし、電源を切ります。最後に、機械の清掃基準に従って機械を拭き、保護油を塗布する。
4) 垂直ボール盤のメンテナンス
機械設備の適切なメンテナンスは、設備の故障を減らし、機械の寿命を延ばすために非常に重要な役割を果たす。機械保全は、日常保全、第一保全、第二保全の「三段階保全システム」を実施している。
- 縦型ボール盤の日常的なメンテナンス。デイリーケアとも呼ばれ、オペレーターが行うもので、整頓、清潔、安全、潤滑の4つの要件を満たす必要がある。日常的な手入れは、予防を主目標として定期的に実施されるべきであり、潜在的な問題が発見された場合は速やかに対処し、重大な問題は直ちに報告されるべきである。
- 縦型ボール盤の一次および二次メンテナンス。二次メンテナンスとも呼ばれ、主にオペレーターがメンテナンス作業員の支援を受けながら実施する。
- 機械の外観。機械表面、作業台、リードスクリュー、ラック、ベベルギアを清掃する。ガイドレールの表面や作業台の表面のバリを取り除き、欠落したネジやハンドルボールなどを交換する。
- スピンドルとフィードボックス。スピンドルのテーパー穴からバリを取り除く;モーターの駆動ベルトを調整する;様々なハンドルの位置をチェックする;必要な摩耗した伝動機構部品を交換する。
- 潤滑。オイルの質と量を点検する。オイルフェルトを清掃し、オイルラインを点検し、二次整備時にオイルを交換する。
- 冷却。冷却ポンプ、フィルタ、クーラント・タンクを 清掃し、配管を点検する。二次保守点検時に切削液を交換する。
- 電気。モータと電気ボックスを清掃する(必要であれば電気技師の支援を受ける)。二次メンテナンスでは、必要に応じてモータを分解して清掃し、グリースを交換します。
(3) ラジアルボール盤のメンテナンス
ラジアルボール盤はラジアルドリルとも呼ばれ、大型ワークや多穴ワークの加工に適している。立型ボール盤で多穴ワークを加工する場合、穴を開けるごとにワークを移動させて位置合わせをする必要があり、大型ワークでは非常に手間がかかるうえ、ドリル中心とワークの穴中心を正確に合わせるのが難しい。この場合、主軸が可動するラジアルボール盤を使用した方が加工に便利である。
ラジアルボール盤Z35の構成を図7に示す。ワークが大きくない場合は、ワークテーブル5上にクランプして加工することができ、ワークが非常に大きくワークテーブル5上に収まらない場合は、ワークテーブル5を取り外し、ワークをベース6上に直接置いて加工することができる。
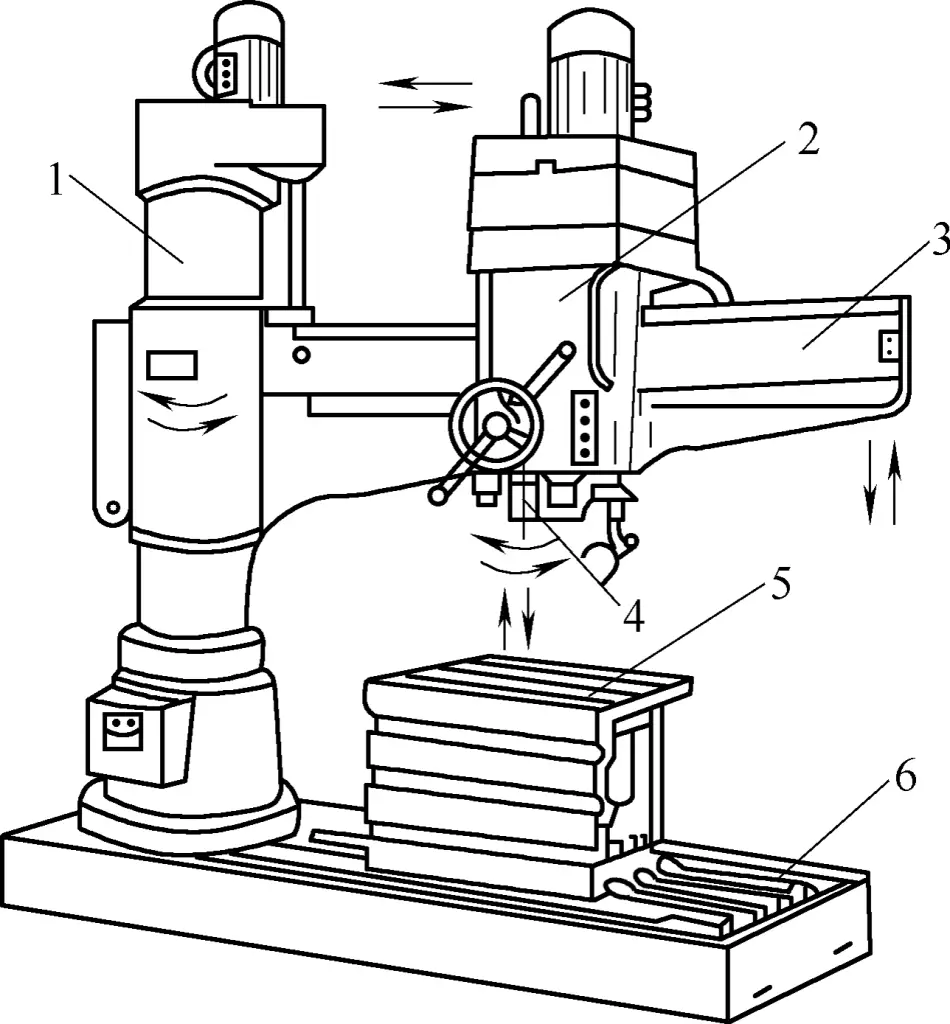
1カラム
2スピンドルボックス
3アーム
4スピンドル
5-ワークテーブル
6ベース
スピンドルボックス2はアーム3に取り付けられており、アーム3は垂直コラム1の周りを回転することができ、アーム上の水平ガイドレールに沿って前後に移動することができる。これら2つの動きにより、スピンドル4は機械の加工範囲内の任意の位置に調整することができる。従って、ラジアルボール盤は非常に広い範囲で穴加工を行うことができる。
