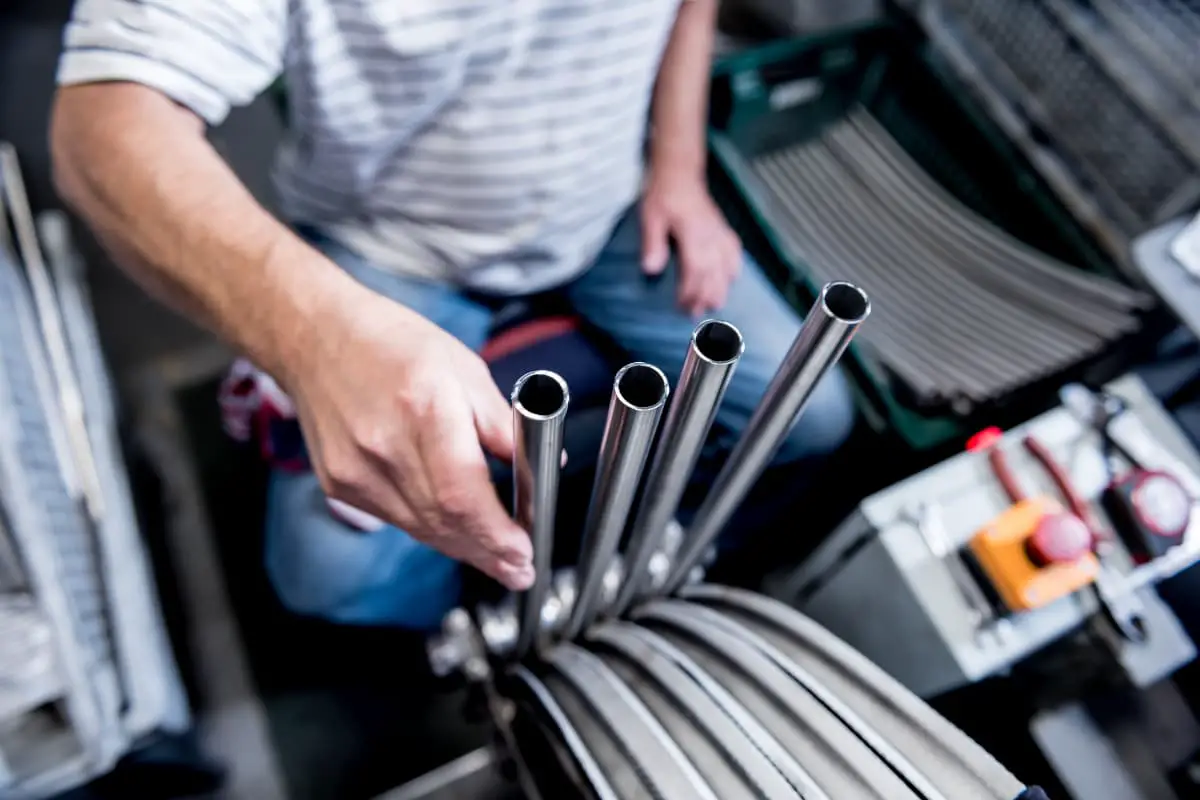
I. 커팅 모션
공작 기계의 공작물에서 여분의 금속을 제거하고 치수 정확도, 기하학적 정확도 및 표면 품질 요구 사항을 충족하는 공작물을 얻으려면 공구와 공작물 사이에 상대적인 움직임, 즉 절삭 동작이 있어야 합니다.
절단 공정에서 절단 모션의 역할에 따라 그림 1과 같이 절단 모션은 메인 모션과 이송 모션으로 나눌 수 있습니다.
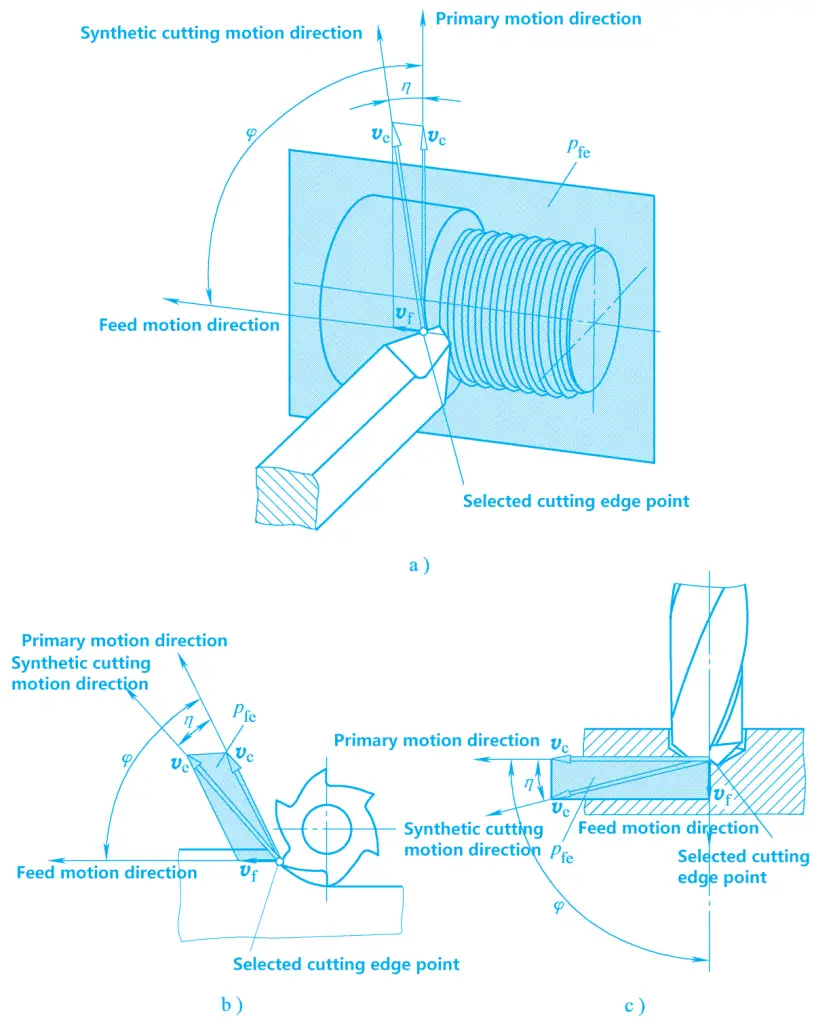
a) 회전
b) 밀링
c) 드릴링
1. 메인 모션
메인 모션은 공작물에서 여분의 금속층을 제거하고 공작물에 새로운 표면을 형성하는 데 필요한 모션입니다. 공작 기계가 제공하는 기본 모션입니다. 메인 모션은 가장 빠른 속도와 가장 많은 전력 소비가 특징입니다.
