
Ручная гибка - это метод ручного сгибания части листа или профиля относительно другой части по прямой линии или кривой на определенный угол. Это одна из самых основных операций при формовке листового металла. Обычные детали, сгибаемые вручную, показаны на рисунке 1.

I. Ручная гибка небольших и тонких листов
К распространенным инструментам для ручной гибки относятся деревянные молотки, молотки различных форм, утюги различных форм, калибровочные утюги, деревянные планки, резиновые планки, общие острые шаблоны R, платформы, носовые зажимы и тиски; широко используемое оборудование - ручное фальцовочная машинаВ основном используется для гибки простых листовых деталей с прямым изгибом.
Ручная гибка в основном используется для тонких листов толщиной менее 3 мм и небольших размеров, особенно для тонких листов толщиной от 0,6 до 1,5 мм. Для гибки более толстых листов чаще всего используется метод локального нагрева на участке гибки с последующей ручной гибкой.
1. Расчет длины развернутого изгиба
При гибке листового металла сначала необходимо рассчитать длину развернутой детали. Точность длины развернутой части гнутой детали является основной гарантией точности формы гнутой детали. Во время деформации при изгибе листовой материал имеет следующие характеристики: Материал внутреннего слоя сжимается и укорачивается, материал внешнего слоя растягивается и удлиняется, а между средним и внутренним слоями находится слой материала, который не удлиняется и не укорачивается (этот слой материала называется нейтральным слоем). Таким образом, длина нейтрального слоя в гибочной детали - это длина заготовки гибочной детали в развернутом виде.
Таким образом, ключ к расчету длины всей заготовки гнутой детали заключается в том, как определить радиус кривизны нейтрального слоя при гибке. В производстве радиус кривизны нейтрального слоя ρ обычно определяется по эмпирической формуле:
ρ=r+xt
В формуле
- r - внутренний радиус изгиба листа;
- x - коэффициент нейтрального слоя, зависящий от степени деформации, выбирается в соответствии с таблицей 1;
- t - толщина листа.
Таблица 1 Значения коэффициента нейтрального слоя x
р/т | 0.1 | 0.2 | 0.3 | 0.4 | 0.5 | 0.6 | 0.7 | 0.8 | 1 | 1.2 |
x | 0.21 | 0.22 | 0.23 | 0.24 | 0.25 | 0.26 | 0.28 | 0.3 | 0.32 | 0.33 |
р/т | 1.3 | 1.5 | 2 | 2.5 | 3 | 4 | 5 | 6 | 7 | ≥8 |
x | 0.34 | 0.36 | 0.38 | 0.39 | 0.4 | 0.42 | 0.44 | 0.46 | 0.48 | 0.5 |
После определения положения нейтрального слоя можно рассчитать длину прямого и дугового участков, которая является длиной развернутого материала согнутой части.
Однако из-за влияния многих факторов на деформацию при изгибе (таких как свойства материала, конструкция пресс-формы, метод гибки и т.д.), для сложных форм, многократных изгибов и небольших допусков на размеры гнутых деталей необходимо провести предварительные расчеты по приведенной выше формуле для определения пробной заготовки для гибки. После того как пробный изгиб будет квалифицирован, можно определить точную длину заготовки.
Значения, приведенные в таблице 1, также применимы для расчета длины в развернутом виде для прутков и труб.
(1) Расчет частей изгиба 90°
В производстве, когда угол изгиба составляет 90°, для расчета длины развернутой гнутой детали часто используется метод вычитания, как показано на рис. 2. Когда толщина листа равна t, внутренний радиус изгиба равен r, а развернутая длина согнутой заготовки L равна
L=a+b-u
В формуле
- a, b - длины двух сторон прямого угла;
- u - разница между суммой длин двух сторон прямого угла и длиной нейтрального слоя, т.е. значение вычета для развернутой длины, как показано в таблице 2.
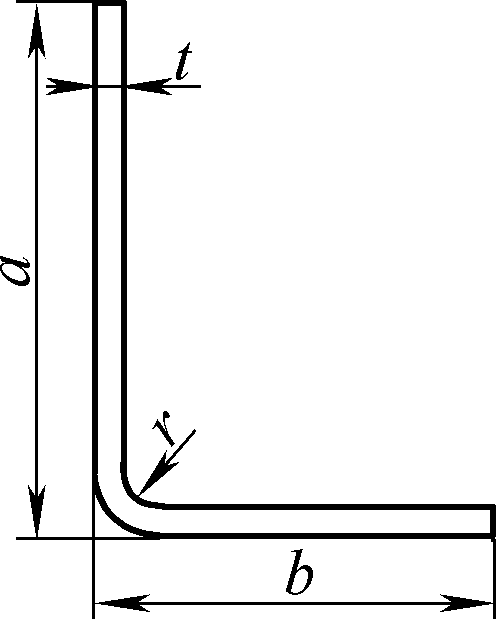
Таблица 2 Значения вычитания для неразогнутой длины изгибов 90° (Единицы измерения: мм)
Радиус изгиба r | ||||||||||||
Толщина листа t | 1 | 1.2 | 1.6 | 2 | 2.5 | 3 | 4 | 5 | 6 | 8 | 10 | 12 |
Среднее значение вычета u для развернутой длины | ||||||||||||
1 | 1.92 | 1.97 | 2.1 | 2.23 | 2.24 | 2.59 | 2.97 | 3.36 | 3.76 | 4.57 | 7.39 | 7.22 |
1.5 | 2.64 | - | 2.9 | 3.02 | 3.18 | 3.34 | 3.7 | 4.07 | 4.45 | 7.24 | 7.04 | 7.85 |
2 | 3.38 | - | - | 3.81 | 3.98 | 4.13 | 4.46 | 4.81 | 7.18 | 7.94 | 7.72 | 7.52 |
2.5 | 4.12 | - | - | 4.33 | 4.8 | 4.93 | 7.24 | 7.57 | 7.93 | 7.66 | 7.42 | 8.21 |
3 | 4.86 | - | - | 7.29 | 7.5 | 7.76 | 7.04 | 7.35 | 7.69 | 7.4 | 8.14 | 8.91 |
3.5 | 7.6 | - | - | 7.02 | 7.24 | 7.45 | 7.85 | 7.15 | 7.47 | 8.15 | 8.88 | 9.63 |
4 | 7.33 | - | - | 7.76 | 7.98 | 7.19 | 7.62 | 7.95 | 8.26 | 8.92 | 9.62 | 10.36 |
4.5 | 7.07 | - | - | 7.5 | 7.72 | 7.93 | 8.36 | 8.66 | 9.06 | 9.69 | 10.38 | 11.1 |
5 | 7.81 | - | - | 8.24 | 8.45 | 8.76 | 9.1 | 9.53 | 9.87 | 10.48 | 11.15 | 11.85 |
6 | 9.29 | - | - | - | 9.93 | 10.15 | - | - | - | - | - | - |
7 | - | - | - | - | - | - | - | - | 11.46 | 12.08 | 12.71 | 13.38 |
8 | - | - | - | - | - | - | - | - | 12.91 | 13.56 | 14.29 | 14.93 |
9 | - | - | – | – | – | 13.1 | 13.53 | 13.96 | 14.39 | 17.24 | 17.58 | 17.51 |
На производстве, если не требуется точное определение длины гнутой детали, можно произвести приблизительный расчет длины L развернутой заготовки гнутой детали по следующей формуле:
Когда радиус изгиба r ≤ 1,5t, L = a + b + 0,5t;
Когда 1,5t<r≤5t, L=a+b;
Когда 5t
Когда радиус изгиба r > 10t, L = a + b - 3,5t.
(2) Расчет частей, согнутых под произвольным углом
Гнутые детали с произвольными углами изгиба, показанные на рисунке 3, можно рассчитать следующим образом.
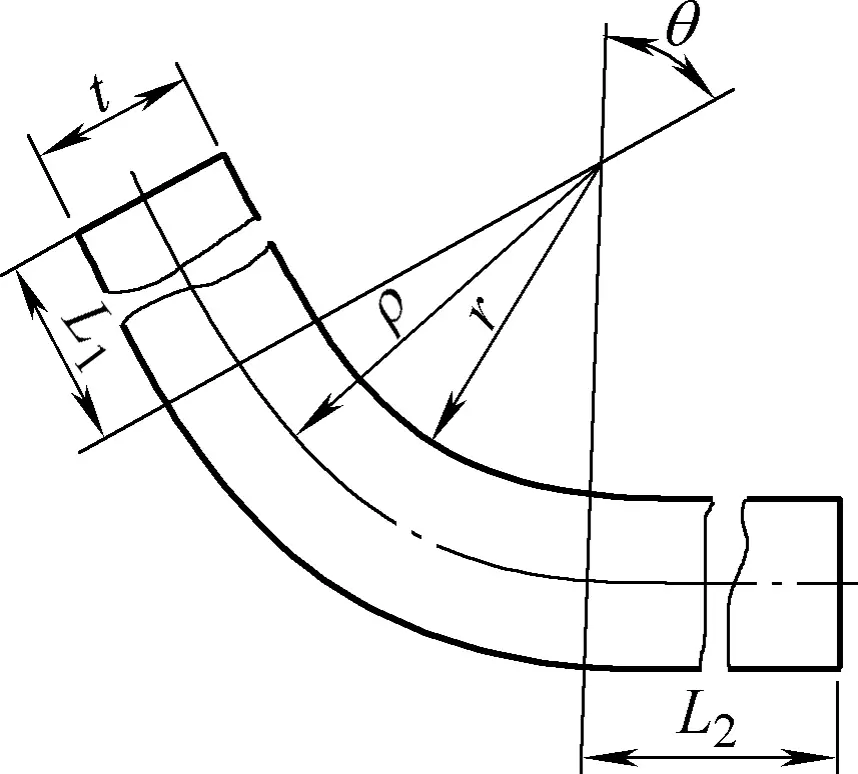
L=L1+L2+πθρ/180≈L1+L2+0.0175(r+xt)(180°-α)
В формуле
- L1, L2 - длины прямых частей (мм) соответственно;
- ρ - радиус нейтрального слоя гнутой детали (мм);
- α - угол изгиба (°), α = 180° - θ;
- θ - центральный угол изогнутой части (°);
- x - коэффициент нейтрального слоя, зависящий от степени деформации, выбирается по табл. 1; при использовании штампа для прокатки деталей шарниров (см. рис. 4) выбирается по табл. 2;
- t - толщина листа (мм).
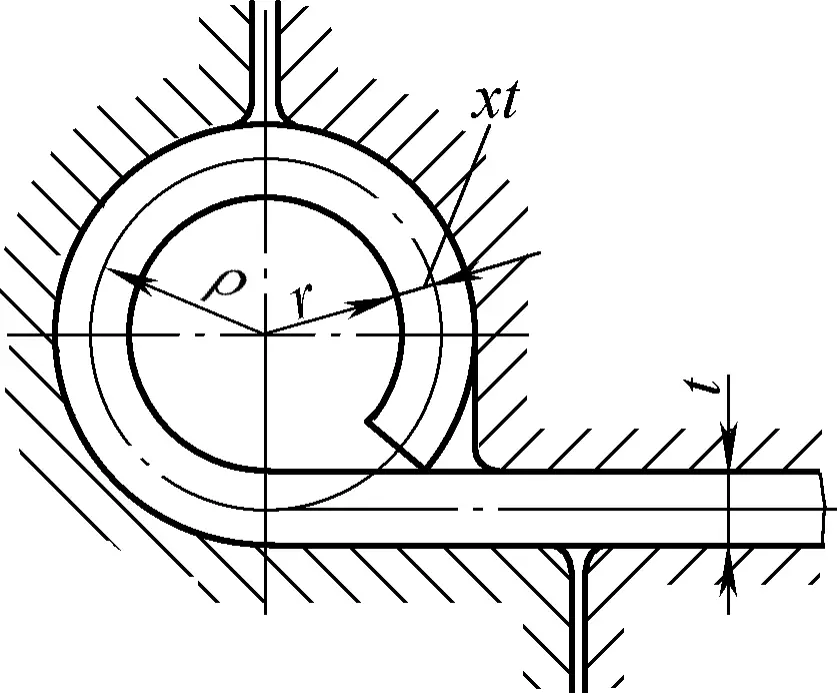
Для гнутых деталей шарнирного типа с r = (0,6 ~ 3,5)t при использовании для гибки метода прокатного штампа, показанного на рис. 4, давление прикладывается пуансоном к одному концу заготовки, что приводит к пластической деформации, отличной от общей гибки на прессе. Материал не истончается, а утолщается, и нейтральный слой смещается от середины толщины листа к внешнему слою изгиба, поэтому коэффициент смещения нейтрального слоя больше или равен 0,5 (см. табл. 3).
Таблица 3 Коэффициент смещения нейтрального слоя при прокатке
р/т | 0.5 | 0.6 | 0.7 | 0.8 | 0.9 | 1.0 | 1.1 | 1.2 |
X | 0.77 | 0.76 | 0.75 | 0.73 | 0.72 | 0.70 | 0.69 | 0.67 |
р/т | 1.3 | 1.4 | 1.5 | 1.6 | 1.8 | 2.0 | 2.5 | ≥3 |
X | 0.66 | 0.64 | 0.62 | 0.60 | 0.58 | 0.54 | 0.52 | 0.5 |
2. Ручные методы гибки листового металла
К распространенным ручным инструментам для гибки относятся деревянные молотки, деревянные клинья, настольные тиски и формы для гибки кромок, как показано на рисунке 5.
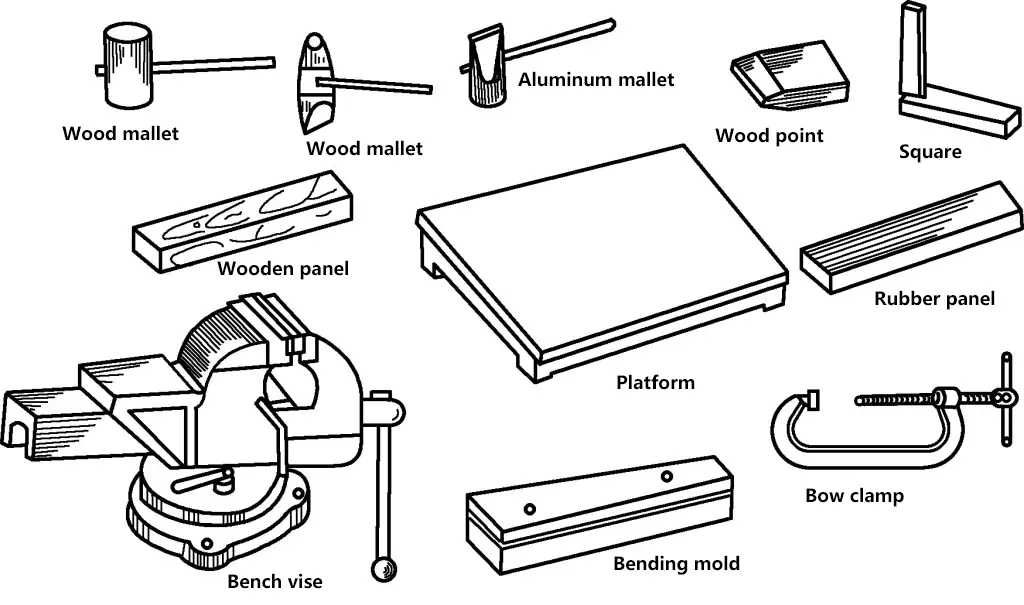
Для различных форм гнутых деталей из листового металла используются различные методы гибки. Ручная гибка подразделяется на гибку с одним краем и гибку с несколькими краями, а методы гибки выглядят следующим образом:
(1) Сгибание одного края
Для деталей с одним краем сначала разверните их в соответствии с вышеупомянутым методом, чтобы получить развернутые размеры, расплющите и отметьте линию сгиба; затем подготовьте два модуля или калибровочных утюга длиной больше, чем длина детали, зажмите заготовку согнутой детали между двумя калибровочными утюгами и при сгибании плотно совместите линию сгиба с закругленным краем калибровочного утюга, как показано на рис. 6a.
