O equipamento de produção é a ferramenta de trabalho dos montadores. Saber como usá-lo e mantê-lo pode garantir a utilização eficaz e prolongar sua vida útil, além de evitar lesões pessoais e acidentes com o equipamento.
Este capítulo começa com os procedimentos operacionais dos equipamentos comuns usados pelos montadores. Inicialmente, ele apresenta a operação e o uso de furadeiras, ferramentas elétricas, esmerilhadeiras, guindastes e outras ferramentas e equipamentos. Esses são conteúdos fundamentais que devem ser dominados com proficiência. Em seguida, apresenta a estrutura, o uso e a manutenção de equipamentos comuns para montadores, que exigem que os trainees dominem na prática. Com o desenvolvimento contínuo da ciência e da tecnologia, o avanço e o nível de automação dos equipamentos melhorarão muito, e os padrões de manutenção de equipamentos também mudarão.
I. Procedimentos operacionais para equipamentos comuns usados por montadores
Objetivo do treinamento: Dominar os procedimentos operacionais de equipamentos comuns usados por montadores.
1. Procedimentos operacionais da prensa de perfuração
(1) Perfuração
1) É estritamente proibido usar luvas durante a perfuração. As mangas devem ser bem amarradas, e as trabalhadoras devem usar toucas de trabalho. Os operadores não devem segurar fios de algodão ou outros materiais têxteis ou tecidos em suas mãos para evitar acidentes causados por cavacos ou brocas que se prendam acidentalmente a eles.
2) Não use as mãos ou panos para remover cavacos durante a perfuração e não os assopre com a boca. Deve-se usar uma escova para remover os cavacos. No caso de cavacos em forma de tira, use um gancho para quebrá-los ou corte-os imediatamente e tente removê-los quando a máquina estiver parada.
3) Durante a operação, a cabeça do operador não deve ficar muito próxima do eixo rotativo para evitar perigo. Ao parar, deixe o eixo parar naturalmente, não freie com a mão e não use a rotação reversa para frear.
4) Ao perfurar, a peça de trabalho deve ser fixada com firmeza, especialmente ao fazer furos de grande diâmetro em peças de trabalho menores. A fixação deve ser segura.
5) A broca deve ser afiada e a força de avanço deve ser adequada durante a perfuração. Especialmente na perfuração de furos passantes, reduza a força de avanço quando o furo estiver prestes a ser perfurado para evitar acidentes, como o lançamento da peça de trabalho para fora devido a um aumento repentino do avanço.
6) É estritamente proibido instalar ou remover peças de trabalho enquanto a máquina estiver funcionando. A inspeção das peças de trabalho e a alteração das velocidades do eixo devem ser feitas quando a máquina estiver parada.
7) A energia deve ser desconectada ao limpar a furadeira ou adicionar óleo lubrificante.
8) O ajuste da taxa de alimentação deve ser feito quando a máquina estiver parada. Para alimentação automática, ajuste a taxa de avanço de acordo com o diâmetro da broca e o tipo de material da peça de trabalho e fixe o bloco de limite de deslocamento.
9) O operador é estritamente proibido de sair enquanto a furadeira estiver funcionando, especialmente quando estiver usando alimentação elétrica, para evitar acidentes com o equipamento causados pela ultrapassagem do limite de deslocamento.
10) Ao remover a luva cônica de transição da broca, use uma cunha padrão. É estritamente proibido usar martelos, barras de ferro ou outras ferramentas inadequadas para forçar, para evitar danos ao eixo.
11) Ao usar uma furadeira radial, a broca deve ser mantida longe da peça de trabalho e da mesa de trabalho quando o braço estiver abaixado. O operador deve estar concentrado e operar com cuidado para evitar mau funcionamento ou deslizamento do equipamento, o que poderia levar a erros operacionais e danos ao equipamento. Nunca levante ou abaixe a caixa do eixo durante a perfuração.
12) Quando o diâmetro da perfuração se aproximar do limite máximo da furadeira radial, a peça de trabalho deve ser fixada perto do lado da coluna e deve ser trabalhada em um estado fixado.
(2) Fixação da peça de trabalho
1) Ao fazer furos em chapas finas ou peças menores com diâmetro superior a 8 mm, um torno de bancada ou um pequeno torno de máquina deve ser usado para segurar a peça de trabalho. Não segure diretamente a peça de trabalho com a mão para fazer a perfuração (Figura 1a).
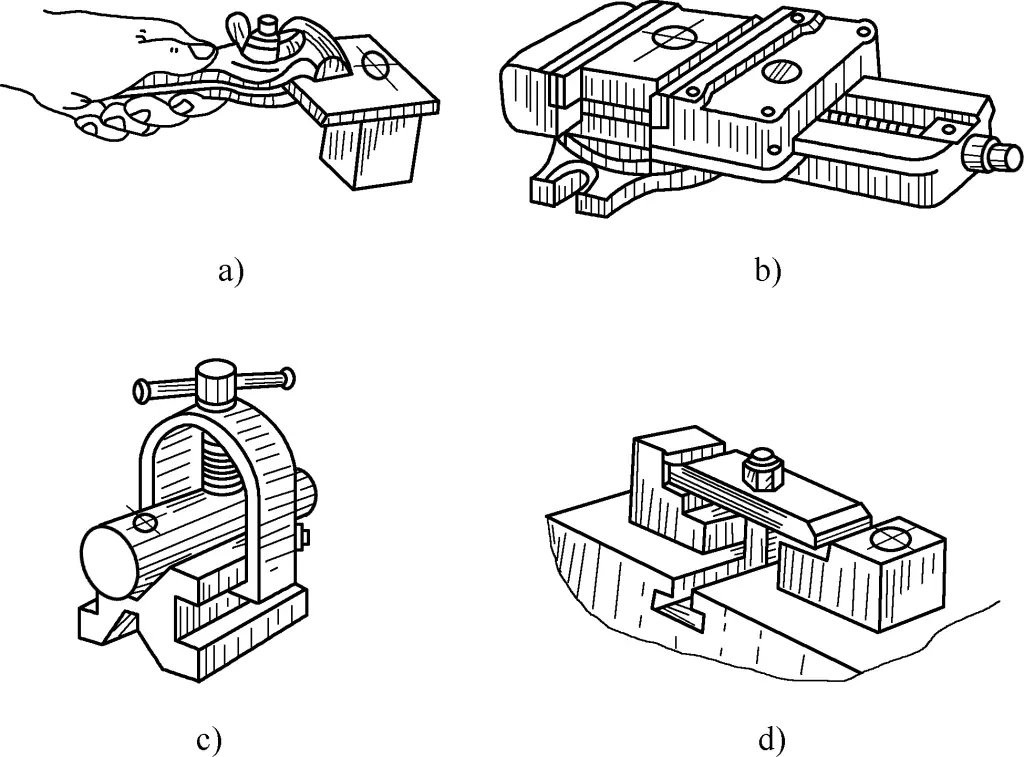
2) Ao fazer furos em peças de trabalho mais longas, embora elas possam ser seguradas com a mão, é melhor adicionar parafusos fixos na mesa de trabalho da furadeira para apoiar a peça de trabalho, o que é mais seguro e confiável.
3) Ao fazer furos em peças de trabalho planas, geralmente prenda a peça de trabalho em um torno de máquina (Figura 1b). Ao fixar, certifique-se de que a superfície da peça de trabalho esteja perpendicular à broca. Se o diâmetro da perfuração for relativamente grande, o torno da máquina deve ser fixado à mesa de trabalho da furadeira com parafusos e placas de pressão. Ao usar um torno de máquina para fixar peças de trabalho para perfuração de furo passante, coloque um espaçador sob a peça de trabalho para deixar espaço para a área de perfuração e evitar danificar o torno de máquina.
4) Ao fazer furos em peças de trabalho cilíndricas, coloque a peça de trabalho em um bloco em V (Figura 1c) para evitar que a peça de trabalho gire. Ao fixar, certifique-se de que a linha central da broca coincida com o plano simétrico das duas superfícies inclinadas do bloco em V para garantir que a linha central do furo passe pelo eixo da peça de trabalho.
5) Para furos grandes ou peças de trabalho que não sejam fáceis de fixar com um torno de máquina, use placas de pressão, parafusos e espaçadores para fixá-los na mesa de trabalho da furadeira (Figura 1d). Preste atenção ao seguinte:
① Os espaçadores devem estar o mais próximo possível da peça de trabalho para reduzir a deformação por flexão da placa de pressão.
② Os espaçadores devem ser ligeiramente mais altos do que a superfície fixada da peça de trabalho, mas não mais baixos do que ela. Caso contrário, quando a peça de trabalho for fixada, o ponto de pressão entre a placa de pressão e a peça de trabalho ficará na borda da peça de trabalho. Quando apenas uma placa de pressão é usada para prender a peça de trabalho, a peça de trabalho se levantará. Quando o espaçador é ligeiramente mais alto, mesmo que a placa de pressão se curve um pouco, ele ainda pode garantir que o ponto de pressão não fique na borda da peça de trabalho, evitando que a peça de trabalho se levante.
③ Os parafusos devem estar o mais próximo possível da peça de trabalho, o que pode proporcionar maior força de fixação na peça de trabalho e evitar o movimento da peça de trabalho durante o processo de fixação.
④ Se a superfície de fixação da peça de trabalho tiver sido usinada com precisão, deve-se usar uma folha de cobre ou material semelhante como amortecedor para evitar recuos da placa de pressão. É estritamente proibido usar tecido ou outros materiais têxteis ou trançados como amortecedores em superfícies usinadas para evitar acidentes causados por cavacos enganchados neles.
(3) Precauções para a instalação de brocas
As brocas de haste reta são presas por mandris de perfuração, com um comprimento de fixação não inferior a 15 mm; caso contrário, a broca pode ficar desalinhada ou cair devido a forças de torção durante a perfuração. As brocas de haste cônica são conectadas diretamente à luva do eixo da furadeira usando o cone Morse na haste. Ao conectar, a haste cônica da broca e o furo cônico do fuso devem ser limpos, e a extremidade plana da haste cônica deve estar alinhada com o furo em forma de cintura no fuso. Use força de impacto acelerada para instalar de uma só vez.
Quando a haste cônica da broca é menor do que o furo cônico do fuso, uma luva de transição pode ser usada para a conexão. Certifique-se de que a broca esteja firmemente conectada ao fuso da furadeira e que o desvio radial (usado para tolerâncias geométricas) seja mínimo durante a rotação.
(4) A correção é necessária se a posição de perfuração se deslocar após o início
Antes da perfuração, a marca do centro do furo não deve ser muito pequena, caso contrário, a borda do cinzel da broca não poderá cair inicialmente no furo cônico da marca do centro ao iniciar a perfuração, e a broca se desviará do centro durante a perfuração.
Ao iniciar a perfuração, primeiro alinhe a broca com o centro do furo para criar uma cavidade cônica rasa, verifique visualmente a concentricidade da cavidade cônica rasa inicial com o círculo traçado e faça correções continuamente. Se a posição do furo estiver significativamente deslocada, você pode corrigir a marca de punção central na direção oposta ou usar um cinzel para criar várias ranhuras na cava cônica rasa para reduzir a resistência de corte nessa área, permitindo que a broca se desloque e atinja o objetivo da correção (Figura 2).
