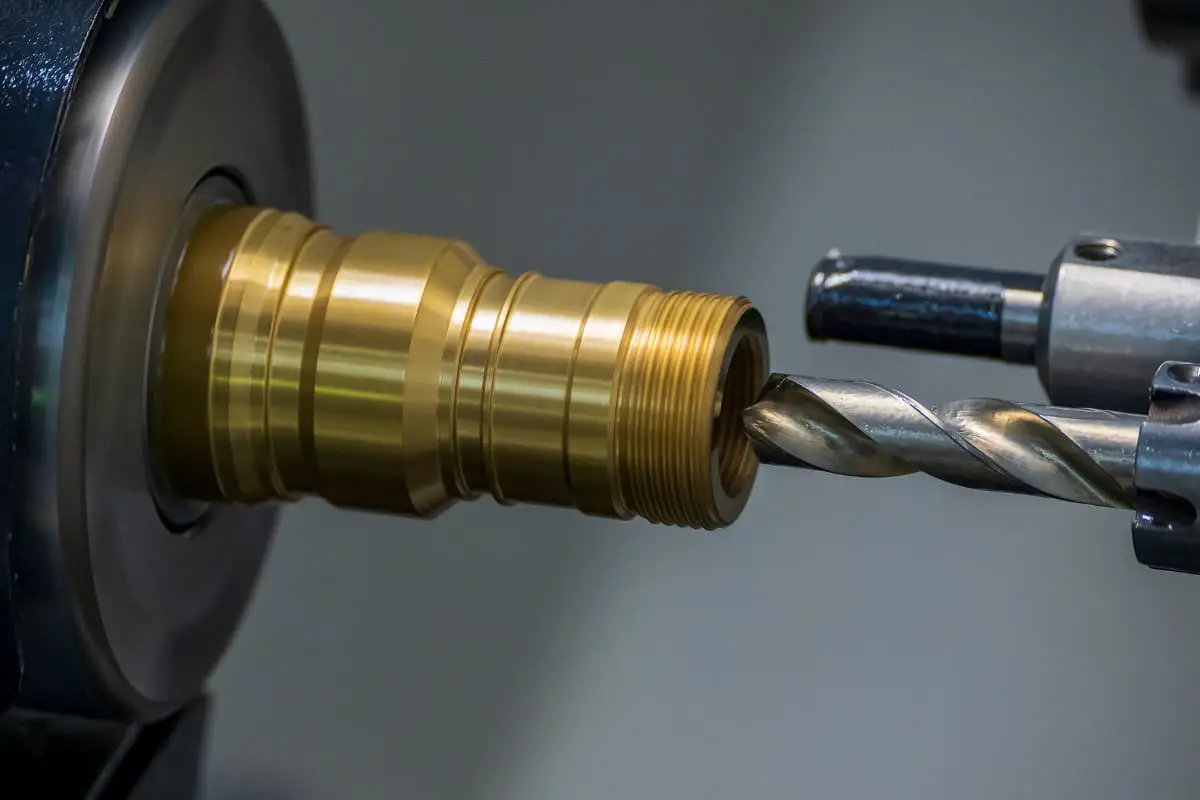
図2-137に旋盤による通常の穴型ワークの旋削加工を示す。
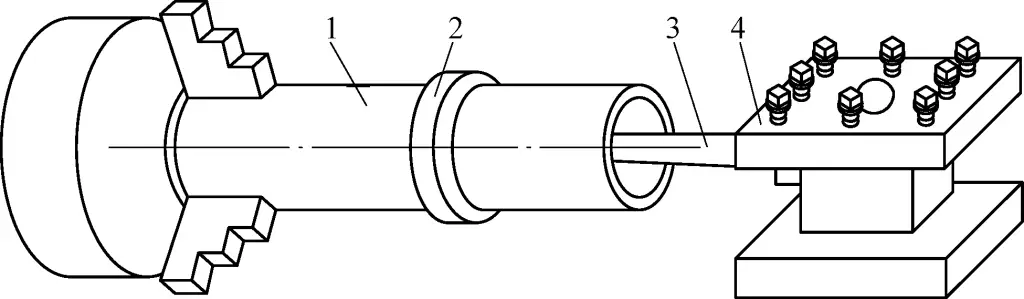
1-防振リング
2ワーク
3-ボーリングツールホルダー
4ツールポスト
I.ボーリング工具
ボーリング条件や被削材の違いにより、選択するボーリング工具の幾何学的角度も異なる。
図2は、焼入れ鋼(硬度55~60HRC)の内孔加工に使用するボーリング工具で、図2aは荒ボーリング工具、図2bは仕上げボーリング工具である。工具インサートの材質はYT30超硬合金、工具ホルダーの材質は45質炭素鋼で、焼入れ後の硬度は35~45HRCである。
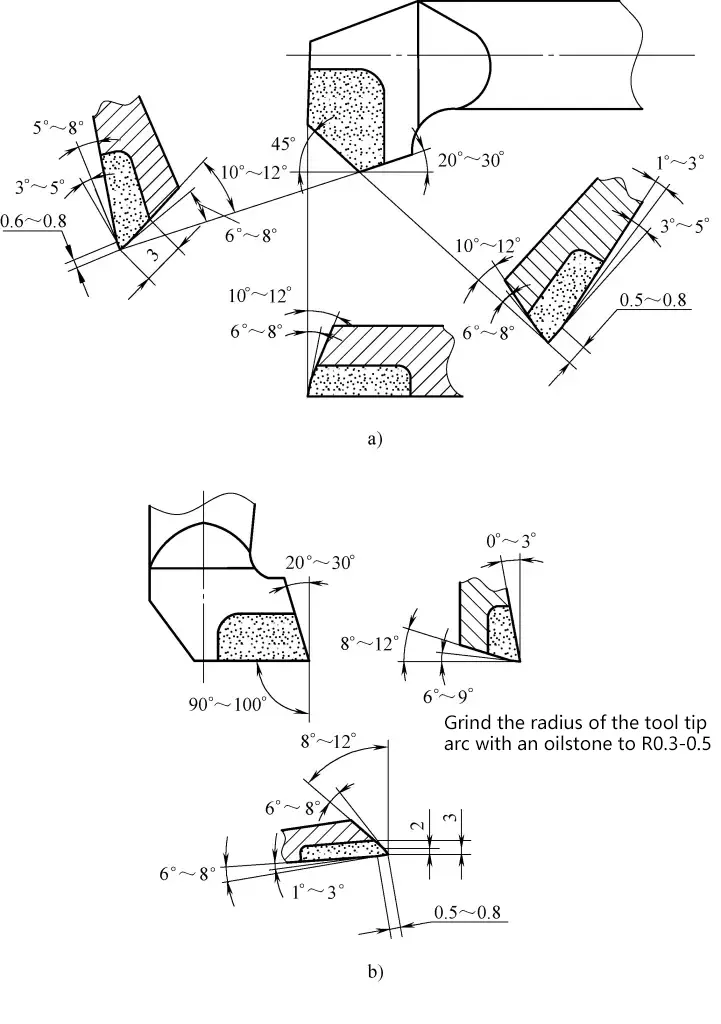
a) 荒ボーリング工具
b) 仕上げ用ボーリング工具
仕上げ用中ぐり工具の刃先の表面粗さRaは0.4μmである。小径穴を加工する場合、工具ホルダーの底面が内孔表面に接触して擦れると、図3に示すように、工具ホルダーの底面がR形円弧状に研削されることがある。
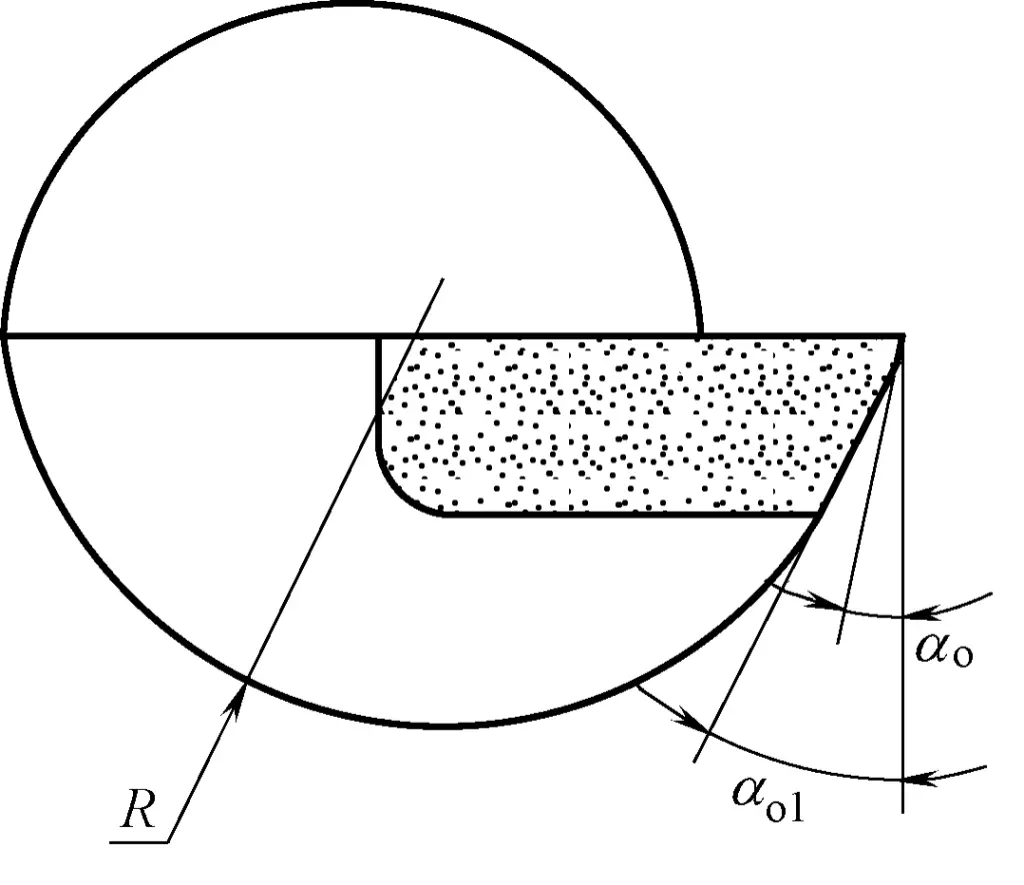
使用した切削パラメータは以下の通り。被削材は焼入れ鋼材であるため 切断速度 vは低くする。荒ボーリングではv=8~12m/min、仕上げボーリングではv=12~16m/min。粗中ぐりではf=0.1~0.15mm/r、仕上げ中ぐりではf=0.05~0.1mm/rとする。荒ボーリングの場合、背面切削深さaは0.05mmを超えないようにする。 切削油剤 は使用されない。
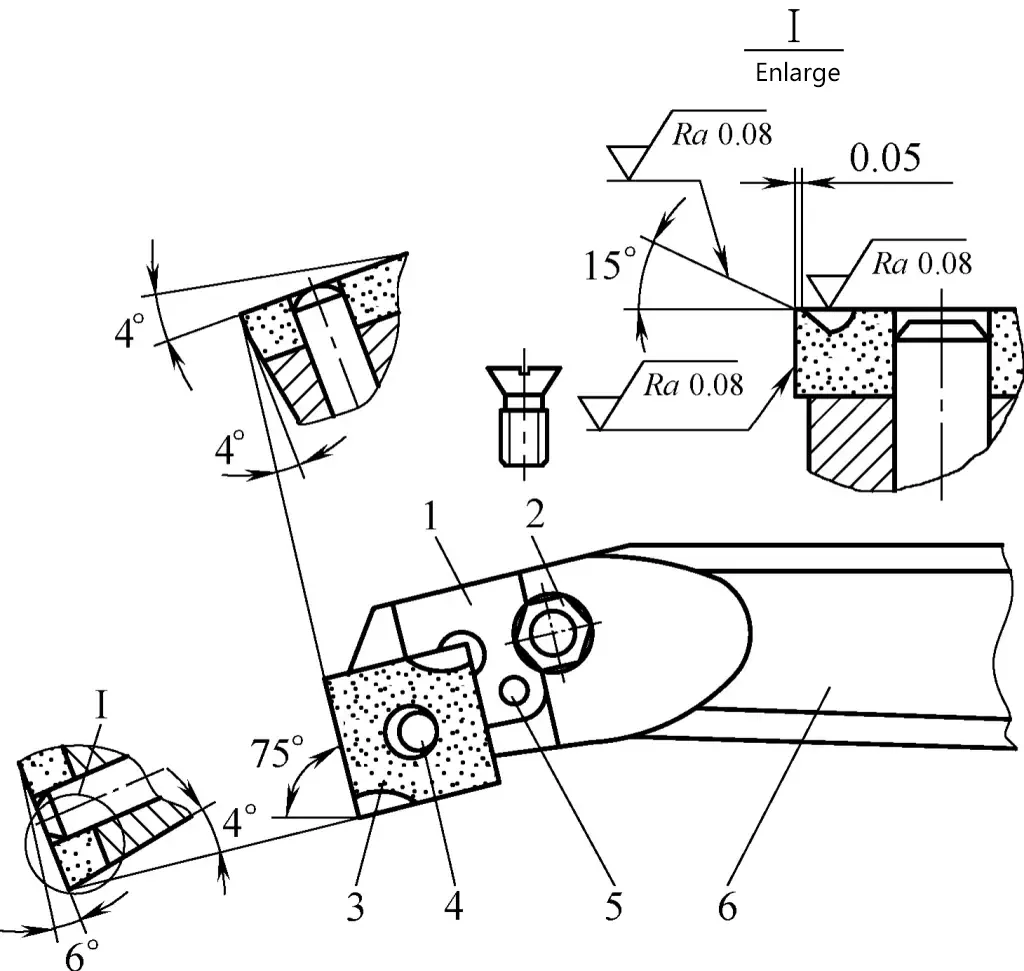
1-クランプブロックを挿入
2-クランプネジ
3-挿入
4-円筒ピン
5-ピボットピン
6ツールシャンク
図6は、すくい角γ=15°、主切れ刃角K=75°、チップブレーカ溝幅2mm、正面表面粗さRa値<0.8μmの機械クランプ式薄肉管用ボーリング工具である。ボーリング加工では、切削はスムーズで速く、切りくずは銀白色に見える。切削パラメータは、切削速度v=80m/min、送り速度f=0.1mm/r。
鋳造穴の高速旋削用ボーリング工具の形状を図5に示す。YGタイプの超硬チップを使用している。切刃は長さ4mmの主切刃、長さ1mmの中間切刃、幅1.2f(fは送り速度)の研磨切刃からなる。主切刃は粗加工に、中間切刃は中仕上げ加工に、研磨切刃は既に旋削された内孔面の研磨に使用される。
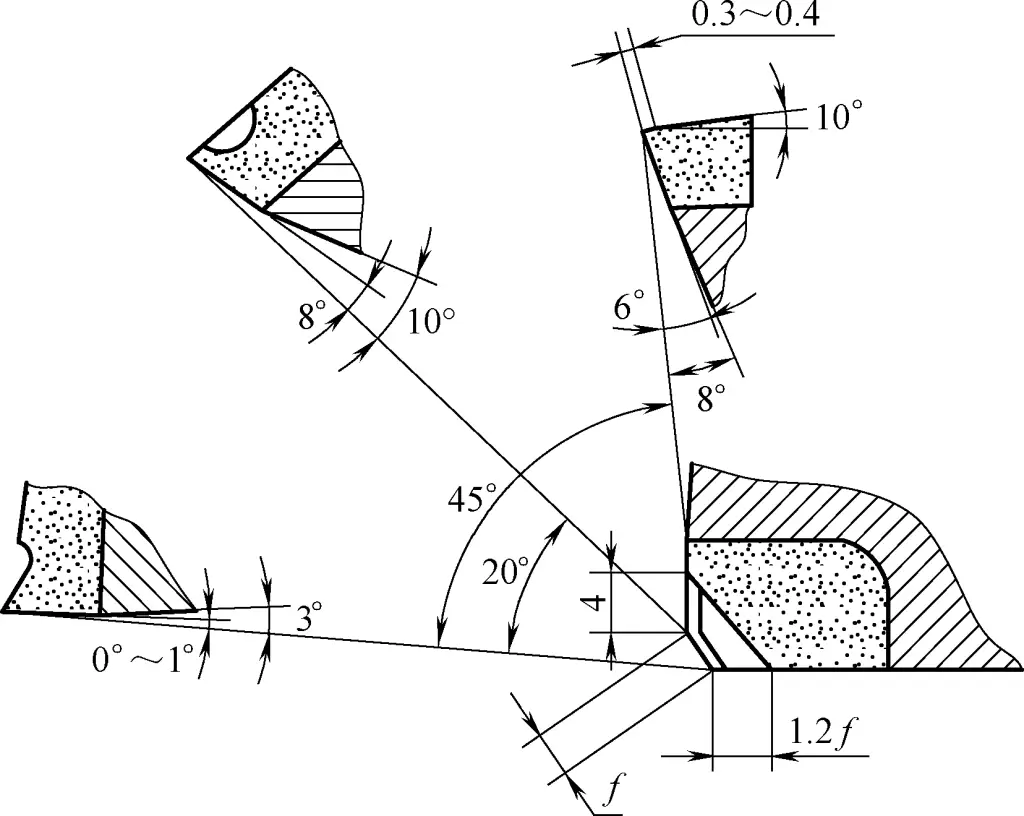
このボーリング工具は、すくい角γ=10°、逃げ角α=8°ですが、研磨刃の逃げ角は1°しかありません。ボーリング中に穴壁と擦れると、工具の底面を丸く研磨することができる。使用した切削パラメータは、切削速度v=200m/min、送り速度f=0.5mm/rである。
図6はYT15超硬チップを使用した折れ線刃のハイパワー中ぐり工具である。この中ぐり工具は、CA6140横型旋盤や中型旋盤で、鋼材に直径60~150mmの短くて太い内径穴を加工する場合に威力を発揮する。
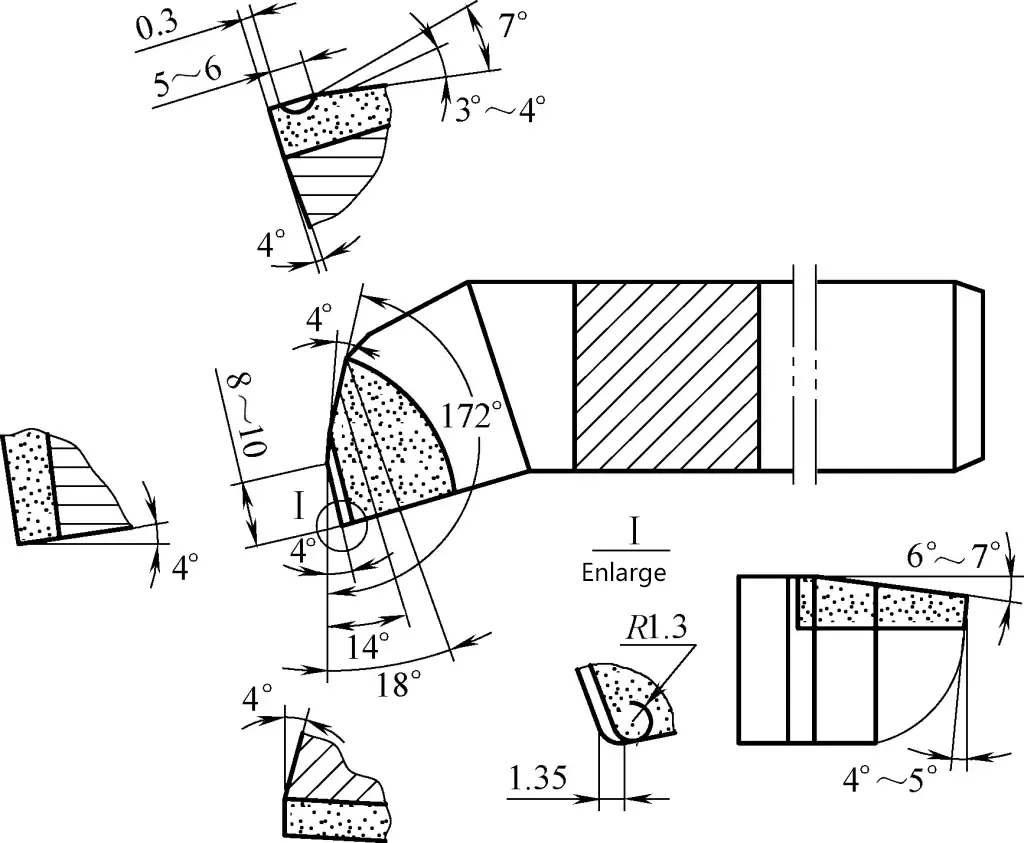
不等辺すくい角を採用し、主切刃を折れ線形状にしたボーリング工具です。ボーリング加工中、左右の切れ刃に力がかかるため、切削力が適切にバランス・相殺され、ラジアル切削力が低減され、切削加工が安定します。主切刃は、チップブレーカープラットフォームと切屑排出傾斜面と角度を形成し、切屑排出性を向上させ、自然な切屑分断を可能にします。
