
1.溶接棒の分類
(1) 溶接棒の用途による分類
1) 炭素鋼溶接棒は、主に低炭素鋼と低合金鋼の低強度グレードの溶接に使用されます。
2) 低合金鋼溶接棒は、主に低合金高強度鋼、モリブデン含有耐熱鋼、コバルトモリブデン耐熱鋼、低合金元素含有耐熱鋼、低温鋼の溶接に使用される。
3) ステンレス鋼溶接棒は、主にモリブデン耐熱鋼、コバルトモリブデン耐熱鋼など合金元素の多い鋼種や各種ステンレス鋼の溶接に使用される。
4)ハードフェーシング溶接棒は、金属表面のハードフェーシングに使用され、その析出金属は室温または高温で良好な耐摩耗性と耐食性を有する。
5) 鋳鉄溶接 ロッドは特に鋳鉄の溶接や補修溶接に使用される。
6) ニッケルおよびニッケル合金溶接棒は、ニッケルおよびニッ ケル合金の溶接、補修溶接、ハードフェーシングに使 用される。
7) 銅および銅合金の溶接棒は、銅および銅合金の溶接、補修溶接、またはハードフェーシングに使用され、特定の鋳鉄の補修溶接や異種金属の溶接にも使用できる。 金属.
8) アルミニウムおよびアルミニウム合金の溶接棒は、アルミニウムおよびアルミニウム合金の溶接、補修溶接、ハードフェーシングに使用される。
9) 特殊用途溶接棒は、水中溶接、切断、パイプ溶接などに使用される。
(2) 電極被覆の溶融後に形成されるスラグの特性に基づく分類
溶接プロセスでは、電極被覆が溶融した後、 生成されるスラグが酸性か塩基性かに基づいて、 電極は塩基性電極(スラグ塩基度≥1.5)と酸性 電極(スラグ塩基度≤1.5)に分けられる。酸性電極と塩基性電極の加工性能と溶接金属 特性の比較を表5-7に示す。酸性電極は、合金元素の含有量が高い 溶接材料には適さない。塩基性電極は、塑性性、靭性、耐割れ性 が酸性電極より優れているため、重要な部 品の溶接には一般的に使用される。
表5-7 酸性電極と塩基性電極のプロセス性能および溶接金属特性の比較
比較項目 | 酸性電極 | 基本電極 |
---|---|---|
プロセス・パフォーマンス | 始動が容易で、交流でも直流でも安定したアークが得られる。錆、油、水分の影響を受けにくく、耐気孔性にも優れている。 | フラックス中の酸化物がガスのイオン化に影響し、アークの安定性が悪く、直流でしか使用できない。水や錆による気孔の影響を受けやすく、使用前に350~400℃で1時間の予熱が必要。 |
溶接金属の特性 | 通常の常温および低温衝撃性能で、合金元素の焼損が多い。 | 良好な常温および低温衝撃性能;効果的な合金元素移行により、良好な塑性と靭性を有する;依然として良好な低温衝撃靭性を示す;強力な脱酸および脱硫能力により、溶接部の水素、酸素および硫黄含有量が低く、良好な耐亀裂性を有する。 |
2.電極の要件と選択の原則
