
I. Назначение автоматической линии размотки и выравнивания листов
В области листового металла, с развитием науки и техники и быстрым развитием производительности, использование рулонных материалов достигло значительного прогресса по сравнению с листовыми материалами. Это объясняется тем, что с точки зрения оборота материала, рулонные материалы обеспечивают сухую упаковку и транспортировку от сталелитейных заводов к потребителям, уменьшая деформацию и потери; с точки зрения использования, поскольку пользователи могут готовить материалы на месте в соответствии с потребностями продукции, и могут максимально использовать рулонные материалы для производства, значительно улучшая коэффициент использования материалов и повышая экономическую выгоду пользователей.
Все эти изменения обусловлены развитием и совершенствованием автоматической производственной линии для размотки листов. За последние двадцать лет технический уровень автоматической линии для размотки листов улучшился в связи с постоянным ростом требований к процессу производства продукции, ее разнообразием и широкой применимостью, что позволяет конечным пользователям полностью реализовать соотношение цены и производительности после выбора этого типа производственной линии.
Автоматическая линия для размотки листов может перерабатывать широкие рулоны в продольном или поперечном направлении в узкие рулоны или отдельные листы требуемого размера, а затем отправлять их на линию штамповки или систему обработки гибких листов на заводе, например, в таких отраслях, как производство двигателей и электроприборов. Есть также некоторые крупные производители штампованных деталей, которые создали автоматические линии для размотки листов, выравнивающей штамповки с большими механическими прессами, выбивающими заготовки сложной формы, а затем отправляющими их на линию штамповки для обработки готовой продукции, например, линии по производству дверей для автомобилей в автомобильной промышленности, линии по производству внешней оболочки для холодильников и т.д.
Кроме того, используются различные углеродистые, низколегированные и цветные стали. металлы рулонов, а также цветных рулонов с покрытием. Диапазон технических характеристик рулонов также постепенно расширяется, в настоящее время толщина рулонов составляет 0,1~25 мм, ширина - 100~2500 мм, а вес - до 40 тонн. Скорость линии размотки линии поперечной резки достигла 80 м/мин (состояние остановки резки), 120 м/мин (состояние летящих ножниц); скорость линии размотки линии продольной резки достигла 200 м/мин.
Все эти рулоны могут быть переработаны на автоматической линии размотки листов, поэтому этот тип автоматической линии широко используется в отраслях, где используется большое количество листовых материалов, таких как автомобильная, сельскохозяйственная техника, двигатели, электроприборы, инструменты, легкая промышленность, бытовая техника, строительные материалы и т.д.
II. Типы и технические параметры автоматической линии выравнивания размотки листов
Автоматическая линия для выравнивания размотки листов состоит из множества отдельных машин, транспортировочных устройств, накопителей и т.д., соединенных вместе. Каждое устройство на линии отвечает производственным требованиям всей линии, с разумной конфигурацией процесса.
Как правило, автоматическая линия размотки листов должна включать в себя следующее оборудование и устройства: загрузочный вагон, разматыватель, устройство подачи, устройство выравнивания, оборудование для резки, пробивное оборудование, устройство смены мостов, механизм ввода, повторный размотчик, механизм укладки и т.д., в зависимости от технологического назначения конкретной линии и потребностей обрабатываемых заготовок. Распространенными типами автоматических линий для размотки и выравнивания листов являются следующие:
1. Автоматическая линия для продольной резки листового металла с размоткой и выравниванием
Автоматическая линия для размотки листового металла, выравнивания продольных ножниц, как показано на рисунке 1.
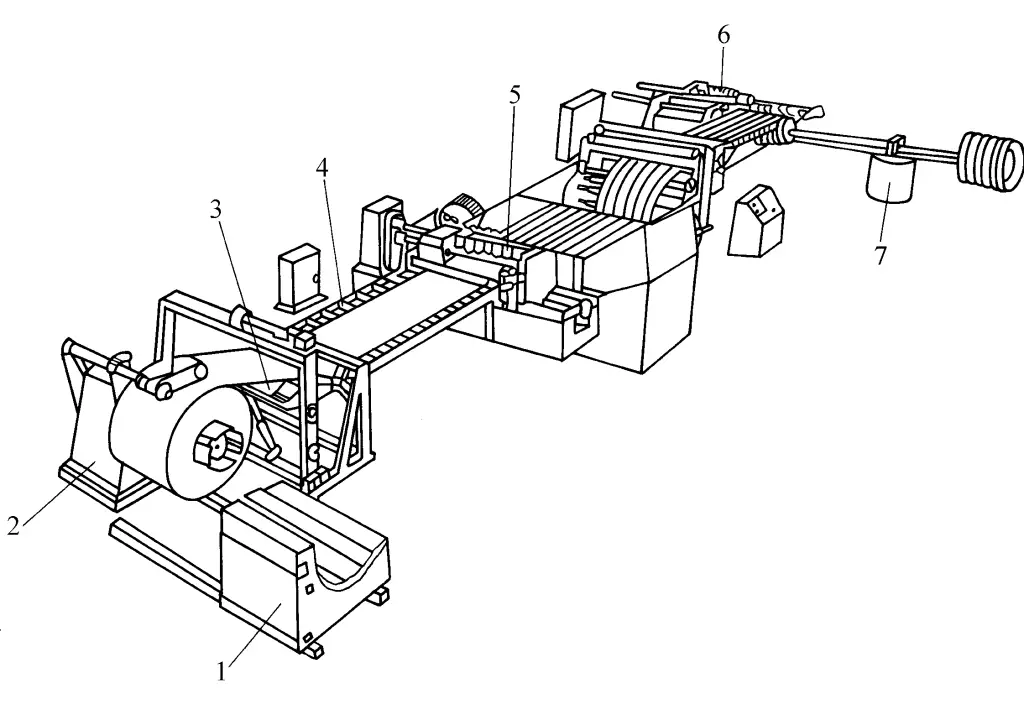
1-Погрузочная тележка
2 - Разматыватель
3Устройство для выравнивания
4-Материальный стеллаж
5-многополосный стригальная машина
6-перемотчик
7-катушечная стойка
Поместите широкий рулонный материал, приобретенный на сталепрокатном заводе, в загрузочную тележку 1, заведите ее и остановите в соответствующем положении разматывателя 2, поршень гидроцилиндра поднимает рулонный материал так, чтобы центр внутреннего отверстия рулонного материала совпал с центром барабана разматывателя, запустить загрузочную тележку так, чтобы барабан разматывателя вошел во внутреннее отверстие рулонного материала, рулон расширяется, затягивает рулонный материал и поддерживает вес, поршень гидроцилиндра втягивается, загрузочная тележка покидает разматыватель и останавливается на месте, и загружает другой рулонный материал для следующего использования.
Рулонный материал на разматывателе прижимается прижимным роликом, рулон ослабляется, а головка материала обрабатывается и поступает на подающий ролик, выравнивается многороликовым устройством выравнивания пластин 3, проходит через стойку для материала 4, подающий ролик и поступает в многополосный ножничный станок 5, регулирует расстояние между соседними дисковыми ножами, зазор и перекрытие между верхним и нижним дисковыми ножами в соответствии с требуемой шириной полосы, после чего можно срезать необходимые полосы. После прохождения через разделительное устройство она поступает в отдатчик 6 через натяжное устройство, преобразуя таким образом широкий рулонный материал в несколько полос одинаковой или разной ширины для использования на различных линиях производства прессы.