主切刃角はダブル主切刃で、角度は比較的大きい。一般的なボーリング工具に比べ、工具先端のくさび角が172°追加され、負の面取りと工具先端のRで研削され、工具強度が向上し、寿命が延びます。工具ホルダーの材質は45の高品質炭素鋼です。高出力ボーリング工具のため、剛性アップと振動低減のため、ツールホルダ寸法を適度に大きくする必要がある。
使用した切削パラメータは、切削速度v=140-150m/min、背面切削深さa=12-15mm、送り速度f=0.3-0.5mm/rである。
取り付けの際、このボーリングツールはワーク中心より1.5~2mm高くする。
また、大規模生産において、加工能率の向上と中ぐり品質の確保を図るために、図7に示すような中ぐり工具を使用することもできる。加工代が大きい場合や加工代が不均一な長穴を加工する場合に使用できる高能率な中ぐり工具である。
その構造は、両刃のツールヘッドを持つツールインサート式カッターである。工具ヘッドの背面には、4つの合金製サポートブロックが均等に溶接されており、合金製サポートブロックの外径は、工具ヘッドによって穿孔される穴の内径よりも約0.04mm小さい。
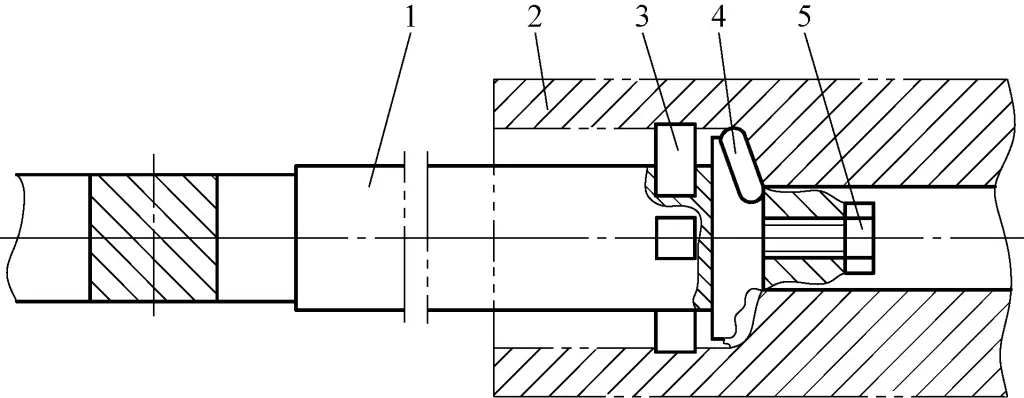
1-ツールホルダー
2ワーク
3-合金サポートブロック
4-両刃ボーリングツールヘッド
5-固定ネジ
加工中、ツールシャンクはツールホルダにクランプされ、その軸は回転中心と一致する。中ぐり加工では、まず両刃の工具ヘッドが切り込み、その直後に内孔を支える合金製のサポートブロックが続く。
4つの合金製サポートブロックの外径は、工具ヘッドによってボーリングされる穴径よりもわずかに小さいことが望ましい。ボーリング加工中、合金製サポートブロックはサポートを提供し、工具シャンクの剛性を確保すると同時に、内孔の円筒度を向上させ、表面粗さを低減させるスクレーパとしても機能する。
長穴加工や大きな取り代の切削加工を行う場合、加工代が大きくなると切りくずが広がります。このような場合、主切刃の後方に複数の切屑分断溝を研削することで、切屑の排出を容易にし、切削液の進入を確保することができる。
切断速度v c 送り速度f=0.2mm/r。取り代40mm程度のワークであれば、1パスで切削が完了する。
II.ツールシャンクの構造形式
旋盤用ツールシャンクの構造は、ワークの状態や加工条件によって多種多様です。ここでは10種類以上の中ぐり工具シャンクをご紹介します。
1.通常のボーリング工具シャンク
(1) ツールシャンク 1
図8に示すように、曲げ加工された鋼板から鍛造され、超硬工具チップが工具ヘッドに溶接されて使用される。代わりに、高速度鋼材を必要なボーリング工具形状に一体鍛造することもできる(工具ヘッドを溶接する必要なし)。
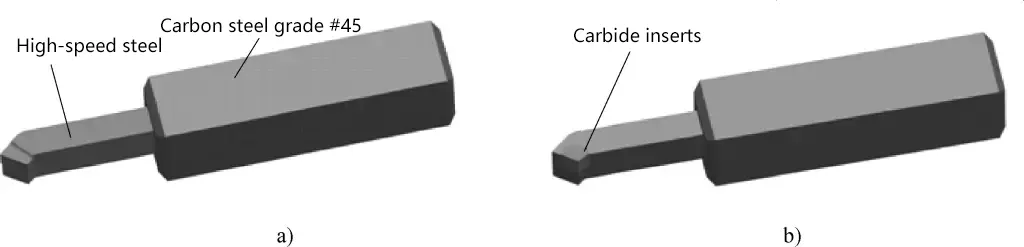
a) 一体型高速度鋼ボーリング工具
b) 溶接ボーリング工具
ボーリングの際は、クロススライドハンドルのダイヤルで背面の切り込み深さを調節する。
(2) ツールシャンク 2
図9に示すように、このボーリング工具のツールヘッドとシャンクは分離している。ネジを緩めれば工具ヘッドを取り外すことができるので、工具の研磨や交換が便利です。

a) 書式 I
b) フォームII
c) フォーム III
通常のボーリング工具のシャンクの構造は最も単純である。工具ヘッドの延長長さを調整する場合、一般的には工具ヘッドをタップし、ノギスで延長長さが条件を満たしているかどうかを測定する(図10)。不適当な場合は、穴径の寸法が保証できるまで、さらに数回タップする。