절삭 가공에는 공작물 또는 공구에 의해 수행될 수 있는 하나의 주요 동작만 있습니다. 예를 들어 선삭 중 공작물의 회전 동작과 밀링 및 드릴링 중 밀링 커터와 드릴 비트의 회전 동작은 모두 주 동작입니다.
2. 피드 모션
이송 모션은 절단할 금속층을 절단 공정에 간헐적 또는 연속적으로 이송하는 모션입니다. 메인 모션과 결합하면 금속층을 연속적으로 제거하여 원하는 공작물 표면을 얻을 수 있습니다. 이송 모션은 저속과 저전력 소비가 특징입니다.
절삭 가공에서 이송 동작은 한 동작, 두 동작 또는 여러 동작이 될 수 있습니다. 외부 선삭 중 공작물 축에 평행한 선반 공구의 종방향 동작과 같은 연속 동작이거나 평면 가공 중 공작물 또는 공구의 횡방향 동작과 같은 간헐적인 동작일 수 있습니다.
3. 합성 커팅 모션
그림 1과 같이 복합 절삭 모션은 주 모션과 이송 모션이 합성된 모션입니다. 공작물에 대한 공구의 절삭날에서 선택한 지점의 순간 복합 동작 방향을 복합 절삭 동작 방향이라고 하며, 그 속도를 복합 동작 속도라고 합니다. 절단 속도.
II. 공작물 표면
절삭 공정 동안 공작물의 금속 층은 공구에 의해 지속적으로 절단되어 칩이 되고 공작물에는 새로운 표면이 형성됩니다. 새로운 표면이 형성되는 동안 그림 2와 같이 공작물에는 지속적으로 변화하는 세 개의 표면이 있습니다.
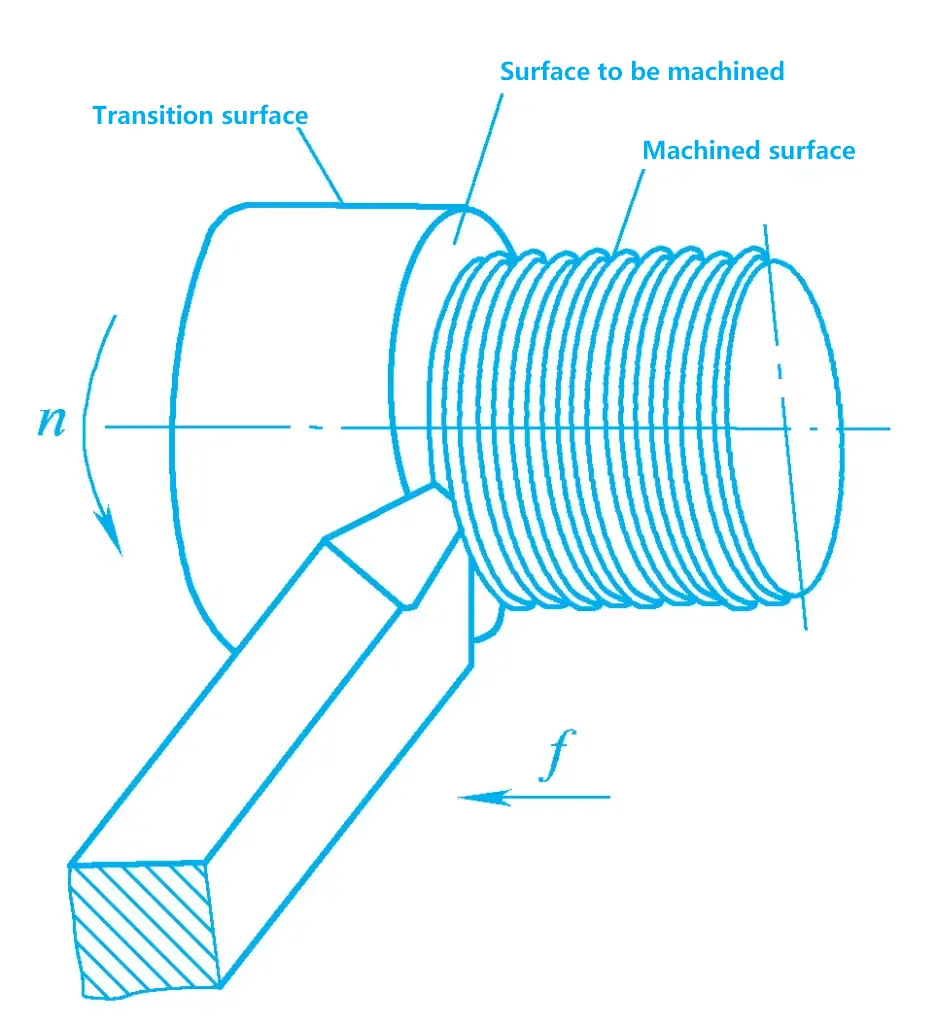
(1) 가공할 표면
제거할 공작물의 표면을 가공할 표면이라고 합니다.