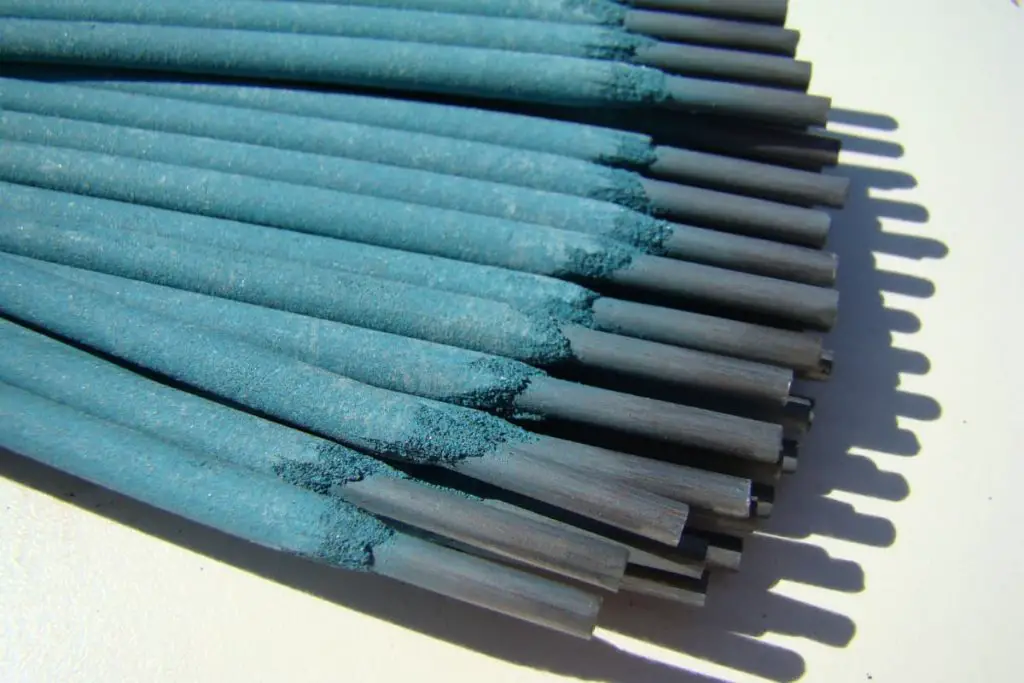
(1) 電極の基本要件
溶接プロセス中、電極は良好なプロセス性能を有 し、溶接金属が要求される機械的特性、化学組成、 または特殊特性を持つことを保証しなければな らない。そのため、電極には以下の要件が提案され ている:
1) アークが点火しやすく、溶接プロセス中に安定し て燃焼し、再点火しやすいこと。
2) フラックス・コーティングは、固まったり落ちたりすることなく均一に溶けること。フラックス被膜の溶融速度は、芯線の溶融速度よりわずかに遅くする。これにより、電極の溶融端が釣鐘状のスリーブを形成し、金属液滴の移行と保護雰囲気の形成に寄与する。
3) 溶接工程では、過度の煙や、大きすぎたり多すぎたりするスパッタがあってはならない。
4) 析出した金属が一定の耐クラック性、要求される機械的特性、化学組成を有することを確認する。
5) 正常な溶接部形成と容易なスラグ除去を確保する。
6) 溶接継ぎ目のX線検査は、GB/T 3323-2005「金属溶融溶接継ぎ目のX線写真撮影」に規定されるレベルⅡ基準以下であってはならない。
(2) 電極選択の原則
1) 溶接金属の性能要件。
構造用鋼の溶接では、同じ種類の鋼材を溶接する場合、鋼材の引張強さに合わせるという原則に従って電極を選択する;
異なる種類の鋼材を溶接する場合は、強度の低い方から選択する;
耐熱鋼溶接では、溶接金属の常温性能だけでなく、高温性能も考慮して選定する;
ステンレス鋼溶接の場合、溶接成分が母材成分 に適合していることを確認し、溶接継手の特 殊性能を確保する。
2) 溶接部の作業条件を考慮する。
高温または低温条件下で作業する溶接部品には、耐熱鋼電極または低温鋼電極を使用すべきである;
耐摩耗性や耐傷性が要求される溶接部品には、使用温度に応じ、常温または高温硬度で、耐傷性、耐酸化性などに優れた電極を選択する;
腐食性媒体と接触する溶接部品には、ステンレス鋼電極または他の耐食性電極を使用する。振動または衝撃荷重を受ける溶接部品には、引張強度の確保に加えて、より高い塑性と靭性を持つ低水素電極を選択する;
静的荷重のみを受ける溶接部品の場合は、母材 と同等の引張強度を持つ電極を選択すればよい。
3) 溶接部の形状、剛性、溶接位置を考慮する。
複雑で硬い溶接部品では、溶接金属の収縮に よって発生する応力が大きいため、より優れた塑性 性を持つ電極を使用すべきである。同じタイプの 電極を選択する場合は、機械的特性だけでなく、 溶接継手の形状の影響も考慮する必要がある。
なぜなら、突合せ継手を溶接する場合、強度と塑性が中程度であれば、隅肉溶接を溶接する場合、強度は高く、塑性は低くなるからである。洗浄が困難な溶接部品には、酸化性、錆び、油に弱い酸電極を使用し、溶接の品質を確保する。
