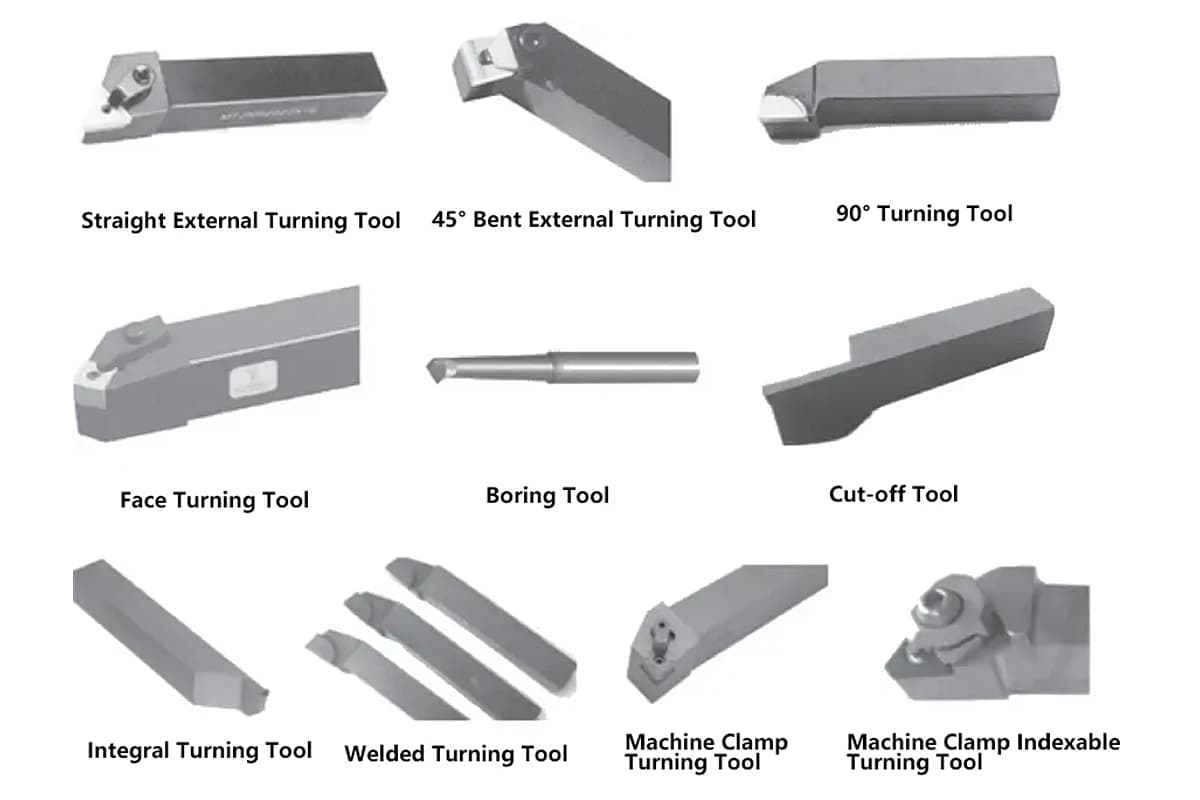
I.旋盤用治具
1.旋盤治具の種類と特徴
旋盤は主に、部品の内外円筒面、円錐面、回転成形面、ねじ面、端面の加工に使用される。これらの加工特性と工作機械上の固定具の位置に基づいて、旋盤用固定具は次の2つの基本タイプに分けられる:
(1) 旋盤主軸に取り付けた治具
この種の固定具では、さまざまなチャック、面板、センター、その他の一般的な固定具や工作機械の付属品に加えて、加工ニーズに応じてさまざまなマンドレルやその他の特殊な固定具を設計することができる。加工中、フィクスチャーは旋盤スピンドルと一緒に回転し、工具は送り運動を行う。
(2) 旋盤サドルに取り付けた治具
不規則な形状や大きなワークピースの場合、フィクスチャーは旋盤のサドルに取り付けられることが多い。工具は回転運動のために旋盤主軸に取り付けられ、固定具は送り運動を行う。本節では、旋盤主軸に取り付ける最も広く使用されている旋盤用特殊治具を主に紹介する。
2.特殊旋盤用治具の代表例
生産現場では、ハウジング、ブラケット、レバー、ジョイントなどの部品の円筒面や端面を、以下のような状況で使用することがよくあります。 旋盤加工.これらの部品は複雑な形状をしていることが多く、3つ爪のセルフセンタリングチャックでワークを直接クランプするのは難しい。このような場合、特別な旋盤用固定具を設計する必要がある。以下に代表的な旋盤用治具をいくつか紹介する。
(1) アングル・アイアン固定具
図1はアングルアイアン旋盤用固定具である。ワークの位置決めは、冶具の傾斜した位置決め支持板上と、円筒ピンとダイヤモンドピンの1面2穴を位置決め基準とし、フック状の2枚の加圧板でクランプする。
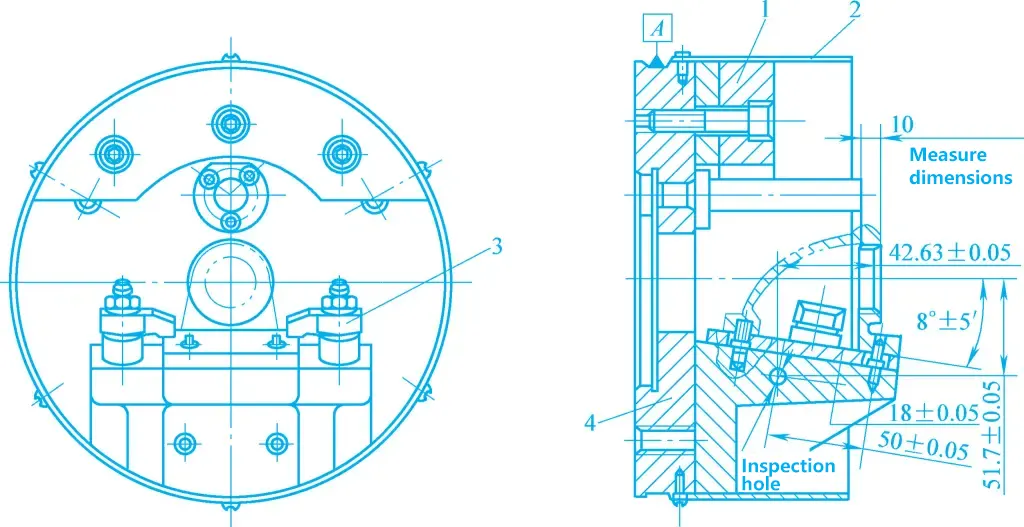
1-バランス・ブロック
2-保護カバー
3フック型プレッシャープレート
4-器具本体
加工面は穴と端面である。加工端面の寸法や加工穴と位置決め基準面との角度を加工中に検査しやすくするため、加工面の近傍に測定基準面と加工穴を設計する。治具本体4上の基準円Aは位置合わせ円である。
(2) フェースプレート固定具
図2にギヤポンプハウジングの加工工程図を示す。ワークの外円Dと端面Aは加工済みである。加工面は2つのΦ35mm穴、端面T、穴底面Bであり、部品図に指定された関連技術要件を満たす必要がある。2つのΦ35mm穴の直径精度は主に加工方法の正確さに依存し、その他の技術要件は固定具によって確保されます。
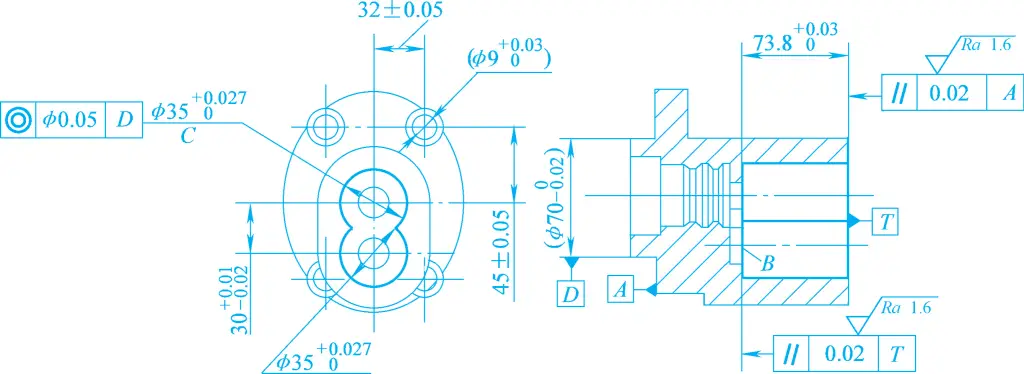
図3はギヤポンプハウジングの2つのΦ35mm穴加工に使用した特殊面板治具である。端面A、Φ70mm外円周面、小穴Φ9mm内円周面を位置決め基準としてワークを位置決めし、ターンテーブル2のN面、Φ70mm円形穴、トリミングピン4に2組のスパイラル加圧板5でクランプする。
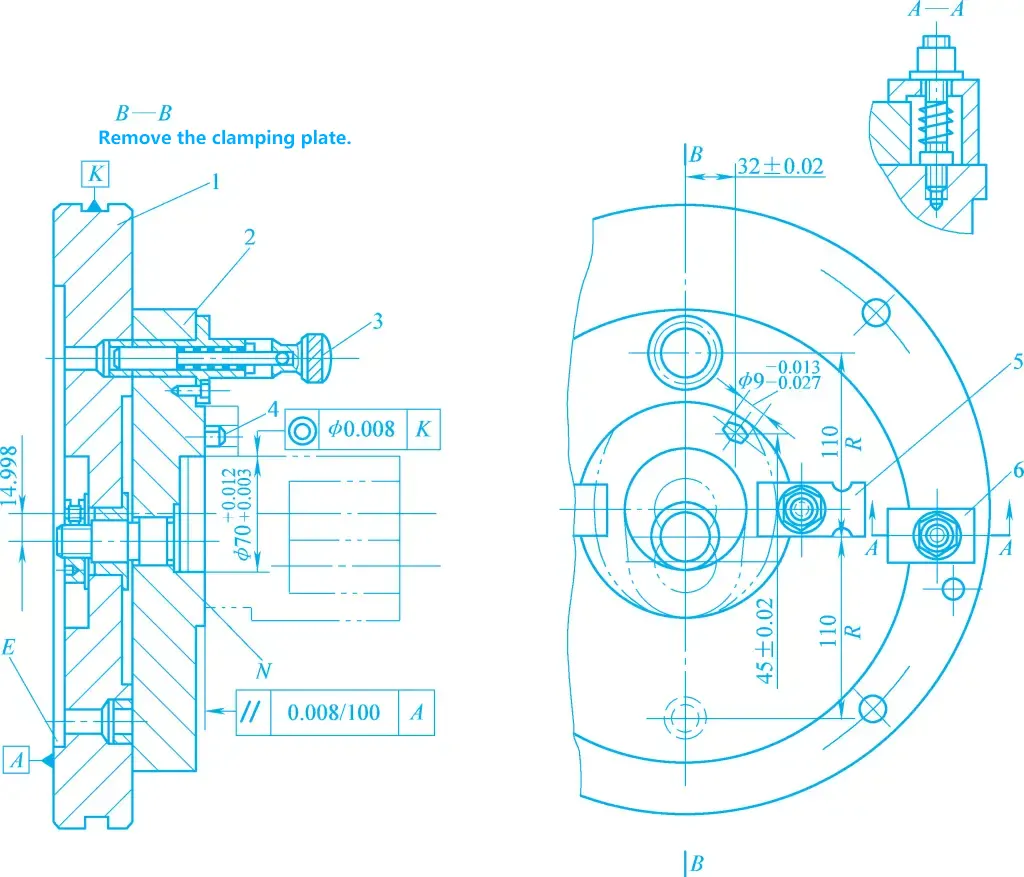
1-器具本体
2ターンテーブル
3-アライメントピン
4トリミングピン
5、6-圧力プレート
ターンテーブル2は、2組の螺旋状プレッシャープレート6によって固定具本体1にクランプされている。Φ35mmの穴の一つを加工した後、アライメントピン3が引き抜かれ、2組の螺旋状プレッシャープレート6が緩められる。ターンテーブルはワークピースと共に180°回転し、アライメントピンはバネの力で固定具本体の別の割り出し穴に挿入される。ターンテーブルをクランプした後、2つ目のΦ35mmの穴を加工することができる。
この特別な固定具は、固定具本体のラベットEを使用して、トランジションプレート上のフランジを介して旋盤スピンドルと接続します。フィクスチャーを取り付ける際、アライメントサークルK(フィクスチャーの回転軸を表す)を使用して、フィクスチャーと旋盤スピンドルの同軸度を合わせます。
(3)センタリングクランプ治具
回転ワークピースや回転面によって位置決めされるワークピースには、センタリングクランプ治具を使用することができます。一般的なタイプには、スプリング・スリーブや液体プラスチック固定具がある。図4に示す固定具では、ワークピースは液体プラスチック固定具を使って内孔によって位置決めされ、クランプされている。
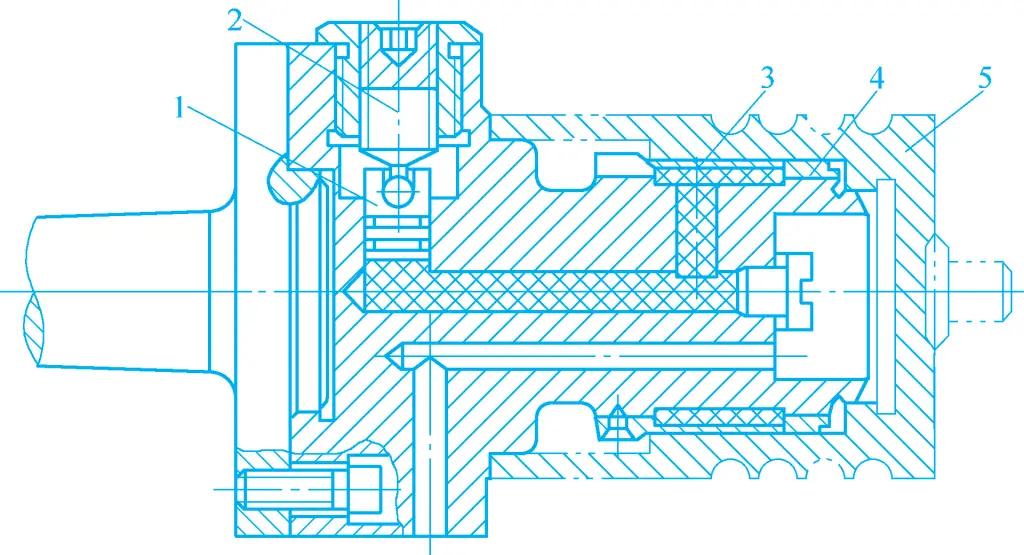
1-スライド式コラム
2-コンプレッションスクリュー
3液プラスチック
4薄肉ポジショニング・スリーブ
5-ワークピース
ワークは、端面を軸に位置決めされた位置決めシリンダ上に載置される。コンプレッションスクリュー2を回転させることにより、スライドコラム1と液状プラスチック3が薄肉の位置決めスリーブ4を変形させ、ワーク5をセンタリングしてクランプする。