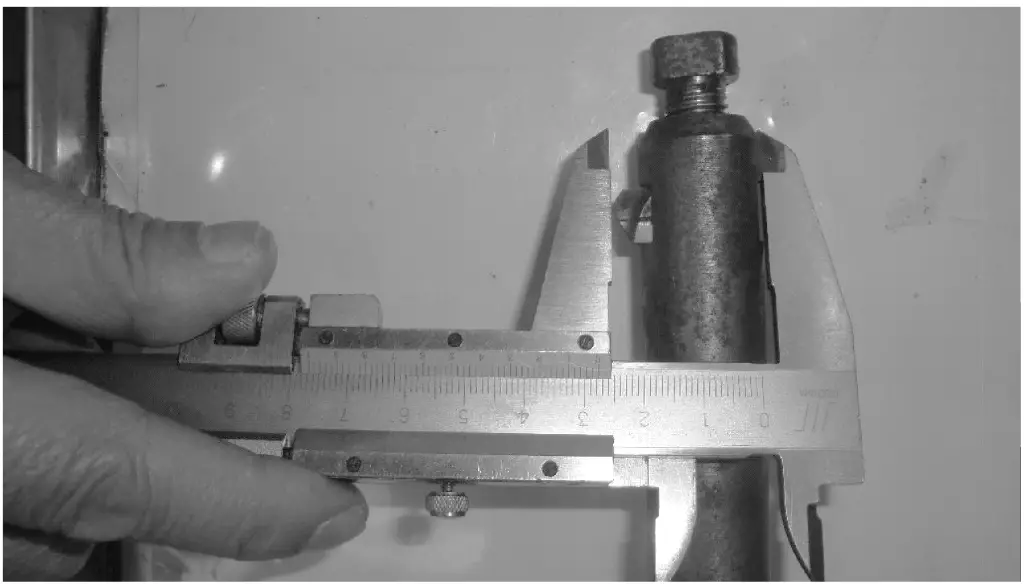
2.小穴ボーリング工具シャンク
図11aは、小径穴あけ工具シャンク本体を示す。使用時には、小径穴あけ工具(図11c)を本体の穴に挿入し、ナット(図11b)を締めて穴あけ工具を固定する。
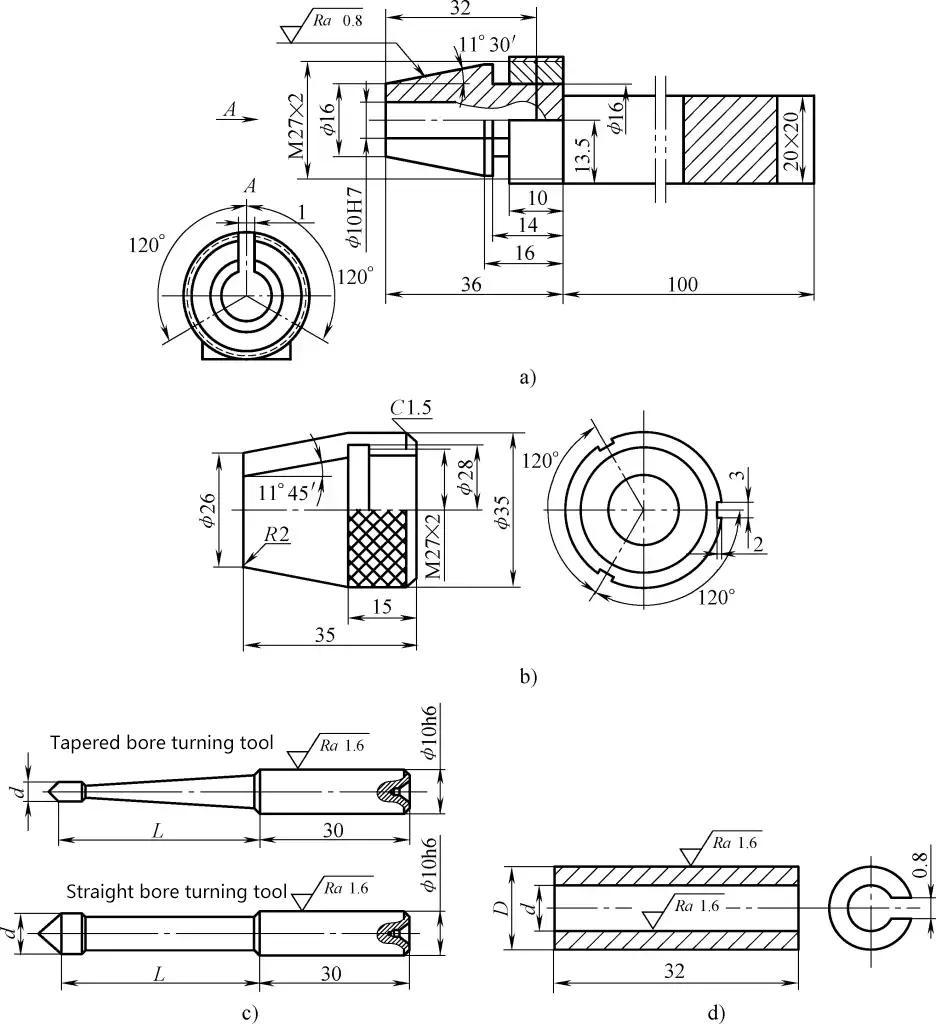
a) 中ぐり工具シャンク本体
b) ボーリングツールシャンクナット
c) 小径穴あけ工具
d) オープンエンドソケット
ボーリングツールを取り付ける際は、小さく曲げたスパナでナットの開いている溝に引っ掛けてください。ボーリングツールシャンク本体の左端は焼き入れされた弾性体なので、ボーリングツールを確実にクランプすることができます。
1本の中ぐり工具シャンクに様々な仕様の中ぐり工具を装着することができ、異なる径の小径穴の加工ニーズに対応できる。このタイプのボーリングツールシャンクは、オープンエンドソケット(図11d)と併用することで、小径のセンタードリル、ドリルビット、リーマなどを保持し、他の加工に使用することもできる。
3.スパイラル溝付きボーリング工具シャンク
使用時には、ボーリングツールシャンクのツールホールにスモールツールシャンクを挿入し、ナットを締めてスモールツールシャンクを固定します。このタイプのシャンク(図12)は、直径20~40mmの穴あけに非常に適している。切削中は切削液を多量に使用する。
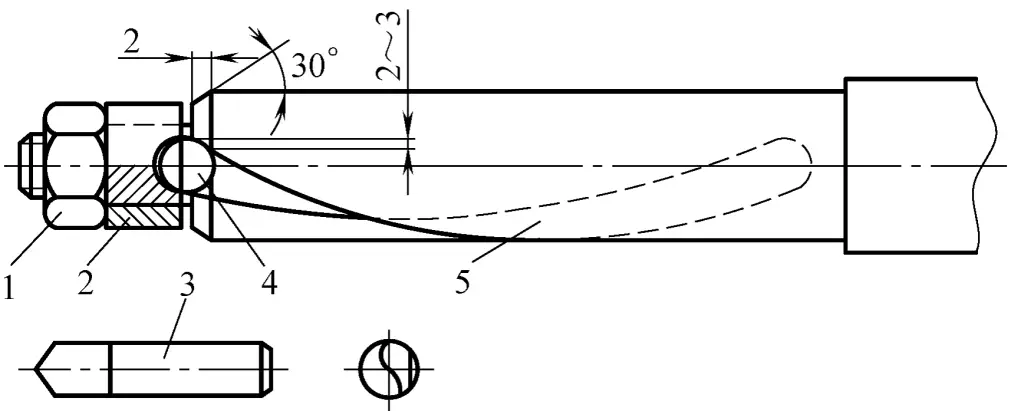
1ナット
2ツールクランプ
3-小型ツールシャンク
4ツールホール
5-ボーリング工具シャンク
スパイラル溝付きボーリングツールシャンクは、切り屑がスパイラル溝に沿って排出されるため、切り屑詰まりを防ぐことができます。振動を低減し、背面切込み深さを増加させるために、製造時に工具シャンクの直径を適切に増加させる必要があります。このボーリングツールシャンクは、貫通穴のボーリングに適しており、切削油剤を使用してください。
4.ピボット調整式ボーリングツールシャンク
(1) ツールシャンク 1
図13に示すように、ピンを支点に回転する。左のねじを締め、右のねじを緩めると中ぐり径が大きくなり、右のねじを締め、左のねじを緩めると中ぐり径が小さくなる。チャックヘッドを心押台のテーパ穴に挿入するか、チャック本体のハンドル部を円錐状にして心押台のテーパ穴に直接挿入する。
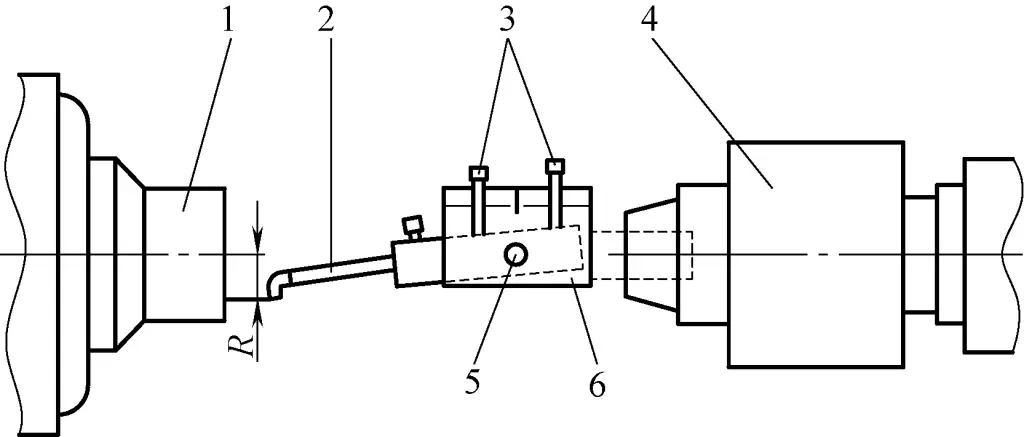
1-ワークピース
2-ボーリング工具
3スクリュー
4ピン
5-チャックボディ
6チャックヘッド
(2) ツールシャンク 2
図14に示すように、このボーリング工具のシャンクは角シャンク形状を採用している。使用時には、工具本体の角穴に挿入し、固定ねじと揺動圧ねじでクランプする。揺動圧ねじは、支点としても機能する。使用時には、調整ねじを回して、ボーリングツールシャンクをピボットプレッシャーねじを中心に適切な角度だけ回転させ、微調整を行います。
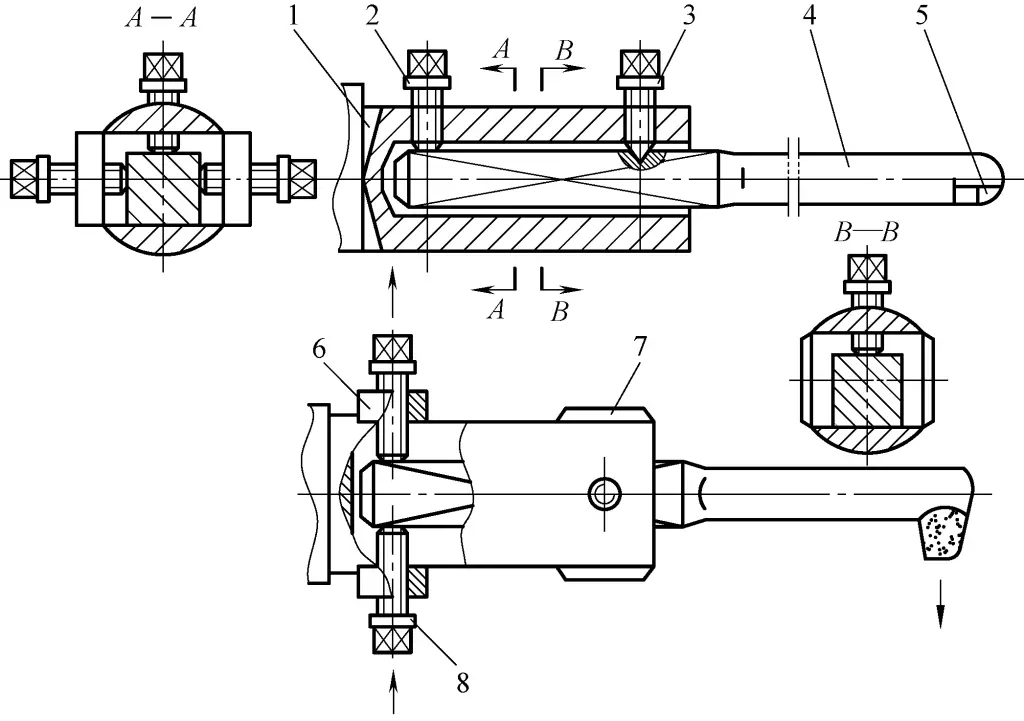
1-ツール本体
2-固定ネジ
3-ピボット圧力ねじ
4-ボーリング工具シャンク
5ツールヘッド
6角アイアン
7-接続ブロック
8-調整ネジ
このボーリング工具のシャンクは、テコの原理に基づいて設計されています。
5.回転ボーリング工具シャンク
図15に示すように、本体は旋盤主軸のフランジに連結されている。偏心スリーブの内孔は、その外周円に対して偏心量eを持っている(偏心量eは状況に応じて決定される)。穴あけ寸法を調整するには、固定ねじをゆるめて偏心スリーブを回転させます。
