
I. Taşlama ve Taşlama Makineleri
1. Taşlama
Taşlama, yaygın olarak kullanılan bir yarı bitirme ve bitirme yöntemidir. Diğer takım tezgahlarıyla karşılaştırıldığında, temel fark kullanılan kesici takımda yatmaktadır. Taşlama, iş parçası yüzeyini işlemek için yüksek hızlı dönen taşlama taşları, titreşimli taşlama taşları veya dönen aşındırıcı kayışlar kullanır. Taşlama esas olarak çeşitli iç ve dış silindirik yüzeyleri, iç ve dış konik yüzeyleri, düz yüzeyleri ve ayrıca dişler, dişliler ve yivler gibi özel ve karmaşık biçimli yüzeyleri işlemek için kullanılır.
Taşlama makinesi, iş parçalarının yüzeyini taşlamak için aşındırıcılar kullanan bir makine aletidir. Çoğu taşlama makinesi, taşlama için yüksek hızlı dönen taşlama taşları kullanırken, birkaçı honlama makineleri, süper finisaj makineleri, bantlı taşlama makineleri, lepleme makineleri ve parlatma makineleri gibi işleme için taşlama taşları, aşındırıcı kayışlar ve gevşek aşındırıcılar gibi diğer aşındırıcıları kullanır.
Taşlama taşı, taşlama için ana kesici alettir ve taşlama makinesinin kesici aleti olarak hizmet eder. Aşındırıcı tanelerin yüksek sertliği nedeniyle, taşlama taşı kendi kendini bileme özelliklerine sahiptir. Taşlama, sertleştirilmiş çelik, yüksek mukavemetli alaşımlı çelik, karbürler, demir dışı malzemeler dahil olmak üzere çeşitli malzemeleri işlemek için kullanılabilir. metaller (demir dışı malzemeler), cam, seramik ve mermerin yanı sıra diğer yüksek sertlikteki metalik ve metalik olmayan malzemeler.
Taşlama hızı, taşlama çarkının doğrusal hızını ifade eder. Sıradan taşlama için, taşlama çarkının doğrusal hızı genellikle 30-35 m/s'dir. Yüksek hızlı taşlama için doğrusal hız tipik olarak 45-160 m/s'dir. 160 m/s'yi aştığında, buna ultra yüksek hızlı taşlama denir.
Taşlama genellikle yarı bitirme ve bitirme için kullanılır. Boyutsal tolerans derecesi IT8 ila IT5'e veya daha da yükseğe ulaşabilir. Genel taşlama için yüzey pürüzlülüğü Ra 1.25-0.16 μm, hassas taşlama için Ra 0.16-0.04 μm, ultra hassas taşlama için Ra 0.04-0.01 μm'dir ve ayna taşlama Ra 0.01 μm'nin altına ulaşabilir.
Taşlama için spesifik enerji tüketimi (veya iş parçası malzemesinin birim hacmini kaldırmak için tüketilen enerji olan spesifik enerji) genel kesme işleminden daha yüksektir ve talaş kaldırma oranı genel kesme işleminden daha düşüktür. Bu nedenle, taşlamadan önce, iş parçaları genellikle işleme payının çoğunu kaldırmak için diğer kesme yöntemlerine tabi tutulur ve yalnızca 0,1-1 mm veya daha az taşlama payı bırakılır.
Sürünme beslemeli taşlama ve yüksek hızlı taşlama gibi yüksek verimli taşlama tekniklerinin geliştirilmesiyle, artık parçaları doğrudan hammaddeden taşlamak mümkündür. Taşlama ayrıca döküm kapıları ve yükselticileri, dövme parlaması ve çelik külçe kaplamalarının çıkarılması gibi kaba işleme için de kullanılır.
2. Taşlama makinelerinin geliştirilmesi
1730'larda saatler, bisikletler, dikiş makineleri ve ateşli silahlar için sertleştirilmiş parçaların işlenmesi ihtiyacını karşılamak üzere İngiltere, Almanya ve Amerika Birleşik Devletleri'nde doğal aşındırıcı taşlar kullanan taşlama makineleri geliştirildi.
Bu taşlama makineleri, torna ve planya gibi mevcut takım tezgahlarına taşlama kafaları eklenerek modifiye edilmiştir. Basit yapıları, düşük rijitlikleri vardı ve taşlama sırasında titreşime meyilliydiler. Operatörlerin hassas iş parçalarını taşlamak için çok yüksek becerilere sahip olması gerekiyordu.
1876 yılında Amerikan Brown & Sharpe Şirketi tarafından üretilen ve Paris Sergisi'nde sergilenen üniversal silindirik taşlama makinesi, modern taşlama makinelerinin temel özelliklerine sahip ilk makineydi. İş parçası mesnedi ve punta pistonlu bir çalışma tablasına monte edilmişti, kutu şeklindeki yatak makinenin sertliğini artırdı ve bir iç taşlama ataşmanı ile birlikte geldi. 1883 yılında bu şirket, taşlama kafası bir sütuna ve ileri geri hareket eden bir çalışma tablasına monte edilmiş bir yüzey taşlama makinesi üretti.
1900 yılı civarında, yapay aşındırıcıların geliştirilmesi ve hidrolik şanzımanın uygulanması, taşlama makinelerinin gelişimini büyük ölçüde destekledi. Modern endüstrinin, özellikle de otomotiv endüstrisinin gelişmesiyle birlikte, çeşitli taşlama makineleri ortaya çıktı. Örneğin, 20. yüzyılın başlarında, silindir blokları için gezegensel iç taşlama makineleri, krank mili taşlama makineleri, eksantrik mili taşlama makineleri ve elektromanyetik aynalı piston segmanı taşlama makineleri art arda geliştirildi.
Otomatik ölçüm cihazları 1908 yılında taşlama makinelerine uygulanmaya başlandı. 1920'lere gelindiğinde, puntasız taşlama makineleri, çift yüzlü taşlama makineleri, rulo taşlama makineleri, kızak taşlama makineleri, honlama makineleri ve süper finisaj makineleri birbiri ardına geliştirildi ve kullanıma sunuldu.
1950'lerde, ayna taşlama yapabilen yüksek hassasiyetli dış silindirik taşlama makineleri ortaya çıktı; 1960'ların sonlarında, taşlama taşı doğrusal hızları 60-80 m/s olan yüksek hızlı taşlama makineleri ve büyük kesme derinliğine ve yavaş ilerlemeye sahip yüzey taşlama makineleri ortaya çıktı; 1970'lerde, mikroişlemciler kullanan dijital kontrol ve uyarlanabilir kontrol gibi teknolojiler taşlama makinelerinde yaygın olarak uygulandı.
Yüksek hassasiyetli ve yüksek sertlikteki mekanik parçaların sayısındaki artışın yanı sıra hassas döküm ve hassas dövme teknolojilerinin gelişmesiyle birlikte, taşlama makinelerinin performansı, çeşitliliği ve üretimi sürekli olarak gelişmekte ve artmaktadır.
Taşlama makineleri, tüm metal kesme takım tezgahları arasında en çeşitli kategoridir. Başlıca türleri arasında dış silindirik taşlama makineleri, iç taşlama makineleri, yüzey taşlama makineleri, merkezsiz taşlama makineleri ve takım taşlama makineleri bulunmaktadır.
- Dış silindirik taşlama makineleri, esas olarak silindirik ve konik dış yüzeylerin taşlanması için kullanılan genel tiplerin temel serisidir.
- İç taşlama makineleri, esas olarak silindirik ve konik iç yüzeylerin taşlanması için kullanılan genel tiplerin temel serisidir. Ayrıca hem iç hem de dış taşlama yapabilen taşlama makineleri de bulunmaktadır.
- Jig taşlama makineleri, hassas koordinat konumlandırma cihazlarına sahip iç taşlama makineleridir.
- Merkezsiz taşlama makineleri, genellikle bir ayar çarkı ve bir iş dayanağı bıçağı arasında desteklenen iş parçalarını merkezsiz olarak tutar. Ayar çarkı, iş parçasının dönmesini sağlar ve çoğunlukla silindirik yüzeylerin taşlanması için kullanılır.
- Yüzey taşlama makineleri esas olarak iş parçalarının düz yüzeylerini taşlamak için kullanılır.
- Bantlı taşlama makineleri, taşlama için hızlı hareket eden aşındırıcı bantlar kullanan taşlama makineleridir.
- Honlama makineleri, iş parçalarının çeşitli yüzeylerini honlamak için kullanılan taşlama makineleridir.
- Alıştırma makineleri, iş parçalarının düz yüzeylerini veya silindirik iç ve dış yüzeylerini alıştırmak için kullanılan taşlama makineleridir.
- Kızak taşlama makineleri esas olarak takım tezgahı kızaklarının taşlanması için kullanılır.
- Takım taşlama makineleri, takımların taşlanması için kullanılır.
- Çok amaçlı taşlama makineleri silindirik, konik iç ve dış yüzeyleri veya düz yüzeyleri taşlamak için kullanılır ve aşağıdaki cihazları ve ataşmanları kullanarak çeşitli iş parçalarını taşlayabilir.
- Özel amaçlı taşlama makineleri, belirli parça türlerinin taşlanması için özel olarak tasarlanmış takım tezgahlarıdır. İşleme nesnelerine göre sınıflandırılabilirler: kam mili taşlama makineleri, krank mili taşlama makineleri, kam taşlama makineleri, dişli taşlama makineleri, diş taşlama makineleri, eğri taşlama makineleri vb.
3. Taşlamanın temel özellikleri
(1) Taşlama, yüksek işleme hassasiyeti ve düşük yüzey pürüzlülüğü değerleri elde edebilir.
Boyutsal tolerans dereceleri IT6 ve üzerine ulaşabilir; yüzey pürüzlülüğü değerleri Ra 0,8 ila 0,01 μm arasında değişir ve ayna taşlama için Ra 0,01 μm ve üzeri olabilir. Taşlama sadece finisaj için değil aynı zamanda kaba taşlama, kaba taşlama ve ağır yük taşlama için de kullanılabilir.
(2) Taşlamadaki radyal taşlama kuvveti büyüktür.
Taşlamadaki radyal taşlama kuvveti (geri kuvvet) büyüktür ve teknolojik sistemin daha düşük sertliğe sahip olduğu yönde etki eder, bu da iş parçasının, fikstürün ve makine takımının elastik deformasyonuna neden olarak işleme doğruluğunu etkileyebilir.
Bu nedenle, daha düşük sertliğe sahip iş parçalarını işlerken (ince şaftların taşlanması gibi), iş parçası deformasyonunun işleme hassasiyetini etkilemesini önlemek için uygun önlemler alınmalıdır.
(3) Taşlamadaki yüksek kesme hızı, yüksek taşlama sıcaklıklarına yol açar.
Deneysel ölçümlere göre, 60 m/s'lik bir taşlama taşı doğrusal hızında taşlama sıcaklığı (ortalama çalışma sıcaklığı) 30 m/s'ye göre 50%-70% daha yüksektir; 80 m/s'de taşlama sıcaklığı 60 m/s'ye göre 15%-20% daha yüksektir. Bunun nedeni, taşlama taşı doğrusal hızı arttıkça, birim zamanda taşlamaya katılan aşındırıcı tanelerin sayısının artması, sürtünmenin yoğunlaşması ve enerji tüketiminin de artarak iş parçası yüzey katmanının sıcaklığını yükseltmesidir.
Araştırmalar, taşlama sırasında oluşan ısının 80%-90%'sinin iş parçasına aktarıldığını göstermektedir (10%-15% taşlama taşına, 1%-10% taşlama talaşları tarafından taşınır). Taşlama taşının zayıf termal iletkenliği ile birleştiğinde, bu kolayca iş parçası yüzeyinin yanmasına ve mikro çatlaklara neden olabilir.
Bu nedenle, büyük miktarlarda kesme sıvısı Taşlama sıcaklığını düşürmek için taşlama sırasında yüksek soğutma verimliliğine sahip soğutma sıvısı kullanılmalıdır. Yüksek hızlı taşlamada, çalışma sırasında daha iyi soğutma etkileri elde etmek için kesme sıvısı genellikle ayrı olarak soğutulur.
(4) Taşlama taşlarının kendi kendini bileme etkisi vardır.
Taşlama işlemi sırasında, aşındırıcı tanelerin kırılması yeni, daha keskin kenarlar üretir ve aşındırıcı tanelerin dökülmesi yeni bir keskin taneler tabakası ortaya çıkararak taşlama taşının kesme kabiliyetini kısmen geri kazanmasını sağlar. Bu fenomen, taşlama için faydalı olan ve diğer kesici takımlarda bulunmayan taşlama taşının kendi kendini bileme etkisi olarak adlandırılır.
Taşlama yaparken, taşlama taşının sertliğini uygun şekilde seçerek taşlama verimliliğini artırmak için genellikle taşlama taşının kendi kendini bileme etkisinden yararlanılır. Ancak, aşındırıcı tanelerin düzensiz dökülmesi taşlama taşının şekil doğruluğunu kaybetmesine neden olabilir; kırık aşındırıcı taneler ve talaşlar taşlama taşını tıkayabilir. Bu nedenle, belirli bir süre taşlama yaptıktan sonra, kesme kabiliyetini ve şekil doğruluğunu geri kazandırmak için taşlama taşının giydirilmesi gerekir.
