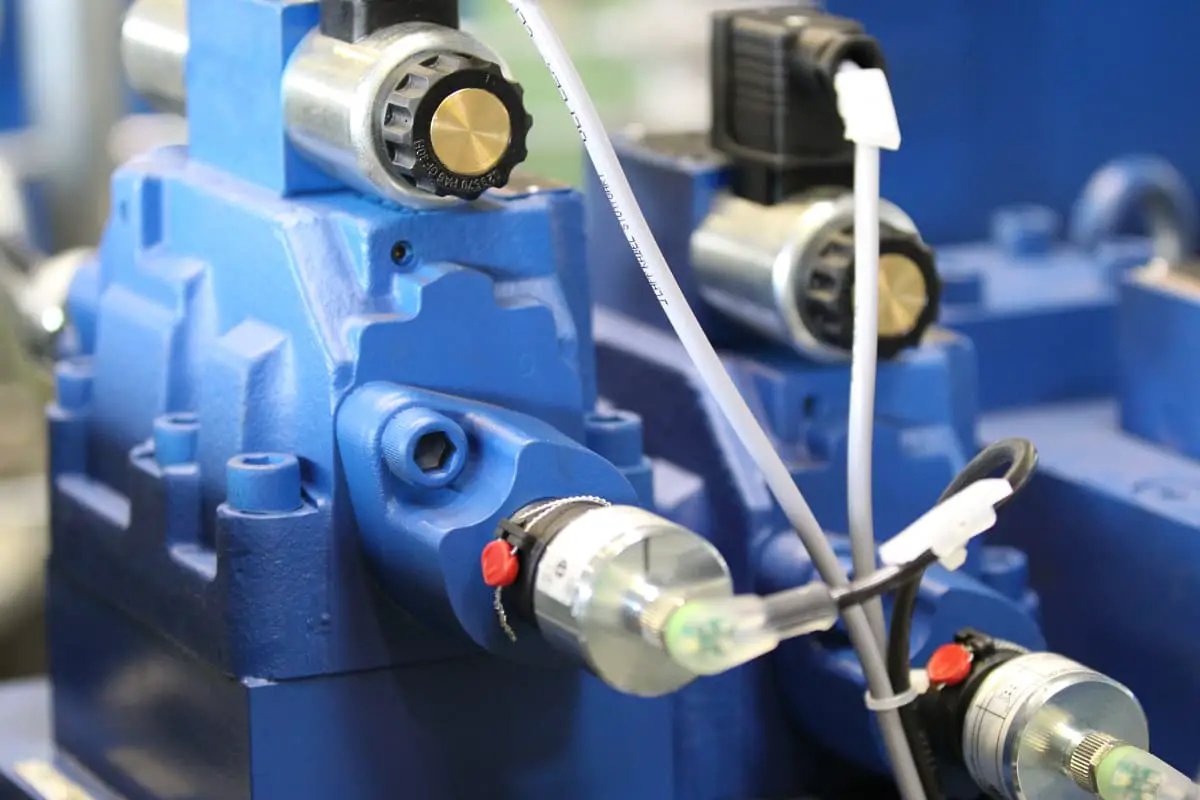
I.空気圧システムの設置
1.パイプラインの設置
- 設置する前に、パイプラインの内壁が滑らかかどうかをチェックし、錆を除去してきれいにする。
- パイプラインサポートは堅固でなければならず、運転中に振動してはならない。
- すべてのジョイントを締め、パイプラインから空気が漏れないようにする。
- パイプラインの溶接は、指定された標準条件を満たす必要がある。
- ホースを取り付ける際は、その長さに一定の余裕を持たせること。曲げる際は、端の継ぎ手から曲げ始めないこと。直線部分を取り付ける際は、端の継ぎ手とホースの間を伸ばさないこと。ホースは、熱源からできるだけ離して取り付けるか、遮熱板を取り付けること。パイプラインシステムのどの部分も取り外し可能であること、 曲げ半径パイプラインの設置、間隔、勾配は、関連法規に適合していなければならない。
2.コンポーネントの取り付け
- 取り付け前に、構成部品を清掃し、必要に応じてシーリングテストを実施してください。
- 各種バルブボディの矢印やマーキングの方向は、エアフローの方向と一致していなければならない。
- 制御回路の必要性に応じて論理部品をグループ化してベースプレートに設置し、空気回路はベースプレート上に導出してホースで接続する。
- 特にV字型のシーリングリングは抵抗が大きいため、適切な締め付けが必要です。
- 移動するシリンダーの中心線と 荷重 同心でなければ、横方向の力がかかり、シール部品の摩耗を早め、ピストンロッドを曲げることになる。
- 各種自動制御機器、自動コントローラー、圧力リレーなどは、設置前に校正しておく必要がある。
II.システムの洗浄と圧力テスト
パイプラインシステム設置後、圧力0.6MPaのドライエアでシステム内の不純物を全て吹き飛ばす。白い布で確認し、5分以内に不純物がなければ合格です。ブロー後、バルブコア、フィルターエレメント、ピストン等の部品を分解洗浄する。
システムの密閉性が基準を満たしているかどうかを確認するには、通常、定格圧力の1.2~1.5倍の圧力に一定時間(例えば2時間)保ち、気密試験を行う。環境温度変化による誤差を除き、圧力変化は技術文書に規定された値を超えてはならない。試験中、安全弁を試験圧力に調整する。
圧力試験中は、段階的な試験方法を採用し、常に安全性に注意を払うことが最善です。システムに異常が発見された場合は、直ちに試験を中止し、原因を突き止め、故障を除去してから試験を続行する。
III.システム・デバッグ
1.デバッグ前の準備
- システムの原理、構造、性能、操作方法を十分に理解するために、マニュアルおよびその他の関連技術資料に精通してください。
- 装置上の調整が必要な部品の実際の位置、操作方法、調整ノブの向きを理解する。
- デバッグツール、計測器を準備し、マニュアルに従ってテストパイプラインを接続する。
2.無負荷試運転
無負荷試運転は2時間以上とする。圧力、流量、温度の変化に注意すること。異常現象が認められた場合は、直ちに機械を停止して点検し、異常がなくなってから運転を続行してください。
3.負荷試験操作
