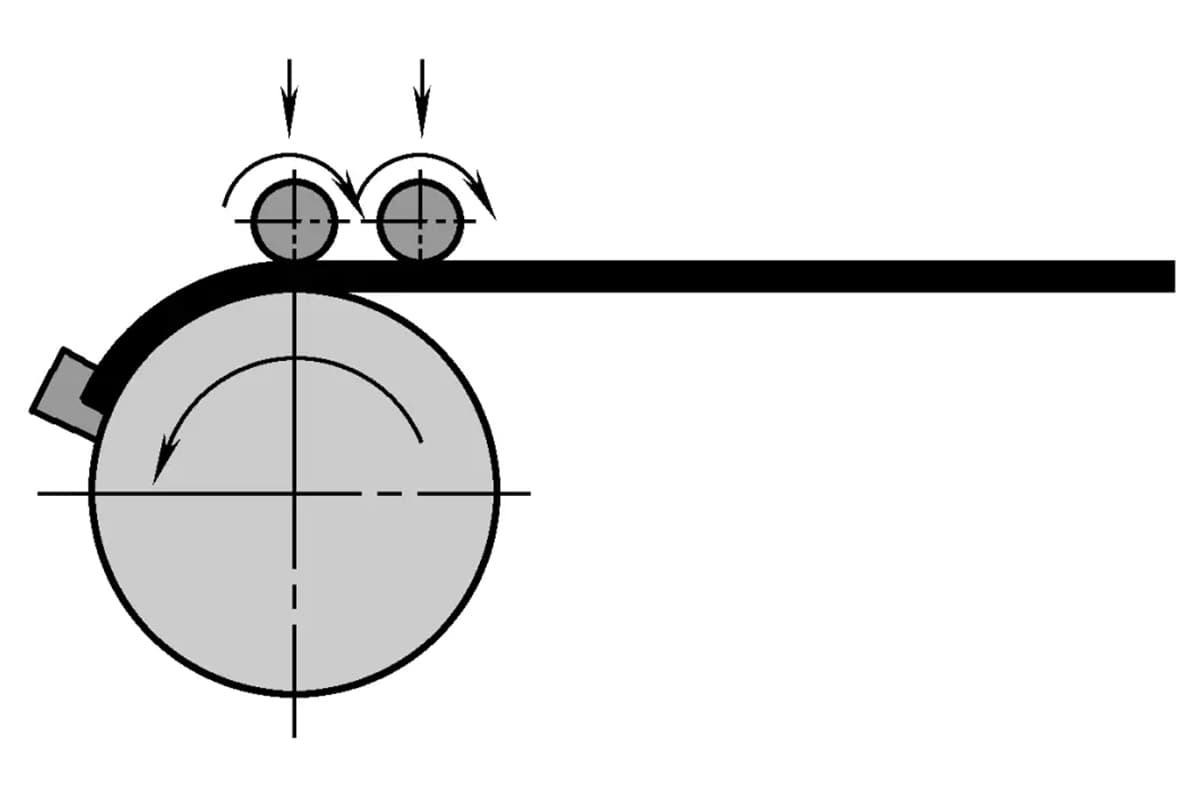
Несмотря на то, что вопросы остаточных напряжений учитываются при проектировании конструкций и в процессе сварки принимаются меры по предотвращению или снижению остаточных напряжений, из-за сложности сварочных напряжений значительные остаточные напряжения могут сохраняться и после сварки конструкции.
Кроме того, в некоторых конструкциях в процессе сборки могут возникать новые внутренние напряжения. Эти остаточные напряжения от сварки и напряжения при сборке могут повлиять на эксплуатационные характеристики конструкции, особенно для ответственных сварных конструкций. Поэтому необходимо принять соответствующие меры для устранения остаточных напряжений, чтобы обеспечить безопасность использования конструкции. К распространенным методам устранения остаточных напряжений относятся:
1. Метод термической обработки
Метод термообработки использует снижение предела текучести материала и явление ползучести при высоких температурах для снятия остаточных напряжений при сварке. Термообработка также улучшает характеристики сварного соединения. Обычно используются такие методы термообработки, как общий высокотемпературный отпуск и локальный высокотемпературный отпуск.
(1) Общий высокотемпературный отпуск
Температуры закалки для различных материалов приведены в таблице 9-1.
Таблица 9-1 Температура закалки для различных материалов
Тип материала | Углеродистая сталь и низко- и среднелегированная сталь① | Аустенитная сталь | Алюминиевый сплав | Магниевый сплав | Титановый сплав | Ниобиевый сплав | Чугун |
Температура закалки/℃ | 580~680 | 850 ~1050 | 250~300 | 250~300 | 550 ~600 | 1100 ~1200 | 600 ~650 |
После отпуска низколегированной стали, содержащей ванадий, при температуре 600~620°C пластичность и вязкость снижаются, поэтому температуру отпуска следует выбирать в диапазоне 550~560°C.
