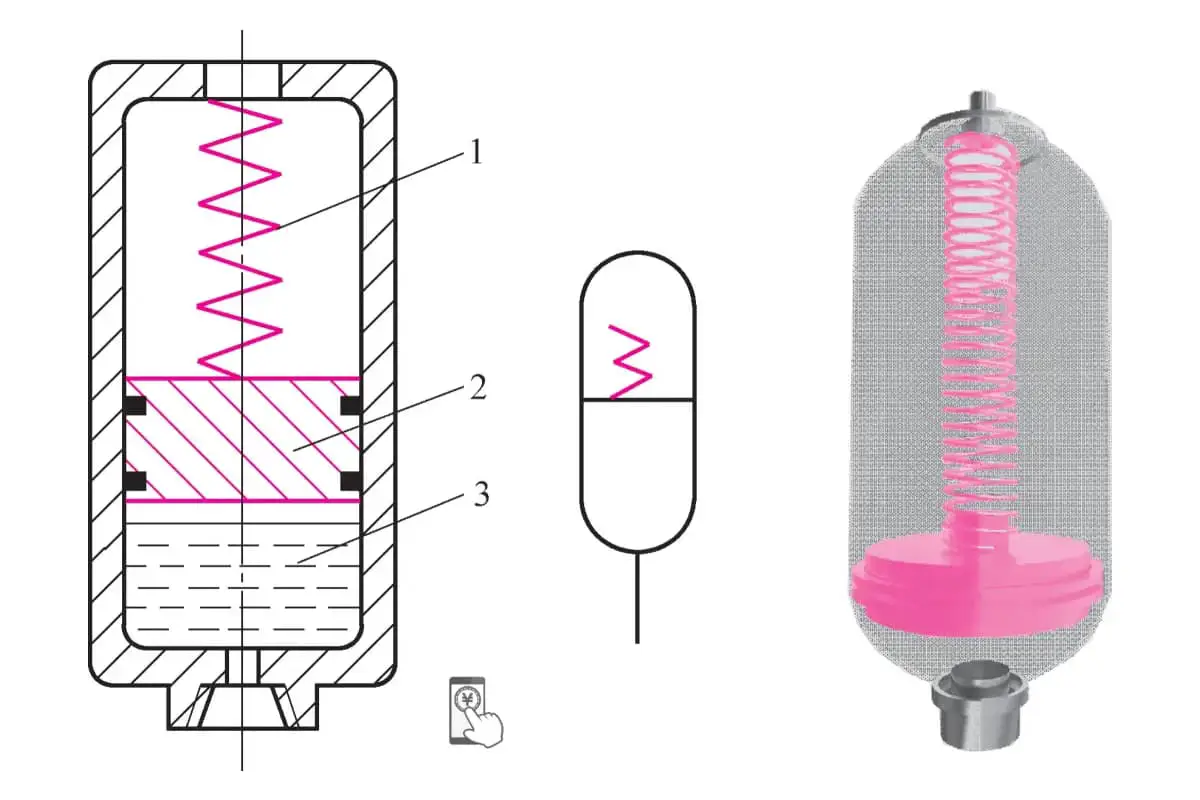
1. Процесс подгонки файлов
Операция по использованию метода подачи для приведения двух или более подходящих деталей в соответствие с заданными техническими требованиями называется подгонкой напильником.
(1) Выбор эталонных деталей для подгонки напильников
1) Определение эталонных деталей для подгонки напильников
Эталонные детали для подгонки напильников относятся к "шаблонной детали", выбранной путем анализа процесса перед подгонкой напильников среди всех деталей для подгонки напильников. Эта деталь после обработки может использоваться в качестве шаблона для измерения, взаимодействуя с измерительными инструментами во время подгонки других подходящих деталей для совместного измерения и контроля точности подгонки других подходящих деталей, тем самым точно и быстро выполняя требуемую подгонку. фитинг точность.
2) Принципы выбора эталонных деталей
Эталонные детали должны легче достигать требуемой точности размеров, точности формы и положения, а также шероховатости поверхности путем обработки напильником, чем другие подходящие детали.
Выпуклые детали предпочтительнее использовать в качестве эталонных деталей, поскольку по сравнению с вогнутыми деталями выпуклые детали легче измерять, т.е. легче контролировать их точность путем измерения. Поскольку вогнутые детали имеют внутренние поверхности, измерительные инструменты трудно ввести в них, что делает измерительные операции сложными. Если вогнутые детали легко измерять, их также можно использовать в качестве эталонных деталей для подгонки выпуклых деталей.
(2) Процесс подгонки файлов
1) Подшивка справочных материалов
Процесс подгонки файлов обычно делится на процесс индивидуальной подшивки и процесс корректировки подшивки. Метод индивидуальной обработки напильником описан ранее. Обычно процесс подгонки напильников выглядит следующим образом: сначала напильником обрабатываются эталонные детали. Когда эталонные детали соответствуют требуемой точности размеров, точности формы и положения, а также шероховатости поверхности (шероховатость поверхности эталонных деталей обычно на один класс выше, чем технические требования, указанные в чертежах), обработка заканчивается. При последующей подгонке файлов эталонные детали, как детали-шаблоны, больше не могут обрабатываться.
2) Подшивка других подходящих деталей
Обработайте другие подходящие детали напильником, чтобы удовлетворить требованиям к точности формы и положения и шероховатости поверхности, оставляя припуск на подгонку напильником. Если вогнутая деталь является совпадающей, то для облегчения контроля точности обработки при обработке внутренней поверхности вогнутой детали рекомендуется выбирать соответствующие внешние поверхности вогнутой детали в качестве эталонов измерения; следовательно, опорная поверхность контура вогнутой детали должна обеспечивать более высокую точность формы и положения.
3) Процесс корректировки
Используйте эталонную деталь для сравнения и пробной подгонки других подходящих деталей. Измерьте подходящие детали, используя метод светового зазора или метод мазка красителем, чтобы определить области подгонки подходящих деталей. Затем комбинируйте измерительные инструменты для измерения подходящих деталей, определения припусков на обрезку и постепенной обработки для достижения требуемой точности посадки.
(3) О бесконтактной подгонке
При бесконтактной подгонке, поскольку невозможно использовать эталонные детали (измерительные шаблоны) для прямого измерения подходящих деталей, для достижения требуемой точности подгонки можно только контролировать точность размеров, формы и положения всех подходящих деталей путем тщательных измерений.
