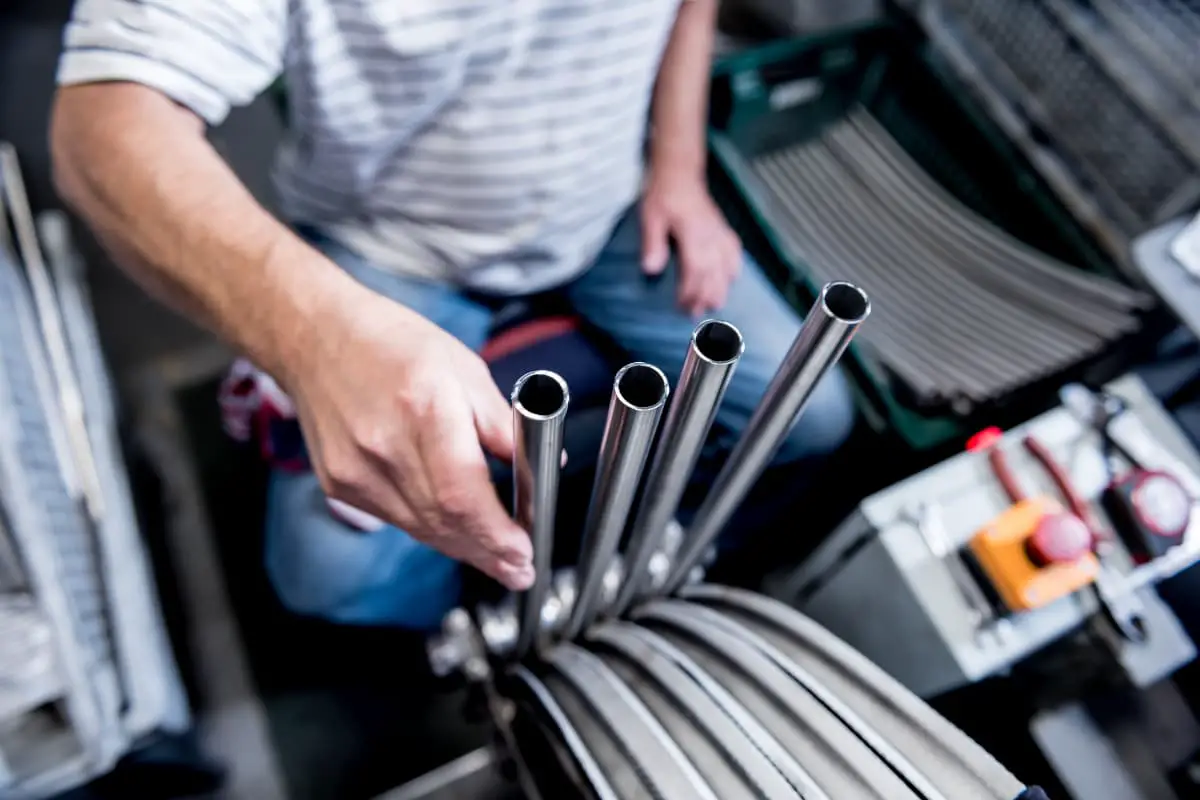
I. Классификация оборудования для гибки труб
1. Трубогиб
Трубогиб является основным оборудованием для обработки труб. Существует множество конструктивных форм трубогибов, которые можно разделить на трубогибы для холодных труб и трубогибы для горячих труб в зависимости от того, применяется ли нагрев при гибке, на механические и гидравлические в зависимости от способа передачи, а также на ручные, полуавтоматические, автоматические и с ЧПУ в зависимости от способа управления. Трубогибы с механической передачей имеют простую конструкцию, удобны в производстве и обладают большей универсальностью.
Гидравлические трубогибы имеют плавную и надежную передачу, низкий уровень шума, компактную конструкцию и могут гнуть трубы различных диаметров. Трубогибы с полуавтоматическим управлением, как правило, автоматически контролируют только угол гиба и используются в основном для среднего и мелкосерийного производства. Трубогибы с автоматическим управлением могут автоматически контролировать весь процесс подачи трубы, гибки и гибки угла поворота в пространстве. Этот тип трубогибов обычно использует гидравлическую передачу и подходит для массового производства и случаев с различными размерами труб.
Трубогибы с ЧПУ могут автоматически управлять процессом гибки в соответствии с программой и размерами, указанными на чертеже детали, путем ввода данных. Они подходят для массового производства, особенно в тех случаях, когда параметры размеров труб часто меняются. В этом разделе кратко представлены базовая структура и основные технические характеристики широко используемых в производстве трубогибов для холодной и горячей гибки труб.
(1) Холодный трубогиб
1) Ручной трубогиб.
Обычно используемый ручной трубогиб, как показано на рисунке 4-39, может гнуть трубы диаметром 15, 20, 25. Ручной трубогиб состоит из стальной оболочки 1, неподвижного направляющего колеса 3, подвижного направляющего колеса 2 и зажимного кольца 4 и крепится к раме болтами.
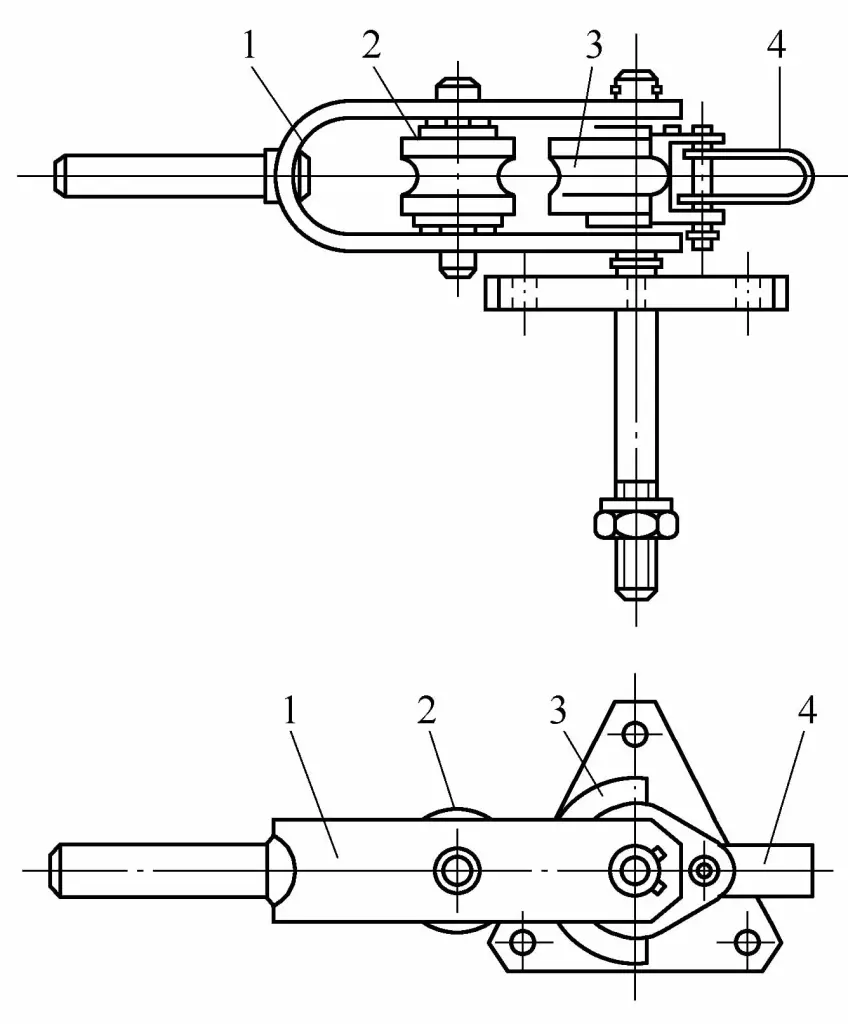
1-Стальная куртка
2-Подвижный шкив
3-Фиксированный шкив
4-Зажимное кольцо
Перед гибкой трубы сначала поместите трубную заготовку между двумя шкивами и вставьте конец трубы в зажимное кольцо неподвижного шкива. Во время гибки вращайте стальную оболочку и приводите подвижный шкив во вращение вокруг неподвижного шкива, завершая тем самым процесс гибки. Максимальный угол гибки на этом ручном гибочном станке может достигать 180°, а его технические характеристики приведены в таблице 4-10.
Таблица 4-10 Технические характеристики ручного гибочного станка
Технические индикаторы | Данные | ||
Диаметр гнутой трубы/мм | 15 | 20 | 25 |
Радиус изгиба/мм | 50 | 63 | 85 |
Размеры/мм | 500 ×152 ×292 | 640×162 x292 | 722 ×230 ×271 |
Вес/Н | 110 | 140 | 170 |
2) Моторизованный гибочный станок.
Обычно используемый моторизованный (с приводом от червячной передачи и червяка) гибочный станок, как показано на рисунке 4-40, может сгибать трубы диаметром от Φ15 до Φ32 мм. Моторизованный гибочный станок состоит из рамы 1, червячного редуктора 2, электродвигателя 4 и четырех комплектов шкивов 3, а принцип его работы такой же, как и у ручного гибочного станка.
