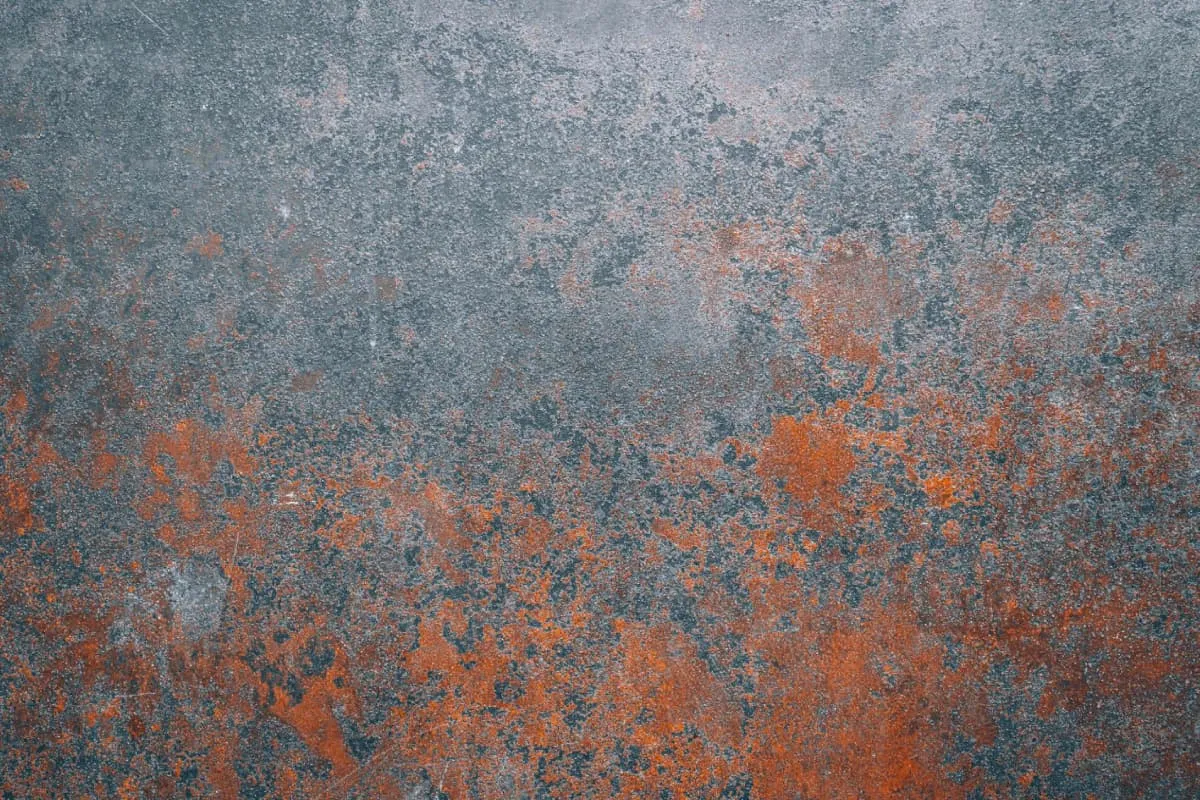
Нержавеющая сталь - это вид высоколегированной стали с низким содержанием углерода (обычно не более 0,4% по массе) и содержанием различных легирующих элементов (с массовой долей легирующих элементов более 13%).
По структуре матрицы нержавеющая сталь подразделяется на ферритную, аустенитную и мартенситную. Нержавеющая сталь обладает высокой устойчивостью к деформации, низкой теплопроводностью, высокой чувствительностью к перегреву и плохо поддается ковке.
Ковка ферритной нержавеющей стали
Ферритная нержавеющая сталь содержит небольшое количество углерода, с массовой долей хрома от 16% до 30% (например, 20Cr13, 10Cr17 и т.д.). Этот тип стали не претерпевает структурных изменений при нагреве и охлаждении, и не может использовать методы термообработки для повышения прочности или измельчения зерен, только методы ковки могут измельчить зерна. Температура рекристаллизации низкая, скорость рекристаллизации быстрая, зерна склонны к росту при нагреве, а кузнечная способность плохая. Ключевые моменты процесса ковки ферритной нержавеющей стали заключаются в следующем:
1) Зерно ферритной нержавеющей стали начинает расти при температуре 600°C. Чтобы избежать огрубления зерна в процессе нагрева, температура нагрева не должна быть слишком высокой, а время выдержки не должно быть слишком долгим. Обычно используется начальная температура температура ковки составляет 1100-1150°C, а температура нагрева последнего пламени не должна превышать 1000°C. Чтобы сократить время пребывания заготовки при высоких температурах, ее следует быстро нагреть до начальной температуры ковки после медленного нагрева до 760°C.
2) Поскольку ферритная нержавеющая сталь не может использовать методы термообработки для уточнения зерен, она должна быть полностью прокована во время ковки для уточнения зерен и обеспечения достаточной деформации и равномерной деформации. Деформация последнего пламени должна быть больше, чем 12% - 20%. Температура окончательной ковки должна быть ниже 800°C, чтобы предотвратить повторную агрегацию рафинированных зерен. Однако, чтобы избежать упрочнения, вызванного слишком низкой температурой, температура окончательной ковки должна быть не ниже 750°C.
3) После ковки сталь следует охладить на воздухе, чтобы она быстро прошла через зону охрупчивания 475°C. Кратковременный отжиг при температуре выше 550°C (обычно от 700 до 800°C) может вернуть охрупченную нержавеющую сталь к ее первоначальному нехрупкому состоянию.