4) 溶接金属の耐割れ性を考慮する。
溶接部の剛性が高い場合、母材中の炭素、硫黄、リンの含有量が多い場合、外気温が低い場合などは、溶接部に割れが発生しやすい。溶接には耐割れ性の高いアルカリ性電極を選ぶのがよい。
5) 電極の操作性を考慮する。
溶接工程では、アークが安定し、スパッタが少なく、整然 とした対称的な溶接部が形成され、スラグ除去が容易で、 全姿勢溶接に適したものでなければならない。
酸性電極とアルカリ性電極の両方が要求を満たす場 合、操作性の良い酸性電極をできるだけ使用すべきである が、まず溶接部の性能と耐亀裂性を確保しなければならな い。
6) 設備と施工条件を考慮する。
直流溶接機がない場合は、直流電力に限定した電極は使用せず、交流と直流の両方に適した低水素電極を選択すべきである。被加工物を回転させることができず、すべての位置で溶接しなければならない場合は、さまざまな空間位置に適応できる電極を選択すべきである。
立向および上向きの溶接では、チタン・タイプ、イルメナイト・タイプの被覆の順に電極を選ぶことを推奨する。
狭い容器や狭い環境で溶接する場合は、換気をよくすることに加え、アルカリ性低水素電極は溶接中に有害なガスや粉塵を多量に放出するため、できるだけ使用しないことが必要である。
溶接後の熱処理が必要だが、施工条件により熱処理ができないワーク(パーライト系耐熱鋼など)には、溶接後の熱処理を避けるために特殊な電極を選択することができる。
7) 経済合理性について考える。
溶接に要求される性能を確保する同じ条件下で は、より低コストの電極を選択すべきである。
例えば、イルメナイト型電極は、チタンカルシウム型電極に比べ、コストが非常に低く、性能確保を前提にイルメナイト型電極を選択する必要がある。また、性能と操作性を両立させることを前提に、スペックが大きく、効率の高い電極を選択することが望ましい。
3.電極の使用
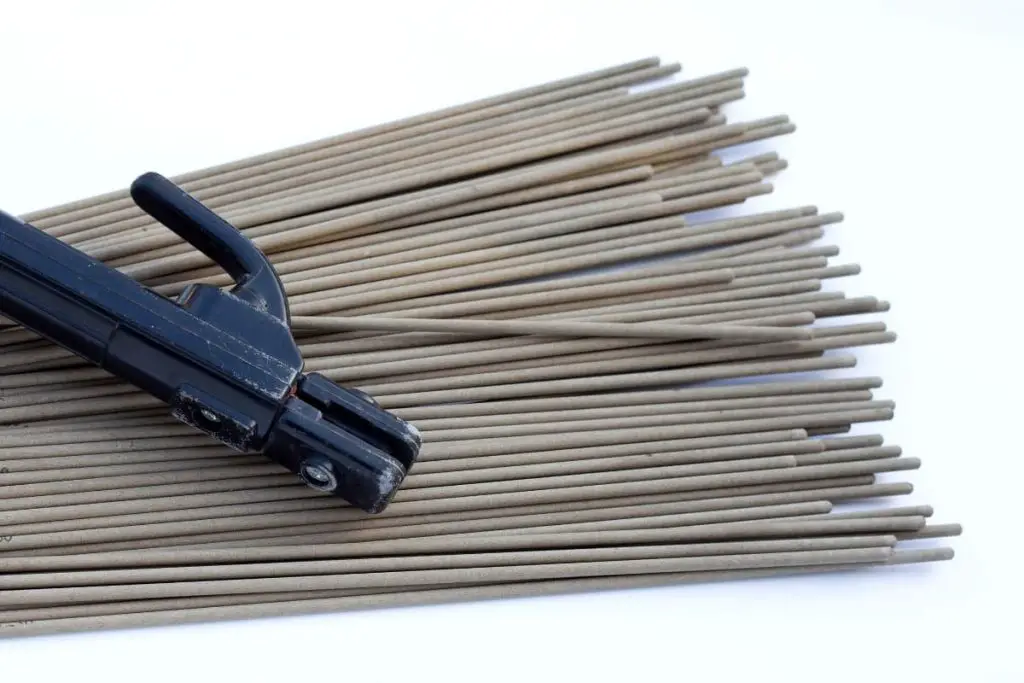
電極はメーカーからの品質証明書が必要であり、品質証明書がない場合や品質に疑問がある場合は、バッチサンプリングテストを実施する必要がある。
特に重要な製品を溶接する場合は、溶接前に選択した電極を確認し、長期保管した電極も確認した上で使用可否を判断する必要がある。
電極内部に錆が発見された場合は、使用前に試験し、適格であることを確認しなければならない。電極の被覆がひどく湿っていて、被覆の剥離が観察される場合は、廃棄しなければならない。
電極は通常、使用前にマニュアルで指定された温度で乾燥させる必要があります。電極を乾燥させる際には、以下の点に注意する必要がある:
1) セルロース電極は焦げやすいので、使用前に100~200℃で1時間乾燥させる。