Затем с помощью резиновой полоски или деревянного молотка постучите по материалу в направлении калибровочного железа R edge, уделяя особое внимание простукиванию средней и нижней части заготовки, выходящей за пределы формы, насколько это возможно, чтобы она поместилась в форму, как показано на рис. 6b.
Чтобы обеспечить усадку материала и его прилегание к форме, используйте деревянный молоток и деревянный клин для равномерного забивания детали R от начала до конца, чтобы она прилегала к форме, как показано на рис. 6c; чтобы устранить пружинящую спинку, коробление и обратную кривизну (чрезмерное забивание во время гибки легко приводит к обратному изгибу), используйте деревянный клин для забивания снаружи внутрь, непрерывно от одного конца к другому, как показано на рис. 6d.
Для гнутых деталей с короблением и пружинящей спинкой, чтобы устранить их, выберите калибр с прямой поверхностью и зажмите его на платформе с помощью носового зажима, при этом загнутый край должен прилегать к прямой поверхности калибра. Слегка постучите деревянным молотком по деревянному клину под углом 45°, двигаясь и постукивая вдоль загнутой части, простукивая по всей длине, как показано на рис. 6e. Наконец, зажмите заготовку в калибровочном железе и постучите по ней резиновой полоской, пока она не войдет в форму, как показано на рис. 6b.
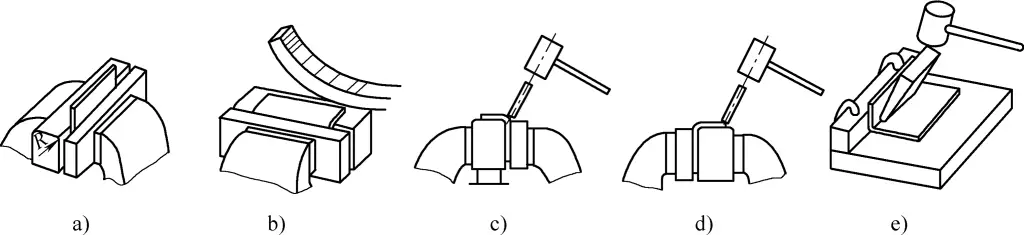
a) Плотно зажмите манометром.
b) Установите в направлении R края калибровочного железа
c) Забейте молотком R-образную часть заготовки
г) Сжать и подогнать под форму
e) Устранить коробление и пружинящую спинку
(2) Сгибание нескольких краев
Метод гибки нескольких кромок такой же, как и для гибки одной кромки, но следует обратить внимание на последовательность гибки. Если для гибки используется калибровочное железо, то, как правило, последовательность сначала внутренняя, затем внешняя, чтобы обеспечить размеры каждой части гнутой детали, как показано на рис. 7a и 7b (цифры на рисунке указывают на последовательность гибки).
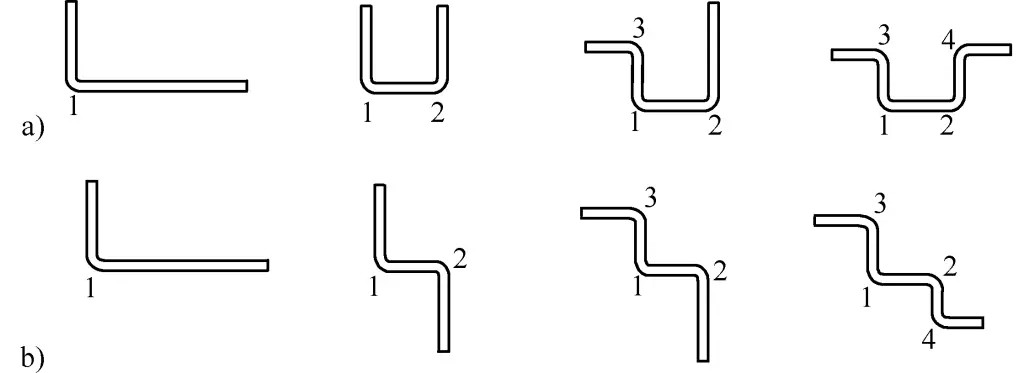
При сгибании нескольких кромок необходимо учитывать, что детали с несколькими кромками состоят из нескольких однокромочных сгибов. Последовательность сгибания необратима, и выполнение последующего сгиба не может исправить предыдущий, поэтому после сгибания необходимо тщательно проверить каждую кромку, выравнивая ее с помощью квадратной линейки, чтобы обеспечить прямые края. Каждый размер кромки должен быть точным; в противном случае совокупность ошибок сделает повторную обработку невозможной.
Во время формовки каждый изгиб можно прижать длинной деревянной доской, затем деревянную доску кладут плашмя на согнутый край и постукивают по ней деревянным молотком, пока она не прилегает к форме, обеспечивая прямолинейность изгиба и отсутствие пульсаций, как показано на рис. 8. Железная площадка на тисках должна быть хорошо набита, иначе материал будет проскальзывать во время простукивания, что повлияет на размеры сгиба.
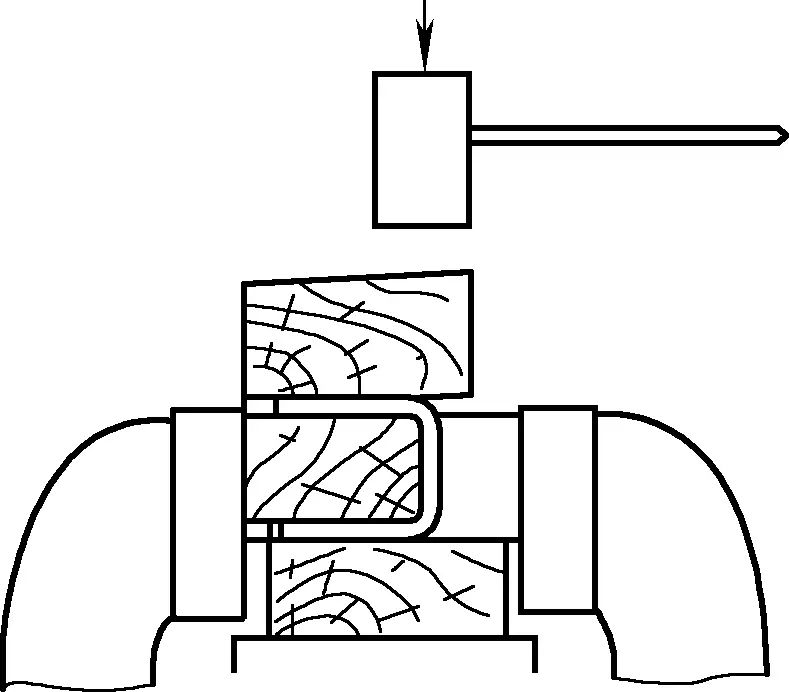
3. Меры предосторожности при ручном сгибании
Детали из листового металла, сгибаемые вручную, обычно представляют собой тонкие листы. Из-за их слабой несущей способности при воздействии локальных ударных нагрузок материал подвержен дефектам коробления из-за уменьшения локальной толщины. Поэтому нагрузка, прикладываемая к материалу, должна быть распределенной (например, линейной или поверхностной), а любая концентрированная нагрузка на поверхность материала запрещена.
Если сгибаемый материал представляет собой лист цветного металла, то твердость поверхности низкая. Чтобы избежать следов от молотка на поверхности материала при ручной гибке, твердость поверхности используемых инструментов должна быть ниже твердости материала, например молотков и реек из чистой меди, твердой древесины или резины.
При гибке нескольких кромок, ввиду необратимого и неисправимого характера деформации при гибке, перед гибкой необходимо произвести точные расчеты и разметку. Порядок сгибания кромок должен быть разумно организован, и каждый угол кромки и радиус сгиба R должны быть достигнуты, прежде чем переходить к следующей кромке. В противном случае накопленные ошибки повлияют на общую точность размеров деталей с несколькими сгибаемыми кромками и не смогут быть исправлены.
II. Операция прокатки кромок
Завальцовка кромок подразумевает закатывание края листового материала. Основные методы включают прокатку проволочной кромки и прокатку полой кромки. Поскольку листовой материал, используемый для прокатки кромок, обычно тонкий (толщина < 1 мм), с низкой жесткостью и прочностью, прокатка кромок позволяет увеличить площадь поперечного сечения и повысить жесткость и прочность конструкции, достигая легкого веса и высокой прочности. Поэтому прокатка кромок широко используется в обработка листового металла.
1. Расчет длины необработанной кромки
Как и в других процессах ручной гибки листового материала, точное определение длины необкатанной кромки является необходимым условием для обеспечения качества детали с обкатанной кромкой. На рисунке 9 показана принципиальная схема расчета длины необкатанной кромки, а формула расчета длины необкатанной кромки l имеет вид
l=d/2+3/4π(d+t)
В формуле
- d - диаметр проволоки (мм);
- t - толщина листа (мм).
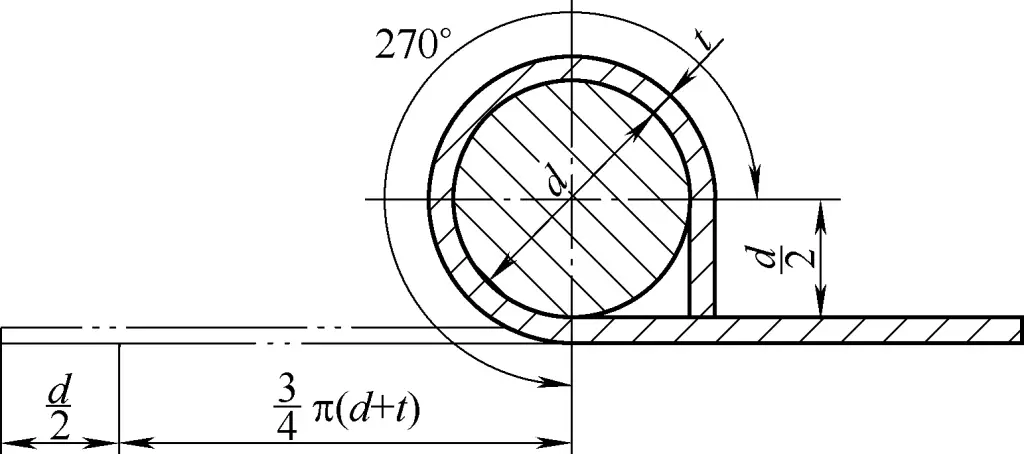
Толщина проволоки определяется в зависимости от размера детали и силы, которую она будет выдерживать. Как правило, диаметр проволоки более чем в три раза превышает толщину листового материала.
2. Процесс прокатки кромок
Инструменты, используемые для прокатки кромок на различных конструкциях, могут отличаться, но процесс и методы работы в целом схожи. На рис. 10 показан процесс ручной прокатки кромок проволокой, который выглядит следующим образом:
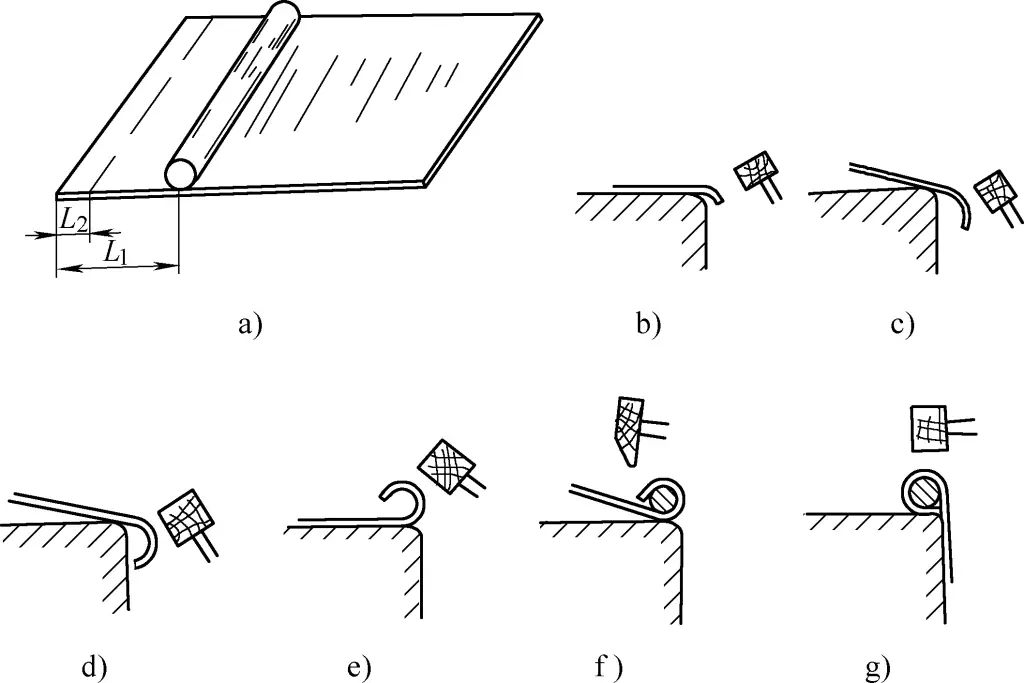
1) Нарисуйте две линии прокатки краев на материале заготовки, как показано на рис. 10a, где:
L1=2.5d
L2=(1/4~1/3)L1
В формуле d - это диаметр проволоки.
2) Поместите заготовку на платформу (или квадратную железку, дорожку и т.д.) с размером открытой платформы, равным L2Левой рукой нажмите на заготовку, а правой нанесите удар молотком по открытой кромке платформы, согнув ее до 85° ~ 90°, как показано на рис. 10b.