(5) Taşlama geniş bir teknolojik uygulama yelpazesine sahiptir.
Dökme demir, karbon çeliği ve alaşımlı çelik gibi genel yapısal malzemeleri işlemenin yanı sıra taşlama, sertleştirilmiş çelik, karbürler, seramikler ve cam gibi genel takımlarla kesilmesi zor olan yüksek sertlikteki malzemeleri de işleyebilir. Ancak, yüksek plastisiteye sahip demir dışı metal iş parçalarının son işlemesi için uygun değildir. Taşlama sadece dış silindirik yüzeyler gibi çeşitli yüzeyleri işleyemez,
iç silindirik yüzeyler, düz yüzeyler, şekillendirilmiş yüzeyler, dişler ve dişli profilleri, aynı zamanda çeşitli kesici takımların bilenmesi için de yaygın olarak kullanılır.
II. Öğütme işlemlerinin türleri ve öğütme özellikleri
1. Öğütme işlemlerinin sınıflandırılması
Taşlama işlemleri genellikle taşlama aletinin türüne göre sınıflandırılır ve iki ana kategoriye ayrılır: Şekil 1'de gösterildiği gibi sabit aşındırıcı işleme ve gevşek aşındırıcı işleme.
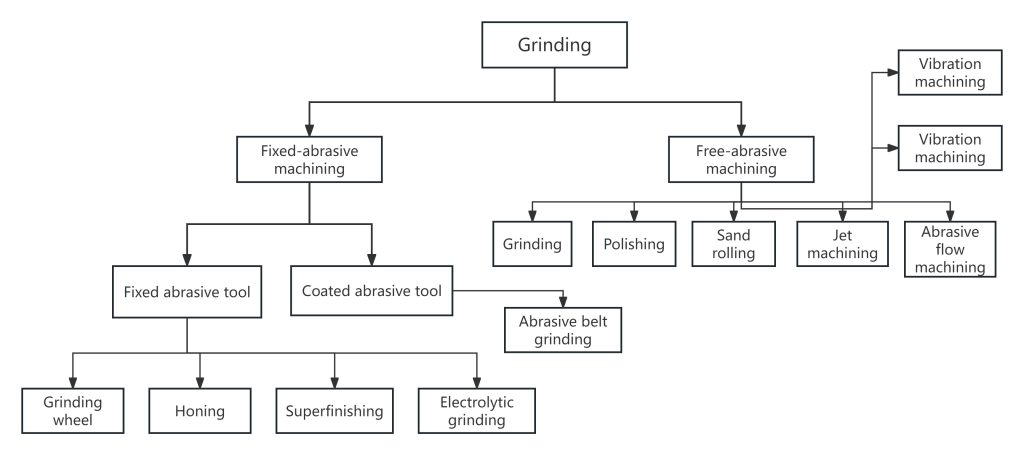
Farklı taşlama işlemlerinin uygulamaları, çalışma prensipleri ve hareket şekilleri açısından önemli farklılıkları vardır. Bunlar genellikle işleme nesnesine göre Şekil 2 ve Tablo 1'de gösterildiği gibi dış silindirik, iç silindirik, yüzey ve form taşlama olarak sınıflandırılabilir. Bununla birlikte, tüm taşlama işlemleri sürtünme, mikro kesme ve yüzey kimyasal-fiziksel reaksiyonları içerir, sadece biçim ve derece bakımından farklılık gösterir. "Taşlama" terimi genellikle bir taşlama taşı kullanılarak yapılan taşlamayı ifade eder.
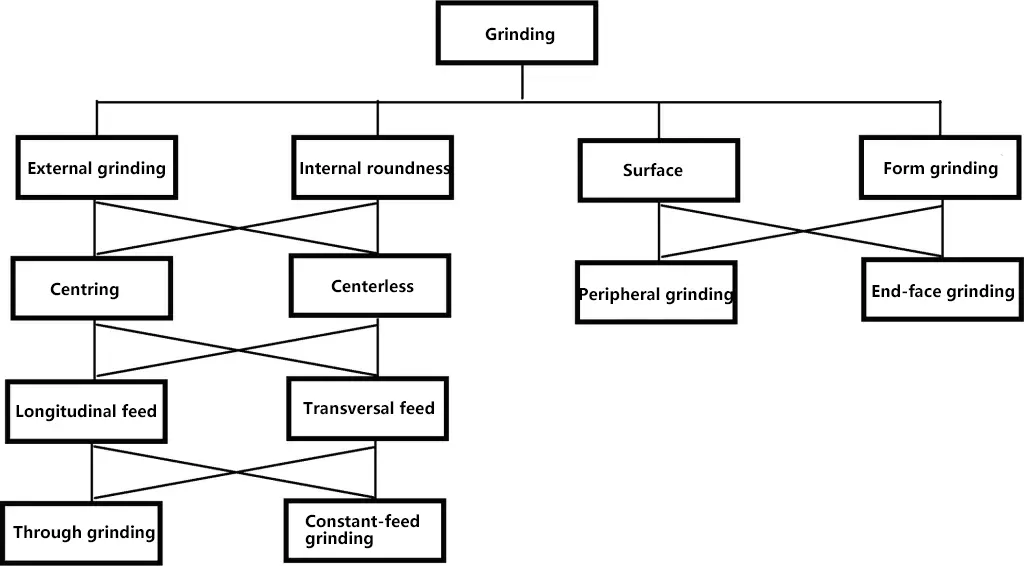
Tablo 1 Temel Taşlama Yöntemleri
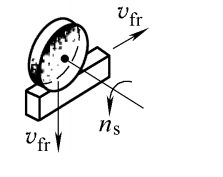
Genel dönel yüzeyler (iç ve dış), iş parçasını bağlama ve sürme yöntemine göre merkez taşlama ve merkezsiz taşlama olarak sınıflandırılabilir; ilerleme yönü ile işlenen yüzey arasındaki ilişkiye göre, uzunlamasına ilerlemeli taşlama ve enine ilerlemeli taşlama olarak ayrılabilir; taşlama vuruşundan sonra taşlama çarkının iş parçasına göre konumu dikkate alındığında, bunlar ayrıca içinden taşlama ve daldırmalı taşlama olarak ayrılabilir; taşlama çarkı çalışma yüzeyinin türüne göre, çevresel taşlama, yüzey taşlama ve çevresel yüz taşlama olarak sınıflandırılabilir.
Şekil 2'de gösterilen taşlama yöntemleri ve teknikleri özel koşullara göre seçilmelidir. Örneğin, bir düzlem yüzey taşlanırken, ekipmana, işleme koşullarına ve işleme alışkanlıklarına bağlı olarak yüzey taşlama veya çevresel taşlama kullanılabilir.
Aşındırıcı taşlarla taşlamanın iki temel amacı vardır: Birincisi, sertleştirilmiş çelik ve çeşitli yüksek sertlikte, yüksek mukavemetli, işlenmesi zor alaşımlı malzemelerin yanı sıra seramik, optik cam, kauçuk ve ahşap gibi metalik olmayan malzemeler için bir işleme yöntemi olan yarı finiş ve finiş için iş parçalarını belirli boyutlara ve şekillere işlemektir.
Diğer amaç, yüzey kusur katmanlarını gidermek için çelik kütükler üzerinde ağır hizmet tipi taşlama gibi kaba taşlamada büyük miktarda malzemeyi en düşük maliyetle hızlı bir şekilde kaldırmaktır; burada malzeme kaldırma hızı saatte yüzlerce kilograma ulaşabilir ve toplam kütük kütlesinin 3% ila 7%'sine karşılık gelir.
Son yıllarda, aşındırıcı bant taşlama kademeli olarak teşvik edilmiş ve bazı yönlerden taşlama taşlarının yerini alma eğilimi göstermiştir. Avantajları arasında yüksek taşlama verimliliği, basit ekipman, düşük maliyet ve güçlü uyarlanabilirlik yer alır ve bu da ona "evrensel taşlama" unvanını kazandırır.
Yukarıdakilerden, taşlamanın geniş anlamda sabit aşındırıcı takımlar kullanarak işleme anlamına geldiği görülebilir. Ancak bu kitapta taşlama, dar anlamda taşlama olan yüksek hızlı dönen taşlama taşları kullanılarak yapılan işlemeyi ifade etmektedir.
2. Taşlamanın Özellikleri
Taşlama, aşındırıcı taneler ve aşındırıcı takımlar kullanılarak yapılan işleme için kullanılan genel bir terimdir. Tornalama ve frezeleme gibi kesme işlemleriyle karşılaştırıldığında aşağıdaki özelliklere sahiptir:
(1) Taşlama taşı yüzeyindeki kesici kenarlar çok sert mineral aşındırıcı tanelerdir
Şekilleri, boyutları ve dağılımları rastgele bir durumdadır. Aşındırıcı takım özellikleri ve taşlama koşullarındaki farklılıklar nedeniyle, taş yüzeyindeki gerçek taşlama taneleri, yüzeydeki toplam tane sayısının 10% ila 50%'sini oluşturur. Şu anda elmas aşındırıcı taneler ve kübik bor nitrür (CBN) taneleri de uygulanmaktadır.
(2) Taşlamadaki her bir aşındırıcı tanenin kesme kalınlığı çok incedir
Genellikle sadece 1-10μm, bu nedenle işlenmiş yüzeyde yüksek doğruluk ve düşük yüzey pürüzlülüğü elde edilebilir. Tipik olarak, Ra0.1-0.05μm yüzey pürüzlülüğü değerleri ile IT6-IT7 boyutsal tolerans dereceleri elde edilebilir. Ayna taşlama için yüzey pürüzlülük değerleri Ra0.04-0.01μm'ye ulaşabilir. Böylece, taşlama ile elde edilen doğruluk ve yüzey pürüzlülüğü diğer kesme işlemlerinden daha üstündür.
(3) Aşındırıcı tanelerin kesme hızı yüksektir.
Genel taşlamada, taşlama çarkının doğrusal hızı 35-60 m/s'dir ve bu hız sıradan kesici takımların 20 katından fazladır ve daha yüksek talaş kaldırma oranlarına olanak tanır. Günümüzde, farklı aşındırıcı takımlar kullanılarak, ultra yüksek hızlı taşlama için taşlama taşı doğrusal hızları 120-300m/s'ye ulaşabilir ve bu da yüksek elastikiyete sahip malzemelerin işlenmesini mümkün kılar. Her bir talaş çok küçük olsa da, genel işleme verimliliği artırılabilir.
(4) Taşlama taşı aşındırıcı taneleri yüksek sertliğe ve iyi termal kararlılığa sahiptir.
Sadece çelik, dökme demir ve diğer malzemeleri değil, aynı zamanda sertleştirilmiş çelik, karbürler, cam, seramik ve taş gibi çeşitli yüksek sertlikteki malzemeleri de taşlayabilirler. Bu malzemelerin geleneksel tornalama, frezeleme ve diğer yöntemlerle işlenmesi zordur.
(5) Aşındırıcı taneler belirli bir kırılganlığa sahiptir.
Taşlama sırasında, aşındırıcı tanelerin ön tarafındaki aşınmış kesici kenarlar, aşırı taşlama kuvvetleri altında kırılır ve yeni keskin kesici kenarlar oluşturur. Bu, taşlama taşlarının "kendi kendini bileme etkisi" olarak bilinir.
(6) Taşlama taşlarını giydirmek ve keskinleştirmek kolaydır.
Taşlama taşlarının aşındırıcı kesici kenarları çok yüksek sertliğe sahiptir, ancak aynı zamanda aşındırıcı kesici kenarları giydirmeyi ve keskinleştirmeyi kolaylaştıran belirli bir kırılganlığa sahiptir. Elmas taşlama taşları için bile, düşük tane kırılganlığı nedeniyle, bakır alaşımları veya reçine bağlayıcılar gibi daha yumuşak metal bağlayıcıların kullanılması, bağlayıcı yok edildiğinden ve taneler düştüğünden, cam gibi oldukça kırılgan malzemeleri işlerken elmas taşların giydirilmesini mümkün kılar.
(7) Öğütme noktasındaki sıcaklık yüksektir.
Birim hacimdeki talaşı kaldırmak için belirli miktarda enerji gereklidir ve talaş boyutu küçüldükçe daha fazla enerjiye ihtiyaç duyulur. Aşındırıcı taneler ve iş parçası arasında güçlü sürtünme ve hızlı plastik deformasyon meydana gelir, bu da büyük miktarda taşlama ısısı üretir ve taşlama sıcaklıkları 1000-1500°C'ye ulaşır. Bu nedenle, taşlama sırasında soğutma için büyük miktarda kesme sıvısına ihtiyaç duyulur.
3. Temel Taşlama Parametreleri
Taşlama işlemi sırasında, taşlama taşı ve iş parçası Şekil 3'te kısaca sınıflandırıldığı gibi birbirlerine göre hareket eder.