(4) モジュラー・フィクスチャー
モジュラー・フィクスチャーは、特別なものである。 組立式 設計された位置決めとクランピング・スキームに従って、あらかじめ製造された標準フィクスチャー・コンポーネントから作られます。特殊なフィクスチャーの利点と標準化・汎用化の利点を兼ね備えています。製品変更後、フィクスチャー・コンポーネントは分解、洗浄、保管が可能で、無駄を省くことができます。新製品の試作や多品種少量生産に適しています。
を広く使用する現代企業における機械製品の生産において、ユニークな利点がある。 CNCマシン 工具を使用し、CAD/CAM/CAPP技術を適用する。図5は典型的な旋盤用モジュラー治具である。ワークピースは、加工された底面と2つの位置決め穴を使って位置決めされ、2枚のプレッシャープレートでクランプされる。冶具本体、位置決めピン、プレッシャープレート、ベースはすべて標準部品である。
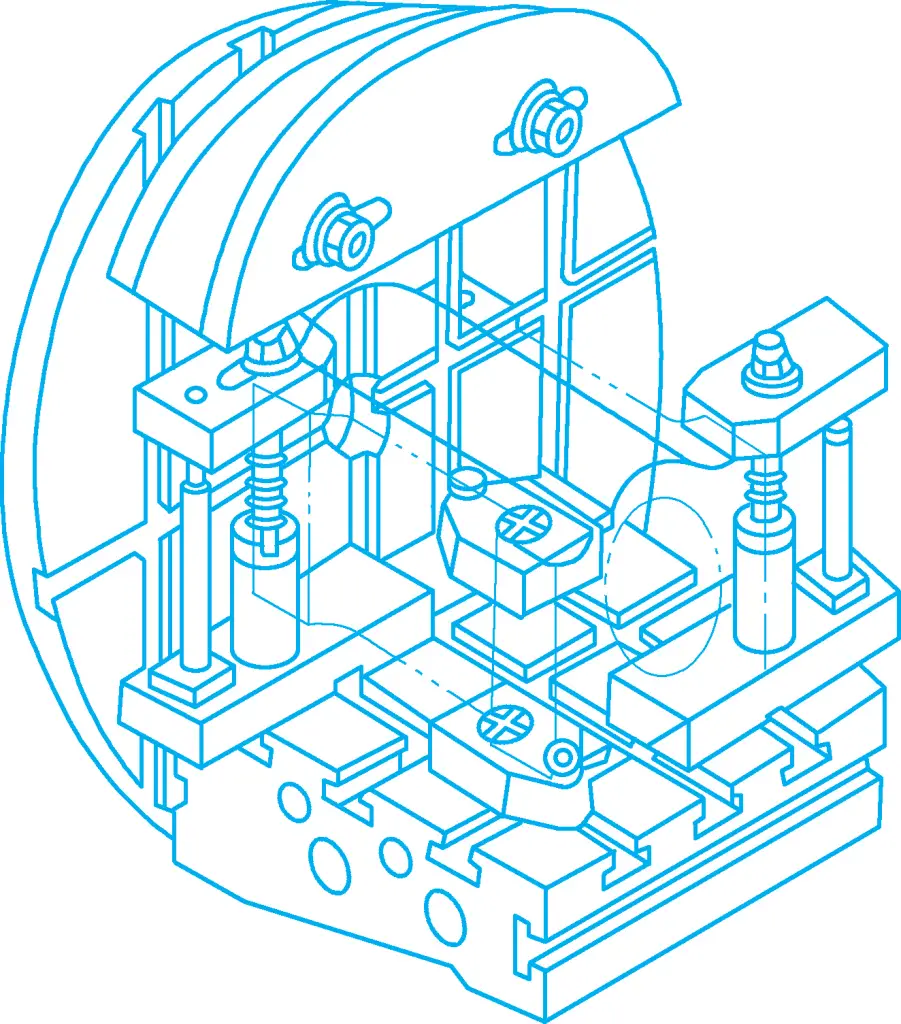
3.旋盤用治具の構造的特徴
(1) 位置決め装置
旋盤で回転面を加工する場合、工作物の回転面の軸は旋盤主軸の回転軸と一致しなければならない。冶具上の位置決め装置の構造と配置は、これを確実にしなければなりません。
(2) クランプ装置
旋削加工中、ワークピースと固定具はスピンドルと一緒に回転するため、固定具は加工中の切削トルクに加えて遠心力を受ける。回転速度が高いほど遠心力は大きくなり、クランプ機構のクランプ効果に影響を与える可能性がある。
さらに、切削力の方向や重力に対するワークの位置決め基準の位置も変化する。そのため、クランプ機構が発生するクランプ力は十分でなければならず、加工中にワークが位置決め要素から外れないようにするためには、セルフロック性能が良好でなければならない。
(3) 旋盤冶具と機械主軸の接続
固定具の回転軸は、旋盤スピンドル軸と可能な限り高い同軸精度を持たなければならない。旋盤冶具のラジアルサイズに応じて、一般的に次の2つがあります。 接続方法 機械主軸と
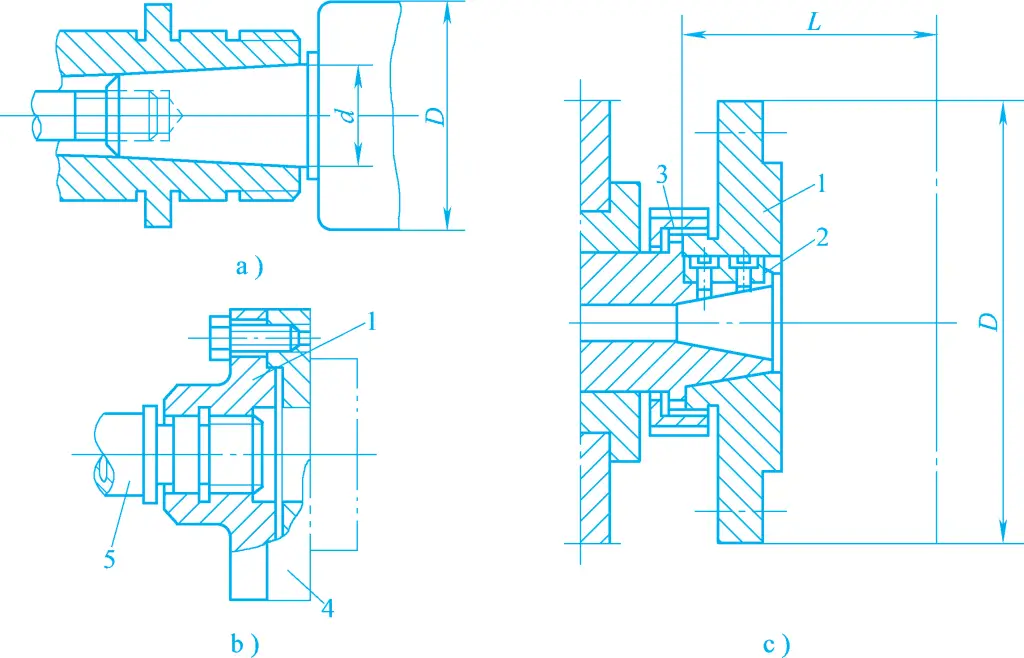
1-トランジションプレート
2-フラットキー
3ナット
4-フィクスチャー
5スピンドル
1) ラジアル寸法D<140mm、またはD<(2~3)dの小型治具の場合、接続構造を図6aに示す。一般的には、旋盤主軸のテーパー穴にテーパーシャンクを介して取り付け、ボルトロッドで締め付ける。この連結方式は芯出し精度が高い。
2) より大きなラジアル寸法の治具には、旋盤主軸の前端に接続するトランジション・プレートを使用する。トランジションプレートの構造を図6bと図6cに示す。トランジション・プレートの一端は機械主軸に接続され、相手面の形状は主軸前端の構造に依存する。もう一方の端は、通常、治具本体の位置決めショルダーと嵌合するフランジを有し、スピンドル上での治具のセンタリングを実現する。
旋盤用取付具の取付具本体は、一般に、図1及び図3に示すように、アライメント穴又はアライメント円を有するべきである。アライメント穴または円は、旋盤主軸に旋盤固定具を取り付ける際の同軸性を確保するためのアライメント基準として機能し、旋盤固定具の製造および組立の際の組立基準としても機能する。また、治具本体の機械加工時の工程基準にもなることが多い。
旋盤の固定具は、回転アンバランスの問題を解消するはずである。バランスをとる手段のひとつは、軽い側にバランスブロック(カウンターウェイト)を追加することであり、もうひとつは、重い側に重量を減らす穴を加工することであり、あるいはその両方を組み合わせることである。バランス・ブロックの位置と重量は、調整可能であることが望ましい。
安全なオペレーションを確保するために、フィクスチャーはできるだけ鋭利なコーナーやフィクスチャー・ボディの円形の輪郭からはみ出したコンポーネントを持たないようにしてください。必要であれば、保護カバーを追加すべきである。さらに、クランプ装置のセルフ・ロック性能は、回転中に緩んでワークが飛び出すことを防ぐために信頼できるものでなければならない。
II.フライス盤治具
1.フライス盤治具の種類と特徴
フライス盤用治具は、送り方法の違いにより、直線送りタイプ、円送りタイプ、テンプレートタイプに分けられる。このセクションでは、主に最初の2つのタイプを紹介します。
(1) リニアフィード式フライス盤治具
これらの固定具は一般的にフライス盤のワークテーブル上に設置され、加工中、固定具はワークテーブルと共に直線的に移動する。一度にクランプされるワークピースの数によって、単一ピースのフライス盤用固定具と複数ピースのフライス盤用固定具に分けられる。
