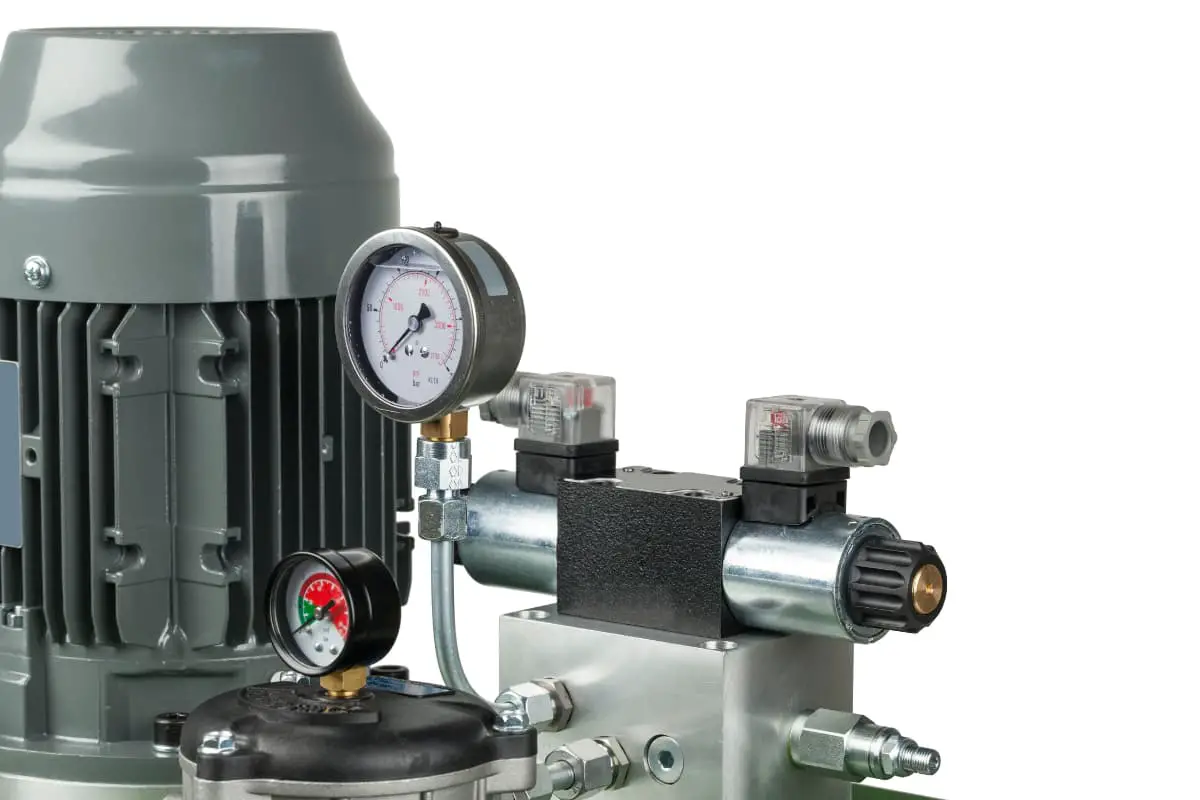
油圧システムにおいて、アキュムレータ、フィルタ、タンク、熱交換器、配管などの構成部品は補助部品である。これらの構成部品は比較的単純な構造で、機能も単一であるが、油圧システムの作動性能、騒音、温度上昇、信頼性に直接影響する。
したがって、油圧補助部品には十分な注意を払う必要がある。油圧補助部品のうち、ほとんどの部品は標準化されており、専門メーカーによって生産されているため、設計プロセスで選択することができる。オイルタンクのような標準化されていない部品は、種類が少なく、要件が大きく異なるため、油圧機器の要件に応じて設計する必要がある場合がある。
I.フィルター
1.フィルターの機能と性能
(1) フィルターの機能
油圧システムでは、内部形成または外部からの侵入により、作動油中に汚染物質が必然的に存在する。これらの汚染粒子は、油圧部品の摩耗を促進するだけでなく、バルブの小孔を詰まらせたり、バルブスプールを詰まらせたり、シールに傷をつけたりして、油圧バルブの誤動作やシステムの故障の原因となる。
したがって、作動油中の不純物や汚染粒子を清浄化する必要がある。現在、作動油の清浄度を管理する最も効果的な方法はフィルタを使用することである。フィルタの主な機能は作動油をろ過し、清浄度を制御することである。
(2) フィルターの性能指標
フィルターの主な性能指標には、濾過精度、流量、圧力損失などがあり、濾過精度が第一の指標となる。
1) ろ過精度
フィルタは、特定の孔径のフィルタエレメントを使用して汚染物質をろ過する。ろ過精度とは、フィルタによって作動油からろ過される不純物粒子の最大サイズ(平均粒径dで表される)を意味する。
現在使用されているフィルターは、濾過精度によって、粗いフィルター(d≧0.1mm)、標準フィルター(d≧0.01mm)、細かいフィルター(d≧0.001mm)、超微細フィルター(d≧0.0001mm)の4段階に分けられる。
濾過精度を選択する原則は、濾過された汚染物質粒子の大きさが油圧部品のシーリングクリアランスの半分以下になるようにすることである。システム圧力が高ければ高いほど、油圧部品の比較的可動な部品間のはめあいすきまは小さくなるため、より高いろ過精度が要求される。油圧システムのろ過精度は主にシステム圧力に依存する。表 6-1 にフィルタろ過精度の推奨値を示す。
表1 フィルターろ過精度の推奨値
システムタイプ | 潤滑システム | 送電システム | サーボシステム | ||
圧力/MPa | 0-2.5 | 14 | 4<p<21 | >21 | 21 |
ろ過精度/μm | 100 | 25-50 | 25 | 10 | 5 |
2) 流量
フィルターの流量は一般に定格流量で表され、フィルターエレメントのろ過面積に比例する。
3) 圧力損失
定格流量におけるフィルターの入口と出口の圧力差。一般に、フィルターの流量容量が大きいほど、圧力損失は小さくなる。
4) その他の性能特性
フィルターのその他の性能特性とは、主にフィルターエレメントの強度、フィルターエレメントの寿命、フィルターエレメントの耐食性などの定性的な指標を指す。これらの特性はフィルターによって大きく異なることがあり、その長所と短所は比較することで判断することができる。
2.フィルターの代表的な構造
濾過メカニズムによって、フィルタはメカニカルフィルタとマグネットフィルタの2つに分類される。前者は、作動油がフィルタエレメントの孔を通過する際に、フィルタエレメントの片面に汚染物質の粒子を捕捉するものであり、後者は、作動油が通過する際に、磁気フィルタエレメントを用いて作動油中の強磁性粒子を吸着するものである。
一般的な油圧システムではメカニカルフィルタがよく使用されますが、より高い要求があるシステムでは、上記の両方のタイプのフィルタを組み合わせて使用することができます。ここでは、メカニカルフィルタを中心に紹介する。
(1) 金網フィルター
図1に示すように、金網フィルターは、上部エンドキャップ1と下部エンドキャップ4の間に接続された多数の孔を有する円筒形のプラスチック(または金属)骨格からなり、1層または数層のフィルターメッシュ2が骨格に巻き付けられている。
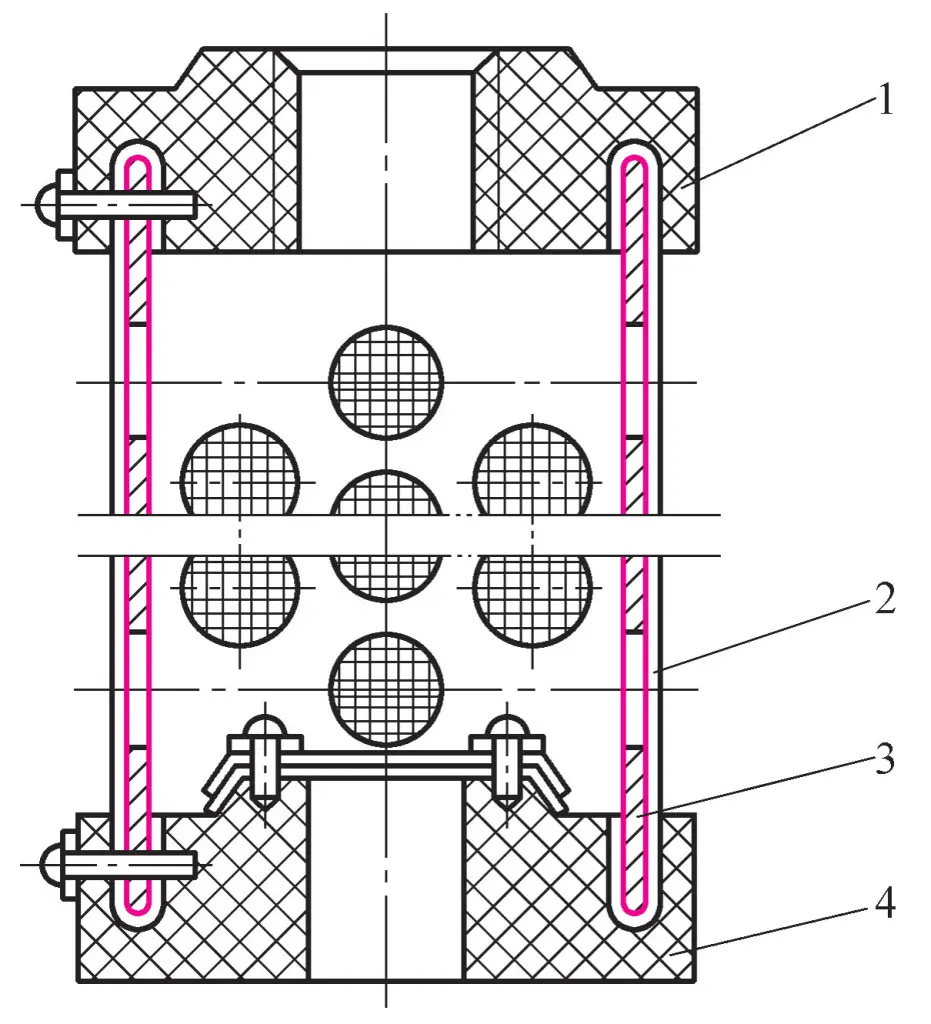
1-アッパーエンドキャップ
2-フィルターメッシュ
3-スケルトン
4-下部エンドキャップ
フィルター作動時、作動油は外側からフィルターメッシュを通ってフィルターに入り、上部キャップポートからシステム内に入ります。このフィルタは濾過精度0.13~0.04mm、圧力損失0.025MPa以下の粗いフィルタである。このタイプのフィルターの濾過精度は、銅金網のメッシュサイズと銅金網の層数に関係します。
金網フィルターの特徴は、構造が簡単で、油流量が多く、圧力損失が小さく、洗浄が容易であるが、濾過精度が低いことである。一般的に油圧ポンプの吸込口に設置され、ポンプを保護する。
(2) 巻線フィルター
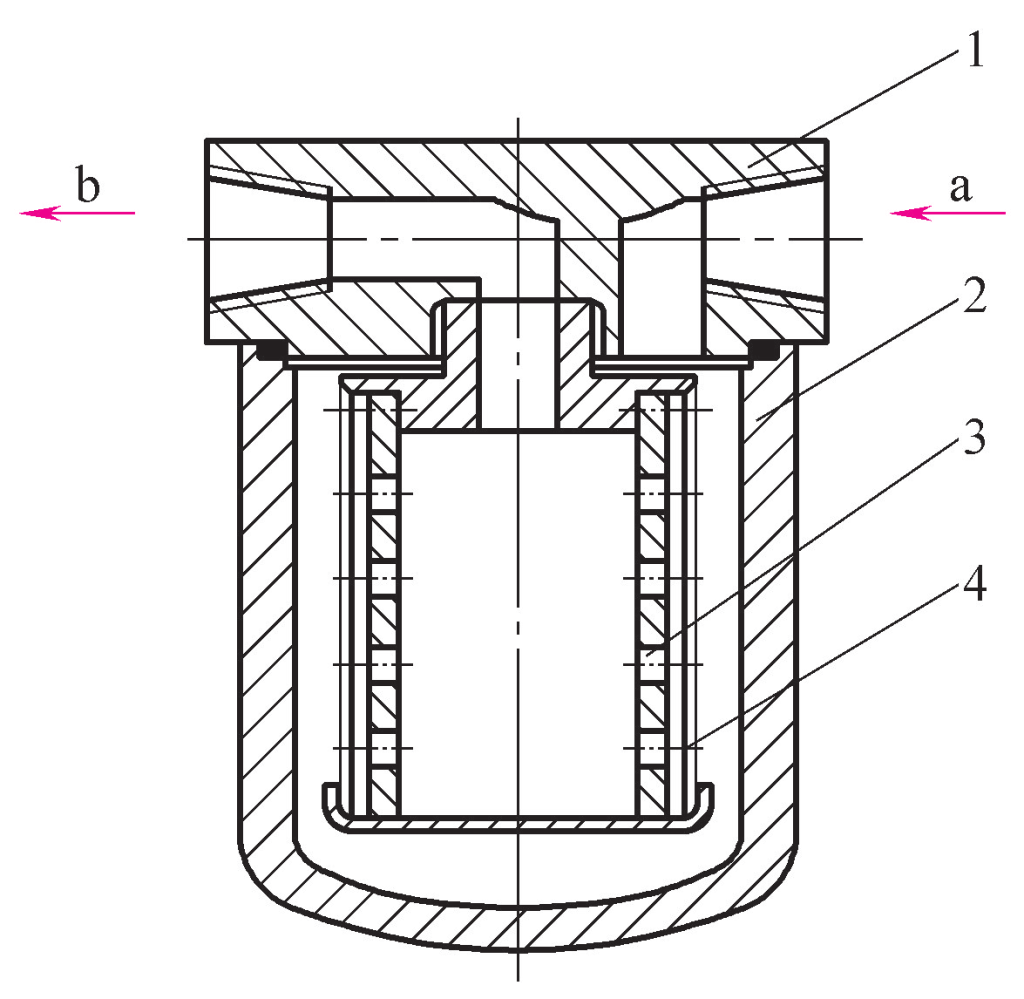
1-エンドキャップ
2-住宅
3-スケルトン
4-金属巻線
濾過精度は30μm、50μm、80μmの3段階で、定格流量は6~250L/min。定格流量時の圧力損失は0.03~0.06MPa。巻線フィルターは、吸込配管用と圧力配管用に分けられる。
前者は油圧ポンプのサクションパイプに取り付けられ、ろ過精度は0.05~0.1mm、定格流量時の圧力損失は0.02MPa以下、後者は油圧システムのプレッシャーパイプに使用され、ろ過精度は0.03~0.08mm、圧力損失は0.06MPa以下である。
このタイプのフィルターの特徴は、構造が簡単で、オイルフロー性能がよく、ろ過精度が比較的高いため、広く使用されている。欠点は、洗浄が難しいことと、フィルターエレメントの強度が低いことである。主に中低圧システムで使用される。
(3) ペーパーコアフィルター
