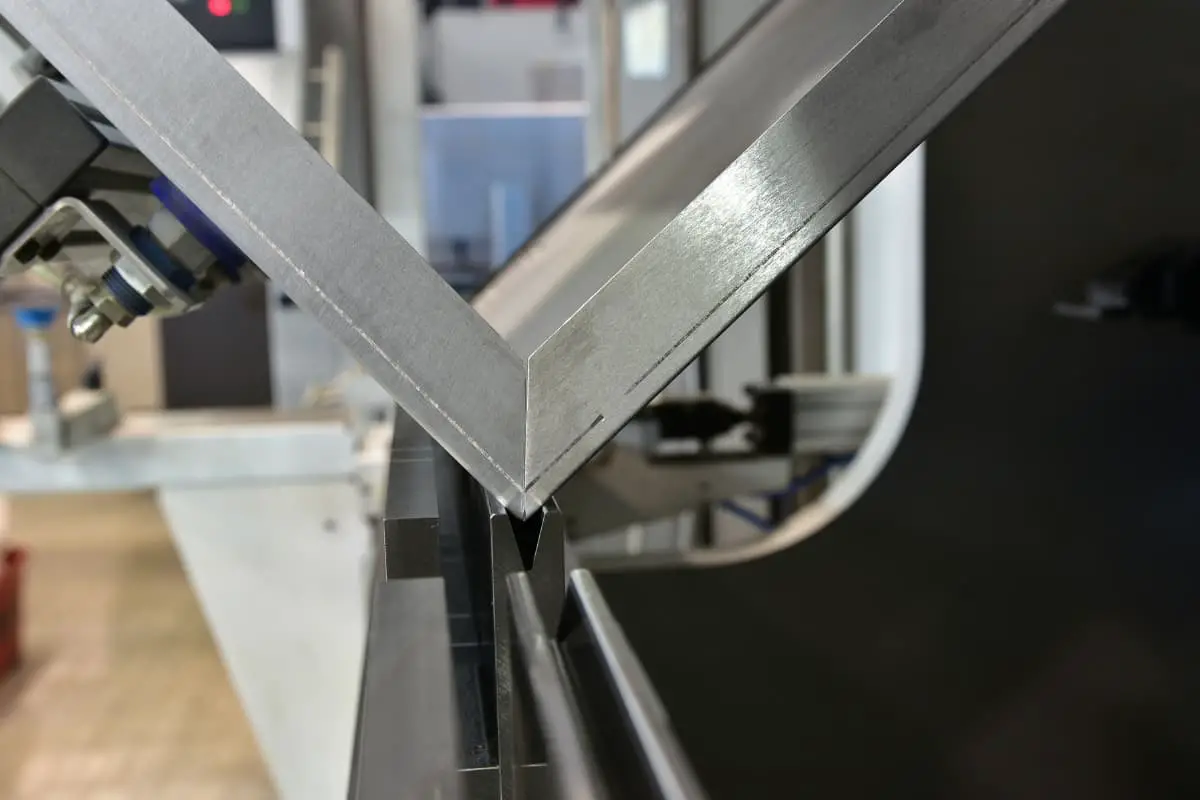
I.鋳造
鋳造とは、鋳型の空洞に液体の鋳造材料を充填するプロセスを指す。液体金属が凝固した後、材料は一定の形状を得る。
1.基礎知識
- 鋳造工程は、砂型鋳造と特殊鋳造の2つに大別される。
- 一般的な鋳造材料には、鋳鉄、鋳鋼、非鉄合金などがある。


2.金型の構造

金型の主な構造には、砂型、砂中子、ゲートシステムなどがある。
金型キャビティは、パターンを取り除いた後に得られる。2つの鋳型の接合面はパーティングラインと呼ばれる。砂中子は鋳物の内部の空洞や穴を形成するもので、中子端の延長部分を中子印刷という。中子座は中子印刷が置かれる鋳型の空洞で、パターンを使って砂型とともに作られます。
ゲートシステムは、注湯口、インゲート、ランナー、スプルーから構成される。砂型と砂中子のベントは、注湯中に空気を逃がすためのものです。注湯中、溶湯は外部ゲートに注がれ、スプルー、湯道、湯口を通って鋳型キャビティに流れ込みます。押湯は鋳型キャビティの最も高い位置に設置され、金属液が鋳型に満たされているかどうかを観察するために使用され、ベントとしても機能する。
鋳型とも呼ばれるパターンは、鋳型のキャビティを形成するために使用されるプロセス機器です。一般的に木や金属などの材料で作られている。パターンの形状は鋳造品と似ていますが、鋳造品にある穴や空洞がパターンにはない点が異なります。コア・プリントパターンは、鋳型のキャビティ内に中子座を形成する。

3.手動成形工具
(1) 一般的に使用される成形工具
鉄製スコップ、ふるい、サンドランマー、スクレーパー、ベントワイヤー、ドロースパイクとドローピン、スリック、スワブ、パウダーバッグ、ハンドベローズ、空気式ランマーなど。


(2) 一般的な金型仕上げ工具
鏝、砂掛け、半丸道具、丸鼻道具、フランジスパイン、整形鏝、スプーン、両端真鍮スプーンなど。




II.圧延、絞り、プレス
圧延製品を製造する場合、必要な仕様のインゴットをまず鋼塊鋳型で鋳造し、次に炉(1200℃)で加熱し、最後に圧延機で板、切片、管に圧延する。

1.セクションとプレートの製造

2段圧延機の2本のロールは反対方向に回転する。溝のない円筒ロールは板材の圧延に使われ、溝のある円筒ロールは切片の圧延に使われます。
2段圧延機ではパスごとにロールの向きを変える必要があるため、ロールの冷却時間が長くなる。3段圧延機は、3本のロールが垂直に並んでいるため、パスごとにロールの回転方向を変える必要がありません。
2.ワイヤー製造

直径5mm以下のワイヤーは、伸線機を使用して製造することができる。リング状の 抜き型 漏斗状の穴の開いたダイスを使用し、目的の直径のワイヤーを伸線する。細線は超硬合金またはダイヤモンドの伸線ダイスを通して伸線される。加工硬化のため、線材は中間加熱を必要とする。
3.チューブ製造
(1) 溶接鋼管

帯鋼は成形ロールで管状に成形された後、トンネル型の連続加熱炉を通過し、側面に配置されたガスバーナーで溶接温度に加熱され、最後に溶接ロールでエンドレス管に溶接される。
(2) シームレス鋼管
1) マンネスマンのスキュー圧延ピアスミルを使用して、ソリッドビレットに穴を開け、特殊な方法(周期的な溝圧延など)で目的のチューブ寸法に圧延する。

2) エルハルト・プッシュベンチ法では、まず高温の角鋼ビレットを円筒形の金型キャビティ内のカップ状の管ビレットに押し出し、次に管ビレットを長いマンドレルにはめ込み、複数のダイス(各ダイスは前のダイスより小さい)を通して押し出す。この方法では、同じ内径の薄肉管を製造することができる。

4.ディープ・ドローイング
深絞り加工とは、シートメタルを中空形状に加工したり、すでに絞り加工された中空体をさらに引き伸ばしたりすること。

深絞りダイは、パンチ、ダイキャビティ、ブランクホルダーから構成される。
ダイキャビティに固定されたスペーサーブロックがシートメタルをセンタリングします。ブランクホルダーがシートをクランプした後、パンチが下方に移動し、シートがダイキャビティから引き抜かれます(深絞り加工では、ワークの下端に角丸が現れます)。

パンチがダイキャビティからワークを完全に抜き取る場合、ワークがパンチの戻りストロークで付着することがある。これを防ぐために、ストリッパープレートが使用される。ワークが上端で引っかかる場合は、スプリング駆動のエジェクターを使ってワークを上方に押し上げ、ダイキャビティから出します。
深絞り加工に適した材料だけが、激しい変形下でも割れを避けることができる。このような材料は、十分な強度と同時に優れた延性を持たなければならない。

断面積に対する高さの比率が高いワークピースは、数段階に分けて絞り加工を行う必要がある。絞り加工の段数は、次の原則によって決定される。円筒形の絞り加工部品の場合、次の絞り加工のパンチ径は、前の絞り加工よりも約1/3小さく、最初の絞り加工の直径は、素材径よりも1/5小さくする必要がある。
5.後方押し出し

ある種の材料の流動特性に基づいて、後方押出しは、ディスク(板)ブランクから薄肉中空部品を加工するために使用することができる。
後方押出成形に適した材料は、主に鉛、亜鉛、銅、アルミニウム、銅合金、軟質黄銅などである。
完成品と同じ断面形状の円盤状ブランクをダイキャビティに入れる。押し出しパンチとダイキャビティの直径差は、完成品の肉厚の2倍に等しい。プレスの押し出しパンチが円板状のブランクを圧縮すると、材料がダイキャビティの中を流れます。 パンチとダイの隙間 空洞をパンチの動きと反対方向に移動させる。
材料が流れやすいように、押し出しパンチの端面には一定の凸部やテーパーがあります。押し出しパンチの直径は、ワークの内径より約0.2mm小さい。パンチの戻りストロークで、ストリッパープレートがパンチからワークを取り除きます。後方押し出しは、チューブ、缶、その他の薄肉中空部品を製造するための経済的な方法です。
III.鍛造
鍛造とは、鍛造機械のハンマー、アンビル、ポンチ、あるいは金型を通してワークに圧力を加え、塑性変形させて製品の所望の形状と寸法を得る成形プロセスを指す。
1.基本原則
(1) 鍛造中の結晶粒組織の変化
鍛造品のファイバー・フロー分布は、機械加工品よりも良好で、耐荷重性が高い。鋼の鍛造性は、炭素含有量が増加するにつれて低下する。鋼中の硫黄は熱間短絡の原因となり、リンは冷間短絡の原因となるため、鋼中の硫黄とリンの合計含有量は0.1%(質量分率)を超えてはならない。

鍛造中、材料の引張強さは弾性限界を超えなければならない。

ゾーン1では結晶粒の変形は小さく、ゾーン2では結晶粒の変形とスリップが大きく、ゾーン3では結晶粒の変形とスリップも小さい。
(2) 鍛造温度

について 鍛造温度 は鍛造品の材料に依存する。ワークの加熱時間はできるだけ短くする。過剰な加熱時間や加熱強度は、鋼組織の粗大化や脆化を引き起こし、強度を低下させる。鋼材は白熱状態でスパークやスケールを起こし始める。過熱した鋼は鍛造できない。焼戻し温度(290~350℃)での鋼の延性は特に劣る。
冷間鍛造は粒界応力を発生させ、最初は硬化として現れ、最終的には亀裂を形成する。焼きなましは内部応力を除去することができる。純銅は冷間鍛造が可能です。鍛造温度は銅に含まれる合金元素の含有量に応じて上昇し、最高800℃まで上昇します。
アルミニウムの鍛造温度は400~500℃である。
(3) 熱源