シングル・ピース・フィクスチャは、小ロット生産でより一般的に使用されるが、マルチ・ピース・フィクスチャは、小~中サイズの部品の大量生産で広く使用される。図8は、図7に示したセンター・スリーブにダブル・スロットを加工するためのダブル・ピース・フライス盤用治具である。

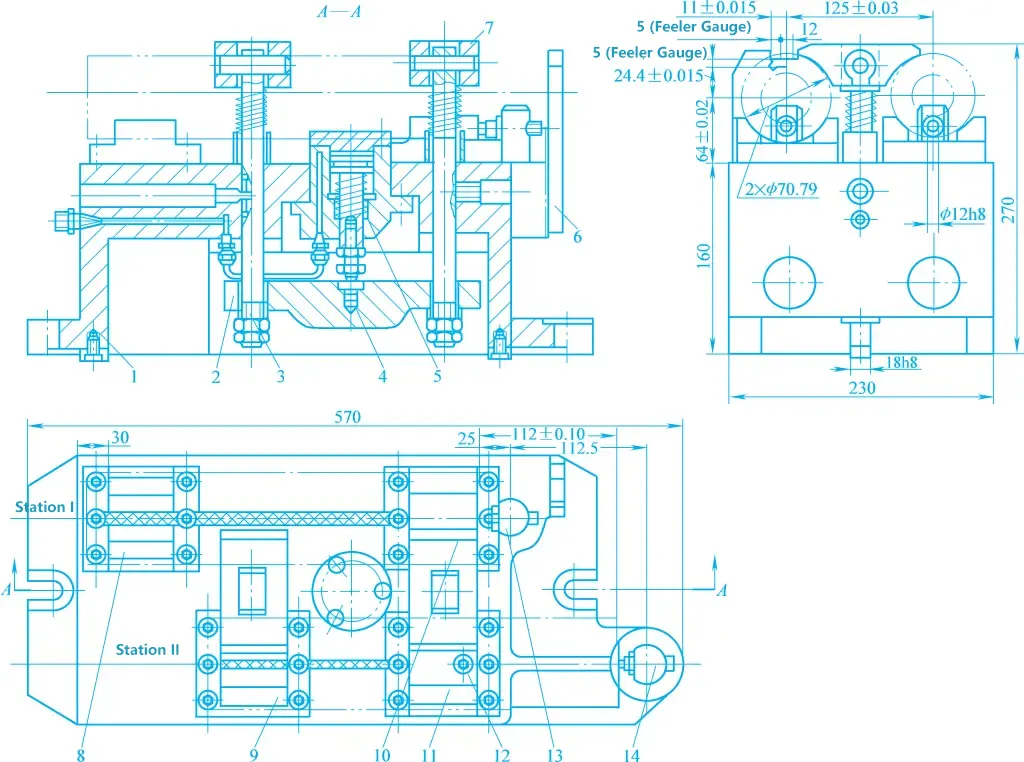
1-器具本体
2-フローティング・レバー
3スクリュー・ロッド
4-サポートピン
5-油圧シリンダー
6ツールブロック
7-圧力プレート
8、9、10、11-Vブロック
12-回転防止ピン
13、14-スラストピン
(2) サーキュラーフィード型フライス盤治具
サーキュラーフィードタイプのフライス盤用フィクスチャーは、主にロータリーテーブル付きのフライス盤で使用される。一般的なフライス盤で使用する場合は、図9に示すように、フライス盤にロータリーテーブルを追加する必要がある。
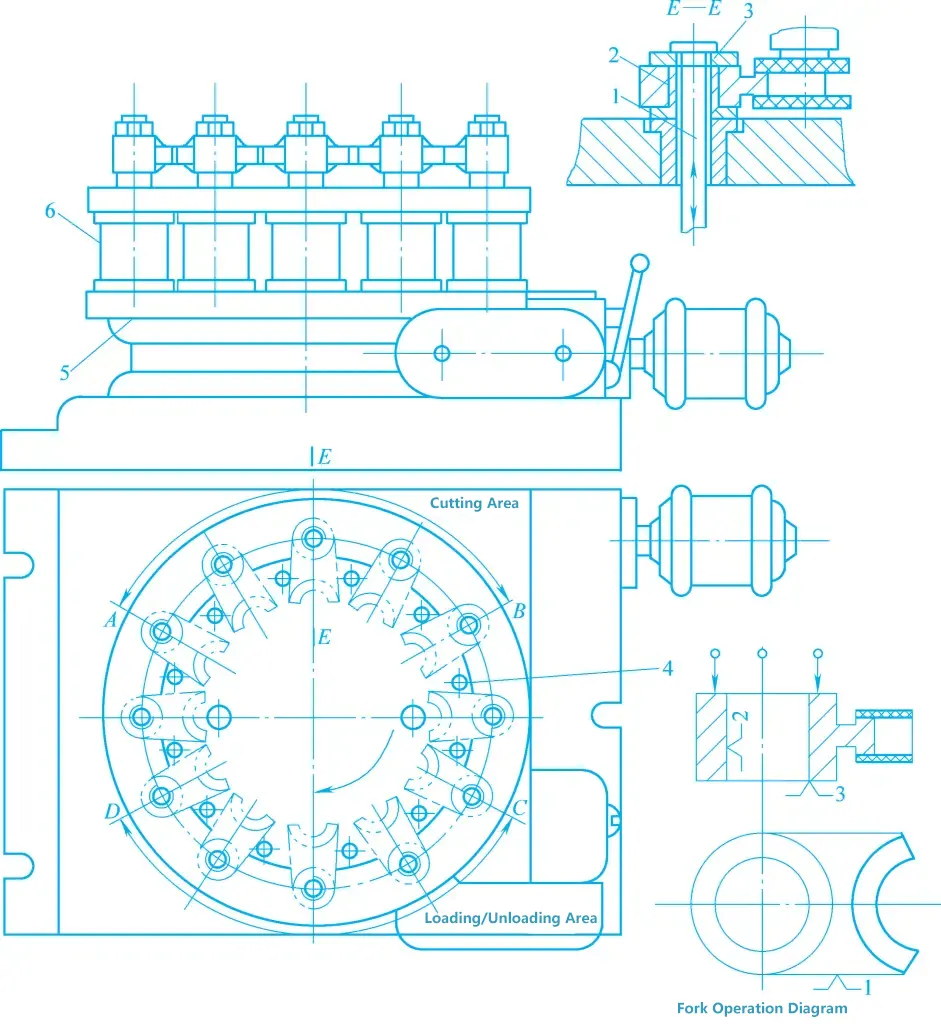
1-プルロッド
2ポジション・ピン
3分割ウォッシャー
4ストップピン
5回転テーブル
6-油圧シリンダー
円弧状の送り動作は連続的で、機械を停止させることなくワークのローディングとアンローディングができるため、高い生産性が得られる。小物から中物部品の大量生産に適しているが、操作上の安全性とオペレーターの労働強度には特に注意が必要である。
2.フライス盤用特殊治具の代表例
図7は、旋盤の心押台スリーブにキー溝と油溝を加工する工程図である。ワークの内円と外円、両端面が加工されている。この工程では、2つのフライスカッターを使用して、キー溝と油溝を同時に加工する。図8は量産時に使用される冶具で、典型的な直線送りフライス盤の冶具である。
ステーションIでは、キー溝を加工するために3面エッジフライスカッタが使用される。ワークピースはVブロック8、10、スラストピン13の外周と端面によって位置決めされ、5つの自由度が制限される。ステーションIIでは、アークフライスカッタを使用してオイル溝をフライス加工する。ワークピースは、Vブロック9、11、回転防止ピン12、スラストピン14を使用して、外周、すでに加工されたキー溝、端面によって位置決めされ、完全に位置決めされる。
キー溝と油溝の長さが異なるため、同時に加工を完了するために、2つのスラストピンの位置をずらすことができ、簡単に調整できるように設計されている。
クランプは油圧駆動のリンククランプを使用する。圧油が油回路システムから油圧シリンダー5の上部チャンバーに入ると、ピストンを押し下げ、支持ピン4、フローティングレバー2、スクリュー3を介してヒンジプレッシャープレート7を押し下げ、ワークをクランプします。プレッシャープレートがワークを均等にクランプするために、リンククランプ機構のすべての部品はフローティングコネクションを使用しています。
図9に示す円周送りフライス盤用固定具は、立フライス盤でフォークの上下端面を連続フライス加工する際に使用する。ワークの丸穴、端面、側面をボス付き位置決めピン2とストップピン4で位置決めし、割り座金3を介して油圧シリンダ6で駆動されるプルロッド1でクランプする。
治具は同時に12個のワークをクランプし、ワークテーブルはウォームギア機構を介してモーターで回転駆動される。ABセクターは切断エリアであり、CDセクターは搬出入エリアである。ワークがワークテーブルと共にABエリアまで回転すると、油圧シリンダー6がプルロッド1を下降駆動してワークをクランプし、ワークがワークテーブルと共にCDエリアまで回転すると、油圧シリンダー6がプルロッド1を上昇駆動してワークを解放する。
ワークの切削と搬出入の間、ワークテーブルは停止することなく連続的に回転します。そのため、加工時間とワークの搬出入の補助時間が重なり、高い生産性を実現する。
3.フライス盤治具の構造特性
(1) ロケート・キー
フライス盤の固定具には、一般に、固定具本体の底面にある長手方向のスロットに位置決めキーが取り付けられている。通常、できるだけ間隔をあけて2つ使用する。小型の治具では、断面が長方形の長いキーを1本使用することもできる。
位置決めキーはフライス盤のワークテーブルのT溝に適合します。その主な機能は、固定具とフライス盤ワークテーブル間の正しい位置関係を確保することです。また、切削トルクの一部を負担することができ、固定具本体とワークテーブルをつなぐボルトへの負荷を軽減し、加工中の固定具の安定性を高めます。
位置決めキーには、長方形と円筒形の2種類がある。一般的な長方形キーには、図10aと10bに示すような2つの構造がある。前者は、固定具の方向精度の要求が高くない場合に使用される。固定具の方向精度を向上させるために、固定具を取り付ける際に、位置決めキーの片側を作業台のT溝の片側にぴったりとはめ込むべきである。
