Os principais fatores que afetam a qualidade da corte a laser podem ser divididos em duas categorias: a influência do desempenho do sistema de corte a laser e a influência dos parâmetros de corte a laser. A primeira deve ser considerada na compra de lasers e no estabelecimento de um sistema de corte a laser, enquanto a segunda está relacionada a como escolher e otimizar os parâmetros durante o processo de corte a laser. processo de corte a laser.
Impacto do desempenho do sistema de corte a laser na qualidade do corte
Modo de feixe
Quanto menor o modo do feixe, menor o tamanho do ponto após a focalização, maior a iluminação radiante, mais estreito o corte e maior a eficiência do corte e a qualidade da superfície. A Figura 8-8 mostra a curva de impacto de dois modos de feixe sobre a rugosidade da superfície de corte. Usando um TEM00 para cortar uma placa de 2 mm de espessura, a rugosidade da superfície de corte Rz é de apenas 0,8μm, alcançando um nível muito suave.
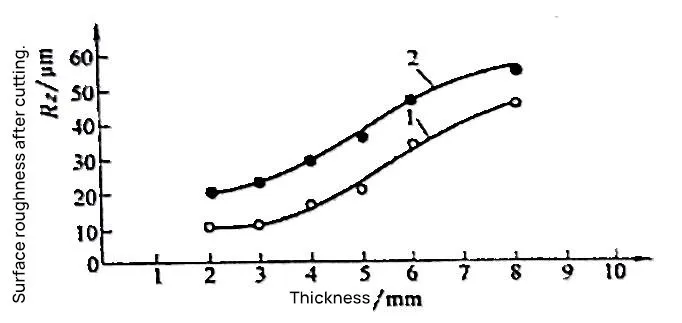
- 1-TEM00
- 2-TEM01
A qualidade de corte com o TEM01 é um pouco pior, mas ainda mantém um bom nível. A Figura 8-9 mostra a curva de impacto dos dois modos de feixe na velocidade de corte. Como visto na Figura 8-9, quando corte uma placa de aço inoxidável de 2 mm de espessura com um laser de modo TEM00 de 500 W, a velocidade de corte pode chegar a 2,0 m/min, enquanto com um laser de modo TEM01, a velocidade de corte é de apenas 1,0 m/min.
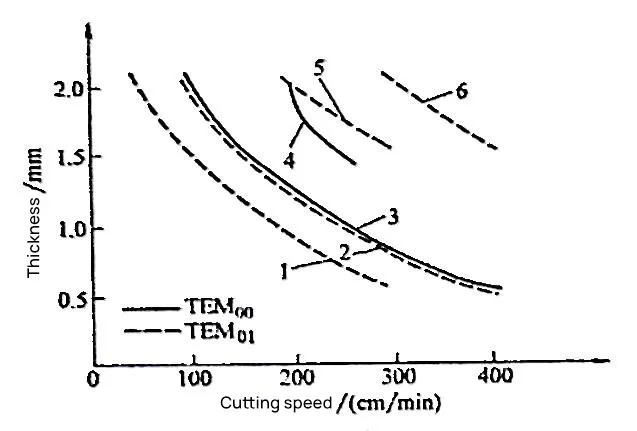
- 1, 3-300W
- 2, 4-500W
- 5-800W
- 6-1000W
- Observação: Material: Aço inoxidável SUS304.
Portanto, para obter uma melhor qualidade de corte e uma maior eficiência de corte, é melhor escolher um equipamento TEM00 ou, pelo menos, não superior ao laser de modo TEM01 modo. Lasers com modos superiores a TEM01 não pode garantir a qualidade do corte e não deve ser usado.
Polarização do feixe
A polarização do feixe de laser afeta muito a qualidade e a eficiência do corte a laser. Se a luz linearmente polarizada for usada para o corte, a direção do corte mudará em relação à direção de polarização do feixe, a taxa de absorção da borda de corte para o laser mudará, afetando assim o efeito do corte a laser.
