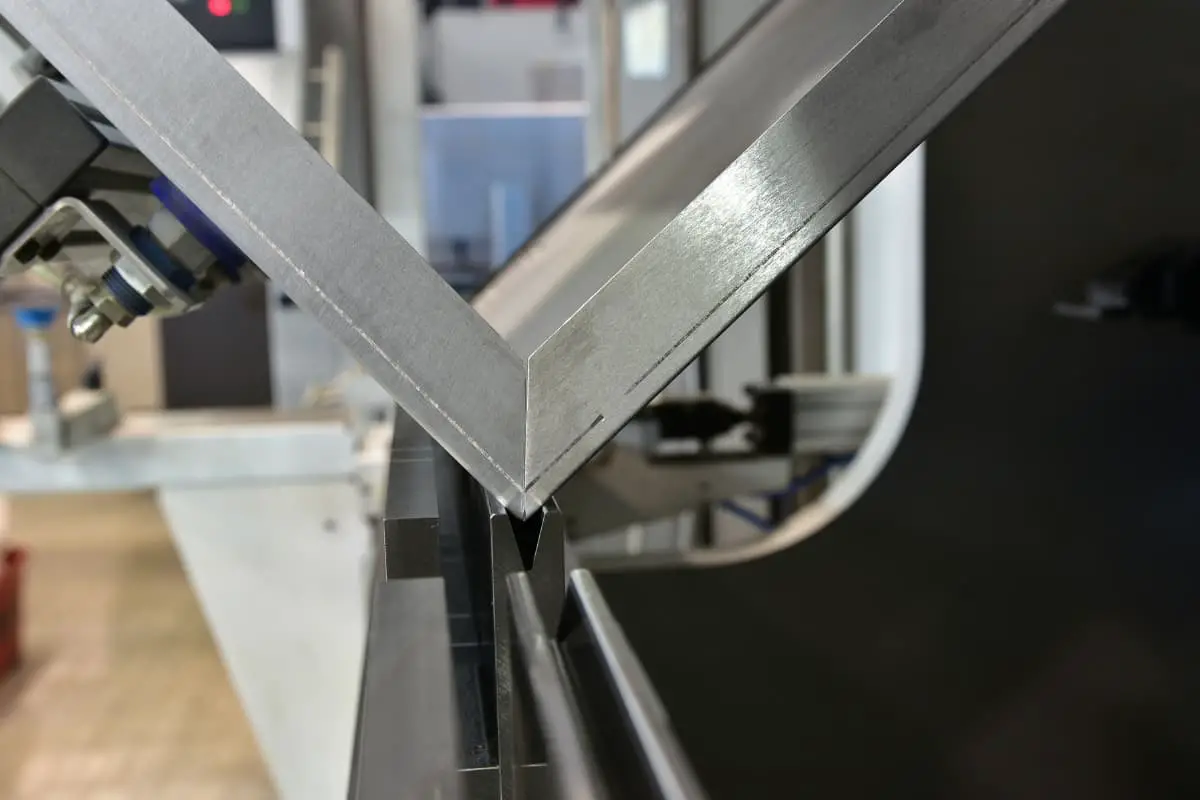
Malzemeleri belirli bir açıya, eğriliğe ve şekle bükme işlemine bükme denir. Bükme, malzeme şekillendirmede en yaygın yöntemlerden biridir ve metal yapı bileşenlerinin imalatında yaygın olarak kullanılır.
Bükme sac, çubuk, boru ve profil bükme olarak kategorize edilebilir. Farklı kesit şekilleri nedeniyle, malzemelerin iç gerilimleri bükme işlemi sırasında deformasyonu farklı şekilde etkiler ve farklı modeller ortaya çıkar.
Bükme Bileşenlerinin Türleri ve Malzemeleri
Hammaddelerin şekline bağlı olarak, bükme bileşenleri sac bükme olarak sınıflandırılabilir, tüp bükmeçubuk bükme ve profil bükme. Ayrıca, bükme işlemleri, kullanılan alet ve ekipmanlara göre, ortak bir pres makinesinde kalıplarla presleme ve özel bükme ekipmanlarında gerçekleştirilen bükme, rulo bükme, çekme bükme vb. olarak kategorize edilebilir.
Bükme bileşenleri için malzemeler öncelikle çelik plakalar, alüminyum alaşımlı plakalar ve haddelenmiş profillerdir.
Bükme Bileşenlerinin Üretim Süreci
Bükme Bileşenlerinin Deformasyon Karakteristikleri
(1) Minimum Bağıl Bükülme Yarıçapı
Bir levhayı bükerken göz önünde bulundurulması gereken konu, minimum bağıl bükülme yarıçapı (R/t).
Malzemenin minimum bükülme yarıçapı, malzemenin açılım ve bükme bileşeninin geri yaylanmasının tümü bağıl bükme yarıçapını içerir. Süreç analizi hesaplaması sırasında, bağıl eğilme yarıçapının minimum eğilme yarıçapından daha büyük olduğundan emin olmak gerekir.
(2) Bükme Geri Yaylanması
Bükme bileşeni preslemeden sonra dış kuvvetten serbest bırakıldığında, bükme sırasındaki elastik deformasyon nedeniyle, iş parçasının açısında, köşe yarıçapında ve yay uzunluğunda, dış kuvvet kalıptan çıkarılmadığında şekil ile tutarsız olan değişiklikler meydana gelir.
Bu olgu geri yaylanma olarak bilinir. Geri yaylanma sorununu göz önünde bulundurmak için, kalıbın ilgili boyutlarını bükme malzemesine göre ayarlamak gerekir.
(3) Geri Yaylanmayı Etkileyen Faktörler
Ana faktörler malzemenin mekanik özellikleri, göreceli bükülme yarıçapı ve şekli, kalıbın boyutları, boşluk ve bükülme düzeltme kuvvetidir.
1) Malzemenin mekanik özellikleri. Malzemenin akma noktası ne kadar yüksekse, elastik modülü ne kadar küçükse, geri yaylanma o kadar büyük olur.
2) Malzemenin bağıl bükülme yarıçapı R/t. R/t değeri ne kadar küçükse, geri yaylanma o kadar küçük olur.
3) Bükülmüş iş parçasının şekli. Genel olarak, bir kerede preslenen U şeklindeki bir iş parçasının geri yaylanması, V şeklindeki bir iş parçasınınkinden daha küçüktür.
4) Kalıbın boyutları. Zımbanın r yarıçapı sabit olduğunda, kalıbın açılma mesafesi arttıkça V şeklindeki bükme bileşeninin geri yaylanması azalır. U şeklindeki kalıbın açıklığı ne kadar derin olursa, geri yaylanma o kadar küçük olur.
5) Kalıp boşluğu. U şeklindeki bükme kalıbının zımbası ve kalıbı arasındaki boşluk ne kadar büyükse, geri yaylanma o kadar büyük olur.
6) Bükme düzeltme kuvveti. Düzeltme kuvvetinin artırılması geri yaylanma miktarını azaltabilir.