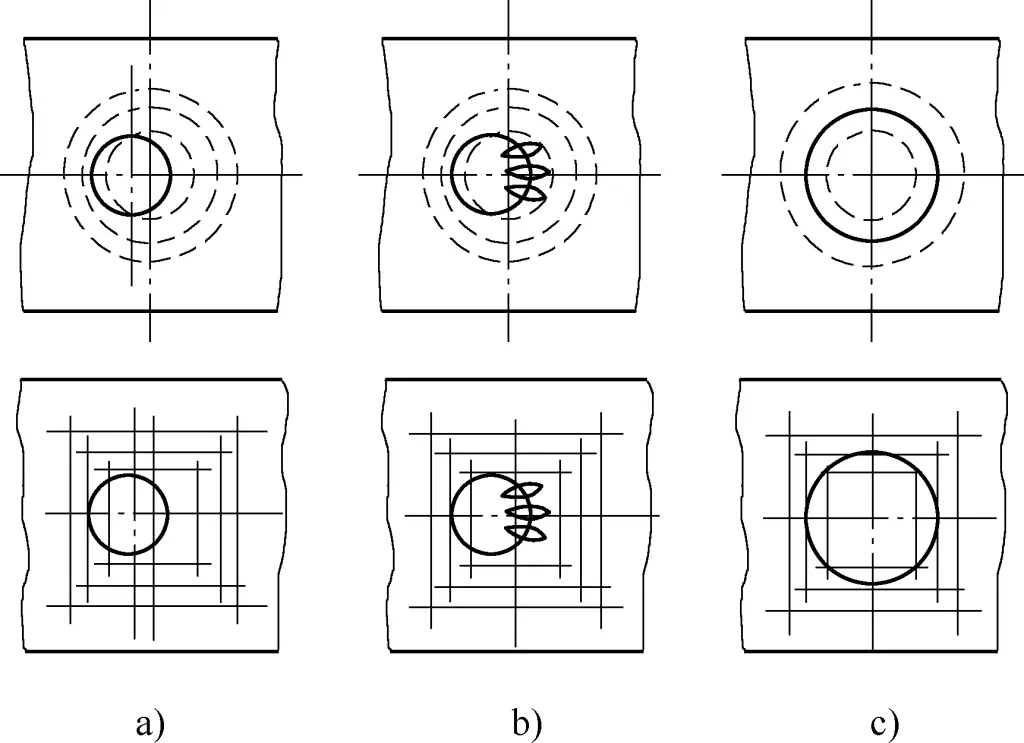
O processo de correção deve ser concluído antes que o diâmetro do poço cônico inicial se torne menor do que o diâmetro da broca. Essa é uma etapa importante para garantir a precisão da posição do furo. Se o diâmetro do furo cônico inicial já tiver atingido o diâmetro do furo e a posição do furo ainda estiver deslocada, será difícil corrigi-lo nesse ponto, o que levará a um erro maior na posição do furo e afetará a precisão da montagem.
Ao usar a alimentação manual, a força de alimentação não deve ser muito grande, caso contrário, fará com que a broca se dobre e se deforme (especialmente proeminente ao perfurar furos longos e finos), levando a um eixo de furo inclinado (Figura 3). Um eixo de furo inclinado afetará diretamente a forma, a precisão da posição e a qualidade da montagem do furo. Também pode ser perigoso, podendo causar a quebra da broca ou a ejeção da peça de trabalho.
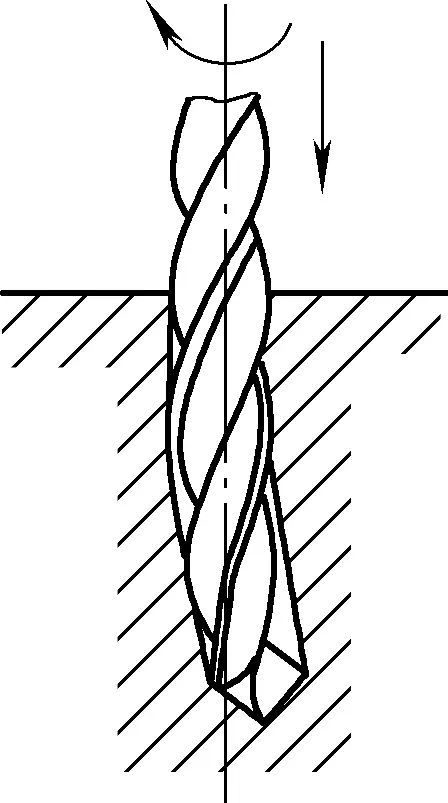
2. Procedimentos operacionais para furadeiras elétricas manuais
1) Escolha a furadeira elétrica portátil apropriada com base nos diferentes diâmetros de furo e preste atenção ao aterramento de proteção ou à conexão zero de proteção.
2) Antes de usar a furadeira elétrica manual, opere-a sem carga para verificar se o som das peças de transmissão e o sentido de rotação estão normais. Ao usar a furadeira elétrica manual, aplique a força uniformemente e concentre-se no controle da pressão. A pressão deve ser adequada e manter o eixo da broca perpendicular à superfície de usinagem. Reduza a pressão quando estiver prestes a perfurar para evitar força excessiva. Quando a broca encontrar resistência repentina, tome cuidado para não machucar o pulso devido à força de reação. Deve-se ter o mesmo cuidado ao reiniciar a perfuração depois que a broca parar de girar no furo.
3) Não sobrecarregue a furadeira elétrica manual. Quando o diâmetro da broca estiver próximo ou igual à capacidade máxima de trabalho da furadeira elétrica manual, a força aplicada deve ser reduzida adequadamente para evitar danos por sobrecarga à furadeira.
4) Não use a furadeira elétrica manual como substituta de uma chave elétrica para apertar parafusos. Devido à alta velocidade das furadeiras elétricas manuais, quando um parafuso é parado repentinamente após o aperto, a força de reação pode facilmente causar lesões no pulso.
5) As furadeiras elétricas devem ser limpas regularmente contra poeira e óleo e garantir a ventilação adequada. As furadeiras elétricas não devem ser usadas em condições inflamáveis ou explosivas, nem armazenadas em ambientes úmidos ou com gases corrosivos. Não arraste ou jogue as furadeiras elétricas sem cuidado para evitar danos.
6) As furadeiras elétricas novas ou aquelas armazenadas por muito tempo devem ter sua resistência de isolamento testada antes do uso. O valor da resistência deve ser superior a 0,5 MΩ; caso contrário, elas devem passar por um tratamento de secagem.
3. Procedimentos de operação de ferramentas elétricas
1) É proibido conectar cabos de força de ferramentas elétricas portáteis sem autorização. Quando houver necessidade de ferramentas elétricas, um eletricista deve conectar os fios e verificar se o invólucro de metal está eletrificado. Deve haver um aterramento de segurança, de preferência com um soquete de proteção de segurança.
2) É proibido usar ferramentas elétricas com cabos de alimentação danificados. Durante o uso, deve-se tomar cuidado para proteger o cabo de alimentação. É proibido arrastar, e deve-se evitar que objetos pesados ou rodas esmaguem o cabo de alimentação, o que poderia danificar o isolamento e causar choque elétrico ou acidentes com curto-circuito.
3) É proibido usar ferramentas elétricas sem medidas de proteção de isolamento. Especialmente ao operar em ambientes relativamente úmidos, é importante usar sapatos isolantes, luvas isolantes e trabalhar em um tapete de borracha isolante ou em uma tábua de madeira seca para evitar choques elétricos.
4) É proibido usar ferramentas elétricas com fios neutro e terra compartilhados. Quando o cabo de alimentação é puxado ou o fio neutro tem mau contato, a superfície metálica da ferramenta elétrica gera tensão, causando acidentes por choque elétrico.
4. Procedimentos de operação do moedor
A esmerilhadeira é um equipamento comum no local de trabalho do montador, composto por um motor elétrico, base da esmerilhadeira, descanso de ferramenta e tampa protetora. É usado principalmente para afiar cinzéis, brocas, raspadores e outras ferramentas de corte, ou para remover rebarbas, bordas afiadas e camadas de superfície dura de peças ou materiais.
As esmerilhadeiras também são equipamentos propensos a acidentes de segurança. O rebolo é frágil e gira em alta velocidade. Portanto, ao usar uma esmerilhadeira, é necessário seguir rigorosamente os procedimentos operacionais para evitar acidentes de segurança.
1) Ao usar uma esmerilhadeira, antes de começar, verifique cuidadosamente se há objetos estranhos entre o rebolo e a tampa protetora e se o rebolo apresenta marcas de impacto ou danos. Somente inicie o esmeril depois de confirmar que não há problemas. Depois de ligar o esmeril, espere até que o rebolo gire de forma estável antes de esmerilhar. Se o rebolo oscilar visivelmente, pare a máquina imediatamente para ajuste.
2) A distância entre o descanso de ferramenta da esmerilhadeira e o rebolo deve ser mantida dentro de 3 mm para evitar que as peças de trabalho fiquem presas e causem acidentes. Se a distância for muito grande, ela deve ser ajustada antes do uso. Ao retificar peças de trabalho ou ferramentas de corte, não aplique força excessiva.
3) Não moer macio metais como alumínio, cobre ou madeira na esmerilhadeira. Não use o rebolo quando ele estiver desgastado além de seu limite.
4) Ao esmerilhar, o operador deve ficar na lateral ou na diagonal do esmeril para evitar ferimentos causados por fragmentos do rebolo em caso de quebra.
5) Não use rebolos de qualidade inferior. Ao substituir os rebolos, consulte os procedimentos de operação de segurança para esmerilhadeiras. É proibido usar rebolos rachados ou danificados.
6) Ao instalar o rebolo, as placas de fixação não devem entrar em contato direto com o rebolo. As arruelas de papel devem ser colocadas entre as placas de fixação e o rebolo. O conjunto deve ser circular e girar suavemente.
7) Óculos de proteção devem ser usados ao utilizar um esmeril.
5. Procedimentos de operação do esmeril portátil
1) Não use esmerilhadeiras manuais sem proteções de segurança ou aterramento adequado. Antes de usar, verifique cuidadosamente se há danos por impacto e rachaduras no rebolo, se a carcaça de metal não está eletrificada e se o cabo de alimentação está intacto. Se estiver danificado, conserte-o antes de usar. Sempre faça um teste de funcionamento sem carga antes de usar um esmeril portátil e só o use depois de confirmar o sentido de rotação correto.
2) Ao usar um moedor portátil, é necessário ter concentração total. Antes de ligar a esmerilhadeira, segure firmemente o corpo da esmerilhadeira. Evite colocar o rebolo próximo ao chão ou à peça de trabalho para evitar que a esmerilhadeira role ao longo da superfície devido à força de reação quando iniciada, o que poderia fazer com que o rebolo voasse e resultasse em um acidente.
Não coloque aleatoriamente uma esmerilhadeira manual rotativa no chão ou na peça de trabalho. Ela deve ser colocada em um local seguro designado somente depois que o rebolo tiver parado completamente. Quando não estiver em uso temporário, a energia deve ser desligada.
3) Não use a lateral do rebolo para esmerilhar as peças. Ao usar uma esmerilhadeira manual, use a face do rebolo, segure a esmerilhadeira com firmeza e entre em contato lentamente com a peça de trabalho. Impactos ou pressões repentinas são proibidos. É melhor que ninguém fique por perto durante a operação. O operador não deve ficar de frente para o rebolo diretamente e deve usar óculos de proteção e outros equipamentos de proteção necessários.