1) Quando a direção de corte é paralela à direção da polarização, a taxa de absorção da borda de corte em relação ao laser é a mais alta, de modo que o corte é estreito, a perpendicularidade e a rugosidade do corte são baixas e a velocidade de corte é rápida, conforme mostrado na Figura 8-10a.
2) Quando a direção de corte é perpendicular à direção da polarização, a taxa de reflexão da borda de corte para o laser é a mais alta, a taxa de absorção é a menor e a taxa de absorção lateral aumenta, de modo que a velocidade de corte diminui, o corte se alarga e o valor da rugosidade da superfície de corte também aumenta, conforme mostrado na Figura 8-10b.
3) Quando a direção de corte está em um ângulo com a direção de polarização, a direção com a maior taxa de absorção do laser também está em um ângulo com a direção de corte, resultando em uma inclinação na parte inferior do corte, conforme mostrado nas Figuras 8-10c e 8-10d.
4) Para evitar alterações no formato do corte e na qualidade da superfície de corte devido a mudanças na direção do corte, deve-se usar luz polarizada circularmente para o corte. A amplitude do vetor elétrico da luz polarizada circularmente é igual em todas as direções, de modo que a taxa de absorção da borda de corte para o laser não muda com a mudança na direção de corte, e o corte é uniforme e limpo, conforme mostrado na Figura 8-10e.
Para converter a saída de luz linearmente polarizada do laser em luz circularmente polarizada, um polarizador circular deve ser adicionado na saída do feixe.
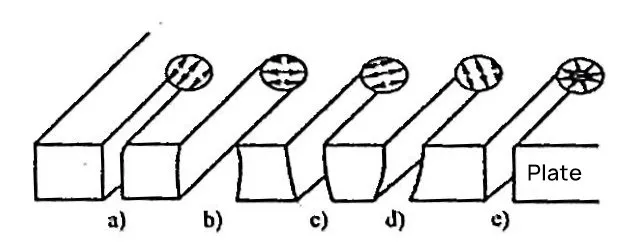
Bocal e fluxo de gás
A pressão e a vazão do gás auxiliar estão relacionadas à estrutura e ao tamanho do bocal, que influenciam muito a qualidade e o desempenho do produto. velocidade de corte a laser.
(1) Estrutura do bocal
A Figura 8-11 lista várias formas estruturais de bicos de corte a laser, entre as quais o bico cônico mostrado na Figura 8-11a é o mais usado.
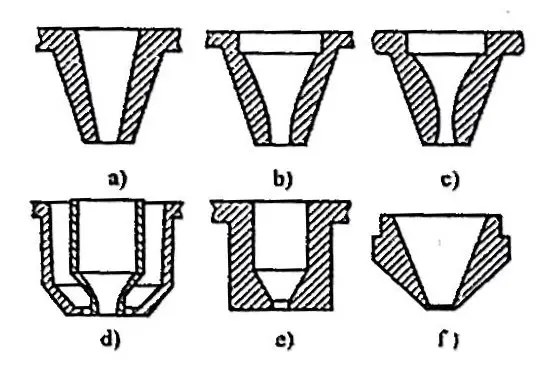
(2) Abertura do bocal
O tamanho da abertura do bocal deve primeiro garantir que o feixe possa passar suavemente, evitando que o feixe dentro do orifício toque a parede interna do bocal. Quanto menor a abertura, mais difícil será a colimação do feixe, portanto, a abertura não pode ser muito pequena.
Além disso, sob uma determinada pressão de gás auxiliar, há uma faixa ideal para a abertura do bocal. Uma abertura muito pequena ou muito grande afetará a folga do produto fundido no corte pelo gás auxiliar, afetando, assim, a velocidade de corte. As Figuras 8-12 e 8-13 mostram o impacto da abertura do bocal sobre a velocidade de corte. velocidade de corte de uma placa de aço de baixo carbono com 2 mm de espessura sob determinada potência de laser e pressão de gás auxiliar.
