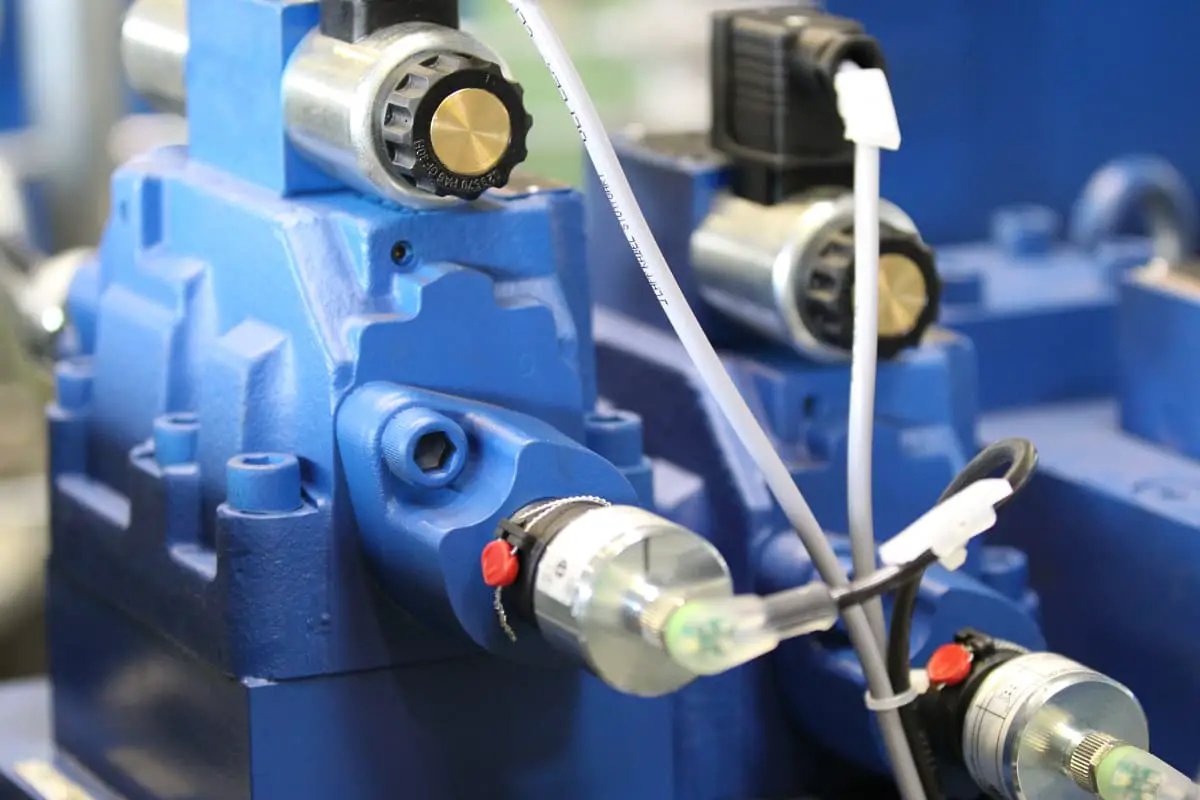
I. Pnömatik Sistemlerin Kurulumu
1. Boru Hatlarının Kurulumu
- Kurulumdan önce, boru hattının iç duvarının pürüzsüz olup olmadığını kontrol edin ve pası giderin ve temizleyin.
- Boru hattı destekleri sağlam olmalı ve çalışma sırasında titreşmemelidir.
- Tüm bağlantıları sıkın ve boru hattı hava sızdırmamalıdır.
- Boru hattı kaynağı belirtilen standart koşulları karşılamalıdır.
- Hortumları monte ederken, uzunlukları belirli bir marja sahip olmalıdır; bükerken, bükmeye uç eklemden başlamayın; düz bölümleri monte ederken, uç eklem ile hortum arasında germeyin; hortumlar ısı kaynaklarından mümkün olduğunca uzağa monte edilmeli veya ısı kalkanları takılmalıdır; boru hattı sisteminin herhangi bir bölümü çıkarılabilir olmalıdır; eğim, bükülme yarıçapıBoru hattı kurulumunun aralıkları ve eğimi ilgili yönetmeliklere uygun olmalıdır.