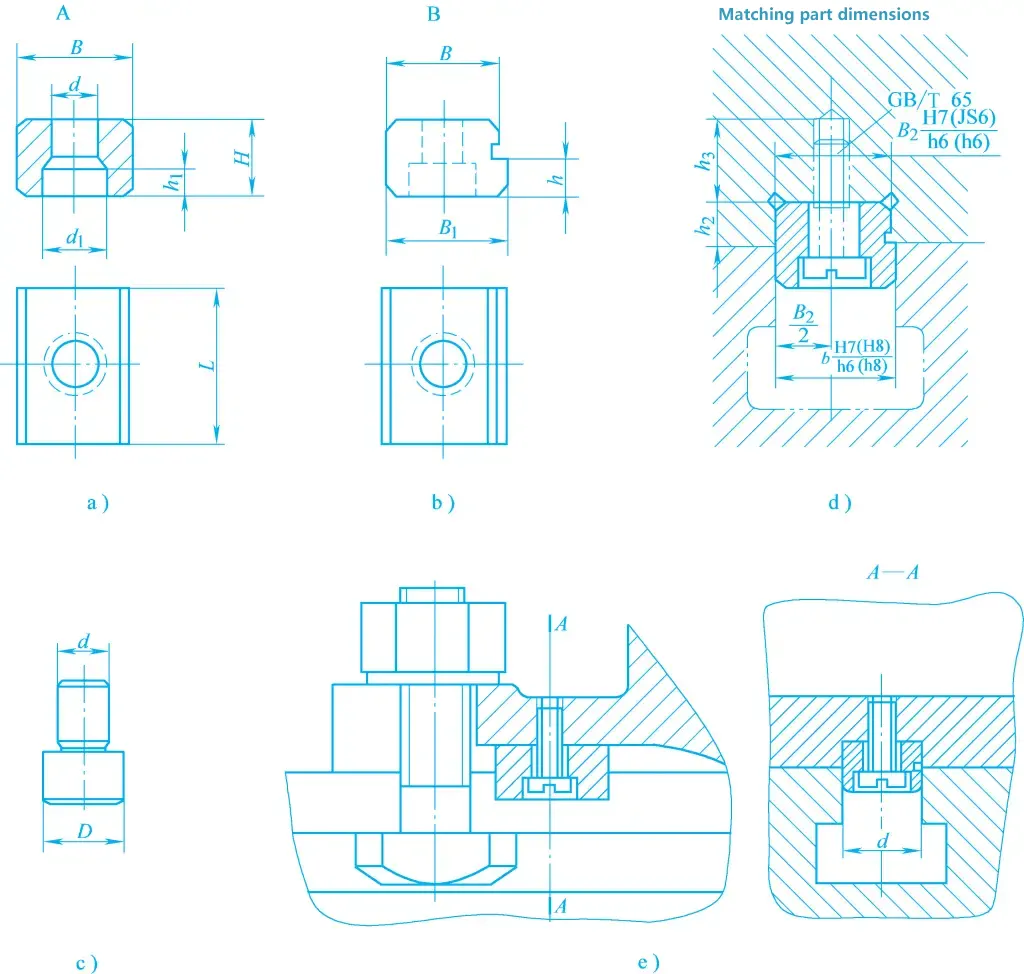
固定具本体のキー溝の精度を確保するのが難しいため、近年、図10cに示すような円筒形の位置決めキーが登場している。このタイプの位置決めキーを使用する場合、治具の2つの穴は座標ボーリングマシンで加工されるため、高い位置精度が得られ、治具の製造工程が簡略化される。
しかし、円筒形の位置決めキーは摩耗しやすく、生産現場ではあまり使用されていない。図10dと10eは、固定具本体への位置決めキーの取り付けと、作業台へのフライス盤固定具の取り付けを示している。
大型のフィクスチャーや高い方向精度が要求される場合、位置決めキーは適さない。その代わりに、図11に示すように、フィクスチャーの取り付け位置を修正するためのアライメントの基準面として、フィクスチャー本体に細長い平面を加工する。
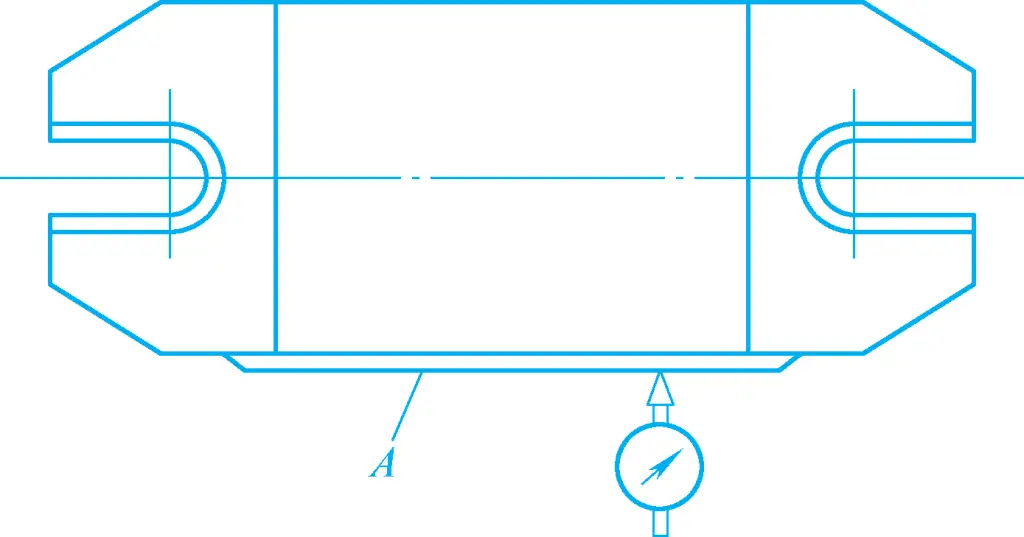
(2) 工具セッティング装置
フライス盤の固定具は一般に、工具計測ブロックとフィーラーゲージからなる工具計測装置を備えている。工具計測ブロックは、固定具と工具の相対位置を決定するために使用されます。フィーラーゲージは、工具セッティング中に刃先や工具セッティングブロックの損傷を防ぐために使用される。使用時には、工具と工具計測ブロックの間に挿入され、工具の固定具に対する最終的な位置は、その接触強度に基づいて決定されます。
図12は、いくつかの一般的な工具計測ブロックを示している。図12aに示す丸型工具計測ブロックは、1つの平面を加工する際の工具計測に使用します。図12bに示す直角工具計測ブロックは、互いに直交する2つの平面またはスロットを加工する際の工具計測に使用する。図12cおよび図12dに示す工具計測ブロックは、成形フライスカッターで成形面を加工する際の工具計測に使用する。
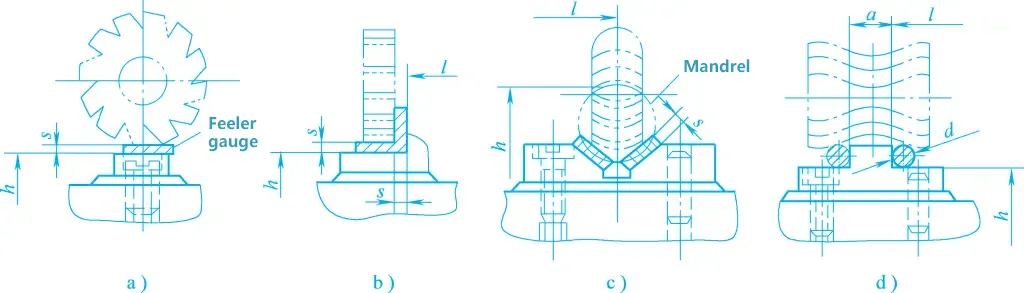
ツール・セッティング・ブロックは通常、2本のピンとネジでフィクスチャー本体に固定される。その位置は、工具のセッティングを容易にし、ワークピースの出し入れや加工の妨げにならないようにする。工具調整に工具計測装置を使用する場合、精度はIT8を超えない。より高い加工精度が要求される場合や、工具計測ブロックを設置するのが不便な場合は、試削り、標準部品の工具計測、ダイヤル・インジケータを使用して工具位置を合わせるなどの方法がある。
(3) 固定具本体
固定具本体の構造形式は、位置決め要素、クランプ装置、その他の部品の構造と配置に大きく依存する。取付け具の構造をコンパクトにし、工作機械への取付けの安定性を確保するために、図13aに示すように、ワークピースの加工面をできるだけワークテーブル面に近づけ、取付け具の重心を下げる必要がある。
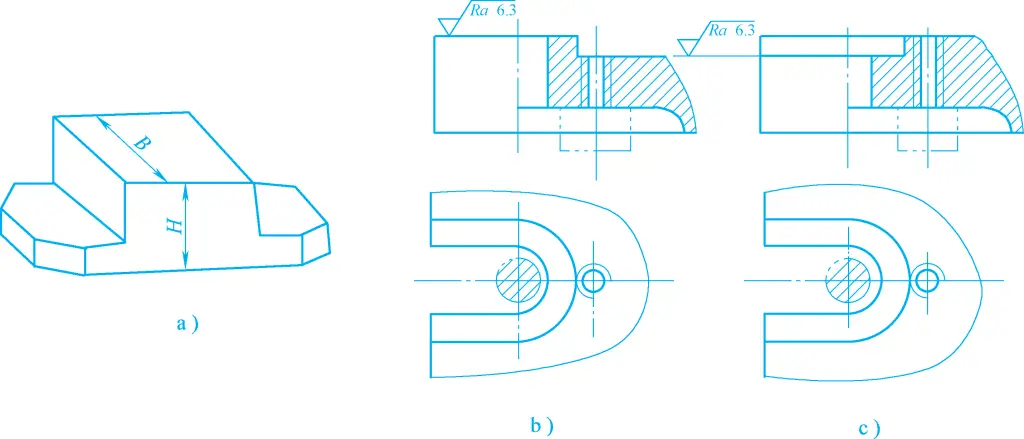
さらに、固定具本体は十分な強度と剛性を持つべきであり、ラグシートは合理的に配置されるべきである。一般的なラグシートの構造を図13bと13cに示す。固定具本体の幅が比較的広い場合は、2つのラグシートを同じ側に配置することができ、2つのラグシート間の中心距離は、フライス盤作業台の2つのTスロットの中心距離と一致させる。重量のあるフライス盤用固定具の場合は、取り扱いを容易にするため、固定具本体に持ち上げリングをセットする。
III.ドリルプレス治具
1.ドリル治具の種類と特徴
ドリル治具は、ボール盤で穴あけ、リーマ加工、中ぐり加工に使用される機械治具です。これらの治具は、ドリルテンプレートとドリルブッシュを備えており、ブッシングを通して工具をガイドするため、一般的にドリル治具と呼ばれています。使用条件によって、固定式、回転式、フリップ式、カバープレート式、スライディングコラム式に分けられます。
(1) 固定式ドリル治具
固定式ドリル治具の特徴は、加工中も位置が変わらず、高い加工精度を確保できることです。通常、ドリル治具は、治具本体の耳座穴にTボルトを通してボール盤の作業台に固定するか、ボルトとプレッシャープレートを使って作業台に直接クランプします。固定式ドリルジグは主に、立型ボール盤でより大きな単穴を加工する場合や、ラジアルボール盤で平行穴システムを加工する場合に使用されます。
縦型ボール盤で平行穴システムを加工するために固定ドリル治具を使用する場合、多軸ドライブヘッドを機械主軸に取り付ける必要があります。縦型ボール盤にドリル治具を取り付ける場合、スピンドルに取り付けた寸法工具(高精度の場合はマンドレル)をドリルブッシュに挿入してドリル治具の位置を決め、固定するのが一般的です。
図14aは、レバーにΦ10mmの穴を加工するための固定ドリル治具である。このドリル治具は、ボルトとプレッシャープレートでボール盤のワークテーブルに固定できる。