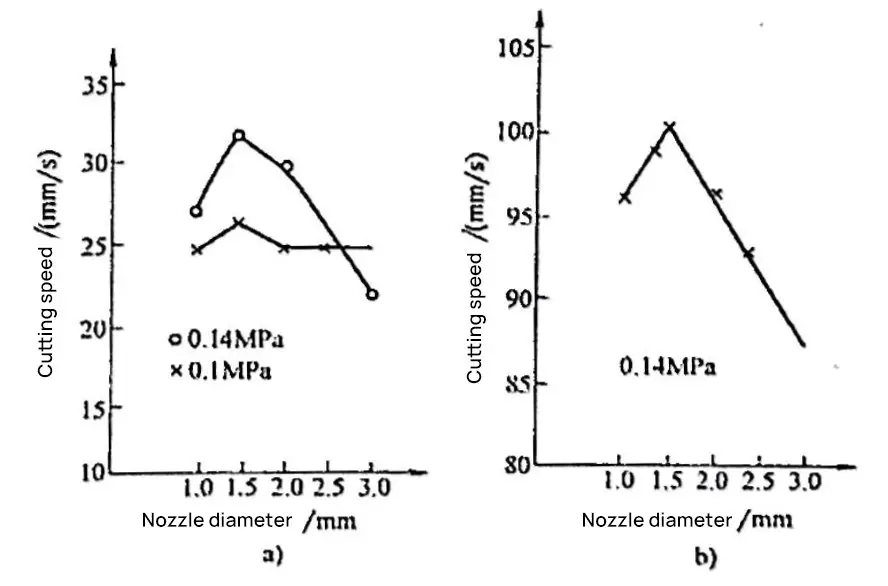
a) Argônio
b) Oxigênio
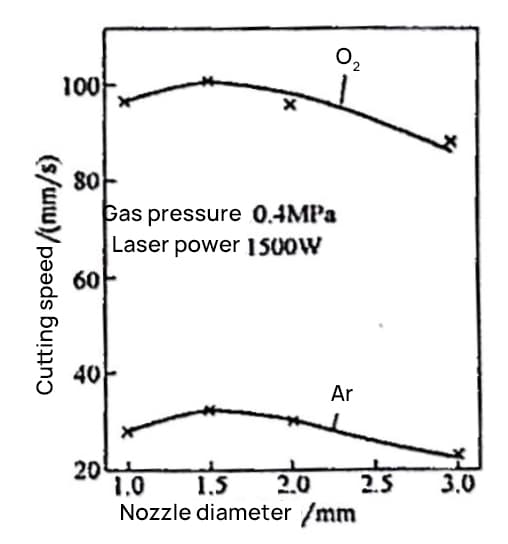
Como pode ser visto nas Figuras 8-12 e 8-13, há um valor ideal de abertura do bocal para atingir a velocidade máxima de corte. Independentemente de o oxigênio ou o argônio ser usado como gás auxiliar, esse valor ideal é de cerca de 1,5 mm. Os testes de corte a laser em ligas duras, que são difíceis de cortar, mostram que o valor ideal da abertura do bocal também é muito próximo dos resultados acima, conforme mostrado na Figura 8-14.
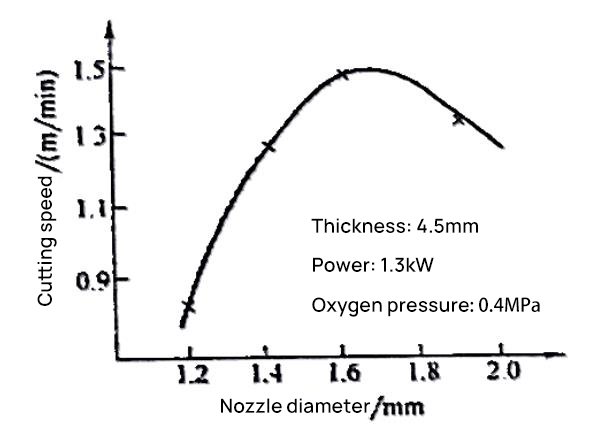
A abertura do bico também afeta a largura da fenda de corte e o tamanho da zona afetada pelo calor, conforme mostrado na Figura 8-15. Como pode ser visto na Figura 8-15, à medida que a abertura aumenta, o corte se alarga e a zona afetada pelo calor se estreita. A principal razão para o estreitamento da zona afetada pelo calor é que o efeito de resfriamento do fluxo de gás auxiliar no material de base na área de corte é aumentado.