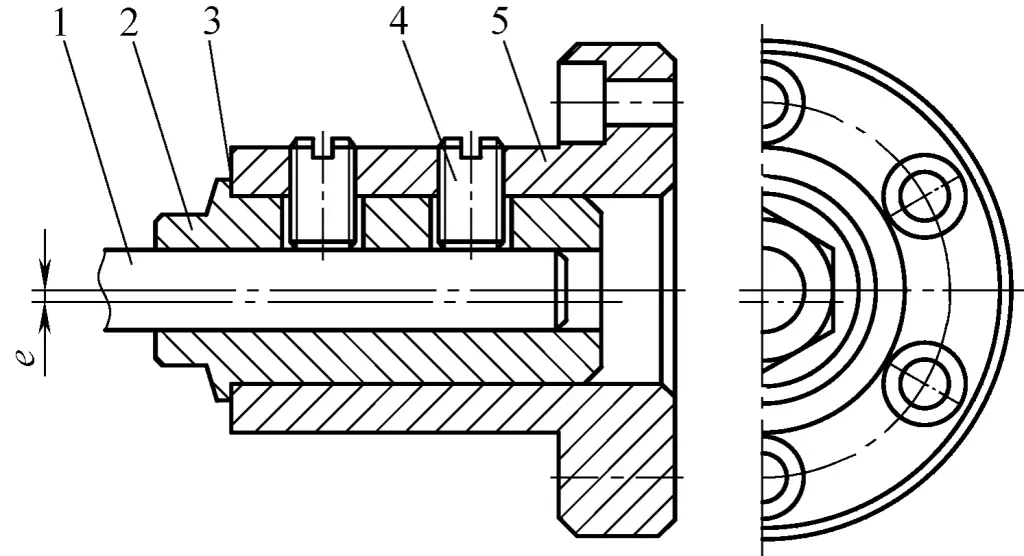
1-ツールシャンク
2-偏心スリーブ
3スケールライン
4-固定ネジ
5-本体
偏心スリーブの端面と本体の両方に目盛り線があります。調整量は目盛線から確認できます。調整後、固定ねじを締めます。このボーリングツールシャンクは、比較的小さな穴のボーリングに適しています。
6.ボーリングツールシャンク
図16に示すように、ボーリング工具シャンクの端面と工具ヘッドの底面の両方に等間隔に尖った歯があり、互いに噛み合っている。ボーリングツールシャンクの前端には、2つのツールヘッド1、2が互いに180°の角度で取り付けられている。
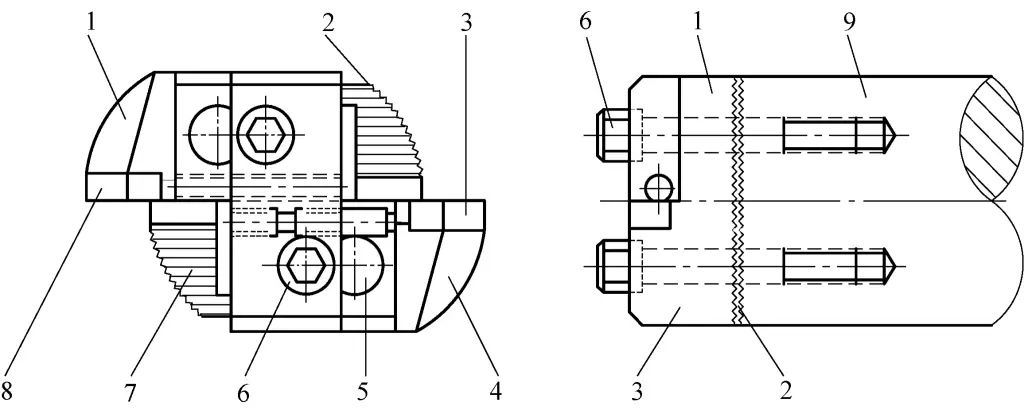
1-ツールヘッド 1
2本歯
3-ツール・インサート 2
4-ツールヘッド 2
5本歯溝
6スクリュー
7-ボーリング工具
8ツールインサート1
9-ボーリング工具シャンク
ツールインサートは、長い溝を持つツールヘッドに溶接されている。ツールインサートの延長距離を調整するには、ネジを緩め、ツールヘッドが歯溝に沿って半径方向に移動できるようにします。調整後はネジを締める。尖った歯は、損傷や変形を防ぐため、一定の硬度を持つように硬化させる必要がある。
7.傾斜変位微調整ボーリング工具シャンク
(1) ツールシャンク 1
図17に示すように、ボーリングツールシャンク2は主軸1のテーパ孔に取り付けられ、ツールシャンク8は内筒5のねじ孔に取り付けられ、外筒3はねじを介してボーリングツールシャンク2に連結されている。内筒5と外筒3は摺動嵌合している。
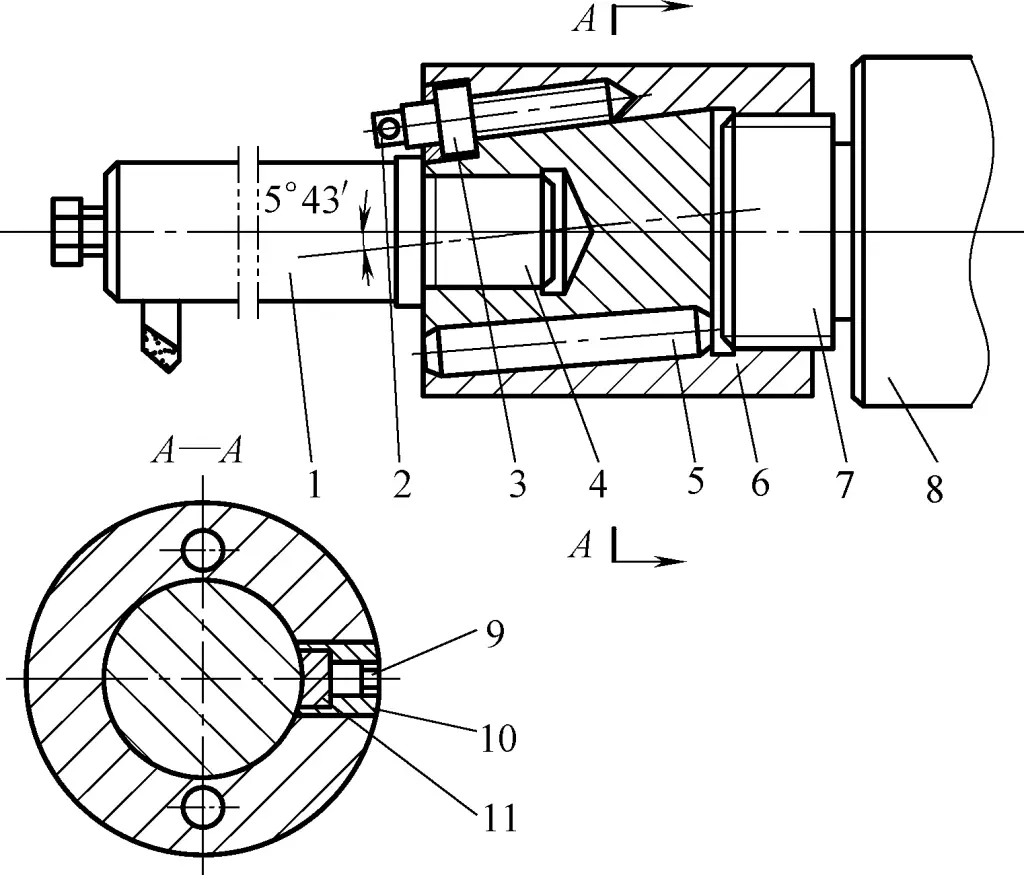
1スピンドル
2-ボーリング工具シャンク
3-アウタースリーブ
4-円筒ピン
5インナーシリンダー
6-ゼロリング
7-微調整用スクリューロッド
8-ツールシャンク
9-六角穴付きネジ
10スレッドスリーブ
11-真鍮固定ワッシャ
外筒3の内孔の中心線は、ボーリング工具シャンク2の軸線に対して5°43′の角度で傾斜している。ボーリング工具を調整するには、まず六角穴付きねじ9を緩め、微調整ねじロッド7を回して外筒3内の内筒5を傾斜した中心線に沿って半径方向に移動させる。調整後、六角穴付きねじ9を締める。
微調整ねじロッド7の肩部には、等間隔に円形の目盛りが付けられています。そのピッチが1.5mmのとき、1回転するとシリンダ5の半径方向の移動量aは次のようになる:15mm×sin5°43’=1.5mm×0.0996=0.1494mm≈0.15mm.微調整ねじロッド7に30目盛りがある場合、1目盛りの半径方向移動量はa/30=0.1494mm/30≒0.005mmとなります。
(2) ツールシャンク 2
図18に示すように、このボーリング工具シャンクの斜め穴は、工具シャンク軸に対して60°の角度を形成している。斜め穴には二重キー溝があり、工具クランプスクリューロッドが収納されている。二重凸キーは斜め穴の二重キー溝内を摺動可能であり、円筒部は斜め穴と摺動嵌合する。円形鉄ワッシャーは、ボーリング工具シャンクの斜め穴に固定されています。
割り出しナットは、工具ヘッドの延長距離を調整するために使用します。ツールクランプスクリューロッドを必要なサイズに調整した後、スクリューと円形鉄ワッシャを一緒にロックします。ワッシャー、シールガスケット、弾性リングは、防塵と制振のために使用されます。
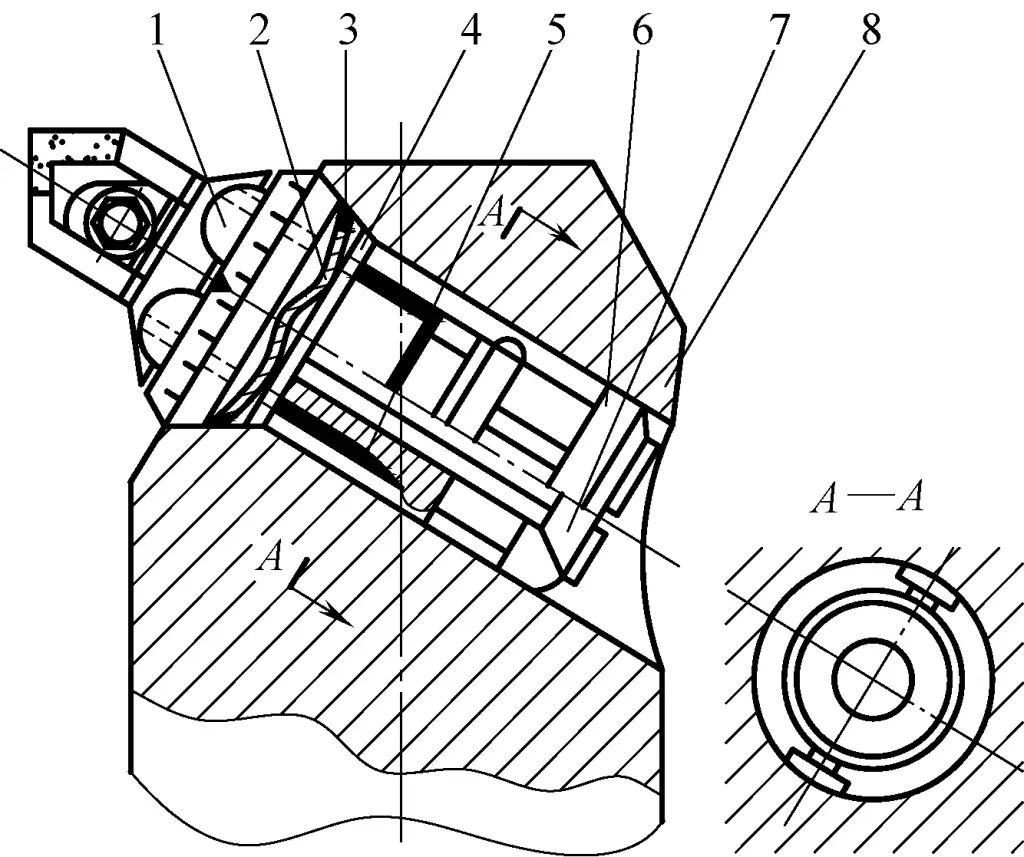
1-インデックス・ナット
2-弾性リング