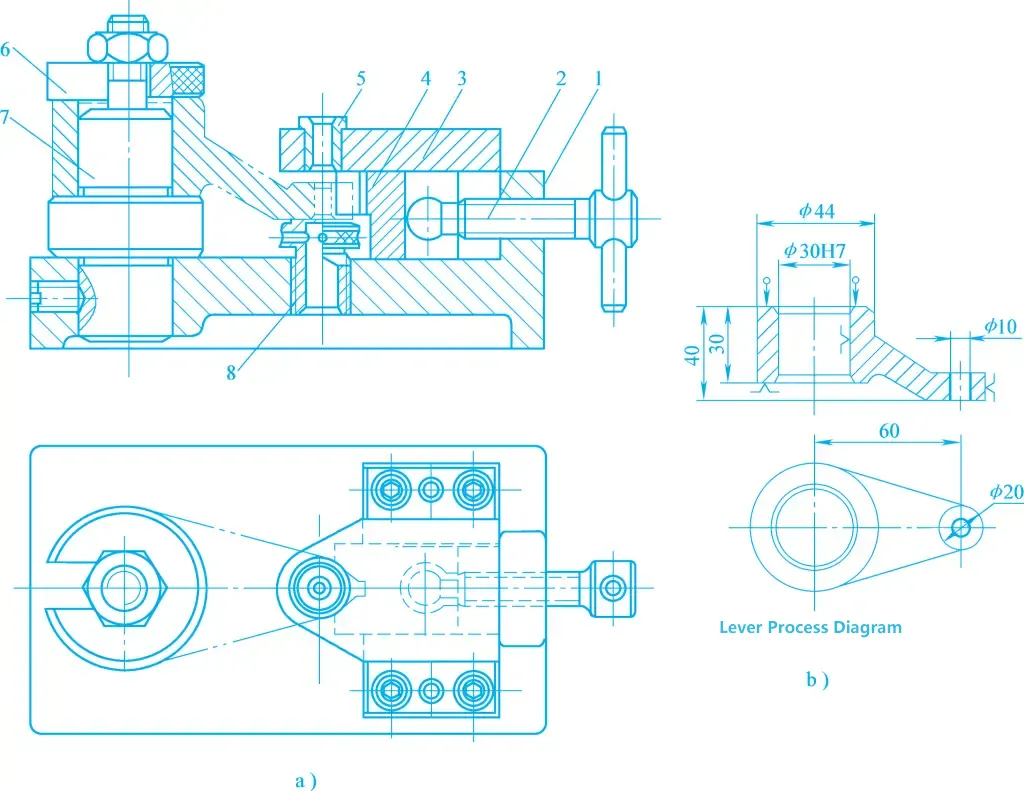
1-ジグ・ボディ
2-固定ハンドル圧スクリュー
3-ドリル・テンプレート
4可動Vブロック
5-ドリル・ブッシュ
6分割ウォッシャー
7ポジション・ピン
8-補助サポート
ワークはΦ30H7の穴と大きな端面を利用して位置決めピン7に位置決めされ、可動Vブロック4を介してΦ20mmの外周円によりワークの回転自由度が制限される。ワークのクランプは、ねじクランプ機構と割り座金を用い、Φ20mm外周円の下端面を補助サポート8で支持します。ドリルビットはドリルブッシュ5を通してΦ10mmの穴を加工するためにガイドされます。
このような穴あけ治具をボール盤のワークテーブルに固定しなければ、移動式穴あけ治具となり、単軸立型ボール盤で被加工物の同一面に複数の平行な小穴を連続してあけることができる。
(2) 回転ドリル治具
回転ドリル治具は、回転割出装置または一般的な回転テーブルと組み合わせて使用することから名付けられました。同一円周上の平行穴加工や円周上に分布する放射状穴加工に使用されます。一般的なロータリーテーブルは構造が標準化されているため、ほとんどの場合、専用の作業治具を設計するだけで使用できます。専用の回転割出装置を備えた特殊なロータリードリル治具は、特殊な場合にのみ設計される。
図15aはΦ70mmの円周上にΦ10mmの穴を6個均等に加工する垂直軸回転ドリル治具である。位置決めディスク4、位置決めピン3、キーの底面、Φ40H7穴、キー溝側の面を用いてワークを位置決めし、ナットと割り座金でクランプしている。
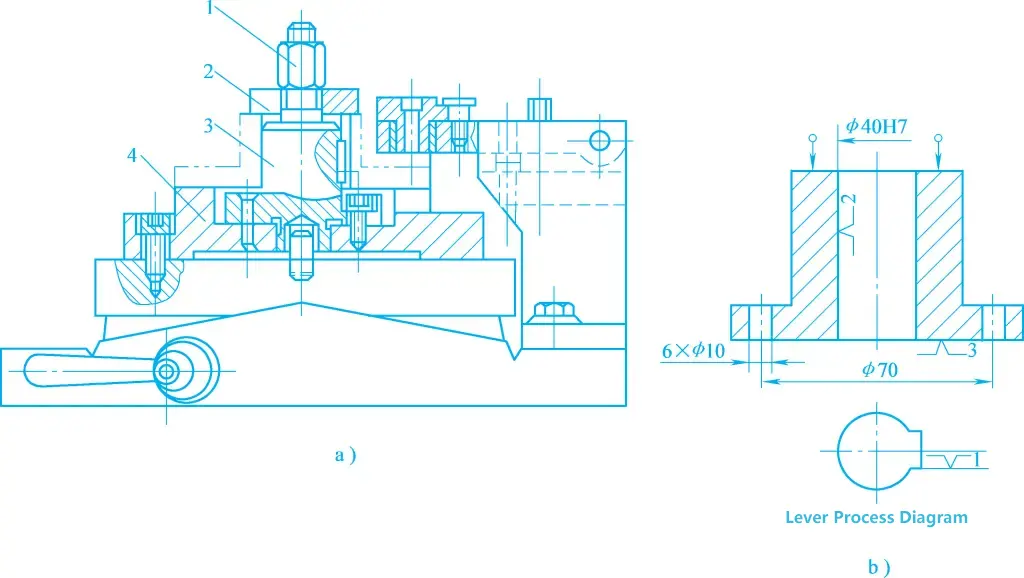
1-クランピングナット
2分割ウォッシャー
3コンビネーション位置決めピン
4ポジション・ディスク
治具は回転テーブルのターンテーブル中央の位置決めピンに位置決めディスクのブッシュ穴を通して取り付け、ネジで固定する。さらに、ロータリーテーブル上にヒンジ付きドリルテンプレートを取り付け、ターンテーブルの回転割り出しによりΦ6×10mmの穴を順次加工していく。
(3) フリップ式ドリル治具
このタイプのドリル治具は、主に小さなワークの異なる面に分布する小さな穴を加工するために使用されます。構造はシンプルで、使用時には手動で反転させる必要があります。つまり、一面の穴を加工した後、治具と一緒にワークを反転して置き、他の面の穴を加工します。
加工中に治具を頻繁に反転させる必要があり、ドリルプレスのテーブルに固定されていないため、ワークとともに治具の重量もあまり重くならないようにする(一般に8~10kgが限度)。加工される穴は一般にΦ10mm以下であり、反転後の固定具の安定性と切りくずの除去に注意を払う必要がある。
図16は、スリーブの円筒面に放射状に4つの小穴を加工するためのフリップ式ドリル治具である。被加工物は、位置決めピン1の端面と穴によって位置決めされ、ナット3と割り座金2でクランプされる。一組の穴をあけた後、ドリル治具を60°反転させ、もう一組の穴をあける。
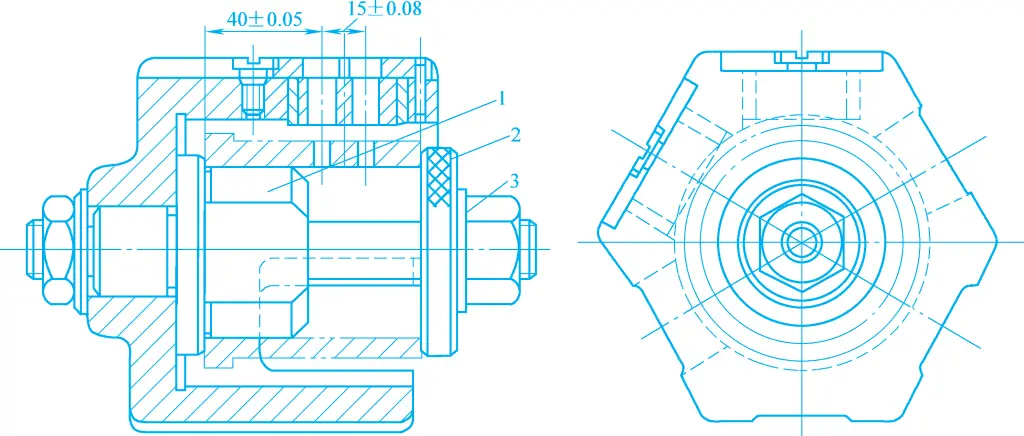
1-位置決めピン
2-ワッシャー
3ナット
(4) カバープレート・ドリル治具
このタイプのドリル治具は治具本体を持たず、大きなワークピースに複数の平行な小穴を加工する場合によく使用されます。一般的に、ドリルテンプレートにはドリルブッシュに加え、位置決め要素やクランプ装置も装備されています。加工中は、ワークピースの上に置くだけでよい。
図17は、旋盤キャリッジ上で複数の小穴を加工するために使用されるカバープレートドリル治具を示す。円筒ピン2と平ピン3によって被加工物の2つの穴に位置決めされ、3本の支持ピン4によって被加工物の上面に支持される。ドリルテンプレートが比較的重く、加工される穴が比較的小さい場合、加工中のクランプは必要ないかもしれません。
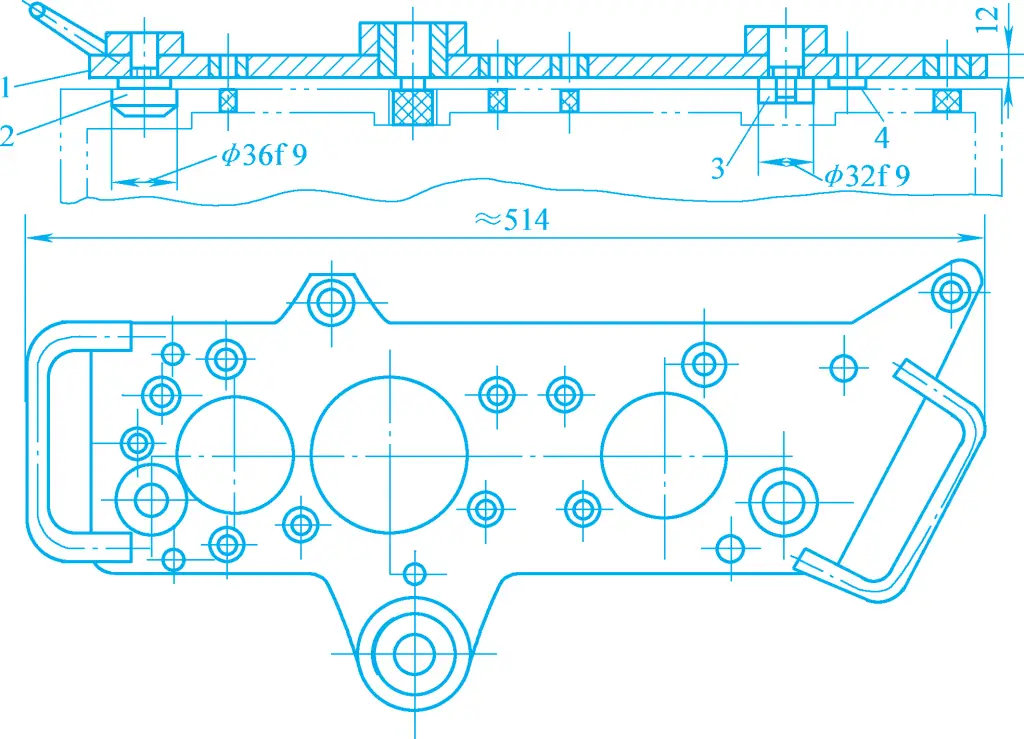
1-カバープレート
2-円筒ピン
3-フラットピン
4-サポートピン
(5) スライド式コラム・ドリル治具
スライディングコラムドリル治具は、一般的に治具本体、スライディングコラム、昇降式ドリルテンプレート、ロック機構から構成されている。その構造は標準化され、一般化されている。共通部品は主に固定具本体とドリルテンプレートである。このタイプの治具は生産現場で広く使用されているが、ドリル穴の垂直性と穴間隔の精度はあまり高くない。