ラジアルボール盤は、主軸回転数と送り速度の調整範囲が広く、高い生産効率と加工精度を実現します。ラジアルボール盤で多穴ワークを加工する場合、ワークを固定したまま、アームとアーム上のスピンドルボックスの位置を調整するだけで、穴の中心を合わせることができます。さらに、アームはコラムに沿って昇降し、ワーク加工エリアの高さに合わせてスピンドルボックスの高さを調整することもできます。
現在、中国で生産されているラジアルボール盤には多くの仕様があるが、その中でもZ35ラジアルボール盤は、図7に示すように、組立製造業で広く使用されている。
Z35ラジアルボール盤の主な性能と仕様は以下の通り:
最大穴あけ直径ϕ50mm
スピンドル穴テーパー モースNo.5
主軸台内部のスピンドルの最大移動量 350mm
アームガイドレールに沿ったスピンドルの最大移動量 1050mm
スピンドル速度レベル数 18
主軸回転速度範囲 34~2000r/min
送り速度レベル数 18
送り速度範囲 0.3~1.2mm/r
コラムに沿ったアームの最大移動量 680mm
メインモーター出力 4~5kW
2.圧入機の使用、メンテナンス、手入れ
圧入組立は、組立工場では一般的な干渉嵌合の一種です。また、熱間や冷間と比較して、経済的で効率的な組立方法です。 フィッティングこれは、組立フィッターが習得すべき作業技術である。ほとんどの圧入組立品には、キー構造が付加されている。
圧入組立には大きな押し付け力が必要な場合が多いため、一般に油圧制御の油圧圧入機が使用される。これは、油圧システムは圧力調整が容易で、大きな力が得られ、低速での圧入が可能で、操作が簡単で、作業が安全であり、システム圧力計によって圧入工程中の圧力の大きさや変化を監視することができ、圧入工程の安全な制御を実現できるからである。
油圧プレスフィッティングマシンは、使用シーンが異なるため、ワークや構造に応じて優れた利点があります。油圧圧入機は、構造寸法が小さく、操作・制御が容易で、適用範囲が広く、縦型と横型に分けられます。
図8は、フレーム構造の縦型油圧圧入機を示し、その油圧システムおよび制御部品は図示していない。圧入機の油圧システムは非常にシンプルであり、単純な動作のためシステム構成部品も少ない。圧入機は一般に高い使用圧力(32MPa)を必要とするため、可変容量ピストンポンプが主に使用される。可変ポンプは圧入速度に応じて出力流量を調整することができる。
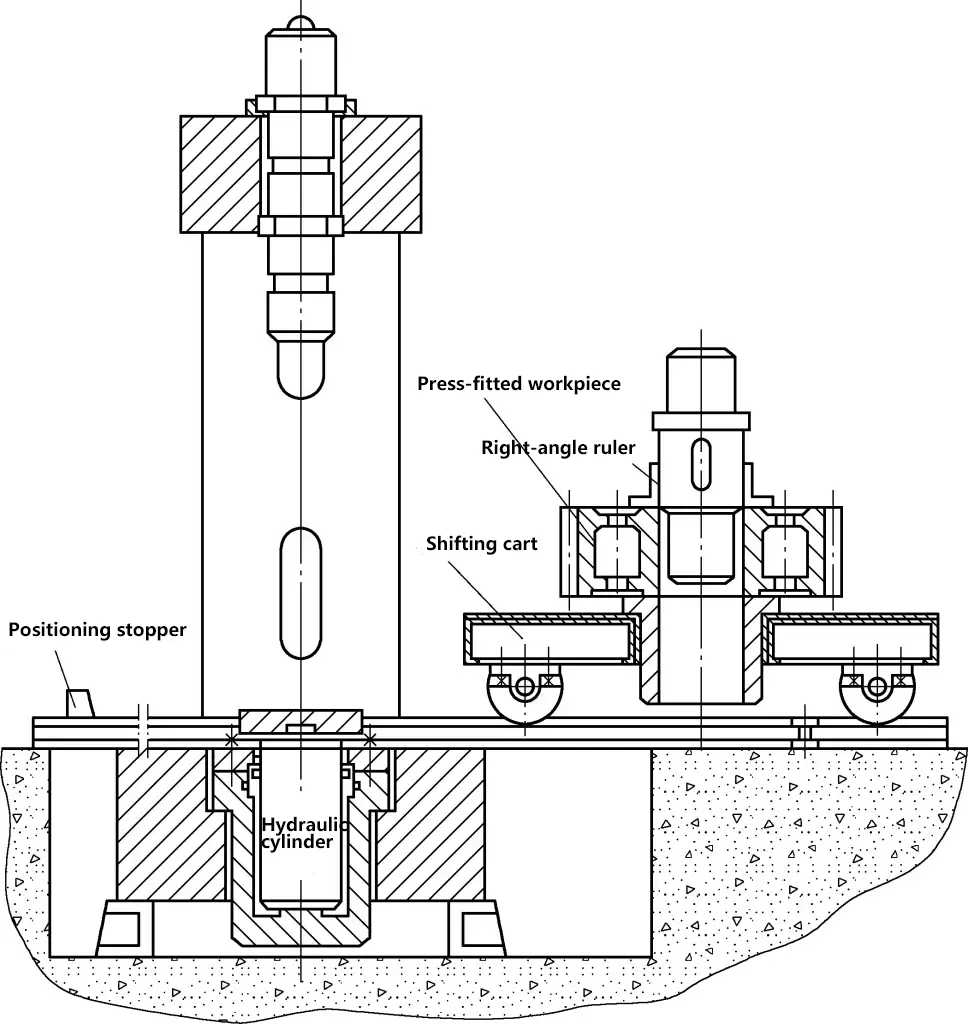
システムには、油圧ポンプを保護しシステムの安全性を確保するリリーフバルブ、システムの清浄度を維持するフィルタ、圧力ゲージ、チェックバルブ、油圧バルブ、ストップバルブ、コントロールスライドバルブなどの油圧コンポーネントがある。
より完全な機能を備えた圧入機には、圧入中の圧力曲線の記録・作図装置が装備されている。例えば、横型列車輪軸圧入機は、列車輪軸の圧入工程中の圧力変化に対して厳しい要求がある。そのため、圧入中の圧力変化の実態を反映・記録し、その圧力変化過程を曲線で描写することで、要件を満たしているかどうかの判断基準とし、アーカイブとして保存する必要がある。