Чтобы сделать работу по подгонке напильников более эффективной, необходимо всесторонне проанализировать влияние ошибок формы и положения на функциональные размеры и по возможности использовать эталонные детали в качестве шаблонов для сравнительной работы. Благодаря тщательному наблюдению и точным измерениям выполняются корректировка и пробная подгонка подходящих деталей.
Кроме того, чтобы выполнить удовлетворительную бесконтактную подгонку, необходимо обладать хорошей наблюдательностью и чувствительностью рук во время пробной подгонки. Техника использования острых штангенциркулей может значительно облегчить коррекцию при примерке. Эти навыки требуют изучения, обобщения и накопления опыта.
(4) Об измерении и контроле симметрии в подаче материала
После обработки детали фурнитуры должны соответствовать определенным требованиям к точности, а также к прямолинейности и плоскостности контура.
Для симметричных деталей обычно требуется вращательная подгонка. Если требования к симметрии не соблюдаются при индивидуальной обработке, то после подгонки будет трудно обеспечить требуемую точность, особенно после вращения, где плоскостность контура не может быть обеспечена, как показано на рис. 1. Поэтому порядок обработки должен быть разумно организован, а симметрия контролироваться с помощью измерений.
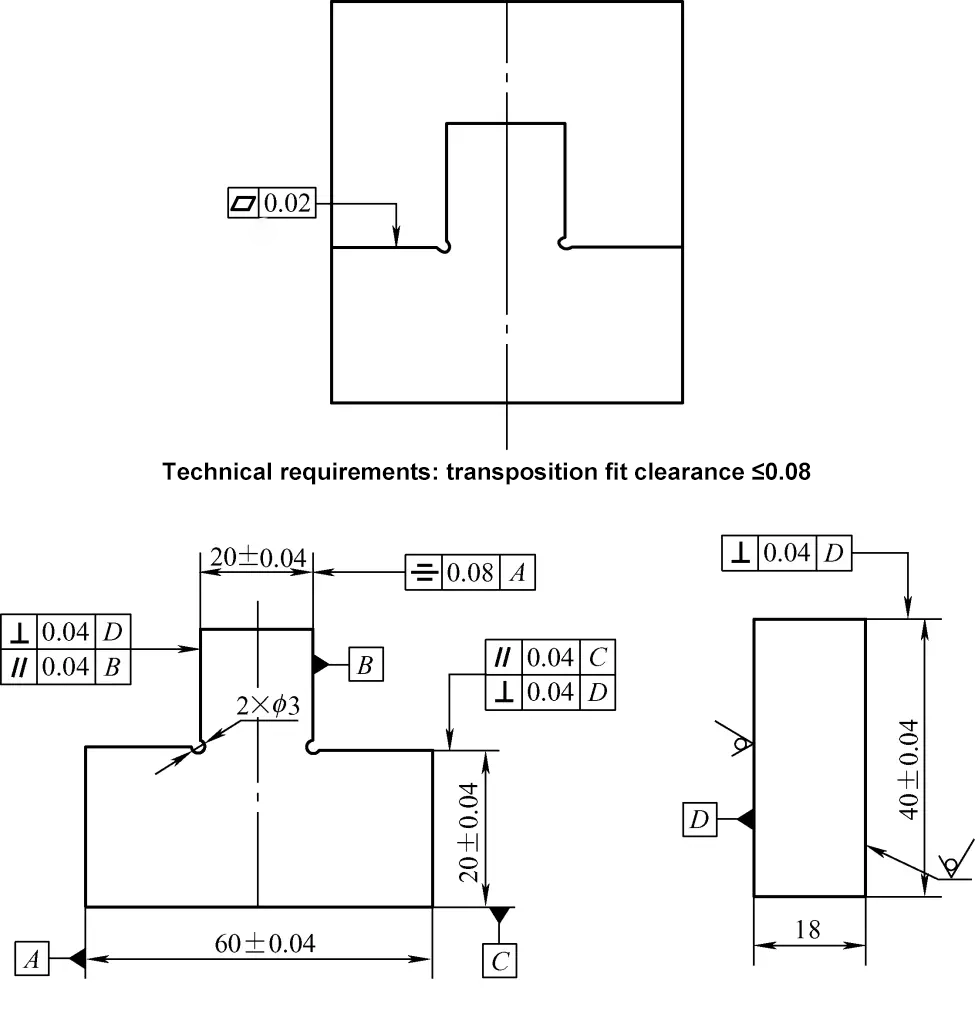
1) Обработка заказа
Как показано на рис. 1, для обеспечения симметрии бобышки (размер 20) по отношению к эталону A (см. рис. 1) при обработке следует оставить материал с одной стороны (см. рис. 2), а не выпиливать весь материал с обеих сторон бобышки. Контролируйте размер L на опиленной поверхности I. Если размер L соответствует требованиям (как описано ниже), отпилите оставшийся материал с этой стороны и одновременно контролируйте опиленную поверхность II до (20±0,04) мм.
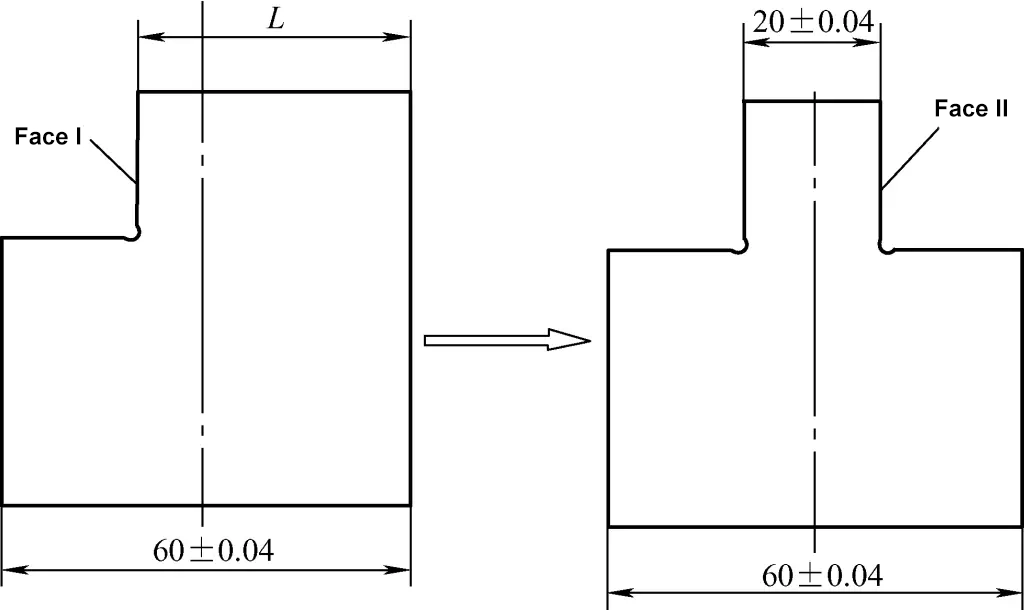
2) Измерение ошибки симметрии
С точки зрения обработки напильником, ошибка симметрии означает отклонение между центральной плоскостью двух обработанных поверхностей и теоретической центральной плоскостью после обработки напильником.
