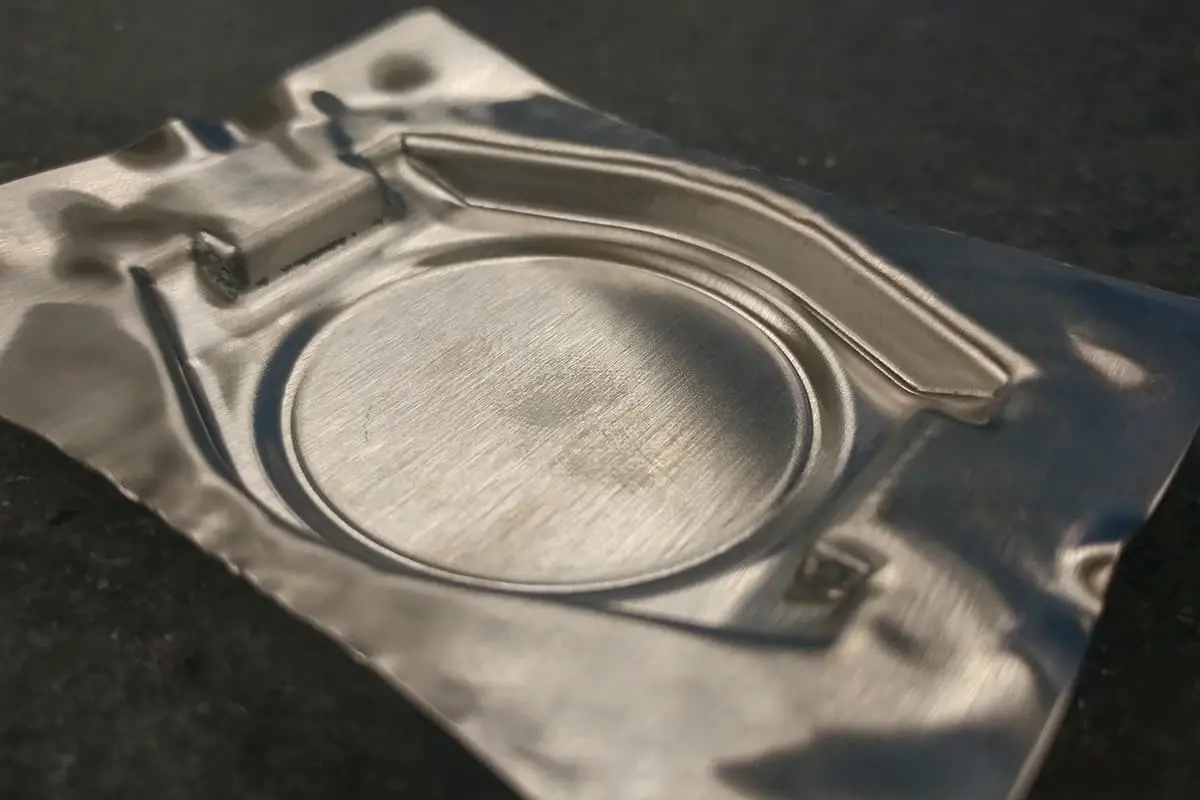
Çekme Kalıplarının Sınıflandırılması
Çekme kalıpları flanş tipine göre bağlayıcılı olanlar ve olmayanlar olarak sınıflandırılabilir. Ayrıca işlem sırasına göre ilk işlem çekme kalıpları ve sonraki işlem çekme kalıpları olarak sınıflandırılırlar. Yapısal olarak, doğrudan çekme kalıpları, ters çekme kalıpları ve inceltme çekme kalıpları olarak ayrılabilirler.
Paslanmaz çelik ürünlerin üretiminde doğrudan ve ters çekme yaygın olarak kullanılmaktadır. Bununla birlikte, paslanmaz çeliğin zayıf termal iletkenliği nedeniyle, ısı birikimine yol açabilen ve çekme koşullarını hızla bozabilen inceltme çekimi nadiren kullanılır ve bu kitapta tartışılmayacaktır.
