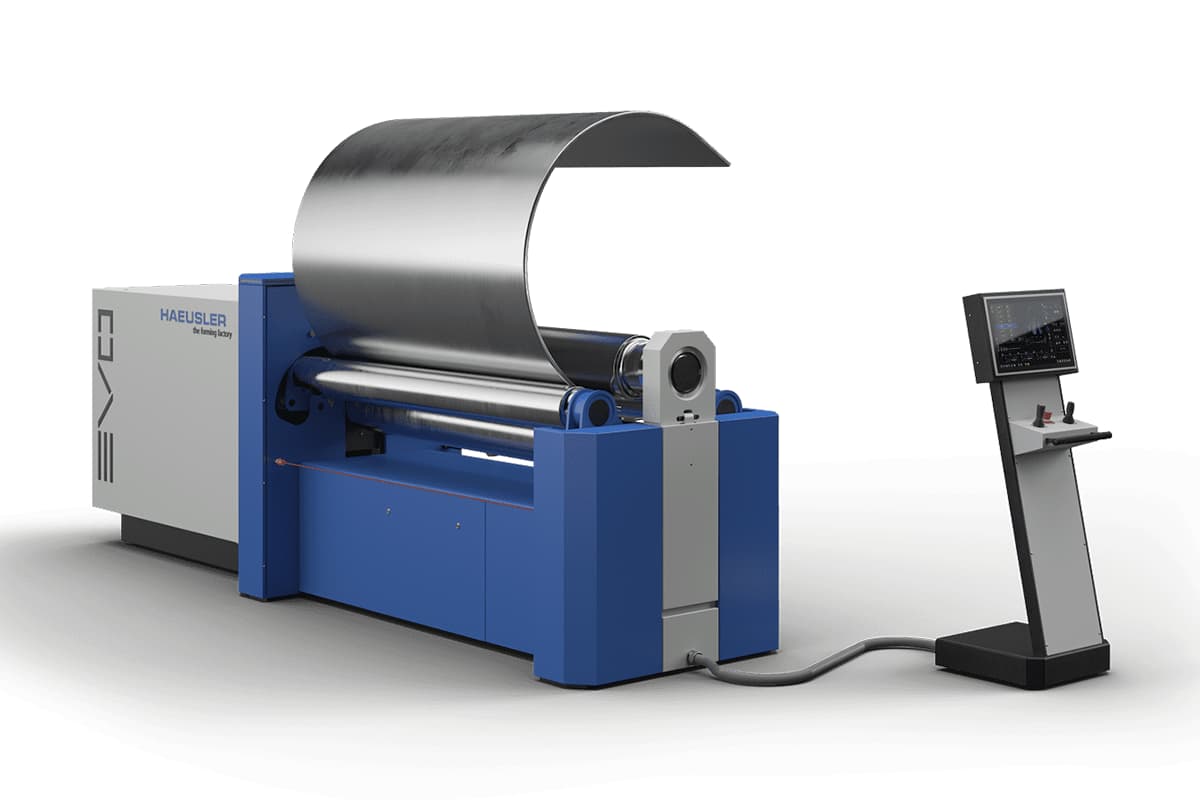
Сварка
I. Принципы, характеристики и область применения дуговой сварки в защитных слоях металла
1. Принцип дуговой сварки в защитной металлической оболочке
Дуговая сварка в защитной среде - это основной метод сварки плавлением, при котором используется ручное управление электродом, а сварочная дуга, возникающая между электродом и изделием, нагревает и расплавляет основной металл или электрод в месте сварки для формирования сварного шва, как показано на рисунке 7-1.
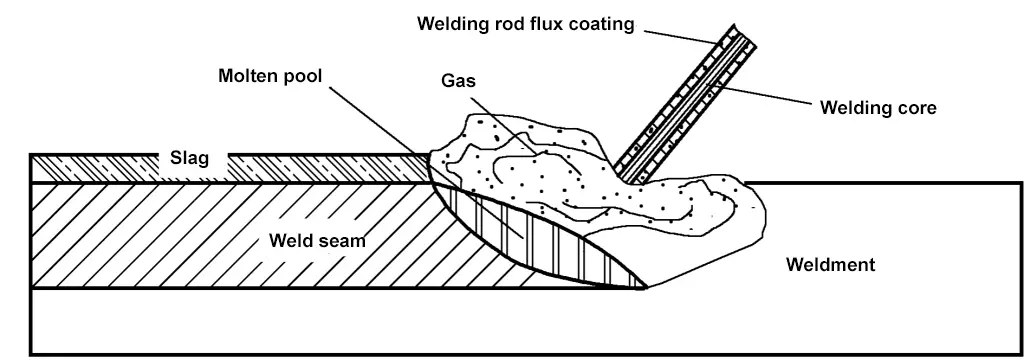
2. Характеристики дуговой сварки в защитных слоях металла
1) Процесс отличается гибкостью и высокой адаптивностью. Во время сварки с помощью ручного управления можно регулировать длину дуги, угол наклона электрода, скорость сварки и т.д., что подходит для различных металлических материалов, толщин, структурных форм и положений.
2) Легко рассеивать сварочное напряжение и контролировать сварочную деформацию путем изменения технологических операций.
3) По сравнению с такими методами, как сварка в газовой среде и дуговая сварка под флюсомОборудование простое, обслуживание удобное, а производственные затраты ниже.
4) Низкая эффективность производства, высокая трудоемкость и качество сварки требуют высокого уровня квалификации и опыта оператора.
3. Область применения дуговой сварки в защитных слоях металла
Дуговая сварка в защитной оболочке широко используется в различных отраслях народного хозяйства. Она может использоваться для сварки углеродистой стали, низколегированной стали, жаропрочной стали и нержавеющей стали. Она также подходит для сварки высоколегированной стали, чугуна, цветных металлов. металлы, разнородных сталей, а также для наплавки различных металлических материалов.
II. Электроды и принципы выбора электродов
Электрод - это сварочный материал, покрытый флюсом для использования при дуговой сварке в защитной металлической среде. Во время сварки электрод выполняет две функции: электрода и присадочного металла, который плавится и соединяется с основным материалом, образуя сварной шов.
Существует множество типов электродов, каждый из которых имеет свою область применения. Правильный выбор электродов оказывает значительное влияние на качество сварки, стоимость продукции и производительность труда. При выборе электродов следует руководствоваться следующими принципами:
1) Выбирайте электрод в зависимости от механических свойств и химического состава основного материала. При сварке таких основных материалов, как низкоуглеродистая сталь, среднеуглеродистая сталь или обычная низколегированная сталь, выбирайте электрод с соответствующей прочностью, чтобы обеспечить сварному шву те же характеристики, что и основному материалу.
2) Для важных конструкций, требующих высокой прочности и пластичности сварного шва, или для стали с высокой склонностью к образованию трещин и высокой жесткостью, выбирайте электроды с основной, высокой прочностью или даже электроды с ультранизким содержанием водорода.
3) При выборе электродов для сварки нержавеющей, молибденовой и хромомолибденовой жаропрочной стали или для наплавки следует исходить из обеспечения специальных характеристик сварного соединения, требуя, чтобы химический состав и тип металла шва были такими же или близкими к основному материалу.
4) Для сварки разнородных металлических соединений между низкоуглеродистой и низколегированной сталью выбирайте электрод на один уровень прочности ниже.
4) Для сварки разнородных металлических соединений между низкоуглеродистой и низколегированной сталью выбирайте электрод на один уровень прочности ниже.
5) Выберите электроды с учетом имеющегося оборудования и условий строительства. Предпочтительно использовать электроды, подходящие как для переменного, так и для постоянного тока. Если скошенную поверхность заготовки трудно очистить, используйте кислотные электроды, которые сильно окисляются и нечувствительны к ржавчине и масляным пятнам; в закрытых контейнерах или в условиях плохой вентиляции используйте кислотные электроды, которые выделяют меньше вредных газов во время сварки.
6) Учитывайте трещиностойкость металла шва. Если свариваемая конструкция имеет высокую жесткость, большую толщину и сложную форму, используйте трещиностойкие основные электроды с низким содержанием водорода.
7) Если сварные детали подвергаются вибрационным или ударным нагрузкам, помимо обеспечения прочности, используйте основные электроды с лучшей пластичностью и вязкостью.
8) При выборе, основанном на упрощении процессов, производительности и экономической эффективности, старайтесь использовать электроды, которые производят меньше пыли и вредных веществ и являются недорогими. Для сварных деталей с большим объемом сварочных работ используйте более крупные и эффективные электроды, такие как высокоэффективные электроды из нержавеющей стали и гравитационные электроды, обеспечивая при этом производительность сварки.
III. Классификация и меры по предотвращению остаточной деформации при сварке
Неравномерный нагрев и усадка в процессе сварки являются основными причинами возникновения остаточных напряжений, а остаточные напряжения - основной причиной структурных деформаций.
1. Классификация остаточных деформаций при сварке
В реальном производстве деформация сварных конструкций довольно сложна. В соответствии с влиянием остаточной деформации при сварке на всю конструкцию, ее можно разделить на две категории: одна - локальная деформация, которая происходит в некоторых частях сварной конструкции, как показано на рисунке 7-2; другая - общая деформация, которая вызывает изменения формы и размера всей сварной конструкции, как показано на рисунке 7-3.
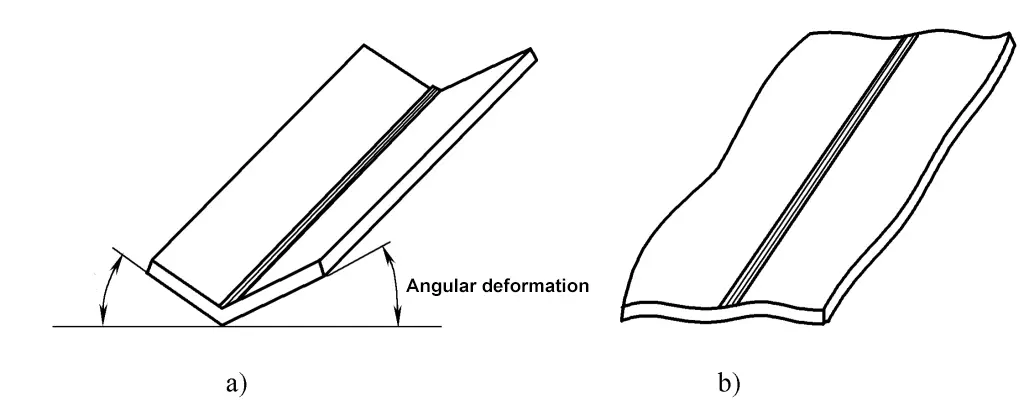
a) Угловая деформация
б) Волнистая форма края
В соответствии с характеристиками сварочных остаточных деформаций их можно разделить на шесть основных форм: усадочная деформация, угловая деформация, деформация изгиба, волнистая деформация, деформация кручения и деформация смещения, как показано на рисунках 7-2 и 7-3.