Время выдержки при высокой температуре определяется толщиной материала. Для стали оно рассчитывается как 1~2 мин/мм, обычно не менее 30 минут и не более 3 часов. Для равномерного повышения температуры по всей толщине листа до требуемого уровня необходимо определенное время выдержки после того, как поверхность листа достигнет требуемой температуры.
Термообработка обычно проводится в печи. Для больших контейнеров ее также можно выполнить, покрыв внешнюю стенку контейнера изоляционным слоем и нагревая внутреннюю часть пламенем или электрическим сопротивлением.
На рис. 9-36 показана схема общей термической обработки большого сферического резервуара с использованием газового пламени на месте. На схеме сферический резервуар рассматривается как нагревательная печь, со сверхскоростными соплами для сжигания, вставленными из нижнего люка, использующими сжиженный нефтяной газ или городской угольный газ в качестве топлива, впрыскивающими газ со скоростью 150~300 м/с в резервуар, использующими принудительную конвекцию горячего воздуха, чтобы заставить газ завихряться вдоль внутренней стенки резервуара, равномерно нагревая стенку резервуара.
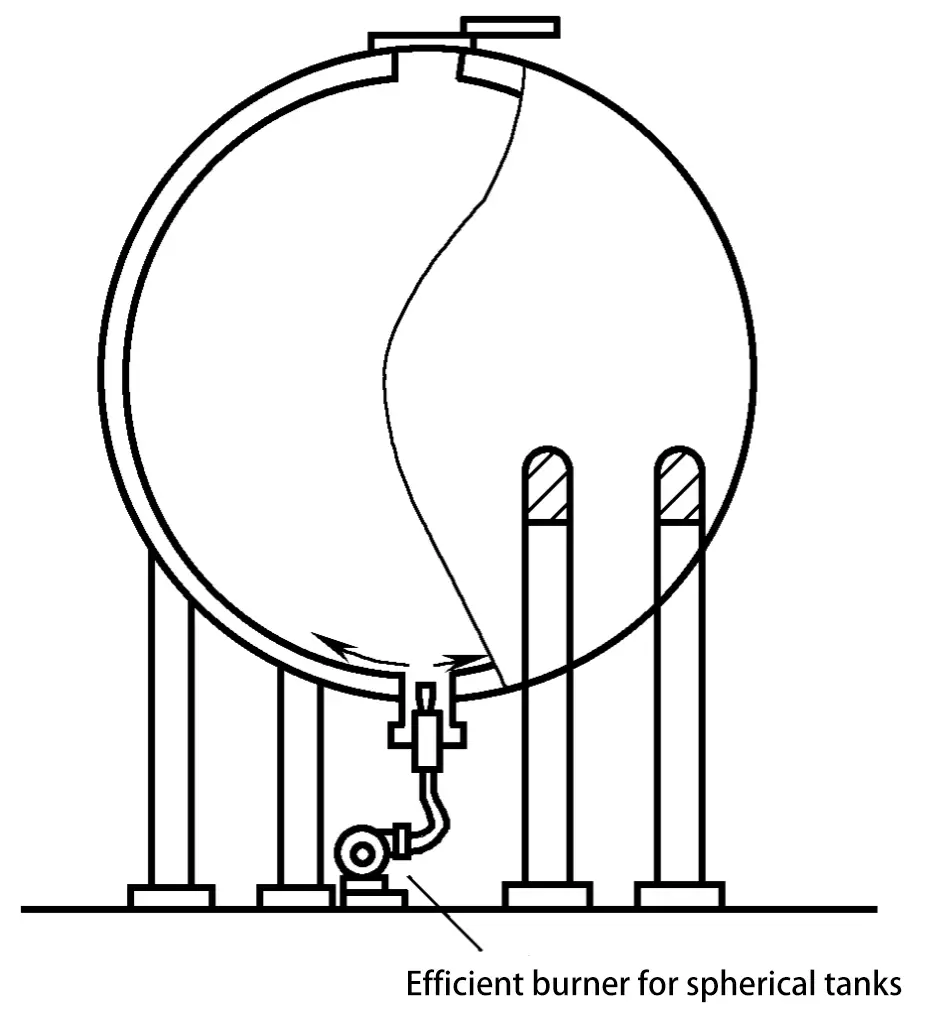
Температура регулируется путем управления потоком газа, объемом воздуха, углом впрыска и открытием выпускной заслонки. Отработанные газы выходят через верхнее отверстие. На внешней поверхности резервуара находится изоляционный слой (на схеме не показан) для предотвращения диффузии тепла. Через каждые 4~5 м на внешней поверхности сферы устанавливается термопара для контроля температуры стенки.
