
1. Kaynak Çubuklarının Sınıflandırılması
(1) Kaynak çubuğunun kullanım amacına göre sınıflandırma
1) Karbon çelik kaynak çubukları esas olarak düşük karbonlu çelik ve düşük alaşımlı çeliğin daha düşük mukavemet derecelerinde kaynaklanması için kullanılır.
2) Düşük alaşımlı çelik kaynak çubukları esas olarak düşük alaşımlı yüksek mukavemetli çelik, molibden içeren ve düşük alaşımlı elementlere sahip kobalt-molibden ısıya dayanıklı çelik ve düşük sıcaklık çeliğinin kaynağı için kullanılır.
3) Paslanmaz çelik kaynak çubukları esas olarak molibden ısıya dayanıklı çelik ve daha yüksek alaşımlı elementlere sahip kobalt-molibden ısıya dayanıklı çelik ve çeşitli paslanmaz çelik türlerinin kaynağı için kullanılır.
4) Sert dolgu kaynak çubukları, biriken metali oda veya yüksek sıcaklıklarda iyi aşınma direncine ve korozyon direncine sahip olan metal yüzey sert dolgusu için kullanılır.
5) Dökme demir kaynağı çubuklar özellikle dökme demirin kaynak ve onarım kaynağı için kullanılır.
6) Nikel ve nikel alaşımlı kaynak çubukları, nikel ve nikel alaşımlarının kaynağı, onarım kaynağı veya sert dolgu için kullanılır.
7) Bakır ve bakır alaşımlı kaynak çubukları, bakır ve bakır alaşımlarının kaynağı, onarım kaynağı veya sert dolgu için kullanılır ve ayrıca belirli dökme demirlerin onarım kaynağı veya benzer olmayan malzemelerin kaynağı için de kullanılabilir. metaller.
8) Alüminyum ve alüminyum alaşımlı kaynak çubukları, alüminyum ve alüminyum alaşımlarının kaynağı, onarım kaynağı veya sert yüzey kaplaması için kullanılır.
9) Özel amaçlı kaynak çubukları su altı kaynağı, kesme ve boru kaynağı vb. için kullanılır.
(2) Elektrot kaplamasının eritilmesinden sonra oluşan cürufun özelliklerine göre sınıflandırma
Kaynak işlemi sırasında, elektrot kaplaması eridikten sonra elektrotlar, ortaya çıkan cürufun asidik veya bazik olmasına bağlı olarak bazik elektrotlar (cüruf bazikliği ≥1,5) ve asidik elektrotlar (cüruf bazikliği ≤1,5) olarak ayrılır. Asidik ve bazik elektrotların proses performansı ve kaynak metali özelliklerinin karşılaştırması Tablo 5-7'de gösterilmiştir. Asidik elektrotlar yüksek alaşım elementleri içeren malzemelerin kaynağı için uygun değildir. Asidik elektrotlara göre daha iyi plastisite, tokluk ve çatlama direncine sahip olan bazik elektrotlar genellikle önemli bileşenlerin kaynağında kullanılır.
Tablo 5-7 Asidik ve bazik elektrotlar arasında proses performansı ve kaynak metali özelliklerinin karşılaştırılması
Karşılaştırma Öğesi | Asidik Elektrotlar | Temel Elektrotlar |