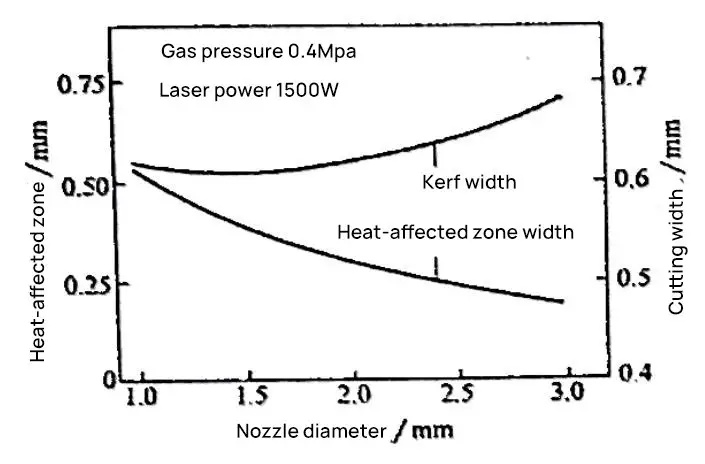
(3) Pressão do gás do bocal
O aumento da pressão do gás pode melhorar a velocidade de corte, mas, depois de atingir um valor máximo, outros aumentos na pressão causarão uma diminuição na velocidade de corte.
Como pode ser visto nas Figuras 8-16 e 8-17, a velocidade máxima de corte é uma função da potência do laser e da espessura da placa da peça de trabalho. Em altas pressões de gás auxiliar, a velocidade de corte diminui. As razões para essa diminuição podem ser atribuídas não apenas ao efeito de resfriamento aprimorado das altas velocidades do fluxo de ar na área de ação do laser, mas também à interferência de ondas de choque intermitentes no fluxo de ar com a área de ação do laser.
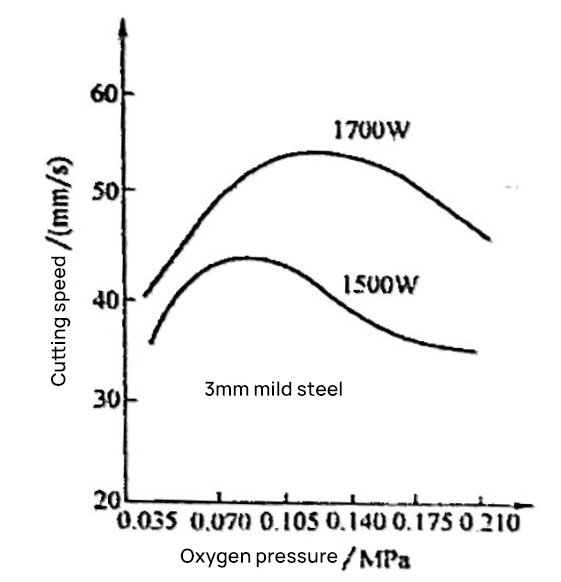
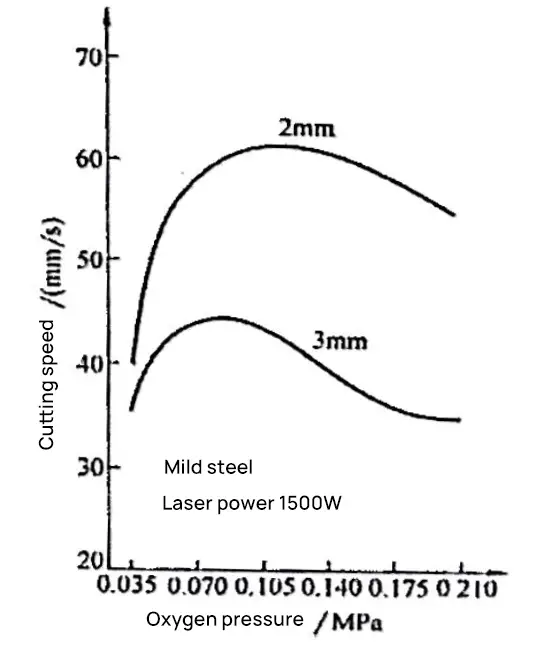
A presença de pressão e temperatura irregulares no fluxo de ar causará alterações na densidade do campo de fluxo de ar. SteenWM e outros mediram que, sob altas pressões de gás, há um campo de gradiente de densidade na superfície da peça de trabalho diretamente na frente do bocal, cuja forma e tamanho dependem da pressão do gás, da distância entre a extremidade do bocal e a peça de trabalho e da abertura do bocal.