主に使用される加熱炉には、反射炉、重油炉、ガス炉、石炭ガス鍛造炉、抵抗炉などがある。
2.鍛造設備
1) 一般的な自由鍛造設備には、鍛造用ハンマーとプレスがある。一般的な鍛造ハンマーには、エアーハンマー、スチームエアーハンマーがある。プレスは油圧プレス、オイルプレスが一般的である。

2) 一般的に使用される型鍛造設備には、型鍛造ハンマー、クランクプレス、平型鍛造機、フリクションプレス、スクリュープレス、コイニングプレス、ウェッジクロスローリングマシンなどがある。

3.鍛造作業
(1) 自由鍛造
簡単な鍛造用工具を使ってワークを成形する。
(2) 引き出す

まず、鍛冶用ノミで金敷の角や縁を縦に抜き、金敷の面で平らにする。
(3) 動揺させる

鍛造ブランクを加熱した後、まずアプセットする範囲を限定し、金敷面または金敷台の上でハンマーを使ってアプセットする。
(4) オフセット

まず、荒いブランクの一部分を別の部分に対してオフセットし、次にオフセットした部分を鍛造して必要な断面にする。
(5)カッティング

切断には熱間鍛造ノミを使う。
(6) パンチング

パンチングハンマーがパンチをワークピースに打ち込み、パンチはその軸を中心に回転し、パンチングパッド上の穴を打ち抜く。
(7) スロット加工
ホールチゼルを使って、まずワークの両端にスロットを割り、次にスロットを必要な穴の形に広げる。
(8) 鍛造溶接

鍛接とは、2つのワーク(炭素量0.2%以下の鋼材)を粘性のある状態で鍛造法により1つに接合することをいう。まず、鍛接するワークをバイト溶接または重ね溶接の形状に加工し、溶接温度(1300~1400℃)まで加熱した後、スケールを除去して急速鍛接する。鍛接の溶接強度は母材強度の70%~85%である。
4.金型鍛造
型鍛造とは、ワークを鍛造温度まで加熱し、金型キャビティ内で1段階または複数段階の型鍛造により、原形から必要な形状に成形する工程を指す。
金型が閉じた後、材料は金型キャビティを満たし、余分な材料はフラッシュとして押し出される。型鍛造では、材料はまずアプセットされ、次にキャビティ内で流動し、最後に最終形状にアプセットされる。
金型が高価なため、型鍛造は大量生産にしか適さない。型鍛造に適した材料には、合金鋼、非合金鋼、銅、銅合金、マグネシウム合金などがある。
金型は上型と下型からなる。

鍛造用金型は永久型である。鍛造温度に加熱された予備成形されたワークを鍛造型に入れ、金型キャビティの形状に押し込む。大きなワークや複雑な形状のワークは、複数の鍛造型で数回に分けて鍛造される。型鍛造の利点は、加工費が安く、寸法が正確で、表面が比較的滑らかなことである。
(1) 金型材料

水焼き入れ炭素鋼(炭素含有量質量比0.9%)は、浅いキャビティを持つ金型の製造に適している。より大きな変形には、クロム-ニッケル-モリブデン合金鋼が使用されます。金型は無垢のダイス鋼からフライス加工されます。脱型を容易にするため、金型の抜き勾配は内側キャビティが1:5、外側キャビティが1:10である。
材料の収縮と金型の熱膨張のため、1.2%~1.5%の収縮率を考慮する必要がある。金型キャビティは研磨され、硬度、耐摩耗性、耐熱性、耐圧性、耐クラック性が要求される。要求精度にもよりますが、鍛造用金型は6,000~25,000個のワークを生産することができます。
(2) 作業順序

ビレット金型による自由鍛造 - 型鍛造 - 応力除去焼鈍。
基本的な成形作業は、最終金型でのワークの鍛造精度を向上させ、最終金型の寿命を延ばすために、主に予備鍛造、自由鍛造、中間型鍛造によって完了する。
(3) フラット鍛造

平板鍛造後、元の素材断面が増加する。
平型鍛造機の2つのクランプスライドでブランクをクランプする。メインスライドに取り付けられた凸型がアプセットに使用される。多条アプセットでは1回の加熱で済みます。
平鍛造の利点は、型鍛造に比べて抜き勾配がなく、焼損が少なく、経済的であることである。
IV.曲げ
曲げ加工は、主に曲げモーメントによって成形部での(金属の)流れが引き起こされる成形方法である。
1.基本原則
(1) 素材構造の変化

被加工材の曲げ性能は、被加工材の延性に依存する。多くの金属や合金は冷間曲げ加工が可能ですが、一部の金属や合金は、曲げ温度を下げるために一定の温度まで加熱する必要があります。 曲げ半径例えば、亜鉛は150℃に、マグネシウム合金は300℃に加熱する必要がある。
曲げ加工中、内側の結晶粒は圧縮され、外側の結晶粒は引き伸ばされ、中性層だけが変化しない。

結晶粒内で原子の滑りが見られる。外層の引張応力は破壊限界に近づき、曲げられた部分の引張応力領域の断面には明らかな横方向の収縮が見られるが、圧力領域では縦方向の収縮が見られる。したがって、構造体の伸縮は縦方向の変形だけでなく、横方向の変形も引き起こす可能性がある。伸ばせば断面が小さくなり、圧縮すれば断面が大きくなる。
(2) ワークの曲げ強度

ワークピースの曲げ強度は、温度、ワークピースの材質、断面寸法、曲げ軸に対する相対位置などの要因に関係する。
曲げ強度はワークの幅に比例する。幅が2倍になれば、張力と圧縮を受ける繊維の本数も2倍にならざるを得ない。同じ曲げ半径の場合、高さ方向の引張・圧縮を受ける繊維の量は幅方向よりはるかに多いので、前者に必要な曲げ力は後者よりはるかに大きくなければならない。
(3) 曲げ半径

曲げ半径は最小値以下であってはならない。曲げ半径は、材料の伸び、ワークの厚さ、ワークの断面形状、圧延方向に関係する。棒材の場合、鋼と軟質アルミの曲げ半径は板厚の1.5倍、硬質アルミは板厚の2~4倍、銅と亜鉛合金は1/3~1/2です。
曲げ加工中のプレート表面の切り欠き感度が高いため、プレート表面は平滑で、気孔がないことが求められる。
曲げ角度は大きいよりも小さい方が有利である。曲げ半径と曲げ角度が許容値より小さい場合は、熱間曲げを使用する。
2.板金曲げ

小さな部品はマシンバイスで曲げることができる。必要な曲げ半径を得るには、角を面取りしたストップ・ブロックを使用する。角を鋭く曲げすぎると、板金の曲げ部分に亀裂が入る。
最小曲げ半径=板厚×換算係数
最小曲げ半径の換算係数
素材 | ソフト・スチール | 中硬度鋼 | 銅 | 真鍮 | アルミニウム合金(焼入れ) |
換算係数 | 0.5 | 0.55 | 0.25 | 0.3~0.4 | 2-4 |
例厚さ3mmの中硬鋼板をマシンバイスでクランプに曲げる。その最小曲げ半径=3mm×0.55=1.65mm。
曲げ加工:
1) 被加工物に印を付け、マシンバイスを使って一端を直角に曲げる。
2) 高さをマークし、木製のストップブロックを使って2つ目の直角を曲げる。
……
4) 木製のストップブロックを置き、4回目のベンドを行う。
曲げ強さとは、物体が曲げ変形に抵抗する能力のことである。山形鋼やI形鋼など、幅と高さの比が大きいものは曲げ強度が高い。剛性は、スピン成形、圧延、曲げ、折り曲げなどの方法で高めることができる。

3.パイプ曲げ

パイプの曲げ半径が小さいと、パイプが扁平になることがある。曲げ加工時には、パイプの内側に充填材を入れるか、ガイド・ホイール付きの曲げ装置を使用する必要がある。曲げ半径が大きい場合は、パイプ内部に充填材を入れる必要はないかもしれない。小径の引き抜き管や圧延管は、冷間曲げ加工が可能である。
熱間曲げの場合、シワを避けるため、パイプの内側の加熱温度を外側より高くする。曲げ半径は、少なくともパイプ直径の3倍以上とする。曲げ加工中の引張応力や圧縮応力を避けるため、パイプの溶接継ぎ目は中立地帯になければならない。
4.構造用鋼の曲げ加工

構造用鋼の曲げ加工は難しい。山形鋼、Uチャンネル鋼、I形鋼を鋭角に曲げるには、曲げ箇所に切り欠きを入れ、曲げた後に切り口を溶接する必要がある。

切り欠きの形状は、曲げ角度と山形鋼エッジの厚さに依存する。曲げ部の内側は圧縮されているので、2つの面取りされたエッジの間に一定の距離(すなわち、カットエッジ距離a)が必要です。この距離は、山形鋼のエッジが厚く、曲げ角度が小さいほど大きくなります。
a=Stanα/2
圧縮を避けるためには、圧縮された部分の金属をドリルで取り除かなければならない。ドリルビットの直径d = Sa/100。
構造用鋼材は、構造用鋼材曲げ機を使って円形に曲げられる。このベンディング・マシンの上下のローラーは調整不可能で、手動または電動モーターで駆動します。上部ローラーは調整可能で、これを調整することで曲げ半径を変えることができます。
V.矯正
矯正の目的は、板金、ワイヤー、棒材の真直度と平坦度の誤差を減らすことである。
1.基本原則
内部応力、一方的な加熱または冷却、衝撃、打撃、一方的な切断加工などが、材料の反りやねじれを引き起こす原因である。ワークピースは、加圧、ハンマー、火炎加熱によって矯正し、平坦にすることができる。
2.ハンマーまたは圧力による矯正