ペーパーコアフィルターは濾過材として濾紙を使用する。フェノール樹脂または木材パルプでできた厚さ0.35~0.7mmの平織りまたは波織りの微多孔濾紙が、穴のあいた錫メッキ鉄の骨格に巻き付けられ、ペーパーフィルター・コアを形成する(図3)。オイルはフィルター・コアの外側からろ紙を通ってコアに流れ込み、その後、通路aを通って外に出る。
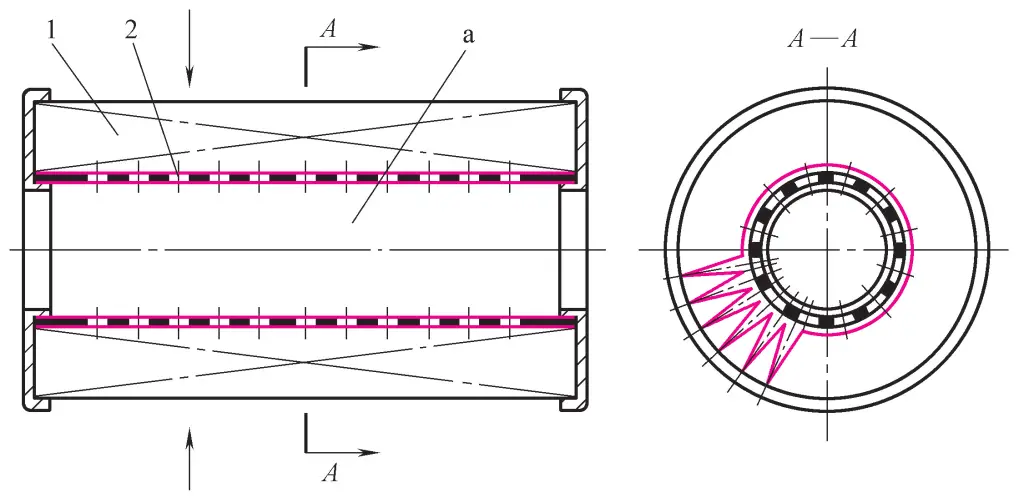
1-フィルターペーパー
2-スケルトン
濾紙1の濾過面積を大きくするため、紙芯は一般に折り畳み状に作られている。このタイプのフィルターには2種類の濾過精度の仕様があります:0.01mmと0.02mmがあり、圧力損失は0.01~0.04MPa。濾過精度が高いのが特徴です。欠点は、一度目詰まりすると洗浄ができず、定期的にペーパーコアの交換が必要なことです。強度が低く、一般的に精密濾過システムに使用される。
(4) 焼結フィルター
図4に示すように、焼結フィルターはエンドキャップ1、ハウジング2、フィルターエレメント3から構成されている。フィルタエレメントは粒状の銅粉を焼結したものである。作動油は孔aから入り、銅粒子間の微細孔を通ってフィルターエレメントの内部に入り、孔bから流出する。
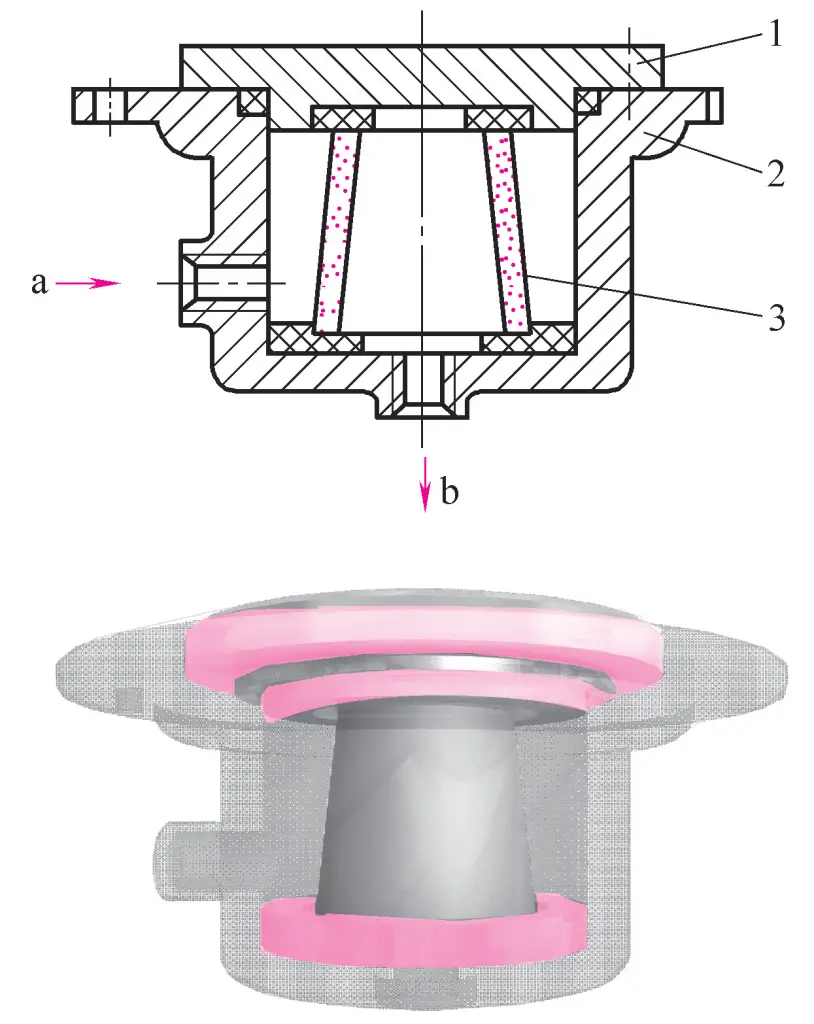
1-エンドキャップ
2ケーシング
3-フィルター・エレメント
焼結フィルターの濾過精度は、フィルターエレメント上の銅粒子間の微細孔の大きさに関係する。異なる粒子径の粉末を選択し、異なる厚さのフィルターエレメントを作ることで、異なる濾過精度を達成することができます。
焼結フィルターの濾過精度は0.001~0.01mm、圧力損失は0.03~0.2MPaである。このタイプのフィルターの特徴は、強度が高いこと、様々な形状に加工できること、製造が簡単なこと、濾過精度が高いことなどである。欠点は、洗浄が難しいこと、金属粒子が剥離しやすいことである。細かい濾過が必要な場合に使用される。
3.フィルターの選択
フィルタを選択する場合、油圧システムの技術的要件とフィルタの特性に基づいて主に検討する。考慮すべき主な要素は以下の通りである:
(1) システム使用圧力
システムの使用圧力は、フィルタの精度を選択する主な基準の1つである。システム圧力が高いほど、油圧部品のはめあい精度は高くなり、したがって要求されるろ過精度も高くなる。
(2) システム流量
フィルターの流量容量は、システムの最大流量によって決定される。フィルターの定格流量は、システムの流量を下回ってはならない。そうでないと、フィルターの圧力損失が大きくなり、フィルターが目詰まりしやすくなり、寿命が短くなる。しかし、フィルターの定格流量が大きくなればなるほど、その容積は大きくなり、コストも高くなる。したがって、適切な流量を選択する必要がある。
(3) フィルターエレメントの強度
フィルターエレメントの強度は重要な指標である。フィルター構造によって強度は異なる。高圧または高衝撃の油圧回路では、強度の高いフィルタを選択する必要がある。
4.フィルターの設置
フィルターの設置位置は、システムの必要性に応じて決定され、一般的には図5に示すように様々な位置に設置することができる。
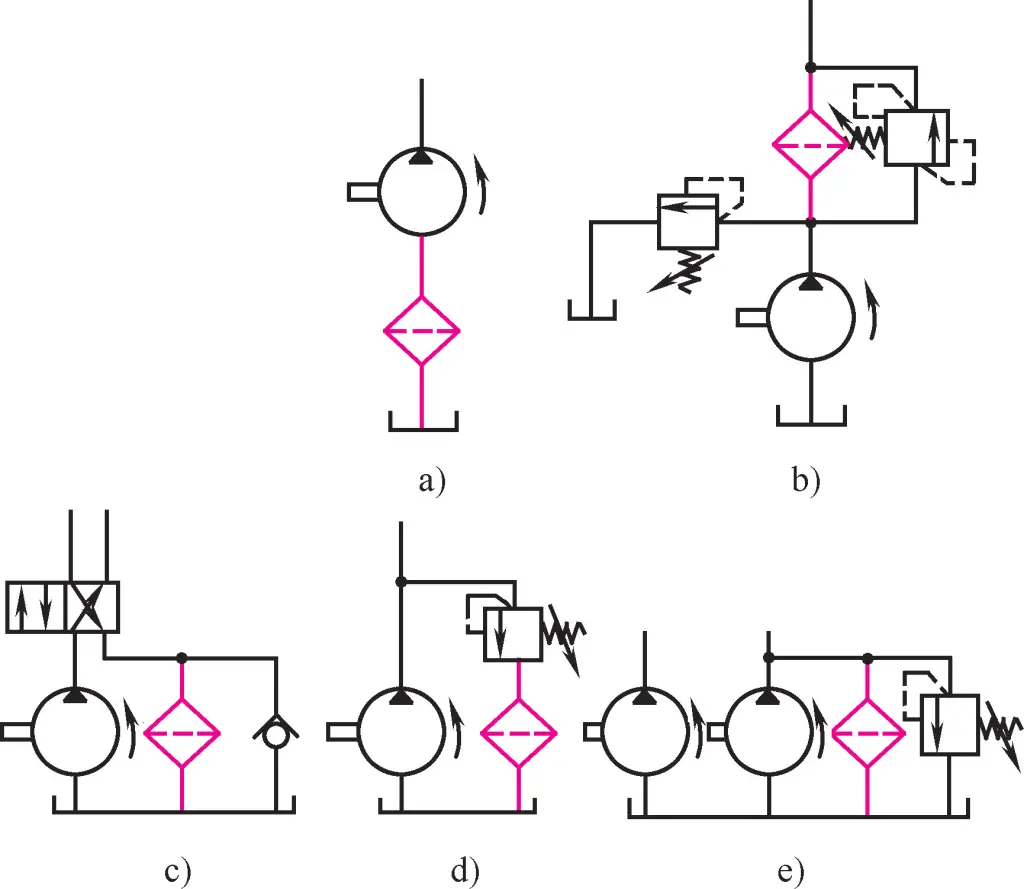
(1) 油圧ポンプの吸込口に取り付ける。
図 5a に示すように、油圧ポンプの吸込口にフィルタを設置することで、システム内の全構成部品を保護す ることができる。しかし、ポンプの吸込抵抗には限界があるため、圧力損失の低いメッシュフィルタしか選択できない。このタイプのフィルタは濾過精度が低く、ポンプの摩耗によって発生した粒子がシステム内に侵入し、他の油圧部品を十分に保護することができない。他のフィルタは油路に直列に接続して使用する必要がある。
(2) 油圧ポンプ出口への設置
図5bに示すように、この取り付け方法は、ポンプを除くすべての油圧部品を効果的に保護することができる。しかし、フィルタは高圧で作動するため、フィルタエレメントには高い強度が要求される。ポンプの過負荷やフィルタの破損の原因となるフィルタの目詰まりを防止するため、目詰まりインジケータやバイパ スバルブをフィルタに併設して保護することが多い。
(3) リターン・オイル・ラインへの取り付け
図5cに示すように、フィルタはシステムの戻り油ラインに設置される。この方法では、油タンクや配管壁からの酸化層の剥離や油圧部品の摩耗によって生じる粒子をろ過することができ、タンク内の作動油の清浄度を確保し、油圧ポンプやその他の部品を保護することができる。戻り油の圧力は比較的低いため、必要なフィルタ強度はそれほど高くする必要はない。
(4) 支線への設置
この方法は図5dに示すように、主にリリーフバルブの戻り油ラインに設置される。これは主油ラインの圧力損失を増加させず、フィルタ流量は油圧ポンプ流量より小さくすることができ、経済的で合理的である。しかし、すべての油をろ過することはできず、不純物がシステム内に入らないようにすることはできない。
(5) 分離ろ過
図 5e に示すように、油圧ポンプとフィルタを用いてシステムとは独立したフィルタリング回路を形成し、システ ム内の不純物を連続的に除去してシステムの清浄度を確保する。一般に大型の油圧システムで使用される。
II.アキュムレーター
アキュムレータは、油圧システムにおいて圧力エネルギーの貯蔵と放出を行うコンポーネントである。また、短時間のオイル供給やシステムの振動や衝撃の吸収にも使用されます。
1.アキュムレータの種類と構造
アキュムレータには、主に重量式、スプリング式、ガスチャージ式の3種類がある。
(1) 加重アキュムレーター
ウエイト式アキュムレータは、図6に示すように、ウエイトの位置変化を利用してエネルギーの蓄積と放出を行う。おもり1はプランジャ2を介して作動油3に作用し、圧力を発生させます。
