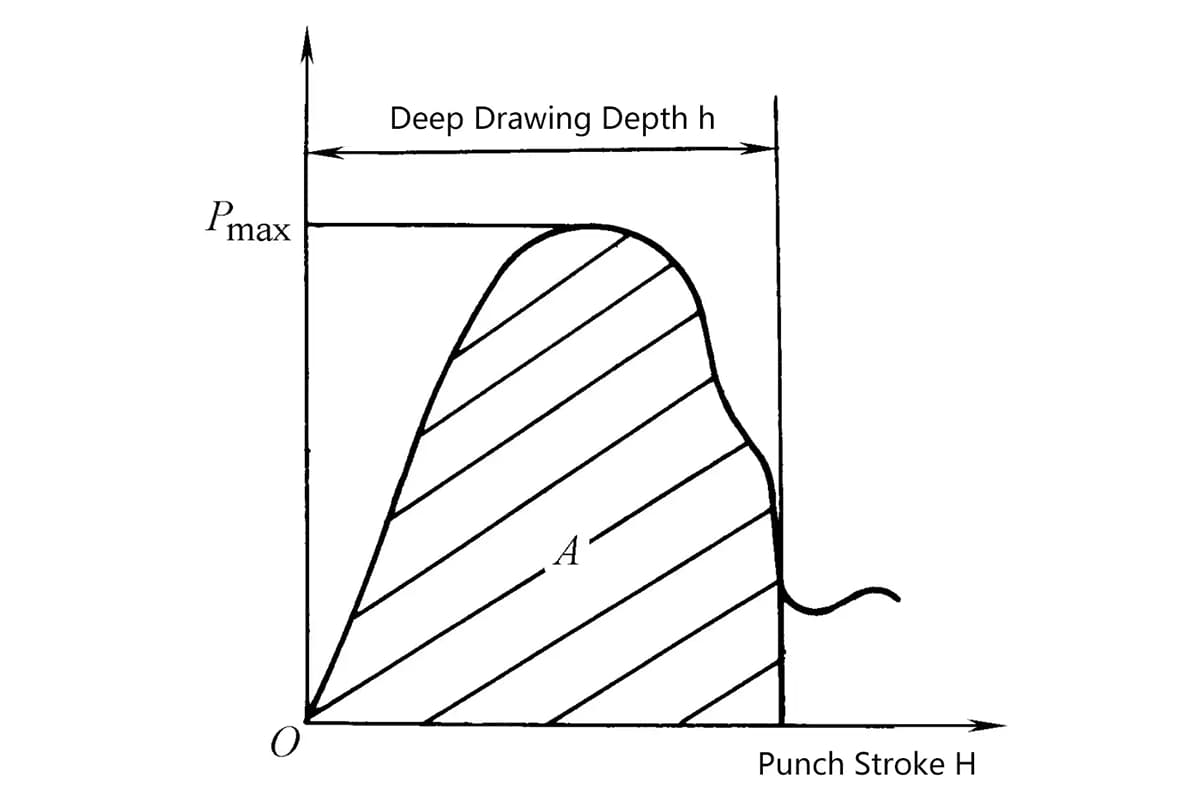
Волочение - это процесс формования листового металла, при котором плоский лист под давлением пресса и действием штампа вдавливается в открытую полую часть.
Как правило, при обработке волочения используется вытяжной штамп, который завершает процесс волочения под действием давления пресса. На рисунке 1 показана схема процесса цилиндрического волочения. Заготовка, помещенная на поверхность вогнутого штампа 3, втягивается в вогнутый штамп 3 под давлением держателя заготовки 1 и силой вытяжки пуансона 2, в результате чего образуется цилиндрическая вытянутая деталь.
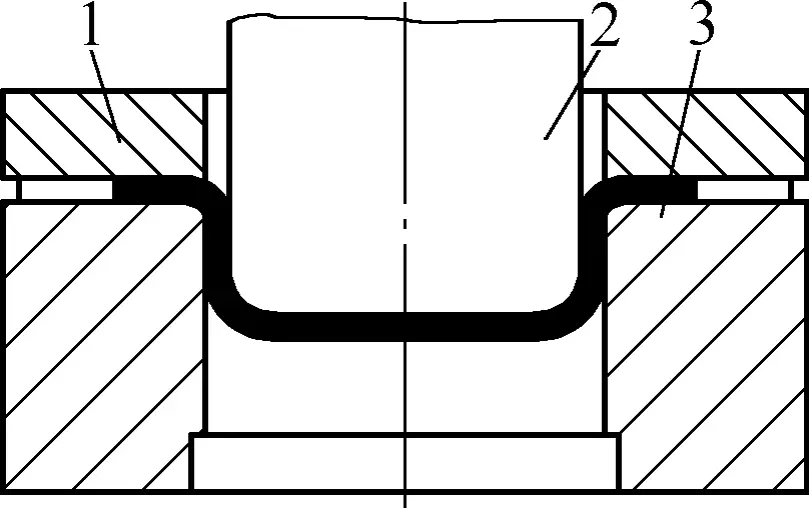
1 - Держатель заготовок
2-Панч
3-Die
I. Оборудование и инструменты для рисования
В процессе волочения можно получить тонкостенные детали различной формы: цилиндрические, ступенчатые, конические, квадратные, сферические и различные неправильные формы.
В производстве обработка чертежей может осуществляться на общих прессах одинарного действия (в основном используются для средних и мелких чертежных деталей) или на прессах двойного или тройного действия (в основном используются для крупных и средних сложных чертежных деталей или автомобильных панелей), а чертежный штамп является наиболее важным инструментом для завершения процесса чертежа.
Как правило, точность обработки вытянутых деталей зависит от конструкции и точности вытяжного штампа, а также от формы и размера самой вытянутой детали. Экономические допуски на размеры деталей, изготовленных методом волочения, лучше всего поддерживать на уровне ниже IT11.
1. Общие конструкции волочильных штампов
Постоянно меняющиеся формы вытягиваемых деталей приводят к широкому разнообразию конструкций вытяжных штампов. Чаще всего для вытяжки деталей из листового металла используются однооперационные штампы, которые выполняют только одну вытяжку за один ход пресса.
Волочильные штампы можно разделить на два типа в зависимости от последовательности обработки вытянутых деталей: штампы для начального и последующего волочения. В зависимости от того, используется ли держатель заготовок, их также можно разделить на те, которые имеют или не имеют держатель заготовок.
(1) Чертежные штампы без держателя заготовок
На рисунке 2 показана конструкция первого вытяжного штампа для нефланцевых цилиндрических деталей без держателя заготовки. Неглубокий паз D на верхней поверхности вогнутого штампа 2 на рисунке используется для размещения чертежной заготовки. К его глубине не предъявляется особых требований, лишь бы он был удобен для размещения заготовки.
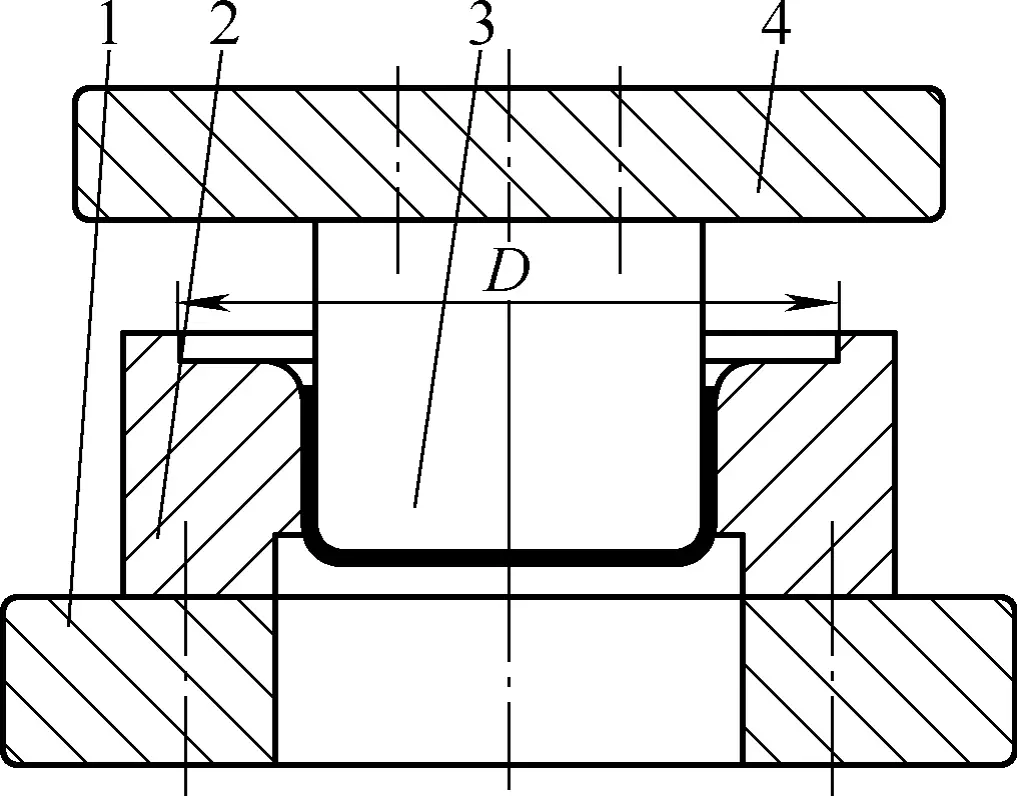
1-Нижний шаблон
2-Die
3-Панч
Шаблон 4-Upper
(2) Чертежные штампы с держателем заготовок
На рисунке 3 показана структура штампа с использованием держателя заготовок для первоначального рисунка. Держатель заготовок 4 установлен на нижнем штампе, а усилие удержания заготовок передается через выталкивающий штифт 5, установленный на нижнем штампе. Источником силы удержания заготовки может быть упругий буфер, пружина, усилие цилиндра пресса и т. д. Материал заготовки помещается в кольцо позиционирования держателя заготовки 4. В результате взаимодействия пуансона 3, матрицы 2 и держателя заготовок 4 заготовка вытягивается.