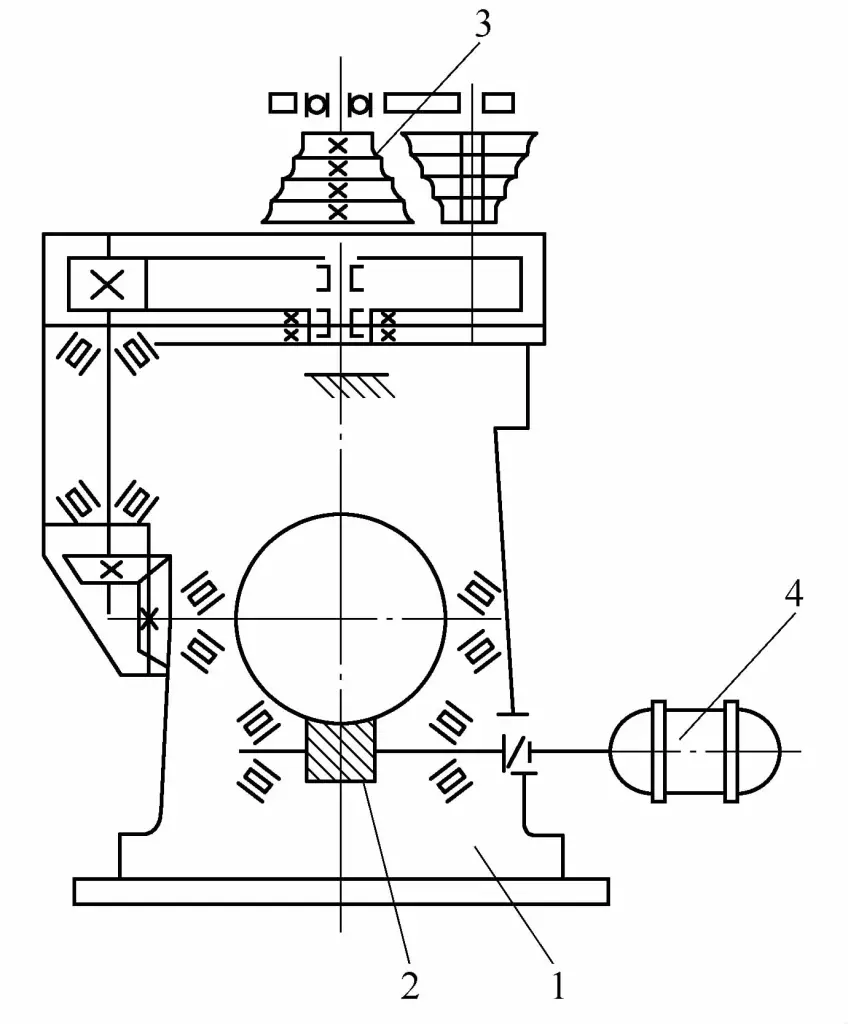
1-рама
2-Червячный редуктор
3 - 4 направляющих колеса
4-Электрический двигатель
При гибке трубы сначала загрузите трубную заготовку в пару направляющих колес соответствующего диаметра и закрепите ее с помощью зажимного кольца. Затем включите электродвигатель, чтобы вращать подвижное направляющее колесо вокруг неподвижного направляющего колеса для завершения гибки. Технические характеристики данного трубогиба приведены в таблице 4-11.
Таблица 4-11 Технические характеристики моторизованного трубогиба
Технические индикаторы | Данные | |||
Диаметр гнутой трубы/мм | 15 | 20 | 25 | 32 |
Радиус изгиба/мм | 49 | 63 | 87 | 114 |
Максимальный угол изгиба/(°) | 180 | |||
Мощность электродвигателя/кВт | 2.8 | |||
Размеры/мм | 650 ×975 ×1341 | |||
Вес/Н | 4900 |
3) Оправка трубогиба
Трубогиб с дорном, как показано на рисунке 4-41, может гнуть трубы диаметром от Φ32 до Φ159 мм. При гибке труб разного диаметра можно использовать направляющие колеса, прижимные блоки и оправки разного диаметра.
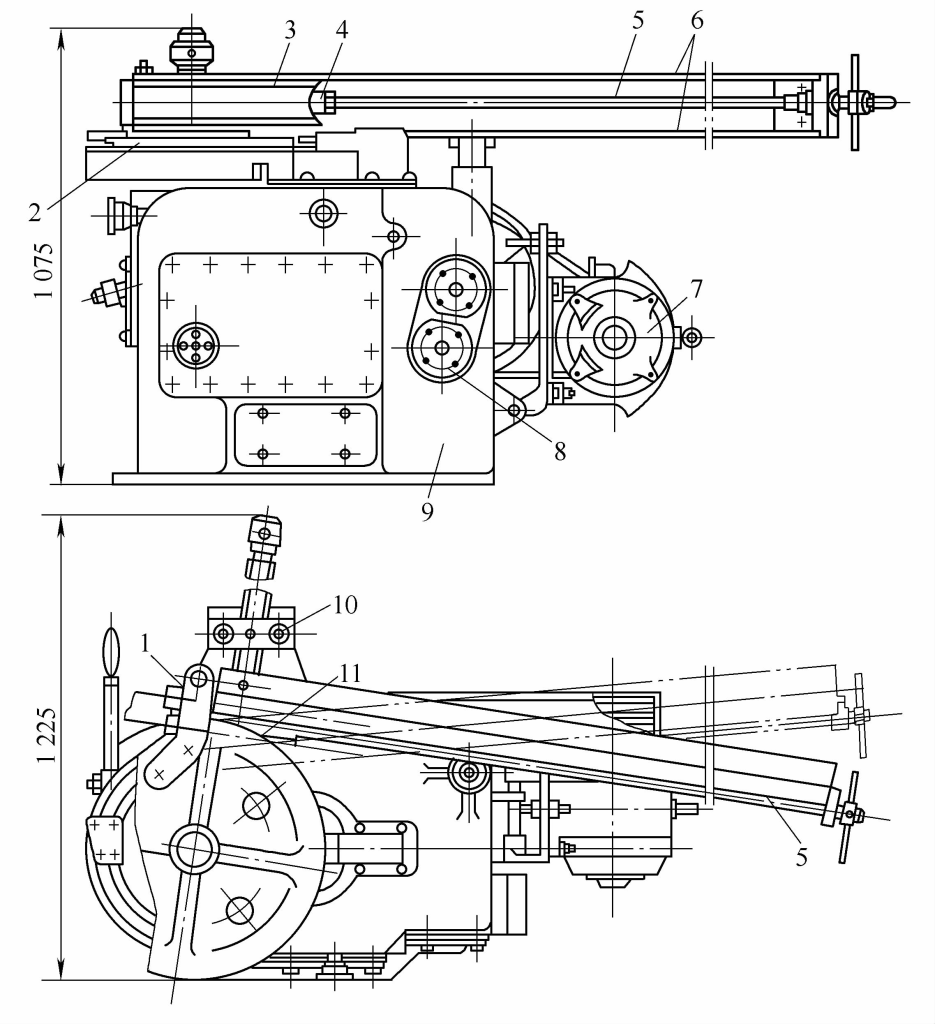
1-Эксцентриковый зажим
2-Поворотный рабочий стол
3-Сгибающий шкив
4-Мандрел
5-Протяжка
6-Опорный стержень
7-Электрический двигатель
8-ступенчатая пара
9-рамочный
10-Топочная рама
11-Пресс-блок
Станок для гибки оправок состоит из рамы 9 (с редуктором внутри рамы), вращающегося рабочего стола 2, гибочного шкива 3, опорной штанги 6 для блока пресса 11, верхней рамы 10, оправки 4, эксцентриковой муфты 1, электродвигателя 7 и т.д. Гибочный станок имеет рукоятку, которая может управлять муфтой редуктора станка, а также продвижением и отходом верхней рамы и прижимного блока, чтобы регулировать степень зажима трубной заготовки. Скорость гибки может быть отрегулирована путем изменения пары шестерен.
При гибке труб сначала вставьте оправку в трубную заготовку, а затем закрепите трубную заготовку на направляющем колесе с помощью эксцентрикового зажима. При вращении поворотного стола трубная заготовка постепенно изгибается. Оправка остается неподвижной в течение всего процесса гибки, поддерживая стенку трубы изнутри, чтобы предотвратить овальность согнутой части. Технические характеристики трубогиба с дорном приведены в таблице 4-12.
Таблица 4-12 Технические характеристики трубогиба с дорном
Технические индикаторы | Данные | |||
Диаметр гнутой трубы/мм | 32~89 | 38 ~108 | 38 ~159 | |
Максимальная толщина стенки гнутой трубы/мм | 5 | 8 | 8 | |
Радиус изгиба/мм | 85~350 | 75 ~800 | 75 ~1000 | |
Максимальный угол изгиба/(°) | Когда радиус изгиба составляет ≤ 400 мм | 180 | 180 | 180 |
При радиусе изгиба >400 мм | - | 90 | 90 | |
Скорость вращения гибочного направляющего колеса / (r-min -1 ) | 0.6 | 0.43 | 0.43 | |
Количество подходящих направляющих колес | 6 | 9 | 11 | |
Мощность электродвигателя/кВт | 4.5 | 7 | 2×7 | |
Вес/Н | 16740 | 27340 | 40000 |
Трубогиб с большим дорном, как показано на рисунке 4-42, может гнуть трубы диаметром от Φ108 до Φ219. Станок оснащен секторной тяговой плитой 2, полным набором сменных гибочных секторных колес 1, держателем трубной заготовки 3, оправкой 4, рабочим столом 5, опорой 6, опорной штангой 7 и электрической лебедкой 8.