4) Não use rebolos com sinais de danos. Esmerilhadeiras manuais sem interruptores manuais não devem ser usadas. Devido à alta velocidade de rotação e à baixa resistência dos rebolos de esmeril manuais, eles são propensos a se quebrar. Ao instalar o rebolo, certifique-se de que o encaixe esteja correto e aperte a porca adequadamente com uma chave inglesa.
5) Guarde os moedores de mão em um local seco. Evite armazená-los em áreas úmidas ou em locais onde possam entrar em contato com água para evitar danos ao isolamento interno.
6. Procedimentos de elevação durante a montagem
Durante o processo de montagem, os montadores devem usar equipamentos de elevação para peças ou componentes mais pesados a fim de reduzir o esforço físico do operador, melhorar a eficiência do trabalho e garantir a segurança da produção.
(1) Procedimentos de operação do macaco
Os macacos são adequados para elevar objetos pesados a alturas limitadas e para mover objetos pesados. Os tipos comumente usados incluem macacos de parafuso, macacos de cremalheira e pinhão e macacos hidráulicos. Os procedimentos a seguir devem ser seguidos ao usar macacos:
- O macaco deve ser colocado verticalmente sob o objeto pesado, e a superfície de trabalho deve ser firme e nivelada para evitar afundamento ou inclinação.
- Ao usar um macaco de cremalheira e pinhão, a lingueta antirreversão deve estar em contato próximo com a roda da catraca.
- Ao usar um macaco hidráulico, o parafuso de ajuste não deve ser estendido demais. Evite estender totalmente o parafuso, e o curso do pistão principal não deve exceder a marca de altura extrema.
- A carga não deve exceder a capacidade de carga do macaco para garantir o uso seguro.
- Ao usar um macaco, a base deve ser sólida e o posicionamento deve ser estável. Levante lentamente e adicione apoio à medida que for levantando. Quando vários macacos são usados simultaneamente para levantar um objeto pesado, uma pessoa designada deve coordenar a manutenção da velocidade e da altura de elevação consistentes entre os macacos para evitar que o objeto se incline. Levante e abaixe com firmeza para evitar acidentes.
(2) Procedimentos de operação do guindaste
1) É proibido usar talhas manuais com ganchos, correntes, freios ou outros riscos potenciais defeituosos. Ao levantar peças de trabalho ou objetos pesados com uma talha manual, a estrutura que suporta a talha deve ser segura e confiável.
2) É proibido sobrecarregar as talhas manuais ou forçá-las a levantar objetos pesados. Escolha a talha manual apropriada com base no tamanho e no peso do objeto a ser levantado.
3) É proibido suspender objetos pesados em pleno ar por períodos prolongados. É proibido que as pessoas passem por baixo ou permaneçam embaixo de cargas suspensas. Ao levantar objetos, eles devem ser fixados com segurança. As cordas devem ser usadas dentro de sua faixa de carga permitida. Quando as cordas passarem por bordas relativamente afiadas, deve-se usar material macio como acolchoamento para evitar o desgaste excessivo e a quebra da corda. Ao usar dois ou mais guinchos para levantar o mesmo objeto simultaneamente, uma pessoa designada deve coordenar. A elevação ou o abaixamento deve ser feito lentamente.
4) Ao levantar objetos pesados, é estritamente proibido apressar o levantamento. Primeiro, verifique se a amarração está segura e se o centro de gravidade está posicionado corretamente. Em seguida, levante 0,5 m e prossiga com o levantamento somente depois que a inspeção confirmar que é seguro.
5) Ao instalar o equipamento, ele deve ser levantado de forma razoável. Escolha o comprimento e a espessura das cordas de acordo com o peso do equipamento. Primeiro, levante cerca de 0,5 m para testar o centro de gravidade do objeto pesado e, depois de confirmar, prossiga com o levantamento. O levantamento inadequado é estritamente proibido para evitar a deformação do equipamento e afetar a precisão.
6) É proibido usar cabos de aço que excedam o padrão de desgaste. Também é proibido o uso de cabos de aço com fios quebrados que excedam as normas ou com juntas danificadas.
7) É proibido que os cabos de aço em uso entrem em contato com metal energizado (incluindo fios elétricos, cabos de máquinas de solda etc.) para evitar queimaduras ou redução da resistência do cabo. cabo de aço devido ao calor.
8) É proibido elevar objetos além da capacidade do cabo de aço. O diâmetro do cabo de aço deve ser escolhido de forma razoável de acordo com o peso do objeto que está sendo levantado.
9) Ao usar um guincho, coloque-o em uma superfície plana e livre de obstáculos. Use âncoras de solo seguras ou âncoras de estacas para mantê-lo no lugar. A fixação deve ser confiável para evitar que a estrutura se mova ou se incline sob força.
10) Ao usar um guincho, o cabo de aço deve ser guiado horizontalmente em direção à polia guia, e não diretamente para uma posição elevada.
11) Ao usar um guincho, uma extremidade do cabo de aço deve ser puxada para fora da parte superior do núcleo do tambor e apertada por uma pessoa experiente. Em geral, o cabo deve ser enrolado em torno do núcleo do tambor de 4 a 6 voltas.
12) Durante as operações de elevação, o ângulo horizontal entre a eslinga e o objeto deve estar preferencialmente acima de 45°. Se o ângulo horizontal for muito pequeno, a altura da eslinga poderá ser reduzida, mas a força horizontal sobre a eslinga ou o equipamento aumentará. A força excessiva pode facilmente causar deformação e danos à máquina quando a resistência é fraca.
II. Manutenção, uso e cuidados com equipamentos comuns
Objetivo do treinamento: Ser capaz de usar corretamente o equipamento comum do instalador e realizar manutenção e cuidados.
1. Uso, manutenção e cuidados com as máquinas de perfuração
Uma máquina de perfuração é uma máquina-ferramenta comum de processamento de furos. Ao instalar brocas, alargadores, escareadores, alargadores, ferramentas de perfuração, machos e outras ferramentas na máquina de perfuração, é possível realizar operações como perfuração, alargamento, escareamento, alargamento, perfuração e rosqueamento. As furadeiras são uma das máquinas-ferramentas mais comumente usadas pelos montadores.
As furadeiras podem ser classificadas em três tipos com base em sua estrutura e faixa de aplicação: furadeiras de bancada (abreviadas como furadeiras de bancada), furadeiras verticais (abreviadas como furadeiras verticais) e furadeiras radiais (abreviadas como furadeiras radiais).
(1) Estrutura e operação de máquinas de perfuração de bancada
Uma furadeira de bancada é uma pequena máquina de perfuração que pode ser usada em uma bancada de trabalho, com um diâmetro máximo de perfuração geralmente de até 12 mm. A velocidade mais baixa do fuso de uma furadeira de bancada é relativamente alta, geralmente não inferior a 400r/min, portanto, não é adequada para escareamento, alargamento e rosqueamento. As furadeiras de bancada geralmente usam transmissão por correia em V, com uma polia cônica de cinco etapas para alterar as velocidades.
O avanço do fuso de uma furadeira de bancada é apenas manual e geralmente tem dispositivos para controlar a profundidade da perfuração, como mostradores graduados, réguas graduadas ou dispositivos de deslocamento fixo. Após a perfuração, o fuso pode retornar automaticamente à sua posição original sob a ação de uma mola espiral.
1) Estrutura de uma máquina de perfuração de bancada
A furadeira de bancada Z512 é uma estrutura simples comumente usada por montadores, conforme mostrado na Figura 4.
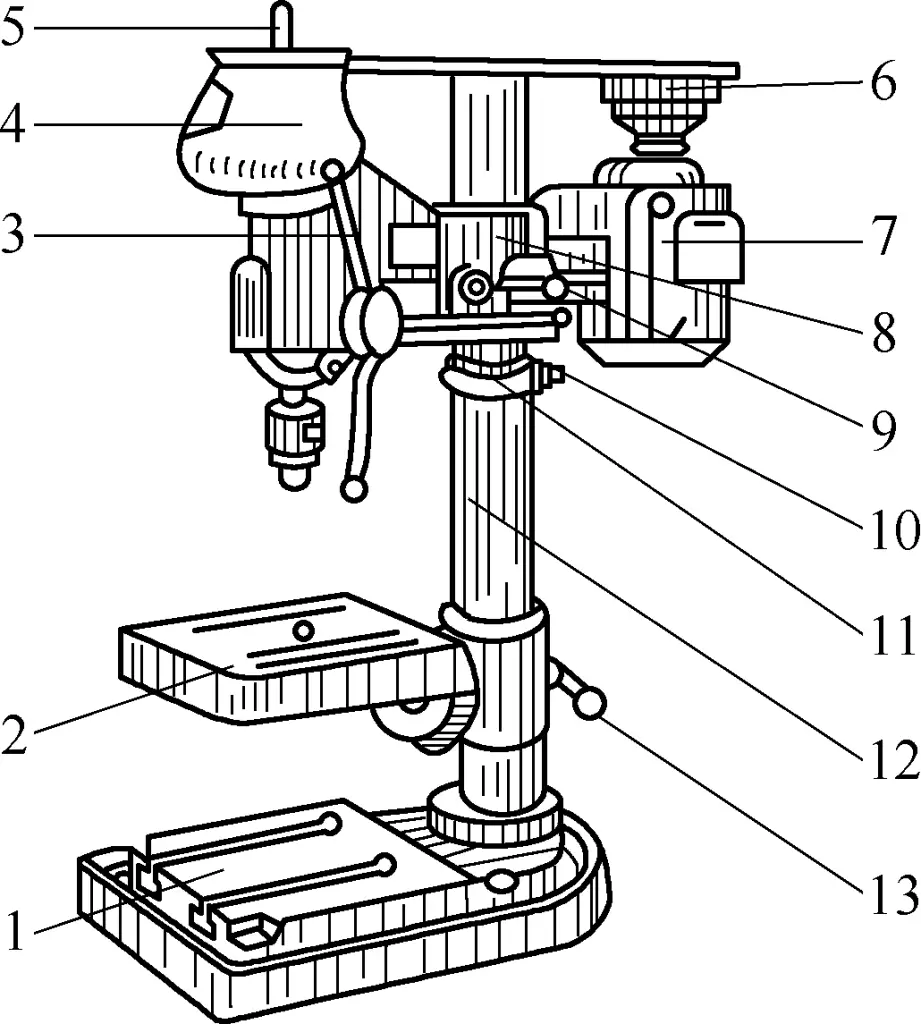
1-Base
2-Mesa de trabalho
3-Alavanca de alimentação
4 capas
5 eixos
6-Pulley
7-Motor
8-Corpo
9 alças
10 parafusos
11-Anel de segurança
12 colunas
13-Alça de travamento da mesa de trabalho
O motor 7 aciona o eixo 5 por meio da polia 6 e da correia em V para atingir várias velocidades de rotação diferentes. O corpo 8 é encaixado na coluna 12 para movimento para cima e para baixo e pode ser girado para qualquer posição em torno do centro da coluna. Após o ajuste na posição adequada, ele pode ser travado com a alça 9. Se o corpo precisar ser abaixado, primeiro ajuste o anel de segurança 11 na posição adequada e trave-o com o parafuso 10; em seguida, afrouxe levemente a alça para permitir que o corpo caia sobre o anel de segurança com seu próprio peso e, então, trave a alça 9.