3-シールリング
4ワッシャー
5-ツールクランプスクリューロッド
6-円形鉄ワッシャー
7-スクリュー
8-ボーリング工具シャンク
割り出しナットには目盛りがあります。割り出しナットが1回転すると、工具クランプねじロッドが1ピッチ移動します。例えば、ねじ山がM18×1.5の場合、ボーリング工具のシャンク軸に対して60°傾いているので、工具先端の半径方向の移動量は1.5mm×sin60°=1.299~1.33mm.割り出しナットの目盛りが65目盛りとすると、割り出しナットを1目盛分回転させると、工具先端の半径方向の変位量は0.02mmとなります。
8.垂直ツールヘッドフィード ボーリングツールシャンクの微調整
(1) ツールシャンク 1
図19に示すように、このボーリングツールシャンクのツールヘッドエクステンションの調整方向は、ツールシャンク軸に対して垂直である。図において、本体スリーブはボーリング工具シャンクに取り付けられ、長いねじで固定されている。ツールヘッドはツールクランプスリーブの穴に取り付けられ、小ねじで締め付けられます。
ねじ棒の小さい端は用具の締め金で止める袖のねじ穴にねじ込まれ、大きい端は本体の袖のねじ穴にねじ込まれる。ねじ棒の大端と小端のピッチは異なる。調整するには、回転させる
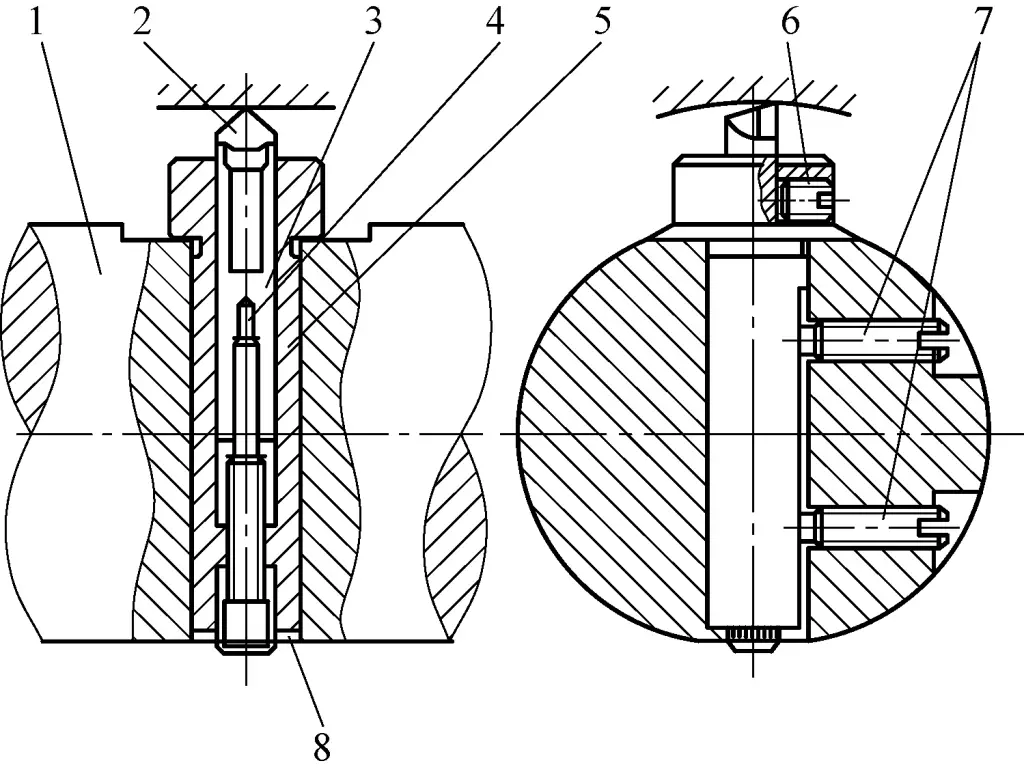
1 - ボーリング・バー
2 - ツールヘッド
3 - ツールホルダースリーブ
4 - ネジ付きロッド
5 - 本体スリーブ
6 - 小ネジ
7 - ロングスクリュー
8 - グラデーション・ライン
調整するには、まずツールヘッドを固定している小さなネジを緩めます。ネジ付きロッドヘッドに目盛りが付いているため、ツールヘッドの動きを正確にコントロールできます。
(2) ボーリング・バー 2
図20に示すように、バー上のボーリング工具ヘッドは円筒状である。微調整ねじ6を回すと、ボーリング工具ヘッド4がボーリングバーに沿って半径方向に移動します。六角穴付きねじ5を締めたり緩めたりすると、スライディングブロック2および3が移動し、ボーリング工具ヘッド4をクランプまたは解放します。
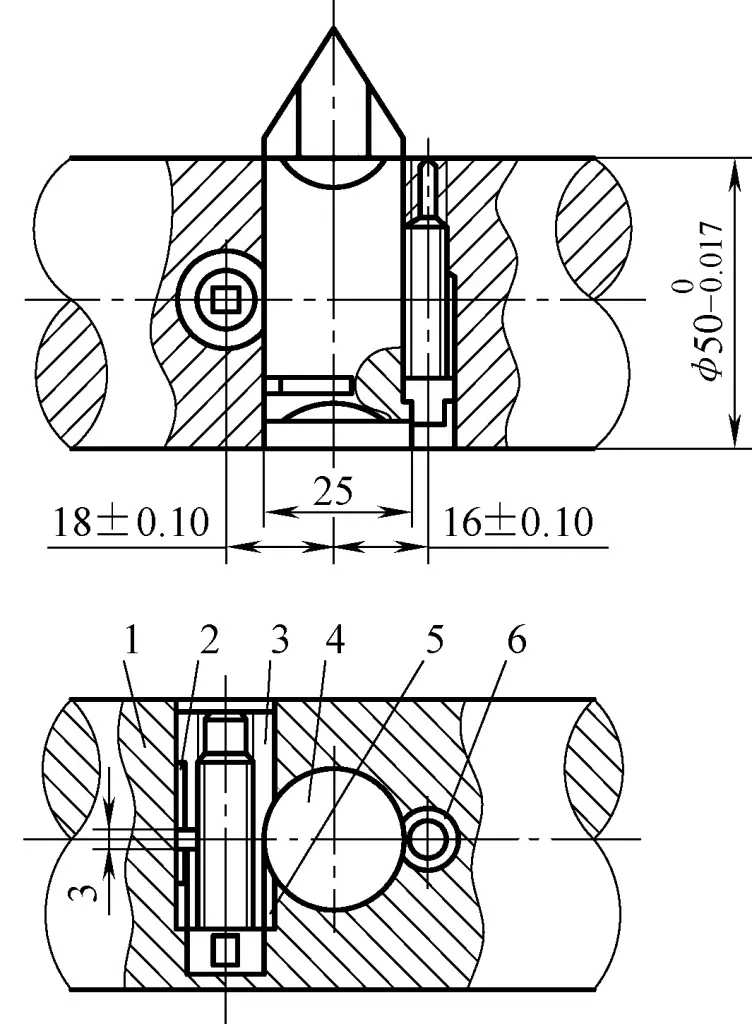
1-ボーリングバー
2、3-スライダー
4-カッティングヘッド
5角ソケットネジ
6-微調整ネジ
9.双方向微調整ボーリングバー
図21に示すように、ボーリングバーの先端に横方向に角穴を加工する。両端から高速度鋼製の短いボーリング工具を挿入する。短尺ボーリング工具の内端はV字形に研削され、締付けねじで固定される。短尺ボーリング工具の突き出し長さを調整する場合、45°の角度で調整ネジを回して円筒ピンを前方に押し出し、短尺ボーリング工具を移動させます。
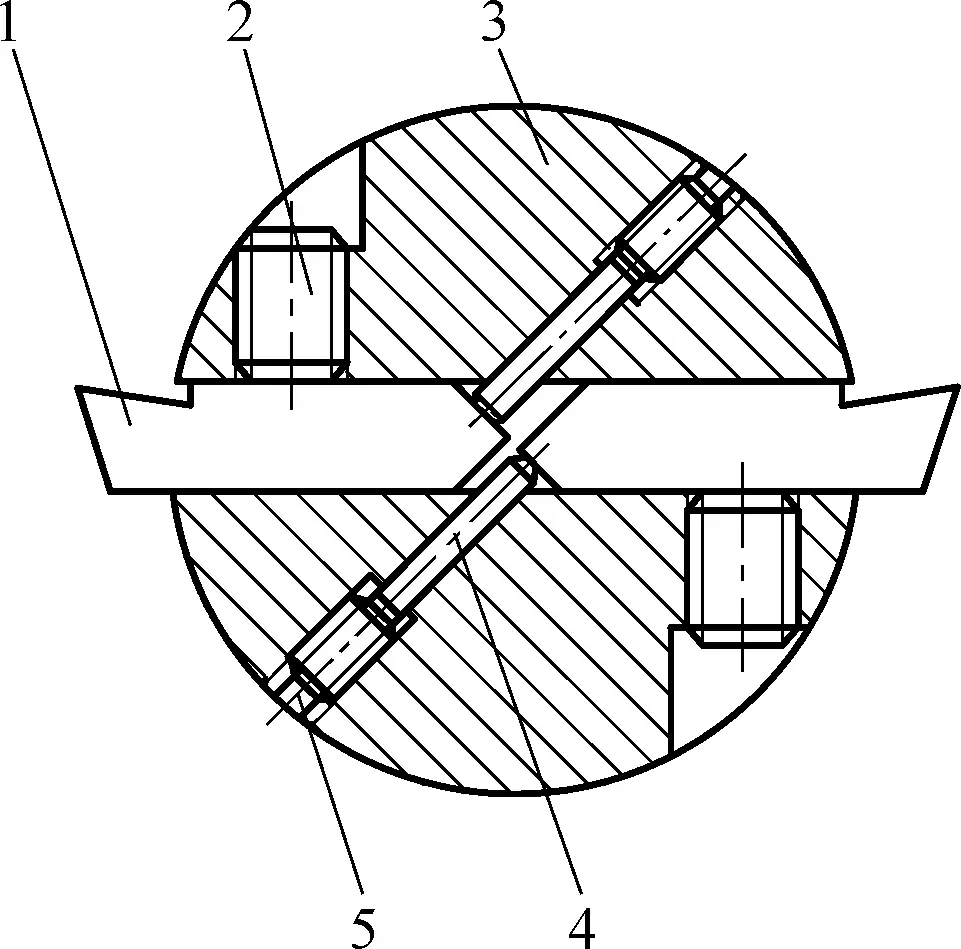
1-ボーリング工具
2-固定ネジ
3-ボーリングバー
4-円筒ピン
5-調整ネジ
中ぐり加工では、2本の短い中ぐり工具がそれぞれ背面切削深さの半分を負担し、あるいは一方が荒ぐり工具として、他方が細ぐり工具として機能する。
10.ボーリングヘッドの微調整
(1) ボーリング・バー 1
(図22)使用時には、テーパーシャンクが主軸のテーパー穴に嵌合します。テーパ穴に挿入後、旋盤主軸後端のドローバーでボーリングヘッドを引っ張り、剛性を高めて抜けを防止します。テーパーシャンクの下にアリ溝があり、アリ溝ブロックがスライドする。リードスクリューを回転させると、アリ溝ブロックがアリ溝に沿って移動し、カッティングヘッドの回転径を調整することができます。
