
품질에 영향을 미치는 주요 요인 레이저 커팅 레이저 커팅 시스템 성능의 영향과 레이저 커팅 파라미터의 영향이라는 두 가지 범주로 크게 나눌 수 있습니다. 전자는 레이저를 구매하고 레이저 절단 시스템을 구축할 때 고려해야 하며, 후자는 레이저 절단 과정에서 파라미터를 선택하고 최적화하는 방법과 관련이 있습니다. 레이저 커팅 프로세스.
레이저 커팅 시스템 성능이 절단 품질에 미치는 영향
빔 모드
빔 모드가 낮을수록 초점 후 스폿 크기가 작아지고, 복사 조명이 커지고, 커프가 좁아지고, 절단 효율과 표면 품질이 높아집니다. 그림 8-8은 절단 표면의 거칠기에 대한 두 가지 빔 모드의 영향 곡선을 보여줍니다. TEM 사용00 모드 레이저로 2mm 두께의 판재를 절단하는 경우, 절단 표면 거칠기 Rz 는 0.8μm에 불과하여 매우 부드러운 수준을 달성합니다.
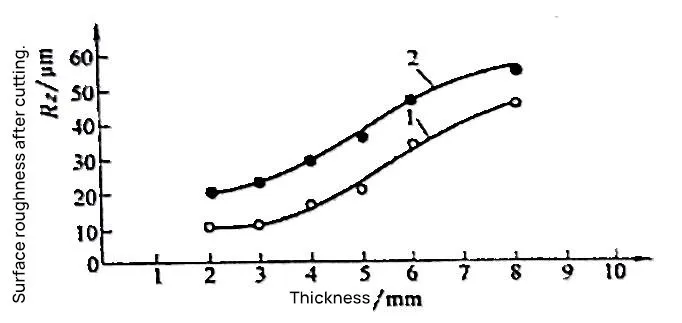
- 1-TEM00
- 2-TEM01
TEM을 사용한 커팅 품질01 모드가 약간 더 나쁘지만 여전히 좋은 수준을 유지합니다. 그림 8-9는 두 가지 빔 모드가 절단 속도에 미치는 영향 곡선을 보여줍니다. 그림 8-9에서 볼 수 있듯이 절단 2mm 두께의 스테인리스 강판을 500W TEM00 모드 레이저로 절단할 경우 절단 속도는 2.0m/min에 달하지만, TEM01 모드 레이저를 사용하면 절단 속도는 1.0m/min에 불과합니다.
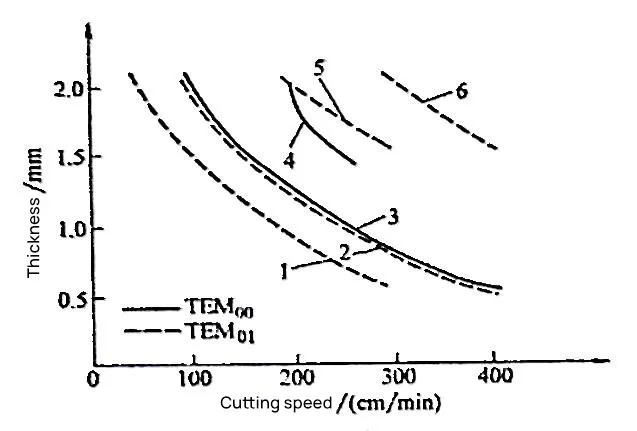
- 1, 3-300W
- 2, 4-500W
- 5-800W
- 6-1000W
- 참고: 자료: SUS304 스테인리스 스틸.
따라서 더 나은 절단 품질과 더 높은 절단 효율을 얻으려면 TEM을 선택하는 것이 가장 좋습니다.00 모드 레이저 또는 적어도 TEM보다 높지 않은01 모드로 설정합니다. TEM보다 높은 모드의 레이저01 절단 품질을 보장할 수 없으므로 사용해서는 안 됩니다.
빔 편광
레이저 빔의 편광은 다음과 같은 품질과 효율성에 큰 영향을 미칩니다. 레이저 커팅. 선형 편광을 절단에 사용하면 빔의 편광 방향에 따라 절단 방향이 변경되고 절단 날과 레이저의 흡수 비율이 변경되어 레이저 절단 효과에 영향을 미칩니다.