材料の厚さに応じて、冷間矯正または熱間矯正を選択します。
小さな矯正力であれば、ワークを矯正プレートの上に置き、大きな矯正力であれば、矯正機を使用する。
(1) 板金平坦化
柔らかい板金(銅、亜鉛、アルミニウム)の膨らみは、木槌、ゴム槌、プラスチック・ハンマーを使って平らにすることができる。硬い板金の場合は、膨らみの外縁に沿って、内側から外側へらせん状にハンマーで叩いて伸ばす。
シートメタルが矯正ローラーを通過すると、平坦になるまで均一に引き伸ばされ、圧縮されます。一般的に、板金用ローラー矯正機を使用する方が経済的です。


(2) ワイヤー矯正
ワイヤーをまっすぐにするには、万力でクランプし、2つの木製ブロックに通してまっすぐに引っ張るか、ワイヤー矯正機を使う。
(3) バーおよびプロファイルの矯正
バー矯正機とプロファイル矯正機がそれぞれ使用される。
3.熱矯正

火炎加熱には、点状加熱、点線状加熱、くさび状加熱の3つの形式がある。加熱形態の選択は、ワークピースの形状、サイズ、厚さに依存する。反りのある面を加熱する、つまり、まず長い方を加熱して反りを大きくする。

しかし同時に、加熱部分の体積増加により大きな圧縮応力が発生する。材料の降伏点まで加熱を続けると、内圧によって長い側が圧縮される。冷却中、圧縮された部分は収縮し、その結果、ワークピースはそれ自体まっすぐになる。この工程は、ハンマリングと組み合わせて行われる。
点加熱または点線加熱は板金や棒鋼に使用され、くさび加熱は圧延プロファイルに使用され、くさび加熱はくさび先端から開始しなければならない。
また、矯正、曲げ、ハンマリング、絞り加工は、材料の冷間加工硬化を引き起こし、硬度を高めるが、これは焼きなましによって除去することができる。
VI.スタンピング
スタンピングとは、プレスや金型を用いて板金、帯板、パイプ、プロファイル材に外力を加え、塑性変形や剥離を起こさせ、所望の形状・寸法のワーク(プレス部品)を得る成形加工である。曲げ型、カール型、成形型などがある。

1.金型
(1) プレス加工
冷間成形中、材料の曲げ端にかかる荷重は弾性限界を超え、(塑性)変形が始まり、継続する。材料の外縁は、冷間成形中に最大の伸びと応力を受ける。ひび割れを避けるため、冷間成形には高い伸びと適度な強度を持つ材料が選ばれる。

(2) 金型曲げ

曲げダイスを使用すると、シートやストリップ材をアングル鋼、Z型鋼、U型鋼に曲げることができます。曲げ加工では、材料の厚みを変える必要はありません。曲げダイスは、パンチとダイスキャビティで構成されています。
曲げ部分に亀裂が入るのを避けるため、曲げ半径は許容最小値より小さくしてはならない。曲げ加工後のスプリングバック効果により、パンチとダイキャビティによって形成される曲げ角度は、完成したワークピースの曲げ角度よりもわずかに小さくなければなりません。ワークピースのスプリングバック力は、曲げ半径、材料厚さ、材料特性などの要因に関係します。
(3) カーリング

シートメタルは、カーリングによってヒンジの耳、補強材、強化エッジに成形することができる。カーリングを行う前に、シートメタルはあらかじめ曲げられている必要があります(そうでなければまっすぐになってしまいます)。次に、あらかじめ曲げられたワークピースが下型に挿入されクランプされ、対応するプロファイルを持つカーリングパンチが下方に移動してカーリングを行います。
(4) フォーム曲げ
このタイプの金型は、あらゆる形状の中空ボディや補強リブ(缶の蓋、車のロゴ)を曲げることができます。対応する形状の上型と下型を作り、シートメタルを必要な形状にプレスします。曲げ加工中、板厚は基本的に変化しません。
2.プレス
プレスはスライドの上下運動によって、摩擦プレス、クランクプレス、偏心プレス、油圧プレスなどに分類され、鍛造装置と同様である。プレススライドには、切断型や絞り型の凸型や上パンチがクランプされている。加工精度を高めるためには、プレススライドを正確にガイドする必要がある。凹型はプレスベッドに取り付けられる。
(1) フリクションプレス

フリクションプレスは、様々な産業で圧力加工に広く使用されている汎用性の高い圧力加工機です。機械製造業界では、フリクションプレスはさらに広く使用されており、金型鍛造、アプセット、曲げ、矯正、精密プレスなどの作業を完了するために使用することができます。一部のフラッシュレス鍛造もこのタイプのプレスを使用している。
(2) クランク・プレス、エキセントリック・プレス

クランクシャフトジャーナルに取り付けられた偏心スリーブは、シャフト端の着脱可能なクローカップリングを介してドライブシャフトに連結されている。爪環を緩めることによって偏心スリーブを回転させ、ストローク長を調整することができる。
この2種類のプレスは、モーターの回転運動を、コネクティングロッドまたはボールソケットジョイントを介して、クランクシャフトまたは偏心シャフトを介してスライドの直線運動に変換する。
(3) 油圧プレス
A 油圧プレス は、パスカルの原理に基づき、液体を作動媒体としてエネルギーを伝達し、様々な加工を実現する機械である。油圧プレスは一般に、主機、動力系、油圧制御系の3つの部分から構成される。
VII.シャーリング
剪断は、両刃の刃物を使って材料を切り離す工程である。
1.ハサミで切る
一般的な工具は、1本の切れ刃で被削材に切り込みを入れるが、この工具では、1本の切れ刃で被削材に切り込みを入れる。 剪断工程上刃と下刃の2つのくさび形刃先が相対的に材料に働きかけます。上刃と下刃の2つのくさび形の刃先が、横から互いにすれ違うようにスライドする。最初に、被削材は2つの刃先から両側に溝が切られる。
くさび形の刃先の圧力は、材料の構造を密にする。材料の抵抗が大きくなると、刃はある深さまでしか切り込めなくなる。材料の降伏点を超えてさらに圧力を上げると、組織が分離し、2つの破断面がスライドして離れる。分離した加工物の表面は、さまざまなせん断プロセスによって不規則になり、外側は滑らかで、内側は粗くひび割れたようになる。
2.簡単なシート材の手作業による切断
厚さ1.5mm以下のシートであれば、手鋏でカットすることができる。
(1) ストレート・ハンド・鋏

直線的なカット、わずかにカーブしたショートカットに使用。
(2) ストレート・スルー・シャー

長くてまっすぐなワークの切断に使用。
(3) 穴ばさみ

刃の先端は尖っており、内側のカーブを切るのに使われる。
(4) 丸鋏

ブレードは薄くて長く、さまざまな形状に対応できる。
(5) 電気手ばさみ

作業中、下刃は静止したままで、上刃が切断動作を行う。
3.手動マシン・シャー
(1) レバー鋏

大型ワークの切断に適している。
(2) 機械鋏
別名パラレルブレード 剪断機上刃はガイドレール内を垂直に移動する。上刃は下刃に対して傾いたり平行になったりする。
(3) 丸鋏、カーブ鋏
あらゆる円や曲線のカットに使用。カーブをカットする場合は、シートを手動で送ります。
4.剪断欠陥
刃先の大きなバリ、高い剪断力の消費、刃のチッピング、マークされたラインからの切断のずれ。
5.パンチングツール

パンチを使って穴を開けるのも、剪断加工である。薄いシート、段ボール、バネ鋼板、シールリングの場合は、穴あけよりもパンチングの方が早い。厚みのある素材は、打ち抜き加圧機で穴あけするのが効率的で切りくずも出ない。柔らかい素材にはエッジタイプのパンチ金型を使用します。

VIII.ブランキングブランキング
ブランキング・ダイは、パンチ(オス型)とダイ(メス型)で構成され、シート材から任意の形状を打ち抜くことができる。1つの形状に1セットのダイが必要なため、大量生産に向いている。

材料が低温で変形するため、シートが最初にポンチに接触するとき、シートは容易に押し込まれる。パンチの角が小さく丸みを帯びている場合、シートの下端も小さく丸みを帯びる。パンチが下方に移動し続けると、その剪断力は材料の剪断強度を上回り、材料組織は比較的滑らかな剪断面で分離する。パンチ、カッティング・エッジ、ダイ・カッティング・エッジが交差する前に、材料の残りの破断面が分離する。ダイの穴は緩やかなテーパー構造になっている。

ブランキングとは、金型を使って材料や被加工物の一部を、材料や被加工物、廃棄物の別の部分から分離するプレス加工のことである。ブランキングは、シャーリング、ブランキング、パンチング、ノッチング、スロッティング、パーティング、チゼル、トリミング、トング、カットオープン、フィニッシングなどの分離工程の総称である。
ブランキングは、ワッシャー、自転車のチェーンホイール、計器用ギア、カム、シフトフォーク、計器パネル、モーターや電化製品用の珪素鋼板、集積回路のコネクターなどの直接加工によく使われる。
IX.ベンチワークの基本操作
ベンチワーク用の一般的な機材には、以下のようなものがある:
1) 作業台

ワークピースや各種工具、測定器を置くための、ベンチワーカーの主な仕事場。
2) ベンチバイス

ワークを固定するための万能治具。
1.レイアウトマーキング
レイアウトマーキングとは、設計図面や現物から要求される寸法に従って、ワークのブランクや半製品に加工境界をマーキングしたり、基準点や基準線を見つける作業のことである。レイアウトマーキングによって、ワークの加工代や加工面の位置を決定し、ブランクの形状や寸法が図面要求と合致しているかを確認し、加工代を合理的に割り当てることができる。
(1) よく使われるレイアウトマーキングツール
一般的なレイアウトマーキングツールには、レイアウトプレート、スクライバー、レイアウトディスク、ディバイダー、センターパンチ、Vブロック、ジャックなどがある。



(2) 基本的なレイアウトマーキング技術
使用する道具はスクライバー。正しい方法は、スクライバーをスチール定規の外側に15度から20度傾け、同時に印をつける方向に45度から75度傾けることである。

1) 直線をマークする。

マーキングの際は、左手でスチール定規を持ち、右手の親指と人差し指でスクライバーを握り、中指でスクライバーの先端が定規のガイド面に密着するようにスクライバーを押し、スクライバーの後方に向かって引くと、はっきりとした直線が引ける。
2) 垂線に印をつける。

垂直線は、幾何学的な構造、四角定規、またはスクライビング・ディスクを使って引くことができる。最も簡単な方法は、隣接する辺を基準にして、角定規で簡単に垂線を引くことである。
3) 平行線のマーキング。