Технические параметры автоматической линии для размотки, выравнивания и продольной резки листов приведены в таблице 1.
Таблица 1 Технические параметры автоматической линии для размотки, выравнивания и продольной резки листов (производство компании Jinan Foundry and Forging Jiemai Forging Press Company)
Параметры | Толщина сдвигаемой пластины/мм | Ширина сдвигаемой пластины/мм | Количество полос сдвига/(полос) | Вес рулонного материала/т |
0.5×800 | 0.05~0.5 | 300~800 | 10~40 | 4 |
1.5×1000 | 0.2~1.5 | 600~1000 | 10~40 | 5 |
2×1250 | 0.3~2 | 600~1250 | 10~30 | 10 |
3×1600 | 0.4~3 | 1000~1600 | 8~20 | 10 |
4×1600 | 0.5~4 | 1000~1600 | 8~20 | 10 |
6×1600 | 1~6 | 1000~1600 | 6~20 | 15 |
10×1600 | 3~10 | 1000~1600 | 3 ~10 | 20 |
2. Листовой металл размотка выравнивание поперечные ножницы автоматическая линия
Автоматическая линия для размотки листового металла, выравнивания поперечных ножниц, как показано на рисунке 2.
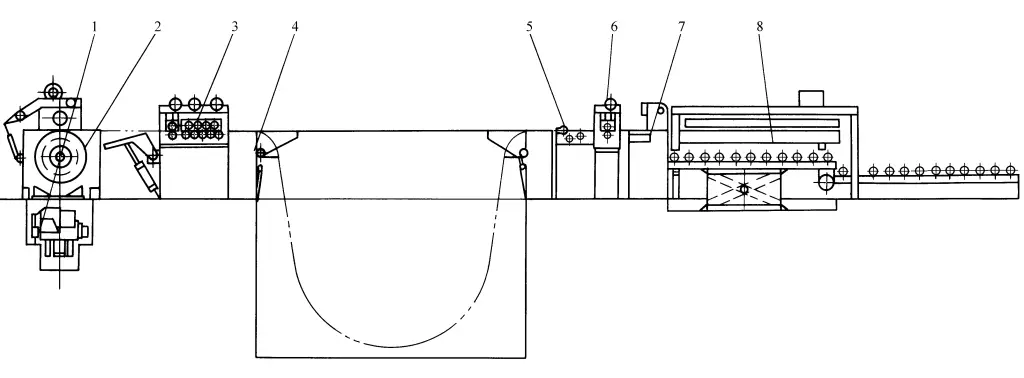
1 - Грузовая тележка
2 - Разматыватель
3 - Машина для выравнивания рулонных плит
4 - Качающийся мост
5 - Механизм коррекции отклонений
6 - Механизм подачи
7 - Машинка для стрижки овец
8 - Механизм штабелирования
Рулонный материал подается в разматыватель 2 подающей тележкой 1, рулон расширяется и после затяжки прижимного ролика ослабляется, лист поступает в многорулонную машину для выравнивания листов 3, после выравнивания проходит через поворотный мост 4, накопительную яму, механизм коррекции отклонений 5 регулирует центр подачи, затем поступает в подающий механизм 6 и подается в ножницы 7 (или летучие ножницы), система управления выдает сигнал на ножницы, которые затем могут разрезать на отдельные листы необходимой длины, а затем поступают в укладочный механизм 8 для пакетирования или отправляются на линию тиснения для использования.
Технические параметры автоматической линии поперечных ножниц для размотки и выравнивания листов приведены в таблице 2.
Таблица 2 Технические параметры автоматической линии поперечных ножниц для размотки и выравнивания листов (производство компании Jinan Foundry and Forging Jiemai Forging Company)
Параметры | Толщина среза/мм | Ширина клипборда/мм | Длина среза/мм | Масса катушки/т |
0.5×800 | 0.05~0.5 | 200~800 | 200~2500 | 5 |
1×1250 | 0.1~1 | 600~1200 | 200~2500 | 5 |
2×1250 | 0.3~2 | 1000~1600 | 200~2500 | 10 |
3×1600 | 0.5~3 | 1000~1600 | 500~2500 | 10 |
6×2000 | 2~6 | 1000~2000 | 200~4000 | 10 |
8×1600 | 2~8 | 1000~1600 | 200~2500 | 20 |
10×2000 | 3~10 | 1000~2000 | 200~2500 | 25 |
12×2000 | 4~12 | 1000~2000 | 200~2500 | 30 |
16×2000 | 5~16 | 1000~2000 | 200~2500 | 35 |
20×2500 | 8~20 | 1000~2500 | 1000~5000 | 40 |
3. Комбинированная автоматическая линия для размотки, выравнивания, продольной и поперечной резки листового металла
Для того чтобы полностью использовать производственные мощности онлайн-оборудования, сократить инвестиции в оборудование и заводскую площадь, а также сэкономить энергию, некоторые производители недавно оснастили автоматические линии размоткой, выравниванием, продольной и поперечной резкой листового металла, значительно повысив эффективность производства оборудования на линии, расширив диапазон применения оборудования, и позволив одной линии выполнять функции двух линий. Цзинаньский научно-исследовательский институт литейного и кузнечного оборудования, учитывая потребности рынка, своевременно разработал автоматическую линию данного типа, конфигурация оборудования которой показана на рисунке 3.
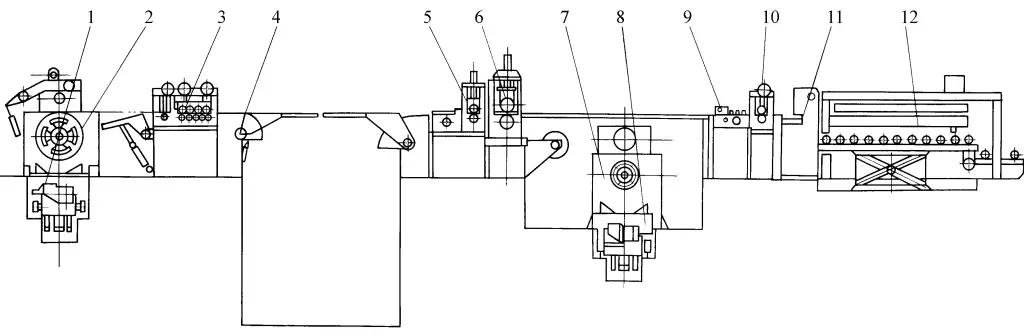
1 - Грузовая тележка
2 - Разматыватель
3 - Многороликовая машина для выравнивания плит
4 - Качающийся мост
5 - Механизм подачи
6 - Многополосная машинка для стрижки
7 - Моталка
8 - Разгрузочная тележка
9 - Механизм исправления
10 - Механизм подачи
11 - Машинка для стрижки овец
12 - Механизм штабелирования
Рулонный материал подается с загрузочной тележки 1 в разматыватель 2, барабан расширяется и зажимает рулонный материал, затем ослабляет его, и лист поступает в многовалковую машину для выравнивания листов 3, проходит через качающийся мост 4, поступает через механизм подачи 5 в многополосную ножницы 6, поднимает мост материала, и после разделения ножницами многополосный материал поступает в моталку 7. Сформированные многодисковые рулоны упаковываются и отправляются на разгрузочную тележку 8, тем самым завершая продольную процесс стрижки.
