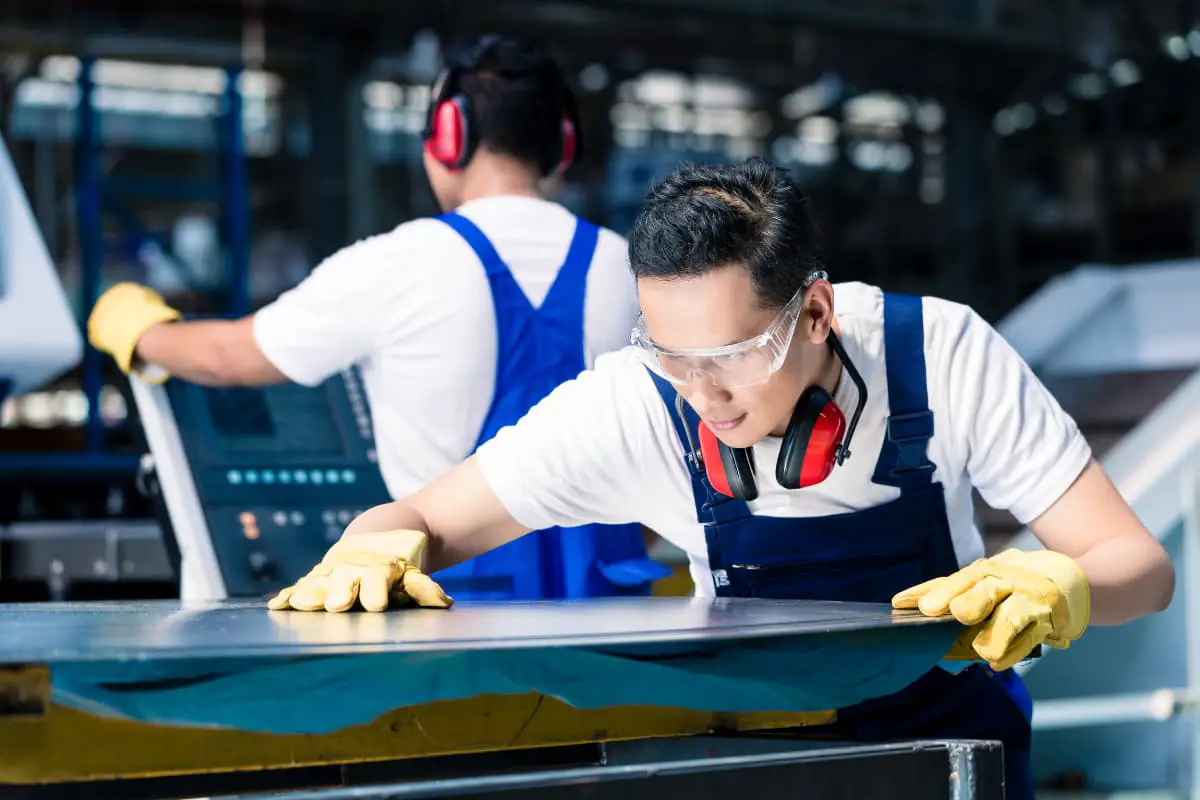
일반 펀칭으로 얻은 공작물은 전단 표면에 모따기, 파단 영역 및 버가 있으며 표면 거칠기 Ra가 6.3~로 뚜렷한 테이퍼가 있습니다.
12.5μm이며 동시에 펀칭 부품의 치수 정확도는 상대적으로 낮으며 일반적으로 부품의 기술적 요구 사항을 충족 할 수있는 일반적으로 T10 ~ T11입니다.
그러나 펀칭 부품의 전단 표면이 기준 표면, 결합 표면, 조립 조인트 표면 또는 이동 표면으로 사용되는 경우 펀칭 부품의 단면 품질 및 치수 정확도에 대한 더 높은 요구 사항이 필요합니다. 이때 요구 사항을 충족하기 위해 펀칭 부품의 품질과 정확도를 향상시키는 기술 방법을 채택해야합니다 (표 1 참조).
표 1 펀칭 부품의 품질과 정확성을 개선하기 위한 몇 가지 기술적 방법
카테고리 | 프로세스 이름 | 도식 | 방법의 핵심 사항 | 방법의 핵심 사항 |
마무리 | 오버홀 | ![]() | 불결한 표면, 0.006~0.01mm의 일방적 간격 또는 마이너스 간격을 제거하고 재료 두께와 모양에 따라 오버홀의 양과 빈도를 결정합니다. | 고정밀, 낮은 표면 거칠기, 작은 붕괴 각도 및 버. 높은 포지셔닝 요구 사항, 칩 제거가 쉽지 않음. 정밀 스탬핑보다 효율성이 낮음 |
압출 연마 | ![]() | 원추형 오목 다이 압출 연마, 한 면의 허용 오차 0.04 ~ 0.06mm 미만. 볼록 다이와 오목 다이 사이의 간격은 일반적으로 (0.1~0.2)t(t는 재료 두께)입니다. | 오버홀 및 정밀 스탬핑보다 낮은 품질, 부드러운 소재에만 적합, 정밀 스탬핑보다 낮은 효율성 | |
반정밀 스탬핑 | 네거티브 클리어런스 스탬핑 | ![]() | 오목 다이 크기보다 큰 볼록 다이 크기(0.05~0.3)t, 오목 다이 반경(0.05~0.1)t | 부드러운 비철에 적합한 낮은 표면 거칠기 금속 및 합금, 연강 등입니다. |
작은 간격의 둥근 모서리 블레이드 펀칭 | ![]() | 0.02mm 미만의 간격 블랭킹: 다이 블레이드 둥근 모서리 반경은 0.1t입니다. 펀칭: 펀치 블레이드 둥근 모서리 반경은 0.1t입니다. | 더 작은 표면 거칠기 값, 더 큰 붕괴 각도 및 버 | |
위아래 펀칭 | ![]() | 첫 번째 단계는 볼록을 누르고 깊이를 (0.15 ~ 0.30)t로 펀칭하고 두 번째 단계는 공작물을 역 펀칭합니다. | 위쪽과 아래쪽에 버가 없고, 여전히 붕괴 각도와 골절 표면, 복잡한 동작이 있습니다. | |
위아래 펀칭 | ![]() | 펀치는 플레이트 재료 (0.15 ~ 0.35)t로 절단하고, 펀치 ab 표면은 플레이트 재료를 압착하고, 펀치와 다이 사이의 단면 간격은 0.01 ~ 0.05mm, 블레이드 둥근 모서리 반경은 0.05 ~ 0.2mm입니다. | 절단면이 매끄럽고 표면 거칠기 값이 작습니다. 특수한 정밀 펀칭 장비 없이도 소재의 성능과 두께에 맞게 조정할 수 있습니다. | |
정밀 펀칭 | 톱니 링 압력 플레이트 정밀 펀칭 | ![]() | / | |
반대쪽 오목 다이 정밀 펀칭 | ![]() | / | ||
반대쪽 오목 다이 정밀 펀칭 | ![]() | / |
다음은 몇 가지 마감 및 반정밀 펀칭 방법에 대해 간략하게 설명합니다.
I. 리피니싱
리피니싱은 펀칭 부품의 외부 가장자리 또는 구멍 벽을 따라 얇은 칩 층을 긁어내는 마무리 다이를 사용하여 일반 펀칭 중에 단면에 남은 붕괴, 버 및 파단 영역을 제거하여 매끄럽고 수직 인 단면과 정확한 크기의 부품을 얻습니다. 일반적으로 리피니싱 후 부품은 IT6~IT7의 공차를 달성할 수 있으며 표면 거칠기 Ra는 0.4~0.8μm에 달할 수 있습니다.
리피니싱 방법은 그림 1에 나와 있습니다. 다듬어진 부품의 외부 모양을 가장자리 다듬기(그림 1a 참조)라고 하고, 펀칭된 부품의 내부 모양을 내부 가장자리 다듬기(그림 1b 참조)라고 하며, 다듬는 메커니즘은 펀칭과는 완전히 다르며 절단 가공과 유사합니다.