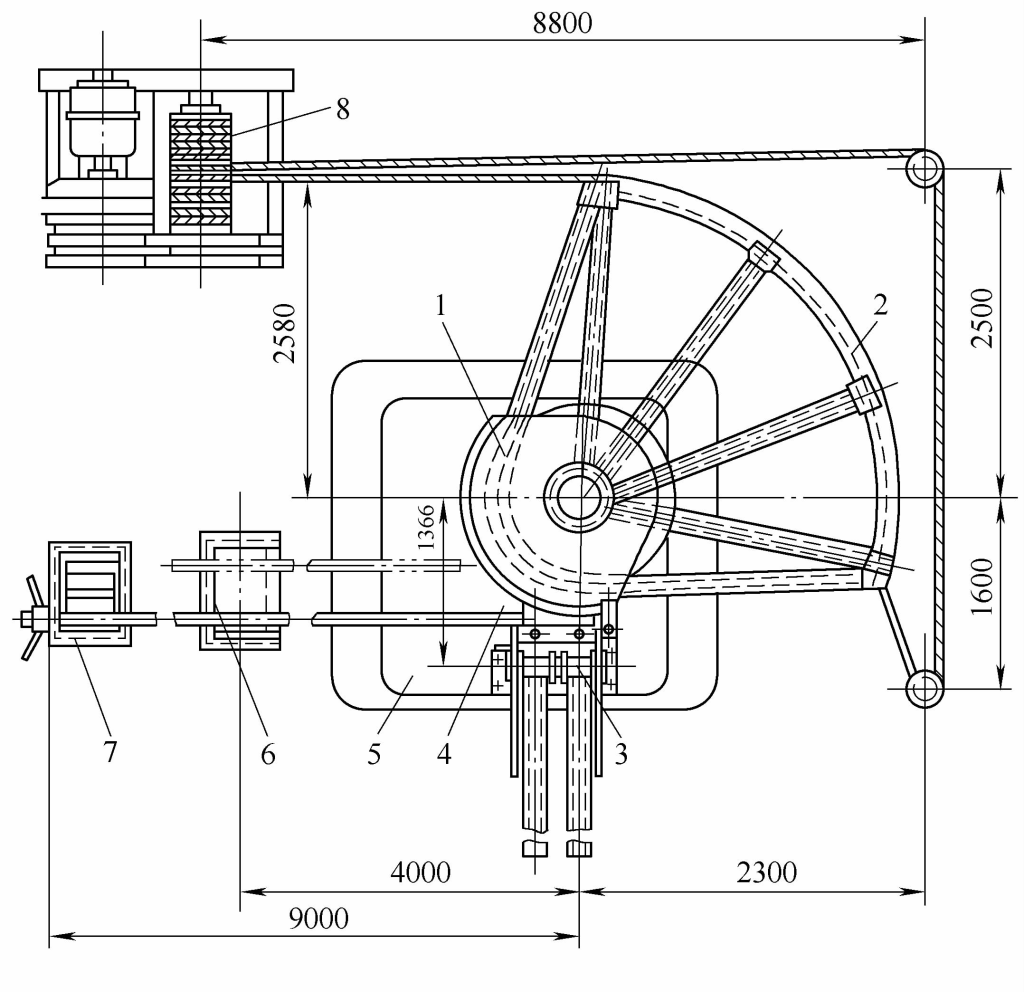
1-Сгибаемое секторное колесо
2-секторная тяговая пластина
3-трубный держатель заготовки
4-Мандрел
5-рабочий стол
6-створчатый
7-ми стержневая опора
8-Электрическая лебедка
Электрическая лебедка для трубогиба приводится в движение, протягивая секторный стержень через стальной проволочный трос. Барабан лебедки разделен на две части: одну для наматывания, другую для отпускания. Когда барабан вращается в обратном направлении, секторный стержень возвращается в исходное положение.
При гибке труб различных диаметров можно заменять гибочные секторные колеса, держатели заготовок и оправки соответствующего диаметра.
Технические характеристики этого большого трубогиба приведены в таблице 4-13.
Таблица 4-13 Технические характеристики большого трубогиба
Технические индикаторы | Данные |
Диаметр гнутой трубы/мм | 108,114,133,159,168,219 |
Максимальная толщина стенки гнутой трубы/мм | 8 |
Радиус изгиба/мм | 4D (D - диаметр кривизны) |
Максимальный угол изгиба/(°) | 90 |
Скорость изгиба/(м-мин-") | 8 ~10 |
Тяговое усилие/кН электрической лебедки во время гибка труб | 50 |
Размеры/м | 11,8 x4,65 x1,3 |
4) Гидравлический трубогиб
Широко используемый гидравлический трубогиб показан на рисунке 4-43, а его технические характеристики приведены в таблице 4-14.
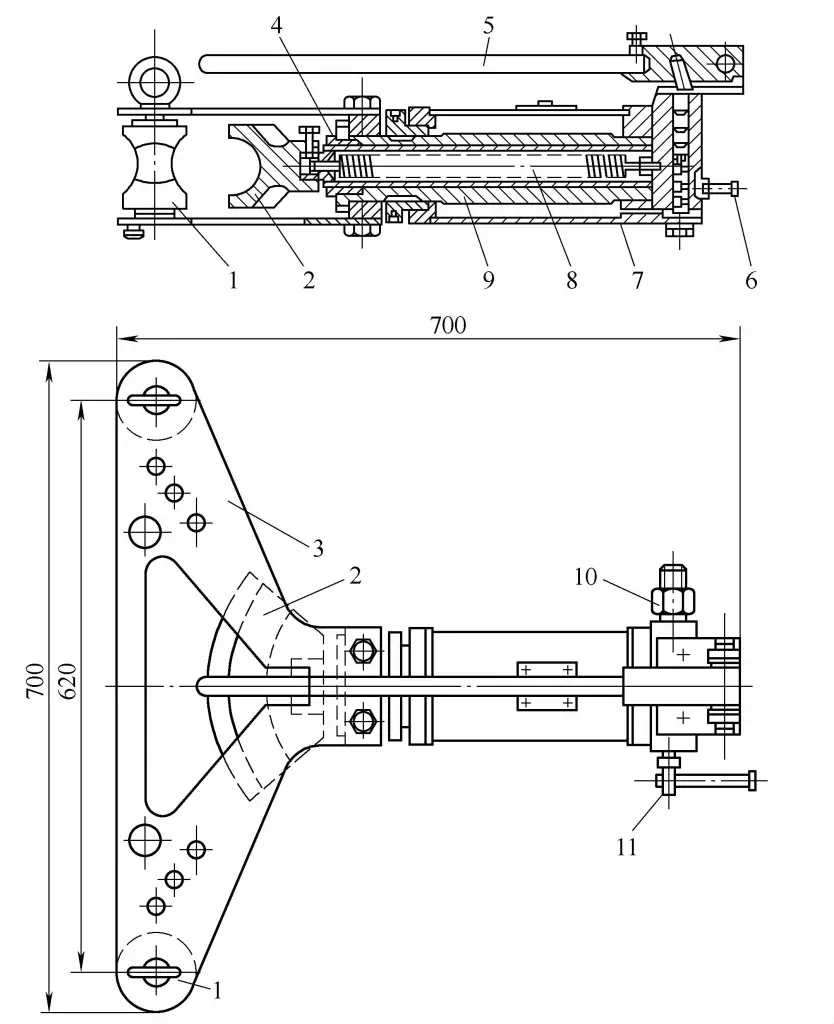
1-Верхний ролик
2-Трубогибочный пресс
3-куртка
4-Сбросная пружина
5-ручка
6-Масляная форсунка
7-Масляный бак
8-поршневой шток
9-Гидравлический цилиндр
10-Маслозаборная форсунка
11-Игольчатый клапан
Таблица 4-14 Технические характеристики гидравлического трубогиба
Технические индикаторы | Данные | ||
Диаметр гнутой трубы/мм | 15,20,25 | 25,32,40,50 | 76,89,114,127 |
Максимальный угол изгиба/(°) | 90 | 90 | 90 |
Максимальный ход штока поршня/мм | 300 | 310 | 530 |
Максимальное давление/МПа | - | 300 | 300 |
Гидравлический пресс Производительность | Ручной поршневой насос | Ручной поршневой насос или насос с электродвигателем | Электрический поршневой насос |
Максимальное давление ручного насоса /N | 200 | 230 | - |
Мощность электродвигателя/кВт | - | - | 2.8 |
Скорость вращения формы для гибки труб во время гибки / (мм-с -1 ) | - | - | 4.5 |
Размеры/мм | - | 700 ×700 ×220 | 1500 x1400 x700 |
Вес/Н | 175 | 460 | 6320 |
Примечание: Толщина стенки трубы составляет от 3 до 7 мм.
(2) Трубогиб с индукционным нагревом средней частоты
Трубогиб с индукционным нагревом средней частоты - это широко используемое оборудование для термической гибки, способное выполнять процесс гибки с нагревом, сгибанием и охлаждением непрерывно. Данный тип трубогиба состоит из механической и электрической частей, где механическая часть включает в себя зажимные и прикладывающие усилие части для гибки, а электрическая часть включает в себя двигатель и генератор средней частоты. В зависимости от способа приложения изгибающего момента трубогибы делятся на толкающие и тянущие.
1) Трубогибочный станок с индукционным нагревом средней частоты.
Принцип работы трубогиба толкающего типа со среднечастотным индукционным нагревом показан на рисунке 4-44. Процесс гибки завершается приложением осевого усилия F к трубной заготовке, нагревом, гибкой и распылением воды для охлаждения. Технические характеристики этого трубогиба приведены в таблице 4-15.
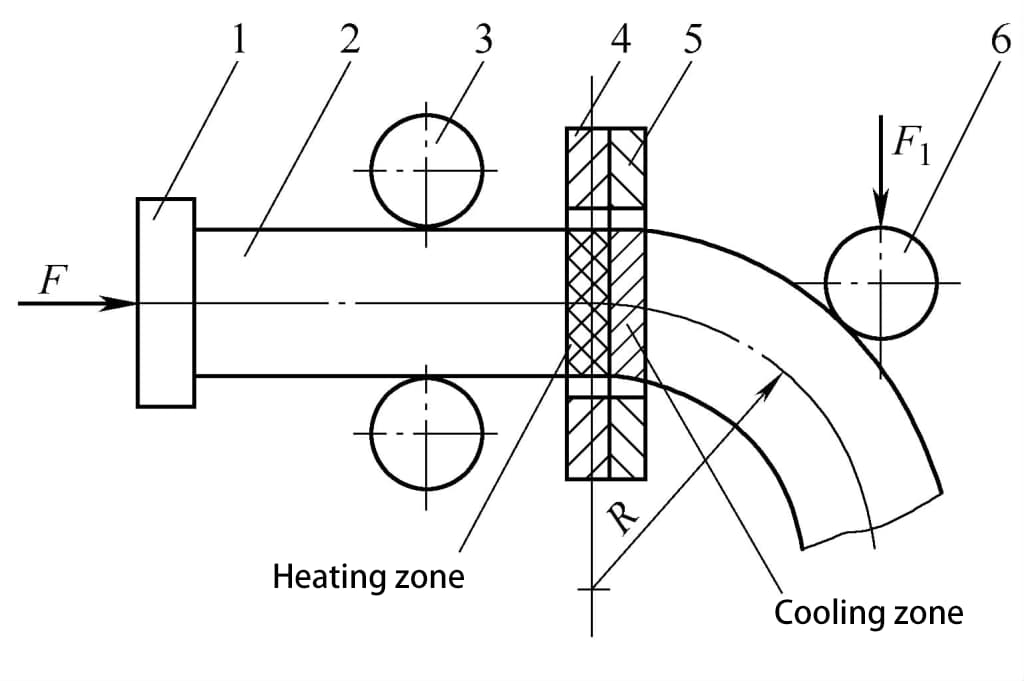
1-Тормозная перегородка
2-трубная заготовка
3-х направляющее колесо
4 - Индукционная катушка средней частоты
5-охладитель
6-Топовое колесо
Таблица 4-15 Технические характеристики трубогибочного станка с индукционным нагревом средней частоты
Технические характеристики | Данные | |
Диаметр гибки трубы/мм | 952~99 | |
Толщина стенки трубы / мм | <10 | |
Минимальный радиус изгиба / мм | 1,5D (где D - диаметр изгиба) | |
Скорость подачи механизма / (мм-с -1 ) | Продольный | 0.3~3 |
Латеральный | 0.2~2 | |
Мощность двигателей продольной и поперечной трансмиссии/кВт | 4.5 | |
Индукционный нагревательный прибор средней частоты | Мощность/кВт | 100 |
Частота/Гц | 2500 | |
Размеры/м | 5. 2 x1. 62 x1. 05 | |
Вес/кН | 50 |
2) Среднечастотный индукционный электрический нагревательный трубогибочный станок.