負荷試運転は段階的に行い、運転時間は2時間以上とする。摩擦部分の温度上昇に注意し、関連データを別途測定し、試運転記録に記録すること。
IV.空気圧システムの使用とメンテナンス
1.使用上の注意
- 運転の前後に、システム内の凝縮水を抜き、すべての調整ノブが正しい位置にあるか確認してから運転してください。トラベルバルブ、トラベルスイッチ、ストッパーの位置が正しく固定されていることを確認してください。ガイドレールやピストンロッドなどの露出部品の合わせ面を拭いてください。
- 圧縮空気の清浄度に常に注意してください。水分離器のフィルターエレメントは定期的に清掃し、オイルミスト装置には定期的にオイルを加えてください。
- 装置を長期間使用しない場合は、バネの故障が部品の性能に影響するのを防ぐため、すべてのノブを緩めてください。
- 誤った調整による事故を防ぐため、各部品の制御機構の作動特性を熟知してください。各部品の調整ノブの回転方向と圧力・流量の変化の関係に注意してください。
2.圧縮空気の汚染と防止
圧縮空気の品質は、空気圧システムの性能に大きく影響します。汚染されると、パイプラインや部品の腐食、シールの変形、ノズルの閉塞を引き起こし、システムが正常に機能しなくなります。圧縮空気の主な汚染源は、水分、油分、粉塵です。
(1) 水分
エアコンプレッサーは水分を含んだ空気を吸入する。圧縮後は圧力が上昇し、再び冷却されると凝縮水が析出し、圧縮空気に浸入して配管や部品の腐食を引き起こし、性能に影響を与える。
凝縮水が圧縮空気に浸入するのを防ぐ方法には、以下のようなものがある:
- システムのドレンバルブに溜まった凝縮水を適時に排出する。
- 自動排水口と乾燥機が正常に機能しているか定期的にチェックする。
- 水分離器と自動ドレンの内部部品を定期的に清掃する。
(2) オイル
熱により劣化した使用済み潤滑油のこと。エアコンプレッサで使用された潤滑油の一部は、圧縮空気とミスト状に混ざり合い、加熱されることで気化し、圧縮空気とともに系内に侵入し、シールの変形、エア漏れ、摩擦抵抗の増大、バルブやアクチュエータの性能低下、環境汚染などを引き起こす。
圧縮空気から油を除去する方法には、油水分離器や水分離器を使用して空気から大きな油粒子を分離し、装置のドレンバルブから排出する方法がある。より小さな油粒子は、活性炭による吸着によって除去することができる。
(3) ホコリ
大気中のほこり、パイプライン内のさび粒子、シール材の破片が圧縮空気に浸入し、可動部品の詰まり、誤作動、ノズルの詰まり、部品の摩耗の促進、耐用年数の短縮、故障の原因となり、システムの性能に深刻な影響を与えます。
圧縮空気に粉塵が侵入するのを防ぐ主な方法には、以下のようなものがある:
- エアコンプレッサーの前にあるプレフィルターを定期的に清掃する。
- 水分離器のフィルターエレメントは定期的に清掃してください。
- フィルターエレメントの適時交換。
3.空気圧システムの日常メンテナンス
空気圧システムの日常的なメンテナンスには、主に凝縮水の管理とシステムの潤滑が含まれる。
(1) コンデンセートの管理