Sac Bükme
Sac bükmenin hesaplanması ve kalıp tasarımı ile ilgili olarak aşağıdaki hususların dikkate alınması gerekmektedir.
1) Bükme boşluğunun ilgili boyutları önce hesaplanır ve ardından test bükme ile belirlenir.
2) Bükme kalıbının zımba ve kalıbının boyutları, dış boyut işaretlemesi için farklı gereksinimlere göre dikkate alınır.
3) Bükme bileşeninde bir delik olduğunda, delik belirli bir mesafeye kadar deformasyon bölgesinin dışında tutulmalıdır, aksi takdirde bükme deliğin deformasyonuna neden olur.
Deliğin kenarından r bükülme yarıçapının merkezine kadar olan L mesafesi plakanın kalınlığı ile ilgilidir (bkz. Şekil 2-17). Plaka kalınlığı t 2 mm'den az olduğunda, L mesafesi 1,5t'den büyük olmalıdır; plaka kalınlığı t 2 mm'den fazla olduğunda, L mesafesi 2t'den büyük olmalıdır. L mesafesi çok küçükse, bükme işleminden sonra delik açmak daha iyidir.
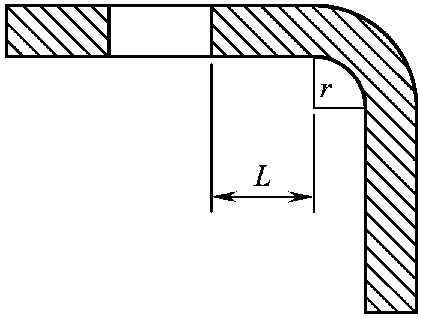
4) Bazı karmaşık şekilli iş parçaları için büküm sayısı gerçek duruma göre belirlenmelidir.
Şekil 2-18'de gösterildiği gibi, karmaşık şekilli bükme bileşenlerinin bir sınıfının tamamlanması için özel kalıplar gerekir ve bükme sayısı gerçek duruma göre belirlenmelidir.

Şekil 2-18a'da gösterilen parça soğuk presleme altında iyi şekillenmez, bu da sıcak preslemeyi daha uygun bir seçim haline getirir. İlgili kalıp ve şekillendirme yöntemi Şekil 2-19'da gösterilmiştir.
Şekil 2-18b'de gösterilen parça sıcak presleme yoluyla daha iyi şekillendirilir, ancak bu yaklaşım verimsizdir, enerji tüketir ve gerilme yaralanmalarına neden olmaya eğilimlidir. İki aşamalı bir soğuk presleme yönteminin kullanılması tercih edilir ve ilgili kalıp ve bükme yöntemi Şekil 2-20'de gösterilmiştir.
Şekil 2-18c'de gösterilen parça asimetrik bir kesite sahiptir, bu da presleme sırasında her iki tarafta düzensiz ve dengesiz malzeme akışına neden olur. Kalıba, parçanın kalıptan çıkarılmasını da kolaylaştıran bir tepeleme cihazı eklenmesi tavsiye edilir. İlgili kalıp ve presle bükme yöntemi Şekil 2-21'de gösterilmektedir.
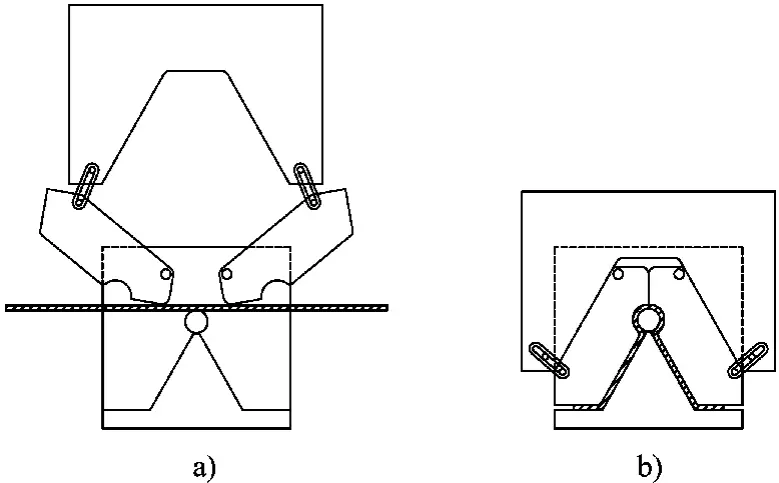
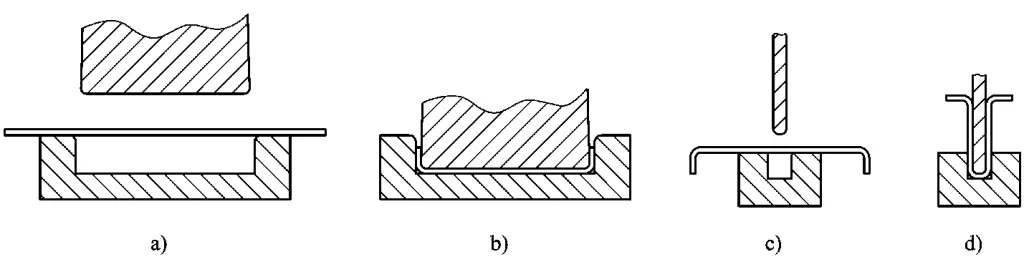
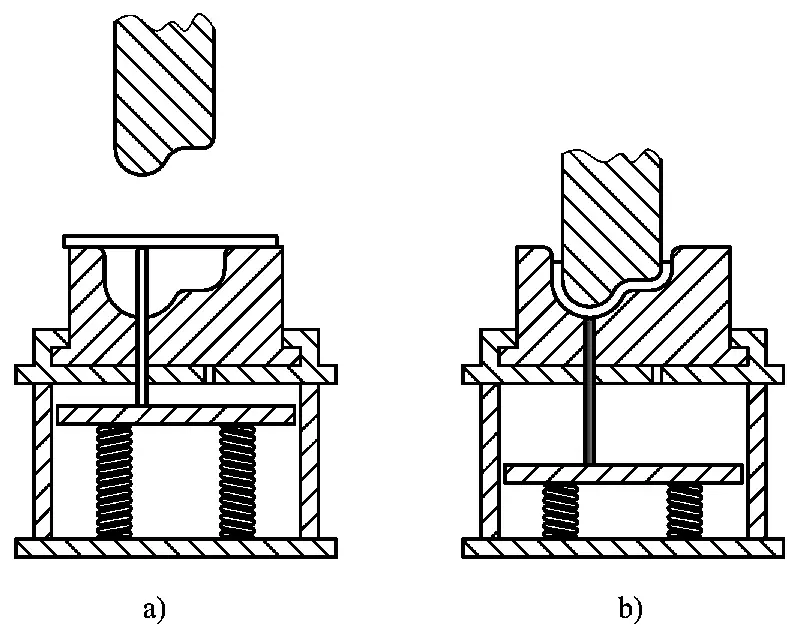
Şekil 2-18e ve 2-18f'de gösterilen parçaların her ikisinde de bir uçta genel bir kalıp kullanılarak gerçekleştirilemeyen ileri ve geri bükümler vardır. İki aşamalı bir pres bükme yöntemi tercih edilir. Bir uçtaki ileri ve geri bükümleri tamamladıktan sonra (Şekil 2-22), sonraki bükümle devam edin.