Если верхний режущий вал многополосной стригальной машины 6 поднимается и мостик материала выравнивается, то выровненный лист металла выравнивается выпрямляющим механизмом 9 к центру, направляется в подающий механизм 10 и стригальную машину 11, таким образом стрижется в единый лист металла фиксированной длины, направляется в укладочный механизм 12 и используется непосредственно на линии штамповки после упаковки, завершая тем самым процесс поперечной стрижки. В зависимости от потребностей, продольная резка, намотка, поперечная резка и штабелирование рулонного материала могут выполняться одновременно.
4. Листовой металл размотка выравнивание штамповка автоматическая линия
Существует два типа автоматических линий для размотки листового металла, одна из них - автоматическая линия заготовительного типа, а другая - автоматическая линия штамповки, как показано на рисунке 4.
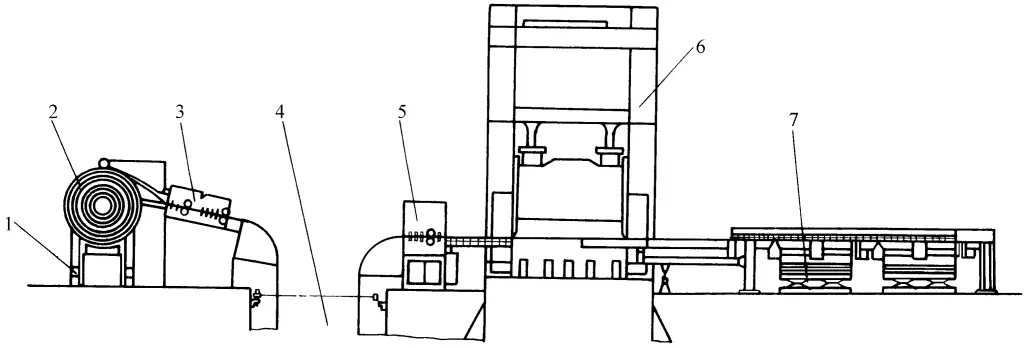
1 - Разматыватель
2-катушка
3 Устройство для выравнивания листов
4-Складская яма
5-Подающий блок
6-Механический пресс
7-Устройство для штабелирования
Устройство подачи рулонов 2 направляет рулон в разматыватель 1, после разрыхления он поступает в устройство выравнивания листов 3, после выравнивания проходит через накопительную яму 4, а устройство подачи 5 направляет листовой материал в механический пресс 6 для обрезки. Затем обрезанный материал транспортируется конвейерной лентой к штабелирующему устройству 7, а затем коллективно транспортируется к следующему процессу.
Этот тип крупномасштабной штамповочной автоматической линии в основном используется для заготовки, и широко применяется в автомобильной промышленности, например, для автоматических линий для автомобильных дверей или других крупных деталей крышки для подготовки заготовок. Автоматическая линия для штамповки заготовок требует только настройки соответствующего разматывающего и выравнивающего устройства перед открытым или закрытым механическим прессом в соответствии с размером и формой деталей, и детали могут быть непосредственно произведены.
5. Устройство для разматывания и разравнивания
Вышеупомянутые типы автоматических линий для размотки и выравнивания листов в основном используются для модификации рулонов или для подготовки заготовок для крупных автоматических линий для штамповки листов. Для модифицированных узких рулонов разматывающее и выравнивающее устройство для Развернуть Обработка перед штамповкой показана на рисунке 5.
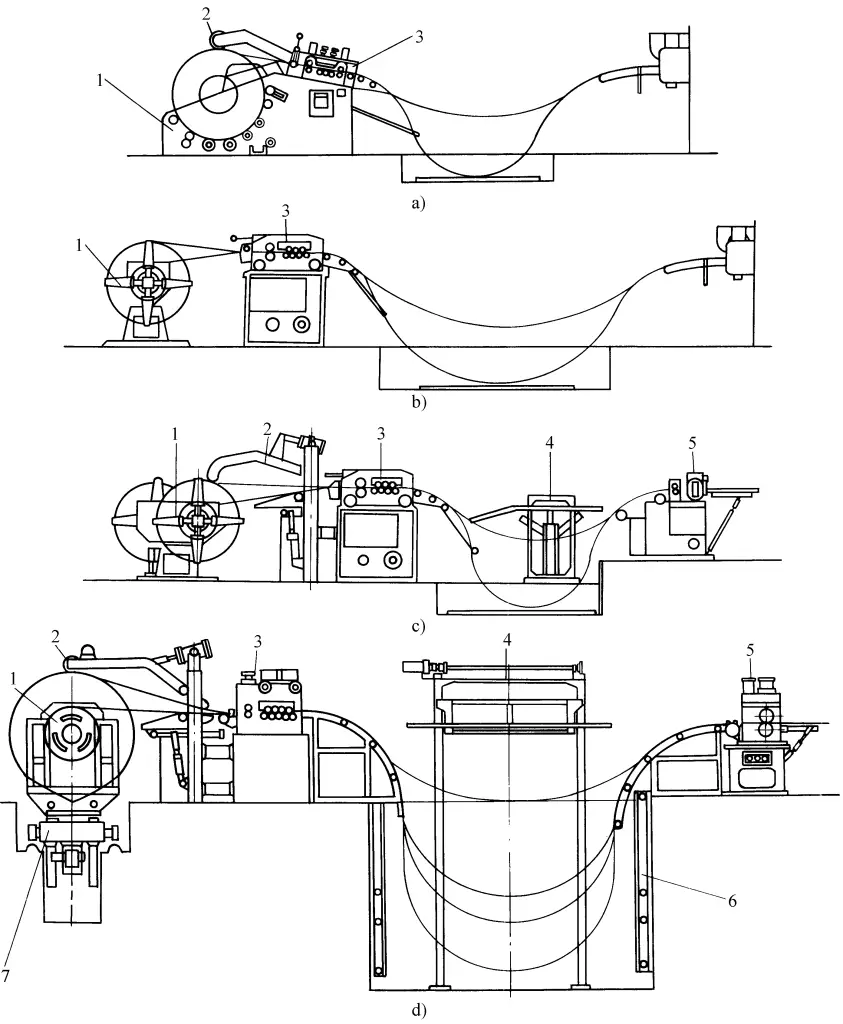
a) Тип I
б) Тип II
в) Тип III
г) Тип IV
1 - Разматыватель
2 - Прижимной ролик
3 - Выравнивающее устройство
4 - Направляющая платформа
5 - Устройство подачи с ЧПУ
6 - Фотоэлектрическое устройство контроля
7 - Погрузочная тележка
Тип I: Устройство для выравнивания размотки типа "люлька" (см. рис. 5a). Используется для рулонов толщиной 0,6~3,2 мм, ширина рулона менее 400 мм, максимальный вес рулона 1500 кг.
Тип II: однорулонное простое разматывающее устройство (см. рис. 5b). Используется для рулонов толщиной 0,6~3,2 мм, ширина рулона менее 610 мм, максимальный вес рулона 3000 кг.
Тип II: двухрулонное простое разматывающее устройство (см. рис. 5c). Используется для рулонов толщиной 0,6~4 мм, шириной рулона 150~610 мм, максимальный вес рулона 3000 кг.
Тип M: устройство для выравнивания размотки в тяжелых условиях (см. рис. 5d). Используется для рулонов толщиной 0,6~3,2 мм, шириной рулона 300~1300 мм, максимальным весом рулона 15000 кг.