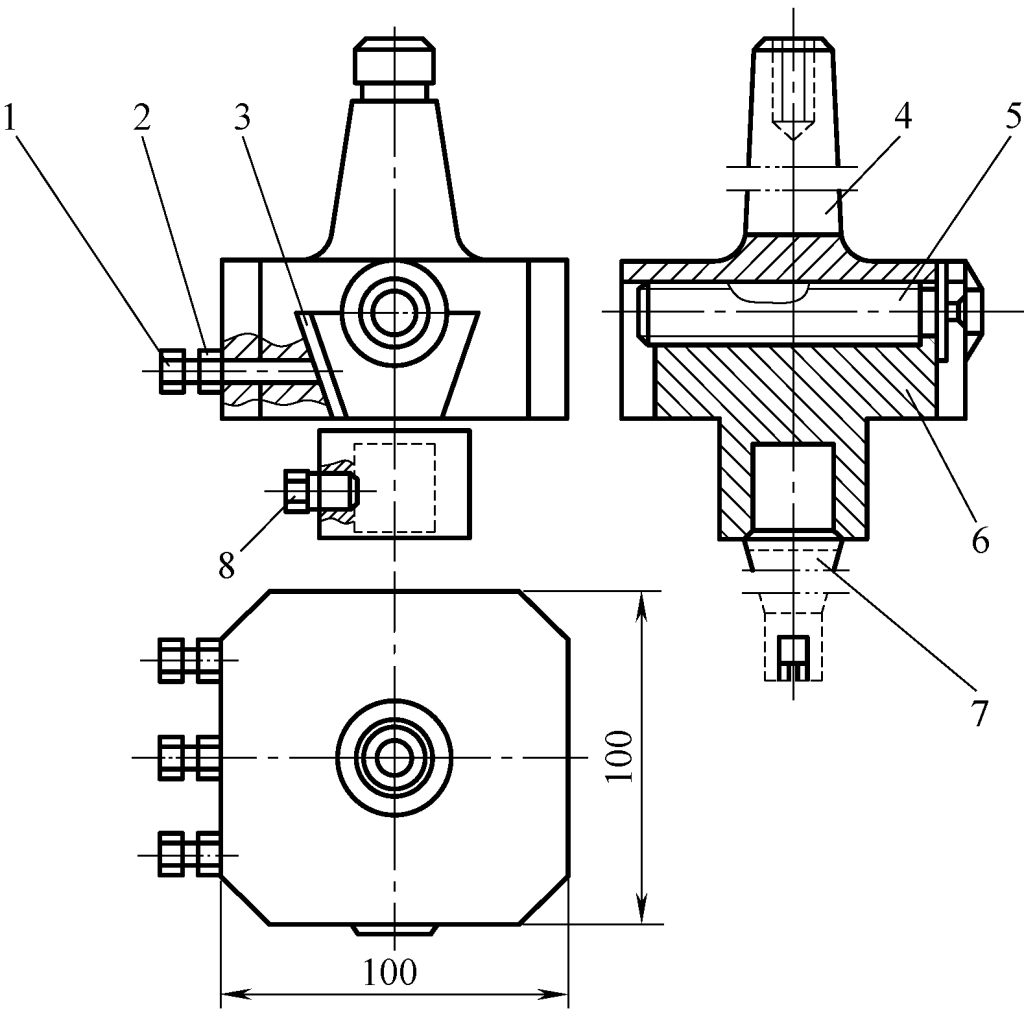
1-ロックネジ
2-ロックナット
3-調整プレート
4-本体
5リードスクリュー
6-ダブテールブロック
7-ボーリングバー
8-固定ネジ
リードスクリューの一端に目盛ダイヤルが付いており、バックカットの深さを調節できる。ダイヤルには目盛りがあり、100分割されている。リードスクリューのネジ山はM20×2で、1分割するごとに0.02mmずつ背面切削深さが増えます。ボーリングバーは固定ネジで固定されています。寸法を調整する場合は、まず固定ネジを緩め、次にリードネジを回します。調整後、ロックボルトとロックナットを締めます。
このボーリングヘッドを製造する際には、アリ溝ブロックと本体の内ねじが、リードスクリューとの締まりばめを保証するために、一緒に加工されていることを確認してください。
微調整可能なボーリングバー構造は、大口径の穴あけに適しています。
(2) ボーリング・バー 2
(図23)リードスクリューを回すと、角ナットがツールホルダー上のアリ溝ブロックをアリ溝溝に沿って半径方向に移動させ、ボーリングバーの回転直径を調整します。調整後、ロッキング・スクリューのナットを締めます。
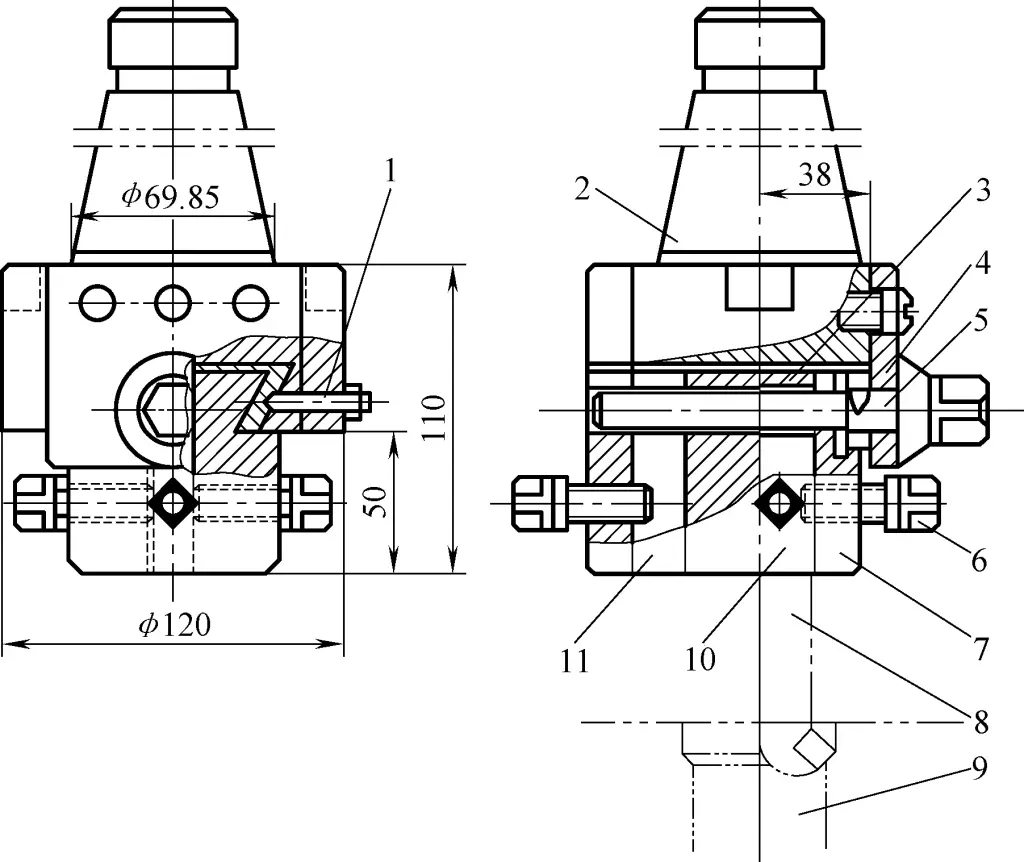
1-ロックネジ、ナット
2テーパーシャンク
3-角ナット
4ポジションプレート
5リードスクリュー
6スクリュー
7-ツールホルダー
8ボーリングバー
9-ワークピース
10-第一工具取り付け穴
11-工具取り付け穴
ツールホルダーには、ボーリングバーのテーパーシャンクの中心からの距離が異なる2つの工具取付穴が開いています。大きな穴をあける場合は、2つ目の取り付け穴に、小さな穴をあける場合は、1つ目の取り付け穴に、ボーリングバーを取り付けます。各取付穴の側面には、ボーリング工具を固定するためのネジが1本(2本でも可)あります。
リードスクリューは長方形でピッチは3mm。テーパーダイアルには100本の等間隔の目盛線があります。各マークを回転させると、ツールホルダーが0.03mm移動します。
11.大穴ボーリングバー
大径の穴あけには、図24に示す大穴用ボーリングバー(コンビネーション・ボーリングバーともいう)を使用することができる。旋盤の小スライドを外し、大穴用ボーリングバー本体を取り付ける。ボーリングバー本体をクランプし、ボーリングヘッドをボーリングバー左端の角穴に挿入し、固定ねじを締め、スラストロッドでボーリングヘッドを固定します。六角穴付ネジを緩めると、ボーリングバーの突き出し長さを変えることができます。
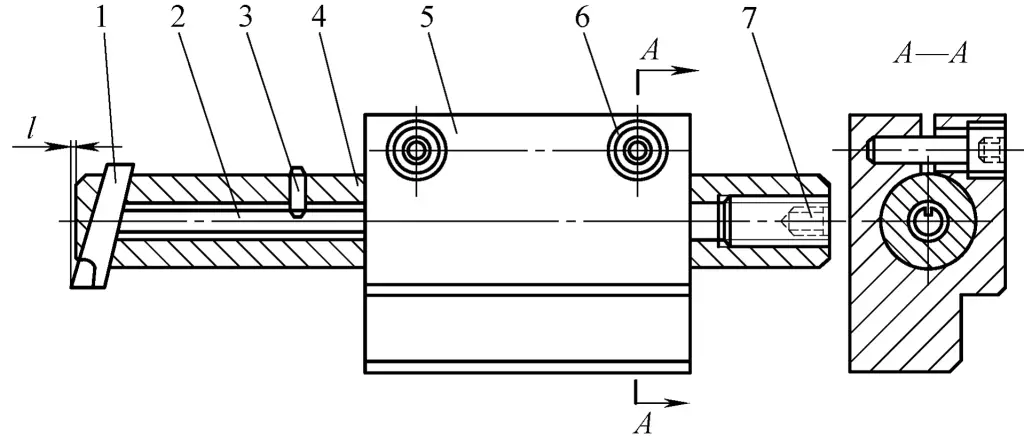
1-ボーリングヘッド
2-スラストロッド
3-位置決めピン
4-ボーリングバー
5-本体
6角ソケットネジ
7-固定ネジ
位置決めピンがボーリングバーの中に出ている長さは、スラストロッドがボーリングバーの中で自由に動くようにする。ボーリングバーの突き出し長さを調整した後、六角穴付きネジを締めます。
大穴ボーリングバー本体は鋳鉄製で、振動減衰性に優れている。
III.一般的な穴型ワークの旋削加工
1.穴加工ワークの基本的な旋削方法
図25は、旋盤での中ぐり加工に用いられる最も基本的な方法を示している。ワークが大きすぎたり長すぎたりして、旋盤に都合よく取り付けられない場合は、複合スライドにワークを取り付けて中ぐりを行う方法がよく用いられる。
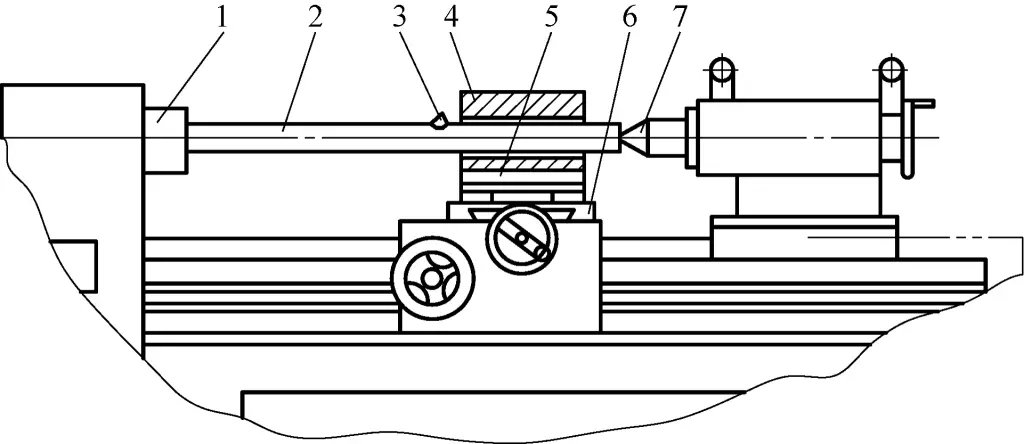
1スピンドル
2-ボーリングバー
3-カッティングヘッド
4ワーク
5-フィクスチャー