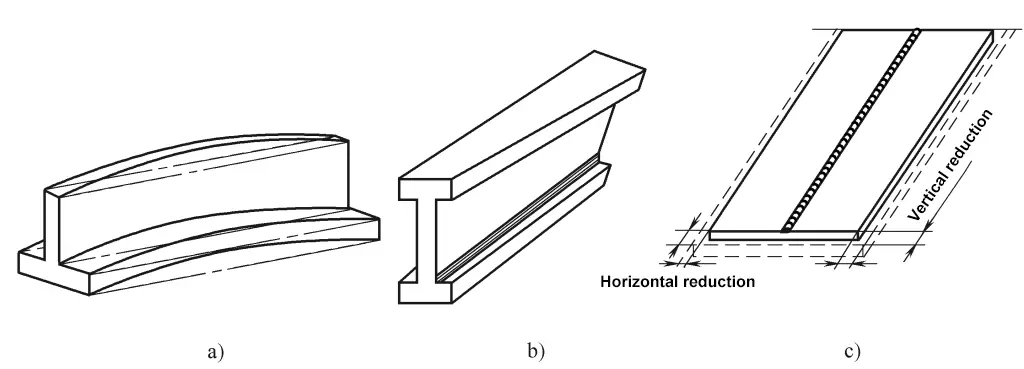
a) Деформация изгиба
b) Деформация кручения
c) Усадочная деформация
2. Меры по предотвращению остаточной деформации при сварке
Чтобы контролировать остаточную деформацию при сварке, рассмотрим следующие часто используемые меры с точки зрения технологического процесса:
(1) Используйте разумную последовательность сварки при сборке
1) Используйте метод симметричной сварки для получения симметричных швов
Поскольку сварка всегда имеет определенную последовательность, и по мере продвижения процесса сварки жесткость конструкции также увеличивается. Поэтому сварные швы, которые свариваются первыми, обычно вызывают деформацию конструкции. Таким образом, даже если структура сварных швов симметрична, после сварки произойдет деформация. Цель симметричной сварки - преодолеть или уменьшить деформацию, вызванную первым сварным швом, когда жесткость сварной детали низкая.
2) Для асимметричных швов сначала сваривайте сторону с меньшим количеством швов
Для конструкций с асимметричными сварными швами сначала сваривайте сторону с меньшим количеством швов, а затем сторону с большим количеством швов. Это позволит компенсировать деформацию от более поздней сварки за счет деформации ранее сваренной стороны, уменьшая общую деформацию.
3) Используйте различные последовательности сварки для контроля сварочной деформации
При сварке длинных швов в конструкциях, если используется непрерывная сквозная сварка, она вызывает значительные деформации. Это связано не только с направлением сварки, но и с тем, что сварной шов нагревается в течение длительного времени. Если возможно, замена непрерывной сварки на сегментную и соответствующее изменение направления сварки могут уменьшить деформацию, вызванную локальными швами, или компенсировать друг друга для достижения цели уменьшения общей деформации. Как показано на рисунке 7-4.
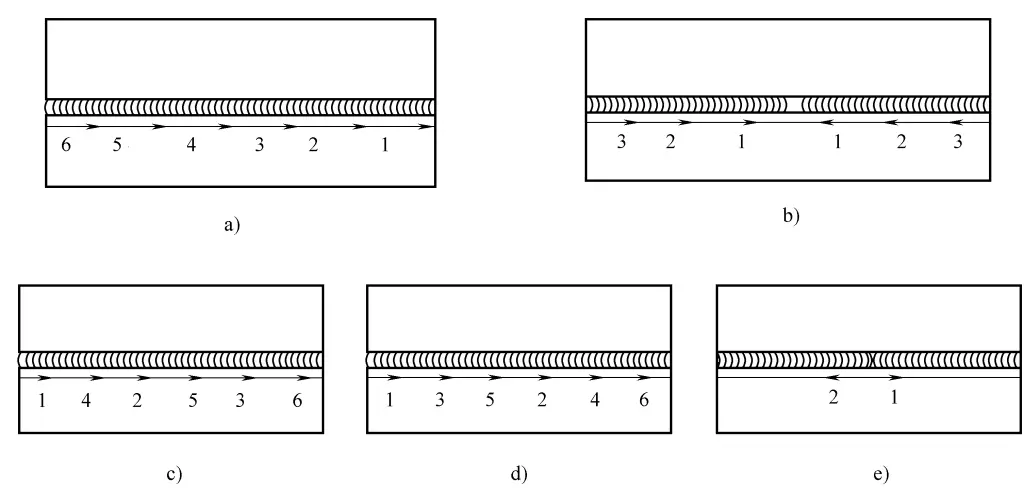
a) Метод сварки с обратным шагом
b) Метод сварки с шагом назад по центру
c) Метод сварки с пропуском
d) Метод попеременной сварки
e) Метод стыковой сварки средней части
(2) Метод встречной деформации
В соответствии с характером деформации сварного шва, искусственно поместите сварной шов в деформацию, противоположную направлению сварочной деформации, заранее, чтобы достичь цели противодействия сварочной деформации. Этот метод называется методом противодействия деформации (также известен как метод резервного припуска). Использование этого метода требует опыта в прогнозировании величины встречной деформации, а угол обратного изгиба должен контролироваться, не быть слишком маленьким или слишком большим. Стыковая сварка Y-образного паза, показанная на рисунке 7-5, является примером контроля угловой деформации с помощью метода встречной деформации.
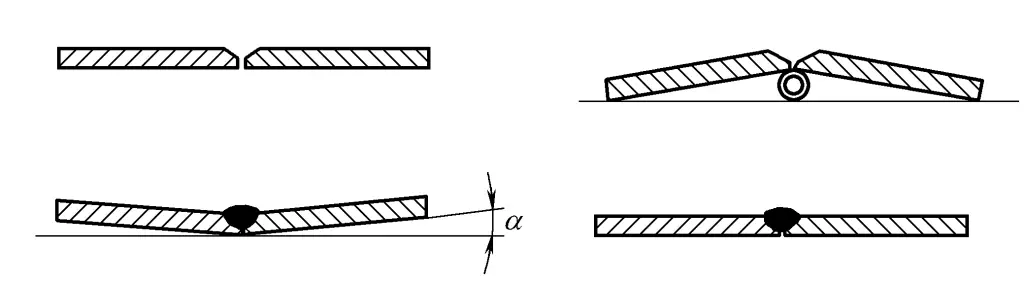
(3) Метод жесткой фиксации
Величина деформации сварного соединения зависит от жесткости конструкции; чем больше жесткость, тем меньше деформация после сварки, а жесткость конструкции в основном зависит от формы и размера конструкции. С точки зрения способности конструкции сопротивляться растяжению или сжатию, величина жесткости связана с размером площади поперечного сечения.
Чем больше площадь поперечного сечения, тем выше жесткость и способность сопротивляться деформации. Поэтому толстые стальные листы меньше деформируются после сварки по сравнению с тонкими стальными листами.
Метод жесткой фиксации заключается в использовании принудительных мер или использовании приспособлений с высокой жесткостью для компонентов, которые сами не обладают достаточной жесткостью, чтобы ограничить и уменьшить степень деформации после сварки. При этом методе фиксированные приспособления можно удалить только после полного остывания сварного шва. На рисунках 7-6-7-8 показаны примеры различных сварных конструкций с использованием метода жесткой фиксации для уменьшения сварочных деформаций.
1) Используйте тяжелые предметы для прижатия или используйте прихваточную сварку для позиционирования. Этот метод подходит для сварки тонких листов, когда прихватка используется вокруг листа, чтобы прочно приварить его к платформе или раме, а тяжелые предметы размещаются по обе стороны сварного шва. После полного остывания сварного шва удалите тяжелые предметы, зачистите места прихваток и добейтесь снижения деформации. Как показано на рисунке 7-6.
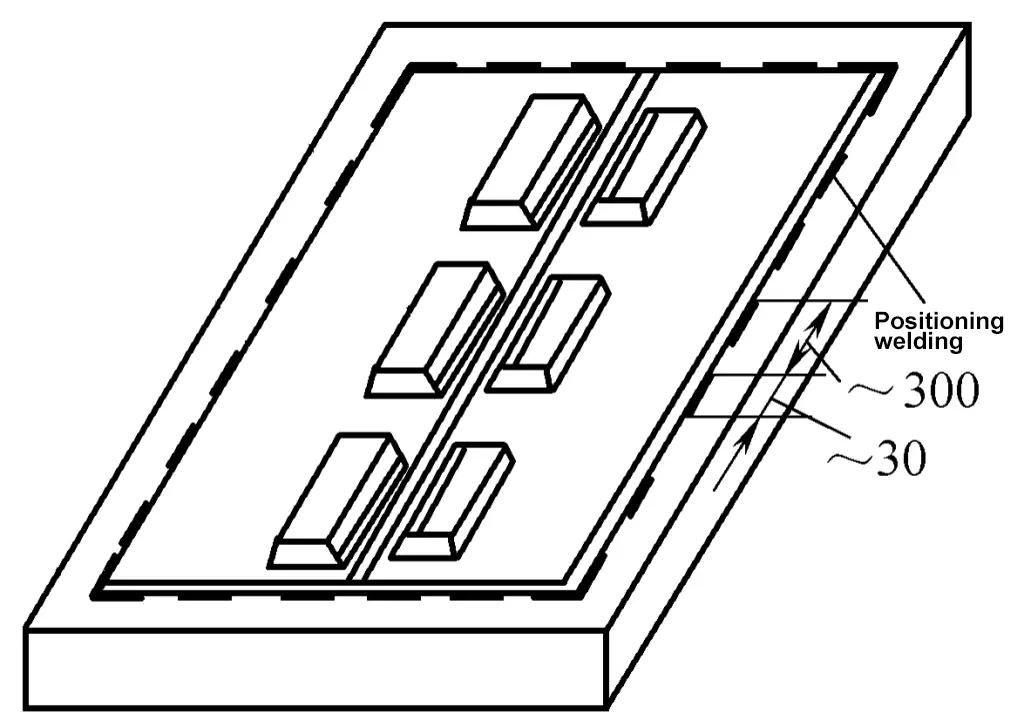
2) Используйте приспособления для фиксации. Как показано на рисунке 7-7a, перед сваркой двутавровой балки прочно прикрутите фланцы к платформе, используя жесткость платформы для уменьшения угловой деформации и деформации изгиба после сварки.
Если условия ограничивают применение вышеуказанного метода, можно также использовать метод, показанный на рис. 7-7b, объединяя две двутавровые балки вместе, используя клиновые зажимы для стягивания двух фланцев, увеличивая жесткость двутавровой рамы для достижения цели уменьшения деформации после сварки. Этот метод также широко используется при монтажной сварке оснований, рам и других компонентов.
