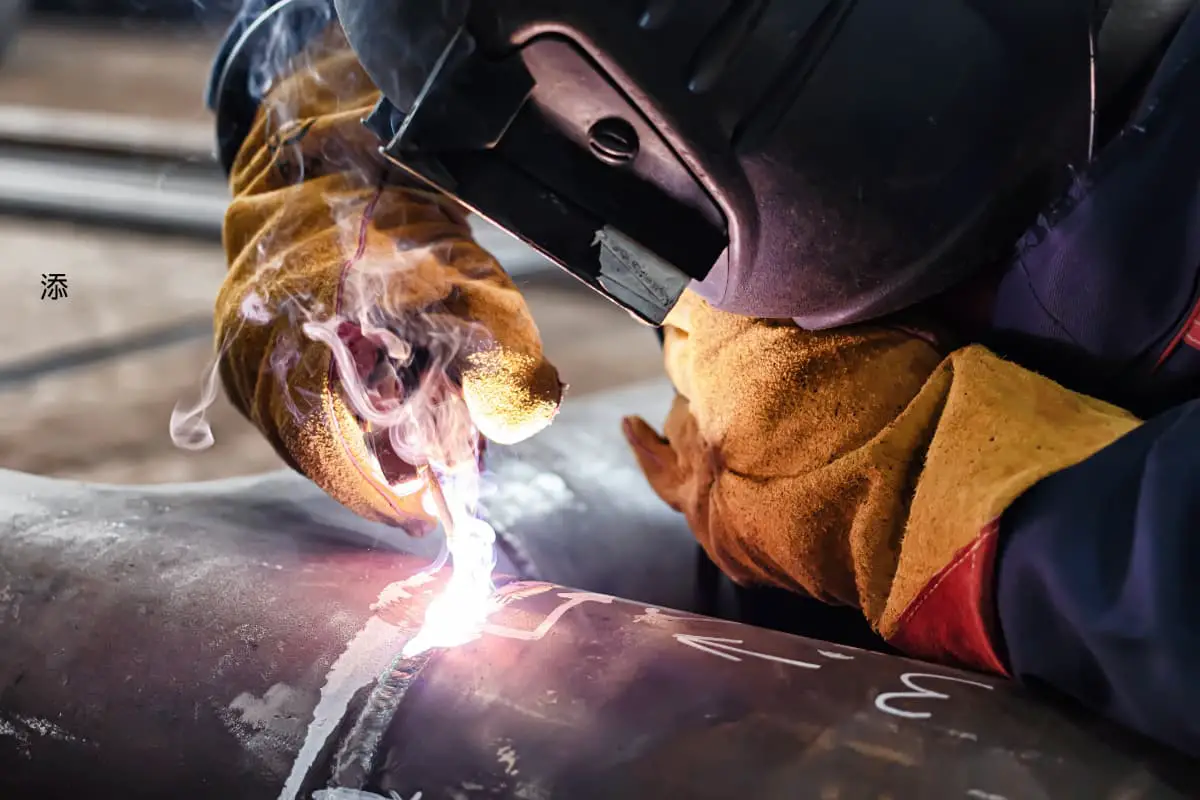
I.溶接の定義、特徴、方法
1.溶接の定義
溶接は、溶加材の有無にかかわらず、加熱、加圧、またはその両方によって、被加工物の原子的結合を実現する加工法である。したがって、溶接は、別々の金属部品を分離不可能な全体として連結する加工方法である。加圧によって接合面の酸化皮膜などの吸着層を破壊し、接触面を塑性変形させて接触面積を拡大する。
変形が十分であれば、原子結合も直接形成され、強固な接合となる。加熱は、接合部を局所的に塑性または溶融状態に加熱し、原子のエネルギーを刺激して高め、拡散、結晶化、再結晶化を通じて強固な接合を形成・発展させる。
2.溶接の特徴
溶接が広く使用される前は、取り外し不可能な接続の主な方法はリベット止めであった。リベッティングに比べ、溶接は金属を節約し、生産性が高く、コンパクトで、作業条件がよく、機械化・自動化が容易であるという特徴がある。したがって、溶接は現在、基本的にリベッティングに取って代わっている。
3.溶接方法
溶接には様々な方法があるが、その特徴から「融接」「圧接」「ろう接」の3つに大別される。
(1) フュージョン溶接
溶融溶接は、加圧することなくワークの接合部を溶融状態に加熱して溶接を完了させる方法である。熱源によっては、このタイプの 溶接方法 ガス溶接、アーク溶接、エレクトロスラグ溶接、レーザー溶接、電子ビーム溶接、プラズマアーク溶接など。
(2) 圧力溶接
加圧溶接は、溶接を完了させるために、溶接プロセス中に(加熱の有無にかかわらず)被加工物に圧力を加えなければならない方法である。このカテゴリーに属する方法には、抵抗溶接がある、 摩擦圧接超音波溶接、冷間圧接など。
(3) ろう付け
ろう付けは、母材よりも融点の低い金属材料をろう材として使用する。ワークピースとろう材は、ろう材の融点より高く母材の融点より低い温度に加熱される。液体金属フィラーは母材を濡らし、接合ギャップを満たし、母材と拡散してワークピースの接続を実現する。このカテゴリーに属する方法には、硬ろう付けと軟ろう付けがある。
溶接とは、溶加材の有無にかかわらず、加熱、加圧、またはその両方によって被加工物の原子的結合を実現する加工法を指す。
金属溶接には多くの種類がある。溶接時の物理的冶金学的特性から、融接、圧接、ろう接の3つに大別される。現在、最も広く使用されているのは融接である。
I.溶融溶接
溶融溶接は、圧力をかけずにワークの接合部を溶融状態に加熱する局所加熱を利用した溶接方法である。
溶融溶接は、使用する熱源の種類によって、アーク溶接(溶接アークを熱源とする)、プラズマアーク溶接(プラズマアークを熱源とする)、エレクトロスラグ溶接(溶融スラグの抵抗熱を熱源とする)、電子ビーム溶接(電子ビームを熱源とする)、レーザー溶接(レーザーを熱源とする)、ガス溶接(火炎を熱源とする)などに分類される。この中で最も広く使われているのがアーク溶接である。
1.アーク溶接
アーク溶接は、アークを熱源とする融接法である。一般的なアーク溶接には、被覆アーク溶接がある、 サブマージアーク溶接およびガスシールドアーク溶接。
(1) シールド金属アーク溶接
被覆アーク溶接は、最も早く開発されたアーク 溶接法のひとつで、現在でも広く使用されている。溶接棒を電極と溶加金属の両方に使用し、溶接棒の先端とワークの間に発生するアークを溶接の熱源とする。
溶接中、アークは溶接棒の端部および被加工物の局 所を溶融状態まで加熱する。溶接棒の溶融端は液滴を形成し、溶融母材と融合して溶接プールを形成する。アークが前進するにつれて、溶接プールの溶融金属は徐々に冷えて凝固し、溶接継ぎ目を形成する。図1に、被覆アーク溶接プロセスの概略図を示す。

1-ベースメタル
2-スラグシェル
3ウェルドシーム
4-溶融スラグ
5-保護ガス層
6-溶接棒コーティング
7-溶接コア
8-液滴
9-アーク
10ウェルド・プール
手動金属アーク溶接に使用される装置はシンプルで、方法は簡単で柔軟性があり、強力な適応性がある。様々な条件下で、様々な位置の溶接に使用できる。継手形状、溶接形状、長さに制限はないが、溶接工に高い技術力が要求され、溶接品質はある程度溶接工の作業技術に左右される。
