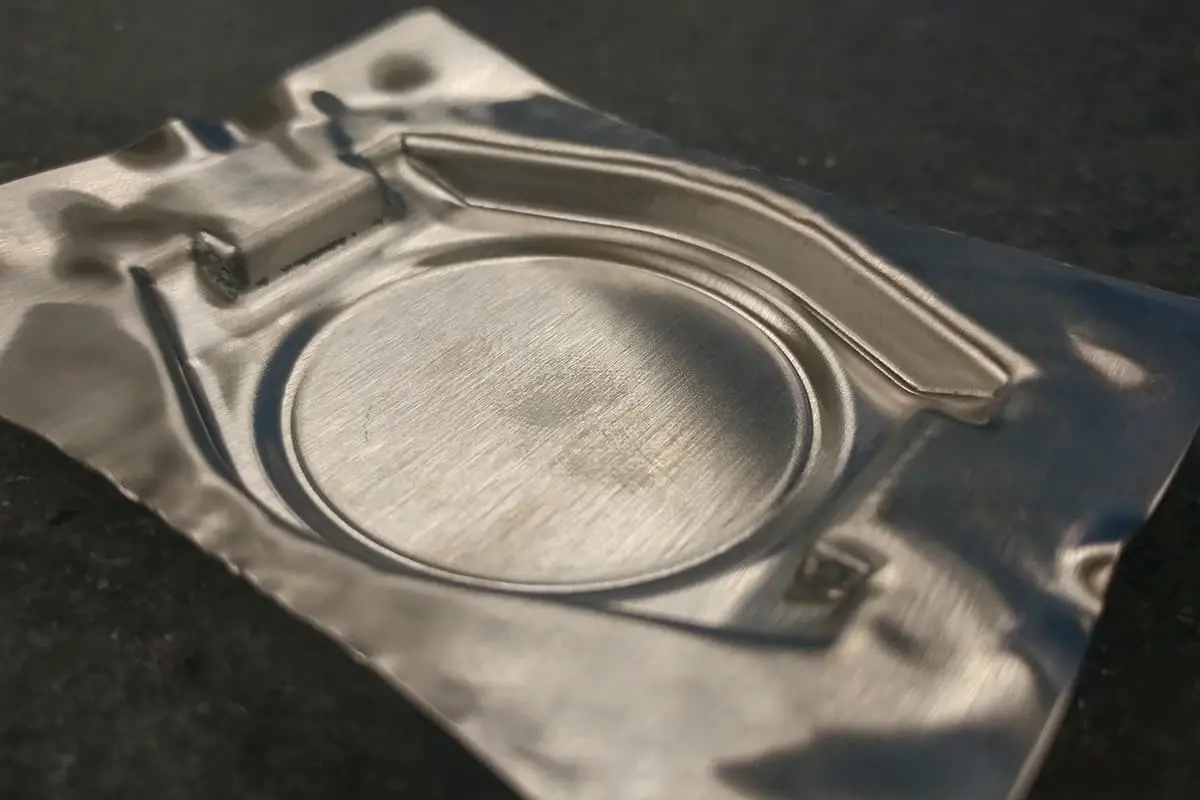
絞り金型の分類
絞りダイスは、フランジタイプによりバインダー付きとバインダーなしに分類される。また、加工順序によって、先加工絞りダイスと後加工絞りダイスに分類される。構造的には、直絞りダイス、逆絞りダイス、間引きダイスに分けられる。
ステンレス鋼製品の製造では、直接引抜と逆引抜が 一般的に使用されている。しかし、ステンレス鋼の熱伝導 性が低いため、熱の蓄積を招き絞り条件を 急速に悪化させる薄肉絞りは、ほとんど使用 されず、本書では取り上げない。
直引きダイは、さらに上置き型と下置き型に分けられる。トップマウント・ダイは、パンチが上にあり、ダイが下にあるタイプが一般的です。逆に、ボトムマウント・ダイは、この配置を逆にしたものです。
絞りパンチとブランキングパンチの位置関係から、順送絞り加工ではトップマウント絞りダイが頻繁に採用される。
第一回オペレーション・ドローイング・ダイス
第一操作の絞りダイスは、上置きタイプと下置きタイプに分けられる。
(a)トップマウント初動絞りダイス
図4-10に示すように、フランジのない部品でバインダーを必要としないもの、またはバインダーを必要とするが最小限の力しか必要としないものには、便利な低排出で効率を高めるために、トップマウント絞りダイが使用される。単動ダイスでは、上部に取り付けた絞りダイスは、パンチの周囲に取り付けた弾性エレメントだけに頼って圧力を与えます。
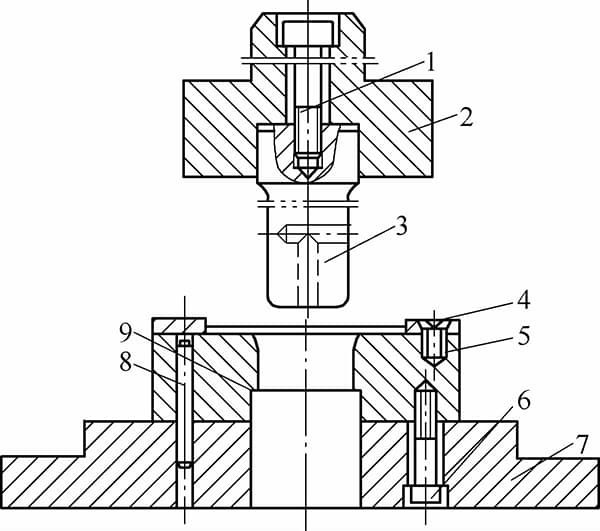
1、5、6 - ネジ; 2 - ダイハンドル; 3 - パンチ; 4 - 位置決めプレート; 7 - 下部ダイシュー; 8 - ダボピン; 9 - ダイキャビティ
そのため、ブランクを保持する力とストロークの両方がかなり制限され、これらは通常、高い絞り比の部品、バインダーなし、またはバインダーはあるが最小限の力しか必要としない部品に使用される。