Ковка аустенитной нержавеющей стали
Массовая доля углерода в аустенитной нержавеющей стали составляет менее 0,25%, массовая доля хрома - от 17% до 19%, массовая доля никеля - от 8% до 18%, например, 12Cr18Ni9, 17Cr18Ni9 и т.д. Аустенитная нержавеющая сталь не претерпевает структурных превращений при охлаждении и не может использовать методы термической обработки для повышения прочности и измельчения зерен, возможны только термическая деформация при ковке и рекристаллизация. Зерна аустенитной нержавеющей стали склонны к росту при высоких температурах, но тенденция к росту не такая сильная, как у ферритной нержавеющей стали.
Условия нагрева аустенитной нержавеющей стали аналогичны таковым для ферритной стали: начальная температура ковки обычно составляет 1150-1180°C, а конечная температура ковки должна быть не ниже 850°C; в противном случае осаждение карбидов в структуре повышает сопротивление деформации, что делает ковку склонной к образованию трещин.
Ключевые моменты процесса ковки аустенитной нержавеющей стали заключаются в следующем:
1) Строго избегайте науглероживания при нагреве. Углерод и хром легко образуют карбидные соединения хрома на границах зерен, что снижает содержание хрома в матрице вблизи границ зерен и повышает чувствительность стали к межкристаллитной коррозии. Нагрев следует проводить в слабоокислительной атмосфере.
2) При ковке стальных слитков начинайте с легкого прессования. Только когда деформация стального слитка достигнет 30%, можно применять тяжелое прессование. Во время ковки слиток следует подавать в одном направлении, чтобы избежать повторных ударов молотом по одному месту, что предотвращает появление центральных поперечных трещин.
3) Коэффициент ковки для стальных слитков устанавливается в пределах от 4 до 6, а для заготовок - от 2 до 4, в зависимости от размера зерна исходного материала. Размер зерна аустенитной нержавеющей стали в значительной степени влияет на ее коррозионную стойкость. Для получения мелкозернистой структуры необходимо обеспечить достаточный коэффициент ковки при последнем нагреве, при этом величина деформации должна превышать критическую степень деформации для рекристаллизации.
4) Для достижения более однородной зернистой структуры в процессе деформации требуется равномерная деформация. Для круглых дисковых поковок можно рассмотреть следующие меры:
- Используйте гладкую поверхность платформы и наковальни, при необходимости смажьте;
- Разогрейте платформу и поверхность наковальни до 150-450°C;
- Добавьте прокладки из низкоуглеродистой стали на оба конца заготовки диска;
- Используйте ковку с укладкой;
- Применяйте прерывистое сжатие во время деформации;
- Используйте кожух для расстроповки.
5) Аустенитная нержавеющая сталь имеет особенно большую скорость усадки. Когда поковка приобретает окончательную форму, следует учитывать большую скорость усадки (от 1,5% до 1,7%), чтобы избежать отбраковки поковки из-за недостаточных размеров после охлаждения.
6) Воздушное охлаждение после ковки. Аустенитная нержавеющая сталь после ковки может охлаждаться на воздухе, в яме или в песке.
7) Чтобы повторно растворить карбиды, выпавшие в процессе ковки и воздушного охлаждения, в аустените, получив однородную и единую аустенитную структуру при комнатной температуре, нержавеющая сталь должна пройти обработку раствором, т.е. нагрев и выдержку при температуре 1020-1050°C, затем водяное охлаждение. Температура не должна быть слишком высокой, а время выдержки не должно быть слишком долгим, чтобы предотвратить рост зерен.
3. Ковка мартенситной нержавеющей стали
Мартенситная нержавеющая сталь имеет массовую долю углерода от 0,1% до 4% и массовую долю хрома от 12% до 14%, например, 20Cr13, 30Cr13, 40Cr13 и т.д. Этот тип стали является аустенитным при высоких температурах и переходит в мартенситную структуру при охлаждении до комнатной температуры. Она имеет более высокую твердость, чем ферритные и аустенитные нержавеющие стали, а ее размер зерна может быть уточнен и механические свойства улучшены путем термообработки.
Температура нагрева для мартенситной нержавеющей стали не должна быть слишком высокой, так как слишком высокая температура может привести к образованию δ-феррита, снижающего пластичность стали. Начальная температура ковки обычно составляет 1100-1150°C. Этот тип стали обладает плохой теплопроводностью, и быстрый нагрев может легко привести к образованию трещин. Поэтому ее необходимо медленно нагревать до 850°C, и только после улучшения пластичности ее можно быстро нагреть до начальной температуры ковки.
Этот тип стали имеет однофазную аустенитную структуру при высоких температурах, и особых трудностей при ковке не возникает, но следует избегать сильных ударов в диапазоне 900-950°C во избежание осыпания. К величине деформации при последнем обжиге также не предъявляется особых требований, а температура окончательной ковки обычно составляет около 900°C.
Если сталь этого типа охладить на воздухе после ковки, она сразу же превратится в мартенситную структуру. В кованом изделии возникают значительные термические напряжения, остаточные напряжения при ковке и структурные напряжения, которые могут легко привести к растрескиванию поверхности. Поэтому после ковки ее следует медленно охладить в горячем песке или в печи и своевременно отжечь, чтобы устранить внутренние напряжения и снизить твердость, облегчив механическую обработку.