(2) 가공된 표면
공구로 절삭한 후 공작물에 형성된 표면을 가공된 표면이라고 합니다.
(3) 전이 표면(가공 표면)
절삭 날에 의해 절단되는 표면을 전이 표면이라고 하며, 이는 가공할 표면과 가공된 표면 사이의 연결 표면입니다.
III. 도구의 절단 부분의 기하학적 각도
금속 절삭 공구에는 많은 종류와 모양이 있지만 공구의 절삭 부분 구성에는 공통점이 있습니다. 외부 선삭 공구의 절삭 부분은 다양한 공구의 절삭 부분의 가장 기본적인 형태라고 할 수 있습니다. 선삭 공구의 절삭 부분을 설명하는 일반적인 용어는 다른 금속 절삭 공구에도 사용할 수 있습니다.
1. 터닝 도구의 구성
선삭 공구는 공구 샹크와 공구 헤드로 구성됩니다. 공구 샹크는 공구의 클램핑 부분이고 공구 헤드는 공구의 절삭 부분입니다. 그림 3과 같이 공구 헤드는 다음과 같은 부품으로 구성됩니다:
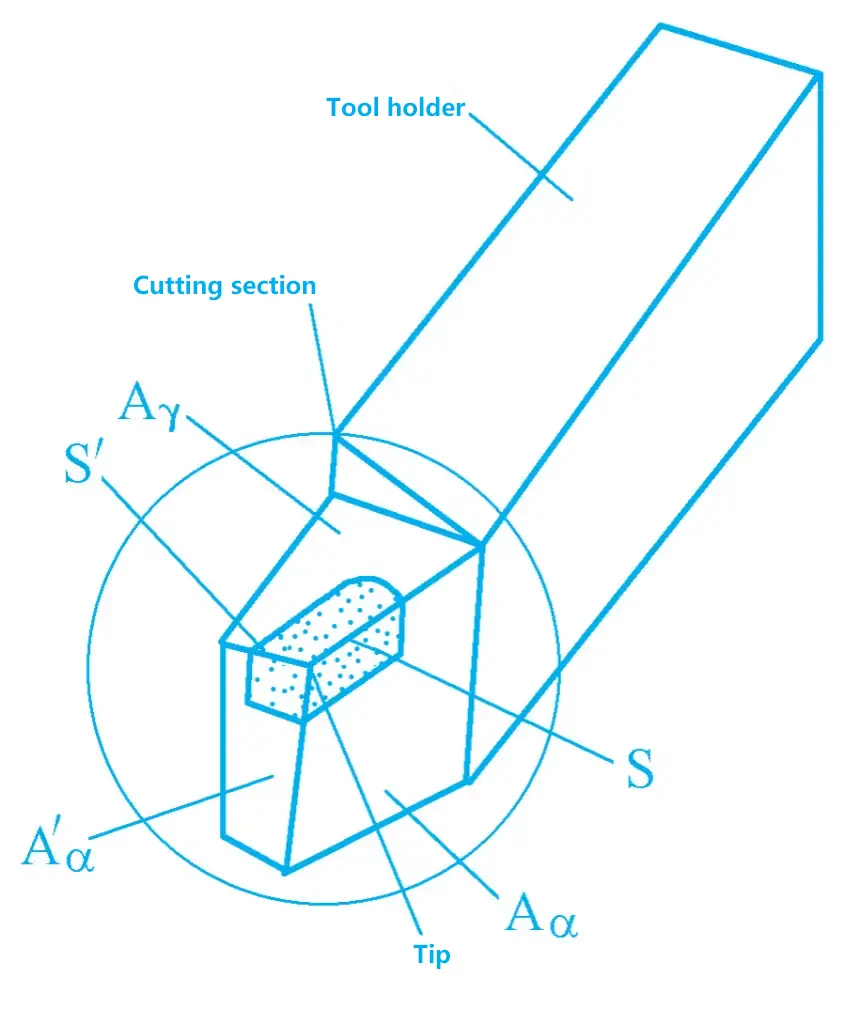
(1) 레이크면 Aγ
칩이 흘러나오는 도구 면을 레이크 면이라고 합니다.
(2) 측면면 Aα
전환면의 반대쪽 도구 면을 측면 면(주 측면 면이라고도 함)이라고 합니다.
(3) 보조 측면면 A'α
가공된 표면의 반대쪽 공구 면을 보조 측면 면이라고 합니다.
(4) 메인 커팅 엣지 S
레이크 면과 메인 측면 면 사이의 교차선을 메인 커팅 엣지라고 합니다. 커팅 과정에서 주 커팅 작업을 수행합니다.
(5) 보조 절삭날 S′
레이크면과 보조 측면면 사이의 교차선을 보조 절삭 날이라고 합니다. 주 절삭 날과 협력하여 절삭 작업을 완료하고 최종적으로 공작물의 가공된 표면을 형성합니다.
(6) 도구 팁
공구 팁은 주 절삭날과 보조 절삭날의 연결 부분 또는 주 절삭날과 보조 절삭날의 교차점입니다. 대부분의 공구는 공구 팁에 작은 직선 모서리 또는 호 모서리가 연마되어 있지만, 일부 공구는 그림 4와 같이 주 절삭날과 보조 절삭날이 직접 교차하여 날카로운 공구 팁을 형성합니다.