---|---|---|
Süreç Performansı | Hem AC hem de DC ile çalışan kararlı bir ark ile başlatması kolay; güçlü gözeneklilik direnci ile pas, yağ ve neme karşı daha az hassas; elektrotlar kullanımdan önce 75-150 ° C'de 1 saat önceden ısıtılmalıdır; minimum sıçrama ve iyi cüruf giderme; daha az kaynak dumanı | Flukstaki oksitler gaz iyonizasyonunu etkileyerek daha zayıf ark kararlılığına neden olur ve sadece DC ile kullanılabilir; su ve pasın neden olduğu gözenekliliğe karşı daha hassastır, kullanımdan önce 350-400°C'de 1 saat ön ısıtma gerektirir; daha fazla sıçrama ve biraz daha zayıf cüruf giderme; daha fazla kaynak dumanı |
Kaynak Metal Özellikleri | Daha fazla alaşım elementi yanması ile sıradan ortam ve düşük sıcaklık darbe performansı; zayıf kükürt giderme etkisi ve sıcak çatlamaya karşı düşük direnç | İyi ortam ve düşük sıcaklık darbe performansı; iyi plastisite ve tokluğa sahip etkili alaşım elementi geçişi; hala iyi düşük sıcaklık darbe tokluğu sergiler; güçlü deoksidasyon ve kükürt giderme yetenekleri, kaynakta düşük hidrojen, oksijen ve kükürt içeriği ve iyi çatlak direnci ile sonuçlanır |
2. Elektrotlar için gereklilikler ve seçim ilkeleri
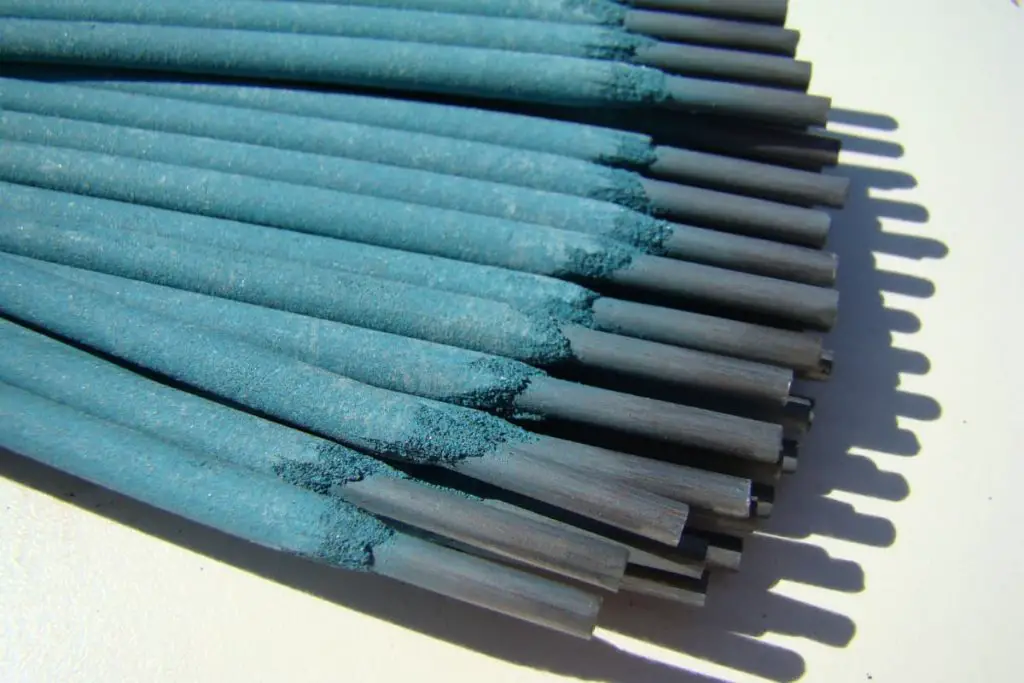
(1) Elektrotlar için temel gereklilikler
Kaynak işlemi sırasında, elektrotlar iyi bir işlem performansına sahip olmalı ve kaynaklı metalin gerekli mekanik özelliklere, kimyasal bileşime veya özel özelliklere sahip olmasını sağlamalıdır. Bu nedenle elektrotlar için aşağıdaki gereklilikler önerilmektedir:
1) Arkın tutuşması kolay olmalı, kaynak işlemi sırasında sabit bir şekilde yanmalı ve yeniden tutuşması kolay olmalıdır.
2) Akı kaplaması topaklanmadan veya düşmeden eşit şekilde erimelidir. Akı kaplamanın erime hızı, çekirdek telinkinden biraz daha yavaş olmalı ve elektrotun erime ucunun, metal damlacıklarının geçişine ve koruyucu bir atmosferin oluşturulmasına elverişli olan çan şeklinde bir manşon oluşturmasına izin vermelidir.
3) Kaynak işlemi sırasında aşırı duman veya çok büyük ya da çok fazla sıçrama olmamalıdır.
4) Depolanan metalin belirli çatlak direncine, gerekli mekanik özelliklere ve kimyasal bileşime sahip olduğundan emin olun.
5) Normal kaynak oluşumu ve kolay cüruf giderimi sağlayın.
6) Kaynak dikişinin radyografik muayenesi GB/T 3323-2005 "Metal Füzyon Kaynaklı Bağlantıların Radyografik Fotoğraflanması "nda belirtilen Seviye II standardından daha düşük olmamalıdır.
(2) Elektrot seçimi için prensipler
1) Kaynak metalinin performans gereksinimleri.
