
被削材の被削性を改善し、切削油剤を合理的に選択し、工具形状パラメータと切削量を合理的に選択することは、加工品質と加工効率を向上させ、加工コストを削減するための重要な対策である。
I.被削材の加工性向上
被削材の被削性とは、特定の切削条件下で被削材を加工することの容易さを指す。被削性を研究する目的は、材料の被削性を向上させる方法を見つけることである。
1.被削材の被削性を測定する指標
被削材の被削性は化学組成に関係する、 熱処理 状態、金属組織、物理的・機械的特性、材料の切削条件。被削性は、工具寿命、切削力、切削温度、加工面の粗さなどの指標によって測定することができる。
一般的な金属材料を切削する場合、その材料の加工性は、許容される切削速度によって評価される。 切断速度 v60 難削材を切削する場合、被削材の加工性はv20 値である。
ある材料の被削性は他の材料との相対的なものであるため、被削性は相対的なものである。鋼の被削性を論じる場合、v 60 の45鋼(170~229HBW、σb =637MPa)が一般的にベンチマークとして使用される。060 とv60 トヴ 060 すなわち、相対的被削性である、
Kr=v60/v060
Kの場合r >1以上の場合、45鋼よりも加工しやすく、加工性は良好である。r <1 の場合、45 鋼よりも加工が難しく、被削性は悪い。表2-5に相対的な被削性とその分類を示す。
表1 相対的被削性とその分類
被削性グレード | 被削材の分類 | 相対切削性 K | 代表的な素材 | |
1 | 非常に加工しやすい素材 | 一般非鉄金属 | >3.0 | アルミニウム・マグネシウム合金、ZnCuAll0Fe3 |
2 | 加工しやすい素材 | 快削鋼 | 2.5~3.0 | 焼鈍15Cr、自動機械用鋼 |
3 | 鋼材の加工が比較的容易 | 1.6~2.5 | ノーマライズド30スチール | |
4 | 通常の材料 | 一般鋼、鋳鉄 | 1.0~1.6 | #45鋼、ねずみ鋳鉄、構造用鋼 |
5 | 機械加工がやや難しい素材 | 0.65~1.0 | 焼入れ・焼戻し 2Cr13, 85 鋼 | |
6 | 機械加工が難しい素材 | 機械加工が比較的難しい素材 | 0.5~0.65 | 焼入れ・焼戻し 45Cr、焼入れ・焼戻し 65Mn |
7 | 機械加工が難しい素材 | 0.15~0.5 | 1Cr18Ni9Ti、焼き戻し50CrV、一部のチタン合金 | |
8 | 加工が非常に困難な素材 | <0.15 | 鋳造ニッケル基超合金、一部のチタン合金 |
2.被削材の被削性向上策
(1) 切りやすいスチールを選ぶ
易削鋼とは、機械的性質を低下させることなく、被削性を向上させる添加物を含む材料である。この種の材料を切削する場合、工具寿命は長く、切削抵抗は低く、切りくずは容易に破損し、加工部品の表面品質は良好である。
(2) 適切な熱処理を行う
高炭素鋼や工具鋼など硬度の高い材料は、焼鈍を施して硬度を下げ、被削性を向上させることができる。低炭素鋼は、焼ならしや冷間引抜きなどの加工を施すことで、塑性を抑え硬さを増すことができ、切削加工が容易になる。
中炭素鋼は、均一なミクロ組織と材料硬度を達成するために、焼ならし熱処理を施すこともでき、それによって被削性を向上させることができる。
(3) 道具材料の合理的な選択
被削材の特性や要件に合った工具材料を選択する。
(4) 加工方法の選択
被削材の特性や要求に適した加工方法を選択する。加工技術の発展に伴い 切断技術加熱切削、低温切削、振動切削などの新しい加工方法が登場し、その中には難削材を効果的に加工できるものもある。
II.切削油剤の合理的な選択
切削油剤を適切に使用することで、切削条件を改善し、工具摩耗を低減し、加工面の品質を向上させることができる。
1.切削油剤の機能
(1) 冷却機能
切削液を切削領域に流し込むと、伝導、対流、気化によって切りくず、工具、被削材間の摩擦を減らし、発熱を抑えます。また、発生した熱を運び去り、切削温度を下げ、冷却効果をもたらします。
(2) 潤滑機能
切削油剤の潤滑機能は、工具、切り屑、ワーク表面の間に潤滑油膜を形成することで達成される。
(3) 洗浄・防錆機能
切削油剤の洗浄機能により、工作機械、切削工具、治具に付着した微細な切り屑や砥粒を除去し、加工面の傷を防ぎ、工具の摩耗を低減する。
洗浄機能の効果は、切削油剤の油性、流動性、圧力に依存する。切削油剤に防錆添加剤を加えると、切削油剤に保護膜を形成することができる。 金属表面工作機械、切削工具、ワークピースが周囲の媒体によって腐食されるのを防ぐ。
2.切削油剤の種類
(1) 水溶性切削油剤
水溶性切削油剤には、主に水溶液、エマルジョン、合成油剤がある。
1) 水溶液
水溶液は、水を主成分とし、防錆添加剤を加えた切削油剤である。水は熱伝導率、比熱、気化熱が高いため、主に冷却機能を持つ。潤滑性能が低いため、主に粗加工や通常の研削加工に使用される。
2) エマルジョン
エマルジョンは、乳化油を95%~98%(体積比)の水で希釈した切削油剤です。乳化油は鉱油と乳化剤から作られます。乳化剤は鉱油を水と乳化させ、安定した切削油を形成します。
3) 化学合成油
化学合成油は、水、各種界面活性剤、化学添加剤で構成されている。冷却性、潤滑性、洗浄性、防錆性に優れている。化学合成油にはオイルが含まれていないため、エネルギーを節約できる。
(2) 油溶性切削油剤
油溶性切削油には主に切削油と極圧切削油がある。
1) 切削油
切削油とは、鉱油を主成分とし、特定の添加剤を加えた切削油のことである。切削油に使用される鉱油には、主に全損システム油、軽油、灯油などがある。切削油は主に潤滑機能を果たす。
2) 極圧切油
切削油に硫黄、塩素、リンなどの極圧添加剤を加えると、潤滑効果と冷却機能が大幅に向上し、硫黄添加油が最も広く使用されている。
(3) 固形潤滑油
一般的に使用される固体潤滑剤は二硫化モリブデンで、非常に低い摩擦係数、高温耐性、高圧耐性を持つ潤滑膜を形成する。切削中に工具表面に塗布したり、切削液に添加したりすることができる。
