1. Techniki cięcia i przekłuwania
Każda technika cięcia termicznego wymaga zazwyczaj utworzenia niewielkiego otworu w materiale, z wyjątkiem kilku przypadków, w których proces można rozpocząć od krawędzi arkusza.
Wcześniej, w kombinacjach wykrawarek laserowych, wykrawarka początkowo tworzyła otwór, a następnie cięcie laserowe rozpoczynało się od tego małego otworu. W przypadku wycinarek laserowych bez urządzeń wykrawających istnieją dwie podstawowe metody przebijania:
Blast Piercing - Ciągłe promieniowanie laserowe tworzy wgłębienie w środku materiału, a następnie strumień tlenu współosiowy z wiązką laserową szybko usuwa stopiony materiał, tworząc otwór.
Ogólnie rzecz biorąc, rozmiar otworu jest powiązany z grubością blachy, przy czym średnia średnica przebicia jest równa połowie grubości.
W związku z tym przebijanie strumieniowo-ścierne tworzy większe, nieokrągłe otwory w grubszych blachach, które są nieodpowiednie dla części wymagających wysokiej precyzji i nadają się tylko do złomu.
Dodatkowo, ponieważ ciśnienie tlenu używanego do przekłuwania jest takie samo, jak w przypadku cięcia, rozpryskiwanie jest znaczące.
Pulse Piercing - Laser impulsowy o wysokiej mocy szczytowej topi lub odparowuje niewielką ilość materiału. Powietrze lub azot są często używane jako gaz pomocniczy w celu zminimalizowania rozszerzania się otworów w wyniku utleniania egzotermicznego, a ciśnienie gazu jest niższe niż ciśnienie tlenu używanego podczas cięcia.
Każdy impuls lasera wytwarza mały strumień cząstek, który stopniowo penetruje materiał, dlatego przebijanie grubych arkuszy może trwać kilka sekund. Po zakończeniu przebijania gaz pomocniczy jest natychmiast zastępowany tlenem w celu cięcia.
Metoda ta zapewnia mniejsze otwory i lepszą jakość przebijania w porównaniu do przebijania strumieniowego. Wykorzystywane do tego lasery nie tylko muszą mieć wysoką moc wyjściową, ale co ważniejsze, czasowa i przestrzenna charakterystyka wiązki musi być optymalna.
W związku z tym typowe lasery CO2 o przepływie poprzecznym są generalnie nieodpowiednie dla cięcie laserowe wymagania. Co więcej, przebijanie impulsowe wymaga niezawodnego systemu kontroli gazu do zarządzania rodzajem gazu, zmianami ciśnienia gazu i kontrolą czasu przebijania.
W przypadku stosowania przebijania impulsowego, w celu uzyskania wysokiej jakości cięcia, należy zwrócić szczególną uwagę na przejście od przebijania impulsowego na postoju do cięcia ciągłego ze stałą prędkością.
Teoretycznie warunki cięcia, takie jak ogniskowa, pozycja dyszy i ciśnienie gazu, mogą być zmieniane podczas fazy przyspieszania, ale w praktyce ramy czasowe są zbyt krótkie, aby zmiany te były wykonalne.
W produkcji przemysłowej bardziej realistycznym podejściem jest dostosowanie średniej mocy lasera, w szczególności poprzez modyfikację szerokości impulsu, zmianę częstotliwości impulsu lub jednoczesną regulację szerokości i częstotliwości impulsu. Praktyczne wyniki wskazują, że trzecia metoda zapewnia najlepsze rezultaty.
2. Analiza odkształceń podczas wycinania małych otworów (średnica mniejsza niż grubość blachy)
Wynika to z faktu, że obrabiarki (w szczególności wycinarki laserowe o dużej mocy) nie wykorzystują metody perforacji strumieniowej podczas obróbki małych otworów, ale zamiast tego stosują metodę pulsacyjnego przebijania (miękkie przebicie).
Powoduje to nadmierną koncentrację energii lasera na małym obszarze, spalając i deformując obszar nieobrobiony oraz wpływając na jakość pracy. W takich przypadkach powinniśmy zmodyfikować program obróbki z przebijania pulsacyjnego (miękkie przebicie) na perforację strumieniową (zwykłe przebicie), aby naprawić problem.
