
Temel Teknik Resim Bilgisi
Ortografik Projeksiyon
Projeksiyon yöntemi, bir formun şeklini ve yapısını doğru ve eksiksiz bir şekilde temsil eder ve basitliği ve iyi ölçüm özellikleri nedeniyle mühendislik çizimlerinde yaygın olarak kullanılır.
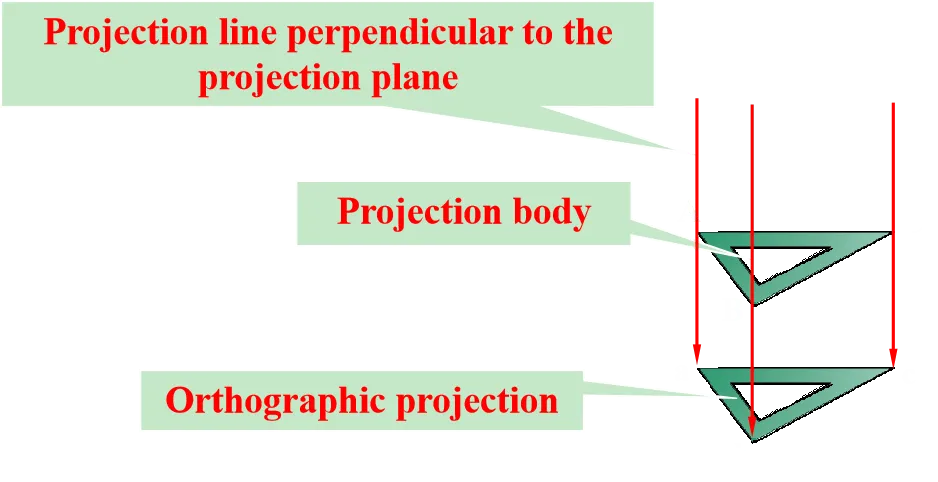
Üç Görünümlü Çizim
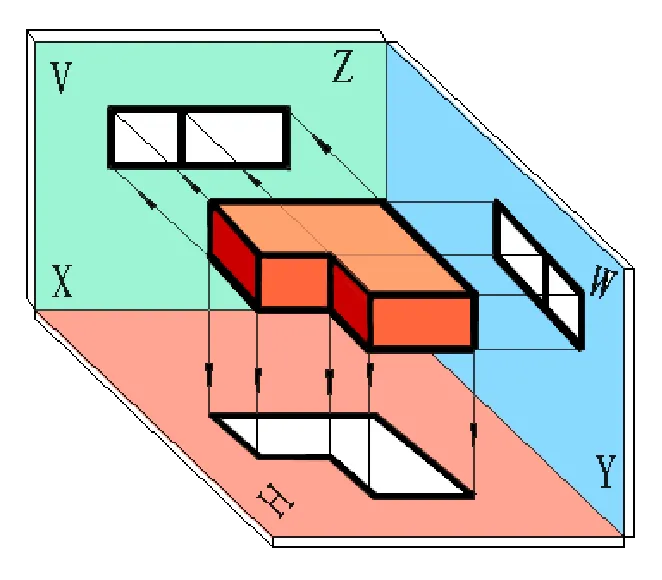
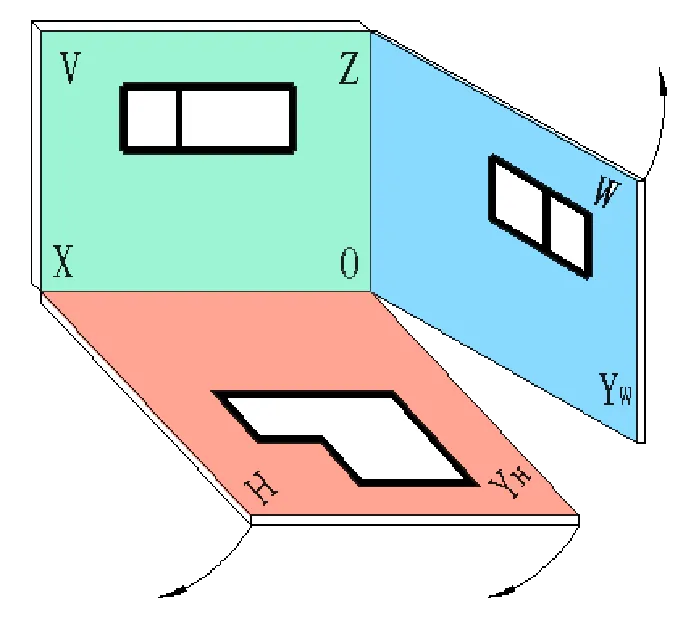
Üç görünümlü çizimin projeksiyon ilişkisi: uzunluk ön görünümde, yükseklik üst görünümde ve genişlik yan görünümde temsil edilir.
Temel Görünümler
Üç temel görünüme (önden görünüm, üstten görünüm, soldan görünüm) ek olarak, sağdan görünüm, alttan görünüm ve arkadan görünüm de ek görünümler arasındadır.
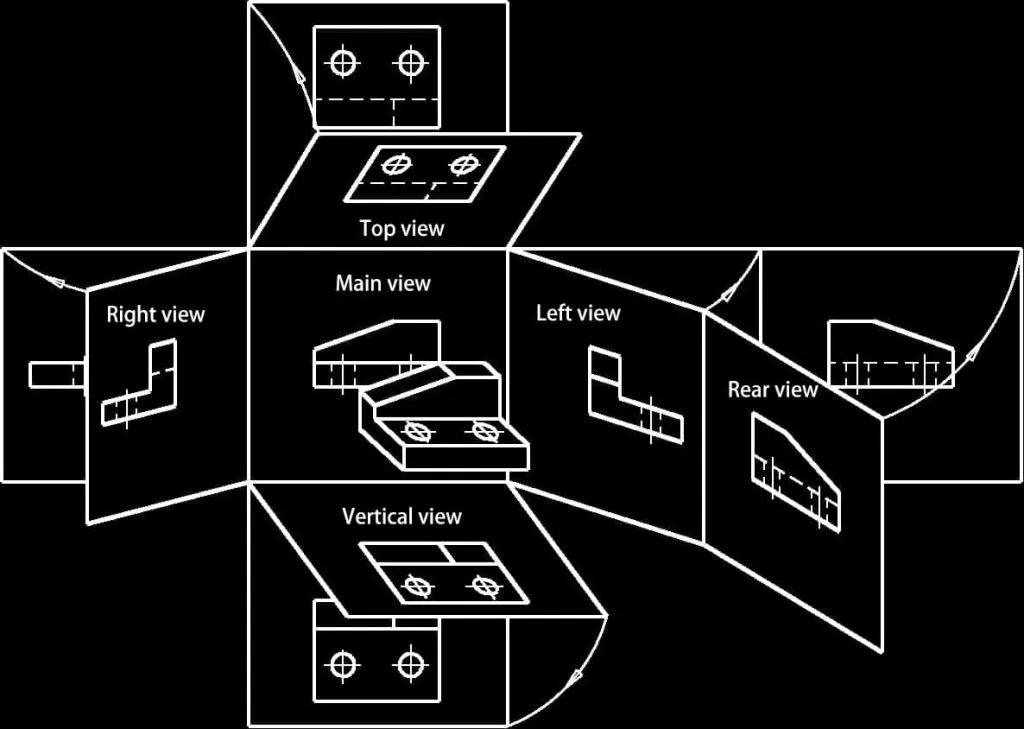
Kesit Görünümü
Görünümleri kullanarak bir makine parçasının iç yapısını ifade ederken, iç yapı kesikli çizgiler kullanılarak temsil edilir. İç yapının şekli ne kadar karmaşık olursa, görünümde o kadar fazla kesikli çizgi görünür, bu da çizimin netliğini etkileyebilir ve görüntüleme ve boyutlandırma için elverişsiz hale getirebilir.
Görünümdeki kesikli çizgilerin sayısını azaltmak ve netliği sağlamak için, makine parçasının iç yapısını ve şeklini temsil etmek üzere kesit görünüm yöntemi kullanılabilir.