Doğrudan çekme kalıpları ayrıca üste monte edilen ve alta monte edilen tipler olarak alt bölümlere ayrılır. Zımbanın yukarıda ve kalıbın aşağıda olduğu üste monteli kalıp yaygın olarak kullanılır. Buna karşılık, bu düzenlemenin tersine çevrildiği bir alttan monteli kalıp kullanılır.
Çekme zımbasının körleme zımbasıyla hizalanması nedeniyle, üstten monteli çekme kalıpları aşamalı çekme işlemlerinde sıklıkla kullanılır.
İlk Operasyon Çizim Kalıpları
İlk operasyon çekme kalıpları üste monte edilen ve alta monte edilen tipler olarak ikiye ayrılır.
(a) Üstten Monteli İlk Operasyon Çizim Kalıpları
Bağlayıcı gerektirmeyen flanşsız parçalar veya bağlayıcı gerektiren ancak minimum kuvvet gerektiren parçalar için, Şekil 4-10'da gösterildiği gibi, uygun düşük boşaltma ile verimliliği artırmak için üste monte edilmiş çekme kalıpları kullanılır. Tek operasyonlu kalıplarda, üste monte edilen çekme kalıbı basınç sağlamak için yalnızca zımbanın etrafına takılan elastik elemanlara dayanır.
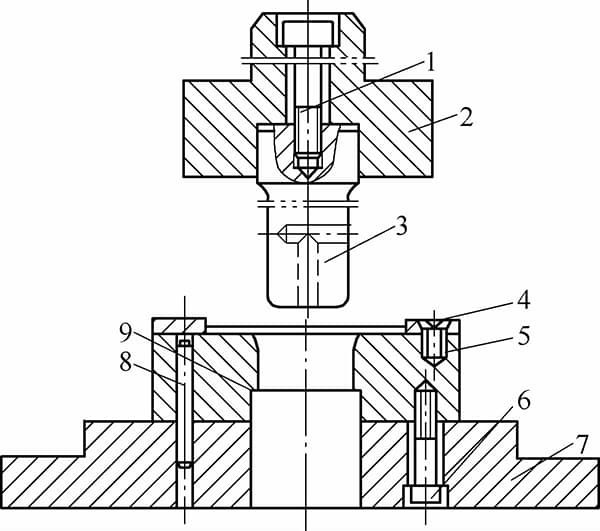
1, 5, 6 - Vidalar; 2 - Kalıp kolu; 3 - Zımba; 4 - Yerleştirme plakası; 7 - Alt kalıp pabucu; 8 - Dübel pimi; 9 - Kalıp boşluğu
Bu nedenle, hem işlenmemiş parça tutma kuvveti hem de strok oldukça sınırlıdır ve bunlar tipik olarak yüksek çekme oranına sahip, bağlayıcı içermeyen veya bağlayıcı içeren ancak minimum kuvvet gerektiren parçalar için kullanılır.
Flanşlı olmayan parçalar için, genellikle geçiş tipi bir boşaltma yöntemi kullanılır. Zımba yükseldikçe, şekillendirilen parçanın kenarındaki hafif bir geri tepme, genişlemesine ve kalıbın alt kenarına takılmasına neden olarak boşaltmayı kolaylaştırır. Bu nedenle, Şekil 4-11'de gösterildiği gibi, üste monte edilmiş çekme kalıbı oldukça verimlidir.
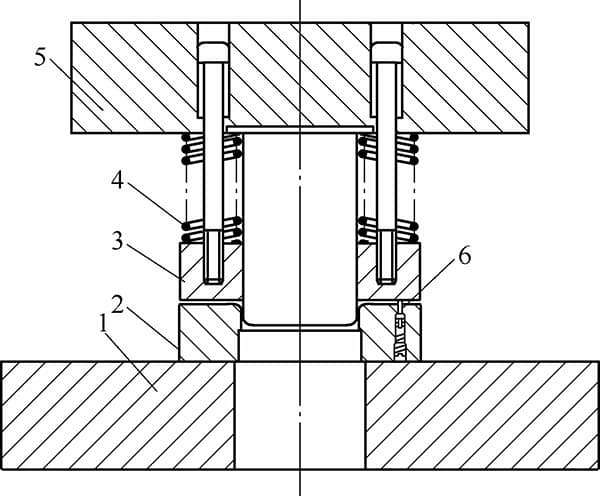
Bileşenler aşağıdaki gibidir: 1 - Alt kalıp pabucu, 2 - Kalıp boşluğu, 3 - Boşluk tutucu, 4 - Yay, 5 - Üst kalıp pabucu, 6 - Hareketli pilot pimi.