さらに、手動金属アーク溶接は作業条件が悪く、生産性が低い。主に単品または少量生産に適し、板厚3~20mmのワークの溶接に適している。活性金属(チタン、ニオブなど)および耐火性金属(タンタル、モリブデンなど)は、手動金属アーク溶接を使用できない。
(2) サブマージアーク溶接
サブマージアーク溶接とは、アークがフラックス層の下で燃焼するアーク溶接法を指す。溶接中、アークの点火、ワイヤ送給、溶接継目に沿ったアークの移動は、装置によって自動的に行われる。
サブマージアーク溶接の形成過程を図2に示す。溶接中、溶接ワイヤの先端が被溶接物に接触した後、フラックス漏斗が開き、被溶接物の溶接部分に厚さ30~50mmのフラックス層が散布される。通電後、溶接ワイヤを上方に引っ込め、アークに点火する。
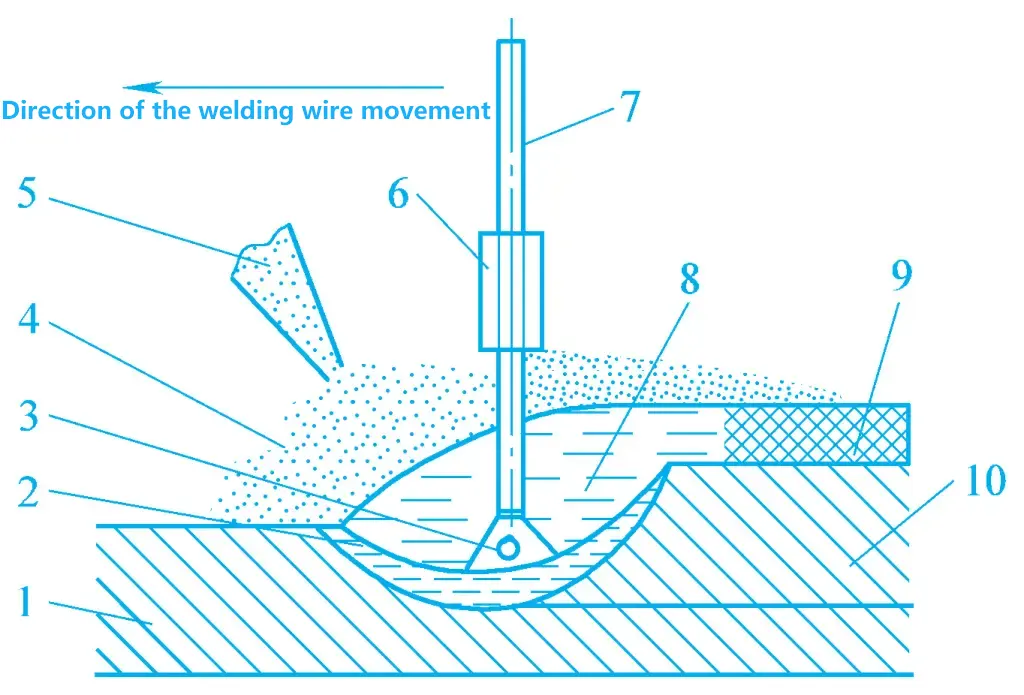
1-ワークピース(基材)
2-溶けたプール
3液滴
4-フラックス
5流体ファンネル
6接点チップ
7-溶接ワイヤ
8-スラグ
9スラグシェル
10ウェルド
フラックス層の下で燃焼するアークが熱を発生させ、アーク近傍の母材と粒状フラックスを溶かしてスラグを形成する。発生した高温ガスがスラグを押し流し、閉じたスラグ・バブルを形成する。スラグ気泡は表面張力によって、空気が溶接プールに入るのを効果的に防ぎ、液滴が飛び散るのを効果的に防ぐ。溶融していないフラックスは、アークを外気から隔離し、アーク熱の損失を低減する。
アークが前進すると、供給された溶接ワイヤと、その前方の母材金属およびフラックスを連続的に溶融する。溶接プールの後方にある液体金属は徐々に冷却され、端から凝固して溶接部を形成し、液体スラグも凝固して溶接面を覆うスラグ・シェルを形成する。溶接部の金属は、フラックス層とスラグ気泡の両方によって保護されるため、熱損失が低く、溶け込みが深い。
サブマージアーク溶接は、手動金属アーク 溶接に比べて、溶接速度が速く、生産効率が高 く、溶接品質が高く安定しており、溶接部の外観 が美しく、作業条件が良いという利点がある。しかし、設備コストが高く、プロセス設備が複雑であるため、複雑な構造物や傾斜した溶接部を持つワークの溶接には不向きであるという欠点がある。
そのため、サブマージアーク溶接は主に、大ロット生産、厚肉(6~60mm)、長尺の直線平板溶接、または大径の円形溶接に使用される。適用材料は、低炭素鋼、低合金鋼、ステンレス鋼、その他の金属板である。
(3) ガス・シールド溶接
ガス・シールド溶接とは、保護媒体として外部ガスを使用するアーク溶接法を指す。特殊材料の溶接や溶接プロセスの自動化において、ますます重要な役割を果たしている。
サブマージアーク溶接と比較すると、アークと 溶接池の見通しが良く、操作が簡単で、スラグが出 ないため、多層溶接で溶接後のスラグ洗浄時間を大幅に 節約でき、全姿勢溶接が可能という利点がある。ただし、屋外での作業には特別な防風対策が必要である。
溶接プロセスで使用される保護ガスの違いにより、一般的なタイプにはアルゴンアーク溶接とCO2ガスシールド溶接がある。アルゴン・アーク溶接は、保護媒体としてアルゴンを使用し、使用する電極の違いにより非消耗電極アルゴン・アーク溶接と消耗電極アルゴン・アーク溶接に分けられる。
図3は、CO2ガス・シールド溶接の模式図である。CO2ガスシールド溶接は、保護媒体としてCO2ガス(CO2+O2の混合ガスの場合もある)を使用する。連続的に送給される溶接ワイヤを電極とし、溶接ワイヤと被溶接物の間のアークを利用して被溶接物の金属と溶接ワイヤを溶融させ、溶接池を形成して凝固させて溶接する方法である。
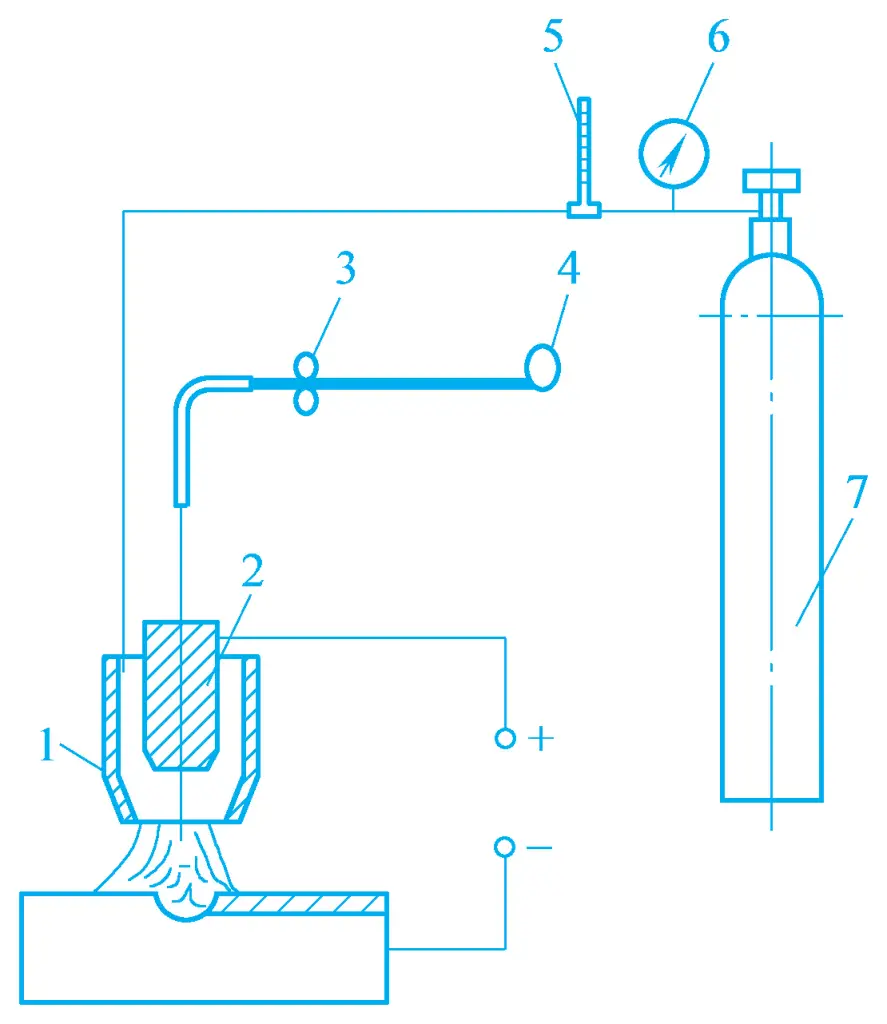
1-溶接ガンノズル
2接点チップ
3線式給電メカニズム
4線スプール
5-フローメーター
6-圧力レデューサー
7-CO 2 ガスボンベ