縦型圧入機と横型圧入機は形状が異なるため、使用時にそれぞれの長所と短所が現れる。
縦型圧入機には2つの構造形式がある。1つは上置き油圧シリンダで、主油圧シリンダは圧入機の上部ビームに設置されるが、油圧シリンダはピストン構造でなければならず、そうでなければ油圧シリンダの戻り制御をピストン式の副油圧シリンダに頼ることになる。もう 1 つは、図 8 に示すようなボトムマウント油圧シリンダで、油圧シリンダは圧入機の下部ビーム(機台)内に設置され、プランジャ型油圧シリンダを使用することができ、プランジャと連結部品の自重でプランジャが復帰する。
フレームにもフレームタイプとコラムタイプがある。フレーム構造は主に溶接接続を使用するため、ボルト予締め構造を使用する場合でも、サイドフレームと上下の梁の接触面が非常に大きく、フレーム自体の剛性が高く、大きなトン数の圧入に適応できる。コラム構造(多くの場合2コラム)はシンプルで、加工とスケジューリングに便利で、小さいトン数の圧入に適している。
縦型圧入機の最大の利点は、コンパクトな構造、小さな設置面積、圧入時のワークセンタリングが良好、縦型圧入操作が便利、スキュー、ジャミングなどの不利な現象が発生しにくい、ボトムマウントのプランジャー油圧シリンダーはピストン油圧シリンダーに比べて構造が簡単、コストが低い、戻りがスムーズ、操作がより確実で合理的である、などである。
その欠点は、上梁があるため、圧入工程中のワークの吊り上げ作業が不便である。しかし、移動台車を設置すれば、ワークの積み下ろしは圧入機の外で行うことができ、構造上の欠点を克服することができる。移動台車はガイドレール上を自由に押すことができ、前端には位置決めストッパーがあり、圧入ワークが油圧シリンダー圧入センターと同軸になるようにするため、操作は非常に便利です。
もう一つの問題は、油圧シリンダーが下部に設置された構造である。圧入機は低重心で安定性が高いが、圧入工程では油圧シリンダーのプランジャーが上方に押し上げられると、圧入されるワークも上方に移動する。圧入部品の構造と寸法が大きく、自重が大きいため、不安定で安全性が低い。フレームが広いため、圧入作業位置の一部を占め、圧入観察に不便と死角を生む。
横型圧入機は縦型圧入機とは正反対である。ワークピースを水平に設置するため、広い設置面積を必要とする。自重の影響を受け、芯出しや調整が難しい。芯出しや位置決めが不安定なため、圧入工程や作業中にトラブルが発生しやすい。
プランジャー油圧シリンダーのストロークが立形機ほど大きくなく、戻りが難しい。横型圧入機は、ほとんどがコラム構造で、水平寸法が小さく、オペレーターがワークを観察し、接近するのに有利である。その優れた利点は、広々とした環境、ワークのロード、アンロード、および操作に便利で、明確な観察、安定したワークの配置、および落下の危険性がないことです。
圧入機の使用とメンテナンスにおいて、以下の点に注意する必要がある:
- 圧入機を使用する際は、作業圧力、作業ストローク、作業台面が定格作業範囲内であるかどうかを考慮してください。