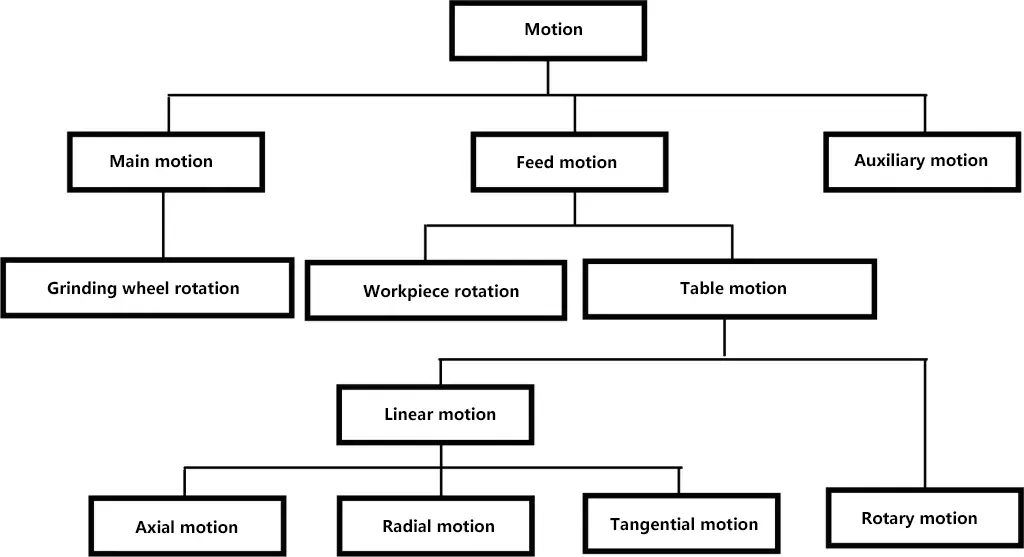
Genellikle dış silindirik taşlama, iç silindirik taşlama, yüzey taşlama, form taşlama, diş taşlama ve dişli taşlama dahil olmak üzere birçok taşlama yöntemi vardır. Bununla birlikte, taşlama taşının çalışma yüzeyine bağlı olarak, Şekil 2 ve Tablo 1'de gösterildiği gibi temel olarak çevresel taşlama, yüzey taşlama ve form taşlama olarak sınıflandırılabilirler. Farklı taşlama yöntemlerinin çeşitli hareketlerine göre, bunlar iki tipte özetlenebilir: birincil hareket ve besleme hareketi.
(1) Birincil Hareket
Metali iş parçasından doğrudan kaldıran ve talaşa dönüştüren harekete birincil hareket denir. Taşlamada, taşlama çarkının dönme hareketi birincil harekettir. Birincil hareket hızı yüksektir ve takım tezgahının gücünün çoğunu tüketir.
Taşlama çarkının maksimum çapındaki teğetsel hız, taşlama hızı vs. Yani
vs=πdsns/1000×60
Nerede
- vs - öğütme hızı (m/s);
- ds - taşlama taşı çapı (mm);
- ns - taşlama taşı dönüş hızı (d/dak).
Dış silindirik ve yüzey taşlama için taşlama hızı genellikle 35-60m/s iken, iç taşlama için genellikle 15-30m/s'dir. Yukarıdaki denklemden, aşınma nedeniyle taşlama taşı çapı azaldıkça, taşlama hızının düşeceği, taşlama kalitesini ve üretim verimliliğini etkileyeceği görülebilir. Bu nedenle, taşlama çarkı çapı belirli bir değere düştüğünde, makul bir taşlama hızı sağlamak için çark değiştirilmeli veya çark hızı artırılmalıdır.
(2) Besleme Hareketi
İş parçası yüzeyinin tamamını kademeli olarak kesmek için kesilecek metali kesme işlemine sürekli olarak besleyen harekete besleme hareketi denir.
Dış silindirik taşlamada, iş parçasının kendi ekseni etrafındaki dönme hareketi, iş parçasının dairesel besleme hareketidir; iş parçasının ileri geri doğrusal hareketi, iş parçasının eksenel besleme hareketidir (uzunlamasına besleme hareketi olarak da adlandırılır); taşlama çarkının enine hareketi, çarkın radyal besleme hareketidir (enine besleme hareketi olarak da adlandırılır).
1) İş parçası dönme hareketi
İş parçası çevresel besleme hareket hızı v için hesaplama formülüw (m/dak) ise
vw=πdwnw/1000
Nerede
- dw - iş parçası çapı (mm);
- nw - iş parçası dönüş hızı (d/dak).
İş parçası çevresel hızı genellikle 10-30 m/s'dir ve işleme gereksinimlerine göre seçilir. Daha yüksek hassasiyet için daha düşük bir hız seçilebilir; aksi takdirde daha yüksek bir hız seçilebilir. Gerçek üretimde, iş parçası hızı genellikle önce seçilir, ardından takım tezgahı hızını ayarlamak için iş parçası dönüş hızı hesaplanır. Bu amaçla, yukarıdaki formül şu şekle dönüştürülebilir
nw=1000vw/πdw≈318vw/dw
2) Eksenel besleme hareketi
Eksenel besleme hareketi, çalışma tablasının taşlama taşı eksenine paralel yönde hareketini ifade eder. Eksenel besleme miktarı (uzunlamasına besleme miktarı), her bir iş parçası dönüşü (veya her bir strok) için çalışma tablasının taşlama taşı eksenine göre hareketini ifade eder ve fa (mm/r).
Eksenel ilerleme miktarı taşlama taşının genişliği ile sınırlıdır ve seçim yaparken aşağıdaki formül kullanılarak hesaplanabilir
fa=(0.1~0.8)B
Burada B, taşlama çarkının genişliğidir (mm).
Çalışma tablası eksenel ilerleme hızı (mm/dak) için hesaplama formülü şöyledir
vfa=nwfa
3) Radyal besleme hareketi
Taşlama taşı kızağının çalışma tezgahına dik yöndeki radyal besleme miktarı, her bir iş parçası dönüşü (veya her bir strok) için taşlama taşı kızağı tarafından radyal beslemenin yer değiştirmesini ifade eder ve f olarak gösterilir. Radyal besleme hareketi genellikle süreksizdir ve taşlama taşı yalnızca her bir iş parçası strokunun sonunda radyal olarak beslenir. Bu nedenle, radyal besleme miktarı f mm/tek strok veya mm/çift strok olarak ifade edilir.
Dış silindirik taşlama için, enine besleme miktarı olarak da bilinen besleme miktarı, taşlama taşının iş tablasının her uzunlamasına ileri geri hareketinin sonunda enine hareket ettiği mesafeyi ifade eder. Daha büyük bir besleme miktarı daha yüksek üretkenlikle sonuçlanır, ancak taşlama hassasiyetini artırmak ve yüzey pürüzlülüğü değerlerini azaltmak için elverişsizdir.
Besleme miktarı ap iş parçası yüzeyine dik olarak ölçülen taşlama taşı kesme derinliğini ifade eder, bu nedenle
ap=(D-d)/2
Nerede
- D - besleme öncesi iş parçası çapı (mm);
- d - besleme sonrası iş parçası çapı (mm).
Tipik olarak, dış silindirlerin kaba taşlanması için birp=0.01-0.025mm; dış silindirlerin finiş taşlaması için, ap=0,005-0,015 mm, finiş taşlama için daha küçük değerler ve kaba taşlama için daha büyük değerler.
Modern yüksek hızlı harici silindirik taşlama makineleri için, harici silindirlerin kaba taşlaması birp=0,05-0,5 mm; dış silindirlerin finiş taşlamasında birp=0.005-0.015mm.
(3) Temas yayı uzunluğu lg taşlama taşı ve iş parçası arasında
l için hesaplama formülüg o
lg≈√(apDs)
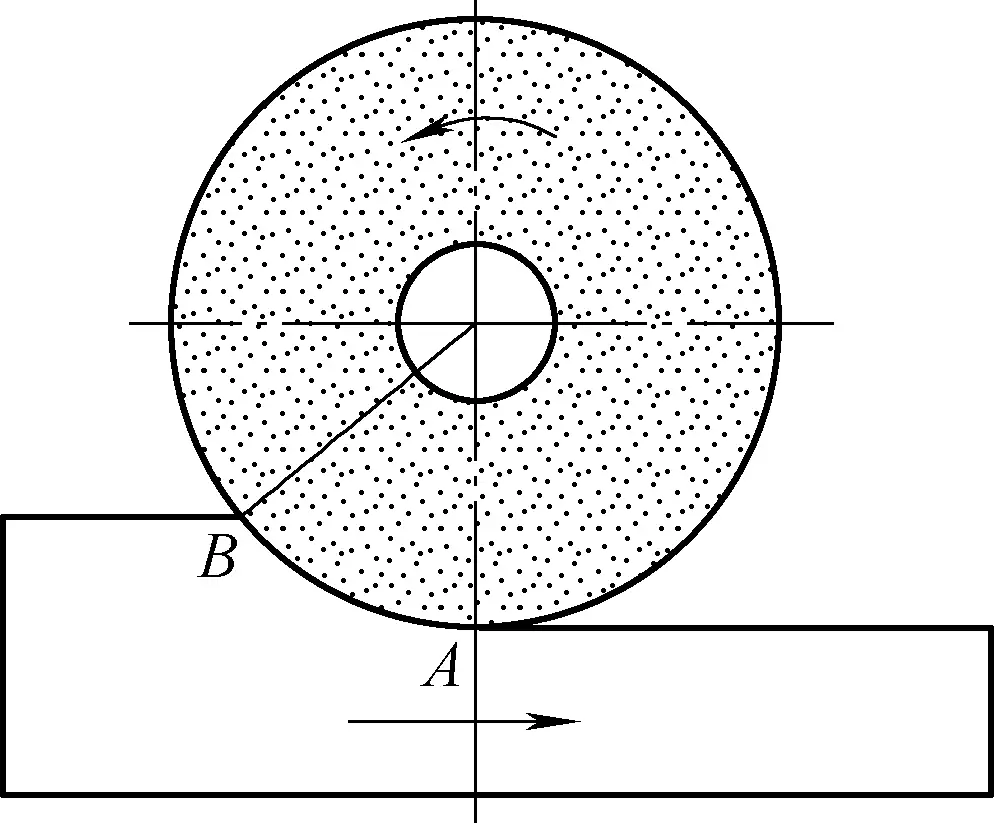
Şekil 4'te gösterildiği gibi, lg ısı kaynağının boyutunu gösterir. Daha büyük lg taşlama ısı kaynağı ne kadar büyükse, soğutma ve talaş kaldırmayı zorlaştırır ve taşlama taşı tıkanmaya eğilimlidir. Genel olarak, iç silindirik taşlama en uzun temas arkı uzunluğuna sahiptir, bunu yüzey taşlama takip eder ve dış silindirik taşlama en küçüktür.
(4) Ortalama taşlama kalınlığı acg
Ortalama taşlama kalınlığı a için hesaplama formülücg o
acgmax=2vwlx/vs√[(1/dw±1/Ds)fr]
Formülde, v ne kadar küçüksew/vs değeri ne kadar küçükse, acgmax olacaktır, bu nedenle yüksek hızlı taşlama faydalıdır; bircgmax √f ile orantılıdırr, taşlama derinliği fr 1 kat artar, acgmax sadece yaklaşık 40% artar, üretim verimliliğini artırma perspektifinden bakıldığında, fr (derin öğütme yöntemi) v değerini artırmaktan daha faydalıdır.w; aşındırıcı taneler arasındaki mesafe l olduğundax azalır (ince tane boyutu), acgmax da azalır, bu nedenle ince öğütme için daha ince aşındırıcı taneler kullanılır; artan Dw ve Ds azaltabilircgmax.
(5) Malzeme kaldırma oranı Qw
Birim zamanda taşlanan iş parçası malzemesi hacmine malzeme kaldırma oranı (mm3/dak). Hesaplama formülü şöyledir
Qw=1000vwfrap
Birim efektif taşlama taşı genişliği başına malzeme kaldırma oranı Q'w (mm)3/mm-min) ise
Q'w=Qw/b
Burada b, tekerleğin etkin taşlama genişliğidir (mm).
Q'w tekerleğin taşlama performansını ve verimliliğini gösterir. Yüksek bir Q'w değeri, iyi öğütme performansını ve yüksek üretim verimliliğini gösterir.
(6) Öğütme oranı G
Öğütme oranı G için hesaplama formülü şöyledir
G=Qw/Qs
Nerede Qs dakikada düşen taşlama taşı malzemesi hacmini temsil eder ve taşlama taşı aşınma oranı olarak da bilinir. Büyük bir G değeri, tekerleğin iyi kesme performansını, yüksek üretim verimliliğini ve iyi ekonomik etkiyi gösterir.
Aşınma oranı G için hesaplama formülü şöyledir
Gs=1/G=Qs/Qw
Küçük bir Gs değeri uzun tekerlek ömrünü ve iyi ekonomik etkiyi gösterir.
(7) Spesifik öğütme enerjisi Uc
N-m/mm birimleriyle, birim hacimdeki (veya kütledeki) malzemeyi çıkarmak için harcanan enerji3 veya J/mm3. Uc genellikle öğütme kuvvetini ve gücünü tahmin etmek için kullanılır. Daha küçük bir Uc malzemenin daha iyi öğütülebilirliğini ve nispeten yüksek talaş kaldırma oranını gösterir.