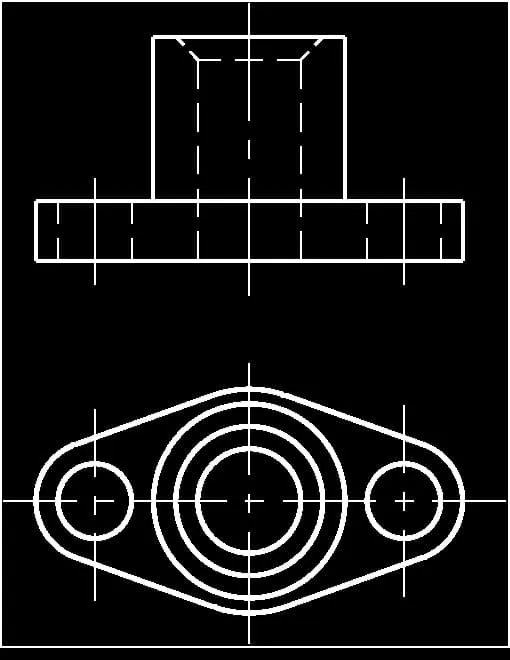
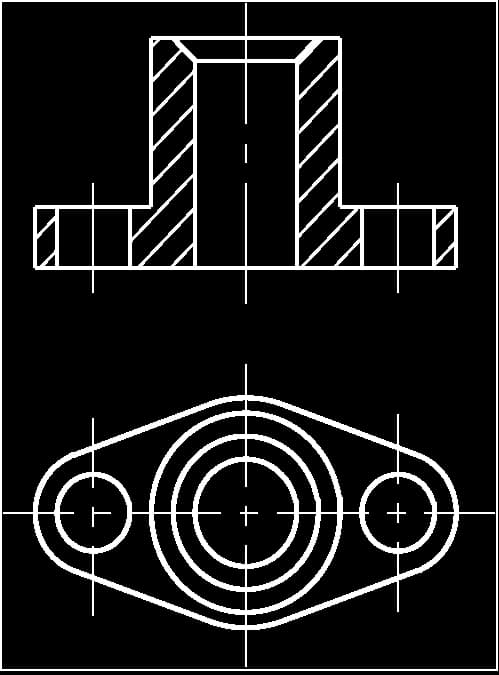
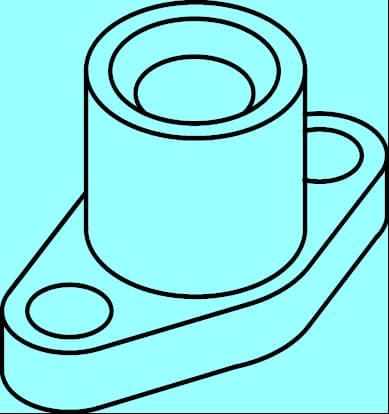
Yüzey Pürüzlülüğü ve Tolerans Uyumu
1. Yüzey Pürüzlülüğü
Yüzey pürüzlülüğü, bir parçanın işlenmiş yüzeyindeki küçük aralıklar ve tepe ve vadilerin oluşturduğu mikro-geometrik şekil hatalarını ifade eder.
Yüzey pürüzlülüğünü değerlendirmek için birincil parametre, profil aritmetik ortalama sapması Ra'dır.
- Profil aritmetik ortalama sapması-Ra
- Maksimum profil tepe-vadi yüksekliği-Rz
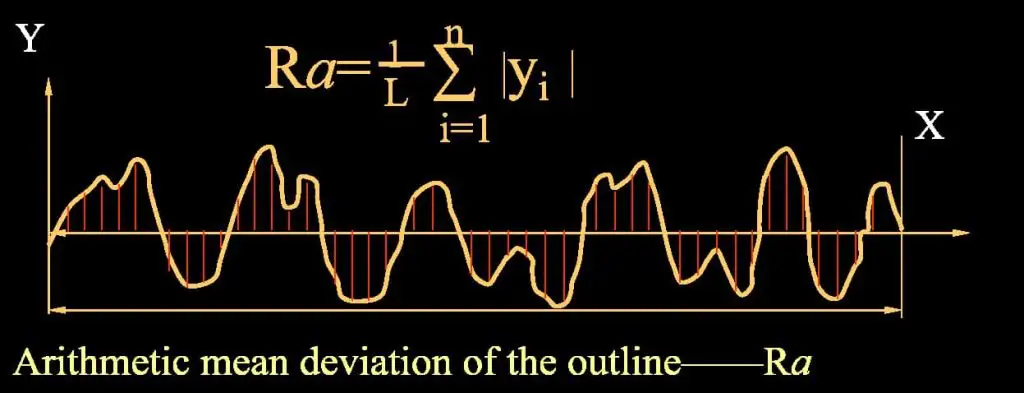
Yüzey pürüzlülüğü sembolü
sembolü | Anlamı ve Tanımı: |
![]() | Herhangi bir yöntemle elde edilen yüzey (tek başına kullanıldığında anlamsızdır) |
![]() | Malzeme kaldırma yöntemleri ile elde edilen yüzey |
![]() | Malzeme kaldırma yöntemleri ile elde edilen yüzey |
![]() | İlgili parametreleri ve açıklamaları belirtmek için kullanılan yatay çizgi |
![]() | Tüm yüzeylerin aynı yüzey pürüzlülüğü gereksinimine sahip olduğunu gösterir |
Yüzey Pürüzlülüğü Gösterim Örneği:
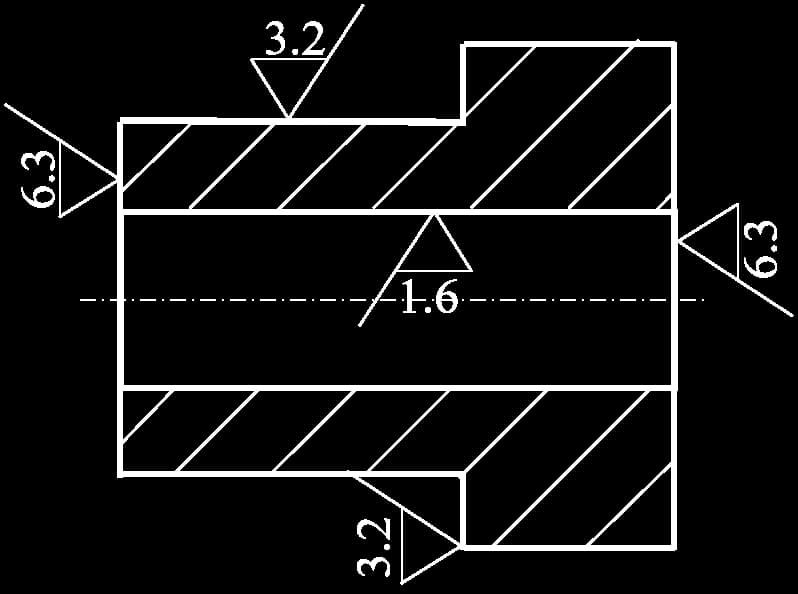
Bir parçanın çoğu yüzeyi aynı pürüzlülük gereksinimine sahip olduğunda, en yaygın olarak kullanılanın sembolü, "diğerleri" kelimesinin eklenmesiyle birlikte çizimin sağ üst köşesinde tek tip olarak belirtilebilir.
Örneğin:
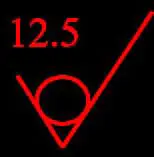
Yüzey pürüzlülüğü parametresinin birimi μm'dir.
2. Tolerans Uyumu
Temel Kavramlar ve İsimlendirme
- Temel boyut: Tasarım sırasında belirlenen boyut.
- Gerçek boyut: Parça üretildikten sonra ölçülen boyut.
- Sınır boyut: Parçadaki gerçek boyut varyasyonuna izin veren iki sınır değer.
- Maksimum sınır boyutu: Gerçek boyut için izin verilen maksimum değer.
- Minimum sınır boyutu: Gerçek boyut için izin verilen minimum değer.
Parça kabulü için koşul: Maksimum sınır boyutu > gerçek boyut > minimum sınır boyutu.
Örnek:
- Bir şaftın çapı Φ50±0,008'dir
- Temel boyut: Φ50
- Maksimum sınır boyutu: Φ50.008
- Minimum sınır boyutu: Φ49.992
Parça kabulü için koşul: Φ50.008 ≥ gerçek boyut ≥ Φ49.992.
Boyutsal Sapma ve Tolerans, Tolerans Bölgesi Diyagramı
Üst sapma = Maksimum sınır boyutu - Temel boyut
Alt sapma = Minimum sınır boyutu - Temel boyut
Boyutsal tolerans (tolerans olarak anılır): Gerçek boyutlarda izin verilen varyasyon.
Tolerans = Maksimum sınır boyutu - Minimum sınır boyutu= Üst sapma - Alt sapma
Örnek: Φ50±0.008
Üst sapma = 50,008 - 50 = +0,008 (sapma pozitif veya negatif olabilir)
Düşük sapma = 49.992 - 50 = -0.008
Tolerans = 0,008 - (-0,008) = 0,016 (tolerans her zaman pozitiftir)
Uyuyor
(1) Uyum kavramı: Aynı temel boyutlara sahip deliklerin ve şaftların tolerans bölgesi arasındaki ilişki.
Boşluk veya girişim: δ = deliğin gerçek boyutu - şaftın gerçek boyutu ,δ ≥ 0 boşluk ,δ ≤ 0 girişim
(2) Uyum türleri: Açıklık uyumu, Girişim uyumu, Geçiş uyumu
(3) Uyumların temeli:
① Temel delik sistemi: Temel delik için temel sapma sembolü "H "dir.
② Temel şaft sistemi: Temel şaft için temel sapma sembolü "h "dir.
Uyum notasyonu şöyledir:
Temel boyut Delik için temel sapma sembolü, tolerans derecesi / Mil için temel sapma sembolü, tolerans derecesi
Örneğin:
- Φ30 H8/f7 Temel delik sistemi boşluk uyumu
- Φ40 H7/n6 Temel delik sistemi geçiş uyumu
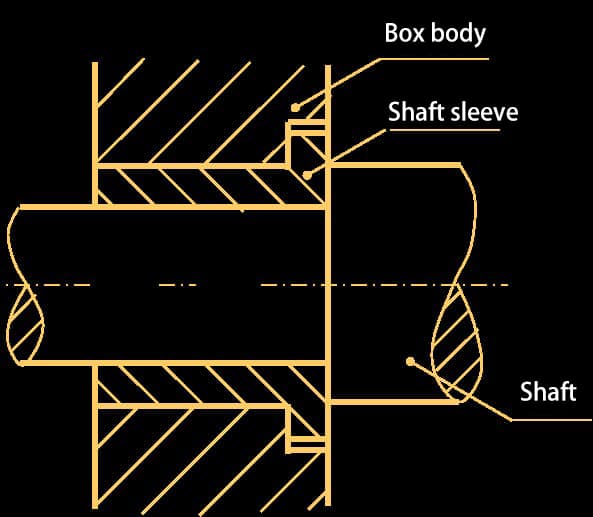
Yaygın Malzemeler ve Isıl İşlem
Ortak Malzemeler
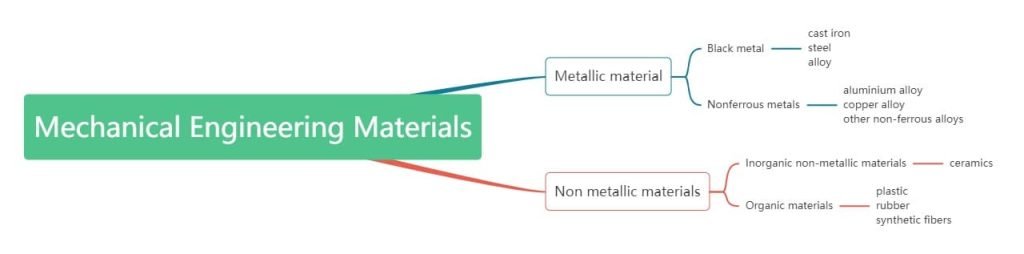
Çelik Malzemeler (demirli metaller)
1. Alaşımsız Çelik (Karbon Çelik)
- Minimum safsızlık içeren, 2%'den daha az karbon içeren demir-karbon alaşımları.