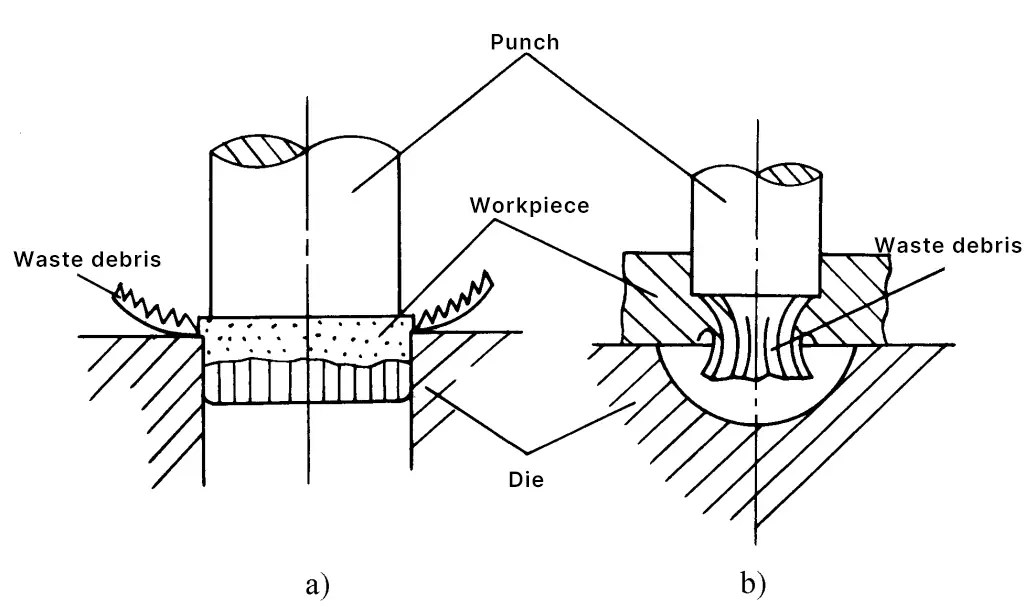
1. 재충전 수당
재연마 허용치는 적절하게 선택해야 하며, 너무 크거나 작으면 재연마된 부품의 품질이 저하됩니다. 재연마 허용치는 부품의 재질, 두께 및 모양뿐만 아니라 재연마 전 처리 조건과도 관련이 있습니다. 예를 들어, 정삭 전에 큰 간격 펀칭을 사용하는 경우 단면의 큰 테이퍼 파단 영역을 차단하기 위해 더 큰 정삭 여유가 필요하지만, 작은 간격 펀칭을 사용하면 중간 거친 밴드와 2차 전단에 의해 형성된 잠재적 균열을 차단하기 위해 큰 정삭 여유가 필요하지 않습니다.
내부 가장자리 리피니싱의 경우 드릴링이 필요한 경우 리피니싱 허용치는 펀칭보다 작을 수 있습니다. 홀 리피니싱 시 홀 간격의 정확도도 요구되는 경우 리피니싱 허용치를 늘려야 합니다. 큰 간격 펀칭의 정삭 여유는 표 2에 나와 있으며, 작은 간격 펀칭의 정삭 여유는 그림 2에서 확인할 수 있습니다.
표 2 양방향 마감 허용 오차 y(단위: mm)
재료 두께 | 황동, 연강 | 중간 경질 강철 | 단단한 강철 | |||
Min | 최대 | Min | 최대 | Min | 최대 | |
0.5~1.6 | 0.1 | 0.15 | 0.15 | 0.2 | 0.15 | 0.25 |
>1.6 ~3.0 | 0.15 | 0.2 | 0.2 | 0.25 | 0.2 | 0.3 |
>3.0~4.0 | 0.2 | 0.25 | 0.25 | 0.3 | 0.25 | 0.35 |
>4.0~5.2 | 0.25 | 0.3 | 0.3 | 0.35 | 0.3 | 0.4 |
>5.2~7.0 | 0.3 | 0.35 | 0.4 | 0.45 | 0.45 | 0.5 |
>7.0~10.0 | 0.35 | 0.4 | 0.45 | 0.5 | 0.55 | 0.6 |
참고:
1. 단순한 모양의 공작물에는 가장 작은 여유량을 사용하고 복잡한 모양이나 날카로운 각도의 공작물에는 가장 큰 여유량을 사용합니다.
2. 여러 번 수리하는 경우 표에서 가장 작은 값이 두 번째 및 그 이후의 수리에 사용됩니다.
3. 티타늄 합금의 수리 허용량은 (0.2 ~ 0.3) t입니다.
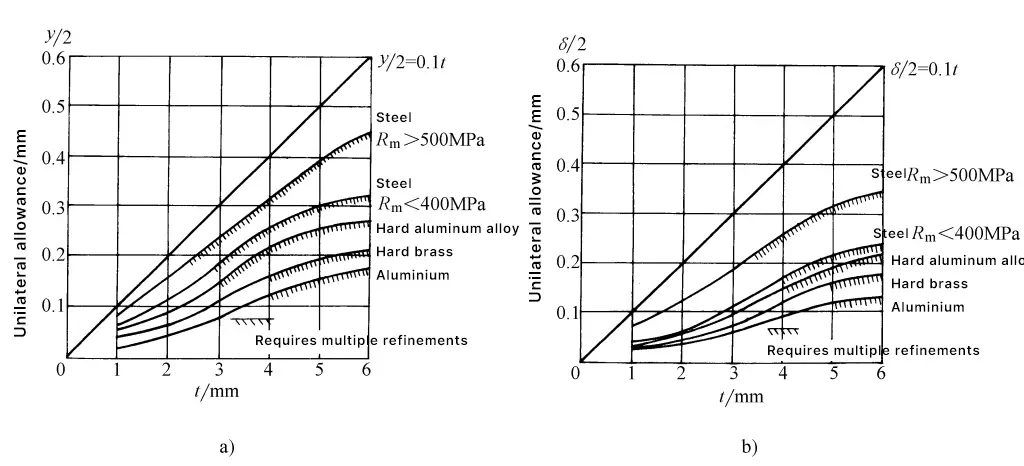
a) 블랭킹
b) 펀칭
의 크기에 따라 다이 클리어런스 블랭킹 중 다이의 작업 부분 치수 계산 방법은 두 가지 유형으로 나뉩니다. 블랭킹 다이의 치수 계산은 표 3을, 펀칭 다이의 치수 계산은 표 4를 참조하세요.
표 3 수리 전 블랭킹 다이의 작업 부분 치수 계산
금형 치수 및 수리 허용치 | 첫 번째 유형의 수리 방법 큰 간격 블랭킹 사용 | 첫 번째 유형의 수리 방법 큰 간격 블랭킹 사용 |
![]() | ![]() | |
블랭킹 다이 크기 블랭킹 펀치 크기 단일 측면 간격 오버홀 수당 총 제거 허용량 | ![]() y 표 2 참조 δ는 2C에 Y를 더한 값입니다. | ![]() δ, 그림 2a 참조 |
참고:
- C-펀칭을 위한 단일 측면 여유 공간;
- y-수리 수당은 표 7을 참조하세요;
- 수리 부품의 D-기본 치수입니다;
- 수리 부품의 두께입니다;
- δ p , δ d - 볼록 및 오목 다이의 제조 편차, δ p , δ d = (0.8~1.2) (c 최대 -c 최소 );
표 4 수리 전 펀치 몰드 작업 부분의 치수 계산
금형 치수 및 수리 허용치 | 첫 번째 수리 방법 큰 간격 펀칭 사용 | 두 번째 수리 방법 작은 간격 펀칭 채택 |
![]() | ![]() | |
펀치 다이 크기 펀치 펀치 크기 단일 측면 간격 수리 수당 총 제거 허용량 | ![]() y 표 2 참조 δ는 2C에 Y를 더한 값입니다. | ![]() δ, 그림 2b 참조 δ |
참고: d--수리 구멍의 기본 크기입니다;
2. 수리 횟수
수리 횟수는 공작물의 재료 두께 및 모양과 관련이 있습니다. 두께가 3mm 미만이고 모양이 단순하고 매끄러운 공작물의 경우 일반적으로 한 번의 수리만 필요하며, 두께가 3mm 이상이거나 각도가 날카로운 공작물의 경우 찢어짐을 방지하기 위해 두 번 이상의 수리가 필요합니다. 두 번째 수리에 대한 수당 분포는 그림 3에 나와 있습니다. 수리 횟수는 재료 두께와 공작물 모양의 복잡성에 따라 표 5에서 결정할 수 있습니다.