III. Taşlama kuvvetleri ve taşlama ısısı
1. Öğütme işlemi
Taşlama işleminin özü, iş parçasının metal yüzey tabakasının sayısız aşındırıcı tanenin anlık sıkıştırması, çizmesi, kesmesi ve sürtünme ile parlatması altında taşlanmasıdır. Taşlama sırasında aşındırıcı taneler ile iş parçası arasındaki temas Şekil 5'te gösterilmiştir. Taşlama sırasında talaş oluşum süreci kabaca aşağıdaki üç aşamaya ayrılabilir:
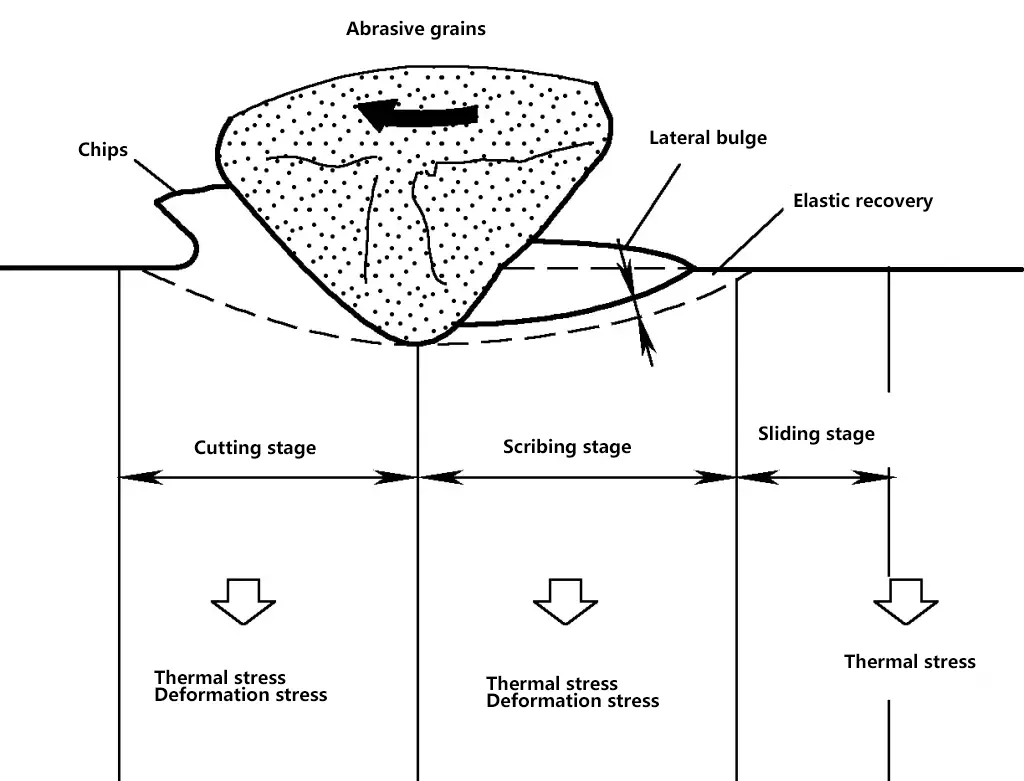
Aşama I: Aşındırıcı tane iş parçasına temas etmeye başlar, ancak onu kesmez, sadece yüzeyde sürtünmeye neden olur ve iş parçasının yüzey katmanında termal stres üretir. Bu aşama kayma sürtünmesi aşaması olarak adlandırılır.
Aşama II: Aşındırıcı tanenin kesme derinliği arttıkça, iş parçasını kademeli olarak keser ve malzemenin her iki tarafta şişmesine neden olarak iş parçası yüzeyinde oluklar oluşturur. İş parçası plastik deformasyonun ikinci aşamasına girer. Bu sırada, aşındırıcı tane ile iş parçası arasındaki sürtünmeye ek olarak, daha da önemlisi, malzemenin iç sürtünmesi ve elastik deformasyonun neden olduğu stres meydana gelir. Bu aşama, iş parçasının yüzey pürüzlülüğünü ve yanıklar ve çatlaklar gibi yüzey kusurlarını etkiler. Bu aşamaya scribing aşaması denir.
Aşama III: Bu noktada, aşındırıcı tane belirli bir derinliğe kadar kesmiştir ve normal kesme kuvveti belirli bir seviyeye yükselmiştir. Kesilen alan da belirli bir sıcaklığa ulaşmıştır, bu da malzemenin bu kısmındaki tanelerin kaymasına ve plastik deformasyonun sürekli artmasına neden olur. Taşlama kuvveti iş parçasının mukavemet sınırına ulaştığında, taşlanmış katman malzemesi ezilme yaşar ve malzeme talaş oluşturmak için kesme düzlemi boyunca kayarak iş parçasının yüzey katmanında termal gerilim ve deformasyon gerilimi üretir. Bu aşamaya kesme aşaması denir.
Taşlama işlemi, kuvvet ve ısı etkileri ile karakterize edilir. Taşlama işlemi sırasında, bazı çıkıntılı ve keskin aşındırıcı taneler, sıkıştırma ve sürtünme etkisi altında belirli bir kalınlıkta metali keser; daha mat taneler sadece yüzey kazımasına neden olurken; düşük çıkıntılı ve mat taneler veya iki bitişik tanenin ikincisi sadece sürtünme üretir. Aşındırıcı taneler tarafından kesilen talaşlar çok küçüktür (ağır taşlama hariç), genellikle şerit benzeri talaşlar, parçalanmış talaşlar ve erimiş küresel talaşlar olarak ayrılır.
2. Öğütme kuvvetleri ve öğütme gücü
(1) Öğütme kuvveti
Taşlama sırasında, taşlama taşı ile iş parçası arasında sürtünme ve talaş deformasyonu meydana gelir, bu da Şekil 6'da gösterildiği gibi taşlama kuvvetleri olarak adlandırılan taşlama taşı ve iş parçası üzerinde etkili olan eşit ve zıt kuvvetlere neden olur.
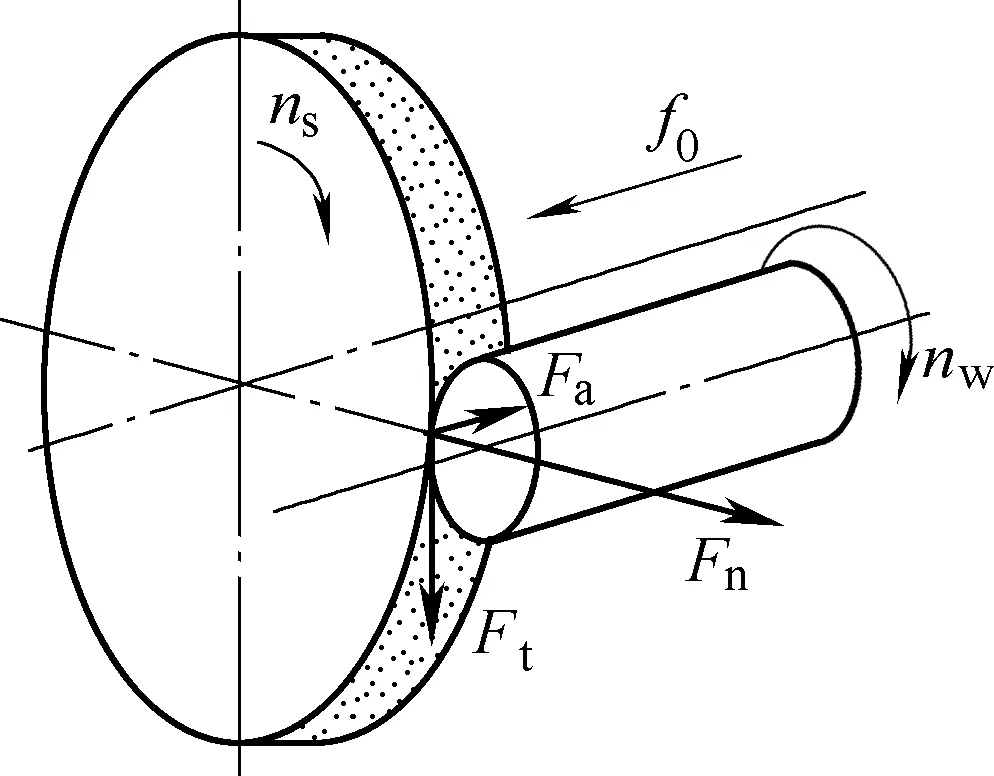
- Ft-Teğetsel taşlama kuvveti
- Fn-Normal taşlama kuvveti
- Fa-Eksenel taşlama kuvveti
Genel dış silindirik taşlamada, taşlama kuvveti karşılıklı olarak dik üç bileşene ayrıştırılabilir: teğetsel taşlama kuvveti Ft (taşlama çarkının dönme çevresi teğeti yönünde); normal taşlama kuvveti Fn (taşlama taşı ile iş parçası arasındaki temas yüzeyine normal yönde, radyal bileşen olarak da adlandırılır); eksenel taşlama kuvveti Fa (uzunlamasına besleme yönünde).
Genel olarak, üç öğütme kuvveti bileşeninin oranı şöyledir: Fa=(0.1~0.2)Ft, Fn=(1.5~3.2)Ft. Buradan, Fn en büyüğüdür ve Fa en küçük olanıdır. Ft taşlama makinesinin motorunun gücünü belirlemek için ana parametredir ve ana taşlama kuvveti olarak da adlandırılır. Fn esas olarak taşlama taşının ve iş parçasının deformasyonuna neden olur, taş körelmesini hızlandırır ve iş parçasının işleme hassasiyetini ve yüzey kalitesini doğrudan etkiler. Fa taşlama makinesinin besleme sistemine etki eder, ancak değeri F'ye kıyasla çok küçüktür.t ve genellikle göz ardı edilebilir.
Taşlama kuvveti bir dinamometre ile ölçülebilir veya ampirik formüller kullanılarak hesaplanabilir (ilgili kılavuzlara bakın). Üretimde, motorun gerçek giriş gücü F(N) temel alınarak da hesaplanabilir. Yani
Ft=PEηE/πnsDs×106
Nerede
- PE - Taşlama kafası motorunun ölçülen giriş gücü (kW);
- ηE - Motor aktarım verimliliği;
- ns - Taşlama taşı hızı (d/dak);
- Ds - Taşlama taşı çapı (mm).
Bu yöntem çeşitli taşlama modları için uygundur, ancak yalnızca teğetsel taşlama kuvvetinin ortalama değerini belirleyebilir.
(2) Öğütme gücü
Öğütme gücü Pm bir taşlama makinesinin güç parametrelerinin tasarlanması veya doğrulanması için temel oluşturur. Yüksek tekerlek hızı ve büyük güç tüketimi nedeniyle, gerektiğinde doğrulama gereklidir. Ana hareket tarafından tüketilen güç, yani taşlama gücü Pm (kW), ise
Pm=Ftvs/1000
Taşlama çarkı motor gücü Ph aşağıdaki formül ile hesaplanır
Ph=Pm/ηm
Burada ηm taşlama makinesinin toplam mekanik iletim verimliliğidir, genellikle ηm = 0,70 ila 0,85.
3. Öğütme ısısı ve öğütme sıcaklığı
Öğütme sırasında, yüksek kesme hızıküçük kesme kalınlığı ve küt aşındırıcı taneler nedeniyle kesme sırasındaki güç tüketimi çok yüksektir, tornalama veya frezelemenin yaklaşık 10 ila 20 katıdır. Tüketilen enerjinin çoğu ısıya dönüştürülür. Bu ısının yaklaşık 80%'si iş parçasına aktarılır (tornalamadaki sadece 3% ila 9%'ye kıyasla), 4% ila 8%'si talaşlar tarafından taşınır, 10% ila 16%'si taşlama taşı tarafından alınır ve küçük bir kısmı iletim ve radyasyon yoluyla dağıtılır.
Yüksek taşlama hızı nedeniyle, ısının iş parçasının derinliklerine nüfuz edecek zamanı yoktur ve anında yüzey tabakasında birikir. Yüzey tabakasının altındaki sıcaklık (yaklaşık 1 mm derinlikte) sadece birkaç düzine derecedir, bu nedenle büyük bir sıcaklık gradyanı oluşturur. Yüzey tabakası sıcaklığı çok yüksek olduğunda, işlenmiş yüzeyde yanıklar ve termal deformasyon meydana gelebilir, bu da yüzey kalitesini ve işleme hassasiyetini etkiler. Bu nedenle, taşlama sıcaklığını kontrol etmek ve azaltmak, taşlama kalitesini sağlamada çok önemli bir adımdır.
Öğütme bölgesi yakınındaki büyük sıcaklık farklılıkları nedeniyle, öğütme sıcaklıkları genellikle kategorilere ayrılır:
(1) Aşındırıcı tane öğütme noktası sıcaklığı
Aşındırıcı kesme kenarı ile iş parçası veya talaşlar arasındaki temas noktaları, taşlama sırasında anlık olarak 1000°C'nin üzerine çıkabilen en yüksek sıcaklığa sahip alanlardır. Bunlar sadece işlenmiş yüzey kalitesini etkilemekle kalmaz, aynı zamanda aşındırıcı tane aşınmasını, parçalanmayı, talaş ve aşındırıcı tane yapışmasını, erimeyi ve taş tıkanmasını da etkiler.
(2) Öğütme bölgesi sıcaklığı
Bu, taşlama taşı ile iş parçası arasındaki temas alanındaki ortalama sıcaklığı ifade eder, genellikle 500-800°C'dir. Zemin yüzeyindeki artık gerilimi, yanıkları ve çatlakları etkiler.