3) Вытяните и согните материал заготовки наружу, пока край платформы не совпадет с линией прокатки второго края, что означает, что размер открытой платформы равен L1, и прижмите край, который был задет ранее, к платформе, как показано на рисунках 10c и 10d.
4) Переверните заготовку, переверните ее лицевой стороной вверх и аккуратно и равномерно простучите молотком по перекатанному краю, постепенно формируя круговую дугу, как показано на рис. 10e.
5) Вложите проволоку в прокатанный край, начиная с одного конца, чтобы проволока не выскочила, сначала закрепите один конец, а затем продолжайте сегмент за сегментом. Закрепив всю длину, аккуратно вбейте проволоку в кромку, чтобы она плотно прилегала к ней, как показано на рис. 10f.
6) Переверните заготовку так, чтобы интерфейс упирался в край платформы, и аккуратно забейте ее молотком, чтобы закрепить интерфейс, как показано на рис. 10g.
Процесс ручной прокатки полых кромок такой же, как и при прокатке проволочных кромок, за исключением того, что проволока удаляется в конце. Чтобы удалить проволоку, зажмите один конец и поверните деталь, потянув ее наружу.
3. Обработка дефектов на операциях прокатки кромок
При прокатке кромок длина прокатанной кромки может быть неправильной из-за различий в раскрое материала или методах работы. Хотя для различных конструкций деталей с прокатанной кромкой из листового металла могут использоваться разные инструменты, методы и меры обработки в целом одинаковы. Следующее объяснение основано на операции прокатки кромки конической раковины (см. рис. 11).
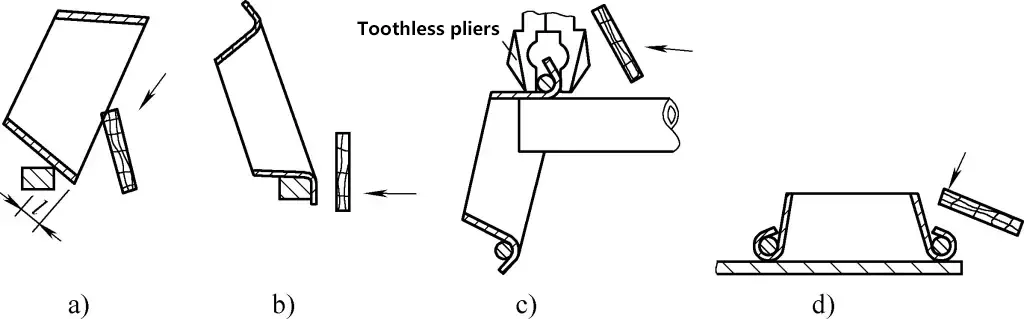
Чтобы повысить эффективность прокатки кромок без повреждения материала, лучше всего использовать плоскую доску для прокатки кромок. Плоская доска может использовать плоскость или кромку для прокатки кромки. Можно также использовать тупую кромку молотка, но это с большей вероятностью приведет к повреждению материала. Последовательность операции прокатки кромки и методы устранения дефектов работы следующие:
1) С помощью компаса проведите линию сгиба на внутренней стороне корпуса бассейна, l=2,5d, где d - диаметр проволоки.
2) На краю платформы или горизонтального стального рельса, используя небольшую площадь соприкосновения с краем, постепенно отгибайте край наружу по линии сгиба с помощью плоской доски. Не складывайте сразу весь край, складывайте его постепенно, как показано на рис. 11a.
3) Поместите корпус бассейна на край платформы, постепенно регулируйте величину сгиба и используйте плоскую доску, чтобы расправить сложенный край для подготовки к следующему этапу прокатки края, как показано на рис. 11b.
4) Поместите корпус бассейна на конец круглой стальной или толстостенной стальной трубы, поместите проволоку в прокатанный край, зажмите ее беззубыми плоскогубцами и с помощью плоской доски загните край вниз с обеих сторон плоскогубцев, пока проволока не будет закреплена (достаточно 4-5 мест по окружности, чтобы закрепить проволоку), как показано на рис. 11c.
Следующий шаг - закрепление валика. Все еще используйте плоскогубцы, чтобы плотно зажать его, чтобы предотвратить отскок и повысить эффективность прокатки. Зажмите участок и бейте по нему молотком, пока весь край не будет закреплен. Если на продольном шве есть несколько перекрывающихся слоев, можно подбить его железным молотком.
5) Установите корпус бассейна на платформу и с помощью плоской доски или железного молотка плотно прибейте внешний край завальцованного края, одновременно регулируя уровень завальцованного края в устье бассейна, как показано на рис. 11d.
6) Если длина завальцованной кромки недостаточна для плотного прилегания проволоки (завальцованная кромка слишком коротка), наклоните корпус бассейна вниз и с помощью плоской доски ударьте по завальцованной кромке вниз и наружу. Проволока и прокатанный край сместятся к меньшему концу, увеличивая длину прокатанного края, как показано на рис. 12a.
Если длина прокатанной кромки слишком велика, наклоните корпус бассейна вниз и с помощью плоской доски подбейте меньший конец прокатанной кромки. Проволока и прокатанная кромка переместятся к большему концу, сокращая длину прокатанной кромки, как показано на рис. 12b.
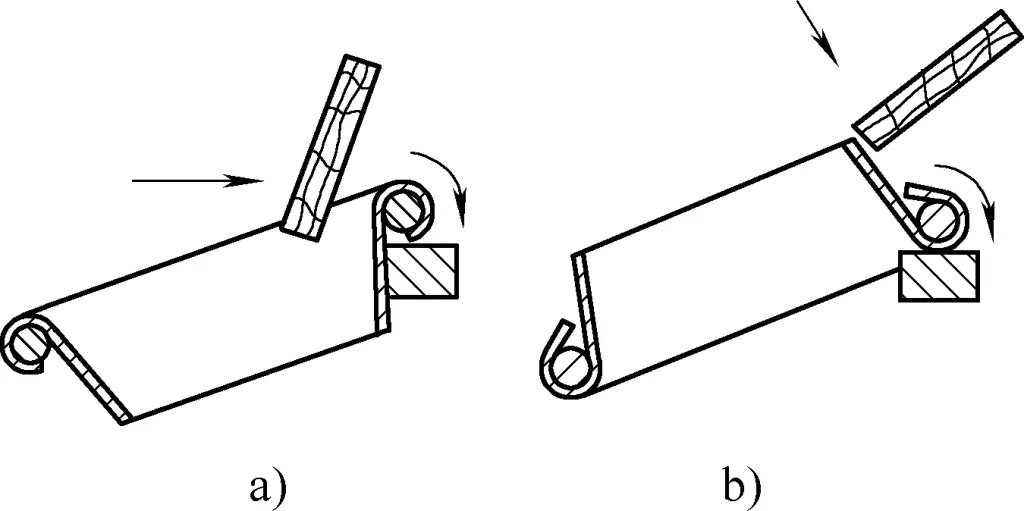
a) Метод обработки при недостаточной длине прокатанной кромки
b) Метод обработки чрезмерной длины кромки проката
III. Ручное рифление круглых и квадратных труб
Кругло-квадратные трубы - распространенные детали из листового металла, встречающиеся в производстве. Если листовой материал тонкий и не может быть сформован с помощью пресса, обычно используется ручное рифление и формовка. Для удобства обработки и сборки материал обычно разрезают на две половины для обработки, а затем сваривают вместе. Если высота не превышает 100 мм и требуется хороший внешний вид, материал может быть разрезан на цельные куски, затем обработан пазами и сварен для придания формы.
1. Изготовление формы
Чтобы вручную изготовить кругло-квадратную трубу с прорезью, необходимо сначала создать форму. Форма, используемая для ручного изготовления пазов, может быть прямой, как швеллерная сталь, или радиальной, изготовленной из круглой стали. Первый вариант используется в случае тонких листов, небольших внешних размеров и малых партий, но часто приводит к появлению большого количества дефектов. Второй вариант используется в серийном производстве, что приводит к уменьшению количества дефектов и обеспечивает удобство сборки.
На рис. 13 показана форма для небольшой кругло-квадратной трубы ручной работы.
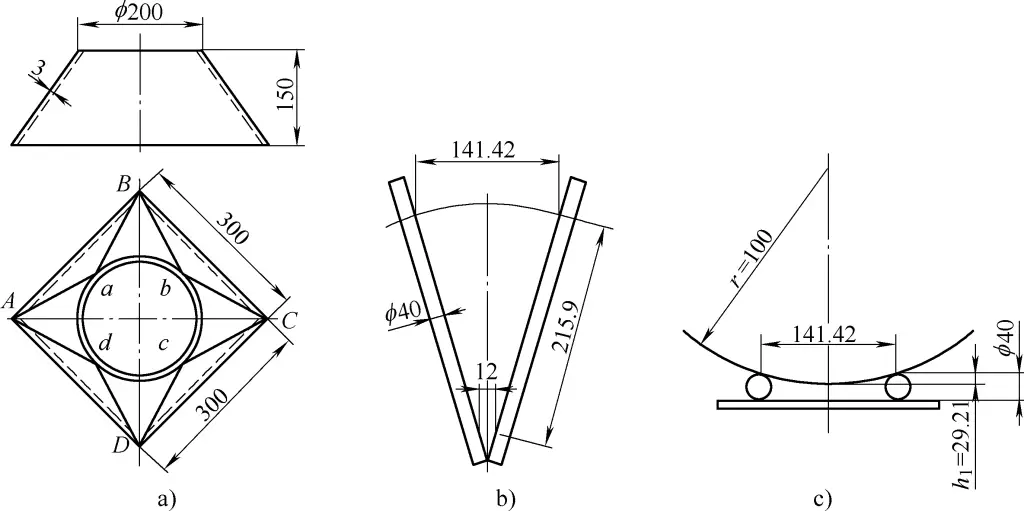
a) Чертеж детали
б) Структура пресс-формы
в) Принцип расчета диаметра круглой стали пресс-формы
На рис. 13a показан чертеж детали кругло-квадратной трубы, а на рис. 13b - изготовленная радиальная пресс-форма. Пресс-форма изготовлена из круглой стали, расположенной радиально, причем длина круглой стали определяется самой длинной переходной линией кругло-квадратной трубы плюс дополнительный запас около 100 мм. Поскольку восемь переходных линий круглой квадратной трубы имеют одинаковую длину (т.е. на рис. 13a, Aa=Ba=Bb=Cb=Cc=Dc=Dd=Ad=l), длина l=√(1472+(147-97)2+1502)мм (рассчитано на основе внутреннего слоя листовой детали, где 97 - внутренний радиус круглого конца, 147 - половина внутренней длины квадратного конца, а 150 - высота детали); ширина отверстия на большом конце пресс-формы составляет 1/4 длины внешней хорды круглого конца, рассчитанной как (200×sin45°)мм=141,42 мм. Учитывая, что толщина листа относительно мала (3 мм), а два слоя составляют 6 мм, плюс запас в два раза больше толщины листа, 6 мм, размер малого конца 12 мм является достаточным. На рисунке 13c показан принцип расчета диаметра круглой стали пресс-формы, где расстояние h1 от верхнего конца круглой стали до нижней части формируемой детали после формирования дуги составляет [100-√(1002-141.422/4)]мм=29,29 мм. Учитывая соответствующий зазор при формовке, диаметр круглой стали устанавливается равным ϕ40 мм.
В производственных операциях размещение форм для ручного пазования также может быть выполнено без вышеупомянутых расчетов, приблизительно позиционируя круглую сталь под углами от 10° до 15° и диаметром от ϕ25 до ϕ60 мм.
2. Методы ручного пазования
Для небольших кругло-квадратных труб материал обычно разрезается либо как половина расширенного материала, либо как целый материал. На рисунке 14 показан метод ручной прорезки с использованием цельного материала, где на рисунке 14a показано соотношение между вогнутой формой и пластиной для пересечения плоскости и изогнутого треугольника во время прорезки. На рисунке 14b показано соотношение между вогнутой формой и пластиной для изогнутого треугольника во время пазования.
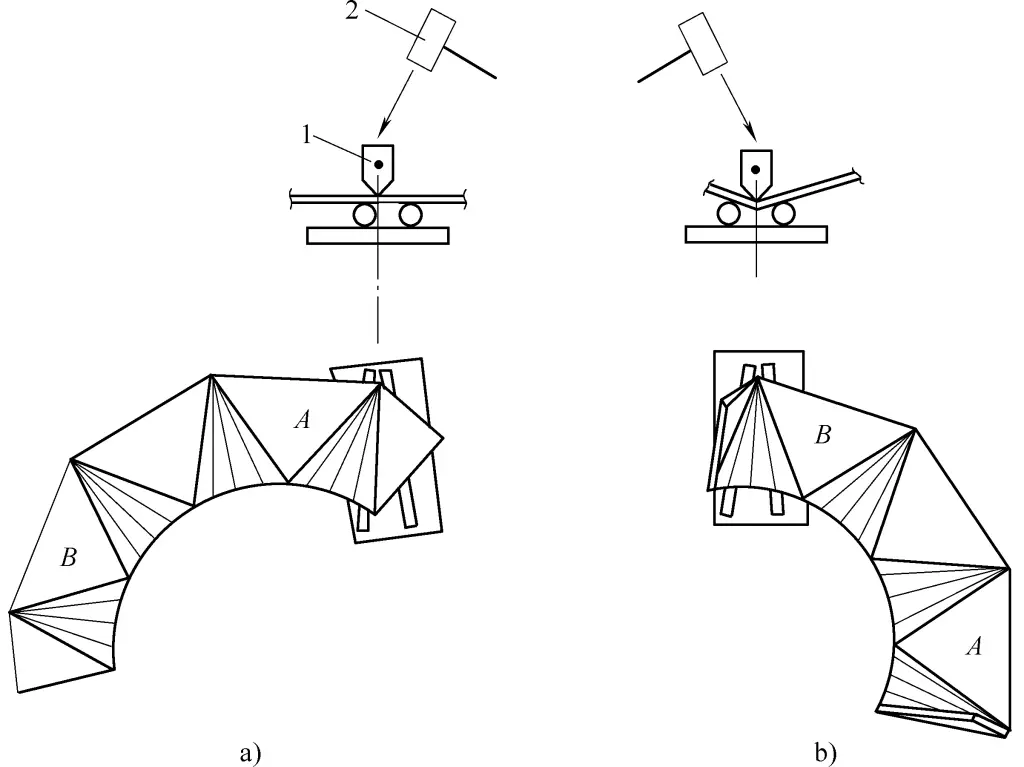
a) Положение вогнутой формы и пластины при прорезке торцевых треугольников
b) Положение вогнутой формы и плиты при прорезке переходных линий
Дуговой молоток с 1 пазом
2-Кувалда
При выполнении пазов необходимо придерживаться принципа: начинать с обоих концов, а затем с середины. В противном случае, из-за поднятия согнутых частей, это повлияет на движение кувалды.