III. Основное оборудование Структурные характеристики автоматической линии размотки и выравнивания листового металла
В связи с повышенными требованиями к производительности, в качестве основного технологического оборудования в автоматической линии размотки и выравнивания листового металла чаще всего используется специализированное оборудование, такое как разматыватели, ножницы, выравниватели, продольные машины и повторные разматыватели. Эти типы оборудования представлены следующим образом:
1. Разматыватель
Разматыватель в основном используется для поддержки рулонного материала и размотки рулонного материала с заданной скоростью линии через систему передачи или с минимальным внешним усилием. Поскольку рулонный материал уже подвергся упруго-пластической деформации изгиба при наматывании, при разматывании он расслабляется за счет эффекта отскока. Для предотвращения несчастных случаев на верхней части разматывателя обычно устанавливается прижимной ролик, и только после прижима рулон может быть ослаблен.
Конструкция и тип разматывателя различаются по форме опор, причем разные опоры подходят для рулонов разного веса и ширины. Для крупнотоннажных рулонных материалов часто используется тип двойной опоры, который предполагает использование конусов на концах двух валов разматывателя для вставки во внутренние отверстия на обоих концах рулонного материала, поднимая рулонный материал, при этом недостатком является деформация внутреннего кольца рулонного материала. Другой способ предусматривает использование веерообразной пластины для затягивания внутреннего отверстия рулонного материала, что позволяет преодолеть вышеупомянутый недостаток.
Расстояние между двумя разматывателями можно регулировать. Для рулонных материалов небольшого тоннажа в основном используется одноопорный тип, при котором внутреннее отверстие рулонного материала устанавливается на оправку одного разматывателя, а веерообразная пластина подпирает его, затягивая рулонный материал. Вращение большой оправки разматывателя и рулонного материала обычно приводится в движение электродвигателем через систему редукции, а движение открытия и закрытия веерообразной пластины, затягивающей внутреннее отверстие рулонного материала, приводится в движение гидравлической или винтовой парой, также используется ручное управление.
Технические параметры разматывателя приведены в таблице 3.
Таблица 3 Технические параметры разматывателя (производство Цзинаньской литейно-кузнечной компании Jiemai Forging Company)
Параметры | Максимальная масса рулонного материала/кг | Максимальная ширина рулонного материала/мм | Внутренний диаметр рулонного материала/мм | Максимальный внешний диаметр материала рулона/мм | Тип открывания и закрывания барабана | Величина регулировки положения/мм |
E-1-30 | 1000 | 300 | 800 | 1200 | Руководство | - |
E-3-61 | 3000 | 610 | 1200 | Руководство | - | |
EDR-1-30 | 1000×2 | 300 | 1200 | Руководство | - | |
EDR-3-61 | 3000×2 | 610 | 1200 | Руководство | - | |
E-5-61 | 5000 | 610 | 1500 | Гидравлика | - | |
E-5-100 | 5000 | 1000 | 1500 | Гидравлика | - | |
E-10-61 | 10000 | 610 | 508 | 1800 | Гидравлика | - |
E-10-100 | 10000 | 1000 | 1800 | Гидравлика | - | |
EA-5-61 | 5000 | 610 | 1500 | Гидравлика | 200 | |
EA-5-100 | 5000 | 1000 | 1500 | Гидравлика | 250 | |
EA-10-61 | 10000 | 610 | 1800 | Гидравлика | 200 | |
EA-10-100 | 10000 | 1000 | 1800 | Гидравлика | 250 | |
EA-15-130 | 15000 | 1300 | 1800 | Гидравлика | 400 |
2. Ножницы
Ножницы - важное оборудование автоматической линии для размотки, выравнивания и поперечной резки листового металла. Количество режущих ходов ножниц в значительной степени определяет производительность линии размотки. Это связано с тем, что линия размотки предъявляет следующие особые требования к ножницам:
- Высокая производительность;
- Полная загрузка;
- Высокая надежность;
- Разнообразие материалов катушек;
- Специальные методы резки и т.д.
Поэтому обычные машинки для стрижки уже не могут удовлетворить требования линии размотки, и требуются специальные машинки для стрижки. Ниже мы расскажем о нескольких типах таких машин:
(1) Продукты для стоп-резки
В этом типе разматывающей линии лента разрезается в остановленном состоянии после подачи фиксированной длины, что является так называемым состоянием "остановки резания" с помощью режущего устройства.
1) Выделенная гидравлическая трансмиссия стригального станка
Изначально в линиях размотки, производимых в Китае, в основном использовались гидравлические ножницы. Они бывают двух конструктивных форм: гильотинные и с поворотной балкой, где гильотинный тип используется в основном для тонких листов (толщина ≤6 мм), а тип с поворотной балкой - для толстых листов (толщина ≥6 мм).
Вышеперечисленные продукты с их существующей производительностью в сочетании с последующим устройством укладки материала могут удовлетворить потребности многих пользователей, которые не предъявляют высоких требований к производительности линий размотки. Например, при резке листов фиксированной длины 2000 мм на линии размотки 3×1600 гидравлическая машина для резки может достигать только 20 листов/мин.
2) Машинка для стрижки овец с механической передачей
Машинка для стрижки овец с механической трансмиссией, в которой используется комбинированная пневматическая фрикционная муфта, имеет наибольшее преимущество в быстродействии: частота холостого хода достигает 80-120 минут, что недостижимо для гидравлических машинок для стрижки овец.
Теоретически, время одного цикла стрижки составляет всего 0,37~0,75 с, а при использовании соответствующего механизма подачи с ЧПУ с фиксированной длиной производительность может достигать 30 листов/мин на линии размотки толщиной 3 мм с фиксированной длиной 2000 мм.
Этот тип ножниц оснащен трехточечным зажимом направляющих качения, который не только устраняет зазор между направляющими, упрощает смазку направляющих, предотвращает нагрев и растяжение направляющих, но и, что более важно, позволяет регулировать зазор между лезвиями в режиме онлайн, что делает его удобным для пользователей.
(2) Изделия из летучих ножниц
Летающие ножницы - это машина для стрижки, которая может выполнять поперечную стрижку фиксированной длины во время движения полосы, и ее главная особенность - непрерывная стрижка. Она может удовлетворить потребности некоторых полос с высокими требованиями к качеству поверхности, таких как нержавеющая сталь, алюминий, оцинкованный лист, лист с цветным покрытием и т.д.
Традиционные летучие ножницы широко используются на непрерывных прокатных станах и линиях непрерывной отделки в металлургической промышленности. Однако из-за сложной конструкции и высокой стоимости они не подходят для использования в вышеупомянутых линиях размотки.
До конца прошлого века появление новых летающих ножниц в значительной степени решало эти проблемы. Новые летучие ножницы были быстро разработаны за рубежом. Некоторые отечественные производители разматывающих линий также занимаются их разработкой и исследованием. Ниже представлены роторные летучие ножницы.
Рабочая скорость этого типа разматывающей линии может достигать 100 м/мин или даже выше. Система управления также автоматически генерирует числовые команды для привода летучих ножниц на основе заданной фиксированной длины и скорости подачи, а также сравнивает обнаруженные скорость подачи и длину с командами.
Когда длина подачи близка к заданной, летучие ножницы ускоряются или замедляются, точно позиционируясь в месте резки, в то время как летучие ножницы и материал пластины достигают синхронизации скорости и выполняют резку, затем летучие ножницы ускоряются или замедляются, и лезвие возвращается в исходное положение.