Этот же метод можно применить и для термообработки на месте вертикальных удлиненных контейнеров (контейнеров-башен), как показано на рис. 9-37. Поскольку этот контейнер имеет высокую и тонкую форму, добиться равномерного распределения температуры нагрева сложно, поэтому количество горелок соответствующим образом увеличивается, а горячий воздух распыляется из небольших отверстий центрально расположенной распределительной трубы.
В целом высокотемпературный отпуск позволяет устранить 80%~90% остаточных напряжений.
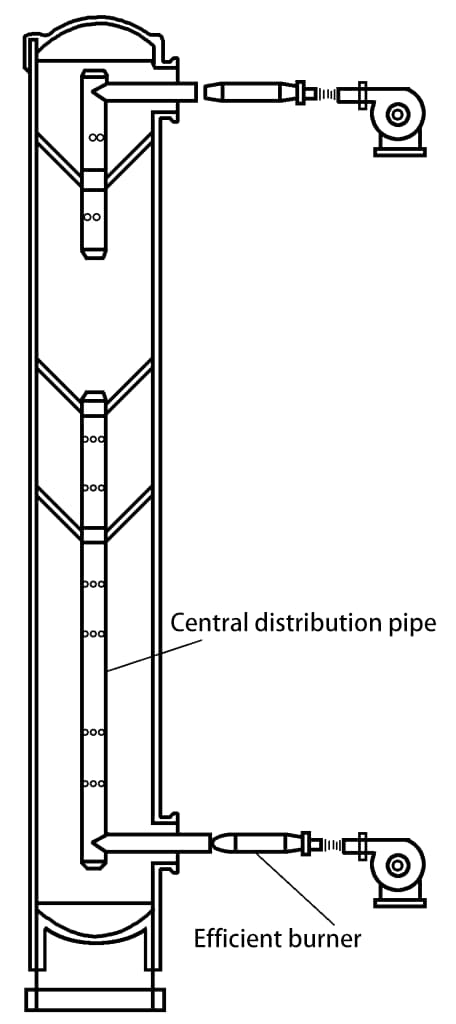
(2) Местный высокотемпературный отпуск
Нагрейте сварной шов и близлежащие зоны повышенных нагрузок до температуры высокотемпературного отпуска, затем выдержите температуру и медленно охладите. Этот способ часто используется для соединений относительно простой формы с небольшими ограничениями, таких как соединения труб, длинных цилиндрических контейнеров и стыковых соединений длинных деталей. Локальный высокотемпературный отпуск может осуществляться с помощью сопротивления, инфракрасного излучения, пламени и индукционного нагрева промышленной частоты.
Локальный высокотемпературный отпуск не может полностью устранить остаточное напряжение, но может уменьшить его пик и сделать распределение напряжения более плавным. Эффект снятия напряжения зависит от равномерности распределения температуры в локальной области. Для достижения лучшего эффекта снижения напряжений необходимо поддерживать достаточную ширину нагрева.
Например: Ширина зоны нагрева цилиндрического соединения обычно берется из формулы на рисунке, а для стыковых соединений длинных пластин B=W принимается, как показано на рис. 9-38 (R - радиус цилиндра, δ - толщина стенки, B - ширина зоны нагрева, W - ширина стыковой детали).
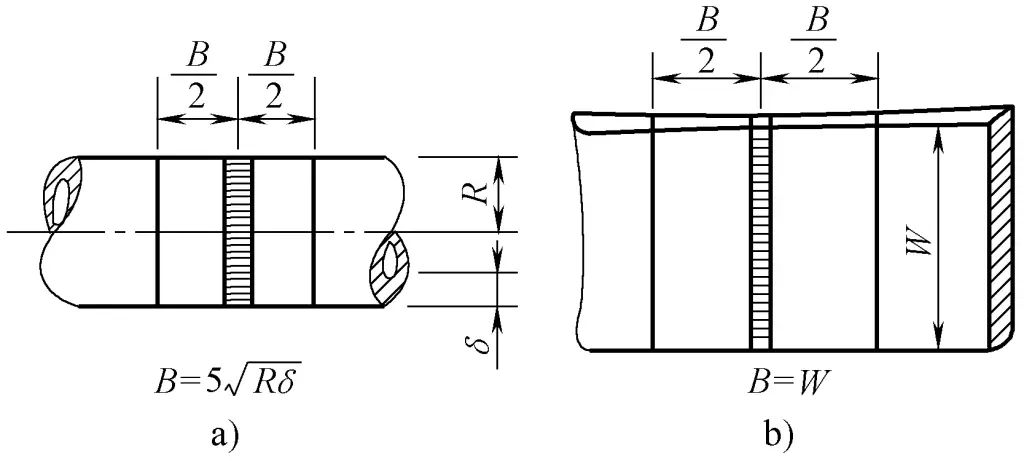
a) Сварка по окружности b) Сварка встык с длинными элементами
2. Метод механического растяжения
После сварки нагрузите сваренные детали, чтобы вызвать растягивающую пластическую деформацию в зонах с более высоким растягивающим остаточным напряжением, а разгрузка может уменьшить сварочное остаточное напряжение. Чем выше напряжение при нагружении, тем больше компенсируется сжимающая пластическая деформация, образовавшаяся в процессе сварки, и тем тщательнее устраняется внутреннее напряжение.