Esse campo de gradiente de densidade causa alterações no índice de refração dentro do campo, interferindo, assim, na focalização do feixe de laser, causando a refocalização ou a divergência do feixe, conforme mostrado na Figura 8-18. Essa interferência pode afetar a eficiência da fusão e, às vezes, pode alterar a estrutura do modo, causando uma queda na qualidade do corte. Se o feixe divergir muito, tornando o ponto muito grande, o corte normal pode até se tornar impossível.
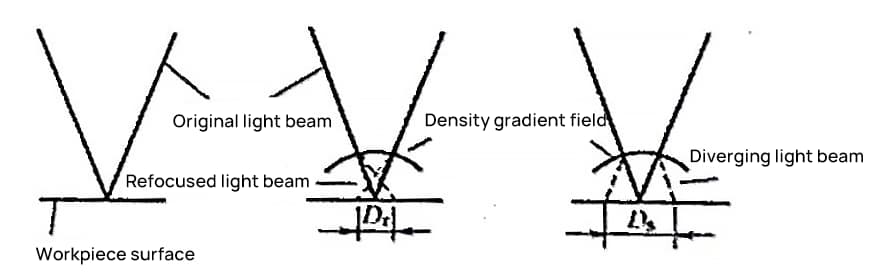
Impacto dos parâmetros de corte a laser na qualidade do corte
Influência da posição do foco na rugosidade da superfície
O impacto da posição do foco na rugosidade da superfície do corte é mostrado na Figura 8-19, em que a coordenada horizontal na Figura 8-19 é a razão ab da distância da peça de trabalho até a lente de foco e a distância focal.
Na Figura 8-19, é possível observar que a faixa mais suave da superfície do corte é: 0,988 <ab< 1,003, portanto, para o corte geral, o foco geralmente é colocado a 1 mm abaixo da superfície da peça de trabalho.
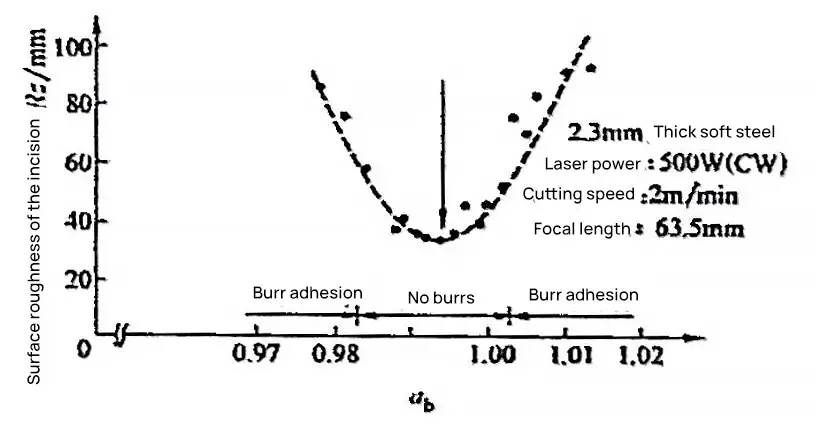
Impacto da potência do laser e da velocidade de corte na largura do Kerf
A largura do corte aumenta com o aumento da potência do laser e diminui com o aumento da velocidade de corte, conforme mostrado nas Figuras 8-20 e 8-21.
