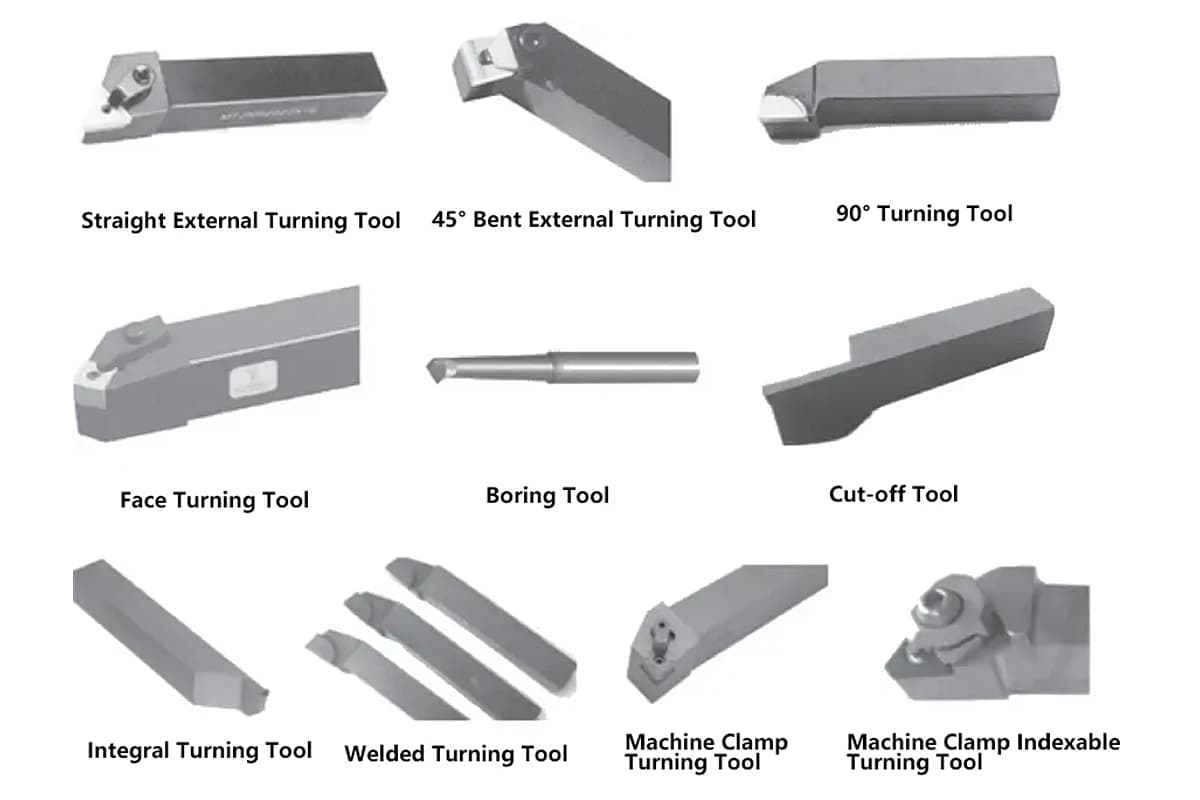
I. Токарные приспособления
1. Типы и характеристики приспособлений для токарных станков
Токарный станок в основном используется для обработки внутренних и наружных цилиндрических поверхностей, конических поверхностей, вращающихся образующих, резьбовых и торцевых поверхностей деталей. Исходя из этих характеристик обработки и положения приспособления на станке, токарные приспособления можно разделить на следующие два основных типа:
(1) Приспособления, установленные на шпинделе токарного станка
В этом типе приспособлений, помимо различных патронов, торцевых планок, центров и других общих приспособлений или принадлежностей для станков, могут быть разработаны различные оправки или другие специальные приспособления в соответствии с потребностями обработки. Во время обработки приспособление вращается вместе со шпинделем токарного станка, а инструмент совершает движение подачи.
(2) Приспособления, установленные на седле токарного станка
Для некоторых заготовок неправильной формы и больших размеров приспособление часто устанавливается на седло токарного станка. Инструмент устанавливается на шпиндель токарного станка для вращательного движения, а приспособление выполняет движение подачи. В этом разделе представлены наиболее распространенные специальные приспособления для токарных станков, устанавливаемые на шпиндель токарного станка.
2. Типичные примеры специальных приспособлений для токарных станков
В производстве часто встречаются ситуации, когда цилиндрические поверхности и торцы деталей, таких как корпуса, кронштейны, рычаги и шарниры, являются обработанный на токарном станке. Такие детали часто имеют сложную форму, что затрудняет прямой зажим заготовки трехкулачковым самоцентрирующимся патроном. В таких случаях необходимо разрабатывать специальные приспособления для токарных станков. Ниже представлены несколько типичных приспособлений для токарных станков.
(1) Крепление из углового железа
На рисунке 1 показано приспособление для токарного станка из углового железа. Заготовка располагается на наклонной опорной плите приспособления, на цилиндрическом и алмазном штифтах, используя одну грань и два отверстия в качестве опорных точек, и зажимается двумя прижимными пластинами в форме крюка.
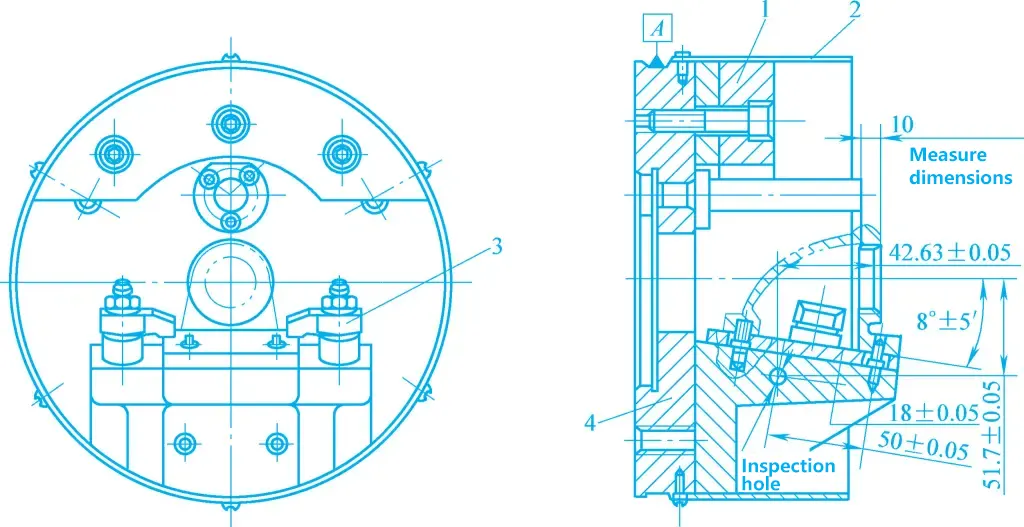
1-Балансировочный блок
2-Защитная крышка
Нажимной диск в форме крюка
4-Корпус светильника
Обрабатываемые поверхности представляют собой отверстия и торцы. Для облегчения контроля размеров обработанной торцевой поверхности и угла между обработанным отверстием и позиционирующей базовой поверхностью во время обработки рядом с обрабатываемой поверхностью проектируются измерительная базовая поверхность и технологическое отверстие. Контрольная окружность A на корпусе приспособления 4 является окружностью выравнивания.
(2) Крепление для лицевой панели
На рисунке 2 показана технологическая схема изготовления корпуса шестеренчатого насоса. Внешняя окружность D и торцевая поверхность A заготовки были обработаны. Обрабатываемые поверхности - это два отверстия диаметром Φ35 мм, торцевая поверхность T и нижняя поверхность отверстия B. При этом должны быть соблюдены соответствующие технические требования, указанные в чертеже детали. Точность диаметра двух отверстий Φ35 мм в основном зависит от правильности метода обработки, в то время как другие технические требования обеспечиваются приспособлением.
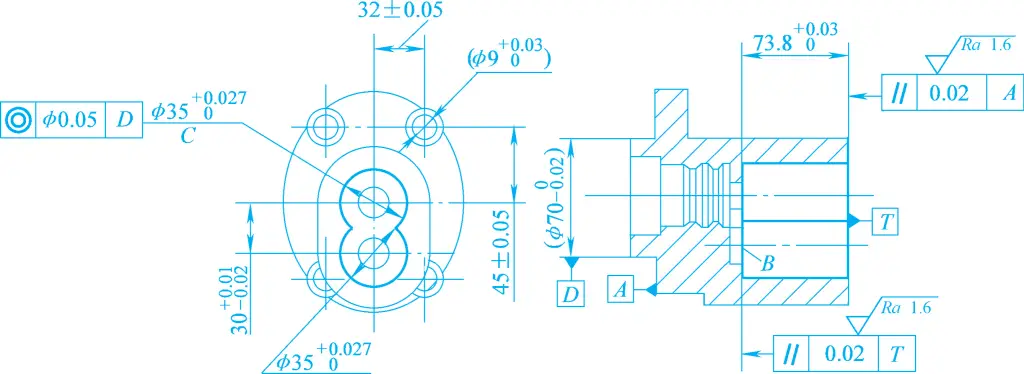
На рисунке 3 показано специальное приспособление, используемое для обработки двух отверстий диаметром Φ35 мм в корпусе шестеренчатого насоса. Заготовка позиционируется с использованием торцевой поверхности A, внешней круговой поверхности Φ70 мм и внутреннего кругового отверстия Φ9 мм в качестве опорных точек, и зажимается двумя наборами спиральных прижимных пластин 5 на поверхности N поворотного стола 2, круглого отверстия Φ70 мм и обрезанного штифта 4.
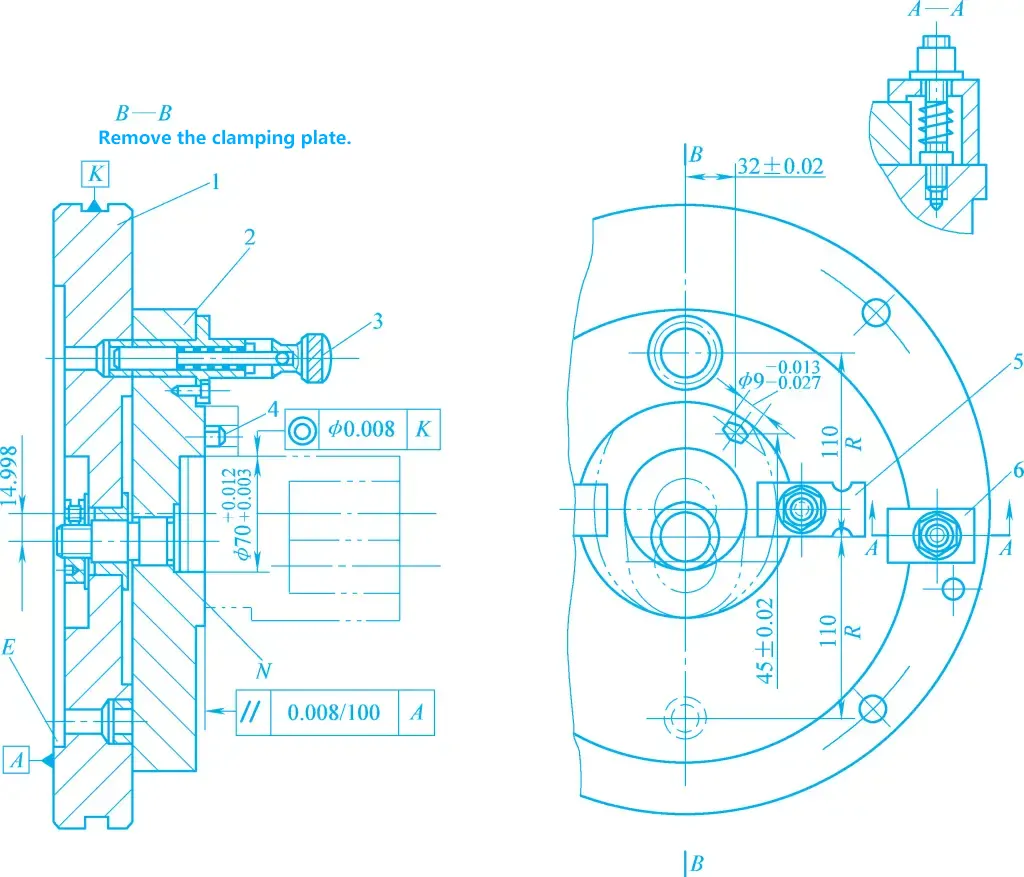
1-Корпус светильника
2-поворотный стол
3-Выравнивающий штифт
4-Триммированный штифт
5, 6Плиты давления
Поворотный стол 2 зажимается на корпусе приспособления 1 двумя наборами спиральных прижимных пластин 6. После обработки одного из отверстий Φ35 мм выравнивающий штифт 3 вытаскивается, и два комплекта спиральных прижимных пластин 6 ослабляются. Поворотный стол вместе с заготовкой поворачивается на 180°, и центровочный штифт под действием силы пружины вставляется в другое индексирующее отверстие на корпусе приспособления. После фиксации поворотного стола можно обрабатывать второе отверстие диаметром Φ35 мм.
Специальное приспособление использует выемку E на корпусе приспособления для соединения со шпинделем токарного станка через фланец на переходной плите. При установке приспособления выравнивающий круг K (представляющий собой ось вращения приспособления) используется для выравнивания соосности приспособления со шпинделем токарного станка.