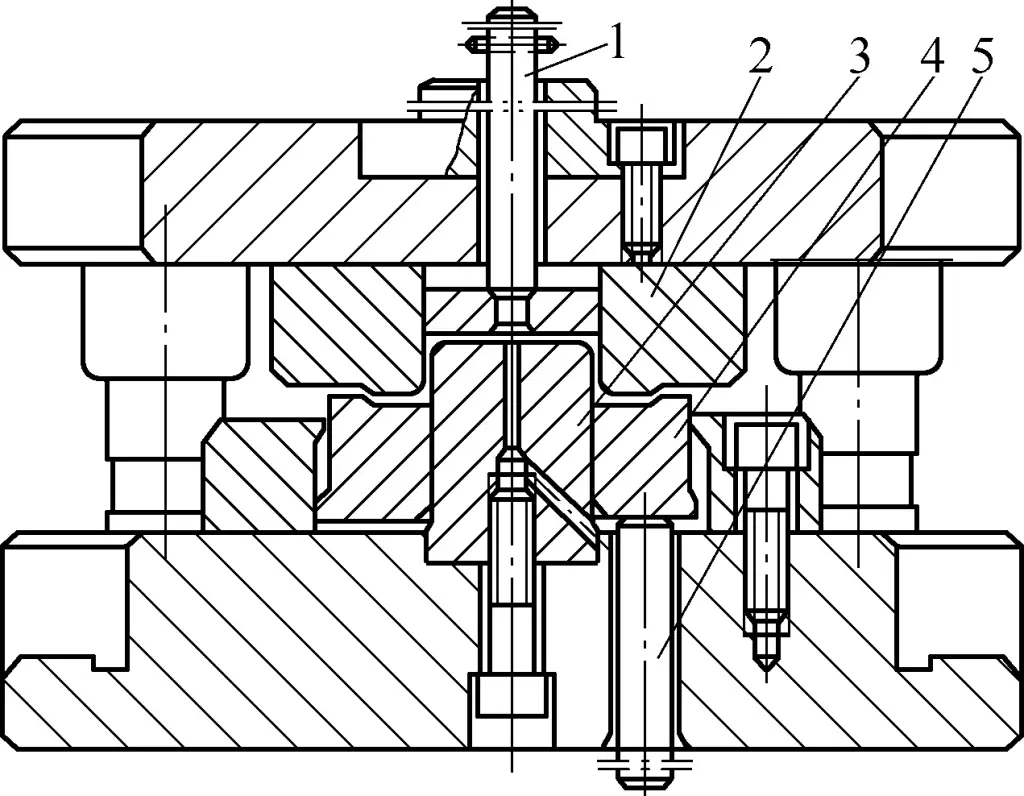
1-Подъемный стержень
2-Die
3-Панч
4-Бланкодержатель
5-выталкивающий штифт
Конструкция штампа, показанная на рисунке 3, также может использоваться для первоначального и последующего вытягивания деталей с фланцами. Во время вытяжки предварительно вытянутый фланец помещается в кольцо позиционирования держателя заготовки 4.
2. Структурный состав волочильного штампа
Как было сказано выше, вытяжной штамп обычно состоит из трех частей: пуансона, матрицы и держателя заготовок (иногда он может быть без держателя заготовок). Кроме того, имеются устройства позиционирования и разгрузки, а также другие. Пуансон и матрица являются основными компонентами, которые непосредственно производят воздействие на материал, в то время как держатель заготовки в основном используется для регулировки давления на заготовку и контроля сопротивления подачи заготовки.
II. Определение параметров процесса волочения
Для обеспечения качества вытяжки деталей необходимо определить следующие параметры процесса при формулировании процесса вытяжки и проектировании соответствующих вытяжных штампов.
1. Определение размера заготовки для вытяжки деталей
Правильность расчета размеров заготовок для вытяжки деталей напрямую влияет на качество обработки штамповочные детали. Хотя формулы расчета материала заготовки для вытяжки деталей различной формы отличаются, они следуют одному и тому же основному принципу расчета диаметра материала заготовки: "Поскольку толщина заготовки до и после волочения изменяется очень незначительно, объем до и после деформации остается неизменным, а значит, площадь поверхности заготовки до волочения равна площади поверхности заготовки после волочения".
Перед расчетом материала заготовки, учитывая такие факторы, как неравномерный зазор вытяжного штампа и анизотропия материалов для вытяжки, в большинстве случаев край обода или фланца вытянутой детали получается неровным и нуждается в обрезке. Поэтому при расчете размера заготовки необходимо зарезервировать определенный припуск на обрезку Δh в направлении высоты.
Припуск на обрезку Δh для вытянутых деталей различной формы может быть разным. В таблице 1 приведены припуски на обрезку для цилиндрических деталей без фланцев.
Таблица 1 Припуск на обрезку Δh для цилиндрических деталей без фланцев (единицы измерения: мм)
Общая высота детали h | Относительная высота детали h/d | Дополнительная диаграмма | |||
0.5~0.8 | 0.8~1.6 | 1.6~2.5 | 2.5~4 | ||
10 | 1 | 1.2 | 1.5 | 2 | ![]() |
20 | 1.2 | 1.6 | 2 | 2.5 | |
50 | 2 | 2.5 | 3.3 | 4 | |
100 | 3 | 3.8 | 5 | 6 | |
150 | 4 | 5 | 6.5 | 8 | |
200 | 5 | 6.3 | 8 | 10 | |
250 | 6 | 7.5 | 9 | 11 | |
300 | 7 | 8.5 | 10 | 12 |
После определения припуска на обрезку диаметр заготовки D для нефланцевых цилиндрических деталей может быть рассчитан по следующей формуле (значения параметров в формуле приведены на дополнительной схеме в таблице 1):
D=√[d2+4d(h+Δh)]
2. Определение количества пропусков розыгрыша
Степень деформации вытянутых деталей из разных материалов и разной формы различна. Для вытяжки квалифицированных деталей необходимо определить степень деформации и, соответственно, количество проходов волочения. В противном случае в процессе волочения из-за чрезмерной деформации растягивающее напряжение в опасных сечениях может превысить предел, что приведет к образованию трещин.
Степень деформации при волочении деталей различной формы также различна. Количество проходов волочения для цилиндрических деталей без фланцев может быть определено с помощью двух различных методов расчета процесса.
1) Рассчитайте относительную высоту h/d вытягиваемой детали и относительную толщину t/D×100 материала. Количество проходов волочения можно получить, обратившись непосредственно к таблице 2.
Таблица 2 Максимальная относительная высота вытяжки h/d для цилиндрических деталей без фланцев
Количество проходов рисунка | Относительная толщина заготовки t/D×100 | |||||
2~1.5 | 1.5~1 | 1~0.6 | 0.6~0.3 | 0.3~0.15 | 0.15~0.08 | |
1 | 0.94~0.77 | 0.84~0.65 | 0.7~0.57 | 0.62~0.5 | 0.52~0.45 | 0.46~0.38 |
2 | 1.88~1.54 | 1.6~1.32 | 1.36~1.1 | 1.13~0.94 | 0.96~0.83 | 0.9~0.7 |
3 | 3.5~2.7 | 2.8~2.2 | 2.3~1.8 | 1.9~1.5 | 1.6~1.3 | 1.3~1.1 |
4 | 5.6~4.3 | 4.3~3.5 | 3.6~2.9 | 2.9~2.4 | 2.4~2 | 2~1.5 |
5 | 8.9~6.6 | 6.6~5.1 | 5.2~4.1 | 4.1~3.3 | 3.3~2.7 | 2.7~2 |
Примечание: Большое соотношение h/d применимо для первого процесса с большим радиусом угла штампа (когда t/D×100=2~1.5, rумереть=8t - t/D×100=0.15~0.08, rумереть=15t), а малое соотношение применимо при малом радиусе угла штампа rумереть=(4~8)t.