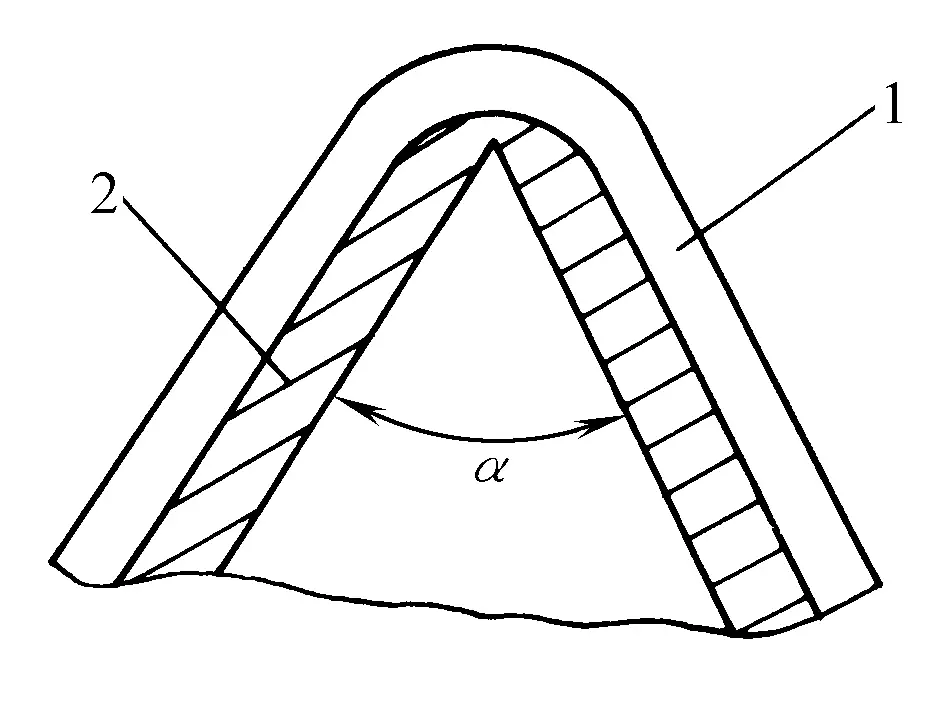
1-첫 수리
2초 수리
표 5 수리 프로세스 빈도
공작물 윤곽의 복잡성 | 재료 두께 / mm | |
<3 | <3 | |
날카로운 각도 없이 부드러운 윤곽 | 1 | 2 |
날카로운 각도의 복잡한 윤곽 | 2 | 3~4 |
3. 수리력
오버홀에 필요한 힘은 다음 공식으로 대략적으로 계산할 수 있습니다.
Pz=L(δ+0.1tn) τb
어디
- L - 오버홀의 둘레 길이(mm)입니다;
- Δ - 총 제거 허용치(mm);
- n - 다이에 동시에 클램핑된 부품 수입니다:
- t - 재료 두께(mm);
- τ b - 재료 전단 강도(MPa).
4. 오버홀 몰드의 작업 부품 치수 계산 4.
오버홀 몰드의 작업 부품 치수를 계산하는 공식은 표 6에 나와 있습니다.
표 6 오버홀 몰드 작업 부품의 치수 계산
공작물 치수 | 외부 가장자리 리컨디셔닝(프로세스) | 내부 엣지 리컨디셔닝(프로세스) |
금형 치수 재조정 | ![]() | 금형은 일반적으로 블랭크만 지원하며 캐비티의 모양과 치수를 엄격하게 지정할 필요가 없습니다. |
펀치 치수 재조정 | ![]() | ![]() |
참고:
- D 최대 는 리컨디셔닝된 부품의 최대 제한 크기(mm)입니다;
- d 분 는 리컨디셔닝된 부품의 최소 제한 크기(mm)입니다;
- Δ는 리컨디셔닝된 부품의 공차(mm)입니다;
- C′- 리컨디셔닝 금형의 단일 측면 클리어런스, 2C'=0.01~0.025mm;
- δ p , δ d 볼록 및 오목 금형 제조 공차(mm), δ p =0.2Δ, δ d =0.25Δ;
- ε y - 리퍼브 후 구멍의 수축
- 알루미늄의 경우: ε y =0.005~0.01mm;
- 황동: ε y =0.007~0.012mm;
- 소프트 스틸: ε y =0.008~0.015mm.
5. 기타 리퍼비시 방법
(1) 버니싱 리퍼비시
가장자리 버니싱 리퍼브는 일반 펀칭에서 얻은 블랭크를 원형 또는 원추형 오목 금형 (그림 4 참조)으로 구멍에 강제로 밀어 넣어 표면 소성 변형을 사용하여 깔끔하고 매끄러운 단면을 얻는 것입니다. 일방적 버니 싱 허용치는 0.04 ~ 0.06mm 미만입니다. 이 공정은 일반적으로 부드러운 소재에만 적합하며 품질은 절단 보수 공정보다 약간 낮습니다.
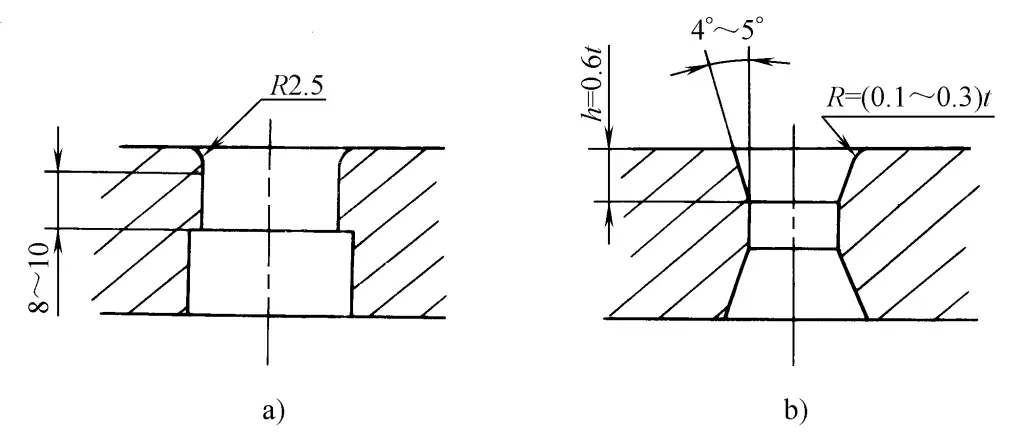
a) 둥근 오목한 몰드
b) 원추형 오목 몰드
오목 금형의 작업 부품 크기 결정은 리퍼브 금형과 동일하지만이 방법은 공작물의 탄성 변형이 더 크고 (30mm 이내의 공작물의 경우 탄성 변형이 0.01 ~ 0.025mm에 도달 할 수 있음) 리퍼브 공작물의 두께에 따라 증가하므로 오목 금형 크기를 적절히 고려해야합니다. 볼록한 금형 크기는 오목한 금형 크기보다 (0.1 ~ 0.2)t 더 큽니다.