Yapısal çelik kaynakları için, aynı tip çeliği kaynaklarken, elektrotları çeliğin gerilme mukavemetine uygunluk ilkesine göre seçin;
Farklı çelik türlerini kaynaklarken, daha düşük mukavemetli tarafa göre seçim yapın;
Isıya dayanıklı çelik kaynağı için, kaynak metalinin sadece oda sıcaklığı performansını dikkate almakla kalmayın, aynı zamanda yüksek sıcaklık performansına göre seçim yapın;
Paslanmaz çelik kaynağı için, kaynak bileşiminin ana malzeme bileşimi ile uyumlu olduğundan emin olun, böylece kaynaklı bağlantının özel performansı sağlanır.
2) Kaynaklı parçaların çalışma koşullarını göz önünde bulundurun.
Yüksek veya düşük sıcaklık koşullarında çalışan kaynaklı parçalar için ısıya dayanıklı çelik elektrotlar veya düşük sıcaklık çelik elektrotları kullanılmalıdır;
Aşınma direnci ve çizilme direnci gerektiren kaynaklı parçalar için, çalışma sıcaklıklarına göre oda sıcaklığında veya yüksek sıcaklıkta sertliğe ve iyi çizilme direncine, oksidasyon önleyici ve diğer özelliklere sahip elektrotlar seçin;
Korozif ortamla temas eden kaynaklı parçalar için paslanmaz çelik elektrotlar veya diğer korozyona dayanıklı elektrotlar kullanın; titreşim veya darbe yüklerine maruz kalan kaynaklı parçalar için, çekme mukavemetini sağlamanın yanı sıra, daha yüksek plastisite ve tokluğa sahip düşük hidrojenli elektrotlar da seçin;
Sadece statik yüklere maruz kalan kaynaklı parçalar için, ana malzemeyle karşılaştırılabilir gerilme mukavemetine sahip elektrotları seçin.
3) Kaynaklı parçaların şeklini, sertliğini ve kaynak pozisyonunu göz önünde bulundurun.
Karmaşık, sert kaynaklı parçalar için, kaynak metalinin büzülmesiyle oluşan büyük stres nedeniyle, daha iyi plastisiteye sahip elektrotlar kullanılmalıdır; aynı tip elektrot seçerken, sadece mekanik özellikleri değil, aynı zamanda kaynaklı bağlantının şeklinin etkisini de göz önünde bulundurun.
Çünkü, alın bağlantılarını kaynaklarken, mukavemet ve plastiklik orta düzeydeyse, köşe kaynaklarını kaynaklarken, mukavemet yüksek ve plastiklik düşük olacaktır; temizlenmesi zor kaynaklı parçalar için, kaynak kalitesini sağlamak için oksitleyici, pas ve yağa duyarlı olmayan asit elektrotları kullanın.
4) Kaynak metalinin çatlama direncini göz önünde bulundurun.
Kaynaklı parçanın sertliği yüksek olduğunda, ana malzemedeki karbon, sülfür ve fosfor içeriği yüksek olduğunda veya dış sıcaklık düşük olduğunda, kaynaklı parça çatlamaya eğilimlidir. Kaynak için daha yüksek çatlak direncine sahip bir alkali elektrot seçmek en iyisidir.
5) Elektrotun çalışabilirliğini göz önünde bulundurun.
Kaynak işlemi sırasında ark kararlı olmalı, minimum sıçrama, düzgün ve simetrik kaynak oluşumu, kolay cüruf giderme ve her pozisyonda kaynak için uygun olmalıdır.
Hem asit hem de alkalin elektrotların gereksinimleri karşıladığı durumlarda, mümkün olduğunca iyi çalışabilirliğe sahip asit elektrotlar kullanılmalıdır, ancak öncelikle kaynağın performansı ve çatlama direnci sağlanmalıdır.
6) Ekipman ve inşaat koşullarını göz önünde bulundurun.
DC kaynak makinesinin olmadığı durumlarda DC güçle sınırlı elektrotlar kullanılmamalı, bunun yerine hem AC hem de DC'ye uygun düşük hidrojenli elektrotlar seçilmeli; iş parçasının döndürülemediği ve her pozisyonda kaynak yapılması gerektiği durumlarda çeşitli uzaysal pozisyonlara uyum sağlayabilen elektrotlar seçilmelidir.
Dikey ve baş üstü kaynak için, elektrotların titanyum tipi ve ilmenit tipi kaplamalar sırasına göre seçilmesi önerilir.