幾何学的方法、四角定規によるマーキング、スクライビングディスクによるマーキングの3つの方法がある。
4) 円弧をマークする。

使用する道具はディバイダー。使うときは、デバイダーの2本の足を両手で開いて調整し、デバイダーのジョイント部分を右手で握る。円を描くときは、時計回りと反時計回りの両方向に描くことで、2つの半円の弧を組み合わせる。
5) センター・パンチング。

後工程でのワークの位置合わせを容易にするため、センター・パンチは適切な大きさで均一でなければならない。パンチポイントは加工ラインの中心にあり、ずれてはならない。ずれたパンチポイントは、その後のライン補足を誤らせるからである。
操作の際は、左手でセンターポンチを少し前に傾け、ポンチの先端をラインの中心に合わせる。位置を合わせたら、ポンチがラインの中心に垂直になるようにまっすぐにし、ハンマーでポンチの先端を軽くたたいてセンターマークをつける。
2.チゼリング
チゼリングとは、ハンマーでノミを叩き、ワークを切断する加工方法である。フランジの除去、材料の分離、油溝のノミ入れ、薄いワークのブランキング、粗加工など、主に機械的な加工が不便な場合に用いられる。
(1) ノミ
平ノミ、先ノミ、油溝ノミの3種類がある。ノミの持ち方はノーマルグリップ、リバースグリップ、バーチカルグリップの3種類。


(2) ハンマー
ハンマーの握り方には、タイトグリップとルーズグリップがある。タイト・グリップ:ハンマーを持ち上げる時や叩く時、5本の指すべてがハンマーを強く握る必要がある。ルーズ・グリップ:ハンマーを持ち上げる時、親指と人差し指は強く握り、小指、薬指、中指は少し力を抜く。打撃時、ハンマーが打撃点に近づくにつれ、小指、薬指、中指が急に締まり、落下するハンマーの打撃力が増す。

ハンマーの振り方には、ハンドスイング、エルボースイング、アームスイングの3種類がある。

(3) チゼリング姿勢
作業者は作業台の前に立ち、左足はバイスの中心線に対して35°の角度で、右足はバイスの中心線に対して75°の角度で、ハンマーを立って振るとき、打撃点がノミの先端に一致するようにする。チゼルを持つ手の前腕は水平に保ち、チゼルの切れ角に影響を与えないよう、肘を垂らしたり上げたりしない。

3.製材
鋸引きとは、手鋸を使って金属材料を切断したり、工作物に溝を切ったりする作業のことである。さまざまな材料や半製品を切り離したり、ワークの余分な部分を切り落としたり、溝を切ったりするのに使われる。
(1) ソーイングツール

1) 鋸フレーム
鋸刃にテンションをかけるためのもので、固定式と調整式がある。
2) 鋸の刃
材料や加工物を直接鋸で切る工具。長さは両端の取り付け穴の中心距離で表す。長さ300mm、幅12mm、厚さ0.8mmのものが一般的。
3) 鋸刃の取り付け

ハンドソーは前方に押している間だけ切断するので、ハンドソーを取り付けるときは、歯の先端を前方に向ける。
(2) 製材姿勢
1) ソーフレームの持ち方

正しいグリップは、ソーイングの質に大きな影響を与えます。左手でソーフレームの前部を支え、右手でソーハンドルを握るのが正しい方法です。
2) 立ち位置

のこぎりを切るときは、作業者は中心線の片側でベンチバイスに向かい、左足はベンチバイスの中心線に対して35°の角度で、右足はベンチバイスの中心線に対して75°の角度で立ちます。
3) 製材姿勢

右手でノコギリを押すとき、それに応じて体が前傾する。この体の動きにより、右手の押す力を増加させ、右手の疲労を軽減し、作業効率を向上させることができます。鋸を押す力はすべて右手でコントロールする。左手の圧力は大きすぎてはいけません。左手の主な役割は、鋸のフレームをまっすぐに保つことです。
(3) 基本的な製材方法
1) ワーククランプ
ワークピースは通常、操作しやすいようにベンチバイスの左側にクランプします。ワークがバイスのジョーから大きくはみ出さないようにします。のこぎりの切り口は、加工中の振動を防ぐため、バイスのジョーから20mmほど離します。のこぎりの切り口は、バイスの爪の側面と平行になるようにします。ワークピースは、損傷や変形を避けるため、しっかりとクランプしてください。
2) 速度とストローク長制御
のこぎりの歯の摩耗を防ぐため、のこぎりを押すときは適切な力をかけ、引くときは力を抜いてください。ノコギリを使用する際は、ノコギリの刃の有効長を使用するようにしてください。前後ストロークの頻度
普通鋼の場合は毎分30~40回、軟質金属や非金属の場合は毎分50~60回が適当である。
3) 鋸の始動
鋸刃の前端または後端を使用し、鋸刃を加工面に対して15°の角度にして、加工面の端に置いて鋸引きを開始する。少なくとも3枚の鋸歯が同時にワークと接触するようにします。安定性と精度を高めるため、親指で鋸刃をブロックし、正しい位置に保つことができます。

4) 丸パイプの製材方法

ノコギリの刃は目の細かいものを選ぶ。パイプの壁を切り開いたら、すぐにパイプをノコギリを押した方向に適当な角度だけ回転させ、ノコギリを切り続ける。パイプが完全に切断されるまで、この回転を繰り返す。
5) 棒材の製材
平らな断面が必要な場合は、一方向から製材を開始し、終了するまで続けます。要求が高くない場合は、製材面を減らし、効率を向上させるために、複数の方向から製材することができます。
6) 薄板の製材
可能であれば、幅の広い側から鋸を入れるようにする。どうしても幅の狭い側から鋸で挽きたい場合は、木製のスペーサーを2枚クランプしてシートと一緒に鋸で挽くか、薄いシートを直接万力にクランプして、手鋸で斜めに押し込む。
7) 平鋼の鋸引き
切断線に印をつけ、幅の広い方の両端からのこぎりを入れる。2つののこぎりの切り口が合わさるところで、軽くたたいて割って切り離す。
4.ファイリング
ヤスリは歯のついた切削工具である。
外面、内孔、溝、様々な複雑形状のワークの加工が可能です。加工精度は0.01mmに達します。
(1) ファイル

ヤスリには、台ヤスリ、整形ヤスリ、特殊ヤスリがある。ベンチ・ヤスリは、断面形状により、平ヤスリ、角ヤスリ、丸ヤスリ、三角ヤスリ、半丸ヤスリに分けられます。整形用
ヤスリは、ワークピースの小さな領域を仕上げるために使用されます。特殊な面を加工する場合は、特殊ヤスリを使用します。ヤスリには多くの種類、仕様、型式があり、ワークの形状、硬さ、加工代、要求精度に応じて選択することができます。
(2) ファイルの持ち方

右手でナイフの柄をしっかりと持ち、柄の先端を親指の付け根の手のひらに当てる。親指を柄の上部に置き、残りの指で柄を下から上に巻きつける。左手は、親指の付け根の筋肉をヤスリの頭に押し付け、親指を自然に伸ばし、他の4本の指を手のひらの方に丸め、中指と薬指でヤスリの前端をつまむ。ヤスリをかけるときは、手でヤスリを押して進行方向を決め、左手は右手と協力してヤスリのバランスを保つ。
(3) 出願姿勢

ヤスリがけの際、作業者はベンチバイスの中心線に対して左足を35°の角度、右足を75°の角度にして、中心線の片側に向かい合います。
ヤスリがけをするときは、両足でしっかりと立ち、体を前傾させ、左足に重心を置き、左ひざを曲げた方に体を傾け、両肩を自然に水平に保ち、ヤスリ面を見て、右前腕は基本的にヤスリ面と平行に保つ。
(4) 基本的なファイリング方法
1) 平らな面のファイリング

ストレート・ファイリング、クロス・ファイリング、プッシュ・ファイリングの3つの方法がある。
2) 外部アークのファイリング

クロス・ファイリングとロール・ファイリングである。クロス・ファイリングは円弧の粗加工に使われ、ロール・ファイリングは円弧の微細加工やわずかな取り代の場合に使われる。
3) 内部円弧のファイリング

クロス・ファイリングとプッシュ・ファイリングである。クロス・ファイリングは、外部円弧の粗加工に使用される。プッシュ・ファイリング方式では、前進、左右への移動、ヤスリの中心線を中心とした回転の3つの動作を同時に行う。
5.スクレイピングとグラインディング
スクレイピングとグラインディングは、表面品質と寸法精度を向上させるために使用される手作業の精密機械加工プロセスである。
機械的な加工(バニシング、圧延)とは別に、多くの機械加工工程では、スクレイピングとグラインディングが最終工程となることが多い。これらは、残存する粗いピークを除去する。表面粗さは、指定された表面からの実際の表面品質の偏差である。単位は1/1000mm。微細加工の後、支持面、相手面、シール面の耐荷重面積を80%まで増加させることができる。削った面は完全にシールしてください。
(1) スクレイピング
スクレーパーは、細かい切り屑を切断できるものでなければならない。平らな面にはフラット・スクレーパーを、曲面にはスプーン型のスクレーパーや三角スクレーパーを使用する。くさび角は85°~95°で、前角はマイナス。


長いストリップ・スクレイピングによって、残っている粗いピークを取り除き、表面のマークを減らすことができる。スクレーパーは削り跡に対して角度をつける。前方に削るときは軽く圧力をかけ、削り終わるごとに圧力を下げて凹みを防ぐ。

注:スクレーパーは、コランダムまたは炭化ケイ素の砥石で研ぎ、砥石で磨く。
(2) 研磨
極めて小さな凹凸を識別するために、平らな表面に色を塗る。まず、スクレイピング・プレートの上に色を塗り、ワークを台の上に置きます。大きなワークピースの場合は、ワークピースの表面にカラーを塗布してから、スクレイピングプレートまたはスクレイピングルーラーを載せて移動させます。

高い部分は光沢が出るので、スクレーパーで取り除く。削る動作は短く、わずかにカーブさせる。表面全体のポイントができるだけ多く、均等になるまで処理を続ける。1回削るごとに、削る方向を変える。

削った表面に1平方センチメートルあたり5~10点が確認できれば十分である。
X.穴加工(ドリル、カウンターシンク、リーマ)
穴加工は、ベンチワーカーにとって重要な作業技能の一つである。穴加工には主に2種類あり、1つは中実の被加工物に穴を開ける方法、すなわちツイストドリルやセンタードリルなどで直接穴を開ける方法であり、もう1つは既存の穴を加工する方法、すなわち拡大ドリル、皿ドリル、リーマなどを使って穴の拡大、皿掘り、リーマ加工を行う方法である。リーマー加工とは、リーマーを使って、すでに開けられた穴を加工する方法である。皿穴加工は、皿ドリルで穴の先に平坦な面や様々な形状の穴を開ける加工方法である。
1.よく使う道具