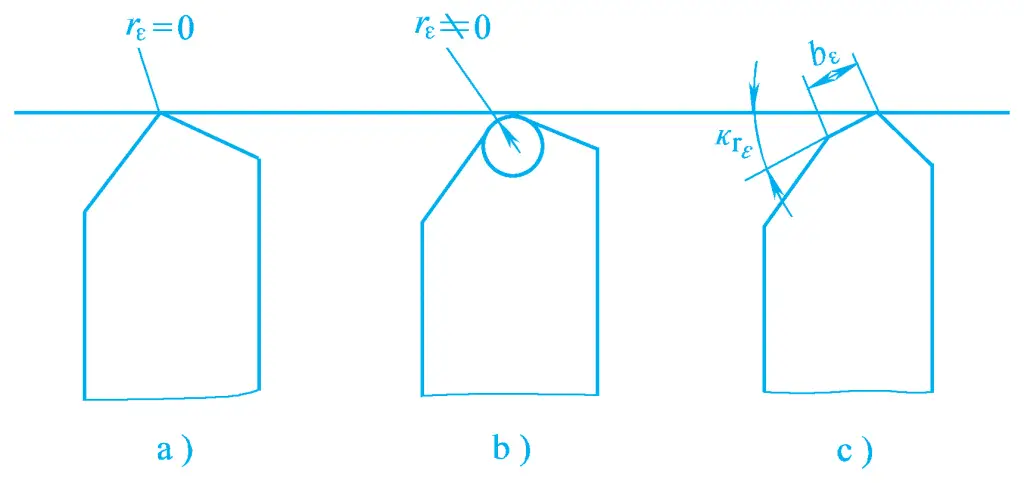
a) 선명한 도구 팁
b) 둥근 도구 팁
c) 모따기 도구 팁
공구 종류에 따라 공구면과 절삭날의 개수가 다를 수 있지만, 공구 절삭 부분의 가장 기본적인 단위는 두 개의 공구면(Aγ , Aα )와 하나의 메인 절삭 날로 구성됩니다. 복잡한 멀티 엣지 도구는 기본 단위로 분해하여 분석할 수 있습니다.
2. 도구의 직교 평면 고정 기준 시스템
공구 면과 공구 절삭 부분의 절삭 날의 공간 위치를 분석하고 공구의 설계, 제조, 연삭 및 측정을 용이하게 하려면 공구의 고정 각도 기준 시스템이라고 하는 공간 좌표 평면 기준 시스템을 설정해야 합니다.
절삭 공정 중 공구의 기하학적 각도의 역할을 쉽게 분석하려면 공구의 고정 각도 기준 시스템에서 좌표 평면을 설정할 때 절삭 동작을 기반으로 해야 합니다.
먼저 가정된 동작 조건과 가정된 설치 조건이 포함된 가정된 작업 조건이 주어진 다음 참조 시스템이 설정됩니다. 이 기준 시스템에서 결정된 도구 형상 각도를 도구의 정적 각도, 즉 주석이 달린 각도라고 합니다.
(1) 가정된 근무 조건
1) 가정된 모션 조건
공작물에 대한 절삭날에서 선택한 지점의 순간 주 동작 방향(공작물 회전 중심 평면에 위치한 경우)이 가정된 주 동작 방향으로 간주되고, 공작물에 대한 절삭날에서 선택한 지점의 순간 이송 동작 방향은 일반적으로 이송 동작 크기의 영향을 무시하고 즉, 이송 속도 f=0으로 가정하여 가정된 이송 동작 방향으로 간주됩니다.
2) 가정 설치 조건
선반 공구가 완전히 올바르게 설치되었다고 가정합니다. 즉, 선반 공구를 설치할 때 공구 팁이 공작물 회전 중심과 같은 높이에 있어야 하고 선반 공구 생크의 대칭면이 공작물 회전 축에 수직이어야 합니다.
(2) 도구의 정적 기준 시스템의 좌표 평면
1) 기본 평면 pr
절삭 날에서 선택한 지점을 통과하고 가정된 주 동작 방향에 수직인 평면을 기준 평면이라고 합니다. 선반 공구의 경우 기준 평면은 선반 공구 생크의 바닥면과 평행합니다.
2) 절단면 ps
절삭 날에서 선택한 지점을 통과하고 주 절삭 날에 접하며 기본 평면에 수직인 평면을 절삭 평면이라고 합니다.
3) 직교 평면 po
절단 모서리에서 선택한 점을 통과하고 기준면과 절단면 모두에 수직인 평면입니다.
3. 직교 평면 정적 참조 시스템 및 각도 주석
일반적으로 사용되는 직교 평면 정적 참조 시스템과 각도 주석은 아래에 소개되어 있습니다.
(1) 참조 시스템 구축
직교 평면 기준 시스템은 그림 5와 같이 이 세 개의 상호 수직인 좌표면이 시스템을 구성하며, 기준 평면 pr, 절단 평면 ps, 직교 평면 p로 구성됩니다.