Kapalı bir kapta veya dar bir ortamda kaynak yaparken, havalandırmayı artırmanın yanı sıra, alkali düşük hidrojenli elektrotları kullanmaktan da mümkün olduğunca kaçınmak gerekir, çünkü bu elektrotlar kaynak sırasında büyük miktarda zararlı gaz ve toz açığa çıkarır.
Kaynak sonrası ısıl işlem gerektiren ancak yapı koşulları nedeniyle ısıl işlem uygulanamayan bazı iş parçaları için (perlitik ısıya dayanıklı çelik gibi), kaynak sonrası ısıl işlemden kaçınmak için özel elektrotlar seçilebilir.
7) Ekonomik rasyonaliteyi göz önünde bulundurun.
Kaynağın performans gereksinimlerini sağlayan aynı koşullar altında, daha düşük maliyetli elektrotlar seçilmelidir.
Örneğin, ilmenit tipi elektrotların maliyeti titanyum kalsiyum tipi elektrotlara göre çok daha düşüktür ve performansın sağlanması öncülünde ilmenit tipi elektrotlar seçilmelidir. Ek olarak, performans ve çalışabilirliği karşılama öncülü altında, daha büyük özelliklere ve daha yüksek verime sahip elektrotlar uygun şekilde seçilmelidir.
3. Elektrotların kullanımı
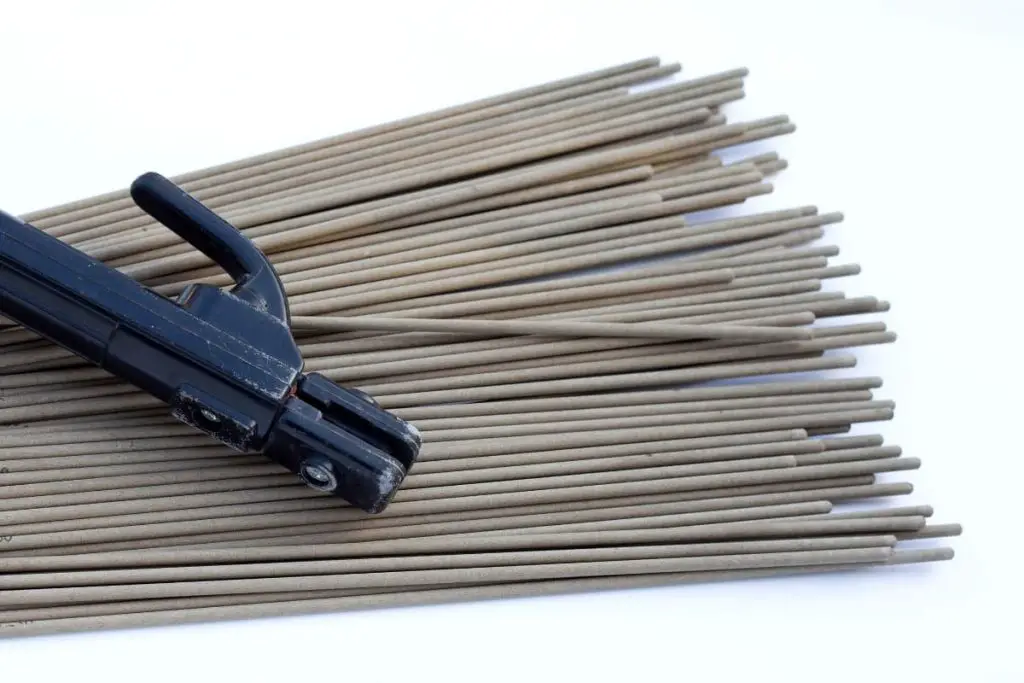
Elektrotların üreticiden alınmış kalite sertifikası olmalı, kalite sertifikası yoksa veya kalitesi konusunda şüpheler varsa parti örnekleme testleri yapılmalıdır.
Özellikle önemli ürünlerin kaynağında, seçilen elektrotlar kaynak öncesinde tanımlanmalı ve uzun süre depolananlar da kullanılıp kullanılamayacağına karar verilmeden önce tanımlanmalıdır.
Elektrotun içinde pas bulunursa, kullanılmadan önce test edilmeli ve nitelikli olduğu belirlenmelidir. Elektrot kaplaması aşırı derecede nemliyse ve kaplamada ayrılma gözleniyorsa, hurdaya çıkarılmalıdır.