- 機械を始動する前に、圧入機のすべての潤滑箇所に潤滑油が満たされていることを確認してください。
- 各可動部間のクリアランスやブレーキの締め付けが適切かどうかを確認する。
- 回転部分に異物が挟まっていないか。
- 電源に接続した後、空のストロークの動きが指定された要件を満たしているかどうかを確認します。
- 作業場の清潔を保つ。
- 圧入精度に影響する要素には、作業面とスライダー底面の平坦度、2つの面の平行度、圧入ストロークの作業台面に対する垂直度、ガイドレールのクリアランスなどがある。これらはすべて、圧入機を維持するための重要なポイントである。
- 油圧システムを使用する圧入機では、油圧システムの適切なメンテナンスも必要である。
3.クリーニング
機械組立工程での洗浄は、製品の組立品質を向上させ、製品寿命を延ばすために重要です。これは、ベアリング、精密部品、シール、特殊な洗浄が必要な部品にとって特に重要です。
洗浄プロセスには、洗浄液、洗浄方法、プロセスパラメーターが含まれ、これらはワークピースの洗浄要件、生産バッチサイズ、ワークピースの材質、表面グリース、汚れ、機械的不純物の性質と付着状態などの要因に基づいて決定する必要がある。同時に、選択された洗浄液は、洗浄方法に適合したものでなければならない。また、ワークピースは洗浄後、一定の中間防錆能力を持つべきであることにも留意すべきである。
(1) 洗浄方法
一般的な洗浄方法の特徴と適用範囲を表1に示す。
表1 一般的な洗浄方法の特徴と適用範囲
洗浄方法 | 洗浄液 | 特徴 | 適用範囲 |
拭き取り | ガソリン、灯油、軽油、エタノール、化学洗浄液 | シンプルな操作、シンプルな洗浄装置、低い生産性 | 小型・中型ワークの単品・小ロット生産と大型ワークの局所洗浄 |
浸漬洗浄 | 一般的に使用される様々な洗浄液に対応 | 操作は簡単で、洗浄時間は通常2~20分と長い。通常、多段階洗浄を採用 | 複雑な形状のワークの大量ロットに。軽い油汚れの洗浄 |
スプレー洗浄 | ガソリン、灯油、軽油、化学洗浄液、トリクロロエチレン およびアルカリ溶液 | 良好な洗浄効果、高い生産性 より高い、より良い労働条件、より複雑な 設備 | 中・大量生産ワーク用、複雑な形状には不向き。ひどく付着した汚れや半固形の油汚れの洗浄。 |
気相洗浄 | トリクロロエチレン蒸気 | 良好な洗浄効果、より複雑な設備、高い労働保護要件 | 小型・中型ワーク用。適度に付着した油汚れの洗浄に適しており、汚れの除去に効果的。 |
超音波洗浄 | ガソリン、灯油、軽油、化学洗浄液、トリクロロエチレン | 良好な洗浄効果、高い生産性、より複雑な機器のメンテナンスと管理 | 洗浄要求の高い小型・中型ワークピース用で、ワークピースの最終洗浄によく使用されます。 |
浸漬洗浄とスプレー洗浄の組み合わせ | ガソリン、灯油、軽油、化学洗浄液、トリクロロエチレン およびアルカリ溶液 | 洗浄効果が高く、生産性が高い。洗浄装置の設置床面積が広く、保守・管理が複雑。 | バッチ生産、複雑な形状、洗浄要求の高いワークに。油汚れ・半固形油汚れの洗浄 |