- Kütle oranına göre sınıflandırılır: düşük karbonlu çelik, orta karbonlu çelik, yüksek karbonlu çelik.
- Kalite derecesine göre sınıflandırılır: sıradan, yüksek kaliteli ve özel kalite.
- Kullanıma göre sınıflandırılmış: karbon yapısal çelik, karbon takım çeliği.
2. Alaşımlı Çelik
Cr, Mn, Ni, Ti, Mo, vb. ile yapay olarak eklenmiş, yüksek mukavemet, tokluk, sertlik ve bazı özel özelliklere (korozyon direnci, yüksek sıcaklık mukavemeti, vb.) sahip.
3. Dökme Demir
İyi döküm performansı, sürtünme azaltma, titreşim emilimi, işlenebilirlik, düşük çentik hassasiyeti, basit üretim süreci ve düşük maliyet sergiler.
- Gri Dökme Demir: C - serbest haldeki pul grafit formunda.
- Sünek Demir: C - küresel grafit formunda, daha yüksek mukavemet, iyi plastisite ve tokluğa sahiptir.
Çelik Isıl İşlem
1. Isıl işlem tanımı:
Isıtma, yalıtım, soğutma → istenen özellikleri elde etmek için metalin genel veya yüzey yapısının değiştirilmesi.
2. Isıl işlem türleri:
- Yaygın ısıl işlem: tavlama, normalleştirme, su verme, temperleme
- Yüzey ısıl işlemi ve kimyasal ısıl işlem: indüksiyonla ısıtma, alevle ısıtma, dirençli ısıtma, elektrolitik ısıtma, karbürleme, nitrürleme, karbürleme ve nitrürleme vb.
3. Diğer ısıl işlemler
- Tavlama: ısıtma, yalıtım, fırın soğutma
Amaç: sertliği azaltmak, taneleri inceltmek, iç gerilimi ortadan kaldırmak
- Normalleştirme: ısıtma, yalıtım, hava soğutma
Amaç: daha yüksek mekanik performans ile tavlamaya benzer
- Söndürme: ısıtma, yalıtım, su, yağ veya tuzlu su ile soğutma
Amaç: parça sertliğini ve aşınma direncini artırmak, malzemeyi güçlendirmek. Bununla birlikte, su verme işleminden sonra iç gerilme meydana gelir ve malzemeyi kırılgan hale getirerek temperleme gerektirir.
- Temperleme: Su verme işleminden sonra, parçanın kritik sıcaklığın altına ısıtılması, bekletilmesi ve ardından belirli bir hızda soğutulması.
Amaç: Tasarım çizimlerinin gerektirdiği sertliği elde etmek, iç gerilimi ortadan kaldırmak.
Temperleme işlemlerinin türleri:
- Düşük sıcaklıkta temperleme (150~250°C)
- Orta sıcaklıkta temperleme (350~500°C)
- Yüksek sıcaklıkta temperleme (500~650°C)
- Yaşlandırma işlemi: Su verme + yüksek sıcaklıkta temperleme
- Yüzey ısıl işlemi: Çeliğin bileşimini değiştirmeden sadece yüzeyini ısıtan ve soğutan bir ısıl işlem.
Amaç: Parçanın yüzey sertliğini ve aşınma direncini arttırmak.
- Kimyasal ısıl işlem: Çeliğin belirli bir sıcaklıkta aktif bir ortama yerleştirilmesi, tutulması, bir veya daha fazla elementin yüzeyine sızmasına izin verilmesi, kimyasal bileşiminin ve yapısının değiştirilmesi ve teknik gereksinimleri karşılamak için iyileştirilmiş bir yüzey performansı elde edilmesi.
Amaç: Çelik parçanın yüzey aşınma direncini, korozyon direncini, oksidasyon direncini ve yorulma mukavemetini iyileştirmek.
Sac Metal Malzemeler
1. Elektrolitik Plaka: (galvanizli plaka olarak da bilinir) SECC (N) (parmak izine dayanıklı plaka), SECC (P), DX1, DX2, SECD (germe plakası).
Malzeme sertliği: HRB50°±5°, germe plakası: HRB32°~37°.
2. Soğuk Haddelenmiş Levha: SPCC, SPCD (germe plakası), 08F, 20, 25, Q235-A, CRS. Malzeme sertliği: HRB50°±5°, germe plakası: HRB32°~37°.
3. Alüminyum Levha: AL, AL (1035), AL (6063), AL (5052) vb.
4. Sıcak Haddelenmiş Levha: Q435, Q436, QSPH75, ZJ330B, ZJ400, Q195, Q215, Q235B, Q226, 08KP, 08YU, HJ41, HP295, vb.
5. Paslanmaz Çelik Levha: SUS, SUS301, 2Cr13, 1Cr18Ni9Ti, vb.
6. Yaygın olarak kullanılan diğer malzemeler şunlardır: saf bakır levha (T1, T2), sıcak haddelenmiş levha, yay çeliği levha, alüminyum-çinko kaplı levha, alüminyum profiller, vb.
Yüzey Açılım Diyagramı
Üç boyutlu bir yüzeyin gerçek şekline ve boyutuna göre bir düzlem üzerinde sıralı ve sürekli olarak düzleştirilmesi işlemine açılım üç boyutlu bir yüzeyin. Açma işleminden sonra elde edilen diyagrama yüzey açma diyagramı denir.
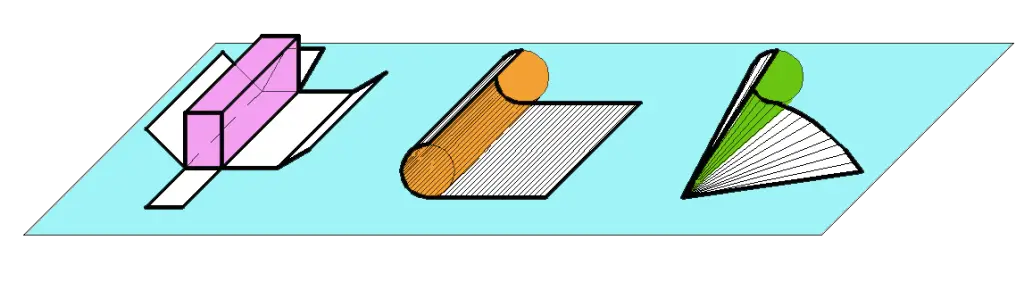
Üç boyutlu yüzey, geliştirilebilir yüzeyler (düzlemsel katıların yüzeyleri; kavisli katılarda silindirik ve konik yüzeyler) ve geliştirilemez yüzeyler (küresel ve sarmal yüzeyler gibi) olarak ikiye ayrılır.
Düzlemsel Katıların Açılımı
Örnek: Bir Prizmanın Yüzeyinin Açılması
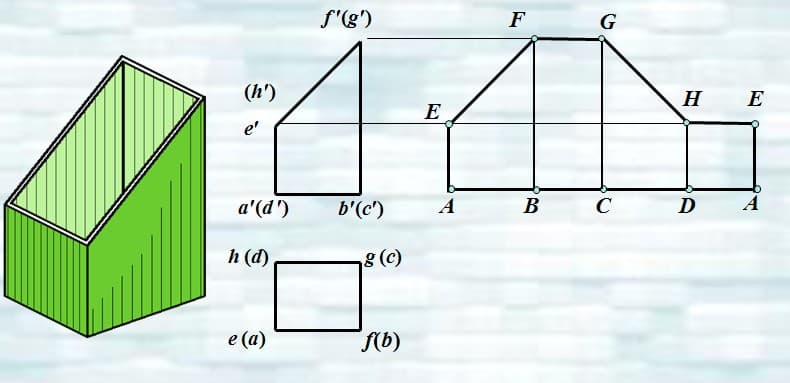
Geliştirilebilir Yüzeylerin Açılması
Örnek: Eğik Dairesel Silindir Yüzeyin Açılması
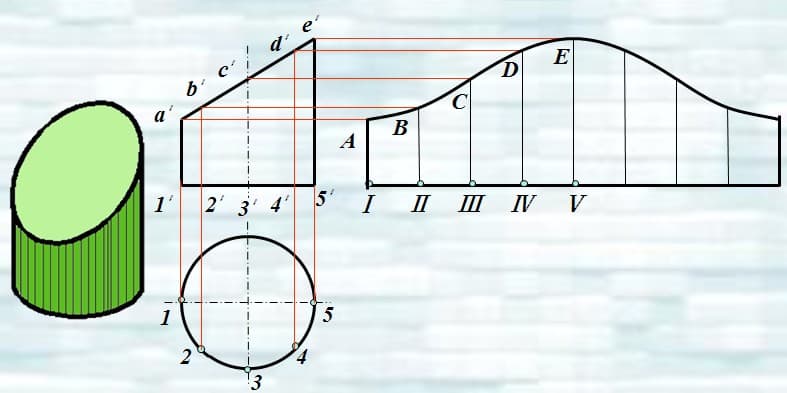
Kaynak Sembolleri
Yaygın Kaynaklı Bağlantılar:

Kaynak şeması, kaynak işlemleri için kullanılan bir modeldir. Kaynaklı iş parçasının yapısını açıkça ifade etmenin yanı sıra, kaynağın konumunu, birleştirme şeklini ve boyutlarını da açıkça belirtmelidir.