Elektrotlar genellikle kullanılmadan önce kılavuzda belirtilen sıcaklıkta kurutulmalıdır. Elektrotlar kurutulurken aşağıdaki noktalara dikkat edilmelidir:
1) Selüloz elektrotlar kullanılmadan önce 100~200°C'de 1 saat kurutulmalı, selüloz yanmaya eğilimli olduğundan aşırı ısınmamasına dikkat edilmelidir.
2) Asit elektrotlar nemlilik derecesine bağlı olarak 70~150°C'de 1~2 saat kurutulmalıdır. Depolama süresi kısaysa ve ambalaj sağlamsa, kullanmadan önce daha fazla kurutmadan genel yapısal çelik kaynağı için kullanılabilirler.
3) Alkali elektrotlar genellikle 350~400°C'de 1~2 saat süreyle kurutulur. Kaynak yapılan düşük alaşımlı çelik soğuk çatlamaya yatkınsa, kurutma sıcaklığı 400~450°C'ye çıkarılabilir ve hemen kullanım için 100~150°C'lik bir ısıtma silindirinde tutulabilir.
4) Elektrotları kuruturken, elektrotları fırına daha düşük bir sıcaklıkta yerleştirin ve sıcaklığı kademeli olarak artırın.
Yüksek sıcaklıktaki bir fırından doğrudan çıkarmayın; soğuk elektrotların yüksek sıcaklıktaki bir fırına yerleştirilmesi veya ani soğutma nedeniyle kaplamanın çatlamasını önlemek için çıkarmadan önce fırın sıcaklığının düşmesini bekleyin.
5) Kaynak çubukları kurutulurken, istiflenmemeli veya paketlenmemeli, ancak her katman çok kalın olmayacak şekilde, genellikle 1 ~ 3 katman olacak şekilde katmanlar halinde yerleştirilmelidir.
6) Düşük hidrojenli kaynak çubukları, düşük sıcaklıklı bir fırında sabit sıcaklıkta tutulanlar hariç, genellikle oda sıcaklığında 4 saatten fazla kalmışlarsa yeniden kurutulmalıdır. Yeniden kurutma sürelerinin sayısı 3'ü geçmemelidir.
7) Açık havada çalışırken, kaynak çubukları gece boyunca uygun şekilde saklanmalı ve açık havada bırakılmasına izin verilmemelidir.
4. Kaynak çubuklarının yönetimi
(1) Kaynak çubuklarının depolanması ve muhafazası
1) Kaynak çubukları türüne, markasına, partisine, özelliklerine ve depolama süresine göre depolanmalı ve karışıklığı önlemek için her istif açıkça işaretlenmelidir.
2) Kaynak çubukları kuru ve iyi havalandırılan kapalı bir ortamda depolanmalıdır. Kaynak çubukları için depolama odasına bir termometre ve higrometre yerleştirilmelidir. Düşük hidrojenli kaynak çubukları için oda sıcaklığı 50°C'den düşük olmamalı ve bağıl nem 60%'nin altında olmalıdır.
3) Kaynak çubukları, raf yüksekliği yerden en az 300 mm ve duvarlardan en az 300 mm olacak şekilde raflarda depolanmalıdır. Nemi önlemek için rafların altına kurutucu maddeler yerleştirilmelidir.
4) Kullanıcı birimine tedarik edildikten sonra, kaynak çubuklarının en az 6 ay boyunca sürekli kullanımı garanti edilmeli ve kaynak çubuklarının verilmesinde ilk önce depolananlara öncelik verilmelidir.
5) Nemli veya ambalajı hasarlı olan kaynak çubuklarının ve yeniden muayeneden geçemeyenlerin depoda saklanmasına izin verilmez.
6) Nemli, renksiz veya paslı kaynak çubukları kalite değerlendirmesinden önce kurutulmalıdır. Sadece tüm performans standartlarını karşılıyorlarsa depolanabilirler, aksi takdirde depolanmalarına izin verilmez.
7) Bir yıldan uzun süre depolanan kaynak çubukları dağıtılmadan önce çeşitli performans testlerinden geçirilmelidir. Sadece gereklilikleri karşılamaları halinde dağıtılabilirler, aksi takdirde depodan çıkarılmamalıdırlar.
8) Önemli kaynak projelerinde kullanılan kaynak çubukları, özellikle düşük hidrojenli çubuklar, ideal olarak belirli sıcaklık ve nem seviyelerini koruyan özel bir depoda saklanmalıdır. Önerilen sıcaklık 10~25°C, bağıl nem <50%'dir.