1) 절단 방향이 편광 방향과 평행하면 그림 8-10a와 같이 레이저에 대한 절삭 날의 흡수율이 가장 높으므로 커프가 좁고 절단의 직각도와 거칠기가 낮으며 절단 속도가 빠릅니다.
2) 절단 방향이 편광 방향에 수직 인 경우 레이저에 대한 절단면의 반사 비율이 가장 높고 흡수 비율이 가장 작으며 측면 흡수 비율이 증가하므로 그림 8-10b와 같이 절단 속도가 감소하고 절단이 넓어지며 절단 표면의 거칠기 값도 증가합니다.
3) 절단 방향이 편광 방향과 비스듬한 경우, 레이저에 대한 흡수율이 가장 높은 방향도 절단 방향과 비스듬해져 그림 8-10c 및 8-10d와 같이 커프 바닥이 기울어집니다.
4) 절단 방향의 변화로 인한 커프의 모양과 절단 표면의 품질 변화를 방지하려면 절단에 원형 편광을 사용해야합니다. 원형 편광의 전기 벡터 진폭은 모든 방향에서 동일하므로 절단 방향의 변화에 따라 절단 날과 레이저의 흡수 비율이 변경되지 않으며 그림 8-10e와 같이 커프가 균일하고 깔끔합니다.
레이저에서 출력되는 선형 편광을 원형 편광으로 변환하려면 빔의 출구에 원형 편광기를 추가해야 합니다.
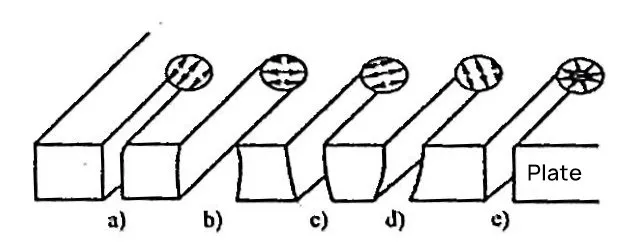
노즐 및 가스 흐름
보조 가스의 압력과 흐름은 노즐의 구조 및 크기와 관련이 있으며, 둘 다 품질에 큰 영향을 미치고 레이저 절단 속도.
(1) 노즐 구조
그림 8-11에는 다양한 구조의 레이저 커팅 노즐이 나와 있으며, 그 중 그림 8-11a에 표시된 원뿔형 노즐이 가장 널리 사용됩니다.
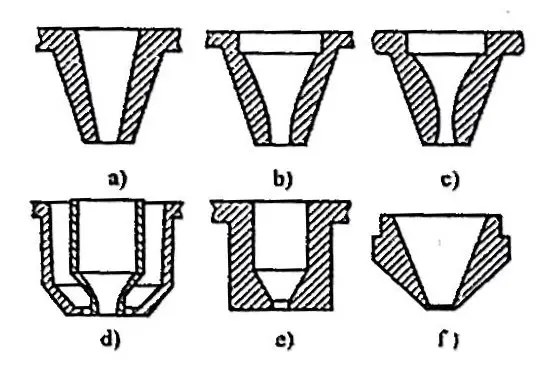
(2) 노즐 조리개
노즐 조리개의 크기는 먼저 구멍 내부의 빔이 노즐의 내벽에 닿지 않도록 빔이 원활하게 통과할 수 있도록 해야 합니다. 조리개가 작을수록 빔의 시준이 더 어려워지므로 조리개가 너무 작아서는 안 됩니다.
또한 특정 보조 가스 압력 하에서는 노즐 조리개에 대한 최적의 범위가 있습니다. 조리개가 너무 작거나 너무 크면 보조 가스에 의해 커프에서 용융된 제품의 간격이 영향을 받아 절단 속도에 영향을 미칩니다. 그림 8-12 및 8-13은 노즐 구경이 절단 속도에 미치는 영향을 보여줍니다. 절단 속도 특정 레이저 출력과 보조 가스 압력 하에서 2mm 두께의 저탄소 강판을 절단합니다.