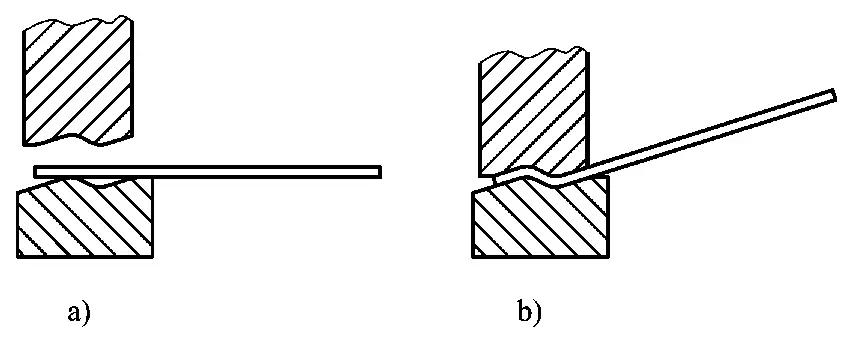
Şekil 2-18e'de gösterilen parça için ilk pres bükümü tamamlandıktan sonra, ikinci pres bükümü için V şeklinde bir kalıp kullanılır. Şekil 2-18f'de gösterilen parçanın sonraki pres bükümünü tamamlamak için Şekil 2-18b'de gösterilen parçanın ikinci pres bükümüne benzer bir yöntem benimsenmelidir.
Profil Bükme
Şekil 2-23 ve 2-24 lokomotiflerde yaygın olarak kullanılan tipik profil yeniden bükme bileşenlerini göstermektedir.
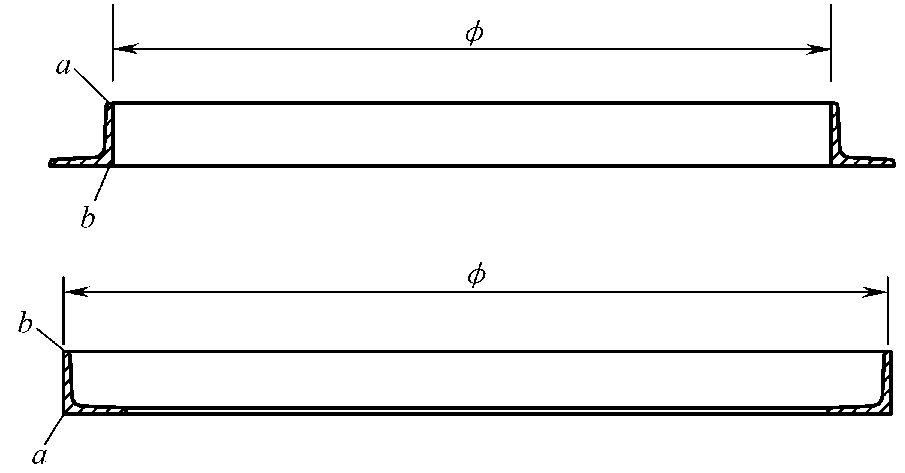
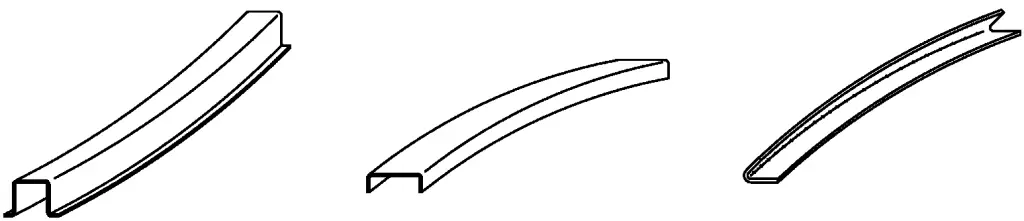
(1) Profil Bükme Sırasında Kanat Yüzeyinde Geri Yaylanma
Profil bükme profilin kesit şekli ve simetrisi nedeniyle sac bükmeden farklıdır. Genel olarak, profilin daha güçlü sertliği nedeniyle, profilin bükülme geri yaylanması sacınkinden daha azdır. Bununla birlikte, bazı profillerin asimetrik kesitleri vardır, bu da bükme sırasında tutarsız kanat yüzeyi geri yaylanmalarına neden olarak malzeme kararsızlığına yol açar ve bükülmüş deformasyonla sonuçlanır.
Şekil 2-23'te gösterilen açılı çelik bükme bileşeni asimetrik geri esnemenin tipik bir örneğidir. Bükme sırasında, kanat yüzeyindeki 'a' noktasındaki geri yaylanma en büyükken, 'b' noktasındaki geri yaylanma daha küçüktür ve açılı çelik bükme bileşeninin spiral bükülmeye maruz kalmasına neden olur. Açılı çelik bükme kalıbı tasarlanırken, geri esnemedeki bu tutarsızlık dikkate alınmalıdır.
Şekil 2-24'te gösterilen profil bükme bileşeni, kanat yüzeyi geri yaylanmasının tutarlı olma eğiliminde olduğu ve profil bükme bileşeninin herhangi bir bükülme sergilemediği tipik bir simetrik geri yaylanma örneğidir.
Profilin kanat yüzeyinin geri yaylanma üzerinde bir etkisi vardır, ancak bu etkinin ne kadar önemli olduğu şu anda kesin bir sonuçtan yoksundur.
(2) Profil Bükme Kalıbı Tasarımı için Ampirik Formül ve Katsayı Değerleri
Profil bükme uygulamasında, profil bükme kalıbı tasarımı için ampirik bir formül ve katsayı değerleri referansınız için özetlenmiştir (bkz. Şekil 2-25 ve Tablo 2-1).
Dışbükey kalıp yarıçapı için hesaplama formülü şöyledir:
Nerede?
- Riçbükey - dışbükey kalıp yayının yarıçapı;
- R - bükülmüş bileşenin iç yay yarıçapı;
- K - malzemenin elastik modül katsayısı;
- A - profil kanat yüzeyinin katsayısı;
- H - profil kanat yüzeyinin boyutu.