CO 2 ガス・シールド溶接は、溶接速度が速く、溶接後にスラグが発生せず、スラグの洗浄時間を節約できるため、生産性が高い。シールド・ガスの価格はアルゴンより低く、消費電力が少ないため、コストが低い。アークの熱が集中するため、溶融池が小さく、溶接速度が速く、溶接熱影響部が小さく、変形や亀裂の傾向が小さく、溶接部の形成が良好である。
低炭素鋼や低合金鋼の溶接には、高能率、低コ スト、高品質の溶接法である。欠点は、酸化しやすい非鉄金属の溶接には不向きであること、溶接部形成が滑らかで美しくないこと、アーク光が強く、溶滴飛散が激しく、煙が多いので防風対策が必要なことである。
CO 2 ガス・シールド溶接は、主に強度レベルの低い低炭素鋼や通常の低合金構造用鋼の溶接に使用される。溶接部の最大板厚は50mm(突合せ継手)に達し、造船、自動車、クレーン、各種タンク、農業機械などの産業分野で広く使用されている。
2.プラズマアーク溶接
プラズマ・アーク溶接は、プラズマ・アークを熱源とする溶融溶接法である。溶接中は、プラズマ・アークの周囲にシールド・ガス(アルゴン)を流し、溶融池と溶接部を大気の有害な影響から保護する。
プラズマアーク溶接は、溶接電流によってマイクロビームプラズマアーク溶接と大電流プラズマアーク溶接に分けられる。マイクロビームプラズマアーク溶接は、一般に溶接電流が0.1~30Aで、厚さ0.025~2.5mmの金属箔や薄板を溶接することができ、大電流プラズマアーク溶接は、一般に溶接電流が100~300Aで、厚さ2.5~12mmの金属を溶接することができる。
プラズマ・アーク溶接の特徴は、プラズマ・アークのエネルギー密度が高いこと、アーク柱温度が高いこと、溶け込みが強いこと、板厚12mm以下のワークを開先加工なしで溶接できることである。
電流が0.1Aと低い場合でも、プラズマアークは非常に安定しており、良好な方向性とアーク直進性を確保できるため、厚さ0.01~1mmの箔や薄板の溶接が可能で、溶接速度が速く、生産性が高く、溶接品質が良好で、溶接熱影響部が小さく、溶接物の変形が小さい。プラズマアーク溶接設備は比較的複雑で、ガス消費量が多く、屋外溶接には適さず、柔軟性はアルゴンアーク溶接ほど良くない。
プラズマアーク溶接は、タングステン、ニッケル、チタン、銅、モリブデン、アルミニウムおよびその合金、ステンレス鋼、高強度鋼など、さまざまな耐火性、易酸化性、熱に敏感な金属材料の溶接に適しています。現在、主に化学、原子力、電子機器、精密機器、ロケット、航空、宇宙技術などに使用されている。
3.エレクトロスラグ溶接
エレクトロスラグ溶接は、溶融スラグに電流を通したときに発生する抵抗熱を熱源として、被溶接材と溶加材を局部的に溶融させ、冷却・凝固させて溶接部を形成する溶融溶接プロセスである。
エレクトロスラグ溶接は、他の溶融溶接と比較して次のような特徴がある:
- 非常に厚い溶接物を1パスで溶接することができ、開先加工なしで一定の隙間しか必要としないため、溶接生産性が高い。フラックス、溶接ワイヤ、電気エネルギーの消費量がサブマージアーク溶接より少ない。
- 金属溶融池の凝固速度が遅く、溶融池が長時間液体のままであり、溶融池中のガスや不純物が浮き出しやすいため、溶接部にポロシティやスラグ巻き込みが発生しにくい。しかし、粗大組織を形成しやすく、衝撃靭性が低下するため、溶接後に焼ならしまたは焼鈍処理を行う必要がある。
- 一般に、溶接部を予熱する必要はなく、焼入れ硬化鋼を溶接する際に焼入れ割れが発生しにくい。
エレクトロスラグ溶接は、炭素鋼、合金鋼、鋳鉄の溶接のほか、アルミニウム、マグネシウム、チタン、銅合金の溶接にも使用できる。溶接厚さは一般に30mm以上で、現在、ボイラー、重機、石油化学などの産業で、鍛造溶接や鋳造溶接の構造部品などに広く使用されている。
4.電子ビーム溶接
電子ビーム溶接は、加速・集束された電子ビームが溶接 部の表面に照射される際に発生する熱を利用して、 金属溶接部を局部的に溶融し、冷却・凝固させて 溶接部を形成する融合溶接プロセスである。溶接部は真空中または非真空中に置かれる。真空中で行われる電子ビーム溶接は真空電子ビーム溶接と呼ばれ、大気圧の作業環境で行われる電子ビーム溶接は非真空電子ビーム溶接と呼ばれる。
真空電子ビーム溶接の特徴は以下の通りである:
- 溶接品質が良い。特に、化学的活性が高く、純度が高く、大気で汚染されやすい金属の溶接に適している。
- エネルギー密度が高く(アーク溶接の約5000~10000倍)、溶け込みが強く、溶接速度が速い。板厚200~300mmまでの鋼板や板厚300mm以上のアルミ合金などの厚肉ワークの溶接が可能です。
- 溶接の熱影響部は小さく、溶接変形は非常に小さく、すでに機械加工された組立部品の溶接も可能である。
- 電子ビーム・パラメーターは調整でき、溶接プロセス制御は柔軟で、適応性は強いが、溶接装置は複雑で、コストが高く、溶接物の外観サイズは真空チャンバーによって制限される。
- 真空電子ビーム溶接は、レアメタルの溶接など、一般的なガスシールド溶接では解決できない問題を解決する。
現在、真空電子ビーム溶接は、航空宇宙、原子力、自動車、化学、電子、電力、機械製造などの分野で広く使用されている。
非真空電子ビーム溶接は、高真空条件下で発生した電子ビームを大気圧の作業環境に導入してワークを溶接するもので、大気圧電子ビーム溶接とも呼ばれる。主な利点は、真空チャンバーが不要、生産性が高い、コストが低い、大型ワークの溶接が可能、電子ビーム溶接技術の応用範囲が広がるなどである。
非真空電子ビーム溶接は、エネルギー産業(各種コンプレッサー・ローター、インペラー・アセンブリー、原子炉シェルなど)、航空産業(エンジン・ベース、ローター・コンポーネントなど)、自動車製造業(ギヤ・アセンブリー、リア・アクスル、トランスミッションなど)、さらに計器、化学、金属構造物製造業などで広く使用されている。
5.レーザー溶接
レーザー溶接は1970年代に開発された新しい溶接技術である。集光レーザーを溶接熱源とする溶融溶接である。金属箔(厚さ0.5mm以下)、フィルム(数ミクロン~数十ミクロン)、金属線(直径0.6mm以下)などの溶接が可能。
レーザー溶接の特徴は、溶接速度が速い、熱影響部が小さい、溶接部の変形が小さい、溶接材料が酸化しにくいなどである。電子ビーム溶接に比べ、レーザー溶接はX線を発生せず、真空チャンバーを必要とせず、観察が容易で、複雑な構造や精密部品の溶接に適している。
レーザーは反射、透過、さらには光ファイバー伝送が可能なため、長距離溶接にも対応できる。また、密閉型電子管の内部ワイヤ継手の異種金属溶接も実現できる。現在、レーザー溶接は主に半導体、通信機器、無線工学、精密機器、計器部門の小型・微細部品の溶接に使用されている。
6.ガス溶接
ガス溶接は、ガスの燃焼によって放出される熱を溶接に利用する溶融溶接プロセスである。可燃性ガスには、アセチレン、水素、天然ガス、プロパンなどがある。ガス溶接で一般的に使用される火炎は、アセチレンと酸素を一定の割合で混合したガスに点火して形成され、オキシ・アセチレン火炎とも呼ばれる。アセチレンと酸素の体積比によって、浸炭炎、中性炎、酸化炎の3種類に分類される。
浸炭炎は遊離炭素を含み、溶接中の炭素損失を補い、強い還元作用と一定の浸炭作用がある。浸炭炎は、主に高炭素鋼、高速度鋼、硬質合金などの炭素含有量の高い材料の溶接に使用され、鋳鉄の補修にも使用できます。
中性炎は、酸素とアセチレンの完全燃焼によって形成され(過剰な酸素とアセチレンを含まない)、最も広い応用範囲を持っています。主に低炭素鋼、低合金鋼、ステンレス鋼、純銅などの溶接に用いられる。
酸化炎は過剰な酸素を持ち、溶接中に金属を酸化させる。酸化炎は溶融金属の表面にシリコン酸化膜(溶接ワイヤに含まれるシリコン)を形成し、亜鉛やスズなどの低融点金属を蒸発から守ることができるため、主に黄銅や青銅などの溶接に用いられる。
炭素鋼を溶接する場合は、溶接ワイヤをそのまま使用できる。しかし、ステンレス鋼、銅合金、アルミニウム合金を溶接する場合は、金属の酸化を防ぎ、すでに形成された酸化物を除去するために、ガス溶接フラックスを使用しなければならない。
ガス溶接の特徴は、ガス溶接炎の温度がアーク溶接より低く、加熱・冷却速度が遅く、加熱面積が広く、溶接変形が大きいことである。しかし、電気を必要とせず、設備が簡単で、汎用性が高い。ガス溶接は薄肉部品の溶接に適しており、主に板厚2mm程度の部品を溶接する。
II.圧接