3.切削油剤の合理的な選択と使用
(1) 切削油剤の合理的な選択
切削油剤は、被削材の材質、工具の材質、加工方法、技術的要求などの特定の条件に基づいて合理的に選択されるべきである。
高速度工具鋼工具は耐熱性に劣り、切削油剤を使用する必要がある。粗加工では冷却を重視し、切削抵抗と消費電力を低減することが望ましい。3%から5%のエマルジョンが使用できる。仕上げ加工では、加工物の表面品質を向上させ、工具摩耗を低減し、ビルドアップエッジを最小限に抑えることが主な目的です。15%~20%(体積比)の乳剤を使用できます。
超硬工具は耐熱性が高く、一般に切削液を必要としない。切削液を使用する場合は、連続的かつ十分に供給しなければならない。さもなければ、急激な冷却や加熱による内部応力によって、工具に亀裂が生じる。
鋳鉄の切削では、断片化した切屑が形成されるため、一般に切削油剤は必要ない。銅合金や非鉄金属を切削する場合は、被削材表面の腐食を避けるため、一般に硫黄を含む切削油は使用しない。アルミニウム合金の切削には、一般に切削油剤は必要ないが、リーマ加工やねじ切り加工の際には、灯油と機械油を5:1の体積比で混合したものや、軽油を加えることが多い。要求が高くない場合は、エマルジョンを使用することもできます。
(2) 切削油剤の使用方法
切削油剤の合理的な使用は非常に重要である。注ぐ場所、適切さ、注ぎ方は、切削油剤の効果に直接影響する。
切削変形領域は発熱の核となる領域であり、切削液はできるだけこの領域に注ぐべきである。また 切削油剤の種類と選択 を表2に示す。
表 2 切削油剤の種類と選択
いや。 | 名称 | 構成 | 主な用途 | |
1 | 水溶液 | 硝酸ナトリウム、炭酸ナトリウムなどを水に溶かし、水で100~200倍に希釈した溶液。 | 研磨 | |
2 | エマルジョン | (1)鉱油はほとんどなく、主に界面活性剤で乳化された油で、水で40~80倍に希釈され、冷却と洗浄性能が良い。 | 旋盤、ドリル | |
(2)鉱油を主成分とし、少量の界面活性剤を加えた乳化油を、10~20倍の水で希釈したもので、冷却性能と潤滑性能に優れている。 | 旋盤加工、ねじ切り | |||
(3) エマルジョンに添加物を加える。 | 高速旋盤、ドリル | |||
3 | 切削油 | (1) ミネラルオイル(L-AN15または全損システム用L-AN32オイル)の単独使用 | ギヤホビング、ギヤシェイピング | |
(2) 鉱物油と植物油または動物油を混合し、潤滑性能の良い混合油を形成する。 | 精密ねじ切り | |||
(3) 鉱油または混合油に添加剤を加え、極圧油を形成する。 | 高速ギヤホブ、ギヤシェーパ、ねじ切り等 | |||
4 | その他 | 液体CO2 | 主に冷却に使用 | |
二硫化モリブデン+ステアリン酸+パラフィンをクレヨンにし、工具表面に塗布。 | スレッディング |
III.工具形状パラメータの合理的な選択
工具は切削加工のための直接の道具である。その構造と幾何学的パラメータの合理性は、切削加工の品質と効率において非常に重要な役割を果たす。工具の幾何学的パラメータを合理的に選択することで、その切削性能を十分に発揮することができる。良い仕事をするためには、まず工具を研がなければならない」という中国の古いことわざがあるが、この原則を物語っている。
工具のいわゆる合理的な幾何学的パラメータとは、加工品質を保証しながら、高い生産性と低い加工コストを確保できる幾何学的パラメータを指す。
工具幾何学パラメータの基本的な内容は以下の通り:
- 直線刃、ジグザグ刃、円弧刃、波刃などの刃先形状は、切削層の形状に直接影響する。合理的な切れ刃形状を選択することは、工具寿命の向上、被削材表面の品質向上、工具の耐振動性の向上、切り屑の形状の変化に直接影響する。
- 切れ刃部分の断面形状は、シャープエッジ、ネガティブ面取り、振動減衰面取り、丸みを帯びたエッジ、エッジバンドなどがある。これらの形状を合理的に選択することは、切削生産性、表面品質、経済性を向上させるために重要である。
- 切りくず溝、切りくずブレーカープラットフォーム、背面工具面の両刃研削などの工具面形状は、切削力、切削温度、工具摩耗、工具寿命、切りくず制御に直接影響する。
- すくい角、逃げ角、主切れ刃角、切れ刃傾斜角、副逃げ角、副切れ刃角などの工具角度。
工具幾何学パラメータは有機的な全体であり、パラメータ間の相互関連と制約がある。切削工程における各パラメータの切削性能への影響には、有益な側面と不利な側面の両方がある。
したがって、工具形状パラメータを選定する際には、具体的な生産条件から出発し、主な矛盾点、すなわち切削性能に影響を及ぼす主なパラメータに着目し、パラメータ間の相互関係を総合的に検討・分析して、各パラメータの有益な効果を十分に発揮させ、悪影響を抑制・克服する必要がある。
1.すくい角と正面工具面の選択
(1) すくい角の機能
すくい角を大きくすることで、切削変形と摩擦を低減し、切削力と切削温度を下げ、工具摩耗を減らし、加工品質を向上させ、刃先の盛り上がりを抑制することができる。しかし、すくい角を大きくしすぎると、切れ刃の強度や放熱性が弱くなり、刃先が欠けやすくなる。したがって、すくい角は小さすぎず大きすぎず、図1および図2に示すような適正な値が望ましい。
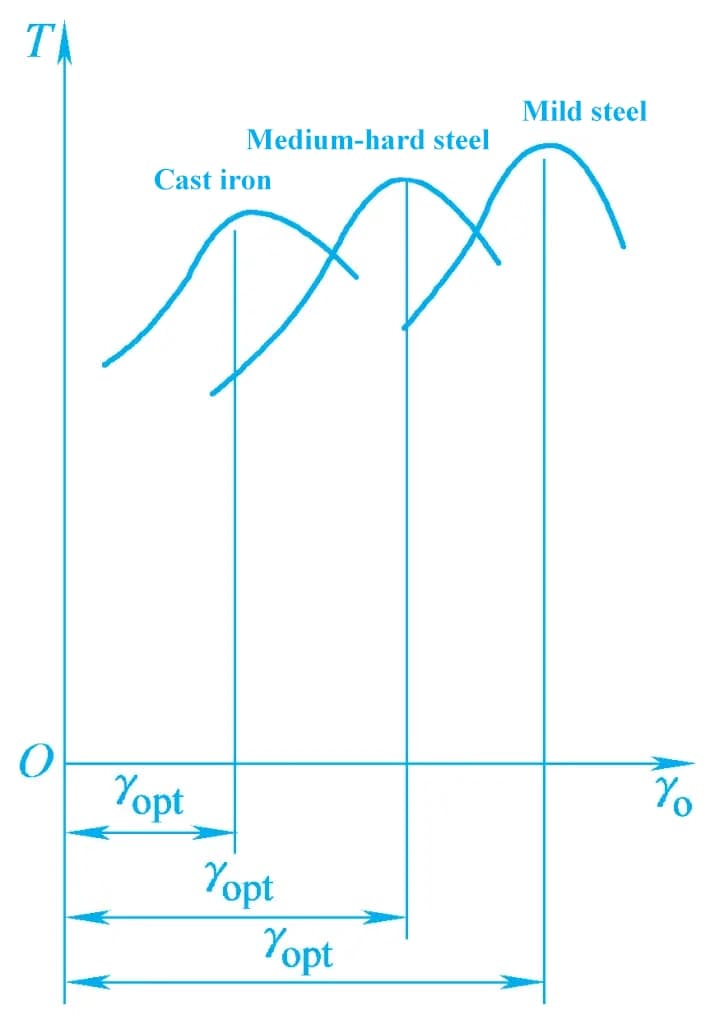
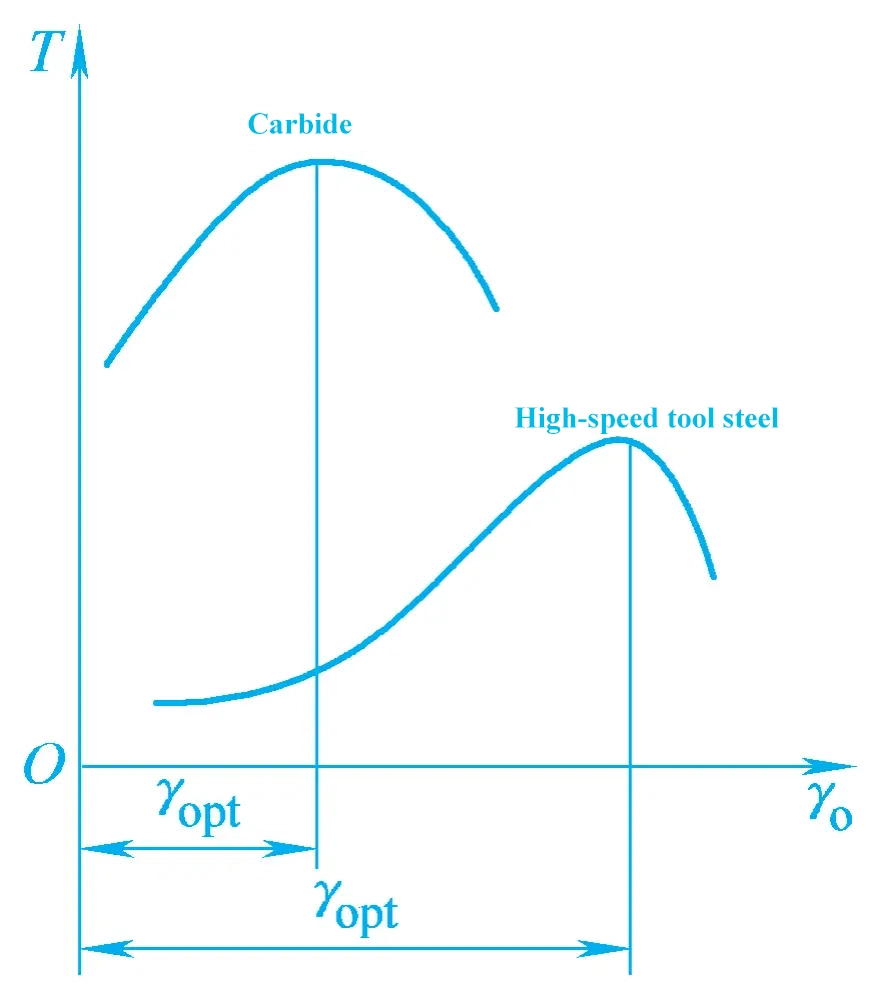
(2) すくい角選択の原則
1) 被削材の特性に応じたすくい角の選択
図1に示すように、加工材料の塑性が大きいほど、すくい角を大きく選択する必要がある。すくい角を大きくすることで、切削変形を抑え、切削温度を下げることができるからである。