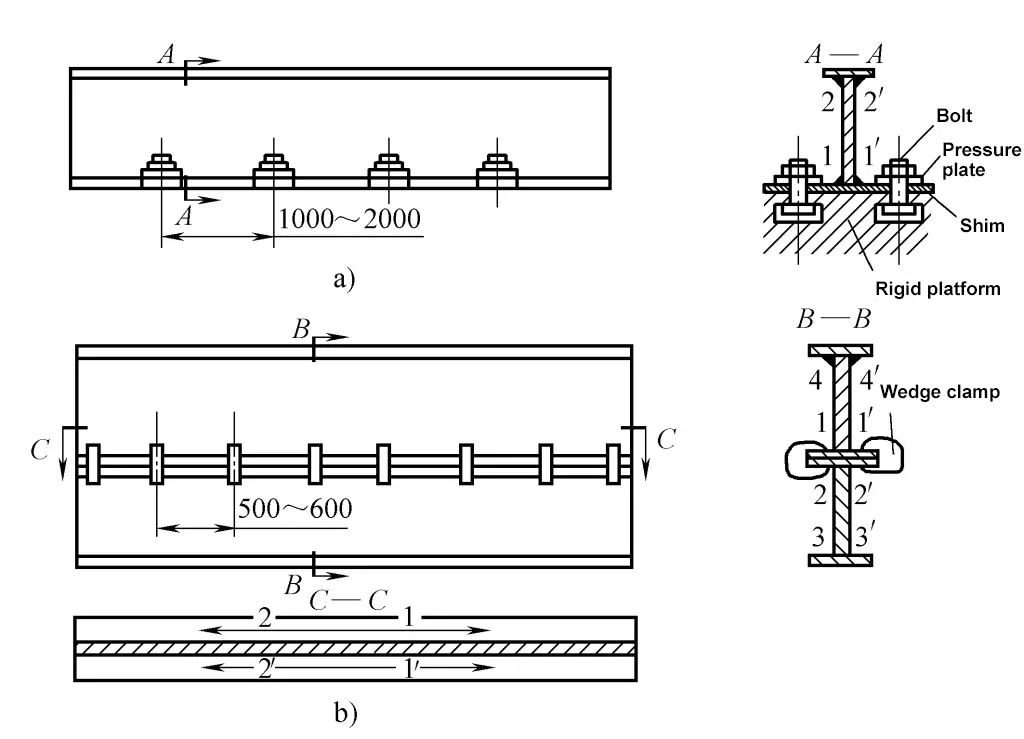
a) Одна двутавровая балка
б) Комбинация двух двутавровых балок
3) Используйте для фиксации "пильные колья" или временные опоры. При стыковой сварке стальных листов для контроля деформации можно также использовать метод фиксации с помощью "пильных костылей", который является простым и надежным методом, широко применяемым в производстве. Для общих небольших сварных соединений можно также использовать метод жесткой фиксации с временными опорами, как показано на рис. 7-8.
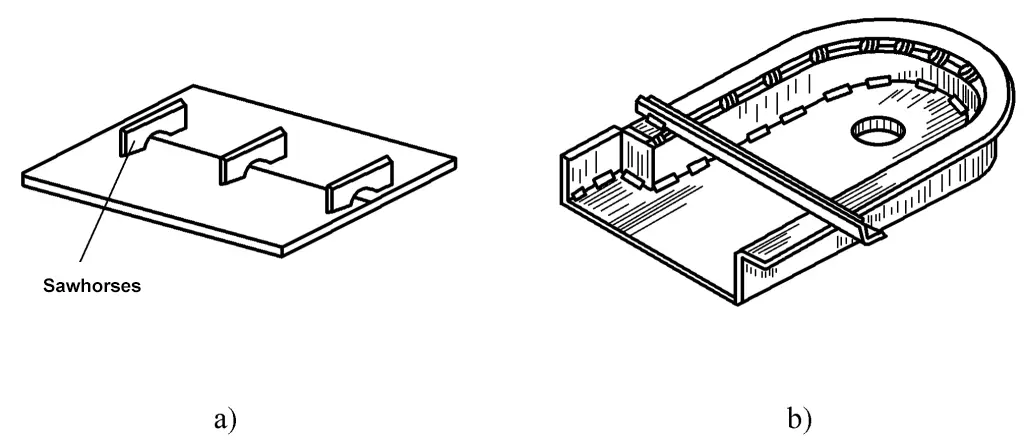
a) Метод фиксации с помощью "пильных костылей"
b) Метод крепления с использованием временных опор
Следует отметить, что хотя сварочная деформация эффективно контролируется при жесткой фиксации, из-за больших ограничений в конструкции возникают значительные внутренние напряжения. Поэтому жесткая фиксация подходит только для сварных соединений с хорошей свариваемостью. Для среднеуглеродистой и легированной стали с плохой свариваемостью жесткая фиксация не должна использоваться для сварки во избежание образования трещин.
Кроме того, выбирая разумные методы сварки и параметров также может уменьшить сварочную деформацию. Например, использование концентрированного тепла, узкой зоны термического влияния CO, сварки в газовой защите, плазменной дуговой сварки вместо газовой сварки и дуговой сварки в защитном металле может уменьшить сварочную деформацию; использование меньших параметров сварки для уменьшения теплового воздействия также может уменьшить сварочную деформацию.
Клепка
I. Принципы клепки
Клепка - это метод соединения двух или более деталей из одного или разных материалов с отверстиями для заклепок в единое целое с помощью клепальных инструментов и оборудования, использующих деформацию заклепок при комнатной температуре или после нагрева.
Общий процесс клепки выглядит следующим образом:
1) С помощью сверления, рассверливания, протягивания и развертывания обработайте отверстия под заклепки на соединительных деталях.
2) В соответствии с требованиями к размерам конструктивного чертежа, выберите эталон сборки для позиционирования клепаных деталей.
3) Правильно подбирайте заклепки, соответствующие техническим требованиям.
4) Определите оборудование и инструменты для клепки.
5) Выполнять операции клепки: обжиг, соединение, нарезка резьбы и зачистка.
6) Проверка качества клепки.
Клепка отличается простотой технологического оборудования, равномерным и надежным распределением напряжений, минимальной деформацией после сборки, высокой прочностью, простотой контроля качества, удобством осмотра, соединениями, не склонными к расшатыванию, длительным сроком службы, простотой обслуживания и контроля. Это неразъемное соединение, обычно используемое в соединениях, которые должны выдерживать большие ударные и вибрационные нагрузки, плохую свариваемость или неметаллические материалы.
С развитием промышленных технологий клепка постепенно вытесняется сваркой и склеиванием из-за своих недостатков, таких как многократность процесса, высокая трудоемкость, высокий уровень шума и низкая эффективность работы, но она по-прежнему широко используется в таких отраслях, как автомобилестроение, авиация, приборостроение, мостостроение и строительство.
II. Классификация и область применения клепки
1. Виды клепки
В зависимости от рабочих характеристик деталей и сферы применения клепку можно разделить на:
(1) Прочная клепка
От заклепок и компонентов требуется только достаточная прочность, чтобы выдерживать большие нагрузки, без особых требований к герметичности соединения. Например, мосты, балки, транспортные средства, башни и другие элементы ферм.
(2) Плотная клепка
Требуется не только достаточная прочность соединения, чтобы выдержать определенные усилия, но и хорошая герметичность соединения, чтобы исключить утечку жидкостей или газов при определенном давлении. Этот тип заклепок обычно используется в деталях сосудов высокого давления, таких как котлы, газовые баллоны и т. д.
(3) Плотная клепка
Соединение не выдерживает значительных усилий, требуется только высокая герметичность для предотвращения утечки воды и воздуха, в основном используется для соединения тонкостенных элементов контейнеров, таких как резервуары для воды, нефтяные баки и т.д.
2. Формы клепки
В соответствии с различным взаимным расположением соединяемых деталей, они делятся на три вида: нахлесточные, стыковые и угловые соединения.
(1) Круг
Один лист приклепывается к другому листу, как показано на рисунке 7-9.
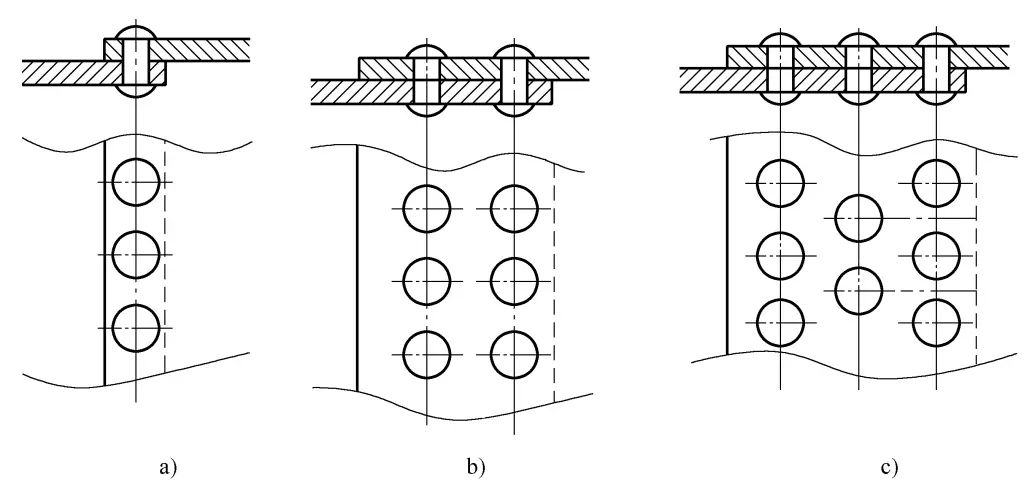
a) Однорядные
б) Двойной ряд
в) Несколько рядов
(2) Стыковое соединение
Клепка выполняется путем расположения стыков двух пластин в одной плоскости и использования накладной пластины в качестве соединителя для соединения стыков. Существует два типа накладных пластин: одинарные и двойные, которые подразделяются на однорядные, двухрядные и многорядные в зависимости от количества рядов заклепок. Расположение заклепок может быть как параллельным, так и ступенчатым, как показано на рис. 7-10.

a) Один ряд, одна накладная пластина
b) Двойной ряд, двойная крышка
в) Стыковое соединение из углового железа
(3) Угловое соединение
Соединяет две пластины, расположенные перпендикулярно или под определенным углом друг к другу, обычно с использованием углового железа в качестве соединителя, выпускается в одностороннем и двухстороннем вариантах, как показано на рис. 7-11.
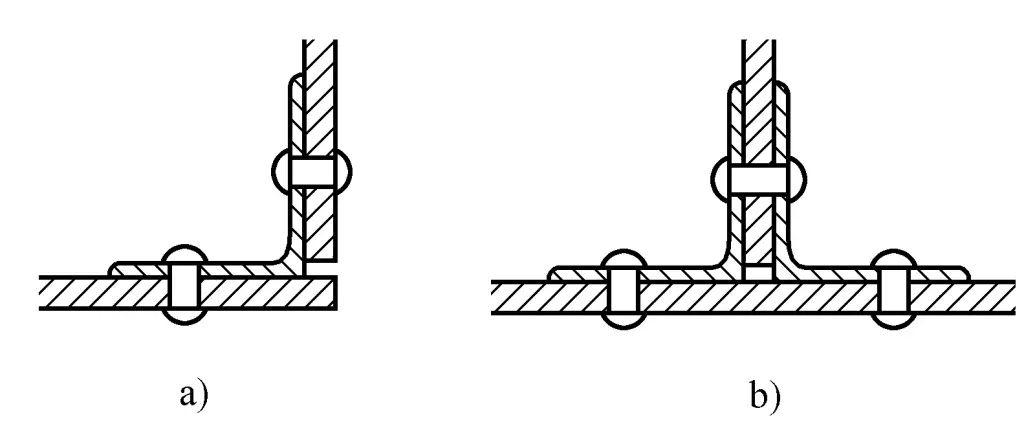
a) Одностороннее угловое соединение
b) Двусторонняя угловая стыковка
III. Основные параметры расположения заклепок
Основные параметры - это расстояние между заклепками, расстояние между рядами и расстояние между кромками, как показано на рисунке 7-12.
1) Расстояние между заклепками t: Расстояние между центрами двух соседних заклепок в одном ряду.
2) Расстояние между рядами c: Расстояние между центрами двух соседних рядов заклепок.
3) Расстояние до края e: Расстояние от крайнего ряда заклепок до края рабочей пластины.