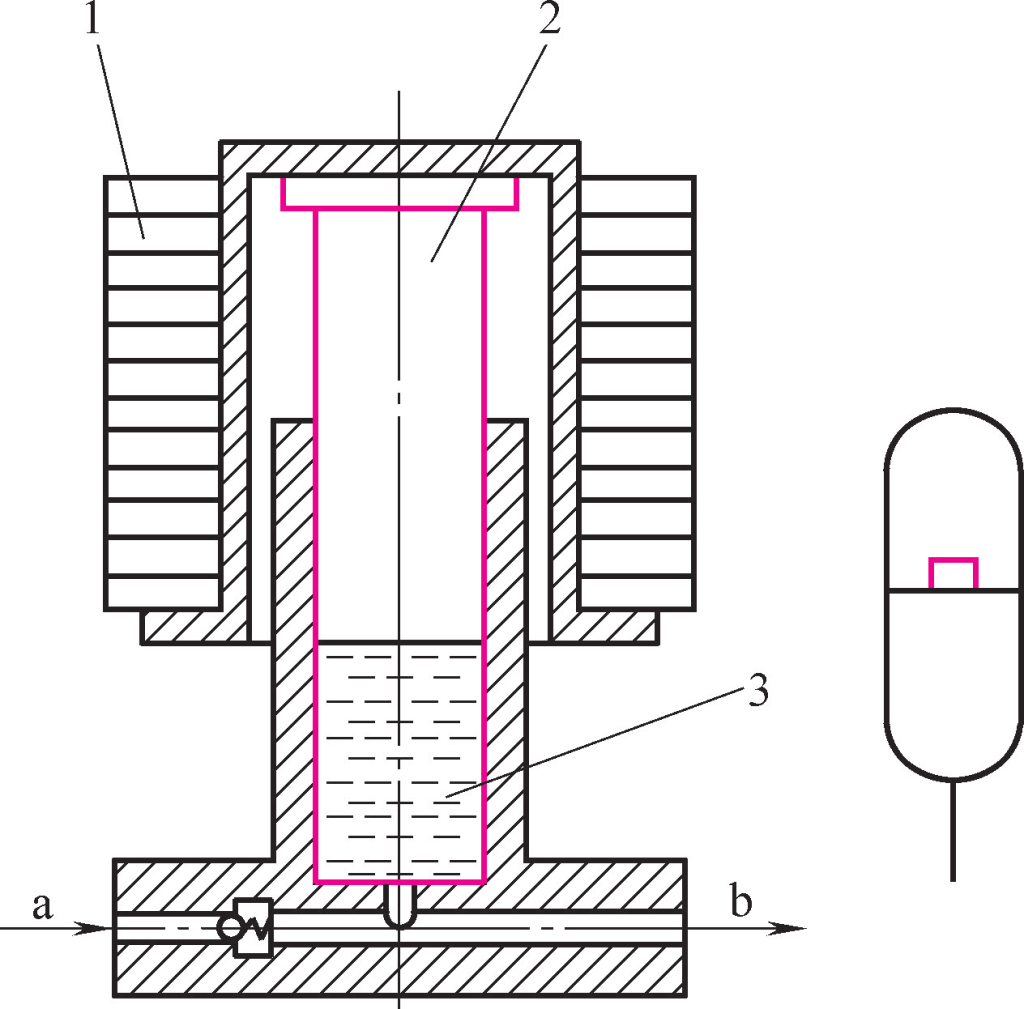
1-重量
2プランジャー
3-作動油
このタイプのアキュムレータは、構造が簡単で圧力も安定しているが、容量が小さく、容積が大きく、応答性に融通が利かず、漏れやすいという欠点がある。現在のところ、一部の大型固定機器の油圧システムにのみ使用されている。
(2) スプリング式アキュムレーター
図7は、ばねの伸縮を利用してエネルギを蓄えたり放出したりするばね式アキュムレータを示している。スプリング 1 の力はピストン 2 を介して作動油 3 に作用する。作動油の圧力は、ばねの予圧とピストンの有効作用面積に依存する。ばねの力が伸縮中に変化すると、その結果生じる油圧も変化する。
このばらつきを小さくするためには、一般にばねの剛性を高くしすぎず、ばねのトラベルを大きくしすぎず、このタイプのアキュムレータの使用圧力を制限する必要がある。このアキュムレータは、低圧で小容量のシステムで使用され、多くの場合、油圧システムのバッファリングに使用される。スプリング式アキュムレータは、構造が簡単で比較的敏感な応答性を持つが、容量が小さく耐圧性が低い。
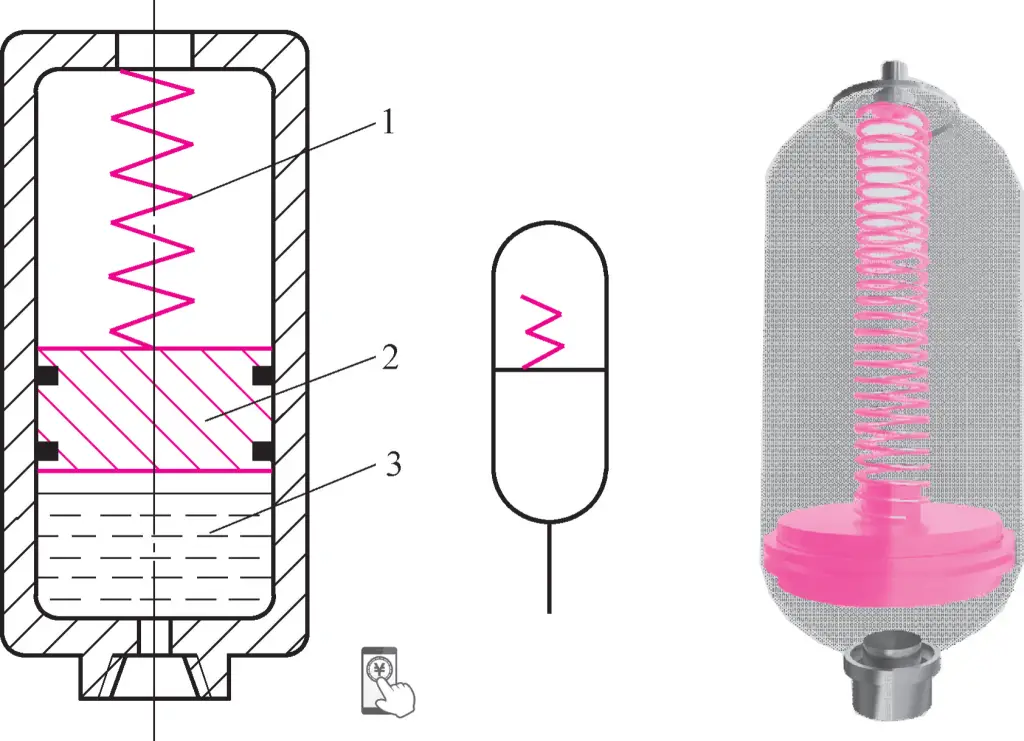
1-スプリング
2ピストン
3-作動油
(3) ガスチャージ式アキュムレーター
ガスチャージ式アキュムレータは、ガスを圧縮・膨張させることでエネルギーを貯蔵・放出します。安全上の理由から、使用されるガスは一般に不活性ガスまたは窒素です。一般的に使用されるガスチャージ式アキュムレータには、図8に示すようなピストン式とブラダ式があります。
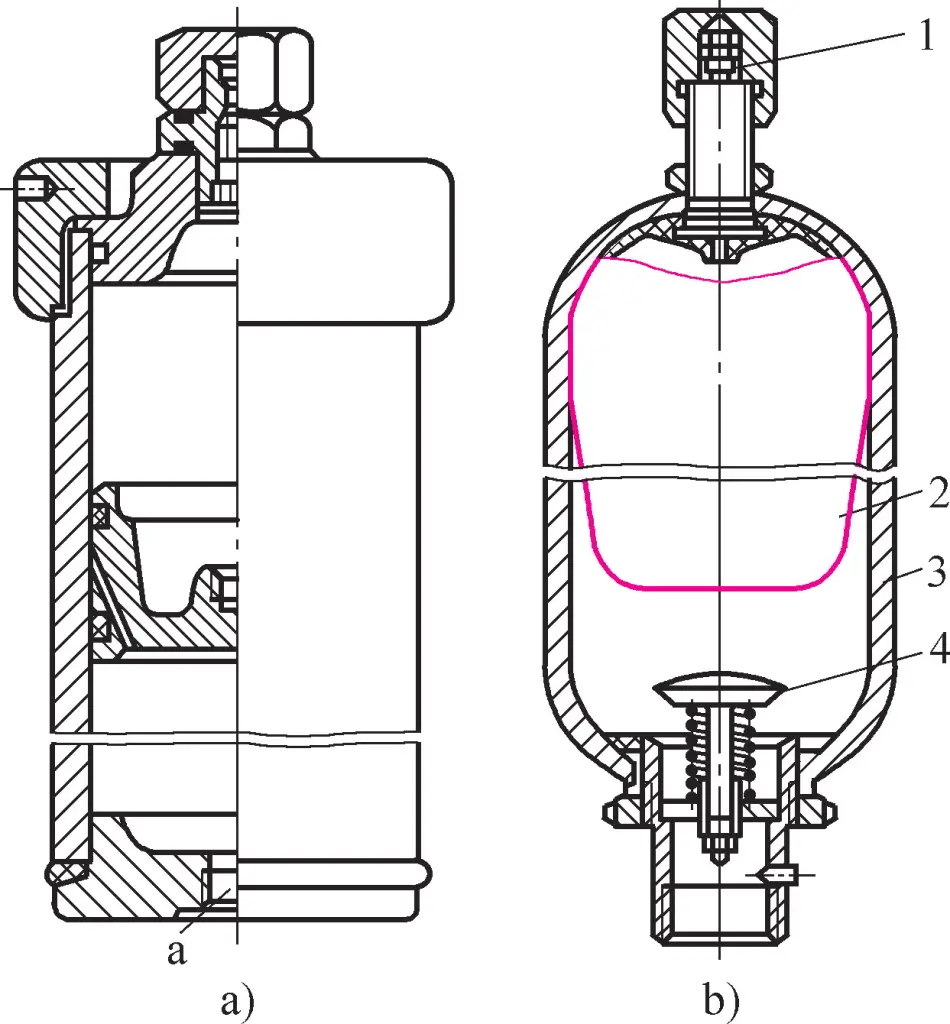
a) ピストン式アキュムレータ
b) ブラダー型アキュムレーター
1-ガスバルブ
2-ガスブラダー
3シェル
4-リミットバルブ
1) ピストン式アキュムレータ 図 8a はピストン式アキュムレータを示し、作動油がポート a から入り、ピストンを押し、上部チャンバ内のガスを圧縮してエネル ギを蓄える。システム圧力がアキュムレータ内の圧力より低くなると、ガスがピストンを押して作動油を放出し、シス テムニーズを満たす。
このタイプのアキュムレータは、構造が簡単で、作動が確実で、保守が容易であるという長所がある。しかし、シリンダの加工精度が高く、ピストンシールの摩耗やピストンの慣性・摩擦の影響を受けるため、コストが高い、液漏れしやすい、応答感度が悪いなどの欠点がある。
2) ブラダ式アキュムレータ 図 8b はブラダ式アキュムレータを示し,ガスブラダ 2 がシェル 3 内に設置されている。ガス弁1はブラダ内に窒素を充填するために使用されます。作動油は入口からアキュムレータに入り、リミットバルブ4を開いてブラダを圧縮します。ブラダ内のガスは圧縮されてエネルギーを蓄えます。システム圧力がアキュムレータ圧力より低くなると、ブラダは膨張して作動油を出力し、アキュムレータはエネルギーを放出します。
リミットバルブの目的は、ブラダが膨張したときにオイルポートで突出して破損するのを防ぐことである。このタイプのアキュムレータの特長は、気体と油の完全分離、ブラダ慣性の低さ、柔軟な応答性、構造の小型化、軽量化、設置の容易さなどである。ブラダ式アキュムレータは、現在最も広く使用されているアキュムレータの一つである。
2.アキュムレータの容量計算
アキュムレータの容量は、アキュムレータを選定する際の主な指標の一つです。アキュムレータによって容量の算出方法は異なります。ここでは、補助エネルギー源として広く使用されているブラダ型アキュムレータの容量計算方法を簡単に紹介します。
運転前に、ブラダ型アキュムレータはガスで予備充電する必要があります。充填後、ブラダはアキュムレータシェルの全容積を占めるようになります。このときのブラダの体積を V0 圧力はp0 .運転中、作動油がアキュムレータに入り、ブラダを圧縮します。このとき、ブラダ内のガス体積はV1 油圧はp1 .作動油が放出された後、ブラダは膨張し、その体積は V2 となり、圧力はp2 図9に示すように。
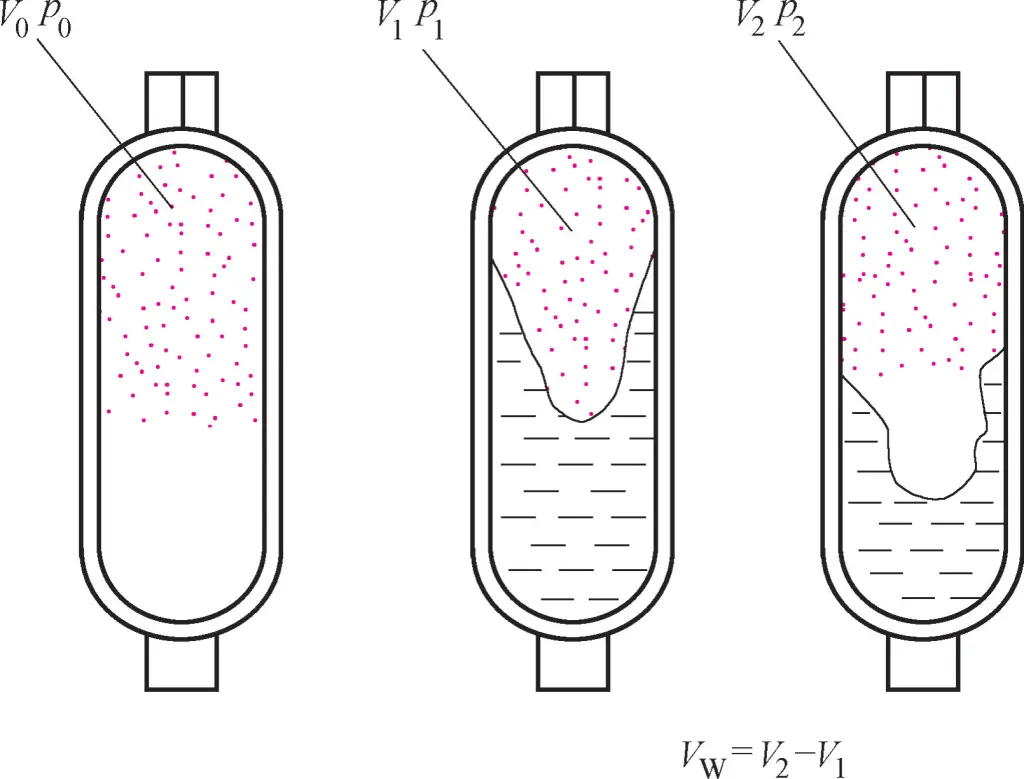
ボイルの気体の法則によれば
P0V0n=p1V1n=p2V2n=const
ここでP0 とV0 は、アキュムレータに作動油が入力されていないときのブラダ内のプレチャージガスの圧力と体積、p1 とV1 は、アキュムレータの作動状態における圧縮後のブラダ内部の圧力と体積、P2 とV2 は、アキュムレータがエネルギーを放出した後のブラダ内の圧力と体積です。
n はアキュムレータの作動状態によって決まる指数です:アキュムレータが圧力維持やリーク補償のためにゆっくりとエネルギーを放出する場合、ガスは等温条件下で動作すると考えることができ、n=1 をとります。アキュムレータが大量の給油のように急速にエネルギーを放出する場合は、n=1.4 として断熱条件下で動作すると考えることができます。
アキュムレータに蓄えられるオイルの最大量をV W そして
VW = V2 -V1
上記の2つの式を組み合わせると、次のようになる。
V0=VW (p2/p0)1/n/[1-(p2/p1)1/n]
または
VW=V0p01/n[(1/p2)1/n-(1/p1)1/n]
理論的には、充電圧力p0 に等しくなければならない。2 エネルギー解放後しかし、システムのリークにより、システム圧力がp.2 , p0 < p2 .折り畳み式ブラダーの場合、p 0 = (0.8~0.85)p2 段ボール製ブラダーの場合は、pを取る。0 = (0.6~0.65)p2 .
p 1 とp2 は、それぞれシステムの最高使用圧力と、システムの運転を維持するための最低使用圧力であり、いずれもシステム要件によって決定される。V0 はブラダの最大容積であり、アキュムレータの容積と見なすこともできる。V0 を計算する。0 標準アキュムレータ容量を選択するには、取扱説明書を参照してください。