2) Используйте формулу для прямого расчета количества операций рисования n:
n=1+[lgdn-lg(m1D)]/lgmn
В формуле
- n - количество операций рисования;
- dn - диаметр заготовки (мм);
- D - диаметр заготовки (мм);
- m1 - первый коэффициент чертежа, см. таблицу 3;
- mn - средний коэффициент вытяжки для последующих рисунков, см. таблицу 3.
Рассчитанное количество операций рисования принимается за наибольшее целое значение, которое и является требуемым количеством операций рисования.
Таблица 3: Коэффициенты вытяжки для различных металлических материалов
Материал | Первый рисунок m1 | Последующие чертежи мn |
Сталь 08 | 0.52~0.54 | 0.68~0.72 |
Алюминий и алюминиевый сплав 8A06M, 1035M, 3A21M | 0.52~0.55 | 0.70~0.75 |
Твердый алюминий 2A12M, 2A11M | 0.56~0.58 | 0.75~0.80 |
Латунь H62 | 0.52~0.54 | 0.70~0.72 |
Латунь H68 | 0.50~0.52 | 0.68~0.70 |
Чистая медь T1, T2, T3 | 0.50~0.55 | 0.72~0.80 |
Бескислородная медь | 0.50~0.55 | 0.75~0.80 |
Жесть | 0.58~0.65 | 0.80~0.85 |
Сплав нихрома Cr20Ni80 | 0.54~0.59 | 0.78~0.84 |
Легированная сталь 30CrMnSiA | 0.62~0.70 | 0.80~0.84 |
Нержавеющая сталь 1Cr18Ni9Ti① | 0.52~0.55 | 0.78~0.81 |
Нержавеющая сталь 12Cr13 | 0.52~0.56 | 0.75~0.78 |
Травленый стальной лист | 0.54~0.58 | 0.75~0.78 |
① Марка 1Cr18Ni9Ti была отменена в GB/T20878-2007
3. Расчет силы тяги
Цель расчета усилия вытяжки - выбор оборудования и проектирование пресс-форм. Для цилиндрических деталей без фланцев усилие вытяжки F для первого процесса вытяжки рассчитывается как F=πd1tσbk1, а для второго и последующих процессов сила вытяжки F рассчитывается как:
F=πdntσbk2
В формуле
- F - сила вытяжки (Н);
- d1, d2, ..., dn - диаметры нейтральных слоев цилиндрической части для 1-го, 2-го, ..., n-го процессов, рассчитанные по нейтральной линии (d1=d-t, d2=d1-t, ..., dn=dn-1-t) (мм);
- t - толщина материала (мм);
- σb - предел прочности (МПа);
- k1, k2 - коэффициенты, см. таблицу 4.
Таблица 4: Коэффициенты k1, k2 для чертежей цилиндрических деталей
m1 | 0.55 | 0.57 | 0.60 | 0.62 | 0.65 | 0.67 | 0.70 | 0.72 | 0.75 | 0.77 | 0.80 |
k1 | 1.00 | 0.93 | 0.86 | 0.79 | 0.72 | 0.66 | 0.60 | 0.55 | 0.50 | 0.45 | 0.40 |
m2 | 0.70 | 0.72 | 0.75 | 0.77 | 0.80 | 0.85 | 0.90 | 0.95 | - | ||
k2 | 1.00 | 0.95 | 0.90 | 0.85 | 0.80 | 0.70 | 0.60 | 0.50 | - |
4. Определение зазора в вытяжном штампе
Односторонний зазор z вытяжного штампа равен половине разницы между диаметром отверстия штампа Dумереть и диаметр пуансона Dперфоратор, который является важным параметром, влияющим на качество вытягиваемых деталей.
Слишком маленький зазор увеличивает трение, из-за чего вытянутая деталь легко ломается, царапает поверхность и сокращает срок службы штампа; слишком большой зазор делает вытянутую деталь легко морщинистой и влияет на точность детали. Рисование зазор между штампами обычно рассматривается в следующих двух ситуациях:
1) Без использования держателя заготовок, учитывая возможность образования складок, односторонний зазор z=(1~1.1)tmax, где tmax верхний предел толщины материала.
2) При использовании держателя заготовок величина зазора выбирается в соответствии с таблицей 5.
Таблица 5: Величина одностороннего зазора z для глубокой вытяжки с холостым держателем (Единицы измерения: мм)
Процесс рисования | Степень допуска вытянутой детали | |
IT11, IT12 | IT13~IT16 | |
Первый розыгрыш | z=tmax+a | z=tmax+(1.5~2)a |
Промежуточное рисование | z=tmax+2a | z=tmax+(2.5~3)a |
Окончательный рисунок | z=t | z=t+2a |
Примечание: 1. Для более толстых материалов возьмите меньшее значение в скобках, а для более тонких материалов (t/D×100=1~0.3) возьмите большее значение в скобках.
2. В таблице z - односторонний зазор между пуансоном и матрицей (мм); tmax - верхний предел толщины материала (мм); t - номинальная толщина материала (мм); a - увеличенное значение (мм), см. таблицу 6.
Таблица 6 Величина прироста a (единицы измерения: мм)
Толщина материала | 0.2 | 0.5 | 0.8 | 1 | 1.2 | 1.5 | 1.8 | 2 | 2.5 | 3 | 4 | 5 |
Увеличить значение a | 0.05 | 0.1 | 0.12 | 0.15 | 0.17 | 0.19 | 0.21 | 0.22 | 0.25 | 0.3 | 0.35 | 0.4 |
При вытяжке прямоугольных деталей, учитывая, что углы материала будут значительно толще, зазор в углах вытяжного штампа должен быть больше на величину 0,1t по сравнению с деталями с прямыми краями.
При работе на прессе двойного действия с жестким бланкодержателем необходимо определить минимальный зазор для определенной толщины материала, чтобы не прижимать заготовку мертво, без движения, и не допускать появления складок. Величина увеличения a может быть определена по формуле: a≈0,15t (t - толщина материала).
В производстве для глубоко вытянутых деталей с высокими требованиями к точности часто используется отрицательный зазор, то есть зазор при вытяжке устанавливается на уровне (0,9-0,95)t.
5. Определение размеров рабочих секций пуансонов и штампов
Определение размера рабочей части вытяжного штампа включает в себя, главным образом, радиусы углов пуансона и штампа, а также размеры и производственные допуски пуансона и штампа, которые непосредственно влияют на точность размеров и качество поверхности вытянутой детали.
(1) Определение радиуса угла чертежного штампа
Радиус угла вытяжного штампа оказывает значительное влияние на процесс вытяжки. Как правило, радиус угла штампа должен быть как можно больше. Больший радиус угла может уменьшить предельный коэффициент вытяжки и улучшить качество вытянутой детали.
Однако если радиус угла штампа слишком велик, это ослабит действие бланкодержателя и может привести к образованию складок. При выборе нормального коэффициента вытяжки радиус угла штампа rВогнутый для начального розыгрыша также может быть выбрана в соответствии с таблицами 7 и 8.
Таблица 7 Радиус углового сечения штампа для исходного чертежа rВогнутый с бланкодержателем (единицы измерения: мм)
Метод рисования | Относительная толщина заготовки t/D×100 | ||
2~1 | 1~0.3 | 0.3 ~0.1 | |
Без фланца | (6~8)t | (8~10)t | (10~15)t |
С фланцем | (10~15)t | (15~20)t | (20~30)t |
С ребрами жесткости | (4~6)t | (6~8)t | (8~10)t |
Таблица 8 Начальный радиус штампа для вытяжки rВогнутый без держателя (единицы измерения: мм)
Материал | Толщина t | rВогнутый | |
Первый розыгрыш | Последующие розыгрыши | ||
Сталь, латунь, чистая медь, алюминий | 4~6 | (3~4)t | (2~3)t |
6~10 | (1.8~2.5)t | (1.5-2.5)t | |
10-15 | (1.6-1.8)t | (1.2-1.5)t | |
15-20 | (1.3-1.5)t | (1-1.2)t |
Для последующих процессов вытяжки радиус угла штампа rВогнутый n можно постепенно уменьшать, как правило, до rВогнутый n = (0.6-0.8)rВогнутый n-1но не менее 2 т.
(2) Определение радиуса угла пуансона rВыпуклый
Влияние радиуса угла пуансона rВыпуклый на чертеже не так значителен, как радиус угла штампа rВогнутыйно если rВыпуклый слишком мала, это приведет к снижению эффективной прочности на растяжение в опасной зоне передачи цилиндрической стенки, что вызовет значительное утонение в опасной зоне.
Если rВыпуклый слишком велик, то ширина заготовки, не соприкасающейся с поверхностью штампа на начальном этапе волочения, увеличится, что сделает эту часть заготовки склонной к образованию складок. Выбор радиуса угла пуансона rВыпуклый обычно следует следующим принципам:
1) Для первого розыгрыша, когда t/D×100>0,6, возьмите rВыпуклый=rВогнутый.
2) Когда t/D×100=0,3-0,6, возьмите rВыпуклый=1.5rВогнутый.
3) Если t/D×100<0,3, возьмите rВыпуклый=2rВогнутый.