(3) Центрирующее зажимное приспособление
Для вращающихся заготовок или заготовок, позиционируемых вращающейся поверхностью, можно использовать центрирующие зажимные приспособления. К распространенным типам относятся пружинные втулки и приспособления из жидкого пластика. В приспособлении, показанном на рис. 4, заготовка позиционируется и зажимается внутренним отверстием с помощью приспособления из жидкого пластика.
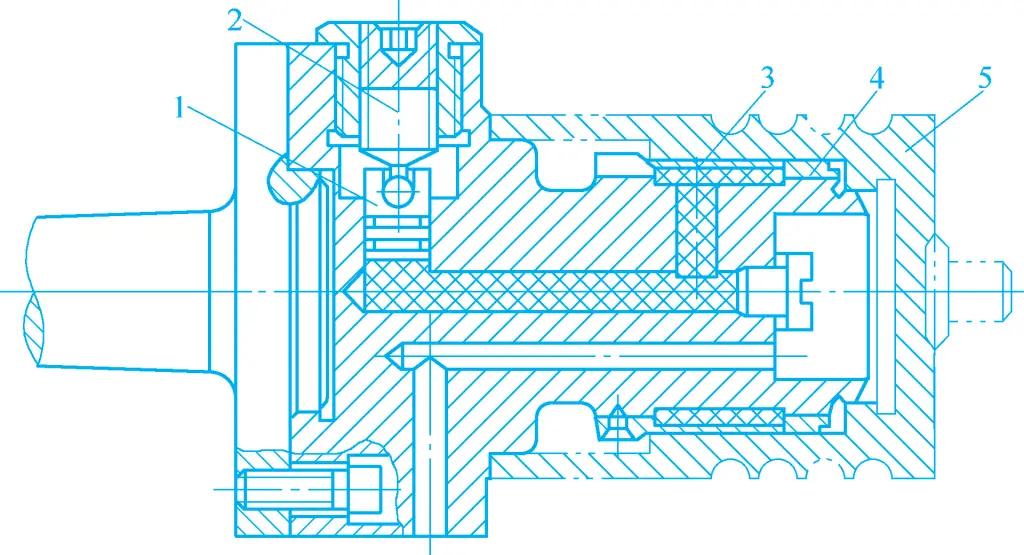
1-Сдвижная колонна
2-Компрессионный винт
3-жидкий пластик
Позиционная втулка с 4 тонкими стенками
5-заготовка
Заготовка помещается на позиционирующий цилиндр, расположенный в осевом направлении торцевой поверхностью. При вращении нажимного винта 2 подвижная колонна 1 и жидкий пластик 3 вызывают деформацию тонкостенной позиционирующей втулки 4, тем самым центрируя и зажимая заготовку 5.
(4) Модульное крепление
Модульное крепление - это специальная крепление в сборе из предварительно изготовленных стандартных компонентов крепежа в соответствии с разработанной схемой позиционирования и зажима. Он сочетает в себе преимущества специальных приспособлений с преимуществами стандартизации и обобщения. После смены продукции компоненты приспособления можно разобрать, очистить и убрать на хранение, избежав образования отходов. Приспособление подходит для пробного производства новых изделий и мелкосерийного производства нескольких сортов.
Он обладает уникальными преимуществами при производстве механических изделий на современных предприятиях, которые широко используют станок с ЧПУ инструменты и применять технологии CAD/CAM/CAPP. На рисунке 5 показано типичное модульное приспособление для токарного станка. Заготовка позиционируется с помощью обработанной нижней поверхности и двух отверстий для позиционирования, а также зажимается двумя прижимными пластинами. Корпус приспособления, позиционирующие штифты, прижимные пластины и основание являются стандартными компонентами.
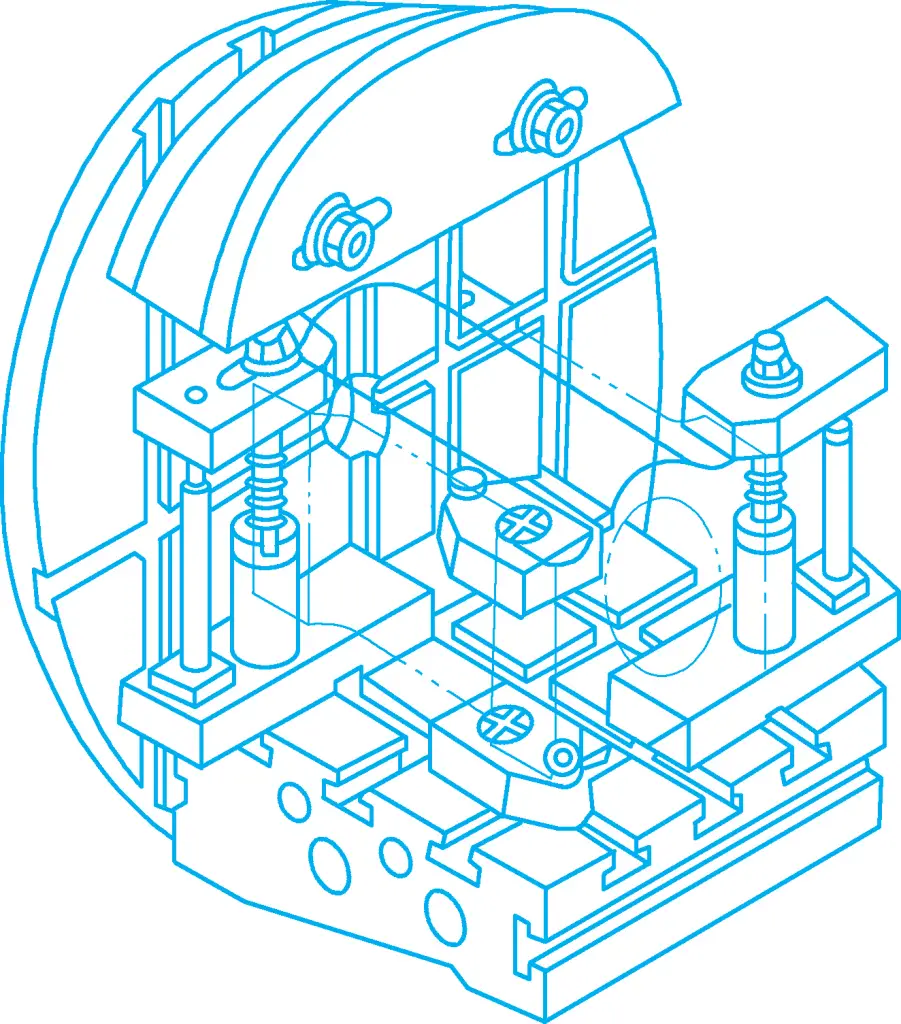
3. Конструктивные характеристики приспособлений для токарных станков
(1) Устройство позиционирования
При обработке вращающихся поверхностей на токарном станке ось вращающейся поверхности заготовки должна совпадать с осью вращения шпинделя токарного станка. Это должно быть обеспечено конструкцией и расположением позиционирующего устройства на приспособлении.
(2) Зажимное устройство
Поскольку заготовка и приспособление вращаются вместе со шпинделем во время точения, в процессе обработки на приспособление действует центробежная сила в дополнение к моменту резания. Чем выше скорость вращения, тем больше центробежная сила, что может повлиять на зажимной эффект зажимного механизма.
Кроме того, положение опорной точки заготовки относительно направления силы резания и силы тяжести меняется. Поэтому сила зажима, создаваемая зажимным механизмом, должна быть достаточной, а самоблокировка должна быть хорошей, чтобы предотвратить отсоединение заготовки от позиционирующих элементов во время обработки.
(3) Соединение между токарным приспособлением и шпинделем станка
Ось вращения приспособления должна иметь максимально возможную точность соосности с осью шпинделя токарного станка. В зависимости от радиального размера приспособления для токарного станка, как правило, существует два варианта методы соединения со шпинделем станка:
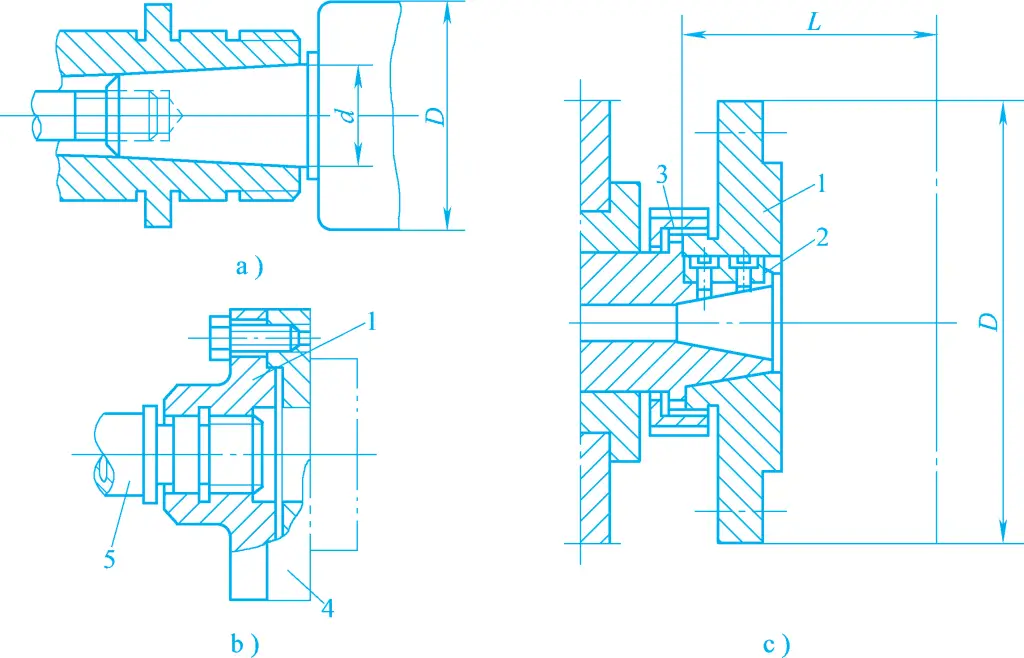
1-переходная пластина
2-плоский ключ
3 гайка
4-Фиксатор
5-шпиндель
1) Для небольших приспособлений с радиальными размерами D<140 мм или D<(2~3)d структура соединения показана на рис. 6a. Обычно они устанавливаются в коническое отверстие шпинделя токарного станка через конический хвостовик и затягиваются болтом. Этот метод соединения имеет высокую точность центрирования.
2) Для приспособлений с большими радиальными размерами используется переходная плита для соединения с передним концом шпинделя токарного станка. Конструкция переходной плиты показана на рисунках 6b и 6c. Один конец переходной плиты соединяется со шпинделем станка, причем форма сопрягаемой поверхности зависит от конструкции переднего конца шпинделя. Другой конец обычно имеет фланец, который сопрягается с позиционирующим буртиком на корпусе приспособления, обеспечивая центрирование приспособления на шпинделе.
На корпусе токарного приспособления, как правило, имеются центровочные отверстия или центровочные окружности, как показано на рис. 1 и 3. Центровочные отверстия или окружности служат для обеспечения соосности при установке токарного приспособления на шпиндель токарного станка, а также в качестве контрольных точек при изготовлении и сборке токарного приспособления. Кроме того, они часто являются технологической привязкой при обработке самого корпуса приспособления.
Приспособление для токарного станка должно устранить проблему вращательного дисбаланса. Одним из способов балансировки является установка балансировочного блока (противовеса) на более легкой стороне, другим - обработка отверстий для уменьшения веса на более тяжелой стороне, или комбинация обоих способов. Желательно, чтобы положение и вес балансировочного блока можно было регулировать.
Для обеспечения безопасной работы приспособление должно по возможности не иметь острых углов или деталей, выступающих за пределы кругового контура корпуса приспособления. При необходимости следует установить защитную крышку. Кроме того, самоблокировка зажимного устройства должна быть надежной, чтобы предотвратить ослабление во время вращения, что может привести к вылету заготовки.
II. Приспособления для фрезерных станков
1. Типы и характеристики приспособлений для фрезерных станков
В соответствии с различными способами подачи, приспособления для фрезерных станков делятся на линейные, круговые и шаблонные. В данном разделе представлены в основном первые два типа.
(1) Приспособления для фрезерных станков с линейной подачей
Как правило, такие приспособления устанавливаются на рабочий стол фрезерного станка, и в процессе обработки приспособление линейно перемещается вместе с рабочим столом. В зависимости от количества заготовок, зажимаемых за один раз, их можно разделить на приспособления для фрезерных станков с одной деталью и приспособления для фрезерных станков с несколькими деталями.
Однокомпонентные приспособления чаще всего используются в мелкосерийном производстве, в то время как многокомпонентные приспособления широко применяются в массовом производстве деталей малого и среднего размера. На рис. 8 показано приспособление для фрезерования двойных пазов на центральной втулке, показанной на рис. 7.