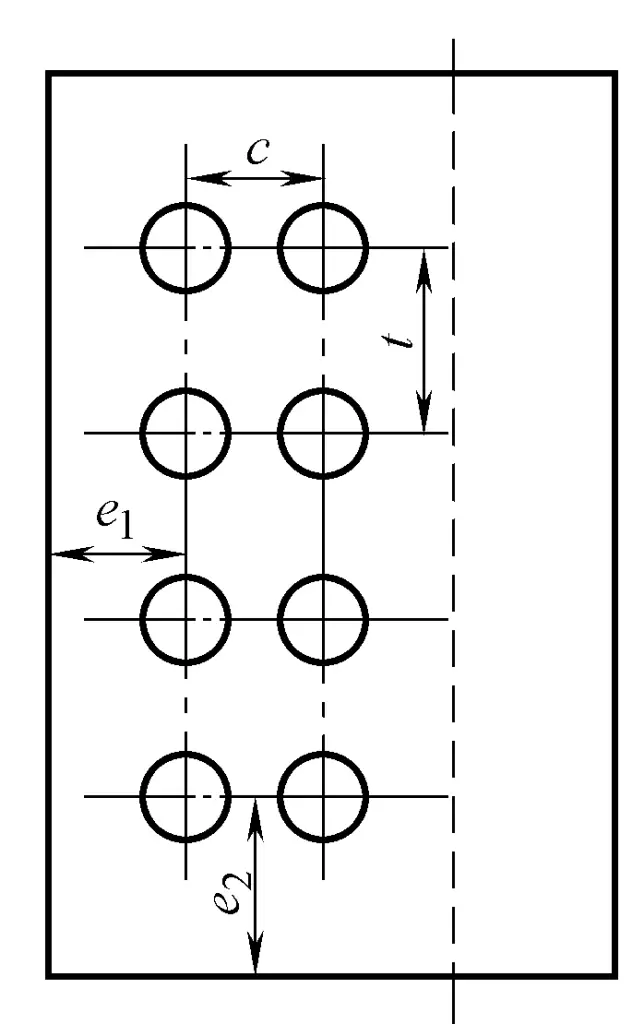
Определение параметров расположения заклепок на стальных пластинах, см. таблицу 7-1.
Таблица 7-1 Определение параметров расположения заклепок на стальных пластинах
Имя | Расположение и ориентация | Максимально допустимое расстояние (возьмите минимальное из двух) | Минимально допустимое расстояние | |
Расстояние между заклепками t или шаг c | Внешний ряд | 8d 0 или 12δ | 3d0 | |
Средний ряд | Компонент под сжатием | 12d 0 или 18δ | ||
Компонент под сжатием | 16d 0 или 24δ | |||
Маржа e | Параллельно направлению нагрузки e 1 | 4d 0 или 8δ | 2d0 | |
Направление, перпендикулярное нагрузке e 2 | Режущая кромка | 1.5d0 | ||
Прокатный край | 1.2d0 |
Примечание: d 0 диаметр отверстия под заклепку; δ - толщина более тонкой пластины
IV. Определение заклепок, их диаметра, длины и размера отверстий
1. Заклепки
Заклепка состоит из головки и цилиндрического хвостовика, причем головка заклепки часто выковывается из штампов, и может быть сплошной и полой. Сплошные заклепки делятся на различные формы, такие как круглые головки, потайные, полупотайные, плоские конические и плоские головки; полые заклепки легкие и удобные для клепки, но имеют низкую прочность головки, подходят для конструкций, подвергающихся меньшим нагрузкам.
Согласно GB/T116-1986, стальные заклепки включают Q215, Q235, ML2, ML3, 10, 15, медные заклепки включают T3, H62, а алюминиевые заклепки включают L3, LY1, LY10, LF10 (используйте новые марки материалов, соответствующие национальным стандартным правилам для заклепок).
Поскольку в процессе клепки заклепка должна выдерживать значительные пластические деформации, материал заклепки должен обладать хорошей пластичностью. По этой причине заклепки, изготовленные методом холодной штамповки, должны быть отожжены. В соответствии с требованиями, заклепки должны проходить испытания на кузнечную прочность и механическую прочность, например, на растяжение и сдвиг. Поверхность заклепки не должна иметь дефектов, влияющих на ее использование.
2. Диаметр заклепки
Диаметр заклепки определяется толщиной соединительной пластины в соответствии с требованиями к прочности конструкции, и зависимость между толщиной пластины δ и диаметром заклепки d обычно следующая:
1) Для однорядных и двухрядных нахлесточных соединений d≈2δ.
2) Для однорядных и двухрядных соединений накладных пластин d≈(1,5~1,75)δ.
Диаметр заклепки также можно определить по таблице 7-2.
Таблица 7-2 Определение диаметра заклепки (единицы измерения: мм)
Толщина пластины δ | 5~6 | 7~9 | 9.5 ~12.5 | 13 ~18 | 19 ~24 | >25 |
Диаметр заклепки d | 10 ~12 | 14 ~25 | 20 ~22 | 24~27 | 27~30 | 30 ~36 |
При определении диаметра заклепки в зависимости от толщины листа необходимо руководствоваться следующими принципами:
1) При притирке пластин одинаковой толщины берите толщину более толстой пластины.
2) При притирке пластин со значительной разницей в толщине берите толщину более тонкой пластины.
При соединении пластин и профилей берите среднюю толщину обоих.
Общая толщина соединяемых деталей не должна превышать 5-кратный диаметр заклепки.
3. Длина заклепки
Качество клепки напрямую зависит от выбранной длины стержня заклепки. Если стержень слишком длинный, головка заклепки будет слишком большой, и стержень, скорее всего, погнется; если стержень слишком короткий, будет недостаточное усилие, и головка заклепки не будет полностью сформирована, что сильно повлияет на прочность и герметичность заклепки.
Длина заклепки должна определяться с учетом таких факторов, как общая толщина соединяемых деталей, зазор между отверстием и диаметром стержня, а также метод клепки. Длина стержня заклепки со стандартным диаметром отверстия может быть рассчитана по следующей формуле:
Заклепка с круглой головкой L = (1,65 ~ 1,75)d + 1,1∑δ
Потайная заклепка L = 0,8d + 1,1∑δ
Полупотайная заклепка L = 1,1d + 1,1∑δ
- L - длина стержня заклепки (мм);
- d - диаметр стержня заклепки (мм);
- Общая длина соединенных частей (∑δ) в мм.
Рассчитанные выше длины заклепок являются приблизительными; фактическую длину стержня заклепки для массового клепания необходимо определить после пробного клепания.
4. Определение диаметра отверстия под заклепку
Посадка между диаметром отверстия под заклепку и заклепкой должна быть определена на основе различных методов холодной и горячей клепки.
При холодной клепке хвостовик нелегко расстроить, и для обеспечения прочности соединения диаметр отверстия должен быть близок к диаметру хвостовика.
При горячей клепке заклепка расширяется и утолщается под воздействием тепла, но остается податливой; чтобы облегчить вставку, разница между диаметром отверстия и диаметром хвостовика должна быть немного больше. Стандартные диаметры отверстий см. в таблице 7-3. При плотной клепке многослойных пластин диаметр отверстия должен быть уменьшен на 1~2 мм в соответствии со стандартным размером отверстия, а для цилиндрических деталей отверстия должны быть просверлены до гибки, а диаметр отверстия должен быть уменьшен на 1~2 мм от стандартного, чтобы обеспечить развертку при сборке.
Таблица 7-3 Стандартные диаметры отверстий под заклепки (единицы измерения: мм)
Диаметр стержня заклепки | Диаметр отверстия d0 | |
Точная сборка | Грубая сборка | |
3.5 | 3.6 | 3.9 |
4 | 4.1 | 4.5 |
5 | 5.2 | 5.5 |
6 | 6.2 | 6.5 |
8 | 8.2 | 8.5 |
10 | 10.3 | 11 |
12 | 12.4 | 13 |
14 | 14.5 | 15 |
16 | 16.5 | 17 |
18 | 19 | |
20 | 21.5 | |
22 | 23.5 | |
24 | 25.5 | |
27 | 28.5 | |
30 | 32 | |
36 | 38 |
V. Часто используемое клепальное оборудование и инструменты
1. Заклепочный пистолет
Заклепочный пистолет - основной инструмент для сварки. Также известен как пневматический пистолет, как показано на рисунке 7-13. В основном он состоит из рукоятки 2, корпуса пистолета 4, выключателя 3 и трубчатого соединителя 1. В отверстие на переднем конце корпуса пистолета можно установить различные клепальные матрицы или пуансоны для выполнения заклепочных или штамповочных работ. В процессе использования матрица обычно привязывается к рукоятке тонкой стальной проволокой, чтобы предотвратить выскальзывание поршня, когда матрица отсоединяется от корпуса пистолета при его подъеме.
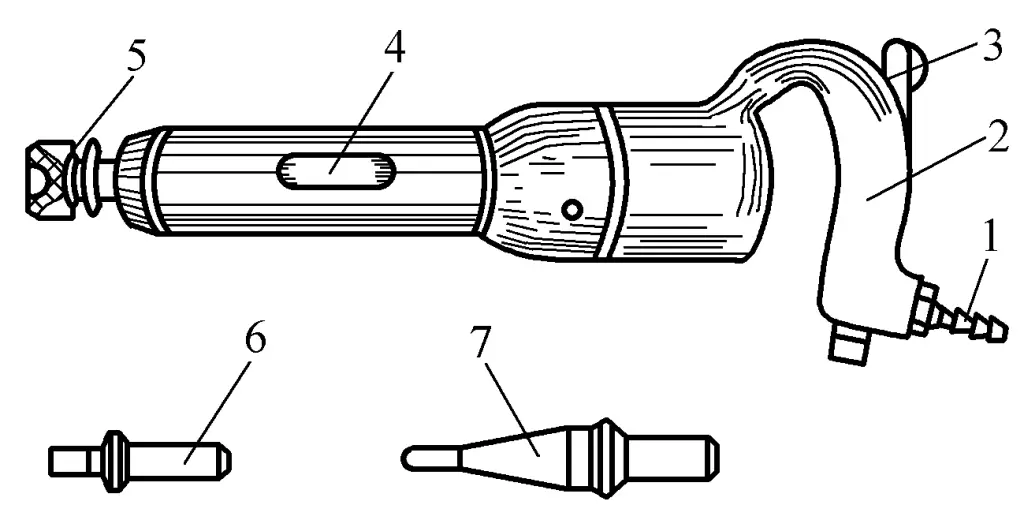
1-трубчатый коннектор
2-ручка
3-выключатель
Четырехствольный корпус
5-Die
6 Заклепка с плоской головкой
7-Панч
Перед использованием заклепочного пистолета впрысните небольшое количество машинного масла в воздухозаборник, чтобы корпус пистолета был хорошо смазан во время работы, затем выдуйте грязь из шланга сжатого воздуха и подсоедините его к шланговому разъему заклепочного пистолета. Объем всасываемого воздуха контролируется клапаном регулировки давления, а давление сжатого воздуха обычно составляет 0,4~0,6 МПа. Заклепочный пистолет компактен, прост в эксплуатации и может выполнять различные неизвестные задачи по клепке, но он очень шумный во время работы.
2. Клепальный станок
В отличие от заклепочного пистолета, заклепочный станок - это специализированное оборудование, использующее гидравлическое или пневматическое давление для пластической деформации стержня гвоздя с целью формирования головки заклепки. Он имеет два механизма: заклепочный и верхний штифт. Благодаря высокому и равномерному давлению, создаваемому клепальной машиной, качество и прочность заклепок высоки, и они работают без шума.
Существует два типа клепальных машин: стационарные и мобильные. Стационарные клепальные машины имеют высокую эффективность производства, но более дорогие, поэтому подходят только для профессионального производства; мобильные клепальные машины гибкие и широко используются, доступны в гидравлическом, пневматическом и электрическом типах.