Desen üzerindeki kaynak, teknik çizim yöntemleri kullanılarak temsil edilebilir. Desen üzerindeki kaynağı basitleştirmek için, kaynak sembolleri ve sayısal kodlar kaynak yöntemleri̇ genellikle temsil için kullanılır.
Kaynak Sembolleri (GB324-1988)
Temel Semboller: Kaynağın enine kesit şeklini temsil eden semboller.
Kaynaklar için ortak temel semboller ve bunların açıklamalarına örnekler.
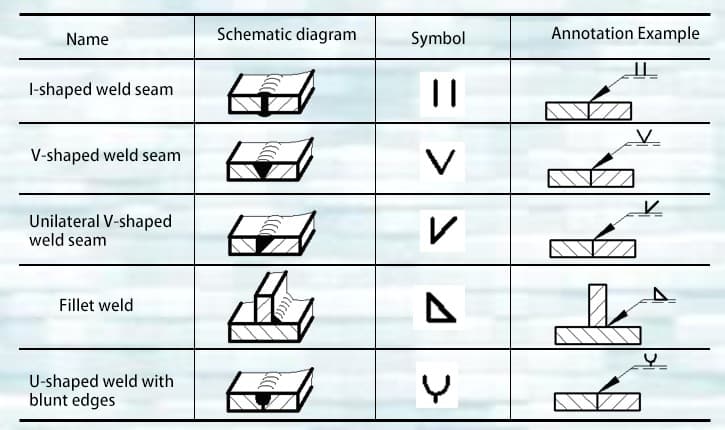
Tamamlayıcı Semboller: Kaynağın yüzey şekli özelliklerini temsil eden semboller.
Tamamlayıcı semboller ve açıklamalarına örnekler.
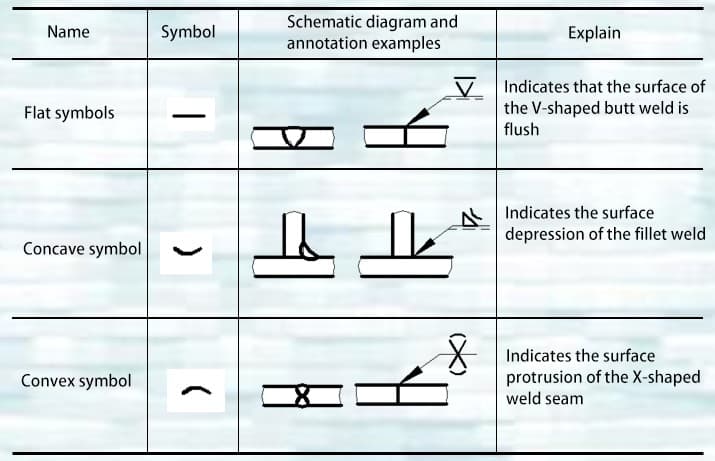
Tamamlayıcı Semboller: Kaynağın belirli özelliklerinin tanımını tamamlamak için kullanılan semboller.
Tamamlayıcı semboller ve açıklamalarına örnekler.
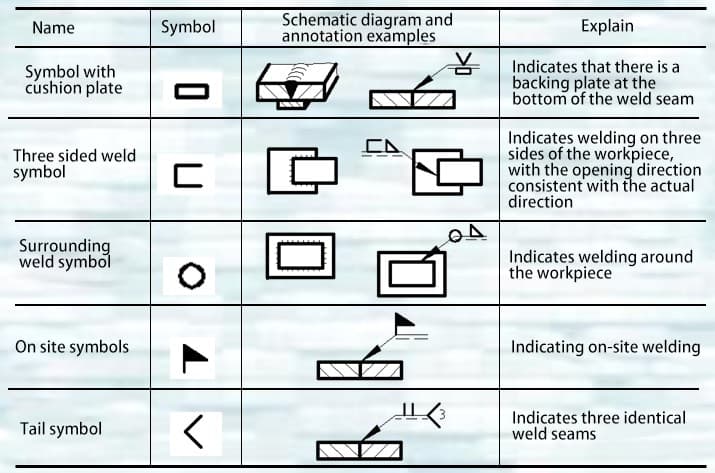
Tipik Kaynak Sembol Gösterimi
Kaynak Sembol Gösterimi Örneği (1)
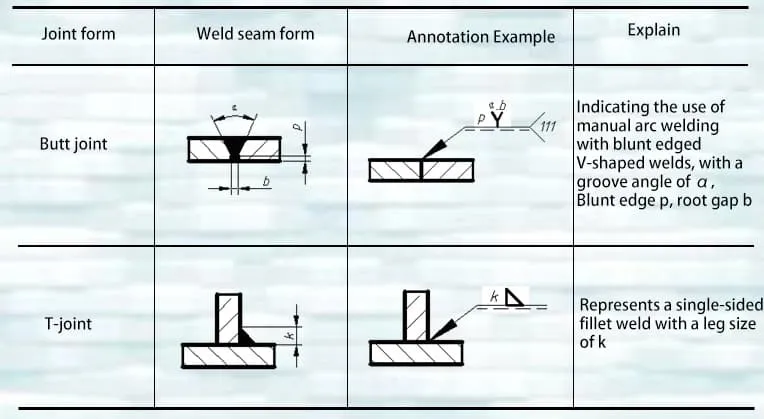
Kaynak Sembol Gösterimi Örneği (2)
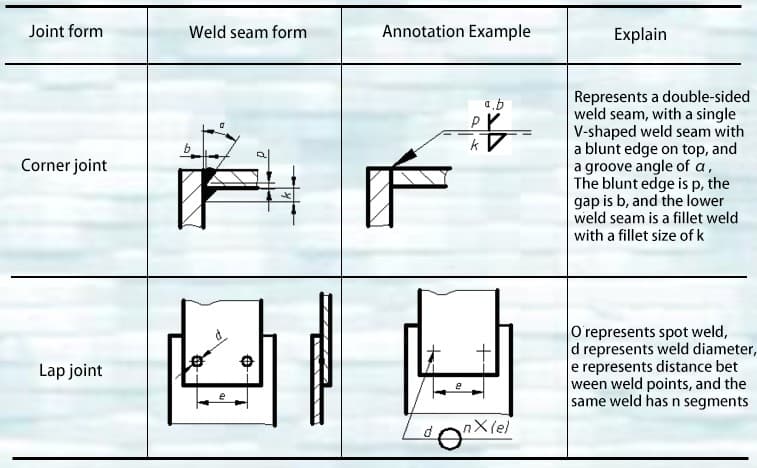
Makine Mühendisliğinde Sac Metal Şekillendirme
Mekanik Şekillendirmenin Avantajları
Manuel şekillendirme ile karşılaştırıldığında, sac metal mekanik şekillendirmenin en önemli avantajı yüksek işleme hassasiyeti, yüksek otomasyon derecesi ve çok yüksek üretim verimliliğidir.
Şekillendirme Prosesleri ve Ortak Ekipmanlar
Malzeme Kesimi:
Malzeme kesimi, malzemenin aşağıdakilere göre gerekli şekillerde kesilmesini içerir açılım. Malzeme kesimi için kesme, zımbalama ve delme olarak kategorize edilebilecek çeşitli yöntemler vardır. lazer kesim takım tezgahının türüne ve çalışma prensibine bağlı olarak.
1. Makaslama: Bu yöntem, bir kesme aleti kullanarak gerekli şekillerin kesilmesini içerir. makaslama maki̇nesi̇ veya makas. Hassasiyet 0,2 mm veya daha fazlasına ulaşabilir, öncelikle şeritleri kesmek veya malzemeleri temizlemek için kullanılır.
2. Delme: Malzeme kesme işlemi sayısal kontrollü bir delme makinesi (NC) veya geleneksel bir delme presi kullanılarak gerçekleştirilir. Her iki yöntem de 0,1 mm veya daha fazla hassasiyet elde edebilir. Bununla birlikte, birincisi kesme sırasında bıçak izleri bırakabilir ve nispeten daha düşük verimliliğe sahipken, ikincisi yüksek verimliliğe sahiptir, ancak büyük ölçekli üretim için uygun olan yüksek başlangıç maliyetleri gerektirir.
2.1 İçinde CNC zımba presleriÜst ve alt kalıplar sabittir ve çalışma tablası sac metali delmek ve kesmek için hareket ederek gerekli iş parçası şeklini üretir.