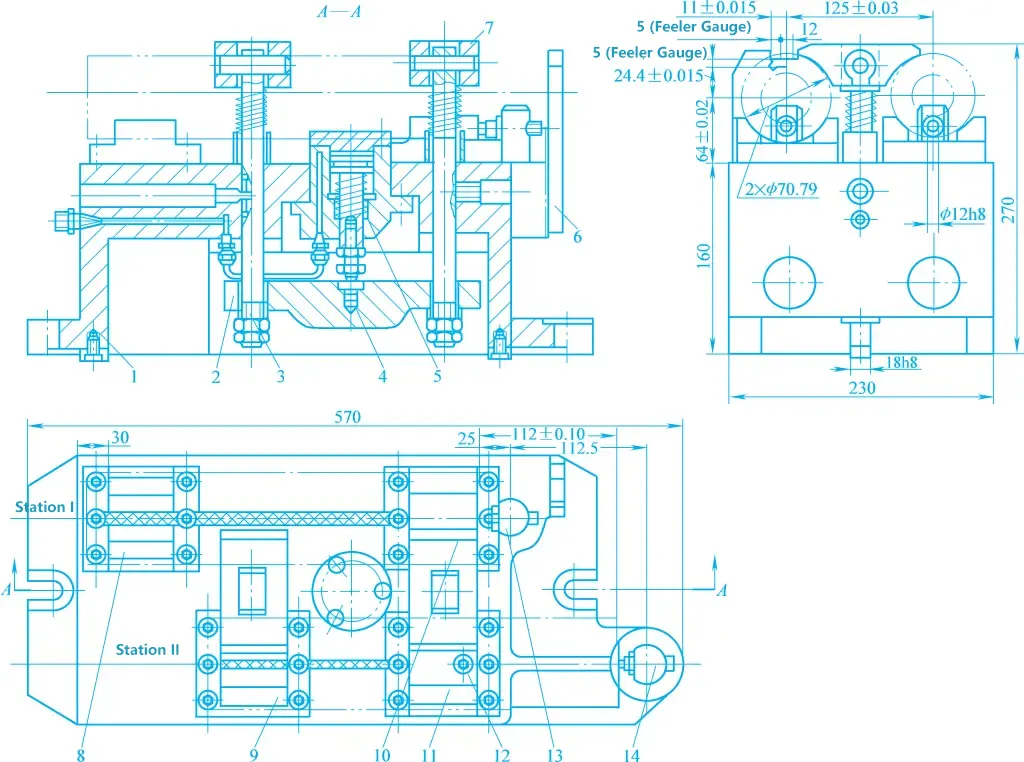
1-Корпус светильника
2-плавающий рычаг
3-винтовой стержень
4-Опорный штифт
5-Гидравлический цилиндр
Блок из 6 инструментов
7-Пластина давления
8, 9, 10, 11-V-блоки
12-Антиротационный штифт
13, 14 - Упорные штифты
(2) Приспособления для фрезерных станков с круговой подачей
Приспособления для фрезерных станков с круговой подачей чаще всего используются на фрезерных станках с поворотным столом. При использовании на общих фрезерных станках к ним следует добавить поворотный стол, как показано на рис. 9.
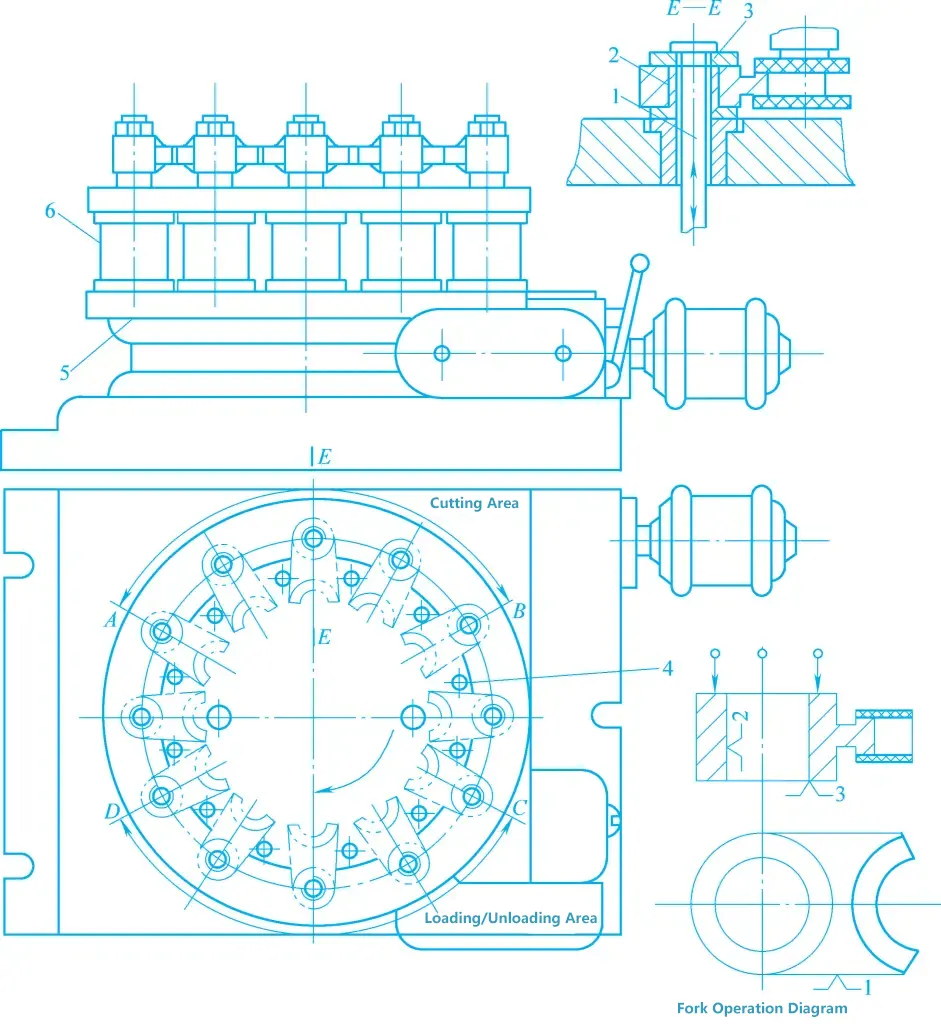
1-Протяжка
2-позиционный штифт
3-секционная стиральная машина
4-стопорный штырь
5-поворотный стол
6-Гидравлический цилиндр
Круговая подача происходит непрерывно, что позволяет загружать и выгружать заготовки без остановки станка, обеспечивая тем самым высокую производительность. Он подходит для массового производства деталей малого и среднего размера, однако особое внимание следует уделить безопасности эксплуатации и трудоемкости работы оператора.
2. Типичные примеры специальных приспособлений для фрезерных станков
На рисунке 7 показана технологическая схема фрезерования шпоночных пазов и масляных канавок на втулке задней бабки токарного станка. Обработаны внутренняя и внешняя окружности и обе торцевые поверхности заготовки. В этом процессе шпоночные пазы и масляные канавки обрабатываются одновременно двумя фрезами. На рис. 8 показано приспособление, используемое в серийном производстве, - типичное приспособление для фрезерного станка с линейной подачей.
На участке I для фрезерования шпоночного паза используется трехсторонняя кромочная фреза. Заготовка располагается на V-образных блоках 8, 10 и упорном пальце 13 по внешней окружности и торцевой поверхности, ограничивая пять степеней свободы. На участке II для фрезерования масляной канавки используется дуговая фреза. Заготовка позиционируется по внешней окружности, уже обработанному шпоночному пазу и торцевой поверхности, используя V-образные блоки 9, 11, противовращающийся палец 12 и упорный палец 14 для полного позиционирования.
Поскольку длина шпоночного паза и масляной канавки различна, для одновременной обработки положения двух упорных штифтов могут быть расположены в шахматном порядке и сконструированы так, чтобы их можно было легко отрегулировать.
Для зажима используется гидравлический привод. Когда масло под давлением поступает в верхнюю камеру гидроцилиндра 5 из системы масляного контура, оно толкает поршень вниз, заставляя шарнирную нажимную плиту 7 опускаться через опорный палец 4, плавающий рычаг 2 и винт 3, чтобы зажать заготовку. Чтобы прижимная пластина равномерно зажимала заготовку, во всех частях механизма зажима шарнира используются плавающие соединения.
Приспособление для фрезерования с круговой подачей, показанное на рис. 9, используется для непрерывного фрезерования верхней и нижней торцевых поверхностей вилки на вертикально-фрезерном станке. Заготовка устанавливается круглым отверстием, торцом и боковой поверхностью на фиксирующий штифт 2 с бобышкой и упорный штифт 4 и зажимается тягой 1, приводимой в движение гидроцилиндром 6 через разрезную шайбу 3.
Приспособление одновременно зажимает 12 заготовок, а рабочий стол приводится во вращение двигателем через червячный механизм. Сектор AB - это зона резки, а сектор CD - зона загрузки и выгрузки. Когда заготовка поворачивается вместе с рабочим столом в зону AB, гидравлический цилиндр 6 приводит тягу 1 вниз, чтобы зажать заготовку; когда заготовка поворачивается вместе с рабочим столом в зону CD, гидравлический цилиндр 6 приводит тягу 1 вверх, чтобы освободить заготовку.
В процессе резки и загрузки/выгрузки заготовки рабочий стол непрерывно вращается без остановки. Таким образом, время обработки и вспомогательное время на загрузку/выгрузку заготовки перекрываются, что обеспечивает высокую производительность.
3. Конструктивные характеристики приспособлений для фрезерных станков
(1) Ключ для поиска
Приспособления для фрезерных станков обычно имеют фиксирующие ключи, установленные в продольных пазах на нижней поверхности корпуса приспособления. Обычно их используется две, расположенные на максимально возможном расстоянии друг от друга. В небольших приспособлениях может также использоваться один длинный ключ прямоугольного сечения.
Фиксирующий ключ устанавливается в Т-образный паз рабочего стола фрезерного станка. Его основная функция - обеспечение правильного позиционирования между приспособлением и рабочим столом фрезерного станка. Он также может воспринимать часть крутящего момента при резании, снижая нагрузку на болты, соединяющие корпус приспособления с рабочим столом, и повышая устойчивость приспособления во время обработки.
Существует два типа ключей: прямоугольные и цилиндрические. Обычные прямоугольные ключи имеют две конструкции, как показано на рис. 10a и 10b. Первый используется, когда требования к точности ориентации приспособления невысоки. Чтобы повысить точность ориентации приспособления, при установке приспособления одна сторона фиксирующего ключа должна плотно прилегать к одной стороне Т-образного паза рабочего стола.
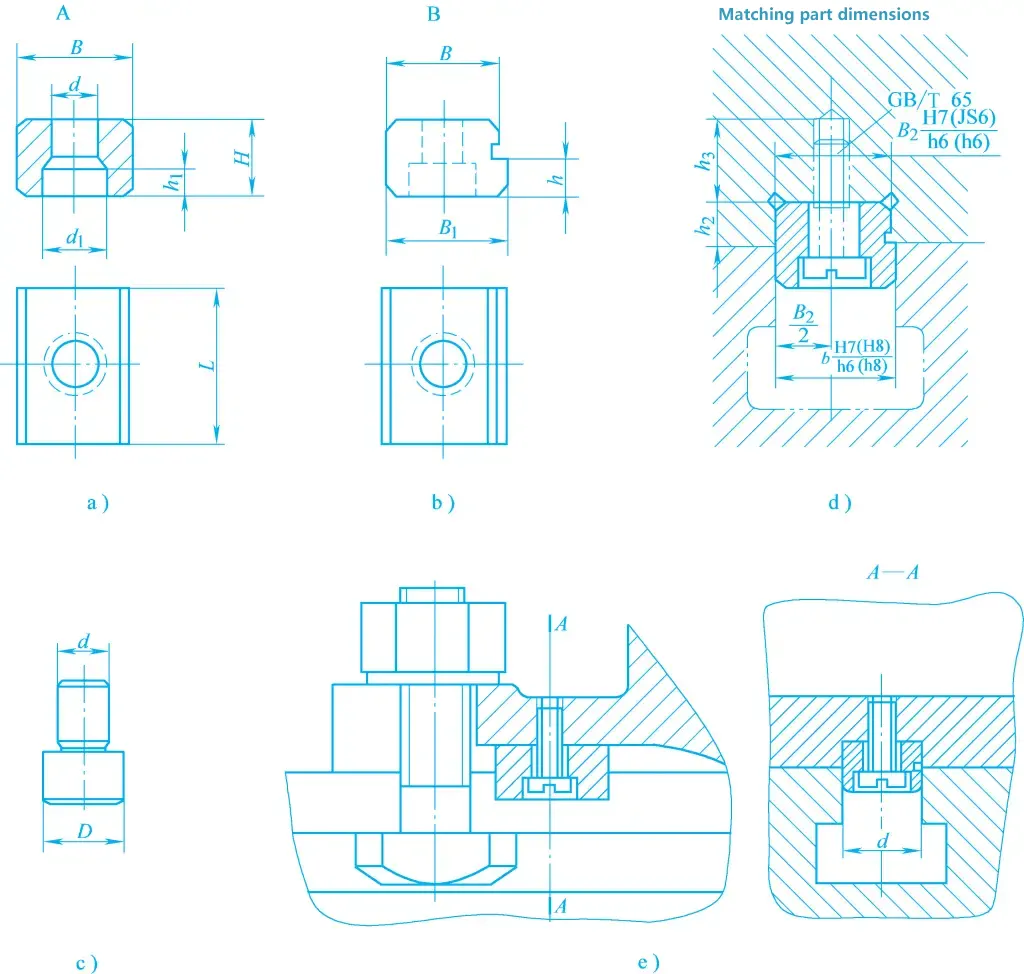
В связи с трудностями обеспечения точности ключевых пазов на корпусе приспособления в последние годы появились цилиндрические фиксирующие ключи, как показано на рис. 10c. При использовании этого типа ключа два отверстия на приспособлении обрабатываются на координатно-расточном станке, что позволяет достичь высокой точности позиционирования и упростить процесс изготовления приспособления.
Однако цилиндрические фиксирующие ключи подвержены износу и не находят широкого применения в производстве. На рис. 10d и 10e показана установка фиксирующих ключей на корпус приспособления и установка приспособлений для фрезерного станка на рабочий стол.