圧接とは、加熱と加圧によって金属を塑性状態にし、塑性変形と再結晶を起こさせ、最終的に分離した2つの面の原子を格子間隔に近づけることで、剥離しない接合部を実現する溶接法である。主な種類は抵抗溶接と摩擦溶接である。
1.抵抗溶接
抵抗溶接は圧接の一種で、接合部の接触面に電流を流すことで発生する抵抗熱を熱源としている。抵抗溶接は、電極と継手の形態によって次のように分けられる。 スポット溶接シーム溶接、突合せ溶接。
(1) スポット溶接
スポット溶接は抵抗溶接の一種で、ワークピースを重ね継手に組み立て、2つの円筒形電極の間に押し込む。抵抗熱によって母材が局部的に溶融し、溶接ナゲットが形成される。スポット溶接の強度は溶接ナゲットの直径に依存し、一般的にd=2t+3mm(tは板厚)である。溶接ナゲットの品質は、溶接電流、溶接時間、電極の圧力、および加工面の清浄度に左右される。
スポット溶接は主に薄いプレス部品や棒鋼の溶接に使用され、自動車や航空機の薄板シェルのスプライスや組み立て、電子機器やメーターなどの工業製品の生産に使用される。スポット溶接の適用板厚範囲は0.05~6mmで、適用材料はステンレス鋼、銅合金、チタン合金、アルミニウム・マグネシウム合金などである。
(2) シーム溶接
シーム溶接は、連続スポット溶接プロセスであり、円筒状電極の代わりに連続回転する円盤状電極を使用し、非常に短い間隔でスポット溶接を行うため、溶接ナゲットが重なり合った連続溶接シームが得られる。
シーム溶接の溶接ナゲットは50%以上重なっているため、シール性は良好である。しかし、シーム溶接には深刻なシャント現象があり、同じ厚さのワークを溶接するのに必要な溶接電流は、スポット溶接の約1.5~2倍になる。そのため、シーム溶接は、燃料タンクや小型コンテナ、パイプラインなど、密閉が必要な肉厚3mm以下の薄肉構造物にしか適さない。
(3) バット溶接
突合せ溶接は抵抗溶接の一種で、ワークピースを突合せ継手に組み立てる。突合せ溶接では、溶接部品の品質を確保するために、ワークの端面が同じか類似の形状およびサイズであることが要求される。突合せ溶接は主に、閉鎖部品の製造、圧延材の延長、自転車のリム、レール、工具などの異種材料部品の製造に使用される。
2.摩擦圧接
摩擦圧接は圧接の一種で、ワーク表面の摩擦で発生する熱を利用して端面を熱可塑性状態にし、素早く鍛造して接合を完了する。
摩擦圧接の特徴は以下の通りである:
- 摩擦過程でワーク接触面の酸化皮膜や不純物が除去されるため、接合部に気孔やスラグ介在物などの欠陥が生じにくい。組織が緻密で、接合品質が良い。
- 溶接可能な材料の範囲が広く、非鉄とステンレス、アルミと銅、アルミとセラミックスなどの異種材料の突き合わせ溶接に適している。
- 装置はシンプルで、消費電力が少なく、操作が簡単で、溶接材料を必要とせず、自動化が容易で、生産性が高い。
III.ろう付け
ろう付けは、ワークの融点よりも低い融点を持つ金属フィラーを使用する溶接方法である。フィラーメタルを加熱して溶かし、液状のフィラーメタルが母材を濡らし、接合部の隙間を埋めて母材と拡散し、永久的な接合を実現する。使用するろう材の融点により、ろう付けは硬ろう付けと軟ろう付けの2つに分けられる。
ろう付けの特徴は以下の通りである:
- ろう付けは、加熱温度が低く、接合部が滑らかで平坦であり、ワークの寸法が正確である。
- 異種金属や板厚の大きなワークの溶接が可能。
- ワーク全体を加熱することで、複数の接合部からなる複雑な部品のろう付けを同時に行うことができ、高い生産性を実現する。
- ろう付け設備はシンプルで、生産投資コストは低い。
しかし、ろう付けの接合強度は比較的低く、耐熱性が劣り、許容使用温度は高くなく、溶接前に厳密な洗浄が必要である。溶加棒のコストも比較的高い。そのため、ろう付けは主に精密機器、電気部品、異種金属部品、一部の複雑な薄肉部品(サンドイッチ構造や自動車のラジエーターなど)の溶接に使用される。また、さまざまなワイヤーや硬質合金工具の溶接にもよく使われる。
IV.電極アーク溶接