蒸気浸漬、蒸気スプレー、または蒸気浸漬-スプレーの複合洗浄 | トリクロロエチレン溶液およびトリクロロエチレン蒸気 | 上記と同じだが、生産性は若干低い | 気相洗浄に適しており、洗浄要求の高い小型ワークに適している。油汚れの洗浄が可能で、特に気相・浸漬複合スプレータイプは、以下のような洗浄が可能です。 汚れの除去効果が高く、ひどくこびりついた汚れを落とす。 |
(2) 洗浄液
1) 石油系溶剤
石油系溶剤は保管や防錆剤の配合が容易で、伝統的な洗浄液である。これらの洗浄液を使用する場合は、火災防止と換気の安全対策を考慮しなければならない。
一般的に使用される石油系溶剤は、主にガソリン、灯油、軽油などである。特殊な要求には、エタノールやアセトンなどの同様の有機溶剤を使用することもできる。
工業用ガソリンとストレートランガソリンは、主にグリース、汚れ、一般的に付着した機械的不純物の洗浄に使用され、鉄鋼や非鉄金属の工作物に適しています。航空ガソリンは、高品質の工作物の洗浄に使用されます。
灯油や軽油の用途はガソリンに似ているが、洗浄能力はガソリンに劣る。洗浄後の乾燥は遅いが、ガソリンよりも安全である。
ワークの発錆を防止するために、変位型防錆油や防錆添加剤を石油系溶剤に少量(例えば質量比で1%〜3%)添加することができる。置換型防錆油としては、201、FY-3、661等が挙げられる。また、防錆ガソリンを自己調合することもでき、防錆ガソリンの処方を表2に示す。
この防錆ガソリンは、洗浄力が強く、手汗、無機塩類、グリースなどを洗浄でき、鉄鋼、銅合金などのワークの中間防錆ができる。同時に、作業者は手汗によるワークの錆を防止し、ガソリン、灯油、軽油などによる手の刺激を避けるため、手に「液体手袋」をはめる必要がある。
表 2 防錆ガソリンの配合
コンポーネント | 質量分率(%) |
石油硫酸ナトリウム | 1 |
スパン80 | 1 |
ラウリルアルコールアシルアミド | 1 |
1%ベンゾトリアゾールアルコール溶液 | 1 |
蒸留水 | 2 |
200号ガソリン | 94 |
石油系溶剤は一般に常温で使用される。加熱が必要な場合は、ランプ用灯油は油温40℃以下、溶剤用灯油は65℃以下とし、容器を炎で直接加熱してはならない。機械油、タービン油、変圧器油の場合、油温は120℃を超えないこと。
2) アルカリ溶液
アルカリ溶液を調製する場合、洗浄能力を高めるために少量の界面活性洗浄剤を加えることができる。アルカリ溶液で洗浄する場合の注意点:厚い油汚れは最初に拭き取ること、異なる材質のワークは一緒に洗浄しないこと、洗浄後、ワークは水洗いまたは水洗いできれいにし、乾燥させること。一般的なアルカリ溶液の処方、プロセスパラメーター、適用性を表3に示す。
表3 一般的なアルカリ溶液の処方、プロセスパラメーター、適用可能性
組成/(g/L) | 主なプロセスパラメーター | 適用性 |
水酸化ナトリウム 50-55 リン酸ナトリウム 25-30 炭酸ナトリウム 25-30 ケイ酸ナトリウム 10-15 | 洗浄温度90~95 浸漬洗浄またはスプレー洗浄 洗浄時間10分 | ひどい油汚れや少量の不溶性の油汚れや不純物が付着した鋼鉄製のワークピース。 |