Для больших приспособлений или когда требуется высокая точность ориентации, фиксирующие ключи не подходят. Вместо этого на корпусе приспособления обрабатывается узкая длинная плоскость в качестве опорной поверхности для выравнивания, чтобы скорректировать положение установки приспособления, как показано на рис. 11.
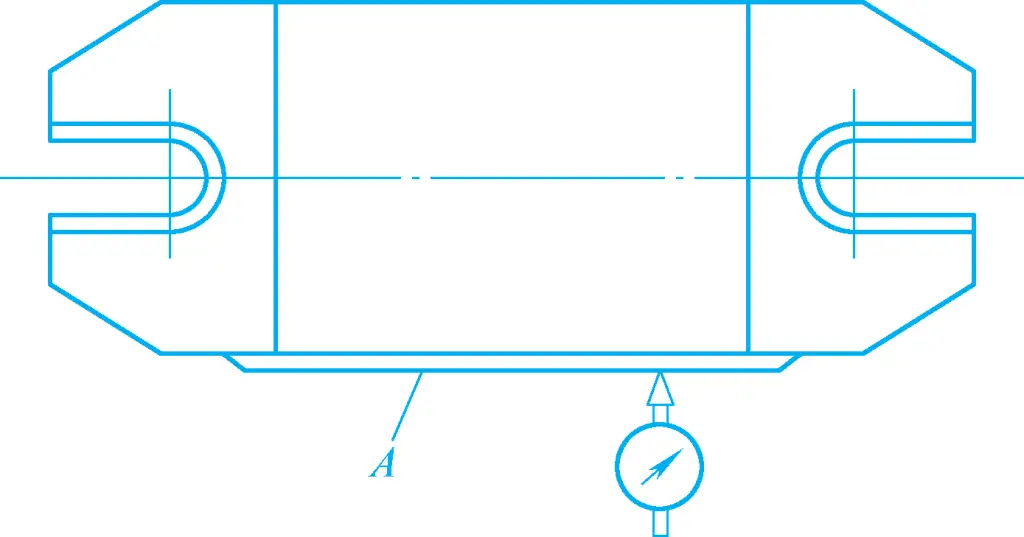
(2) Устройство для установки инструмента
Приспособления для фрезерных станков обычно имеют устройство для установки инструмента, состоящее из блока для установки инструмента и щупа. Блок для установки инструмента используется для определения относительного положения приспособления и инструмента. Щуп используется для предотвращения повреждения режущей кромки и блока при установке инструмента. В процессе работы он вставляется между инструментом и блоком, и окончательное положение инструмента относительно приспособления определяется по плотности контакта.
На рисунке 12 показаны несколько распространенных блоков для настройки инструмента. Круглый блок настройки инструмента, показанный на рисунке 12a, используется для настройки инструмента при обработке одной плоскости. Прямоугольный блок настройки инструмента, показанный на рисунке 12b, используется для настройки инструмента при обработке двух взаимно перпендикулярных плоскостей или пазов. Блоки настройки инструмента, показанные на рисунках 12c и 12d, используются для настройки инструмента при обработке формообразующих поверхностей формообразующими фрезами.
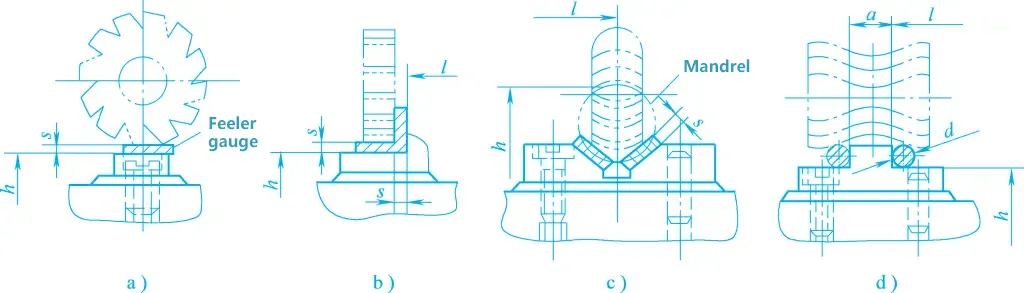
Блоки для настройки инструмента обычно крепятся к корпусу приспособления с помощью двух штифтов и винтов. Их положение должно облегчать настройку инструмента и не препятствовать загрузке и выгрузке или обработке заготовки. При использовании приспособления для настройки инструмента точность не должна превышать IT8. Если требуется более высокая точность обработки или неудобно устанавливать блок для настройки инструмента, можно использовать такие методы, как пробное резание, настройка инструмента по стандартной детали или использование циферблатного индикатора для выравнивания положения инструмента.
(3) Корпус приспособления
Конструктивная форма корпуса приспособления во многом зависит от структуры и расположения фиксирующих элементов, зажимных устройств и других компонентов. Чтобы сделать конструкцию приспособления компактной и обеспечить устойчивость установки приспособления на станке, обрабатываемая поверхность заготовки должна быть как можно ближе к поверхности рабочего стола, чтобы снизить центр тяжести приспособления, как показано на рис. 13a.
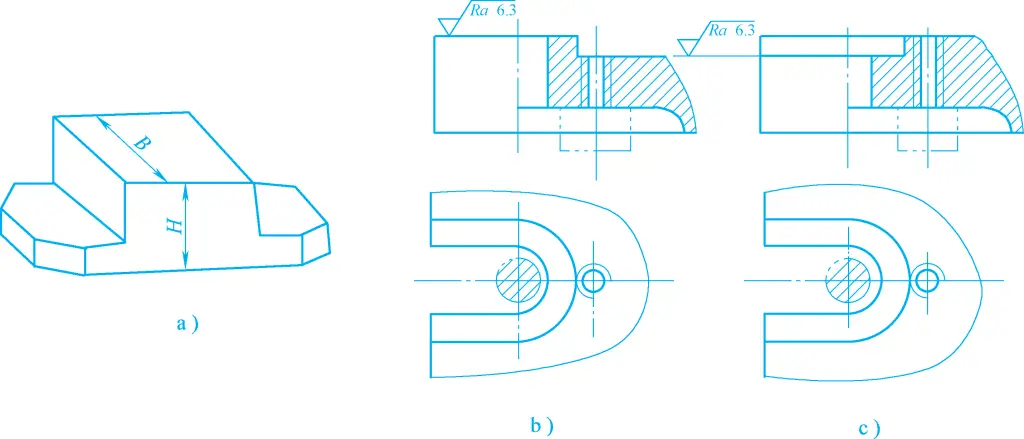
Кроме того, корпус крепежа должен обладать достаточной прочностью и жесткостью, а посадочные места для ушек должны быть расположены разумно. Обычные конструкции посадочных мест для ушек показаны на рисунках 13b и 13c. Если корпус приспособления относительно широкий, два гнезда для ушек могут быть расположены на одной стороне, а центральное расстояние между двумя гнездами для ушек должно соответствовать центральному расстоянию между двумя Т-образными пазами на рабочем столе фрезерного станка. Для тяжелых приспособлений для фрезерных станков на корпусе приспособления должны быть установлены подъемные кольца для удобства перемещения.
III. Приспособления для сверлильного пресса
1. Типы и характеристики сверлильных станков
Сверлильные приспособления - это приспособления, используемые на сверлильных станках для сверления, развертывания и растачивания. Эти приспособления оснащены шаблонами и втулками для сверления, направляющими инструмент через втулку, поэтому их принято называть сверлильными приспособлениями. В зависимости от требований к использованию, их конструктивные формы можно разделить на неподвижные, поворотные, откидные, с накладной плитой и с подвижной колонной.
(1) Стационарный сверлильный станок
Особенностью неподвижной сверлильной оснастки является то, что ее положение остается неизменным в процессе обработки, что обеспечивает высокую точность обработки. Обычно сверлильная оснастка крепится к рабочему столу сверлильного станка с помощью Т-образных болтов через посадочные отверстия для ушек на корпусе оснастки или может быть прижата непосредственно к рабочему столу с помощью болтов и прижимных пластин. Стационарные сверлильные приспособления в основном используются для обработки больших одиночных отверстий на вертикально-сверлильных станках или систем параллельных отверстий на радиально-сверлильных станках.
При использовании неподвижной сверлильной оснастки для обработки параллельных систем отверстий на вертикально-сверлильном станке необходимо установить на шпиндель станка многошпиндельную приводную головку. При установке сверлильной оснастки на вертикально-сверлильном станке размерный инструмент (или оправка для высокой точности), закрепленный на шпинделе, обычно вставляется во втулку для определения положения сверлильной оснастки, которая затем фиксируется.
На рисунке 14a показано неподвижное сверлильное приспособление для обработки отверстия диаметром Φ10 мм в рычаге. Эта оснастка крепится к рабочему столу сверлильного станка с помощью болтов и прижимных пластин.
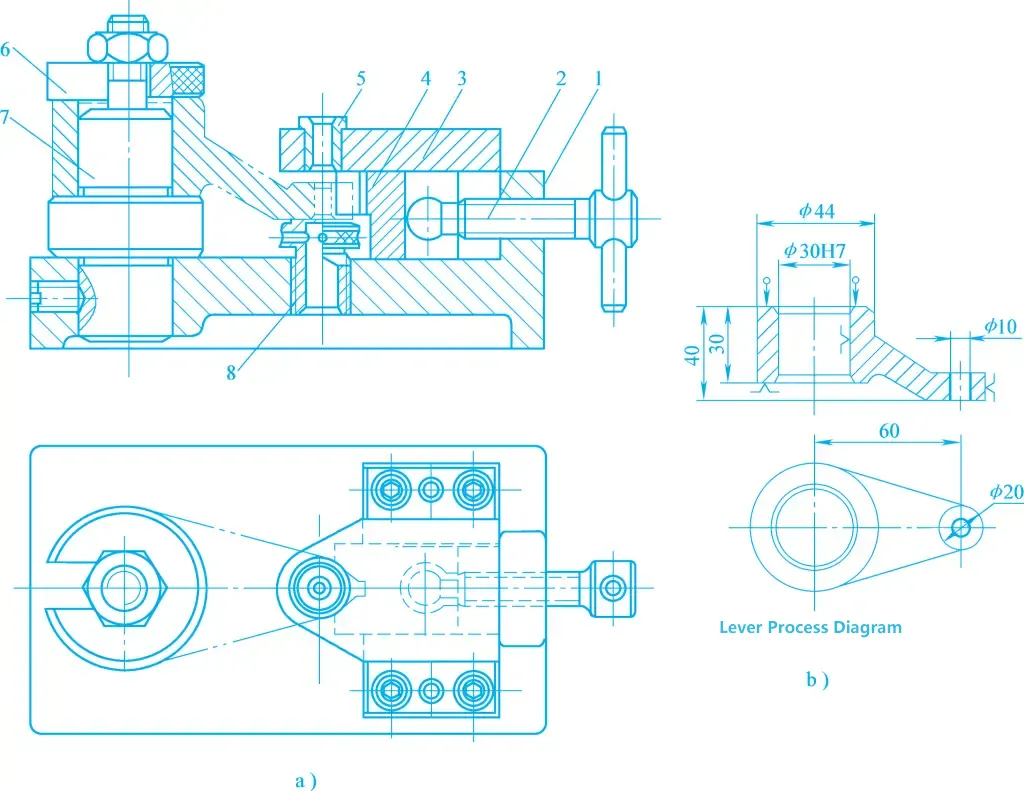
1-Джиг Корпус
2-Прижимной винт фиксированной рукоятки
3-Drill Template
4-подвижный V-образный блок
5-Сверлильная втулка
6-секционная стиральная машина
7-Позиционный штифт
8-Вспомогательная поддержка
Заготовка размещается на позиционирующем штифте 7 с помощью отверстия Φ30H7 и большой торцевой поверхности, а свобода вращения заготовки ограничивается внешней окружностью Φ20 мм через подвижный V-образный блок 4. Заготовка зажимается с помощью винтового зажимного механизма и разъемной шайбы, при этом нижняя торцевая поверхность Φ20 мм внешней окружности поддерживается вспомогательной опорой 8. Сверло направляется через втулку 5 для обработки отверстия диаметром Φ10 мм.
Если такие сверлильные приспособления не закреплены на рабочем столе сверлильного станка, они превращаются в мобильные сверлильные приспособления, которые можно использовать на одношпиндельных вертикально-сверлильных станках для последовательного сверления нескольких параллельных небольших отверстий на одной и той же поверхности заготовки.
(2) Вращающаяся дрель
Ротационные сверлильные приспособления получили свое название благодаря наличию вращающихся индексирующих устройств или использованию с общими поворотными столами. Они используются для обработки параллельных систем отверстий на одной окружности или радиальных систем отверстий, распределенных по окружности. Поскольку конструкция общих поворотных столов стандартизирована, в большинстве случаев для их использования требуется разработка только специальных рабочих приспособлений. Специальные сверлильные приспособления со специальными устройствами для индексации вращательного движения разрабатываются только в особых случаях.
На рисунке 15a показано приспособление для обработки 6×Φ10 мм отверстий, равномерно распределенных по окружности Φ70 мм. Заготовка позиционируется с помощью нижней поверхности, отверстия Φ40H7 и боковой поверхности шпоночного паза на позиционирующем диске 4, позиционирующем штифте 3 и ключе, и зажимается с помощью гайки и разрезной шайбы.