3.アキュムレータの設置と使用
油圧システムにおけるアキュムレータの取付け位置は、その機能によって決定される。アキュムレータの使用および取付けに際しては、次の点に注意してください:
- ブラダ型アキュムレータは垂直に設置してください。斜めまたは水平に設置すると、アキュムレータのブラダとシェルが摩耗し、アキュムレータの寿命に影響します。
- 圧力の脈動や衝撃を吸収するためのアキュムレータは、振動源の近くに設置する。
- パイプラインに設置されるアキュムレータは、アキュムレータがエネルギーを貯蔵または放出するときに発生する運動量反力に耐えるように、ブラケットまたはバッフルで固定する必要があります。
- アキュムレータと配管の間には、インフレーションやメンテナンスのために逆止弁を設置する必要があります。ポンプ停止時の油の逆流を防止するため、アキュムレータと油圧ポンプとの間に一方向弁を設ける。
III.オイルタンク
オイルタンクの主な機能はオイルを貯蔵することであり、タンク本体は放熱、沈殿物の沈降、オイルからの空気分離、設置台としての役割も果たす。
1.オイルタンクの分類と代表的な構造
(1) 石油タンクの分類
オイルタンクは開放構造と閉鎖構造に分類される。開放構造タンクは、油面が大気と連通する自由な構造で、主に各種固定設備に使用され、閉鎖構造タンクは、油が大気から隔離された構造で、主に移動設備や車両に使用される。
開放型オイルタンクは、さらに一体型と分離型に分けられる。一体型オイルタンクは、メインマシンのベースをオイルタンクとして使用する。コンパクトで油圧部品の漏れを回収しやすいが、放熱性が悪くメンテナンスが困難で、主機の精度や性能に影響を与える。
セパレート型オイルタンクは、メインマシンから切り離された独立したオイル供給ステーションを形成する。一体型に比べて放熱性、メンテナンス性、修理性に優れるが、床面積が増える。現在、精密機器ではセパレートタイプが主流である。
(2) オイルタンクの典型的な構造
図10は開放構造の分離型オイルタンクである。タンク本体は一般に厚さ2.5~4mmの鋼板を溶接したもので、表面には耐油コーティングが施されている。タンクの中央には、油圧ポンプの吸込管1と戻り管4を分離するための2つのバッフル7、9があり、戻り管から発生する沈殿物や泡をブロックしている。タンク上部の取付板5は、電動機、油圧ポンプ、一体型ブロックなどを設置するための厚鋼板製である。
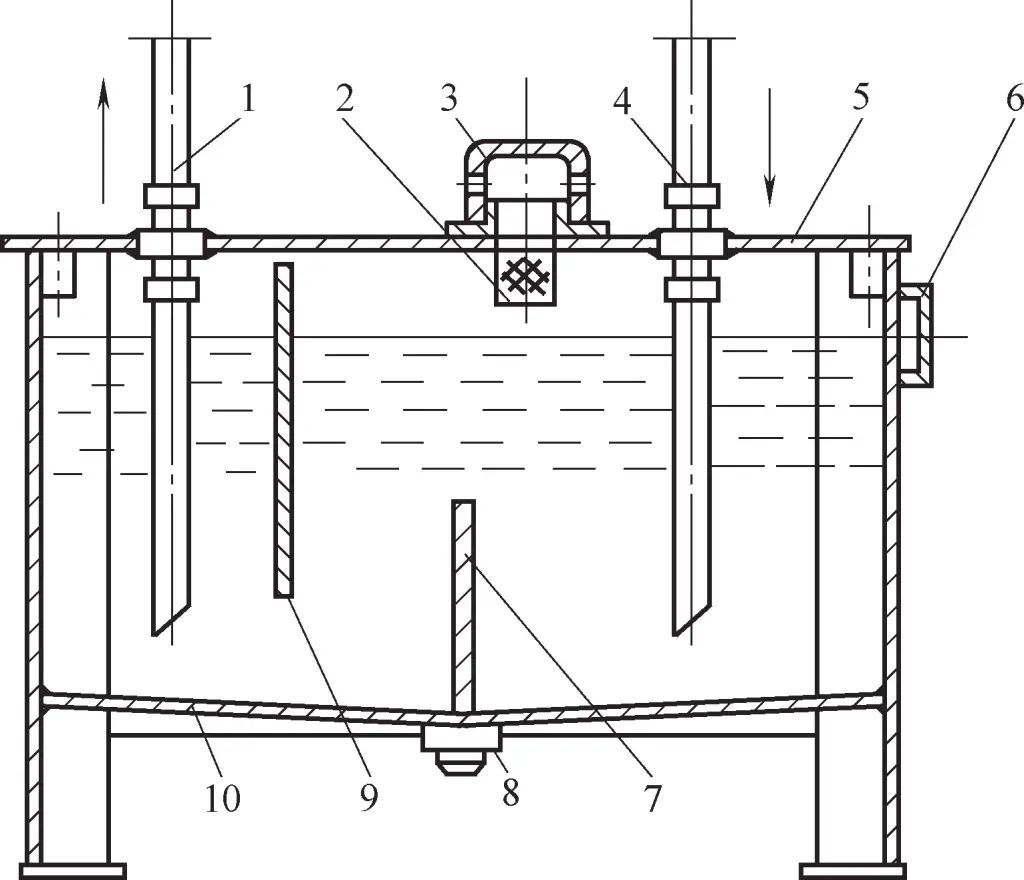
1-吸引パイプ
2-フィルタースクリーン
3-ダストカバー
4-リターンパイプ
5-マウンティングプレート
6レベルゲージ
7-下部バッフル
8-ドレンバルブ
9-アッパーバッフル
10タンクボディ
取り付けプレートには、オイル充填時のフィルタリングとタンク内への異物落下を防止するためのフィルタスクリーン2とダストカバー3が装備されている。ダストカバーの側面には大気と連通する小さな穴が開いている。タンク側面には油量を表示するレベルゲージ6が設置されている。タンク底部には、オイル交換時にオイルや沈殿物を排出するためのドレンバルブ8が設置されている。
2.オイルタンクの設計
オイルタンクは非標準的な部品であり、しばしば実用的な状況における特定のニーズに応じて設計される。オイルタンクを設計する際、主に考慮されるのはタンクの容積、構造、放熱である。紙面の都合上、設計手法の簡単な紹介にとどめる。
(1)オイルタンク容量の推定
オイルタンクの容積は、設計時に決定される主なパラメータである。タンク容積が大きいと放熱効果は高いが、油の使用量が多くなり、コストも高くなる。タンク容積が小さければ、占有スペースが小さくなり、コストも下がるが、放熱条件が不十分となる。
実際の設計では、経験式を用いてタンク容積を最初に決定し、タンクの放熱量 Q₀を確認し、システムの発熱量 Q₁ を計算することができる。タンクの放熱量が油圧システムの発熱量より大きい場合(Q₂>Q₃)、タンク容積は適切であり、そうでない場合は、タンク容積を増やすか、冷却手段を採用する必要がある(タンクの放熱量と油圧システムの発熱量の計算については、関連マニュアルを参照)。
オイルタンクの容積を推定する経験式は次のとおりである。
V=αq
式中
- Vはオイルタンクの容積(L);
- q は油圧ポンプの定格総流量(L/min)である;
- αは経験係数(min)で、低圧系ではα=2~4min、中圧系ではα=5~7min、中高圧高出力系ではα=6~12min。
(2) 設計上の考慮事項
容積を決定した後、オイルタンクの構造設計はオイルタンクの様々な機能を実現するための主な仕事になる。オイルタンクの構造を設計する際には、以下の点に注意する必要がある:
1) タンク本体には十分な強度と剛性が必要である。石油タンクは一般的に2.5~4mm厚の鋼板を溶接したもので、大型のものは補強リブを溶接する必要がある。
2) ポンプのサクションパイプには、100~200メッシュのスクリーンフィルターを取り付け、フィルターとタンク底部との間隔を20mm以上とする。ポンプが空気を吸い込んで騒音を発生するのを防ぐため、フィルターは油面より上に露出させないこと。システムの戻り油配管は、飛散や気泡の発生を防ぐため、油面より下に挿入すること。
3) サクション・パイプとリターン・パイプは可能な限り離して設置する。バッフルを数枚使用して分離し、油の循環距離を長くして、油中の汚染物質や気泡を完全に沈殿または分離させる。バッフルの高さは、一般に油面の高さの3/4である。
4) 汚染防止シーリング。オイル汚染を防止するため、カバープレートと窓のすべての接続部にシーリングガスケットを追加し、オイルパイプが通過するすべての穴にシーリングリングを追加する必要があります。
5) オイルタンクの底は勾配があり、タンク底と地面との間に一定の距離があること。オイルドレンプラグをタンク底部の最も低い位置に設置する。