図18は、手動スライドコラムドリル治具のユニバーサルベースを示す。昇降式ドリルテンプレート1は、2本のガイドコラム7を介して治具本体5のガイド孔に連結されている。操作ハンドル6を回すことにより、ベベルギア4がベベルラックシャフト3を駆動して移動し、ドリルテンプレートを持ち上げることができる。異なるワークピースの形状と加工要件に応じて、対応する位置決め要素、クランプ要素、およびドリルブッシュを構成して、スライディングコラムドリル治具を形成することができます。
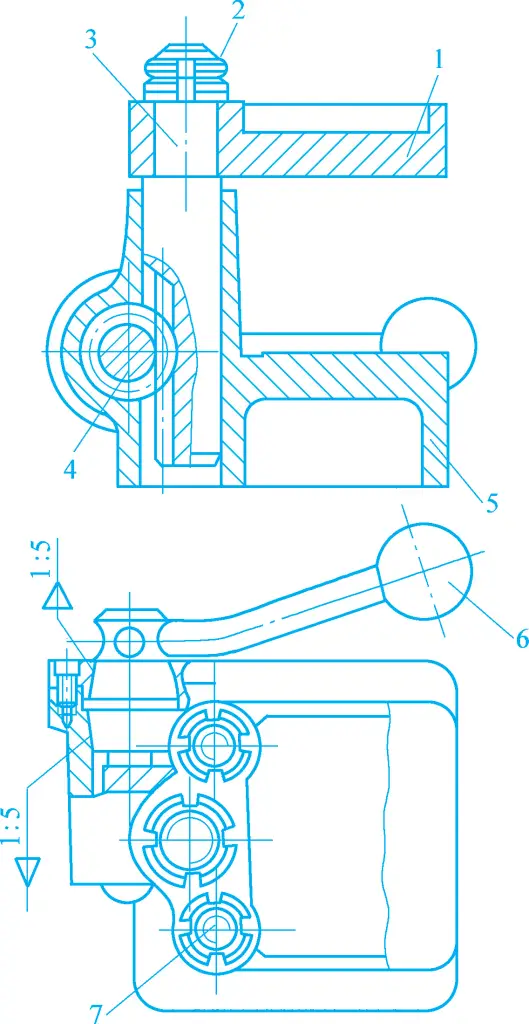
1-リフティング・ドリル・テンプレート
2-ロッキングナット
3段ラックシャフト
4段ベベルギア
5フィクスチャー・ボディ
6操作ハンドル
7ガイドコラム
図19は、フォークワークのφ20H7穴あけ、リーマ加工、ブローチ加工に使用する手動スライド式コラムドリル治具を示す。ワークピースは、位置決めテーパスリーブ9、2つの調整可能サポート2、および円筒形ストップピン3を用いて、それぞれ外側の円形端面、底面、および背面側の面によってベース1上に位置決めされる。 これらの位置決め要素はすべてベース1上に設置されている。
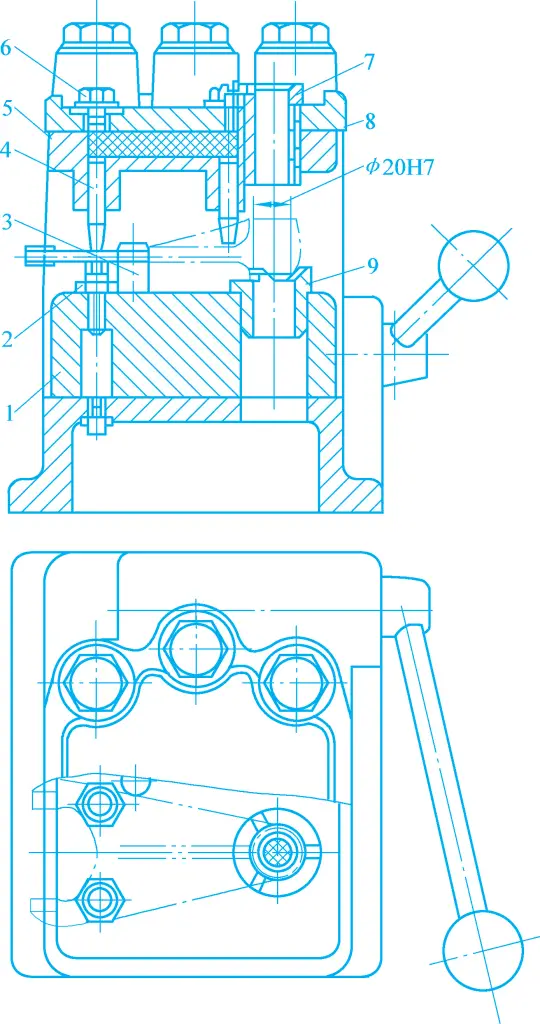
1ベース
2アジャスタブル・サポート
3-円筒形ストップピン
4プレスコラム
5プレス・コラム・ボディ
6スクリュープラグ
7-クイック・チェンジ・ドリル・ブッシュ
8-ブッシング
9ポジションテーパースリーブ
次にギヤラック機構を介してハンドルを回転させると、スライドコラムがドリルテンプレートを押し下げ、2本のプレスコラム4がワークをしっかりとクランプします。工具はクイックチェンジドリルブッシュ7を順に通過し、ドリル加工、リーマ加工、中ぐり加工ができる。
2.ドリルプレス治具の構造特性
(1) ドリル・ブッシュ
ドリルブッシュはドリル治具のユニークな部品で、その機能は工具と治具の相対位置を決定し、ドリルビットとリーマをガイドして加工中のたわみを防止し、加工システムの剛性を向上させ、加工穴の位置精度を確保することである。その構造は以下の4種類がある:
1) 固定ドリルブッシング。
主に小~中ロット生産に使用される。図20aはショルダーレスドリルブッシュ、図20bはショルダー付きドリルブッシュを示しています。ドリルブッシュのショルダーの下端面を組立ベース面として使用する場合や、ドリルテンプレートが比較的薄く、切粉などがドリルブッシュの穴に入らないようにする必要がある場合は、ショルダードリルブッシュを使用することが多い。
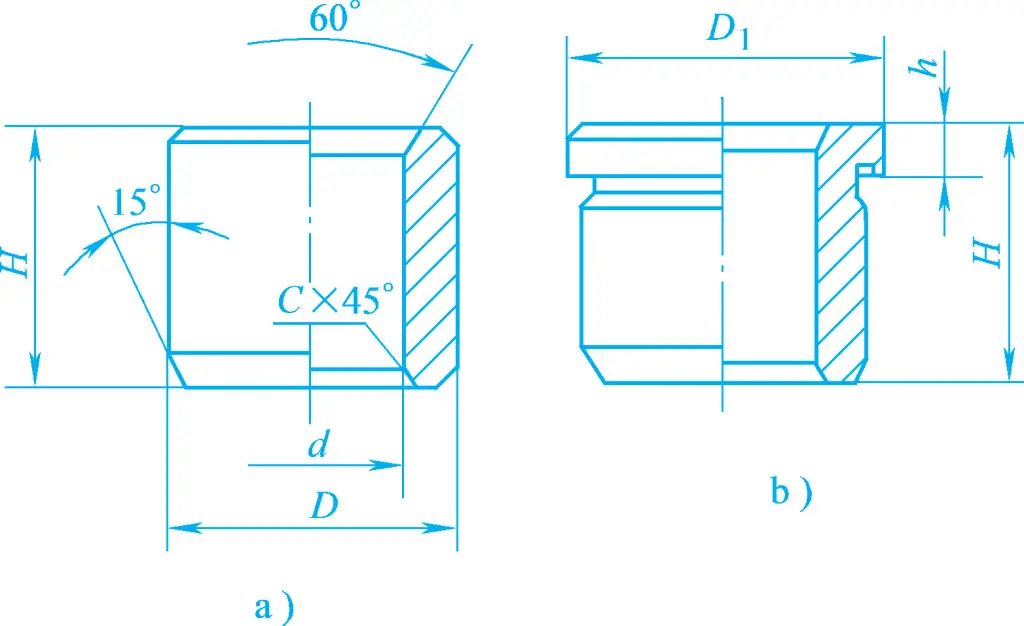
ドリルブッシュとドリルテンプレートの間のフィットは、一般的にH7/n6またはH7/r6を使用しています。このタイプのドリルブッシュは、穴あけの位置精度が高く、シンプルな構造を持っていますが、摩耗後に交換することは容易ではありません。
2) 交換可能なドリル・ブッシュ。
主に大量生産で使用される。ドリルブッシュが摩耗した場合、交換を容易にするため、図21に示すような構造形状と組立条件を持つ交換可能なドリルブッシュがよく使用される。ドリルブッシュ交換時のドリルテンプレートの摩耗を避けるため、ドリルブッシュとドリルテンプレートの間にブッシュを追加し、ドリルブッシュをネジで固定する。
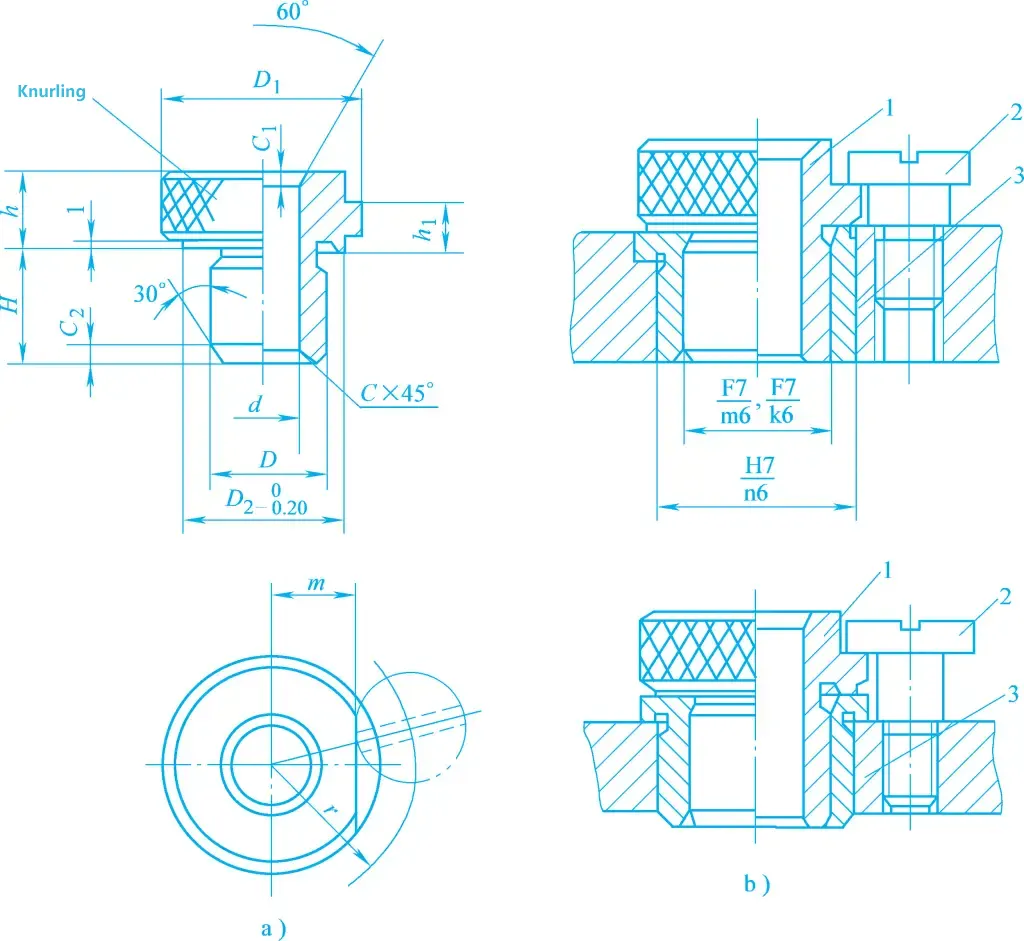
1-交換可能ドリルブッシング
2-ドリルブッシング用ネジ
3-ドリルブッシング用ブッシング
3)クイックチェンジドリルブッシュ。
加工穴が連続したドリル加工、リーマ加工、ボーリング加工、または段付き穴加工やタッピング加工などの多段加工を必要とする場合、内径の異なるドリルブッシュを素早く交換できるクイックチェンジドリルブッシュを使用する。その構造形状と組立要件を図22に示す。
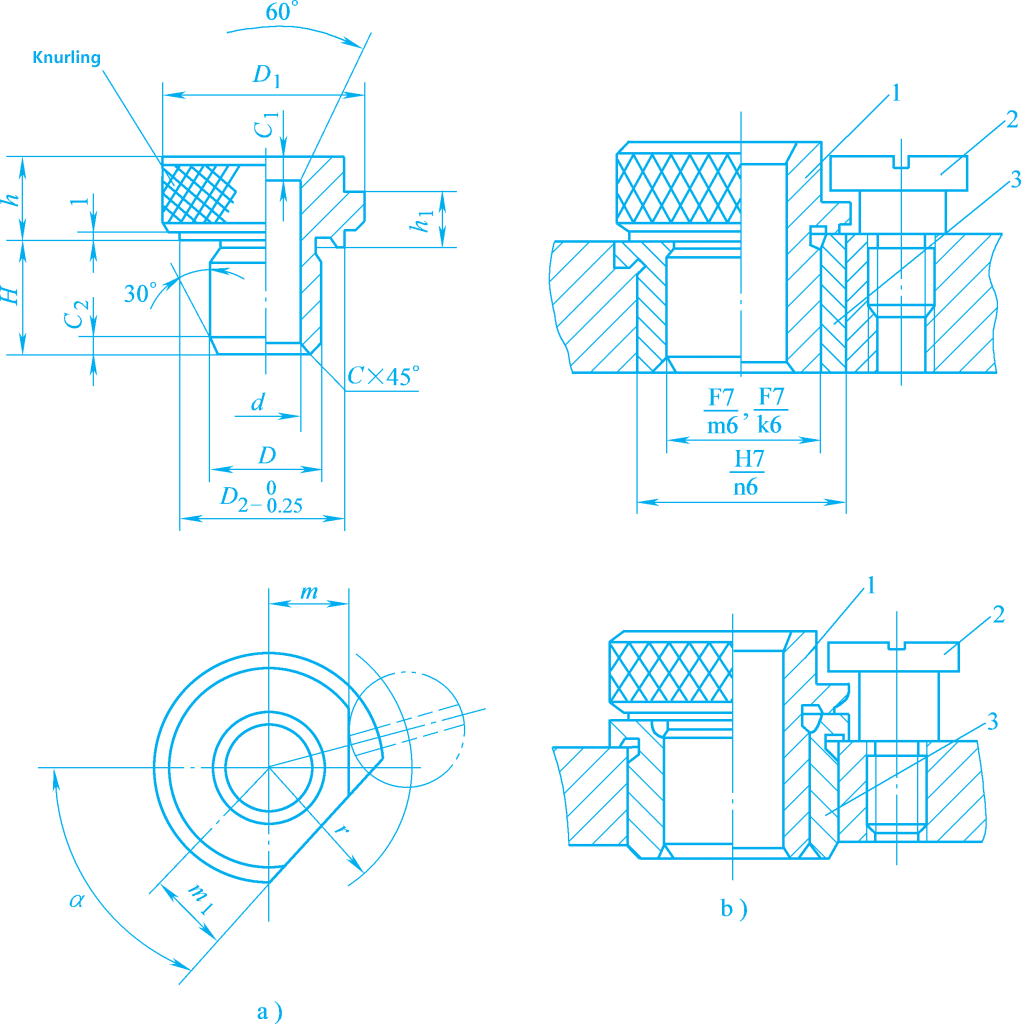
1-クイックチェンジドリルブッシュ
2-ドリルブッシング用ネジ
3-ドリルブッシング用ブッシング
ドリルブッシングを交換する際、ネジを緩める必要はありません。ドリルブッシングをある角度まで回転させ、面取り(または切り欠き)をネジの頭に合わせるだけで取り外すことができます。ただし、面取り(または切り欠き)の位置は、工具とドリルブッシュの内壁との摩擦トルクの方向を考慮し、引き込み時にドリルブッシュが工具と一緒に引き抜かれないようにする必要があります。
4) 特殊ドリル・ブッシュ。
ワークの形状や穴位置の分布により、上記の標準ドリルブッシュの使用が制限される場合は、必要に応じて特殊構造のドリルブッシュを設計することができます。