(b) Alttan Monteli İlk İşlem Çizim Kalıpları
Uygulamada, alta monte edilen kalıplar üste monte edilenlere göre daha yaygın olarak kullanılmaktadır. Bunun nedeni, bir preste flanşlı parçalar çizerken, alta monte edilen kalıpların montajının daha kolay olması, elastik elemanlar için daha fazla alan sunması, daha fazla işlenmemiş parça tutma kuvveti sağlaması ve işlenmemiş parça tutucunun daha kolay ayarlanmasına izin vererek işlemleri daha kolay hale getirmesidir.
Hidrolik preslere monte edilen çoğu ilk işlem çekme kalıbı, alttan monte edilmiş olarak tasarlanmıştır ve boş tutma kuvvetini ayarlamak için alt hidrolik silindiri kullanır. Şekil 4-12'de gösterildiği gibi, alttan monte edilen kalıpları test ederken üstten monte edilenlere kıyasla çeşitli kolaylıklar da vardır.
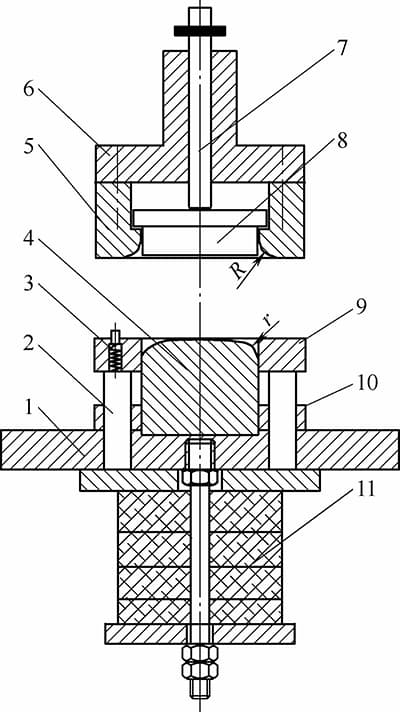
1-Alt kalıp tutucu 2-Kaldırma çubuğu 3-Boşluk bulucu 4-Punch 5-Kalıp 6-Üst kalıp tutucu 7-Ejektör çubuğu 8-Ejektör plakası 9-Boşluk tutucu 10-Punch tutucu plakası 11-Sıyırıcı mekanizması
Sonraki İşlem Çizim Kalıpları
(a) Alttan Monteli Sonraki İşlem Çizim Kalıpları
Sonraki işlem çizim kalıplarının alta monte edilmiş olarak tasarlanması, parçaların görünümünde istikrarlı bir kalite sağlar. Bu kalıplar Şekil 4-13'te gösterildiği gibi bir kalıp, bir knockout cihazı, bir kalıp seti ve bir zımbadan oluşur.