Гидравлический клепальный станок использует гидравлические принципы для клепки, как показано на рисунке 7-14. Она состоит из рамы 1, поршня 5, вогнутой головки 3, верхнего штифта вогнутой головки 2 и буферной пружины 9. Когда гидравлическое масло поступает в гидроцилиндр через патрубок 8, оно толкает поршень вниз. Нижний конец поршня имеет вогнутую головку 3, и заклепка вдавливается между верхней и нижней вогнутыми головками, образуя головку заклепки.
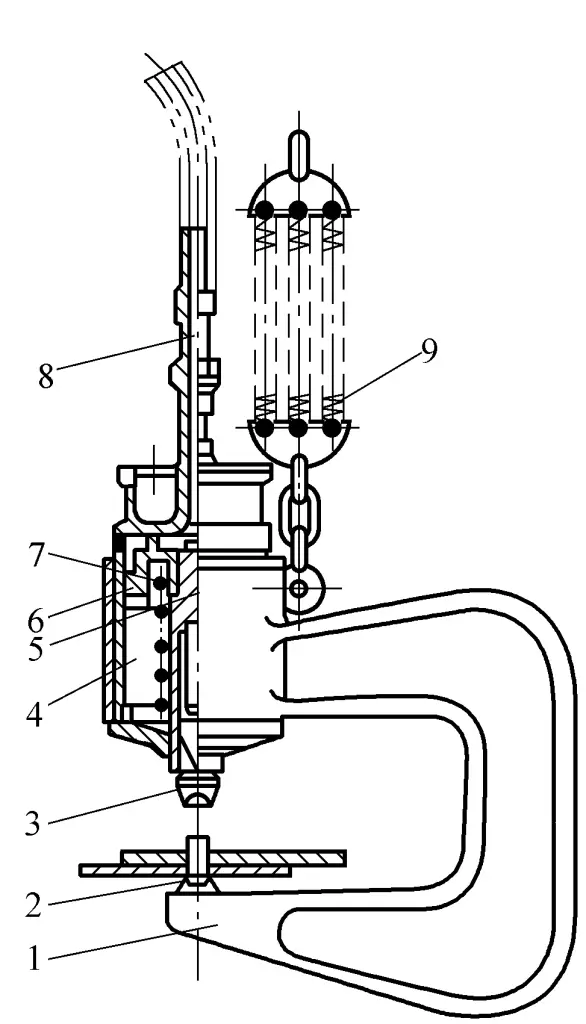
1-рама
2- Верхний штифт с вогнутой головкой
3-Вогнутая головка
4-Гидравлический цилиндр
5-поршневой
6-Уплотнительная прокладка
7-весна
8-трубный фитинг
9-буферная пружина
Когда поршень движется вниз, пружина 7 сжимается и деформируется. После завершения клепки поршень возвращается в исходное положение под действием упругости пружины. Функция уплотнительной прокладки 6 заключается в предотвращении утечки масла из поршня. Вся клепальная машина может перемещаться с помощью крана, а для предотвращения вибрации во время клепки пружина на подъемном кольце может использоваться для амортизации.
VI. Процесс клепки
В зависимости от температуры клепка делится на холодную и горячую; в этом разделе рассказывается в основном о горячей клепке.
1. Холодная клепка
Клепка при комнатной температуре называется холодной клепкой. Холодная клепка требует, чтобы заклепка обладала хорошей пластичностью. При использовании заклепочного станка для холодной клепки максимальный диаметр заклепки не должен превышать 25 мм. При использовании заклепочного пистолета для холодной клепки диаметр заклепки обычно не превышает 12 мм.
2. Горячая клепка
Клепка после нагрева заклепки называется горячей клепкой. После нагрева прочность хвостовика заклепки уменьшается, пластичность увеличивается, и головка заклепки легко формируется. Внешнее усилие, необходимое для клепки, значительно снижается по сравнению с холодной клепкой, поэтому горячая клепка обычно используется для заклепок большого диаметра или массовой клепки.
При горячей клепке, помимо формирования герметичной головки заклепки, один конец хвостовика заклепки также разгибается, чтобы заполнить отверстие заклепки. После охлаждения заклепка уменьшается в длине, оказывая достаточное давление на склепываемые детали, делая шов более плотным и, таким образом, достигая достаточной прочности соединения.
Основной процесс горячей клепки заключается в следующем:
(1) Крепление клепаных деталей и рассверливание отверстий под заклепки
При сборке клепаных деталей необходимо выровнять отверстия на пластинах и затянуть их болтами соответствующих спецификаций. Распределение болтов должно быть равномерным, а их количество должно составлять не менее четверти от количества отверстий под заклепки. После затяжки болтов поверхности швов должны быть плотными.
При сборке деталей из-за ошибок обработки могут возникнуть некоторые несоосности отверстий, поэтому перед клепкой необходимо рассверлить отверстия под заклепки с помощью корректирующего пуансона или развертки, чтобы обеспечить концентричность и плавность клепки. Отверстия под заклепки, имеющие припуски, оставленные при предварительной обработке, следует рассверливать за один прием. Последовательность рассверливания такова: сначала рассверливают отверстия без затянутых болтов, затем вставляют болты после рассверливания, и, наконец, удаляют оригинальные болты и рассверливают отверстия.
(2) Нагрев заклепки
При клепке с помощью заклепочного пистолета заклепку необходимо нагреть до 1000~1100℃. Во время нагрева заклепка нагревается до оранжево-желтого цвета (около 900~1100℃), затем переводится на медленный огонь для тления, что позволяет равномерно нагреть заклепку по всей длине и внутри, после чего хорошо нагретую заклепку можно вынуть для клепки (перегретые или недостаточно нагретые во время нагрева заклепки использовать нельзя).
(3) Захват и установка заклепки
Бросайте заклепку точно, ловите заклепку уверенно, быстро вставляйте заклепку в отверстие после ловли, стремясь завершить клепку при высокой температуре.
(4) Верхняя заклепка
Качество верхней заклепки напрямую влияет на качество клепки. Форма и характеристики вогнутой головки на верхней ручке должны соответствовать головке готовой заклепки. Вогнутость" должна быть более мелкой, а заклепывание верхней части должно быть сильным, чтобы сформированная головка заклепки плотно прилегала к поверхности пластины.
(5) Клепка
Первоначально при клепке используется прерывистая подача воздуха, а после того, как гвоздь расстроен, объем воздуха увеличивается, чтобы выковать обнаженный гвоздь в форме головки заклепки. После того как головка заклепки сформирована, заклепочный пистолет слегка наклоняют и поворачивают вокруг головки заклепки на один оборот, чтобы заставить головку заклепки плотно прилегать к поверхности детали, но чрезмерный наклон не допускается, чтобы не повредить поверхность детали с вогнутой головкой. Как показано на рисунке 7-15.
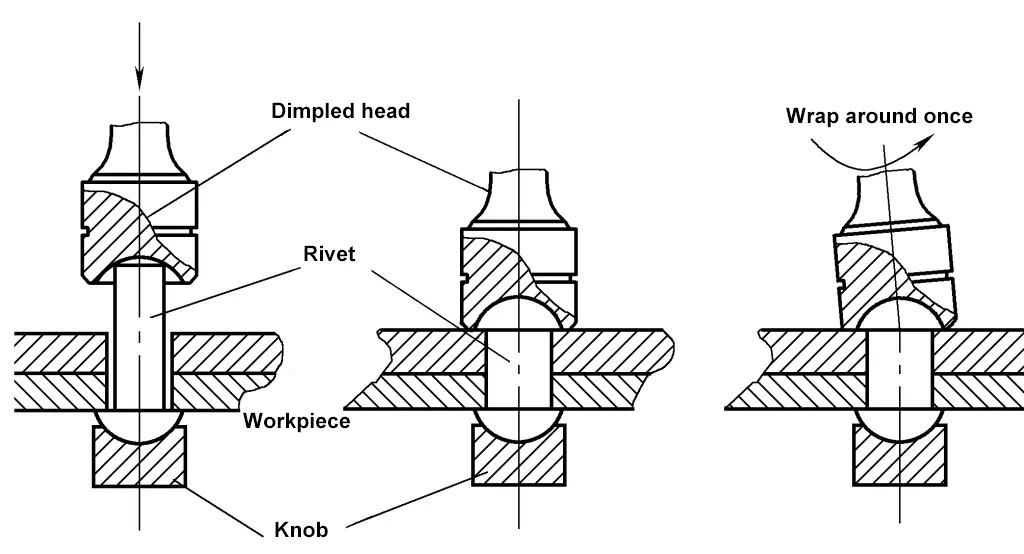
Для обеспечения качества клепки давление сжатого воздуха должно быть не менее 0,5 МПа; конечная температура клепки должна составлять 450~600℃. Если конечная температура клепки слишком высока, она уменьшит начальное напряжение гвоздевого стержня, не позволяя заклепанным компонентам быть полностью затянутыми; если конечная температура клепки слишком низкая, заклепка станет хрупкой.
Поэтому процесс горячей клепки должен быть завершен как можно быстрее в течение короткого времени. В конструкциях с высокими требованиями к герметичности швов после клепки необходимо выполнить затяжку швов. После завершения клепки следует проверить качество каждой заклепки в отдельности, а те, что оказались ослабленными и непоправимыми, выбить зубилом и заклепать заново.
Прикусной сустав
I. Определение структурной формы и размера прикусного шва
1. Характеристики укуса по шву
Закусывание шва - это метод соединения, при котором края соединяемых деталей сгибаются под определенным углом, сцепляются и затем прижимаются друг к другу. Шовные соединения достаточно прочны, имеют хорошую плотность шва, предъявляют меньшие требования к оборудованию и инструментам и просты в исполнении. Швовые соединения часто используются в конструкциях из металлических листов толщиной менее 2 мм, например, в широко используемых проектах трубопроводов, где швы во многих местах заменяют пайку.
По форме соединения швы подразделяются на одношовные, двухшовные и комбинированные; по форме шва - на плоские, угловые и вертикальные; по расположению шва - на продольные и поперечные.
Соединение швов обычно выполняется вручную или с помощью механического оборудования. При единичном или мелкосерийном производстве ручная расшивка швов широко используется для изготовления небольших изделий из листового металла, отличающихся низкой стоимостью и удобством.
Для массового производства используется механическая обрезка швов, которая по сравнению с ручной имеет такие преимущества, как меньший шум, лучшее качество шва, меньшая трудоемкость для рабочих и более высокая эффективность производства (может быть увеличена в 8~25 раз), но требует больших единовременных инвестиций в оборудование. Если условия позволяют, следует как можно чаще использовать механическую нарезку швов.
2. Формы шва
В зависимости от структуры и требований, предъявляемых к деталям из листового металла, используются различные формы швов. Общие формы швов приведены в таблице 7-4.