図23は、特殊ドリルブッシングのいくつかの構造形式を示している。図23aは、カウンターシンクや溝上の穴加工に使用されるドリルブッシュを示す。図23bは、傾斜面や曲面への穴加工に使用するドリルブッシュで、切り込み時にドリルビットがずれたり折れたりするのを防ぐことができる。図23cは、間隔の詰まった複数の穴加工に使用するドリルブッシュを示す。図23dは、補助クランプ工具として使用されるドリルブッシュを示す。
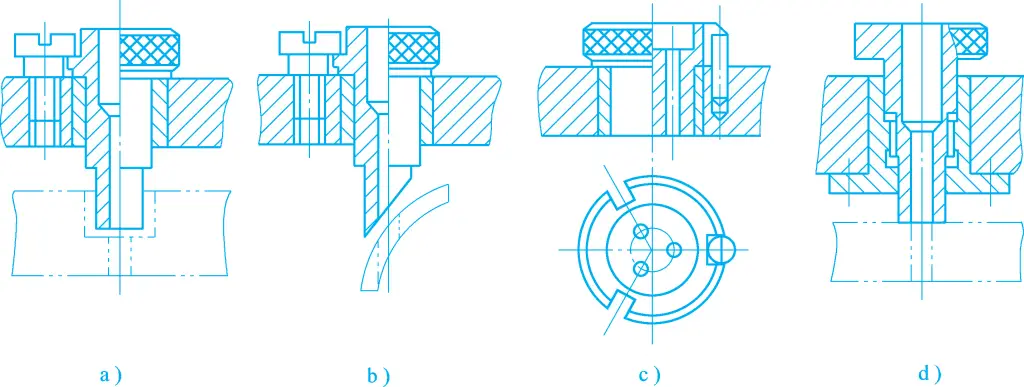
クランプ反力に耐えるため、ドリルブッシュとスリーブはねじで連結され、ガイド穴の正しい位置を確保するため、ドリルブッシュとスリーブの間には円筒状のはめあいも必要です。
(2) ドリル・テンプレート
ドリルブッシングの取り付けに使用されるドリルテンプレートは、フィクスチャーボディとの接続方法によって以下のタイプに分けられる:
1) 固定ドリル・テンプレート
図24に示すように、固定ドリル・テンプレートは、フィクスチャー本体と一体に鋳造されるか、ネジとピンでフィクスチャー本体に接続される。また、フィクスチャー本体やブラケットに溶接することもできる。構造が簡単で、穴あけ精度が高いが、ワークの出し入れの妨げにならないように注意しなければならない。
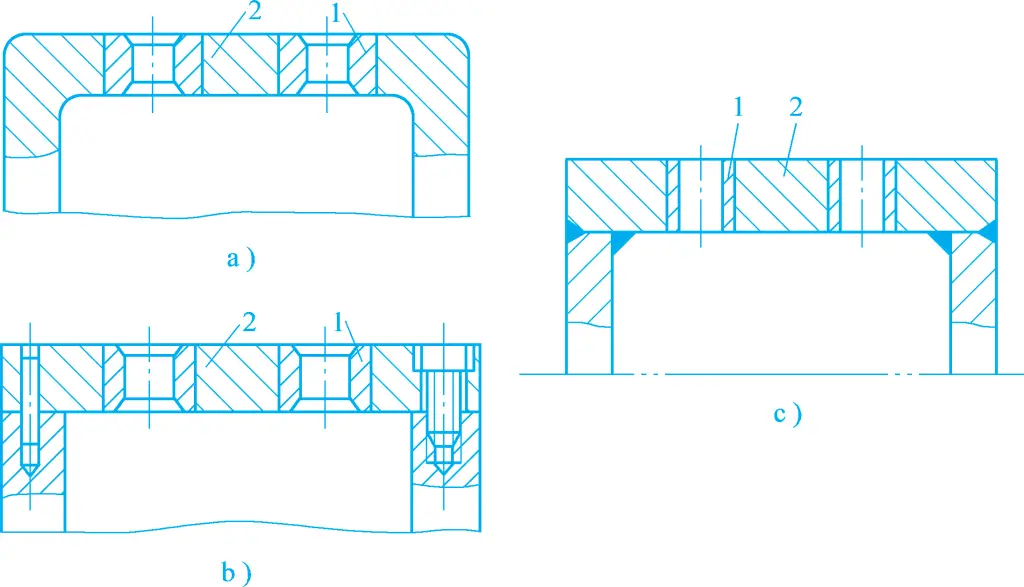
a) 一体鋳造
b) ネジとピンで接続
c) 溶接
1-ドリルブッシング
2-ドリル・テンプレート
2) ヒンジ付きドリル・テンプレート
ドリル・テンプレートがワークの着脱の妨げになる場合や、ドリル加工後にねじ切りや皿穴加工が必要な場合は、図25に示すようなヒンジ付きドリル・テンプレートを使用できます。
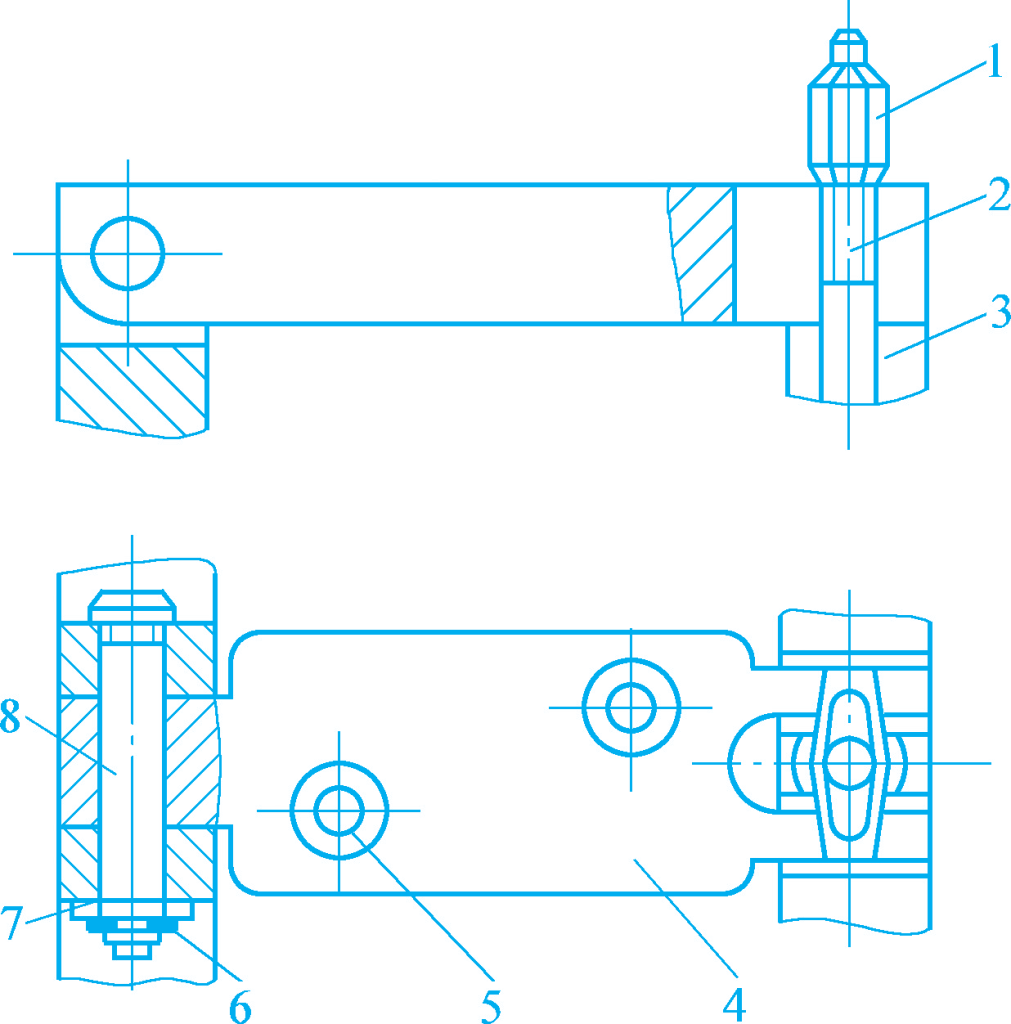
1-菱形のナット
2-トグルボルト
3フィクスチャー・ボディ
4-ドリル・テンプレート
5-固定ドリル・ブッシュ
6コッターピン
7-ワッシャー
8ヒンジピン
ヒンジピンと穴の間の嵌め合いクリアランスのため、確保できる加工精度は固定ドリルテンプレートよりも低く、穴あけ位置精度が高くない状況で使用される。ヒンジ付きドリルテンプレートの位置は加工中に固定されるため、位置決めとクランプのための構造的要件を考慮する必要があります。
3) 取り外し可能なドリル・テンプレート
図26に示すように、ドリルテンプレートは、2つの穴を通して固定具本体の円筒ピン3と平ピン4上に配置され、ヒンジボルトを使用してワークと一緒にクランプされる。1つのワークを加工した後、ドリルテンプレートを取り外して、ワークのロードとアンロードを行う。このタイプのドリルテンプレートは、ワークの着脱に時間と手間がかかり、ドリルブッシュの位置精度が比較的低いため、他のタイプのドリルテンプレートではワークのクランプに不便な場合にのみ使用されるのが一般的である。
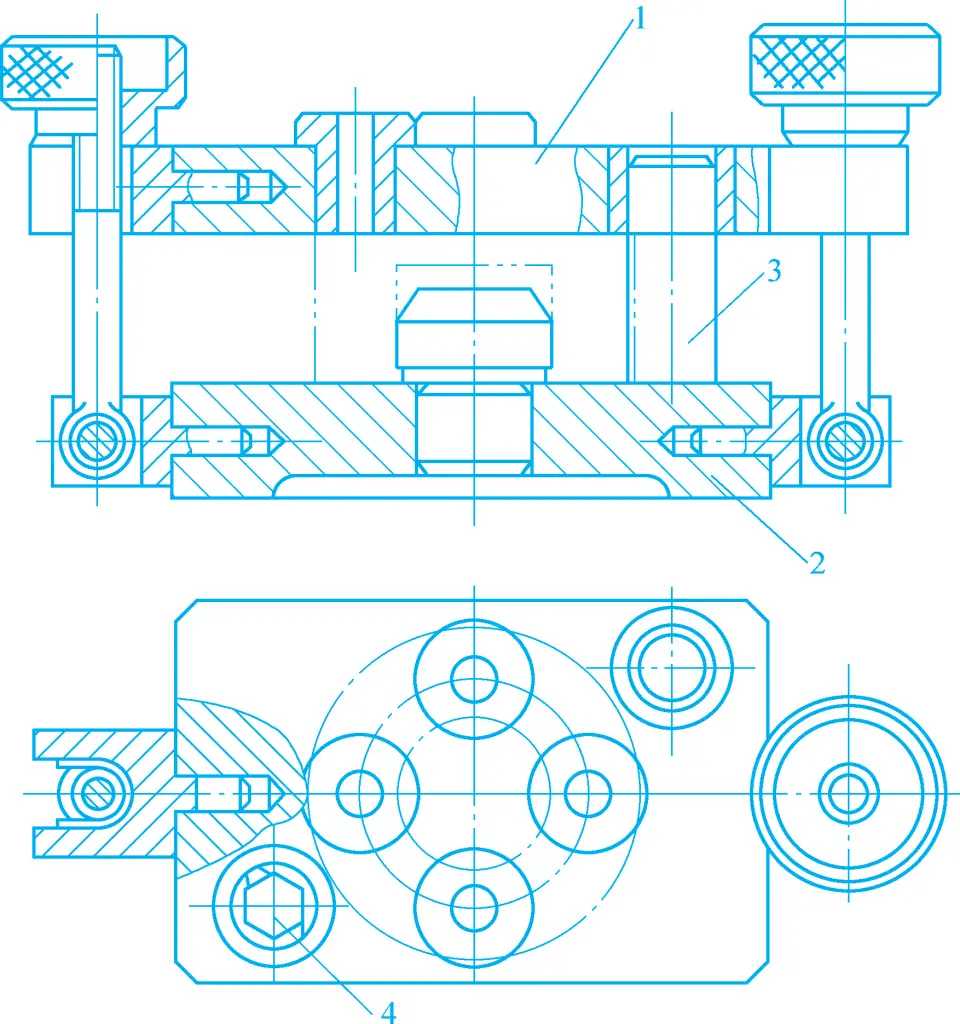
1-ドリル・テンプレート
2クランプボディ
3-円筒ピン
4エッジカッティングピン
IV.ボーリングマシンの治具
1.中ぐり盤用治具の主な種類と特徴
中ぐり治具とも呼ばれる中ぐり盤用治具は、主にボックスやサポートなどの部品に穴や穴システムを加工するために使用されます。ワークピース上の穴または穴システムの位置精度は、主にボーリング治具によって確保されます。中ぐり治具は、中ぐりスリーブの配置の違いにより、シングルサポート、ダブルサポート、サポートなしの3種類に分けられます。
(1) シングル・サポート・ガイド
ボーリングバーは、ボーリング治具内で工具の前方または後方に配置された1つのボーリングスリーブによってガイドされる。ボーリングバーは主軸に剛体的に連結され、ボーリングスリーブの中心線は主軸の軸線と一致しなければならない。この場合、主軸の回転精度が中ぐり精度に影響します。このタイプの中ぐり治具は、短穴や小穴の加工に適しています。
図27aは、主にD>60mm、l/D<1の貫通穴に使用されるシングルサポートフロントガイドを示している。この方法は、加工工程中の観察と測定を容易にし、特に面取り加工やねじ切り加工に適している。欠点は、切り屑がボーリングスリーブに入りやすく、ボーリングバーとスリーブの摩耗を引き起こすこと、工具がワークピースに出入りする際の移動距離が長くなることである。
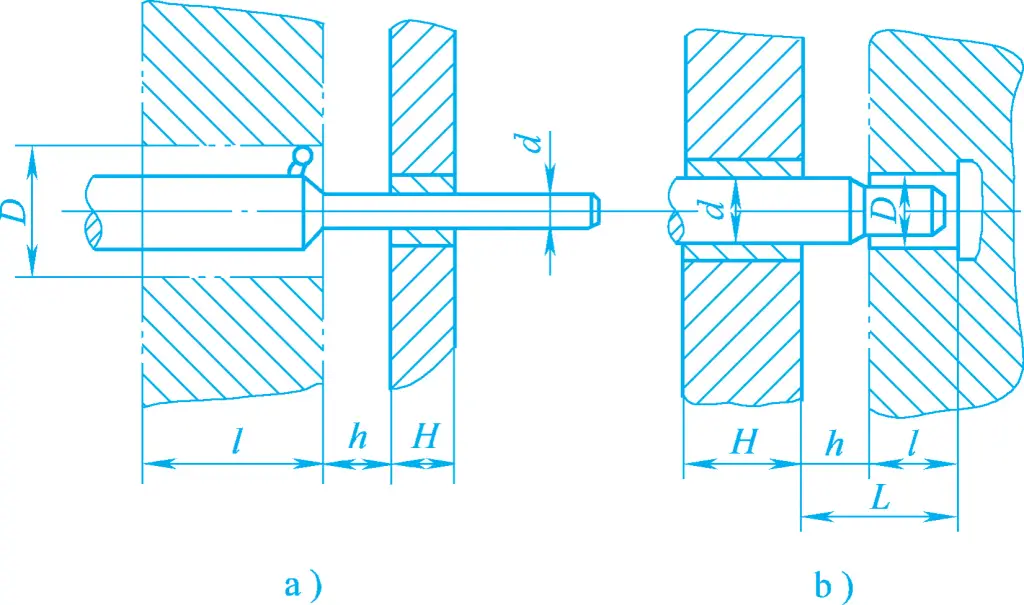
a) シングル・サポート・フロント・ガイド
b) シングルサポート・リアガイド
図27bは、主にD<60mmの貫通穴またはブラインド穴のボーリングに使用されるシングルサポートリアガイドを示す。
(2) ダブル・サポート・ガイド
ボーリングバーは機械主軸にフレキシブルに連結され、ボーリング穴の位置精度はボーリングスリーブの位置精度で決定される。図28に示すように、ボーリングスリーブには2つの配置がある。図28aは、ワークの前後に配置された2つのボーリングスリーブを示しており、穴径が大きくl/D>1.5の穴加工や、穴そのものと穴間の距離の両方に高い精度が要求される同軸の穴加工に使用される。