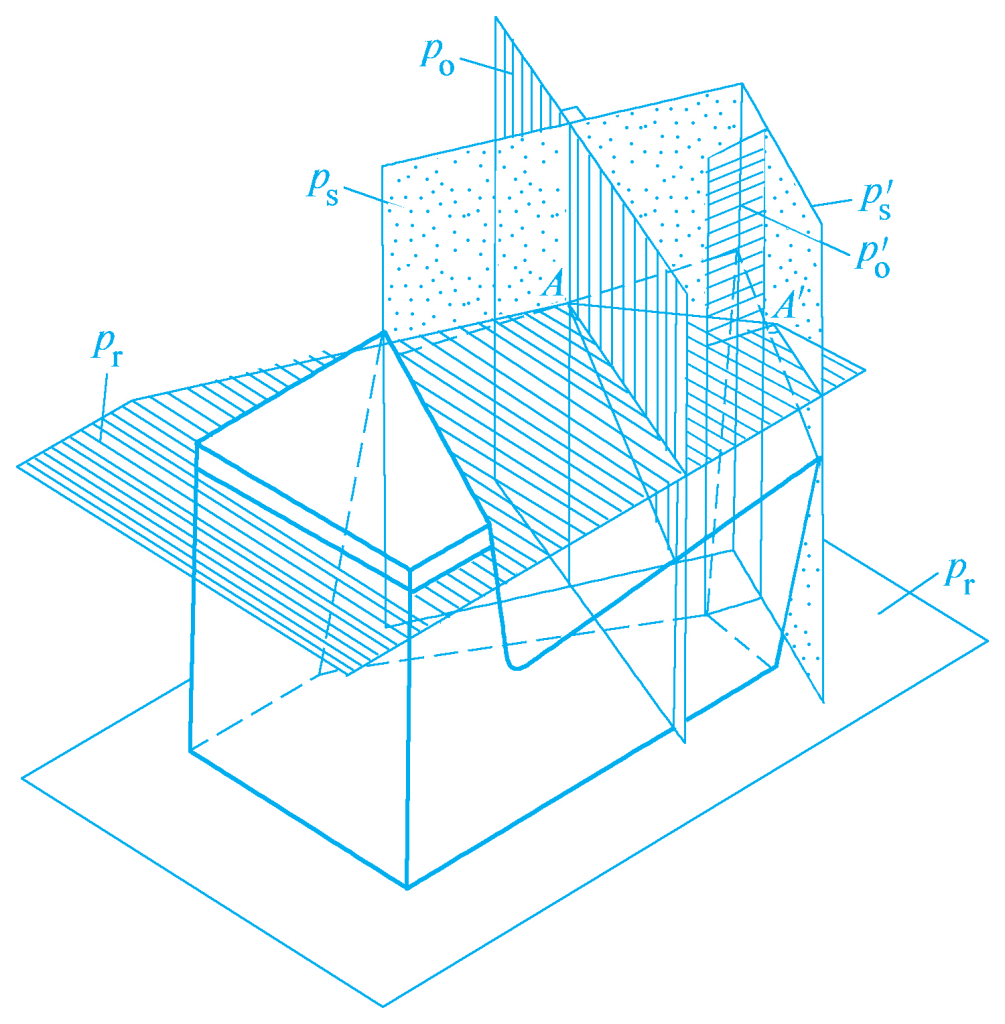
(2) 각도 주석
그림 6과 같이 이 참조 시스템에서 다음 각도에 주석을 달 수 있습니다.
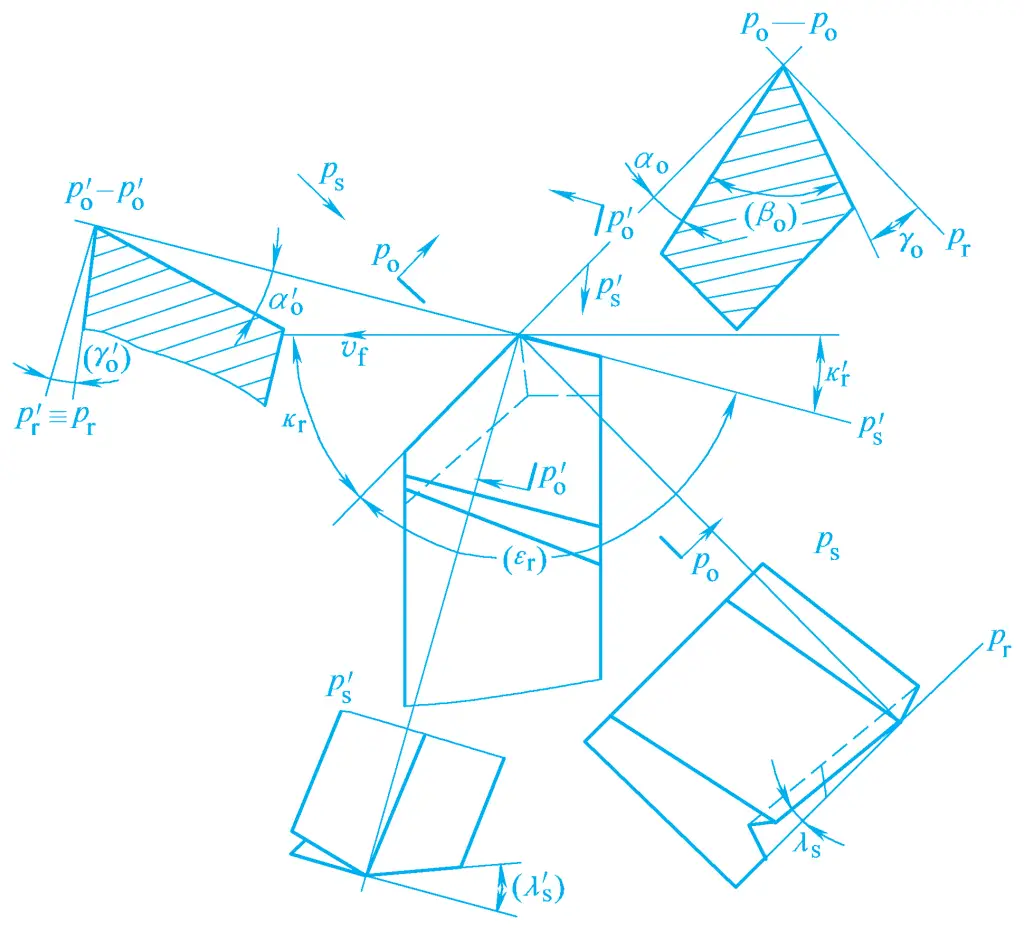
1) 주 편각 kr
베이스 평면에서 측정된 주 절삭날과 가정된 이송 동작 방향 사이의 각도를 주 편각이라고 합니다.