2. Bileşenlerin Kurulumu
- Kurulumdan önce bileşenleri temizleyin ve gerekirse sızdırmazlık testleri yapın.
- Çeşitli vana gövdeleri üzerindeki okların veya işaretlerin yönü hava akışının yönüne uygun olmalıdır.
- Mantıksal bileşenler, kontrol devresinin ihtiyaçlarına göre gruplandırılmalı ve taban plakasına monte edilmeli ve hava devresi taban plakasına yönlendirilmeli ve hortumlarla bağlanmalıdır.
- Sızdırmazlık halkasını, özellikle V şeklindeki sızdırmazlık halkasını çok sıkı takmayın, çünkü yüksek dirence sahiptir, bu nedenle sıkılık uygun olmalıdır.
- Hareketli silindirin merkez çizgisi ile silindirin merkez çizgisi yük kuvveti eş merkezli olmalıdır, aksi takdirde yanal kuvvete neden olur, sızdırmazlık parçalarının aşınmasını hızlandırır ve piston kolunu büker.
- Çeşitli otomatik kontrol aletleri, otomatik kontrolörler, basınç röleleri vb. kurulumdan önce kalibre edilmelidir.
II. Sistem Yıkama ve Basınç Testi
Boru hattı sistemi kurulduktan sonra, sistemdeki tüm kirleri dışarı üflemek için 0,6MPa basınçlı kuru hava kullanın. Kontrol etmek için beyaz bir bez kullanın ve 5 dakika içinde kirlilik yoksa yeterlidir. Üfledikten sonra, valf çekirdekleri, filtre elemanları ve pistonlar gibi parçaları sökün ve temizleyin.
Sistemin sızdırmazlığının standartlara uygun olup olmadığını kontrol etmek için, sistemi genellikle nominal basıncın 1,2 ila 1,5 katında bir süre (örneğin 2 saat) tutarak bir hava sızdırmazlık testi gerçekleştirin. Çevresel sıcaklık değişimlerinden kaynaklanan hatalar hariç olmak üzere, basınç değişimi teknik belgelerde belirtilen değeri aşmamalıdır. Test sırasında emniyet valfini test basıncına ayarlayın.
Basınç testi sırasında, adım adım test yöntemi kullanmak ve her zaman güvenliğe dikkat etmek en iyisidir. Sistemde herhangi bir anormallik bulunursa, testi derhal durdurun, nedenini bulun, arızayı giderin ve ardından teste devam edin.
III. Sistem Hata Ayıklama
1. Hata Ayıklama Öncesi Hazırlıklar
- Sistemin prensiplerini, yapısını, performansını ve çalıştırma yöntemlerini tam olarak anlamak için kılavuza ve diğer ilgili teknik materyallere aşina olun.
- Ekipman üzerinde ayarlanması gereken bileşenlerin gerçek konumunu, çalıştırma yöntemlerini ve ayar düğmelerinin yönünü anlayın.
- Hata ayıklama araçlarını, aletlerini hazırlayın ve kılavuzun gerektirdiği şekilde test boru hatlarını bağlayın.
2. Yüksüz Deneme Çalışması
Yüksüz deneme çalışması 2 saatten az olmamalıdır. Basınç, akış ve sıcaklıktaki değişikliklere dikkat edin. Herhangi bir anormal durum tespit edilirse, inceleme için makineyi derhal durdurun ve ancak arıza giderildikten sonra çalışmaya devam edin.
3. Yük Deneme İşlemi
Yük deneme işlemi aşamalı olarak gerçekleştirilmeli ve işlem 2 saatten az olmamalıdır. Sürtünme parçalarının sıcaklık artışına dikkat edin, ilgili verileri ayrı ayrı ölçün ve test çalıştırma günlüğüne kaydedin.
IV. Pnömatik Sistemin Kullanımı ve Bakımı
1. Kullanım Sırasında Alınacak Önlemler
- Sürüşten önce ve sonra sistemdeki yoğuşma suyunu boşaltın ve sürüşten önce tüm ayar düğmelerinin doğru konumda olup olmadığını kontrol edin. Hareket valfinin, hareket anahtarının ve durdurucunun konumlarının doğru ve güvenli olduğundan emin olun. Kılavuz raylar ve piston çubukları gibi açıkta kalan parçaların eşleşme yüzeylerini silin.