맨드릴 또는 정밀 프레스 볼을 사용한 내부 가장자리 마감(그림 5 참조). 이 공정은 볼록 몰드의 압력을 사용하여 필요한 크기보다 약간 작은 공작물의 구멍을 통해 높은 경도(63-66 HRC)의 강철 볼(또는 맨드릴)을 강제로 통과시켜 구멍 표면을 평평하게 만드는 것입니다. 볼로 원형 홀을 가공할 수 있을 뿐만 아니라 맨드릴을 사용하여 노치가 있는 비원형 홀도 가공할 수 있습니다.
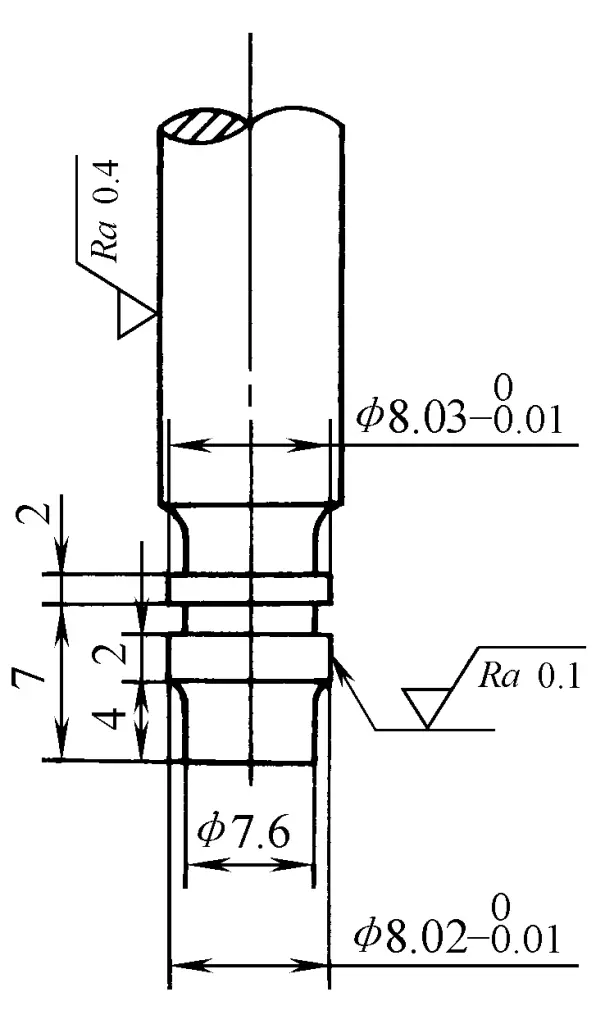
(2) 라미네이트 마감
일반적인 마감 방법을 사용하면 간격이 매우 작기 때문에 금형 제조에 높은 정밀도가 필요하며 최적의 마감 허용치를 선택해야 하는 문제도 있습니다. 따라서 한 번의 마감 처리로 매끄러운 표면을 얻을 수 없으며, 적층 마감은 앞서 언급한 문제를 피할 수 있습니다.
적층 마감은 볼록 몰드의 직경이 오목 몰드보다 큰 두 개의 블랭크를 함께 쌓고, 볼록 몰드가 블랭크 중 하나를 통해 마감되는 블랭크를 누르는 방식으로 이루어집니다. 마감 처리가 블랭크 플레이트 두께의 2/3 ~ 3/4에 도달하면 다음 마감 스트로크를 위해 두 번째 블랭크가 공급됩니다(그림 6 참조).
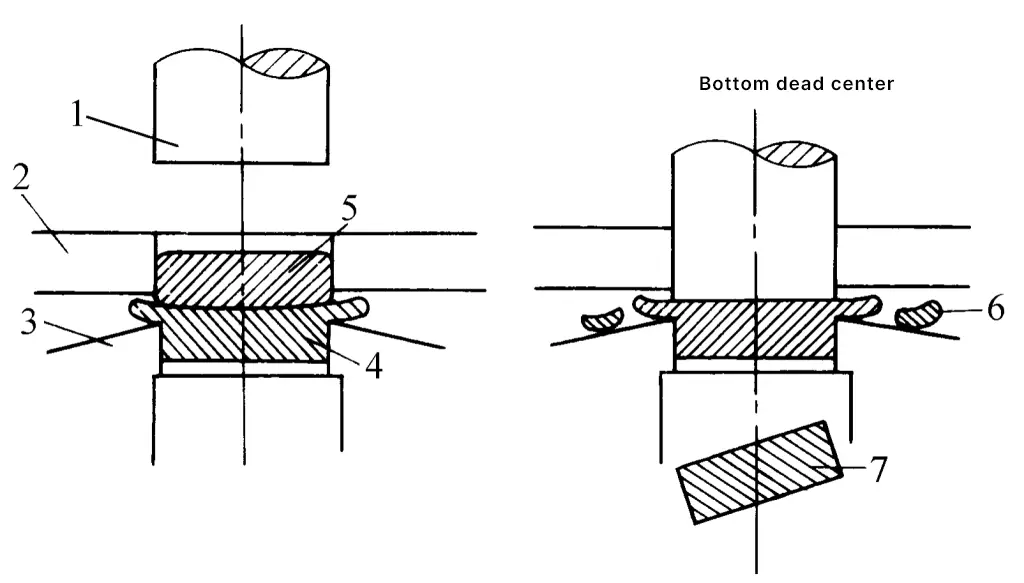
1-볼록 몰드
2-가이드 플레이트
3-오목 몰드(선행 각도 포함)
4-판 두께의 2/3 ~ 3/4까지 초기 블랭크 마감 처리
5-다음 조정을 위한 중복 빌릿
6-칩
7-작품
리퍼비시 시 펀치가 금형에 들어가지 않으므로 금형 제작이 용이합니다. 리퍼브에 적합한 소재와 가공 공차 범위가 일반 리퍼브 방식보다 넓습니다. 단점은 다음 스트로크에서 블랭크가 들어간 후 칩을 제거해야 하므로 다이의 끝면에 10°~15° 리드각 또는 칩 브레이킹 홈을 가공하고 고압 압축 공기를 사용하여 칩을 날려버리는 등 대응 조치가 필요하다는 점입니다. 또 다른 문제는 큰 버입니다.
(3) 진동 수리
캠이나 기어와 같이 복잡한 형상의 소형 고정밀 부품의 경우, 진동 슬라이더가 장착된 특수 진동 프레스에서 이 슬라이더에 연결된 펀치가 진동하도록 하는 두 번째 모터를 사용하여 진동 리퍼브 작업을 수행할 수도 있습니다. 리퍼비시 다이에 놓인 부품은 프레스가 스트로크당 0.05~0.06mm 전진할 때 분당 1200~2000회의 짧은 충격을 견뎌냅니다.
진동 리퍼브의 변형은 처리되는 금속의 작은 부피에 국한되어 납 균열의 확장 및 찢어짐 발생을 방지합니다. 또한 다이 엣지 스크래핑의 진동 작용으로 인해 전단 표면이 매끄러워지고 부품의 변형이 최소화됩니다. 리퍼브 후 부품의 치수 정확도는 0.05~0.01mm, 표면 거칠기 Ra는 0.4~0.8μm에 달할 수 있습니다.
II. 네거티브 클리어런스 펀칭
그림 7에서 볼 수 있듯이 네거티브 클리어런스 펀칭은 본질적으로 펀칭과 리퍼브의 복합 공정입니다. 펀치의 크기가 다이보다 크기 때문에 펀칭 과정에서 발생하는 크랙의 방향이 일반 펀칭과 반대이므로 역원뿔 모양의 블랭크가 형성됩니다. 펀치는 계속해서 아래로 누르면서 블랭크를 다이 안으로 밀어 넣고 여분의 재료를 잘라내어 리퍼브 공정과 동일한 고품질 단면을 얻습니다.
