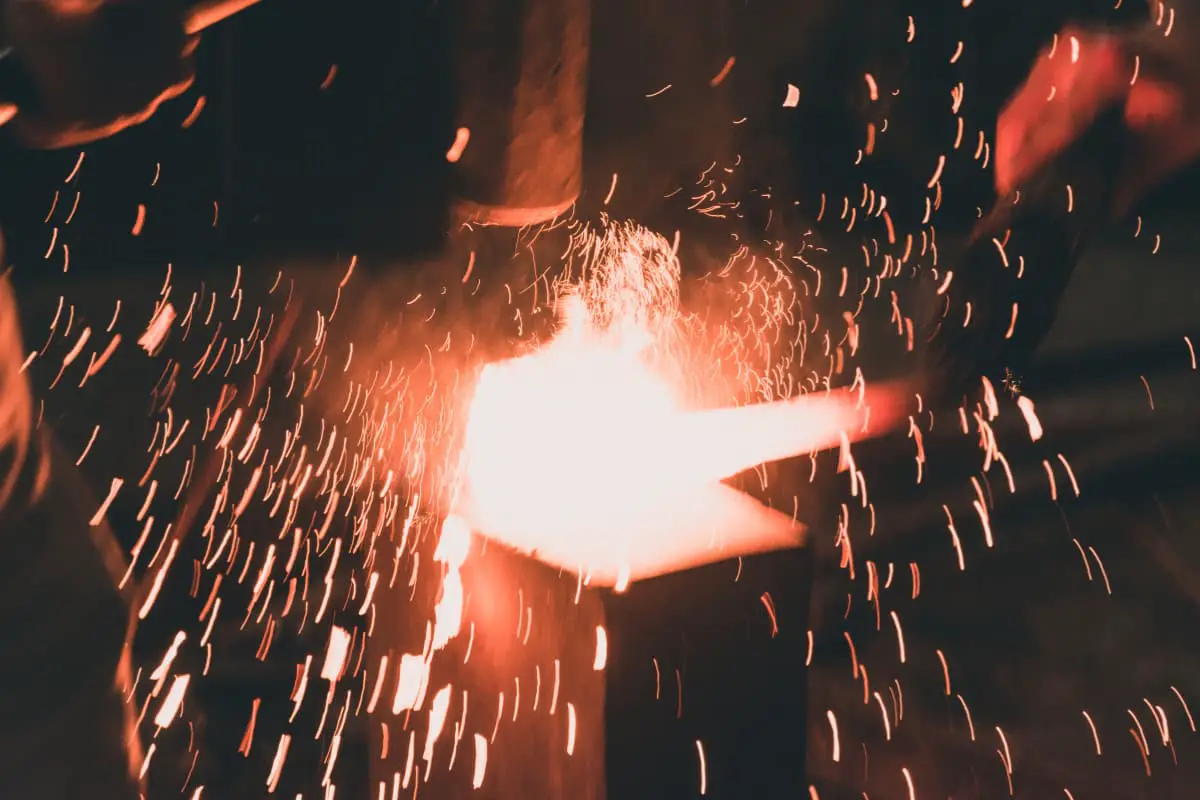
1. Çatlak
(1) Yüzeyde aşırı yanmanın neden olduğu çatlaklar Bu çatlaklar çoğunlukla biyel dövme parçalarının köşe kenarlarında, özellikle de dövme sırasında çekme gerilimine maruz kalan bölgelerde dağılır. Özellikleri, çatlakların kısa ve kalın olması, dövme yüzeyinde düzensiz bir şekilde yoğun olarak dağılması ve tane sınırları boyunca içe doğru uzanması; çatlakların içinin oksitlerle dolu olması, her iki tarafta şiddetli dekarbürizasyon, iri taneler ve Widmanstätten yapısının varlığıdır.
(2) Son dövme veya boyutlandırma sırasında çok düşük sıcaklıktan kaynaklanan çatlaklar Bu çatlaklar çoğunlukla kalıpta dövme sırasında çekme gerilimine maruz kalan dövme bölgelerinde veya metal akış sınırlarında dağılır. Derin, uzun ve nispeten yoğun olmaları ile karakterize edilirler.