Z drugiej strony, w przypadku wycinarek laserowych o niższej mocy najlepiej jest stosować metodę przebijania pulsacyjnego, aby uzyskać lepszą gładkość powierzchni podczas obróbki małych otworów.
3. Rozwiązania dla zadziorów pojawiających się w obrabianych przedmiotach podczas cięcia stali niskowęglowej laserem
W oparciu o zasady działania i projektowania Cięcie laserem CO2Przeanalizowaliśmy następujące główne przyczyny, które przyczyniają się do powstawania zadziorów na obrabianych elementach:
- Nieprawidłowe pozycjonowanie ogniska lasera w górę i w dół, wymagające testu pozycji ogniska i regulacji zgodnie z przesunięciem ogniska;
- Niewystarczająca moc wyjściowa lasera, wymagająca sprawdzenia wydajności generatora lasera oraz, jeśli jest to normalne, obserwacji i regulacji prawidłowych wartości wyjściowych na przycisku sterowania laserem;
- Zbyt niska prędkość linii cięcia, wymagająca zwiększenia prędkości linii podczas kontroli operacyjnej;
- Niewystarczająca czystość gazu tnącego, wymagająca zapewnienia wysokiej jakości gazu do cięcia;
- Przesunięcie ogniskowania lasera, wymagające testu pozycji ogniskowania i regulacji w oparciu o przesunięcie ogniskowania;
- Niestabilność obrabiarki z powodu długiego czasu pracy, w którym to przypadku konieczne jest wyłączenie i ponowne uruchomienie.
4. Analiza powstawania zadziorów w laserze Cięcie stali nierdzewnej i blachy powlekane cynkiem i aluminium
Wystąpienie powyższej sytuacji wiąże się przede wszystkim z czynnikami prowadzącymi do powstawania zadziorów podczas cięcia stali niskowęglowej.
Jednak samo zwiększenie prędkość cięcia nie jest rozwiązaniem, ponieważ czasami powoduje niepełną penetrację blachy, co jest szczególnie widoczne podczas obróbki blach powlekanych aluminium i cynkiem.
W tym momencie konieczne jest rozważenie innych czynników związanych z obrabiarką, takich jak konieczność wymiany dyszy lub niestabilność ruchu szyny.
5. Analiza niekompletnego cięcia laserowego
Po analizie stwierdzono, że następujące sytuacje są głównymi przyczynami niestabilnego przetwarzania:
- Wybrana dysza głowicy laserowej nie pasuje do grubości obrabianego arkusza;
- Prędkość linii cięcia laserowego jest zbyt duża, co wymaga kontroli operacyjnej w celu zmniejszenia prędkości linii.
Dodatkowo należy zauważyć, że gdy L3030 wycinarka laserowa cięcie blach ze stali węglowej o grubości powyżej 5 mm wymaga wymiany soczewki lasera o ogniskowej 7,5″.
6. Rozwiązanie dla nieprawidłowych iskier podczas cięcia stali niskowęglowej
Sytuacja ta może mieć wpływ na gładkość sekcji tnącej i jakość obróbki części.
W takim przypadku, gdy wszystkie inne parametry są w normie, należy rozważyć następujące kwestie: zużycie dyszy głowicy lasera (NOZZEL) - dyszę należy wymienić w odpowiednim czasie.
Jeśli nie można wymienić dyszy, należy zwiększyć ciśnienie gazu roboczego; gwinty na połączeniu dyszy i głowicy lasera są luźne.
Cięcie należy natychmiast wstrzymać, sprawdzić stan połączenia głowicy laserowej i ponownie prawidłowo zamocować gwinty.
7. Wybór punktów przebicia podczas cięcia laserowego
Zasada działania wiązki laserowej podczas cięcia laserowego jest następująca: W procesie tym, po ciągłym naświetlaniu laserem, w środku materiału tworzy się wgłębienie. Wgłębienie to jest następnie szybko usuwane przez współosiowy przepływ powietrza roboczego, tworząc otwór w materiale.
Otwór ten jest podobny do otworu gwintowanego w cięciu drutem, w którym wiązka lasera rozpoczyna cięcie konturowe.