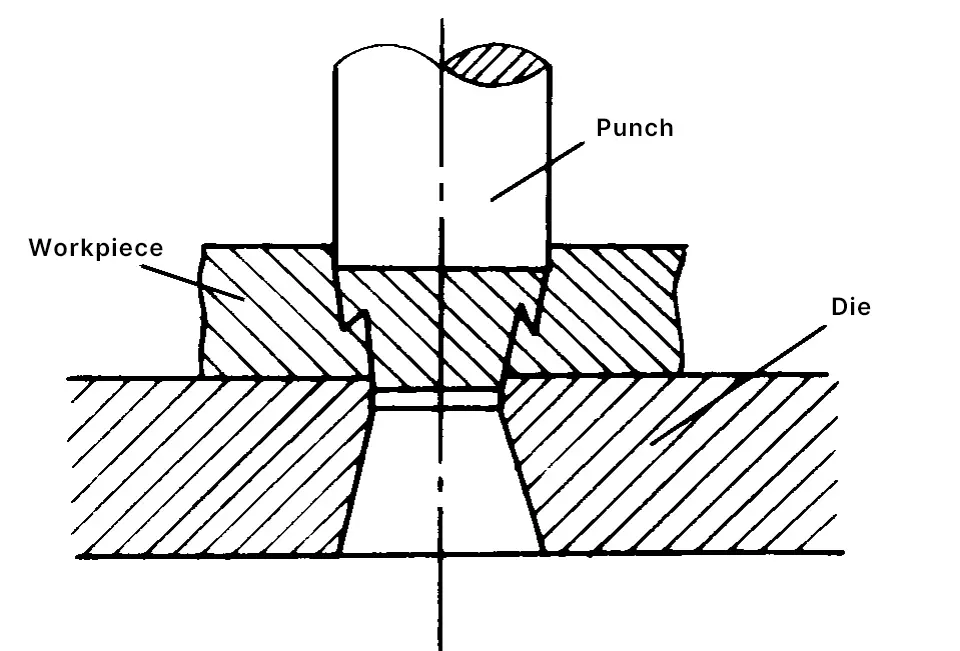
일반적으로 펀치의 크기는 다이의 크기보다 (0.1~0.2)t 더 큽니다. 원형 공작물의 경우 펀치가 금형보다 큰 둘레가 균일합니다. 오목한 부분과 돌출부가 있는 공작물의 경우 그림 8과 같이 돌출된 모서리는 나머지 모서리보다 2배, 즉 (0.2~0.4)t 커야 하며, 오목한 부분은 절반, 즉 (0.05~0.1)t 줄여야 합니다.
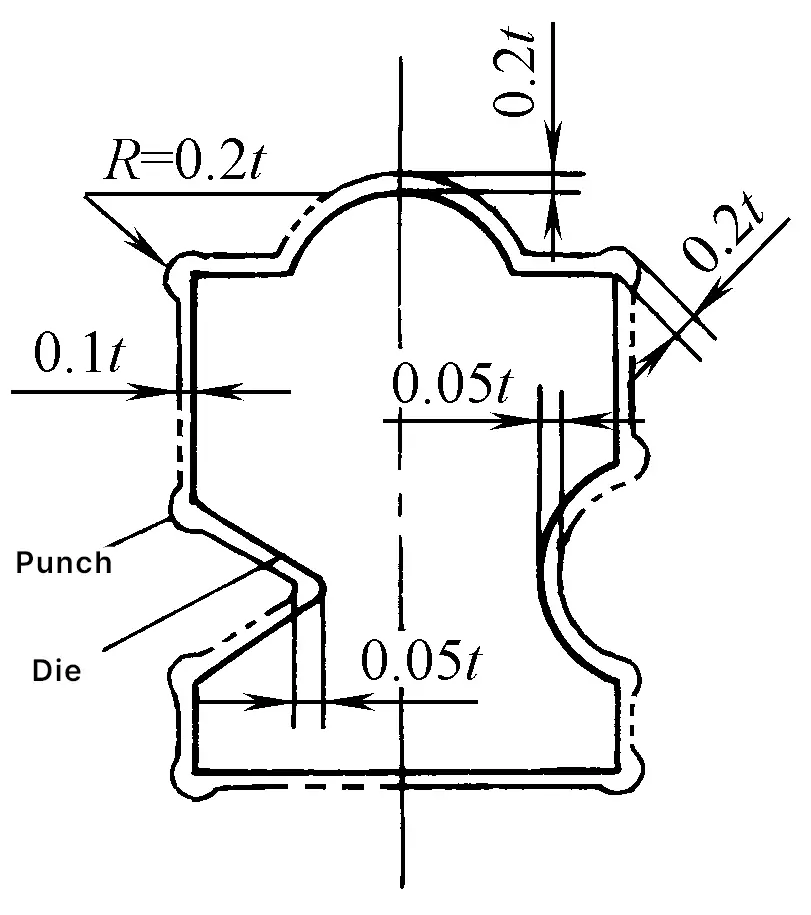
전단 표면의 표면 거칠기 값을 낮추기 위해 다이 가장자리에 0.1 ~ 0.3mm의 반경을 만들 수 있습니다. 펀치가 다이보다 크기 때문에 펀칭이 완료된 후 펀치가 다이 구멍에 들어가서는 안되며 다이 상부 표면에서 0.1 ~ 0.2mm의 거리를 유지해야합니다.
이때 블랭크가 다이에 완전히 압입되지 않았으므로 다음 부품을 펀칭하는 동안 완전히 압입해야합니다. 공작물이 다이 입구에서 떨어지면 탄성 변형으로 인해 크기가 0.02 ~ 0.06mm 증가합니다. 따라서 금형의 작업 부분을 설계할 때 이 변형을 적절히 줄여야 합니다.
이 방법을 사용하면 펀칭 된 공작물의 표면 거칠기 Ra는 0.4 ~ 0.8μm에 도달 할 수 있으며 치수 정확도는 IT9 ~ IT11에 도달 할 수 있습니다. 그러나 두께가 t≤1.5mm인 대형 박판의 경우 상당한 아치가 발생할 수 있습니다. 또한 네거티브 클리어런스 펀칭은 연질 알루미늄, 구리, 연강 등과 같이 가소성이 좋은 연질 소재에만 적합합니다. 주로 냉간 압출 판재 블랭크 및 일부 간단한 평면 부품의 정밀 블랭킹에 사용됩니다.
네거티브 클리어런스 펀칭에 필요한 힘은 일반 펀칭보다 훨씬 크며 금형에 더 큰 압력이 가해지기 때문에 금형이 깨지기 쉽습니다. 윤활유를 잘 사용하면 재료가 금형에 달라붙는 것을 방지하고 금형의 수명을 연장할 수 있습니다.
음의 클리어런스 펀칭 P에 대한 힘은 다음 공식으로 추정할 수 있습니다.
Pf=CP
공식에서
- P - 보통 펀칭력 (N);
- C - 재질에 따라 선택되는 계수입니다: 알루미늄: C=1.3~1.6; 황동: C=2.25~2.8; 연강: C=2.3~2.5.
III. 작은 간격 둥근 모서리 펀칭
블랭킹하는 동안 다이 모서리는 작은 둥근 또는 타원형 모서리를 가지며(그림 9 참조), 펀치는 표준 형태입니다. 펀칭하는 동안 펀치 모서리는 둥근 모서리를 가지며 다이의 형태는 표준 형태입니다. 양면 펀치와 다이 사이의 간격 는 0.01~0.02mm 미만이며 재료 두께와 무관합니다.