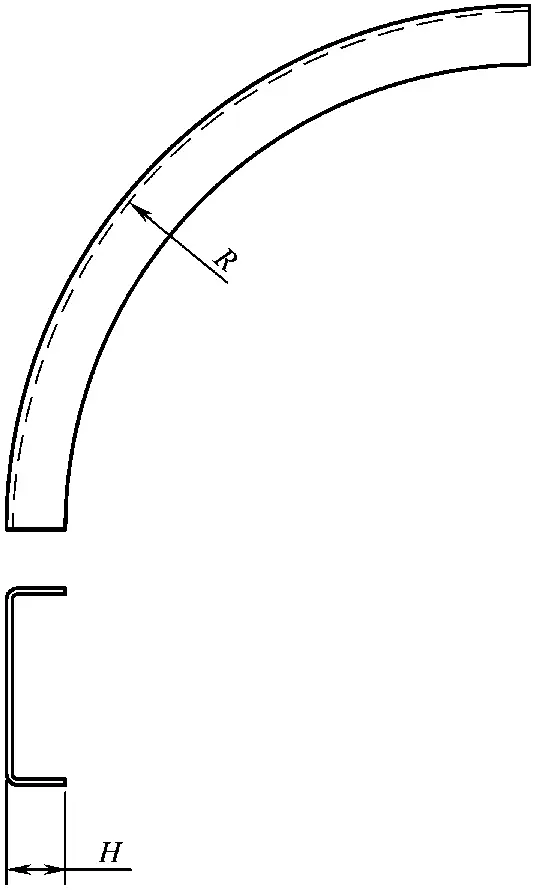
Tablo 2-1: Bükülmüş Kanal Çeliği için Geri Tepme Değeri A
Hayır. | R/H Değeri | Bir Değer | Hayır. | Hayır. | Bir Değer | Hayır. | R/H Değeri | Bir Değer |
1 | 5 | 0. 2 | 7 | 11 | 0. 45 | 13 | 17 ~ 23 | 0. 68 |
2 | 6 | 0. 24 | 8 | 12 | 0. 49 | 14 | 24 ~ 38 | 0. 70 |
3 | 7 | 0. 28 | 9 | 13 | 0. 53 | 15 | 39 ~ 57 | 0. 72 |
4 | 8 | 0. 34 | 10 | 14 | 0. 57 | 16 | 58 ~ 65 | 0. 76 |
5 | 9 | 0. 39 | 11 | 15 | 0. 61 | 17 | 66 ~ 76 | 0. 86 |
6 | 10 | 0. 42 | 12 | 16 | 0. 65 | 18 | >88 | 1. 00 |
(3) Kanal Çeliği Bükme Sırasında Büküm Kontrolü
Kanal çeliği için bükme kalıbı tasarlanırken, bükme sırasında kanat yüzeyinin potansiyel dengesizliği ve bükülmesi göz önünde bulundurulmalı ve uygun önlemler alınmalıdır. Burada, referans olarak iki kalıp kontrol yöntemi tanıtılmaktadır.
Birinci Yöntem: Basınçlı ekipmanın kendisinde hem dikey hem de yatay hidrolik silindirler olduğunda, dikey kuvvet bükme için kullanılır ve yatay kuvvet bükülmeyi bastırmak için kullanılır. Kalıbın yapısı Şekil 2-26'da gösterilmektedir. Bu kalıbın üretimi basittir, kullanımı uygundur ve iş parçasının bükme sırasında kalıptan çıkarılması kolaydır.

İkinci Yöntem: Basınçlı ekipman sadece dikey bir hidrolik silindire sahip olduğunda, Şekil 2-27'de gösterilen kalıp yapısı kullanılabilir.
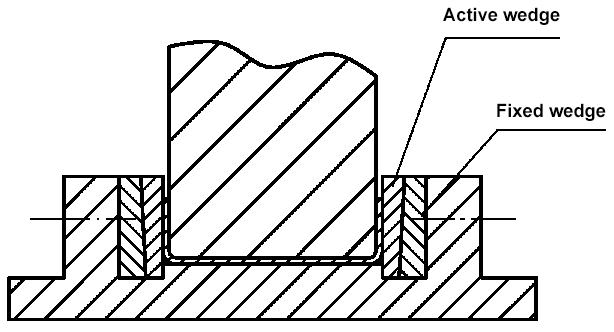
Kalıp içindeki hareketli kalıp demiri, zımba büküldükten sonra yükseldiğinde yukarı doğru hareket edebilir ve zımba ve kalıp arasındaki boşlukBu sayede iş parçasının kalıptan çıkarılması kolaylaşır.
Özel Bükme
(1) Oluklu Levhanın Bükülerek Şekillendirilmesi
Oluklu sac, dalga bileşeni olarak da bilinen yaygın bir bükülmüş bileşendir (Şekil 2-28). Bu dalga bileşeni tek bir şekillendirme işleminde tamamlanamaz, ancak her seferinde bir dalga preslenmelidir. Kalıbının şekli Şekil 2-29'da gösterilmiştir.
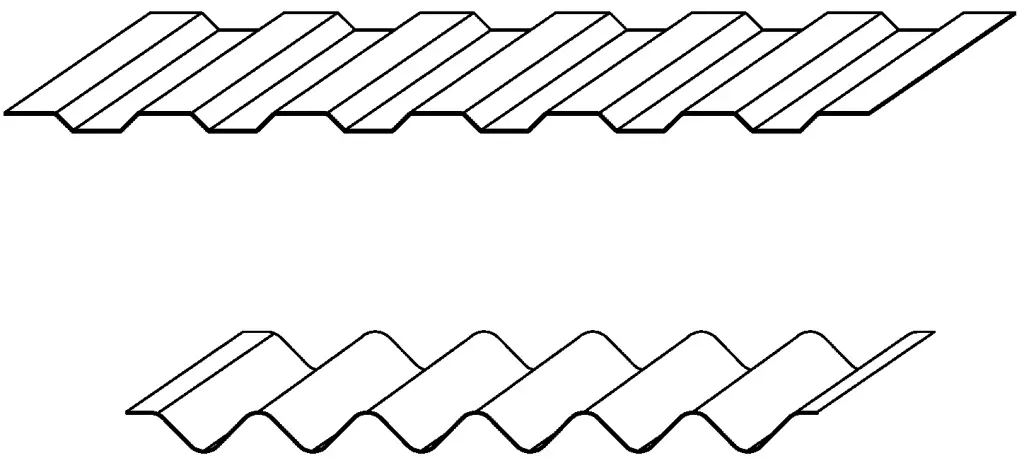
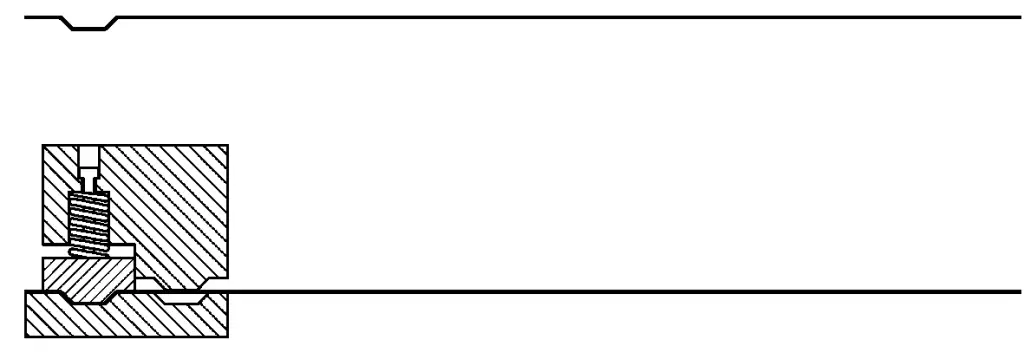
Şekilde gösterildiği gibi, bu çift dalga formlu bir kalıptır. İlk olarak, tabakanın bir ucuna bir dalga formu bastırılır. İlk dalga formuna basıldığında, malzeme kalıbın her iki tarafından merkeze doğru akar ve çift yönlü malzeme akışına izin verir.