6) オイルタンクの内面は、特別に処理されるべきである。オイルタンク内壁のコーティングの剥離を防止するため、新しいオイルタンクの内壁は、ショットブラスト、酸洗浄、表面洗浄を行った後、作動液に適合するプラスチックフィルムまたは耐油ワニスの層でコーティングする。
IV.熱交換器
油圧システムが作動しているとき、作動油の温度は15~65℃に維持されなければならない。油温が高すぎると、油は急速に劣化し、粘度が低下してシステムの効率を低下させる。油温が低すぎると油の流動性が悪化し、システムの圧力損失が増加し、ポンプの自吸能力が低下する。したがって、油温を適正に保つことは油圧システムを正常に作動させるための必要条件である。
車両負荷などの制約により、オイルタンク自体の自然調節では油温要件を満たせない場合があり、機器の油温要件を満たすために外部設備が必要となる。熱交換器は、最も一般的に使用される温度制御設備である。熱交換器は、クーラーとヒーターの2つのカテゴリーに分けられる。
1.クーラー
クーラーは冷却方式によって水冷式、空冷式、アンモニア冷却式などに分類される。このうち、水冷式と空冷式が一般的な冷却方式である。
図11aは、一般的に使用されているサーペンタイン管式ウォータークーラーであり、サーペンタイン管がオイルタンク内に設置され、冷却水が管内を流れてオイルで発生した熱を除去する。このタイプのクーラーは構造が簡単で低コストであるが、熱交換効率が低く、水の消費量が多い。
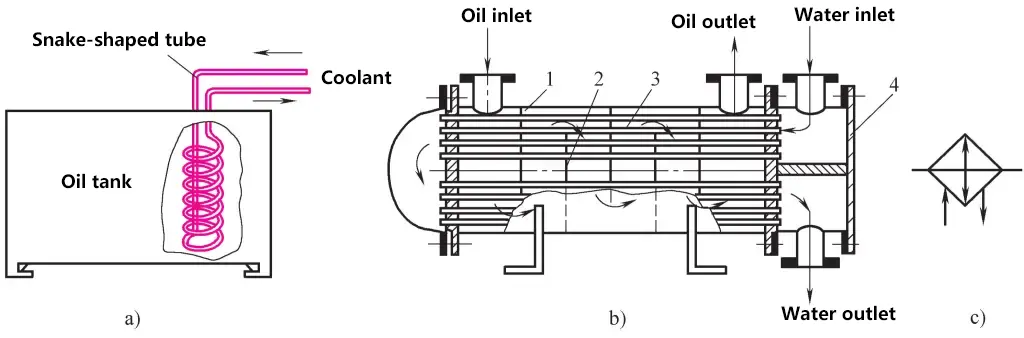
a) サーペンタイン・チューブ・タイプ
b) シェル&チューブ・タイプ
c) グラフィック・シンボル
1シェル
2バッフル
3-冷却銅管
4-シェル右コンパートメント
図11bは、シェル1、冷却用銅管3、バッフル2からなる、大型機器で一般的に使用されるシェル&チューブクーラーを示しています。シェル1の左側のオイルポートから作動油が入り、冷却のために複数の冷却銅管3とバッフルを通り、シェルの右側のポートから流出します。
冷却水は、シェルの右コンパートメント4の上部入口から入り、上部冷却銅管3を通ってシェルの左エンドキャップに流れ、下部冷却銅管3を通ってシェルの右コンパートメント4の下部出口から出ます。複数の冷却銅管とバッフルの効果により、このタイプの冷却器は熱交換効率が高いのですが、サイズが大きく高価です。
図11cにクーラーの図記号を示す。移動体の油圧機器では空冷式ラジエータが一般的である。空冷式クーラにはチューブタイプとフィンタイプ(単層管壁)があり、水冷式に比べて小型であるが冷却効率が低い。
クーラは一般に油圧システムの戻り油ラインまたはリリーフ弁のオーバーフローラインに設置される。図12に示すように、ポンプから出力された作動油は直接システムに入り、加熱された戻り油とリリーフ弁からオーバーフローした油はクーラ1で一緒に冷却されてからオイルタンクに戻る。逆止弁2はクーラを保護するためのものであり、シャットオフバルブ3はクーラが不要なときに開いて作動油の通路とする。
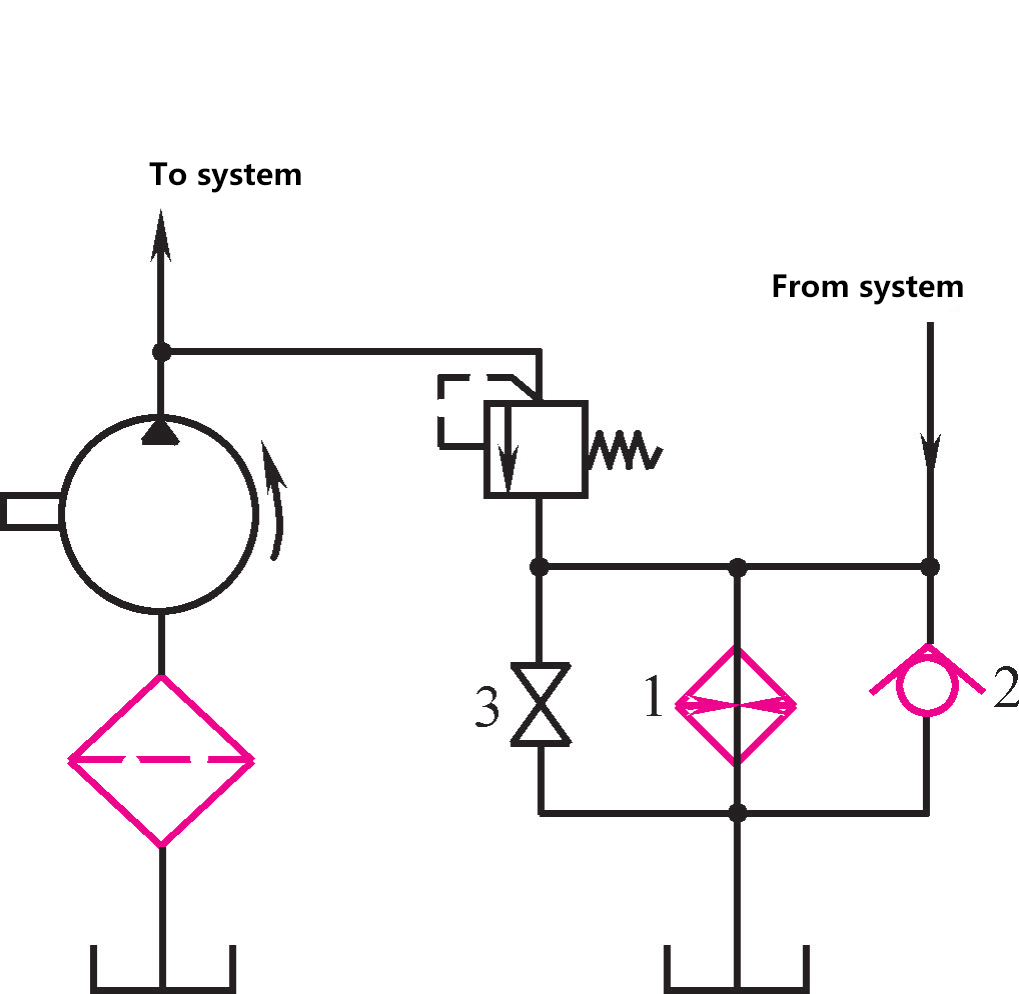
1-クーラー
2-チェックバルブ
3-シャットオフバルブ
2.ヒーター
油圧システムに使用されるヒーターは、一般に電気加熱方式を採用している。電気ヒーターは構造が簡単で、制御が便利で、所望の温度を設定でき、温度制御誤差が小さい。
しかし、電気ヒーターの加熱管は作動油と直接接触するため、タンク内の油温にムラが生じやすく、時には油のクラッキングを促進することもある。そのため、ヒータを複数設置し、ヒータ制御を高くしすぎないようにする。図13aに示すように、ヒータ2はオイルタンクのタンク壁に設置され、フランジで接続される。図13bにヒーターの図記号を示す。

1-オイルタンク
2ヒーター
V.コネクター
オイルパイプとパイプ継手はコネクタと呼ばれ、分散した油圧コンポーネントを接続して完全な油圧システムを形成する機能を果たす。コネクタの性能や構造は、油圧システムの作動状態に直接影響する。ここでは、油圧機器の設計やコネクタ選定の参考として、一般的に使用されている油圧コネクタの構造を紹介する。
1.オイルパイプ
(1) オイルパイプの種類
油圧システムでは、鋼管、銅管、ナイロン管、プラスチック管、ゴムホースなど多くの種類のオイルパイプが使用される。選定にあたっては、油圧システムの高圧・低圧、油圧機器の設置位置、油圧機器の使用環境などを考慮する必要がある。
1) 鋼管
シームレス鋼管と溶接鋼管に分けられる。前者は一般的に高圧システムで使用され、後者は中低圧システムで使用される。鋼管の特徴は、耐圧力が強く、価格が安く、強度が高く、剛性が高いが、組み立てや曲げ加工が難しいことである。現在、各種油圧機器に最も広く使用されているのは鋼管である。
2) 銅パイプ
銅管は真鍮管と純銅管に分けられ、純銅管の方が多く使用されている。銅管は組立や曲げ加工が容易であるなどの長所があるが、強度が低い、耐振動性に劣る、材料価格が高い、作動油が酸化しやすいなどの短所もある。一般に油圧機器内の組み立てが困難な場所や、圧力0.5~10MPaの中低圧システムで使用される。
3) ナイロンパイプ
乳白色半透明の新素材で、耐圧性能は2.5MPaと8MPa。ナイロンパイプは、低価格で曲げ加工が容易という特徴があるが、寿命が短い。低圧システムで銅パイプに代わって使用されることが多い。
4) プラスチックパイプ
プラスチックパイプは価格が安く、取り付けも簡単だが、耐圧性に劣り、老朽化しやすい。現在は、リーク・パイプとリターン・オイル・ラインにのみ使用されている。
5)ゴムホース
このオイルパイプには高圧タイプと低圧タイプがある。高圧ホースは、耐油ゴムに鋼線を編み込んだもので、鋼線の層数が多いほど耐圧性が高くなる。低圧用ホースは、帆布または綿糸の編組層がある。ゴムホースは、相対運動する油圧部品の接続に使用される。
(2) オイルパイプの計算