Таблица 7-4 Формы шва
Название шва | Упрощенная диаграмма | Размер припуска на шов | Использование | |
Плоский шов | Плоский обычный шов | ![]() | Припуск на швы - 3 раза Ширина шва | Используется для соединения цилиндрических, конических и прямоугольных труб. Используйте гладкий шов, если шов должен быть прикреплен к плоской поверхности или должен быть герметичным; используйте двойной шов, если требуется повышенная прочность и герметичность. |
Плоский гладкий шов | ![]() | |||
Плоский подвесной шов | ![]() | |||
Плоский двойной шов | ![]() | Припуски на швы в 5 раз больше ширины шва | ||
Угловой шов | Угловой одинарный шов | ![]() | Припуски на швы в 3 раза больше ширины шва | Угловой шов, используемый при изготовлении локтевых отводов |
Угловой двойной шов | ![]() | |||
Угловой комбинированный шов | ![]() | Припуски на швы в 4 раза больше ширины шва | ||
Вертикальный шов | Вертикальный одинарный шов | ![]() | Припуски на швы в три раза больше ширины шва | Используется для различных переходных соединений при соединении отводов, колен и переходе от круглого к другим сечениям |
Вертикальный двойной шов | ![]() | Припуски на швы в пять раз больше ширины шва |
II. Инструменты и их использование для наложения швов
1. Инструмент для обработки швов
Инструмент для выполнения швов, как показано на рисунке 7-16.
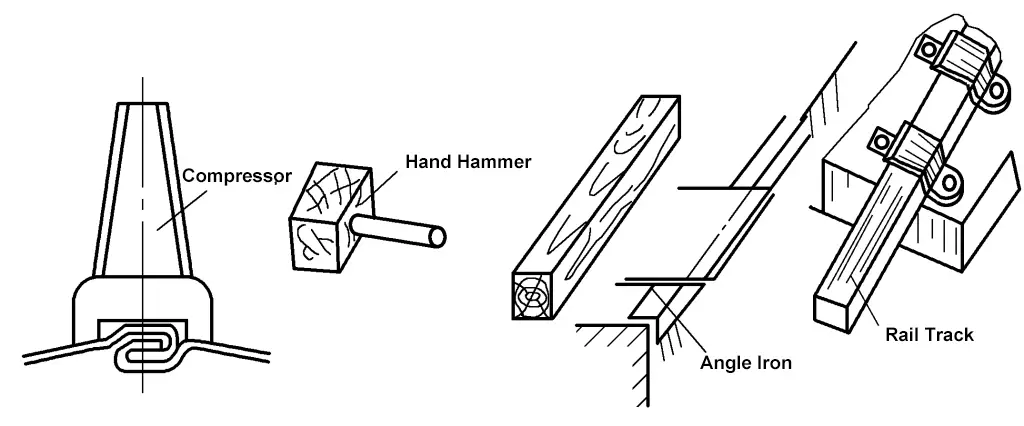
2. Шаги при выполнении операции заделки швов
Наложение швов путем откусывания обычно выполняется вручную, а общие действия выглядят следующим образом:
1) Рассчитайте припуски на швы в зависимости от типа шва.
2) Нарисуйте линию сгиба шва на краю пластины.
3) Согните край пластины по линии сгиба.
4) Закрепите и прижмите две стороны вместе, чтобы завершить шов.
3. Плоское одношовное соединение
Плоские одинарные швы обычно используются для соединения пластин толщиной 0,2~1,5 мм, при этом ширина шва зависит от толщины пластины. При толщине пластины 0,2~0,5 мм ширина шва составляет 3~5 мм; при толщине пластины 0,75~1,5 мм ширина шва составляет 5~8 мм. Припуск на плоский одинарный шов в три раза больше ширины шва. Процесс обработки швов выглядит следующим образом:
1) Определите ширину шва, исходя из толщины листа, и сделайте припуск на шов, в три раза превышающий ширину шва.
2) Нарисуйте линию сгиба шва на краю пластины (один край на ширине шва, другой край - на удвоенной ширине шва).
3) Совместите линию сгиба края пластины с углом или краем квадратного бруска и ударами киянки согните его под прямым углом, как показано на рис. 7-17a.
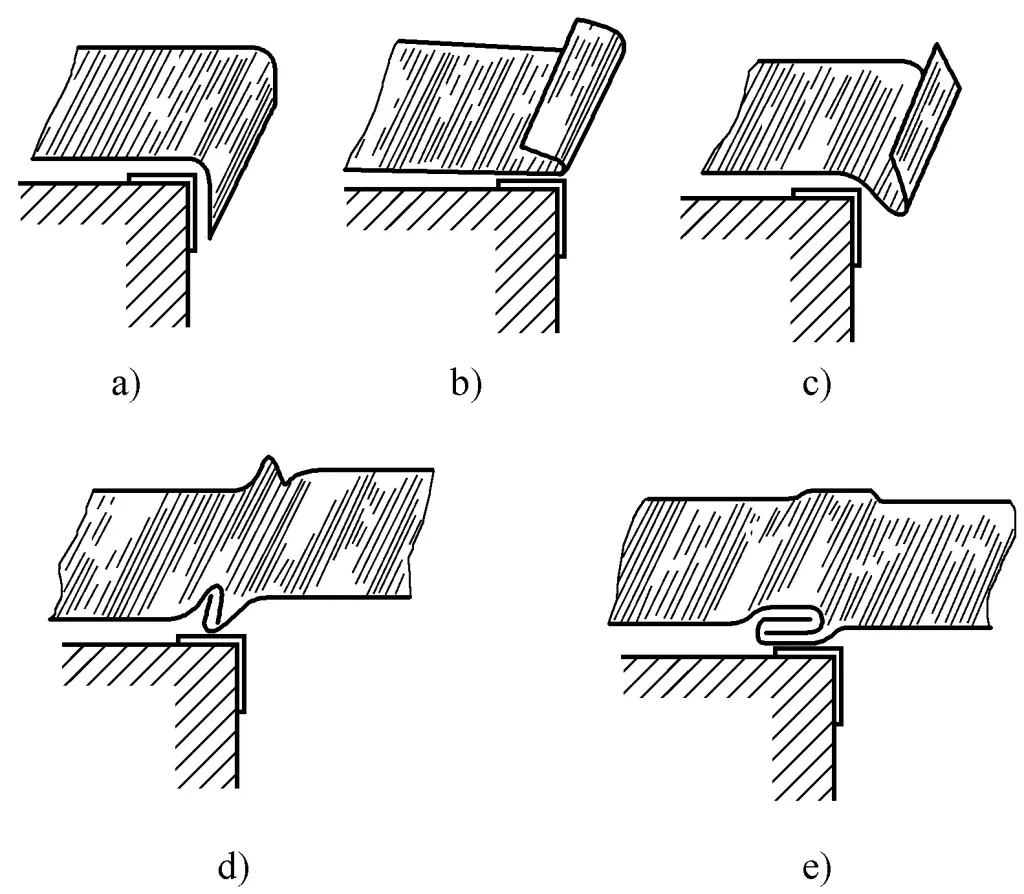
4) Переверните лист и с помощью киянки дополнительно согните край листа, как показано на рис. 7-17b. Обратите внимание, что при сгибании следует оставлять зазор, превышающий толщину листа, иначе другой край невозможно будет вставить и соединить.
5) Передвиньте лист вперед на ширину, немного превышающую ширину загнутого края, ударьте по нему киянкой, чтобы загнуть примерно на 45°, как показано на рис. 7-17c. Другой край делается таким же образом.
6) Скрепите два края вместе и нанесите удар, чтобы сжать, как показано на рисунках 7-17d и 7-17e. Если требуется плоский внутренний или внешний шов, его можно выдавить с помощью шовного пресса, как показано на рис. 7-18a, или с помощью края платформы или квадратного бруска, как показано на рис. 7-18b.
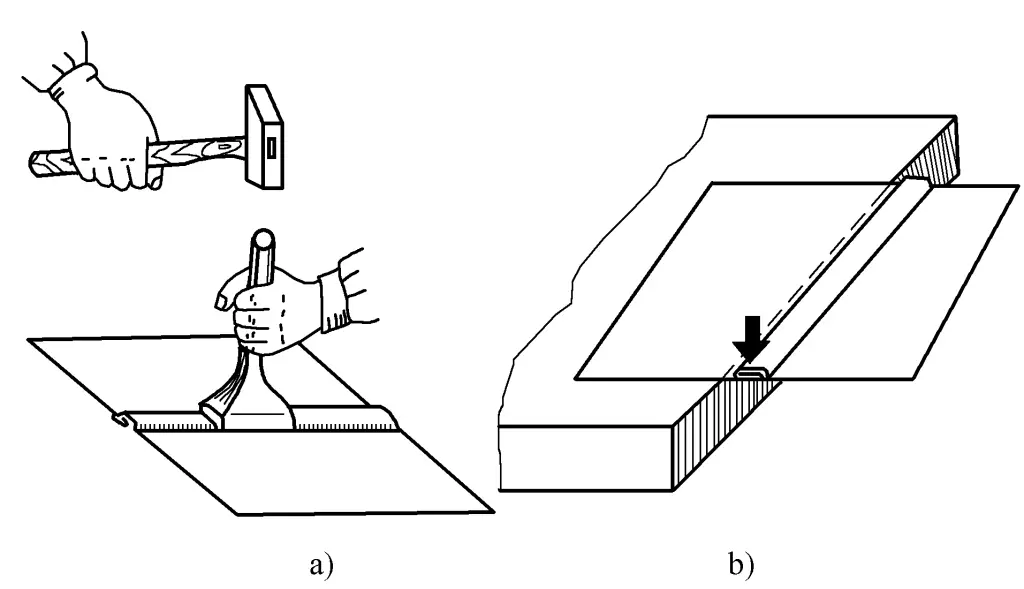
a) Выдавливание с помощью пресса для швов
b) Выдавливание с помощью края платформы, квадратного бруска
4. Угловой шов
Ширина углового шва определяется толщиной листа, как правило, в пределах 3~8 мм, при этом для тонких листов используется меньшее значение, а для толстых - большее. Припуск на соединение углового шва в три раза превышает ширину шва. Процесс производства выглядит следующим образом:
1) Определите ширину шва, исходя из толщины листа, освободите припуск на шов и проведите линию сгиба по краю листа (одна сторона - ширина шва, другая - вдвое больше ширины шва).
2) Совместите линию сгиба с платформой или краем квадратного бруска, согните его под прямым углом с помощью киянки, затем переверните пластину и еще больше согните ее ударами киянки (оставляя зазор больше толщины пластины), как показано на рис. 7-19a и 7-19b.
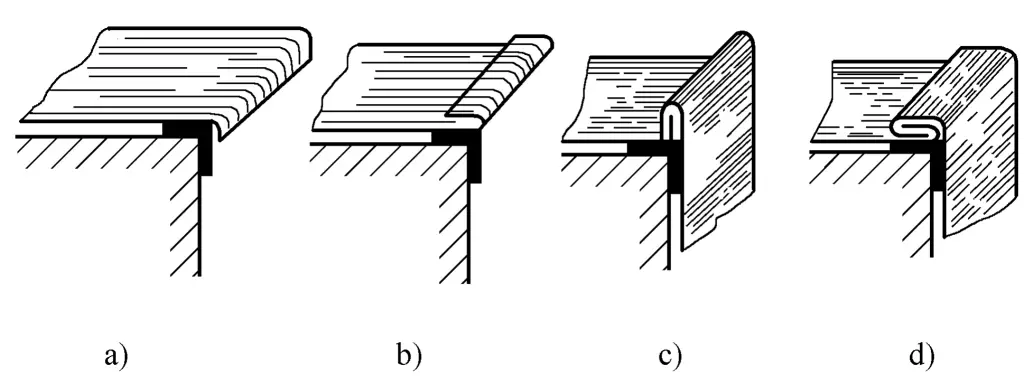
3) Согните еще одну пластину под прямым углом, затем переверните ее так, чтобы уже согнутая пластина зацепилась за прямой край, как показано на рис. 7-19c.
4) Согните и прижмите зацепленную деталь с прямым краем, как показано на рисунке 7-19d.