İlk dalga formu oluşturulduktan sonra sol konumlandırma kalıbına yerleştirilir, zımba aşağı iner ve yaylı zımba ilk olarak ilk dalga formuna basar. Zımba inmeye devam ederek ikinci dalga formunu bastırmaya başlar. Kalıbın sağ tarafındaki malzeme sola doğru akarak tek yönlü malzeme akışına izin verir ve bu da ikinci dalga formunun preslenmesi için malzemeyi tamamlayabilir.
(2) Kanal Çeliğinin Yanal Bükülmesi
Kanal çeliğinin yanal bükülmesi nispeten nadirdir (Şekil 2-30) ve bükme yöntemi de oldukça benzersizdir.
Kanal çeliğini bükmeden önce, kanal çeliğinin deformasyon bölgesinin oluğuna bir destek plakası yerleştirilmelidir. Bükme sırasında, ısıtılmış bir presleme yöntemi kullanılmalıdır.
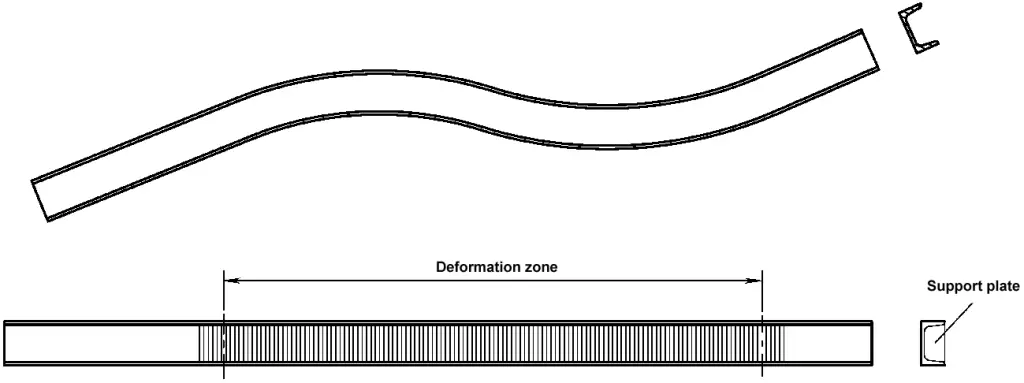
(3) Havza Şeklindeki Kanal Çeliğinin Bükülmesi
Havza şeklindeki kanal çeliği için bükme kalıbı birkaç parçanın birleşimidir (Şekil 2-31). Sol ve orta zımbalar bağlantı plakasına sabitlenir ve sağ zımba cıvatalarla bağlanır ve sağ zımba ile orta zımba arasında 1-2 mm boşluk bırakılır. Sol, orta ve sağ zımbalar bir bütün olarak cıvatalarla bağlanır ve bağlantı plakasına sabitlenir.
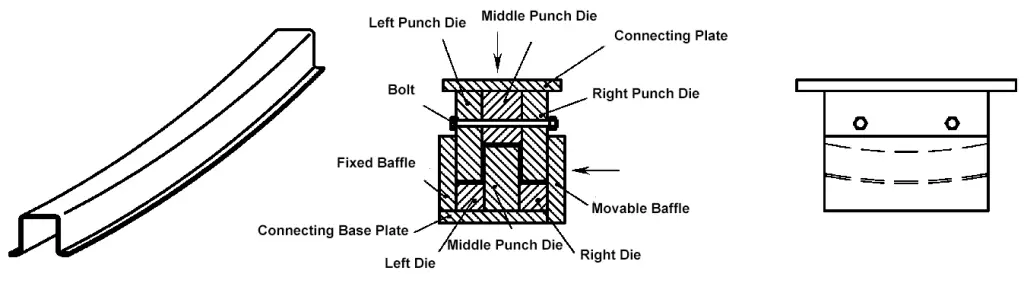
İş parçasını bükerken, havza şeklindeki kanal çeliğini kalıba yerleştirin, ardından hareketli bölmeyi kalıp gövdesine sıkıca oturacak şekilde itmek için yatay hidrolik silindiri kullanın ve ardından kalıp gövdesinin bükme için alçalmasını sağlamak için dikey hidrolik silindiri çalıştırın.
Bükme Konumlandırması ile İlgili Sorunlar
Bükülmüş bir parçanın kalitesi büyük ölçüde konumlandırmasının hassasiyetine ve bükme sırasının ve konumlandırma kriterinin makul olup olmadığına bağlıdır. Bükme konumlandırması kabaca ön uç konumlandırma, arka uç konumlandırma, yan yardımcı konumlandırma, merkez hattı konumlandırma ve yardımcı hat konumlandırma olarak ayrılabilir. Her konumlandırma türünün kendine has özellikleri vardır ve bunların uygun seçimi çok önemlidir.
(1) Ön uç konumlandırma (arka ölçme) yaygın ve basit bir konumlandırma yöntemidir. Günümüzde bükme makineleri, kullanımı kolay ve konumlandırmada doğru olan çok eksenli CNC arka uç konumlandırma cihazlarıyla donatılmıştır. Bununla birlikte, birden fazla büküm olduğunda, konumlandırma tabanındaki değişiklik nedeniyle sonraki konumlandırmanın tabanı önceki bükümün hassasiyetinden etkilenebilir (Şekil 2-32).

(2) Arka Uç Konumlandırma
Arka uç konumlandırma ön uç konumlandırma kadar kullanışlı olmasa da, bu yöntem kaç büküm yapıldığından bağımsız olarak aynı konumlandırma tabanını kullanır. Bu nedenle, bükme boyutları diğer faktörlerden etkilenmez (Şekil 2-33).
(3) Yan Yardımcı Konumlandırma
Dar ve uzun parçalar üzerinde çoklu paralel bükümler yaparken, her bir büküm hattının birbirine paralel olmasını sağlamak için, ön uç veya arka uç konumlandırmanın ayarlanmasına ek olarak, malzemenin kenarındaki uzunluk yönü boyunca yardımcı konumlandırma da ayarlanmalıdır (Şekil 2-34).
(4) Merkez Çizgisi Konumlandırma
Bazı bükülmüş parçaların ön uç veya arka uç konumlandırma yöntemleri kullanılarak doğru şekilde konumlandırılması zordur. Şekil 2-35'te gösterildiği gibi merkez hattı konumlandırma yönteminin kullanılması önerilir.
(5) Yardımcı Hat Konumlandırma
Büyük yarıçaplı çoklu bükümler yaparken, zımba büküm çizgisini doğru bir şekilde yakalamakta zorluk çekiyorsa, yardımcı çizgi konumlandırma yönteminin kullanılması önerilir (Şekil 2-36).