Метод механического растяжения особенно эффективен для устранения внутренних напряжений в некоторых сварных контейнерах. Он позволяет устранить некоторые остаточные напряжения при сварке путем проведения испытания на прочность при перегрузке при комнатной температуре.
3. Метод термического дифференциального растяжения
Нагрейте каждую сторону шва кислородно-ацетиленовой горелкой до температуры около 200°C. Охладите струей воды на определенном расстоянии за горелкой. Горелка и струя воды движутся вперед с одинаковой скоростью (см. рис. 9-39). Это создает разницу температур, при которой боковые стороны имеют высокую температуру (около 200°C), а зона сварки - низкую (около 100°C). Металл на боковых сторонах расширяется из-за нагрева, растягивая более холодную зону сварки, вызывая растягивающую пластическую деформацию, которая компенсирует первоначальную сжимающую пластическую деформацию, тем самым устраняя часть напряжения. Параметры метода термического дифференциального растяжения приведены в таблице 9-2.
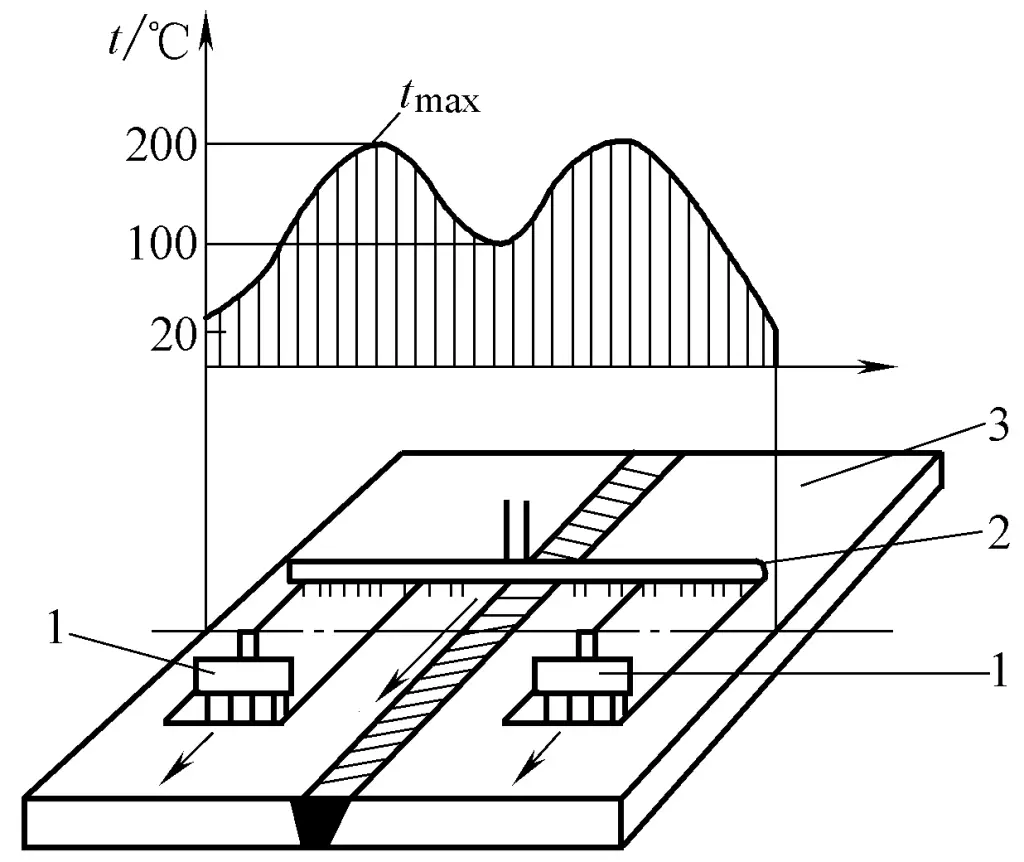
1-Пламенный нагревательный резак
2 - Труба для распыления воды
3-Вельдмент
Таблица 9-2 Параметры метода теплового расширения
Толщина стального листа /мм | Ширина обогрева /мм | Расстояние от центра сварочной горелки /мм | Скорость перемещения факела / (мм/мин) |
8 | 60 | 115 | 600 |
10 | 100 | 125 | 400 |
15 | 100 | 180 | 500 |
17 | 100 | 180 | 300 |
20 | 100 | 180 | 250 |
25 | 100 | 180 | 200 |
30 | 100 | 180 | 175 |
35 | 100 | 180 | 150 |
40 | 100 | 180 | 125 |
При ширине сопла 100 мм расход ацетилена на каждое сопло составляет 17 м³/ч, расход воды - 5~6 л/мин, а расстояние между пламенным соплом и водопроводной трубой - 130 мм.