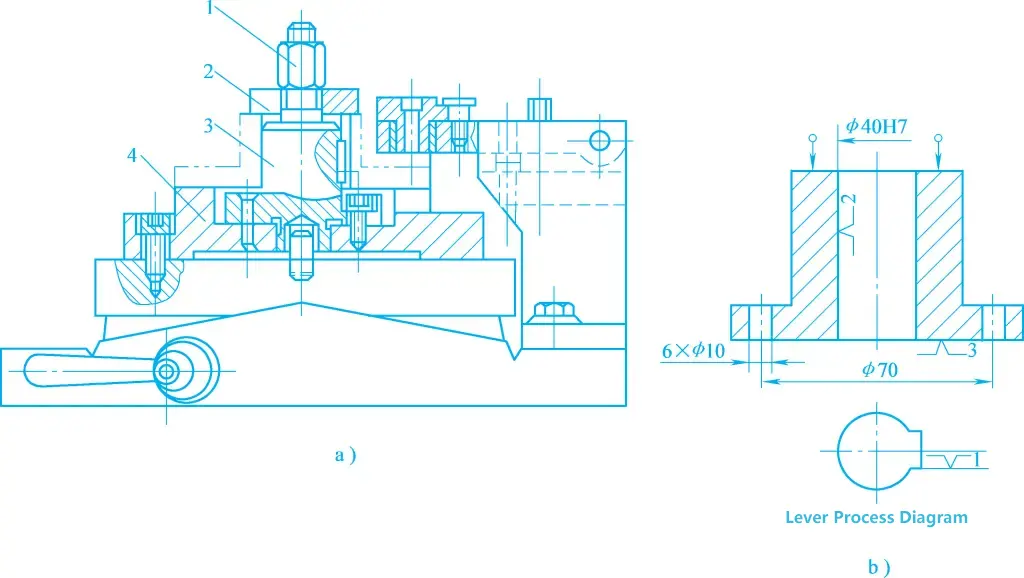
1-зажимная гайка
2-секционная стиральная машина
3-комбинированный штифт для позиционирования
4-позиционный диск
Приспособление устанавливается на позиционирующий штифт в центре поворотного стола через отверстие во втулке на позиционирующем диске, а затем закрепляется винтами. Кроме того, на поворотном столе устанавливается шарнирный шаблон для сверления, и отверстия 6xΦ10 мм последовательно обрабатываются с помощью вращающегося поворотного стола.
(3) Сверлильный станок перекидного типа
Этот тип сверлильного станка в основном используется для обработки небольших отверстий, расположенных на разных поверхностях небольших заготовок. Его конструкция проста, а во время использования требуется ручное переворачивание. То есть, после обработки отверстий на одной поверхности, заготовка вместе с приспособлением переворачивается и устанавливается, а затем обрабатываются отверстия на других поверхностях.
Поскольку приспособление необходимо часто переворачивать во время обработки и оно не закреплено на столе сверлильного станка, вес приспособления вместе с заготовкой не должен быть слишком большим (обычно не более 8-10 кг). Обрабатываемые отверстия обычно не превышают Φ10 мм, поэтому следует обратить внимание на устойчивость приспособления после переворачивания и удаления стружки.
На рис. 16 показан перекидной сверлильный станок для обработки четырех радиальных малых отверстий на цилиндрической поверхности втулки. Заготовка устанавливается на фиксирующий штифт 1 торцом и отверстием и зажимается гайкой 3 и разрезной шайбой 2. После сверления одного набора отверстий сверлильный станок переворачивают на 60° для сверления другого набора отверстий.
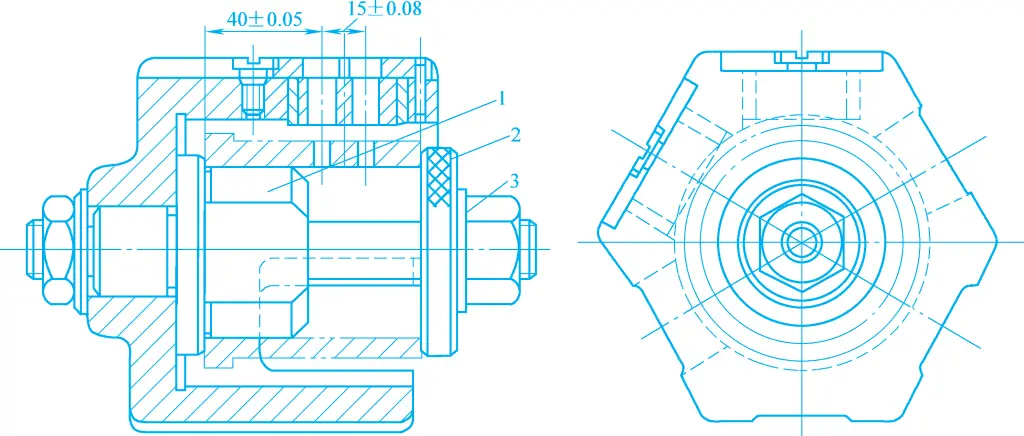
1-Соединительный штифт
2-шайба
3 гайка
(4) Приспособление для сверления крышек
Этот тип сверлильной оснастки не имеет корпуса приспособления и часто используется для обработки нескольких параллельных небольших отверстий в крупных заготовках. Как правило, помимо сверлильных втулок, сверлильный шаблон также оснащен фиксирующими элементами и зажимными приспособлениями. В процессе обработки его нужно только разместить над заготовкой.
На рис. 17 показана оснастка для сверления накладных пластин, используемая для обработки нескольких небольших отверстий на каретке токарного станка. Он размещается в двух отверстиях заготовки с помощью цилиндрического штифта 2 и плоского штифта 3, а также поддерживается на верхней поверхности заготовки тремя опорными штифтами 4. Если сверлильный шаблон относительно тяжелый, а обрабатываемые отверстия относительно малы, зажим может не потребоваться во время обработки.
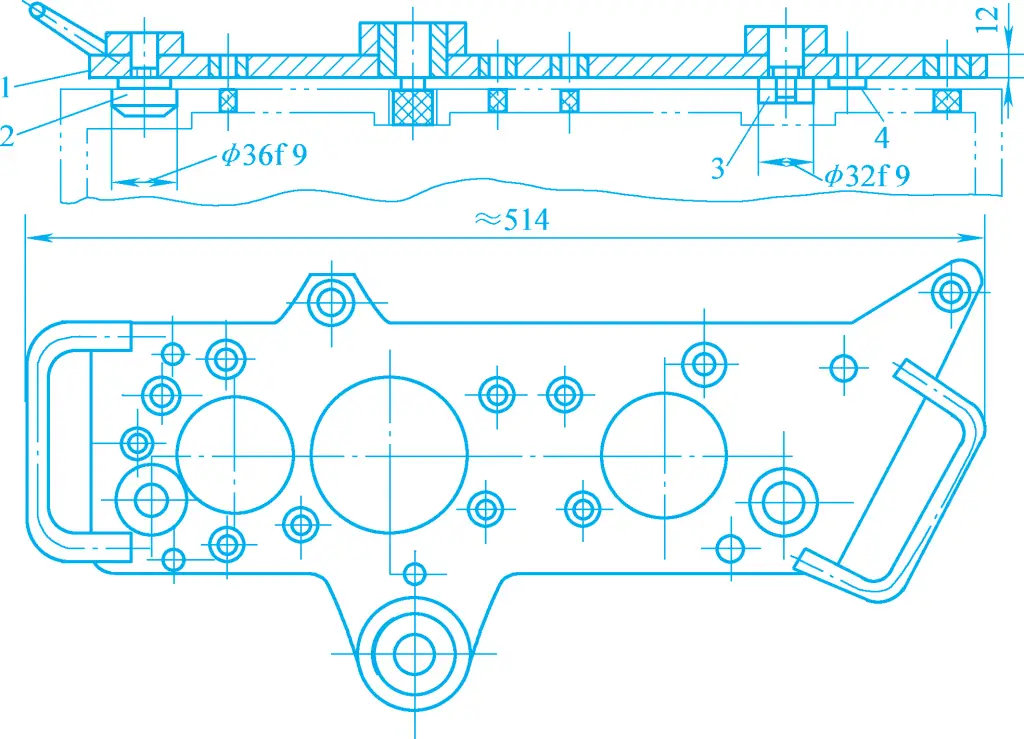
1-Пластина для крышки
2-Цилиндрический штифт
3-плоский штифт
4-Опорный штифт
(5) Сверлильный станок для раздвижных колонн
Сверлильный станок с раздвижной колонной обычно состоит из корпуса приспособления, раздвижной колонны, подъемного сверлильного шаблона и механизма блокировки. Его структура была стандартизирована и обобщена. Общими частями являются, в основном, корпус приспособления и шаблон сверла. Этот тип приспособления широко используется в производстве, но вертикальность просверленных отверстий и точность расстояния между отверстиями не очень высоки.
На рис. 18 показано универсальное основание ручного сверлильного станка с раздвижными колоннами. Подъемный сверлильный шаблон 1 соединен с направляющими отверстиями корпуса приспособления 5 через две направляющие колонны 7. При повороте рукоятки управления 6 коническая шестерня 4 приводит в движение вал конической стойки 3, обеспечивая подъем сверлильного шаблона. В соответствии с формой и требованиями к обработке различных заготовок, для формирования сверлильного станка с подвижной колонной могут быть использованы соответствующие фиксирующие, зажимные элементы и сверлильные втулки.
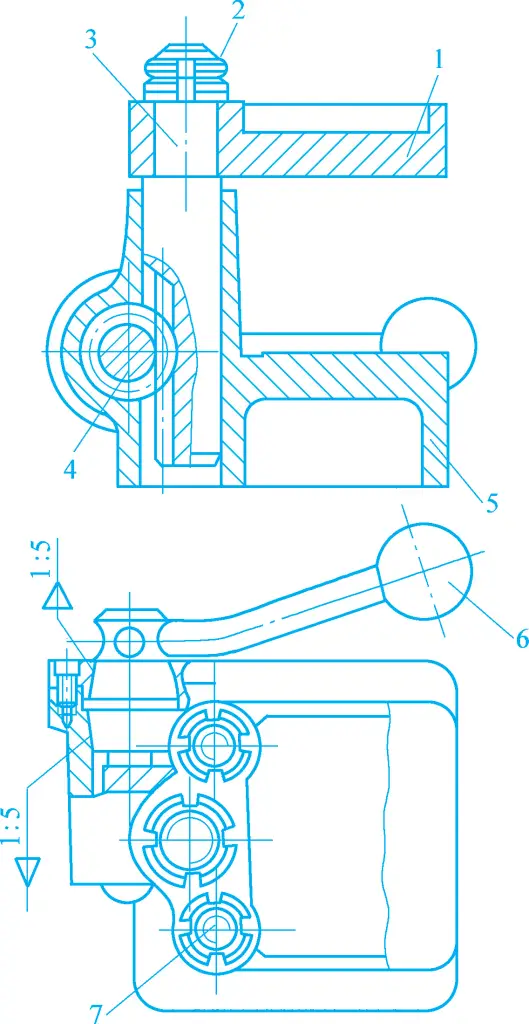
Шаблон для дрели 1-Lifting
2-Стопорная гайка
3-уровневый реечный вал
Четырехступенчатая передача
5-Фиксаторный корпус
6-операционная рукоятка
Колонка с 7 гидами
На рис. 19 показана ручная раздвижная колонковая сверлильная оснастка, используемая для сверления, развертывания и протягивания отверстий φ20H7 в заготовке вилки. Заготовка позиционируется на основании 1 по внешней круглой торцевой, нижней и задней боковым поверхностям соответственно с помощью фиксирующей конической втулки 9, двух регулируемых опор 2 и цилиндрического упорного штифта 3. Все эти фиксирующие элементы установлены на основании 1.
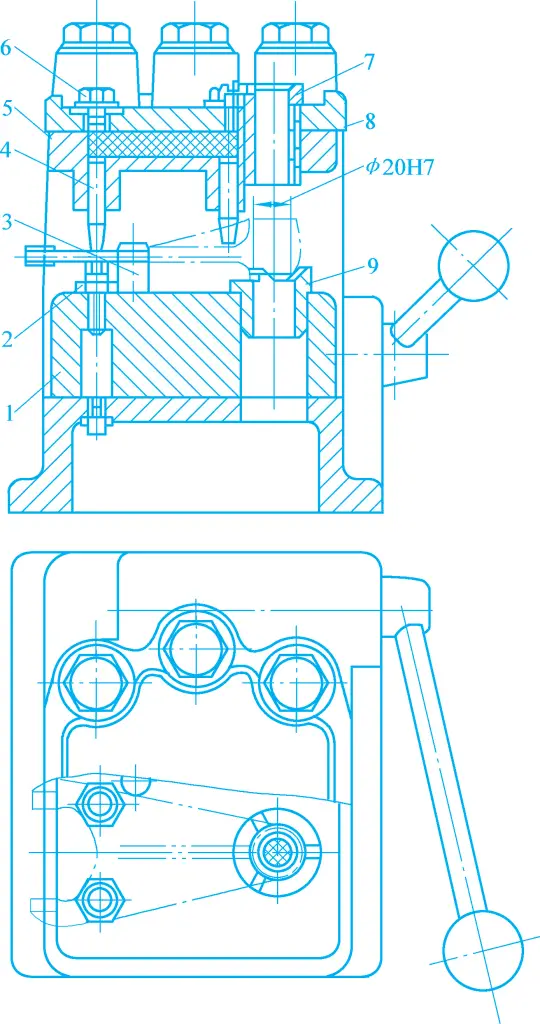
1-База
2-Регулируемая опора
3-Цилиндрический стопорный штифт
Колонна с 4-мя прессами
Корпус колонны с 5 прессами
6-винтовая заглушка
7- Быстросменная втулка для сверла
8-втулка
9-позиционная коническая втулка
Затем поверните рукоятку через механизм зубчатой рейки, в результате чего подвижная колонна опускает шаблон сверла вниз, а две прижимные колонки 4 плотно зажимают заготовку. Инструмент последовательно проходит через быстросменную сверлильную втулку 7, позволяя выполнять сверление, развертывание и растачивание.