2) 커팅 엣지 경사각 λs
절삭 평면에서 측정된 주 절삭날과 공구 팁을 통과하는 베이스 평면 사이의 각도를 절삭날 경사각이라고 합니다.
3) 레이크 각도 γo
직교 평면에서 측정한 레이크 면과 기준 평면 사이의 각도를 레이크 각도라고 합니다.
4) 클리어런스 각도 αo
직교 평면에서 측정한 클리어런스 면과 절단면 사이의 각도를 클리어런스 각도라고 합니다.
위의 네 가지 각도를 사용하여 레이크면, 클리어런스면 및 주 절삭날의 방향을 결정할 수 있습니다. 레이크 각도 γo 와 절삭날 경사각 λs 레이크면의 방향, 주 경사각 K를 결정합니다.r 와 이격각 αo 클리어런스 면의 방향과 주 편각 K를 결정합니다.r 와 절삭날 경사각 λs 주 절삭 날의 방향을 결정합니다.
마찬가지로 보조 절삭 날의 한 점을 선택하면 보조 모재 평면 P'r 보조 절단면 p's 및 보조 직교 평면 p'o 도 설정할 수 있습니다. 보조 레이크 면과 보조 측면 면의 해당 위치는 보조 경사각 k'에 의해 결정됩니다.r , 보조 에지 경사각 λ's 보조 경사각 γ'o 및 보조 클리어런스 각도 α'o .
보조 절삭날과 주 절삭날이 모두 동일한 레이크 면에 있기 때문에, 각도가 γo 및 λs 가 결정되면 레이크면의 위치가 고정됩니다. 따라서 각도 γ'o 및 λ's 도 결정됩니다. 따라서 보조 측면면의 위치를 결정하려면 일반적으로 보조 경사각 k'만 결정하면 됩니다.r 와 보조 클리어런스 각도 α'o 보조 절삭 날을 통해
5) 보조 경사각 k'r
베이스 평면에서 측정된 보조 절삭날과 가정된 이송 방향 사이의 각도를 보조 경사각이라고 합니다.
6) 보조 클리어런스 각도 α'o
보조 직교 평면에서 측정한 보조 측면 면과 보조 절단면 사이의 각도를 보조 간격 각도라고 합니다.
따라서 그림 6에 표시된 외부 선삭 공구에는 3개의 면과 2개의 절삭 날이 있으며, 표시해야 하는 독립적인 각도는 γ만 6개입니다.o , αo , kr , k'r , λs , α'o . 그중에서도 kr 및 k'r 는 기본 평면에 표시되어 있고, γo 및 αo 은 직교 평면에 표시되고, λ s 은 절단면에 표시되고 α'o 는 보조 직교 평면에 표시됩니다.
도구를 분석할 때 다음 두 가지 파생된 각도가 자주 사용됩니다(그림 6의 괄호 안의 두 각도):
7) 쐐기 각도 βo
직교 평면에서 측정한 레이크 면과 측면 면 사이의 각도를 쐐기 각도라고 합니다.
βo = 90° - (γo + αo )
8) 도구 팁 각도 εr
베이스 평면에서 측정된 주 절삭날과 보조 절삭날 사이의 각도를 공구 팁 각도라고 합니다.
εr = 180° - (kr + k'r )
(3) 각도의 포지티브 및 네거티브에 대한 규정
그림 7a에서와 같이 경사면이 기준면과 평행하면 경사각은 0이고, 경사면과 절단면 사이의 각도가 90°보다 작으면 경사각은 양수이고, 90°보다 크면 경사각은 음수입니다. 측면면과 기준면 사이의 각도가 90° 미만이면 클리어런스 각도는 양수이고, 90°보다 크면 클리어런스 각도는 음수입니다.