Zazwyczaj kierunek ścieżki latającej wiązki laserowej ścieżki optycznej jest prostopadły do kierunku stycznej konturu cięcia obrabianej części.
Dlatego od momentu, gdy wiązka lasera zaczyna penetrować stalową płytę, aż do momentu wejścia w konturowe cięcie części, następuje znaczna zmiana prędkości cięcia w kierunku wektorowym - obrót o 90°.
Kierunek zmienia się z prostopadłego do stycznej konturu cięcia na pokrywający się z nią, tj. kąt 0° ze styczną konturu. Ta szybka zmiana kierunku wektora wiązki laserowej w krótkim czasie skutkuje raczej szorstką powierzchnią cięcia na obrabianym materiale.
W związku z tym aspekt ten należy wziąć pod uwagę podczas korzystania z cięcia laserowego do obróbki części.
Ogólnie rzecz biorąc, jeśli w projekcie nie ma wymagań dotyczących chropowatości ciętej powierzchni części, ręczne regulacje nie są konieczne podczas programowania cięcia laserowego. Oprogramowanie sterujące może automatycznie generować punkty przebicia.
Jeśli jednak projekt wymaga wyższego stopnia chropowatości powierzchni cięcia obrabianej części, należy zająć się tą kwestią.
Zazwyczaj podczas programowania procedury cięcia laserowego konieczne jest ręczne dostosowanie pozycji początkowej wiązki lasera, tj. ręczne sterowanie punktami przebicia.
Pierwotnie wygenerowane punkty przebicia w programie laserowym muszą zostać przesunięte do rozsądnej pozycji, aby spełnić wymagania dotyczące dokładności powierzchni obrabianej części.
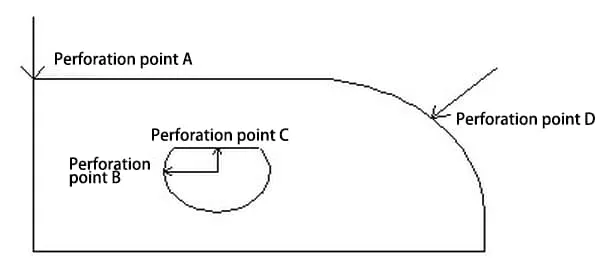
Jak pokazano na rysunku 1, jeśli ten element wymaga precyzji w łuku, punkty początkowe (punkty przebicia) dla programu cięcia laserowego powinny być ustawione na A i C, a nie na B i D. Jeśli jednak precyzja wymagana dla tego elementu dotyczy tylko prostych krawędzi, punkty początkowe dla programu cięcia laserowego powinny być ustawione na B i D, a nie na A i C.
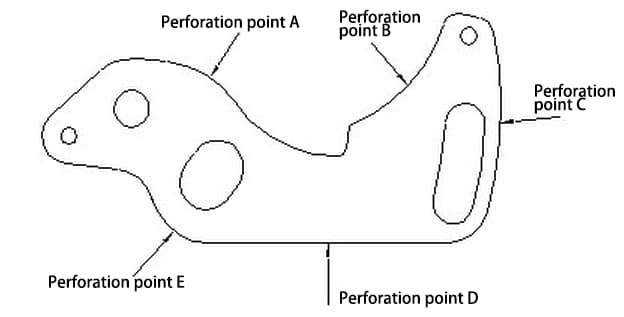
Jak pokazano na rysunku 2, jeśli konstrukcja tego elementu wymaga precyzji łuku, punkt początkowy (punkt przebicia) programu cięcia laserowego można ustawić tylko w punkcie D.
Jeśli jednak część wymaga precyzji tylko na prostych krawędziach, możemy wybrać dowolny punkt inny niż D jako punkt początkowy (punkt przebicia) podczas tworzenia programu cięcia laserowego.
Cięcie laserowe części blaszane to zaawansowana technika produkcji. Nie tylko znacznie skraca cykl rozwoju i koszty produkcji form, ale także poprawia jakość i wydajność produkcji, ułatwiając innowacje techniczne i sprzętowe w przemyśle wytwórczym.
W praktycznych zastosowaniach istotne jest, abyśmy stale gromadzili doświadczenie, pogłębiali nasze zrozumienie i ćwiczyli. W ten sposób ta nowa technologia może przyczynić się do zwiększenia naszej produktywności.