2. Конструктивные характеристики приспособлений для сверлильного пресса
(1) Втулка для сверла
Сверлильная втулка является уникальным компонентом сверлильного станка, ее функция заключается в определении относительного положения инструмента и приспособления, направлении сверла и развертки для предотвращения отклонения во время обработки и повышения жесткости технологической системы, обеспечивая тем самым точность позиционирования обрабатываемого отверстия. Его структура включает следующие четыре типа:
1) Фиксированная втулка для сверла.
В основном она используется в мелко- и среднесерийном производстве. Ее конструктивная форма и требования к сборке показаны на рис. 20, где на рис. 20а показана втулка для сверления без буртика, а на рис. 20б - втулка для сверления с буртиком. Если нижняя торцевая поверхность буртика сверлильной втулки используется в качестве базовой поверхности при сборке, или если шаблон сверла относительно тонкий и необходимо предотвратить попадание стружки и другого мусора в отверстие сверлильной втулки, часто используется сверлильная втулка с буртиком.
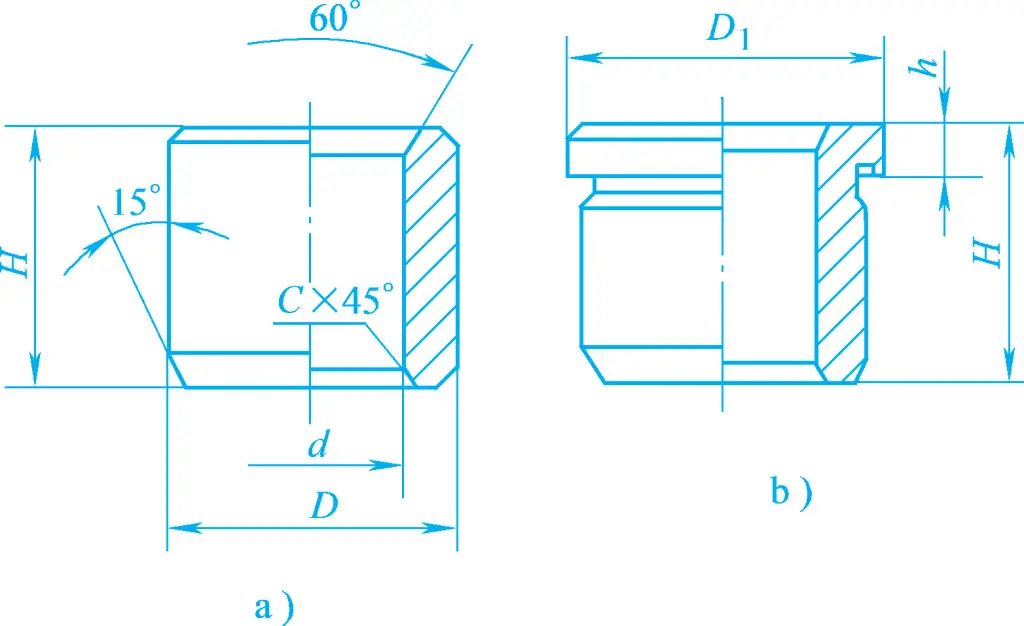
Для посадки между сверлильной втулкой и шаблоном сверла обычно используется H7/n6 или H7/r6. Этот тип сверлильной втулки имеет высокую точность позиционирования при сверлении, простую конструкцию, но нелегко заменяется после износа.
2) Сменная втулка для сверла.
В основном она используется в массовом производстве. При износе сверлильной втулки для облегчения замены часто используется сменная сверлильная втулка с конструктивной формой и требованиями к сборке, показанными на рис. 21. Чтобы избежать износа шаблона сверла при замене втулки, между втулкой сверла и шаблоном сверла устанавливается втулка, которая крепится винтами.
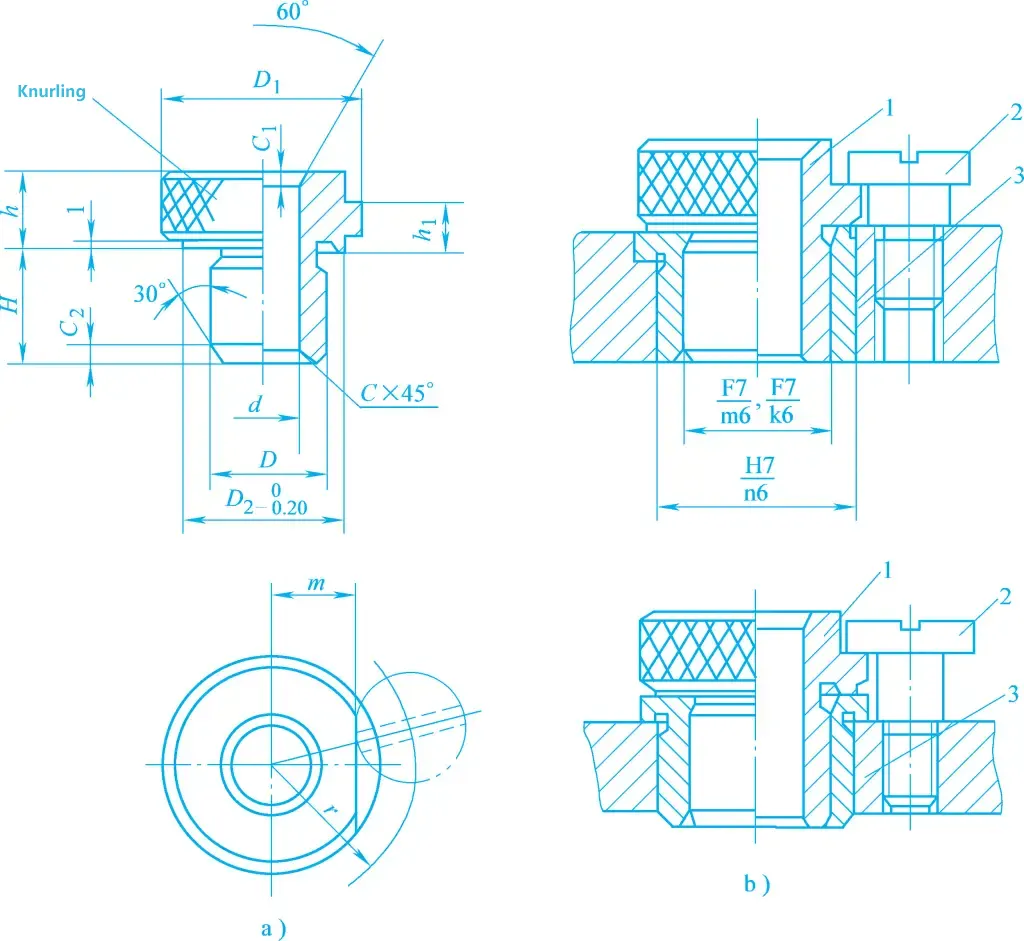
1-Сменная втулка для сверла
2 - Винт для втулки сверла
3-Втулка для втулки сверла
3) Быстросменная втулка для сверла.
Если обрабатываемое отверстие требует последовательного сверления, развертывания, растачивания или многоступенчатой обработки, такой как обработка ступенчатых отверстий и нарезание резьбы, следует использовать быстросменную втулку для быстрой замены втулок с различными внутренними диаметрами. Ее конструктивная форма и требования к сборке показаны на рис. 22.
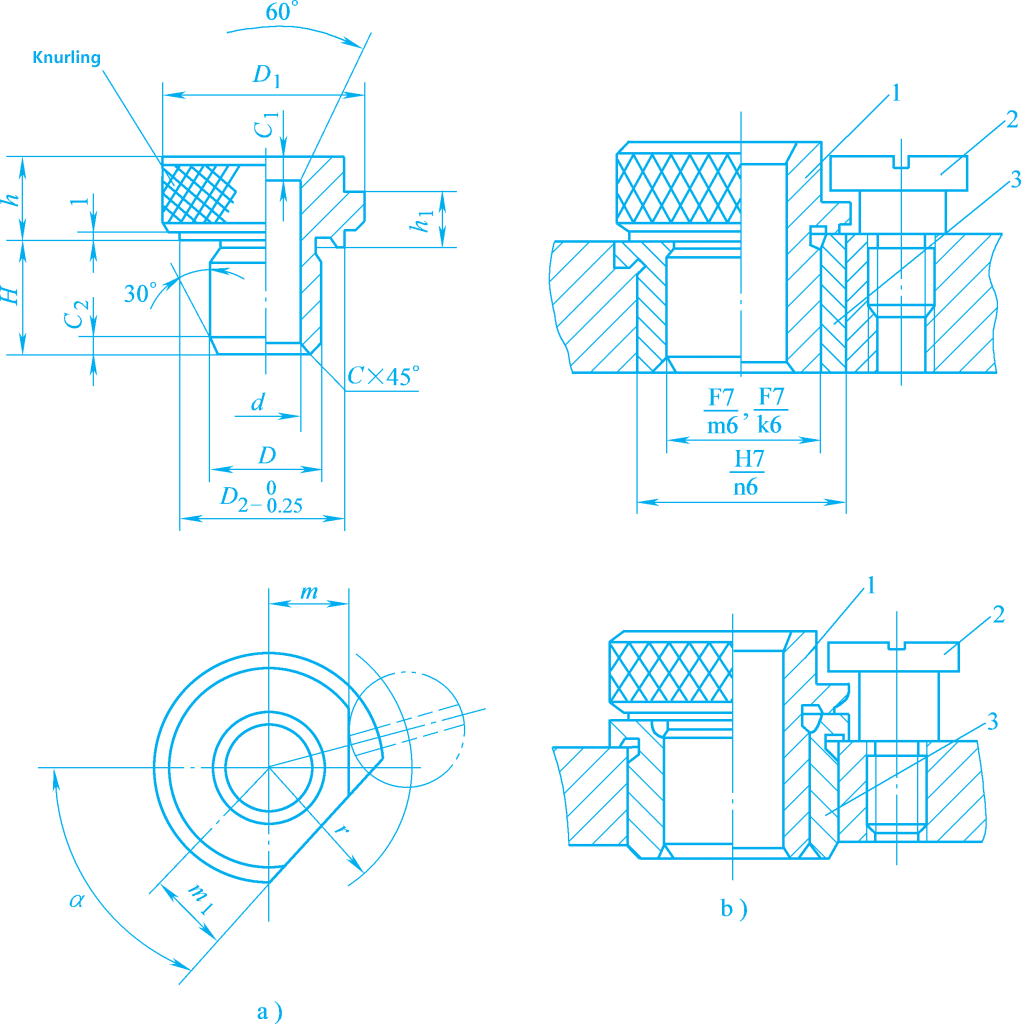
Втулка для сверла 1Quick Change
2 - Винт для втулки сверла
3-Втулка для втулки сверла
При замене втулки сверла нет необходимости ослаблять винты. Для снятия втулки достаточно повернуть ее на определенный угол так, чтобы фаска (или выемка) совпала с головкой винта. Однако положение фаски (или выемки) должно учитывать направление момента трения между инструментом и внутренней стенкой втулки, чтобы предотвратить вытягивание втулки вместе с инструментом при втягивании.
4) Специальная втулка для сверления.
Если форма заготовки или распределение расположения отверстий ограничивает использование вышеуказанных стандартных сверлильных втулок, при необходимости могут быть разработаны сверлильные втулки специальной конструкции.
На рисунке 23 показаны несколько конструктивных форм специальных сверлильных втулок. На рис. 23a показана втулка для сверла, используемая для обработки отверстий на зенкерах или канавках. На рис. 23b показана сверлильная втулка, используемая для сверления отверстий на наклонных или криволинейных поверхностях, которая может предотвратить отклонение или поломку сверла при врезании. На рис. 23c показана втулка для сверла, используемая для обработки нескольких близко расположенных отверстий. На рис. 23d показана сверлильная втулка, используемая в качестве вспомогательного зажимного инструмента.
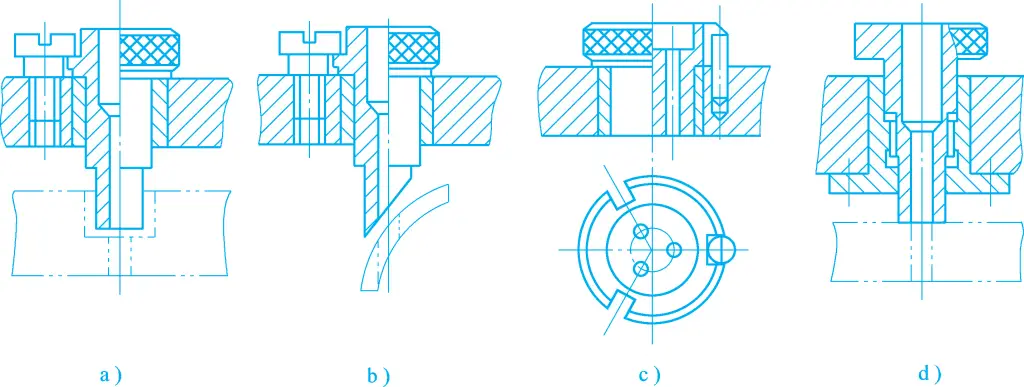
Чтобы выдержать силу зажимной реакции, втулка сверла и гильза соединяются резьбой, кроме того, между втулкой и гильзой должна быть цилиндрическая посадка для обеспечения правильного положения направляющего отверстия.