(3) İş parçası ortalama sıcaklığı
İş parçasına aktarılan taşlama ısısı, genellikle sadece birkaç düzine derece olmak üzere toplam sıcaklığını artırır. Bu da iş parçasının şeklini ve boyutsal hassasiyetini doğrudan etkiler.
Taşlama sıcaklığı genellikle taşlama bölgesindeki sıcaklığı ifade eder. Taşlama sıcaklığını azaltmak için, taşlama parametreleri rasyonel bir şekilde seçilmeli, taşlama derinliği azaltılmalı, taşlama hızı uygun şekilde düşürülmeli ve iş parçasındaki yüzey yanıklarını ve çatlakları azaltmak için iş parçası dönüş hızı artırılmalıdır.
Taşlama taşını doğru seçin, daha kaba aşındırıcı taneler seçin, taş sertliğini azaltın ve taşı zamanında giydirin. Gerekirse, geniş gözenekli bir taş kullanın; taşlama sıvısını doğru seçin, basıncı ve akış hızını artırın ve soğutma ve yağlama etkilerini iyileştirmek için uygun dökme yöntemlerini kullanmaya dikkat edin.
IV. Aşındırıcılar ve Aşındırıcı Aletler
1. Geleneksel aşındırıcılar ve aşındırıcı aletler
Aşındırıcı aletler arasında taşlama taşları, taşlama taşları, monte edilmiş uçlar, taşlama segmentleri, kaplanmış aşındırıcılar (zımpara kağıdı, zımpara bantları) ve taşlama macunları bulunur. Taşlama taşı, aşındırıcı alet olarak da bilinen özel bir kesme aletidir. Bir aşındırıcı aletin yapısı üç unsurdan oluşur: Şekil 7'de gösterildiği gibi aşındırıcı taneler, bağlayıcı madde ve gözenekler.
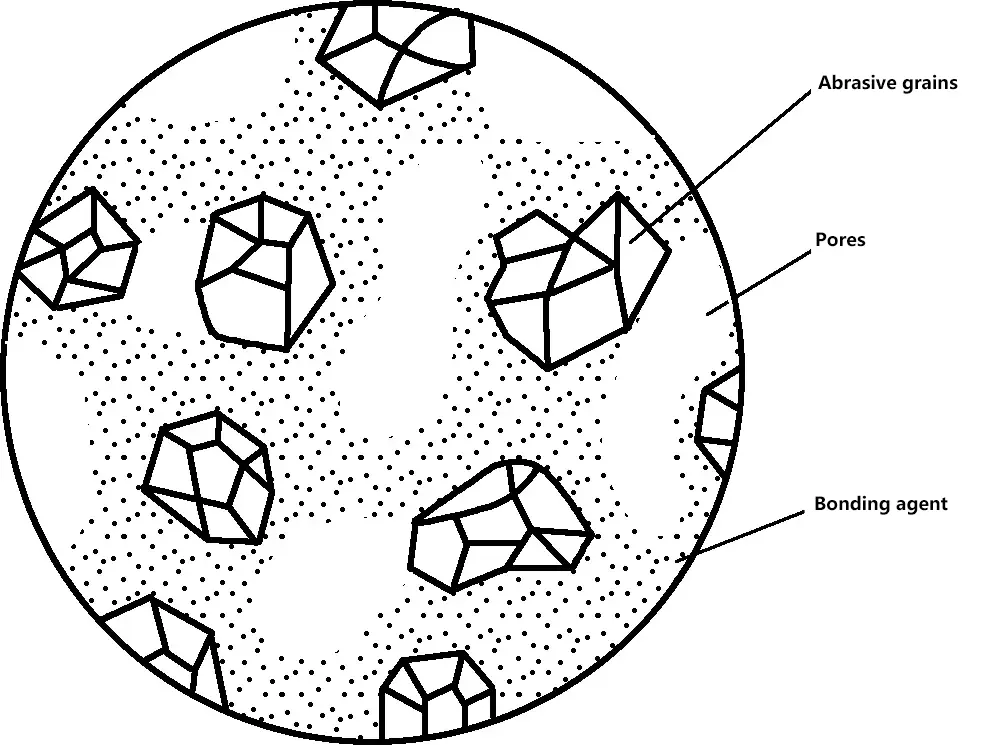
Genel olarak, bağlı aşındırıcı takımlar, aşındırıcı tanelerin karıştırma, kalıplama, kurutma, sinterleme, şekillendirme, statik dengeleme, sertlik testi ve güvenlik rotasyon testi dahil olmak üzere karmaşık bir üretim süreci boyunca bir bağlayıcı madde ile bağlanmasıyla yapılır. Bağlayıcı madde aşındırıcı taneleri belirli bir şekle bağlar; aşındırıcı tanelerin açıkta kalan kısımları kesme işlemini gerçekleştirir; gözenekler talaşları, taşlama sıvısını barındırır ve ısı dağılımına yardımcı olur.
Aşındırıcı aletlerin performansını artırmak için gözeneklere kükürt, molibden disülfür, balmumu, reçine vb. gibi belirli dolgu maddeleri emdirilebilir. Bazıları bu emdirilmiş maddeleri bağlı aşındırıcı aletlerin dördüncü unsuru olarak görmektedir.
Aşındırıcı takımların çalışma özellikleri, aşındırıcı malzeme, tane boyutu, bağlayıcı madde, sertlik, yapı, şekil ve boyutlar, mukavemet ve statik denge gibi faktörler tarafından belirlenir. Farklı çalışma özelliklerinin, aşağıda kısaca tanıtılan kendi uygulanabilir aralıkları vardır.
(1) Aşındırıcılar
Aşındırıcılar, aşındırıcı aletlerin üretimi için ana hammaddedir ve kesme işinden doğrudan sorumludur. Çeşitli işleme gereksinimlerinin ihtiyaçlarını karşılamak için aşındırıcılar yüksek sertliğe, belirli tokluğa ve mekanik mukavemete sahip olmalıdır. Ayrıca, termal kararlılığa ve kimyasal kararlılığa sahip olmalıdırlar. Şu anda yaygın olarak kullanılan aşındırıcılar arasında kahverengi alüminyum oksit (A), beyaz alüminyum oksit (WA), siyah silisyum karbür (C) ve yeşil silisyum karbür (GC) bulunmaktadır.
Aşındırıcılar iki ana kategoriye ayrılır: doğal aşındırıcılar ve yapay aşındırıcılar. Doğal aşındırıcılar genellikle yüksek safsızlık içeriği ve düzensiz kalite gibi dezavantajlara sahiptir, bu nedenle nadiren kullanılırlar. Şu anda ağırlıklı olarak yapay aşındırıcılar kullanılmaktadır.
Yapay aşındırıcılar ayrıca geleneksel aşındırıcılar (alümina bazlı ve karbür bazlı tipler dahil) ve süper aşındırıcılar (sentetik elmas ve kübik bor nitrür dahil) olarak ikiye ayrılır. Geleneksel aşındırıcıların özellikleri ve uygulama aralıkları Tablo 2'de gösterilmektedir.
Tablo 2 Geleneksel aşındırıcıların özellikleri ve uygulama aralıkları
Kategori | Aşındırıcı adı ve kodu | Özellikler | Uygulama aralığı |
Alümina bazlı | Kahverengi alüminyum oksit A(GZ) | Kahverengi renk, iyi tokluk, nispeten yüksek sertlik, ucuz | Orta karbonlu çelik, düşük karbonlu çelik, düşük alaşımlı çelik, dövülebilir dökme demir, sert bronz vb. öğütmek için uygun, nispeten düşük sertlik ve yüksek plastisiteye sahip malzemelerin öğütülmesi için kullanılır. Yaygın olarak uygulanır |
Beyaz alüminyum oksit WA(GB) | Beyaz renk, kahverengi alüminyum oksitten daha yüksek sertlik, kahverengi alüminyum oksitten daha düşük tokluk. Keskin kenarlar, iyi kendiliğinden bilenme, kahverengi alüminyum okside kıyasla taşlama sırasında daha düşük ısı üretimi | Sertleştirilmiş çelik, yüksek karbonlu çelik, yüksek hız çeliği, dişler, dişliler ve ince duvarlı taşlama için uygun, nispeten yüksek sertlik ve plastikliğe sahip malzemelerin taşlanması için kullanılır parçalar, vb. | |
Tek kristal alüminyum oksit SA(GD) | Açık sarı veya beyaz renk, beyaz alüminyum oksitten daha yüksek sertlik ve tokluk. Küresel parçacıklar, iyi aşınma direnci, güçlü kesme kabiliyeti | Paslanmaz çelik ve yüksek vanadyumlu yüksek hız çeliği ve yüksek mukavemet ve tokluğa sahip diğer malzemelerin taşlanması için uygundur. Düşük yüzey pürüzlülüğü gerektiren yüksek hızlı taşlama ve yüzey taşlama için de kullanılabilir | |
Krom alüminyum oksit PA(GG) | Gül veya pembe renk, beyaz alüminyum oksitten daha yüksek tokluk, beyaz alüminyum okside benzer sertlik, taşlanmış iş parçalarında daha düşük yüzey pürüzlülüğü üretir | Sertleştirilmiş çelik ve alaşımlı çelik aletlerin kenar taşlaması ve dişli parçaların, ölçüm aletlerinin ve alet bileşenlerinin hassas taşlaması için uygundur | |
Mikrokristalin alüminyum oksit MA(GW) | Kahverengi alüminyum okside benzer renk, birçok küçük kristalden oluşan aşındırıcı taneler, iyi tokluk, yüksek mukavemet | Paslanmaz çelik, karbon çeliği, rulman çeliği ve özel sfero döküm malzemelerin taşlanması için uygundur. Ağır hizmet tipi ve yüksek hızlı taşlama için de kullanılabilir | |
Zirkonya alüminyum oksit ZA(GA) | Grimsi-beyaz renk, yüksek tokluk, iyi aşınma direnci | Ağır hizmet taşlama, ısıya dayanıklı alaşımlı çeliklerin, kobalt alaşımlı çeliklerin ve östenitik paslanmaz çeliklerin taşlanması için uygundur | |
Siyah alüminyum oksit BA(GH) | Siyah renk, kahverengi alüminyum oksitten daha düşük sertlik, belirli bir tokluğa sahiptir | Parlatma, pas giderme ve cilalama için uygundur | |
Praseodimyum-neodimyum alüminyum oksit NA(GP) | Grimsi-beyaz renk, beyaz alüminyum oksitten daha yüksek sertlik, beyaz alüminyum oksitten daha düşük tokluk | Sfero dökme demir, yüksek fosforlu dökme demir, paslanmaz çelik ve süper sert yüksek hız çeliğinin taşlanması için uygundur | |
Karbür bazlı | Siyah silisyum karbür C(TH) | Parlak siyah, alümina türlerinden daha yüksek sertlik, düşük tokluk, iyi termal iletkenlik, iyi kendini bileme, keskin kenarlar | Dökme demir, bronz, pirinç gibi düşük sertlik ve mukavemete sahip kırılgan malzemelerin taşlanması ve cam, seramik, deri, kauçuk, plastik, değerli taşlar, yeşim taşı vb. malzemelerin taşlanması, parlatılması ve kesilmesi için uygundur. |
Yeşil silisyum karbür GC(TL) | Yeşil renk, bor karbür ve elmastan sonra ikinci sertlik, düşük tokluk, keskin kenarlar, iyi kendi kendini bileme, nispeten pahalı | Yüksek sertlikteki kırılgan malzemelerin işlenmesinde kullanılır. Siyah silisyum karbür ile aynı uygulamalara ek olarak, esas olarak karbür takımların kenar taşlaması için kullanılır, diş taşlama ve ayrıca değerli taşlar, yeşim taşı, değerli metaller ve yarı iletkenlerin kesilmesi ve parlatılması için de uygundur | |
Bor karbür BC(TP) | Siyah renk, elmastan sonra ikinci sertlik, iyi aşınma direnci | Taşlama ve parlatma aletleri, aşındırıcı aletler ve karbür, seramik ve değerli taşlardan yapılmış hassas bileşenler için uygundur | |
Kübik silisyum karbür SC | Açık yeşil renk; kübik kristal yapı, siyah silisyum karbürden daha yüksek mukavemet, güçlü öğütme kabiliyeti | Paslanmaz çelik gibi sert ve yapışkan malzemelerin taşlanması; yatak oluklarının taşlanması veya yatakların süper finisajı vb. |
Tablo 2'den, daha yüksek gerilme mukavemetine sahip taşlama malzemeleri için, alümina ailesinden daha yüksek tokluğa sahip aşındırıcıların seçilmesi gerektiği görülebilir. Daha düşük gerilme mukavemetine sahip taşlama malzemeleri için, karbür ailesinden daha fazla kırılganlığa ve daha yüksek sertliğe sahip aşındırıcılar seçilmelidir. Kahverengi alüminyum oksit, beyaz alüminyum oksit ve silisyum karbür aşındırıcıların kaliteleri Tablo 3'te gösterilmiştir.