Метод термического расширения обычно используется для сварных швов, которые относительно регулярны и не очень толсты (<40 мм) в судах, кораблях и других пластинчатых и оболочечных конструкциях. Он имеет практическое значение. При правильном выборе параметров процесса можно добиться хорошего эффекта снятия напряжений.
4. Метод сварки молотком
После сварки простукивание сварного шва молотком или полусферическим пневматическим молотком определенного диаметра может вызвать деформацию растяжения металла шва, которая может компенсировать часть сжимающей пластической деформации и снизить сварочное напряжение. При ударах молотком следует прилагать умеренное усилие, чтобы избежать появления трещин из-за чрезмерного усилия.
5. Вибрационный метод
Вибрационный метод, также известный как вибрационное старение или снятие напряжения с помощью вибрации (VSR), использует возбудитель, состоящий из эксцентрикового колеса и двигателя с переменной скоростью вращения, чтобы заставить конструкцию резонировать, используя циклическое напряжение, возникающее при резонансе, для снижения внутреннего напряжения. Его эффективность зависит от возбудителя, положения опор заготовки, частоты и продолжительности вибрации.
Оборудование, используемое при вибрационном методе, простое и недорогое, энергосберегающее, с низкими затратами на обработку и небольшой продолжительностью (от нескольких минут до нескольких десятков минут), и не вызывает таких проблем, как окисление поверхности металла при высокотемпературном отпуске. Поэтому в настоящее время она чаще всего используется в сварных, литых и кованых изделиях для повышения стабильности размеров.
(1) Механизм вибрационного старения и оценка его последствий
1) Механизм вибрационного старения.
С точки зрения атомной теории, при температуре выше абсолютного нуля атомы металла всегда находятся в движении. Из-за влияния остаточного напряжения эти атомы находятся в неуравновешенном состоянии, но они стремятся вернуться в исходное положение, что требует затрат энергии. Вибрационное старение - это приложение определенного количества механической энергии к заготовке, заставляющее снять остаточное напряжение, сковывающее атомы металла, и ускоряющее скорость возвращения атомов металла в равновесное положение.
Иными словами, вибрационное старение достигается путем периодического приложения динамических напряжений к заготовке, заставляя ее вибрировать в резонансном диапазоне; в процессе вибрации динамические напряжения, приложенные к различным позициям заготовки, накладываются на внутренние остаточные напряжения. Если сумма амплитуды динамического напряжения и остаточного напряжения в определенных точках заготовки превышает предел текучести, то есть σ0 + σ1 > σ2, эти точки подвергаются незначительной пластической деформации, что позволяет снять остаточное напряжение.
Аналогичным образом, если динамическое напряжение вызывает проскальзывание решетки в определенных точках заготовки, хотя оно еще далеко от макроскопического предела текучести материала, эти точки все равно подвергнутся незначительной пластической деформации на микроскопическом уровне, и эти пластические деформации часто происходят сначала в местах наибольшей концентрации остаточного напряжения, что позволяет достичь цели высвобождения и снижения остаточного напряжения.
2) Применимость вибрационного старения.
Применяемые материалы. Подходит для углеродистой конструкционной стали, нержавеющей стали, чугуна, алюминиевого сплава, медного сплава, а также материалов, прошедших индукционную поверхностную закалку и закалку.
Объекты обработки. С его помощью можно обрабатывать различные базовые детали механических изделий, отливки, поковки, сварные детали, конструкционные детали с черновой механической обработкой, заготовки, требующие стабильности размеров до и после холодной и горячей правки, длинные и большие по диаметру детали валов, различные металлические детали с жесткими требованиями к точности, а также негабаритные заготовки, которые не могут подвергаться термической обработке старением.
Гибкие процедуры обработки. Часто выполняется после ковки, литья, сварки, черновой обработки и поверхностного упрочнения, а также может быть выполнена перед окончательной прецизионной обработкой.