Как показано на рисунке 1, для заготовки допуск симметрии бобышки (20±0,04) мм относительно базовой точки оси A составляет 0,08 мм. Как показано на рисунке 3, чтобы обеспечить это требование симметрии, необходимо гарантировать его путем косвенного измерения размера L.
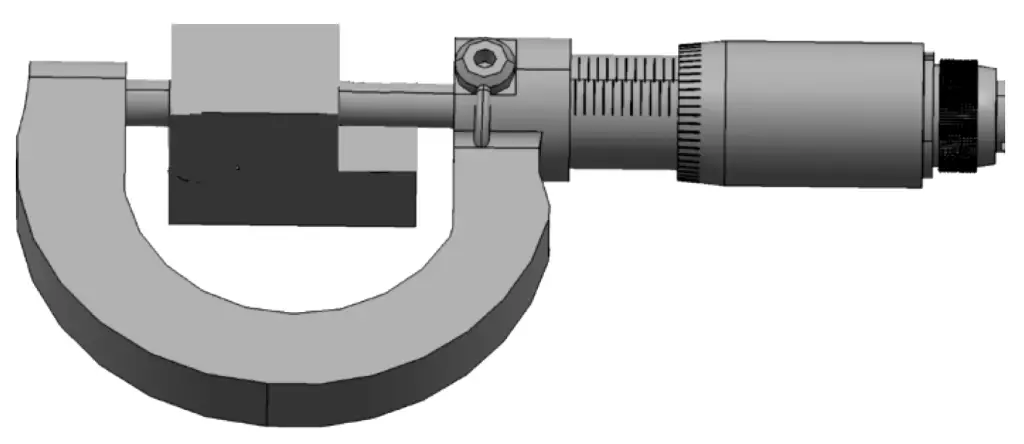
① Максимальный контрольный размер Lmax.
Как показано на рисунке 4, при контроле размеров босса нижнее предельное отклонение составляет 19,96 мм, в результате чего исходное смещение центра влево составляет 0,02 мм. Текущий допуск симметрии составляет 0,08 мм. Согласно концепции допуска симметрии, максимально допустимое левое смещение центральной плоскости бобышки составляет (0,02 + 0,02) мм. Следовательно, контрольный размер Lmax = 40,02 мм.
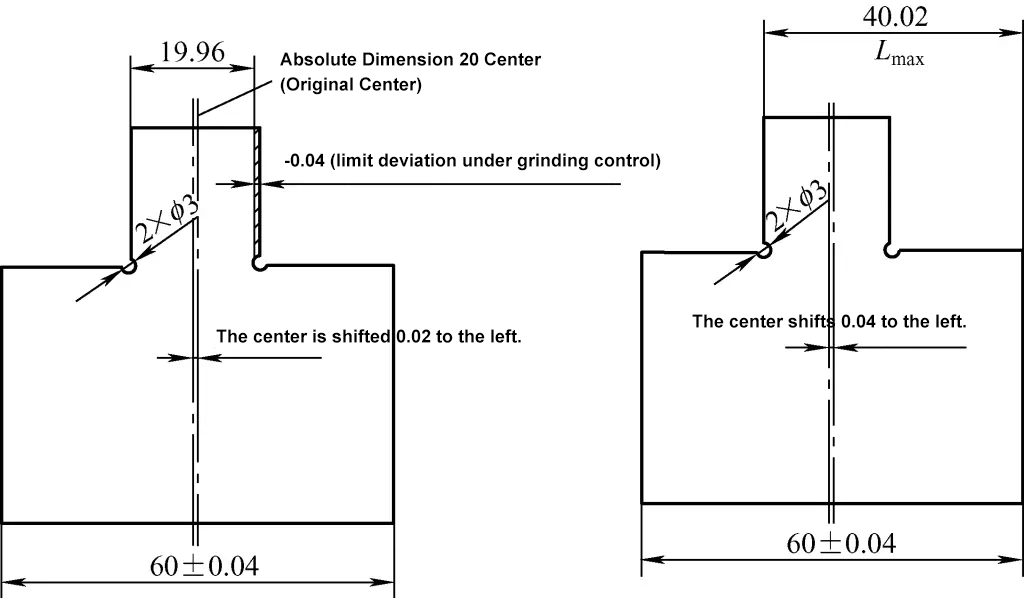
② Минимальный контрольный размер Lмин.
Как показано на рисунке 5, после приведения размера босса к верхнему предельному отклонению 20,04 мм исходное смещение центра вправо составляет 0,02 мм. Текущий допуск симметрии составляет 0,08 мм. Согласно концепции допуска симметрии, максимально допустимое правое смещение центральной плоскости бобышки составляет (0,02 + 0,02) мм. Следовательно, контрольный размер Lmin = 39,98 мм.