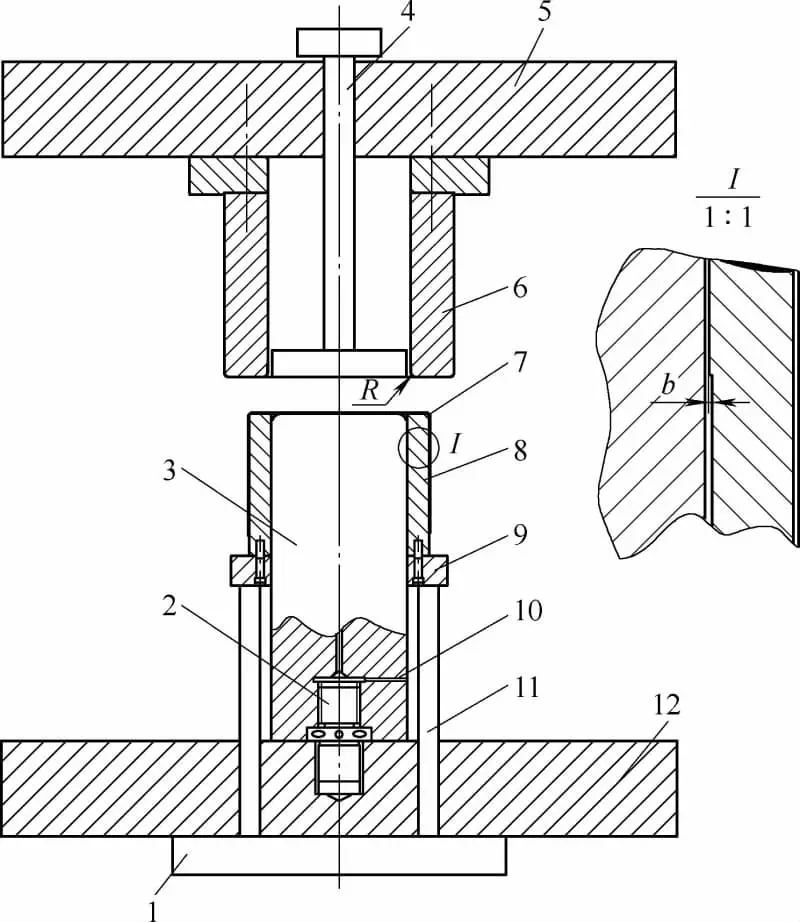
Şekil 4-13'te standart bir hidrolik silindir üst plakası, üniversal bağlantı saplamaları, bir zımba, bir itme çubuğu, bir hidrolik pres kızak, bir kalıp, bir iş parçası, bir kalıp kovanı, bir merkezi destek plakası, havalandırma delikleri, bir kaldırma çubuğu ve bir hidrolik pres çalışma masası.
(b) Bağlayıcısız Sonraki İşlem Çekme Kalıpları
Bağlayıcısız sonraki işlemler için çekme kalıpları 0,8'den daha büyük bir çekme oranına sahip olmalıdır ve genellikle Şekil 4-14'te gösterildiği gibi sürekli çekme işlemlerinde olduğu gibi küçük kalınlıktaki malzemeler ve küçük çaplı ürünler için kullanılır.
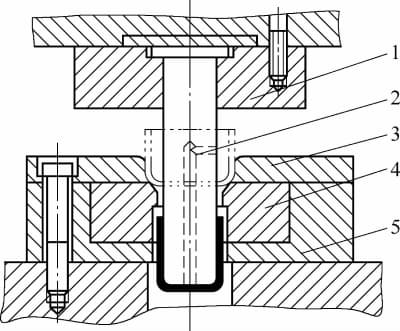
1- Zımba Tutucu Plakası, 2- Zımba, 3- Yer Tespit Plakası, 4- Kalıp ve 5- Kalıp Tutucu Plakası.
Ters Çekme Kalıpları
Bir parça için birden fazla çizim işlemi gerektiğinde, ilk işlem doğrudan çizim kullanır ve sonraki işlemler Şekil 4-15'te gösterildiği gibi şekillendirmeyi kolaylaştırmak için ters ve doğrudan çizim arasında değişir.
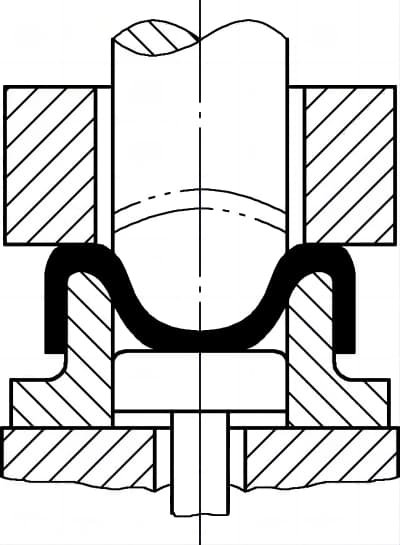
Ters çekme, ilk çekme işleminden gelen yarı mamulün içi boş bir kalıba yerleştirilmesini ve zımbanın daha fazla çekme için dış yüzeyden girmesini içerir. Zımbanın işlenmemiş parça üzerine uyguladığı kuvvet, önceki çekme işleminin tersi yöndedir ve malzemenin iç ve dış yüzeylerinin değişmesine izin vererek deformasyonu artırabilir ve üretim verimliliğini artırabilir.