6-コンパウンド・スライド
7-テールストック・センター
複合スライドからスモールスライドとツールポストを取り外します。フィクスチャー5はT溝を通して複合スライドに固定される。ボーリングバーは主軸と心押台のセンター間に取り付けられ、ワークが固定されたままボーリングバーが回転して加工を行うことができます。
ボーリング位置を決定するために、加工物の両端に加工線を引くことができる。カッティングヘッド3には鋼線針が固定されています。スピンドルとボーリングバーを回転させ、ニードル先端をワーク両端の加工ラインマークに合わせ、位置決めを行う。ワークの横位置は複合スライドで調整し、高さはシムやパッキンプレートで調整する。
このボーリング方法では、ボーリングバー2の両端に高精度のセンタ穴が必要であり、固定センタを使用する(回転センタでは回転誤差が大きくなる)。
2.精密ボーリングにおける背面切削深さの増加方法
精密中ぐりにおいて、背面切削深さを0.05~0.1mmなど微小にしたい場合、コンパウンドスライドハンドルの目盛ではコントロールが難しい。
この場合、先に紹介したダイヤルインジケータによる制御方法と、小スライド角度を回転させてラジアル送りを制御する方法の他に、図26bに示す垂直工具取り付け方法を使用することができる。これは、ボーリングヘッドを(図26aのように水平ではなく)ワークに対して垂直に位置決めし、ボーリング工具をワークの上部で切削できるようにするものである。コンパウンドスライドは、加工される穴に沿って接線方向に移動します。
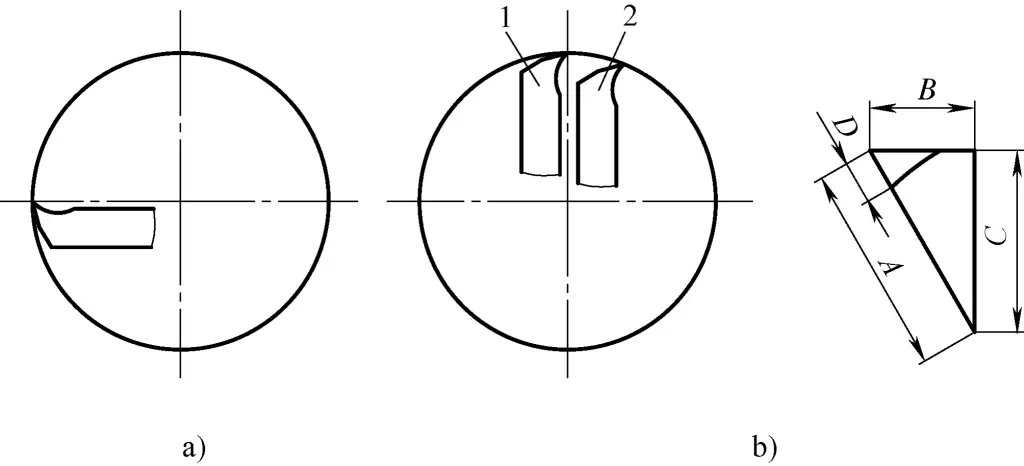
a) 通常の取り付け方法
b) 垂直取り付け方式
1-加工前の工具位置
2-加工後の工具位置
図26bにおいて、Dは穴の加工代であり、Cは加工代Dを達成するために必要な刃物台の移動量である:
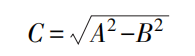
3.ボーリング中の振動を防ぐ
ボーリング中、ボーリング工具は半密閉状態で動作し、ボーリングバーの突出部は比較的長いため、振動が発生しやすい。
ワークの不適切なクランプ、フィクスチャーの剛性不足、スピンドルベアリングの激しい摩耗、ガイドレールの摩耗、スライドクリアランス調整の緩み、刃先のくすみ、ボーリングバーの過度の突き出し(図27)、ボーリングバーの剛性不足、誤った切削パラメータ、不適切な加工方法など、振動の原因は複数あります。振動が検出された場合は、その原因を特定し、適切に対処する必要があります。
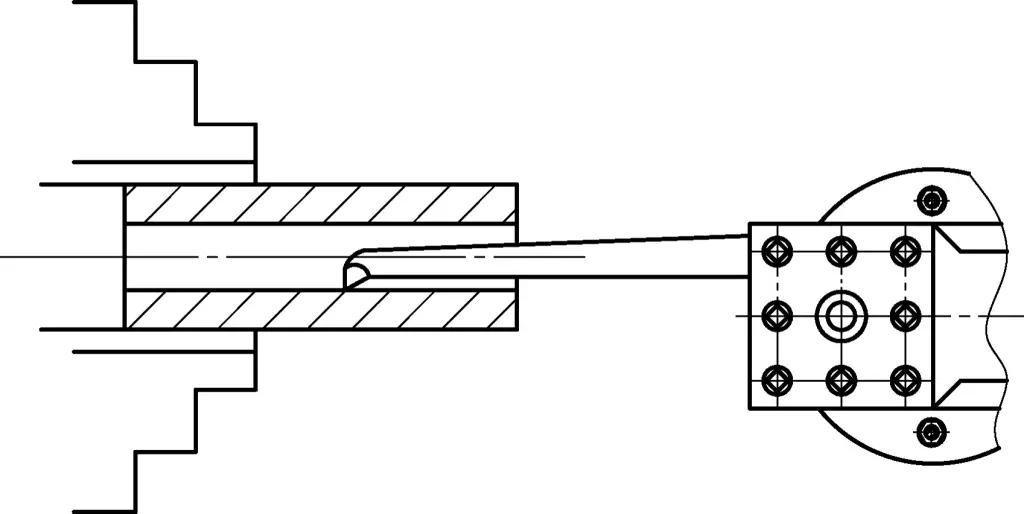
ボーリング中の振動を防止・解決するためには、技術システムの観点から以下のような対策が考えられる:
(1)ボーリングバーの剛性を高める内部支持方式
ボーリングバーの剛性が不足すると、穴あけ時に振動が発生するだけでなく、「工具のたわみ」現象が発生し、穴が内径に向かって細くなるテーパー穴になってしまいます。旋盤の精度に問題がなければ、ボーリングバーの剛性を高める方法を採用する。
ボーリング・バーの剛性を高める方法としては、バーの幅や厚みを増すことが挙げられるが、この場合、バーがかさばり、問題を完全に解決できない可能性がある。また、補助的なサポートを使用する方法もある。以下の方法は、構造上のバリエーションはあるが、原理は同じである。
図28に示すように、ボーリングバーにM10のねじ穴を加工し、適当な長さの丸頭ボルトをねじ込む。中ぐり加工では、まず試し切りをして20~30mmの長さの下穴をあけてから機械を止め、中ぐり棒の丸頭ボルトを丸頭が下穴の壁面に当たるように調整する。丸頭ボルトをロックナット(図示せず)で固定し、ボーリングを進める。