4) Для промежуточных розыгрышей возьмите rВыпуклый=(dn-1-dn-2t)/2, или взять значение, равное или немного меньшее, чем радиус угла штампа rВогнутыйт.е. возьмем rВыпуклый=(0.7-1.0)rВогнутый. В финальном розыгрыше rВыпуклый должен быть равен радиусу детали.
(3) Определение размеров пуансона и матрицы
Размеры пуансона и матрицы определяются в соответствии со следующими принципами:
1) Для вытяжного штампа в окончательном процессе размеры пуансонов и штампов и их допуски должны определяться в соответствии с требованиями к заготовке.
2) Когда требуются внешние размеры заготовки, размер штампа используется в качестве ссылки для расчета, т.е,
Размер матрицы DВогнутый=(D-0.75Δ)+δВогнутый0
Размер пуансона DВыпуклый=(D-0.75Δ - 2z)0-δConvex
Где
- D - номинальный размер формы заготовки (мм);
- Δ - допуск заготовки (мм);
- z - односторонний зазор между пуансоном и матрицей (мм);
- δВыпуклый, δВогнутый - допуски на изготовление пуансона и матрицы, соответственно. Если допуск заготовки выше IT13, допуск на изготовление пуансона и матрицы находится в диапазоне от IT6 до IT8. Если допуск заготовки ниже IT14, то допуск на изготовление пуансона и матрицы составляет IT10.
3) Если требуются внутренние размеры заготовки, то размер пуансона используется в качестве исходного для расчета, т.е,
Размер матрицы dВыпуклый=(d+0.4Δ)0-δConvex
Размер пуансона dВогнутый=(d+0.4Δ+2z)+δВогнутый0
Где d - номинальный внутренний размер заготовки (мм).
4) Для промежуточных переходных процессов полуфабрикатов, поскольку строгие ограничения не нужны, размер штампа просто должен соответствовать размеру переходной заготовки. Если в качестве эталона используется штамп, то
Размер матрицы Dумереть=D+δумереть0
Размер пуансона Dперфоратор=(D-2z)0-δpunch
III. Установка и регулировка штампов для глубокой вытяжки
В процессе глубокой вытяжки, во-первых, необходимо строго следовать процедурам штамповки во избежание ошибок. Во-вторых, чтобы обеспечить качественную глубокую вытяжку деталей, необходимо правильно установить и отрегулировать штамп.
Наиболее часто глубокая вытяжка листового металла выполняется на прессе одностороннего действия, а методы его установки и настройки в основном включают следующие аспекты.
1. Установка штампа для глубокой вытяжки
Установка и регулировка штампа глубокой вытяжки аналогичны гибочному штампу. Помимо общих проблем, таких как разгрузочные устройства и устройства упругой разгрузки, встречающихся при отладке заготовительных и гибочных штампов, существует специфическая проблема, связанная с регулировкой усилия держателя заготовки.
Если сила прижима заготовки слишком велика, вытянутые детали склонны к растрескиванию, если слишком мала - к сморщиванию. Поэтому регулировка давления кольца держателя заготовки в определенной степени имеет решающее значение для успешного выполнения глубокой вытяжки. Регулировку давления следует выполнять постоянно, внося изменения по мере необходимости.
При вытяжке симметричных или замкнутых деталей (например, цилиндрических) во время установки и настройки пресс-формы верхняя форма может быть закреплена на ползуне пресса, а нижняя форма устанавливается на рабочий стол без фиксации. Сначала на стенки полости равномерно укладывается несколько распорок, эквивалентных толщине заготовки, затем верхняя и нижняя пресс-формы выравниваются автоматически, с равномерным зазором. После регулировки закрытого положения нижняя пресс-форма закрепляется на рабочем столе.
Если для штампа глубокой вытяжки нет направляющего устройства, то при установке можно использовать стандартные образцы или прокладки для фитинг регулировка с использованием метода контроля зазора вытяжки для определения относительного положения верхней и нижней пресс-форм.
2. Основные моменты регулировки штампа для глубокой вытяжки
При настройке штампа для глубокой вытяжки следует обратить внимание на следующие аспекты:
(1) Регулировка сопротивления подачи
В процессе глубокой вытяжки, если сопротивление подачи штампа слишком велико, изделие склонно к растрескиванию, а слишком малое - к образованию складок. Поэтому ключевым моментом в процессе настройки является регулировка величины сопротивления подачи. Метод регулировки сопротивления вытяжке включает:
- Регулировка давления ползунка пресса для работы при нормальном давлении.
- Регулировка прижимной поверхности кольца держателя заготовки вытяжного штампа для обеспечения хорошей совместимости с заготовкой.
- Измените радиус галтели штампа, чтобы сделать его подходящим.
- Использование хороших смазочных материалов, увеличение или уменьшение частоты смазки.
(2) Регулировка усилия удержания заготовки
Метод регулировки усилия держателя заготовки следующий: Когда пуансон войдет в полость глубиной 10-20 мм, можно начать пробную штамповку. Когда начинается штамповка, кольцо держателя заготовки должно быть активировано, чтобы на материал действовало усилие держателя заготовки. Когда усилие держателя заготовки отрегулировано до такой степени, что в области фланца глубоко вытянутых деталей не остается явных морщин или трещин, глубину вытяжки можно постепенно увеличивать.
Регулировка усилия держателя заготовки должна быть сбалансированной. Как правило, его можно регулировать в два-три этапа в соответствии с требованиями к высоте глубоко вытянутых деталей. Каждая регулировка должна обеспечивать отсутствие морщин и трещин на заготовке.
Если усилие держателя заготовок обеспечивается воздушной подушкой в нижней части пресса, его можно регулировать путем настройки давления сжатого воздуха. Если усилие обеспечивается за счет упругости резины или пружин в выталкивающем механизме, установленном в нижней части пресс-формы, степень сжатия резины и пружин можно регулировать для настройки усилия держателя заготовок.
Усилие прижима заготовки в прессе двойного действия обеспечивается внешним ползуном пресса, величина которого регулируется винтом (ведущим винтом), соединяющим внешний ползун. Во время регулировки винт, соединяющий внешний ползун, должен быть отрегулирован равномерно, чтобы обеспечить нормальный ход работ по глубокой вытяжке.
(3) Регулировка глубины и зазора чертежа
В процессе волочения несоответствующая глубина волочения и зазор приведут к неудовлетворительному формированию заготовок.
1) При регулировке глубины вытяжки можно разделить глубину на 2-3 участка, начиная с более мелкого участка, а затем регулируя глубину, пока не будет достигнута необходимая глубина вытяжки.
2) При регулировке зазора верхняя форма сначала фиксируется на ползуне пресса, а нижняя форма помещается на рабочий стол без фиксации. Затем в полость пресс-формы помещается образец, верхняя и нижняя пресс-формы выравниваются и центрируются. Зазор во всех направлениях регулируется так, чтобы он был равномерным и постоянным, после чего пресс-формы устанавливаются в закрытое положение, болты затягиваются, нижняя пресс-форма фиксируется на рабочем столе, а образец извлекается и готовится к пробной штамповке.
IV. Работа с типичными чертежными деталями из листового металла
В реальном производстве разнообразие и конструктивные формы тянутых деталей разнообразны. Чтобы обеспечить качество обработки различных вытянутых деталей, необходимо сначала разработать соответствующие пресс-формы в соответствии с различными структурами деталей, разработать разумные методы обработки и применить соответствующие операции.
1. Метод глубокой вытяжки для полусферических деталей
В процессе глубокой вытяжки полусферических деталей пуансон контактирует со средней частью заготовки только в одной точке. Поскольку на точку контакта приходится все усилие вытяжки, материал в точке контакта сильно истончается.
Кроме того, в процессе вытяжки большая часть материала не прижимается кольцом держателя заготовки, поэтому он легко мнется, а из-за большого зазора образовавшиеся морщины нелегко удалить. Распространенные структуры полусферических деталей показаны на рисунке 4.
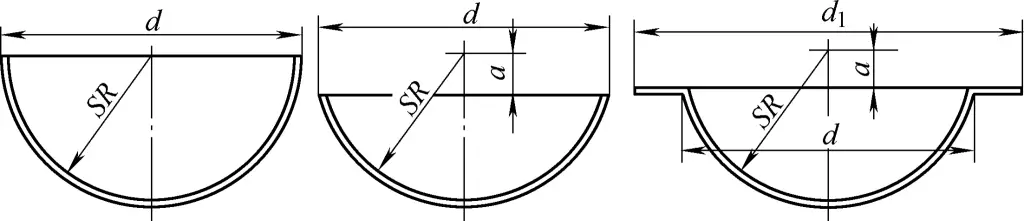
Поскольку коэффициент вытяжки m полусферических деталей постоянен для любого диаметра, его значение составляет
m=d/D=d/√(2d2)=1/1.414=0.71
Поэтому коэффициент вытяжки полусферических деталей не может быть использован в качестве основы для разработки технологических планов. Вместо этого относительная толщина t/D заготовки должна использоваться в качестве основной базы для оценки сложности формования и выбора метода вытяжки. Принципы составления плана обработки и конструкции пресс-формы следующие:
1) Если относительная толщина заготовки t/D×100% больше 3, держатель заготовки не требуется, и для изготовления полусферической детали можно использовать простую пресс-форму. Чтобы обеспечить качество поверхности, геометрическую форму и точность размеров полусферической детали, пресс-форма должна иметь сферическое дно, чтобы в конце процесса вытяжки можно было выполнить окончательную формовку внутри пресс-формы. Конструкция пресс-формы показана на рисунке 5.