2) 酸性電極は、湿気の程度にもよるが、70~150℃で1~2時間乾燥させる。保管時間が短く、包装に異常がなければ、使用前にさらに乾燥させることなく、一般構造用鋼溶接に使用できる。
3) アルカリ電極は、一般に350~400℃で1~2時間乾燥させる。溶接する低合金鋼が低温割れを起こしやすい場合は、乾燥温度を400~450℃に上げ、100~150℃の保温筒に保管してすぐに使用できるようにします。
4) 電極を乾燥させる場合は、低い温度からオーブンに入れて徐々に温度を上げる。
高温のオーブンから直接取り出さず、オーブン温度が下がるのを待ってから取り出す。これは、冷たい電極を高温のオーブンに入れたり、急冷したりすることによるコーティングのひび割れを防ぐためである。
5) 溶接棒を乾燥させる場合、積み重ねたり束ねたりせず、層状に並べ、各層はあまり厚くせず、一般に1~3層とする。
6) 低水素溶接棒は、低温オーブンで一定温度に保たれたものを除 き、一般に室温に4時間以上放置した場合は再乾燥が必要である。再乾燥の回数は3回を超えないこと。
7) 屋外で作業する場合、溶接棒は一晩中適切に保管し、屋外に放置してはならない。
4.溶接棒の管理
(1) 溶接棒の保管と保存
1) 溶接棒は、種類、ブランド、バッチ、仕様、保管期間ごとに保管し、混同を避けるために各スタックに 明確に表示すること。
2) 溶接棒は、乾燥した風通しのよい屋内に保管する。溶接棒の保管室には温度計と湿度計を設置する。低水素溶接棒の室温は50℃以下、相対湿度は60%以下でなければならない。
3) 溶接棒はラックに保管し、ラックの高さは地面から少なくとも300mm、壁から少なくとも300mmとする。湿気を防ぐため、ラックの下に乾燥剤を置くこと。
4) 溶接棒はユーザーユニットに供給された後、少なくとも6ヶ月は継続使用が保証されるべきであり、 溶接棒の発行は保管されていたものを優先すべきである。
5) 湿気のある溶接棒、包装が破損している溶接棒、および再検査に不合格となった溶接棒は、倉庫に保管することはできない。
6) 湿っている、変色している、または錆びている溶接棒は、品質評価の前に乾燥させなければならない。すべての性能基準を満たしている場合のみ保管することができ、そうでない場合は保管できない。
7) 1年以上保管された溶接棒は、流通前に様々な性能試験を受ける必要がある。要件を満たした場合のみ発行することができ、そうでない場合は保管から解放してはならない。
8) 重要な溶接プロジェクトで使用される溶接棒、特に低水素棒は、一定の温度と湿度を維持する専用の倉庫で保管するのが理想的である。推奨温度は10~25℃、相対湿度は50%未満である。
(2) 工事中の溶接棒の管理