Ters çizimin çeşitli özellikleri vardır:
1) Ters çekme ile, işlenmemiş parça ile kalıp arasındaki geniş sarma açısı sürtünme direncini ve bükülme direncini azaltarak kırışmayı daha az olası hale getirir. Kalıp duvarı 28t'den daha ince olduğunda, bir bağlayıcı gerekli olmayabilir.
2) Kuvvet yönü ve bükülme önceki işlemin tersi olduğundan, yarı mamulün işle sertleşmesi doğrudan çekmedekinden daha azdır.
3) Kalıbın iç ve dış köşe yarıçaplarının toplamı kalıp duvar kalınlığını aşamaz. İş parçasının boyut sınırlamaları nedeniyle, boş çap (d) 30t'den az olamaz ve iç köşe yarıçapı 4t'den büyük olmalıdır.
4) Ters çekme için çekme oranı, kalıbın mukavemetini azaltabileceğinden çok büyük olmamalıdır. Genel olarak, çekme oranı doğrudan çekme oranından 10% ila 15% daha az olabilir.
5) Ters çekme, daha büyük gerekli kalıp yarıçapları nedeniyle küçük parçalar için zordur, bu da onu orta ila büyük silindirik parçalar için daha uygun hale getirir.
6) Bir zımba ve kalıp arasındaki boşluk ters çekimde doğrudan çekime göre 15% ila 30% daha büyük olabilir.
7) Kalıp duvar kalınlığı 10t'den az olmamalı ve mutlak değeri 6mm'den az olmamalıdır.
Ters çekme, geniş desteklenmeyen alanlara sahip parçaların şekillendirilmesi için önemli avantajlar sunar. Ters çekmede kullanılan boşluklar düz veya küresel tepeli olarak gelir. Çekme sırasında, küresel tepeli işlenmemiş parça ile zımba arasındaki temas kademelidir, bu da yarım küre, konik veya parabolik parçaların şekillendirilmesi için daha avantajlıdır.
Derin Çekme Kalıbı Seçimi
Planları aldıktan sonra, derin çekilmiş parçaları genel olarak kategorize etmeliyiz. Derin çekme kalıbının yapısal formu öncelikle iş parçasının şeklini ve aşağıdaki gibi ek faktörleri dikkate alır:
1) Malzeme kalınlığının maksimum işlenmemiş parça boyutuna oranı.
2) Boş boyutun nihai biçimlendirilmiş boyutlara oranı.
3) En-boy oranı veya maksimum genişlik-yükseklik oranı.
4) Tabanın açık uç boyutlarına oranı.
5) Yüzey hassasiyeti.
6) Malzemenin çekme dayanımı katsayısı.
Tüm bu veriler toplandıktan sonra, derin çekme kalıbı için uygun yapısal formu belirleyebiliriz.
Derin çekme için kalıp seçimi aşağıdaki koşullara göre yapılmalıdır:
1) d0-d1/2 ≤ 7t için, bağlayıcı halkası olmayan bir doğrudan boşaltma kalıbı kullanın.
2) 7 < d0-d1/2 < 14t için, bağlayıcı halka olmadan boşaltma için konik girintili bir kalıp kullanın.
3) d0-d1/2 ≥ 14t için, bir bağlayıcı halka ile düz bir girinti kalıbı kullanın.
4) Tek operasyonlu silindirik parçalar ters çevrilmiş derin çekme kalıbı kullanmalıdır. Flanşsız veya flanş için düşük düzlük gereksinimleri olan uzun silindirik parçalar, çoklu derin çekme işlemleri için ters çevrilmiş bir kalıp da kullanabilir, ancak malzemenin iş sertleşmesi şiddetli ise ara tavlama düzenlenmelidir.