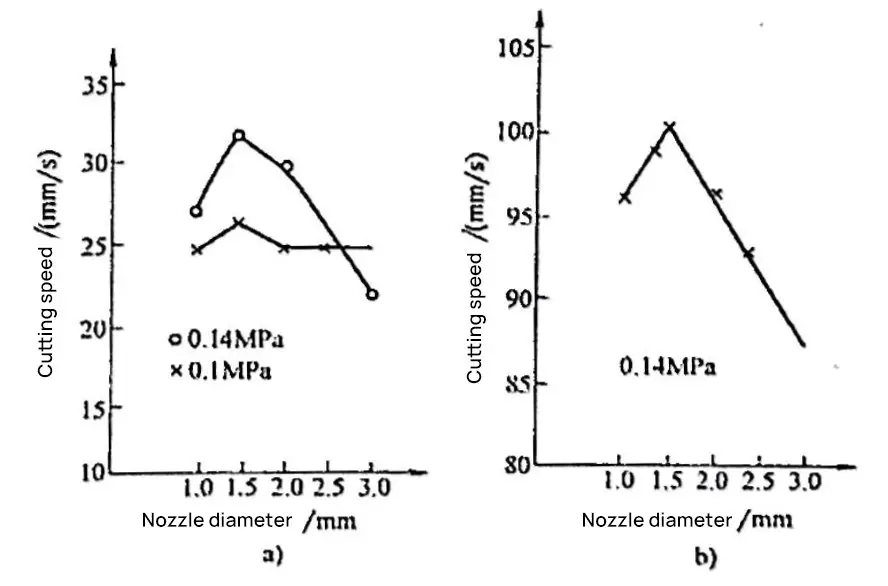
a) 아르곤
b) 산소
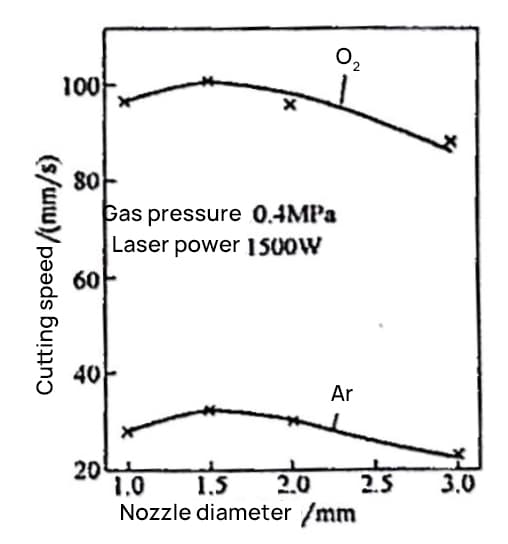
그림 8-12 및 8-13에서 볼 수 있듯이 최대 절단 속도를 달성하기 위한 최적의 노즐 조리개 값이 있습니다. 보조 가스로 산소를 사용하든 아르곤을 사용하든 이 최적 값은 약 1.5mm입니다. 절단하기 어려운 경질 합금에 대한 레이저 절단 테스트에서도 그림 8-14와 같이 최적의 노즐 조리개 값이 위의 결과와 매우 근접한 것으로 나타났습니다.
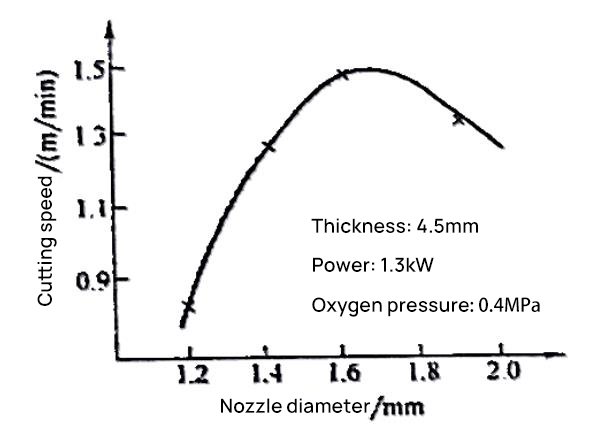
노즐 조리개는 그림 8-15와 같이 커프의 폭과 열 영향 영역의 크기에도 영향을 미칩니다. 그림 8-15에서 볼 수 있듯이 조리개가 커질수록 커프가 넓어지고 열 영향 영역이 좁아집니다. 열 영향 영역이 좁아지는 주된 이유는 절단 영역의 모재에 대한 보조 가스 흐름의 냉각 효과가 향상되기 때문입니다.