- Basınçlı havanın temizliğine her zaman dikkat edin. Su separatörünün filtre elemanını düzenli olarak temizleyin ve yağ buharı cihazına düzenli olarak yağ ekleyin.
- Ekipman uzun süre kullanılmadığında, yay arızasının bileşen performansını etkilemesini önlemek için tüm düğmeleri gevşetin.
- Yanlış ayarlamalardan kaynaklanan kazaları önlemek için bileşen kontrol mekanizmalarının çalışma özelliklerini öğrenin. Her bir bileşenin ayar düğmesinin dönüş yönü ile basınç ve akış hızındaki değişiklikler arasındaki ilişkiye dikkat edin.
2. Basınçlı Hava Kirliliği ve Önlenmesi
Basınçlı havanın kalitesi, pnömatik sistemin performansını büyük ölçüde etkiler. Kirlenmişse boru hattı ve bileşen korozyonuna, conta deformasyonuna ve nozül tıkanmasına neden olarak sistemin düzgün çalışmasını engelleyebilir. Basınçlı hava kirliliğinin ana kaynakları nem, yağ ve tozdur.
(1) Nem
Hava kompresörü su içeren nemli havayı solur. Sıkıştırmadan sonra basınç artar ve tekrar soğuduğunda yoğuşma çökelir, basınçlı havaya sızar ve boru hattı ve bileşen korozyonuna neden olarak performanslarını etkiler.
Yoğuşma suyunun basınçlı havaya sızmasını önleme yöntemleri şunlardır:
- Sistemin tahliye vanalarında biriken yoğuşma suyunun zamanında boşaltılması.
- Otomatik tahliye ve kurutucunun düzgün çalışıp çalışmadığını düzenli olarak kontrol edin.
- Su ayırıcının ve otomatik tahliyenin iç bileşenlerini düzenli olarak temizleyin.
(2) Petrol
Bu, ısı nedeniyle bozulmuş kullanılmış yağlama yağını ifade eder. Hava kompresörü tarafından kullanılan yağlama yağının bir kısmı buğu şeklinde basınçlı havaya karışır, ısıtıldığında buharlaşır ve basınçlı havayla birlikte sisteme girerek conta deformasyonuna, hava sızıntısına, sürtünme direncinin artmasına, zayıf valf ve aktüatör performansına ve çevre kirliliğine neden olur.
Basınçlı havadan yağı çıkarma yöntemleri şunları içerir: yağ-su ayırıcıları ve su ayırıcıları kullanarak daha büyük yağ partiküllerini havadan ayırmak ve bunları ekipmanın tahliye vanasından boşaltmak. Daha küçük yağ partikülleri aktif karbon tarafından adsorpsiyon yoluyla giderilebilir.
(3) Toz
Atmosferdeki toz, boru hatlarındaki pas parçacıkları ve sızdırmazlık malzemelerinden kaynaklanan kalıntılar basınçlı havaya sızarak hareketli parçaların sıkışmasına, arızalanmasına, nozüllerin tıkanmasına, bileşen aşınmasının hızlanmasına, hizmet ömrünün kısalmasına ve arızalara yol açarak sistem performansını ciddi şekilde etkileyebilir.
Tozun basınçlı havaya sızmasını önlemek için başlıca yöntemler şunlardır:
- Hava kompresörünün önündeki ön filtreyi düzenli olarak temizleyin.
- Su ayırıcının filtre elemanını düzenli olarak temizleyin.
- Filtre elemanlarının zamanında değiştirilmesi.
3. Pnömatik Sistemin Günlük Bakımı
Pnömatik sistemin günlük bakımı temel olarak yoğuşma suyunun yönetilmesini ve sistem yağlamasını içerir.
(1) Kondensat Yönetimi
Yoğuşma suyu tahliyesi, hava kompresörü, son soğutucu, hava tankı, boru hattı sistemi, çeşitli hava filtreleri, kurutucular ve otomatik drenajlara kadar tüm pnömatik sistemi kapsar. Operasyonların sonunda, gece sıcaklıklarının 0°C'nin altına düşmesi nedeniyle donmayı önlemek için kondensi tüm konumlardan boşaltın.
Boru hattının içindeki sıcaklık geceleri düştüğünden ve yoğuşma suyunu daha da çökelttiğinden, günlük çalışmadan önce yoğuşma suyunu pnömatik cihazdan boşaltın. Otomatik tahliyenin düzgün çalışıp çalışmadığını kontrol edin ve su kabının aşırı su içermediğinden emin olun.