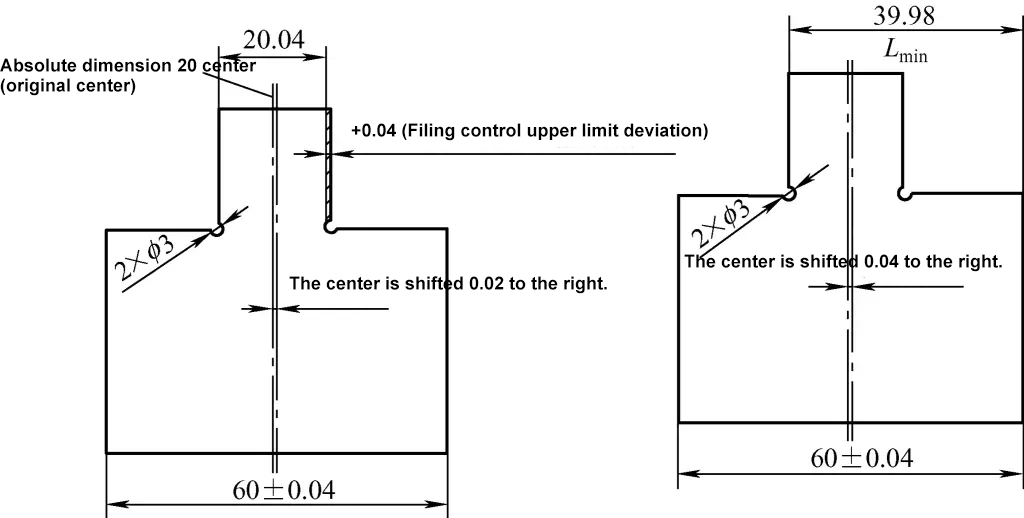
2. Анализ примеров обработки и подгонки деталей - часть первая
Как показано на рисунках 6a и 6b, это прибор для измерения зазора между статором и ротором во время технического обслуживания двигателя (также называемый щупом), структура которого описана следующим образом:
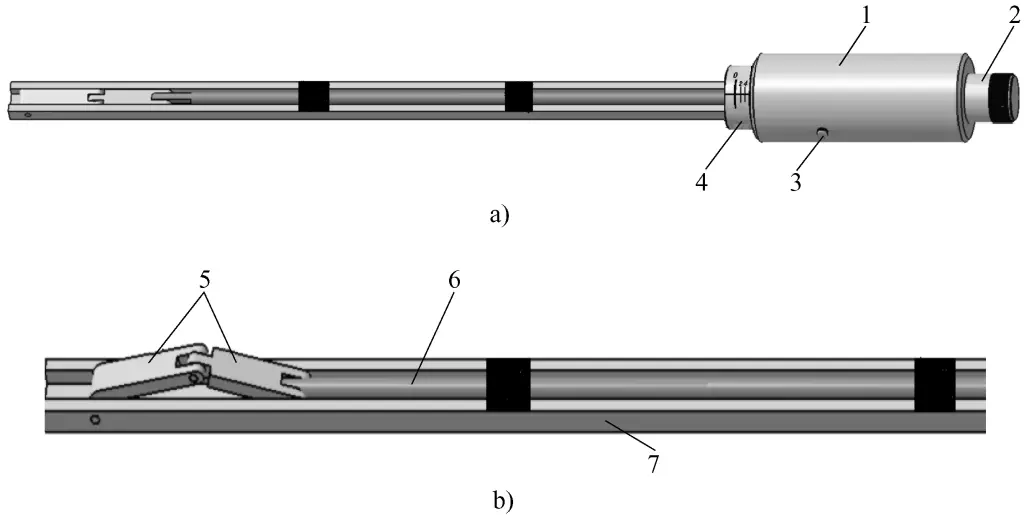
1-Съемный рукав
2-Устройство тонкой регулировки
3-Подвижный штифтовой вал
4-Фиксированная втулка
5-Измерительный блок
6-Подвижный измерительный стержень
Корпус с 7 линейками
1) Подвижная втулка и хвостовая часть подвижного измерительного стержня соединены резьбой (спецификация резьбы - M10×1 мм).
2) Два измерительных блока и подвижный измерительный стержень соединены подвижными шарнирами.
Принцип работы щупа заключается в следующем:
Когда подвижная втулка не вращается, нулевая отметка на неподвижной втулке совпадает с нулевой линией на подвижной втулке (см. рис. 6a). Когда подвижная втулка поворачивается против часовой стрелки, подвижный штифтовой вал вращается по кругу вдоль кругового паза неподвижной втулки. В соответствии с принципом спиральной передачи, подвижный измерительный стержень будет двигаться влево (как показано на рисунке 6). При этом два измерительных блока поднимаются (см. рис. 6b), и поднятая высота может быть отображена на подвижной гильзе.
Текущая задача заключается в обработке напильником и подгонке двух измерительных блоков.
Размеры двух измерительных блоков показаны на рисунке 7.
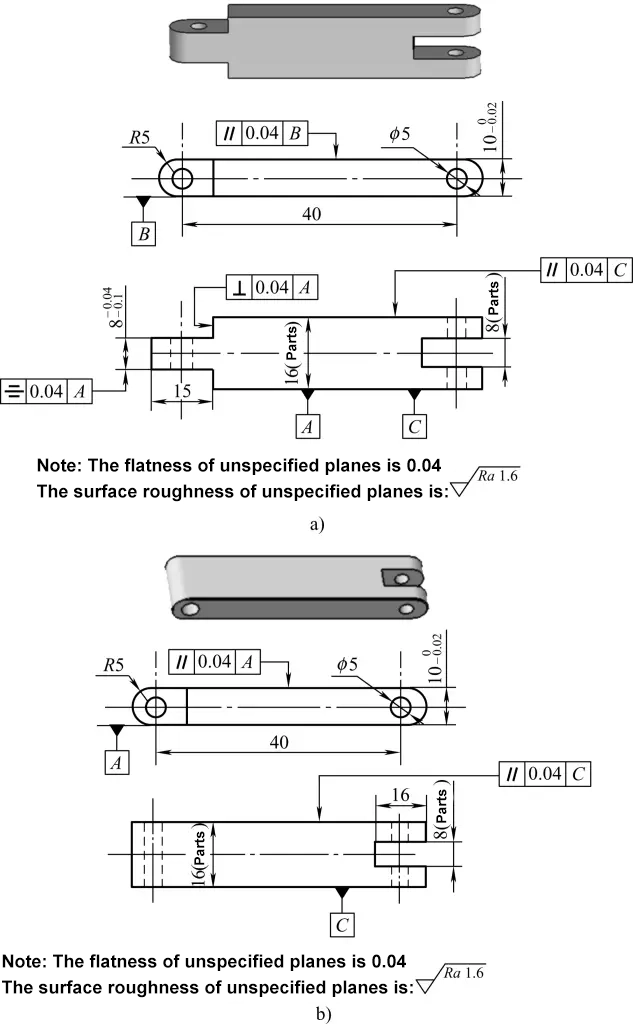
a) Первый измерительный блок
b) Измерительный блок два
(1) Технические требования к подаче документов
1) В соответствии с требованиями к использованию, два измерительных блока должны плавно скользить в пазах корпуса линейки и не шататься влево и вправо. Поэтому после подачи два измерительных блока должны соприкасаться:
① После обработки боковых сторон двух измерительных блоков напильником они должны соответствовать требованиям к размерам и точности формы, показанным на рисунке 7 (требования к установке между измерительным блоком и двумя внутренними сторонами паза корпуса линейки).
После обработки напильником шарнирная часть двух концов измерительного блока должна соответствовать требованиям к точности размеров и формы, указанным на рисунке 7 (требования к посадке выпуклой и вогнутой частей концов измерительного блока).