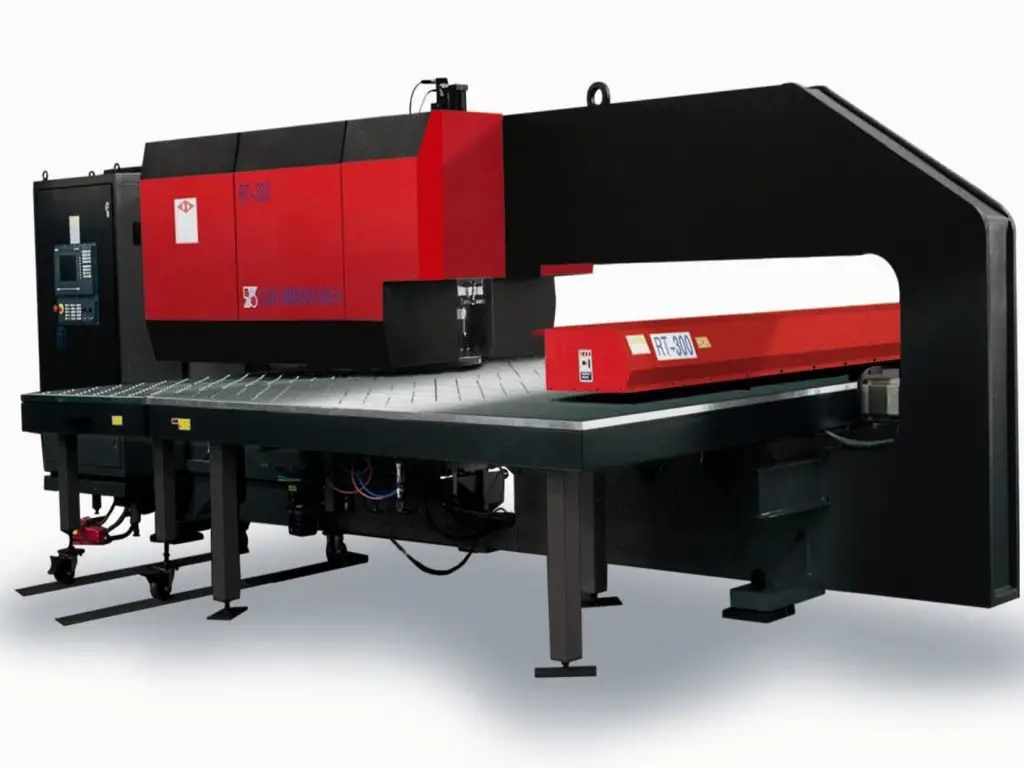
2.2 Geleneksel bir zımba presinde, üst ve alt kalıpların hareketi, bir körleme kalıbı kullanarak, iş parçasının istenen şeklini delip çıkarır. Genel olarak, geleneksel bir zımba presinin bir zımba kalıbı ile birlikte kullanılması gerekir. makaslama gerekli şekli delmek için makine. Bu, şerit malzemenin önce kesme makinesi tarafından kesildiği ve ardından iş parçasının gerekli şeklini delmek için zımba presinin kullanıldığı anlamına gelir.
3. Lazer kesim - Sac metali sürekli olarak kesmek ve gerekli iş parçası şeklini elde etmek için lazer kesim ekipmanının kullanılması. Özellikleri arasında yüksek hassasiyet ve çok karmaşık şekillere sahip iş parçalarını işleme yeteneği bulunur, ancak işleme maliyeti nispeten yüksektir.
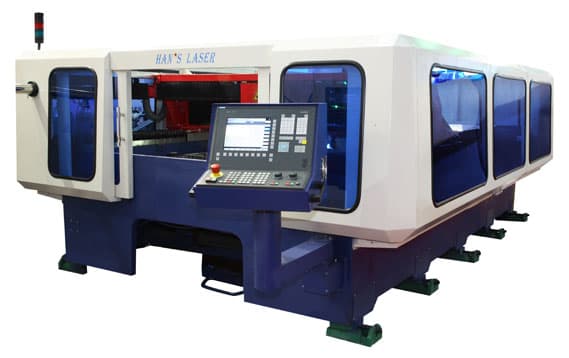
Şekillendirme:
Makine ile şekillendirme temel olarak şunları içerir bükme şekillendirme ve damgalama şekillendirme.
1. Bükme ile şekillendirme bükme maki̇nesi̇ Üst ve alt kalıpları bükme makinesinin üst ve alt çalışma masalarına sabitler ve çalışma masasının göreceli hareketini sağlamak için bir servo motor kullanır. Üst ve alt kalıpların şekilleri ile birleştirildiğinde, bu, sac metalin bükülerek şekillendirilmesini sağlar. Bükmenin şekillendirme hassasiyeti 0,1 mm'ye ulaşabilir.
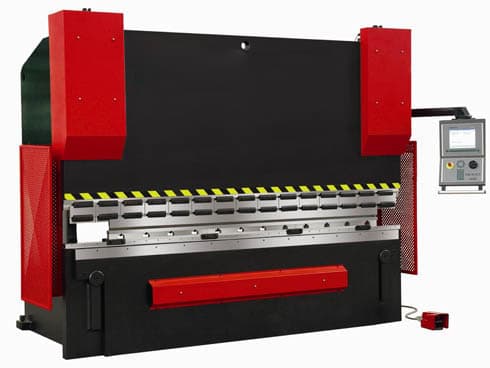
2. Damgalama şekillendirme - Basın üst kalıbı tahrik etmek için motor tahrikli volan tarafından üretilen gücü kullanır. Üst ve alt kalıpların göreceli şekillerini birleştirerek, sac metal deforme olur, iş parçasının işlenmesi ve şekillendirilmesi sağlanır. Damgalamanın şekillendirme doğruluğu 0,1 mm'nin üzerine çıkabilir. Pres, geleneksel presler ve yüksek hızlı presler olarak ikiye ayrılabilir.
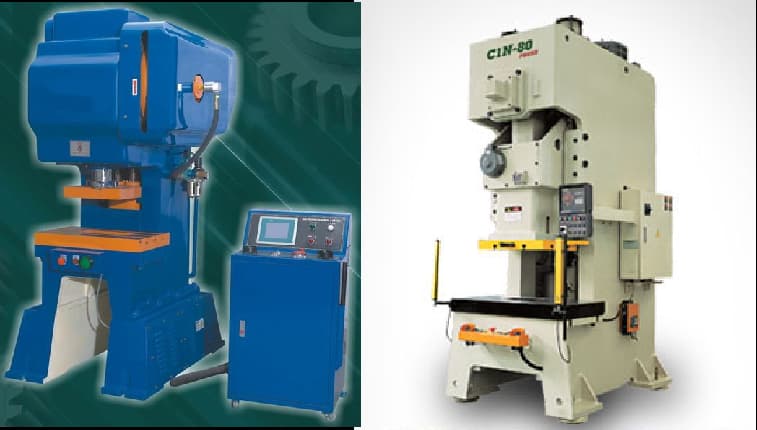
Sac Metal Kaynak İşlemi
Kaynak Özellikleri: Sac metal esas olarak çelik plakalardan veya profillerden oluşur ve yaygın olarak kullanılan kaynak yöntemleri arasında CO2 korumalı kaynak ve manuel ark kaynağı. Kaynak, çelik tasarrufu, basit kullanım ve iyi sızdırmazlık performansı avantajlarına sahiptir.
Ark Kaynağı İşlemi
Manuel ark kaynağı, kaynak çubuklarını manipüle etmek ve iş parçasını bir elektrik arkı kullanarak kaynaklamak için manuel operasyonun kullanıldığı bir yöntemdir. Ark hareket ettikçe, sürekli olarak yeni bir erimiş havuz oluşturulur ve orijinal havuzdaki erimiş metal sürekli olarak soğuyup katılaşarak bir kaynak oluşturur ve böylece iş parçasının iki parçasını bir bütün halinde birleştirir. Ark kaynağı makinesi Şekil 4-1'de gösterilmiştir.

Ark Ateşleme Yöntemleri:
(1) Vurma Yöntemi:
Vurma yöntemi, dikey olarak dokunmayı içerir kaynak çubuğu ardından kaynak çubuğunu hızla kaldırarak ve iş parçasından yaklaşık 3-4 mm mesafeyi koruyarak bir elektrik arkı oluşturun. Bu yöntem çoğunlukla Şekil 4-2a'da gösterildiği gibi iş parçasının dar veya çizilmeye duyarlı alanlarında kullanılır.
(2) Kazıma Yöntemi:
Kaynak çubuğunu iş parçası üzerine hafifçe çizin (yaklaşık 20 mm uzunluğunda), ardından Şekil 4-2b'de gösterildiği gibi bir elektrik arkı oluşturmak için iş parçasından yaklaşık 3-4 mm uzakta tutun.