Принцип строения трубогибочного станка с индукционным электронагревом средней частоты показан на рисунке 4-45, в основном используется для гибки толстостенных (менее 30 мм) трубных фитингов. Этот тип трубогиба проще, чем вышеупомянутый трубогиб с толкателем, поскольку не требует установки механизмов продольной и поперечной верхней трубы, а работа по гибке может быть завершена путем приведения в движение веерообразного диска 5 с помощью электрической лебедки 10.
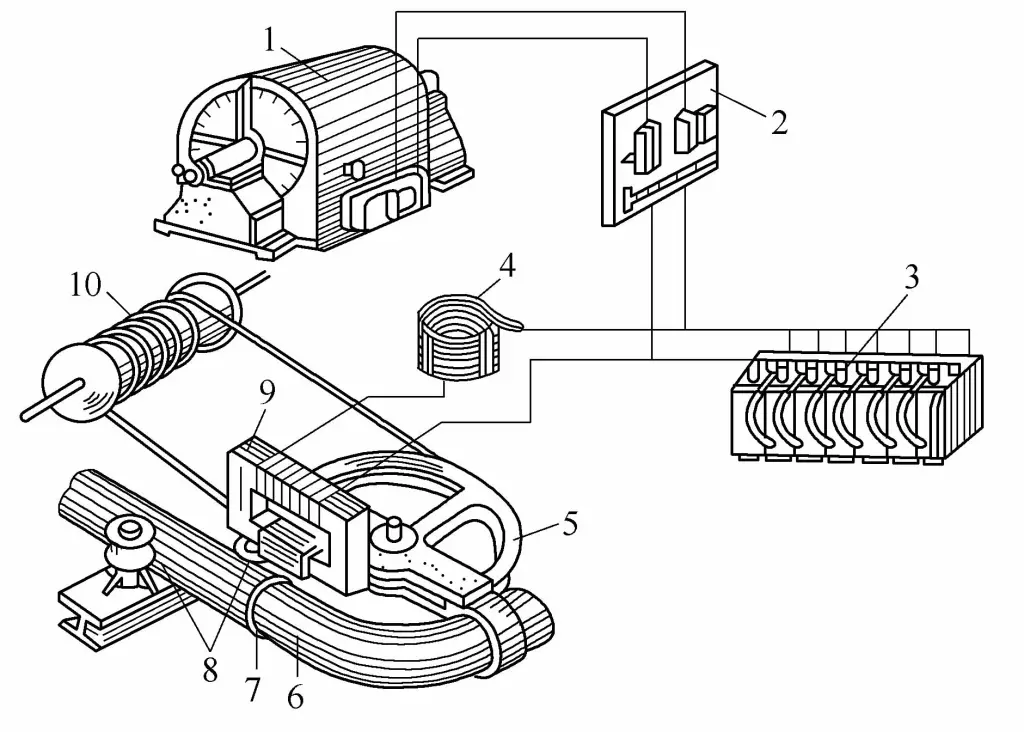
1 - Генератор средней частоты
2-коммутатор
3-Батарейный блок
4-Реактор
5-вентиляторный диск
6-трубная заготовка
7-Индукционная катушка
8-направляющее колесо
9-Трансформатор
10-Электрическая лебедка
При гибке труб с помощью среднечастотного трубогиба с индукционным нагревом зазор между индукционной катушкой и внутренней стороной сгиба должен быть меньше, а снаружи - больше, чтобы обеспечить эффект нагрева внутренней стенки трубы. Ширина индукционного нагрева зависит от мощности средней частоты, ширины индукционной катушки и относительного положения индукционной катушки по отношению к заготовке, обычно около 10~20 мм.
Технические параметры гибки стальной трубы 20# на среднечастотном трубогибе с индукционным нагревом приведены в таблице 4-16, для справки.
Таблица 4-16 Технические параметры среднечастотного изгиба для стальной трубы 20#
(Наружный диаметр D/мм) x (Толщина стенки t/мм) | Потребляемая мощность/кВт | Скорость изгиба / (мм-с -1 ) | Температура нагрева/℃ |
Φ83×14 | 60~70 | 1~1.2 | 900~950 |
Φ102×16 | 70~75 | 0.9~1.1 | 900~950 |
Φ102×22 | 70~75 | 0.8~1 | 900~950 |
Φ127×19 | 70~75 | 0.8~1 | 900~950 |
Φ127×28 | 75~80 | 0.6~0.7 | 950 ~1000 |
Φ159×28 | 80~90 | 0.5~0.6 | 950~1000 |
Φ180×28 | 90~100 | 0.4~0.5 | 1000~1050 |
Трубы из нержавеющей стали могут быть согнуты с помощью индукционного нагревателя средней частоты. Особое внимание следует уделить температуре нагрева, чтобы она была не ниже 900℃. Это связано с тем, что нержавеющая сталь имеет тенденцию страдать от межкристаллитной коррозии при длительном нагреве в диапазоне температур 500~850℃, поэтому трубы из нержавеющей стали могут быть согнуты только холодным или горячим способом при температуре 1100~1200℃. Технические параметры гибки труб из нержавеющей стали с помощью среднечастотного гибочного станка с индукционным нагревом приведены в таблице 4-17.
Таблица 4-17 Технические параметры среднечастотной гибки для труб из нержавеющей стали
(Наружный диаметр D/мм) x (Толщина стенки t/мм) | Потребляемая мощность/кВт | Скорость изгиба / (мм-с -1 ) | Температура нагрева/℃ |
Φ89 x4.5 | 30~40 | 1.8~2 | 1100~1150 |
Φ108 x5.5 | 30~40 | 1.2~1.4 | 1100~1150 |
Φ133×6 | 40~50 | 1~1.2 | 1100~1150 |
Φ159 x6 | 50~60 | 0.8~1 | 1100~1150 |
Φ168×13 | 70~80 | 0.8~1 | 1130~1180 |
Φ102×17 | 80~90 | 0.6~0.8 | 1130~1180 |
2. Гибочный станок
Принцип работы валковая гибочная машина показана на рисунке 4-46. Трубная заготовка помещается между тремя роликами, и труба может быть согнута в трубные фитинги различной кривизны путем регулировки взаимного положения трех роликов. Вальцегибочный станок показан на рисунке 4-47.