В настоящее время технические характеристики разматывающих линий с летучими ножницами, необходимые на внутреннем рынке, как правило, не превышают 3 мм, скорость перемещения полосы находится в пределах 100 м/мин, а максимальное количество разрезов в минуту находится в диапазоне от 100 до 120. Это означает, что при фиксированной длине 2000 мм на линии размотки толщиной 3 мм производительность может достигать 35-40 листов в минуту, что особенно подходит для линий размотки с фиксированной длиной ≤500 мм. Эти параметры приемлемы для большинства пользователей, а также экономически целесообразны.
3. Многороликовая машина для выравнивания плит
Используется для приложения переменных нагрузок к гнутым и деформированным плитам, заставляя их многократно изгибаться в противоположных направлениях, постепенно снижая предел текучести материала, а первоначальная деформация плиты постепенно уменьшается или исчезает. Принцип работы многовалковой машины для выравнивания пластин показан на рисунке 6.
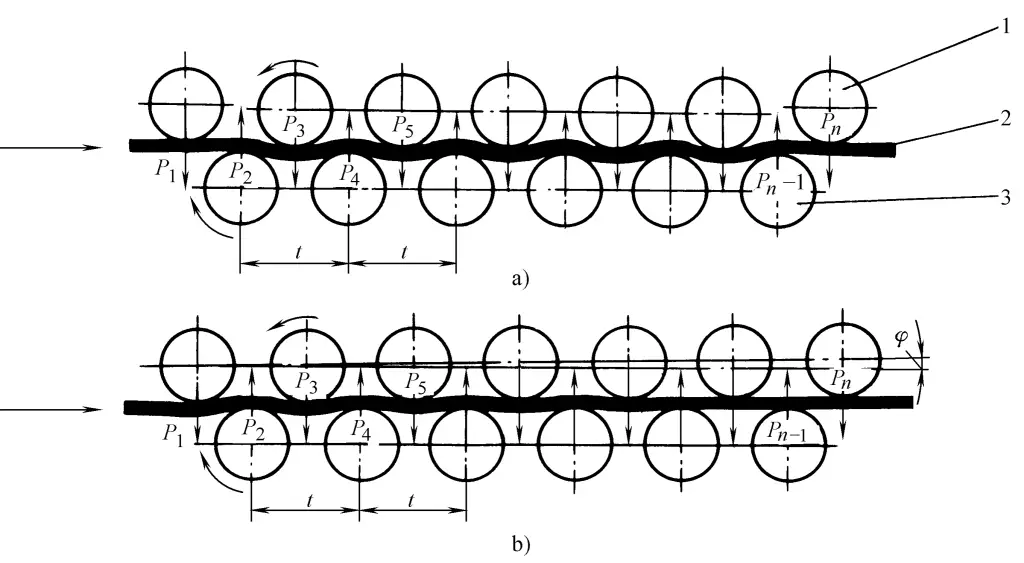
a) Верхний и нижний рабочие валки расположены параллельно
b) Верхний и нижний рабочие валки расположены под углом
1-Верхний рабочий валик
2Материал выравнивающей пластины
3-Нижний рабочий валик
Многовалковая машина для выравнивания плит состоит из верхнего и нижнего рядов рабочих валков, расположенных в шахматном порядке и приводимых в движение электродвигателем через редуктор, распределительную коробку передач и универсальную муфту. Верхний ряд валков можно регулировать вверх и вниз при параллельном расположении (см. рис. 6a), а при наклонном расположении, помимо регулировки вверх и вниз, его можно наклонять на небольшой угол (см. рис. 6b).
Параллельная схема чаще всего используется для выравнивания стальных листов толщиной более 12 мм, а наклонная - для выравнивания стальных листов тоньше 4 мм. Расстояние между валками и их количество напрямую влияют на качество выравнивания стального листа. Слишком большое расстояние между валками снижает точность нивелирования, слишком маленькое - увеличивает давление на корпус рабочего валка (P t к П n ). При выравнивании листового материала необходимо предварительно отрегулировать величину давления верхних рабочих валков в зависимости от толщины листа, чтобы обеспечить качество выравнивания.
Технические параметры многовалковых листовыравнивающих машин китайского производства приведены в таблице 4.
Таблица 4 Технические параметры роликовых пластинчатых нивелиров
Артикул | Группа 1 | Группа 2 | Группа 3 | Группа 4 | Группа 5 | Группа 6 | Группа 7 | |||
Количество рулонов n | 23 | 23 | 23 | 21 | 17(21) | 17 | 13 | |||
Зазор между валками т/мм | 25 | 32 | 40 | 50 | 63 | 80 | 100 | |||
Диаметр рулона D/мм | 23 | 30 | 38 | 48 | 60 | 75 | 95 | |||
Минимальная толщина стального листа hмин (σs ≤392МПа)/мм | 0.2 | 0.3 | 0.4 | 0.5 | 0.8 | 1 | 1.5 | |||
Эффективная длина корпуса вала л / мин | 1200 | Ширина стального листа б / мм | 1000 | 0.6 | 1.2 | 2 | 2.8 | 4 | 5.5 | 8 |
1450 | 1250 | 1 | 1.6 | 2.5 | 3.8 | 5 | 10 | |||
1700 | 1500 | 0.9 | 1.5 | 2.2 | 3.5 | 4.5 | 9 | |||
2000 | 1800 | 1.4 | 2 | 3.2 | 4 | 6 | ||||
2300 | 2000 | 2 | 3 | 4 | 6 | |||||
2800 | 2500 | |||||||||
3500 | 3200 | |||||||||
4200 | 4000 | |||||||||
Максимальная скорость правки Vmax /(м/с) | 1 | 1 | 1 | 1 | 1 | 1 | 1 | |||
Максимальная мощность главного двигателя Nmax /кВт | 13 | 30 | 55 | 80 | 95(110) | 130 | 155 | |||
Характеристика максимальной нагрузки Wx /knm | 0.144 | 0.486 | 0.141 | 3.2 | 7.2 | 12.8 | 28.8 |
Артикул | Группа 8 | Группа 9 | Группа 10 | Группа 11 | Группа 12 | Группа 13 | Группа 14 | |||
Количество роликов n | 13 | 11 | 11 | 9 | 9 | T | 7 | |||
Зазор между валками т/мм | 125 | 160 | 200 | 250 | 300 | 400 | 500 | |||
Диаметр рулона D/мм | 120 | 150 | 180 | 220 | 260 | 340 | 420 | |||
Минимальная толщина стального листа h мин (σs ≤392МПа)/мм | 2 | 3 | 4 | 5 | 6 | 10 | 16 | |||
Эффективная длина корпуса вала л / мин | 1200 | Ширина стального листа б / мм | 1000 | |||||||
1450 | 1250 | 15 | ||||||||
1700 | 1500 | 14 | 19 | |||||||
2000 | 1800 | 8 | 13 | 18 | ||||||
2300 | 2000 | 8 | 12 | 17 | 25 | 32 | ||||
2800 | 2500 | 16 | 22 | 28 | 40 | 50 | ||||
3500 | 3200 | 20 | 25 | 36 | 45 | |||||
4200 | 4000 | 32 | 40 | |||||||
Максимальная скорость правки Vmax /(м/с) | 0.5 | 0.5 | 0.3 | 0.3 | 0.3 | 0.2 | 0.1 | |||
Максимальная мощность главного двигателя Nmax /кВт | 130 | 130 | 245 | 180 | 210 | 180 | 110 | |||
Характеристика максимальной нагрузки Wx /knm | 51.2 | 115.2 | 256 | 512 | 800 | 1640 | 2560 |
4. Машина для многополосных ножниц
Многополосные ножницы часто используются для резки широких рулонных материалов на несколько полос одинаковой или разной ширины в зависимости от потребностей пользователя, а затем перематывают их в рулоны с помощью разматывателя. Они часто используются в линиях размотки, выравнивания и продольной резки, а также для обрезки краев рулонных материалов.