(2) İnşaat sırasında kaynak çubuklarının yönetimi
1) İnşaat sırasında, kaynak çubukları, kaynak çubuğu talep formu ile depodan alan atanmış bir kişi tarafından yönetilmelidir.
Formda çubukları alan kişinin adı, kaynak çubuğunun türü (markası), çapı, alınan miktar, ana birimden sorumlu kişinin imzası, talep tarihi ve üretici, üretim partisi, üretim tarihi ve depolama tarihi ile ilgili notlar yer almalıdır.
2) Kaynak çubuklarını aldıktan sonra, temel üretim birimi, üretici, üretim partisi, kaynak çubuğunun türü (markası), çapı ve alınan miktar gibi ayrıntıları içeren bir kaynak çubuğu depolama defteri doldurmalıdır.
Çubuklar kullanılmadan önce kurutulmalı ve bu işlem sırasında bir kurutma kaydı doldurulmalıdır. Kaydın ana içeriği üretici, kaynak çubuğunun tipi (markası), üretim partisi, çapı, kurutma sıcaklığı, kurutma süresi, kurutulan çubuk miktarı, kurutmadan sorumlu kişinin ve denetçinin imzalarını içerir.
Bu belge kayıt tutma amacıyla üç nüsha olarak hazırlanmalıdır. Kurutulduktan sonra, çubuklar kaynakçılara verilebilir, kaynakçılar kurutulmuş çubuklar için üretici, tip (marka), parti, çap, miktar, talep zamanı ve çubukları alan kişinin imzası gibi ayrıntıları içeren bir talep formu doldurmalıdır.
Notlarda çubukların hangi iş parçalarında hangi kaynaklar için kullanıldığı belirtilmelidir. Çubukları teslim alırken, kaynakçılar kurutma sertifikası belgelerini temel depolama sorumlusundan talep etmelidir. Kurutma belgeleri olmayan çubuklar kaynakçılara verilmemelidir.
3) Kurutulmuş kaynak çubuklarını aldıktan sonra, kaynakçılar bunları bir kaynak çubuğu yalıtım silindirine yerleştirmelidir.
Karışmayı ve olası kaynak kalitesi olaylarını önlemek için silindir başına yalnızca bir tür (marka) çubuğa izin verilir. Kaynakçılar bir seferde 5 kg'dan fazla çubuk almamalı ve kalan çubuklar atölye malzeme odası veya şantiye malzeme ekibi tarafından uygun şekilde depolanmalıdır.
(3) Son kullanma tarihi geçmiş kaynak çubuklarının kullanımı
"Son kullanma tarihi geçmiş" belirli bir saklama süresi sınırının aşılması anlamına gelmez, daha ziyade çeşitli derecelerde kalite bozulması (bozulma) anlamına gelir. İyi saklanmış kaynak çubukları uzun yıllar boyunca değişmeden kalabilir.
1) Uzun yıllar depolanan kaynak çubukları proses performans testlerinden geçirilmelidir. Testten önce, alkali düşük hidrojenli çubuklar yaklaşık 300°C'de 1~2 saat, asidik çubuklar ise yaklaşık 150°C'de 1~2 saat kurutulmalıdır.
Proses performans testi sırasında, flaks parçalar halinde çıkmazsa ve alkali düşük hidrojenli çubuklar gözeneklilik göstermezse, kaynaklı bağlantıların mekanik özellikleri genellikle garanti edilir.
2) Kaynak çubuğu çekirdeği, genellikle mekanik özelliklerini etkilemeyen hafif bir pasa sahiptir, ancak düşük hidrojenli elektrotlar kritik yapıların kaynağı için kullanılmamalıdır.
3) Düşük hidrojenli elektrotlarda ciddi pas varsa veya eritken kaplama soyuluyorsa, uygun şekilde dereceleri düşürülebilir veya genel bileşenlerin kaynağı için kullanılabilirler. Mümkünse, mekanik özellikleri, kalitelerinin düşürülüp düşürülmeyeceğine karar vermeden önce ulusal standartlara göre test edilebilir.
4) Çeşitli kaynak çubukları ciddi şekilde bozulmuşsa, yeniden kullanılmamalıdır; akı kaplaması çıkarılmalı ve çekirdek tel yeniden kullanım için temizlenebilir.