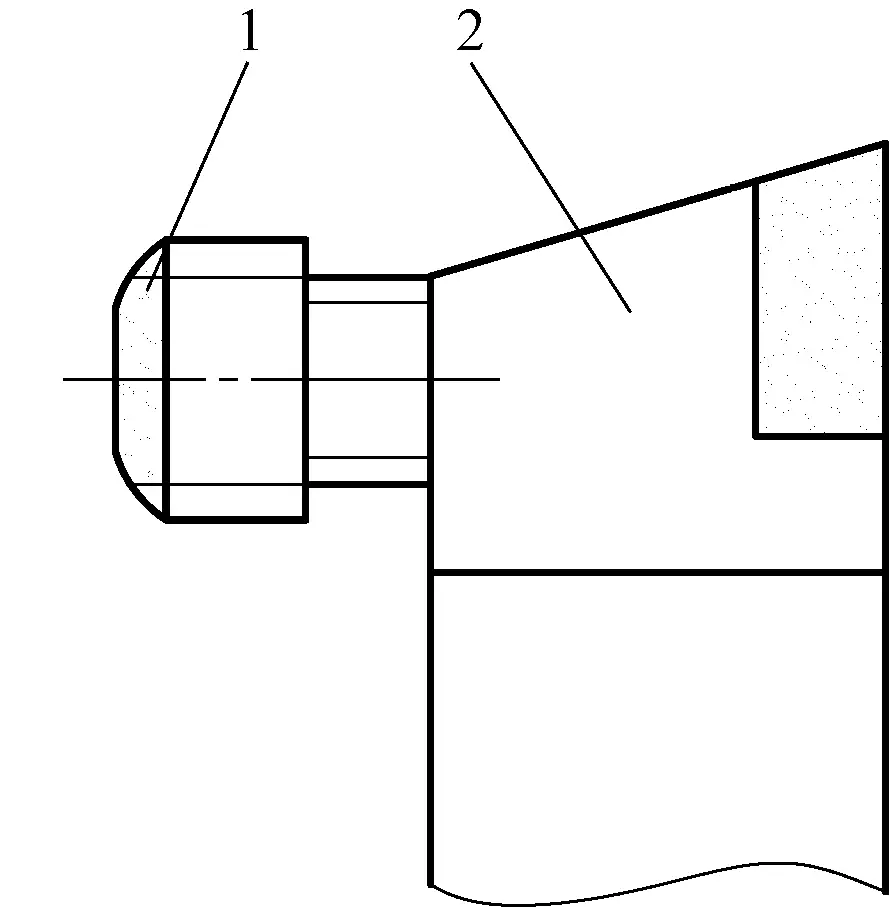
1-丸頭ボルト
2-ボーリングバー
図29に示すように、ボーリング工具先端の後面に、管状ねじコネクターを180°で取り付ける。管状ねじコネクタには鋼球が付いている。ボーリング中、鋼球は自由に回転し、加工面との接触を維持することができ、ボーリングバーの剛性を高めることができる。
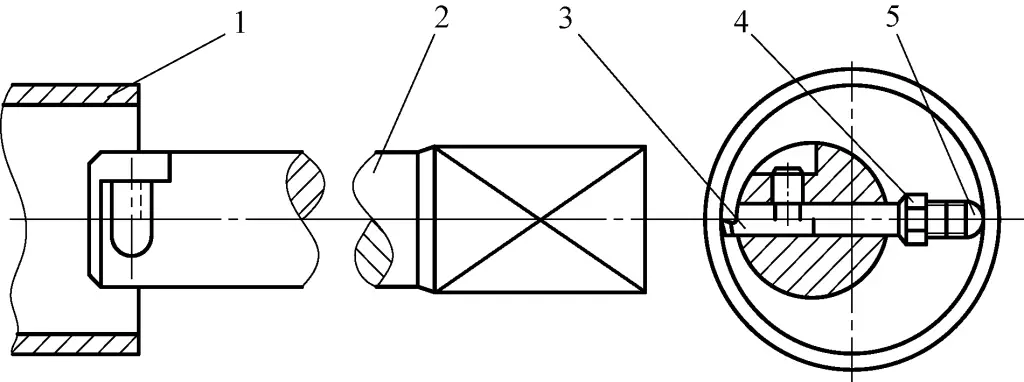
1-ワークピース
2-ボーリングバー
3-カッティングヘッド
4チューブネジコネクター
5-スチールボール
直径と長さの大きな穴の場合、ボーリング中に図30に示す方法を使用することができます。調整ねじは、1本をボーリング工具先端の180°後方に、もう1本を先端に垂直に取り付けます。一方のねじ頭はボーリング工具先端と同じ回転面上にあり、もう一方はやや後方にある。
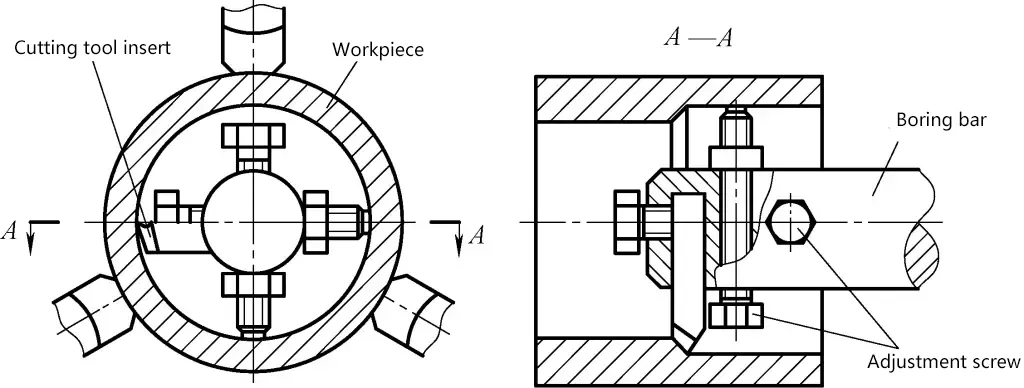
その都度、ネジ頭の突き出し距離を調整し、ロックナットを締める。ボーリング中、ねじ頭は加工面に接触し、ボーリング・バーを支える。
補助サポートを使用してボーリングバーの剛性を高める方法は、荒ボーリングや中仕上げボーリングに適しています。
(2) ワーク剛性を高める外部支持方式
長穴タイプのワークを旋削する場合、図31に示すように、振れ止めを使用してワークを支え、剛性を高めることができます。
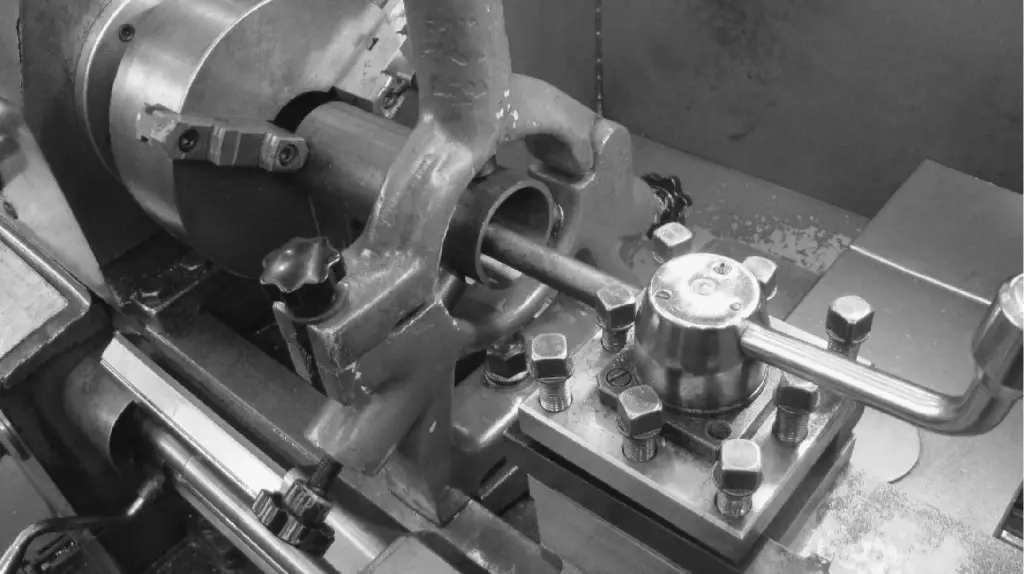
小径の穴型ワークの一括加工には、図32に示すような補助サポートの方法がある。中ぐり加工時には、補助サポートを旋盤のベッドに固定し(振れ止めを固定する要領)、サポートリングの溝をワークの端面と外径に接触させる(サポートリングの穴径は中ぐり径より大きくする)。こうすることで、ワークが回転すると、中ぐり作業中にサポートリングも回転する。
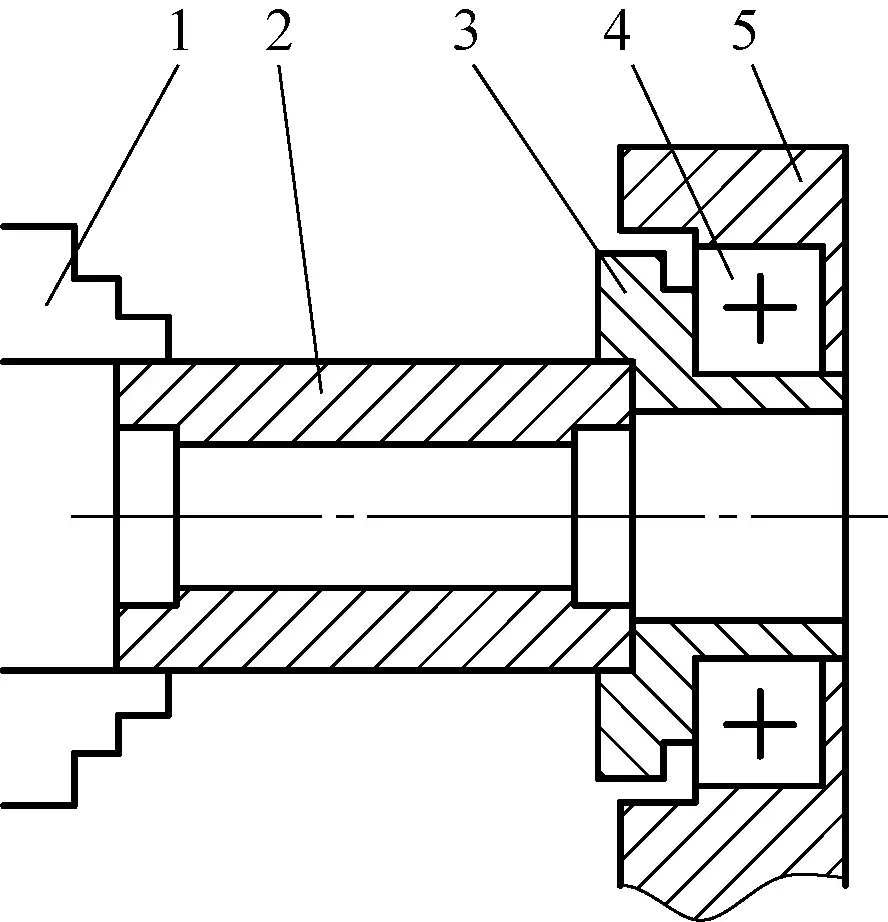
1-チャック・ジョー
2ワーク
3-サポートリング
4-転がり軸受
5-補助サポート
(3) ゴム素材の制振方法
図33aは、厚さ5mmのゴムシート(またはゴムバンド)をワークピースの外周に巻き付け、バネで締め付けたもので、良好な振動減衰効果を得ることができる。薄肉管状ワークピースの直径と幅によっては、図33bに示すように、管状ゴムバンドをワークピースの外周に縫い付けてはめ込み、その後に精密穴加工を行うこともできる。
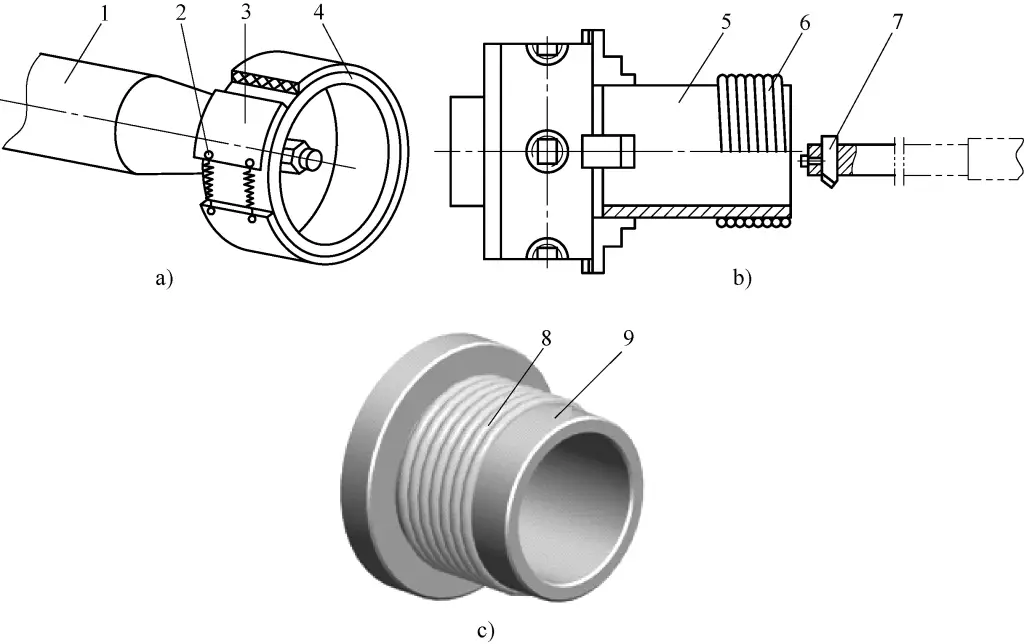
a) 制振ゴムシートの使用
b) 振動減衰のための弾性バンドの使用
c) 制振ゴムチューブの使用
1マンドレル
2-スプリング
3-ラバーシート
4、5-ワーク
6-ゴムバンド
7-ボーリング工具
8-ゴムチューブ
9-管状ワーク
図33cは、ワークの外周にゴムチューブを巻いていますが、これも一定の効果があります。ゴム材料はすべてエラストマーであるため、減衰型制振装置に相当し、減衰を利用してエネルギーを散逸させ、共振振幅を減少させ、振動の除去または低減を実現する。
(4)レリーフ角度0°方式
砥石上でボーリング工具の角度を研削した後、図34に示すように、工具先端の主切刃付近2~3mmに0°の角度を研削する。その目的は、切削加工中、工具シャンクの弾性変形により、工具先端に小さな逃げ角が形成され、切削に有利になり、振動が減少するためである。
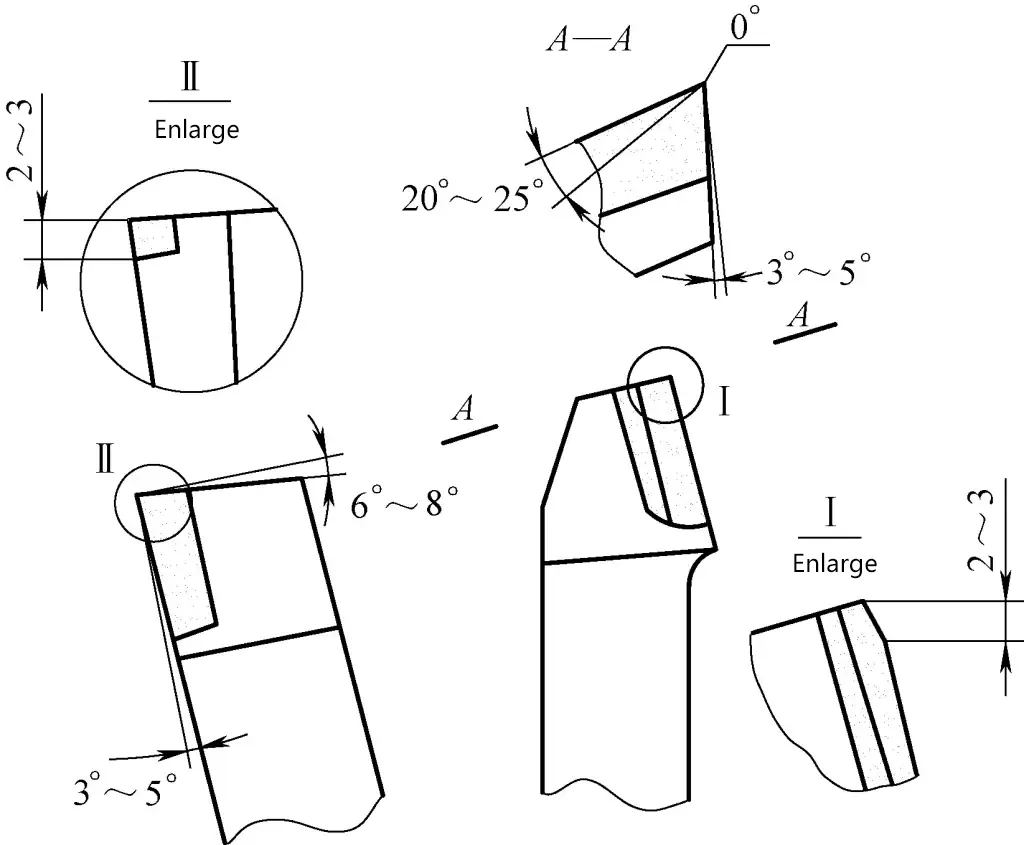