水酸化ナトリウム 70-100 炭酸ナトリウム 20-30 リン酸ナトリウム 20-30 | 洗浄温度90~95 浸漬洗浄またはスプレー洗浄 クリーニング時間 7-10min | ニッケルクロム合金鋼ワークピース |
水酸化ナトリウム 5-10 リン酸ナトリウム 50-70 炭酸ナトリウム 20-30 | 洗浄温度80~90 浸漬洗浄またはスプレー洗浄 洗浄時間5~8分 | 鋼と銅合金のワークピース |
水酸化ナトリウム 5-10 リン酸ナトリウム≈50 ケイ酸ナトリウム≈30 | 洗浄温度60~70 浸漬洗浄またはスプレー洗浄 洗浄時間≒5分 | アルミニウムおよびアルミニウム合金のワークピース |
3) 化学洗浄液
化学洗浄液には界面活性剤が含まれており、乳化剤洗浄液とも呼ばれ、油脂や水溶性の汚れに優れた洗浄能力を発揮する。これらの洗浄液は、調製が容易で、安定性と耐久性に優れ、無毒性、不燃性で、安全に使用でき、低コストであり、一部の化学洗浄液には一定の中間防錆能力もあるため、組立時の中間工程洗浄に非常に適している。化学洗浄液には多くの処方があり、一般的な化学洗浄液の処方、プロセスパラメーター、適用可能性を表4に示す。
表4 一般的な化学洗浄液の処方、プロセスパラメータ、および適用可能性
組成と質量分率(%) | 主なプロセスパラメーター | 適用性 |
105 洗浄剤 0.5 6501 洗浄剤 0.5 水の残り | 洗浄温度85 スプレー圧力 0.15MPa 洗浄時間 1分 | 鋼製ワーク。主に機械油を主成分とする油汚れや機械的不純物の洗浄用。 |
664 洗浄剤 2-3 水の残り | 洗浄温度 75 浸して洗う、上下に動かす 洗濯時間 3~4分 | スチールワーク。銅、亜鉛などの非鉄金属ワークの洗浄には適さない。主にステアリン酸、パラフィン、ワセリン等の洗浄用。 |
6501 洗浄剤 0.2 6503 洗浄剤 0.2 オレイン酸トリエタノールアミン 0.2 水の残り | 洗浄温度 35~45 超音波洗浄(使用周波数17~21kHz) 洗浄時間 4~8分 | 精密機械加工された鋼鉄工作物。酸化クロムなどを含む鉱油や研削ペーストの残留物の洗浄。 |
6503 洗浄剤 0.5 TX-10 洗浄剤 0.3 ポリエチレングリコール(相対分子量約400) 0.2 フタル酸ジブチル 0.2 リン酸三ナトリウム 1.5~2.5 水の残り | 洗浄温度 35~45 超音波洗浄(働く頻度 17~21kHz) 洗浄時間4分 | 精密機械加工された鋼鉄ワークピース。主に洗浄用 グリース |
664 洗浄剤 0.5 平平嘉洗浄剤 0.3 トリエタノールアミン 1.0 オレイン酸 0.5 ポリエチレングリコール(相対分子量約400) 0.2 水の残り | 洗浄温度 75~80 浸して洗う、上下に動かす 洗浄時間 1分 | 精密加工されたスチール製ワークピースグリース洗浄に非常に強い |
4) トリクロロエチレン