(3) Çatlama (bkz. Şekil 6-32) Karakteristik özelliği, çatlakların nispeten sığ ve dövme yüzeyinde ağ benzeri dağılmış olmasıdır. Oluşumlarının ana nedenleri aşağıdaki gibidir:
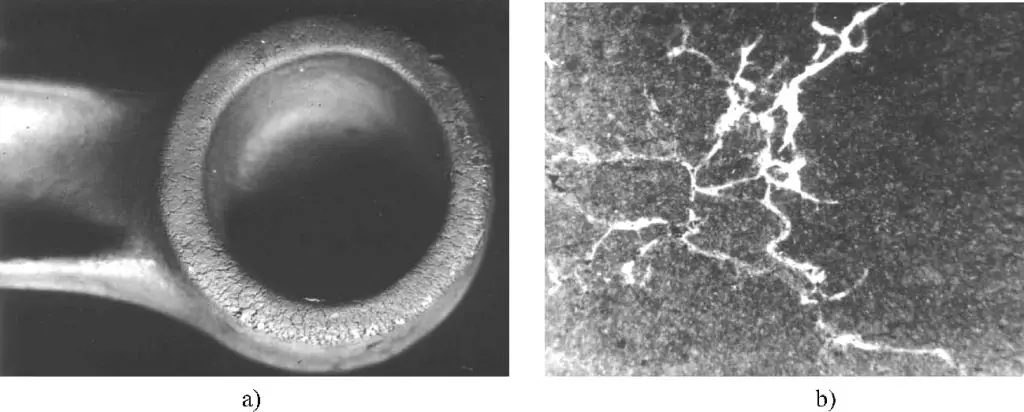
a) Biyel kolunun küçük ucunda çatlama b) Çelik içinde bakır
1) Hammaddede bakır, kalay ayrışması veya aşırı bakır, kalay içeriği. Bakır ve kalay düşük erime noktalarına sahip olduklarından, dövme ısıtması sırasında eriyerek yerel plastikliğin azalmasına ve çatlakların oluşmasına neden olurlar.
2) Yakıtta aşırı kükürt içeriği, özellikle yakıt olarak gaz veya doğal gaz kullanıldığında, eksik kükürt giderme nedeniyle, kükürt ısıtma sırasında tane sınırları boyunca kütüğün yüzey katmanına nüfuz eder, tane sınırlarında sülfür kalıntıları oluşturur, taneler arasındaki bağlantıyı zayıflatır ve kalıpta dövme sırasında çatlamaya neden olur.
(4) Ayrılma çizgisi boyunca boylamasına çatlaklar (bkz. Şekil 6-33) Bu çatlaklar metalik olmayan kalıntılardan kaynaklanır. Çelikteki kükürt ve fosfor gibi metalik olmayan safsızlıklar ve kütük yapımı veya dövme sırasında kaynaklanmayan büzülme ve gözeneklilik gibi kusurlar nedeniyle, kalıpla dövme sırasında flaşın içine sıkışırlar ve kesme sırasında ayırma çizgisinde çatlaklar oluşur.

1) Ağır kusurlu kütükler, kusurlar flaşa sıkıştırılır, flaşın kesik yüzeyi boyunca çatlaklar olarak görünür veya dövme, dövme kalıbının ayrılma çizgisi boyunca ikiye bölünür (bkz. Şekil 6-34). Çekme veya merdaneli dövme sırasında uzayan çelik külçede büzülme veya gözeneklilik bulunması nedeniyle, kalıpla dövme sırasında sıkılan büzülme veya gözenekliliğin kenarları flaşa bastırılır ve bu kusurlar flaşın kesilmesinden sonra ortaya çıkar.

a) Kütük kusurları b) Flaşa sıkıştırılmış kusurlar
2) Dövme işlemi sırasında çatlakların oluşmasının nedeni, metal flaş oluğuna akarken farklı dirence neden olan ve ayırma yüzeyinde kayma gerilmesinin kolayca oluşmasına neden olan flaş oluğunun üst ve alt köprülerinin farklı yüzey pürüzlülüğüdür,
ayırma yüzeyinin delaminasyonuna ve çatlamasına neden olur.
3) Kalıpta dövme sırasında, kesme işlemi sırasında ayırma yüzeyinin yırtılmasına neden olan ciddi yanlış hizalama (bkz. Şekil 6-35).

İşlem sırasında ayırma yüzeyi yırtılır
2. Dövme içine dövülmüş ölçek
Kütüğün enine kesit ve uzunluk boyutlarını değiştirmenin ve metali dağıtmanın yanı sıra, çekiç kalıpla dövmede üzme adımı aynı zamanda tufal çıkarmaya da hizmet eder. Alt üst etme adımı proses gerekliliklerine göre işletilmezse ve tufal tamamen uzaklaştırılmazsa, son dövme sırasında dövmenin içine bastırılacaktır. Tufal dövmeden düştükten sonra, yüzeyde çukurlar oluşur ve işlenmiş yüzeyde siyah tufal bırakır. Asitleme ve dövme tufalının atılmasından sonra kalan izler 3 mm kadar derin olabilir.