5) Yüksek flanş düzlüğü gerektiren çok aşamalı derin çekme parçaları için, kol sapmasının flanş düzlüğü üzerindeki etkisini en aza indirmek için pozitif ve negatif derin çekme arasında geçiş yapın.
6) Üçten fazla derin çekme aşaması olan parçalar için, 1-2 aşamayı konik bir girinti kalıbı ile serpiştirmeyi düşünün.
7) Orta derinlikteki konik parçalar için, pozitif ve negatif derin çekme işlemlerini birleştirmeyi düşünün.
8) Paslanmaz çelik sofra takımı üretiminde, sızdırmazlık performansının kritik olmadığı uzun silindirik parçalar için, derin çekmeye alternatif olarak kaynaklı borular artı alt bağlantı kullanmayı düşünün.
9) Parabolik parçalarda derin çekme ve ardından sert kalıp şişkinliği kullanılmalıdır.
10) Karın bölgesinde kırışmaya eğilimli aerodinamik parçalar için içten dışa doğru derin çekme işlemini düşünün.
11) İkinci derin çekme aşamasından sonra bağlayıcı alanı yetersiz olan parçalar için, ilk derin çekme kalıbının iç köşe yarıçapını büyütmeyi ve içten dışa derin çekme yöntemini kullanmayı düşünün.
12) Ana deformasyon yüzeyinin profil çizgisiyle kesiştiği parçalar için kavisli bir bağlayıcı halka kullanın.
13) Sonraki derin çekme aşamalarından sonra alt malzeme ciddi şekilde incelmişse veya şekillendirme sırasında malzeme kaynağı yoksa ve zımbalamaya izin veriliyorsa, delinmiş alandan malzeme çekmek için bir zımbalama işlemi deliği ekleyin; zımbalamaya izin verilmiyorsa, bu malzemenin ilk derin çekme aşamasında yerinde olduğundan emin olun.
14) Döner gövdeli derin çekme parçalar için, toplam yüksekliğin yarısından az olan yüzeyler veya konik yükseklikler için özel bir önlem gerekmez; toplam yüksekliğin yarısından fazla ancak üçte ikisinden az ise, bir derin çekme basamağı kullanın; üçte ikisinden fazla ise, Şekil 4-16'da gösterildiği gibi bir derin çekme nervürü kullanın.
15) Mümkünse yüksek konik parçaların derin çekilmesinden kaçının; izin veriliyorsa, konik silindirler oluşturmak için yelpaze şeklinde kesme ve bükmeyi ve ardından kaynak yapmayı tercih edin.
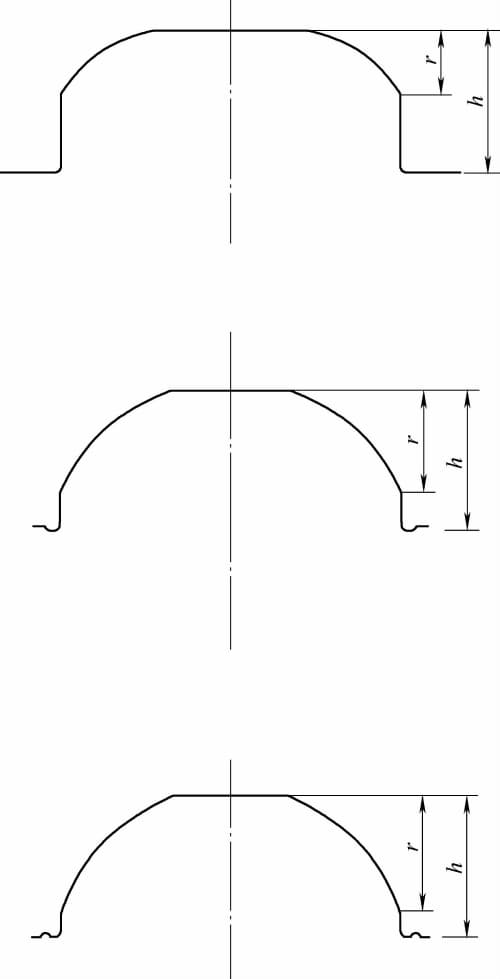