フランジのない部品では、貫通型の排出方法がよく使われる。パンチが上昇するとき、成形品のエッジにわずかな反動が生じ、その反動で成形品が膨張してダイの下端に引っ掛かり、排出が容易になる。従って、図4-11に示すように、上置き絞りダイスは高能率である。
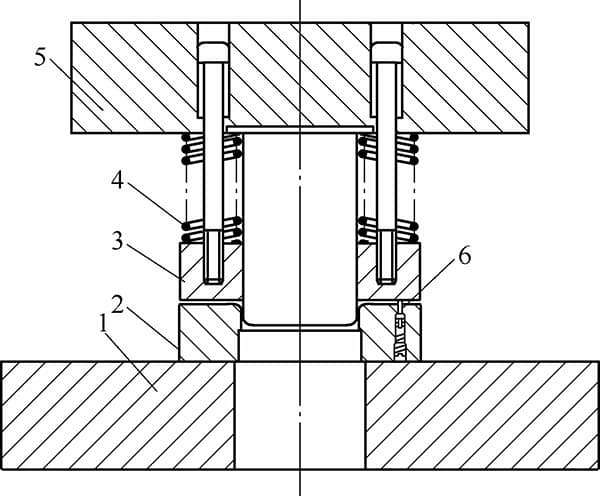
構成部品は以下の通り:1...下ダイシュー、2...ダイキャビティ、3...ブランクホルダー、4...スプリング、5...上ダイシュー、6...可動パイロットピン。
(b)ボトムマウント初動絞りダイス
実際には、下置き金型は上置き金型よりも広く使用されている。これは、プレス機でフランジ部品を絞り加工する場合、下置きダイの方が取り付けが簡単で、弾性要素のスペースが広く、ブランク保持力が大きく、ブランクホルダの調整が容易で、作業が便利だからである。
油圧プレスに設置されるほとんどの初動絞りダイは、ブランク保持力を調整するために下部の油圧シリンダを利用するボトムマウントとして設計される。図4-12に示すように、ボトムマウントの金型を試験する場合、トップマウントの金型と比較していくつかの便利な点がある。
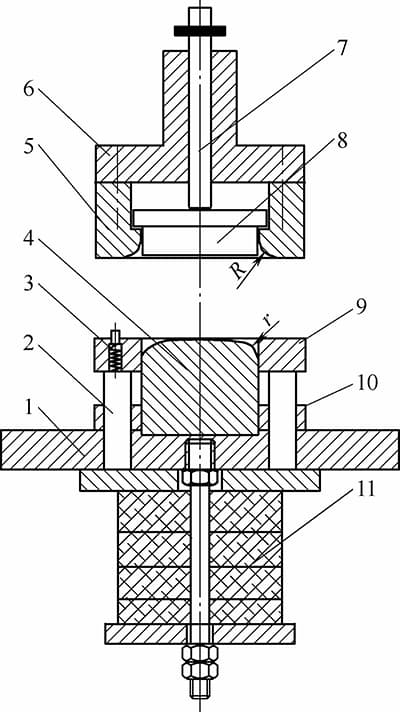
1-下ダイホルダー 2-リフターロッド 3-ブランクロケーター 4-パンチ 5-ダイ 6-上ダイホルダー 7-エジェクターロッド 8-エジェクタープレート 9-ブランクホルダー 10-パンチリテーナープレート 11-ストリッパー機構
その後の操作 引き抜き金型
(a)ボトムマウント式後工程引抜ダイス
後続の加工絞りダイスをボトムマウントに設計することで、部品外観の品質が安定する。これらの金型は、図4-13に示すように、ダイ、ノックアウト装置、ダイセット、パンチから構成される。
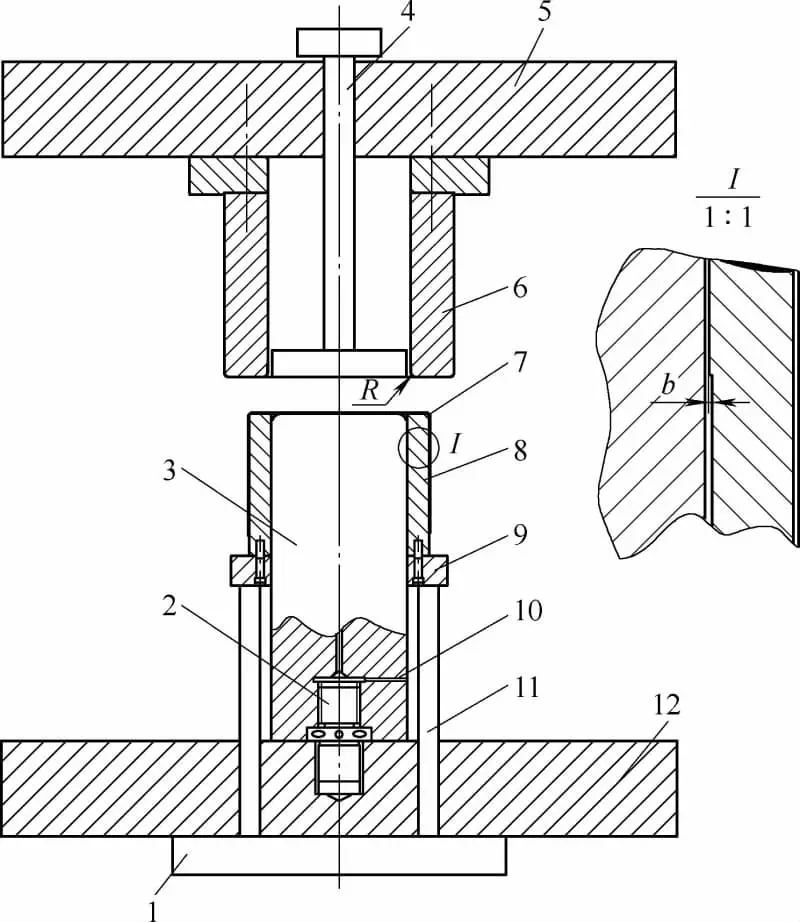