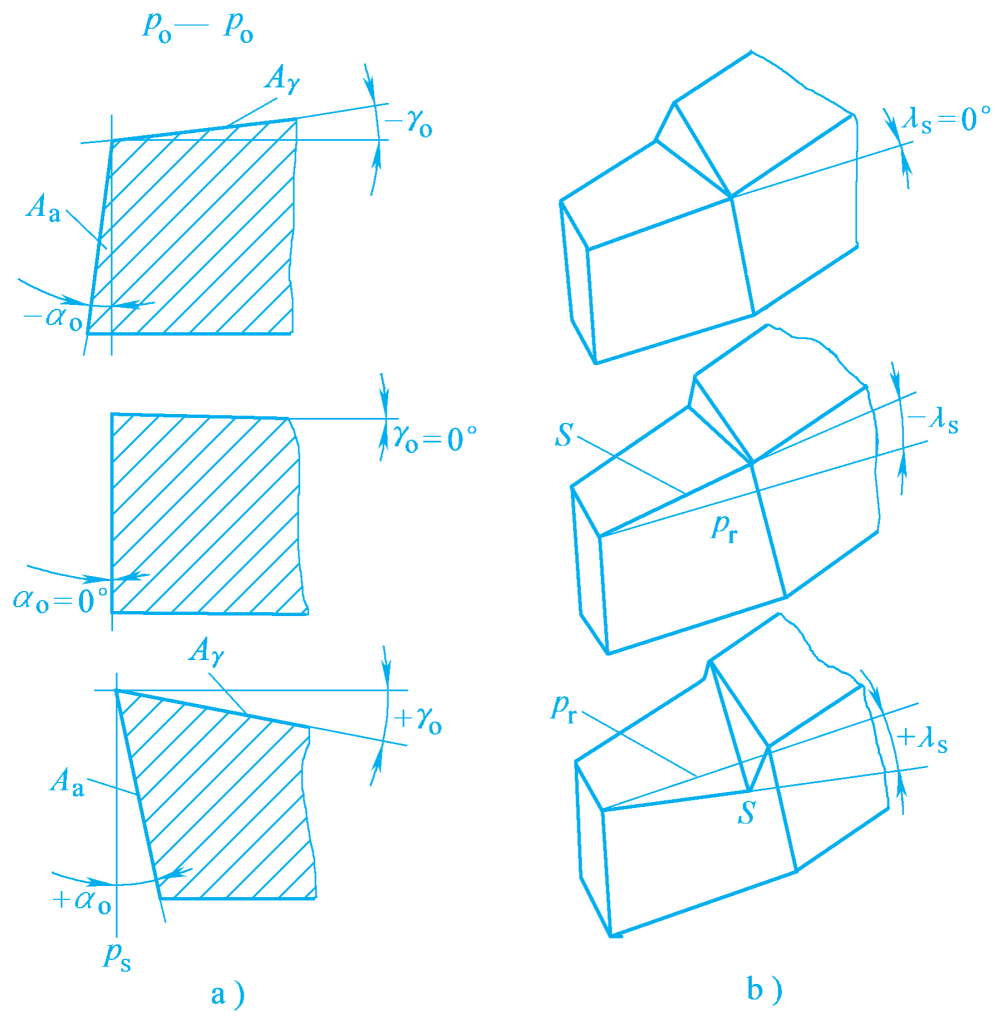
a) 레이크 및 클리어런스 각도
b) 가장자리 경사각
그림 7b와 같이 공구 팁이 절삭 날의 가장 높은 지점에 있으면 절삭 날 경사각은 양수이고, 공구 팁이 절삭 날의 가장 낮은 지점에 있으면 절삭 날 경사각은 음수이며, 절삭 날과 베이스 평면이 일치하면 절삭 날 경사각은 0이 됩니다.
주 경사각과 보조 경사각은 0°에서 90° 사이입니다.
IV. 절단 요소
절단 요소는 절단량 요소와 절단 레이어 요소의 두 가지 주요 범주로 나뉩니다.
1. 절단 금액 요소
절삭 공정 중에는 다양한 공작물 재료, 공구 재료 및 기타 기술적, 경제적 요인에 따라 적절한 절삭량 요소를 선택해야 합니다. 절삭 속도, 이송 속도 및 절삭 깊이를 절삭량의 세 가지 요소라고 하며 공정 절삭 요소라고도 합니다(그림 8 참조). 절삭량 요소는 가공 품질, 높은 생산성 및 낮은 가공 비용을 보장하기 위해 공작 기계를 올바르게 조정하는 데 사용됩니다.
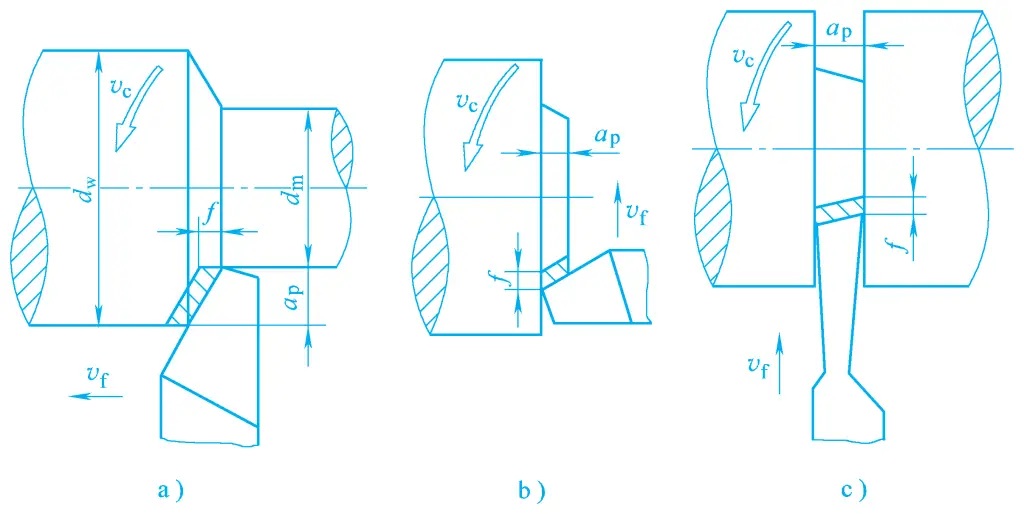
a) 외부 회전
b) 마주보기
c) 그루브
(1) 절단 속도 vc
절삭 속도는 주 동작 방향으로 가공할 표면을 기준으로 공구 절삭 날의 한 지점의 순간 속도입니다. 외부 실린더를 돌릴 때 계산 공식은 다음과 같습니다:
vc = πdw n / 1000
어디
- vc - 절단 속도(m/min 또는 m/s 단위).
- dw - 가공할 공작물 표면의 직경(mm)입니다;
- n - 공작물 회전 속도(r/min 또는 r/s 단위).
절삭날의 여러 지점에서의 절삭 속도가 다릅니다. 계산할 때는 최대 절삭 속도를 사용해야 합니다. 예를 들어 바깥쪽 원을 돌릴 때는 여기서 속도가 가장 높고 공구가 가장 빨리 마모되므로 가공할 표면의 직경이 계산에 사용됩니다.