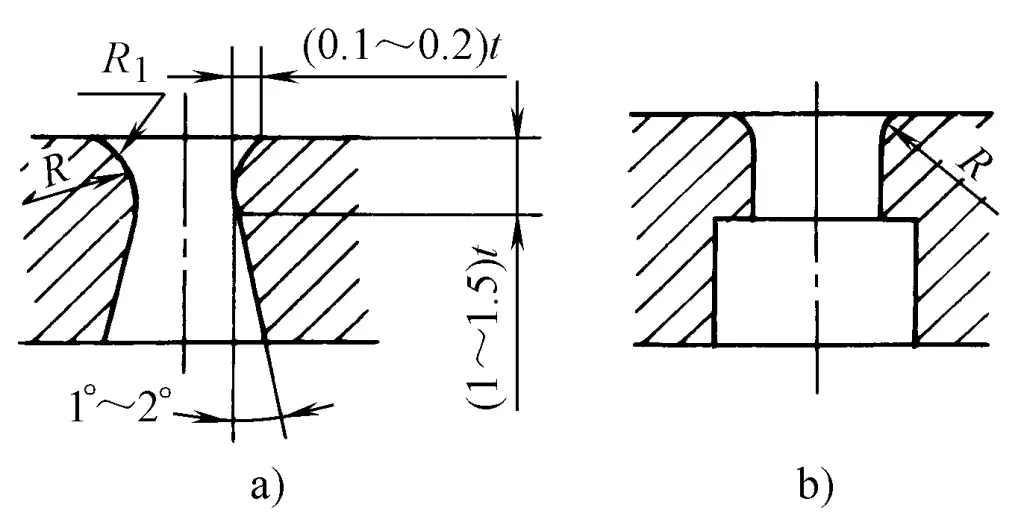
a) 타원형 모서리 포함
b) 모서리가 둥근 경우
다이 모서리가 둥글고 매우 작은 간격을 사용하기 때문에 펀칭 영역의 정수압이 증가하고 인장 응력이 감소하며 둥근 모서리는 응력 집중도도 감소하여 균열 형성을 억제하고 밝은 전단 표면을 얻을 수 있습니다.
그림 9는 모서리가 타원형 또는 둥근 두 가지 형태의 다이를 보여줍니다. 그림 9a는 타원형 모서리가 있는 다이를 보여 주며, 호와 직선의 연결이 날카로운 모서리 없이 매끄럽고 균일해야 합니다.
둥근 모서리 R1의 반경은 표 7에 표시되어 있으며, 이는 직경 25mm의 공작물에 대해 얻은 결과입니다. 다른 크기는 표에 있는 값의 2/3를 선택하고 시험 펀칭 과정에서 필요에 따라 둥근 모서리를 늘릴 수 있습니다. 제조 편의를 위해 그림 9b에 표시된 다이를 사용할 수도 있으며, 여기서 둥근 모서리 반경은 일반적으로 R=0.1t(t는 재료 두께)이거나 표 8에 따라 선택할 수 있습니다.
표 7 타원형 모서리 다이 둥근 모서리 반경 R 1 값(공작물 직경 ϕ = 25mm) (단위: mm)
재료 | 재료 조건 | 재료 두께 | 필렛 반경 R 1 |
연강 | 열간 압연 | 4 | 0.5 |
6.4 | 0.8 | ||
9.6 | 1.4 | ||
냉간 압연 | 4 | 0.25 | |
6.4 | 0.8 | ||
9.6 | 1.1 | ||
알루미늄 합금 | 소프트 | 4 | 0.25 |
6.4 | 0.25 | ||
9.6 | 0.4 | ||
하드 | 4 | 0.25 | |
6.4 | 0.25 | ||
9.6 | 0.4 | ||
구리 | 소프트 | 4 | 0.25 |
6.4 | 0.25 | ||
9.6 | 0.4 | ||
하드 | 4 | 0.25 | |
6.4 | 0.25 | ||
9.6 | 0.4 |
표 8 둥근 모서리 오목 다이 R의 값(단위: mm)
재료 | 재료 두께 1 | 재료 두께 2 | 재질 두께 3 | 재료 두께 4 |
알루미늄 | 0.25 | - | 0.25 | 0. 50 |
구리(T2) | 0.25 | - | 0.5 | (1.00) |
연강 | 0.25 | (0.5) | (1.00) | - |
황동(H70) | (0.25) | - | (1.00) | - |
스테인리스 스틸(0Cr18Ni9) | (0.25) | (0.5) | (1.00) | - |
참고: 괄호 안의 데이터는 참조 값입니다.
작은 간격의 둥근 모서리 펀칭은 부드러운 알루미늄, 순수 구리, 황동, 연강(05F, 08F) 등과 같이 가소성이 좋은 소재에 적합합니다. 공작물은 이상적으로 균일한 매끄러운 윤곽을 가져야 하며, 찢어짐을 방지하기 위해 모서리가 직각이거나 날카로운 모서리는 둥근 모서리를 사용해야 합니다. 펀칭력을 계산할 때는 일반 펀칭력을 기준으로 50%를 늘려야 합니다.
부품의 가공 정확도는 IT9 ~ IT11에 도달 할 수 있으며 표면 거칠기 Ra는 0.4 ~ 1.6um에 도달 할 수 있습니다. 부품이 다이 구멍에서 밀려 나온 후 탄성 변형으로 인해 크기가 0.02 ~ 0.05mm 증가하므로 금형 설계에서 보정해야 합니다.
IV. 위아래 펀칭
상하 펀칭 공정(왕복 펀칭이라고도 함)은 그림 10에 나와 있습니다. 두 개의 볼록한 금형을 사용하여 공작물을 위와 아래에서 펀칭하고, 먼저 위에서 아래로 펀칭하고(그림 a 참조), 상단 볼록 금형이 재료 두께의 15% ~ 30%만큼 재료를 절단하면 중지합니다. 그런 다음 아래쪽 볼록 몰드를 사용하여 역방향으로 위쪽으로 펀칭합니다(그림 b, c, d 참조).
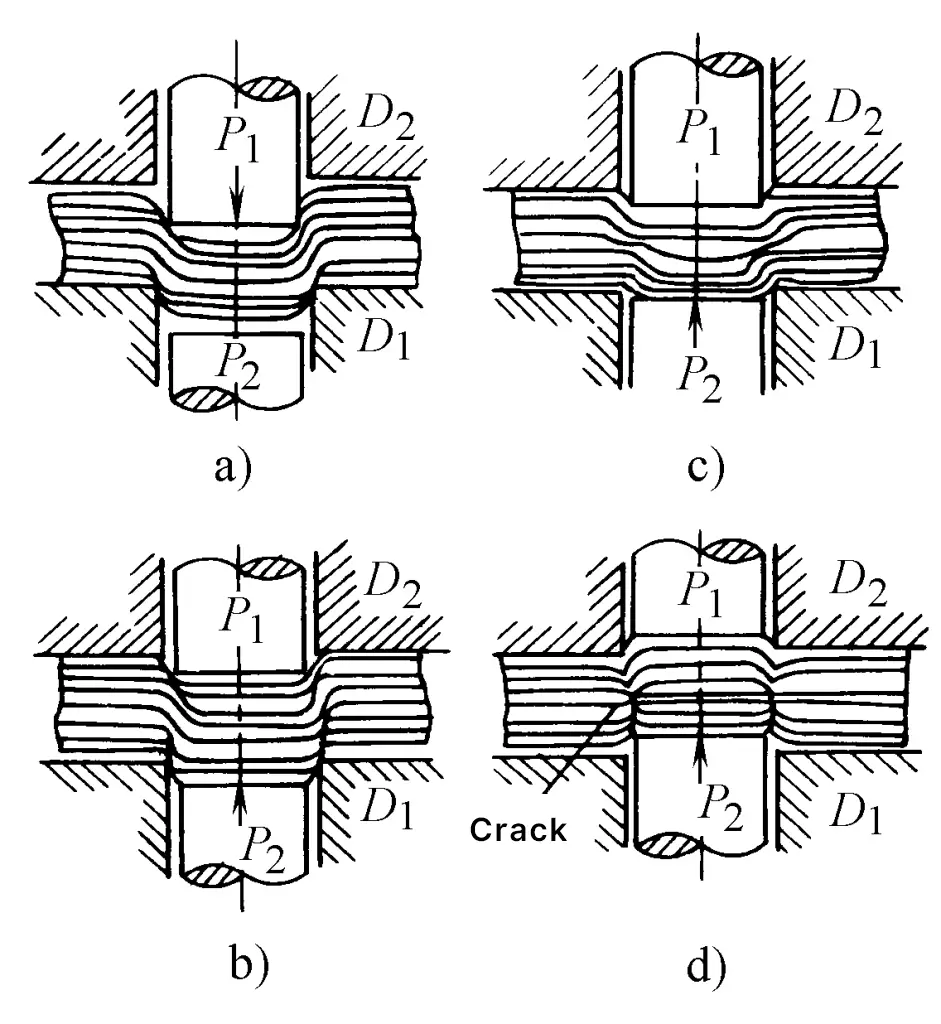
이 방법의 변형 메커니즘은 일반 펀칭과 유사하여 여전히 전단 균열 및 파단 영역을 생성하지만 위아래로 두 번의 펀칭을 거치기 때문에 두 개의 밝은 밴드를 얻을 수 있으므로 전체 단면에서 밝은 밴드의 비율을 높이고 버를 제거하여 펀칭 부품의 단면 품질을 크게 향상시킬 수 있습니다 (그림 11 참조).