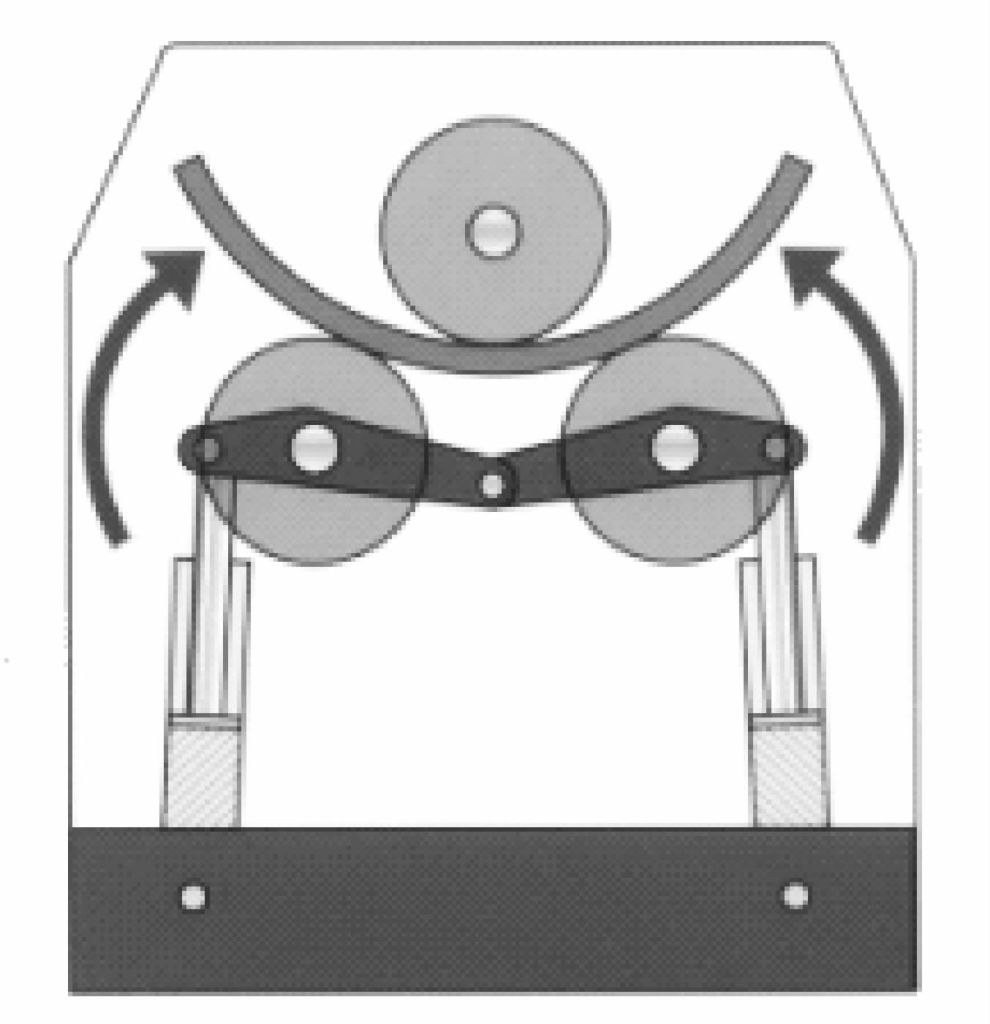
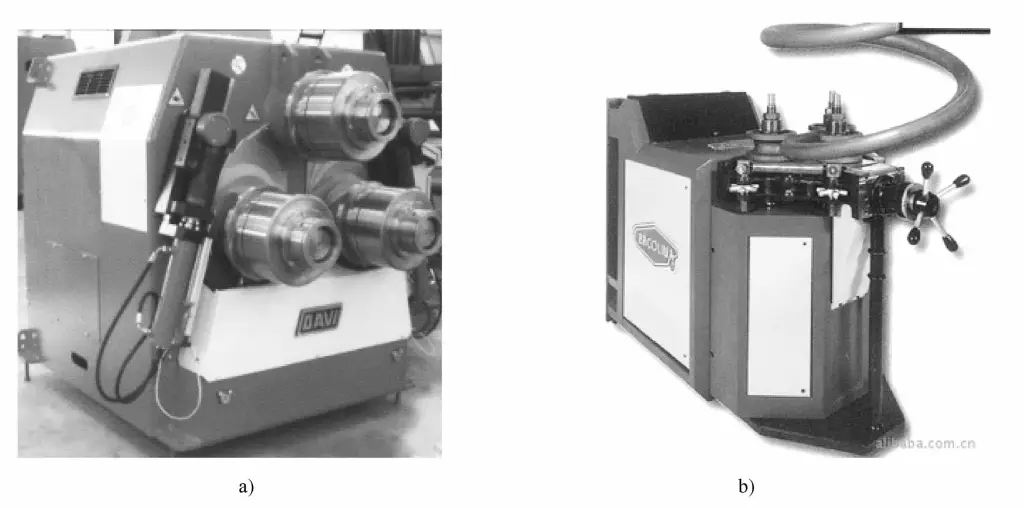
a) Горизонтальный валковый гибочный станок
б) Вертикальная гибочная машина
Валковый гибочный станок в основном используется для гибки металлических профилей или материалов специальной формы, таких как железо, медь, алюминий и т.д. Он широко используется на мебельных фабриках для гибки мебели по круговой дуге или в художественной обработке железа, на фабриках металлических дверей и окон для изготовления железных дверей и окон по круговой дуге или дверей и окон из алюминиевого сплава и т.д. Использование технологии ЧПУ для гибки труб делает операцию гибки профилей более удобной и простой, а также имеет преимущества высокой точности гибки, а согнутые профили имеют меньшую деформацию и не имеют царапин на поверхности.
Широко используемый трубогибочный станок - это трехкоординатное оборудование с ЧПУ. Вальцегибочный станок может получать готовые изделия большого радиуса за счет многократной гибки. Станки общего назначения могут адаптироваться к требованиям обработки некоторых форм и материалов. Полностью гидравлический тип оборудования управляется с помощью восьми программируемых программ, и каждая программа может записывать бесконечно много вариаций.
Все ручные блоки управления специально сконфигурированы для двухскоростных центральных колес. Положение центрального колеса отображается в цифровом виде. Скорость гибки может достигать 20 футов/мин (около 6,10 м/мин). Все модели станков могут работать в горизонтальном и вертикальном положении. Резьбовой приводной вал обеспечивает точную настройку даже при обработке без зазоров.
Соосная конструкция редуктора уменьшает масляную ванну и обеспечивает высокую эффективность передачи мощности. Приводной вал из закаленной легированной стали оснащен коническими роликовыми подшипниками. Используется низковольтный контроллер. Гидравлический цилиндр центрального ролика с улучшенными характеристиками расположен внутри рамы. Ручная панель управления включает в себя педаль управления. Регулируемая система роликов облегчает коррекцию ситуаций вращения. Отсек для хранения инструментов встроен в нижнюю часть машины.
Особенности гибочного станка следующие:
1) Он может использоваться для гибки больших дуг и спиральных труб, обычно с радиусом гиба более 6 раз больше диаметра трубы.
2) Компактная структура, высокая надежность, нелегко соскользнуть, улучшая качество и целесообразность использования трубопроводной арматуры.
3) Плавная передача, используя комбинацию трехроликовых форм, в сочетании с регулировкой и сжатием, можно получить круги, дуги или спирали различной кривизны.
4) Изменяя тип паза пресс-формы, можно обрабатывать различные металлические профили, такие как угловая сталь, плоская сталь, круглые трубы и другие профили специальной формы.
5) Гибка профилей большого радиуса позволяет избежать недостатков, связанных с изготовлением сверхбольших гибочных форм, и выполнять работы, которые не под силу одноголовочным и двухголовочным гибочным станкам.
3. Нажмите
Пресс в основном используется для гибки пресс-форм.
4. 3D гибочный станок
Гибочный станок 3D в основном используется для обработки пластиковых форм дверных коробок автомобилей, оконных рам, водопроводных каналов и других пространственно изогнутых деталей. Это автоматизированное оборудование с электрической и гидравлической передачей. На рисунке 4-48 показан 3D-гибочный станок, произведенный на одном из заводов.
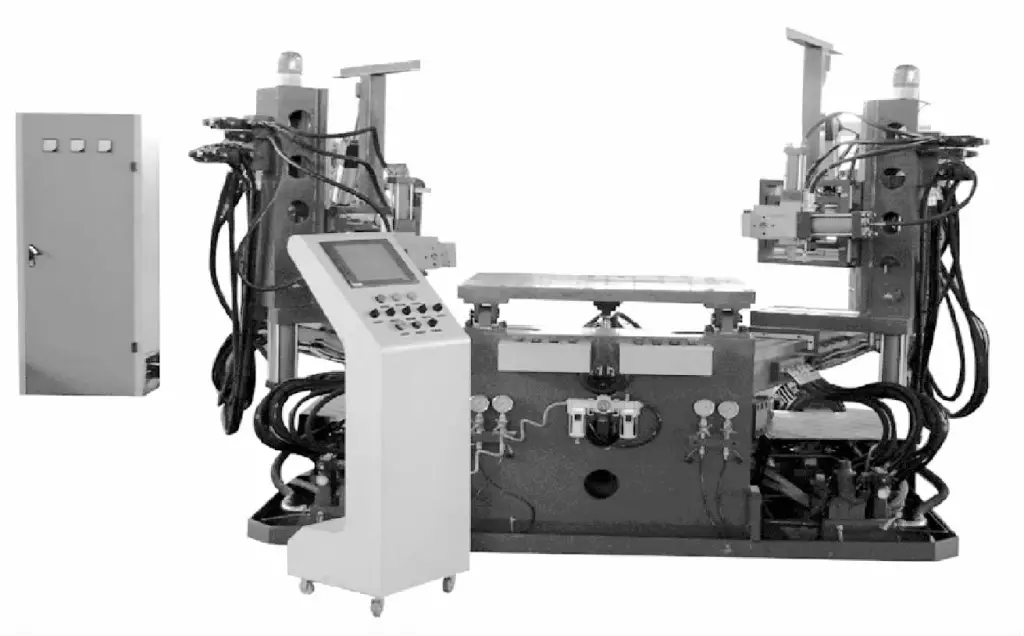
Принцип работы: Это оборудование в основном опирается на гидравлические цилиндры для привода различных подвижных компонентов для достижения обработки и формирования заготовки. Оборудование разделено на 4 гидравлические системы, каждая из которых имеет диапазон давления 0~150 бар (регулируемый), что позволяет превышать давление в системе на 20%.
Подъемная сила левой и правой рук контролируется двумя гидравлическими насосами производительностью 30 л/мин соответственно, с использованием пропорционального перепускного клапана для контроля подъемного момента. Отклонение заданного и фактического давления составляет около 3%, а коэффициент стабильности повторяемости (20°C-40) - 1%. ⊙ ( ⊙ показывает погрешность 1% при температуре 20°C и влажности 40%). Гибочные гидроцилиндры и зажимные, вращающиеся гидроцилиндры на левом и правом рычагах управляются двумя гидравлическими насосами производительностью 80 л/мин.
Подъем оси Z и рабочего стола контролируется двумя гидравлическими насосами производительностью 52 л/мин и 30 л/мин соответственно. Можно выбрать, включать ли мотор гидравлического насоса в зависимости от дуговых требований обрабатываемого продукта, что способствует лучшей экономии энергии.
Кроме того, оборудование оснащено 8 независимыми запасными гидравлическими интерфейсами и 4 независимыми запасными пневматическими интерфейсами. Все запасные интерфейсы подключены к гидравлической, электрической и другим системам всей машины и могут быть настроены в соответствии с требованиями различных пресс-форм.
Оборудование довольно простое с точки зрения замены пресс-форм. Как правило, смена пары обычных неповрежденных пресс-форм занимает у оператора около 2 часов (время может меняться в зависимости от простоты пресс-формы). Оборудование может хранить информацию о нескольких наборах пресс-форм, и после замены пресс-форм оно может оперативно вызывать производственные данные этого набора пресс-форм для производства, эффективно сокращая время отладки и уменьшая цикл обработки.
Технические параметры гибочного станка 3D следующие:
1) Угол поворота поверхности рабочего стола (-13°~+20°); центральный угол поворота левого и правого поворотных рычагов составляет 90° каждый.
2) Расстояние между левым и правым патронами L=0~3500 мм регулируется и может выполнять растягивающее движение на 600 мм.
3) Высота центра патрона H=1280~1880 мм, может перемещаться вверх и вниз на 600 мм по линейному рельсу.
4) Высота рабочего стола H 1 =1200 мм.
5) Гидравлическая сила 20MPa, мощность двигателя 15kW×3.