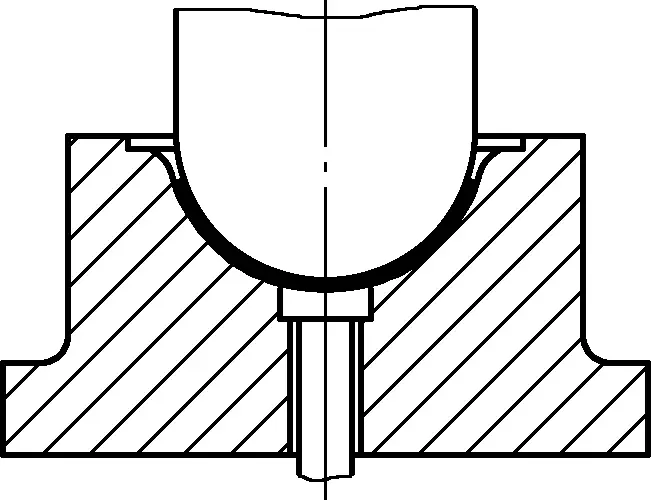
2) Когда относительная толщина заготовки t/D×100 составляет от 0,5 до 3, для предотвращения сморщивания требуется вытяжная форма с держателем заготовки. В это время роль держателя заготовки заключается не только в предотвращении сморщивания в незакрепленной средней части, но и в создании радиального напряжения при вытяжке и увеличении расширения за счет сопротивления трения, вызванного силой удержания заготовки.
3) Если относительная толщина заготовки t/D×100% меньше 0,5, необходимо использовать обратную вытяжку или вытяжную форму с лентой. Структура пресс-формы показана на рисунке 6.
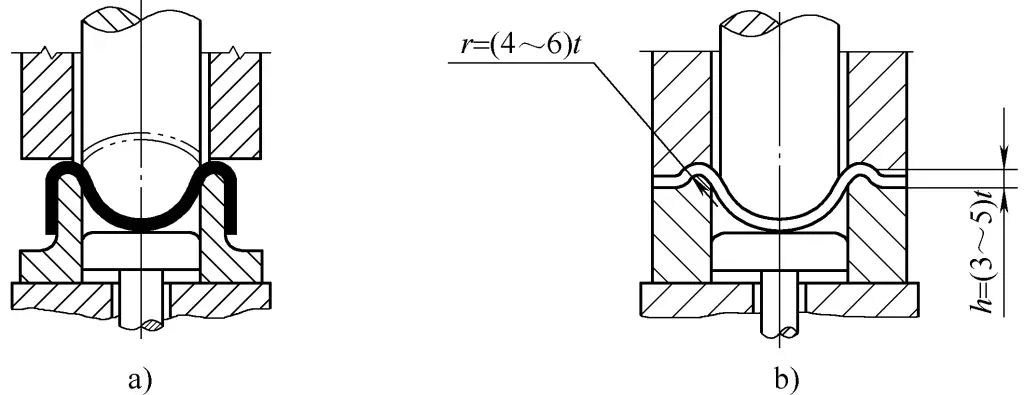
a) Обратный рисунок
б) Рисование с помощью бусинок
Кроме того, для обработки тонких материалов с небольшой относительной толщиной заготовки при составлении планов обработки или конструкций пресс-форм необходимо учитывать следующие моменты:
1) Для тонких полусферических деталей без фланцев при использовании держателя заготовок для вытяжки к заготовке следует добавить припуск на обрезку шириной не менее 10 мм, оставленный в виде фланца на вытянутой детали, иначе заготовку будет трудно вытянуть правильно.
2) Для крупных тонкостенных сферических деталей можно использовать комбинацию методов прямого и обратного волочения, чтобы исключить необходимость в держателе заготовки (см. рис. 7). Зазор с каждой стороны между пресс-формой и матрицей принимается равным (1,3-1,5)t, а зазор с каждой стороны между пресс-формой и пуансоном - (1,2-1,3)t.
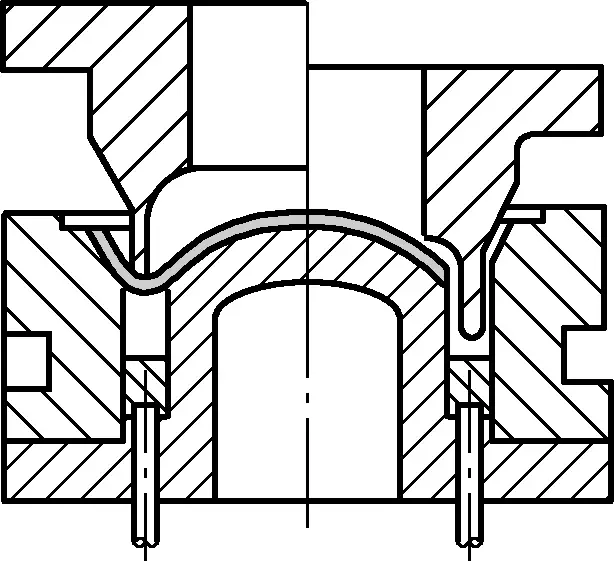
3) Для полусферической вытяжки тонкого материала можно также использовать гидравлическую или резиновую формовку, что не только сокращает количество вытяжек и улучшает условия труда, но и улучшает сам процесс вытяжки.
2. Операция волочения полусферических деталей
Для изготовления малых и средних полусферических деталей, как правило, непосредственно проектируются специальные вытяжные формы, где основная операция заключается в правильной установке и настройке форм.
В зависимости от производственного оборудования, стоимости изготовления и т.д., особенно для вытяжки больших толстых полусферических деталей из листового металла, часто используется точечное прессование или горячее прессование. Точечное прессование и горячее прессование являются распространенными методами в производство листового металлаТочечное прессование позволяет использовать небольшие пресс-формы для формирования крупных заготовок, а горячее прессование позволяет прессовать более толстые листы металла с меньшим давлением.
(1) Операция точечного нажатия
Как показано на рис. 8a, большая полусферическая часть имеет внутренний диаметр 6000 мм и изготовлена из стального листа 16MnR толщиной 20 мм. Из-за большого размера и толстого листа ее необходимо разделить на 11 лепестков для заготовки, при этом каждый сферический лист весит около 800 кг. На рис. 8b показана развернутая схема одного из лепестков. При использовании точечного прессования следует обратить внимание на следующие меры предосторожности.
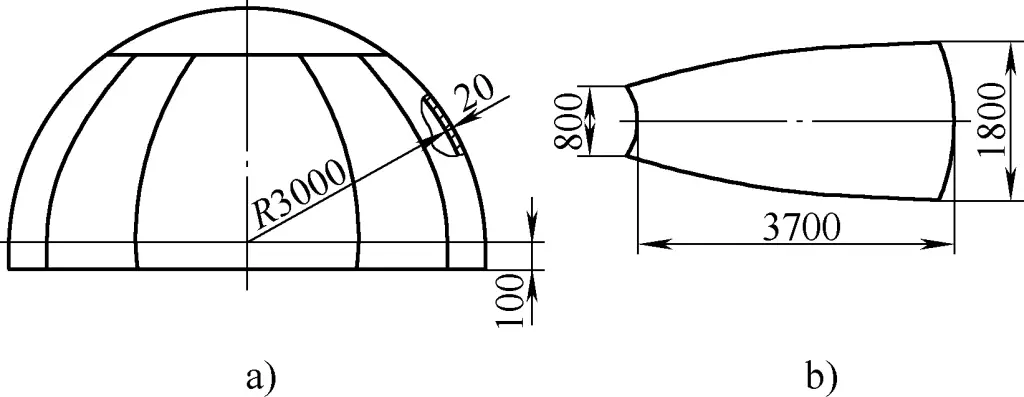
1) Принцип точечного прессования. Принцип работы точечного прессования показан на рисунке 9.