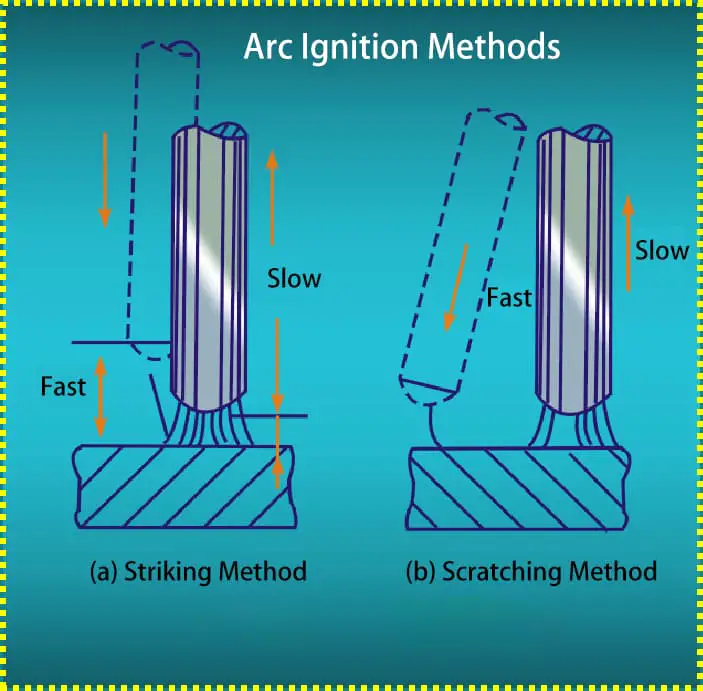
Kaynak Çubuğu Hareket Yönleri:
(1) Doğrusal Seyahat Yöntemi:
Düz çizgi hareket yöntemi yanal salınım içermez ve Şekil 4-3a'da gösterildiği gibi 3-5 mm levha kalınlıkları için eğimsiz alın kaynağının yanı sıra çok katmanlı kaynağın ilk katmanı ve çok pasolu kaynak için uygundur.
(2) Doğrusal İleri-Geri Seyahat Yöntemi:
Düz çizgi ileri geri hareket yöntemi, Şekil 4-3b'de gösterildiği gibi kaynak çubuğunun ucunun kaynak dikişi boyunca ileri geri doğrusal bir salınım yapmasını içerir.
(3) Zikzak Seyahat Yöntemi:
Zikzak hareket yöntemi, Şekil 4-3c'de gösterildiği gibi kaynak çubuğunun ucunun sürekli zikzak şeklinde ileri doğru hareket etmesini ve her iki taraftaki dönüş noktalarında kısa bir süre duraklamasını içerir.
(4) Hilal Şeklinde Seyahat Yöntemi:
Hilal şeklindeki hareket yöntemi, kaynak çubuğunun ucunun Şekil 4-3d'de gösterildiği gibi sürekli sol-sağ hilal şeklinde ileri doğru hareket etmesini ve her iki taraftaki dönüş noktalarında kısa bir süre durmasını içerir.
(5) Üçgen Seyahat Yöntemi:
Üçgen hareket yöntemi Şekil 4-3e'de gösterildiği gibi düz üçgen hareket yöntemi ve eğimli üçgen hareket yöntemi olarak ikiye ayrılır.
(6) Dairesel Seyahat Yöntemi:
Dairesel hareket yöntemi, Şekil 4-3f'de gösterildiği gibi düz dairesel hareket yöntemi ve eğimli dairesel hareket yöntemi olarak ikiye ayrılır.
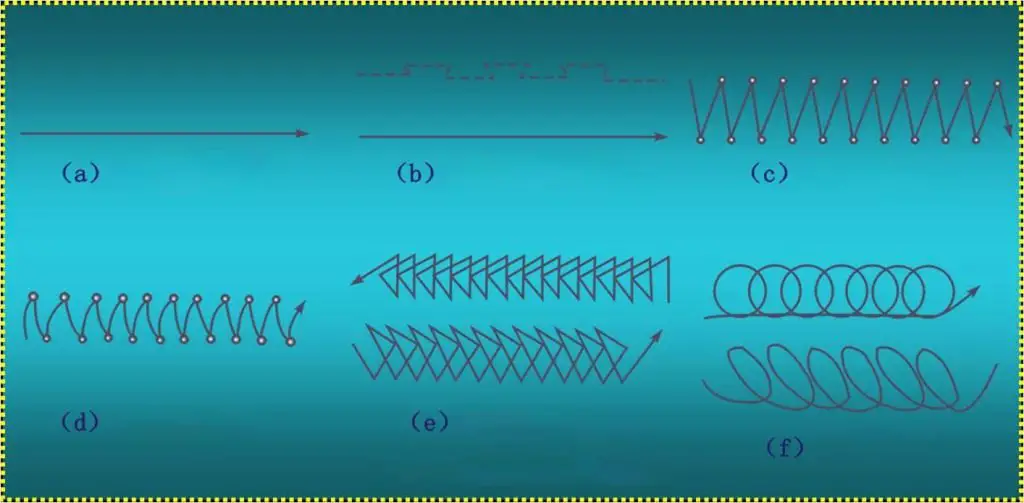
Kaynak Pozisyonları:
(1) Düz Kaynak:
Düz kaynak, düz alın kaynağı ve düz köşe kaynağı olarak ikiye ayrılabilir.
İş parçasının kalınlığı 6 mm'den az olduğunda, genellikle oluksuz düz alın kaynağı kullanılır. Kısa ark kaynağı için $3~φ4mm çapında bir kaynak çubuğu kullanılması, kaynak havuzunun derinliğinin plaka kalınlığının 2/3'üne ulaşması, kaynak genişliğinin 5~8mm'ye ulaşması ve kaynak yönteminin düz çizgi hareketinde olması tavsiye edilir.
İş parçasının kalınlığı 6 mm'den fazla olduğunda, Şekil 4-4'te gösterildiği gibi çok katmanlı kaynak veya çok pasolu kaynak olarak ikiye ayrılan oluklu düz alın kaynağı kullanılmalıdır.
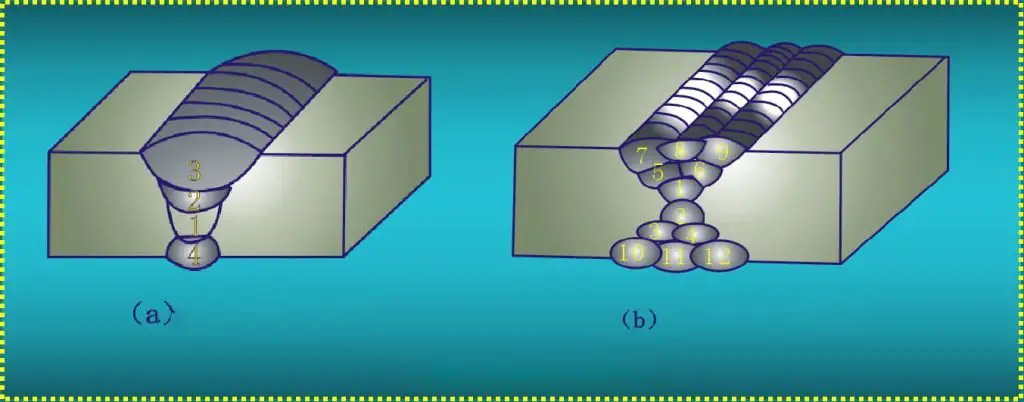
Dolgu kaynağı esas olarak T bağlantılarının ve bindirme bağlantılarının kaynağını ifade eder. Bu iki kaynak yöntemi benzerdir. Dolgu kaynağı tipik olarak 3~5mm kaynak çubukları kullanır ve kaynak çubuğu açısı Şekil 4-5'te gösterildiği gibidir.
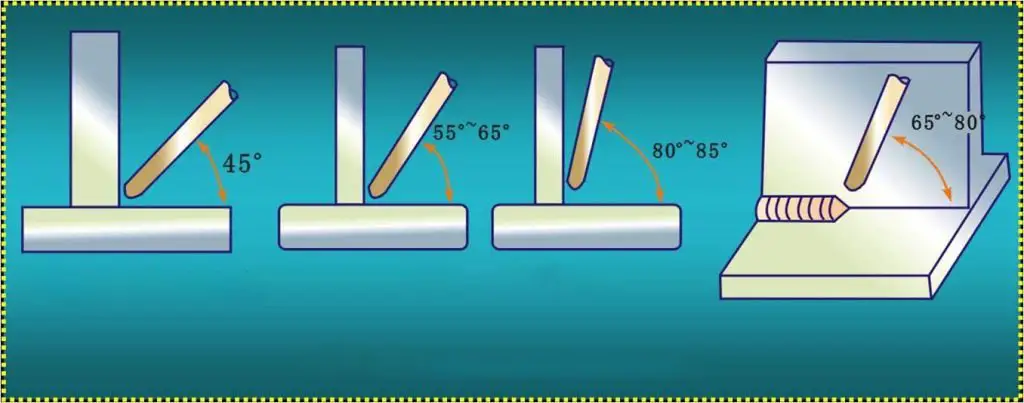
(2) Dikey Kaynak:
Dikey kaynakta kaynak havuzu dikey bir yüzeyde bulunur ve iki kaynak yöntemi vardır: biri aşağıdan yukarıya kaynak, diğeri ise yukarıdan aşağıya kaynak. Genellikle ilk yöntem kullanılır. Dikey kaynak yaparken, kaynak çubuğunun açısı Şekil 4-6'da gösterildiği gibidir.
Kısa ark kaynağı için daha küçük çap ve daha yüksek akım kullanılması tavsiye edilir, genellikle düz bir çizgi ileri geri hareketi ve üçgen hareket kullanılır ve kaynak boncuğu adım adım oluşturulur.