Bu kusur işleme payını aşarsa, dövmenin hurdaya ayrılmasına neden olabilir. Bu nedenle, bu kusurun oluşmasını önlemek için ölçeğin dikkatlice çıkarılması önemlidir.
Bu kalite kusurunun ana nedenleri aşağıdaki gibidir:
1) Dövme kusurları örneğin dövme sırasında kalıp oluklarında temizlenmemiş oksit tufalının neden olduğu girintiler gibi. Özellikle kalıp oluklarının ön ve arka uçlarında hafif bir ihmal üflemede ölü açılara yol açabilir.
2) Kütük ısıtması sırasında oksit skalasının ön dövme sırasında tamamen soyulamadığı ve oksit skalasının kütüğe yapışan kısımları nedeniyle dövme üzerinde girintilere neden olan şiddetli oksidasyon. Bunu temelden çözmek için, ısıtma kalitesini sıkı bir şekilde kontrol etmek gerekir. Bu oksit skalası dövme üzerine dövülürse, yüzeyde çukurlar ve boşluklar oluşturacak veya parçanın çalışma kesitinin boyutunu azaltacaktır.
3) Dövme işlemi sırasında kalıp atlaması, oksit tufalının son dövme kalıbına ikincil olarak girmesine ve dövme üzerinde girintilere neden olur. Bu nedenle, dövme işlemine devam etmeden önce kalıp atlamasından sonra kalıp oluklarındaki oksit tufalının temizlenmesi çok önemlidir.
4) Fırının dibinde cüruf oluşumu, burada oksit tortusu metale güçlü bir şekilde yapışır, kalıpla dövme sırasında silkelemeyi imkansız hale getirir ve asitleme sırasında temizlenemez. Bu tür oksit tortusu dövmeden çıkarılabilse bile, dövmenin boyutları genellikle küçülür.
3. Göçük
Bu tür hurdaların özelliği mekanik hasardır. Mekanik hasar, dövme kalıbı oluklarından çıkarıldığında veya sıcak dövmelerin taşınması sırasında dövmede meydana gelir; veya düzeltme sırasında, ilgisiz nesneler (delikli ince tabakalar gibi) düzeltme kalıbına düştüğünde dövmede mekanik hasara neden olur. Derinlik işleme payını aşarsa, dövme hurdaya ayrılır.
4. Hasarlı dövme
Dövme, alt kalıp oluğuna güvenli bir şekilde yerleştirilmeden önce veya kalıp oluğu içinde hareket ederken darbe nedeniyle hasar görür. Bu tür hurdaların nedenleri aşağıdaki gibidir:
1) Operatör işlenmemiş parçayı son dövme kalıbına veya düzeltme kalıbına doğru şekilde yerleştirmemiştir veya dövme kalıp kanalından dışarı fırladığında darbe almıştır.
2) Dövme çekicinin üst üste binen darbe olayları vardır, yani pedala bir kez basılması çekicin birden fazla kez vurmasına neden olur ve hatalı dövme kalıpları ve düzeltme kalıpları üzerinde de işlem yapılır.
3) Kırpma sırasında, dövme kalıbın içine yerleştirilmezse, dövmeye de zarar verecektir. Dövmenin zarar görmesi çoğunlukla operatörün dikkatsizliğinden kaynaklanır ve dövmenin zarar görmesini önlemenin tek yolu dikkatli çalışmaktır.
5. Yanlış akış çizgisi
Normalde, bir dövmenin akış çizgisi dağılımı Şekil 6-36'da gösterildiği gibi dövmenin şekli ile tutarlıdır.
Bununla birlikte, ön dövme kalıp oluğu makul olmayan bir şekilde tasarlanırsa, işçi uygunsuz bir şekilde çalışırsa veya kalıp aşınması, uygun olmayan kütük üzme yöntemleri veya kütüğün kalıp oluğuna yanlış yerleştirilmesi nedeniyle, düzensiz metal akışına neden olabilir ve potansiyel olarak düzensiz ve türbülanslı akış çizgileriyle sonuçlanabilir.
Düzensiz akış çizgileri, çeşitli mekanik performans göstergelerinde değişen derecelerde düşüşe yol açabilir. Bu nedenle, önemli dövme parçalar için akış çizgisi dağılımı gereksinimleri vardır.

Girdap akımları, geçiş akışı ve nervür penetrasyonu kusurları, katlama ile aynı nedenlerden kaynaklanır; bunların tümü kütük kesitindeki mantıksız metal dağılımından veya kütük hacminin dövmeyi çok aşmasından kaynaklanır ve kalıp oluğunun doldurulması sırasında ciddi düzensiz metal akışına neden olur. Bu üç kusura eğilimli dövme parçaların şekillerine bakıldığında, en çok "L", "Π" veya "T" şekilli kesitlere sahip dövme parçalarda meydana geldiği görülmektedir.