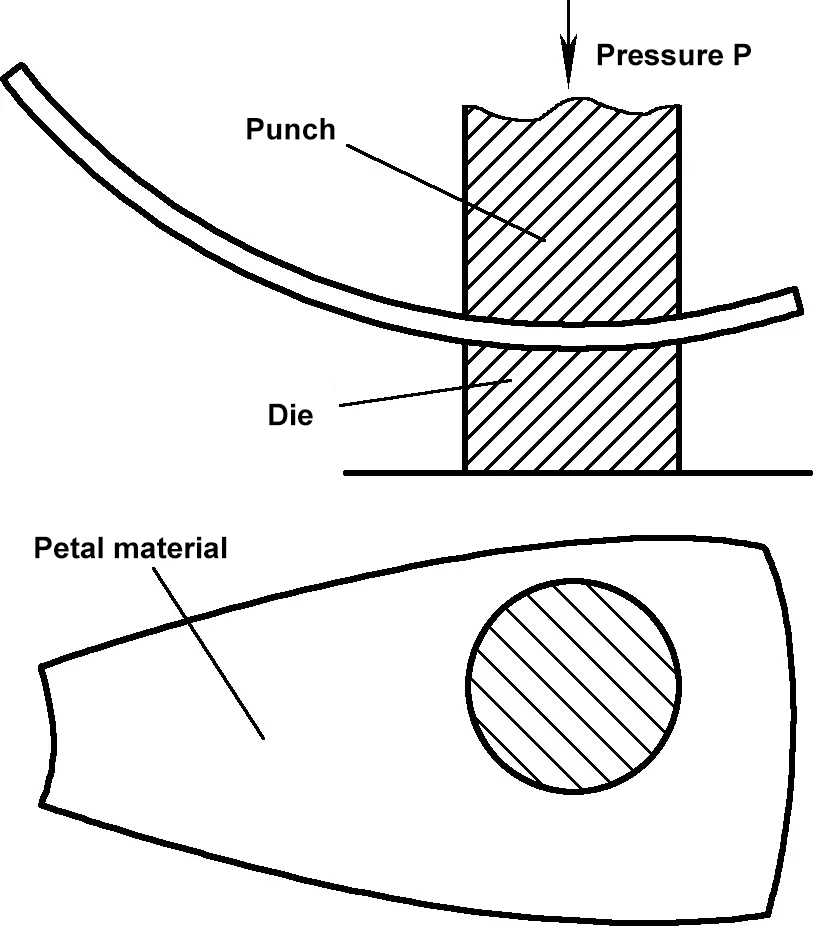
При точечном прессовании под действием внешней силы пресса материал деформируется в зоне точечного прессования формы под действием давления формы, создавая внутреннее напряжение в материале, которое противостоит деформации, и это напряжение уравновешивается внешней силой.
Непрерывное прессование до тех пор, пока внешнее усилие не сравняется с пределом текучести материала, приводит к пластической деформации внешнего слоя, распространяющейся от внешней поверхности к центру. В этот момент прессование прекращается, и пластическая деформация внутри формы сохраняется, вызывая постоянную деформацию. Постепенное перемещение материала для непрерывного точечного прессования завершает формирование сферических лепестков.
2) Выбор мужских и женских пресс-форм. Формы обычно изготавливаются из обработанной литой стали или чугуна, а в некоторых случаях могут быть собраны из стальных листов.
Размеры пресс-формы для точечного прессования включают в себя, главным образом, ширину и радиус мужских и женских форм. Как правило, сначала определяют ширину наружной и внутренней форм, а затем на основе ширины устанавливают радиус их формовки. Поскольку ширина наружной и внутренней пресс-форм напрямую влияет на эффективность точечного прессования, она часто определяется на основе таких факторов, как размер рабочего стола пресса, размер заготовки и фактические условия изготовления.
Например, в данном случае для прессования сферических лепестков используется машина 1200 т. гидравлический пресс, при этом ширина рабочей поверхности внутри колонн пресса составляет 2600 мм. В результате многократной практики было установлено, что оптимальная ширина пресс-форм находится в пределах 800-1000 мм. Хотя увеличение диаметра пресс-формы позволяет сократить количество точечных прессований, это усложняет работу, увеличивает стоимость пресс-формы и требуемое рабочее давление. И наоборот, уменьшение диаметра пресс-формы приводит к слишком большому количеству точечных прессований, что увеличивает трудоемкость обработки материала и снижает эффективность. Поэтому ширина женской пресс-формы для данного сферического лепестка установлена на уровне ϕ1000 мм (см. рис. 10).
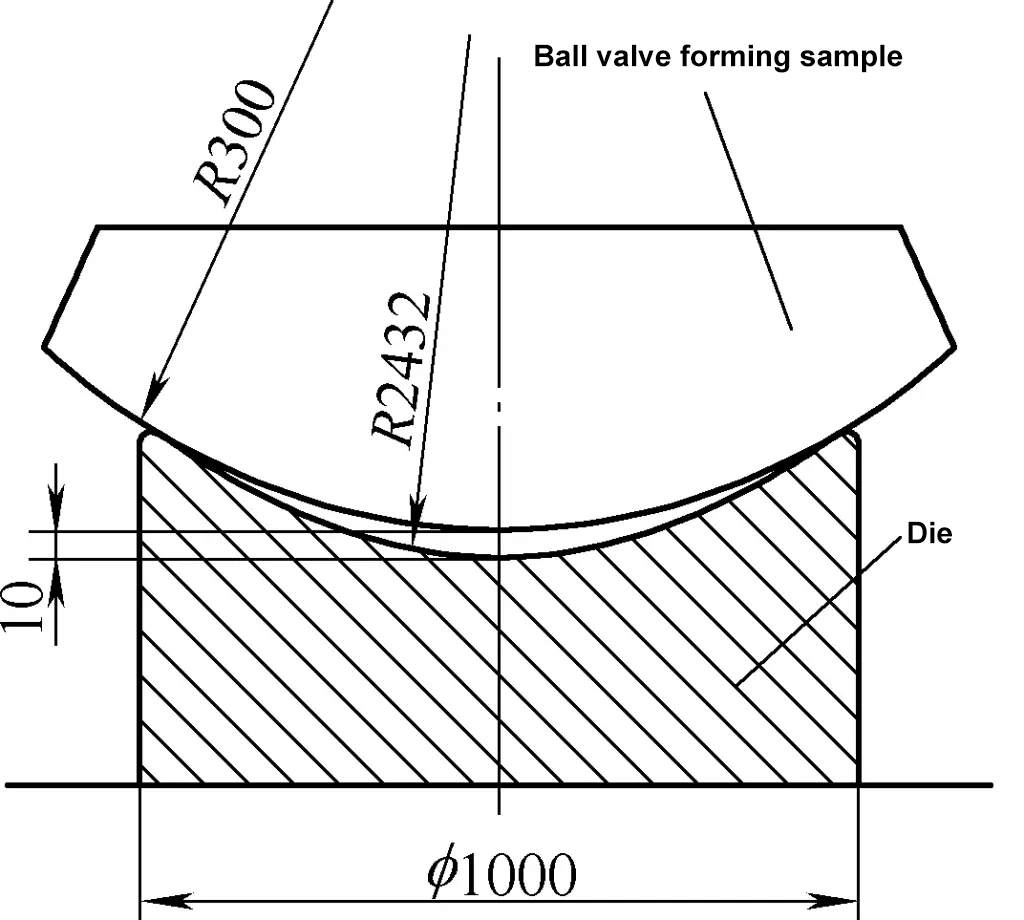
Следует отметить, что ширина мужской формы должна быть на 50-100 мм меньше, чем ширина соответствующей женской формы, чтобы предотвратить обратную деформацию во время прессования. В данном случае ширина мужской формы для сферического лепестка выбрана равной ϕ950 мм.
Во время прессования внутренний слой в зоне прессования пресс-формы сжимается, а внешний слой растягивается, что приводит к упругой деформации наряду с пластической деформацией. Кроме того, из-за напряжения, создаваемого несжатой частью, в зоне прессования возникает пружинящая кривизна.
Расчет этой величины отката сложен, поэтому в производственной практике обычно используется эмпирический метод расчета, который предполагает оставление величины зазора между радиусом спроектированных наружной и внутренней поверхностей пресс-формы и требуемым радиусом формируемой поверхности (радиус формирования детали из листового металла), обычно принимая 10-30 мм в зависимости от ситуации. Прессование проводится с различным давлением для обеспечения заданного сферического радиуса.
Этот метод прессования не только обеспечивает соблюдение размеров обрабатываемой заготовки, но и позволяет прессовать сферические поверхности с различными радиусами кривизны.
Поскольку радиус сферической поверхности заготовки велик, а толщина плиты не оказывает большого влияния, внутренний диаметр сферы R3000 мм можно напрямую использовать в качестве радиуса шаблона для прессования сферического лепестка. Если зазор между радиусом вогнутой поверхности пресс-формы и требуемым радиусом формующей поверхности заготовки (т.е. радиусом шаблона для прессования сферического лепестка) составляет 10 мм, радиус вогнутой поверхности пресс-формы может быть рассчитан как 2432 мм, как показано на рис. 10.
Радиус выпуклой поверхности пресс-формы также определен в 2432 мм, но ширина выпуклой формы установлена в 950 мм. Следует отметить, что для других форм деталей из листового металла размер пресс-формы для точечного прессования может быть определен аналогичным методом.