Резьбовое соединение
I. Структура и общие инструменты резьбового соединения
Разъемное неподвижное соединение, образованное с помощью резьбовых деталей. К распространенным резьбовым соединениям относятся болтовое соединение, соединение шпилькой с двойной головкой и винтовое соединение, которые широко используются благодаря простоте конструкции, надежности крепления, быстроте и удобству монтажа и демонтажа, а также экономичности. Существует множество типов и спецификаций резьбовых крепежных элементов, но их структура, форма и размеры стандартизированы и приведены в соответствующих стандартах.
Среди распространенных инструментов - отвертки, разводные ключи, торцевые ключи, шестигранные ключи, торцевые ключи и гаечные ключи.
II. Процесс резьбового соединения
1. Болтовое соединение
Болтовое соединение состоит из болтов, гаек и шайб, в основном используется для соединений, где детали тонкие и могут образовывать сквозные отверстия.
Существует два типа болтовых соединений: одно - соединение, выдерживающее осевую растягивающую нагрузку, допускающее определенный зазор между стержнем натяжного болта и стенкой отверстия; другое - соединение сдвигового болта, выдерживающее радиальную силу, требующее строгого диаметра отверстия, требующее рассверливания и использующее переходную или интерференционную посадку с основной системой отверстий для стержневой части болта без резьбы. Поэтому оно может точно фиксировать относительное положение соединяемых деталей и выдерживать ножницы и сдавливания, вызванного боковыми нагрузками, как показано на рис. 7-20.
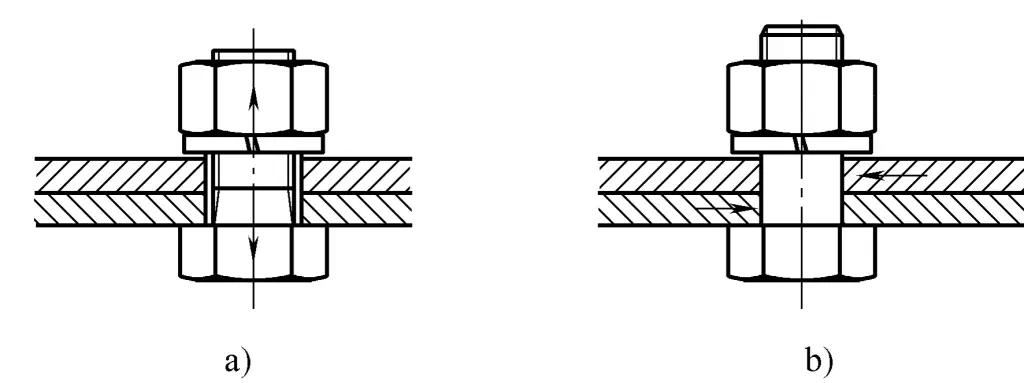
a) Соединение с натяжным болтом
b) Болтовое соединение со сдвигом
(1) Метод монтажа болтового соединения
При выполнении болтового соединения спецификации и количество болтов, гаек и шайб должны определяться исходя из толщины и диаметра отверстий соединяемых деталей. Как правило, длина болта равна суммарной толщине соединяемых деталей, гайки и шайбы, плюс припуск 1~2t (t - размер шага).
При соединении болт проходит через сквозное отверстие на соединяемой детали, а после установки шайбы затягивается гайка. Чтобы болт не вращался вместе с гайкой во время затяжки, используйте гаечные ключи, чтобы держать болт и гайку отдельно и вращать в противоположных направлениях, пока не будет достигнута требуемая затяжка.
При затяжке необходимо контролировать момент затяжки; слишком большой момент может привести к удлинению болтов, поломке и деформации соединяемых деталей; слишком малый момент не может обеспечить требования и надежность соединения во время эксплуатации.
(2) Последовательность сборки сгруппированных болтов
При затяжке сгруппированных болтов необходимо соблюдать определенный порядок и постепенно затягивать их поэтапно (обычно в три этапа), чтобы избежать несоответствия в затяжке, неравномерной нагрузки на болты, деформации крепежа или даже разрушения отдельных болтов под воздействием высокой нагрузки. На рисунке 7-21 показана последовательность затяжки болтов в различных сборочных позициях.
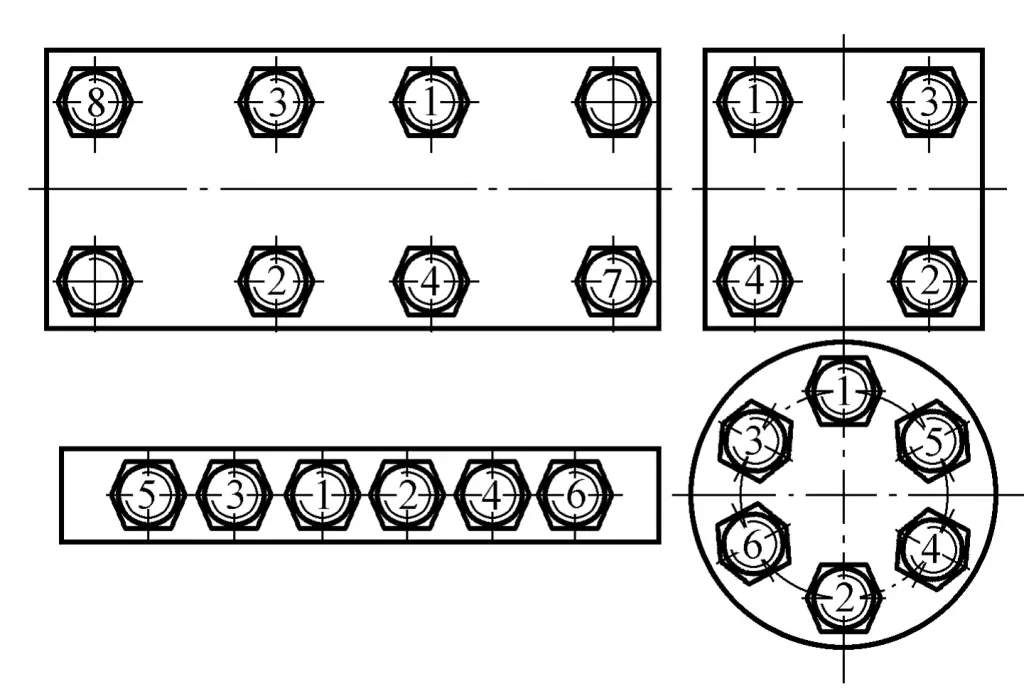
2. Шпилечное соединение
Двусторонние шпильки используются в основном в тех случаях, когда детали слишком толстые для болтовых соединений. При соединении один конец двусторонней шпильки ввинчивается в резьбу глухого отверстия, а другой конец проходит через сквозное отверстие соединяемой детали, затем устанавливается шайба и затягивается гайка. Для демонтажа открутите гайку, чтобы разъединить соединенные детали, как показано на рисунке 7-22.
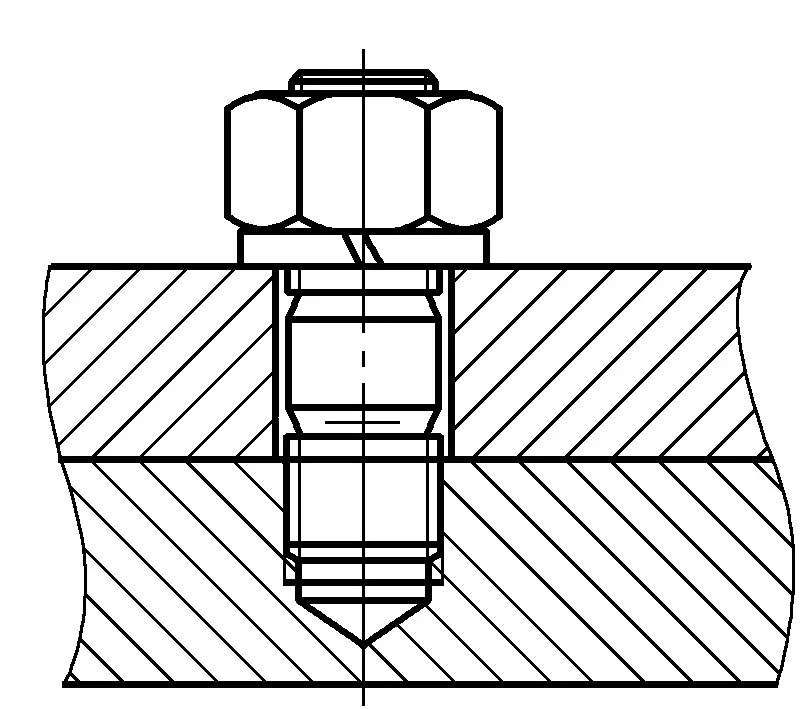
(1) Способ монтажа двусторонних шпилек Поскольку двусторонние шпильки не имеют фиксированного конца, их нельзя напрямую затягивать с помощью ввинченного конца. Обычно используется метод затягивания двойными гайками, обращенными друг к другу, или винтом, обращенным к шпильке, как показано на рис. 7-23.
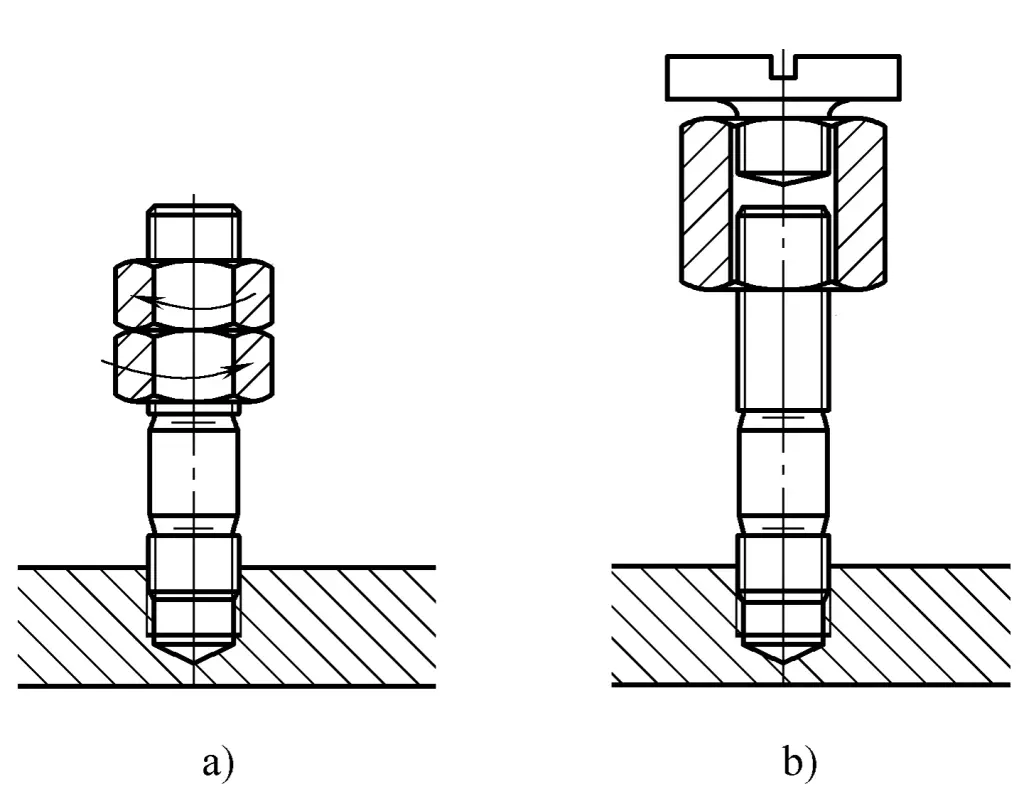
a) Двойные гайки, обращенные друг к другу
b) Винт, обращенный к шпильке
(2) Меры предосторожности при сборке
1) Контактные поверхности шпилек и резьбовых отверстий должны быть чистыми и сухими. Затяните болт вручную до конца резьбы. Если болт не закручивается, не затягивайте его с усилием гаечным ключом, чтобы не повредить резьбу.