電極アーク溶接 は、初期に開発された溶接法であり、現在も最も広く使 われている溶接法である。その特長は、簡単な設備、低コスト、フレキシブルなプロセス、強い適応性(さまざまな材料、長距離、不規則な溶接部に適している)であるが、労働集約度が高く、効率が低い(手作業で、連続溶接ができない)。
1.電極アーク溶接用工具
(1) 溶接トング
その機能は電極を保持し、電流を流すことである。
(2) アークマスクと手袋
アークマスクは、アーク光やその他の危険から顔や皮膚を守るための保護具である。アークマスクには、携帯型とヘルメット型がある。
(3) その他のツール
スラグ除去ハンマーや、溶接部の表面とスラグ・シェル を洗浄するためのワイヤー・ブラシなど。
2.電極アーク溶接の主な設備
電極アーク溶接の主な装置はアーク溶接機である。 溶接機.アーク溶接機は、供給する溶接電流の種類によって交流アーク溶接機と直流アーク溶接機に分けられる。
(1) 交流アーク溶接機
交流アーク溶接機は、溶接用の交流電流を供給します。これは特別な降圧変圧器であり、簡単な構造、低価格、信頼できる使用、低い働く騒音および容易な維持の利点がある。そのため、交流アーク溶接機は溶接によく使用される。主な欠点は、溶接中にアークが安定しないことである。
(2) 直流アーク溶接機
直流アーク溶接機は、溶接に直流電流を供給する。アークが安定し、アーク発生が容易で、溶接品質が良いという利点がある。しかし、直流アーク溶接機の構造は複雑で、 騒音が大きく、コストが高く、保守が難しい。
3.溶接棒
の構成である。 溶接棒 を図1に示す。
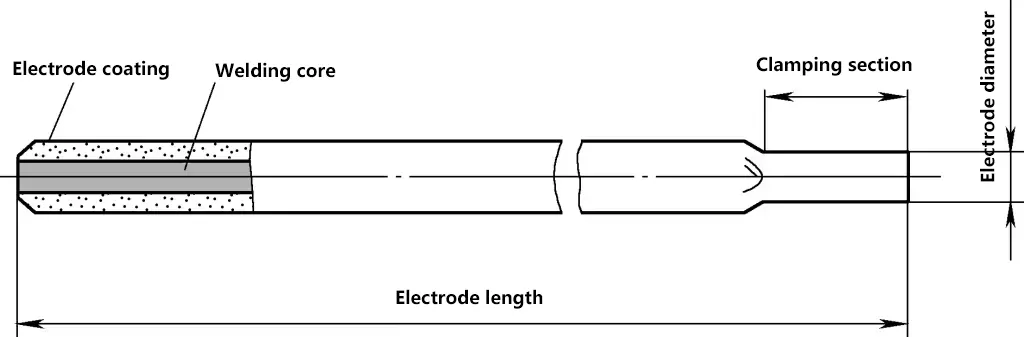
フラックスが塗布されたアーク溶接に使用される溶接棒は、芯線とフラックス・コーティングの2つの部分で構成されている。
芯線は、一定の長さと直径を持つ金属線である(炭素鋼、合金鋼、ステンレス鋼、鋳鉄、銅および銅合金、アルミニウムおよびアルミニウム合金など)。芯線には2つの機能がある。1つは電流を流してアークを発生させること、もう1つは自ら溶けて母材と溶接部を形成することである。芯線の直径は一般に2.5mm、3.2mm、4.0mmである。
フラックス・コーティングは、アーク安定剤(主にカリウム、ナトリウム、カルシウムのイオン化しやすい化合物を使用)、スラグ形成剤(スラグを形成して溶融池の表面を覆い、大気の侵入を防いで冶金的役割を果たす)、ガス形成剤(分解してCOやHなどのガスを発生させ、アークと溶融池を取り囲んで大気を隔離し、溶滴と溶融池を保護する)など、さまざまな材料で構成される。
フラックス・コーティングの主な機能は、アークへの着火を容易にし、安定したアーク燃焼を維持し、空気を遮断することである。フラックス・コーティングは酸性または塩基性である。
溶接棒はその用途によって、構造用鋼溶接棒、耐熱鋼溶接棒、ステンレス鋼溶接棒に分類することができる、 鋳鉄溶接 棒、銅および銅合金溶接棒、アルミニウムおよびアルミニウム合金溶接棒など。このトレーニングで使用する溶接棒のモデルはE4303で、炭素鋼溶接棒に属し、酸性でチタン・カルシウムタイプのフラックス・コーティングが施され、直径は2.5mmです。
4.溶接棒を用いたアーク溶接の溶接原理
溶接回路は、アーク溶接機、溶接ケーブル、溶接クランプ、溶接棒、ワーク、アークで構成される(図2)。アークは接触短絡法で点火される。高温下では、溶接棒とワークが部分的に溶けて溶融池が形成される。アークが連続的に移動すると、溶融池は徐々に冷却され、結晶化して溶接部を形成する。
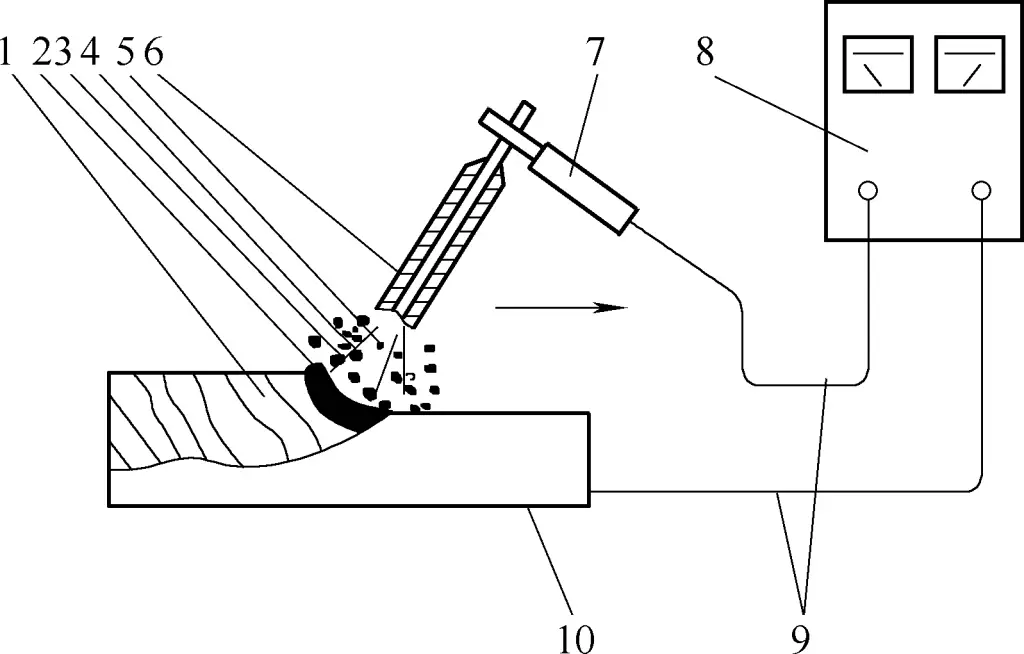
1ウェルド
2-溶けたプール
3-シールド・ガス
4アーク
5-溶けた液滴
6-溶接棒
7-溶接クランプ
8-溶接機
9ケーブル
10ワークピース
5.溶接棒を用いたアーク溶接の溶接パラメータ
溶接棒によるアーク溶接の溶接パラメーターには、溶接電源の種類と極性、溶接棒の直径、溶接電流、アーク電圧、溶接速度、溶接層数などが含まれる。
V.ガス溶接とガス切断
1.ガス溶接の特徴と応用
ガス溶接は、ガス炎を熱源として母材と溶加材を溶かす溶接法である。アセチレンを純酸素で燃焼させると、空気中で燃焼させるよりも火炎温度を大幅に上昇させることができる(最高3000℃以上)。