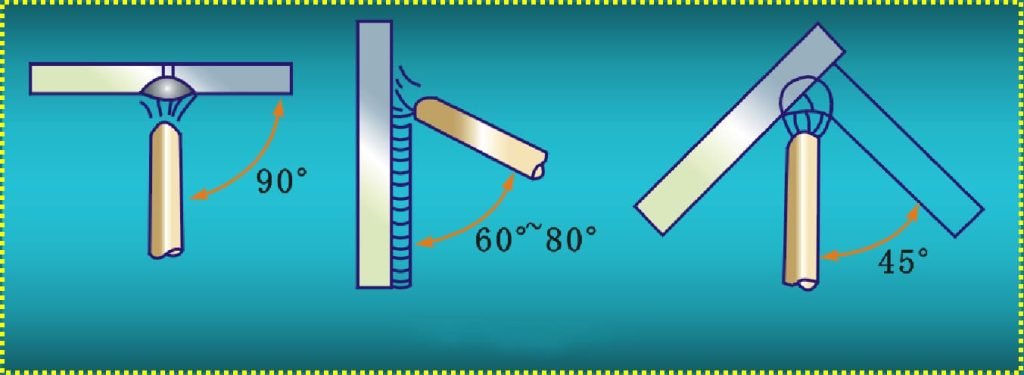
(3) Yatay Kaynak:
Yatay kaynak yaparken, kısa ark yöntemi ve uygun hareket teknikleri kullanılarak daha küçük çaplı kaynak çubukları ve daha düşük kaynak akımları kullanılması tavsiye edilir. İş parçasının kalınlığı 5 mm'den az olduğunda, Şekil 4-7a'da gösterildiği gibi 3,2 mm veya 4 mm kaynak çubukları kullanarak oluksuz kaynak yapmak mümkündür.
Daha kalın iş parçaları için oluklar kullanılmalıdır ve bu durumda Şekil 4-7b'de gösterildiği gibi çok katmanlı veya çok pasolu bir kaynak yöntemi kullanılmalıdır.
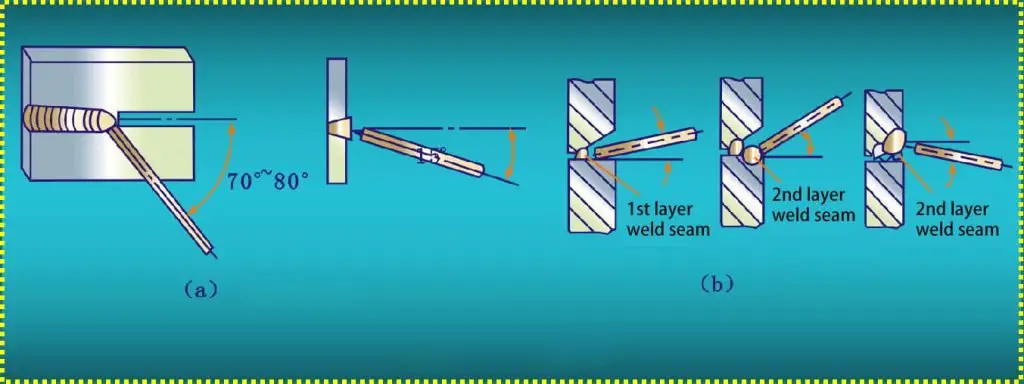
(4) Düz pozisyonda kaynak:
Düz pozisyonda kaynak yaparken, mümkün olan en kısa arkın kullanılması önemlidir, böylece erimiş damlacıklar hemen kaynak havuzuna geçebilir, havuzdaki erimiş metalle hızla birleşebilir ve böylece kaynağın hızlı bir şekilde katılaşmasını sağlar. Tipik olarak φ3 ila φ4mm arasında değişen daha küçük çaplı bir kaynak çubuğu seçilmeli ve kaynak çubuğu açısı Şekil 4-8'de gösterildiği gibi olmalıdır.
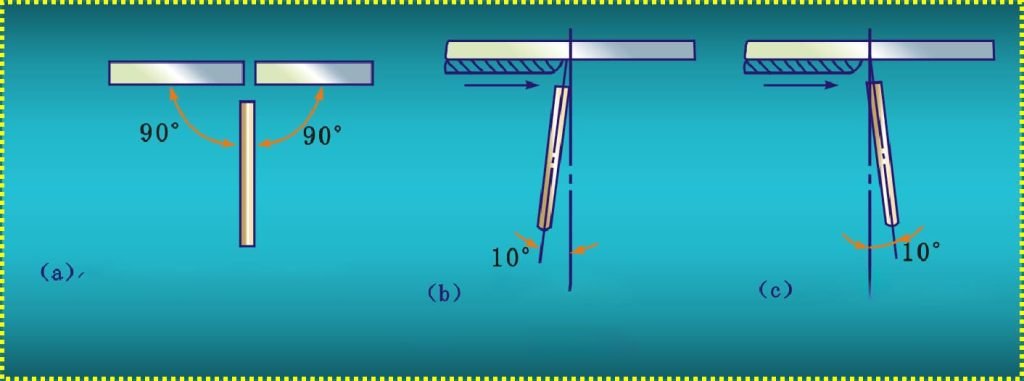
Manuel Ark Kaynağı için Güvenlik Prosedürleri:
(1) Sac metal işçileri gece kaynak işi yaparken elektrikli aydınlatma kullanmalıdır. Elektrikli aydınlatma için güvenli voltaj 36V'tur. İnsan vücudunun direncinin azaldığı nemli ortamlarda kullanım için belirtilen voltaj 12V'tur. Metal konteynerlerde veya boru hatlarında kaynak yaparken 12V gerilim kullanılmalıdır.
(2) Kaynak işlemi sırasında alınacak önlemler: Kaynak yapmadan önce bir yüz siperi, deri eldivenler ve yalıtımlı ayakkabılar giyin ve kaynak eki̇pmanlari ve aletler güvenlidir.
Dar alanlarda kaynak yaparken yalıtımlı ayakkabılar giyin ve iki operatörün dönüşümlü olarak çalışmasını sağlayın. Bir kişi operatörü her zaman izlemeli ve herhangi bir tehlike belirtisi ortaya çıkarsa, kullanım için gücü derhal kesmelidir.
Kişisel korumayı güçlendirin. Yüksek irtifa operasyonları sırasında yüksek gerilim hatlarına dokunmayın ve yağmurlu havalarda açık havada kaynak yapmaktan kaçının.
(3) Kaynak hijyeni ve koruyucu önlemler: Havalandırma tesisleri, kaynak tozunun tehlikelerini ortadan kaldırmak ve çalışma koşullarını iyileştirmek için etkili bir önlemdir. Rolleri, çalışma alanındaki hava ortamının hijyen standartlarını karşılamasını sağlamaktır, bu nedenle havalandırma tesislerinin düzgün çalıştığından emin olmak önemlidir.
Bir atölye içinde kaynak yaparken, kaynak işlemi sırasında ortaya çıkan zararlı maddelerin derhal tahliye edilmesini ve prensip olarak arıtma işleminden geçirilmesini sağlamak gerekir.
Ark kaynağı yaparken koruyucu camlı bir yüz siperi kullanılmalıdır. Filtre camını gelişigüzel değiştirmeyin, yoğun ışığı yansıtmak için beyaz bir iş kıyafeti giyin.
Karbon Dioksit (CO) ile Gaz Metal Ark Kaynağı (GMAW)2) Koruyucu Gaz
En yaygın kullanılan yöntem yarı otomatik CO2 Şekil 4-20'de gösterildiği gibi ark kaynağı makinesi. Makine kaynak telini otomatik olarak besler ve CO2 gazı kullanılırken, dikiş boyunca kaynak manuel olarak yapılır.
Kalınlığı 0,4 mm ila 0,8 mm arasında değişen iş parçalarının (düşük karbonlu çelik, düşük alaşımlı çelik, paslanmaz çelik vb.) düz, dikey ve baş üstü dahil olmak üzere çeşitli pozisyonlarda kaynaklanması için uygun olan 0,6 mm ila 0,8 mm ve 1,0 mm çaplarında kaynak telleri kullanabilir. köşe kaynağı, oluk kaynağı ve ayrıca dökme demirin onarımı için de kullanılabilir.