Максимальная толщина материала, который может разрезать эта машина, составляет до 12 мм, обычно используются материалы толщиной менее 4 мм. Для некоторых материалов с более высокой прочностью минимальная толщина может достигать 0,05 мм при использовании ножниц на растяжение, но при этом трудно гарантировать качество резки. Как правило, 12 пар режущих дисков могут быть установлены на верхнем и нижнем валах этой машины. Для некоторых тонких и узких полос продукция некоторых зарубежных компаний может иметь до 42 пар режущих дисков, способных резать 41 узкую полосу одновременно.
На большинстве линий продольной резки, использующих несколько стриппинг-машин, из-за конструктивных ограничений вспомогательных устройств, качества стрижки и простоты регулировки количество стриппируемых полос обычно ограничено в пределах 20. Максимальная ширина стриженого полосового материала обычно составляет менее 2000 мм, а минимальная ширина зависит от толщины полосы.
Многополосная машинка для стрижки состоит из корпуса 1, подвижного места вала режущего диска 2, неподвижного места вала режущего диска 3 и системы передачи 4. Трансмиссионная система соединена с верхним и нижним валами режущего диска с помощью электродвигателя через редуктор и универсальную муфту, а ее структурный вид показан на рисунке 7.

1-Машинный корпус
2-Подвижное седло вала режущего диска
3-Посадочное место вала режущего диска
4-Трансмиссионная система
5. Перемоточный станок
Перемоточный станок используется для сматывания полосового или узкополосного материала в рулоны. Расширение и сжатие барабана перемоточного станка и зажим губок приводятся в действие гидравлическими и механическими средствами.
Гидравлический привод приводится в действие штоком поршня в гидравлической системе, который приводит в движение наклонный клин, заставляя рулон расширяться и зажимать губки. В основном используется для намотки больших спецификаций широкой ленты или полосового материала. Механический привод приводится в действие винтовой парой, приводящей в движение многоштоковый механизм, заставляющий барабан расширяться и зажимать губки; часто используется для намотки небольших спецификаций узкой полосы или продольно разрезанного полосового материала.
Ниже представлено описание моталки с гидравлическим приводом (см. рис. 8).
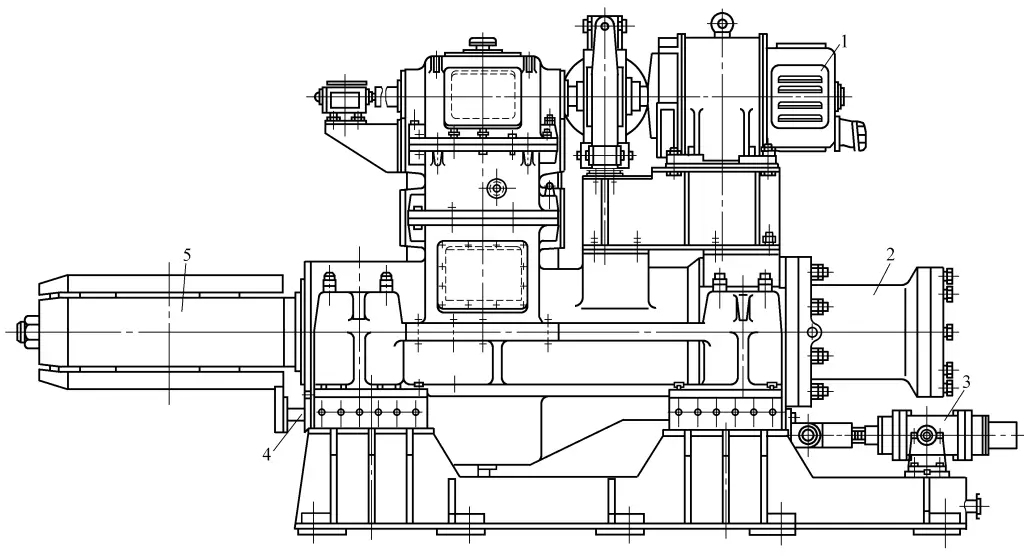
1-Электрический двигатель
2-Осевой гидравлический цилиндр
3-Плавающий гидравлический цилиндр
Устройство для разгрузки 4-х ленточных валов
Барабан с 5 барабанами
Электродвигатель 1 через редуктор приводит во вращение барабан 5. Он оснащен гидравлическим цилиндром 2 с осевым расширением для расширения и сжатия барабана. Чтобы обеспечить выравнивание краев стальной полосы, на моталке установлен плавающий цилиндр 3 для контроля отклонений. Моталка также оснащена гидравлическим цилиндром 4 для выталкивания рулона ленты.
Как правило, моталка имеет единую форму опоры со вспомогательной опорой для стабильной работы. Основная структура моталки аналогична структуре разматывателя, но клиновидная скользящая посадка является неотъемлемой частью для повышения жесткости опоры моталки.
Наматывающее устройство имеет четыре носовидные пластины на упростителе бобины, которые могут радиально расширяться и сжиматься при нажатии и вытягивании наклонного клина с помощью гидравлического цилиндра. При расширении две из носовых пластин образуют пару зажимов, используемых для зажима головки планки, и вращение барабана завершает намотку планки.
Намотчик приводится в действие двигателем переменного тока, скорость которого регулируется регулятором скорости переменного тока. В цепи передачи установлен тормоз. В процессе намотки, по мере увеличения диаметра рулона, система управления автоматически замедляет двигатель намотчика для согласования линейной скорости со станком продольной резки.
IV. Знакомство с работой некоторых вспомогательных машин в автоматической линии выравнивания для размотки листового металла
В связи с растущим разнообразием и диапазоном применения автоматической линии выравнивания для размотки листового металла, с точки зрения фактического использования пользователями, производительность некоторых вспомогательных машин в автоматической линии выравнивания играет очень важную роль в качестве продукции и эффективности производственной линии. Поэтому необходимо представить некоторые ключевые вспомогательные устройства, чтобы привлечь общее внимание производителей оборудования и пользователей.
1. Устройство для открывания материала
После загрузки рулона в разматыватель он проходит через устройство прижима головки свинцового материала, сжимает головку материала перед открытием и поднимает ее во время нормальной работы. Прижимная головка может вращаться двигателем, и головка материала сначала проходит через устройство раскрытия материала, а после того, как головка материала согнута и расплющена, она поступает в выравнивающую машину. Для разных толщин листов или материалов используются разные устройства для раскрытия материала.
Для тонких листов (толщина листа ≤ 6 мм) устройство для раскрытия материала состоит из телескопической платформы и ведущей платформы для материала, приводимых в движение гидравлическими цилиндрами, которые могут поворачиваться вверх и вниз и двигаться вперед и назад.