2.ガス溶接の設備と工具、補助工具、保護具
(1) 酸素ボンベ
酸素ボンベは、高圧酸素を貯蔵・輸送するための容器である。容積は40Lで、最大貯蔵圧力は15MPa。規則により、酸素ボンベの外装はスカイブルーに塗装され、黒いペンキで「Oxygen」と表示されている。
(2) 圧力調整器
減圧器(図3)は、高圧酸素ボンベから供給される高圧酸素を溶接トーチの使用圧力(0.1~0.3MPa)に減圧して溶接に使用するものである。
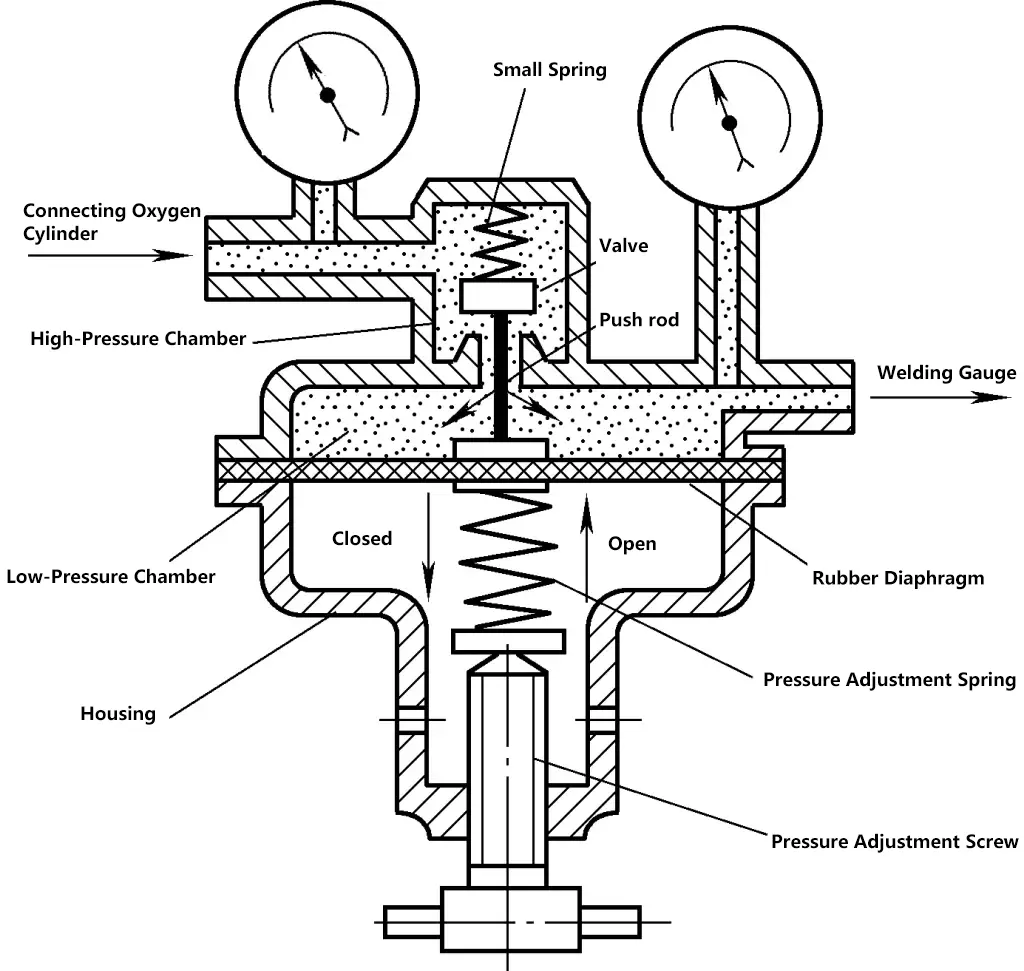
(3) アセチレン・ボンベ
アセチレンボンベは、アセチレンを貯蔵・運搬するための容器である。形状は酸素ボンベに似ているが、表面は白く塗られ、赤いペンキで「Acetylene」と記されている。アセチレンボンベの中には、アセトンを染み込ませた多孔質充填材が充填されている。
(4) 溶接トーチ
溶接トーチ(図4)は、アセチレンと酸素を一定の割合で混合し、安定したガス溶接炎を得るための道具である。
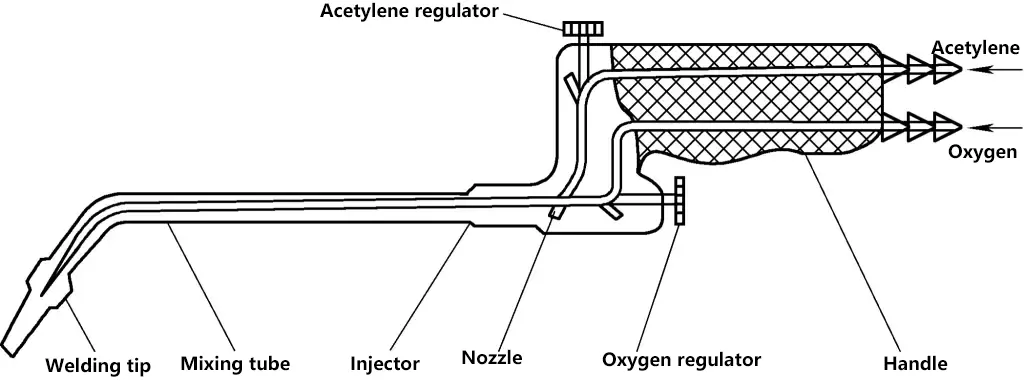
インジェクター式溶接トーチには、アセチレンジョイント、酸素ジョイント、ハンドル、アセチレンバルブ、酸素バルブ、インジェクターチューブ、ミキシングチューブ、ノズルなどが含まれる。
(5) 補助工具および保護具
補助工具には、クリーニング・ニードル、ゴム・ホース、イグナイター、ワイヤー・ブラシ、スラグ・ハンマー、ヤスリなどがある。保護具には、ガス溶接ゴーグル、作業着、手袋、作業靴、レッグガードなどがある。
3.ガス溶接炎(酸素アセチレン炎)
酸素とアセチレンが燃焼してできる炎を酸素アセチレン炎という。酸素バルブとアセチレンバルブの調整により、酸素とアセチレンの混合比を変えることができ、図5に示すように、中性炎、酸化炎、浸炭炎の3種類の炎を得ることができる。
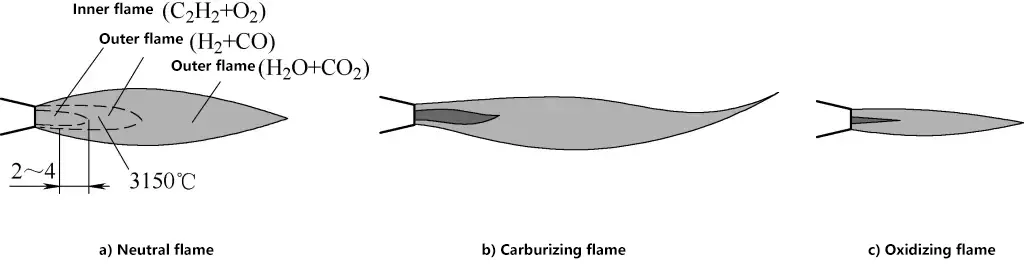
(1) ニュートラル・フレイム(図5a)
酸素とアセチレンの体積比が1~1.2である場合、その火炎は中性火炎と呼ばれ、普通火炎とも呼ばれる。中性炎は一般に溶接に用いられ、低炭素鋼、中炭素鋼、合金鋼、純銅、アルミニウム合金などの溶接に用いられる。
(2) 浸炭炎(図5b)
酸素とアセチレンの体積比が1以下であれば、浸炭火炎が得られる。
(3) 酸化炎(図5c)
酸素とアセチレンの体積比が1.2以上になると、酸化炎が形成される。
4.ガス溶接の基本技術
ガス溶接の際、一般に溶接トーチは右手に持ち、親指をアセチレン・スイッチに、人差し指を酸素スイッチに添えて、いつでもガス流量を調節できるようにする。他の3本の指は溶接トーチのハンドルを持ち、左手は溶接棒を持つ。ガス溶接の基本操作は、点火、炎の調整、溶接、消火である。
(1) 点火、炎の調整、消火
点火の際は、まず酸素バルブを少し開け、次にアセチレンバルブを開け、直火(電子ガンや低圧電気スパークなど)で点火します。この時の炎は浸炭炎で、その後徐々に酸素バルブを開けて浸炭炎を中性炎に調整します。酸素を増やし続ける(アセチレンを減らす)と酸化炎になる。
溶接が終了し、炎を消す必要がある場合は、まずアセチレン・バルブを閉じ、次に酸素バルブを閉じて、逆火を防止し、煙を減らす必要がある。
(2) 通常の溶接
高品質で美観に優れた溶接部を得、溶融池の熱を 制御するためには、図6に示すように、溶接トーチと 溶接棒を均一かつ協調的に移動させる必要があ る。すなわち、ワークの継ぎ目に沿った縦方向の移動、 溶接継ぎ目に沿った溶接トーチの横方向のスイング、 上下に移動する溶接棒の垂直送給である。

1-溶接棒
2-溶接トーチ
3ウェルドメント
(3) ウェルド・シーム・ターミネーション
溶接継ぎ目の端部まで溶接する場合、端部の放 熱条件が悪いため、溶接トーチと被溶接物の間の 角度を小さくし(20°~30°)、溶接速度を上げ、 溶融池が膨張してバーンスルーが発生するのを防ぐた め、溶接ワイヤーを追加する。
5.ガス切断