1) 工事期間中、溶接棒は指定された者が管理し、溶接棒請求書を持って倉庫から取り出さなければならない。
書式には、回収者の氏名、溶接棒の種類(ブランド)、直径、回収数量、拠点責任者の署名、請求日、製造者、製造バッチ、製造日、保管日に関するメモを記載する。
2) 溶接棒を受け取った後、拠点生産部門は溶接棒保管台帳に、製造業者、生産バッチ、溶接棒の種類(ブランド)、直径、受け取り数量などの詳細を記入する。
溶接棒は使用前に乾燥させる必要があり、その過程で乾燥記録を作成する。記録の主な内容は、製造者、溶接棒の種類(ブランド)、製造バッチ、直径、乾燥温度、乾燥時間、乾燥数量、乾燥責任者と検査官の署名などである。
この書類は、記録のために3枚複写で作成する。乾燥後、ロッドは溶接工に支給することができ、溶接工は、製造者、タイプ(ブランド)、バッチ、直径、数量、要求時刻、ロッドを受け取る人の署名などの詳細を含む、乾燥ロッドの要求用紙に記入しなければならない。
注意書きには、その棒がどのワークのどの溶接に使 用されるかを明記しなければならない。溶接棒を受け取る際、溶接工は乾燥証明書類を基 盤保管者に要求しなければならない。乾燥証明書類のないロッドは、溶接工に交付してはならない。
3) 乾燥した溶接棒を受け取ったら、溶接棒保温筒に入れる。
混合や潜在的な溶接品質事故を防ぐため、シリンダー1本につき1種類(銘柄)のロッドしか持ち込んではならない。溶接工は一度に5kgを超えるロッドを持ち出さないようにし、残ったロッドは作業場の資材室または建設現場の資材チームが適切に保管しなければならない。
(3) 期限切れ溶接棒の取り扱い
「期限切れ」とは、特定の保管期限を超えたことを指すのではなく、品質劣化(劣化)の程度に差があることを指す。適切に保管された溶接棒は、何年も変化しないことがある。
1) 長年保管した溶接棒は、プロセス性能試験を受ける必要がある。試験前に、アルカリ性低水素棒は300℃前後で1~2時間、酸性棒は150℃前後で1~2時間乾燥させる。
工程性能試験において、フラックスが塊で剥がれ落ちず、アルカリ性低水素棒に気孔が認められなければ、溶接継手の機械的特性は一般的に保証される。
2) 溶接棒の芯金にはわずかな錆があり、一般に機械的特性には影響しないが、低水素電極は重要な構造物の溶接には使用すべきではない。
3) 低水素電極の錆がひどい場合、またはフラックス 被覆が剥がれている場合は、適宜格下げするか、 一般部品の溶接に使用することができる。可能であれば、格下げを決定する前に、国家規格に従って機械的特性を試験することができる。
4) 各種の溶接棒がひどく劣化している場合は、再利用してはならない。フラックス・コーティングを除去し、芯線を洗浄して再利用することができる。