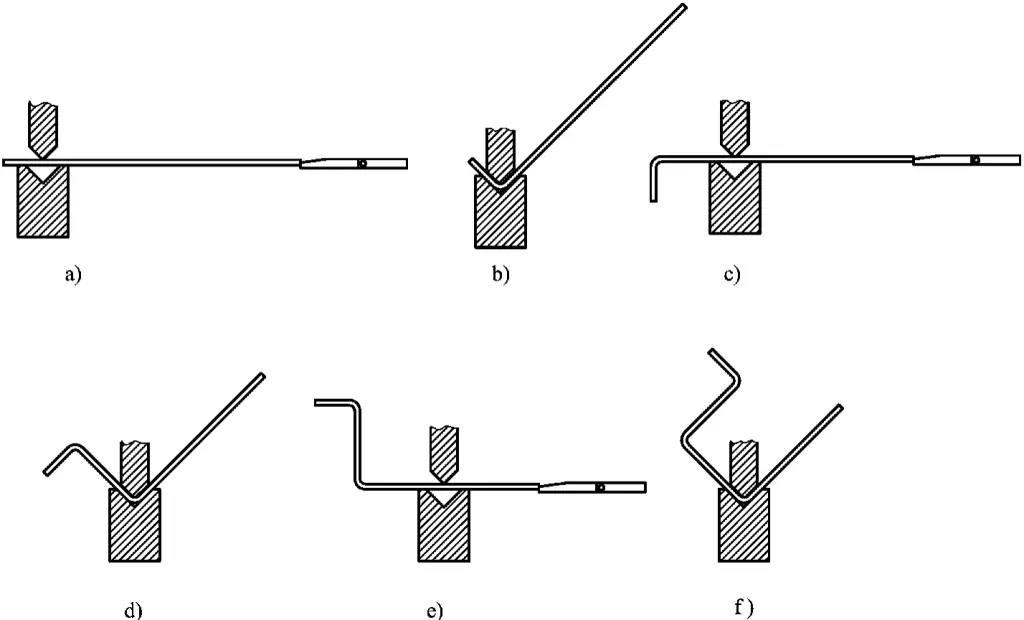
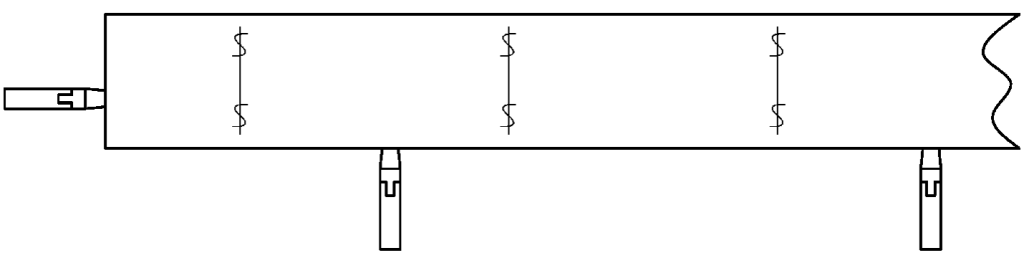
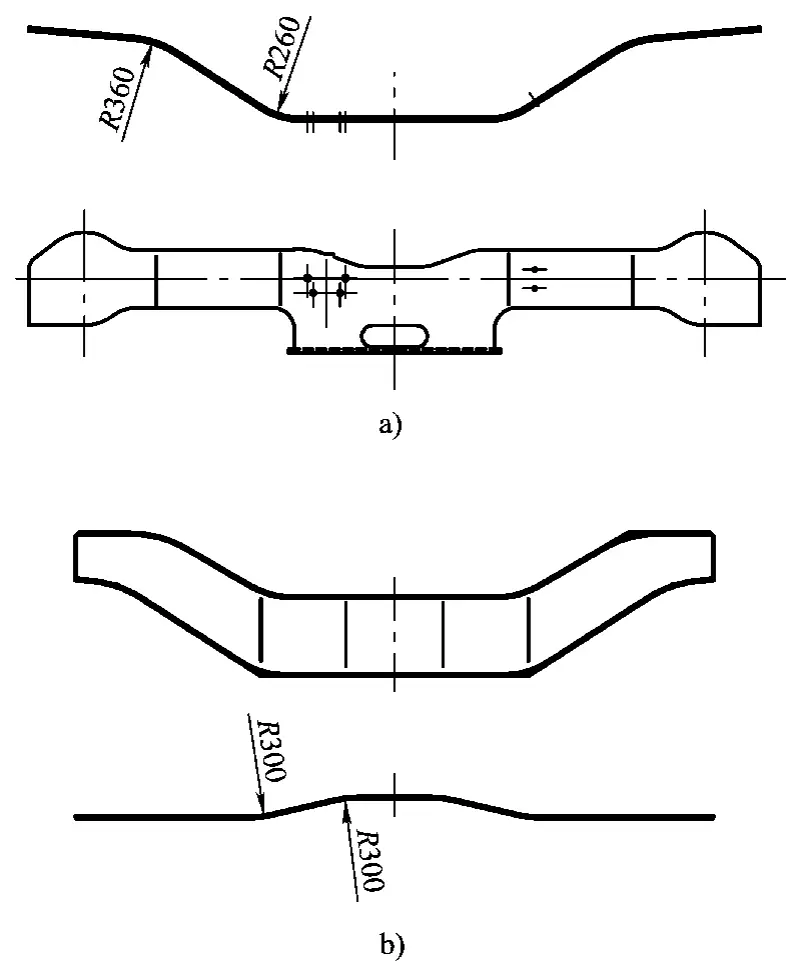
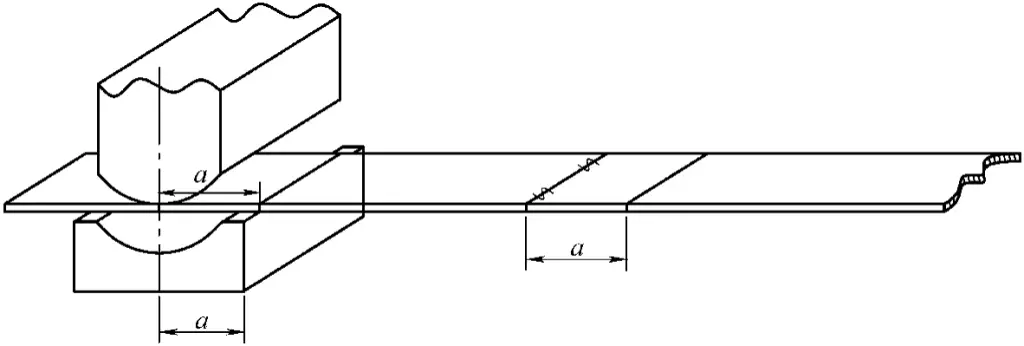
Kombinasyon Bükme Kalıbı
Şekil 2-35a, her bir çifti aynı bükme yarıçapına sahip dört bükümlü dar ve uzun bir bükülmüş parçayı göstermektedir. Bükme sırasına göre, önce iki uç R360 yarıçapı ile bükülmeli, ardından orta kısım R260 yarıçapı ile bükülmelidir. Bu, oldukça zahmetli olabilen iki kalıp değişikliği gerektirir ve iş parçasının sık sık taşınmasını gerektirir. Burada, referans için bir tür kombinasyon bükme kalıbı tanıtıyoruz.