Quando a alça de travamento da mesa de trabalho 13 é solta, a mesa de trabalho 2 também pode se mover para cima e para baixo na coluna 12 ou girar para qualquer posição em torno do centro da coluna. Ao fazer furos em peças pequenas, a peça de trabalho pode ser colocada na mesa de trabalho; para peças maiores ou mais altas, a mesa de trabalho pode ser girada e fixada, e a peça de trabalho pode ser colocada diretamente na base da furadeira 1 para perfuração.
2) Operação de uma furadeira de bancada
① Ajuste da velocidade do fuso.
Escolha uma velocidade adequada com base no diâmetro da broca e no material que está sendo processado. O ajuste da velocidade é feito por meio de um conjunto de polias cônicas dentro da tampa superior 4 da furadeira de bancada. Ao fazer o ajuste, o eixo deve estar parado. Abra a tampa, gire manualmente a polia, primeiro pendure a correia em V na polia menor, depois na polia maior, pendurando gradualmente a correia em V na polia apropriada até atingir a velocidade desejada.
② Ajuste da posição de cima para baixo e da esquerda para a direita da mesa de trabalho.
Segure a mesa de trabalho com a mão esquerda, solte a alça de travamento da mesa de trabalho 13 com a mão direita, gire a mesa de trabalho 2 para movê-la para baixo ou para cima até a posição desejada e, em seguida, trave a alça de travamento da mesa de trabalho 13 novamente.
③ Ajuste da posição de avanço do fuso.
O avanço do fuso é obtido girando a alavanca de avanço 3. A extensão do fuso não deve ser muito longa, portanto, antes de perfurar, primeiro teste a elevação e a redução do fuso para verificar se a altura de colocação da peça de trabalho é adequada (ajuste usando a elevação da mesa de trabalho).
3) Uso e manutenção corretos das furadeiras de bancada
Ao perfurar, a peça de trabalho deve ser fixada com uma placa de pressão (exceto ao fazer pequenos furos em peças maiores, que podem ser seguradas com a mão). Quando o orifício de passagem estiver prestes a ser perfurado, reduza a força de avanço para evitar acidentes, como a aderência da broca ou a projeção da peça de trabalho.
Durante a perfuração, ferramentas, instrumentos de medição e outros itens não devem ser colocados sobre a superfície da mesa de trabalho. Ao perfurar orifícios de passagem, certifique-se de que a broca possa passar pelo orifício de alívio (ou ranhura em T) na superfície da mesa de trabalho, ou coloque um bloco espaçador sob a peça de trabalho para evitar danos à superfície da mesa de trabalho.
③ A superfície da mesa de trabalho deve ser mantida limpa regularmente. Após o uso, as superfícies deslizantes expostas da furadeira de bancada e a superfície da mesa de trabalho devem ser limpas, e óleo lubrificante deve ser adicionado a todas as superfícies deslizantes e orifícios de óleo.
(2) Estrutura, uso e manutenção de máquinas de perfuração vertical
As furadeiras verticais têm diâmetros máximos de perfuração de ϕ25mm, ϕ35mm, ϕ40mm e ϕ50mm, entre outras especificações. As furadeiras verticais podem ter alimentação automática. Tanto a velocidade do fuso quanto a taxa de alimentação automática têm uma ampla gama de ajustes, o que as torna adequadas para perfuração, alargamento, rebaixamento, alargamento e rosqueamento de várias peças de trabalho de tamanho médio. Devido à sua maior potência e ao mecanismo mais completo, ele pode alcançar maior eficiência e precisão de processamento.
1) Estrutura e desempenho da máquina de perfuração vertical Z535
A furadeira vertical Z535 é um tipo de furadeira comumente usada por montadores, conforme mostrado na Figura 5a.
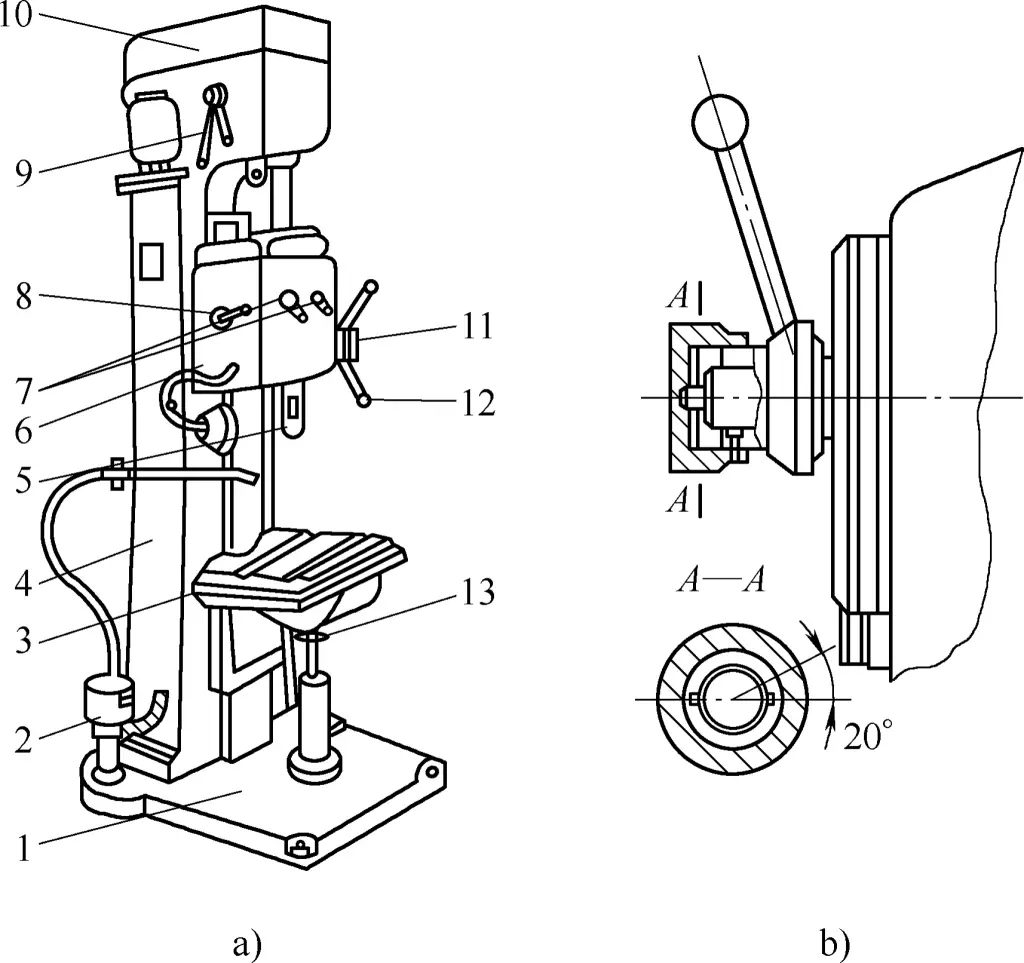
1-Base
2-Bomba hidráulica
3-Mesa de trabalho
4 colunas
5 eixos
6-Caixa de alimentação
7-Puxador de alimentação
8-Alavanca de avanço/retrocesso
Alavanca de troca de 9 velocidades
Caixa de 10 fusos
11-Tampa da extremidade
12-Alça operacional
13-Puxador de elevação da mesa de trabalho
A cama 4 é fixada na base 1. A caixa do fuso 10 é fixada na parte superior da base. A caixa de alimentação 6 é instalada no trilho de guia vertical da mesa e pode se mover para cima e para baixo ao longo dele. Para facilitar a operação, um contrapeso que equilibra o peso próprio do fuso é instalado dentro da base. A mesa de trabalho 3 é instalada na parte inferior do trilho de guia vertical da mesa e também pode se mover para cima e para baixo ao longo dela para acomodar peças de trabalho de diferentes alturas.
A máquina de perfuração vertical Z535 também é equipada com um dispositivo de resfriamento. O fluido de corte é armazenado na cavidade da base e é descarregado pela bomba hidráulica 2 quando em uso.
O principal desempenho e as especificações da máquina de perfuração vertical Z535 são os seguintes:
Diâmetro máximo de perfuração ϕ35mm
Cone do furo do fuso Morse nº 4
Curso do eixo 225 mm
Velocidade do fuso 68~1000 r/min
Taxa de avanço 0,11~1,6 mm/r
Curso da mesa de trabalho 325 mm
Potência do motor 4,5kW
2) Operação da máquina de perfuração vertical
① Ajuste da velocidade do fuso.
Determine a velocidade do fuso com base no diâmetro da broca e no material da peça de trabalho. A mudança de velocidade é obtida por meio da alavanca de mudança de velocidade 9. A alavanca de avanço/retrocesso 8 é usada para controlar a rotação para frente, a rotação reversa ou a parada do fuso 5.
② Ajuste do dispositivo de elevação da mesa de trabalho.
De acordo com a altura da posição de perfuração na peça de trabalho, ajuste a mesa de trabalho para cima e para baixo ao longo do trilho de guia vertical na mesa usando a alça de elevação da mesa de trabalho 13 instalada sob a mesa de trabalho. Há também um tipo com uma base cilíndrica em que a mesa de trabalho é cilíndrica e pode girar em torno de seu eixo enquanto também gira em torno da base, conforme mostrado na Figura 6, facilitando o alinhamento da posição de perfuração da peça de trabalho.
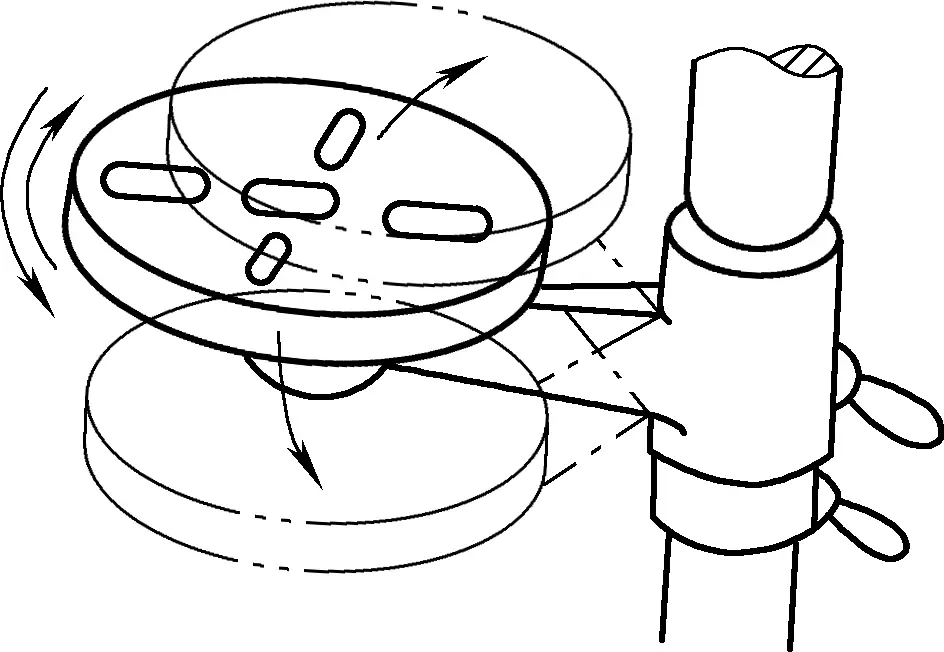
③ Ajuste do avanço do fuso.