3) Метод работы с прессом. Во время прессования необходимо провести пробное прессование, чтобы выбрать давление, затем используется проверка шаблона для определения наиболее подходящего значения давления. Для прессования сферических лепестков используется гидравлический пресс мощностью 1200 тонн. После пробного прессования давление на поверхность составляет 90-120 кг/мм2 выбирается, что означает использование усилия 450-600 т для прессования.
Чтобы сократить количество перемещений листа и повысить эффективность, порядок прессования заключается в постепенном перемещении и точечном прессовании от края, как показано на рис. 11. В зависимости от материала и опыта прессования обычно достаточно двух-трех нажатий для придания формы.
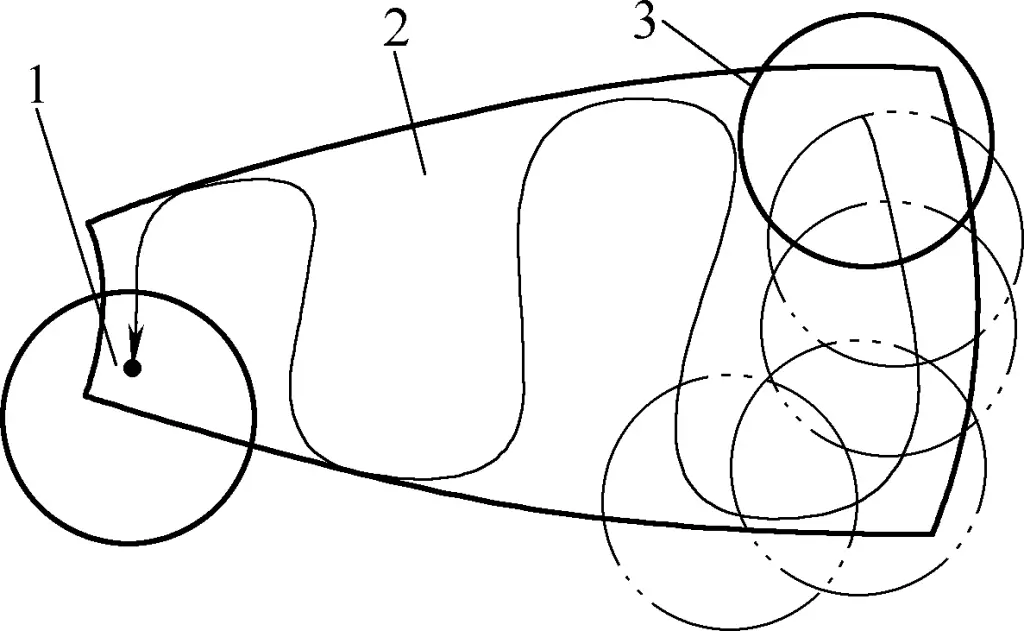
1-Последняя точка нажатия
Материал лепестков 2-Мелон
3-Первая точка нажатия
Расстояние, перемещаемое каждый раз во время прессования, не должно быть слишком большим, обычно около 100 мм. После одного цикла прессования используйте шаблон для проверки продольного и поперечного направлений сферического лепестка. Для одного и того же типа материала направление прокатки волокон связано с упругостью формования; формование лучше происходит вдоль направления прокатки волокон, в то время как вертикальное направление приводит к большей пружинистости, поэтому после первого раунда прессования используйте шаблон для проверки того, что кривизна меньше вдоль направления волокон и больше в вертикальном направлении волокон.
Во время второго раунда прессования расстояние перемещения должно быть уменьшено при движении в вертикальном направлении волокон, а точки прессования должны быть уплотнены. Как правило, после второго цикла прессования основная форма сформирована. Для проверки и повторного прессования локальных точек требуется только использование шаблона. Для локальной обрезки можно использовать выпуклую форму с меньшим радиусом для прессования точек, а освоение соответствующего давления обеспечивает отличное качество формования.
(2) Операция горячего прессования
Для повышения степени деформации материалов, снижения сопротивления деформации материалов и обеспечения качества формованных деталей часто используется горячее прессование, когда толщина листового металла превышает 12 мм, а толщина обеих сторон более 10 мм при гибке или глубокой вытяжке.
Формирование горячим прессованием - это метод, при котором заготовка для глубокой вытяжки сначала нагревается до определенной температуры, а затем выполняется глубокая вытяжка. Следует отметить, что операция горячего прессования применима как к точечному прессованию, так и к формованию всей формы для глубокой вытяжки, а также к другим видам глубокой вытяжки.
1) Температура для горячего прессования.
Температура для горячей штамповки металла должна обеспечивать относительно низкое усилие формования заготовки и в то же время быть выше температуры рекристаллизации. Это связано с тем, что рекристаллизация позволяет устранить внутренние напряжения, возникающие при формовке, и избежать закалки. В таблице 9 приведены температуры горячего прессования для некоторых стальных материалов. Для материалов, требующих отжига или закалки + отпуска, после горячей штамповки необходимо провести дополнительную термическую обработку.
Таблица 9 Температура горячей штамповки для различных сталей (Единицы измерения: ℃)
Материал | Температура горячего формования | |
Отопление | Прервать ≥ | |
Q235, 15, 20, 25 | 900~1100 | 700 |
30, 35, 40, 45, 50 | 950~1050 | 780 |
Q345, Q345R, Q390, Q420, 14MnMoV, 18MnMoNb, 18MnMoNbR, 15MnVNRE | 950~1050 | 750 |
Cr5Mo, 12CrMo, 15CrMo | 1000~1100 | 750 |
14MnMoNbB | 1000~1100 | 750 |
06Cr13, 12Cr13 | 1000~1100 | 850 |
12Cr18Ni9, 12Cr1MoV | 950~1100 | 850 |
Латунь H62, H68 | 600~700 | 400 |
Алюминий и алюминиевые сплавы 1060(L2), 5A02(LF2), 3A21(LF21) | 350~400 | 250 |
Примечание: Цифры в скобках - это обозначения старых стандартов.
Во время горячего прессования температуру нагрева листа обычно определяют по цвету пламени. В таблице 10 приведены значения цвета огня для различных температур. Следует отметить, что наблюдение цвета огня связано с яркостью окружающей среды. Цвета, перечисленные в таблице 10, определяются по наблюдению за цветом огня в темном месте, который будет отличаться при наблюдении при ярком дневном свете.
Таблица 10 Цвет стали при нагревании до различных температур (Единицы измерения: ℃)
Цвет | Температура |
Темно-коричневый | 530~580 |
Красно-коричневый | 580~650 |
Темно-красный | 650~730 |
Темно-вишневый красный | 730~770 |
Вишнево-красный | 770~800 |
Яркий вишнево-красный цвет | 800~830 |
Ярко-красный | 830~900 |
Оранжево-желтый | 900~1050 |
Темно-желтый | 1050~1150 |
Ярко-желтый | 1150~1250 |
Ослепительно белый | 1250~1300 |
Например, при наблюдении из темного места лист становится вишнево-красным при нагреве до 770-800℃. При наблюдении на очень ярком свету сталь будет иметь температуру выше 800℃, когда она станет вишнево-красной.
2) Зазор между штампами для горячего прессования.
Формы, используемые при горячей штамповке, обычно называются штампами для горячего прессования. Из-за расширения листа после нагрева его толщина увеличивается, а толщина верхней части заготовки также увеличивается из-за деформации при горячем прессовании (особенно для горячих деталей глубокой вытяжки). Поэтому зазор формы для горячего прессования должен быть больше, чем зазор формы для холодного прессования, а зазор формы для горячей глубокой вытяжки должен быть больше, чем зазор формы для горячей гибки. Конкретные значения приведены в таблице 11.
Таблица 11 Величина одностороннего зазора штампов для горячего прессования (без учета толщины материала) (Единицы измерения: мм)
Толщина материала | Пресс-форма для глубокой вытяжки | Гибочная форма | ||
Минимальный зазор | Максимальный зазор | Минимальный зазор | Максимальный зазор | |
6~8 | 0.50 | 1.00 | 0.40 | 0.80 |
10~12 | 0.80 | 1.25 | 0.60 | 1.00 |
14~16 | 1.00 | 1.50 | 0.85 | 1.25 |
18~20 | 1.40 | 1.80 | 0.05 | 1.50 |
22~24 | 1.75 | 2.20 | 1.30 | 1.75 |
25~30 | 2.00 | 2.50 | 1.50 | 2.00 |
3) Расчет размеров рабочей части для выпуклых и вогнутых пресс-форм. При проектировании пресс-форм для горячего прессования необходимо учитывать явление холодной усадки заготовки, поэтому размеры рабочей части выпуклых и вогнутых пресс-форм должны быть соответственно увеличены, чтобы компенсировать холодную усадку. Как правило, холодная усадка может быть принята равной 0,6%-0,75%.