После обработки напильником шарнирной части измерительного блока два и подвижного конца измерительного стержня, они должны соответствовать требованиям к точности размеров и формы, показанным на рисунке 7 (требования к посадке выпуклой и вогнутой частей концов измерительного блока).
В соответствии с требованиями к использованию нижние поверхности двух измерительных блоков должны хорошо соприкасаться с нижней поверхностью паза линейки. То есть, когда щуп не используется (подвижная втулка не поворачивается), верхняя поверхность измерительного блока должна находиться в той же горизонтальной плоскости, что и верхняя плоскость корпуса линейки. Таким образом, после обработки измерительного блока напильником верхняя и нижняя поверхности должны соответствовать требованиям к точности размеров и формы, показанным на рисунке 7.
Инструменты для подачи документов
В зависимости от формы и размера двух измерительных блоков для опиливания следует выбрать напильники 10″, 6″ и 4″, а нерабочие края плоского напильника 4″ следует отполировать; набор напильников для придания формы.
Процесс подачи документов
Подготовьте материалы
Подготовьте блок из грубого стального материала (сталь 20) размером 18 мм × 10 мм × 110 мм.
Напилите прямоугольную призму (см. рис. 8)
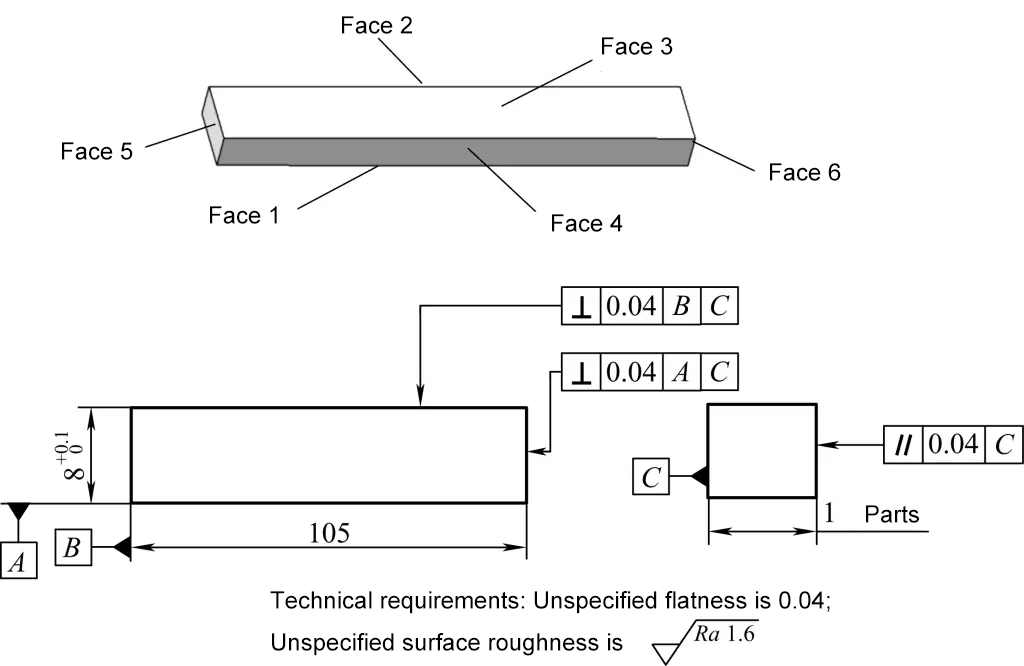
Сначала обработайте поверхность 1 плоским напильником, используя линейку с ножевой кромкой для контроля плоскостности, с точностью до 0,04 мм, при этом значение шероховатости поверхности 1 должно быть в пределах Ra1,6 мкм.
Используйте поверхность 1 в качестве опорной, чтобы отметить границу обработки поверхности 3, обработайте поверхность 3 напильником, чтобы она соответствовала требованиям к размерам и геометрическим допускам, как показано на рис. 8.
Обработайте поверхность 2 с контролем плоскостности и шероховатости, аналогичным поверхности 1, и проконтролируйте перпендикулярность поверхности 2 к поверхности 1 (см. рис. 8).
Как показано на рис. 9, обработайте поверхность 4 напильником в соответствии с фактическим размером паза линейки, контролируя размер до 16 мм, добиваясь зазора между пазом линейки и направлением размера 16 мм 0,04 мм.
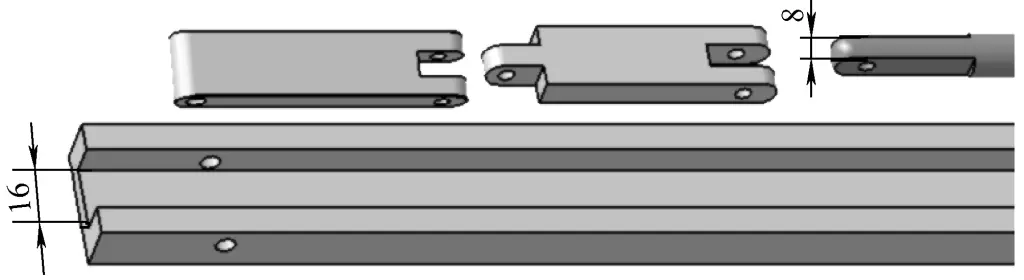
Напильником обработайте обе торцевые поверхности 5 и 6, уделяя особое внимание контролю перпендикулярности поверхности 5 к поверхностям 1 и 2 и перпендикулярности поверхности 6 к поверхностям 1 и 2, контролируя общую длину до 105 мм.
Разделите прямоугольную призму, разделив ее на первую и вторую части, как показано на рисунке 10.