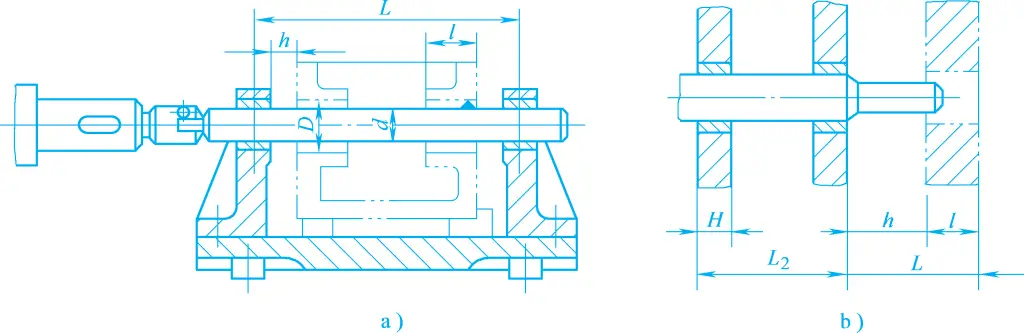
この構造の欠点は、ボーリングバーが長すぎるため、工具の出し入れが不便になることである。ボーリングスリーブ間の距離L>10dの場合、ボーリングバーの剛性を高めるために中間ガイドサポートを追加する必要がある。図28bは、加工条件により前後のダブルガイド構造が使用できない場合に使用されるダブルサポートリアガイドで、工具後方に2つのボーリングスリーブが配置されている。
(3) 支えのないボーリング治具
三次元加工機、マシニングセンタ、ダイヤモンド加工機などで、剛性が高く精度の高いワークに穴あけ加工を行う場合、治具に穴あけスリーブをセットする必要がなく、加工穴の大きさや位置精度は加工機の精度によって確保される。
2.特殊ボーリングマシン治具の代表例
図29にブラケットハウジングの工程図を示す。このワークでは、2×Φ20H7の同軸穴とΦ35H7、Φ40H7の同軸穴を加工する必要がある。この工程で加工される穴はIT7等級の精度で、いくつかの幾何公差が要求される。
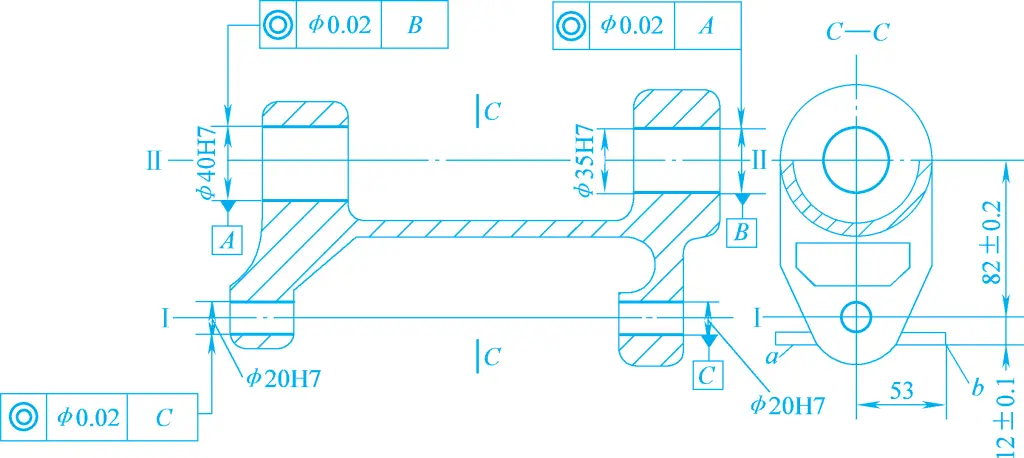
そのため、Φ40H7穴、Φ35H7穴の荒・仕上げ中ぐり、2×Φ20H7穴のドリル、リーマ、ホーニング加工には専用の中ぐり盤治具を使用する。この時、穴距離(82±0.2)mmは中ぐり治具の製作精度で確保する必要がある。基準一致の原則に従い、位置決め基準は2つの平面aとbとして選択される。
図30に示すように、ブラケットハウジング用の中ぐり盤固定具は、位置決め要素として支持板10(一方は側面を有する)とストップピン9を含む。クランプ時には、押圧板8がワークの側板に押し付けられ、ワークの重力とクランプ方向が一致する。
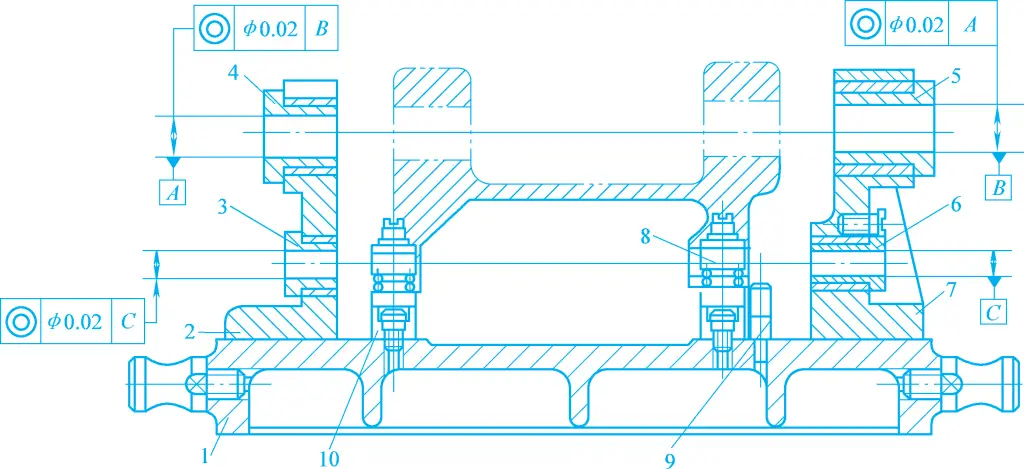
1-器具本体
2、7-ガイドブラケット
3、4、5、6-ボーリングスリーブ
8-プレッシャープレート
9-ストップ・ピン
10-サポートプレート
Φ40H7、Φ35H7穴加工の場合、ボーリングバーはボーリングスリーブ4、5に支持されます。Φ20H7穴加工の場合、ボーリングバーはボーリングスリーブ3、6に支持されます。ボーリングスリーブはガイドブラケット2と7に取り付けられます。ブラケットは固定具本体1にピンとネジで固定されている。
3.ボーリング・テンプレートの構造的特徴
(1) ボーリング・スリーブ
ボーリングスリーブの構造は、固定式と回転式に分けられる。
1) 固定ボーリングスリーブ
穴あけ時にボーリングバーと一緒に回転しないボーリングスリーブは、クイックチェンジドリルブッシュと同じ構造です。図31aは、内孔に油溝を設けた圧入式オイルカップ付きボーリングスリーブである。 切断速度 加工中にボーリングバーはボーリングスリーブ内で回転し、軸方向に移動するため、ボーリングスリーブは摩耗しやすく、オイルカップのないボーリングスリーブは低速切削にしか適していません。
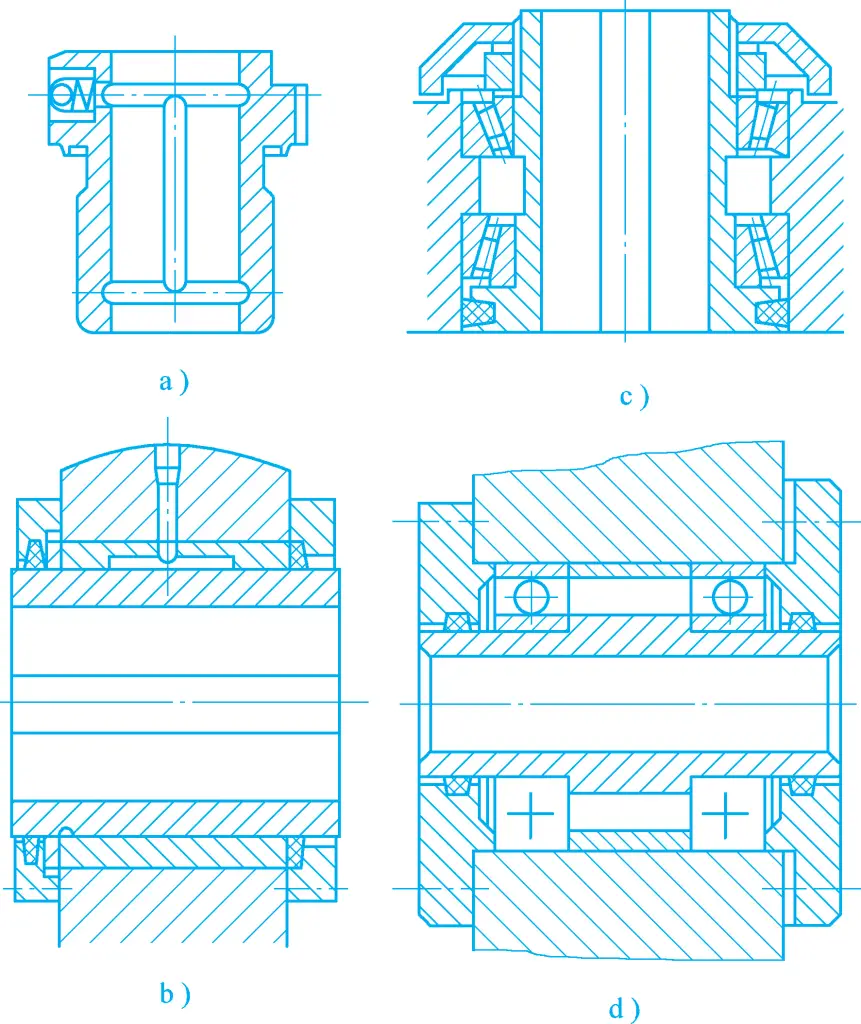
2) 回転ボーリングスリーブ
ボーリング加工中、ボーリングスリーブはボーリングバーとともに回転し、図31b、31c、31dに示すように、特に高速ボーリングに適している。図31bは、内孔にキー溝を設けたスライド式回転ボーリングスリーブを示し、ボーリングバー上のキーがボーリングスリーブを回転させることにより、高い回転精度と良好な振動減衰性を提供し、構造的な大きさは小さく、十分な潤滑を必要とする。
図31cと31dは、それぞれ垂直ボーリングと水平ボーリングに使用されるローリングロータリースリーブを示している。このスリーブは、柔軟な回転が可能で 切断速度しかし、ラジアル寸法が比較的大きく、回転精度が低い。ラジアル寸法を小さくする必要がある場合は、針状ころ軸受を使用することができます。
(2) ブラケットとベース
ボーリング・テンプレート・ブラケットとベースは鋳鉄製で、多くの場合別々に製造されるため、加工、組み立て、経年処理が容易である。加工中の安定性を確保するため、十分な強度と剛性が求められる。溶接構造はできるだけ避け、ネジやピンによる剛性の高い接続が望ましい。
使用中、ブラケットにクランプ力がかからないようにする。作業台にボーリングテンプレートを設置する際のアライメント基準面として使用するため、作業者に面するベースの側面に細長い平面を加工する。ベースには、ボーリング・テンプレートが工作機械の作業台に確実かつ確実に取り付けられるよう、適切な数のラグを設ける。