Его можно даже адаптировать к особым потребностям заготовки, определяя последовательность и частоту старения при различных процессах (например, однократная вибрация, двукратная вибрация). Она может обрабатывать большие заготовки по отдельности или использовать платформенный метод для централизованной смешанной обработки небольших деталей, и не ограничена формой, весом, размером, объемом, партией, местоположением или временем обработки заготовки. Вес обрабатываемых деталей может составлять от нескольких килограммов до более сотни тонн.
3) Метод оценки эффективности старения.
Согласно стандарту JB/T5926-2005, если возникает одна из ситуаций, показанных на рис. 9-40, можно считать, что эффект процесса старения достигнут.
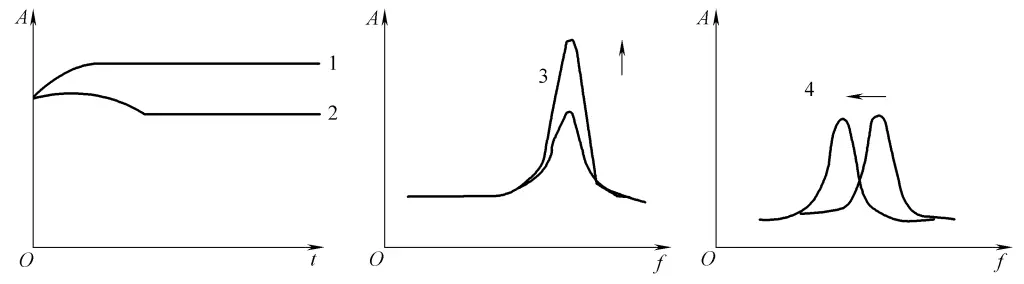
1-Амплитуда-время (A-t) кривая поднимается, затем уплощается
2-Амплитудно-временная (A-t) кривая поднимается, затем опускается, а затем уплощается
3-Амплитудно-частотная (A-f) кривая после пика вибрации выше, чем до вибрации
4-Амплитудно-частотная (A-f) кривая после пика вибрации смещается влево по сравнению с пиком до вибрации
(2) Оборудование для снятия вибрационного напряжения
Вибрационное оборудование для снятия стресса выпускается профессиональными производителями в Китае, оно в основном стандартизировано и все более совершенствуется. При его использовании обратите внимание на следующие моменты.
1) Выбор вибрируемого компонента.
Наиболее экономичным и эффективным методом является резонансная обработка. Для достижения условий резонанса необходимо, чтобы собственная частота вибрируемой детали находилась в диапазоне частот, который может обеспечить вибратор. Диапазон частот стандартного вибратора фиксирован, и если собственная частота заготовки выходит за его пределы, добиться желаемого эффекта будет сложно.
2) Место установки вибратора.
Вибратор обычно устанавливается на пике вибрации заготовки, как показано на рис. 9-41. Это позволяет возбудить заготовку с наименьшей затратой энергии для создания значительной вибрации. Положение пика может быть приблизительно определено пробной вибрацией, на ощупь или путем посыпания песком.
Определенное положение должно обеспечивать устойчивость заготовки в процессе вибрации. Не устанавливайте устройство непосредственно на тонкую пластину заготовки или на детали с усиливающими ребрами, чтобы предотвратить растрескивание заготовки во время вибрации. Для крупных деталей, чтобы достичь лучшего эффекта вибрации, положение установки может быть изменено в соответствии с конкретной ситуацией в конструкции для виброобработки.
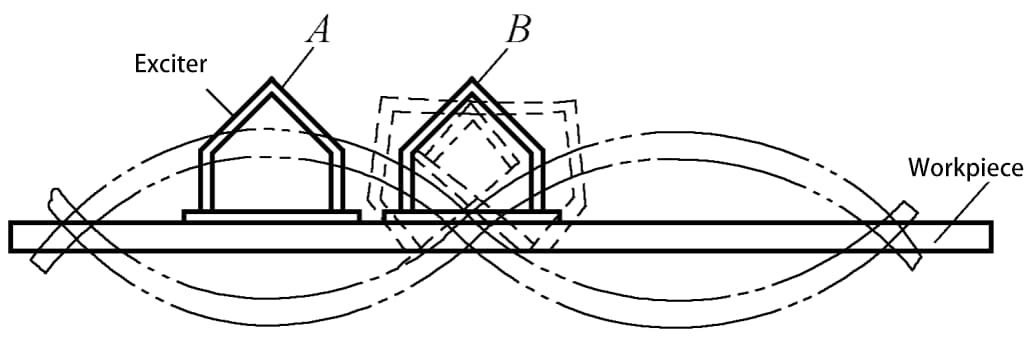
A-правильно B-правильно
3) Положение опоры заготовки.