トリクロロエチレンは、脱脂効率が高く、洗浄効果が高く、不燃性である。適切な安定剤を加えれば、アルミニウムやマグネシウム合金のような非鉄金属ワークも洗浄できる。しかし、その洗浄設備は比較的複雑で、良好な換気システムと洗浄液回収システムを必要とする。また、ワークや洗浄槽の腐食防止にも注意が必要である。
トリクロロエチレンは沸点が低く、気化・凝縮しやすい強溶剤である。蒸気密度が高く拡散しにくいため、蒸気洗浄に適している。また、浸漬洗浄、スプレー洗浄、または3つの洗浄方法の組み合わせにも使用できる。超音波洗浄に使用する場合、特に高い品質が要求される機器部品、光学素子、電子部品の洗浄に適している。
さらに、超音波洗浄がある。超音波洗浄の仕組みは、洗浄液に超音波振動を導入することで、洗浄液中に多数のキャビテーション気泡を発生させ、徐々に成長した後、突然崩壊させる。
気泡が崩壊する際、中心から外に向かってマイクロ波が発生し、その圧力は数百から数千気圧にも達し、ワークに付着した油汚れの除去を促進する。同時に、キャビテーション気泡の強い振動により、油汚れに付着した洗浄液の乳化・可溶化が促進され、洗浄力が向上する。
(3) 洗浄方法の選択
洗浄方法とそれに対応する洗浄装置および洗浄液の選択は、工場の生産規模、バッチサイズ、ワークピースの構造寸法、形状特性、清浄度要件、材料、前洗浄条件などの具体的な条件に基づいて行うべきである。
生産効率の高い大量バッチ生産には、それに見合った洗浄装置を選ぶべきで、ベルトコンベア式の連続運転、連続入出力、さらには図9に示す洗浄機のような高度な自動制御技術の使用も必要である。
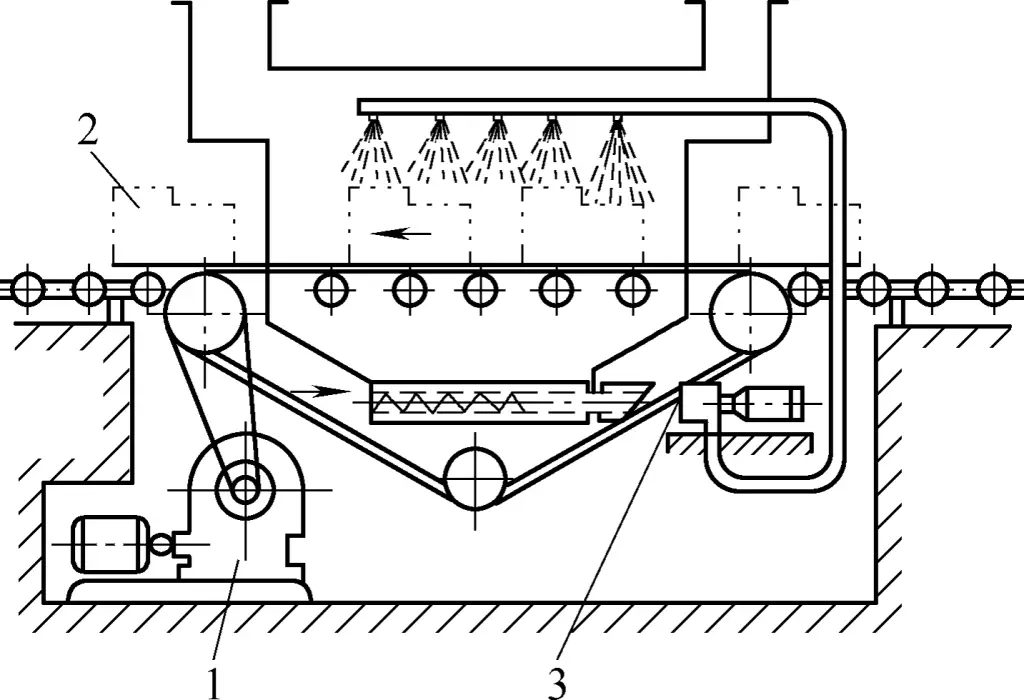
1-電気モーター
2ワーク
3-循環ポンプ
また、いくつかのロボットアームや自動調整・計数、洗浄液回収・処理、自動検査フィードバックなどの制御システムを装備することもできる。大型ワークや小ロットの場合、ターンテーブル式や固定式の洗浄チャンバーを使用し、異なる位置から異なる角度を選択し、洗浄ノズルを使用してワークピースに洗浄液を噴霧することができます。
洗浄中、必要に応じてワークを回転させることができる。スプレー洗浄後はスプレーを止め、圧縮空気で吹き付け洗浄し乾燥させる。圧縮空気ノズルの構造を図10に、洗浄ノズルを図11に示す。
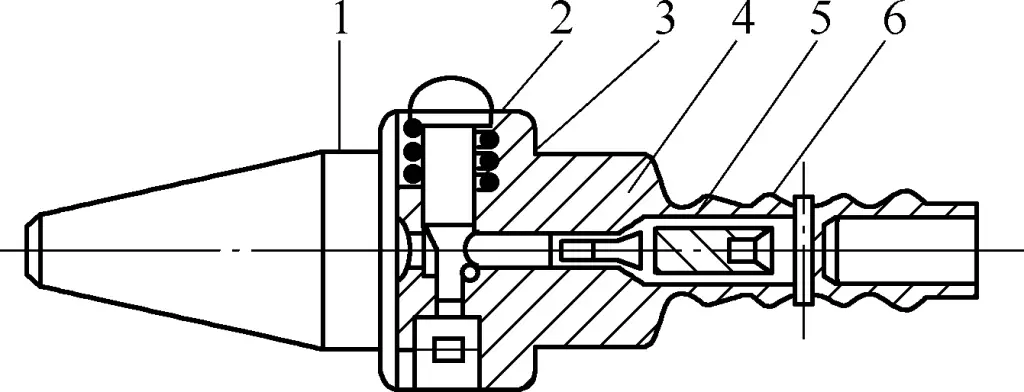
1ノズル
2スイッチ
3-スプリング
4-プッシュロッド
5-コニカルバルブ
6ボディ
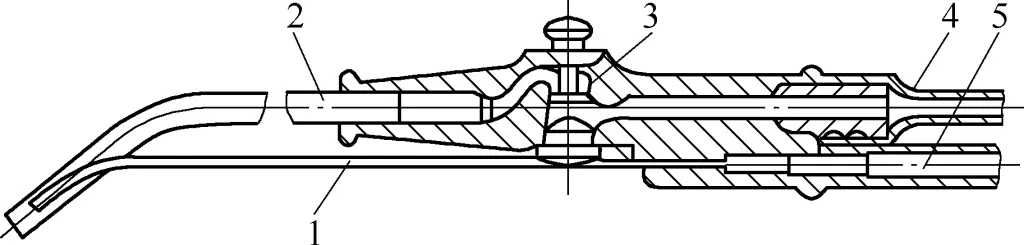
1-洗剤スプレーチューブ
2-圧縮空気スプレーチューブ
3スイッチ
4-圧縮空気パイプ
5-洗剤パイプ
油汚れの付着がひどい小さなワークの場合は、まず浸漬洗浄かスプレー洗浄を行う。洗浄品質を向上させ、洗浄時間を短縮するために、複数の異なる洗浄液を使用することが多く、順次洗浄するために別々のタンクを使用し、各タンクは油汚れ除去の異なる側面に焦点を当てている。