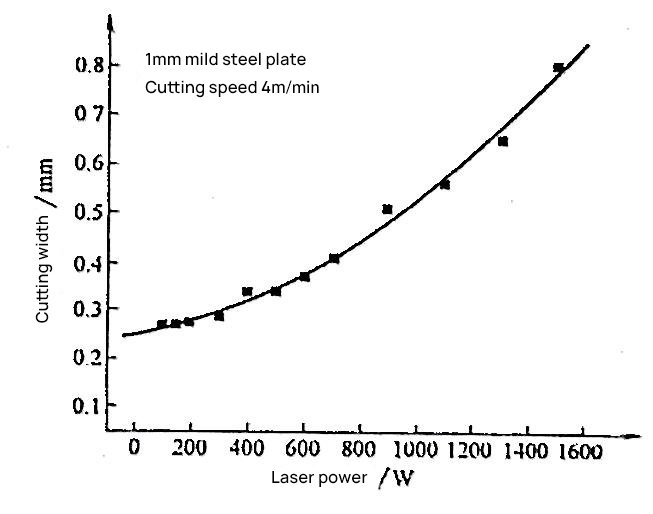
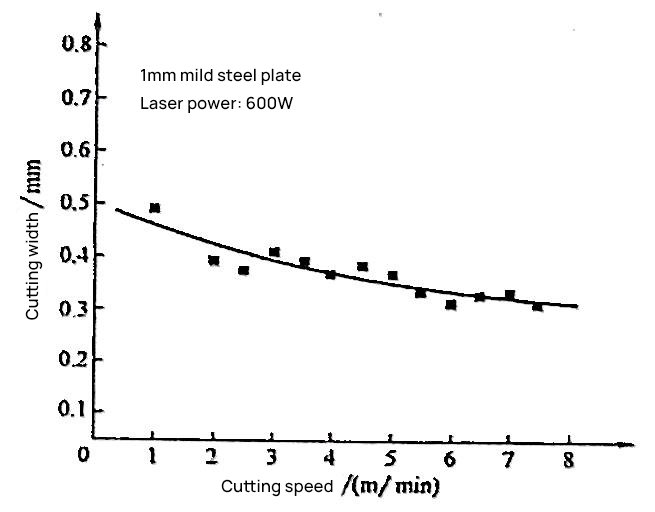
Impacto da potência do laser na rugosidade da superfície
Em uma determinada placa espessura e velocidade de corteSe o laser for usado em uma máquina de corte, há uma faixa ideal de potência do laser, dentro da qual a rugosidade da superfície de corte é a menor possível. Desviar-se da faixa de potência ideal aumentará a rugosidade; aumentar ou diminuir ainda mais a potência resultará em queimadura excessiva ou defeito de escória.
A Figura 8-22 mostra a relação entre a potência do laser e a qualidade da superfície de corte ao cortar uma chapa de aço de baixo carbono com 2 mm de espessura a uma velocidade de corte de 50 mm/s (ou seja, 3 m/min), usando o método de medição da rugosidade perto da borda inferior. Na Figura 8-22, é possível observar que a potência do laser pode ser dividida em três áreas: área de escória, área livre de defeitos e área de queimadura excessiva.
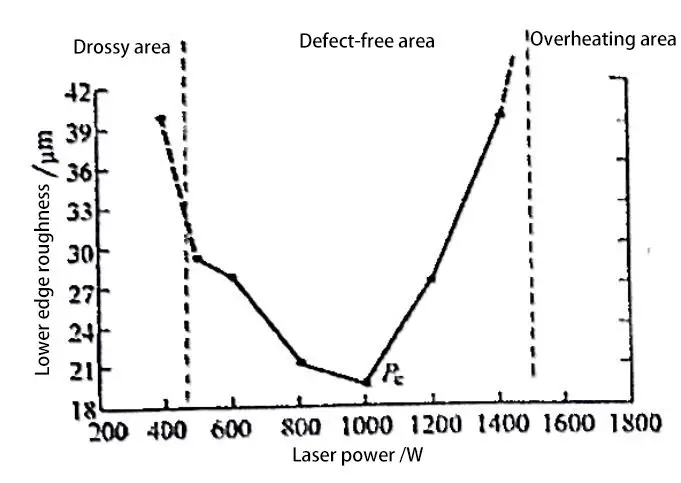
Observação: a espessura da chapa de aço de baixo carbono é de 2 mm, v=50 mm/s.