(2) Шаблоны для сверления
Шаблоны, используемые для установки сверлильных втулок, можно разделить на следующие типы по способу соединения с корпусом крепежа:
1) Фиксированные шаблоны для сверления
Как показано на рис. 24, неподвижные шаблоны для сверления отлиты в корпусе приспособления или соединены с ним с помощью винтов и штифтов. Они также могут быть приварены к корпусу приспособления или кронштейну. Их конструкция проста, и они обладают высокой точностью сверления, однако необходимо следить за тем, чтобы они не мешали загрузке и выгрузке заготовки.
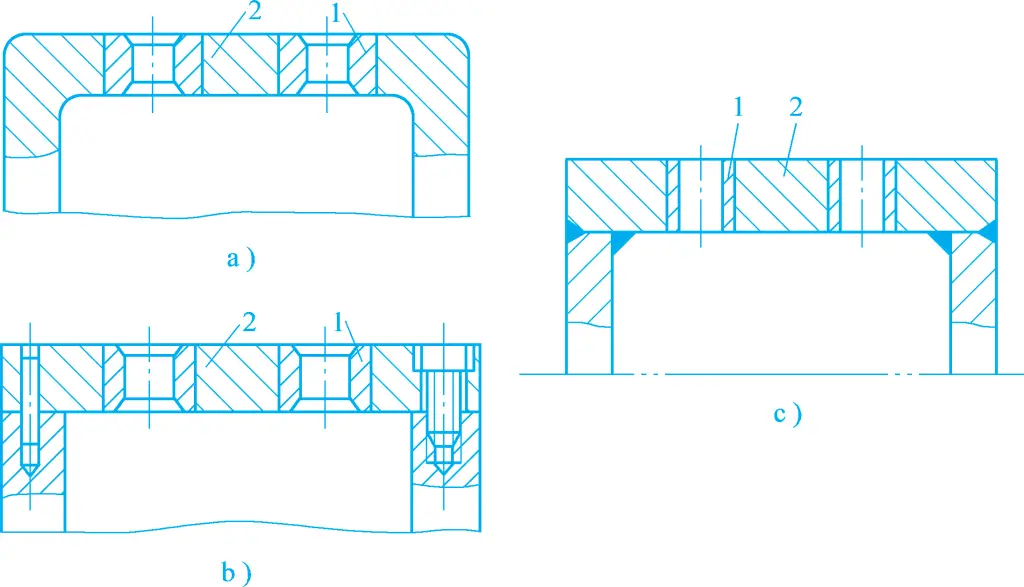
a) Отлитые целиком
b) Соединяются с помощью винтов и штифтов
в) Сварные
1-Сверлильная втулка
2-Сверлильный шаблон
2) Шарнирные шаблоны для сверления
Если сверлильный шаблон мешает загрузке и выгрузке заготовки или если после сверления требуется нарезать резьбу или зенковать, можно использовать шарнирный сверлильный шаблон, как показано на рис. 25.
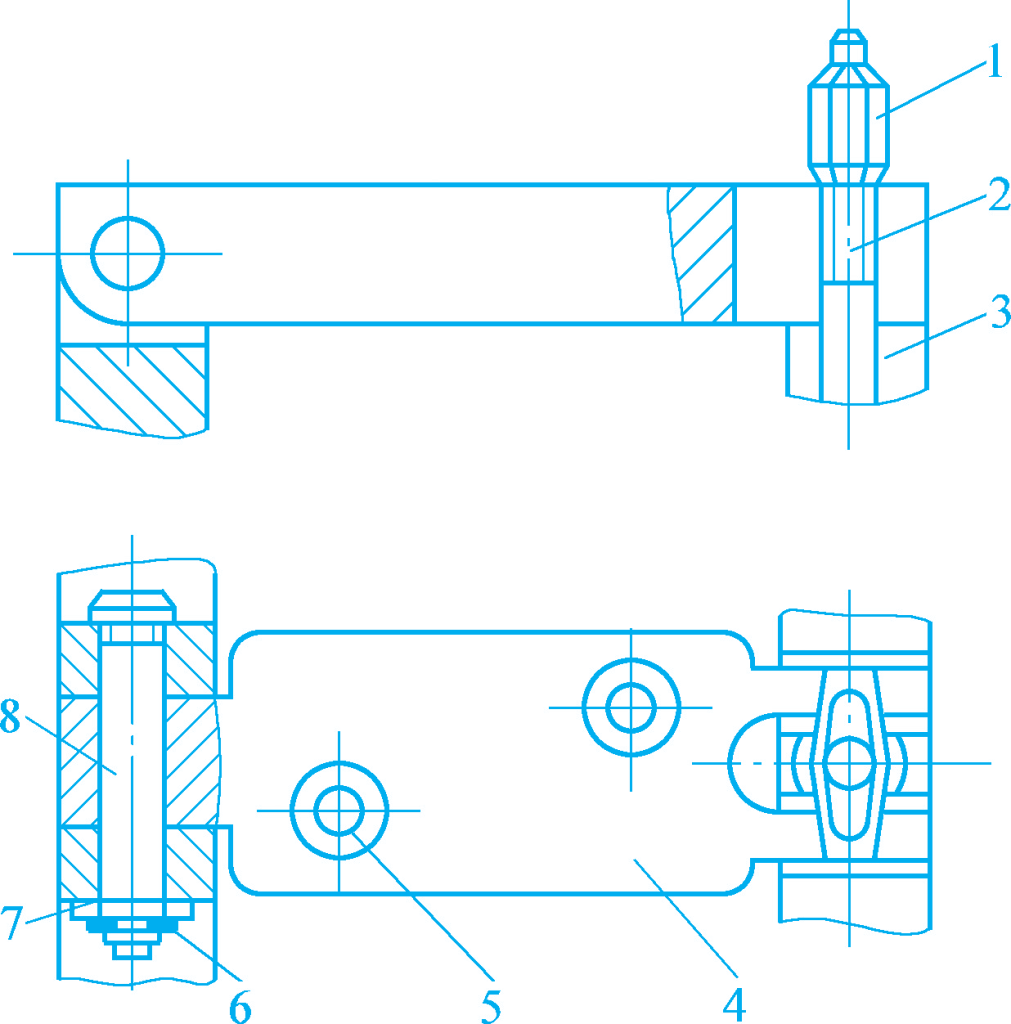
1-ромбическая гайка
2-Тогл болт
Корпус 3 светильника
4-Сверлильный шаблон
5-Фиксированная втулка для сверла
6-шплинт
7-мыльница
8-Штифт шарнира
Из-за зазора между шарнирным штифтом и отверстием точность обработки, которую он может обеспечить, ниже, чем у неподвижных сверлильных шаблонов, поэтому он используется в ситуациях, когда точность позиции сверления невелика. Положение шарнирного сверлильного шаблона фиксируется во время работы, поэтому необходимо учитывать конструктивные требования к позиционированию и фиксации.
3) Съемные шаблоны для сверления
Как показано на рис. 26, шаблон сверла устанавливается на цилиндрический штифт 3 и плоский штифт 4 на корпусе приспособления через два отверстия и зажимается вместе с заготовкой с помощью шарнирного болта. После обработки одной детали сверлильный шаблон снимается для загрузки и выгрузки заготовки. Загрузка и выгрузка этого типа шаблона занимает много времени и сил, а точность позиционирования сверлильной втулки относительно низкая, поэтому он обычно используется только в тех случаях, когда другие типы шаблонов неудобны для зажима заготовки.
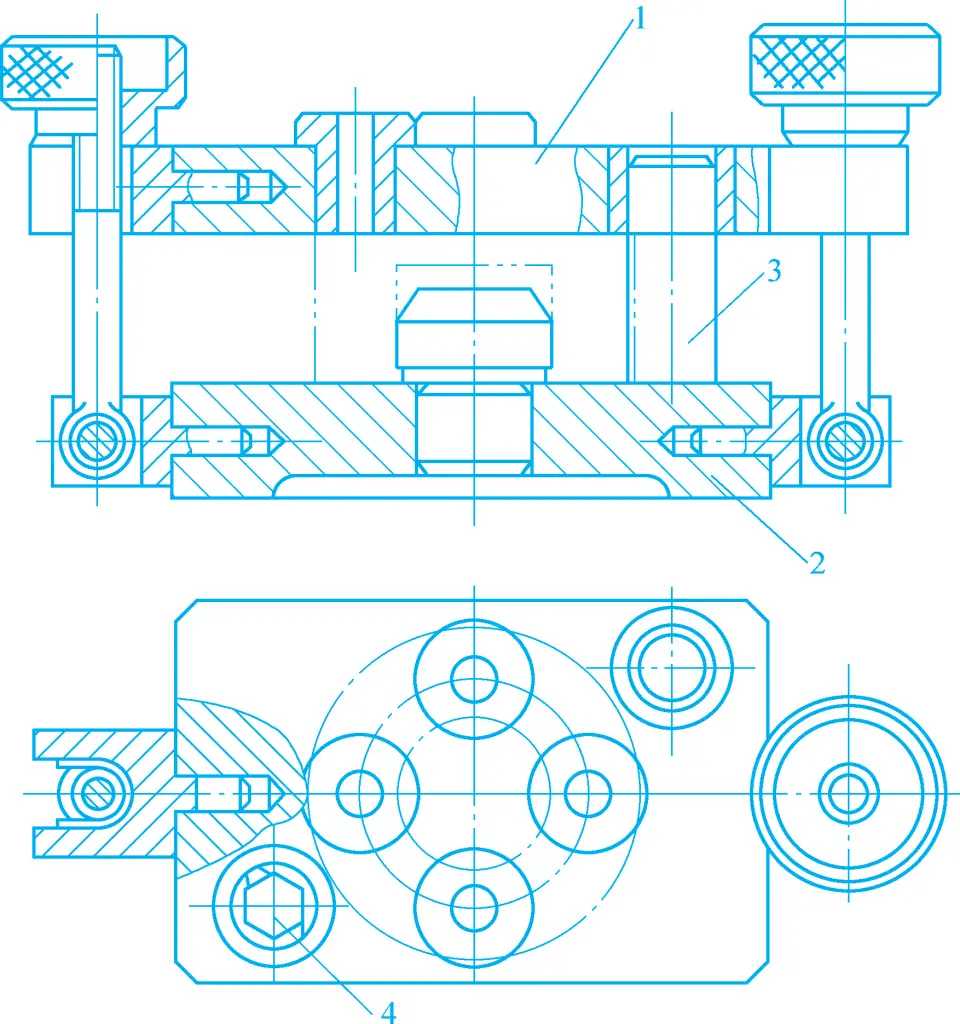
1 - Шаблон для сверления
Корпус с 2 зажимами
3-цилиндрический штифт
Четырехгранный режущий штифт
IV. Приспособления для расточных станков
1. Основные типы и характеристики приспособлений для расточных станков
Приспособления для расточных станков, также известные как расточные приспособления, в основном используются для обработки отверстий или систем отверстий в таких деталях, как коробки и опоры. Точность позиционирования отверстий или систем отверстий на заготовке в основном обеспечивается расточной оснасткой. В зависимости от расположения расточных втулок, расточные приспособления можно разделить на три типа: с одной опорой, с двумя опорами и без опоры.
(1) Одиночная направляющая
Расточная линейка направляется только одной расточной втулкой, расположенной либо перед, либо за инструментом в расточной оснастке. Расточная линейка жестко связана со шпинделем станка, и центральная линия расточной втулки должна совпадать с осью шпинделя. В этом случае точность вращения шпинделя станка будет влиять на точность растачивания. Этот тип расточного станка подходит для обработки коротких и небольших отверстий.
На рис. 27a показана передняя направляющая с одной опорой, используемая в основном для сквозных отверстий с D>60 мм и l/D<1. Этот метод облегчает наблюдение и измерения в процессе обработки и особенно подходит для операций торцевания или нарезания резьбы. Недостатком является то, что стружка легко попадает в расточную втулку, вызывая износ расточной линейки и втулки; инструмент проходит больший путь при входе и выходе из заготовки.
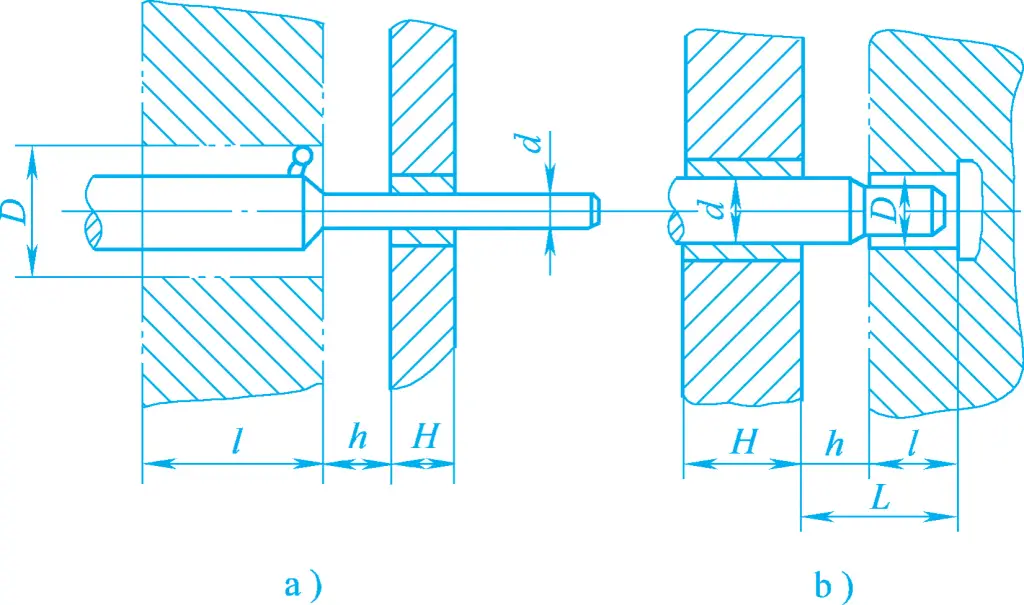
a) Передняя направляющая с одной опорой
b) Задняя направляющая с одной опорой
На рис. 27b показана задняя направляющая с одной опорой, используемая в основном для сверления сквозных или глухих отверстий с D<60 мм.