Для толстых листов (толщина листа ≥ 6 мм) обычно используется устройство для раскрытия материала портального типа. Это устройство состоит из рамы, прижимных роликов, прижимной головки, лопаточной плиты и т. д. Прижимная головка расположена прямо над разматывателем в центре рамы устройства для раскрытия материала, приводится во вращение гидравлическим двигателем и перемещается вверх и вниз с помощью гидравлического цилиндра. Сиденье заслонки приводится в действие цилиндром толкания для перемещения вперед-назад, плита лопаты устанавливается на сиденье плиты лопаты и перемещается вместе с ней, а нижняя часть плиты лопаты оснащена двумя подъемными гидравлическими цилиндрами, позволяющими головке плиты лопаты перемещаться вверх-вниз в соответствии с разматывателем для равномерной подачи материала.
2. Устройство подачи
Подающее устройство играет важную роль в автоматической линии поперечной резки для выравнивания листового металла, обеспечивая точность размеров листового материала. На рисунке 9 показана стандартная структурная схема подающего устройства.
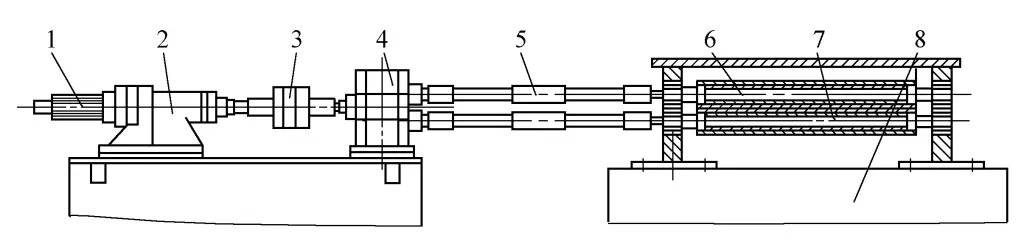
1-Сервомотор
2-Редуктор
Сменщик 3 валов
Коробка передач с 4 передачами
5-Универсальное соединение
6-Верхний ролик
7-Нижний ролик
8-машинная база
Вращение подающих роликов 6 и 7 осуществляется серводвигателем 1 через редуктор 2, коробку передач 4 и карданный шарнир 5 с возможностью регулировки направления и скорости вращения. Верхний ролик 6 может перемещаться вверх и вниз параллельно нижнему ролику 7, облегчая введение и прессование листового материала. Корпуса верхнего и нижнего подающих роликов изготовлены из бесшовных стальных труб, сваренных между собой, а затем покрыты вулканизированной резиной. Требуемая твердость составляет от 86 до 88 HS, а шероховатость поверхности - от Ra0,8 до 0,4 мкм.
Верхний и нижний подающие ролики приводятся в движение одним и тем же двигателем, часто включаются и переключаются между высокой и низкой скоростью, поэтому возникает значительное инерционное воздействие. Чтобы уменьшить инерционное воздействие верхнего и нижнего подающих роликов и обеспечить точность подачи, необходимо минимизировать вес самих подающих роликов, обеспечить высокую жесткость и прочность валов роликов, поэтому подающие ролики имеют полую конструкцию.
3. Устройство обнаружения
Назначение устройства обнаружения заключается в обнаружении и обеспечении обратной связи по точности подачи листового материала. На рисунке 10 показана стандартная структурная схема устройства обнаружения.
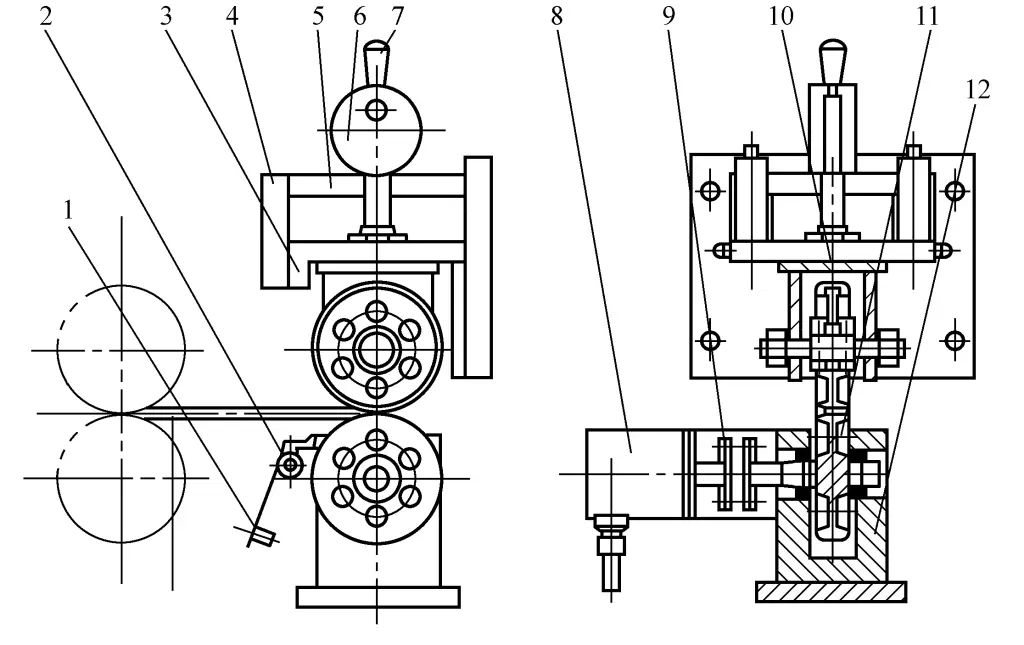
1-Маятник
2-Скрапер
3-сдвижное сиденье
Колонка с 4 направляющими
5-Фиксированный кронштейн
6-эксцентриковое колесо
7-ручка
8-поворотный кодировщик
9-муфта
10-Верхнее колесо обнаружения
11-Нижнее колесо обнаружения
12-Нижний кронштейн
Во время работы сначала потяните за ручку 7, используя эксцентриковое колесо 6 для подъема скользящего сиденья 3 и верхнего детекторного колеса 10. Когда подающий ролик направит лист металла между верхним колесом обнаружения 10 и нижним колесом обнаружения 11, потяните назад рукоятку 7, позволяя опуститься скользящему седлу 3 и верхнему колесу обнаружения 10. Под действием силы пружины верхнее и нижнее детектирующие колеса плотно зажимают металлический лист.
Когда подающий ролик продолжает подавать лист металла, лист металла приводит во вращение два колеса обнаружения. Поворотный энкодер 8 соединен с нижним колесом обнаружения через муфту 9. В это время поворотный энкодер также будет вращаться синхронно, генерируя импульсы. Механизм обнаружения является ключевым компонентом секции подачи, и его конструкция и точность изготовления непосредственно влияют на точность подачи производственной линии, поэтому разработка, изготовление и установка механизма обнаружения особенно важны.
Внешняя окружность верхнего детектирующего колеса покрыта твердой резиной для предотвращения относительного скольжения между детектирующим колесом и поверхностью металлического листа во время измерения длины, что снижает точность измерения. Нижнее колесо обнаружения представляет собой жесткий цельный элемент оси колеса, что уменьшает погрешности при сборке. Его поверхность покрыта твердым хромом с поверхностной твердостью 800~900HV, что обеспечивает длительную работу без износа.
Для обеспечения точной работы колес обнаружения необходимо содержать поверхность колеса в чистоте. Установленный скребок 2 плотно прижимается к поверхности колеса путем регулировки положения тяжелого молотка 1, чтобы удалить все налипания на поверхности колеса, обеспечивая точность измерений.