Во время пазования каждый короткий участок паза следует проверять с помощью пластины-образца, чтобы убедиться, что кривизна идеально соответствует шаблону или немного превышает его.
Метод пазования цельного материала такой же, как и при пазовании полуматериала. После завершения пазования половины материала толстые листы большого размера должны иметь фактическую форму, очерченную на платформе, с приваркой ограничителей для точной монтажной сварки; тонкие листы малого размера могут быть непосредственно собраны и сварены без очерчивания фактической формы.
После сборки и точечная сварка формирования, могут возникнуть различные дефекты сборки, которые можно устранить следующими способами.
(1) Разрывы на малом или большом конце
На рис. 15 показана ситуация, когда на большом конце имеется зазор. В этом случае сначала прочно приваривайте точечной сваркой противоположный конец, затем приваривайте точечной сваркой верхний конец с этой стороны. Приварите короткий угольник с просверленными отверстиями на конце с большим зазором, приварив только внешнюю часть, затем затяните гайку, чтобы сблизить стальные пластины на обоих концах.
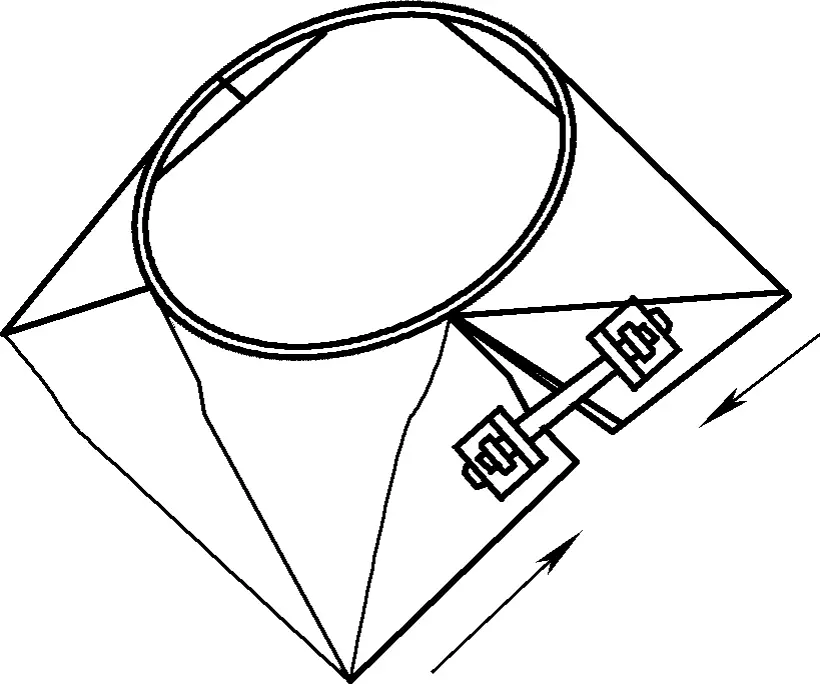
При точечной сварке верхнего порта сварной шов должен быть прочным, но не слишком длинным. Если сварной шов слишком короткий, он недостаточно прочный; если слишком длинный, натяжение болта увеличится. При затягивании болта постоянно проверяйте деформацию зоны точечной сварки. Если есть трещины или отпавшие чешуйки оксида, немедленно устраните их.
Метод обработки следующий: сначала выполните точечную сварку в небольшой точке рядом с предполагаемой трещиной, полностью охладите ее, а затем усильте сварной шов в месте предполагаемой трещины. Не начинайте точечную сварку с предполагаемой трещины, так как нагрев увеличит хрупкость шва, что приведет к образованию полной трещины.
(2) Один стыковочный порт деформирован
На рис. 16 показана ситуация, когда один стыковочный порт выровнен, а другой деформирован. При сборке сначала выполните точечную сварку выровненного стыковочного порта и установите его на платформу.
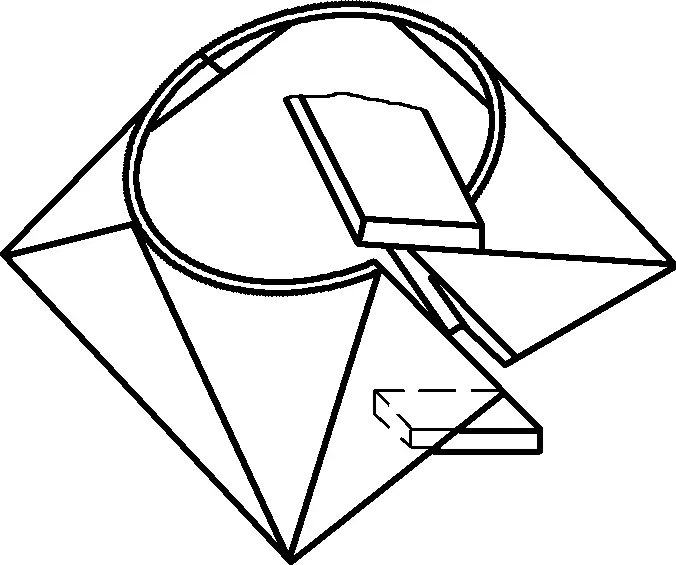
Можно использовать следующие методы: Один из них - метод давления с подкладкой, при котором под не деформированный порт подкладывается более толстая стальная пластина, позволяющая прижать деформированный порт. Используйте прижимную планку и приспособление, чтобы прижать его в самой высокой точке искривления. Если на обоих концах нет несоответствий, выполните точечную сварку в одной точке, а после устранения всех дефектов выполните полную точечную сварку. Обратите внимание, что подкладное железо следует подкладывать только под не деформированный конец, чтобы не повлиять на движение вниз деформированного конца.
Второй метод - метод спирального подхода. Используя резьбовой стержень с гайкой на одном конце, зацепите не деформированный порт за нижний конец, поместите верхний конец через перфорированную пластину на деформированный порт, затяните гайку, и деформированный порт будет постепенно перемещаться вниз. После того как оба порта будут выровнены, выполните точечную сварку.
(3) Круглый конец не идеально круглый
Перед завершением точечной сварки проверьте геометрические размеры детали. С помощью шаблона проверьте округлость круглого торца, и если есть какие-либо неровности, используйте метод обратного молотка для исправления. Если неровности имеются в радиальном направлении, расположите ударный молоток и опорный молоток горизонтально, как показано на рис. 17a; если торцевое отверстие локально не идеально круглое, расположите ударный молоток и опорный молоток вертикально, как показано на рис. 17b.
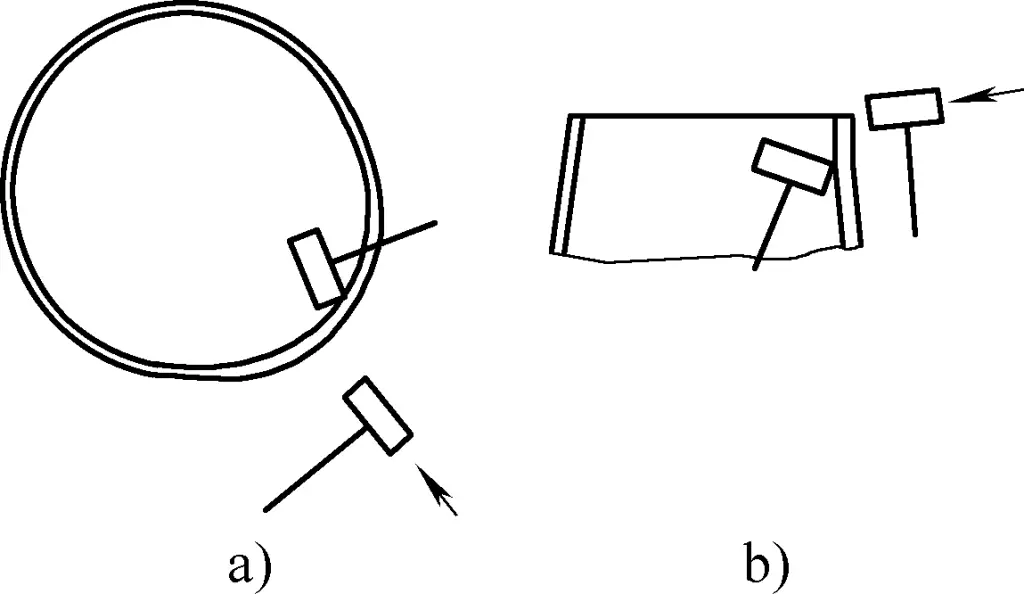
Во время работы опорный молоток должен располагаться вблизи самой высокой точки, а ударный молоток должен бить по самой высокой точке. Чем ближе опорный и ударный молотки, тем больше сила коррекции, но они не должны перекрывать друг друга.
(4) Неравные диагональные линии на конце квадрата
После сборки распространенным дефектом являются неравные диагональные линии на конце квадрата. Методы исправления показаны на рисунке 18. На рис. 18a показано использование цепного подъемника (или винтового домкрата) для исправления, а на рис. 18b - использование пресса (или прижимной планки) для исправления.
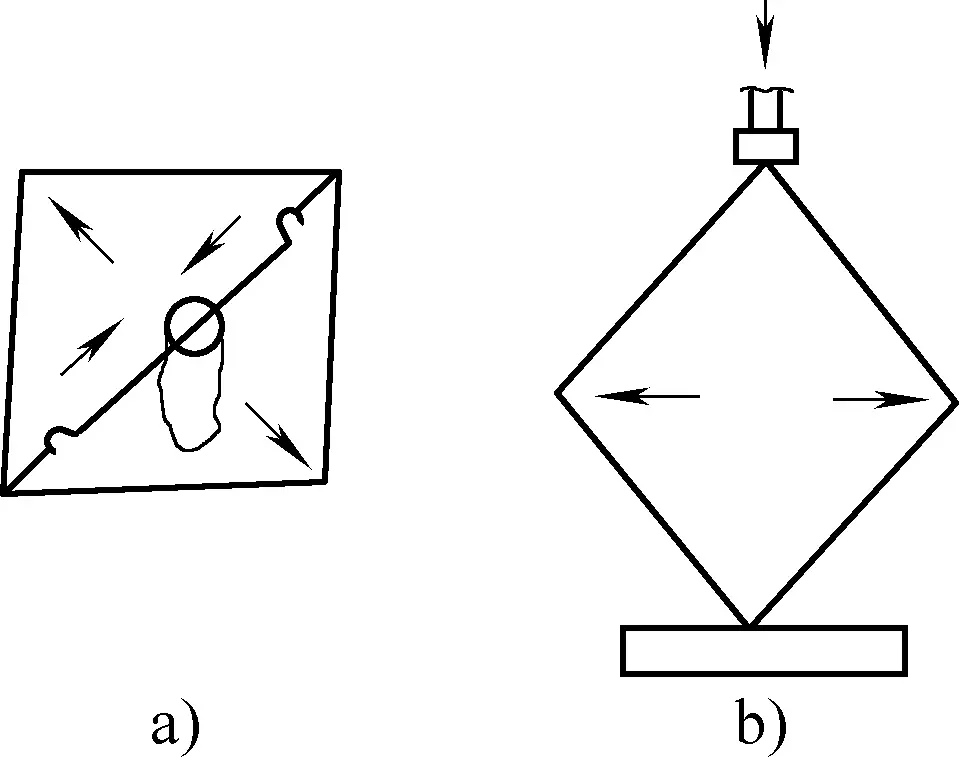
Если сила коррекции невелика, можно использовать кувалду для ручной коррекции по диагонали; если сила коррекции велика, можно применить механическую силу, например пресс или рихтовочную машину. В процессе коррекции необходимо в любое время проверять, чтобы избежать чрезмерной коррекции.
3. Метод исправления дефектов насечки
Для устранения проблем, возникающих в процессе нанесения насечек, можно использовать следующие методы.
(1) Неравномерное выравнивание краев
На рисунке 19a показан трехмерный вид неровного или локально неровного выравнивания кромок, а на рисунке 19b - метод молотка. Для улучшения эффекта коррекции следует отметить, что подкрепляющий молоток должен располагаться рядом с точкой удара, чем ближе, тем лучше, но не перекрывать ее. Чем ближе расстояние, тем больше сила коррекции.
Кроме того, контактная поверхность опорного молотка должна быть как можно меньше, использование края молотка для контакта обеспечивает гораздо большую корректирующую силу, чем полная поверхность молотка. На рис. 19c показан метод подвески на платформе. Поместите неровный край пластины на платформу и ударяйте молотком по выпуклым точкам, чтобы исправить дефект.
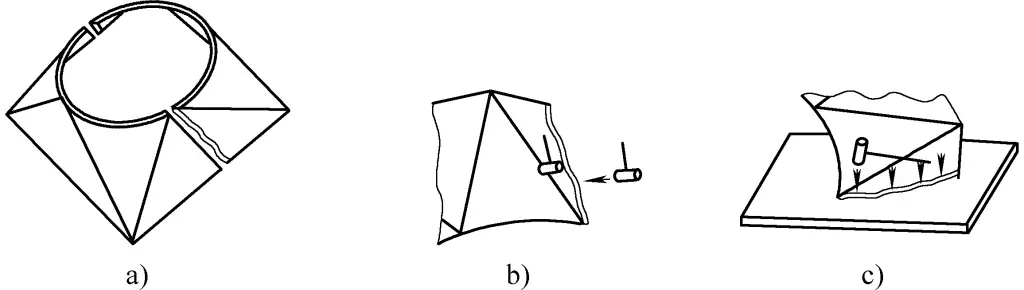
a) 3D-вид неровного выравнивания краев
б) Метод молотка
c) Метод подвески платформы
(2) Внешние углы
На рис. 20a показана трехмерная форма внешнего угла, образовавшегося в стыковом соединении. Первопричиной этого дефекта является недостаточная верхняя дуга: либо угол изгиба линии гребня недостаточен, либо кривизна поверхности дуги недостаточна. Метод исправления заключается в изменении формы поверхности дуги на пресс-форме и проверке с помощью шаблона в любое время.

(3) Внутренние углы
На рис. 20b показана трехмерная форма внутренних углов, образованных двумя соединенными встык прямыми кромками. Этот дефект вызван чрезмерной верхней дугой в процессе надсечки: либо кривизна на линии гребня слишком велика, либо кривизна поверхности дуги слишком велика.
Метод коррекции заключается в том, чтобы провести молотком по линии гребня или поверхности дуги с внешней стороны, проверяя в любое время шаблоном, и скорее оставить его недостаточным, чем чрезмерно корректировать, чтобы избежать повторного образования дефекта внешнего угла.
(4) Наклонное вверх стыковое соединение
На рис. 21 показана трехмерная форма стыкового соединения с наклоном вверх. Основная причина этого дефекта - недостаточный угол изгиба на левом конце линии гребня. Для исправления требуется увеличить угол изгиба на пресс-форме и соответствующим образом увеличить кривизну на линии гребня на правом конце.