オイルパイプの計算では、主にパイプの内径と肉厚を決定する。
オイルパイプの内径の計算式は以下の通り。
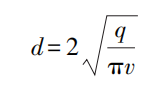
どこ
- qはオイルパイプを通る流量;
- vはパイプラインの推奨流速で、サクションパイプの場合は0.5~1.5m/sである;
- 圧力管は2.5~5m/s、戻り管は1.5~2.5m/s。
パイプ肉厚の計算式は
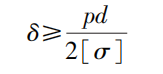
どこ
- pはパイプの内圧;
- [σ]はパイプ材料の許容応力であり、[σ]=Rm/n、ここでR m はパイプ材料の引張強さ、nは安全係数である。
鋼管用
- p<7MPaの場合はn=8とする;
- p≦17.5MPaのとき、n=6とする;
- p>17.5MPaの場合はn=4とする。
2.管継手
管継手は、配管と油圧部品または弁体とを接続する着脱可能なコネクタである。管継手は、組立・分解が容易であること、密閉性が高いこと、しっかりと接続できること、全体寸法が小さいこと、圧力損失が低いこと、製造性が高いことなどの要件を満たす必要がある。
一般的に使用される管継手には多くの種類がある。通路別では、ストレートスルー型、アングル型、ティー型、クロス型があり、バルブボディやバルブプレートとの接続方法別では、ねじ込み型とフランジ型があり、配管と継手との接続方法別では、フレア型、溶接型、フェルール型、圧着型、クイックコネクト型がある。以下では、後者の分類のみを紹介する。
(1) フレア管継手
図14aは、スリーブのクランプ作用を利用してシールするフレア管継手である。このタイプの管継手は構造が簡単で、銅管、薄肉鋼管、ナイロン管、プラスチック管などの接続に適している。
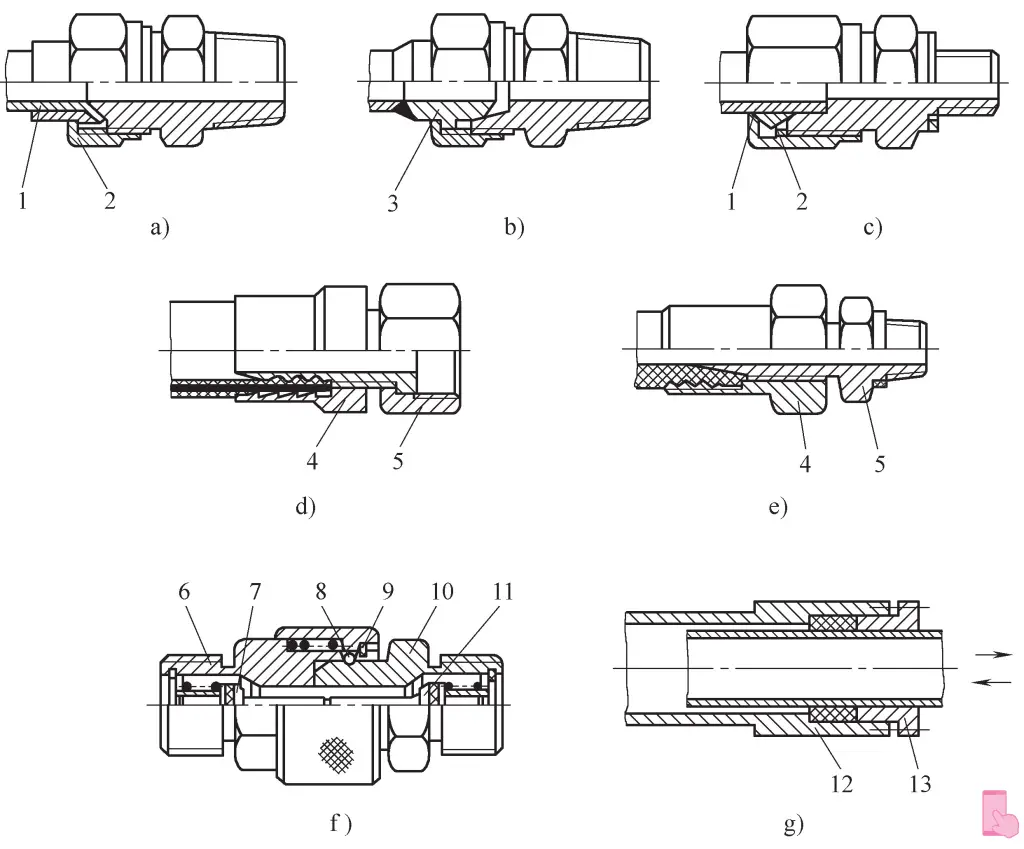
a) フレア管継手
b) 溶接管継手
c) フェルール管継手
d) 圧着管継手
e) 取り外し可能な配管継手
f) クイックコネクトフィッティング
g) 伸縮管継手
1パイプ
2-フェルール
3フィッティング・インナーコア
4フィッティング・アウター・スリーブ
5-フィッティング・コア
6ソケット
7、11-パイププラグ
8-スチールボール
9クランプ
10ノズル
12-アウターチューブ
13インナーチューブ
(2) 溶接管継手
図14bは溶接式管継手を示しており、オイルパイプが継手の内芯3に溶接されている。インナーコアの球面が継手本体の円錐形の穴と強固に接続され、良好なシール性、シンプルな構造、高い耐圧性を実現している。欠点は、溶接が比較的面倒なことである。高圧の厚肉鋼管の接続に適している。
(3) フェルール式管継手
図14cはフェルールタイプの管継手であり、高弾性のフェルール2を用いてオイルパイプ1をクランプしてシールする。構造が簡単で取付けが容易なのが特長であるが、油パイプ外壁の寸法精度が要求される。フェルール式管継手は、高圧冷間引抜継目無鋼管の接続に適している。
(4) 圧着管継手
図14dは、外側スリーブ4と内側コア5から成る圧着式管継手を示す。この継手はフレキシブルホースの接続に適している。
(5) 取り外し可能な管継手
図14eは、取り外し可能な管継手を示している。この継手の外側スリーブ4と内側コア5は六角形であり、フレキシブルホースの頻繁な分解に便利である。高圧の小口径フレキシブルホースの接続に適している。
(6) クイック・コネクト・カップリング
図14fはクイックコネクトカップリングを示し、オイルパイプの迅速な組み立てと分解を容易にします。
原理は次の通りである:カラー9が左に動くと、鋼球8がインサート10の溝から外側に引っ込み、インサートが解放される。この時、パイププラグ7と11がそれぞれのバネの力で2つのパイプ開口部を閉じ、パイプからの油漏れを防ぐ。このタイプの管継手は、頻繁に分解する必要があるフレキシブルなホース接続に適している。
(7) 伸縮式管継手
図14gは伸縮式管継手を示しており、内管13と外管12から構成されている。内管は外管内を自由にスライドでき、Oリングでシールされている。内管の外径は正確に加工する必要がある。このタイプの管継手は、接続部品間に相対的な動きがあるパイプの接続に適している。
VI.シーリング装置
シーリングは、油圧システムの漏れ問題を解決する有効な手段の一つである。油圧システムのシーリングが不十分な場合、外部漏れを引き起こし、環境を汚染する可能性がある。また、空気が油圧システム内に侵入し、油圧ポンプの性能や油圧アクチュエータの円滑な作動に影響を及ぼす可能性もある。内部漏れがひどくなると、体積効率が過度に低下したり、油温が上昇したりして、システムの誤作動を引き起こす。
1.密封装置の要件
- 使用圧力と一定の温度範囲内で良好なシール性能を持ち、圧力が上昇すると自動的にシール性能が向上すること。
- シール装置と可動部品の間の摩擦力は小さく、摩擦係数は安定していなければならない。
- 耐食性が強く、老朽化しにくく、長寿命で、耐摩耗性に優れ、摩耗後もある程度まで自己修復が可能である。
- シンプルな構造で使いやすく、メンテナンスも簡単。
2.シール装置の種類と特徴
シールはその作動原理から非接触シールと接触シールに分けられる。前者は主にクリアランスシールを指し、後者はシールエレメントシールを指す。
(1) クリアランスシール
クリアランスシールは、相対的に動く部品の合わせ面間のわずかな隙間を通してシールを実現します。クリアランスシールは、プランジャー、ピストン、バルブなどの円筒形の嵌合部によく使用されます。
クリアランスシールを使用した油圧バルブには、バルブスプールの外周面に等間隔に圧力バランスをとるための溝が複数あります。その主な機能は、半径方向の圧力を均等に分散し、油圧ロック力を低減し、ボア内のバルブスプールのセンタリングを改善し、それによってクリアランスを最小限に抑えることによって漏れを減らすことです。