ガス切断とは、ガス炎の熱エネルギーを利用して被加工物を一定の温度まで予熱した後、高速の切断用酸素気流を噴射して被加工物を燃焼させ、熱を放出して切断する方法である。金属を溶かすガス溶接とは根本的に異なり、ガス切断は純粋な酸素の中で金属を燃やす。
(1) 金属酸素切断の条件
金属材料の発火点は、その融点より低くなければならない。燃焼によって生成する金属酸化物の融点が、金属自体の融点より低いこと。金属が燃焼すると大量の熱が放出されるため、金属自体の熱伝導率が低いこと。これらの条件を満たす金属材料だけがガス切断できる。高合金鋼、銅、アルミニウムなどはガス切断が難しい。
(2) ガス切断工程
ガス切断は、溶接トーチの代わりに切断トーチを使用し、その他の設備はガス溶接と同じである。切断トーチの形状と構造を図7に示す。
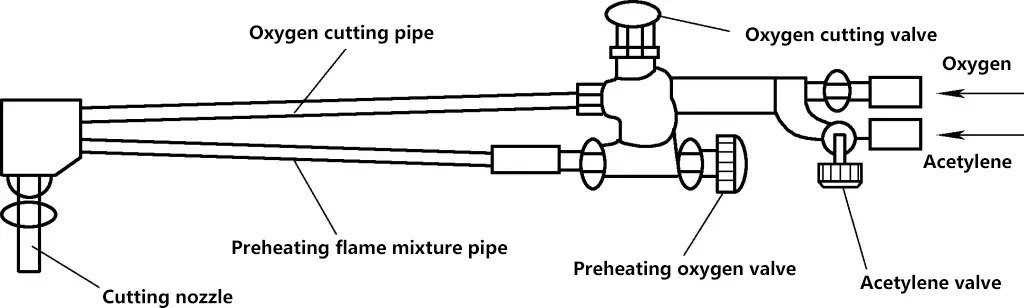
ガス切断では、まず切断部付近の金属を酸素アセチレン炎で発火点(約1300℃、黄白色)まで予熱した後、切断トーチの切断用酸素バルブを開き、高圧酸素噴流によって高温の金属を即座に燃焼させる。その結果、図8に示すように、酸化物(すなわち溶融状態の酸化鉄)も同時に酸素流によって吹き飛ばされる。
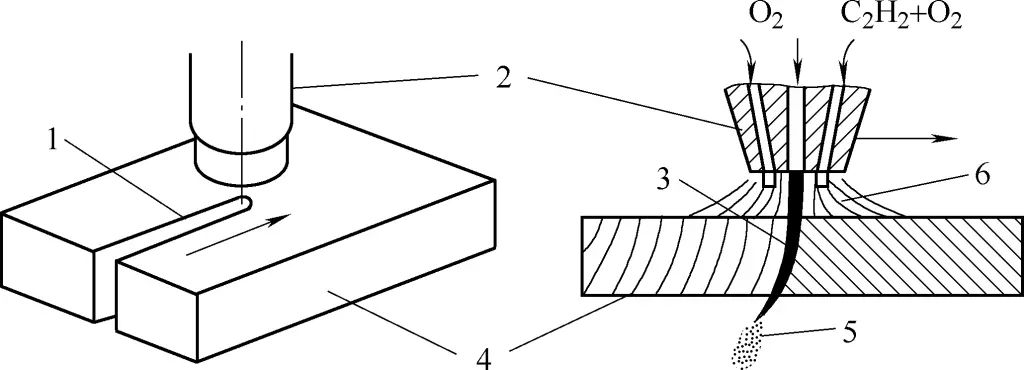
1カット
2カッティングノズル
3-酸素ストリーム
4ワーク
5酸化物
6-予熱炎
VI.ガスシールドアーク溶接
アーク媒体として外部ガスを使用し、アークと溶融池を保護するアーク溶接法をガス・シールド・アーク溶接と呼ぶ。一般的に使用されるシールド・ガスは、アルゴンとCO2である。
1.アルゴンアーク溶接
シールド・ガスにアルゴンを使用するガス・ シールド・アーク溶接は、アルゴン・アーク 溶接と呼ばれる。
(1) アルゴンアーク溶接の基本原理
アルゴン・ガスは、アルゴン・アーク溶接ガンのノズルから均一に噴射され、アークと溶融池の周囲に連続した閉鎖気流を形成して空気を排出し、溶接ワイヤと溶融池を空気との接触から保護する。
アルゴンは不活性ガスであるため、液体金属と化学反応せず、金属に溶解しない。同時に、アルゴン・ガス流はアークに一定の冷却・圧縮効果を与えるため、アルゴン・アークのエネルギーは比較的集中し、加熱速度は速い。そのため、アルゴン・アーク溶接の溶接品質は比較的高い。
(2) アルゴンアーク溶接の特徴
アルゴンは、液体金属を酸化から効果的に保護できる不活性ガスである。アーク熱は集中し、熱影響部は小さく、溶接部の変形は小さい。操作は目に見え、直感的で簡単である。アークは安定し、スパッタは少なく、溶接継ぎ目は緻密で、機械的性質と耐食性に優れ、表面にスラグはなく、溶接継ぎ目の外観は美しい。
(3) アルゴンアーク溶接の応用
アルゴンアーク溶接は、多くの利点を備えた高品質の溶接法であり、造船、航空、航空宇宙、化学、機械、電子などの産業で広く使用されている。
しかし、アルゴンアーク 溶接設備 は複雑で、溶接コストは比較的高い。主に高合金鋼、チタン合金、ステンレス鋼、アルミニウム、銅合金、レアメタルなどの貴重な金属の溶接に使用される。
(4) アルゴンアーク溶接装置とプロセス
このセクションでは、研修会場の実際の設備に基づき、既存の設備、プロセス、主要な操作ポイントを紹介する。
(5) アルゴンアーク溶接作業
代表的なワーク:ステンレス鋼のアルゴンアーク溶接作業。
2.CO2 ガスシールド溶接
COを用いたガスシールド溶接2 をシールド・ガスと呼ぶ。2 ガス・シールド溶接。一般に半自動溶接と自動溶接に分けられる。
(1) COの基本原理2 ガスシールド溶接
消耗電極ガス・シールド溶接の一種で、溶接ワイヤとワークの間に発生するアークを利用して金属を溶かす。CO2 ガスは、溶接ワイヤと溶融した溶接継ぎ目の周りの空間を均一に流れ、空気中の酸素を溶接継ぎ目から隔離し、溶接継ぎ目を保護する。
(2) CO2 ガスシールド溶接
CO2 溶接中、電流密度が高く、アーク熱利用率が高 く、溶接後にスラグを清掃する必要がなく、生産性が 高い。アーク熱が集中し、溶接部の加熱面積が小さ く、変形が小さく、溶接継ぎ目の耐亀裂性が高く、開 放アーク溶接の溶接品質が高い。