Tablo 3 Kahverengi alüminyum oksit, beyaz alüminyum oksit ve silisyum karbür aşındırıcıların kaliteleri
(Referans GB/T2478-2008, GB/T2479-2008, GB/T2480-2008)
Aşındırıcı tipi | Uygulama | Sınıf |
Kahverengi alüminyum oksit | Seramik bağlı aşındırıcı aletler | A |
Yüksek hızlı zımpara bantları (makine ile işlenmiş tabaka zımpara kağıdı dahil) | A-P1 | |
Sac zımpara kağıdı | A-P2 | |
Reçine ve kauçuk bağlı aşındırıcı aletler | A-B | |
Kumlama, parlatma | A-S | |
Beyaz alüminyum oksit | Seramik bağlı aşındırıcı aletler | WA |
Organik bağlı aşındırıcı aletler | WA-B | |
Kaplamalı aşındırıcılar | WA-P | |
Siyah silisyum karbür | Seramik bağlı aşındırıcı aletler, zımpara bantları | C |
Organik bağlı aşındırıcı aletler | C-B | |
Manuel tabaka tipi kaplamalı aşındırıcılar | C-P | |
Yeşil silisyum karbür | Seramik bağlı aşındırıcı aletler, zımpara bantları | GC |
Organik bağlı aşındırıcı aletler | GC-B | |
Manuel tabaka tipi kaplamalı aşındırıcılar | GC-P |
(2) Tane büyüklüğü
Tane boyutu, aşındırıcı parçacıkların boyutunu temsil eder. Tane boyutunu ifade etmek için iki yöntem vardır: elek yöntemi ve fotoelektrik sedimantasyon veya sedimantasyon tüpü granülometre yöntemi. Elek yöntemi, ağ açıklıklarının boyutu ile ifade edilir.
Mikro taneler sedimantasyon süresi ile ölçülür. GB/T2481.1-1998'e göre, kaba aşındırıcı taneler F4'ten F220'ye kadar 26 sınıfa ayrılır ve daha küçük sayılar daha iri taneleri gösterir. GB/T 2481.2-2009'a göre, mikro taneler F230'dan F2000'e kadar 13 sınıfa ayrılır ve daha büyük sayılar daha ince taneleri gösterir.
Tane boyutu seçimi için dikkat edilmesi gerekenler:
1) Yüksek işleme hassasiyeti gerektiğinde, daha ince tane boyutlarını seçin. Daha ince taneler, daha fazla aşındırıcı partikülün aynı anda kesime katılması anlamına gelir ve çalışma yüzeyinde daha küçük kesme izleri bırakarak daha yüksek yüzey kalitesi sağlar.
2) Aşındırıcı takım ile iş parçası arasındaki temas alanı büyük olduğunda veya taşlama derinliği önemli olduğunda, daha iri taneli aşındırıcı takımlar seçilmelidir. Bunun nedeni, daha iri taneli takımların iş parçası ile daha az sürtünmeye sahip olması ve daha az ısı üretmesidir. Örneğin, düz yüzeyleri taşlarken, taşlama taşının uç yüzünü kullanmak, çevresini kullanmaya kıyasla daha iri taneler gerektirir.
3) Kaba öğütme için tane boyutu, üretim verimliliğini artırabilecek ince öğütmeden daha kaba olmalıdır.
4) Kesme ve oluk taşlama işlemleri için iri taneli, gevşek yapılı ve daha yüksek sertliğe sahip taşlama taşları seçilmelidir.
5) Yumuşak metaller veya sünek metaller taşlanırken, taş yüzeyi talaşlarla kolayca tıkanır, bu nedenle iri taneli bir taş seçilmelidir. Yüksek sertlikteki malzemelerin taşlanması için nispeten iri taneli bir taş seçilmelidir.
6) Form taşlamada, çark şeklini daha iyi korumak için daha ince bir tane boyutu seçilmelidir.
7) Yüksek hızlı taşlamada, taşlama verimliliğini artırmak için tane boyutu normal taşlamaya göre 1-2 kademe daha ince olmalıdır. Bunun nedeni, daha ince tanelerde birim çalışma alanı başına daha fazla aşındırıcı parçacık olması ve her tanenin daha az kuvvet taşıyarak körelmeye daha az eğilimli hale gelmesidir. Farklı tane boyutlarının uygulama aralığı Tablo 4'te görülebilir.
Tablo 4 Farklı tane boyutlu aşındırıcıların uygulama aralığı
F14'ün altında | Kaba taşlama veya ağır hizmet taşlama, deri taşlama, zemin taşlama, kumlama, pas giderme vb. için kullanılır. |
F14~F30 | Çelik külçelerin taşlanması, dökme demir çapaklarının alınması, çelik kütüklerin ve boruların kesilmesi, kaba yüzey taşlama, mermer ve refrakter malzemelerin taşlanması için kullanılır |
F30~F46 | Sertleştirilmiş çelik parçaların, pirinç ve karbürlerin genel yüzey taşlayıcılarda, silindirik taşlayıcılarda, merkezsiz taşlayıcılarda, takım taşlayıcılarda vb. kaba taşlanması için kullanılır. |
F60~F100 | İnce taşlama, çeşitli kesici takım kenar taşlama, diş taşlama, kaba lepleme, honlama vb. için kullanılır. |
F100~F220 | Kesici takım kenar taşlama, diş taşlama, ince taşlama, kaba lepleme, honlama vb. için kullanılır. |
F150~F1000 | İnce taşlama, diş taşlama, dişli ince taşlama, hassas alet parçaları ince taşlama, ince lepleme ve honlama vb. için kullanılır. |
F1000'in üzerinde | Süper ince taşlama, ayna taşlama, ince lepleme ve parlatma vb. için kullanılır. |
(3) Bağlayıcı madde
Yapıştırma maddesinin ana işlevi, aşındırıcı taneleri birbirine bağlayarak belirli şekil ve güçlerde aşındırıcılar oluşturmaktır. Yaygın olarak kullanılan bağlayıcı maddelerin kodları, özellikleri ve uygulama aralıkları Tablo 5'te gösterilmektedir.
Tablo 5 Yaygın aşındırıcı yapıştırma maddelerinin kodları, özellikleri ve uygulama aralıkları
İsim ve kod | Özellikler | Uygulama aralığı |
Vitrifiye bağ V(A) | Kimyasal olarak kararlı, ısıya dayanıklı, asit ve alkaliye dayanıklı, yüksek gözeneklilik, düşük aşınma, yüksek mukavemet, iyi şekil tutma, yaygın olarak kullanılır Bor içeren vitrifiye bağ, yüksek mukavemet, daha az bağlayıcı madde gereklidir, buna bağlı olarak aşındırıcının gözenekliliğini artırabilir | İç taşlama, dış taşlama, merkezsiz taşlama, yüzey taşlama, form taşlama ve diş taşlama, takım bileme, honlama ve süper finisaj için uygundur. Çeşitli çeliklerin, dökme demirin, demir dışı metallerin, camın, seramiklerin vb. taşlanması için uygundur. Yüksek poroziteli taşlama taşları için uygundur |
Reçine bağı B(S) | Yüksek yapışma mukavemeti, bir miktar esnekliğe sahiptir, yüksek sıcaklıklarda kolayca yanar, iyi kendiliğinden bilenir, iyi parlatma özellikleri, asitlere ve alkalilere karşı dayanıklı değildir İletken taşlama taşları yapmak için grafit veya bakır tozu ekleyebilir | İnce diskli taşlar, yüksek hızlı, ağır hizmet tipi, düşük yüzey pürüzlülüğüne sahip taşlama, döküm ve dövme parçaların çapaklarının alınması ve iletken taşlama taşları gibi kaba taşlama, kesme ve serbest taşlama için uygundur |
Güçlendirilmiş reçine bağı BF | Jant mukavemetini artırmak için ilave cam elyaf ağ ile reçine bağı | Yüksek hızlı diskler (vs=60~80m/s), ince disk diskler, kaynak taşlama veya kesme için uygundur |
Kauçuk bağ B(S) | Yüksek mukavemet, reçine bağından daha elastik, daha düşük gözeneklilik, aşındırıcı taneler matlaştıktan sonra kolayca düşer. Dezavantajları arasında zayıf ısı direnci (150°C), asitlere ve alkalilere karşı dayanıklı olmaması ve taşlama sırasında koku oluşması sayılabilir | İnce taşlama, ayna taşlama taşları, ultra ince disk taşları, rulmanlar, bıçaklar, matkap ucu olukları vb. için parlatma taşları ve merkezsiz taşlama için kılavuz taşlar için uygundur |
Manyezit bağı Mg(L) | Vitrifiye bağdan daha düşük yapışma mukavemetine sahiptir, ancak iyi kendiliğinden bilenme özelliklerine sahiptir, çalışma sırasında daha az ısı üretir, bu nedenle bazen belirli işlemlerde diğer bağlayıcı maddelerden daha iyi öğütme etkileri sağlar. Dezavantajı, kolayca hidrolize olması ve ıslak öğütme için uygun olmamasıdır | Zayıf ısı iletkenliğine sahip malzemelerin taşlanması ve aşındırıcı ile iş parçası arasında geniş temas alanları olan taşlama için uygundur Güvenlik tıraş bıçakları, kağıt kesme bıçakları, tarım aletleri, tahıl işleme, zemin ve kolloidal malzeme işleme vb. için uygundur. Tekerlek hızı genellikle 20m/s'den azdır |
(4) Sertlik
Bir aşındırıcının sertliği, aşındırıcının yüzeyindeki aşındırıcı tanelerin kesme kuvvetlerinin etkisi altında bağlayıcı maddeden ayrılma zorluk derecesini ifade eder. Taneler kolayca ayrılırsa, aşındırıcı düşük sertliğe sahiptir ve bunun tersi de geçerlidir. Aşındırıcının sertliğini aşındırıcı tanelerin kendi sertliği ile karıştırmamak önemlidir.
Aşındırıcı sertliğini etkileyen ana faktör bağlayıcı madde miktarıdır; daha fazla bağlayıcı madde daha yüksek aşındırıcı sertliği ile sonuçlanır. Ayrıca, aşındırıcı üretim sürecinde, şekillendirme yoğunluğu, fırınlama sıcaklığı ve süresi aşındırıcının sertliğini etkiler.
Aşındırıcı sertliğinin seçilmesindeki temel prensip, taşlama işlemi sırasında aşındırıcının uygun şekilde kendini bilemesini sağlamak, aşırı aşındırıcı aşınmasını önlemek ve taşlama sırasında aşırı taşlama sıcaklıklarının oluşmamasını sağlamaktır.
1) İş parçası sertliği daha yüksek olduğunda, aşındırıcı sertliği daha düşük olmalıdır ve bunun tersi de geçerlidir. Bunun nedeni, iş parçası sert olduğunda, aşındırıcı tanelerin taşlama sırasında daha yüksek basınç taşıması ve körelme olasılığının daha yüksek olmasıdır. Daha yumuşak bir taş seçmek, zamanında kendi kendini bilemeyi teşvik edebilir ve taşın taşlama performansını koruyabilir.
İş parçası sertliği düşük olduğunda, aşındırıcı taneler daha yavaş körelir. Tanelerin körelmeden önce ayrılmasını önlemek için daha sert bir disk seçilmelidir. Bununla birlikte, iş parçası düşük sertliğe ancak yüksek tokluğa sahip olduğunda, talaşlar tekerleği kolayca tıkayabilir, bu nedenle daha iri taneli ve daha düşük sertlikte bir tekerlek seçilmelidir.
2) Genel olarak, kaba taşlama için ince taşlamaya kıyasla daha sert taşlar seçilir; iç taşlama için, tekerlek ile iş parçası arasındaki temas alanı dış taşlamaya göre daha büyük olduğundan ve bu da iş parçasının ısınmasına neden olabileceğinden, daha yumuşak bir tekerlek seçilmelidir. Bununla birlikte, iç delik çapı küçük olduğunda, tekerlek hızı daha düşük olduğunda ve tekerlek iyi kendini bileme özelliklerine sahip olduğunda, biraz daha sert bir tekerlek seçilebilir; yüksek hızlı taşlama için, tekerlek zayıf kendini bileme özelliklerine sahip olduğundan, tekerlek sertliği 1-2 kademe daha düşük olmalıdır.
3) Form taşlama için, taş şeklini korumak için daha sert bir taş seçilmelidir; süreksiz yüzeyleri taşlarken, aşındırıcı taneler darbe nedeniyle ayrılmaya eğilimli olduğundan, daha sert bir taş seçilebilir.
4) Isı iletkenliği zayıf olan ve yanmaya eğilimli malzemeler için (yüksek hız çeliği aletler, rulmanlar, ince duvarlı parçalar vb. gibi) daha yumuşak jantlar seçilmelidir.
5) Taş ve iş parçası arasındaki temas alanı büyük olduğunda, daha yumuşak bir taş seçilmelidir. Örneğin, yüzey taşlama için bir tekerleğin uç yüzünü kullanırken, tekerleğin dış çapını kullanırken olduğundan daha yumuşak olmalıdır.
6) Yüksek yüzey kalitesinin gerekli olduğu ince taşlama için daha yumuşak bir taş seçilmelidir; düşük yüzey pürüzlülüğü taşlama için genellikle ultra yumuşak taşlar seçilir. Farklı taşlama yöntemleri için sertlik aralığı seçimi Tablo 6'da referans alınabilir.