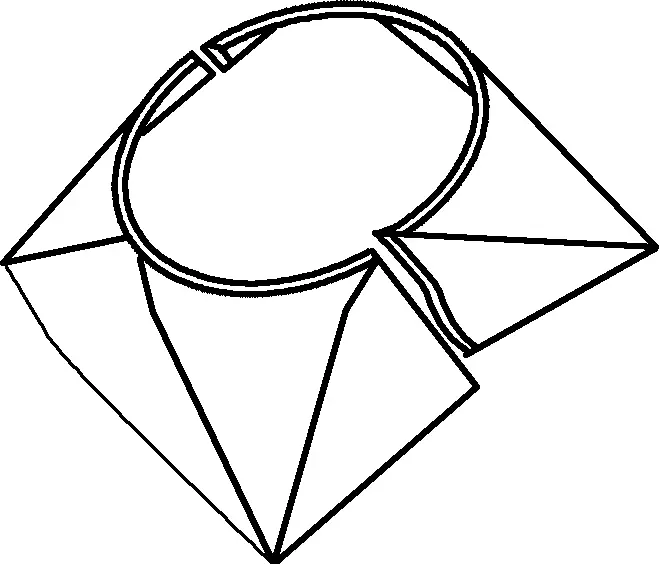
IV. Ручная выемка небольших конических фрустумов
Конические фрустумы также являются распространенными компонентами листового металла в производстве. Они имеют прямые линии с меньшим расстоянием на малом конце и большим расстоянием на большом конце. Большие конические фрусты обычно формируются путем сгибания с прокатная машинаВ то время как небольшие конические фрустумы обычно вырезаются вручную, когда лист металла тонкий и не может быть согнут с помощью прокатного станка.
Аналогично, для удобства вырезания и сборки он обычно разрезается на две половины для вырезания, а затем сваривается. Если высота не превышает 100 мм и требуется эстетичный внешний вид, можно вырезать цельную деталь, а затем сформировать ее с помощью надрезов и сварки.
1. Изготовление формы
Пресс-форма для ручной выемки конической формы может быть выполнена в виде прямого паза или в виде излучающих больших и малых отверстий. В первом случае, как правило, больше дефектов, а во втором - меньше.
Как правило, конусность формы должна быть такой же, как и конусность фруста, что благоприятно для улучшения качества заготовки и уменьшения дефектов. Если конусность отличается, это не способствует улучшению качества заготовки и может привести к увеличению количества дефектов. На рис. 22 показана форма для ручной выемки небольшой конической фрустумы.
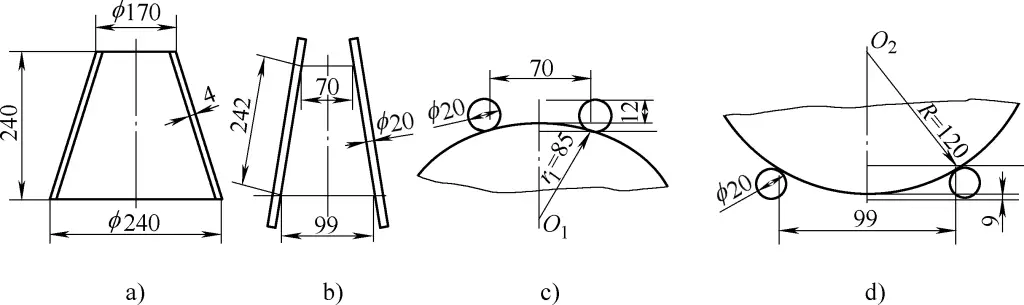
a) Чертеж детали
б) Структура пресс-формы
c), d) Принцип расчета диаметра круглой стали пресс-формы
На рисунке 22a показан чертеж детали маленькой конической формы, а на рисунке 22b - радиационной формы.
Форма изготовлена из радиально расположенной круглой стали, причем длина круглой стали определяется длиной генератрицы конической фрустумы плюс припуск от 50 до 100 мм. Длина генератрицы конической фрустумы l=√[ (120-85)2 + 2402] мм = 242 мм (где 120 - внешний радиус большого отверстия, 85 - внешний радиус малого отверстия, а 240 - высота конуса).
Расстояние между малыми концами формы может быть большим или меньшим, но максимальное не может превышать диаметр малого конца конуса. В данном примере он принят равным 70 мм. Расстояние открытия n большого конца определяется в соответствии с отношением расстояния между большим и малым концами пресс-формы к отношению диаметров большого и малого концов конического фруста, т.е.: n: 70 = 240: 170, поэтому n принимается равным 99 мм.
На рисунках 22c и 22d показан принцип расчета диаметра круглой стали, используемой в пресс-форме. Существует два принципа определения круглой стали: первый заключается в поддержании определенного расстояния между сформированной фрустумой и опорной плитой, а второй - в том, что круглая сталь должна обладать достаточной жесткостью.
Из-за неодинаковых радиусов дуг на большом и малом концах расстояние между ними и опорной плитой должно рассчитываться отдельно. При условии использования круглой стали толщиной ϕ20 мм расстояние от нижней части детали до опорной плиты на малом конце после формовки составляет l1 = 20 – [85 – √(852 – 35 2)] мм = 12 мм, как показано на рисунке 22c.
Аналогично, расстояние от нижней части детали до опорной плиты на большом конце после формовки составляет l2 = 20 – [120 – √(1202 – 49.52)] мм = 9 мм, как показано на рисунке 22d. Поэтому выбор диаметра круглой стали ϕ20 мм является обоснованным.
2. Ручные методы нанесения насечек
Метод ручной обработки желобка конуса в основном такой же, как и метод обработки дуговой части небольшой кругло-трубчатой арочной крыши. Для формовки в основном используется большой молоток и желобковый дуговой молоток на радиальной пресс-форме, по принципу: сначала желобки на концах, затем в середине, постепенно углубляясь от мелких, и с использованием шаблона для проверки кривизны в любое время.
3. Метод исправления дефектов обработки канавок
Для устранения проблем, возникающих при фрезеровании, можно использовать следующие методы.
(1) Внешняя форма персика
На рис. 23a показана трехмерная форма внешнего персика, образованного двумя стыковочными отверстиями. Причиной внешней персиковой формы является недостаточное формирование формы верхней торцевой дуги во время обработки канавки (особенно на конце). На рисунках 23b и 23c показаны методы коррекции, причем на рисунке 23b верхняя дуга корректируется с внешней стороны конуса, а на рисунке 23c - с внутренней.
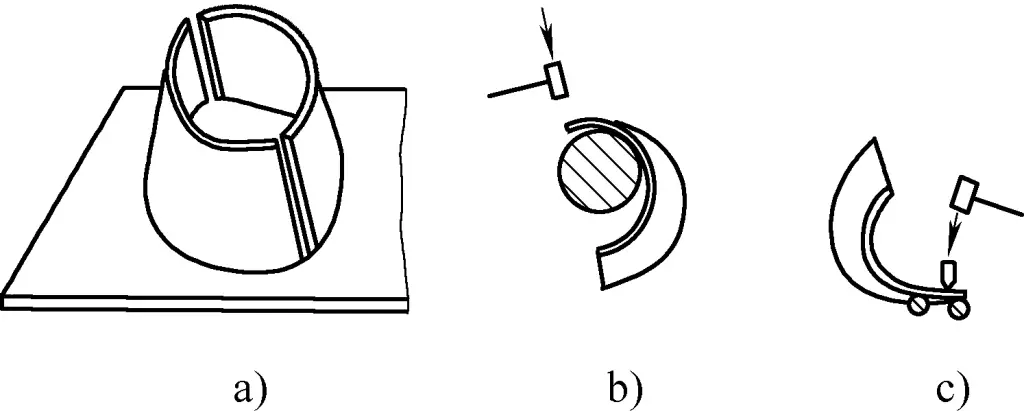
a) Трехмерная диаграмма внешней формы персика
б) Коррекция извне
в) Коррекция изнутри
(2) Внутренняя форма персика
На рис. 24 показана трехмерная форма внутреннего персика, образованного двумя стыковочными отверстиями. Причиной внутренней персиковой формы является чрезмерно сформированная верхняя концевая дуга или чрезмерно сформированная дуга при предварительной гибке.
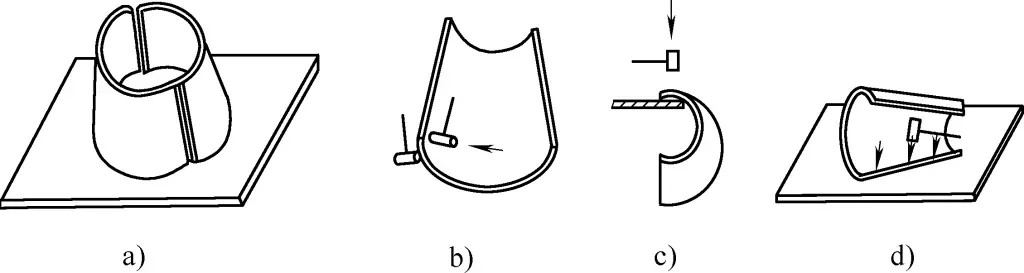
a) Трехмерная диаграмма внутренней формы персика
b) Метод опорного молотка
c) Метод консольной дуги
d) Метод дуги на подвесной платформе
На рисунках 24b, 24c и 24d показаны методы коррекции, причем на рисунке 24b показан метод подкрепляющего молотка, при котором подкрепляющий молоток помещается на излишне сформированную дуговую часть, а силовой молоток прикладывается к краю, перемещаясь и ударяя по нему молотком для его коррекции.
Следует отметить, что расстояние между точкой приложения силы и точкой опоры должно быть небольшим (но не перекрываться). При высокой жесткости толщины плиты работу могут выполнять два человека, а при низкой жесткости - один. На рис. 24c показан метод консольной дуги, при котором дуга проверяется с помощью шаблона во время формования, и необходимо следить за тем, чтобы не перекорректировать ее, так как формование верхней дуги сложнее, чем формование дуги.
На рис. 24d показан метод дуги с подвесной платформой, при котором даже если переформированная часть дуги соприкасается с платформой, противоположный край подвешивается, и сила прикладывается вдоль края для его исправления. Необходимо следить за равномерностью удара молотком, чтобы избежать резких изгибов и смещения краев.
(3) Большая малая торцевая щель и локальная непрерывная внутренняя выпуклость
На рисунке 25a показана трехмерная форма большого малого концевого зазора, образованного, когда большая концевая дуга правильная, но малая концевая дуга недостаточная. На рисунке 25b показана трехмерная форма непрерывной внутренней выпуклости, когда большая концевая дуга правильная, но имеется локальный дефект гребня в направлении генератрицы. Эти два дефекта имеют одинаковую природу, поэтому методы их устранения одинаковы. На рисунке 25c показан метод формирования дуги снаружи, а на рисунке 25d - метод формирования дуги изнутри.
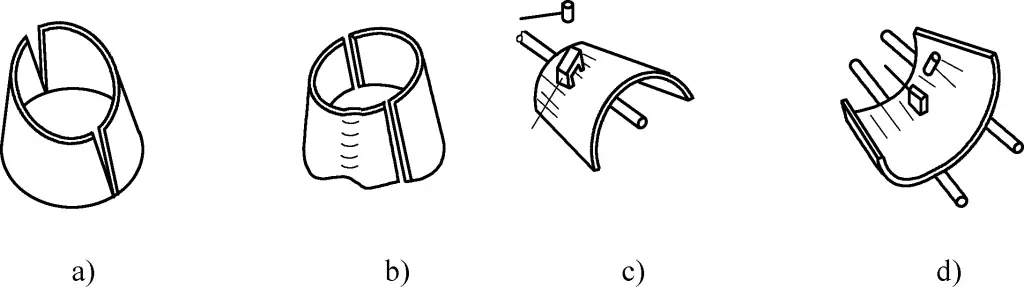
a) Трехмерная диаграмма большого зазора на малом конце
б) Трехмерная диаграмма локальной непрерывной внутренней выпуклости
в) Формирование дуги снаружи
г) Формирование дуги изнутри
Для дефекта, показанного на рис. 25a, формирование дуги ограничено диапазоном малого конца, а длина не должна превышать половины фруста, иначе будет нарушена кривизна большого конца; для дефекта, показанного на рис. 25b, непрерывное формирование дуги может быть выполнено локально, либо изнутри наружу, либо снаружи внутрь.
(4) Крупный крупный гэп
На рисунке 26a показана трехмерная форма большого зазора на большом конце, образовавшегося после размещения одной стороны стыковочного порта и другой стороны, имеющей зазор на большом конце. Причиной этого дефекта является локальный недостаток дуги в точке A на рисунке, в результате чего малый конец опускается на величину e; на рисунке 26b показана трехмерная форма правильной дуги малого конца, но в целом недостаточной дуги большого конца, в результате чего образуется большой зазор на большом конце. У обоих случаев одна и та же причина, поэтому и методы лечения одинаковы.
На рисунке 26c показан метод формирования дуги снаружи, а на рисунке 26d - метод формирования дуги изнутри. Следует отметить, что длина дуги не должна превышать половины генераторной матрицы, иначе это повлияет на малую кривизну конца.
При устранении дефекта, показанного на рис. 26a, достаточно сформировать локальную дугу только в точке A, причем ее длина не должна превышать половины генераторной матрицы. Как только кривизна будет скорректирована, несоосность на малом конце исчезнет сама собой.
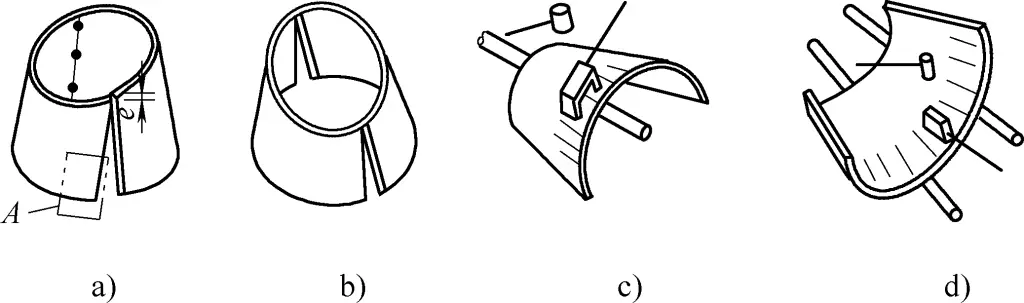
a) Трехмерная диаграмма большого зазора на одном большом конце
б) Трехмерная диаграмма большого зазора на обоих больших концах
в) Формирование дуги снаружи
г) Формирование дуги изнутри
(5) Общая переформированная дуга или локальная непрерывная переформированная дуга
На рисунке 27a показана трехмерная форма левой веерной переформированной дуги, в результате чего четыре угловые точки отклоняются внутрь, а две верхние угловые точки находятся слишком высоко. На рисунке 27b показана трехмерная форма локальной непрерывной переформированной дуги вдоль генераторной матрицы, вызывающей большой зазор в стыковочном порту. У обоих случаев одна и та же причина, поэтому и методы лечения одинаковы.