A alimentação do fuso tem dois tipos: alimentação automática e alimentação manual.
Para a alimentação automática, primeiro ajuste as duas alças de alimentação 7 na posição desejada para determinar a taxa de alimentação necessária e, em seguida, puxe a tampa da extremidade 11 para fora e gire-a 20° no sentido horário em relação à alça, conforme mostrado na Figura 5b, para colocá-la na posição de alimentação automática. Quando o eixo gira, a alimentação automática pode ser obtida. Para a alimentação manual, gire a tampa da extremidade 20° no sentido anti-horário em relação à alça e empurre-a de volta à sua posição original, momento em que o dispositivo de alimentação automática é desengatado.
Para alimentação manual, gire a tampa da extremidade 20° no sentido anti-horário em relação à alça e empurre-a de volta à sua posição original, momento em que o dispositivo de alimentação automática é desengatado. Gire a alça de operação 12 no sentido anti-horário para alimentar e no sentido horário para retrair.
Ao rosquear roscas, a alça deve ser colocada na posição de avanço manual. Primeiro, use o avanço manual para fazer o corte do macho. Depois que o macho tiver dado 2 a 3 voltas, você poderá parar de usar o avanço manual e aplicar pressão axial, contando com a rosca do próprio macho para acionar o avanço do fuso. Após a conclusão do rosqueamento, você pode inverter o fuso para retrair o macho.
3) Regras para o uso de máquinas de perfuração vertical
- Antes do trabalho, lubrifique de acordo com os requisitos de lubrificação e verifique se as posições das alças estão normais e se há algum objeto estranho na superfície do trilho-guia. Dê partida na máquina em baixa velocidade e verifique se há óleo na janela de óleo do eixo e se há algum fenômeno anormal nas peças de transmissão.
- Quando a alimentação automática não for usada durante o trabalho, a tampa da extremidade deve ser empurrada para dentro para desengatar o dispositivo de alimentação automática.
- Preste atenção à segurança durante o trabalho. As peças de trabalho, os acessórios e as ferramentas devem ser fixados com firmeza. Ao fazer furos, coloque um bloco de apoio sob a peça de trabalho. Ao perfurar peças fundidas ou furos profundos, retraia a furadeira com frequência para remover cavacos. Não exceda as especificações de corte.
- Evite que lascas, água e outros detritos caiam na superfície do trilho-guia, no motor ou na caixa elétrica.
- Após o trabalho, coloque todas as alças na posição de parada ou neutra, abaixe a mesa de trabalho até a posição mais baixa e desconecte a energia. Por fim, limpe a máquina e aplique óleo protetor de acordo com os padrões de limpeza da máquina.
4) Manutenção de máquinas de perfuração vertical
A manutenção adequada de equipamentos de máquinas desempenha um papel muito importante na redução de falhas de equipamentos e na ampliação da vida útil das máquinas. A manutenção de máquinas implementa um "sistema de manutenção de três níveis", ou seja, manutenção diária, manutenção de primeiro nível e manutenção de segundo nível.
- Manutenção diária de máquinas de perfuração vertical. Também conhecida como cuidados diários, ela é realizada pelo operador e deve atender a quatro requisitos: asseio, limpeza, segurança e lubrificação. Os cuidados diários devem ser realizados regularmente para que a prevenção seja a principal meta; se forem encontrados problemas em potencial, eles devem ser resolvidos prontamente, e os problemas maiores devem ser relatados imediatamente.
- Manutenção de primeiro e segundo níveis de máquinas de perfuração vertical. Também conhecida como manutenção secundária, ela deve ser realizada principalmente pelos operadores com a ajuda dos funcionários da manutenção.
- Aparência da máquina. Limpe a superfície da máquina, a mesa de trabalho, os parafusos de avanço, as cremalheiras e as engrenagens cônicas. Remova as rebarbas das superfícies dos trilhos-guia e da mesa de trabalho e substitua os parafusos, as esferas do manípulo, etc. que estiverem faltando.
- Eixo e caixa de alimentação. Remova as rebarbas do furo cônico do fuso; ajuste a correia de acionamento do motor; verifique as posições de várias alças; substitua as peças do mecanismo de transmissão que estiverem desgastadas.
- Lubrificação. Verifique a qualidade e a quantidade de óleo; limpe os feltros de óleo, verifique as linhas de óleo e troque o óleo durante a manutenção secundária.
- Resfriamento. Limpe a bomba de resfriamento, o filtro e o tanque de refrigerante e verifique a tubulação. Substitua o fluido de corte durante a manutenção secundária.
- Elétrica. Limpe o motor e a caixa elétrica (com a ajuda de um eletricista, se necessário). Durante a manutenção secundária, desmonte e limpe o motor conforme necessário e substitua a graxa.
(3) Manutenção de máquinas de perfuração radial
As máquinas de perfuração radial, também conhecidas como furadeiras radiais, são adequadas para o processamento de peças maiores e peças com vários furos. Ao processar peças com vários furos em uma furadeira vertical, a peça de trabalho precisa ser movida e alinhada para cada furo, o que é muito trabalhoso para peças grandes e dificulta o alinhamento preciso do centro da broca com o centro do furo na peça de trabalho. Nesse caso, o uso de uma furadeira radial com um eixo móvel é mais conveniente para o processamento.
A composição da máquina de perfuração radial Z35 é mostrada na Figura 7. Quando a peça de trabalho não é grande, ela pode ser fixada na mesa de trabalho 5 para processamento; se a peça de trabalho for muito grande e não couber na mesa de trabalho 5, a mesa de trabalho 5 pode ser removida e a peça de trabalho pode ser colocada diretamente na base 6 para processamento.
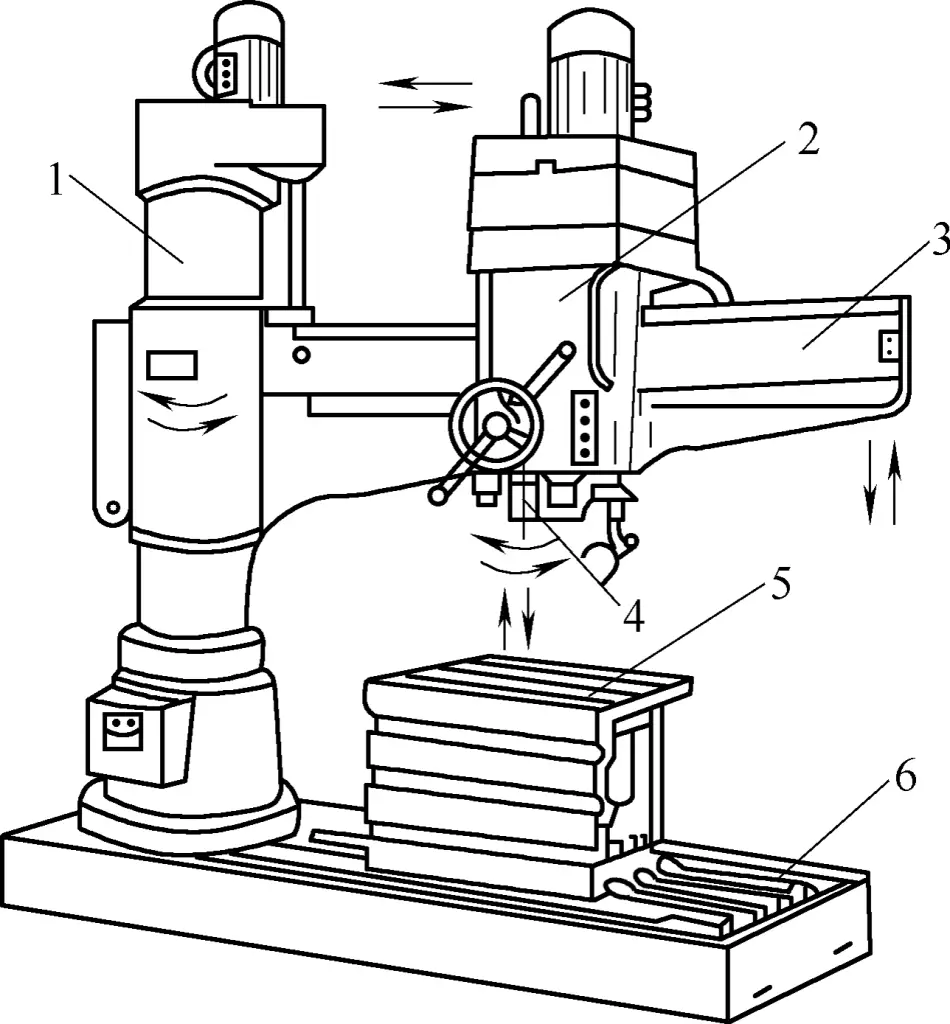
1 coluna
Caixa de 2 fusos
3 braços
4 eixos
5-Mesa de trabalho
6-Base
A caixa do fuso 2 é montada no braço 3, que pode girar em torno da coluna vertical 1 e pode se mover para frente e para trás ao longo do trilho de guia horizontal no braço. Por meio desses dois movimentos, o fuso 4 pode ser ajustado para qualquer posição dentro da faixa de processamento da máquina. Portanto, as máquinas de perfuração radial podem realizar o processamento de furos em uma faixa muito ampla.
As furadeiras radiais têm uma ampla gama de ajustes da velocidade do fuso e da taxa de avanço, permitindo alta eficiência de produção e precisão de processamento. Ao processar peças de trabalho com vários furos em uma furadeira radial, a peça de trabalho pode permanecer estacionária, e somente a posição do braço e a caixa do fuso no braço precisam ser ajustadas para se alinharem convenientemente com os centros dos furos. Além disso, o braço também pode ser levantado e abaixado ao longo da coluna para ajustar a altura da caixa do fuso de acordo com a altura da área de processamento da peça.
Atualmente, há muitas especificações de máquinas de perfuração radial produzidas na China, entre as quais a máquina de perfuração radial Z35 é amplamente utilizada no setor de fabricação de montagens, conforme mostrado na Figura 7.
O principal desempenho e as especificações da máquina de perfuração radial Z35 são os seguintes:
Diâmetro máximo de perfuração ϕ50mm
Cone do furo do fuso Morse nº 5
Curso máximo do fuso dentro do cabeçote 350 mm
Curso máximo do fuso ao longo do trilho de guia do braço 1050 mm
Número de níveis de velocidade do fuso 18
Faixa de velocidade do fuso 34~2000r/min
Número de níveis de taxa de alimentação 18
Faixa de taxa de alimentação 0,3~1,2mm/r
Curso máximo do braço ao longo da coluna 680 mm
Potência do motor principal 4~5kW
2. Uso, manutenção e cuidados com a máquina de prensagem
A montagem por pressão é um tipo comum de ajuste por interferência em oficinas de montagem. É também um método de montagem mais econômico e eficiente em comparação com a montagem a quente e a frio. de encaixee é uma habilidade operacional que os montadores devem dominar. A maioria das montagens de encaixe por pressão é complementada com estruturas-chave.