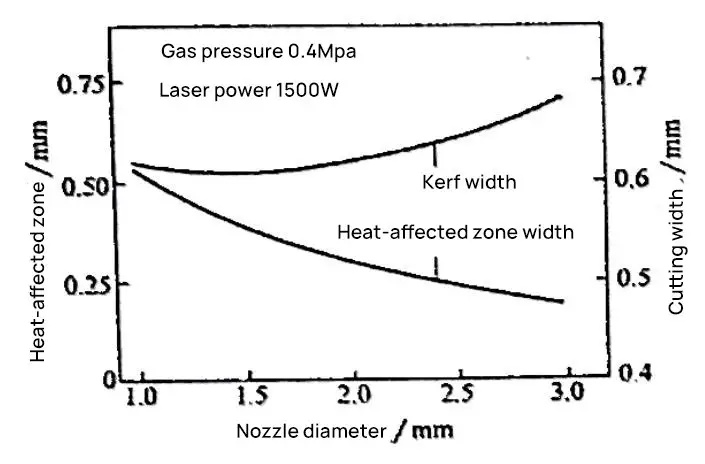
(3) 노즐 가스 압력
가스 압력을 높이면 절단 속도가 향상될 수 있지만 최대 값에 도달한 후에는 압력이 더 증가하면 절단 속도가 감소합니다.
그림 8-16 및 8-17에서 볼 수 있듯이 최대 절단 속도는 레이저 출력과 공작물 판의 두께에 따라 달라집니다. 보조 가스 압력이 높으면 절단 속도가 감소합니다. 이러한 감소의 원인은 높은 기류 속도가 레이저 작용 영역에 미치는 냉각 효과뿐만 아니라 기류의 간헐적 충격파가 레이저 작용 영역과 간섭하기 때문일 수 있습니다.
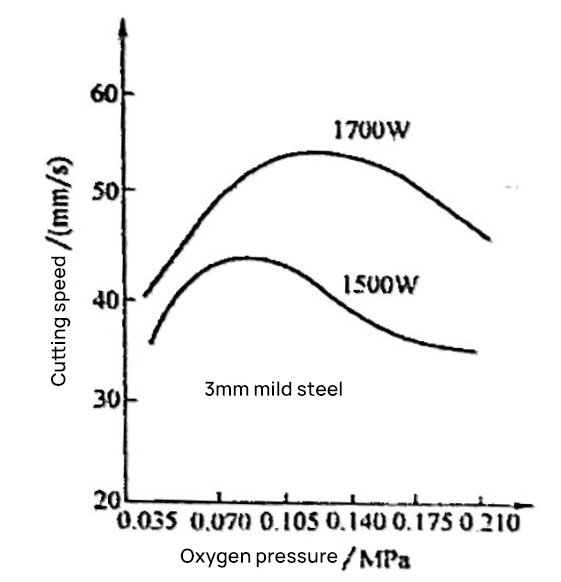
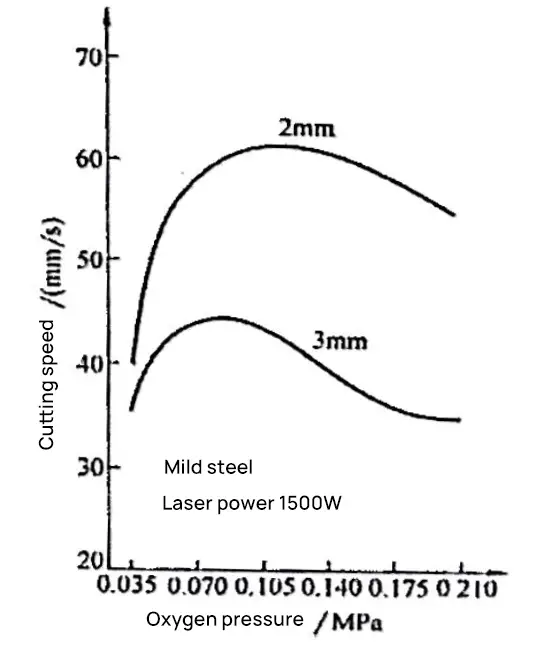
기류에 고르지 않은 압력과 온도가 존재하면 기류 필드의 밀도가 변화합니다. SteenWM 등은 높은 가스 압력 하에서 노즐 바로 앞의 공작물 표면에 밀도 구배 필드가 존재하며, 그 모양과 크기는 가스 압력, 노즐 끝과 공작물 사이의 거리, 노즐 구경에 따라 달라진다는 것을 측정했습니다.