II. Классификация вспомогательного оборудования
Вспомогательное оборудование для труб фитинг Формирование включает в себя оборудование для резки труб, обычно используется фрезерное оборудование, оборудование для обработки отверстий, оборудование для резки пилой, оборудование для плазменной резки и лазерное оборудование для резки труб.
1. Оборудование для фрезерной обработки
Фрезерная обработка в основном используется для обработки относительно простых неровных формообразующих поверхностей между накладками конструкционных трубных фитингов. Оборудование для обработки, используемое на месте, в основном включает фрезерные станки, токарные станки, фрезерные станки с ЧПУ, токарные станки и т. д. Горизонтальный токарный станок показан на рисунке 4-49, а вертикальный фрезерный станок - на рисунке 4-50.
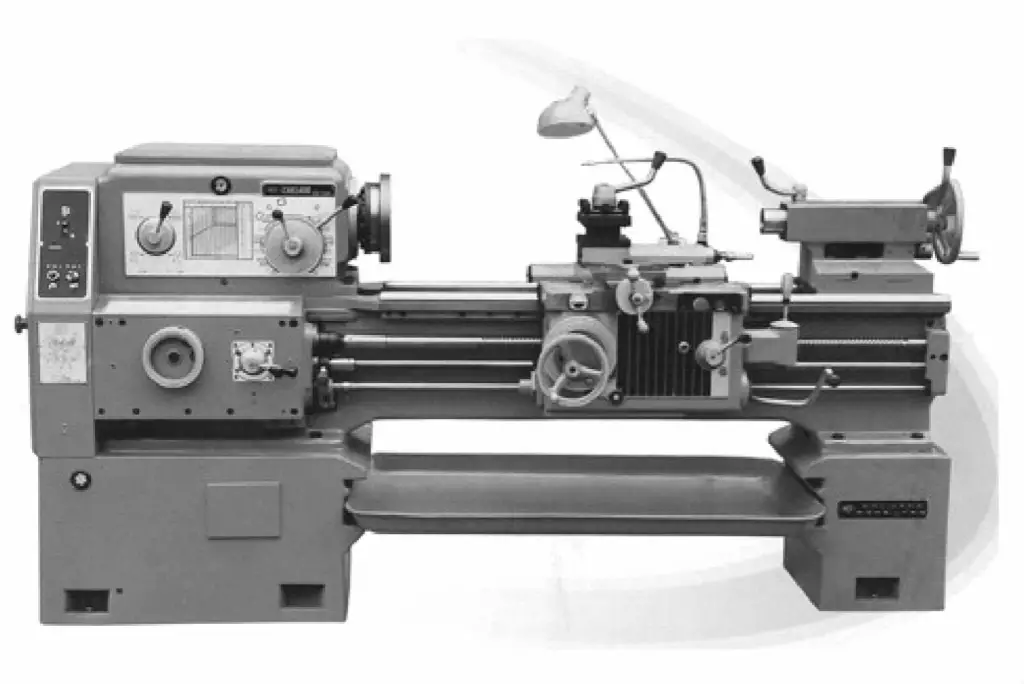
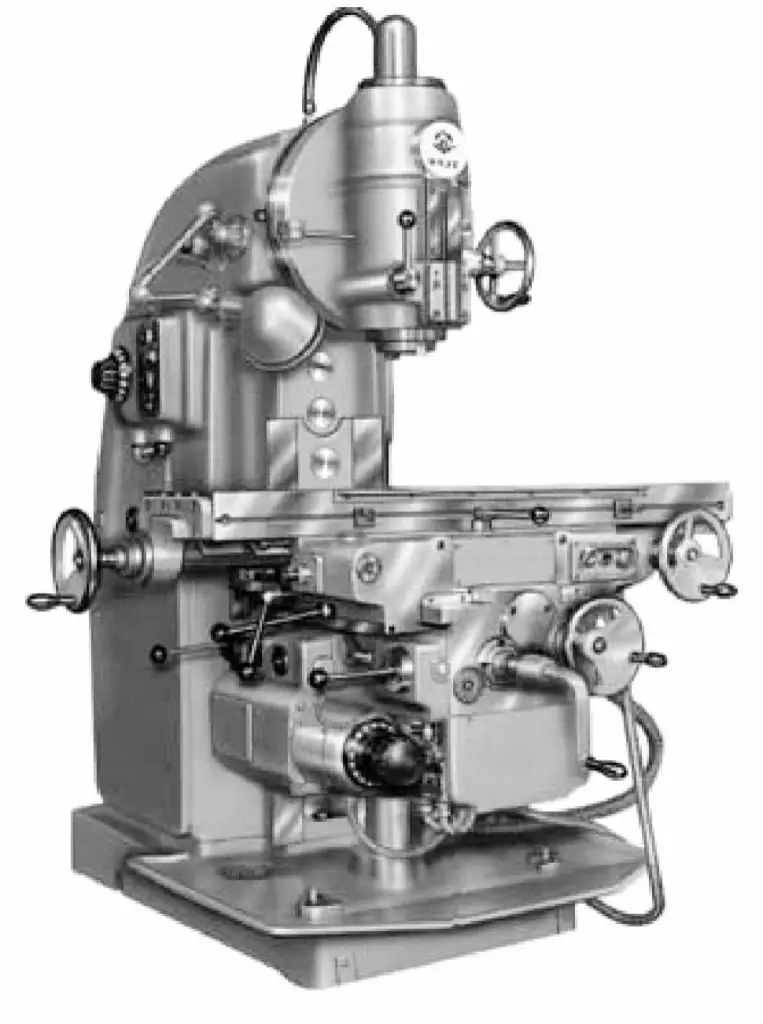
2. Оборудование для обработки отверстий
Оборудование для обработки отверстий в основном используется для обработки отверстий под покраску, монтажных отверстий, отверстий под сварку, технологических отверстий и т.д. на трубопроводной арматуре. Технологическое оборудование, используемое в производстве, включает в себя радиально-сверлильные станки, штамповочные станки и т. д. Радиально-сверлильный станок показан на рисунке 4-51, а пресс - на рисунке 4-52.
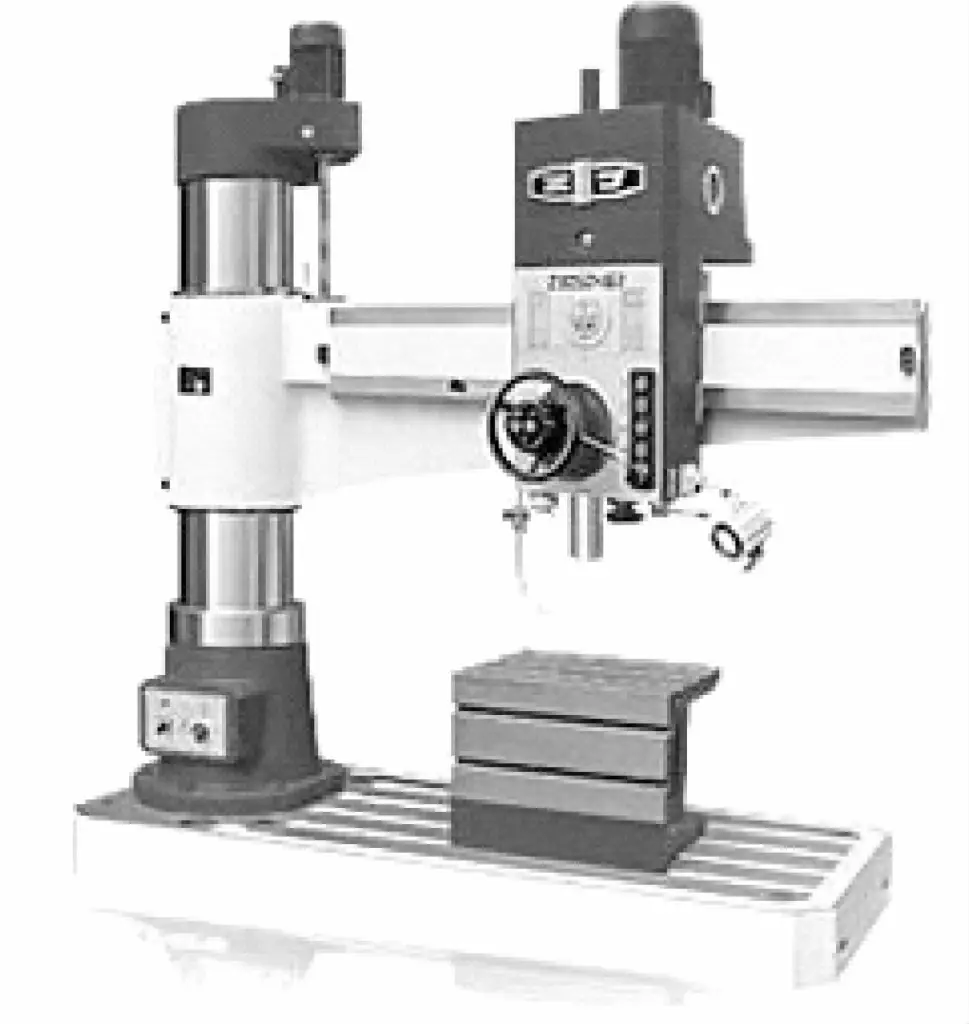
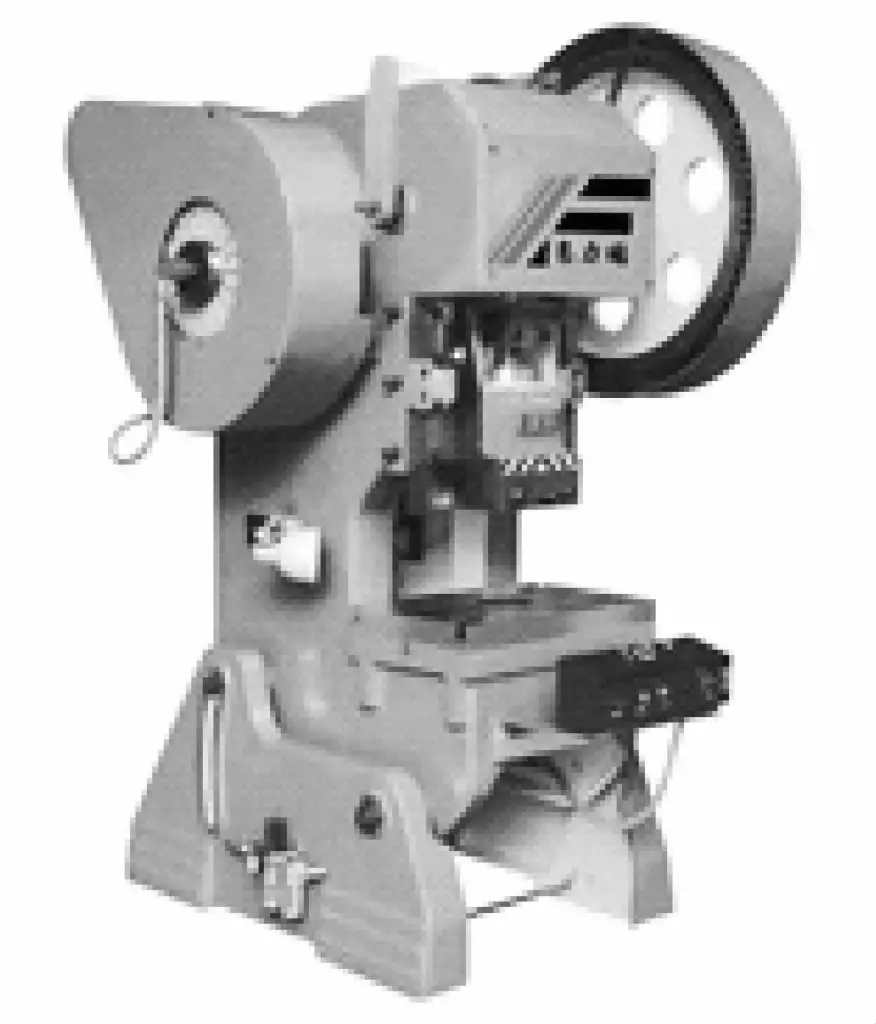
3. Оборудование для распиловки
Пильное оборудование в основном используется для распиловки заготовок перед формовкой фитингов и излишков материала после процесса гибки. В производстве используются дисковые пилы по металлу (рис. 4-53), ленточные пилы (рис. 4-54) и т.д.