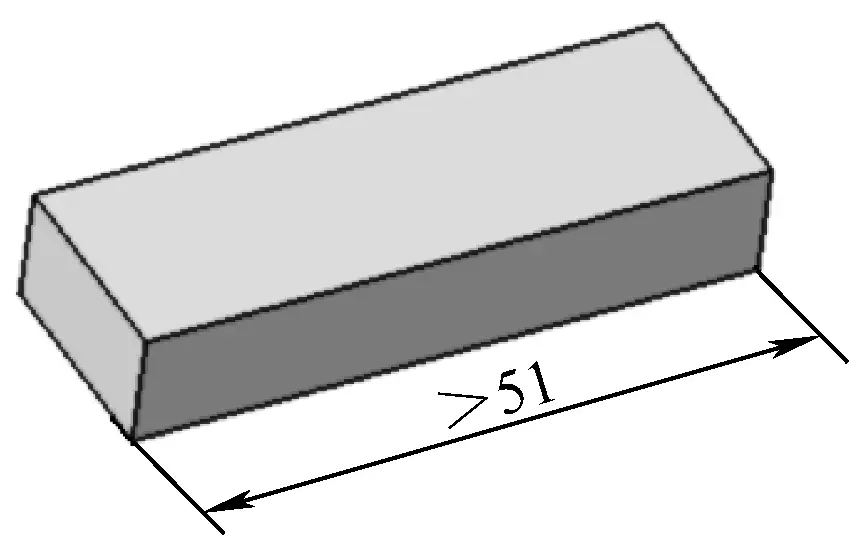
Первый блок измерения процесса
- Пропилите паз 8 мм × 16 мм (в соответствии с посадкой подвижного конца измерительного стержня, см. рис. 7, рис. 9), при этом зазор между подвижным измерительным стержнем и сторонами паза 8 мм × 16 мм должен составлять: 0,04 мм
- Обработайте напильником внешнюю дугу конца паза на R5 мм, чтобы общая длина составила 50 мм.
- Напилите торцевую дугу 8 мм × 15 мм на R5 мм.
- Напилите торцевую бобышку 8 мм × 15 мм до точности размеров и формы, показанной на рисунке 7.
Второй блок измерения процесса (см. Рисунок 7b, Рисунок 9)
Обработайте паз размером 8 мм × 16 мм по тому же методу, что и паз первой детали. Сосредоточьтесь на контроле зазора между пазом и бобышкой первой детали, чтобы он составлял 0,04 мм.
Зашейте левую и правую концевые дуги второй части на R5 мм, чтобы общая длина составила 50 мм.
3. Анализ примера подгонки деталей - часть первая
Съемник изоляционных штырей, показанный на рис. 11, является широко используемым самодельным инструментом при обслуживании и монтаже линий электропередачи. Ниже приводится описание процесса изготовления корпуса съемника:
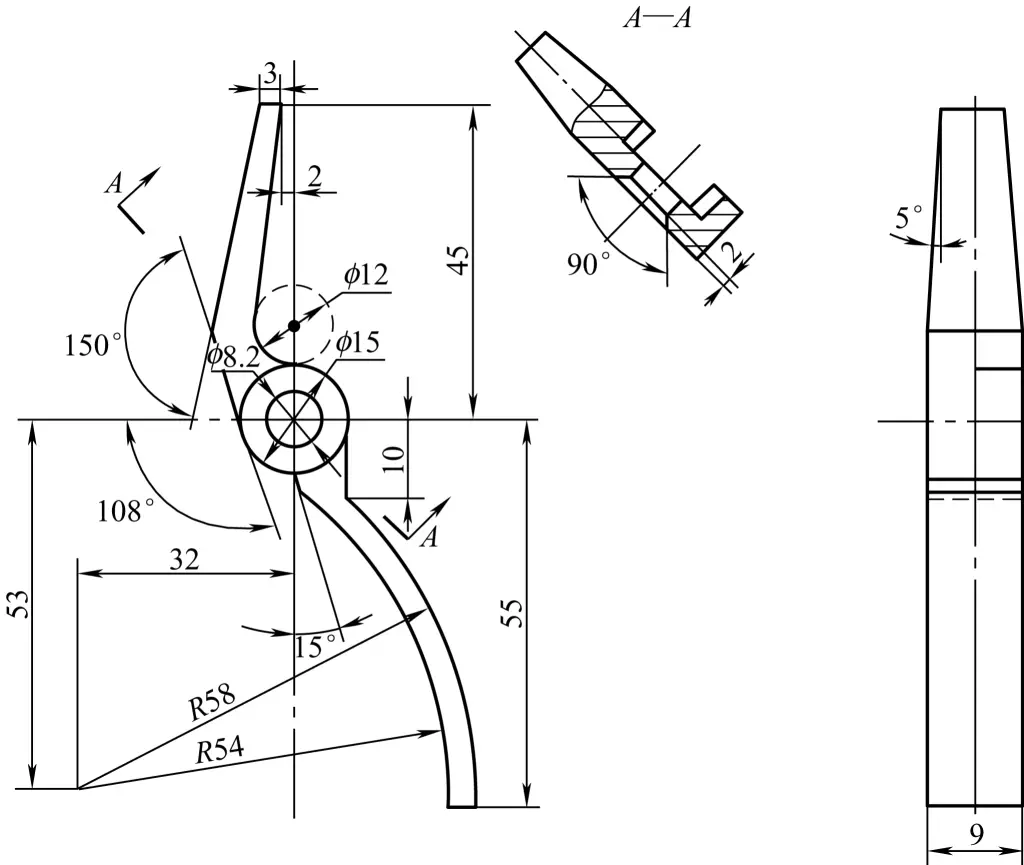
Подготовьте материалы
Размеры стального листа полосы 35 составляют 110 мм × 20 мм × 10 мм (толщина), как показано на рисунке 12.