Как правило, остывшие (иногда еще горячие) сварные детали помещаются на вибростол и поддерживаются подкладками. Подкладки часто изготавливаются из резины, старых шин и других эластичных материалов. Позиции опор выбираются как можно ближе к узлам вибрации, чтобы предотвратить потерю энергии и шум, вызванный столкновением заготовки с опорными площадками во время вибрации. Чем меньше опор при сохранении стабильной вибрации заготовки, тем лучше.
На рис. 9-42 показана схема опоры во время вибрационной обработки заготовки. Целесообразно выбирать опоры в точках 3 и 4, так как вибрация более стабильна, а шум ниже. Если выбрать точки 1 и 2, то энергия, передаваемая заготовке при вибрации, уменьшается, а шум и вибрация грунта увеличиваются.
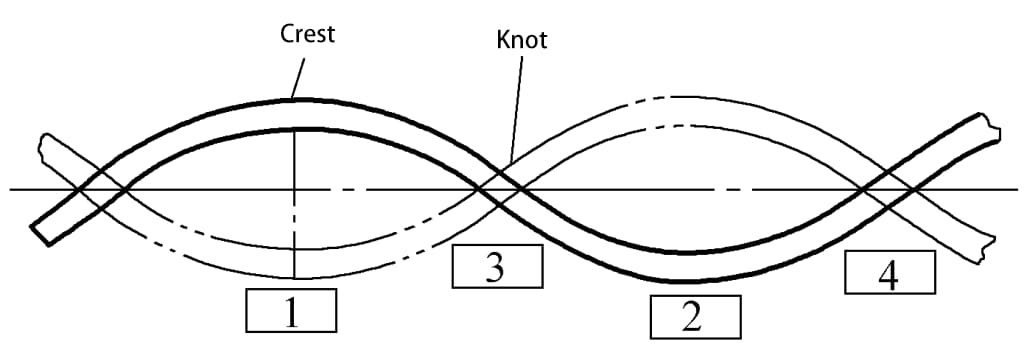
(3) Параметры вибрации
После определения типа заготовки, точки вибрации и положения опоры необходимо контролировать частоту, амплитуду и продолжительность вибрации.
Наилучший эффект резонанса возникает на собственной частоте заготовки. Поэтому сначала следует определить собственную частоту заготовки (например, методом простукивания или резонанса) и использовать ее в качестве частоты вибрации. Циклически изменяющееся динамическое напряжение, прикладываемое к заготовке вибратором в процессе вибрации, является решающим параметром для снижения остаточных напряжений, поскольку оно должно сочетаться с остаточным внутренним напряжением, чтобы вызвать пластическую деформацию для снижения напряжения.
Если остаточное напряжение в заготовке невелико, то для его снижения необходимо использовать достаточно большое динамическое напряжение. И наоборот, если остаточное внутреннее напряжение велико, можно выбрать меньшее динамическое напряжение. Поэтому сначала необходимо измерить или оценить величину и распределение остаточного внутреннего напряжения в сварной детали.
Кроме того, важно обеспечить, чтобы максимальное значение остаточного напряжения в сочетании с дополнительным динамическим напряжением не превышало усталостной прочности во время вибрации или эксплуатации, иначе в процессе вибрации или эксплуатации могут возникнуть повреждения.
В особых случаях, когда невозможно использовать более высокое динамическое напряжение, можно применить более низкое динамическое напряжение с соответствующим увеличением времени вибрации. Величина динамического напряжения может регулироваться величиной возбуждающей силы. Поскольку амплитуда зависит от силы возбуждения, при постоянной частоте колебаний и демпфировании системы большая сила возбуждения приводит к большей амплитуде, тем самым создавая большую динамическую нагрузку на заготовку.
Из-за различий в конструктивных формах и массе сварных изделий величина и распределение остаточных напряжений различны, поэтому выбор времени вибрации также должен быть различным. Обычно оно определяется приблизительно по массе заготовки, как показано в табл. 9-3.
Таблица 9-3 Время вибрации для снятия напряжения методом вибрации
Качество компонентов/кг | 227 | 227~907 | 907 ~4536 | >4536 |
Время вибрации/мин | 5 ~10 | 10 ~ 20 | 20 ~30 | 30 ~45 |
(4) Оценка воздействия вибрации
На месте эксплуатации невозможно определить эффект от устранения остаточного напряжения. Часто о нем судят по некоторым физическим явлениям процесса вибрации, например, по изменению кривых колебаний, резонансной частоты и мощности возбуждения. В настоящее время в основном наблюдаются изменения мощности возбуждения, главным основанием для которых является то, что деталь продолжает вибрировать под действием энергии возбуждения. Когда деталь подвергается пластической деформации, ее остаточное напряжение снимается, и металлический материал укрепляется.