(1) ドリル・ビット
ツイストドリル、フラットドリル、深穴ドリル、センタードリルなど多くの種類がある。最もよく使われるのはツイストドリルで、ストレートシャンクとテーパーシャンクがある。
(2) 拡大ドリル
穴を拡大するための工具。ドリルビットと異なり、拡大ドリルは3-4個の切れ刃を持ち、クロスエッジがないため、穴の精度と表面品質が向上する。
(3) リーマー
ハンドリーマ、マシンリーマ、アジャスタブルテーパリーマなど、さまざまなタイプがある。
(4) カウンターシンク・ドリル
円錐形、円筒形、端面、その他のスタイルがあるカウンターシンキング用工具。
2.操作方法
(1) 掘削

穴の直径の1/4程度の浅い穴をテストドリルで開け、芯出しを確認する。ドリルで穴を開ける際は、送り力をかけすぎず、こまめに持ち上げて切りくずを取り除き、次の作業を行う。 切削油剤.ドリルビットを破損する可能性のある急激な切削力の上昇を防ぐため、穴が貫通しそうになったら送り速度を下げる。
(2) 穴の拡大

すでに加工された穴を拡大するために使用され、多くの場合、穴の半仕上げ作業として使用される。
(3) リーミング

寸法精度と表面品質を向上させるため、リーマを使って穴の壁から金属の層を少し取り除く。許容誤差と穴のサイズについては、関連するマニュアルを参照してください。
(4) カウンターシンク

その目的は、穴の端面と穴の中心線との垂直性を確保し、穴に接続される部品の正しい位置決めと確実な接続を保証することである。
XI.糸処理
1.糸の形成
ねじ山は、平面図形(三角形、長方形、台形など)が円筒形または円錐形の表面上をらせん状の線に沿って移動し、その表面に連続した隆起や溝を作ることによって形成される。円柱(または円錐)の外面に形成されたねじは外ねじと呼ばれ、円柱(または円錐)の穴の内面に形成されたものは内ねじと呼ばれる。
2.スレッドの幾何学的パラメータ

(1) 大径 d(外径)(D)
外ねじ山の頂上に一致する仮想の円柱の直径で、呼び径とも呼ばれる。
(2) 小径 d1 (内径)(D1)
外ねじの根元と一致する仮想の円柱の直径で、強度計算における臨界断面の計算直径として使用できる。
(3) ピッチ直径 d2
軸方向断面において、ねじ山の幅とねじ山間の幅が等しい仮想の円柱の直径。糸の平均直径にほぼ等しい。2 ≈ 0.5(d+d1).
(4) ねじピッチ P
ピッチシリンダーのジェネレーターライン上の隣接するねじ山の対応する点間の軸方向距離。
(5)鉛(Lh)
ピッチシリンダーのジェネレーターライン上の同じらせん上の隣接するねじ山の対応する点間の軸方向距離。
(6) スタート回数 n

ねじ山のらせん線の数で、製造しやすいように一般にn≦4である。ピッチ、リード、スタート数の関係はLh = nPである。
(7) 螺旋角 ψ
ピッチシリンダー上のらせんの接線と、ねじ軸に垂直な平面との間の角度。
(8) ねじ角α
ねじ山の軸方向平面における、ねじ山形状の両側面の間の角度。
(9) 回転方向
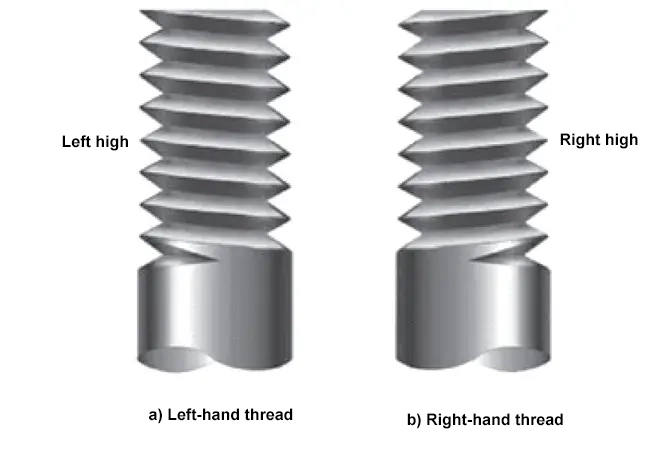
スレッドには右巻きと左巻きがある。右ねじは時計回りに回転させると進み、左ねじは反時計回りに回転させると進む。
3.スレッドプロファイル
(1) 三角ネジ

ねじ角度が大きく、セルフロック性が高く、根元が太く、強度が高い。接続に広く使われている。一般的なタイプには、メートルねじ、インチねじ、パイプねじなどがある。
1) メートルネジ。
国内規格では、ねじ山角α=60°の三角形のメートルねじをメートルねじと呼び、長径を呼び径とする。同じ呼び径でも複数のピッチがあり、最大のピッチを並目ねじ、それ以外を細目ねじと呼ぶ。最も広く使われているのは並目ねじである。
細目ねじは、小径でねじれ角が小さいため、セルフロッキング性に優れ、強度が高いが、耐摩耗性に劣り、ストリッピングを起こしやすい。薄肉部品、動的荷重を受ける接続部、微調整装置の調整機構などに適している。
2) インチねじ
ねじ山の角度はα=55°で、単位はインチ、ピッチは1インチあたりのねじ山数で表される。粗目と細目がある。
3) パイプスレッド
ねじ山形状はα=55°で、丸みを帯びている。嵌合するねじ山間に半径方向の隙間がないため、良好なシール性が得られます。呼び径はパイプの呼び内径です。水、ガス、潤滑、その他の配管システムに広く使用されている。
(2) 台形ネジ
ねじ山形状は二等辺三角形の台形で、ねじ山形状角 α = 30°である。角ねじより効率は悪いが、製造が容易で、芯出しがよく、根元強度が高い。割りナットを使用すると、摩耗によるクリアランスをなくすこともできる。そのため、ねじ駆動装置に広く使用されている。
(3) 角ネジ
ねじ山形状は長方形で、ねじ山形状角度α = 0°、ねじ山厚さはピッチの半分である。等価摩擦係数が小さく、効率が高いが、根元強度が低い。摩耗によるアキシャルクリアランスの補正が難しく、芯出し精度が低い。また、仕上げが難しく、あまり一般的ではない。
(4) バットレスねじ
バットレスねじ山は、加工面の逃げ角が3°、非加工面の逃げ角が30°である。角ねじの高い効率と台形ねじの高い根元強度を兼ね備えていますが、一方向の荷重にしか耐えられません。スクリュープレスやジャッキのような一方向の荷重を受けるスクリュードライブに適している。
4.スレッドマーキング
(1) メートルネジ
1) メートルねじの並目ねじのピッチは記されていないが、細目ねじのピッチは記されていなければならない。例えば、M20は2.5mmピッチの並目(表記なし)、M20×2は2mmピッチの細目(表記あり)。
2) 左ねじにはLH、右ねじにはマークがない。
3) ねじ公差等級記号には、ピッチ径公差等級と長径公差等級がある。外ねじ公差等級は小文字を使用し、内ねじ公差等級は大文字を使用する。例えば、M20-5g6gは、ピッチ径公差等級5g、長径公差等級6gの外ねじを示します。M20-7Hのように、ピッチ径と長径の公差等級が同じ場合は、内ねじのピッチ径と長径の公差がともに7Hであることを意味します。
4) メートルねじのかみ合い長さは、ショート(S)、ミディアム(N)、ロング(L)のいずれかに指定される。中間のかみ合い長さ(N)はマークする必要はない。例M24-5g6g-L、M20×1.5-6H-S-LH、M20×1-6g。係合長さが特定の値である場合は、M20-5g6g-40のように、係合長さが40mmであることを直接表示することができる。
(2) 台形ネジ
Tr40×7LH-7H-Lは、呼び径40mm、ピッチ7mm、左ねじ、ピッチ径公差帯コード7H、噛み合い長さが長い台形ねじを表す。
(3) 55° ノンシールパイプネジ
55°の非シール管用ねじの場合、外ねじには2つの公差等級、AおよびBがあり、これを記載する必要があります。内ねじには1つの公差等級しかなく、これを記載する必要はありません。例えば、G1/4 Aは、サイズコード1/4、公差等級Aの非シール管用ねじ、外ねじを示し、G1/4は、サイズコード1/4の非シール管用ねじ、内ねじを示します。
5.一般的なねじファスナー
ボルト、ネジ、ナットは、取り外し可能な接続を形成するために使用することができる。
(1) ボルトとネジ

頭付きボルトやネジには様々な頭部形状があり、クランプボルト、貫通ボルト、または フィッティング ボルトだ。

1) クランプボルト
カバープレート、フランジ、プレッシャープレート、その他の機械部品の固定に使用される。挿入深さは両端スタッドと同じ。内部に六角形がある円筒ボルトは、皿ボルトにすることができるが、六角ボルトのように締め付けることができる。
2) スルーボルト
ロックにはナットとワッシャーが必要。ボルト頭部、ナット、ワッシャーの接触面の平坦度に注意する。
3) 取り付けボルト
機械部品を所定の位置に固定したり、横方向の力に耐えるために使用される。このタイプの接続にははめあい(H7/k6)が必要で、高価になる。貫通ボルトと1~2本のフィッティングピンの組み合わせが経済的です。
(2) 溝付きネジ

溝付きねじは、さまざまな頭の形をしている。ドライバーでしか締め付けられないため、スパナ締めに比べて締め付け力が弱い。十字溝付きねじは、頭部に貫通溝がないため強度が落ちない。強度が高く、より強固に締め付けることができ、外観もよい。
(3) セルフタッピングネジ

会社の看板や保護板などを板金に固定する際に使用する。
(4) スタッド

スタッドは、挿入端(面取り付き)、シャンク、ナット端(上部)で構成される。クランピングボルトと同じ役割を果たす。利点は、クランピングボルトは何度も緩めるとネジ山を損傷する可能性があるが、スタッドの挿入端は常にねじ込むことができることである。スタッドで固定した部品を取り外すには、ナットだけを取り外せばよい。スタッドの破損を防ぐため、挿入深さはシャンク材の強度に合わせる必要がある。