2) Посадка между двухсторонней шпилькой и резьбовым отверстием должна быть достаточно плотной, чтобы шпилька не ослабевала при снятии или установке гайки. Резьбовой конец шпильки должен иметь переходную посадку во время обработки, чтобы обеспечить определенное вмешательство в средний диаметр резьбы после установки.
3) Центральная линия шпильки должна быть перпендикулярна поверхности соединяемого компонента.
3. Меры по предотвращению ослабления резьбовых соединений
Резьбовые соединения обладают определенной самоблокировкой и не ослабевают сами по себе при статических нагрузках и незначительных изменениях рабочей температуры. Однако в случае ударных нагрузок, переменных нагрузок или значительных изменений рабочей температуры может произойти ослабление. Чтобы обеспечить безопасность и надежность соединения и избежать несчастных случаев, вызванных ослаблением, необходимо принять определенные меры против ослабления.
К распространенным мерам по борьбе с ослаблением относятся механическое ослабление и повышение сопротивления трению.
(1) Механическая защита от ослабления
1) Шплинт против ослабления. Как показано на рисунке 7-24, пропустите шплинт через прорезь на гайке и отверстие на болте, затем загните хвостовую часть, чтобы предотвратить вращение болта и гайки относительно друг друга, таким образом достигается цель предотвращения ослабления. Шплинт против ослабления обычно используется в высокоскоростных машинах, подверженных вибрационным нагрузкам.
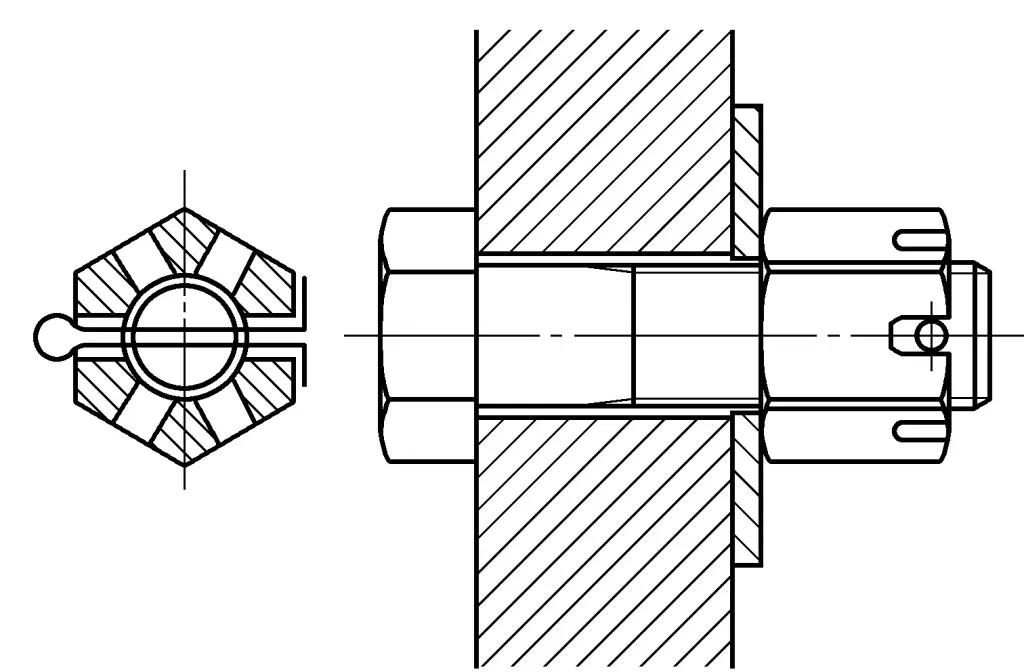
2) Остановите откручивание шайбы. Как показано на рисунке 7-25. Вставьте внутренние крылья стопорной шайбы в осевой паз на конце внешней резьбовой части, затяните гайку, затем отогните внешние крылья шайбы в паз гайки, тем самым заблокировав гайку. Используется для предотвращения ослабления в резьбовых соединениях типа вал.

3) Стопорная шайба против ослабления. Как показано на рисунке 7-26. После затягивания гайки отогните одинарные или двойные ушки стопорной шайбы, чтобы они плотно прилегали к краям детали и гайки, предотвращая ослабление гайки. Ее можно использовать только там, где есть место для размещения загнутых ушек.
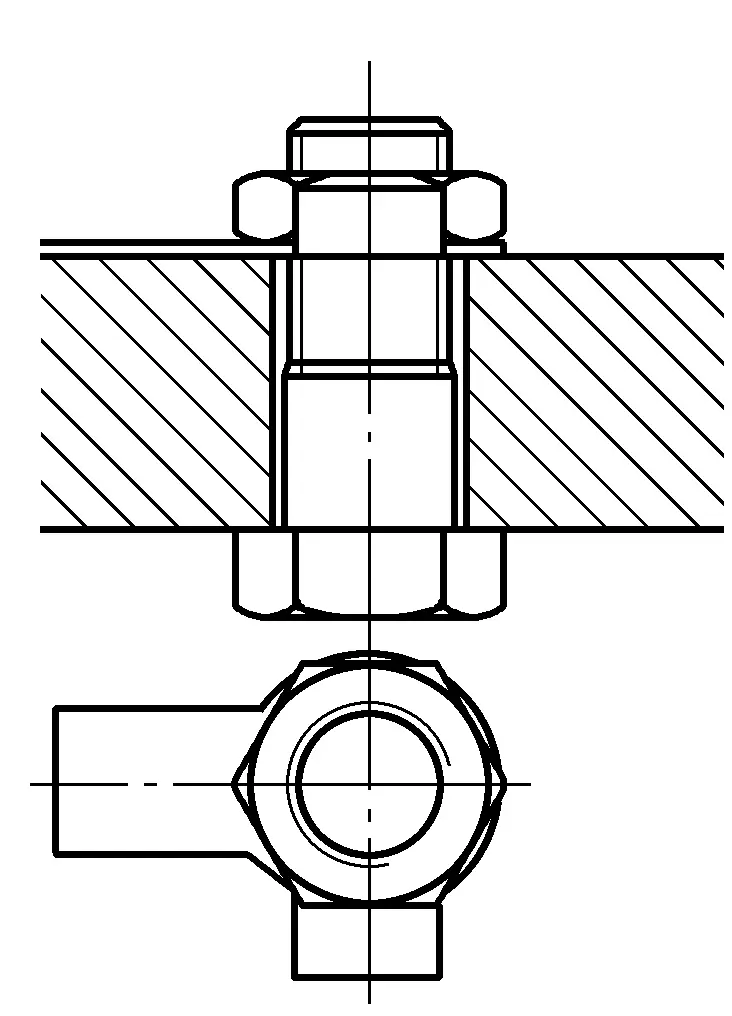
(2) Увеличение трения для предотвращения ослабления
Как показано на рис. 7-27, для предотвращения отвинчивания следует приложить дополнительное осевое усилие для увеличения трения между затянутыми поверхностями резьбы, в основном используя методы пружинных шайб и двойных гаек. Однако эффективность предотвращения ослабления ненадежна и подходит только для ситуаций с небольшими ударами и вибрацией.

a) Пружинная шайба для предотвращения ослабления
b) Двойная гайка для предотвращения ослабления
c) Повышенное трение на резьбовых сопрягаемых поверхностях
Обучение навыкам подключения
I. Схема заготовки для плоской сварки со скошенным швом
Схема заготовки для плоской сварки косым швом показана на рисунке 7-28.
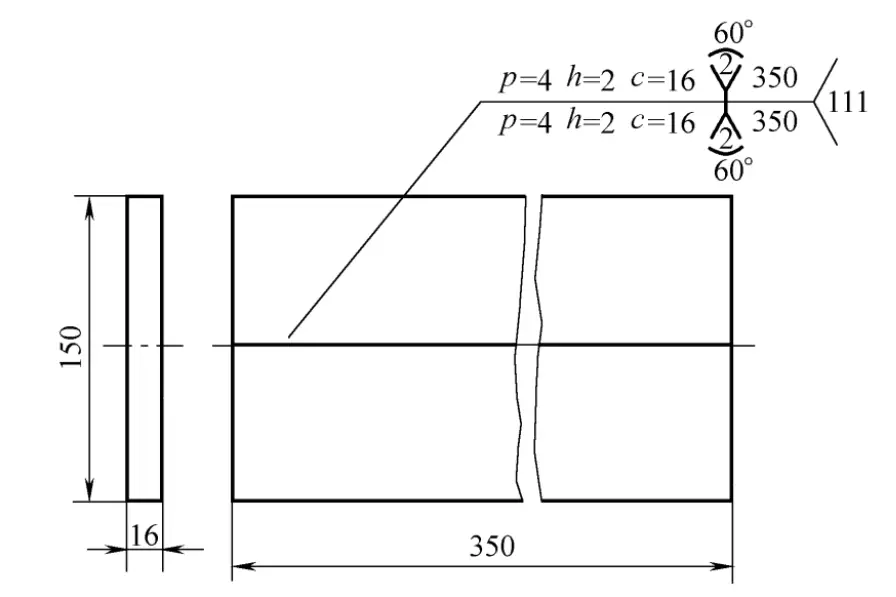
Технические требования
- Заготовка должна использовать двухстороннюю двухслойную сварку, при этом последовательность сварки должна быть симметричной изнутри наружу.
- Каждый внешний сварной шов должен включать в себя как минимум одно соединение, а форма соединения должна соответствовать форме сварного шва.
- Все размеры сварных швов должны соответствовать установленным требованиям и быть эстетически привлекательными, прямыми и не иметь дефектов, таких как подрезы, шлаковые включения и пористость.
- После сварки тщательно удалите весь шлак и брызги. Если заготовка сильно деформирована, ее необходимо выпрямить.
II. Выбор технологических характеристик для стыковой плоской сварки деталей со скосом
1. Выберите форму скоса соединения
Для соединений толстых листов скос должен позволять дуге проникать глубоко в корень шва, обеспечивая проплавление корня и облегчая удаление шлака, достижение достаточной прочности и формирование качественного шва. Выбранный тип скоса должен отвечать следующим условиям: обеспечивать проплавление шва; коническая форма удобна для обработки; высокая производительность, экономия сварочных прутков; меньшая деформация свариваемой детали после сварки. Поэтому для детали, показанной на рис. 7-28, выгоднее использовать Х-образный скос.
2. Выберите диаметр электрода для Х-образного скоса
Поперечное сечение радиальное, и количество присадочного металла в наружном шве намного больше, чем во внутреннем. При выборе электродов диаметр внешнего электрода должен быть больше диаметра внутреннего шва. Как правило, для внутреннего шва можно выбрать электрод диаметром 4,0 мм или использовать электрод диаметром 4,0 мм для обоих слоев.
3. Выбор тока электрода
При сварке электродом диаметром 4,0 мм сварочный ток может быть выбран в диапазоне 160~210 А, при этом сварочный ток для внешнего шва должен быть немного выше, чем для внутреннего слоя. При сварке внешнего шва электродом диаметром 5,0 мм