脆性材料を加工する場合、一般に断片化した切りくずが得られ、切削変形は最小限に抑えられ、切りくずとすくい面の接触面積は小さく、すくい角が大きいほど切れ刃の強度は弱くなる。刃先のチッピングを避けるためには、すくい角を小さく選択する必要がある。被削材の強度や硬度が高い場合は、刃先の強度や放熱面積を十分に確保し、刃先のチッピングや工具の過度の摩耗を防ぐため、すくい角を小さくする。
2) 工具材料の特性に基づいて、すくい角を選択する。
図2に示すように、強度や靭性に優れた工具材料(高速度工具鋼など)を使用する場合は、すくい角を大きくすることができ、強度や靭性に劣る工具材料(超硬合金など)を使用する場合は、すくい角を小さくする必要がある。
3) 加工の性質に応じて、すくい角を選択する。
粗加工の場合、選択される切り込み深さと送り速度は比較的大きい。切削変形を減らし、工具寿命を向上させるには、すくい角を大きく選択する必要がある。
しかし、ブランクの凹凸や硬い表面のため、切れ刃の強度を高めるには、すくい角を小さく選択する必要がある。仕上げ加工では、選択した切り込み深さと送り速度が小さくなり、切削力が小さくなる。シャープな切れ刃を確保し、加工品質を保証するには、より大きなすくい角を選択することができる。表3は、超硬旋削工具の妥当なすくい角の参考値である。
表3 超硬旋削工具の適正すくい角の参考値
被削材 | 適度なすくい角 | |
荒いターン | ターニングの仕上げ | |
低炭素鋼 | 20°~25° | 25°~30° |
中炭素鋼 | 10°~15° | 15°~20° |
合金鋼 | 10°~15° | 15°~20° |
焼入れ鋼 | -15°~-5° | |
ステンレス鋼(オーステナイト系) | 15°~20° | 20°~25° |
灰色の鋳鉄 | 10°~15° | 5°~10° |
銅および銅合金 | 10°~15° | 5°~10° |
アルミニウムおよびアルミニウム合金 | 30°~35° | 35°~40° |
チタン合金Rm ≤1.177GPa | 5°~10° |
(3) すくい面の形状
1)ポジティブすくい面タイプ
図3aに示すように、ポジティブすくい面タイプの特徴は、製造が簡単で、比較的鋭い切れ刃を得ることができるが、強度が低く、熱伝達能力が低いことである。一般に、仕上げ工具、成形工具、フライスカッター、脆性材料の加工用工具に使用される。
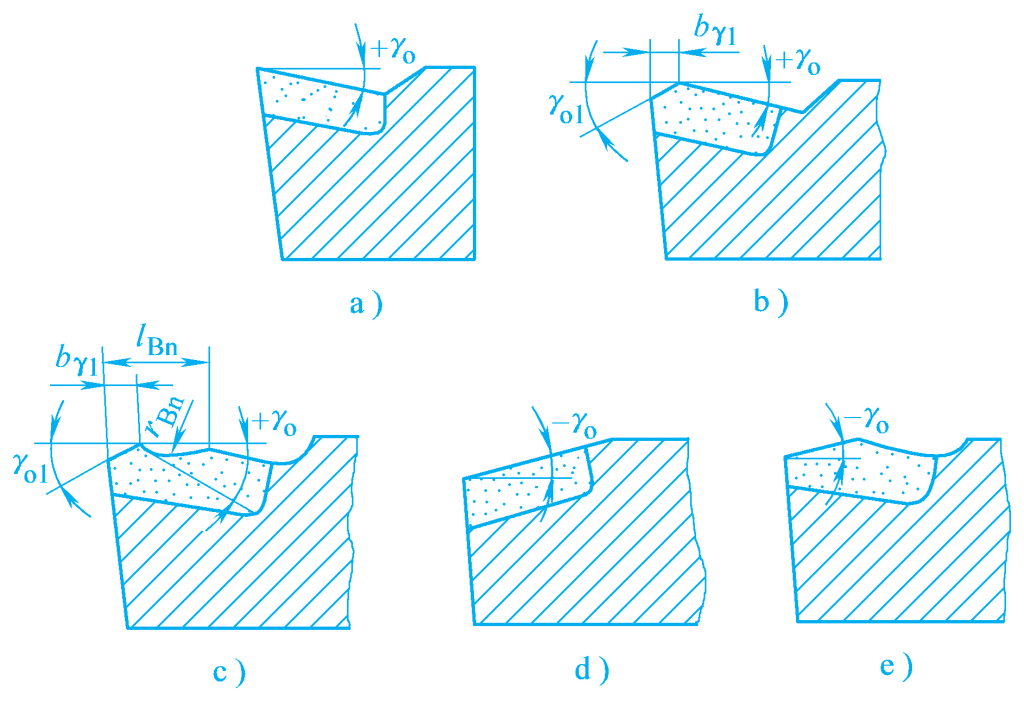
a) 正すくい面タイプ
b) 面取りタイプ正すくい面
c) 面取りされた正のすくい角
d) ネガティブすくい角片面タイプ
e) ネガティブすくい角両面タイプ
2) 面取りされた正のすくい角
図3bに示すように、面取りは、主切刃の切れ刃に非常に狭いエッジを研削することによって形成される。この面取りにより、切れ刃の強度が向上し、放熱性が高まるため、工具寿命が延びる。
面取り幅は非常に狭い。プラスチック材を切断する場合は、bによって選択できます。r1 =(0.5~1.0)f, Yo1 =-5°~-15°.このとき、切りくずはすくい面に沿って流れ、面取り面に沿っては流れない。面取り形状は一般的に、鋳物や鍛造品の荒削りや、断続面の加工に使用される。
3) 面取りされた曲面による正のすくい角
図3cに示すように、この形状は面取りされた平面を持つ正のすくい角に基づいている。切り屑を丸めてすくい角を大きくするため、すくい面には一定の曲面が研磨されている。チップ溝のパラメータはおおよそ次のとおりである。ブン =(6~8)f, rブン =(0.7~0.8)lブン .プラスチック材料の粗加工や仕上げ加工によく使用される。
4)ネガティブすくい角片面タイプ
主に逃げ面に摩耗が発生する場合、図3dに示すような負のすくい角の片面タイプにすることができる。この時、インサートは圧縮応力を受け、切刃強度は良好である。そのため、高硬度(強度)材や焼入れ鋼材の切削に用いられることが多いが、すくい角が負のため切削抵抗が大きくなる。
5)ネガティブすくい角両面タイプ
図3eに示すように、すくい面と逃げ面の両方に摩耗が発生した場合、負のすくい角の両面タイプにすることで、チップの再研磨回数を増やすことができる。このとき、負のすくい角の面取り面は、切り屑が面取り面に沿って流れるように十分な幅が必要である。
2.フランク角、二次フランク角、フランク面の選択
(1) 側面の角度の関数
逃げ面の角度を大きくすることで、逃げ面と被削材の移行面との摩擦を減らし、工具の摩耗を減らすことができる。また、切れ刃の鈍円の半径を小さくすることで、切れ刃を鋭くし、切りくずを切り落としやすくすることができる。 表面粗さ 値である。しかし、逃げ角が大きすぎると、切れ刃の強度と放熱性が低下する。
(2)フランク角選択の原則
逃げ角は主に切削厚さに基づいて選択される。粗加工では、送り速度が大きく、切削厚が大きいので、逃げ角は小さくする。仕上げ加工では、送り速度が小さく、切削厚みが小さいので、逃げ角は大きくする。被削材の強度と硬度が高い場合、切れ刃の強度を向上させるため、逃げ角を小さくする。
加工システムの剛性が低く、振動が発生しやすい場合は、フランク角を適切に小さくする必要がある。寸法工具(丸穴ブローチ、リーマなど)の場合は、再研磨の回数を増やし、工具の寿命を延ばすために、フランク角を小さく選ぶべきである。表4に超硬旋削工具の適正な逃げ角の参考値を示す。
表4 超硬旋削工具の適正フランク角の参考値
被削材 | 適度なフランク・アングル | |
荒いターン | ターニングの仕上げ | |
低炭素鋼 | 8°~10° | 10°~12° |
中炭素鋼 | 5°~7° | 6°~8° |
合金鋼 | 5°~7° | 6°~8° |
焼入れ鋼 | 8°~10° | |
ステンレス鋼(オーステナイト系) | 6°~8° | 8°~10° |
灰色の鋳鉄 | 4°~6° | 6°~8° |
銅および銅合金(脆性) | 6°~8° | 6°~8° |
アルミニウムおよびアルミニウム合金 | 8°~10° | 10°~12° |
チタン合金Rm ≤1.177GPa | 10°~15° |
(3) セカンダリークリアランス角度の選択