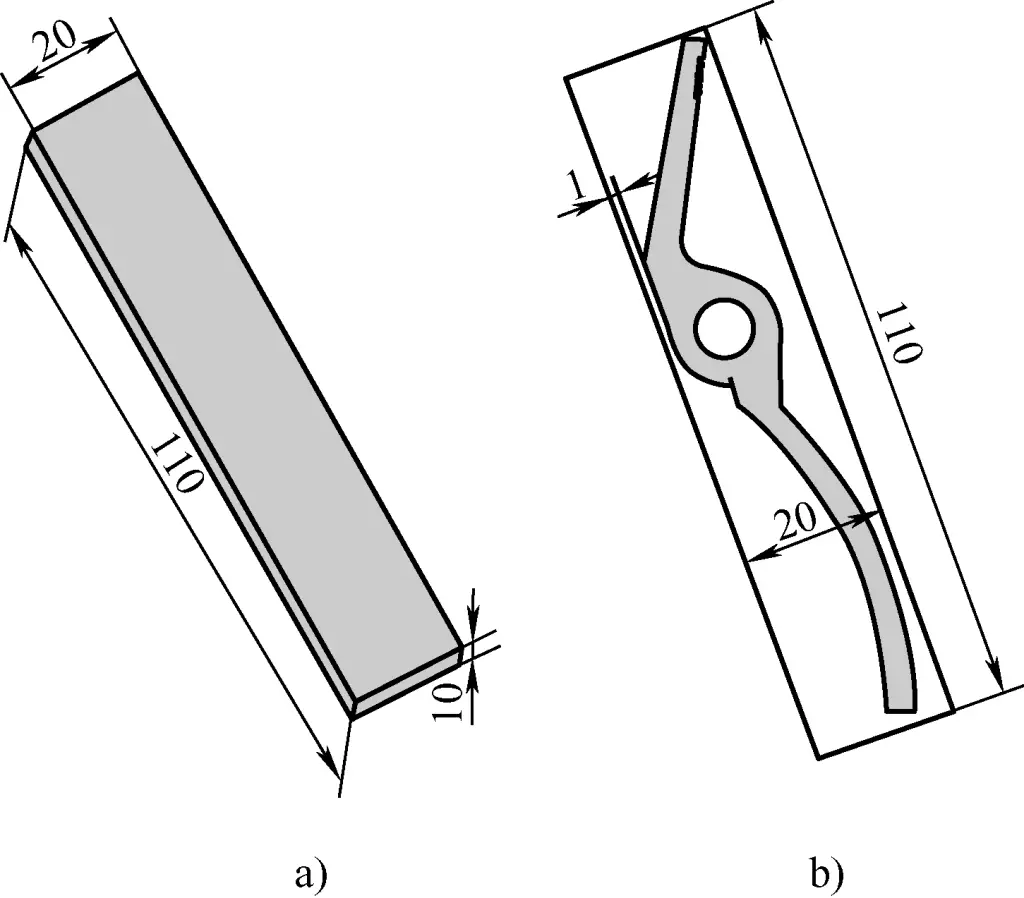
a) Размеры заготовки
b) Форма после формовки
(2) Заготовки пластин для настила (см. рис. 13)
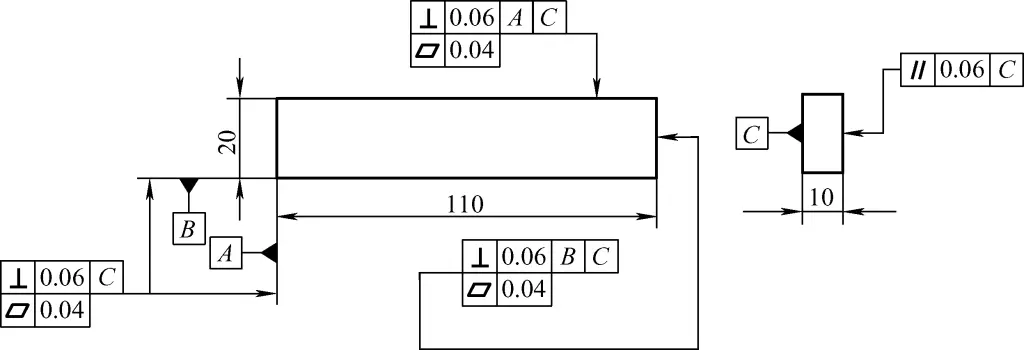
- Зачистите поверхность A полосовой пластины с плоскостностью 0,04 мм перпендикулярно C.
- Обработайте поверхность B полосовой пластины с плоскостностью 0,04 мм, перпендикулярно A и C.
- Используя A и B в качестве эталонов (как для черчения, так и для измерения), обработайте напильником противоположные стороны эталонных поверхностей A и B, чтобы добиться плоскостности 0,06 мм и требуемой перпендикулярности.
(3) Обработка отверстий (см. рис. 14)
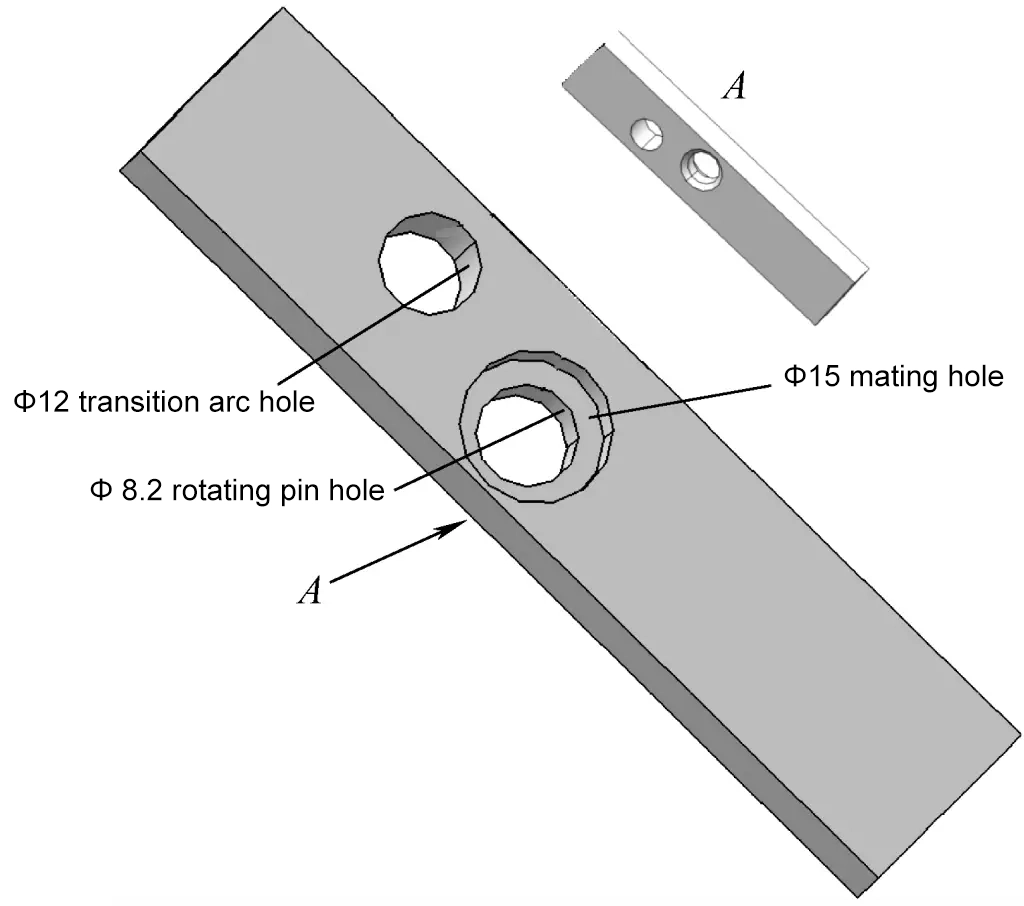
- На основании размеров чертежа отметьте положение и диаметр отверстия для поворотного штифта ϕ8,2 мм и отверстия для переходной дуги ϕ12 мм.