A montagem de acessórios de prensagem geralmente requer grandes forças de prensagem, portanto, geralmente são usadas máquinas de prensagem hidráulica controladas hidraulicamente. Isso ocorre porque os sistemas hidráulicos são fáceis de ajustar a pressão, fornecem alta força, permitem baixas velocidades de encaixe, são fáceis de operar, são seguros para trabalhar e permitem o monitoramento da magnitude e das alterações da pressão durante o processo de prensagem por meio de medidores de pressão do sistema, obtendo um controle seguro do processo de prensagem.
Devido aos diferentes cenários de uso, as máquinas de prensagem hidráulica têm suas vantagens excepcionais para diferentes peças de trabalho e estruturas. As máquinas de prensagem hidráulica têm dimensões estruturais pequenas, são fáceis de operar e controlar, têm uma ampla gama de aplicações e podem ser divididas em tipos verticais e horizontais.
A Figura 8 mostra uma máquina de prensagem hidráulica vertical estruturada em estrutura, com seu sistema hidráulico e peças de controle não mostrados. O sistema hidráulico da máquina de prensagem é muito simples, com poucos componentes de sistema devido à sua ação simples. Como as máquinas de prensagem geralmente exigem altas pressões de trabalho (32 MPa), as bombas de pistão de deslocamento variável são usadas principalmente. As bombas variáveis podem ajustar o fluxo de saída de acordo com a velocidade da prensa.
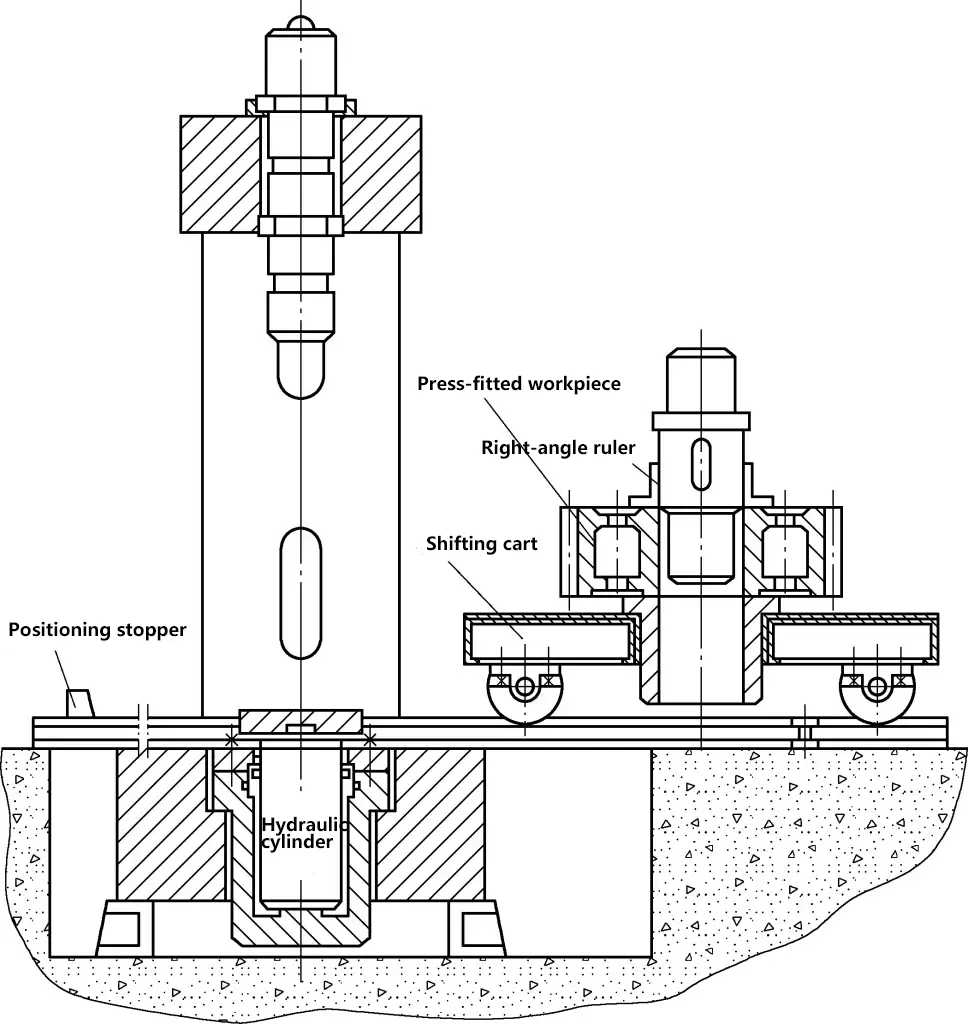
O sistema tem uma válvula de alívio para proteger a bomba hidráulica e garantir a segurança do sistema, filtros para manter a limpeza do sistema e outros componentes hidráulicos, como medidores de pressão, válvulas de retenção, válvulas de pressão de óleo, válvulas de parada e válvulas deslizantes de controle.
As máquinas de prensagem com recursos mais completos são equipadas com dispositivos de registro e plotagem de curvas de pressão durante a prensagem. Por exemplo, as máquinas de prensagem de eixos de rodas de trens horizontais têm requisitos rigorosos para mudanças de pressão durante o processo de prensagem de eixos de rodas de trens. Portanto, o estado real das mudanças de pressão precisa ser refletido e registrado durante o processo de prensagem, com o processo de mudança de pressão representado em forma de curva como base para avaliar se ele atende aos requisitos e, em seguida, arquivado para armazenamento.
As máquinas de ajuste de prensa verticais e horizontais diferem em sua forma, exibindo, portanto, suas respectivas vantagens e desvantagens no uso.
Há duas formas estruturais de máquinas de prensagem vertical. Uma delas é o cilindro hidráulico montado na parte superior, em que o cilindro hidráulico principal é colocado na viga superior da máquina de prensagem, mas o cilindro hidráulico deve ser uma estrutura de pistão, caso contrário, ele dependeria de um cilindro hidráulico secundário do tipo pistão para controlar o retorno do cilindro hidráulico. O outro é o cilindro hidráulico montado na parte inferior, conforme mostrado na Figura 8, em que o cilindro hidráulico é colocado dentro da viga inferior (base da máquina) da máquina de prensagem e pode usar um cilindro hidráulico do tipo êmbolo, com o êmbolo retornando pelo peso próprio do êmbolo e dos componentes conectados.
A estrutura também é fornecida nos tipos de estrutura e coluna. Como a estrutura do chassi usa principalmente conexões soldadas, mesmo que sejam usadas estruturas de pré-aperto com parafusos, a superfície de contato entre o chassi lateral e as vigas superior e inferior é muito grande, de modo que o próprio chassi tem boa rigidez e pode se adaptar a prensas de grande tonelagem. A estrutura da coluna (geralmente de duas colunas) é simples e conveniente para o processamento e a programação, sendo adequada para montagem de prensa de tonelagem menor.
As maiores vantagens das máquinas de prensagem vertical são: estrutura compacta, pequena área ocupada, boa centralização da peça durante a prensagem, operação conveniente de prensagem vertical, menor probabilidade de distorção, emperramento e outros fenômenos adversos, e o cilindro hidráulico de êmbolo montado na parte inferior tem estrutura mais simples, menor custo, retorno mais suave e operação mais confiável e razoável em comparação com o cilindro hidráulico de pistão.
Suas desvantagens são: devido à viga superior, a operação de içamento das peças de trabalho durante o processo de prensagem é inconveniente. Entretanto, se um carrinho móvel for instalado, o carregamento e o descarregamento das peças podem ser feitos fora da máquina de prensagem, superando a desvantagem estrutural. O carrinho móvel pode ser empurrado livremente sobre o trilho-guia, com batentes de posicionamento na extremidade dianteira para garantir que a peça de trabalho de prensagem seja coaxial com o centro de prensagem do cilindro hidráulico, tornando a operação muito conveniente.
Outro problema é a estrutura do cilindro hidráulico montado na parte inferior. Embora a máquina de encaixe por pressão tenha um centro de gravidade mais baixo e seja mais estável, durante o processo de encaixe por pressão, quando o êmbolo do cilindro hidráulico empurra para cima, a peça de trabalho que está sendo pressionada também se move para cima. Como a estrutura e as dimensões do componente encaixado por pressão são grandes e têm peso próprio significativo, ele parece instável e menos seguro. Devido à estrutura mais larga, ele ocupa parte da posição de operação de encaixe da prensa, criando inconvenientes e pontos cegos para a observação do encaixe da prensa.
As máquinas de prensagem horizontais são o oposto das verticais. Elas exigem uma área de instalação maior, com as peças de trabalho colocadas horizontalmente. Afetados pelo peso próprio, a centralização e o ajuste são mais difíceis. Devido à centralização e ao posicionamento instáveis, é mais provável que ocorram problemas durante o processo e a operação de prensagem.
O curso do cilindro hidráulico do êmbolo não é tão grande quanto o das máquinas verticais, e o retorno é difícil. As máquinas de prensagem horizontal são, em sua maioria, estruturas de coluna, reduzindo as dimensões horizontais, o que é benéfico para os operadores observarem e se aproximarem da peça de trabalho. Sua principal vantagem é o ambiente espaçoso, conveniente para carga, descarga e operação de peças de trabalho, observação clara, posicionamento estável da peça de trabalho e nenhum risco de queda.
Os seguintes pontos devem ser observados no uso e na manutenção das máquinas de prensagem:
- Ao usar uma máquina de prensagem, verifique se a pressão de trabalho, o curso de trabalho e a superfície da mesa de trabalho estão dentro da faixa de trabalho nominal.
- Antes de ligar a máquina, verifique se todos os pontos de lubrificação da máquina de prensagem estão cheios de óleo lubrificante.
- Verifique se as folgas entre as várias partes móveis e o aperto do freio estão adequados.
- Verifique se há algum objeto estranho preso nas peças rotativas.
- Depois de conectar a energia, verifique se o movimento do curso em vazio atende aos requisitos especificados.
- Manter a limpeza da área de trabalho.
- Os fatores que afetam a precisão da prensa incluem a planicidade da superfície de trabalho e a superfície inferior do controle deslizante, o paralelismo entre as duas superfícies, a perpendicularidade do curso da prensa em relação à superfície da mesa de trabalho e a folga do trilho de guia. Todos esses são pontos-chave para a manutenção da máquina de prensagem.
- Para máquinas de prensagem que usam sistemas hidráulicos, também é necessária a manutenção adequada do sistema hidráulico.
3. Limpeza
A limpeza durante o processo de montagem da máquina é importante para melhorar a qualidade da montagem do produto e prolongar sua vida útil. Isso é particularmente importante para rolamentos, componentes de precisão, vedações e peças com requisitos especiais de limpeza.
O processo de limpeza inclui soluções de limpeza, métodos de limpeza e parâmetros de processo, que precisam ser determinados com base em fatores como requisitos de limpeza da peça de trabalho, tamanho do lote de produção, material da peça de trabalho, natureza e status de adesão da graxa da superfície, sujeira e impurezas mecânicas. Ao mesmo tempo, a solução de limpeza selecionada deve ser compatível com o método de limpeza. Deve-se observar também que a peça de trabalho deve ter uma certa capacidade intermediária de prevenção de ferrugem após a limpeza.
(1) Métodos de limpeza
As características e as faixas aplicáveis dos métodos de limpeza comuns são mostradas na Tabela 1.