二次逃げ角の大きさは、通常逃げ角と同じです。ただし、パーティングツールのような特殊な工具では、工具強度を確保するために、α₀'=1°~2°を選択することができます。
(4) クリアランス面の形状
1) ダブルクリアランスアングル
図4aに示すように、刃先強度を確保し、逃げ面研削の作業負担を軽減するため、旋削工具の逃げ面には2重の逃げ角が研削されることが多い。
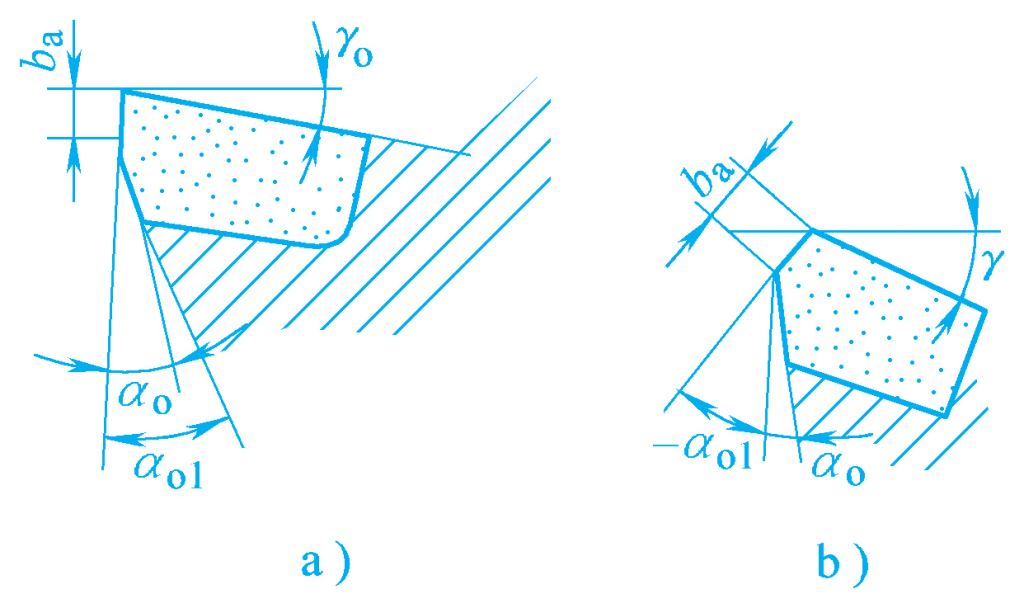
a) エッジバンド、ダブルクリアランスアングル
b) 振動減衰エッジ
2) 振動減衰エッジ
図4bに示すように、逃げ面とワークピースの移行面との接触面積を増やし、減衰性を高め、振動をなくすために、逃げ面に負の逃げ角のエッジを研削し、振動減衰エッジと呼ぶことができる。
3) エッジバンド
図4aに示すように、ブローチやリーマなどの一部の寸法工具では、外径寸法の制御を容易にし、再研磨後の寸法精度の急激な変化を避けるため、逃げ面に逃げ角0度の小さなエッジバンドを研削することが多い。工具上のエッジバンドは、工具を安定させ、ガイドし、減衰させる役割を果たす。エッジバンドは幅が広すぎてはならない。
3.主傾斜角と副傾斜角の選択
(1) 一次傾斜角と二次傾斜角の関数
主傾斜角Kr は切削力成分の大きさに影響する。Kr はFf を減少させる。p 力を与える。一次傾斜角は加工面の表面粗さに影響し、一次傾斜角を大きくすると表面粗さが大きくなる。主傾斜角は工具寿命にも影響し、主傾斜角が大きくなると工具寿命は短くなる。
一次傾斜角はワーク表面の形状にも影響する。段付きシャフトを旋削する場合、Kr =90°が選択される。細長いシャフトを回転させる場合、Kr =75°~90°が選択される。汎用性を高めるため、Kr =45°は、外径、端面、面取りの旋削に選択できます。
二次傾斜角Kを小さくするr 'であれば、副切刃と加工面との接触長さが長くなり、面粗さの値が小さくなり、工具寿命が向上する。ただし、副切刃の傾斜角度が小さすぎると振動の原因となる。
(2) 一次傾斜角と二次傾斜角の選択
一次傾斜角度を選択する原則は、加工システムの許容剛性の範囲内で小さめの一次傾斜角度を選択することであり、これは工具寿命の向上に有益である。生産現場では、表5に示すように、主に加工システムの剛性に基づいて一次傾斜角が選択される。
表5 主切刃角度の参考値
労働条件 | 主切刃角度 Kr | |||||
高いシステム剛性、小さな切り込み、大きな送り速度、高い被削材硬度 | 10°~30° | |||||
高いシステム剛性(l/d<6)、ディスク部品の加工 | 30°~45° | |||||
中程度のシステム剛性(l/d=6~12)、大きな切り込みまたは衝撃 | 60°~75° | |||||
低システム剛性(l/d>12)、段付きシャフトの旋削、溝加工、切断 | 90°~95° |
副切刃角度 Kr 主に加工性に基づいて選択されるが、一般的にはKr '=10°~15°、仕上げ加工では低い方を選ぶ。切削工具など特殊な場合は、工具強度を確保するため、Kr '=1°~2°を選択できる。
4.すくい角の選択
(1) すくい角の機能
1) 切りくずの流れる方向を制御する
図5に示すように、λs = 0°の場合、切り屑は刃先に対して垂直に流出し、λs が負の場合、切屑は加工面に向かって流れ、λs が正の場合、切屑は未加工面に向かって流れる。
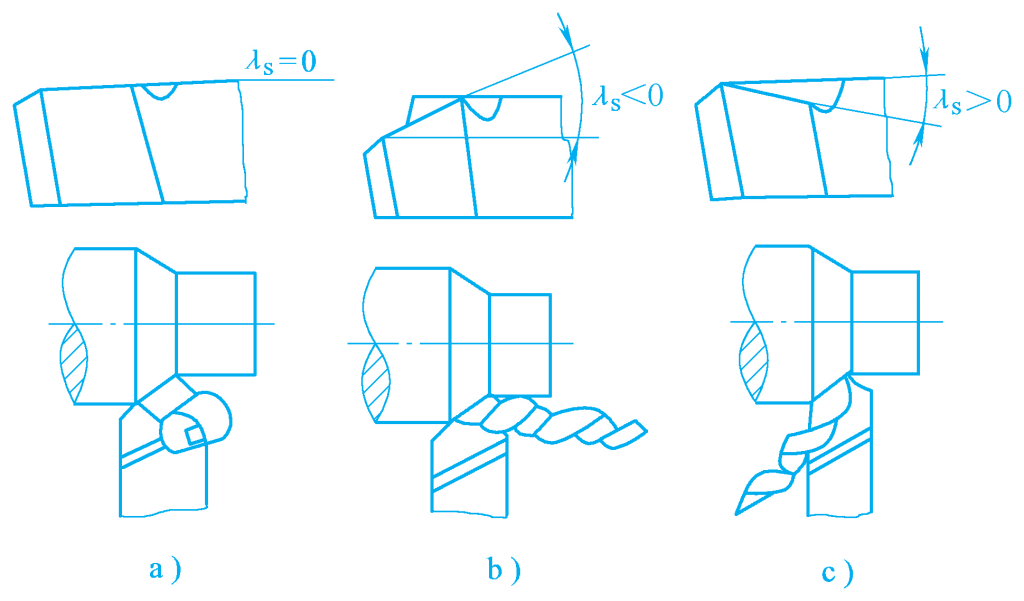
a)λs=0
b)λs<0
c)λs>0
2) 刃先と被削材の初期接触位置の制御
図6に示すように、断続面のある被削材を加工する場合、すくい角が負の場合、切れ刃の最下点が工具先端となり、被削材との最初の接触は工具先端ではなく、切れ刃またはすくい面上の点となるため、工具はある程度の衝撃荷重に耐えることができ、工具先端を保護することができる。すくい角が正の場合、被削材との最初の接触は工具先端となるため、チッピングや工具折損を引き起こす可能性がある。
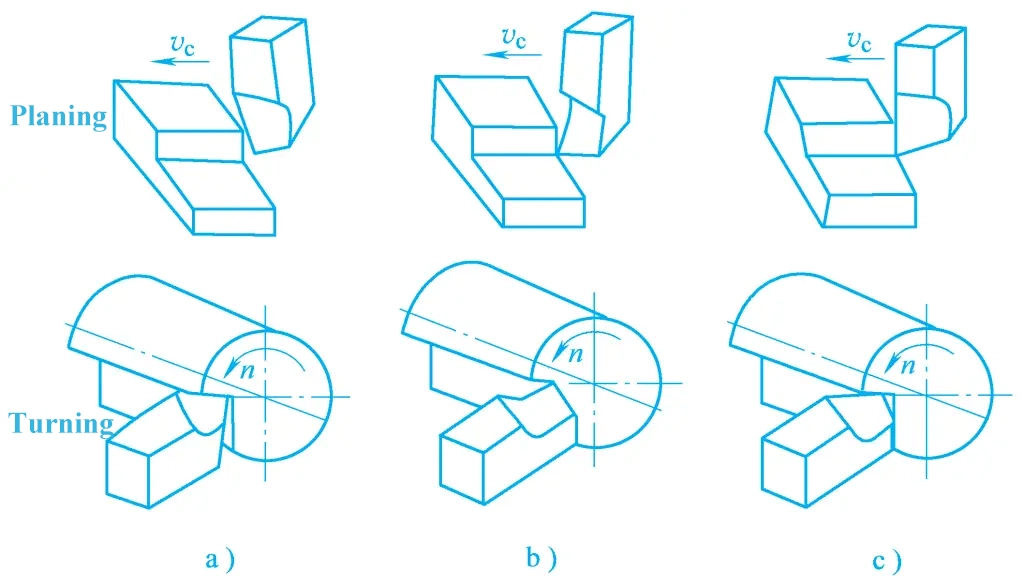
a)λs<0
b)λs>0
c)λs=0
3) ワークに出入りする際の刃先の安定性を制御する。
図6に示すように、断続切削では、すくい角がゼロの場合、切れ刃がワークと同時に接触・離脱するため、大きな振動が発生する。すくい角がゼロでない場合、切れ刃の各点が徐々にワークと接触・離脱するため、より安定した切削加工が可能になる。
4) ラジアル力と送り出し力の比率をコントロールする。
すくい角が正の場合、ラジアル力は減少し、送り力は増加する。すくい角が負の場合、ラジアル力は増加し、送り力は減少する。
(2) すくい角の選択
すくい角を選択する際には、工具の具体的な加工条件に応じて具体的な分析を行う必要がある。一般的には、加工特性に基づいて選択することができる。仕上げ加工では、λs = 粗面加工の場合、λs = 断続切削の場合、λs = 大きなすくい角の仕上げ鉋工具の場合、λs = 75°~80°.
5.ツールチップフォームの選択(トランジションエッジ選択)
切削加工中、工具先端の作業条件は非常に厳しく、強度が低い、放熱性が悪い、摩耗しやすいなどの問題がある。そのため、工具先端の強度を向上させ、工具先端の伝熱面積を増やすことが、工具全体の寿命を延ばす鍵となる。
(1) ストレート・トランジション・エッジ
図7aに示すように、遷移エッジ角Krε ≈ Kr /2、長さb ε ≈ (1/4~1/5) αp このタイプのトランジションエッジは、主に荒加工用工具や重切削用工具に使用される。
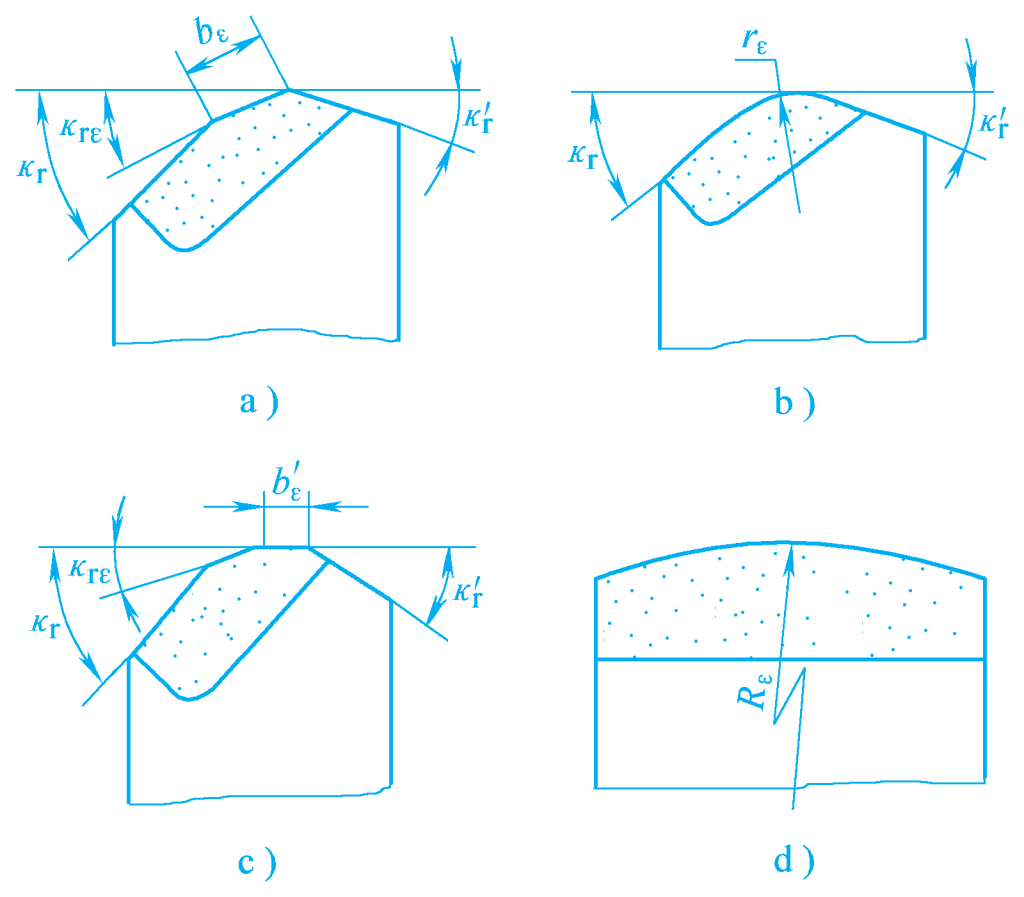
a) ストレートエッジ
b) アークエッジ(工具先端の半径)
c) パラレルエッジ(水平仕上げエッジ)
d) 大きなアークエッジ
(2) アーク遷移エッジ
図7bに示すように、移行エッジは円弧状に研削することもでき、そのパラメータは工具先端の円弧半径r ε .