4. Устройство для укладки бисера
Укладочное устройство в основном обеспечивает укладку и выравнивание листовых материалов после резки и продольной резки (производственная линия имеет возможность как продольной, так и поперечной резки), особенно для листовых материалов, требующих высокой точности поверхности, эта проблема является особенно сложной для решения. Сложность заключается в следующем:
- Выравнивание листовых материалов с прорезями по ширине;
- Не допускать появления царапин на поверхности листовых материалов в процессе укладки.
В соответствии с различными требованиями используются различные штабелирующие устройства. Ниже представлены соответствующие устройства:
(1) Обычное устройство для укладки бисера конвейерного типа
После резки полосы подаются вдоль подающей ленты, затем, используя собственный вес и инерцию, создаваемую скоростью конвейера, они скользят по поверхности предыдущего листа для выравнивания, во время которого используется устройство воздушной подушки для минимизации царапин между листами (см. рис. 11).
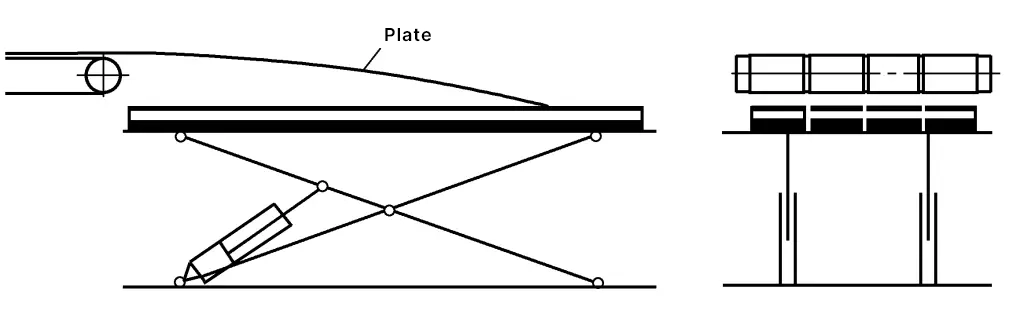
(2) Пневматическое устройство для штабелирования с переворачиванием
Пневматический спуск материала обычно состоит из пневматической опорной рамы, боковых и задних ограждений. Диапазон регулировки штабеля: ширина от 100 до 2500 мм, длина от 100 до 6000 мм. В реальной производственной линии одно или несколько штабелирующих устройств могут быть настроены в режиме онлайн одновременно (см. рис. 12), чтобы соответствовать требованиям скорости производства.
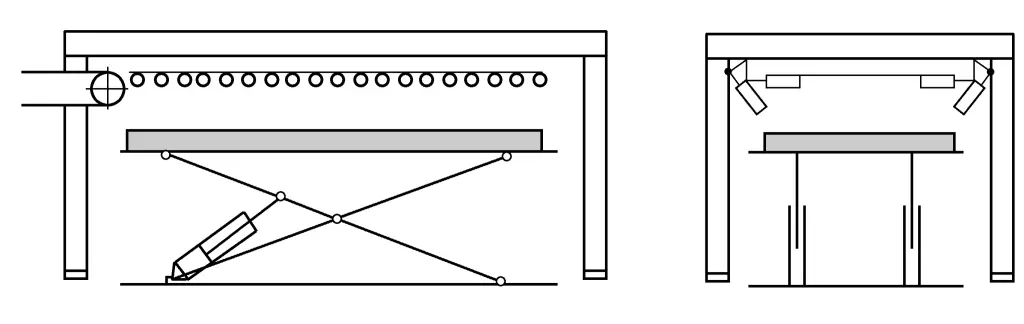
Принцип работы: по окончании поперечной резки лист металла транспортируется конвейерной лентой к пневматической стойке для сброса. На месте по сигналу выключателя стойка переворачивается, и лист металла падает в бункер, образованный двумя боковыми и задней перегородками. Положение боковых перегородок можно регулировать. Он может решить проблему штабелирования всего листа после поперечной резки, но его недостатком является то, что он не может решить проблему штабелирования листов, разделенных на несколько полос.
(3) Устройство для укладки конструкции с присосками
Конструкция с присосками используется для обработки листового металла после резки и раскроя. Основные проблемы, которые она создает, - это либо вынужденное замедление темпов производства, либо чрезмерные производственные затраты.
(4) Электромагнитный ролик конвейерной ленты щелевого штабелирования устройство
В основном используется лента, расположенная снизу, для перемещения подвешенного материала, дополненная разделительной лентой и перфоратором для решения проблемы штабелирования после производственной линии продольной резки. Его главная особенность заключается в том, что в раме конвейерной ленты установлено электромагнитное роликовое устройство, которое может контролировать силу всасывания, позволяя разрезанным материалам висеть под лентой и падать параллельно при отключении питания в заданном положении, тем самым решая проблему разрезания и одновременно обеспечивая отсутствие царапин на поверхности заготовок.
V. Перспективы применения автоматической линии размотки и выравнивания листового металла
1. Специализированная линия размотки и сбрасывания в автомобильной промышленности
В конце 1990-х годов в Китае быстро развивалась современная автомобильная промышленность. Производители автомобилей среднего и высокого класса с годовым объемом выпуска более 100 000 единиц после завершения строительства линий холодной штамповки обратили внимание на инвестиции в разматывающие и сбрасывающие производственные линии.
Причина в том, что листовой металл, поставляемый сталелитейными заводами, имеет следующие недостатки:
- Низкое качество поверхности, не отвечающее высоким стандартам, предъявляемым к наружным покрытиям;
- Низкий коэффициент использования материала, что ограничивает снижение затрат на седацию.
Данный тип производственной линии должен обеспечивать поставки следующих материалов: холоднокатаные листы без покрытия, листы с одно- и двусторонним электролитическим покрытием, одно- и двусторонние горячеоцинкованные листы, высокопрочные холоднокатаные листы, высокопрочные оцинкованные листы, горячекатаные травленые листы, алюминиевые листы.
2. Разматывающая и выравнивающая автоматическая производственная линия для холодной гибки различных типов материалов
Холоднодеформированные профили - это вид материала с потенциалом развития для промышленности и строительства, форма поперечного сечения которого может быть оптимизирована в соответствии с потребностями использования, что позволяет создать наиболее рациональное сечение, снизить расход материала, улучшить механические свойства, повысить несущую способность и общую жесткость компонентов.
В настоящее время наиболее часто используемые размотки и выравнивания холодной гибки автоматическая производственная линия для профилей может завершить различные процессы формирования от катушки до специальной формы профиля. Таких как: C, Z-образная сталь, автомобильные балки, бамперы, профили полок, колонны электрических шкафов, пластины ограждений и т.д., удовлетворяя потребности транспорта, автомобильного производства, строительной промышленности, логистики, и, таким образом, имеет широкое пространство для развития.
Этот тип холодной гибки разматывания и выравнивания автоматической производственной линии обычно состоит из разматывателя, выравнивателя, сварщика резки головы, питателя, пробивной машины, холодной гибка формовка машина, летающие ножницы, система передачи энергии и т.д.
Рулонный материал проходит через разматыватель, выравниватель, качающийся мост, затем поступает в вырубное оборудование для пробивки или резки, затем через валковая штамповка устройство, а затем разрезается на части фиксированной длины на станке с летучими ножницами.