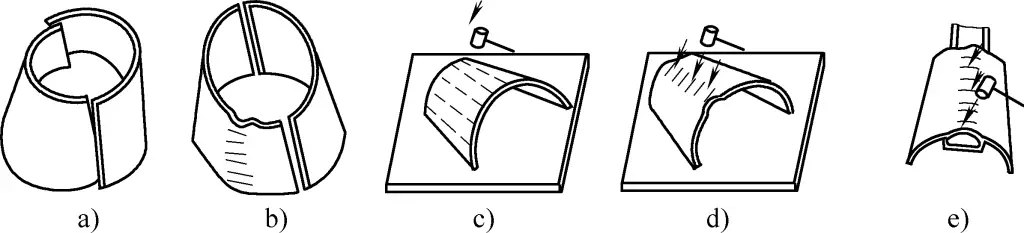
a) Трехмерная диаграмма общей переформированной дуги
b) Трехмерная диаграмма локальной переформированной дуги
c), d) Метод молотковой дуги
e) Метод консольной дуги
На рис. 27c показан метод размещения выпуклой поверхности вверх на платформе или земле и нанесения ударов молотком по всей длине генераторной матрицы для коррекции. Для повышения эффективности формирования дуги можно использовать одну ногу для наступания и нажима вниз перед ударом молотка, чтобы предотвратить отскок и улучшить эффект коррекции. Кривизну следует постоянно проверять с помощью шаблона, чтобы избежать чрезмерного формования, так как сформировать дугу сложнее, чем исправить ее.
На рисунке 27d показан метод коррекции локальной непрерывной переформированной дуги, работа которого аналогична рисунку 27c. На рисунке 27e показан метод консольной дуги, который можно использовать для локальной коррекции непрерывной переформированной дуги. Во время работы один человек должен надежно держать инструмент, а другой - бить молотком, чтобы он не отскочил и не нанес травму.
(6) Чрезмерное перекрытие верхнего конца и большой зазор на нижнем конце
На рис. 28 показана трехмерная форма чрезмерного перекрытия верхнего конца и большого зазора на нижнем конце. Причиной этого дефекта является локальная переформированная дуга в верхней концевой части A и локальная неполноценная дуга в нижней концевой части B, в результате чего верхний конец перекрывается и чрезмерно поднимается, а нижний конец имеет зазор и смещается наружу.
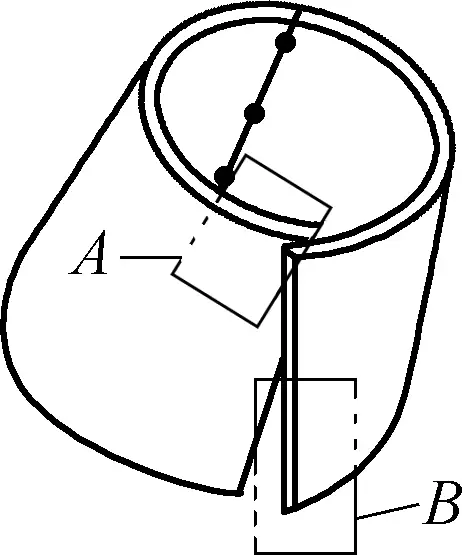
Исправление может быть выполнено с помощью методов формирования и отпускания дуги, показанных на рис. 26 и 27. После коррекции верхняя угловая точка на детали A опустится, нижняя угловая точка на детали B переместится внутрь, и дефект будет устранен.
(7) Несоответствие стыковочных краев
На рисунке 29a показан профиль с неровными или локально выпуклыми и вогнутыми краями. Основная причина этого дефекта - неравномерное усилие молотка при предварительной гибке. На рис. 29b показана схема метода резервного молотка, который используется для улучшения эффекта коррекции. Резервный молоток должен располагаться рядом с выпуклой точкой, по которой нужно ударить, а силовой молоток должен находиться рядом с точкой опоры силы. Чем ближе, тем лучше, так как чем ближе расстояние, тем больше корректирующая сила, но они не должны пересекаться.
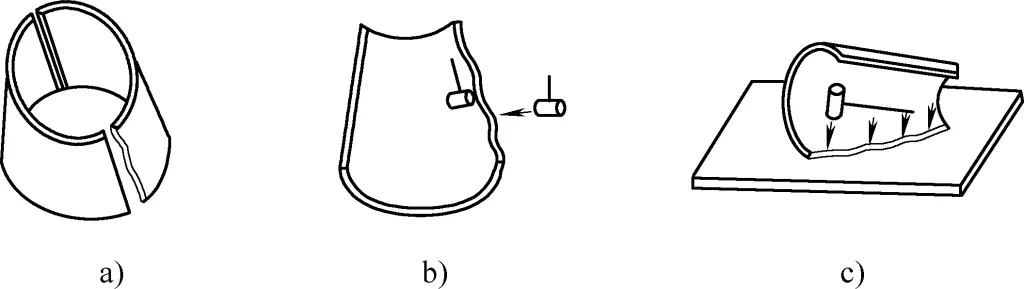
a) Перспективный вид неровных краев
b) Метод резервного молотка
c) Метод подвески платформы
Кроме того, во время работы поверхность контакта силового и резервного молотков должна быть как можно меньше. Корректирующее усилие намного больше при использовании края молотка для контакта, чем при использовании всей поверхности молотка. На рис. 29c показана схема метода подвески платформы для коррекции. Неровный или выпукло-вогнутый край пластины помещается в контакт с платформой, и выпуклая точка ударяется молотком для исправления дефекта.
(8) Зазор на большом (или малом) конце
На рисунке 30a показан вид в перспективе, где один шов двух выровненных сварных пластин имеет зазор на большом конце другого шва. Причина этого дефекта заключается в том, что дуга на малом конце является правильной, в то время как дуга на большом конце является недостаточной. Это можно исправить, используя метод дуги, показанный на рис. 26, или сначала расположив и заварив малое отверстие, а затем расположив и заварив зазор, закрепив два угольника болтами (см. рис. 30a), или используя метод сжатия большого отверстия для его закрытия (см. рис. 30b).
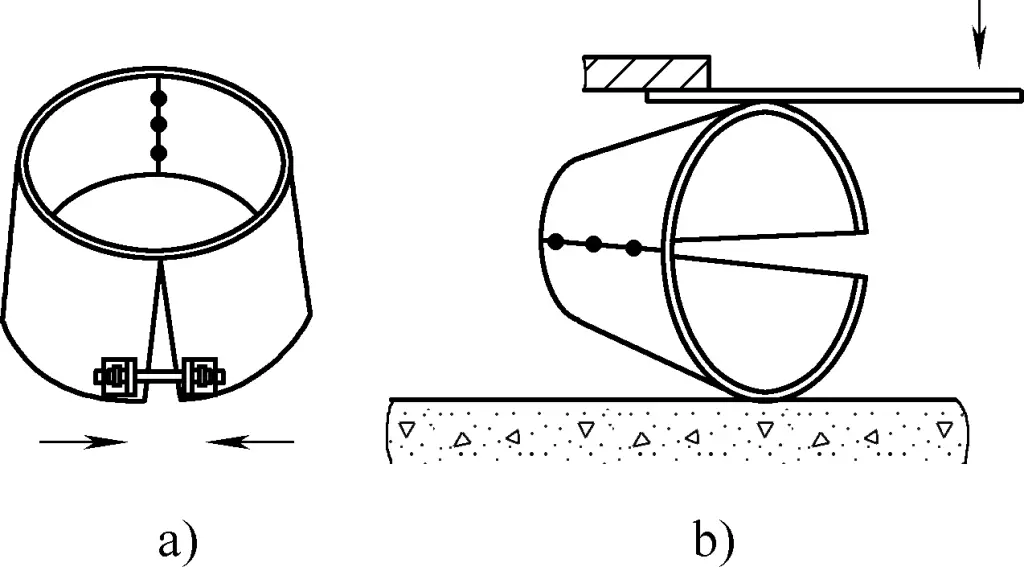
a) Перспективный вид зазора на большом (или малом) конце
б) Сжатие большого порта
Во время работы убедитесь, что малый порт надежно приварен в нужном положении без чрезмерной длины шва. Если шов слишком короткий, его прочность будет недостаточной, что сделает его склонным к растрескиванию и приведет к напрасным усилиям. Слишком длинный шов увеличит тяговое усилие болта.
При затягивании болтов постоянно проверяйте деформацию на позиционных сварных швах на предмет наличия трещин или отслоения оксидного покрытия. Если такие проблемы обнаружены, их следует незамедлительно устранить. Метод заключается в позиционной сварке небольшой точки на участке, подверженном отслоению, дождитесь полного остывания, а затем выполните позиционную сварку другой точки. Категорически не рекомендуется выполнять все позиционные швы сразу, так как это приведет к увеличению термической хрупкости шва, что приведет к образованию трещин.
(9) Твист
На рисунке 31a показан вид в перспективе одной правильно изогнутой пластины и другой изогнутой пластины. Основная причина скручивания - использование неподходящей пресс-формы или неправильное следование пазу для направления оси конуса. Это вызвано несоответствием угловых точек: верхняя угловая точка стороны А ниже и направлена внутрь, а нижняя угловая точка направлена наружу; верхняя угловая точка стороны В направлена наружу и выше, а нижняя угловая точка направлена внутрь и загнута вверх, что приводит к скручиванию.
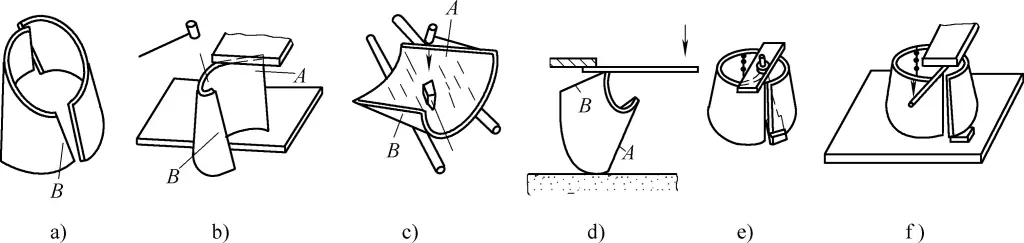
a) Перспективный вид на поворот
b) Метод подвесного молота
в) Метод дуги с обратным пазом
г) Метод прессования прутка
e) Метод вытягивания болтов
f) Метод прессования подушечек
На рисунке 31b показана схема метода подвесного молотка для коррекции. Сторона A помещается внутрь платформы, а верхняя угловая точка прижимается пластиной платформы. Сторона B подвешивается снаружи платформы, и верхняя угловая точка стороны B ударяется молотком вниз, чтобы исправить искривление.
На рисунке 31c показана схема метода коррекции по дуге обратной канавки. При этом формируется обратная канавка, примерно под углом 90° к первоначальному направлению канавки. Верхняя угловая точка стороны A и нижняя угловая точка стороны B перемещаются наружу, а нижняя угловая точка стороны A и верхняя угловая точка стороны B перемещаются внутрь, таким образом исправляя скручивание.
На рисунке 31d показана схема метода прижимания бруса для коррекции. Верхняя угловая точка стороны B помещается под прижимную планку, а нижняя угловая точка стороны A кладется на землю, чтобы предотвратить соскальзывание. Используя тяжелый предмет в качестве точки опоры, приложите усилие к прижимной планке, чтобы плавно исправить искривление.
На рисунке 31e показана схема метода вытягивания болта для коррекции. На рисунке 31f показана схема метода вдавливания накладки для исправления. Во время исправления под нижний конец нескрученной пластины следует подложить толстую пластину, чтобы обеспечить пространство для смещения высокой точки скручивания вниз. Этот метод прост и эффективен и широко используется в производстве.
V. Ручная гибка материала труб
Руководство гибка труб Для гибки трубных заготовок используются простые трубогибочные устройства. В зависимости от того, применяется ли нагрев при гибке, ее можно разделить на холодную и горячую. Как правило, холодная гибка используется для трубных заготовок малого диаметра (наружный диаметр трубной заготовки D ≤ 25 мм) из-за относительно небольшого изгибающего момента, в то время как для трубных заготовок большого диаметра в основном используется горячая гибка.
Ручная гибка труб не требует специализированного трубогибочного оборудования. Необходимые гибочные устройства просты, имеют низкую стоимость изготовления и легко настраиваются для использования, но их недостатком является высокая трудоемкость и низкая производительность. Поэтому он подходит только для сценариев мелкосерийного производства без специализированного гибочного оборудования.
1. Методы гибки материала труб
Для медных труб малого диаметра можно использовать ручную свободную гибку. Перед гибкой медная труба должна быть отожжена и постепенно согнута с одновременной формовкой вручную. Последний этап включает в себя обрезку для достижения овальной формы поперечного сечения и обеспечения плавной и круглой дуги изгиба. Во время работы следует избегать одновременной гибки на большую кривизну во избежание серьезных деформаций мертвых углов, которые не будут способствовать последующей обрезке, как показано на рисунке 32a.
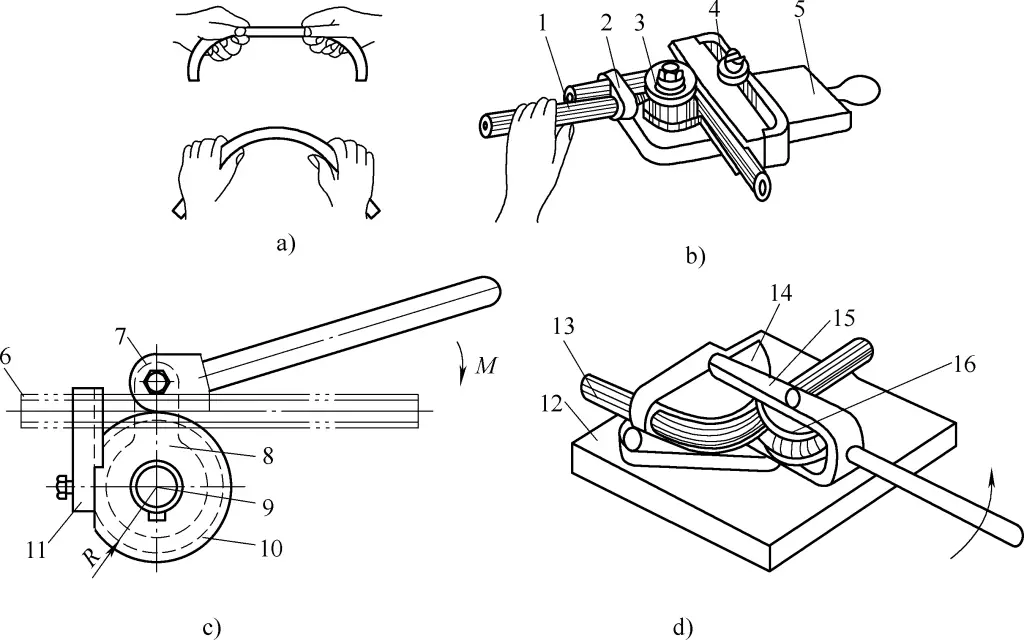
a) Ручное формирование гибки
b) Устройство для гибки труб с вращающимся диском
c) Устройство для гибки пресс-форм
d) Стационарное устройство для гибки пресс-форм
1-ручка
2-крючок
3-поворотный диск
4-Абатмент железный
5-основная пластина
6-трубный
7 Ручной блок для прессования
8 Ушное кольцо
9-Мандрел
10-гибочная форма
11-Блок зажима
12-платформенный
13-трубная заготовка
14-Фиксированная плесень
15-рычаг
16-роликовый
Для стальных труб меньшего диаметра можно использовать ручные трубогибочные устройства для холодной гибки. На рис. 32b показана форма гиба с помощью трубогибочного устройства поворотного типа с круговыми канавками, расположенными по окружности поворотного стола и по бокам железного блока, размер которых может быть рассчитан в зависимости от диаметра сгибаемой трубы.