- Просверлите отверстия ϕ8,2 мм и ϕ12 мм на заготовке полосовой пластины, как показано на рисунке 14.
- Как показано на рис. 14 и 11, используйте коническое зенкерное сверло, чтобы зенковать верхний конус для ϕ8,2 мм (используется для клещей для извлечения штифтов).
- Используйте цилиндрическое зенкерное сверло с плоским дном диаметром ϕ15 мм для зенкования посадочного отверстия диаметром ϕ15 мм на глубину 4,5 мм, как показано на рисунке 14.
(4) Контурная маркировка съемника штырей изолятора (см. рис. 15)
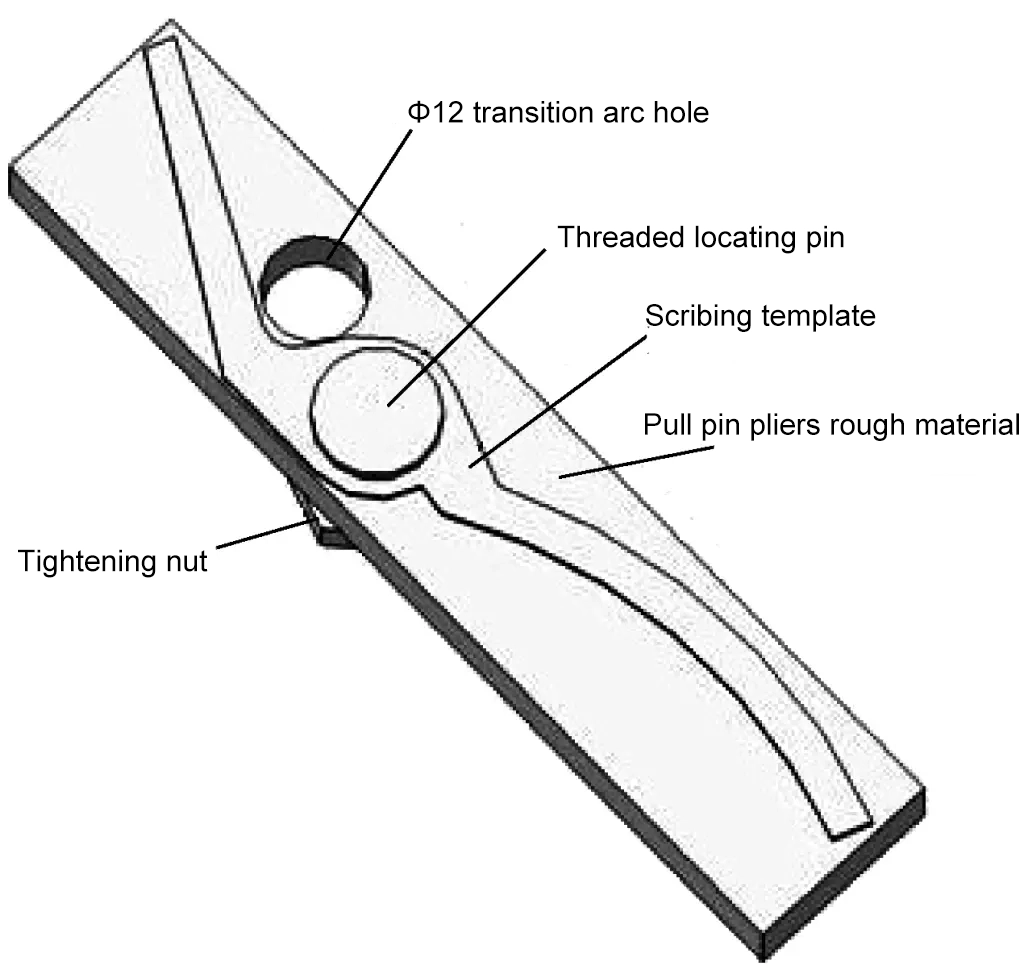
1) Совместите отверстие ϕ8,2 мм для поворотного штифта на шаблоне с отверстием ϕ8,2 мм на заготовке полосовой пластины, вставьте резьбовой фиксирующий штифт и с помощью гайки закрепите шаблон и заготовку полосовой пластины вместе.
2) С помощью линейки отметьте на шаблоне контурные линии для выталкивающих клещей.
(5) Удаление материала
В соответствии с линией обработки, отмеченной на шаблоне, удалите излишки материала с помощью пилы или сверла, стараясь не использовать стамеску, так как это приведет к деформации корпуса клещей.
(6) Общая обработка плоскогубцами штифта изолятора
Последовательность обработки общего напильника клещей для удаления штифтов изолятора показана на рисунке 16. При обработке внутренней стороны губок клещей следите за тем, чтобы контур внутренней стороны был направлен по касательной к соединительной дуге ϕ12 мм.
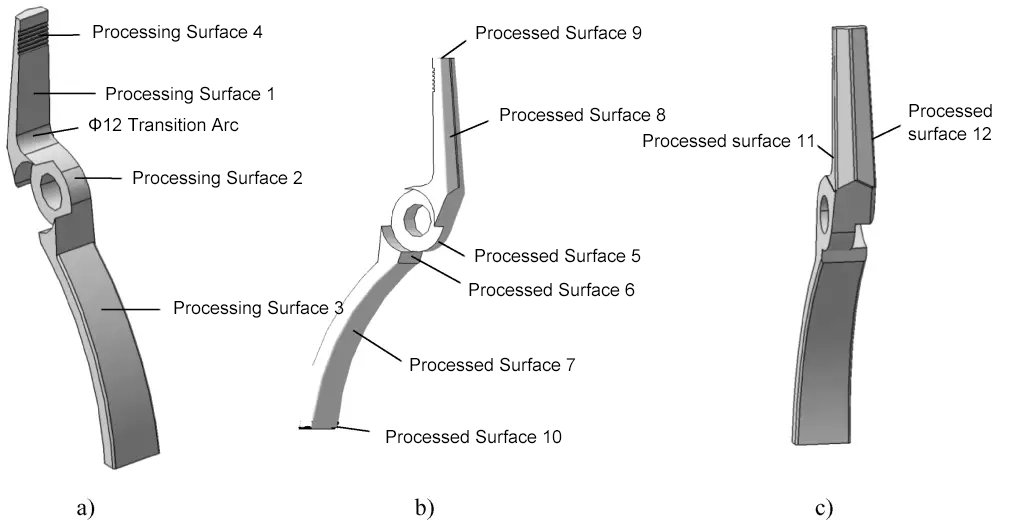
a) Шаг первый
б) Шаг второй
в) Третий шаг