両端スタッドの挿入深さ
素材 | スチール・ブロンズ | 灰色鋳鉄 ガンメタル | アルミニウム合金 | 軟質金属 絶縁材料 |
挿入深さ | 1d | 1.25d | 2d | 2.5d |
(5) セットスクリュー

止めねじは、全長にわたってねじ山があり、先端には挿入と締め付けのための溝がある。位置決めリング、ブッシング、その他の機械部品が動いたりねじれたりしないように固定するのに使われる。スタッドは、取り外し可能な部品を固定するために使用されるねじの変形である。
(6) ナッツの種類

下図は、いくつかの標準的なナットの形状を示している。ナットのねじ山の長さは、ナットとねじの接続の強さにとって極めて重要である。ねじ山の長さは、荷重を支えるねじ山の回転数を決定する。ほとんどのナットでは、ナットの高さはねじ山の長さと等しい。例外として、ブラインドナットがある。
標準ナットの高さ=0.8×呼びねじ径。薄型ナットの高さ 1+d.
6.糸製造
(1) 糸切り
ねじは、らせんの原理に基づいて製造される。下図は旋盤によるねじ切り加工を示している。加工中、円筒形の工作物は一定速度で回転し、切削工具は工作物に接触しながら一定速度で軸方向に移動し、工作物に対する工具先端のらせん運動が生じます。刃先形状の違いにより、ワーク表面で除去される材料の断面形状が変化するため、さまざまなタイプのねじの製造が可能になる。

その他のねじ製造方法には、内ねじ用タッピング、外ねじ用ダイスねじ切り、ねじ成形、ねじ転造、ねじフライス、研削、ラッピングなどがある。

(2) タッピングとダイスねじ切り

タッピン グとは、タップを用いて穴に内ねじを切る加工であり、ダイスレ ッド加工とは、ダイスを用いてロッドやパイプに外ねじを切る 加工である。
1) 共通ツール
タップとタップレンチ

タップはねじ切り専用の切削工具である。構造が簡単で使いやすく、小径の内ねじ加工に広く用いられている。タップの種類は、歯の大きさによって並目タップと細目タップに、機能によってナットタップ、ダイスタップ、テーパねじタップ、台形ねじタップなどに分類される。

タップ・レンチは、タップの四角い端を握って回転させ、切断するために使用する工具である。
金型とダイ・ストック

ダイスは、外ねじを切るための工具で、固定タイプと分割タイプがある。固定ダイスが一般的で、穴の両端に60°のテーパー部があり、これがダイスの切削部分となり、後方の歯はガイドとして機能します。
ダイストックは金型を保持するための工具で、異なるサイズの金型には対応するダイストックがある。
2) タッピング法

- タッピングを行う前に、下穴を開ける。下穴の直径は、関連マニュアルを参照して選択するか、計算式を使って算出する。
- ネジ山をタップする前に、穴の入り口を面取りして、タップの位置決めと進入を容易にする。
- タップを始めるときは、右手のひらでタップレンチの中央を押し、タップの軸に沿って圧力をかけ、左手で時計回りに回転させる。
- 垂直度をチェックする。タップが1~2回転したら、四角を使ってタップと穴の端面の直角度をチェックする。垂直でない場合は、すぐに修正する。目視で確認し、垂直であれば四角定規を使って2方向から確認することができる。
- ネジ山をタップします。タップが切り始め、ガイド部がワークに入ったら、力を入れずにハンドルを平行に回転させます。このとき、1~2回転するごとに1/4回転逆回転させ、切りくずを砕いてネジ山を傷つけないようにする。切削油剤を加えながらタップを行う。
- 切りくずの除去。ブラインド・ホールの場合、タップに深さをマークするだけでなく、頻繁にタップを引き抜いて切りくずを取り除く必要がある。


3) 外ねじのねじ切り方法
- まずロッドの直径を決める。大きすぎるとネジ切りが難しく、小さすぎるとネジ山ができない。計算式で求めることができる。
- 最初のねじ切り技術は、内ねじのタッピングと同じである。
- ねじ切りする際は、ダイスをロッドに対して垂直に保つ。ロッドを30°から45°の角度で面取りする。やり方はタッピングと同じ。回転を始めるときに圧力をかける。ガイド部が切り込んだら、ハンドルを両手で平行に回転させる。頻繁に逆回転させ、切りくずを砕き、切削液を加える。


7.ねじ接続
(1) ボルト接続

通常のボルト接続と精密ボルト接続に分けられる。
1) 通常のボルト接続の場合、接続される部品はそれほど厚くない。ボルトには頭部があり、貫通穴にはネジが切られておらず、ボルトは貫通穴を通ってナットと嵌合する。組み立て後、穴とボルトの間にはクリアランスがあり、使用中になくなってはならない。構造が簡単で、組み立てと分解が容易で、何度も組み立てることができ、広く使われている。
2) 精密ボルト接続は、組み立て後のクリアランスがなく、主に横荷重に耐える。位置決めにも使用できます。ボルト接続用のリーマ穴(例:H7/m6、H7/n6)を持つ基本的なホールシステムフィットを使用します。
(2) ダブルエンドスタッド接続

ボルトには頭がなく、両端にネジ山がある。組み立ての際、一方の端は接続部品にねじ込まれ、もう一方の端にはナットが取り付けられる。頻繁に分解する必要があり、接続部品の一方が厚い場合に適している。分解時には、接続部品からスタッドのねじを外さずに、ナットのみを取り外す必要があります。
(3) ネジ接続
連結された部品の一方(上部にねじ穴がある)が頻繁な組立・分解を必要とせず、一端にねじ頭があり、ナットを必要とせず、比較的小さな荷重に耐える場合に適している。
(4) セットスクリュー接続

締め付け後、ねじの端が他の部品の表面を押すか、部品の対応する切り欠きに回転して、部品の相対位置を固定する。小さな軸力やトルクを伝達することができる。
8.ネジロック
ねじ接続部を揺れ、衝撃、振動のある場所で使用すると、ねじが緩むことがあります。人体の安全に関わる場所では、これらの接続部を固定する必要があります。安全規則により、自動車、エレベーター、鉄道、ケーブルカー、扇風機などではロックが必要です。主な緩み止め対策は以下の通り。
(1) フリクションロック

最も広く使われている緩み止め方法。この方法は、ねじ対の間に外力によって変化しない法線圧力を発生させ、ねじ対の相対回転を防ぐ摩擦力を発生させる。この法線圧は、ねじ対の軸方向圧縮または同時双方向圧縮によって達成できるが、ゆるみを完全に防止することはできない。弾性ワッシャー、ダブルナット、セルフロックナット、ナイロンインサートロックナットなどの方法は、すべて摩擦ロックに属します。
(2) メカニカル・ロック

ストッパーを使用して、ねじペアの相対回転を直接制限します。接続は、ストッパーを取り外した後でなければ分解できない。方法としては、スロット付きナット、コネクティングワイヤー、ロッキングワッシャーを使用したスプリットピンがある。
(3) 永久ロック

締め付け後、ピーニング、溶接、接着剤による接合などの方法で、ねじ対の運動対の特性を失わせ、取り外し不可能な接続にする。ボルトは一度しか使用できず、分解が非常に難しいという特徴がある。分解するには、ねじ対を破壊しなければならない。
XII.ガス切断
ガス切断とは、酸素と混合した可燃性ガスの燃焼によって発生する炎を利用して材料を熱切断することで、酸素切断または火炎切断とも呼ばれる。ガス切断は、様々な産業分野で一般的な金属熱切断方法である。手動ガス切断は柔軟で便利であり、工場での散発的な材料切断、廃棄物解体、設置、撤去作業に不可欠な加工方法である。
1.ガス切断工程
切断と成形は、ガス燃料-酸素炎を使って材料を切断する。その条件は、材料がその融点以下で着火燃焼できることである。炭素含有量が1.6%(質量分率)以下の鋼は、融点が1500℃と酸化物の融点1350℃より高いため、酸化物だけが溶けて溶融シームから吹き出すため、この条件を満たすことができる。
鋼の炭素含有量が増加すると、その融点は低下する。炭素含有量が1.6%(質量分率)を超える鋼は、ガス切断には適さない。
2.カッティングトーチ


切断トーチの機能は、酸素とアセチレンを比例的に混合して予熱炎を形成し、高圧の純酸素を被切断物に噴射して、切断金属を酸素噴流中で燃焼させることである。酸素噴流は燃焼生成物の溶融スラグを吹き飛ばし、切断面を形成する。切断トーチは、被加工物をガス切断するための主要な工具である。
3.切断作業
ノズルからワークまでの距離を決め、フレームコーンがワークに触れないようにします。切断点が白熱に達したら、酸素バルブを開いて切断を開始する。
切削速度ノズルの距離、切断ノズルと加熱ノズルのサイズ、酸素圧力は、材料の厚さに基づいて選択されるべきである。
4.適用範囲
ガス切断は主にコンテナ製造、鉄骨構造物製造、機械製造、造船、廃棄物処理、パイプライン敷設などに適用される。
XIII.溶接

溶接は、加熱、加圧、またはその両方によって2つの被加工物間の原子結合を実現する加工・接合方法である。溶接は広く使われており、金属と非金属の両方に適用できる。
溶接技術は主に金属母材に適用される。一般的な方法にはアーク溶接がある、 TIG溶接CO2 シールド溶接、酸素-アセチレン溶接、 レーザー溶接、エレクトロスラグ加圧溶接、その他多数。プラスチックのような非金属材料も溶接できる。40以上の金属 溶接方法主に、融接、圧接、ろう接の3つに分けられる。

1.融接
溶融溶接は、ワークピースの界面を溶融状態ま で加熱し、圧力をかけずに溶接を完了させる方法 である。溶融溶接では、熱源が溶接される2つのワークの界面を急速に加熱・溶融し、溶融池を形成する。溶融池は熱源とともに前進し、冷却後、2つのワークピースを1つにつなぐ連続溶接シームを形成する。

溶融溶接工程では、高温の溶融池に大気が直接接 触すると、大気中の酸素が金属や各種合金元素を酸化させ る。また、溶融プールに入り込んだ大気中の窒素や水蒸気は、その後の冷却過程で溶接部に気孔、介在物、亀裂などの欠陥を形成し、溶接部の品質と性能を劣化させる。
溶融溶接はさらに、電気アーク熱を熱源とする消耗電極溶接と非消耗電極溶接に分けられる。
2.圧接
加圧溶接とは、加圧条件下で2つのワークを固体状態で原子結合させる溶接法であり、固体溶接とも呼ばれる。一般的に使用される圧接法は抵抗突合せ溶接で、2つのワークの接続端に電流を流すと抵抗が高くなり温度が上昇する。塑性状態まで加熱されると、軸圧下で接合される。圧接の特徴は、溶加材を加えずに加圧しながら溶接することである。
3.ろう付け