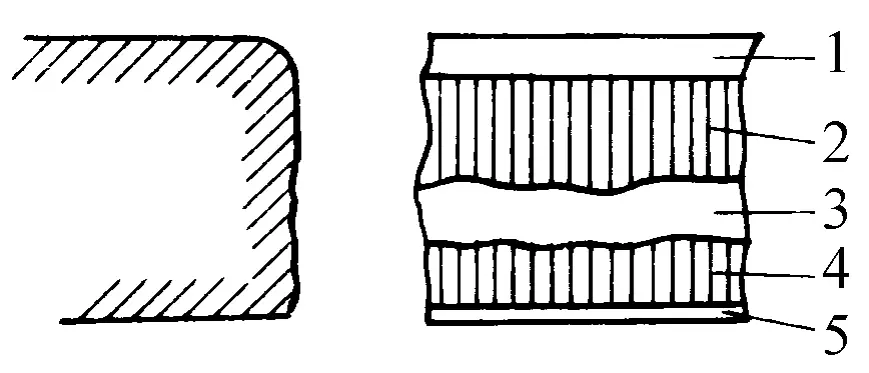
- 1, 5-접힘 각도
- 2, 4-브라이트 밴드
- 3-프랙처 영역
그러나 이 방법은 금형 구조가 더 복잡하기 때문에 펀칭 시간이 길어지고 스탬핑 장비에 대한 특별한 요구 사항이 있으므로 현재 생산에는 잘 사용되지 않습니다. 특수 프레스를 사용하지 않으려면 이 방법을 싱글 액션 프레스의 3 스테이션 프로그레시브 다이를 사용하여 3단계로 구현할 수도 있습니다(그림 12 참조).
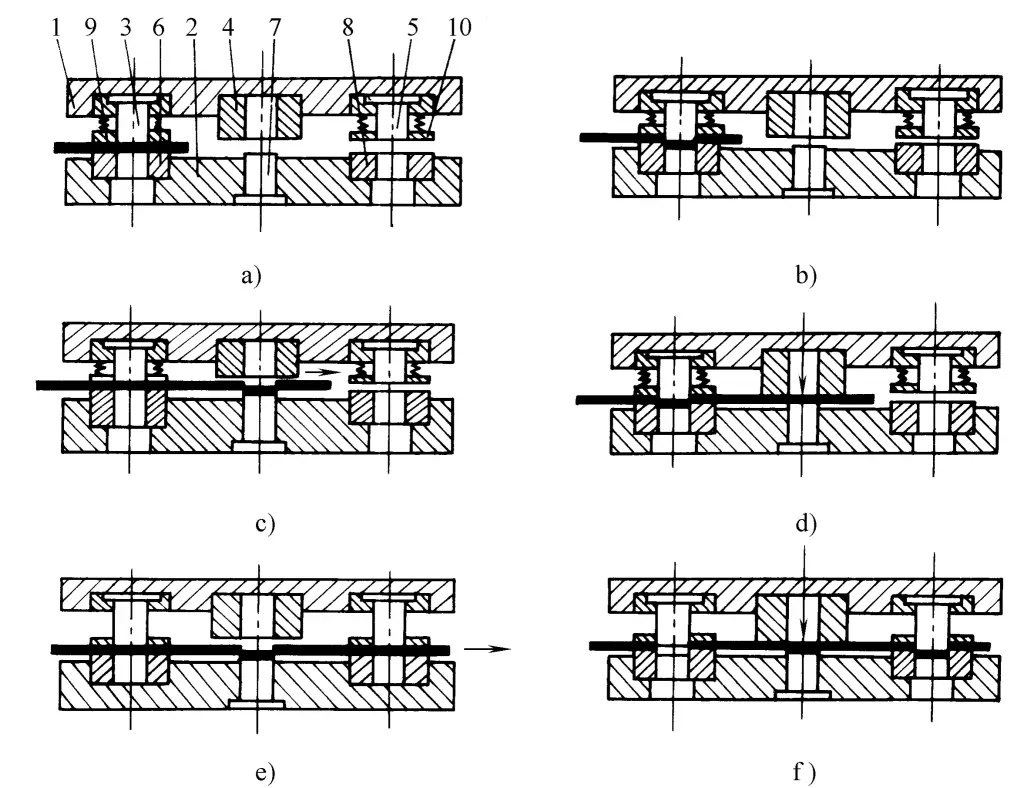
1-어퍼 다이 홀더
2-하부 다이 홀더
3-엠보싱 다이
4-카운터 싱킹 다이
5-세퍼레이션 펀칭 볼록 다이
6-엠보싱 오목 다이
7-리버스 토핑 볼록 다이
8-세퍼레이션 펀칭 오목 다이
9-엠보싱 압력판
10-분리 펀칭 압력판
1. 엠보싱의 첫 번째 단계에서는 재료를 자르지 않고 펀칭 영역의 구덩이로만 누릅니다(그림 12b 참조).
2. 두 번째 단계에서는 엠보싱된 블랭크가 첫 번째 단계의 반대 방향에서 펀칭 영역에서 아직 깨지지 않은 상태로 다시 펀칭됩니다(그림 12d 참조).
3. 세 번째 단계에서는 첫 번째 단계와 같은 방향으로 펀칭을 수행하여 블랭크를 완전히 분리합니다(그림 12f 참조).
엠보싱 및 리버스 펀칭 단계에서의 다이 관통은 주로 소재의 두께와 성능에 따라 결정됩니다. 엠보싱 또는 리버스 펀칭 중 다이 관통 깊이는 펀칭 영역이 아직 찢어지지 않는 수준으로 제한되어야 합니다.
V. 동기식 전단 및 압착 펀칭
동기 전단 및 압착 펀칭 방법(즉, 스텝형 펀치 펀칭)의 작업 프로세스는 그림 13에 나와 있습니다. 펀치가 판재를 절단할 때, 소재는 펀치의 ab 표면이 판재 표면에 닿을 때까지 자체 가소성에 따라 전단 변형을 겪습니다(그림 13a, b 참조). 이 시점에서 판금은 전단 균열을 생성하지 않으며, 이 단계의 지속 시간은 주로 재료의 가소성과 다이 모서리의 상태에 따라 달라집니다.