После того как поворотный стол и железный блок зафиксированы, его можно использовать, вставив трубу в круглые пазы поворотного стола и железного блока, зацепив заготовку трубы и потянув за ручку, чтобы согнуть заготовку трубы на необходимый угол, следуя за ручкой.
На рисунке 32c показано ручное устройство для гибки труб с гибочной формой. Во время гибки гибочная форма остается неподвижной, а прижимной блок вращается вокруг гибочной формы, заставляя трубу формироваться в соответствии с формой. Поскольку ручные трубогибочные инструменты используются только для гибки труб небольшого диаметра, нет необходимости заполнять трубы материалом.
На рисунке 32d показано ручное устройство для гибки труб с фиксированной формой, состоящее в основном из платформы 12, фиксированной формы 14, ролика 16 и рычага 15. Во время работы неподвижная пресс-форма 14 закрепляется на платформе 12, имеющей полукруглый паз, соответствующий внешнему диаметру трубной заготовки 13.
Перед гибкой один конец трубной заготовки 13 помещается в полукруглый паз неподвижной пресс-формы 14 и фиксируется прижимной пластиной. Затем, управляя рычагом 15, ролик 16 (который также имеет полукруглую канавку, соответствующую внешнему диаметру трубной заготовки 13), закрепленный на рычаге 15, давит на трубную заготовку 13, заставляя ее изгибаться и деформироваться вокруг неподвижной пресс-формы 14. Изгиб прекращается при достижении требуемого угла изгиба, завершая процесс гибки труб.
Для труб большего диаметра, поскольку при ручной гибке требуется больший крутящий момент, можно использовать устройство для горячей гибки труб, показанное на рис. 32. Во время гибки используется паяльная лампа или оксиацетиленовое пламя для локального нагрева области гиба трубы. Температура нагрева зависит от свойств стали, обычно нагрев производится до тех пор, пока стальная труба не приобретет вишнево-красный цвет, после чего можно приступать к ручной гибке.
Заменяя поворотный стол 3, гибочную форму 10 и неподвижную форму 14 различных диаметров в вышеупомянутых ручных устройствах для гибки труб, можно гнуть трубы с различными радиусами изгиба. Аналогично, заменив или улучшив формовочную полость поворотного стола 3, гибочной формы 10 и неподвижной формы 14, ручное устройство для гибки труб, показанное на рис. 32, может быть использовано для ручной гибки прутков и профилей.
2. Операции по гибке труб
Чтобы обеспечить качество гибки труб, необходимо освоить и использовать правильные методы гибки, обращая особое внимание на следующие аспекты.
(1) Правильный выбор наполнителей
Чтобы предотвратить деформацию трубы при сжатии, для труб диаметром более 10 мм или с высокими требованиями к форме необходимо использовать заполняющие материалы внутри трубы для изгиба. Выбор наполнителя должен определяться исходя из таких факторов, как материал трубы, относительная толщина и радиус изгиба, как показано в таблице 4. Заполнение песком является наиболее широко используемым методом горячей гибки.
Таблица 4 Выбор наполнителей для гибки труб
Материал трубы | Наполнитель | Желаемая форма изгиба |
Стальная труба | Обычный желтый песок | После полного высыхания песка заполните трубу для горячей или холодной гибки |
Общая чистая медная труба, латунная труба | Свинец или соединения с низкой температурой плавления, такие как канифоль | После отжига медной трубы заполните ее и выполните холодную гибку. Обратите внимание, что при нагревании свинца для его расплавления необходимо предотвратить капание воды, чтобы избежать травм от брызг. |
Тонкостенная труба из чистой меди, латунная труба | Вода | После отжига медной трубы заполните ее водой и заморозьте для холодной гибки. |
Пластиковая труба | Мелкий желтый песок (или без наполнителя) | Быстро сгибаются после нагревания и размягчения |
(2) Основные моменты операций горячей гибки
При ручной гибке трубы с нагревом процесс включает в себя четыре этапа: засыпка песка, разметка линий, нагрев и гибка. Ключевыми моментами являются следующие:
1) Засыпка песком.
При ручной гибке труб для предотвращения деформации поперечного сечения внутри трубной заготовки обычно требуется заполнитель. Обычные наполнители включают кварцевый песок, канифоль и сплавы с низкой температурой плавления. Для трубных заготовок большого диаметра обычно используется песок. Перед засыпкой песка заткните один конец трубной заготовки конической деревянной пробкой, убедившись, что в пробке есть отверстия для свободного выхода расширяющегося воздуха во время нагрева. После засыпки песка заткните другой конец трубной заготовки деревянной пробкой.
Используемый песок должен быть чистым и сухим. Перед использованием его необходимо промыть, высушить и просеять. Если в песке присутствуют примеси и влага, продукты разложения при нагревании будут загрязнять внутреннюю стенку трубы, а влага будет расширяться в виде газа, повышая давление и, возможно, выталкивая деревянные пробки.
Размер частиц песка должен быть менее 2 мм. Если он слишком крупный, он не будет плотно укладываться, что приведет к деформации поперечного сечения при изгибе. Если он слишком мелкий, он будет слишком плотно упакован и не сможет легко деформироваться при изгибе, что может привести к образованию трещин в трубе.
2) Линии разметки.
Линии разметки определяют длину и положение трубной заготовки для нагрева в печи. Длину нагрева трубной заготовки можно определить следующим способом: сначала определите среднюю точку изогнутого участка в соответствии с проектным чертежом, затем измерьте длину изгиба от этой средней точки и прибавьте к ней диаметр трубной заготовки.
3) Отопление.
После засыпки песка и разметки линий можно приступать к нагреву. Топливом для нагрева может служить древесный уголь, кокс, газ или тяжелое дизельное топливо. Обычный котельный уголь не подходит для нагрева трубных заготовок, поскольку он содержит большое количество серы, которая при высоких температурах может проникать в сталь, ухудшая ее качество. Если условия ограничены, для локального нагрева можно использовать пламя оксиацетилена.
Независимо от того, какой метод нагрева используется, нагрев должен быть медленным и равномерным. Неправильный нагрев повлияет на качество гибки. Температура нагрева зависит от свойств стали, обычная углеродистая сталь обычно нагревается до температуры около 1050°C.
Когда заготовка трубы достигает этой температуры, ее следует выдержать некоторое время, чтобы песок внутри также достиг той же температуры, предотвращая быстрое охлаждение заготовки трубы. В идеале гибка должна быть завершена за один нагрев. Повторный нагрев может ухудшить качество стальной трубы и увеличить толщину оксидного слоя, что приведет к истончению стенки трубы.
4) Изгиб.
После нагрева трубной заготовки в печи ее можно вынуть для гибки. Если нагретая часть слишком длинная, ненужный нагретый участок можно охладить водой, прежде чем поместить трубную заготовку на гибочное устройство.
Если радиус изгиба трубы не соответствует требованиям, можно применить следующие методы регулировки: если изгиб слишком мал, внутреннюю сторону изгиба можно охладить водой для усадки внутреннего слоя металла; если изгиб слишком велик, внешнюю сторону можно охладить водой для усадки внешнего слоя металла.
3. Меры предосторожности при гибке труб
(1) Радиус изгиба не должен быть слишком маленьким
Если радиус изгиба слишком мал, труба может треснуть при изгибе. При холодной гибке радиус изгиба должен превышать диаметр трубы более чем в 4 раза. Минимальные значения радиуса изгиба могут быть выбраны в соответствии с таблицей 5.
Таблица 5 Минимальные значения радиуса изгиба для различных труб (единицы измерения: мм)
Трубы из чистой меди и латуни | Алюминиевые трубы | Бесшовные стальные трубы | ||||||
Наружный диаметр материала трубы D | Минимальный изгиб Радиус Rмин | Толщина стенки трубы t | Наружный диаметр материала трубы D | Минимальный изгиб Радиус Rmin | Толщина стенки трубы t | Наружный диаметр материала трубы D | Минимальный изгиб Радиус Rмин | Толщина стенки трубы t |
5.0 | 10 | 1.0 | 6.0 | 10 | 1.0 | 6.0 | 15 | 1.0 |
6.0 | 10 | 1.0 | 8.0 | 15 | 1.0 | 8.0 | 15 | 1.0 |
7.0 | 15 | 1.0 | 10 | 15 | 1.0 | 10 | 20 | 1.5 |
8.0 | 15 | 1.0 | 12 | 20 | 1.0 | 12 | 25 | 1.5 |
10 | 15 | 1.0 | 14 | 20 | 1.0 | 14 | 30 | 1.5 |
12 | 20 | 1.0 | 16 | 30 | 1.5 | 16 | 30 | 1.5 |
14 | 20 | 1.0 | 20 | 30 | 1.5 | 18 | 40 | 1.5 |
14 | 18 | 2.0 | 6.0 | 15 | 1.0 | 12.5 | 30 | 2.25 |
18 | 28 | 2.0 | 8.0 | 15 | 1.0 | 15 | 45 | 2.25 |
22 | 50 | 2.0 | 10 | 20 | 1.5 | 25 | 60 | 2.0 |
25 | 50 | 2.0 | 12 | 25 | 1.5 | 30 | 80 | 3.0 |
32 | 60 | 2.5 | 14 | 30 | 1.5 | 32 | 110 | 3.0 |
38 | 70 | 2.5 | 16 | 30 | 1.5 | 40 | 150 | 3.5 |
45 | 90 | 2.5 | 18 | 40 | 1.5 | 51 | 180 | 4.0 |
(2) Процедура гибки нескольких секций трубного материала
При гибке трубного материала необходимо учитывать следующее: Если на одной трубе необходимо согнуть несколько секций фитингЕсли фитинг представляет собой пространственную гнутую деталь (т.е. направления изгиба нескольких гнутых секций не лежат в одной плоскости), то сначала на платформе следует выполнить один изгиб, а затем поднять и установить один конец фитинга, после чего последовательно согнуть остальные секции.
(3) Изгиб сварной трубы
При гибке сварных стальных труб сварной шов следует располагать на нейтральном слое изгиба, чтобы предотвратить образование трещин в сварном шве, как показано на рисунке 33.
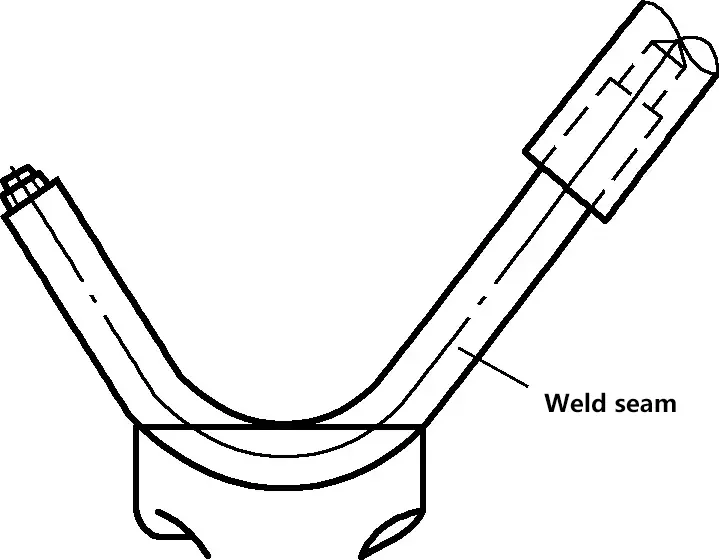
VI. Ручная гибка профилей
Подобно ручной гибке трубного материала, различные профили (такие как плоская сталь, угловая сталь, швеллерная сталь, круглая сталь и т.д.) также могут быть согнуты вручную с помощью соответствующих гибочных устройств. Однако из-за более толстого материала и большей жесткости профилей ручная гибка профилей часто требует использования пресс-форм и часто использует методы горячей гибки.
Как показано на рисунке 34, это ручной метод гибки угловой стали. После нагрева угловой стали ее зажимают на пресс-форме 1 для внутренней гибки, а по горизонтальному краю наносят удары кувалдой, чтобы предотвратить его подъем (см. рис. 34a); для внешней гибки (см. рис. 34b) заштрихованную область нагревают, чтобы предотвратить разрушение горизонтального края, а по вертикальной поверхности наносят удары кувалдой (см. сечение A-A на рис. 34b), чтобы предотвратить уменьшение угла и подъем горизонтальной поверхности.
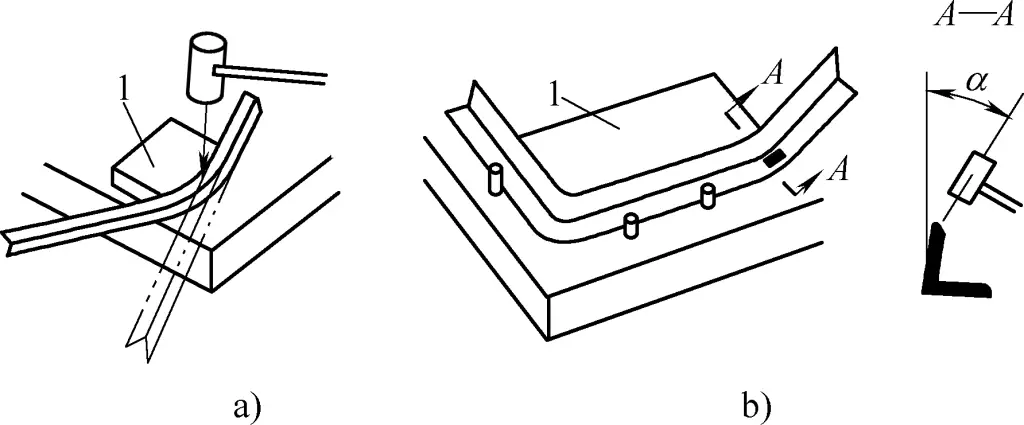
Для профилей с большой площадью поперечного сечения даже горячая гибка может оказаться недостаточной для ручного сгибания в форму, поэтому необходимо использовать механическую гибку. Ниже приведены два примера ручной гибки профилей.