図 4-13 は、標準的な油圧シリンダーのトッププレート、ユニバーサル・コネクティング・スタッド、ポンチ、プッシュ・ロッド 油圧プレス スライド、ダイ、ワーク、ダイスリーブ、中央ボルスタプレート、ベントホール、リフトロッド、油圧プレスのワークテーブル。
(b)バインダーを使用しない後工程絞りダイス
図 4-14 に示すように、バインダーを使用しない後続作業用の延伸ダイスは、延伸比が 0.8 以上であることが必要であり、連続延伸作業のような厚みの小さい材料や小径の製品によく使用される。
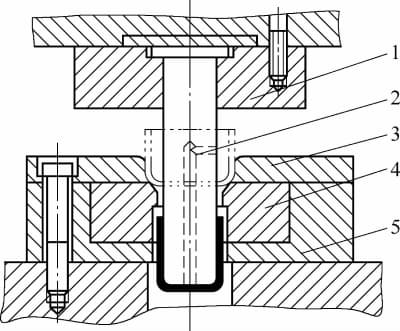
1- パンチリテーナープレート、2- パンチ、3- ロケータープレート、4- ダイ、5- ダイリテーナープレート。
逆絞りダイス
部品に複数の絞り加工が必要な場合、図4-15に示すように、最初の加工は直接描画を使用し、その後の加工は成形を容易にするため、逆方向描画と直接描画を交互に使用する。
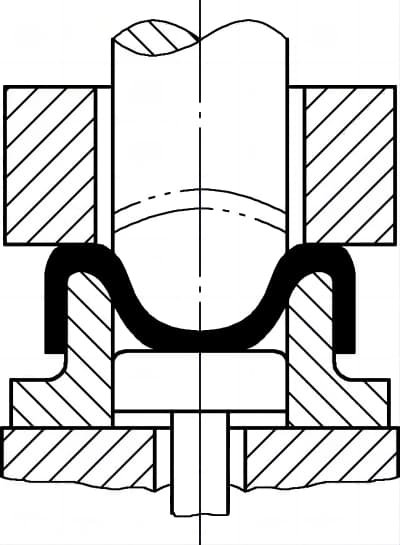
リバース絞り加工は、1回目の絞り加工でできた半製品を中空のダイの上に置き、外面からパンチが入ってさらに絞り加工を行う。パンチがブランクに与える力は、前回の絞り加工とは逆方向であるため、素材の内面と外面が入れ替わり、変形が大きくなって生産効率が向上する。
リバースドローイングにはいくつかの特徴がある:
1)リバース絞りでは、ブランクとダイスのラップ角が大きいため、摩擦抵抗や曲げ抵抗が少なく、しわが発生しにくい。ダイス肉厚が28tより薄い場合、バインダーが不要な場合がある。
2) 力をかける方向と曲げる方向が直前の操作と逆であるため、半製品の加工硬化は直絞りよりも少ない。
3) ダイの内側と外側のコーナー半径の合計は、ダイの肉厚を超えることはできない。ワークピースのサイズ制限のため、ブランクの直径(d)は30t以下にはできず、内側コーナー半径は4t以上でなければならない。