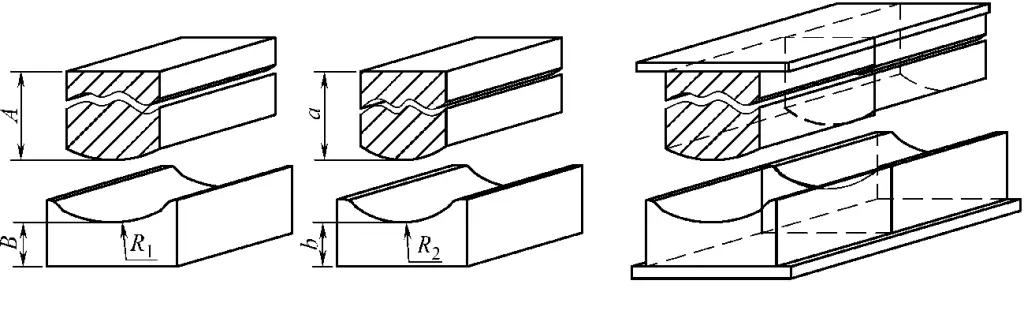
Kombine bükme kalıbı Şekil 2-37'de gösterilmektedir. Tasarım sırasında, her iki bükme yarıçapı için kalıplar aşırı uzun olmamalıdır, sadece iş parçasının genişliğinden biraz daha geniş olmaları gerekir. Kalıp (1) ve Kalıp (2)'nin dışbükey kalıp boyutu A, 'a'ya eşit olmalı ve içbükey kalıp boyutu B, 'b'ye eşit olmalıdır.
Kalıp (1) ve Kalıp (2) işlendikten sonra birleştirilerek Kalıp (3) oluşturulur. Yani, iki set eşit yükseklikte dışbükey kalıp ve üst oturma plakası Kalıp (3)'ün üst kalıbını oluşturur ve iki set eşit yükseklikte içbükey kalıp ve alt oturma plakası Kalıp (3)'ün alt kalıbını oluşturur.
Bu kombinasyon kalıbının kullanımı sadece kalıp kurulumlarının sayısını ve iş parçası taşıma sıklığını azaltmakla kalmaz, aynı zamanda bükme işlemi sırasında kalite kontrolünü de kolaylaştırır.
Bükülmüş Parçalar için Kalıplar ve Üretim Ekipmanları
Bükülmüş Parçalar için Kalıp Türleri
Bükülmüş parçalar için kalıp türleri, bükülmüş parçaların şekline, bükülmüş parçaların malzemesine, kalıbın malzemesine ve kalıba uygulanabilir ekipmana göre sınıflandırılabilir. Bu bükme kalıpları yapı olarak büyük farklılıklar gösterir.
(1) Bükülmüş parçaların şekline göre
Buna tek açılı bükme kalıpları, çift açılı bükme kalıpları (Z şeklinde bükme, U şeklinde bükme) ve çok açılı bükme kalıpları dahildir.
(2) Bükülmüş parçaların malzemesine bağlı olarak
Buna sac bükme kalıpları, profil bükme kalıpları, boru bükme kalıpları ve çubuk (tel) bükme kalıpları dahildir.
(3) Kalıp malzemesine bağlı olarak
Bu, tamamen metal kalıpları ve poliüretan kauçuk bükme kalıplarını (poliüretan kauçuğun çelik kalıbın yerini aldığı) içerir.
(4) Kalıp için geçerli ekipmana göre
Bu, genel presler, bükme makineleri ve bükücüler için bükme kalıplarını içerir.
Bükülmüş Parçalar için Üretim Ekipmanları
Bükme işlemi öncelikle mekanik preslerde gerçekleştirilir ve sac bükme maki̇neleri̇.
Tipik Bükülmüş Parçaların Üretim Örnekleri
U Şeklinde Konnektör ve Bükme Kalıbı
Şekil 2-38'de U şekilli bir konnektörün yapısı ve bükme kalıbı gösterilmektedir.
Bu kalıp, işlenmemiş parçayı tek bir preste bükerek şekillendirir ve aynı anda iki parça üretir.
İşlenmemiş parça, parça konumlandırmada yüksek hassasiyet sağlamak için içine işlenmiş bir oluğu olan stok destek bloğu 12 üzerine yerleştirilir. Pres kızağı aşağı indiğinde, zımba 5 önce işlenmemiş parça ile temas ederek onu aşağı bastırır.
İşlenmemiş parça, kayar kalıbın 11 filetosu boyunca kayarak kalıp boşluğuna girer ve U şeklinde bükülür. Kızak inmeye devam ederken, eğimli kama 3 kayar kalıba 11 temas eder ve kayar kalıbın 11 kalıp tabanının 9 oluğu içinde kalıbın merkezine doğru hareket etmesine neden olarak parçanın kenarlarını düzeltir.
Pres kızağı geri döndüğünde, eğimli kama 3 yukarı doğru hareket eder ve kayar kalıp 11, cıvata 7 ve yay 8'in etkisi altında kalıbın dışına doğru hareket eder. Stok destek bloğu 12, yay 14'ün etkisi altında yukarı doğru hareket ederek parçayı kalıptan dışarı iter.
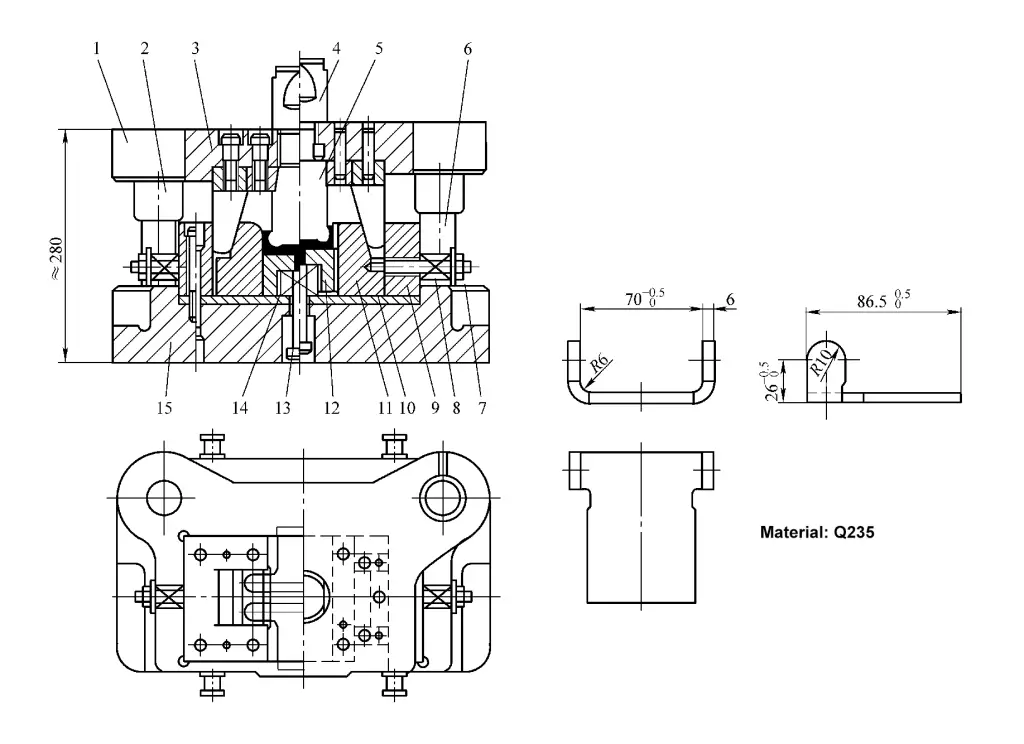
1- Üst kalıp tabanı
2- Kılavuz burç
3- Eğimli kalıp
4- Kalıp sapı
5- Punch kalıp
6- Kılavuz direği
7, 13- Cıvatalar
8, 14- Yaylar
9- Kalıp tabanı
10- Ara parça plakası
11- Kayar kalıp form kalıbı
12- Malzeme destek bloğu
15- Alt kalıp tabanı
İçten Yanmalı Lokomotif Panjur Kanadı ve Bükme Kalıbı
İçten yanmalı bir lokomotifin panjur kanadı, 1 mm kalınlığında bir çelik plakanın bükülmesiyle oluşturulur ve şekillendirilmesi için beş işlem gerekir.