1. Ручная гибка плоского стального кольца по всей окружности
Плоская сталь - один из распространенных профилей, и из-за ее толщины для ручной гибки необходимо использовать пресс-формы. Разработанная форма для плоского стального кольца показана на рисунке 35.
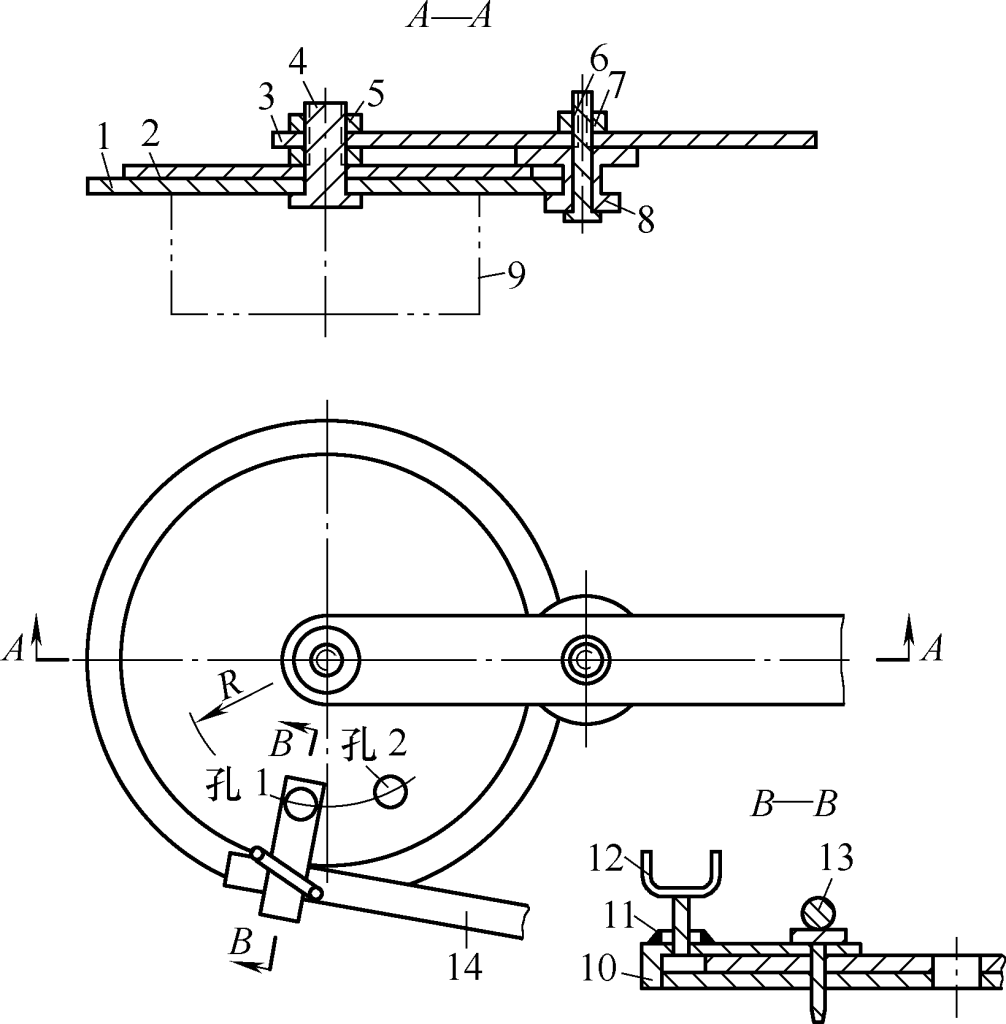
1-формовочная опорная плита
Пластина с 2 формочками
3-ручка
4 болта
5 гаек
6, 7-Вращающийся прижимной болт и гайка
8-роликовый ролик
9-фиксированная рама
10-фиксированная плита для пресса
11-гайка
12-ручка
13-Подвижный штифт
14 Плоская сталь для сгибания
(1) Принципы проектирования и особенности пресс-формы
Чтобы форма плоского стального кольца соответствовала проектным требованиям, опорная плита 1 и плита 2 пресс-формы выполнены в форме круга. Диаметр плиты формы 2 должен быть увеличен на определенный припуск на усадку, основанный на скорости усадки материала (увеличение на 0,1%-0,2% диаметра), чтобы учесть усадку при охлаждении. Края и отверстия должны быть обработаны для повышения точности конструкции.
Толщина плиты формы 2 должна быть на 2-1,5 мм больше толщины сгибаемого плоского проката. Это необходимо для размещения нагретой плоской стали. Кроме того, для повышения точности конструкции и качества плоского стального кольца следует обработать прокатный ролик 8. Он выполнен в форме двутавровой балки с большей верхней частью и меньшей нижней, главным образом для обеспечения достаточной прочности и прилегания плоского стального кольца к форме. Высота паза должна быть на 1-1,5 мм больше, чем суммарная высота пластин 1 и 2.
Внутренняя плоскость верхнего фланца служит для предотвращения сморщивания, а верхний и нижний фланцы обеспечивают направление. Внутренняя плоскость полотна служит для формирования формы раскатки.
Неподвижная прижимная плита 10, гайка 11 и рукоятка 12 вместе плотно прижимают плоскую сталь, предотвращая ее перемещение во время гибки.
Для устранения прямых участков и формирования полной окружности в плоском стальном кольце предусмотрены отверстия 1 и 2.
(2) Метод сгибания
Ниже описаны этапы и методы ручной гибки плоского стального кольца по всей окружности:
1) Нагрейте плоский стальной материал в печи до желто-оранжевого цвета при температуре 900-1000℃ и оставьте его на некоторое время.
2) Закрепите неподвижную прижимную пластину 10 в отверстии 1 и совместите ее с роликом 8. Быстро вставьте и плотно прижмите плоский стальной конец, затем поверните рукоятку 3, чтобы начать гибку. Когда гибка приблизится к неподвижной прижимной пластине 10, чтобы совместить два конца и устранить прямой участок, быстро переместите неподвижную прижимную пластину 10 в отверстие 2, зафиксируйте ее и продолжайте гибку до тех пор, пока концы не наложатся друг на друга и не будет невозможно продолжить.
3) Снимите неподвижную плиту пресса 10, извлеките плоское стальное кольцо с заготовкой и отрежьте перекрывающуюся часть, чтобы получить плоское стальное кольцо полного круга.
2. Ручной изгиб колец с вопросительным знаком
Как показано на рисунке 36, оно представляет собой концентрическое кольцо в форме вопросительного знака. Кольцо изготовлено из круглой стали диаметром ϕ20 мм. Из-за небольшой производственной партии его обычно гнут вручную с помощью пресс-формы.
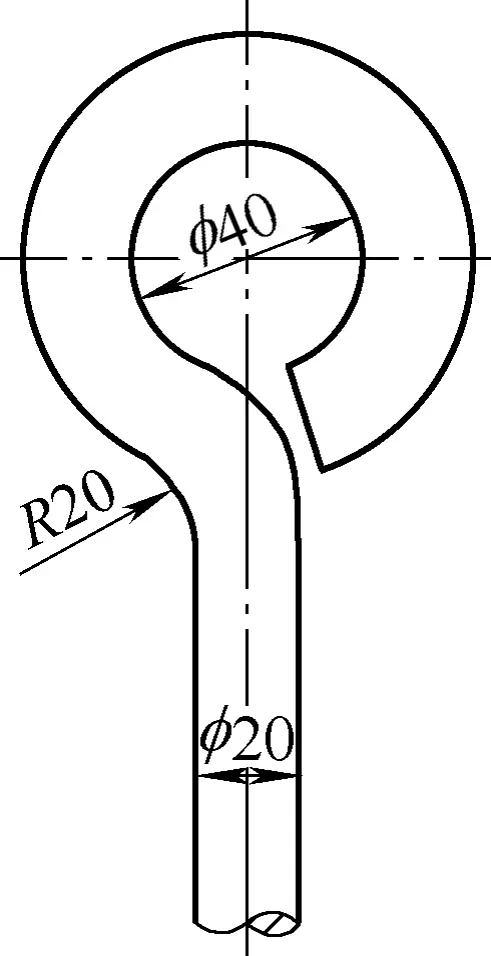
(1) Дизайн пресс-формы
В соответствии с размерами, приведенными на рисунке 36, чтобы диаметр центрального отверстия был равен 40 мм, формирующий цилиндрический штифт должен быть неподвижным, правый цилиндрический штифт может быть неподвижным или подвижным, а левый должен быть подвижным цилиндрическим штифтом. Расстояние между внутренними поверхностями каждого образующего цилиндрического штифта должно быть на 2-3 мм больше, чем диаметр круглой стали (см. рис. 37).
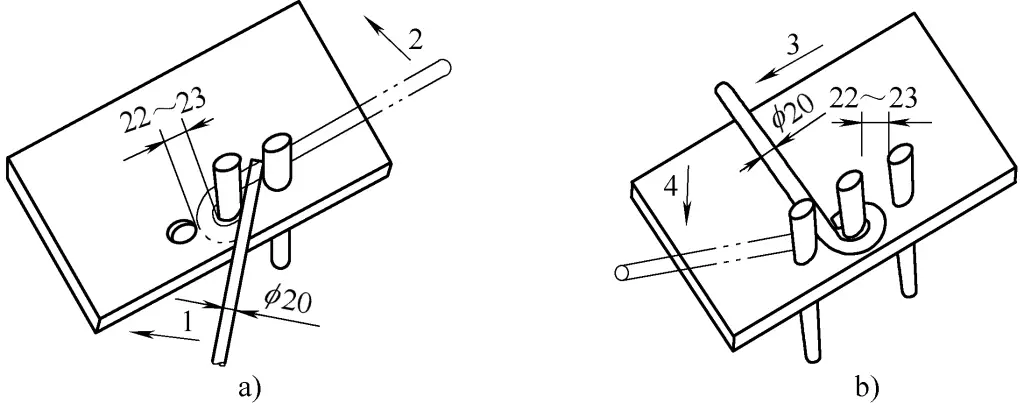
1, 2, 3, 4 - порядок сгибания
(2) Метод сгибания
На рисунке 37a показана ситуация сгибания эксцентрикового кольца. Вставьте круглую сталь между центральным и правым цилиндрическими штифтами и согните из положения 1 в положение 2, следуя направлению стрелки, чтобы сформировать эксцентриковое кольцо.
На рисунке 37b показан процесс сгибания для формирования концентрического кольца, как того требует конструкция. Согните спинку из положения 2 в положение 3 в соответствии с направлением стрелки, затем вставьте цилиндрический штифт в левое отверстие и согните круглую сталь из положения 3 в положение 4 в соответствии с направлением стрелки, чтобы сформировать кольцо.
3. Ручная гибка профилей под любым углом
Для холодной или горячей ручной гибки плоской стали, круглой стали или круглых труб малого диаметра под любым углом используйте пресс-форму, показанную на рис. 38.
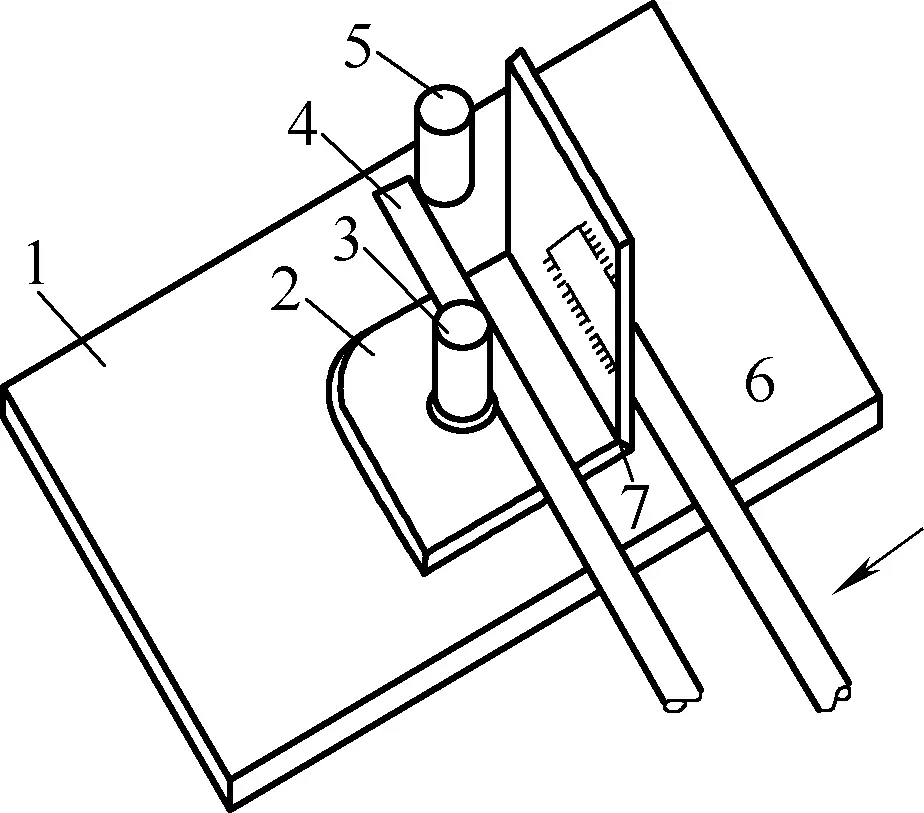
1-Платформа
2-Поворотная угловая стальная пресс-форма
3-цилиндрический штифт
4-Workpiece
5-Фиксированный цилиндрический штифт
6-ручка
7-Контактная точка
(1) Дизайн пресс-формы
Приварите цилиндрический штифт 3 к платформе 1, затем установите на штифт 3 вращающуюся угловую стальную форму 2 с приваренной ручкой 6 с предварительно просверленными отверстиями. 5 - это неподвижный цилиндрический штифт.
(2) Метод сгибания
Поместите заготовку 4 между цилиндрическим штифтом 3 и неподвижным цилиндрическим штифтом 5, с усилием поверните рукоятку 6, вращающаяся угловая стальная форма 2 будет двигаться в направлении, указанном стрелкой. Когда заготовка 4 коснется контактной точки 7, она будет вращаться вместе с вращающейся угловой стальной формой 2. Непрерывное приложение силы может согнуть заготовку на любой угол.