ろう付けは、被加工材よりも融点の低い金属材料をろう材として使用する方法である。ワークとろう材は、ろう材の融点より高くワークの融点より低い温度に加熱される。液状ろう材を利用して被加工材を濡らし、界面ギャップを埋め、被加工材との相互原子拡散を実現し、溶接を行う。
XIVリベッティング
1.原則
リベッティングは、軸力を使って部品のリベット孔内のリベット・シャンクを太くし、リベット・ヘッドを形成して2つ以上の部品を連結するプロセスである。

(1) コールドリベット
室温のリベットで行うリベット打ち。鋼製リベットを使用する場合は、リベットの塑性を改善するために、冷間リベット打ちの前にまず焼きなまし処理を受けなければならない。
(2) ホットリベット
ホット・リベッティングは溶接ではなく、温度を上げることによって2つの金属の接続部分を変化させたり、あるいは溶かしたりする。
(3) リベット材料
強度が340~520MPaのキルド鋼やセミキルド鋼、銅、銅合金、アルミニウム、プラスチックから作られ、一定の可塑性と靭性を持っていなければならない。錆を防ぐため、可能な限り母材に近い材料を選ぶこと。
2.リベット工程

リベット打ち工程穴あけ - (逆シンク) - (バリ取り) - リベット挿入 - バッキング (バッキング・バー) - リベット保持 - リベット・マシンで成形 (または手動 - アップセット - シックニング - ドーム形状に成形)。
3.リベット接合

リベット接合は、部品間の接合形式である。ラップ・ジョイントは、重なり合った鋼板のリベット接合である。カバー・プレート・リベット接合は、部品の端を合わせ、1枚または2枚のカバー・プレートでリベット接合することを指す。


リベットは単列または多列に配置することができ、多列は平行または千鳥配置となる。


- 特殊なリベット方法 - フラッシュリベット。薄板リベッティングに使用され、様々なリベッティングフォームがある。
- 中空リベット。薄い板、厚紙、革などのリベット打ちに使用できる。
- 片面リベット方式。リベット打ちが片側からしかできない場所で、パンチ付き中空リベットやホット・リベット・リベットを使用して使用する。
4.リベットの欠陥

欠陥はリベット接合強度とリベット接着を低下させる。主なリベット打ちの欠陥は、ずれたドリル穴、曲がったリベット、特大のリベット穴、緩すぎたりきつすぎたりするリベット、短すぎるリベットなどである。
XV.接着(金属、プラスチック)
接着とは、接着剤層を介して2つのワークを接合することを指す。


金属接合技術とは、金属補修剤を用いて金属と金属、金属と非金属の固体界面を接続する技術である。接合力は物理的接合力と化学的接合力の和である。接合界面は応力を伝達するだけでなく、密封し腐食を防ぐこともできる。表面と全体的な構造は、旋盤加工、ドリル加工、フライス加工などの機械的加工を施すことができる。

1.接着剤の分類
接着剤には多くの種類があるが、通常は以下のように分類される:
(1) 素材ソースによる分類
1) 天然接着剤
デンプン、タンパク質、デキストリン、動物接着剤、シェラック、皮接着剤、ロジンなどの生物接着剤、アスファルトなどの鉱物接着剤など、自然界に存在する物質に由来する。
2) 人工接着剤
水ガラスのような無機接着剤、合成樹脂や合成ゴムのような有機接着剤など、製造された物質である。
(2) 利用特性による分類
1) 水溶性接着剤
水を溶媒として使用する接着剤で、主にデンプン、デキストリン、ポリビニルアルコール、カルボキシメチルセルロースなどが含まれる。
2) ホットメルト接着剤
加熱溶融して使用する固形接着剤です。一般に熱可塑性樹脂が使用でき、例えばポリウレタン、ポリスチレン、ポリアクリレート、エチレン-酢酸ビニル共重合体などが挙げられる。
3) 溶剤系接着剤
シェラック、ブチルゴムなど、水には溶けないが特定の溶剤には溶ける接着剤。
4) エマルジョン接着剤
ポリ酢酸ビニル樹脂、アクリル樹脂、塩素化ゴムなど、水に懸濁することが多い。
5) 無溶剤液体接着剤
これらはエポキシ樹脂のような室温で粘性のある液体である。
2.接着の原理
接着剤の効果は、接着剤とワークの間の接着力と接着剤内の凝集力に依存する。
3.接着作業
(1) 前処理
接着剤分子が素材に密着できるように、接着面は汚れや油脂を取り除き、十分にクリーニングする必要がある。接着面積を増やすために、サンドペーパー、サンドブラスト、酸エッチングなどで表面を粗くすることもできる。
(2) 接合プロセス
接着には、被接着部品がしっかりと配置されている必要がある。粗い面は両面に接着剤と硬化剤を塗布し、滑らかな面は片面に塗布すればよい。接着剤層の厚さは25~100μmが望ましい。接着した2つの部品は、完全に硬化する前に動かしてはならない。エポキシ樹脂を使用する場合、それ自体の圧力で十分であるため、外部からの圧力は必要ない。
4.結合構造と結合形態


粘着層は引き抜き工具で引き裂くことができる。うまくいかない場合は、引っ張る前にブローカーで約120℃に加熱する。
XVI.キーとピンの接続
1.キーコネクション
キーは、シャフトとシャフト上の伝達部品(ギア、プーリーなど)を接続してトルクを伝達するために使用される標準部品です。2つの側面と底面が被加工物に接触するシンプルな構造です。
(1) パラレルキー
1) 共通パラレルキー
一般的なパラレルキーの種類

キーは標準部品である。一般的な平行キーは3種類に分けられる:A(丸頭)、B(角頭)、C(半円頭)。
共通パラレルキーのマーキング
キーの公称寸法はシャフトの直径である。一般的な平行キーの寸法とキー溝の断面寸法は、シャフトの呼び径に基づく関連国家規格に記載されている。
一般的な並列キーのマーキングにおいて、Aタイプの並列キーは「A」を省略できるが、BタイプとCタイプの並列キーは「B」または「C」をマーキングしなければならない。
共通パラレルキーの接続

一般的な平行キーの表示例:幅b=16mm、高さh=10mm、長さL=100mmのBタイプ平行キーの場合、次のように表示される:GB/T 1096 キーB16×10×100
2) フェザーキーとスライドキー
フェザーキー
シャフトに固定され、動作中にシャフト上の部品が軸に沿ってスライドできるようにする。
スライドキー


ハブ内に固定され、運転中はハブとともにシャフト上のキー溝に沿って動く。
(2) ウッドラフキーの接続

ウッドラフキーも標準的なキーであり、その寸法はシャフトの呼び径に基づいて関連規格に記載されている。
ウッドラフキーの刻印例:幅b=6mm、高さh=10mm、直径D=25mmのウッドラフキーは、次のように表示されます:GB/T 1099.1
キー 6×10×25
(3) ウェッジ・キー

ウェッジキーは一般的なウェッジキーとフック付きウェッジキーに分けられる。一般的なウェッジキーは、さらにタイプA、B、Cに分けられる。作動中、ウェッジキーは上面と下面、シャフトとホイールの溝の間の圧縮によって発生する摩擦によって運動と動力を伝達する。
ウェッジキーのマーキングの例:
幅 b=16mm、高さ h=10mm、長さ L=100mm の一般的なタイプ A のウェッジキーは、次のように表示されます:GB/T 1564 キー16×100
幅b=16mm、高さh=10mm、長さL=100mmの一般的なタイプBのウェッジキーは、次のように表示されます:GB/T 1564 キーB16×100
幅b=16mm、高さh=10mm、長さL=100mmの一般的なタイプCのウェッジキーは、次のように表示されます:GB/T 1564 キーC16×100
(4) スプライン

1) 概要
シャフトとハブ上の複数の突起と溝によって形成される軸連結部品。スプライン接続は、内スプラインと外スプラインで構成される。インターナルスプラインもエクスターナルスプラインも多歯部品で、インターナルスプラインは内側の円筒面に、エクスターナルスプラインは外側の円筒面にある。スプラインは標準的な構造です。
2) スプラインの特徴

- 溝が浅いため、歯の根元への応力集中が小さく、その結果、シャフトの弱体化とハブの強度が低下しにくい。
- 歯数が多いほど総接触面積が大きくなり、より大きな荷重に耐えることができる。
- 高速機械や精密機械にとって重要な、シャフト上の部品のセンタリングが向上する。
- ダイナミックなコネクションにとって重要な良いガイダンスだ。
- 研削方法は、加工精度と接続品質を向上させるために使用できる。
- 製造工程は比較的複雑で、特殊な設備を必要とする場合もあり、コスト高につながる。
3) 適した用途
高いセンタリング精度、大きなトルク伝達、頻繁な摺動を必要とする接続。高い同芯度が要求される高速シャフトや機構に適しています。
2.ピン接続
(1) ピンの機能と分類
ピンは2つの部分の穴を通り、主に位置決め、接続、ガイドの機能を果たす。

構造別には、円柱ピン、テーパーピン、溝付きピン、ピン軸、コッターピンに分類され、機能別には、位置決めピン、連結ピン、安全ピンに分類される。
(2) ピン接続

位置決めにピンを使用する場合、ピンの取り外しを容易にするため、穴は可能であれば貫通穴とする。貫通穴が使用できない場合は、内ねじ付きのピンを使用する。テーパーピンの場合、テーパー面を適切にフィットさせるため、ピン先端とテーパー穴の底の間に隙間が必要である。
XVII.集合の知識
1.組立概要
(1) 組み立てコンセプト
製品は複数の部品やコンポーネントから構成される。指定された技術的要件に従って、複数の部品を部品に結合する、あるいは複数の部品と部品を製品に結合する労働過程を組立と呼ぶ。前者を部品組立、後者を一般組立という。一般的には、組立、調整、検査・試験、塗装、梱包などが含まれる。