4) 逆引きの絞り比は、ダイスの強度を低下させるので、あまり大きくはならない。一般に、絞り比は直接絞りより 10% から 15% 小さくすることができる。
5)逆引きは、必要なダイス半径が大きいため、小さな部品には困難であり、中型から大型の円筒部品に適している。
6) その パンチとダイの隙間 逆引きでは、直接引きよりも15%~30%大きくなる。
7) ダイの肉厚は10t以上、絶対値は6mm以上であること。
リバースドローイングは、大きな非支持領域を持つ部品の成形に大きな利点をもたらします。リバースドローイングに使用されるブランクは、頂部が平らなものと球状のものがある。絞り加工では、球面トップのブランクとパンチの接触が緩やかになるため、半球状、円錐状、放物線状の部品の成形に有利です。
深絞りダイスの選択
設計図を受け取ると、深絞り部品を大まかに分類しなければならない。深絞りダイスの構造形式は、主にワークピースの形状を考慮し、さらに以下のような要素が加わります:
1) 最大ブランクサイズに対する材料の厚さの比率。
2) 最終成形寸法に対するブランク寸法の比率。
3) アスペクト比または最大幅対高さの比率。
4) 開放端寸法に対する底部寸法の比率。
5) 表面精度。
6) 材料の引張強度係数。
これらすべてのデータが集まれば、深絞りダイスの適切な構造形式を決定することができる。
深絞り加工の金型選定は、以下の条件に基づいて行うべきである:
1) d0-d1/2≦7tの場合は、バインダーリングのない直接排出ダイを使用する。
2)7<d0-d1/2<14tの場合は、バインダーリングのない排出用円錐リセスダイを使用する。
3) d0-d1/2≧14tの場合は、バインダーリング付きのフラット・リセス・ダイを使用する。