이 밀도 구배 필드는 필드 내의 굴절률 변화를 일으켜 그림 8-18과 같이 레이저 빔의 초점을 방해하여 재초점 또는 빔 발산을 유발합니다. 이러한 간섭은 용융 효율에 영향을 미칠 수 있으며 때로는 모드 구조를 변경하여 절단 품질 저하를 유발할 수 있습니다. 빔이 너무 많이 발산되어 스팟이 너무 커지면 정상적인 절단이 불가능해질 수도 있습니다.
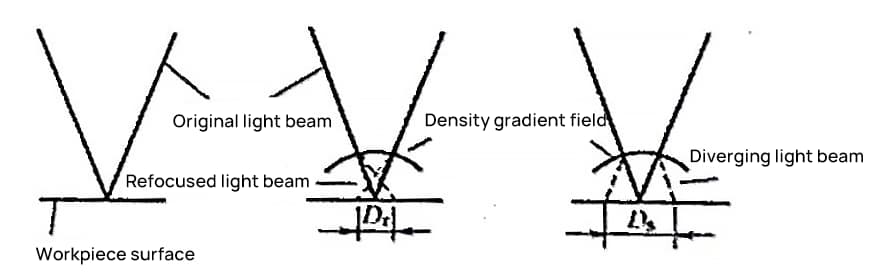
레이저 절단 파라미터가 절단 품질에 미치는 영향
초점 위치가 표면 거칠기에 미치는 영향
초점 위치가 커프의 표면 거칠기에 미치는 영향은 그림 8-19에 나와 있으며, 여기서 그림 8-19의 수평 좌표는 초점 렌즈에서 공작물까지의 거리와 초점 거리의 비율 ab입니다.
그림 8-19에서 커프 표면의 가장 매끄러운 범위가 다음과 같다는 것을 알 수 있습니다: 0.988 <ab< 1.003이므로 일반적인 절단의 경우 일반적으로 초점은 공작물 표면 아래 1mm 이내에 배치됩니다.
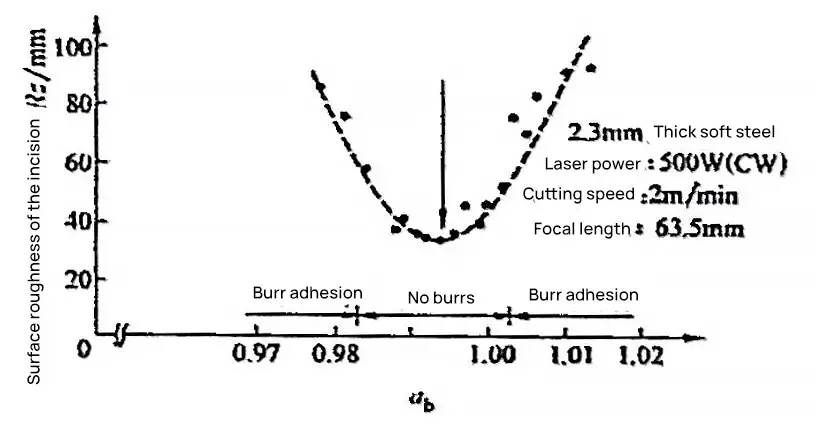
레이저 출력과 절단 속도가 커프 폭에 미치는 영향
그림 8-20 및 8-21과 같이 레이저 출력이 증가하면 커프의 폭이 증가하고 절단 속도가 증가하면 커프의 폭이 감소합니다.