Tabela 1 Características e faixas aplicáveis de métodos de limpeza comuns
Método de limpeza | Solução de limpeza | Características | Faixa aplicável |
Limpando | Gasolina, querosene, óleo diesel leve, etanol e soluções químicas de limpeza | Operação simples, equipamento de limpeza simples, baixa produtividade | Produção de peças únicas e pequenos lotes de peças pequenas e médias e limpeza local de peças grandes |
Limpeza por imersão | Adequado para várias soluções de limpeza comumente usadas | Operação simples; tempo de limpeza mais longo, geralmente de 2 a 20 minutos. Geralmente adota a limpeza em várias etapas | Para lotes maiores de peças de trabalho com formas mais complexas. Limpeza de manchas de óleo levemente aderidas |
Limpeza com spray | Gasolina, querosene, óleo diesel leve, soluções químicas de limpeza, tricloroetileno e solução alcalina | Bom efeito de limpeza, alta produtividade alta, melhores condições de trabalho, maior complexidade equipamentos | Para peças de produção de lotes médios e grandes, não é adequado para formas complexas. Limpeza de sujeira muito aderida e manchas de óleo semi-sólidas |
Limpeza da fase de vapor | Vapor de tricloroetileno | Bom efeito de limpeza, equipamentos mais complexos, altos requisitos de proteção ao trabalho | Peças de trabalho pequenas e médias. Bom para limpar manchas de óleo moderadamente aderidas, eficaz na remoção de sujeira |
Limpeza ultrassônica | Gasolina, querosene, óleo diesel leve, soluções químicas de limpeza e tricloroetileno | Bom efeito de limpeza, alta produtividade; manutenção e gerenciamento de equipamentos mais complexos | Para peças de trabalho pequenas e médias com altos requisitos de limpeza, geralmente usadas para a limpeza final de peças de trabalho |
Limpeza combinada por imersão e spray | Gasolina, querosene, óleo diesel leve, soluções químicas de limpeza, tricloroetileno e solução alcalina | Bom efeito de limpeza, alta produtividade; grande área útil para equipamentos de limpeza, manutenção e gerenciamento mais complexos | Para produção em lote, formas complexas e peças de trabalho com altos requisitos de limpeza. Limpeza de manchas de óleo e manchas semi-sólidas de óleo |
Limpeza combinada por imersão em vapor, vapor-spray ou vapor-imersão-spray | Solução de tricloroetileno e vapor de tricloroetileno | O mesmo que acima, mas com produtividade um pouco menor | Adequado para limpeza em fase de vapor, peças de pequeno porte com altos requisitos de limpeza. Pode limpar manchas de óleo, especialmente o tipo de spray combinado de imersão em vapor, que pode limpa sujeira muito aderida, com bom efeito de remoção de sujeira |
(2) Soluções de limpeza
1) Solventes de petróleo
Os solventes de petróleo são fáceis de armazenar e formular preventivos contra ferrugem, além de serem uma solução de limpeza tradicional. Ao usar essas soluções de limpeza, as medidas de segurança de ventilação e prevenção de incêndio devem ser consideradas.
Os solventes de petróleo comumente usados incluem principalmente gasolina, querosene e óleo diesel leve. Para requisitos especiais, podem ser usados solventes orgânicos semelhantes, como etanol e acetona.
A gasolina industrial e a gasolina de ciclo direto são usadas principalmente para limpar graxa, sujeira e impurezas mecânicas geralmente aderidas, adequadas para peças de aço e de metais não ferrosos; a gasolina de aviação é usada para limpar peças de alta qualidade.
A aplicação do querosene para lâmpadas e do óleo diesel leve é semelhante à da gasolina, mas sua capacidade de limpeza não é tão boa quanto a da gasolina. Eles secam mais lentamente após a limpeza, mas são mais seguros do que a gasolina.
Para evitar o enferrujamento da peça, uma pequena quantidade (como 1% a 3% em massa) de óleo preventivo de ferrugem do tipo deslocamento ou aditivos inibidores de ferrugem pode ser adicionada aos solventes de petróleo. Os óleos preventivos de ferrugem do tipo deslocamento incluem 201, FY-3, 661, etc. A gasolina preventiva contra ferrugem também pode ser autoformulada; a fórmula da gasolina preventiva contra ferrugem é mostrada na Tabela 2.
Essa gasolina preventiva de ferrugem tem grande capacidade de limpeza, pode limpar o suor das mãos, sais inorgânicos, graxa etc. e oferece proteção intermediária contra ferrugem para aço, ligas de cobre e outras peças de trabalho. Ao mesmo tempo, os operadores devem aplicar "luvas líquidas" nas mãos para evitar que o suor das mãos enferruje as peças de trabalho e para evitar a irritação das mãos com gasolina, querosene, diesel etc.
Tabela 2 Fórmula da gasolina antiferrugem
Componente | Fração de massa (%) |
Sulfato de sódio de petróleo | 1 |
Span-80 | 1 |
Álcool laurílico acilamida | 1 |
1% Solução de álcool benzotriazólico | 1 |
Água destilada | 2 |
Gasolina nº 200 | 94 |
Os solventes de petróleo são geralmente usados em temperatura ambiente. Se for necessário aquecer, a temperatura do óleo para querosene de lâmpada não deve exceder 40°C e para querosene solvente não deve exceder 65°C, e o aquecimento direto do recipiente com chamas não é permitido. Para óleo mecânico, óleo de turbina e óleo de transformador, a temperatura do óleo não deve exceder 120°C.
2) Soluções alcalinas
Ao preparar soluções alcalinas, uma pequena quantidade de agente de limpeza surfactante pode ser adicionada para aumentar a capacidade de limpeza. Ao limpar com soluções alcalinas, observe: manchas de óleo espessas devem ser removidas primeiro; peças de diferentes propriedades de materiais não devem ser limpas juntas; após a limpeza, as peças devem ser enxaguadas ou lavadas com água e secas. As fórmulas de soluções alcalinas comuns, os parâmetros do processo e a aplicabilidade são mostrados na Tabela 3.
Tabela 3 Fórmulas de soluções alcalinas comuns, parâmetros de processo e aplicabilidade
Composição/(g/L) | Principais parâmetros do processo | Aplicabilidade |
Hidróxido de sódio 50-55 Fosfato de sódio 25-30 Carbonato de sódio 25-30 Silicato de sódio 10-15 | Temperatura de limpeza 90-95°C Limpeza por imersão ou spray Tempo de limpeza 10min | Peças de aço, com manchas de óleo severamente aderidas ou pequenas quantidades de manchas de óleo insolúveis e impurezas |
Hidróxido de sódio 70-100 Carbonato de sódio 20-30 Fosfato de sódio 20-30 | Temperatura de limpeza 90-95°C Limpeza por imersão ou spray Tempo de limpeza: 7 a 10 minutos | Peças de aço de liga de níquel-cromo |
Hidróxido de sódio 5-10 Fosfato de sódio 50-70 Carbonato de sódio 20-30 | Temperatura de limpeza 80-90°C Limpeza por imersão ou spray Tempo de limpeza 5-8min | Peças de trabalho em aço e liga de cobre |
Hidróxido de sódio 5-10 Fosfato de sódio ≈50 Silicato de sódio ≈30 | Temperatura de limpeza 60-70°C Limpeza por imersão ou spray Tempo de limpeza ≈5min | Peças de trabalho em alumínio e liga de alumínio |
3) Soluções químicas de limpeza
As soluções de limpeza química contêm surfactantes, também conhecidos como soluções de limpeza emulsificantes, que têm boa capacidade de limpeza de graxa e sujeira solúvel em água. Essas soluções de limpeza são fáceis de preparar, estáveis e duráveis, não tóxicas, não inflamáveis, seguras de usar, de baixo custo, e algumas soluções de limpeza química também têm certas capacidades intermediárias de prevenção de ferrugem, o que as torna muito adequadas para a limpeza de processos intermediários durante a montagem. Há muitas fórmulas para soluções de limpeza química; as fórmulas de soluções de limpeza química comuns, os parâmetros do processo e a aplicabilidade são mostrados na Tabela 4.
Tabela 4 Fórmulas de soluções de limpeza química comuns, parâmetros de processo e aplicabilidade
Composição e fração de massa (%) | Principais parâmetros do processo | Aplicabilidade |
105 agente de limpeza 0,5 6501 agente de limpeza 0,5 Restante de água | Temperatura de limpeza 85°C Pressão de pulverização 0,15 MPa Tempo de limpeza 1min | Peças de aço. Principalmente para limpar manchas de óleo e impurezas mecânicas compostas principalmente de óleo de máquina |
664 agente de limpeza 2-3 Restante de água | Temperatura de limpeza 75°C Mergulhe e lave, mova para cima e para baixo Tempo de lavagem 3~4min | Peças de aço. Não é adequado para lavar peças de metal não ferroso, como cobre e zinco. Principalmente para a limpeza de ácido esteárico, parafina, vaselina, etc. |
6501 agente de limpeza 0,2 6503 agente de limpeza 0,2 Oleato de trietanolamina 0,2 Restante de água | Temperatura de limpeza 35~45℃ Limpeza ultrassônica (frequência de trabalho 17~21kHz) Tempo de limpeza 4~8min | Peças de aço usinadas com precisão. Limpeza de óleo mineral e resíduos de pasta de moagem contendo óxido de cromo, etc. |
6503 agente de limpeza 0,5 Agente de limpeza TX-10 0,3 Polietilenoglicol (massa molecular relativa de aproximadamente 400) 0,2 Ftalato de dibutilo 0,2 Fosfato trissódico 1,5~2,5 Restante de água | Temperatura de limpeza 35~45℃ Limpeza ultrassônica (frequência de trabalho 17~21kHz) Tempo de limpeza 4min | Peças de aço usinadas com precisão. Principalmente para limpeza Graxa |
664 agente de limpeza 0,5 Agente de limpeza Pingping Jia 0,3 Trietanolamina 1.0 Ácido oleico 0,5 Polietilenoglicol (massa molecular relativa de aproximadamente 400) 0,2 Restante de água | Temperatura de limpeza 75~80℃ Mergulhe e lave, mova para cima e para baixo Tempo de limpeza 1min | Peças de trabalho de aço usinadas com precisão. Capacidade muito forte de limpar a graxa |
4) Tricloroetileno
O tricloroetileno tem vantagens como alta eficiência de desengorduramento, bom efeito de limpeza e não inflamabilidade. Com a adição de estabilizadores adequados, ele pode limpar peças de metal não ferroso, como ligas de alumínio e magnésio. Entretanto, seu equipamento de limpeza é relativamente complexo, exigindo um bom sistema de ventilação e um sistema de recuperação do líquido de limpeza. Deve-se prestar atenção também à prevenção da corrosão das peças de trabalho e dos tanques de limpeza.
O tricloroetileno é um solvente forte com baixo ponto de ebulição, fácil de vaporizar e condensar. Ele tem alta densidade de vapor e não é facilmente difundido, o que o torna adequado para a limpeza por vapor. Também pode ser usado para limpeza por imersão, limpeza por spray ou uma combinação dos três métodos de limpeza. Quando usado para limpeza ultrassônica, é particularmente adequado para a limpeza de peças de instrumentos, elementos ópticos e componentes eletrônicos com requisitos de alta qualidade.