В результате снижается структурное демпфирование, что позволяет расходовать больше энергии возбуждения на смещение компонента вибрации (т.е. амплитуду), а не на внутреннее демпфирование. Поэтому при вибрации компонентов с остаточным внутренним напряжением, если энергия возбуждения поддерживается постоянной, происходит увеличение амплитуды. Если значение амплитуды контролируется, чтобы оставаться постоянным, требуемая энергия возбуждения уменьшается, что снижает мощность.
Метод снятия напряжений с помощью вибрации имеет много преимуществ, но есть и ряд проблем, которые до конца не решены, например, как обеспечить равномерное снижение внутренних напряжений в сложных сварных конструкциях; как управлять вибрацией, чтобы она снимала внутренние напряжения без снижения усталостной прочности конструкции.
6. Метод взрыва
Взрывное соединение достигается за счет расположения взрывчатых полос на сварном шве и вблизи него, где ударные волны, возникающие при детонации, взаимодействуют с остаточными напряжениями, вызывая соответствующую пластическую деформацию металла, тем самым снимая остаточные напряжения. Количество взрывчатых веществ на единицу длины сварного шва и их расположение следует выбирать в зависимости от толщины свариваемых деталей и свойств материала.
На рис. 9-43 показана схема размещения заряда взрывчатого вещества, используемого для снятия сварочных напряжений в больших пластинчатых сварных конструкциях средней толщины. Стыковые соединения плоских пластин обычно заряжаются в зонах остаточных растягивающих напряжений от сварки, в то время как стыковые соединения изогнутых пластин (например, сварные швы на сосудах или трубах) могут заряжаться как на внутренней, так и на внешней поверхности. Исследования показывают, что зарядка в зонах остаточного растягивающего напряжения на внутренней поверхности изогнутых пластин дает более значительный эффект, чем зарядка на внешней поверхности.
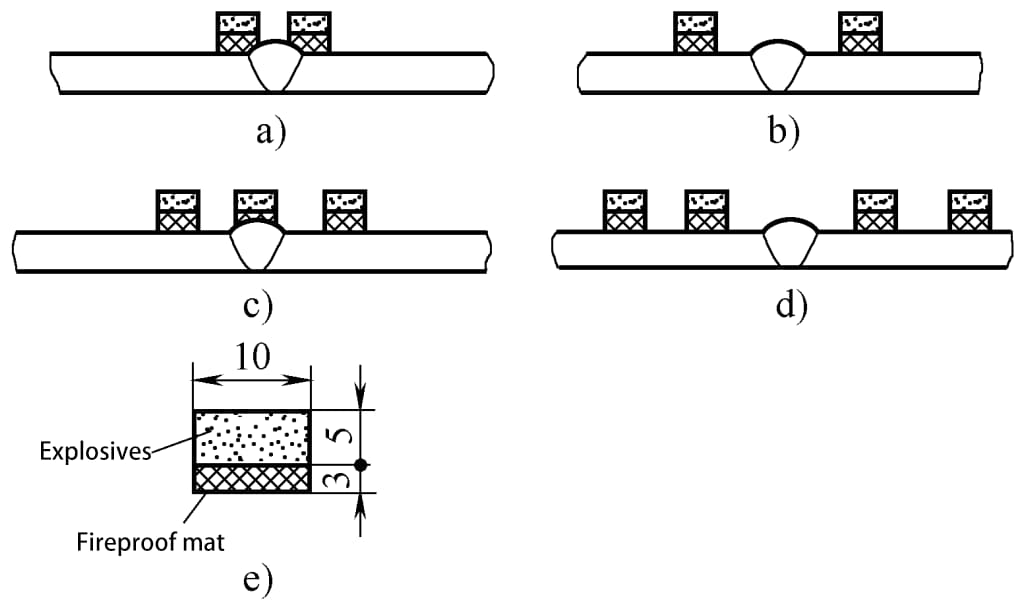
Если трудно нанести лекарство на внутреннюю поверхность, взрыв лекарства в соответствующих местах по обеим сторонам наружного сварного шва также может дать эффект снижения остаточного напряжения. Обычно используется взрывчатое вещество из полосовой резины, со скоростью детонации 5000 м/с, приводимое в действие детонатором.
Метод взрыва для снятия сварочных напряжений применяется в отечественных сосудах высокого давления, башнях химических реакций, трубопроводах, гидротехнических сооружениях и коробчатых балках. Однако для обеспечения безопасности при проведении взрывных строительных работ необходимо строго соблюдать соответствующие национальные правила, строго придерживаться рабочих процедур и каждый раз контролировать количество используемых взрывчатых веществ.