(2) 이송 속도 f
이송 속도는 이송 동작 방향에서 공작물에 대한 공구의 변위입니다. 공구 또는 공작물의 회전당 변위 또는 스트로크당 변위로 표현할 수 있습니다. 주 동작이 회전인 경우 f의 단위는 mm/r입니다.
밀링 커터 및 리머와 같은 다중 톱니 공구의 경우 톱니당 이송량은 다음과 같습니다. z 는 이송 동작 방향에서 공작물을 기준으로 통과하는 톱니당 멀티 톱니 공구의 상대 변위(mm/z 단위)로도 지정됩니다. 이송 속도는 종종 이송 속도 v로 표현되기도 합니다. f 는 이송 동작 방향의 공작물에 대한 절삭 날에서 선택한 지점의 순간 속도(mm/min)입니다.
vf = fn
즉
vf = fz zn
공식에서 z는 치아 수입니다.
(3) 절단 깊이 a p
절삭 깊이는 일반적으로 가공할 표면과 공작물의 가공된 표면 사이의 수직 거리를 나타냅니다. 바깥쪽 원을 돌릴 때:
ap=(dw-dm)/2
어디
- dw - 가공할 표면의 직경(mm)입니다;
- dm - 가공된 표면의 직경(mm)입니다.
2. 절단 층의 공칭 단면 요소
공구 절삭 날에 의해 한 번의 이송으로 가공할 표면에서 절단되는 금속 층을 절삭 층이라고 합니다. 바깥쪽 원을 돌리면 공작물이 한 번 회전하고 공구가 위치 I에서 위치 II로 이동하면서 한 이송 속도만큼 전진합니다. 그림 9에서 음영 처리된 부분이 절삭 레이어입니다.
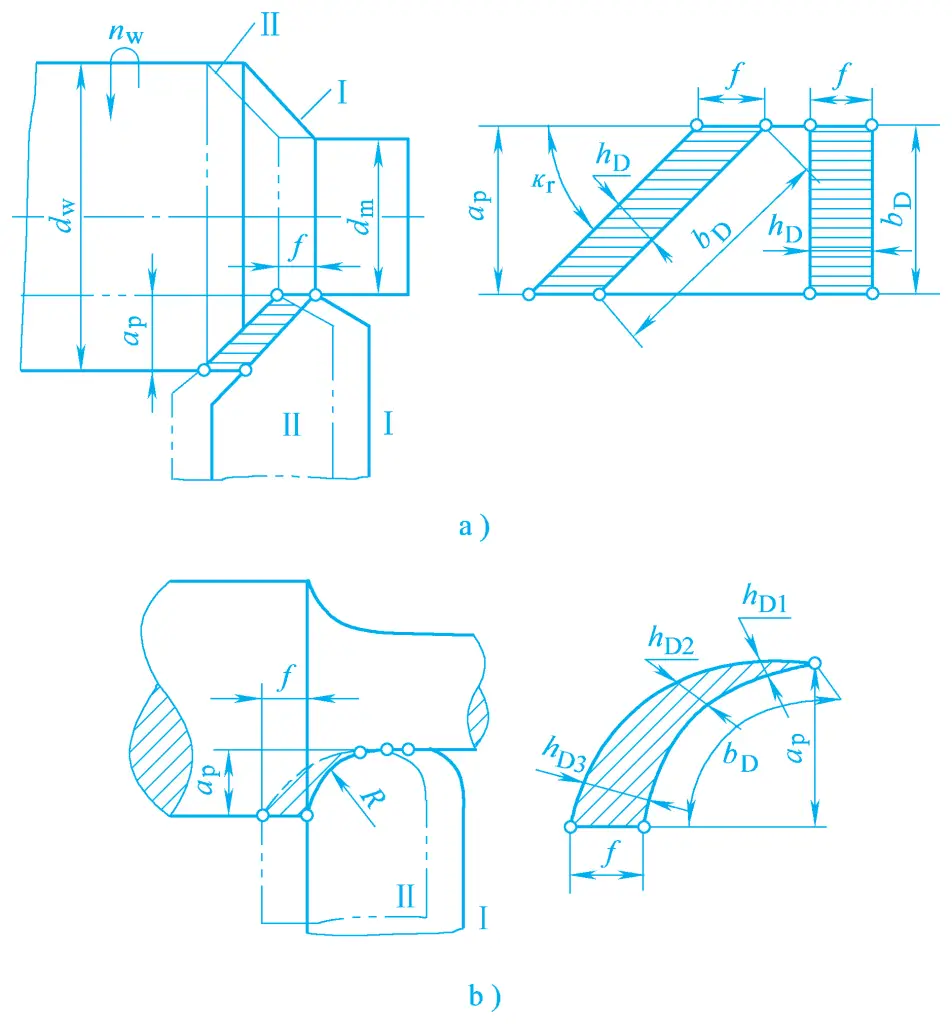
a) 직선 모서리의 경우
b) 곡선형 가장자리의 경우
단면 치수의 크기는 공구에 가해지는 하중과 절삭 레이어의 크기를 결정하는 절삭 레이어 매개변수입니다. 또한 절삭력, 공구 마모, 공작물 표면 품질 및 생산성에도 영향을 미칩니다.
커팅 레이어 크기는 다음 세 가지 매개 변수로 표현할 수 있습니다:
(1) 절단 층의 공칭 두께 hD
절단 레이어의 공칭 두께는 절삭 날의 두 순간 위치의 전이 표면 사이의 거리를 나타냅니다.
(2) 절단 레이어의 공칭 너비 bD
절단 레이어의 공칭 폭은 전환 표면을 따라 측정한 절단 레이어의 크기를 나타냅니다.
(3) 절단 층의 공칭 단면적 AD
절단 레이어의 공칭 단면적은 절단 레이어의 단면적을 나타냅니다.