ドレン排出には、エアコンプレッサー、アフタークーラー、エアタンク、パイプラインシステム、各種エアフィルター、ドライヤー、自動ドレンに至るまで、空気圧システム全体が関与する。運転終了時には、夜間の気温が0℃以下に下がることによる凍結を防ぐため、すべての場所から凝縮水を排出する。
夜間はパイプライン内の温度が下がり、凝縮水がさらに析出するので、毎日の運転前に空気圧装置から凝縮水を排出する。自動ドレンが正常に機能しているか確認し、水カップに過剰な水が入っていないことを確認する。
(2) システム潤滑の管理
空気圧システムでは、制御部品からアクチュエータに至るまで、相対運動をするすべての表面に潤滑が必要です。不適切な潤滑は、摩擦抵抗を増加させ、コンポーネントの性能低下を引き起こし、またはシール面の摩耗によるシステム漏れにつながる可能性があります。
潤滑油の特性は潤滑効果に直接影響する。一般に、高温環境では高粘度の潤滑油が使用され、低温環境では低粘度の潤滑油が使用される。温度が特に低い場合は、オイルカップにヒーターを設置して曇りにくさを克服することができる。
給油量は、潤滑部の形状、運動状態、負荷の大きさによって変化する。給油量は常に実際の必要量より多くしてください。オイルミスト発生装置が正常に作動しているか注意してください。油量が減らない場合は、時間差で滴下量を調整してください。調整しても効果がない場合は、オイルミスト発生装置を修理または交換してください。
4.空気圧システムの定期メンテナンス
定期メンテナンスの間隔は通常3ヶ月。主な内容は以下の通り:
(1) システムの漏れ部分を特定し、その解決を図る。
(2) 方向制御弁の排気口を確認し、潤滑油の量が適正かどうか、空気中に凝縮水があるかどうかを判断する。
潤滑不良の場合、オイルミスト発生装置の仕様が適切か、設置位置は適切か、オイル滴下量は正常か。ドレンが多量に排出される場合は、フィルタの設置位置は適切か、ドレン排出装置は適切か、ドレンは完全に排出されるかなどを検討する。
方向制御弁の排気ポートを閉じたときに、まだ少量の漏れがある場合は、部品の損傷の初期段階であることが多い。点検後、磨耗した部品を交換することで故障を防ぐことができる。
(3) 安全弁、非常用安全スイッチが確実に作動するか確認する。定期保守の際には、機器および人体の安全を確保するため、作動の確実性を確認すること。
(4) 方向切換弁の動作が確実かどうかを観察する。切替時の異常音の有無から、鉄心とアーマチュアの整合部に不純物が混入していないか判断する。弁心の摩耗、シール部品の老朽化の有無を確認する。
(5) 方向切換弁の切換を繰り返し、シリンダの作動を観察し、ピストンのシールが良好であることを確認する。ピストンロッドの露出部を確認し、フロントカバーの合わせ部からの漏れの有無を判断する。
上記の点検と修理の結果は、トラブルシューティングや大規模修理の際に使用するため、記録しておくべきである。
空気圧システムのオーバーホール間隔は1年または数年である。主な内容は、システムの各コンポーネントや部品の性能と寿命をチェックし、通常故障する部品の修理や部品交換を行い、修理間隔内に考えられる故障要因をすべて取り除くことです。