3. Метод глубокой вытяжки параболических деталей
Характеристики деформации при глубокой вытяжке параболических деталей аналогичны характеристикам деформации полусферических деталей. На рис. 12 показана схематическая структура параболических деталей. План обработки и принципы конструирования пресс-формы следующие:
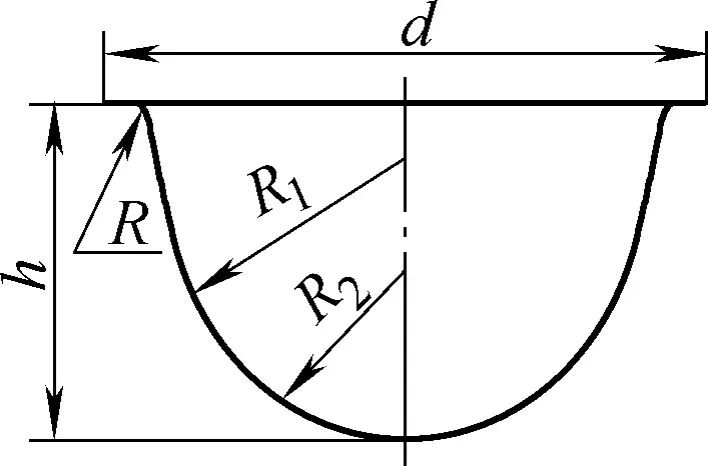
(1) Неглубокие части параболической формы (h/d<0,5)
Характеристики глубокой вытяжки и структура пресс-формы схожи с характеристиками полусферических деталей.
(2) Глубокие части параболической формы (h/d>0,5)
Требуется несколько глубоких вытяжек или обратная вытяжка. Обычно используются следующие методы:
1) Сначала нарисуйте нижнюю часть до приблизительной формы по размеру, затем на этапе перерисовки нарисуйте верхнюю часть детали, и, наконец, сформируйте всю деталь. На рис. 13 показана последовательность обработки глубокого рисунка крышки автомобильной фары.
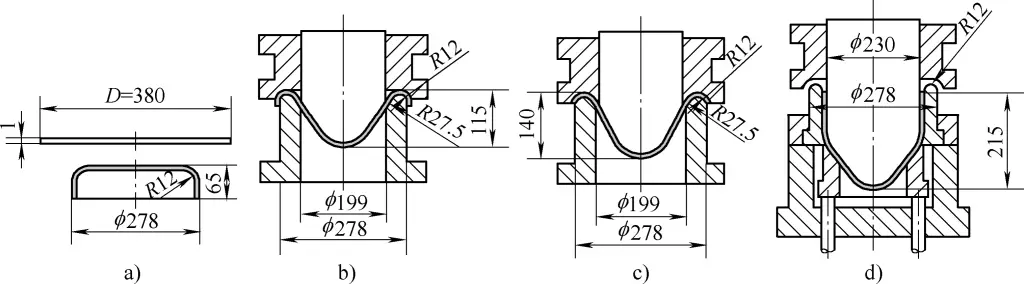
a) Процесс глубокой вытяжки 1
b) Процесс глубокой вытяжки 2
c) Процесс глубокой вытяжки 3
d) Процесс глубокой вытяжки 4
2) Используйте несколько рисунков, чтобы сначала сформировать приблизительную ступенчатую цилиндрическую форму, а затем полностью ее сформировать.
3) Используйте несколько вытяжек для уменьшения диаметра рисунка, создания круглой предварительной формы, затем выполните обратную вытяжку и окончательно сформируйте ее.
(3) Детали параболической формы, изготовленные из тонкого материала
Используйте гидравлическую или резиновую форму.
4. Операции глубокой вытяжки для деталей параболической формы
Как и в случае с полусферическими деталями, для деталей параболической формы различных форм и размеров, а также толщины материала, при глубокой вытяжке могут использоваться такие методы, как точечное прессование, горячее прессование и прямое интегральное формование, с операциями, аналогичными тем, которые выполняются для полусферических деталей.
Следует отметить, что не только полусферические и параболические детали, но и глубокая вытяжка других фасонных деталей может использовать вышеупомянутые методы формования.
V. Распространенные дефекты деталей, изготовленных методом глубокой вытяжки, и способы их устранения
К распространенным дефектам деталей, изготовленных методом глубокой вытяжки, относятся несоответствие размеров, морщины и трещины. Причины могут быть связаны с материалом для глубокой вытяжки, отладкой пресс-формы или проблемами с пресс-формой, а также с ошибками оператора. Решения должны быть основаны на тщательном анализе причин дефектов и принятии целенаправленных мер. Распространенные дефекты деталей глубокой вытяжки и меры по их устранению приведены в таблице 12.
Таблица 12 Распространенные дефекты деталей глубокой вытяжки и способы их устранения
Ситуация с качеством | Причины | Решения | |
Размеры не соответствуют требованиям | Недостаточная высота детали при глубокой вытяжке | 1) Слишком маленький размер бланка 2) Слишком большой зазор между матрицей и пуансоном 3) Слишком маленький радиус заделки пуансона | 1) Увеличьте размер заготовки 2) Замените пуансон или матрицу, отрегулируйте зазор 3) Увеличьте радиус галтели пуансона |
Слишком большая высота детали при глубокой вытяжке | 1) Слишком большой размер пустого места 2) Слишком маленький зазор между штампом и пуансоном 3) Слишком большой радиус заделки пуансона | 1) Уменьшить размер пустого места 2) Отшлифуйте пуансон или матрицу, отрегулируйте зазор 3) Уменьшить радиус галтели пуансона | |
Неравномерная толщина стенок, наклон по отношению к дну заготовки | 1) Несоответствие осей пуансона и матрицы, вызывающее неравномерный зазор 2) Несоответствие компонентов штампа и позиционирования 3) Ось пуансона не перпендикулярна верхней поверхности штампа 4) Неравномерное усилие прижима заготовки 5) Неправильная форма штампа | 1) Выровняйте пуансон или матрицу так, чтобы они были концентрическими 2) Отрегулируйте положение позиционирующего компонента 3) Настройте пуансон или матрицу 4) Отрегулируйте устройство держателя заготовок 5) Корректировка формы штампа | |
Морщины | 1) Усилие держателя заготовки слишком мало или неравномерно 2) Слишком большой зазор между пуансоном и матрицей 3) Толщина материала слишком мала, превышает допустимое нижнее предельное отклонение, или материал имеет низкую пластичность 4) Слишком большой радиус окантовки штампа 5) Кольцо держателя заготовок было рассчитано для использования, но не было применено | 1) Отрегулируйте усилие держателя заготовки 2) Отрегулируйте зазор; замените пуансон или матрицу 3) Заменить материал 4) Шлифовка матрицы или модификация устройства для удержания заготовок 5) Используйте пустое кольцо-держатель | |
Трещины или разрывы | 1) Низкое качество материала (шероховатость поверхности, неоднородная микроструктура, поверхностные царапины, потертости и т.д.) 2) Слишком большое или неравномерное усилие прижима заготовки (материал становится тоньше, появляются вязкие трещины) 3) Неровная поверхность штампа, износ или трещины 4) Радиус галтели слишком мал (материал становится очень тонким). 5) Зазор между пуансоном и матрицей слишком мала (материал становится очень тонким) 6) Необоснованные технологические требования (например, смазка, отжиг и т.д.). 7) Слишком малый радиус заделки пуансона 8) Кромка заготовки не соответствует требованиям, с большими заусенцами 9) Слишком большой размер заготовки, неправильная форма 10) Пуансон и матрица не концентричны и не параллельны 11) Коэффициент прорисовки слишком мал | 1) Замените подходящим материалом 2) Отрегулируйте усилие держателя заготовки 3) Шлифовка или замена матрицы 4) Увеличьте радиус окантовки штампа 5) Отшлифуйте пуансон или матрицу и отрегулируйте зазор 6) Изменение спецификаций процесса 7) Пунш для измельчения 8) Отрегулируйте заготовительную матрицу, удалите заусенцы 9) Изменение размера и формы заготовки 10) Отрегулируйте пуансон и матрицу 11) Увеличить количество процессов и регулировать деформацию в каждом процессе | |
Царапины на поверхности | 1) Слишком маленький или неравномерный зазор 2) Неровная галтель 3) Рабочая поверхность пуансона или поверхность материала не очищены 4) Низкая твердость пуансона и матрицы, прилипание металла к матрице 5) Неправильная смазка | 1) Отшлифуйте зазор между пуансоном и матрицей 2) Шлифовка филе 3) Очистите поверхность 4) Увеличить твердость пуансона и матрицы или заменить матрицу 5) Используйте разумный смазочный материал и метод смазки | |
Форма заготовки неровная (например, впадина на дне или скрученная форма, дно детали неровное) | 1) Отсутствие вентиляционных отверстий на пуансоне 2) Пружинящий эффект материала 3) Слишком большой зазор между пуансоном и матрицей 4) Степень окончательной деформации прямоугольных деталей слишком велика 5) Черновая заготовка неровная, площадь контакта между штоком выбрасывателя и деталью слишком мала, или усилие буферной пружины недостаточно | 1) Создайте вентиляционные отверстия или добавьте процесс формования 2) Добавьте процесс формирования 3) Отрегулируйте зазор 4) Регулируйте степень деформации в процессе или добавляйте процесс формования 5) Сплющивание заготовки, улучшение выталкивающего устройства |