Tablo 6 Farklı taşlama yöntemleri için sertlik aralığı seçimi
1 | 1-Düzgün silindirik taşlama | |||||||||||||
2 | 2-Merkezsiz silindirik taşlama | |||||||||||||
3 | 3-Rulo taşlama | |||||||||||||
4 | 4-Yüzey (yatay iş mili) taşlama | |||||||||||||
5 | 5-Yüzey (dikey iş mili) taşlama | |||||||||||||
6 | 6-İç taşlama | |||||||||||||
7 | 7-Takım taşlama | |||||||||||||
8 | 8-Diş taşlama | |||||||||||||
9 | 9-Düşük yüzey pürüzlülüğü taşlama | |||||||||||||
1 | 10-Ağır hizmet taşlama | |||||||||||||
1 | 11-Yontma | |||||||||||||
1 | 12-Creep besleme taşlama | |||||||||||||
1 | 13-Çapak alma taşlama | |||||||||||||
FGHJKLMNPQRSTY | ||||||||||||||
Yumuşak ↔ Sert |
2. Süper aşındırıcı aletler
Süper aşındırıcılar elmas ve kübik bor nitrür aşındırıcıları ifade eder. Elmaslar doğal elmasları ve sentetik elmasları içerir. Doğal elmas doğadaki en sert maddedir, üretimi az ve fiyatı yüksektir, bu nedenle sentetik elmaslar genellikle daha sık kullanılır.
Kübik bor nitrür, moleküler formülü BN olan kübik kristal yapıya sahip bor nitrürdür. Kristal yapısı elmasa benzer, sertliği elmastan biraz daha düşüktür ve 72000 ila 98000 HV arasında değişir. Bugüne kadar doğal kübik bor nitrür keşfedilmemiştir ve şu anda yapay olarak üretilmektedir.
(1) Sentetik elmas aşındırıcıların özellikleri
- Karbürler, seramikler, optik cam, yarı iletken malzemeler vb. gibi çeşitli yüksek sertlikte, yüksek kırılganlıkta malzemeleri işleyebilir.
- Elmas aşındırıcı taneler keskin kenarlara, güçlü taşlama kabiliyetine, uzun ömre ve küçük taşlama kuvvetine sahiptir, yeşil silikon karbürün sadece 1/4 ila 1/5'i kadardır, bu da iş parçası doğruluğunu artırmak ve yüzey pürüzlülüğünü azaltmak için faydalıdır.
- Elmas taşlama taşları düşük taşlama sıcaklıklarına sahiptir, bu da iş parçasında yüzey yanmasını, çatlamayı ve yapısal değişiklikleri önleyebilir.
- Elmas taşlama taşları uzun ömürlüdür, düşük aşınmaya sahiptir, çalışma saatlerinden tasarruf sağlar ve kullanımı ekonomiktir.
- Nispeten düşük ısı direnci (700~800°C), yüksek kesme sıcaklıklarında kesme kabiliyetini kaybeder. Ayrıca, elmasın demir elementlerine karşı güçlü bir ilgisi vardır, kimyasal aşınmaya neden olur ve genellikle demir içeren malzemelerin taşlanması için uygun değildir.
(2) Kübik bor nitrür (CBN) aşındırıcıların özellikleri
Kesici takım yapımında kullanılmasının yanı sıra, CBN malzemelerinin en büyük uygulama alanı, yüksek hızlı ve yüksek verimli taşlama ve honlama işlemleri için kullanılan CBN aşındırıcıların üretimidir. Bu, taşlama verimliliğini büyük ölçüde artırabilir ve taşlama hassasiyetini ve kalitesini bir seviye artırabilir.
1) İyi termal kararlılık.
Isı direnci sıcaklığı 1200°C'nin üzerindedir, güçlü kimyasal inertliğe sahiptir ve demir elementlerle kimyasal olarak kolayca reaksiyona girmez. Bu nedenle, sert ve sert çelik parçaların (süper sert yüksek hız çeliği gibi) yanı sıra yüksek sıcaklıklarda yüksek sertlik ve düşük termal iletkenliğe sahip malzemelerin işlenmesi için uygundur.
2) İyi aşınma direnci.
Örneğin, alaşımlı takım çeliğini taşlarken, ömrü sıradan korindon taşlardan 100 kat daha fazladır ve bu da otomatik işlemeye ulaşmaya elverişlidir.
3) Yüksek üretim verimliliği.
Sert alaşımlar gibi malzemeler işlenirken elmas taşlar kübik bor nitrür taşlardan daha üstündür. Bununla birlikte, yüksek hız çeliği, ısıya dayanıklı çelik ve aşındırıcı çelik gibi alaşımlı çelikleri işlerken, talaş kaldırma oranı elmas taşların 10 katı ve beyaz korundum taşların 60-100 katıdır.
4) İyi öğütme kalitesi.
Taşlanmış iş parçasının boyutsal doğruluğu yüksektir, yüzey pürüzlülük değeri düşüktür ve yanma ve çatlamaya eğilimli değildir. Yüzey kalıntı gerilimi korundum taşlara göre daha küçüktür.
5) Düşük işlem maliyeti.
Kübik bor nitrür taşlar pahalı olmasına rağmen, yüksek işleme verimliliği, iyi yüzey kalitesi, uzun kullanım ömrü, boyutsal doğruluğun kolay kontrolü ve düşük hurda oranı gibi avantajlara sahiptir ve bu da genel maliyetleri düşürür.
İki süper sert aşındırıcının ortak özellikleri yüksek sertlik, iyi termal iletkenlik ve keskin kenarlardır, ancak her birinin kendine has özellikleri vardır. Elmas zayıf termal stabiliteye sahiptir ve yüksek sıcaklıklarda demir, krom, vanadyum, tungsten, molibden ve titanyum gibi metallerle karbür oluşturmak için yayılır ve aşındırıcı aşınmasını hızlandırır. Bu nedenle, demir içeren metallerin taşlanması için uygun değildir, ancak dökme demirdeki karbon doymuş olduğundan ve daha fazla difüzyon meydana gelmediğinden çeşitli alaşım dökme demirleri taşlayabilir.
Örneğin, alüminyum-silikon alaşımlı döküm parçalar taşlanırken, daha yüksek işleme yüzeyi kalitesi ve ekonomik faydalar elde edilebilir. Elmas aşındırıcıların ömrü, kuru taşlamaya kıyasla ıslak taşlama ile yaklaşık 40% artırılabilir, bu nedenle mümkün olduğunca ıslak taşlama kullanılmalıdır.
Kübik bor nitrür, demir içeren malzemelerin taşlanması için uygundur ve genellikle krank millerinin, eksantrik millerinin, iç deliklerin, dişlilerin, işlenmesi zor malzemelerin ve yüzeylerin taşlanmasında kullanılır. Yüksek hızlı taşlama ve yüksek ilerleme hızında taşlama sağlayarak yanma olmadan düşük yüzey pürüzlülüğü değerleri elde edebilir ve taşlama verimliliğini artırırken daha yüksek hassasiyet elde edebilir.
CBN taşlar uzun kullanım ömrüne ve iyi taşlama performansına sahiptir ve taş değiştirme, pansuman, makine ayarı ve iş parçası incelemesi için yardımcı zamandan tasarruf sağlar. Taşlama sırasında soğutma için genellikle aşırı basınçlı emülsiyonlar veya yüksek hızlı taşlama sıvıları kullanılır. İki süper sert aşındırıcının uygulama aralıklarının karşılaştırması Tablo 7'de gösterilmektedir.
Tablo 7 İki süper sert aşındırıcının uygulama aralıkları
İş parçası malzemesi | Kübik bor nitrür | Elmas | ||
Islak öğütme | Kuru öğütme | Islak öğütme | Kuru öğütme | |
Çeşitli yüksek hız çelikleri | √ | √ | × | × |
Alaşımlı takım çeliği | √ | √ | × | × |
Paslanmaz çelik, ısıya dayanıklı çelik | √ | √ | √ | × |
Krom çelik | √ | √ | × | × |
Aşındırıcı çelik | × | √ | √ | × |
Dökme demir | × | √ | √ | × |
Karbür | × | × | √ | √ |
Cam, seramik, yarı iletkenler | × | × | √ | √ |
Demir dışı metaller | × | × | √ | √ |
Not: √-Uygulanabilir, ×-Uygulanamaz.
3. Kaplamalı aşındırıcılar
Kaplamalı aşındırıcılar, aşındırıcı tanelerin esnek bir destek malzemesine yapıştırıcılarla yapıştırılmasıyla elde edilen ve genellikle "zımpara kağıdı ve zımpara bezi" olarak bilinen aşındırıcılardır. Şu anda Çin'deki bu ürünler başlıca şunları içerir: zımpara bezi, zımpara kağıdı, zımpara kayışları, zımpara diskleri, flap tekerlekler ve zımpara manşonları.
Kaplamalı aşındırıcıların özellikleri kullanımı kolay, basit ekipman, güvenli çalışma; aşındırıcıların kısa üretim döngüsü ve düşük fiyattır. Kağıt zımpara bantları ve çelik kağıt taşlama disklerinin piyasaya sürülmesiyle, kaplamalı aşındırıcıların uygulama aralığı daha da genişlemiştir.
(1) Kaplamalı aşındırıcıların sınıflandırılması ve özellikleri
1) Kaplamalı aşındırıcıların sınıflandırılması
Kaplanmış aşındırıcıların sınıflandırılması Tablo 8'de gösterilmektedir.
Tablo 8 Kaplamalı aşındırıcıların sınıflandırılması
İsim | Tip |
Kum Bezi | Su geçirmez kum bezi |
Flap tekerleği | |
Rulo kum bezi | |
Zımpara Kağıdı | Su geçirmez zımpara kağıdı |
Sac zımpara kağıdı | |
Rulo zımpara kağıdı | |
Metalografik zımpara kağıdı | |
Zımpara kayışı | Su geçirmez zımpara bandı |
Kumaş zımpara bandı | |
Su geçirmez kağıt zımpara bandı | |
Kağıt zımpara bandı | |
Kompozit destekli zımpara bandı | |
Dikişsiz zımpara bandı | |
Eklemli zımpara bandı | |
Örtüşen zımpara bandı | |
Simetrik zımpara bandı | |
Zımpara diski | Yapıştırılmış zımpara diski |
Zımpara kovanı | Silindirik zımpara kovanı |
Konik zımpara kovanı | |
Flap tekerleği | Şaftlı klape çarkı |
Ayna klapesi tekerleği |
2) Kaplanmış aşındırıcıların kum boyutu
GB/9258.2-2008, kaplamalı aşındırıcılar için kaba aşındırıcı tanelerin kum boyutunu ve GB/T9258.3-2000, kaplamalı aşındırıcılar için aşındırıcı mikro tanelerin kum boyutunu belirtir.
Kaba aşındırıcı tanelerin kum boyutu 20 kum numarasına ayrılmıştır: P12, P14, P16, P20, P24, P30, P36, P40, P50, P60, P70, P80, P100, P120, P150, P180, P220.
İnce aşındırıcı tozların kum boyutu 13 kum numarasına ayrılmıştır: P240, P280, P320, P360, P400, P500, P600, P800, P1000, P1200, P1500, P2000, P2500.
3) Kaplanmış aşındırıcılar için yapıştırıcılar
Kaplanmış aşındırıcılar için yapıştırıcılar esas olarak aşındırıcı taneleri ve destek malzemelerini yapıştırmak için kullanılan sıvı malzemelerdir. Kaplamalı aşındırıcılar için yapıştırıcıların türleri ve kodları Tablo 9'da gösterilmiştir; kaplamalı aşındırıcılar için çeşitli yapıştırıcıların performansı ve uygulama aralığı Tablo 10'da gösterilmiştir.
Tablo 9 Yapıştırıcı türleri ve kodları
İsim | Hayvan yapıştırıcısı | Yarı reçine yapıştırıcı | Tam reçine yapıştırıcı | Su geçirmez yapıştırıcı |
Kod (taban kat/boy kat) | G/G | R/G | R/R | WP |
Tablo 10 Kaplanmış aşındırıcılar için çeşitli yapıştırıcıların performansı ve uygulama aralığı
Kategori | Cilt Adı | Performans | Uygulanabilir Aralık |
Hayvan Yapıştırıcısı G/G | Yapıştırıcı Gizle | İyi yapışma performansı, düşük mukavemet, suda çözünür, nemden kolayca etkilenir, ortamdan etkilenen stabilite, zayıf ısı direnci, kırılgan, ancak ucuz | Düşük kesme kuvveti ile kuru ve yağlı taşlama için kullanılabilir, ahşap ürünlerin zımparalanması, metalik olmayan ürünlerin işlenmesi, bakır, kurşun ve diğer metallerin taşlanması ve parlatılması için uygundur |
Jelatin | |||
Kemik Yapıştırıcısı | |||
Tam Reçine R/R | Alkid Reçine | Daha yüksek yapışma mukavemeti, suya ve ısıya dayanıklı, daha uzun süre saklanabilir, kuru ve ıslak öğütme için uygundur, ancak organik çözeltilerde çözünür, daha yüksek maliyet | Ağır hizmet tipi taşlama, taşlanması zor malzemeler ve karmaşık yüzeyli metal şekillendirme taşlama ve parlatma için uygundur |
Amino Reçine | |||
Su Geçirmez Zımpara Verniği | |||
Yarı reçine R/C | Üre-formaldehit Reçine Yapıştırıcı Jelatin Gizle | Baz tutkal, iyi elastikiyet, aşınma direnci ve ısı direncine sahip, suya dayanıklı olmayan ancak neme dayanıklı, hayvan tutkalından daha iyi yapışma performansı, üretimi kolay, daha düşük maliyetli, genellikle kuru öğütme için kullanılan hayvan tutkalıdır | Kuru veya yağlı taşlama, orta yüklü taşlama ve şekillendirme yüzeyi işleme için uygundur. Bu tip bağlayıcı, zımpara bandı taşlamada yaygın olarak kullanılmaktadır |
4) Destek Malzemesi
Destek malzemesi, genellikle yumuşak lifli malzemeler kullanılarak, yüksek gerilme mukavemeti, düşük uzama ve iyi su direnci gerektiren kaplamalı aşındırıcılardaki aşındırıcıların ve bağlayıcıların taşıyıcısını ifade eder. Destek malzemeleri ve kaplamalı aşındırıcıların kullanım alanları Tablo 11'de; destek malzemesi sınıflandırmaları ve kodları Tablo 12'de gösterilmektedir.