工具先端の円弧半径が大きくなると、工具先端の平均主切刃角が小さくなり、面粗さの値を小さくして工具寿命を向上させることができるが、背分力が大きくなって振動が発生しやすくなるので、工具先端の円弧半径はあまり大きくしない方がよい。通常、高速度鋼旋削工具のrε = 0.5~5mm、超硬バイトrε = 0.5~2mm。
(3) 水平仕上げエッジ
図7cに示すように、フィニッシュ・エッジは小さな平行エッジで、Kr '=0°は副切刃の工具先端付近で研削される。その長さb≈(1.2~1.5)f、すなわちbε 'は、送り速度fよりもわずかに大きくなければならない。ε が大きすぎると振動の原因になりやすい。
(4) 大きなアークエッジ
図7dに示すように、大円弧エッジは非常に大きな円弧形状に研磨されたトランジション・エッジであり、その機能は水平仕上げエッジと同等である。
6.切りくず溝形状と切りくず処理
金属切削加工において、切屑形状や切屑の流れ方向の制御を研究することは、特に自動工作機械や自動生産ラインにおいて、正常な生産秩序を維持し、作業者の安全を確保するために非常に重要である。特に自動工作機械や自動生産ラインでは、切屑の折れやカールの問題は、より注意を払うべきであり、そうでなければ正常な生産秩序に影響を与える。
(1)チップのカーリングと流れ方向
1) チップカール
切りくずのカーリングは、切りくずの内部変形、または切りくずを破壊する溝、ボス、工具のすくい面に研削された追加ブロック、その他の障害物に遭遇することによって引き起こされる。
2) 切りくずの流れ方向
切りくずの流れ方向は、主に切れ刃の傾斜角度に影響される。詳しくは前節の切れ刃傾斜角の選定を参照されたい。
(2)チップの破損原因とチップ形状
1) チップは流動過程で障害物に遭遇し、曲げモーメントによって破壊される。
図8aに示すように、チップがチップカーリングステップに遭遇すると、力Fを受け、曲げモーメントが形成され、大きな曲げ応力が発生し、チップカーリンググルーブで破断する。図8bに示すように、曲げ応力がチップを破断させる極限応力に達しない場合、チップは曲げ変形後に方向を変えて移動を続ける。
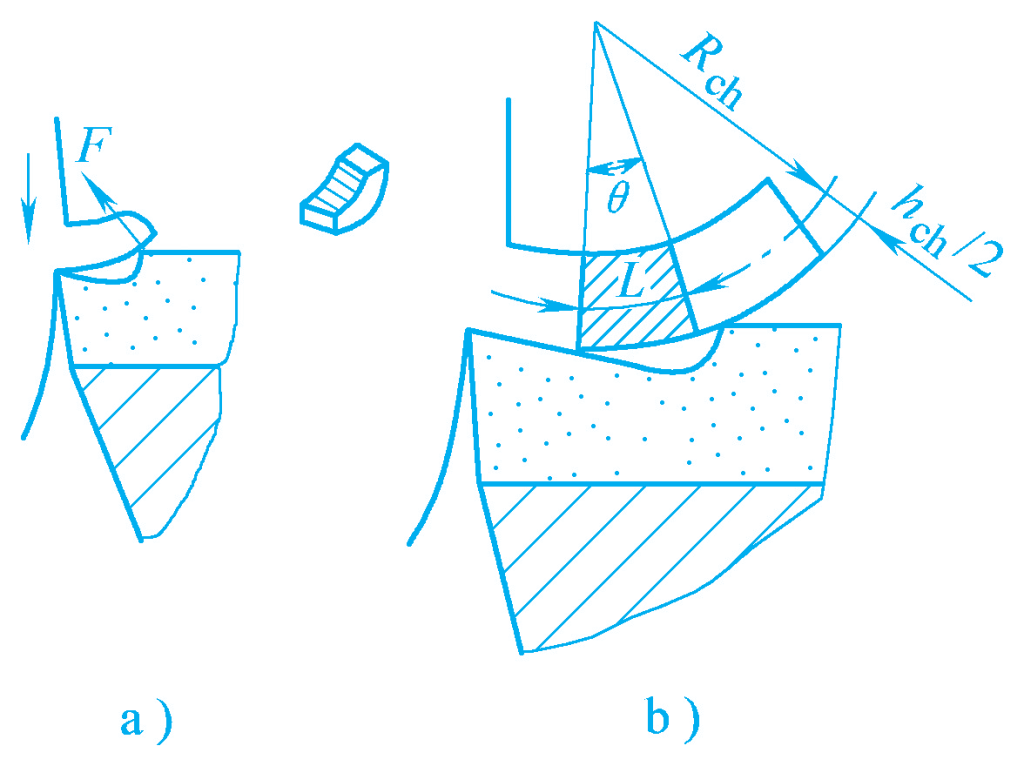
a) 力Fによって破損したチップ
b) 曲げ応力
図9は、カーリング運動中に加工されるワークの表面に遭遇し、曲げ応力を形成する反力を受けて、「C」形状の切り屑に破壊される切り屑を示し、図10は、ワークの移行面に遭遇した後に円形のカーリング切り屑を形成する切り屑を示し、図11は、工具の逃げ面に遭遇した後に「C」形状または「6」形状の切り屑に破壊される切り屑を示す。
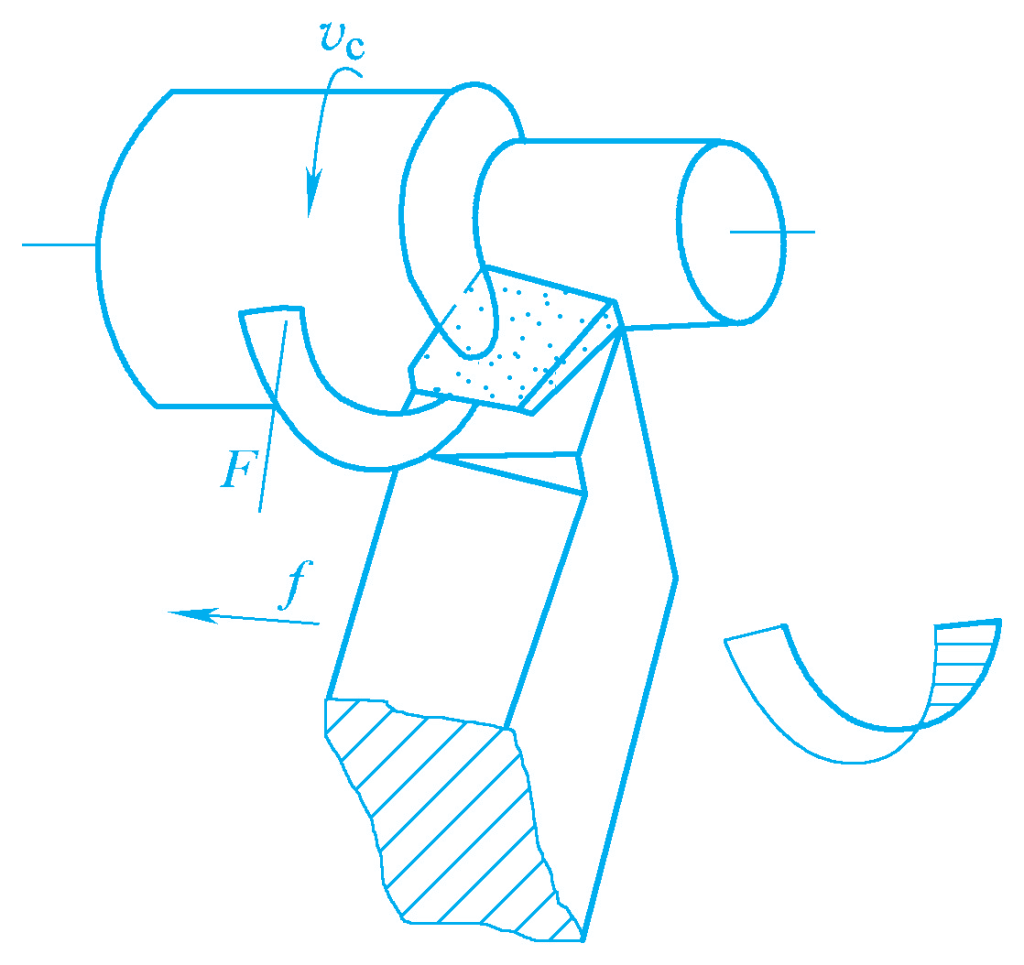
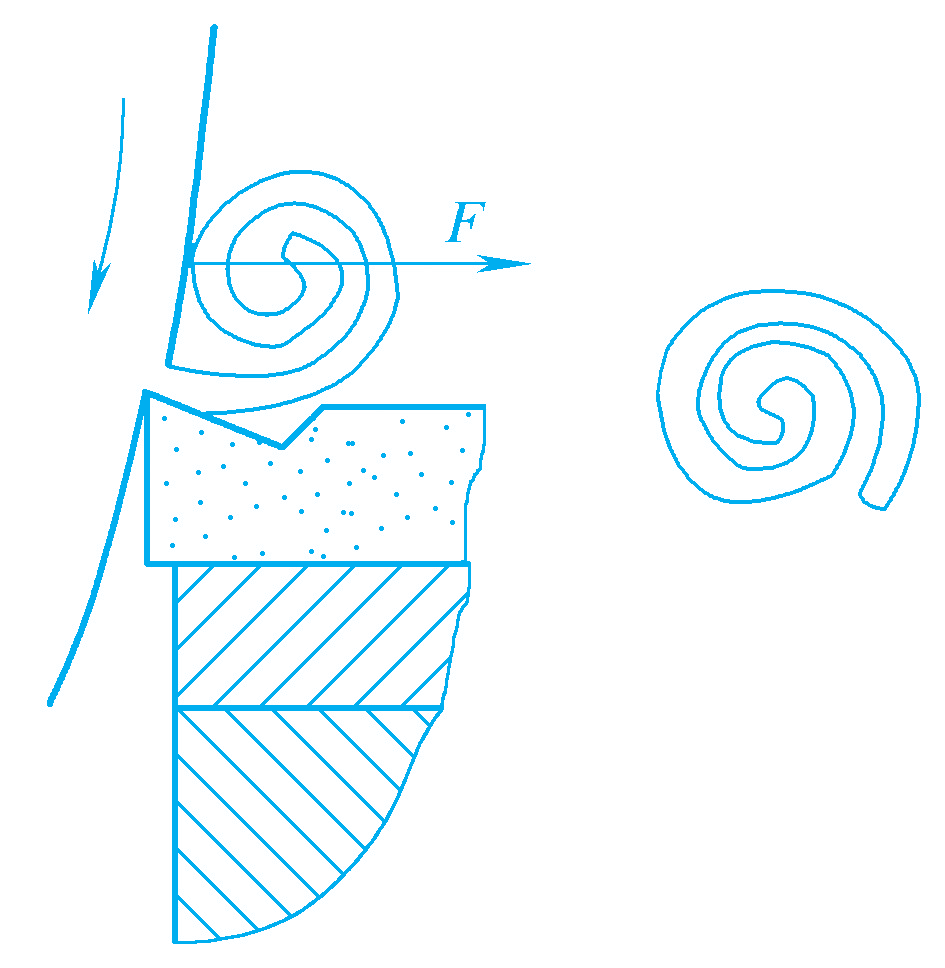
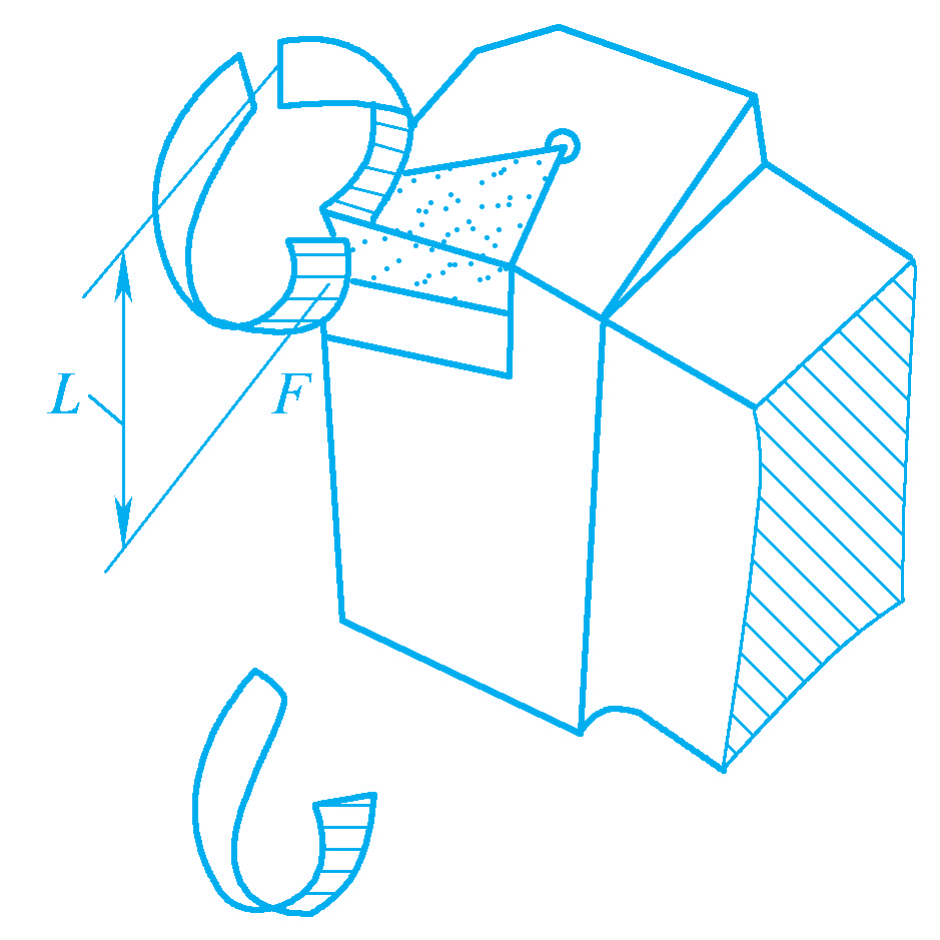
2)チップは流動過程で自重により破壊される。
切屑が工具や被削材に接触せずにすくい面から流出すると、長い帯状の切屑になったり、図12、図13に示すように、切屑カール溝で螺旋状の切屑を形成した後、自重で折損したりする。
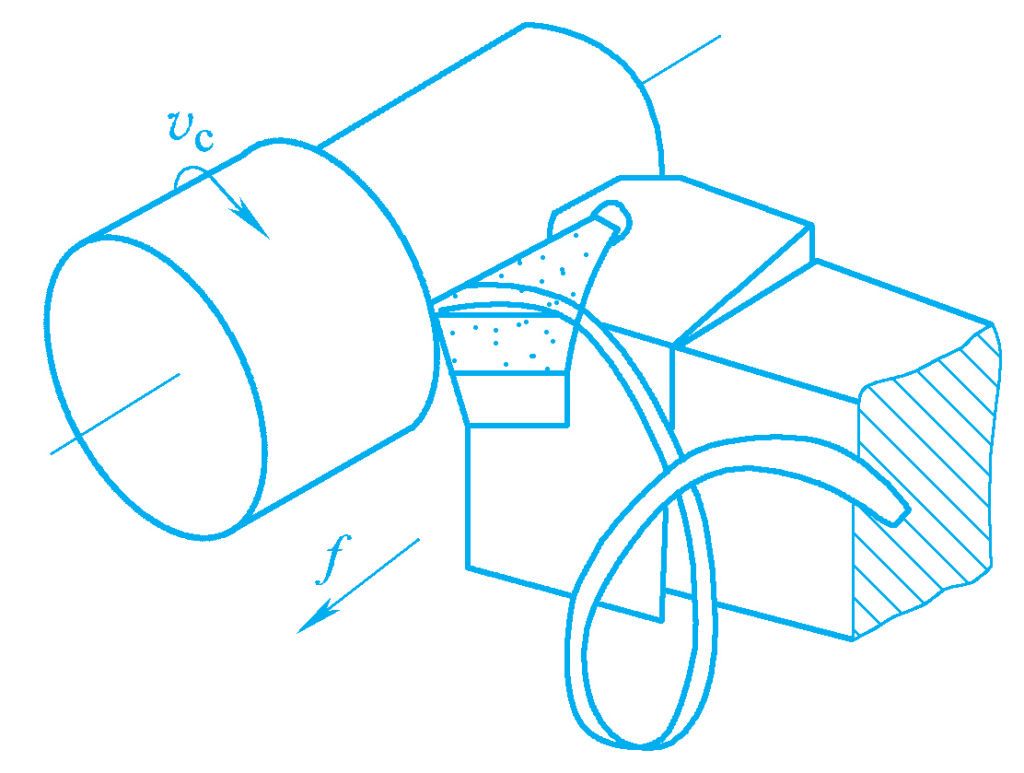
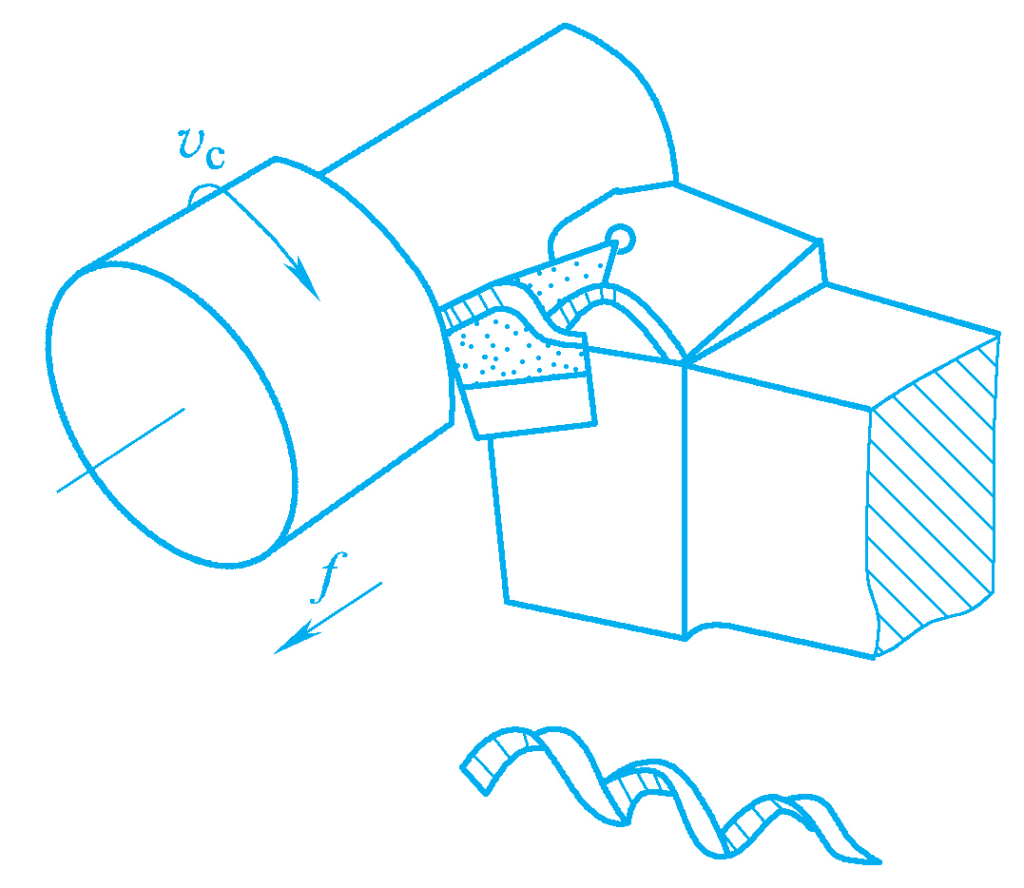