さらに、圧力バランス溝によって形成される抵抗も、漏れを減らす役割を果たす。圧力バランス溝は通常、幅0.3~0.5mm、深さ0.5~1.0mmです。円筒面間のフィッティングクリアランスは、直径サイズに関係する。バルブスプールとバルブボアの場合、一般的に0.005~0.017mmです。
このタイプのシールの長所は摩擦が少ないことであるが、短所は摩耗を自動的に補正できないことである。主に、油圧ポンプのプランジャーとシリンダーの間や、スライドバルブのバルブスプールとバルブボアの間など、直径の小さい円筒面間で使用される。
(2) Oリング・シール
Oリングシールは、一般的に断面が円形の耐油性ゴムでできています。シール性能に優れ、内外面と端面の両方がシール作用を発揮します。コンパクトな構造で、可動部の摩擦が小さく、製造・組立が容易で、低コストであり、高圧・低圧の両方に使用できる。これらの特徴から、油圧システムに広く使用されている。
O-リングシールの構造と使用条件を図15に示す。図15aはO-リングシールの外形断面を示しており、図15bはシール溝に装着された状態を示しています。 1 とδ 2 はOリング装着後の予備圧縮量であり、通常圧縮率Wで表される。
W=[(d0-h)/d0x100%
固定シール、往復運動シール、回転運動シールの場合、十分なシール効果を得るためには、圧縮率がそれぞれ15%-20%、10%-20%、5%-10%に達する必要がある。
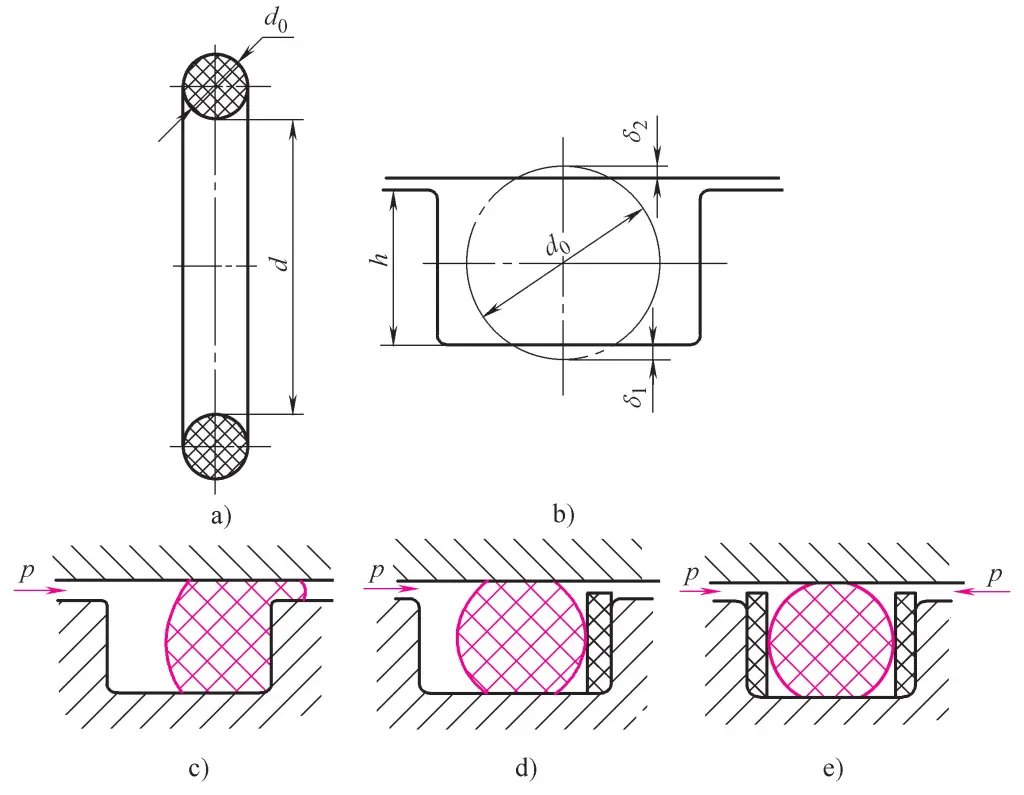
a) 外部断面
b) シール溝に装着した場合の状況
c)~e) 設置方法
作動油の使用圧力が 10MPa を超えると、往復運動中に O リングが隙間に入り込んで容易に破損する(図 15c)。これを防止するため、1.2~1.5mm 厚の PTFE バックアップリングを側面に取り付ける。一方向の力の場合は、力の反対側にバックアップリングを1つ取り付け、双方向の力の場合は、両側にバックアップリングを取り付ける(図15d、e)。
O-リング・シールの取り付け溝は、長方形の他に、V字型、アリ溝型、半円形、三角形などがある。実際に使用する場合は、関連するマニュアルや国家規格を参照する必要があります。
(3) リップシール
リップシールは、その断面形状からY字型、V字型、U字型、L字型などに分類される。その作動原理を図16に示す。油圧がシールの2つのリップエッジを隙間を形成する2つの部品の表面に押し付ける。
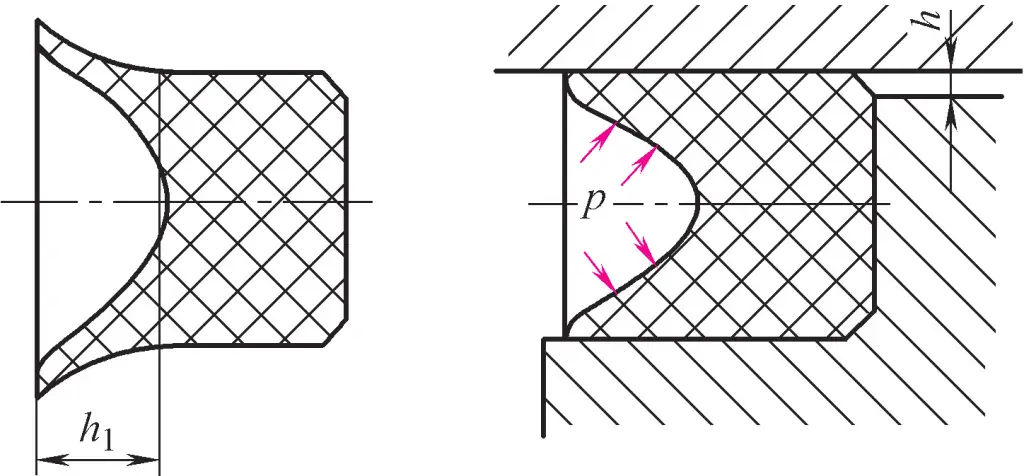
このシール作用の特徴は、使用圧力の変化に応じてシール性能を自動的に調整できることである。圧力が高いほどリップエッジが強く押され、シール性が向上し、圧力が低下するとリップエッジの締まりも低下するため、摩擦抵抗と消費電力が低減する。さらに、リップエッジの摩耗を自動的に補正することもできる。
現在、油圧シリンダでは、主にピストンやピストンロッドのシールに小型のY形シールが広く使用されている。図17aはシャフトシール、図17bはボアシールである。これらの小型Y型シールの特徴は、断面幅と高さの比が大きく、底部支持幅が大きくなり、摩擦力によるシールのめくれやねじれを防止できることである。
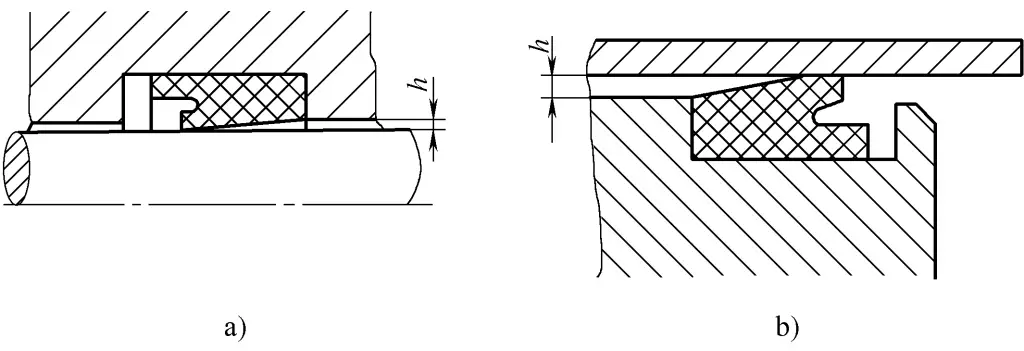
a) シャフトの場合
b) ボア用
V字型シールは、高圧・超高圧(25MPa以上)の軸封によく使用される。V字型シールは、コーティングされた布を何重にもプレスして作られ、その形状は図18に示すとおりである。

V字型シールは通常、プレッシャーリング、シールリング、サポートリングを積み重ねたもので、良好なシール性能を確保できる。圧力がさらに高い場合は、中間シールリングの数を増やすことができます。これらのシールは、取り付け時に予備締めが必要なため、摩擦抵抗が大きくなります。
リップシールを取り付けるときは、リップの開口部を作動油側に向け、2つのリップが開いて部品の表面に押し付けられるようにする。
(4) コンビネーション・シール装置
技術の進歩や機器の性能向上に伴い、油圧システムのシールに対する要求はますます高くなっている。通常のシールリングだけでは、その要求に十分に応えられなくなってきている。そこで、シールリングを含む2つ以上の部品から構成される組合せシール装置が研究開発されている。
Oリングと矩形断面のポリテトラフルオロエチレン(PTFE)プラスチック製スライディングリングからなる組み合わせシール装置を図19aに示す。
スライディングリング2はシール面に密着し、Oリング1はスライディングリングに弾性予圧を与えます。媒体圧力がゼロのときにシールを形成します。シールギャップはOリングではなくスライディングリングに依存するため、摩擦抵抗が小さく安定しており、40MPaまでの高圧に対応します。
往復運動シールでは15m/sに達し、往復スイングとスパイラル運動シールでは5m/sに達する。長方形スライディングリングコンビネーションシールの欠点は、傾きに対する抵抗力がやや弱く、高圧と低圧が交互に発生するような条件下では漏れが発生しやすいことである。
図19bは、サポートリング4とOリング1からなるシャフト用組合せシール装置です。サポートリングと被シール部3との間にラインシールがあるため、その作動原理はリップシールに似ている。サポートリングは、耐摩耗性、低摩擦性、形状保持性に優れた特殊処理合成樹脂製です。使用圧力は80MPaに達する。
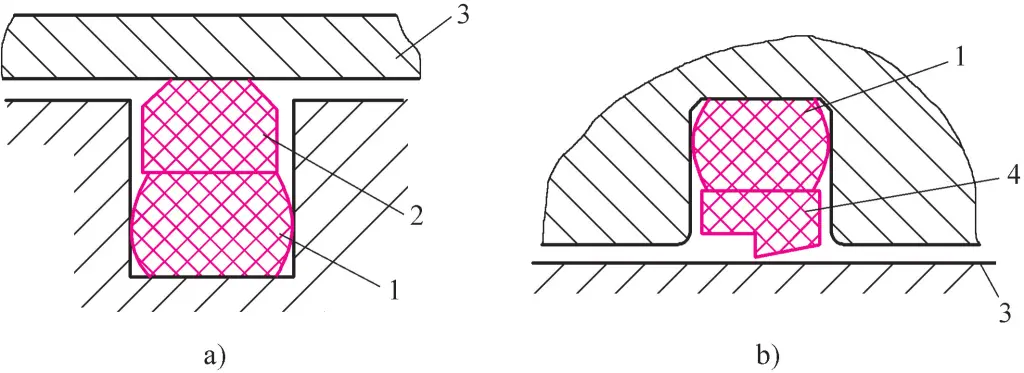
1-Oリング
2-スライドリング
3-シール部
4-サポートリング
ゴム製シールリングとスライディングリング(サポートリング)の長所を生かしたコンビネーションシールです。低摩擦で安定性が高く、信頼性が高いだけでなく、通常のゴムシールに比べて寿命が100倍近く延び、エンジニアリングの分野で広く応用されています。
(5) 回転軸のシール装置