(2) Двойная опорная направляющая
Расточной стержень гибко соединен со шпинделем станка, а точность позиционирования расточенного отверстия определяется точностью позиционирования расточных втулок. Как показано на рисунке 28, существует два варианта расположения расточных гильз. На рис. 28а показаны две расточные втулки, расположенные спереди и сзади заготовки, используемые для обработки отверстий с большим диаметром и l/D>1,5, или набора соосных отверстий, где требуется высокая точность как самих отверстий, так и расстояний между ними.
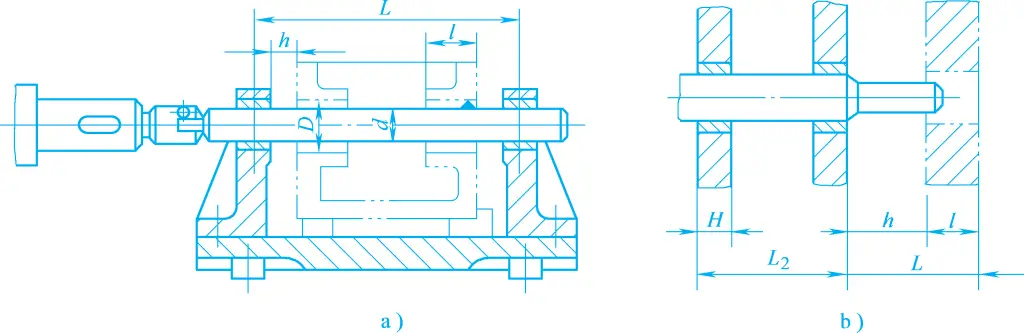
Недостатком такой конструкции является слишком большая длина расточной штанги, что затрудняет загрузку и выгрузку инструмента. Если расстояние между расточными втулками L>10d, необходимо добавить промежуточную направляющую опору, чтобы увеличить жесткость расточной шины. На рис. 28b показана задняя направляющая с двойной опорой, используемая, когда передние и задние двойные направляющие не могут быть использованы из-за условий обработки, с двумя расточными втулками, расположенными за инструментом.
(3) Расточная оснастка без опоры
При растачивании отверстий в заготовках с хорошей жесткостью и высокой точностью на координатно-расточных станках, обрабатывающих центрах или станках алмазного растачивания приспособление не устанавливает расточные втулки, а размер и точность расположения обработанных отверстий обеспечиваются точностью станка.
2. Типичные примеры специальных приспособлений для расточных станков
На рисунке 29 показана технологическая схема изготовления корпуса кронштейна. Эта заготовка требует обработки 2×Φ20H7 коаксиальных отверстий и Φ35H7, Φ40H7 коаксиальных отверстий. Сборочной базой для заготовки является нижняя поверхность a и боковая поверхность b. Отверстия, обработанные в данном процессе, имеют точность класса IT7 с некоторыми требованиями к геометрическим допускам.
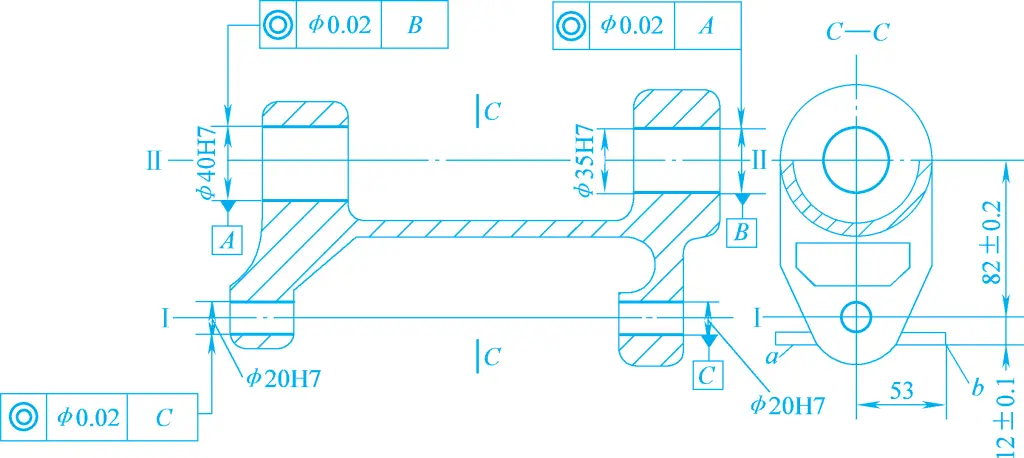
Поэтому для чернового и чистового растачивания отверстий Φ40H7 и Φ35H7, а также сверления, развертывания и хонингования отверстий 2×Φ20H7 используются специальные приспособления для расточных станков. При этом расстояние между отверстиями (82±0,2) мм должно обеспечиваться точностью изготовления расточного приспособления. В соответствии с принципом совпадения опорных точек, в качестве опорных точек позиционирования выбраны две плоскости a и b.
Как показано на рисунке 30, приспособление для расточного станка для корпуса кронштейна включает в себя опорную плиту 10 (одна из которых имеет боковую поверхность) и упорный штифт 9 в качестве позиционирующих элементов. Во время зажима прижимная пластина 8 прижимается к боковым поверхностям заготовки, обеспечивая согласованность силы тяжести заготовки и направления зажима.
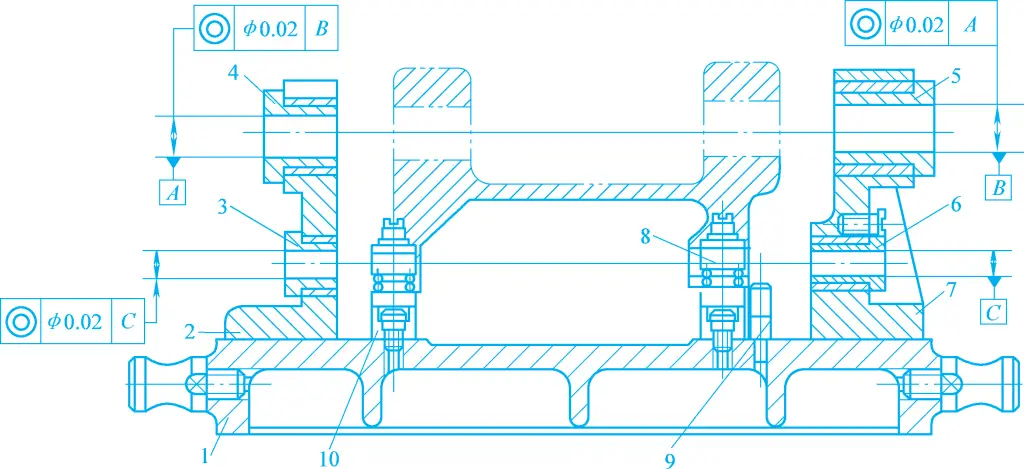
1-Корпус светильника
2, 7-направляющий кронштейн
3, 4, 5, 6 - Расточная втулка
8-Пластина давления
9 Стопорный штифт
10-опорная пластина
При обработке отверстий Φ40H7 и Φ35H7 расточная линейка опирается на расточные втулки 4 и 5. При обработке отверстий Φ20H7 расточная линейка опирается на расточные втулки 3 и 6. Расточные втулки установлены на направляющих кронштейнах 2 и 7. Кронштейны крепятся к корпусу приспособления 1 с помощью штифтов и винтов.
3. Структурные особенности расточного шаблона
(1) Расточная втулка
По конструкции расточные втулки делятся на неподвижные и вращающиеся.
1) Фиксированная расточная втулка
Расточная втулка, которая не вращается вместе с расточным стержнем во время процесса растачивания, имеет такую же структуру, как и быстросменная втулка для сверла. На рисунке 31a показана расточная втулка с запрессованным масляным стаканом, с масляной канавкой во внутреннем отверстии, которая может соответствующим образом увеличить скорость резки во время обработки. Поскольку расточной стержень вращается и перемещается в осевом направлении внутри расточной втулки, она подвержена износу, поэтому расточные втулки без масляных чашек подходят только для низкоскоростного резания.
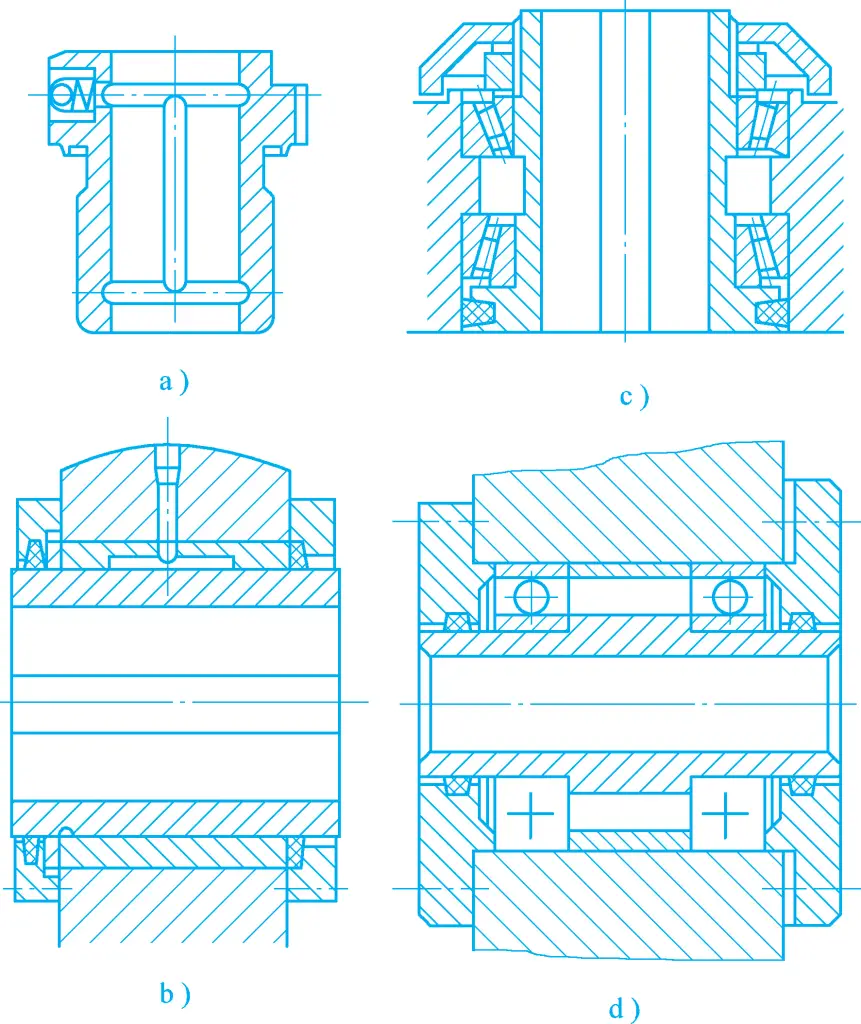
2) Ротационная расточная втулка
В процессе растачивания расточная втулка вращается вместе с расточным стержнем, что особенно подходит для высокоскоростного растачивания, как показано на рисунках 31b, 31c и 31d. На рисунке 31b показана скользящая вращающаяся расточная втулка со шпоночным пазом во внутреннем отверстии, где шпонка на расточном стержне приводит расточную втулку во вращение, обеспечивая высокую точность вращения и хорошее гашение вибраций при небольшом размере конструкции и необходимости достаточного смазывания.
На рисунках 31c и 31d показаны прокатные расточные рукава, используемые для вертикальной и горизонтальной расточки соответственно. Они имеют гибкое вращение и обеспечивают высокую скорости резкиНо их радиальные размеры относительно велики, а точность вращения невысока. Если необходимо уменьшить радиальные размеры, можно использовать игольчатые подшипники.
(2) Кронштейн и основание
Кронштейн и основание расточного шаблона изготавливаются из чугуна и часто производятся отдельно, что облегчает их обработку, сборку и старение. Они должны обладать достаточной прочностью и жесткостью, чтобы обеспечить устойчивость в процессе обработки. Следует по возможности избегать сварочных конструкций и предпочесть жесткие соединения с помощью винтов и штифтов.
Во время работы кронштейн не должен испытывать зажимного усилия. На стороне основания, обращенной к оператору, должна быть обработана узкая длинная плоскость, служащая базовой поверхностью для выравнивания при установке расточного шаблона на верстаке. Основание должно иметь соответствующее количество проушин для обеспечения надежной и прочной установки расточного шаблона на верстаке станка, а для удобства перемещения должны быть предусмотрены подъемные кольца.