4) 単発の円筒部品は、反転深絞りダイスを使用する。フランジのない長尺円筒部品や、フランジに要求される平坦度が低い部品は、複数回の深絞り加工に反転ダイスを使用することもできるが、材料の加工硬化が激しい場合は、中間焼鈍を行う必要がある。
5) 高いフランジ平坦度が要求される多段深絞り部品では、レバーのたわみによるフランジ平坦度への影響を最小にするため、正と負の深絞りを交互に行う。
6) 深絞り段数が3段を超える部品については、円錐リセスダイスを1-2段挟むことを検討する。
7)中程度の深さの円錐形部品については、ポジとネガの深絞り加工の組み合わせを検討する。
8) ステンレス食器の製造において、シール性能が重要でない長い円筒形部品には、深絞り加工の代替として、溶接パイプ+底付けの使用を検討する。
9)放物線状の部品は、深絞り加工を施した後、金型のバルジングを行う。
10)お腹にシワが寄りやすい流線型のパーツは、内側から外側に深絞りすることを検討する。
11)第2深絞り工程後のバインダー面積が不足する部品については、第1深絞りダイスのフィレット半径を大きくし、インサイド・アウト深絞り法を使用することを検討する。
12)主変形面がプロファイル・ラインと交差する部分には、湾曲したバインダー・リングを使用する。
13) その後の深絞り段階で底部の材料が著しく薄くなっている場合、または成形中に材料の供給源がない場合で、打ち抜き加工が許される場合は、打ち抜き加工孔を追加して打ち抜き部分から材料を引き抜く。
14)回転体の深絞り部品の場合、表面や円錐形の高さが全高の半分以下であれば、特別な措置は必要ない。半分以上全高の3分の2以下であれば、深絞り段差を使用し、3分の2以上であれば、図4-16に示すように、深絞りリブを使用する。
15)可能であれば、高円錐部品の深絞り加工は避ける。可能であれば、扇形ブランキングと曲げ加工で円錐シリンダーを形成し、その後溶接する。
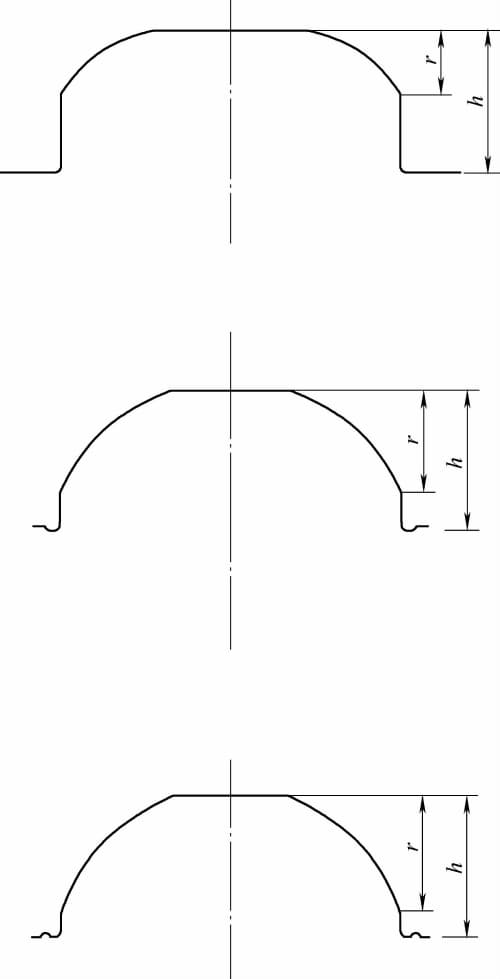