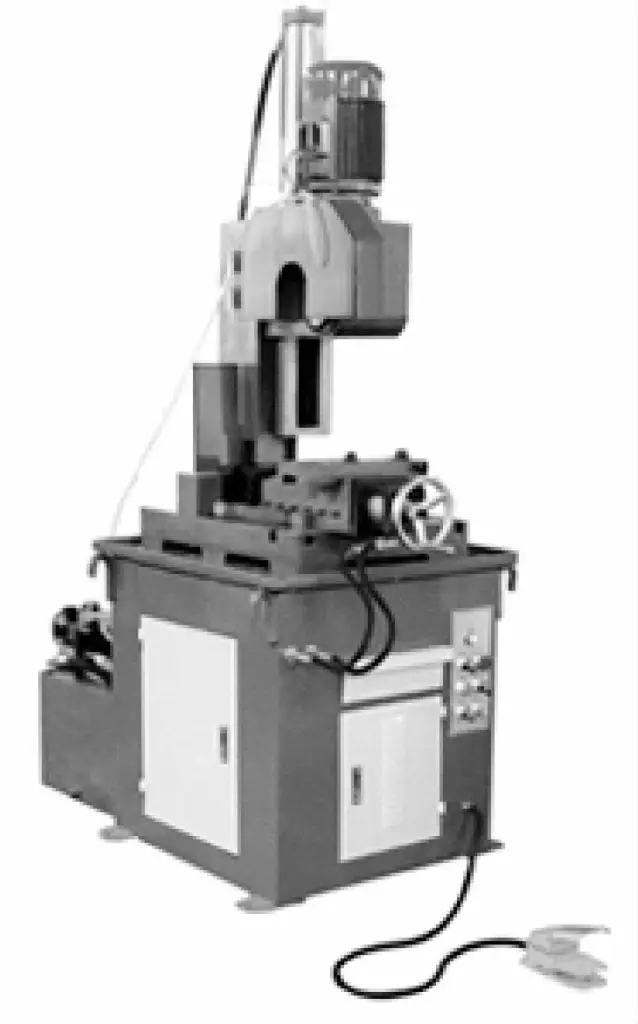
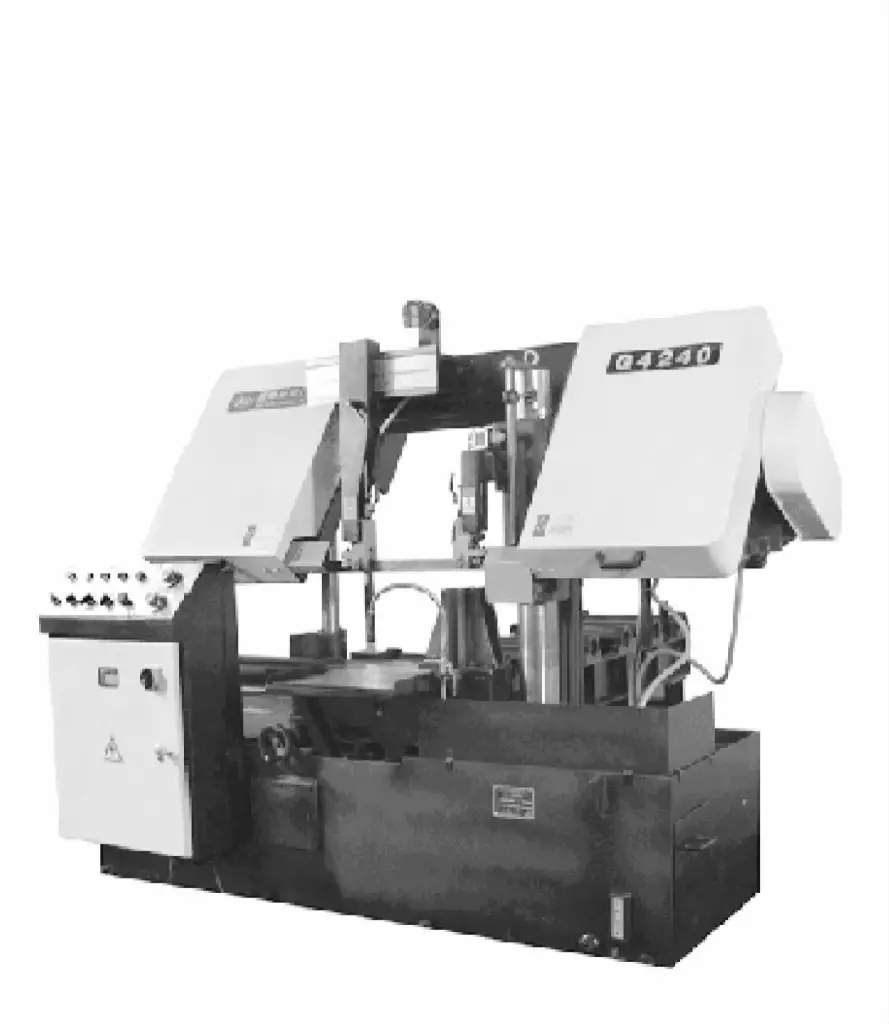
4. Оборудование для плазменной резки
Плазменная резка в основном используется для обработки более сложных поверхностей благодаря удобству и простоте работы по сравнению с фрезерованием. Оборудование для обработки резанием, используемое на объекте, включает в себя ручные машины плазменной резки. Однако в будущих тенденциях развития он будет вытеснен механической обработкой резанием.
5. Оборудование для лазерной резки труб
Оборудование для лазерной резки труб подразделяется на оборудование для резки металлических труб лазерная резка станки для резки труб и станки для лазерной резки как металлических труб, так и пластин. В промышленности обычно используются нестандартные станок лазерной резки Модели со станками лазерной резки металла плюс устройства вращения трубы, которые больше подходят для обработки резанием круглых труб, пересекающихся линий.
В настоящее время он постепенно применяется для резки квадратных труб, например, лазерные станки для резки труб производства Amada. Существуют также станки, в которых позиционирование частей трубы осуществляется за счет вращательного и линейного движения режущей лазерной головки и позиционирования роботов для загрузки и выгрузки, например, станки для лазерной резки труб производства BLM.
Станок для лазерной резки трубок LT823D производства итальянской компании BLM Group (см. рис. 4-55) - это технически совершенный станок для лазерной резки трубок Adige.

Изысканный многоосевой (включая поворотную головку) станок для лазерной резки труб с полным ЧПУ имеет конкурентное преимущество на рынке, превосходя традиционные методы обработки труб. На рисунке 4-56 показан процесс резки трубных деталей с использованием этого оборудования, а на рисунке 4-57 - состав оборудования LT823D.