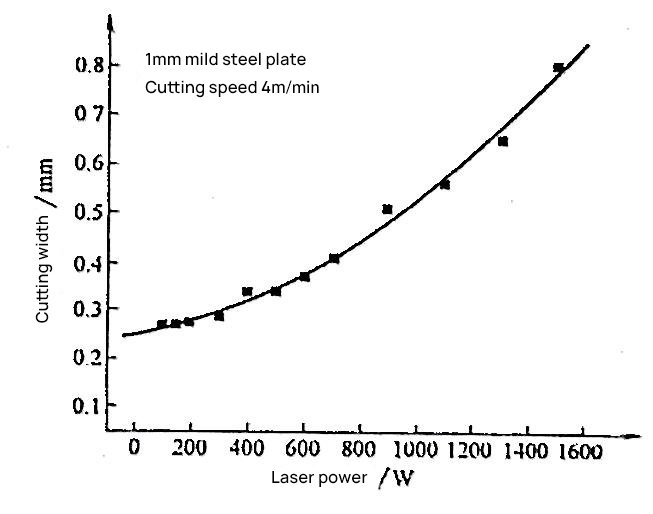
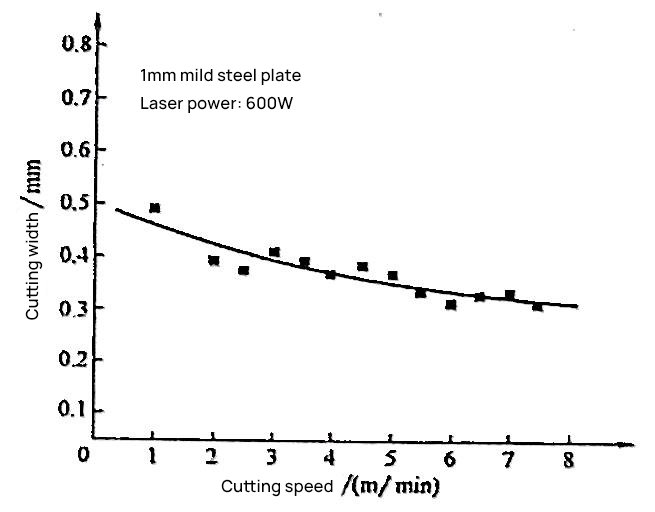
레이저 출력이 표면 거칠기에 미치는 영향
특정 플레이트에서 두께 및 절단 속도레이저 출력의 최적 범위가 있으며, 이 범위 내에서 절단 표면의 거칠기가 가장 작습니다. 최적의 출력 범위에서 벗어나면 거칠기가 증가하고, 출력을 더 높이거나 낮추면 오버번 또는 슬래그 결함이 발생할 수 있습니다.
그림 8-22는 2mm 두께의 저탄소 강판을 50mm/s(즉, 3m/min)의 절단 속도로 절단할 때 레이저 출력과 절단 표면 품질 간의 관계를 하단 가장자리 근처의 거칠기를 측정하는 방법을 사용하여 보여줍니다. 그림 8-22에서 레이저 출력은 슬래그 영역, 결함 없는 영역, 오버번 영역의 세 가지 영역으로 나눌 수 있음을 알 수 있습니다.
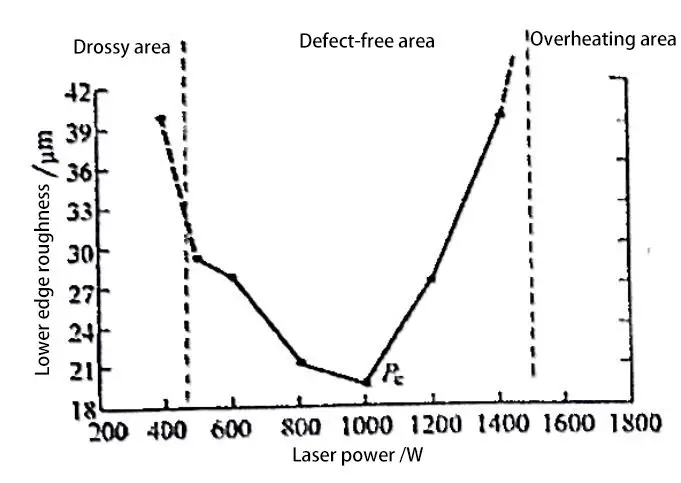
참고: 저탄소 강판 두께는 2mm, v=50mm/s입니다.