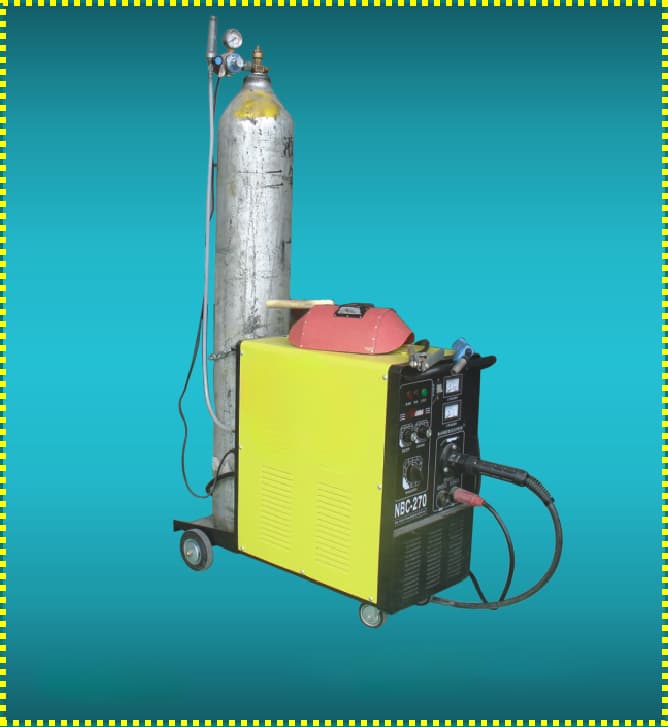
1. CO2 Gaz Korumalı Kaynak için Kaynak Proses Parametreleri: (Bkz. Tablo 4-1)
Parametre Adı | Seçim Kriterleri | Yöntem Seçimi |
Tel Çapı | Tel çapı, iş parçasının kalınlığına, kaynak bağlantısının konumuna ve verimlilik gereksinimlerine göre seçilebilir. | Orta kalınlıkta plakalar üzerinde düz pozisyonda kaynak yaparken, yaklaşık 1,6 mm çapında bir tel uygundur. Dikey, yatay veya baş üstü pozisyonlarda ince veya orta kalınlıkta plakalar üzerinde kaynak yapmak için, çapı 1,6 mm'nin altında olan tel kullanmak yaygındır. |
Kaynak Akımı | Kaynak akımı, iş parçası kalınlığına, tel çapına, kaynak bağlantısının konumuna ve gerekli damlacık aktarım moduna göre seçilebilir. | Kısa devre geçiş kaynağı için 0,8 mm ila 1,8 mm çapında tel kullanıldığında, kaynak akımı 50A ila 230A arasında değişir. |
Ark Gerilimi | Ark gerilimi kaynak akımı ile uygun şekilde koordine edilmelidir. Ark voltajındaki bir artış, kaynak genişliğinde, takviye yüksekliğinde karşılık gelen bir artışa ve nüfuziyet derinliğinde bir azalmaya yol açar. Tersine, ark voltajındaki bir azalma kaynak genişliğinde bir azalmaya yol açar. | Kısa devre geçiş kaynağı sırasında ark gerilimi 16V ila 25V aralığındadır. Kaba damlacık geçiş kaynağı için 1,2 mm ila 3,0 mm çapında tel kullanıldığında, ark voltajı 25V ila 44V aralığında seçilebilir. |
Kaynak Hızı | Kaynak hızı arttıkça, kaynak genişliği, takviye yüksekliği ve nüfuziyet derinliği buna bağlı olarak azalır; tersine, kaynak hızındaki bir azalma bu parametrelerde bir artışa yol açar. | Yarı otomatik kaynak için kaynak hızı 15m/sa ile 30m/sa arasında değişirken, otomatik kaynak için kaynak hızı biraz daha hızlı olabilir, genellikle 40m/sa'i geçmez. |
Elektrot Uzatma Uzunluğu | Elektrot uzatma uzunluğu, kaynak sırasında temas ucundan uzanan elektrot uzunluğunu ifade eder. | Tel uzatmanın uzunluğu tel çapına bağlıdır. Genel olarak, tel çapının yaklaşık 10 katı kadar bir tel uzatma uzunluğu uygundur. |
CO2 Gaz Akış Hızı | CO2 gaz akış hızı, kaynak akımı, kaynak hızı, elektrot uzatma uzunluğu ve nozul çapına göre seçilmelidir. | CO kullanarak ince tel ile kaynak yaparken2 gazı, CO2 gaz akış hızı yaklaşık 5L/dak ila 15L/dak arasındadır; kalın telle kaynak yaparken CO2 gazı, CO2 gaz akış hızı yaklaşık 15L/dak ila 25L/dak arasındadır. |
Güç Kaynağının Polaritesi | Doğru akım elektrot pozitif (DCEP) ile karşılaştırıldığında, doğru akım elektrot negatif (DCEN) kararlı ark, daha az sıçrama ve daha fazla penetrasyon derinliği özellikleri sunar. | CO'nun kaynak kalitesini sağlamak için2 Gaz korumalı kaynakta yaygın olarak benimsenen yöntem, iş parçasının negatif kutba ve kaynak tabancasının pozitif kutba bağlandığı doğru akım ters bağlantısıdır. |
Devre Endüktansı | Kaynak devresindeki endüktans tel çapı, kaynak akımı ve ark gerilimine göre seçilmelidir. | Φ0.6mm ila Φ1.2mm ince tel kullanıldığında, endüktans değeri yaklaşık 0.01mH ila 0.16mH'dir. Φ1.6mm ila Φ2mm kalınlığında tel kullanıldığında, endüktans değeri yaklaşık 0.3mH ila 0.7mH'dir. |
2. CO2 gaz korumali kaynak i̇şlemi̇ni̇n temelleri̇:
(1) Arkın vurulması. Ark kaynağı güç kaynağının düşük yüksüz voltajı ve hafif kaynak teli nedeniyle, arkı vururken sabit bir yanma noktası oluşturmak zordur ve genellikle telin parçalara ayrılmasına neden olur.
(2) Ark sönmesi. Arkı sonlandırırken, kraterde hafifçe duraklamak, ardından krater dolana kadar kaynak tabancasını yavaşça kaldırmak ve erimiş metalin katılaşana kadar gaz tarafından korunmasını sağlamak tavsiye edilir.
(3) Sola doğru kaynak tekniği. Sola doğru kaynak tekniği kullanıldığında, dikiş açıkça görülebilir, kaynak sapması olasılığı azalır ve daha fazla nüfuziyete izin vererek daha düzgün ve estetik açıdan hoş bir kaynak boncuğu elde edilir.
(4) Sağa doğru kaynak tekniği. Sağa doğru kaynak tekniği kullanıldığında, kaynak havuzunun görünürlüğü ve gaz korumasının etkinliği artar, ancak kaynak sırasında dikişin boşluğunu gözlemlemek zahmetlidir ve kaynak sapması riskini artırır.
(5) Kaynak pozisyonları. CO2 gaz korumalı kaynak dört pozisyonu kapsar: Şekil 4-21'de gösterildiği gibi düz, yatay, dikey ve baş üstü.
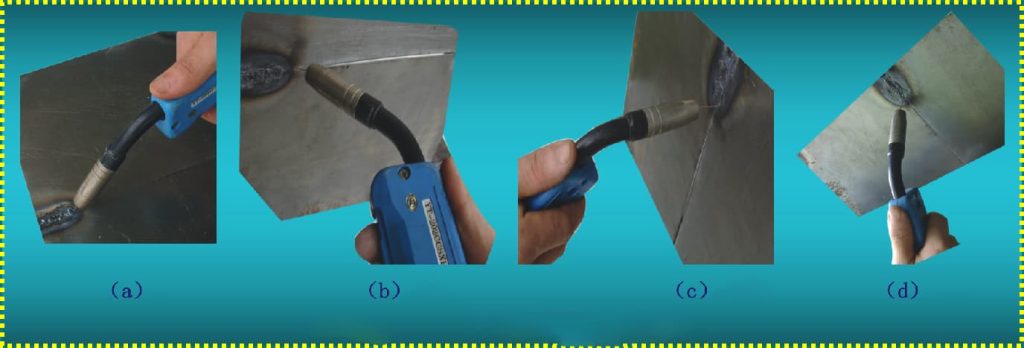
3. Kaynak Formları:
CO'in altı formu vardır2 Şekil 4-22'de gösterildiği gibi gaz korumalı kaynak.
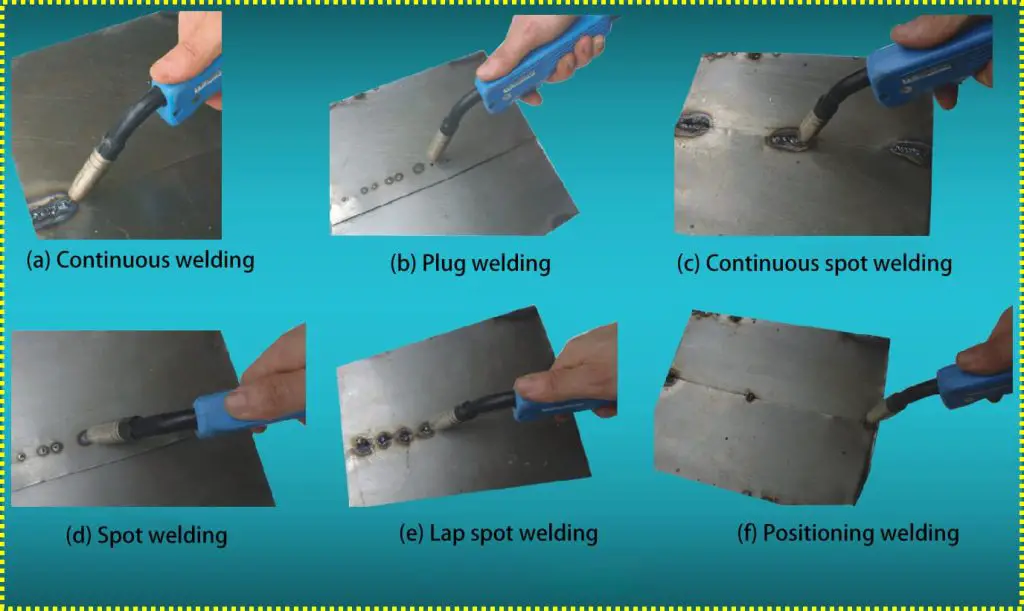
(1) Punta Kaynağı: Aslında, iki kaynaklı parçanın göreceli konumlarını sabit tutmak için kullanılan alternatif bir önlem olan geçici bir nokta kaynağıdır. Şekil 4-23'de gösterildiği gibi.
(2) Sürekli Kaynak: Şekil 4-24'te gösterildiği gibi, kaynak tabancasının sürekli bir kaynak dikişi oluşturmak için kaynak boyunca sürekli ve istikrarlı bir şekilde hareket ettiği kaynak biçimini ifade eder.
(3) Tapa Kaynağı: İki metal plaka bir araya getirildiğinde ve plakalardan birinde bir delik olduğunda, Şekil 4-25'te gösterildiği gibi arkın bu delikten geçirilmesi ve erimiş metal ile doldurulmasıyla oluşturulan kaynağa tapa kaynağı denir.
(4) Nokta Kaynağı: Nokta kaynağı, tel besleme zamanlama darbesi tetiklendiğinde arkın kaynak yapılan iki metal plakaya sokulduğu ve kaynağın bölgesel olarak erimesine neden olan bir kaynak şeklidir.