1) Se a potência do laser for muito alta, causando muita entrada de calor, a faixa de fusão da peça de trabalho será maior do que a faixa que o fluxo de gás de alta pressão pode afastar, e o metal derretido não poderá ser completamente soprado pelo fluxo de gás, resultando em queimadura excessiva.
2) Se a potência do laser for muito baixa, o calor não será suficiente. Quanto mais próximo da borda inferior, menor a temperatura do produto fundido e maior a viscosidade [11], de modo que ele não pode ser completamente soprado pela corrente de gás de alta pressão e permanece na borda inferior da superfície de corte, resultando em escória. Em casos graves, nem mesmo é possível formar um corte.
3) Dentro da área livre de defeitos, há uma faixa ideal de potência do laser (cerca de 800~1000W na Figura 8-22), onde a rugosidade da superfície de corte é a menor.
Impacto da velocidade de corte na rugosidade da superfície
Em uma determinada espessura de chapa e potência do laser, há uma velocidade de corte ideal, na qual a rugosidade da superfície de corte é a menor possível.
O desvio da velocidade de corte ideal aumentará a rugosidade; aumentar ou diminuir ainda mais a velocidade de corte resultará em queimadura excessiva ou defeito de escória [5].
A Figura 8-23 mostra a relação entre a velocidade de corte e a qualidade da superfície de corte de uma chapa de aço de baixo carbono com 2 mm de espessura em uma potência de laser de 1000 W, sendo a coordenada vertical a rugosidade próxima à borda inferior. A partir da Figura 8-23, pode-se ver que a velocidade de corte também pode ser dividida em área de sobrequeima, área livre de defeitos e área de escória.
Se a velocidade de corte for muito baixa, a queima excessiva é causada pela entrada excessiva de calor; se a velocidade de corte for muito alta, há produção de escória ou até mesmo o corte não é concluído.
A razão para a ocorrência de escória devido à alta velocidade de corte, além da entrada insuficiente de calor e da baixa temperatura que causa alta viscosidade do produto fundido, é que a alta velocidade de corte faz com que a frente de corte se incline significativamente para trás (aumentando a quantidade de arrasto), o que é ainda mais desfavorável para o fluxo de gás soprar o produto fundido.
Dentro da área livre de defeitos, há uma velocidade de corte ideal v (50 mm/s na Figura 8-23), onde a rugosidade da superfície de corte é a menor.
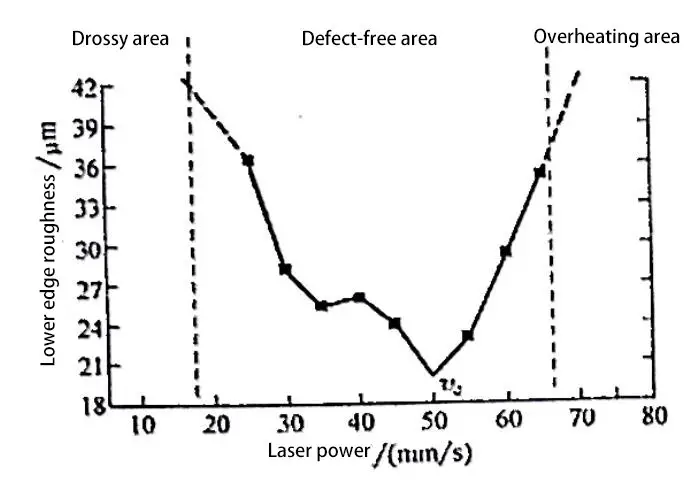
Observação: a espessura da chapa de aço de baixo carbono é de 2 mm, P=1000W.