1) 레이저 출력이 너무 높아 열 입력이 너무 많으면 공작물의 용융 범위가 고압 가스 흐름이 몰아 낼 수있는 범위보다 커지고 용융 금속이 가스 흐름에 의해 완전히 날아갈 수 없어 오버 버닝이 발생합니다.
2) 레이저 출력이 너무 낮 으면 열이 충분하지 않습니다. 하단 가장자리에 가까울수록 용융 제품의 온도가 낮아지고 점도가 높아져[11] 고압 가스 흐름에 의해 완전히 날아가지 못하고 절단 표면의 하단 가장자리에 남아 슬래그가 발생합니다. 심한 경우 절단이 불가능할 수도 있습니다.
3) 무결점 영역 내에는 절단 표면의 거칠기가 가장 작은 최적의 레이저 출력 범위(그림 8-22에서 약 800~1000W)가 있습니다.
절단 속도가 표면 거칠기에 미치는 영향
특정 판재 두께와 레이저 출력에서는 절단 표면의 거칠기가 가장 작은 최적의 절단 속도가 있습니다.
최적의 절삭 속도에서 벗어나면 거칠기가 증가하고, 절삭 속도를 더 높이거나 낮추면 오버번 또는 슬래그 결함이 발생합니다. [5].
그림 8-23은 레이저 출력 1000W에서 2mm 두께의 저탄소 강판에 대한 절단 속도와 절단 표면 품질 간의 관계를 보여주며, 수직 좌표는 하단 가장자리 근처의 거칠기입니다. 그림 8-23을 보면 절단 속도를 오버번 영역, 결함 없는 영역, 슬래그 영역으로 나눌 수 있음을 알 수 있습니다.
절단 속도가 너무 낮으면 과도한 열 입력으로 인해 오버번이 발생하고, 절단 속도가 너무 높으면 슬래그가 생성되거나 절단이 완료되지 않습니다.
높은 절삭 속도로 인해 슬래그가 발생하는 이유는 불충분한 열 입력과 낮은 온도로 인해 용융물의 점도가 높아지는 것 외에도 높은 절삭 속도로 인해 절삭 전면이 크게 뒤로 기울어져(후행량 증가) 가스 흐름이 용융물을 날려버리는 데 더욱 불리하기 때문입니다.
결함이 없는 영역 내에는 절단 표면의 거칠기가 가장 작은 최적의 절단 속도 v(그림 8-23의 50mm/s)가 있습니다.
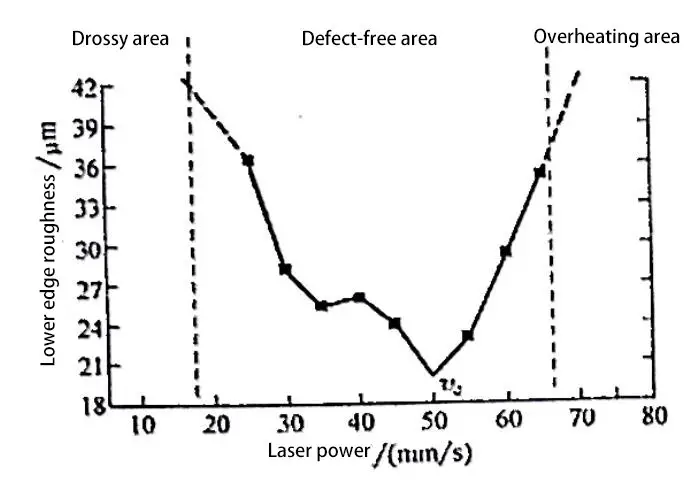
참고: 저탄소 강판의 두께는 2mm, P=1000W입니다.