上記の切り屑の中で、一般的に理想的とされているのは、「C」型切り屑、「6」型切り屑、短い螺旋状切り屑である。このうち、工具の逃げ面に衝突して折損する「C」字型の切屑は、安定性と信頼性が高く、方向性を持って落下し、高速回転する被削材と衝突しないため、切屑の飛散を避けることができる。しかし、切削力にはわずかな変動があり、被削材の表面粗さ値を下げるには不利である。
自重で折れる短いヘリカルチップは、切削力が比較的安定しているのが特徴で、被削材の表面粗さの低減に役立つ。ただし、あまり長いと(60~40mm程度)、作業や切りくずの排出に支障をきたすので、あまり長くならないようにする。
自動工作機械や自動生産ラインでは、ヘリカルチップの長さを管理することが特に重要です。さもなければ、切りくずがワークや工具に巻き付き、正常な生産に影響を及ぼす。重切削加工では、切り込み量と送り速度が大きいため、「C」字型の切り屑は怪我を引き起こしやすいので、バネ状の切り屑を生成することが望ましい。切削中に生成されるさまざまな切りくず形状を図14に示す。
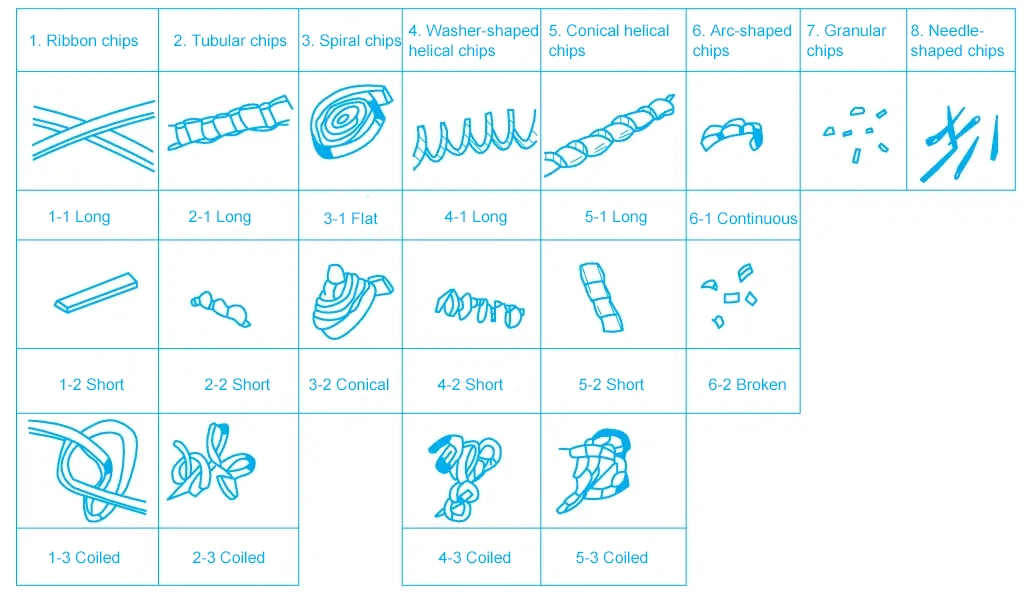
(3) チップ破損に影響する要因
1)チップグルーブ(チップブレーカーグルーブ)
切屑溝の一般的な断面形状は、図15a、図15b、図15cに示すように、折れ線、直線円弧、完全円弧である。切屑溝の幅lnが小さいほど、切屑のカール半径が小さくなり、曲げ応力が大きくなり、切屑が切屑溝内や被削材に衝突した後に折れやすくなる。
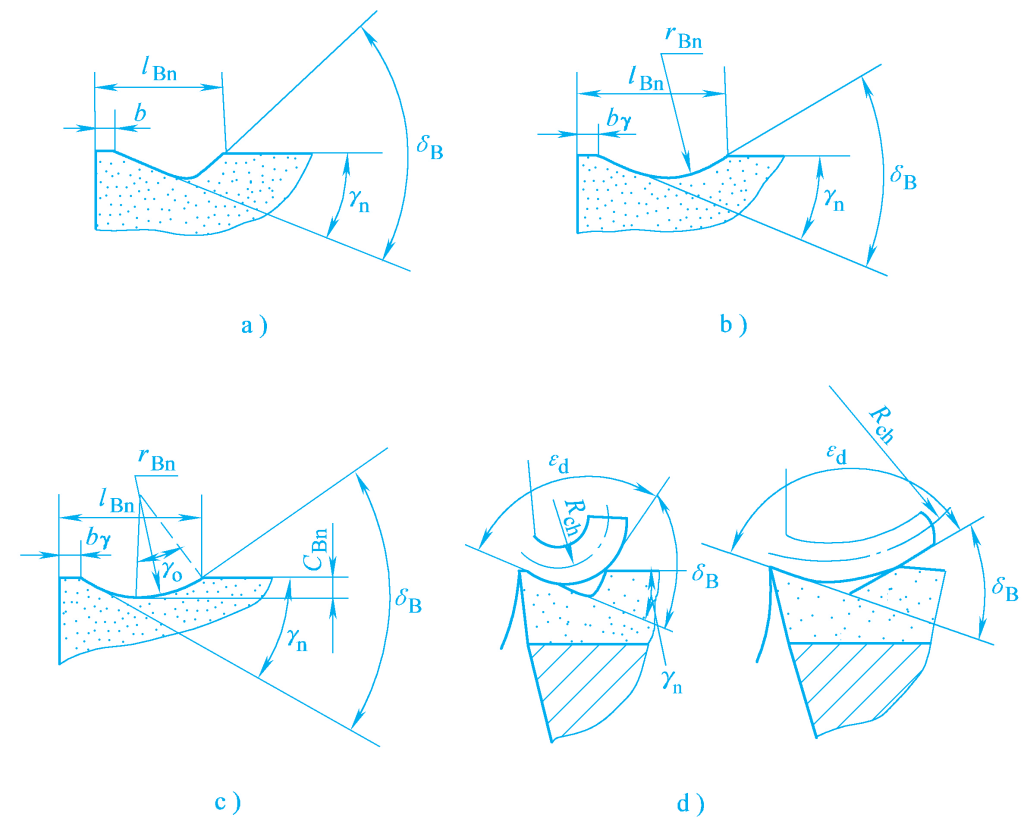
a) 折れ線形状
b) 直線弧状
c) フルアーク形状
d) チップ角度δの影響 B Rについて ch
しかし、小さすぎると切り屑の溝スペースが狭くなり、切削抵抗が増大し、切り屑詰まり、刃先チッピング、切り屑飛散などの好ましくない現象につながるため、小さすぎないことが望ましい。そのため、切りくず溝の幅は、被削材の材質や切削パラメータなどの具体的な加工条件に基づいて決定する必要がある。一般に、送り速度、切り込み深さ、主切刃の角度が大きいほど、また被削材の塑性と靭性が小さいほど、切りくず溝の幅は大きくする必要があり、その逆も同様である。
溝幅に加えて、チップ角度δ B もまた、切屑の破断に影響する大きな要因である。切り屑の角度が大きくなると、切り屑は破断しやすくなるが、切り屑のカール半径R ch は減少し、図15dに示すようにカール変形と曲げ応力が増加する。
切り屑の角度が大きすぎると、切り屑詰まりの原因となり、切削抵抗と切削温度が上昇する。さらに、切屑溝の円弧半径r ブン チップの破壊効果にも影響する。
チップ溝の傾斜角度ρ Bλ は、切屑溝の側面と主切刃とのなす角である。切りくずの流れ方向や切りくずの形状に影響する。一般的な切屑溝の傾斜角度は、図16に示すように、外傾斜、平行、内傾斜である。
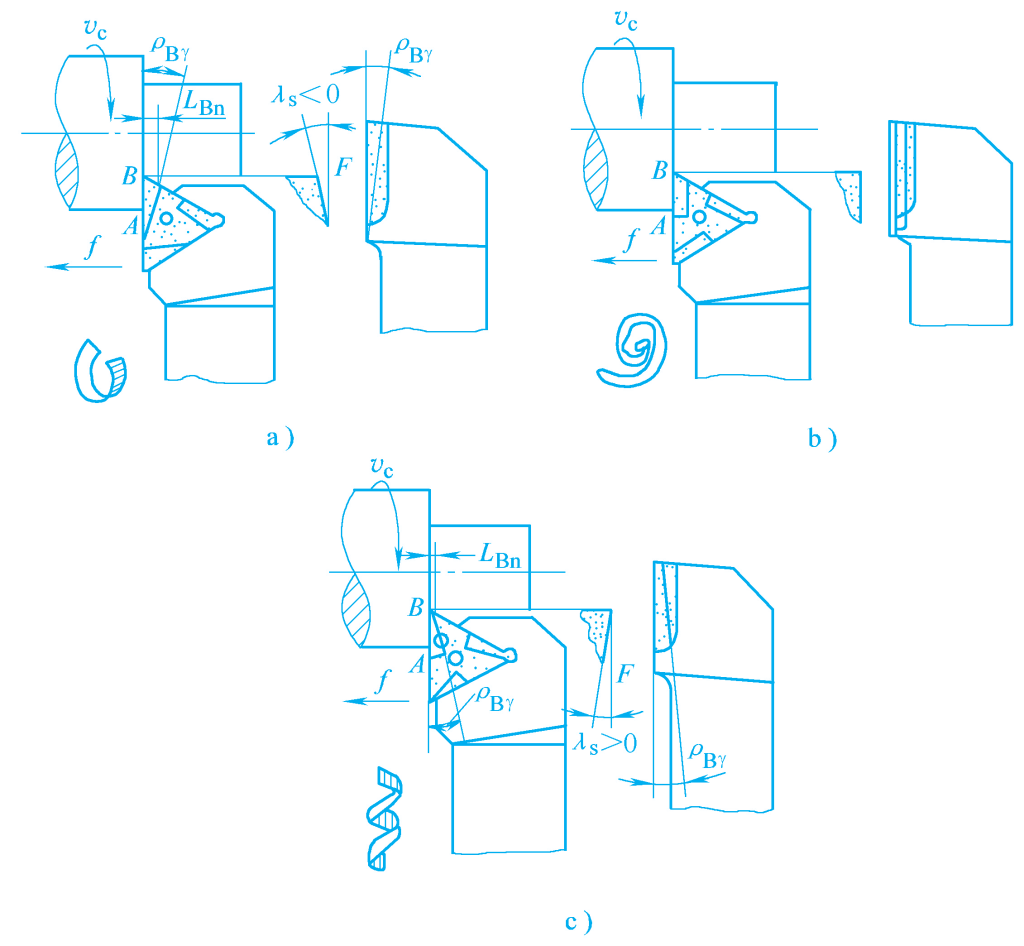
a) 外部傾斜
b) パラレル
c) 内部傾斜
外形傾斜の主な特徴は、チップ溝の幅方向は手前が広く奥が狭く、深さ方向は手前が深く奥が浅いことである。溝のA点では、切削速度が速く、溝幅が狭いため、切屑が最初に小さな半径でカールする。溝のB点では、切りくずはよりゆっくりとカールする。溝底の負のすくい角により、切屑は加工面に向かって流れ、衝突後に「C」または「6」字型の切屑が形成される。