Além disso, há a limpeza ultrassônica. O mecanismo da limpeza ultrassônica é introduzir vibrações ultrassônicas no líquido de limpeza, fazendo com que um grande número de bolhas de cavitação apareça no líquido de limpeza, que cresce gradualmente e, em seguida, entra em colapso repentino.
Quando as bolhas entram em colapso, elas produzem microondas do centro para fora, com pressões que podem chegar a centenas ou até milhares de atmosferas, promovendo a remoção de manchas de óleo aderidas à peça de trabalho. Ao mesmo tempo, a forte oscilação das bolhas de cavitação aumenta e acelera a emulsificação e a solubilização do líquido de limpeza nas manchas de óleo, melhorando a capacidade de limpeza.
(3) Seleção de métodos de limpeza
A seleção dos métodos de limpeza e dos equipamentos e líquidos de limpeza correspondentes deve se basear em condições específicas, como escala de produção da fábrica, tamanho do lote, dimensões da estrutura da peça de trabalho, características de forma, requisitos de limpeza, material e condições de pré-limpeza.
Para a produção de grandes lotes com alta eficiência de produção, devem ser selecionados equipamentos de limpeza adequados, com operação contínua no estilo de esteira transportadora, entrada e saída contínuas e até mesmo o uso de tecnologia avançada de controle automático, como a máquina de limpeza mostrada na Figura 9.
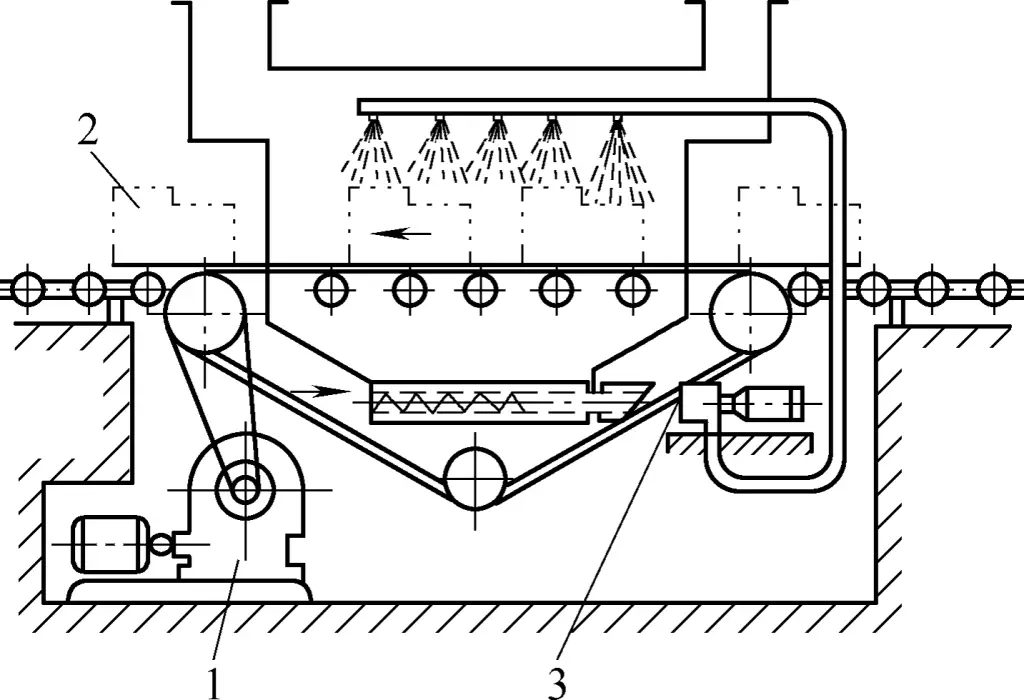
1-Motor elétrico
2 peças de trabalho
3-Bomba de circulação
Ele também pode ser equipado com alguns braços robóticos e ajuste e contagem automáticos, recuperação e tratamento de líquido de limpeza, feedback de inspeção automática e outros sistemas de controle. Para peças maiores e lotes pequenos, podem ser usadas câmaras de limpeza fixas ou giratórias, selecionando ângulos diferentes a partir de posições diferentes para borrifar o líquido de limpeza na peça de trabalho usando bicos de limpeza.
Durante o processo de limpeza, a peça de trabalho pode ser girada conforme necessário. Após a limpeza por pulverização, interrompa a pulverização e use ar comprimido para limpar e secar. A estrutura do bocal de ar comprimido é mostrada na Figura 10; o bocal de limpeza é mostrado na Figura 11.
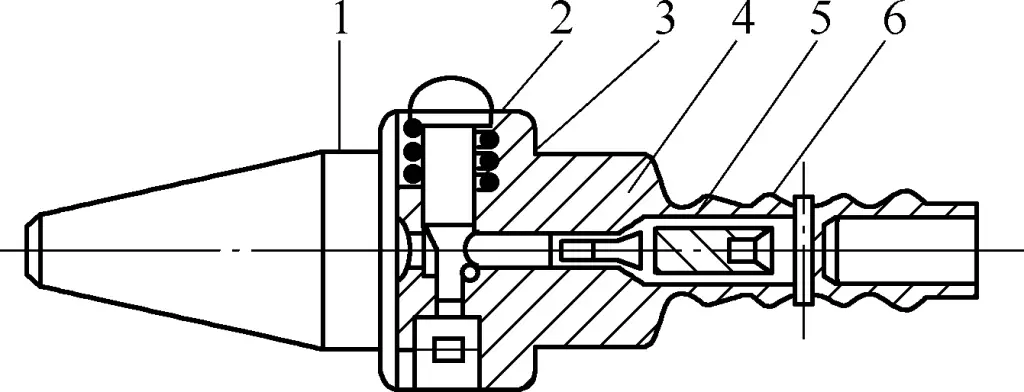
1-Bocal
2 interruptores
3-Primavera
4-Haste de pressão
5-Válvula cônica
6-Corpo
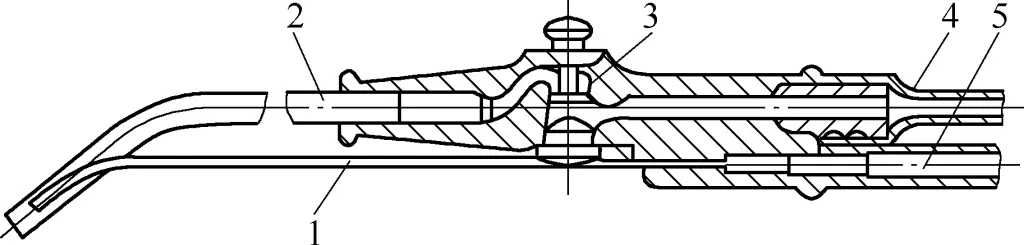
1 tubo de spray de detergente
2 - Tubo de pulverização de ar comprimido
3 interruptores
4 - Tubo de ar comprimido
Tubo de 5 detergentes
No caso de peças pequenas com forte aderência de manchas de óleo, a limpeza por imersão ou spray deve ser feita primeiro. Para melhorar a qualidade da limpeza e reduzir o tempo de limpeza, geralmente são usados vários líquidos de limpeza diferentes, com tanques separados para a limpeza sequencial, cada tanque focado em diferentes aspectos da remoção de manchas de óleo.
Para peças de trabalho com dimensões e massa maiores, a limpeza local é frequentemente usada. A peça de trabalho pode ser parcialmente imersa em um tanque de limpeza ultrassônica para a limpeza; projetos estruturais especiais também podem ser feitos de acordo com o formato de peças grandes ou com os requisitos das áreas de limpeza local para obter a limpeza local.
Para peças com formas muito complexas ou furos e ranhuras de tamanhos variados, pode ser usada a limpeza ultrassônica com diferentes frequências de vibração. As operações de limpeza devem manter um ambiente limpo e seguir rigorosamente as especificações do processo, o que é muito importante para obter uma produção segura.
(4) Precauções para o trabalho de limpeza das peças
1) As peças devem ser cuidadosamente limpas antes da montagem. Antes da montagem, os resíduos de areia de moldagem, lascas, ferrugem etc. nas peças devem ser completamente removidos. Os locais que retêm facilmente detritos, como orifícios e ranhuras, devem ser limpos com cuidado especial, e as rebarbas e bordas afiadas devem ser removidas. Algumas peças, como o interior dos compartimentos, precisam ser pintadas após a limpeza.
Se a limpeza não for completa, isso afetará a qualidade da montagem e a vida útil do maquinário. Por exemplo, as guias deslizantes podem acelerar o desgaste devido a partículas residuais de areia e cavacos entre as superfícies de contato, e podem ocorrer até mesmo acidentes graves, como a "gripagem" da guia.
2) Preste atenção à limpeza dos cavacos gerados durante o processo de montagem. Durante a montagem, algumas peças exigem processamento suplementar, como perfuração, alargamento de orifícios de pinos de localização e roscas de rosca. Os cavacos produzidos devem ser removidos. Quando necessário, o processamento suplementar deve ser feito longe do local de montagem para evitar que os cavacos caiam nas superfícies de contato.
3) Não danifique a precisão original ao limpar superfícies de contato importantes. A ferrugem e a tinta seca nas superfícies usinadas podem ser removidas com limas, raspadores e lixas. No caso de superfícies de contato importantes, deve-se tomar cuidado extra durante a limpeza para não danificar a precisão original.
4) Não danifique as peças durante o processo de limpeza. Deve-se tomar cuidado para não danificar as peças durante a limpeza. Se houver pequenos amassados ou rebarbas, eles podem ser consertados com uma pedra de amolar ou raspador e, em seguida, limpos novamente.
5) Não use gasolina para limpar peças de borracha. Para peças de borracha, como anéis de vedação, é estritamente proibido limpá-las com gasolina para evitar deformações. Deve-se usar líquido de limpeza ou álcool para a limpeza.
6) Não use fios de algodão para limpar os rolamentos. Ao limpar rolamentos, devem ser usadas ferramentas como escovas, e não fios de algodão, para evitar que as fibras de algodão entrem no rolamento e afetem a qualidade da montagem.
7) Evite a contaminação secundária das peças limpas. Para as peças que já foram limpas, não as limpe casualmente durante a montagem, pois isso pode facilmente sujar as peças e causar contaminação secundária.
Após a limpeza, as peças devem secar as gotas de óleo antes da montagem para evitar que a contaminação por óleo afete a qualidade da limpeza da montagem. Se as peças limpas não forem montadas imediatamente, devem ser tomadas medidas para evitar exposição prolongada, o que poderia levar à contaminação das peças por poeira.
8) Não se esqueça de adicionar óleo lubrificante e fazer os ajustes necessários antes da montagem. As superfícies de contato geralmente precisam ser lubrificadas com óleo antes da montagem, caso contrário, podem ocorrer fenômenos como arranhões nas superfícies de contato durante a montagem. No caso de superfícies de contato de conexões móveis, a falta de lubrificação pode facilmente causar resistência ao movimento, desgaste acelerado ou até mesmo embaçamento da superfície devido à falta de lubrificação.
As rebarbas resultantes da usinagem das peças e os amassados causados por colisões durante a transferência do processo geralmente são facilmente ignorados, afetando a precisão da montagem. Portanto, deve-se prestar atenção à retificação desses defeitos nas peças durante a montagem.