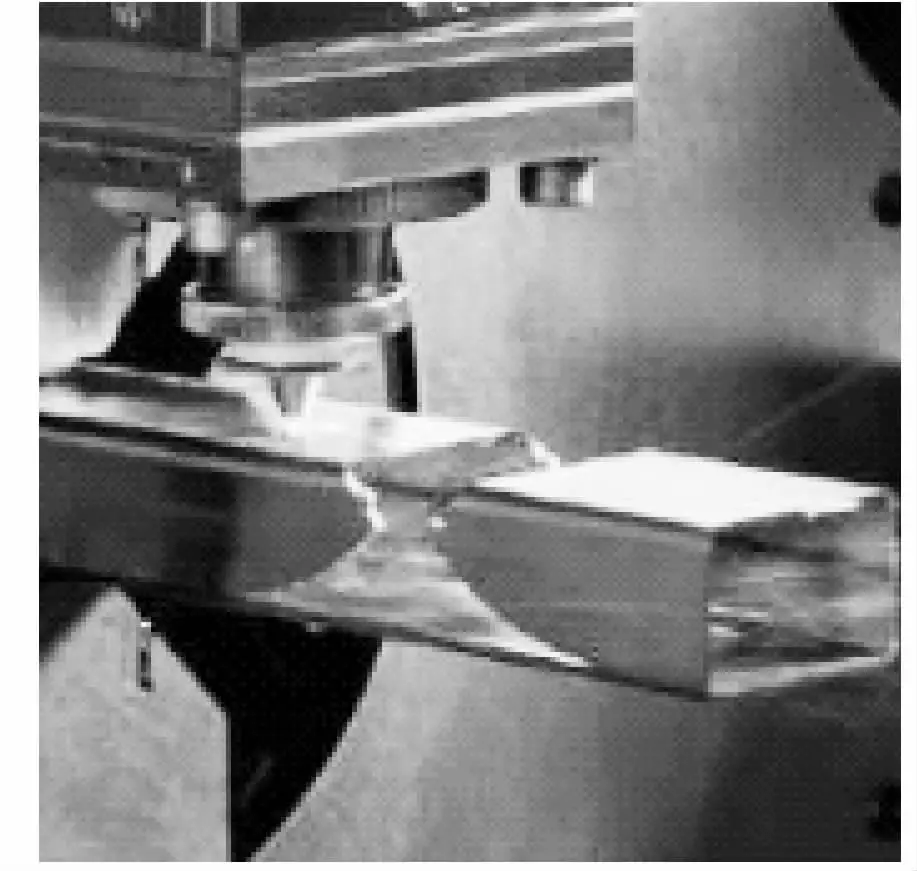
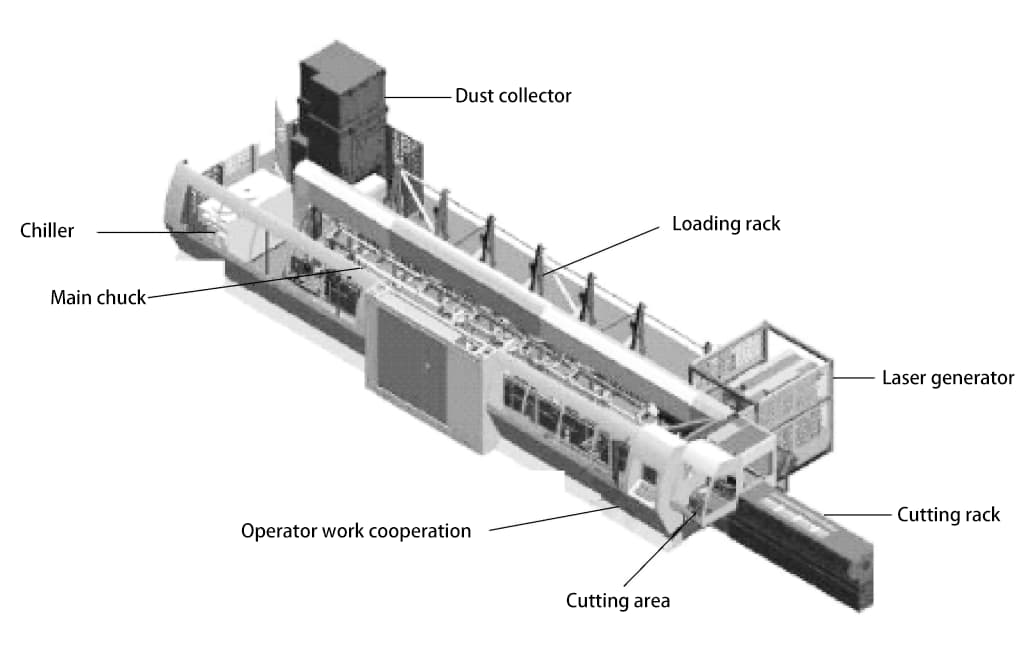
Станок для резки LT823D объединяет различные процессы и процедуры традиционной обработки труб (такие как определение размеров трубы, сверление, фрезерование, шлифование и штамповка) в один, используя однокомпонентную лазерную резку для замены традиционных процедур обработки. Это сокращает прямые и косвенные трудозатраты; в то же время лазерная резка труб повышает качество и точность продукции, а также сокращает традиционные приспособления для обработки и время настройки перед обработкой.
Возможности обработки оборудования: Оно может обрабатывать круглые трубы, квадратные трубы, прямоугольные трубы и другие трубы специальной формы, включая выборочно угловое железо, двутавровые балки и плоское железо. Под действием подходящих вспомогательных газов для лазерной резки, оборудование также может резать и обрабатывать трубы из углеродистой стали, легированной стали, нержавеющей стали и алюминиевых сплавов.
Универсально применим для сельскохозяйственной и промышленной продукции, такой как оснастка, изготовление труб, обработка труб, медицинское оборудование, строительное оборудование и т.д., с эффектом резки, показанным на рисунке 4-58.
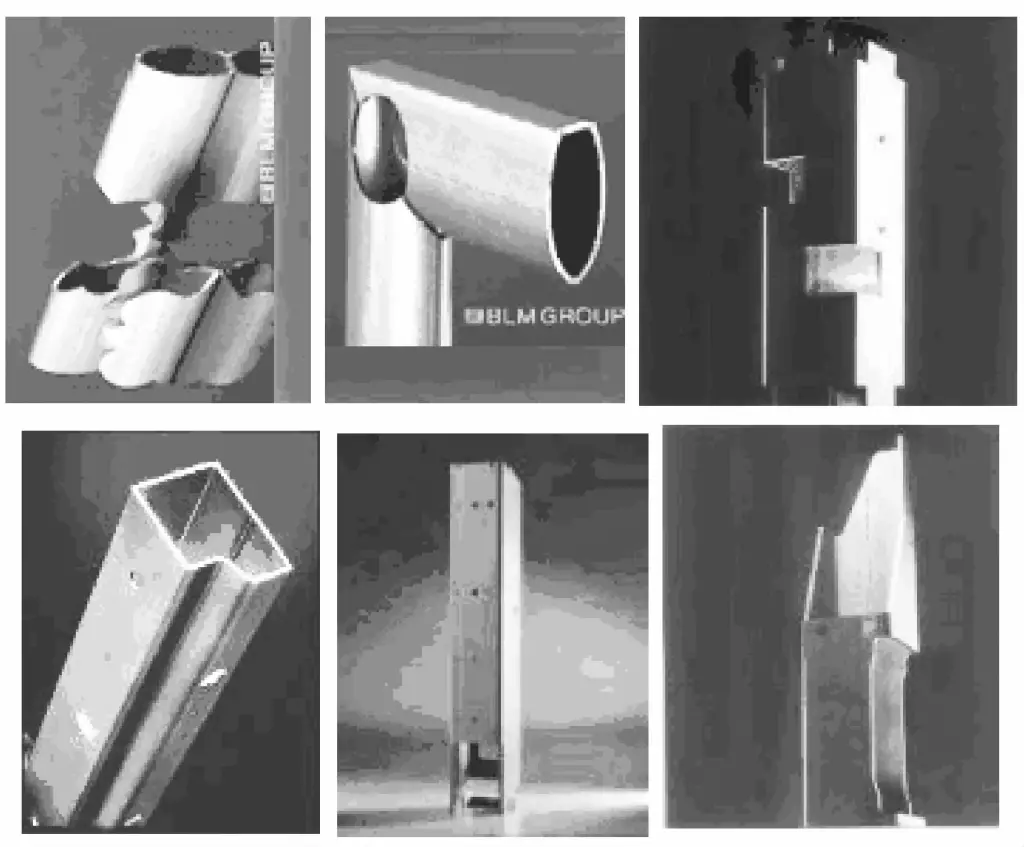
Инструментальное приспособление станка для лазерной резки труб LT823D показано на рис. 4-59a, а на рис. 4-59b приведен пример процесса резки для гибки труб.
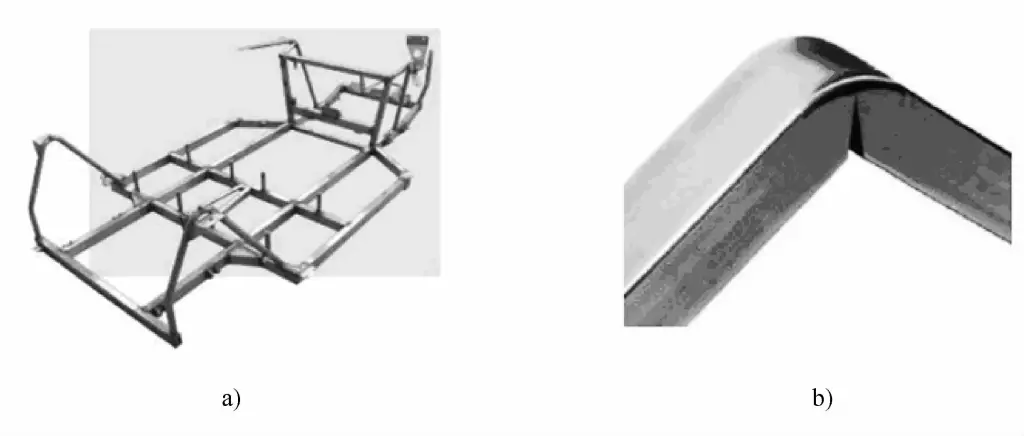
a) Инструментальные приспособления
b) Процесс резки для гибки труб
Поскольку лазерная резка требует высокой точности обработки перед резкой трубы, компания Yituo в основном использует поверхностную обработку формованных трубных фитингов, поэтому принятая схема резки - лазерная резка с роботом в сочетании с режущим рабочим столом, который больше подходит для резки труб и для выемки труб и т.д.
Станок для лазерной резки труб разработан и изготовлен для нужд нефтепроводного оборудования, промышленной выемки металлических труб и обработки специальных форм на стенках труб. Станок лазерной резки металлических труб имеет следующие преимущества:
1) Высококачественный срез, минимальная деформация, гладкий и красивый внешний вид.
2) Быстро скорость резкиВысокая эффективность, низкая стоимость, безопасная эксплуатация и стабильная работа.
3) Используются импортные серводвигатели и направляющие механизмы передачи для высокой точности резки.
4) Используется профессиональное программное обеспечение, позволяющее гибко проектировать и обрабатывать различные фигуры или текст, с простым и удобным управлением.
5) Лазерный луч легко поддается временному или пространственному разделению, что позволяет осуществлять многолучевую обработку или последовательную обработку на нескольких станциях.
6) Одно и то же оборудование может не только выполнять функции резки, но и лазерной сварки.