Şekil 2-39, panjur kanadının birinci ila üçüncü işlemlerinin bükme kalıbı yapısını ve kanat bükmenin şematik diyagramını göstermektedir; Şekil 2-40, dördüncü ila beşinci işlemlerin bükme kalıbını ve kanadın son şeklini, yani iş parçası diyagramını göstermektedir. Kalıp, çok istasyonlu bir kombinasyon kalıbına benzer şekilde, büyük bir kalıp çerçevesi üzerinde bir dizi tek operasyonlu kalıptır.
Şekil 2-39'da gösterilen bükme kalıbında, işlenmemiş parça ilk işlem pres bükme kalıbının malzeme destek plakası 18 üzerine yerleştirilir, konumlandırma plakası 15 tarafından konumlandırılır ve işlenmemiş parçanın bir ucundaki kanca şeklindeki kafa sürgünün aşağı doğru hareketiyle bastırılır.
Preslenmiş kanca kafalı işlenmemiş parça, konumlandırma plakası 14 tarafından konumlandırılan ikinci işlem pres bükme kalıbının kalıbı 13 üzerine yerleştirilir ve işlenmemiş parçanın orta kısmındaki yay preslenir. Preslenmiş kavisli işlenmemiş parça, kanca kafası konumlandırma plakası 12 tarafından konumlandırılan üçüncü işlem pres bükme kalıbının kauçuk bloğu 11 üzerine yerleştirilir ve zımba kalıbı 6 işlenmemiş parçayı ikiye büker.
Şekil 2-40'da gösterilen bükme kalıbında, katlanmış işlenmemiş parça dördüncü operasyon pres bükme kalıbının yüzer kalıbına (I) 9 yerleştirilir, katın bir ucuna konumlandırılır ve diğer ucu bükülür.
Katlanmış işlenmemiş parça, katlanmış ucu kakma blok (II) 6'daki olukla hizalanacak şekilde beşinci işlem bükme kalıbının (II) 7 kalıbına yerleştirilir ve kanca başlı katlanmış kenar, orta yay yüzeyine oturması için bastırılarak iş parçasının son şekli tamamlanır.

1-Üst Kalıp Tabanı
2-Ekle
3-Punch
4-Pad
5-Punch
6-Punch
7-Guide Post
8-Yerleştirme Plakası
9-Konteynerli Çerçeve
10-Yuvarlak Çelik
11-Kauçuk Blok
12-Yerleştirme Plakası
13-Ölmek
14-Yerleştirme Plakası
15-Yerleştirme Plakası
16-Bolt
17-Bahar
18-Destek Plakası
19-Ekle
20-Guide Bush
21-Alt Kalıp Tabanı
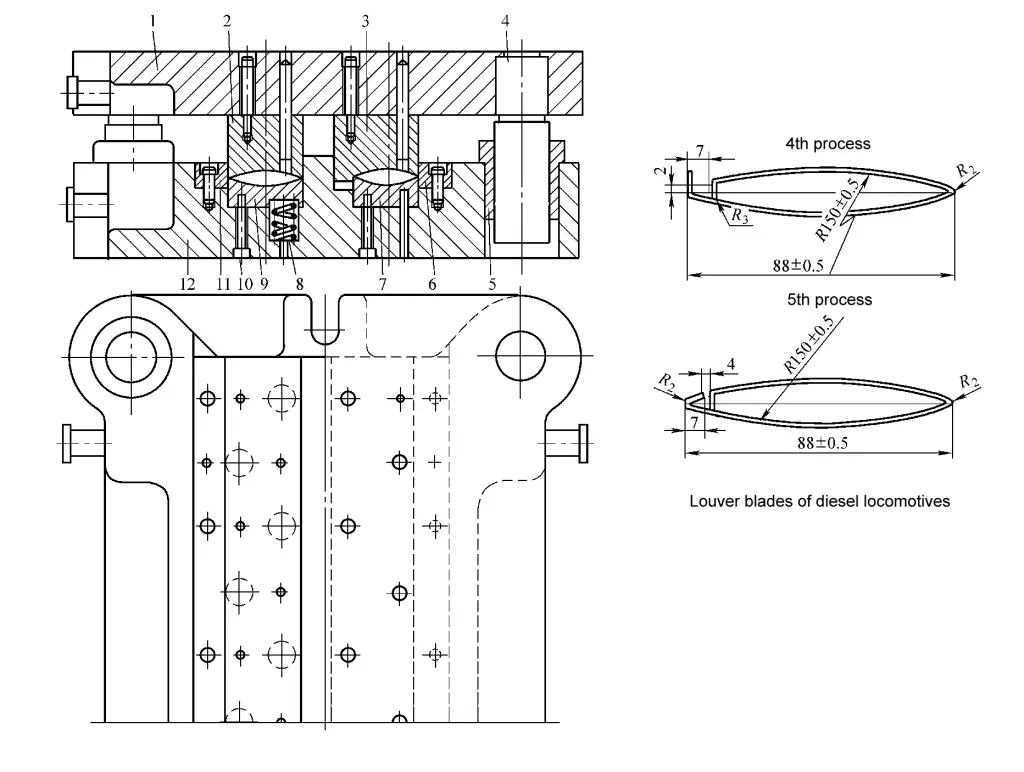
1-Üst Kalıp Tabanı
2-Punch (I)
3-Punch (II)
4-Kılavuz Direk
5-Kılavuz Çalı
6-Ekleme (II)
7-Die (II)
8-Bahar
9-Ölüm (I)
10-Bolt
11-Ekle
12-Alt Kalıp Tabanı