1) 組立ユニット
効率的な組み立て作業を保証するため、機械は通常、独立して組み立てられる複数の組み立てユニットに分割される。
パーツはマシンを構成する最小単位である。セットは、1つ以上のパーツをベースパーツに組み立てることで形成される。グループは、複数のパーツやセットをベースパーツに組み付けることで形成される。コンポーネントは、複数のグループ、セット、パーツをベースパーツに組み立てることで形成される。機械や製品は、部品、グループ、セット、パーツをベースパーツに組み立てることによって形成される。
2) 組立工程

組立工程は、部品、セット、グループ、コンポーネント間の特定の位置関係を確立する。
(2) 組立精度
組立精度とは、組立工程の品質指標である。寸法精度、相対運動精度、相互位置精度、部品と部品の接触精度が含まれます。部品と部品の間の寸法精度には、はめあい精度と距離精度が含まれます。
一般に、組立精度は、関連する構成部品の加工精度によって保証される。組立精度が要求される品目や、多数の部品から構成される部品では、組立精度を部品の加工精度で直接保証しようとすると、部品ごとに非常に高い加工精度が要求され、加工が困難になったり、加工が不可能になったりします。
(3) 組立寸法チェーン
機械の組立関係において、関連部品の寸法や相互の位置関係によって形成される寸法連鎖を組立寸法連鎖という。組立寸法連鎖における組立精度がクロージングリンクであり、関連部品の設計寸法が構成リンクである。
1) リニア・ディメンション・チェーン

長さ寸法を平行リンクで構成した組立寸法チェーン。図に示すように、歯車はシャフトに緩く取り付けられ、組立寸法チェーンAを確立する。1, A2, A3, A4, A5一定のギャップA0 ギアと止め輪の間
2) 角度寸法チェーン

角度、平行度、垂直度などで構成される組立寸法チェーン。角度寸法連鎖は、α、a₂、軸O-OとA-Aの平行度から構成され、旋盤組立に適正な角度を確保する。
3) 平面次元チェーン
ある角度関係を形成する長さ寸法と、それに対応する角度寸法で構成され、すべて同一平面内または平行平面内にある。
4) 空間的次元の連鎖
これは、空間内の交差する平面に位置する直線的な寸法と角度的な寸法で構成されている。
2.組立作業の主な内容
(1) クリーニング
1) 目的
部品に付着した埃、切粉、油汚れを除去し、部品に一定の防錆性を付与する。
2) 方法
拭き取り、浸漬、スプレー、超音波振動など。
3) 洗浄液
よく使われるのは、灯油、ガソリン、アルカリ溶液、化学洗浄液など。
(2) 接続
一般的な接続方法と形式
接続方法 | 分類 | 実施方法 |
固定接続 | 取り外し不可 | 溶接、リベット、エキスパンション・フィッティング、干渉フィット、 鋳造接続、接着接続、プラスチック材料の圧縮成形など。 |
取り外し可能 | ネジ接続、キー接続、ピン接続など。 | |
可動接続 | 取り外し不可 | ボールベアリング、ローラーベアリング、オイルシールなど |
取り外し可能 | 円筒面、円錐面、球面、ネジ面 クリアランス・フィットとその他の素材による達成方法 |
(3) アライメント、調整、フィッティング
1) アライメント
様々な部品間の相対位置のアライメントとそれに対応する調整。アセンブリにおける調整方法と修正方法には、アライメントの内容が含まれる。部品に互換性がある場合や 組立備品 精度を確保するために、アライメントは必要ない。アライメント作業は、大型の動力機械装置でより一般的に使用される。
2) 調整
関連部品やコンポーネント間の相対位置の調整作業を指す。
3) フィッティング
いくつかの部品の合わせ穴あけ、リーマ加工、削り取り、研磨など、組み立て時の追加的なベンチワークや機械加工作業を指す。合わせ穴あけやリーミングは、アライメントと調整の後に行う。削り取りと研削の目的は、合わせ面の接触面積を増やし、接触精度を向上させること。
3.集会組織の形態と構造
(1) 集会の組織形態

組み立て機械、作業場、組み立て作業者間の協力関係の違いから、固定組み立てと移動組み立て、あるいは集中工程と分散工程に分けられる。
1) 集中プロセス

組み立て全体の工程は1つだけで、すべての組み立て作業は同じ作業場所で1つの作業者グループによって完了する。集中工程は、より高い技術力を持つ作業員、より広い生産エリア、より長い組立サイクルを必要とし、単品生産、大型機械、試作品、修理工場での組立作業などに適している。
2) 分散プロセス
組立作業工程は分散化され、1台の機械の組立は複数の異なる作業者グループによって完成され、各グループは作業タスクの特定の部分のみを完了する。分散された工程は、作業者の専門化、より良い専門化された治具と作業場、同時組立、およびより高い生産性を可能にする。
(2) 接触面と接合面構造の合理性


- 2つの部品は、同じ方向に1つの接触面または接合面しか持つことができない。
- シャフトのショルダー部にツールリリーフ溝、または穴部に面取りを加工する。
- 良好な接触を確保するためには、接触面を機械加工する必要があり、加工面積を合理的に削減し、コストを下げ、接触条件を改善する。
(3) スレッド接続の合理的構造




- ねじ接続の構造は合理的でなければならない。
- 貫通穴の直径はスクリューシャフトの直径より大きくする。
- レンチを操作するためのスペースを残しておく。
- ネジの取り付けと取り外しのためのスペースを残しておくこと。
- 穴を追加するか、ダブルボルトを使用する。
(4) 転がり軸受の固定装置

転がり軸受を使用する場合、転がり軸受の内輪と外輪を軸または機械本体に固定するために、その応力状態に応じた一定の構造を採用する必要があります。転がり軸受は、使用温度の変化により焼付きが発生することを考慮し、一定のアキシアルクリアランスを確保する必要があります。
(5) シーリング装置

ダストやデブリのベアリングへの侵入、潤滑油の漏れ、バルブやパイプラインからのガスや液体の漏れを防ぐため、通常は適切な密閉装置が採用される。その際 メカニカルアセンブリシール位置が不適切であったり、シール材の選定や締め付けが不適切であったり、シール装置の組立工程が要件を満たしていなかったりすると、機械装置内で油漏れ、水漏れ、ガス漏れを起こす可能性があります。
4.組立方法の選択
(1)互換アセンブリ方式
1) 完全互換組立方式
部品の各部寸法が寸法要件に従って製造されている限り、要件を満たす完全な互換アセンブリを達成することができる。
- 利点信頼性の高い組立品質、シンプルなプロセス、高効率、自動化が容易、便利な製品の修理。
- デメリット組立精度の要求が高い場合、特に部品点数が多い場合、部品製造が難しくなり、加工コストが高くなる。
- 適用範囲バッチ生産および大量生産のアセンブリ。
2) 不完全互換組立方式
部品を加工しやすくするために、部品の製造公差を適切に拡大する。
- 利点部品の製造公差が大きい、部品製造コストが低い、組立工程がシンプル、生産性が高い。
- 欠点:組立後、ごく少数の製品が指定された組立精度要件を満たさないことがあり、対応する手直し措置が必要となる。
- 適用範囲高精度が要求され、部品点数が多い機械の量産組立。
(2) 選択組立方式
1) 直接選抜方式
組み立ての際、作業員は、組み立て精度の要求を満たすために、多くの待組み立て部品から適切な部品を直接選択する。
2) グループ・アセンブリー方式
部品加工の際、各部品の公差は、完全互換方式に比べて数倍に拡大されることが多く、経済的な精度で寸法を加工することができる。その後、部品は実際に測定された寸法に従ってグループ化され、対応するグループごとに組み立てられて、組立精度要件を満たす。
- 利点部品の製造精度は高くないが、組み立て精度は非常に高い。
- 欠点:部品の測定、グループ分け、保管のための追加作業が必要。
- 適用範囲部品点数は少ないが、特に高い組立精度が要求される機械の量産組立。
3)化合物選択的組立て法
グループ・アッセンブリ方式と直接選択方式を組み合わせたもので、加工後に部品を測定してグループ化し、組み立て時に対応するグループ内で選択する。
(3) フィッティング組立方法
バッチ生産や単品小ロット生産では、組立精度の要求が高く、部品点数が多い場合、組立に互換性方式を用いると、部品の公差要求が厳しくなりすぎ、加工が困難になる。また、部品点数が少なく、品種が多いため、選択組立法も難しい。この場合、組立精度を確保するためにはめあい方式が用いられる。
1) 個別組立方式
マルチコンポーネント組立寸法チェーンでは、固定部品がフィッティングピースとして選択されます。組立中に、金属層を除去することによって寸法を変更し、組立精度要件を満たします。
2) 複合加工とフィッティング法
2つ以上の部品が組み合わされた後、一緒にはめ込まれます。組み合わされた寸法は1つの部品と見なすことができるため、組立寸法チェーンの部品数を減らし、それに伴ってはめ込みの労力も減らすことができる。主に単品生産や小ロット生産に用いられる。
3)自己加工フィッティング法
工作機械製造では、高い組み立て精度が要求されるにもかかわらず、適切なフィッティングピースがない部品がある。最終的な組み立ての際、工作機械そのものを使って特定の部分を加工し、組み立て精度を確保することができる。
(4) 調整組立方法
組立精度要求を閉ループとして確立された組立寸法チェーンでは、調整リンク以外のすべての部品は経済的な加工精度で製造される。
1)可動調整方式
摩耗や熱変形などによる誤差は、機械内の調整ピースを調整することで、いつでも補正することができ、元の組み立て精度に戻すことができる。
利点は、部品の製造精度は高くないが、比較的高い組立精度が得られることである。欠点は、調整機構を追加する必要があり、構造が複雑になることである。生産現場で広く使われている。
2)固定調整方式
組立精度要求を閉ループとして確立された組立寸法チェーンでは、すべての部品は経済的な加工精度で製造されます。クローズドループの寸法変動が限界を超える原因となる部品の製造公差範囲が拡大したため、異なるサイズの固定調整リンクを交換して補正することができ、最終的に組立精度要件を満たすことができます。大量生産と高い組立精度が要求される機械に適しています。
3)エラーキャンセル調整法
機械組立では、組立部品の相対位置を調整して誤差を打ち消すことで、組立精度を向上させることができる。
長所は、すべての部品を経済的な加工精度で製造できる一方、比較的高い組立精度を実現でき、組立効率がはめ込み組立方式より高いことである。欠点は、組立時に誤差の大きさと方向を測定し、値を計算する必要があるため、補助時間が増加し、生産効率が低下することである。また、作業者に高い技術力が要求される。そのため、単品小ロット生産や精密工作機械生産にしか適していない。