外傾斜は切屑分断範囲が広く、安定した確実な切屑分断が可能です。内傾チップ溝は、B点で狭く、A点で広くなっており、B点の切りくずが最初に小さな半径でカールします。溝底の正のすくい角により、切りくずはワークから離れる方向に流れ、きつく巻かれたらせん状の切りくずが形成され、一定の長さに達すると自重で折れます。
主に切削パラメータが小さい精密旋削や準精密旋削に適しているが、切屑分断範囲は大きくない。平行切屑溝は、切屑分断範囲と効果が外傾と似ており、切込み深さが大きく変化する場合に適している。
2) 工具形状
工具形状の角度のうち、主切刃角とすくい角は切りくずの分断と切りくずの流れ方向に大きな影響を与える。主切刃角が大きいほど、切削厚みが大きくなるため、切りくずがカールする際の曲げ力が大きくなり、切りくずの分断が容易になる。そのため、生産時に切屑の分断をよくするためには、主切刃角を大きく選択することができる。 r = 75°~90°.
前述したように、すくい角λ s は、切屑の流れ方向を制御するための重要なパラメータである。すくい角が負の場合、切屑は加工面または移行面に向かって流れ、ワークと衝突した後に「C」または「6」形状の切屑に分断される。すくい角が正の場合、切り屑は未加工面またはワークから離れる方向に流れ、「C」字型の切り屑や、場合によってはヘリカル状の切り屑が形成されます。
3) 切削パラメータ
送り速度を増加させると、それに比例して切削厚さが増加し、切りくずのカール半径が減少し、曲げ応力が増加し、切りくずが破断しやすくなる。したがって、送り速度を上げることは、切屑の分断に比較的有効な手段である。
4) 被削材
被削材の塑性、靭性、強度が高ければ高いほど、切り屑を破砕するのは難しくなる。
切屑処理とは、切屑の流れ方向、カール、破断、切屑形状の制御を含む総合的な問題である。生産においては、一次的な関係と二次的な関係を総合的に区別し、様々な要因が切りくず制御に与える影響を考慮する必要がある。
一般的には、被削材と選択された工具角度と切削パラメータに基づいて、チップブレーカ溝のサイズパラメータを決定する。他の条件に制限されない場合にのみ、主偏向角、すくい角、送り速度などのパラメータを調整し、試切削を通じてより理想的な切りくず処理効果を得る。
IV.切削パラメータの合理的な選択
いわゆる "合理的な "カッティング・パラメーターとは、以下の3つの最適な組み合わせを指す。 カッティングエレメント 工具と工作機械の効率をフルに活用し、加工品質を維持しながら、高い生産性と低い加工コストを確保できる。
3つの切削要素v、f、aは、加工品質、工具寿命、生産性に直接的な影響を与えるが、その程度は様々である。これらは相互に関連し、相互に制約を受けるため、すべてを最大値で選択することは不可能である。そのため、様々な観点からどの要素を最大にすべきかの優先順位をつける必要がある。
1.切削パラメータ選択の基本原則
- 加工代と荒加工/仕上げ加工要件に基づいて、切込み ap を選択する。
- 工作機械の送りシステム、ワークの剛性、仕上げ加工時の表面粗さ要件など、加工システムの許容切削力に基づいて送り速度fを決定する。
- 工具寿命に基づいて切削速度veを決定する。
- 選択した切削パラメータは、工作機械の許容出力の範囲内でなければならない。
2.合理的な切断パラメータの選択方法
(1) カットの深さを決める
一般的に、切込みaは加工の性質と加工代に基づいて決定される。