Bu üç kusur düzensiz metal akışından kaynaklansa da, düzensizliğin derecesi değişir ve farklı sonuçlara yol açar; daha hafif vakalar girdap akımları oluşturur (bkz. Şekil 6-37), daha şiddetli vakalar içinden akış oluşturur (bkz. Şekil 6-38) ve en şiddetli vakalar kaburga penetrasyon çatlaklarına neden olur.
Girdap akımları ve içinden akış genellikle iri taneli olaylara eşlik eder, bu da şiddetli akan metalin toplanma ve yeniden kristalleşme eğiliminden kaynaklanır. Deneysel sonuçlar, girdap akımlarının ve geçiş akışının parça mukavemeti üzerinde çok az etkisi olduğunu, ancak plastisite üzerinde önemli bir etkisi olduğunu ve yorulma performansı ve korozyon direnci üzerinde en ciddi etkiye sahip olduğunu göstermektedir.


6. Dövme deformasyonu
Deformasyon, dövmenin merkez hattının ve düzleminin dövme diyagramındaki doğru şekilden sapması anlamına gelir. Bu kusur kalıpta dövme, delme düzeltme, nakliye veya ısıl işlem sırasında meydana gelebilir. Bu durumlarda oluşan deformasyon düzeltme yöntemleri ile giderilebilir. Dövme kalıbında düzeltme gibi dövmenin sonraki süreçlerinde düzeltme işlemleri vardır. hidrolik preskabartma yoluyla veya manuel olarak.
(1) Kalıptan çıkarmanın neden olduğu deformasyon, bir dökümün kalıptan çıkarılması işlemiyle karşılaştırılarak gösterilebilir. Bir dökümün kalıptan çıkarılması kum kalıbın tahrip edilmesiyle gerçekleştirilebilirken, bir dövmenin kalıptan çıkarılması, döküm sırasında ahşap bir kalıbın kum kalıptan çıkarılmasına benzer şekilde, dövme parçanın kalıp boşluğundan çıkarılmasıyla yapılmalıdır.
Bu nedenle, dövme parçaların kalıptan çıkarılmasını kolaylaştırmak için, dövme basıncı yönüne dik olan tüm kalıp duvarlarına "kum çıkarma boyutu" ilkesini - kum çıkarma için koniklik - uygulamak ve dövme çekme açısı olarak bilinen belirli bir eğim açısı oluşturmak gerekir (tipik olarak 5 ° ile 12 ° arasında).
Aksi takdirde, kalıp boşluğuna sıkıştırılan yumuşak dövme parça sadece pense ile zorla çekilebilir ve bu da zaten dövülmüş olan parçayı deforme eder.
Bazı dövme kalıpları kötü tasarlanmıştır ve dövme parçalarını çıkarmak için keskin bir alet kullanılmasını gerektirir, bu da kaçınılmaz olarak deformasyona neden olur. Daha iyi bir yaklaşım, kalıp konikliğine dikkat etmek ve kalıp boşluğunun derinliğini (ayırma yüzeyinin üstündeki ve altındaki dikey boşluk) genişliğine göre en aza indirmek ve dövme parçanın otomatik olarak dışarı fırlamasını veya minimum çabayla çıkarılmasını sağlamak için ideal olarak uzunluğundan daha azdır.
(2) Delme veya düzeltmenin neden olduğu deformasyon Hatalı düzeltme zımbaları veya zayıf kalıp tasarımı nedeniyle, ince kesitli karmaşık düzeltme profilleri eğrilebilir ve uzun dövme parçalar düzeltme deformasyonu nedeniyle genellikle bükülür.
(3) Dövme sonrası soğutma veya ısıl işlemden kaynaklanan deformasyon Dövme sonrası eşit olmayan soğutma veya ısıl işlem sırasında uygun olmayan ısıtma ve soğutma yöntemleri deformasyona neden olabilir. Yaygın deformasyonlar arasında uzun eksenli dövme parçaların bükülmesi yer alır ve bu durum düzleştirme ile düzeltilebilir.
Orta ve düşük karbonlu çelik ve düşük alaşımlı yapısal çelik dövmeler için, bükülme 10 mm'den azsa, soğuk düzeltilebilir; dövme çelik veya çeşitli alaşımlı takım çeliklerindeki büyük deformasyonlar, orta karbon alaşımlı yapısal çelik dövmeler sıcak düzeltilmeli veya gerilimi azaltmak için düzleştirmeden sonra tavlanmalıdır.