(2) Sistem Yağlamasının Yönetimi
Pnömatik sistemde, kontrol bileşenlerinden aktüatörlere kadar göreceli hareket eden tüm yüzeyler yağlama gerektirir. Yanlış yağlama sürtünme direncini artırabilir, düşük bileşen performansına neden olabilir veya sızdırmazlık yüzeylerindeki aşınma nedeniyle sistem sızıntısına yol açabilir.
Yağlama yağının özellikleri yağlama etkisini doğrudan etkileyecektir. Genel olarak, yüksek viskoziteli yağlama yağı yüksek sıcaklıklı ortamlarda, düşük viskoziteli yağlama yağı ise düşük sıcaklıklı ortamlarda kullanılır. Sıcaklık özellikle düşükse, buğulanma zorluğunun üstesinden gelmek için yağ kabına bir ısıtıcı takılabilir.
Yağ besleme miktarı, yağlama parçasının şekline, hareket durumuna ve yük boyutuna göre değişir. Yağ besleme miktarı her zaman gerçek gerekli miktardan daha fazladır. Yağ buharı jeneratörünün düzgün çalışıp çalışmadığına dikkat edin. Yağ miktarı azalmazsa, yağ damlama miktarını zamanında ayarlayın. Ayarlama etkisizse, yağ buharı jeneratörü onarılmalı veya değiştirilmelidir.
4. Pnömatik sistemin düzenli bakımı
Düzenli bakım aralığı genellikle üç aydır. Ana içerikler şunlardır:
(1) Sistemin kaçak kısımlarını belirleyin ve bunları çözmeye çalışın.
(2) Yön kontrol valfinin egzoz portunu kontrol ederek, yağlama yağı miktarının uygun olup olmadığını ve havada yoğuşma olup olmadığını belirleyin.
Yağlama zayıfsa, yağ buharı jeneratörünün özelliklerinin uygun olup olmadığını, montaj konumunun doğru olup olmadığını ve yağ damlama miktarının normal olup olmadığını göz önünde bulundurun. Büyük miktarda yoğuşma suyu tahliye ediliyorsa, filtrenin montaj konumunun uygun olup olmadığını, yoğuşma suyu tahliye cihazının uygun olup olmadığını ve yoğuşma suyunun tamamen tahliye edilip edilmediğini göz önünde bulundurun.
Yön kontrol valfinin egzoz portu kapatıldığında hala az miktarda sızıntı varsa, bu genellikle bileşen hasarının ilk aşamasıdır. İncelemeden sonra, arızayı önlemek için aşınmış parçalar değiştirilebilir.
(3) Emniyet valfinin ve acil durum emniyet anahtarının güvenilir bir şekilde çalışıp çalışmadığını kontrol edin. Düzenli bakım sırasında, ekipman ve kişisel güvenliği sağlamak için bunların çalışmasının güvenilirliği onaylanmalıdır.
(4) Yön valfinin çalışmasının güvenilir olup olmadığını gözlemleyin. Anahtarlama sırasında sesin anormal olup olmadığına bağlı olarak demir çekirdeğin ve armatürün eşleşen parçalarında kirlilik olup olmadığını belirleyin. Valf çekirdeğinin aşınıp aşınmadığını ve sızdırmazlık parçalarının eskiyip eskimediğini kontrol edin.
(5) Yön valfini tekrar tekrar değiştirin ve piston üzerindeki contanın iyi olup olmadığını belirlemek için silindirin çalışmasını gözlemleyin. Ön kapağın eşleşen kısmında sızıntı olup olmadığını belirlemek için piston kolunun açıkta kalan kısmını kontrol edin.
Yukarıdaki denetimlerin ve onarımların sonuçları, sorun giderme ve büyük onarımlarda kullanılmak üzere kaydedilmelidir.
Pnömatik sistemin revizyon aralığı bir yıl veya birkaç yıldır. Ana içerik, sistemin her bir bileşeninin ve parçasının performansını ve ömrünü kontrol etmek ve onarım aralığı içinde olası tüm arıza faktörlerini ortadan kaldırarak genellikle arızalanan parçalardaki bileşenleri onarmak veya değiştirmektir.