切削加工は一般的に荒加工(表面粗さRa50~12.5μm)、中仕上げ加工(Ra6.3~3.2μm)、仕上げ加工(Ra1.6~0.8μm)に分けられる。
荒加工では、工作機械の剛性が許せば、荒取り代をできるだけ1パスで除去してパス数を減らし、中仕上げと仕上げの取り代を残す。超硬工具を中出力の工作機械で外旋加工に使用する場合、荒加工の切り込みaは2~6mm、中仕上げの切り込みaは0.3~2mm、仕上げの切り込みaは0.1~0.3mmである。
以下のような場合、荒加工は複数回に分けて行うべきである:
- 細身のシャフトや薄肉部品を加工する場合や、加工代が極端に不均一で振動が大きい場合など、加工システムの剛性が低い。
- 加工代が大きすぎる場合、1パスで除去すると切削力が過大になり、工作機械のパワー不足や工具の強度不足につながる。
- 断続切削中、工具は大きな衝撃を受け、工具破損の原因となる。
上記の場合でも、最初のパスまたは最初のパスの切込み深さ ap は大きくする必要がある。2回のパスが必要な場合、最初のパスは一般に加工代の2/3から3/4を要する。
(2) 送り速度の決定
1) 表面品質の要求が高くない荒加工では、送り速度fの選択は主に切削力によって制限される。工具ホルダー、ワークの剛性、チップと工作機械の送り機構の強度が許せば、大きな送り速度を選択すべきである。
2) 中仕上げおよび仕上げ加工では、切り込みが比較的小さく、発生する切削力が大きくないため、送り速度の選択は主に表面粗さの要件によって制限される。
工具が適度な移行刃と仕上げ刃を持ち、高い切削速度を使用する場合、生産性を向上させるために送り速度fを適切に増加させることができる。しかし、fを小さくしすぎると、生産性が低下するだけでなく、切りくずの厚みが不足して加工品質に影響を及ぼすので、fは小さくしすぎないようにする。生産現場では、経験に基づいて、あるいはテーブルを参照して送り速度を選択することが多い。
(3) 切削速度の決定
工具寿命T、切り込みa、送り速度fが決まれば、関連する計算式を使って切削速度を算出することができる。生産現場では、経験に基づいて、または関連する切削パラメータのマニュアルを参照して決定されることが多い。
切削速度を決定した後、スピンドル速度nを計算することができます:
n=1000vc/(πdw)
式の中で:
- d - ブランクの直径(mm);
- v - 切削速度(m/min);
- n - スピンドル速度(r/min)。
選択された速度は、工作機械のマニュアルに従って最終的に決定されるべきであり(下限と類似の工作機械の速度nを取る)、次に実際の切削速度は、選択された速度に従って計算されるべきである。
切削速度を選択する際には、以下の点も考慮する必要がある:
- 仕上げの際、盛り上がりやバリの発生はできるだけ避けるべきである。
- 断続加工中は、衝撃と熱応力を軽減するために、切削速度を適切に下げることが望ましい。
- 大きなワーク、細長いワーク、薄肉のワークを加工する場合は、切削速度を低めに選ぶべきである。フェースターニングの切削速度は、平均切削速度を上げて生産性を向上させるために、外筒ターニングの切削速度よりも高くする必要がある。
- 振動が発生しやすい状況では、切削速度は自励振動の臨界速度を避けるべきである。
実際の生産では、切断パラメータは主に工程マニュアルとオペレーターの実務経験に基づいて選択される。