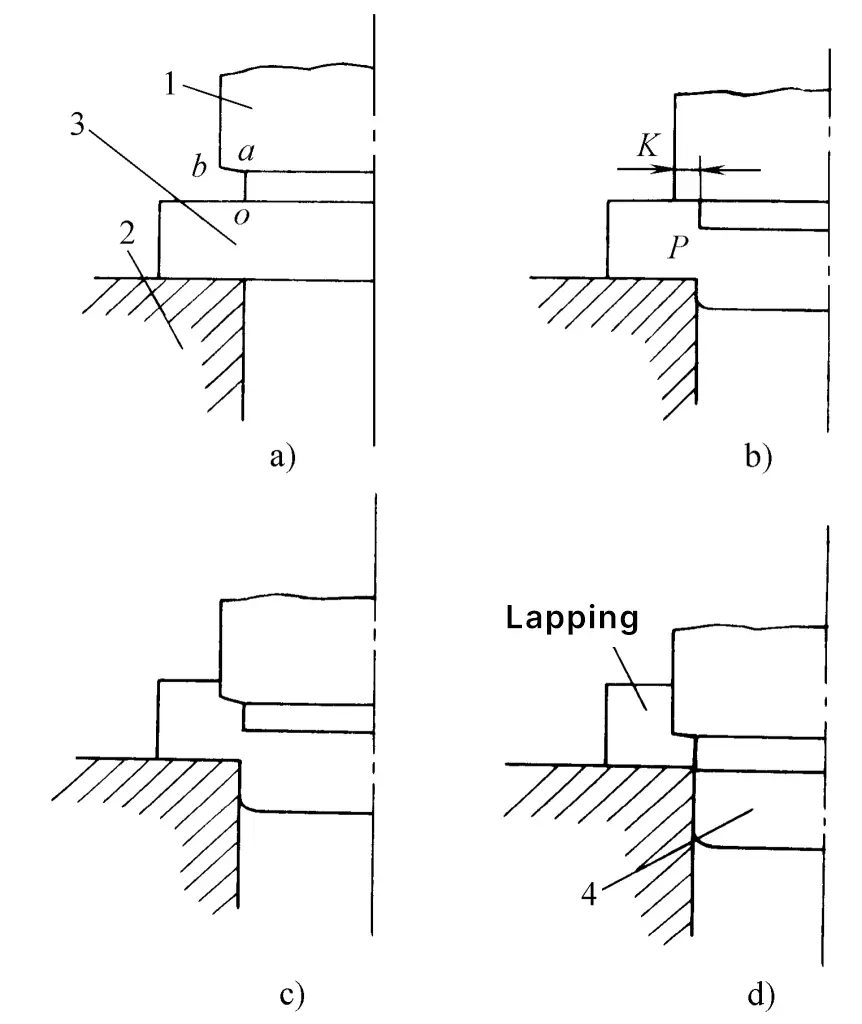
1-펀치
2-다이
3-판금
4-워크피스
펀치가 계속 압입됨에 따라 펀치의 ab 표면이 판금을 누르고 압착하고 압축 된 재료는 전단 영역 P에서 충분히 큰 수압을 설정하여 재료의 가소성을 향상시키고 전단 균열의 생성을 억제하며 소성 전단 변형이 전체 과정에서 계속되도록합니다. 전단 프로세스. 펀치의 끝면이 금형 구멍에 막 들어가면 판금의 정밀한 분리가 최종적으로 완료됩니다(그림 13c, d 참조).
앞서 언급한 전단 공정에서는 재료 고유의 가소성을 적절히 활용한 다음 충분히 큰 수압을 적시에 가하여 전단 균열의 발생을 억제합니다.
펀치의 ab 표면이 점차적으로 압착됨에 따라 수압은 점점 더 커져 전단 공정 중에 판금의 가소성이 점진적으로 감소하는 것을 보상할 뿐입니다. 펀치의 작업 부분에서 ao 섹션의 주요 기능은 정수압의 초기 증가 타이밍을 제어하는 것이고, ab 표면의 주요 기능은 정수압의 크기를 제어하는 것입니다. 크기를 변경함으로써 다양한 성능과 두께의 판금에 적응할 수 있습니다.
동일한 원리를 사용하여 그림 14와 같이 정밀 펀칭도 가능합니다. 이때 펀칭 폐기물은 다이 위에서 배출되어야 합니다.
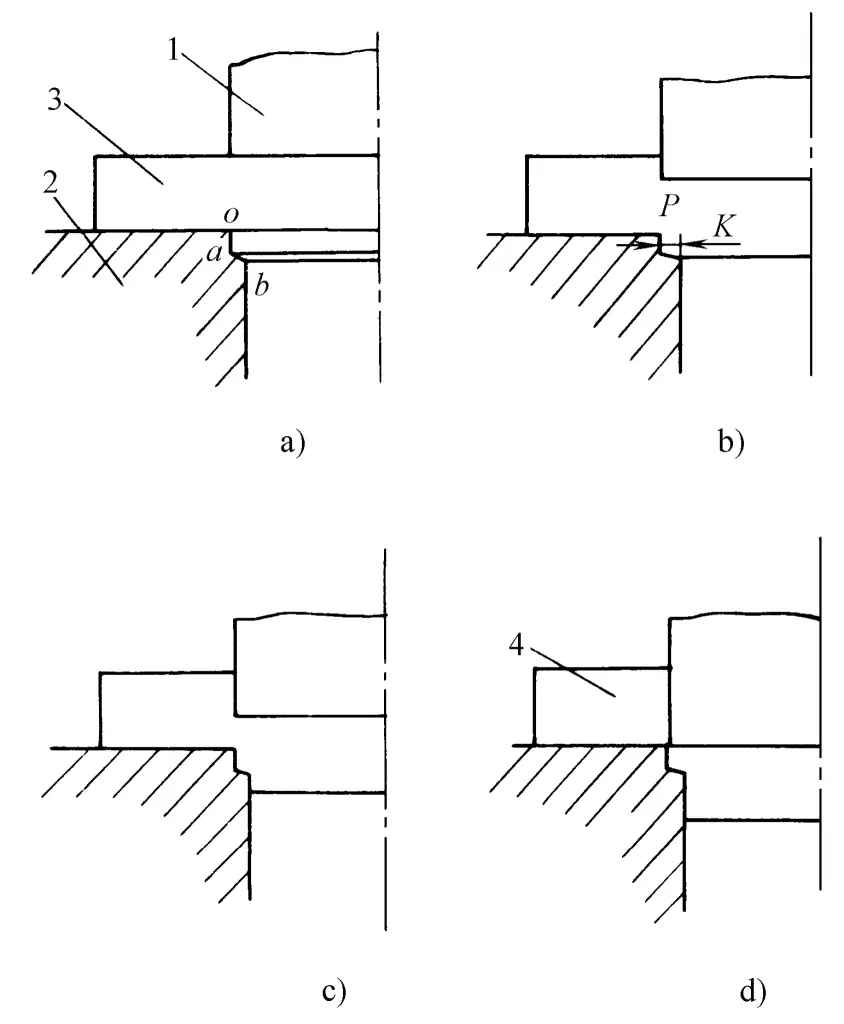
1-펀치
2-다이
3매 자료
4-워크피스
이 방법의 기술적 핵심은 블랭킹 펀치(또는 펀칭 다이)의 작업 부분의 모양과 크기를 합리적으로 결정하고 재료의 다양한 가소성에 따라 권장 값을 선택하는 것입니다.
- ao 섹션의 길이는 (0.15~0.35)t입니다;
- ab 표면의 수평 너비 K=(0.1~0.4)t입니다;
- AB 표면과 수평면 사이의 각도는 0°~20°입니다;
- 펀치(또는 다이) AO 섹션과 다이(또는 펀치) 사이의 일방적인 간격은 0.01~0.05mm입니다;
- 블랭킹 다이(또는 펀칭 펀치)의 가장자리 반경은 0.05~0.2mm입니다.
이 방법을 사용하여 기존 프레스의 가이드 플레이트 금형을 사용하여 순수 구리, 알루미늄 합금, 황동, 08강, 25강(열연강), 아연 합금에 대한 실험을 수행한 결과, 모두 완전히 매끄러운 전단 표면을 얻을 수 있었습니다. 또한 정밀 펀칭이 어려운 납이 함유된 황동의 경우 이 방법을 사용하면 공작물의 전단 표면이 거의 0.9t(t는 재료 두께)에 도달할 수 있습니다.