回転軸のシール装置には様々な形状がある。図20は耐油ゴム製の回転軸用シールリングである。直角円形の鉄の骨格で内部を支持し、らせん状のバネで内周を軸に締め付けてシールしている。
この種のシールリングは、主に油圧ポンプ、油圧モーター、回転油圧シリンダーの延長軸をシールし、ケーシング外部への油漏れを防止するために使用される。使用圧力は一般に0.1MPa以下で、最大許容線速度は4~8m/sであり、潤滑条件下で作動しなければならない。
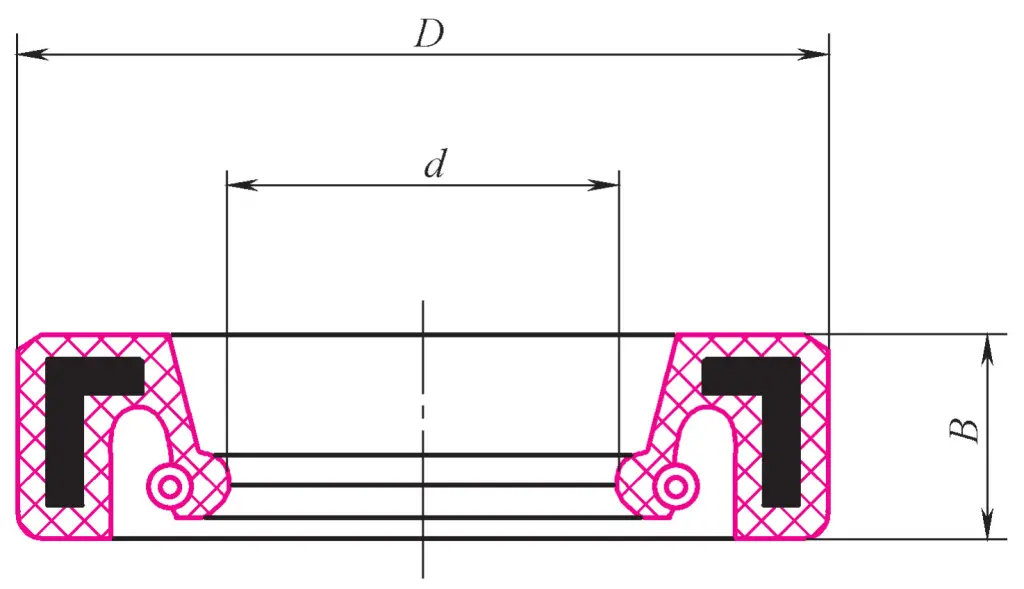
3.新しいタイプのシールエレメント
材料工業の発展とシール理論の改良・発展に伴い、近年、国内外で多くの新しいタイプのシールエレメントが研究・開発されている。これらのシーリングエレメントは、物理的、化学的、シール性能が大幅に向上しただけでなく、構造も大きく変化している。機能もシングルタイプからコンビネーションタイプへと進化している。ここでは8種類の新しいシールエレメントを紹介する。
(1) 星型シール・エレメント
図21は、液圧および空圧アクチュエータの双方向シールに適した星形シールエレメント(X形シールエレメントとも呼ばれる)を示しています。星形シールエレメントは、予圧縮力と流体圧力の両方によってシーリングを実現します。
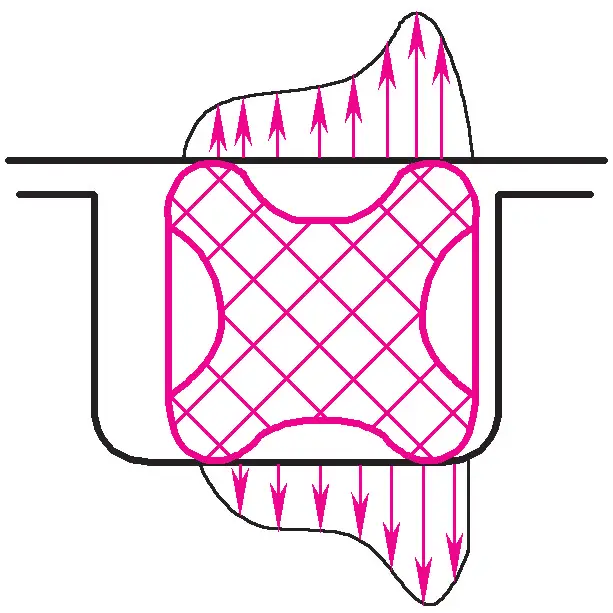
この星型シールエレメントは、直線運動用、回転運動用、静的シール用途に適しており、圧力は40MPa以下、温度は-60~200℃、動作速度は0.5m/s以下です。
(2) ヅルコン-リムリップ・シール・エレメント
ザーコン-リムリップは一方向シールタイプで、双方向シールを実現するには2個1組で使用する必要があります。ザーコン-リムリップは、図22に示すように、直線往復運動、25MPa以下の圧力、-30~100℃の温度範囲、5m/s以下の動作速度で、シャフトと穴の間の動的シールに適しています。
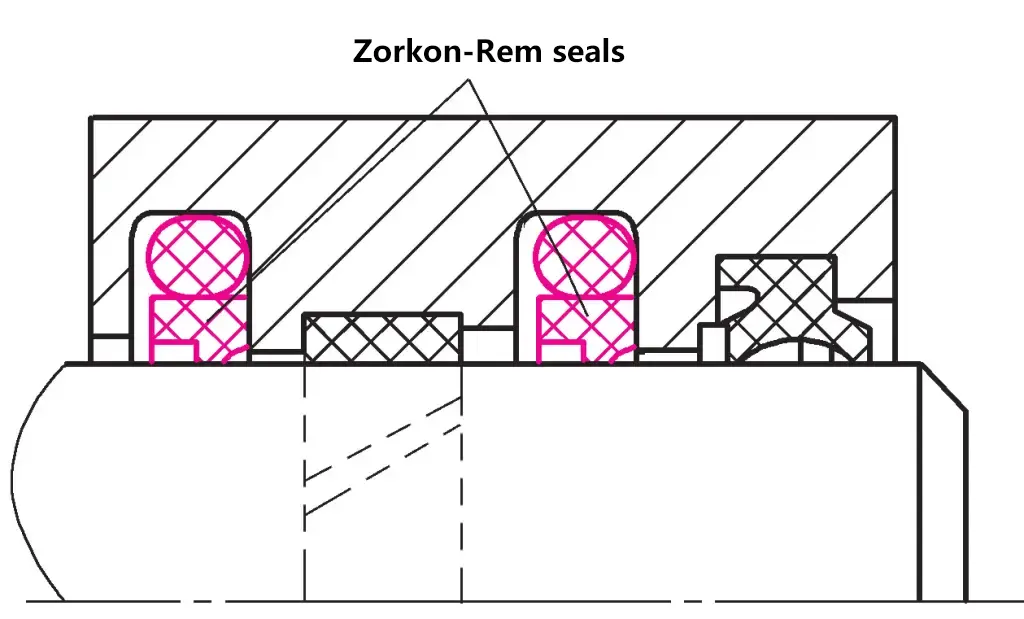
(3) ターコン・バリシール・シーリング・エレメント
ターコン・バリシール・シールエレメントは、それ自体のスプリング、予圧力、油圧の複合作用によってシールを実現します。図23に示すように、U字型のターコンリングと指状のステンレス製フォーススプリングから構成されています。このシールエレメントの特徴は、摩擦が少なく、耐摩耗性に優れていることである。
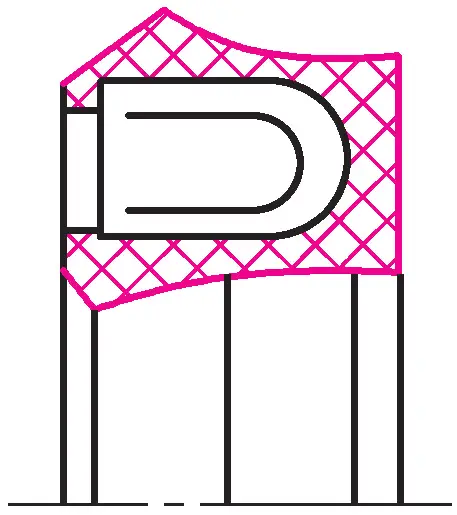
ザーコン-リムリップ・シール・エレメントは、直線往復運動、45MPa以下の圧力、-70~260℃の温度範囲、15m/s以下の動作速度で、シャフトと穴の間のダイナミック・シールに適しています。
(4) ターコングリッドリングシールエレメント
ターコン・グライドリング・シールエレメントは、図24に示すように、Oリングの弾性を利用してシールエレメントに圧力を加え、シールするものである。このシールエレメントの特徴は、低摩擦、低始動抵抗、良好な耐摩耗性、押し出し現象のなさなどである。
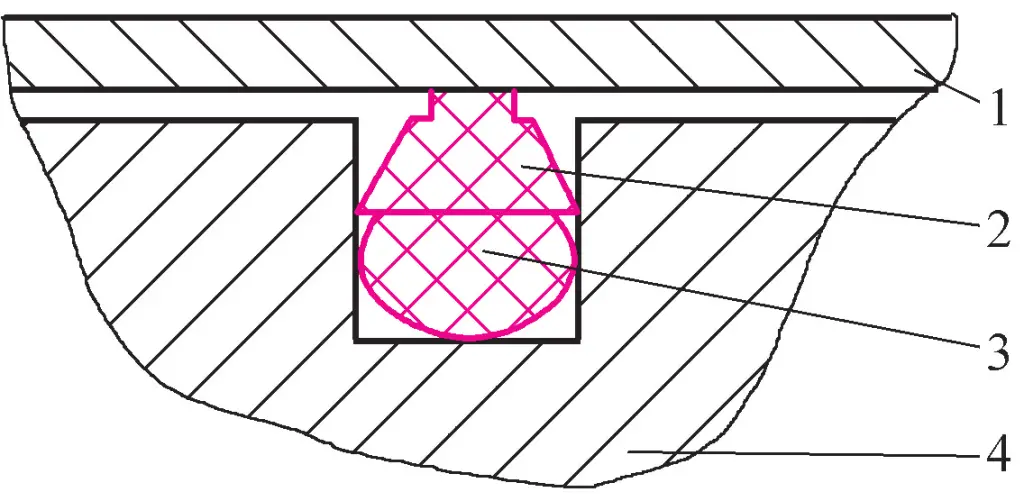
1気筒
2-ターコン・グリッド・リングシール
3-O-リング
4ピストン
ターコングライドリングシールは、圧力80MPa以下、温度-54~200℃、作動速度15m/s以下の直線往復運動におけるピストンとシリンダー間のシールに適しています。
(5) グライドリングとステップシール
グライドリングとステップシールは、図25に示すように、Oリングの弾性と予圧縮力を利用して、Oリングをシリンダ内面とピストンロッド外面に押し付けてシールするものである。この2種類のシールは、圧力50MPa以下、温度-30~120℃、作動速度1m/s以下の油圧シリンダのダイナミックシールに適している。
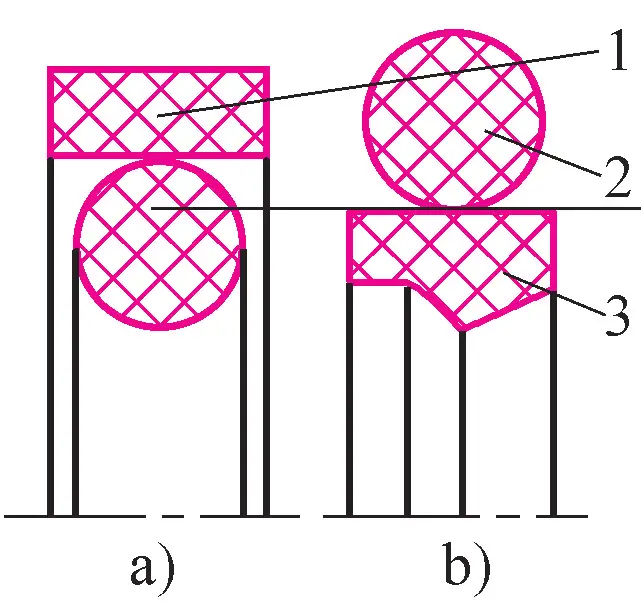
a) ピストン用
b) ピストンロッド用
1-グリッド・リング
2-Oリング
3ステップシール
(6) ウィルス・メタル・シールリング
Willsメタルシールリングは、主に鋼、銅、ニッケル合金、モネル合金などの様々な材料で作られた固体または中空の加圧金属リングです。外面にはカドミウム、銀、金、PTFEなどのメッキが施されることが多い。
図26は、端面静的シールに使用される中空リングのウィルスメタルシールリングを示しており、1000MPa以下の圧力、800℃以下の温度での静的シールに適している。
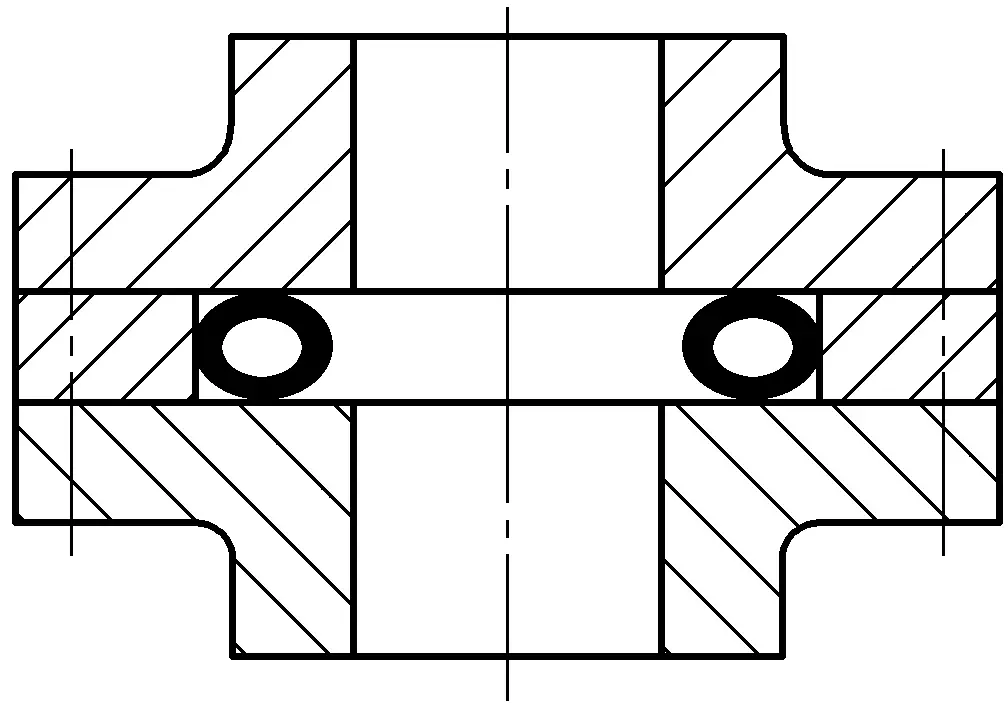
(7) 複合シールリング
複合シールリングは、複合ガスケットとも呼ばれ、図27に示すように、金属リング1とゴムリング2を一体加硫したものである。便利な使用方法と信頼性の高いシールが特徴です。圧力100MPa以下、温度-30~200℃の2つの平面間の静的シールに適しています。
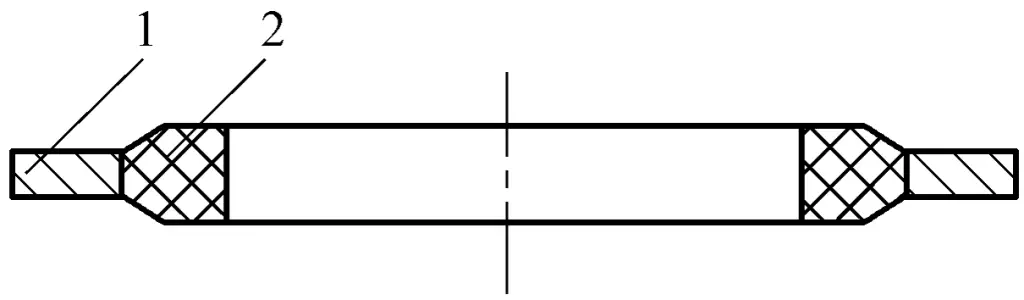
1-金属リング
2-ゴムリング
(8) コンビネーションボアシール(ドイチェシール)
コンビネーションボアシールは、図28に示すように、弾性シールリング3(ニトリルゴム)、2つのバックアップリング2(ポリエステルエラストマー)、2つのガイドリング1(ポリオキシメチレン)から構成され、5ピースのピストンシールセットを形成している。
油圧シリンダーの双方向ピストンシールとして使用され、両方向のシールとピストンの半径方向の力をガイドし、負担することができます。コンパクトな取り付けサイズで、低圧でも良好なシール効果を発揮します。圧力40MPa以下、温度-30~100℃、作動速度0.5m/s以下の油圧シリンダーのダイナミックシールに適している。
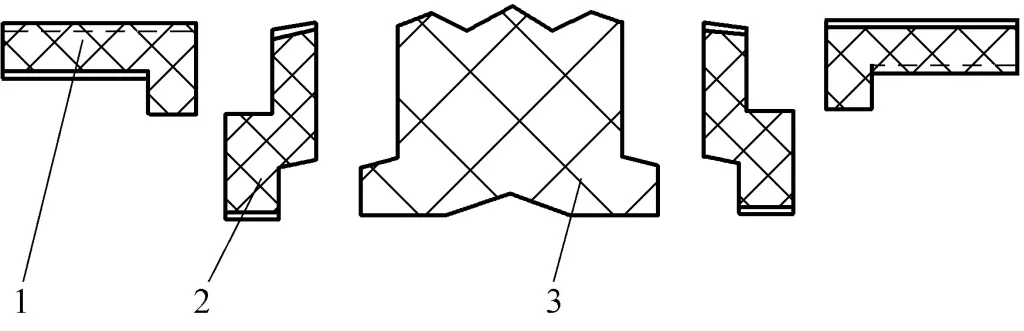
1-ガイドリング
2-バックアップリング
3-弾性シールリング