Tablo 11 Kaplamalı Aşındırıcıların Destek Malzemeleri ve Kullanım Alanları
Destek Malzemesi Kategorisi | Malzeme | Kullanım Alanları |
Kumaş Destek | Kaba ve ince dimi, düz dokuma ve kanvas vb. | Kuru zımparalama, su geçirmez zımpara kağıdı, zımpara bantları vb. |
Kağıt Destek | Kraft kağıt, su geçirmez kraft kağıt, vulkanize elyaf kağıt, vb. | Kuru zımparalama, su geçirmez zımpara kağıdı, vulkanize fiber diskler vb. |
Vulkanize Elyaf Destek | Vulkanize elyaf kağıttan yapılmış destek. Not: Vulkanize elyaf kağıt, elyafların fiziksel özelliklerini değiştirmek için selülozun konsantre sülfat veya çinko oksit ile işlenmesiyle elde edilen homojen bir malzemedir | Zımpara bantları, yüksek hızlı vulkanize fiber kağıt, taşlama diskleri vb. |
Kompozit Destek | İki kağıt katmanı arasında örgü kumaş veya vulkanize elyaf kağıt bulunan kumaş ve kağıt kompozitlerinden yapılmış destek | Zımpara bantları |
Tablo 12 Destek Malzemesi Sınıflandırmaları ve Kodları
Tip | Kumaş Destekli Aşındırıcı | Zımpara Kağıdı | Su Geçirmez Zımpara Kağıdı | ||||||||||
Hafif Kumaş | Orta Boy Kumaş | Ağır Kumaş | Sayfa S | Rulo R | Sayfa S | Rulo R | |||||||
Yüzey Yoğunluğu/g-m-2 | ≥110 | ≥170 | ≥250 | 80 | 100 | 120 | 160 | 220 | 80 | 100 | 125 | 160 | |
Kod | L | M | H | A | B | C | D | E | A | B | C | D |
(2) Bez Destekli Aşındırıcılar, Zımpara Diskleri, Flap Tekerlekler ve Zımpara Kovanları
1) Kuru Zımpara Bezi
Kuru zımpara bezi genellikle manuel veya düşük hızlı, düşük basınçlı kuru zımparalama için kullanılır. Yağ bazlı kesme sıvıları kullanıldığında verimlilik ve işleme kalitesi artırılabilir. Neme maruz kaldıktan sonra, kuru zımpara bezi 60-80°C sıcaklıkta hafifçe kurutulabilir; aşırı kurutma kırılmaya neden olabilir.
Kuru zımpara bezi genellikle tabaka (kod S) ve rulo (kod R) şeklinde üretilir; yüzey yoğunluğuna göre hafif (L), orta (M) ve ağır (H) tiplere ayrılır. Hafif bez ahşap, deri, kauçuk ve diğer işlemler için uygunken, ağır bez metal işleme için uygundur.
2) Su Geçirmez Zımpara Kağıdı
Kullanmadan önce yaklaşık 10 dakika 40°C suda bekletilmeli ve yumuşatıldıktan sonra kullanılmalıdır. Kum seçimi: Kaba taşlama için P80-P150, ince taşlama için P180-P280 ve hassas taşlama için P320 ve üstü. Su geçirmez zımpara kağıdı için en yaygın kullanılan iki aşındırıcı cam kumu (kod GL) ve garnettir (kod G).
İşaretleme: Zımpara kağıdı S G/G C230×280 A P80
3) Vulkanize Fiber Diskler
Vulkanize fiber diskler, bağlayıcı olarak yüksek mukavemetli ısıya dayanıklı sentetik reçine kullanılarak yüksek kaliteli vulkanize fiber kağıdın yüzeyine aşındırıcıların yapıştırılmasıyla yapılır ve dairesel ince diskler oluşturur. Vulkanize fiber diskler, taşlama ve parlatma için el tipi makinelere monte edilebilir, metal veya metal olmayan malzemeler üzerinde pas giderme, parlatma ve diğer kuru taşlama işlemleri için kullanılabilir. Kullanımı kolay, yüksek verimli, çok yönlü ve güvenli ve güvenilirdirler. Vulkanize fiber disklerin maksimum çalışma hızı 80m/s'dir.
4) Aşındırıcı Flap Tekerlekler
Flap diskler, tabaka benzeri bez destekli aşındırıcıların eksenden radyal olarak eşit şekilde dağıtılmasıyla oluşturulan tekerlek veya disk şeklindeki aşındırıcı aletlerdir.
Aşındırıcı flap diskler nispeten yüksek işleme verimliliğine sahiptir ve taşlama ve parlatma için yaygın olarak kullanılır. Demir dışı metallerin ve paslanmaz çelik ürünlerin parlatılmasında ve aşındırıcı aletlerin şekilli yüzeylerinin finisajında etkilidirler. Uç yüzlü flap diskler geniş alanların parlatılması ve finisajı için uygundur. Flap disklerin kullanımı uygundur ve elektrikli ve pnömatik aletlerin yanı sıra torna tezgahları, delme makineleri ve diğer takım tezgahları ile kullanılabilir.
Flap tekerlekler için maksimum çalışma hızı: Şafta monteli ve aynaya monteli flap tekerlekler için 35m/s veya 50m/s, çanak şekilli flap tekerlekler için 80m/s.
5) Silindirik Zımpara Kovanları
Kumaş destekli zımpara manşonları (kod S) olarak da bilinen silindirik zımpara manşonları, aşındırıcıların kumaş veya kağıt destek malzemesine yapıştırılmasıyla yapılan silindirik aşındırıcı aletlerdir. Kullanımları flap disklere benzer ve daha yüksek verimlilikle büyük yatakların parlatılması için daha uygundur. Zımpara manşonları, silindirik bez destekli zımpara manşonları (kod SC) ve silindirik kağıt destekli zımpara manşonları (kod SP) olarak ikiye ayrılır.
(3) Zımpara Kayışları
Zımpara kayışları, sonsuz kayışlar ve eklemli kayışlar olarak ikiye ayrılan halka şeklinde kaplamalı aşındırıcılardır. Sonsuz bantlar, destek malzemesi üretim süreçlerindeki sınırlamalar ve düşük üretim oranları nedeniyle kademeli olarak eklemli bantlarla değiştirilmiştir. Şu anda, yerel ve uluslararası zımpara kayışı standartlarında, zımpara kayışları aslında eklemli kayışları ifade etmektedir.
Zımpara kayışı taşlama, 30 yıl içinde nispeten eksiksiz ve bağımsız bir işleme teknolojisine dönüşen yeni bir taşlama işlemidir. Zımpara bantları ikinci nesil kaplamalı aşındırıcı ürünlerdir. Zımpara kayışı taşlama, geniş bir uygulama yelpazesine sahip özel ekipmanlar üzerinde gerçekleştirilen yüksek verimli bir sürekli işleme yöntemidir ve bu nedenle "evrensel taşlama" teknolojisi olarak adlandırılır.
1) Zımpara Bantlarının Sınıflandırılması
Birçok zımpara kayışı türü vardır. Şekle göre, rulo kayışlar ve halka kayışlar vardır; destek malzemesine göre, kumaş kayışlar, kağıt kayışlar ve kompozit destek kayışları vardır; bağlayıcıya göre, hayvansal tutkal kayışları, yarı reçine kayışları ve tam reçine kayışları vardır; çalışma yüzeyine göre, yoğun taneli kayışlar, seyrek taneli kayışlar ve süper kaplamalı kayışlar vardır. Zımpara bantlarının tipleri ve özellikleri Tablo 13'te gösterilmektedir.
Tablo 13 Zımpara Bantlarının Türleri ve Özellikleri
Kemer Tipi | Destek Malzemesi | Çekme Dayanımı/kPa | 600N Yükte Uzama (%) |
Kumaş Kemer | H Kumaş | ≥32 | ≤3.0 |
M Kumaş | ≥20 | ≤4.5 | |
L Kumaş | ≥15 | ≤5.0 | |
Kağıt Kemer | C Tipi Kağıt | ≥8.4 | - |
E Tipi Kağıt | ≥24 | ≤1.5 | |
Çok Eklemli Kayış | E Tipi Kağıt | ≥8 | - |
Kompozit Destek Kayışı | Kompozit Destek | ≥32 | ≤1.0 |
Çok Eklemli Kompozit Destek Kayışı | Kompozit Destek | ≥13 | ≤3.0 |
2) Zımpara bandı kumunun seçimi
Zımpara bandı kumunun seçimi esas olarak işleme koşullarına ve iş parçasının yüzey pürüzlülüğü gereksinimlerine dayanmaktadır. Uygulanabilir aralığı ve elde edilebilir yüzey pürüzlülüğü Tablo 14'te gösterilmiştir.
Tablo 14 Zımpara bandı kumunun uygulanabilir aralığı ve elde edilebilir yüzey pürüzlülüğü
Kum boyutu | Uygulanabilir işleme aralığı | Ulaşılabilir yüzey pürüzlülüğü Ra/μm |
P16~P24 | Dökme demir, kaynaklı parçaların kaba taşlanması ve çapak alma vb. | - |
P30~P40 | İç dairelerin, dış dairelerin, düzlemlerin ve kavisli yüzeylerin kaba taşlanması | >32 |
P50~P120 | İç dairelerin, dış dairelerin, düzlemlerin ve kavisli yüzeylerin yarı finiş ve finiş taşlaması | 1.6~0.8 |
P150~P240 | İnce taşlama, profil taşlama | 0.8~0.2 |
P280~P1200 | İnce taşlama, süper ince taşlama ve ayna perdahlama vb. | 0,2'nin altında |
3) Zımpara bandı yapıştırıcısı seçimi
Zımpara bandı yapıştırıcılarının türleri, özellikleri ve uygulanabilir aralıkları Tablo 9 ve 10'da gösterilmektedir.
Buna ek olarak, bazı zımpara bantlarının reçine tabakası üzerine uygulanan ekstra bir süper kaplama yapıştırıcı tabakası ile özel gereksinimleri vardır.
① Antistatik kaplama yapıştırıcısı.
Esas olarak ahşap ve plastik ürünlerin işlenmesinde kullanılır, bu da zımpara bandının arkası ile destek arasındaki sürtünmeden kaynaklanan statik elektriğin neden olduğu kesme tozunun yapışmasını önleyebilir, bu da üretim güvenliği için faydalıdır.
② Tıkanma önleyici süper kaplama yapıştırıcı.
Zımpara bandı yüzeyinin tıkanmasını etkili bir şekilde önleyebilen, böylece taşlama verimliliğini ve bant ömrünü artıran, esas olarak metal sabundan oluşan bir reçine kaplamadır.
③ Anti-oksidasyon ayrışma süper kaplama yapıştırıcısı.
Elastik polimer malzemelerden ve oksidasyona ve ayrışmaya dayanıklı aktif malzemelerden oluşur. İşleme sırasında soğutma etkisine sahiptir, bu da zımpara bandının ömrünü ve işlenen yüzeyin kalitesini etkili bir şekilde artırabilir.
4) Zımpara bandı destek malzemesinin seçimi
Zımpara bandı destek malzemesinin seçimi esas olarak kullanım gereksinimlerine dayanmaktadır. Yüksek işleme yükleri ve yüksek hızlar için, destek malzemesi daha yüksek mukavemet ve daha düşük uzama gerektirir. Genellikle pamuk ve keten kumaşlar veya naylon ve polyester elyaf kumaşlar destek malzemesi olarak seçilir. Yaygın zımpara bantları genellikle kumaşın alansal yoğunluğuna ve farklı kum boyutlarına bağlı olarak farklı ağırlık derecelerinde tekstil ve kağıt malzemeler kullanır.
Kağıt destekli zımpara bantları kumaş destekli olanlara göre daha pürüzsüz ve eşittir, ancak daha düşük yük taşıma kapasitesine sahiptirler. Kompozit destek malzemeleri her ikisinin de avantajlarını bir araya getirir ve ağır hizmet tipi taşlama için uygundur. İki tür kompozit destek malzemesi vardır: biri iki kağıt katmanı arasına bir örgü kumaş katmanı eklemektir; diğeri ise kağıt desteğin üzerine bir kumaş katmanı eklemektir.