寸法や質量の大きなワークの場合、局部洗浄がよく用いられる。ワークピースを部分的に超音波洗浄槽に浸漬して洗浄することもできる。大型ワークピースの形状や局所洗浄領域の要件に応じて特殊な構造設計を行い、局所洗浄を実現することもできる。
非常に複雑な形状のワークや、穴や溝の大きさが異なるワークには、振動数の異なる超音波洗浄を使用することができる。洗浄作業は、クリーンな環境を維持し、プロセス仕様に厳密に従う必要があり、これは安全な生産を達成するために非常に重要である。
(4) 部品洗浄作業の注意事項
1) 組立前に部品を十分に洗浄すること。組み立てる前に、部品に残留している成形砂、切粉、錆などを十分に除去する必要がある。穴や溝などゴミが残りやすい場所は特に念入りに清掃し、バリや鋭利な角は取り除くこと。ハウジングの内部など、洗浄後に塗装が必要な部品もある。
清掃が徹底されていないと、機械の組立品質や寿命に影響する。例えば、摺動ガイドでは、相手面間に残留する砂粒子や切粉によって摩耗が促進され、ガイドの「焼き付き」のような重大事故が発生することさえある。
2) 組立時に発生する切粉の清掃に注意する。組み立ての際、ドリル加工、位置決めピン穴のリーマ加工、ねじ山のタップ加工など、補助的な加工が必要な部品がある。その際に発生する切粉を除去する必要がある。必要な場合は、切粉が相手面に落下しないように、組立現場から離れた場所で補助加工を行う。
3) 重要な合わせ面をクリーニングする際は、元の精度を損なわないこと。機械加工面の錆や乾燥した塗料は、ヤスリ、スクレーパー、サンドペーパーなどで取り除くことができる。重要な相手面については、本来の精度を損なわないよう、洗浄時に十分な注意が必要である。
4) 洗浄中に部品を傷つけないこと。洗浄中に部品を傷つけないように注意すること。わずかなへこみやバリがある場合は、砥石やスクレーパーで補修し、再度洗浄する。
5) ゴム部品の洗浄にガソリンを使用しないこと。シールリングなどのゴム部品は、変形を防ぐためガソリンでの洗浄は厳禁です。洗浄には洗浄液またはアルコールを使用すること。
6) 転がり軸受の清掃に綿糸を使用しない。転がり軸受の清掃には、綿糸を使用せず、ブラシなどの工具を使用してください。
7) 洗浄した部品の二次汚染を防ぐ。洗浄済みの部品は、組み立ての際に安易に拭いたりすると、部品が汚れやすくなり、二次汚染の原因になります。
洗浄後、部品を組み立てる前に油滴を乾燥させ、油汚れが組立品の清浄度に影響するのを防ぐこと。洗浄した部品をすぐに組み立てない場合は、粉塵が部品に混入する可能性があるため、長時間の曝露を防止する措置を講じる必要がある。
8) 組立前に潤滑油の補給と必要な調整を怠らないこと。一般に、組立て前に相手面に潤滑油を塗布しておく必要があります。そうしないと、組立て中に相手面に傷がつくなどの現象が発生することがあります。可動接続の嵌合面では、潤滑を怠ると、潤滑不足による可動抵抗、摩耗の促進、あるいは表面の毛羽立ちの原因になりやすい。
部品の機械加工によるバリや、工程移動時の衝突による打痕は見落とされやすく、組立精度に影響を与える。そのため、組立時には、部品のこれらの欠陥の修正に注意を払う必要がある。