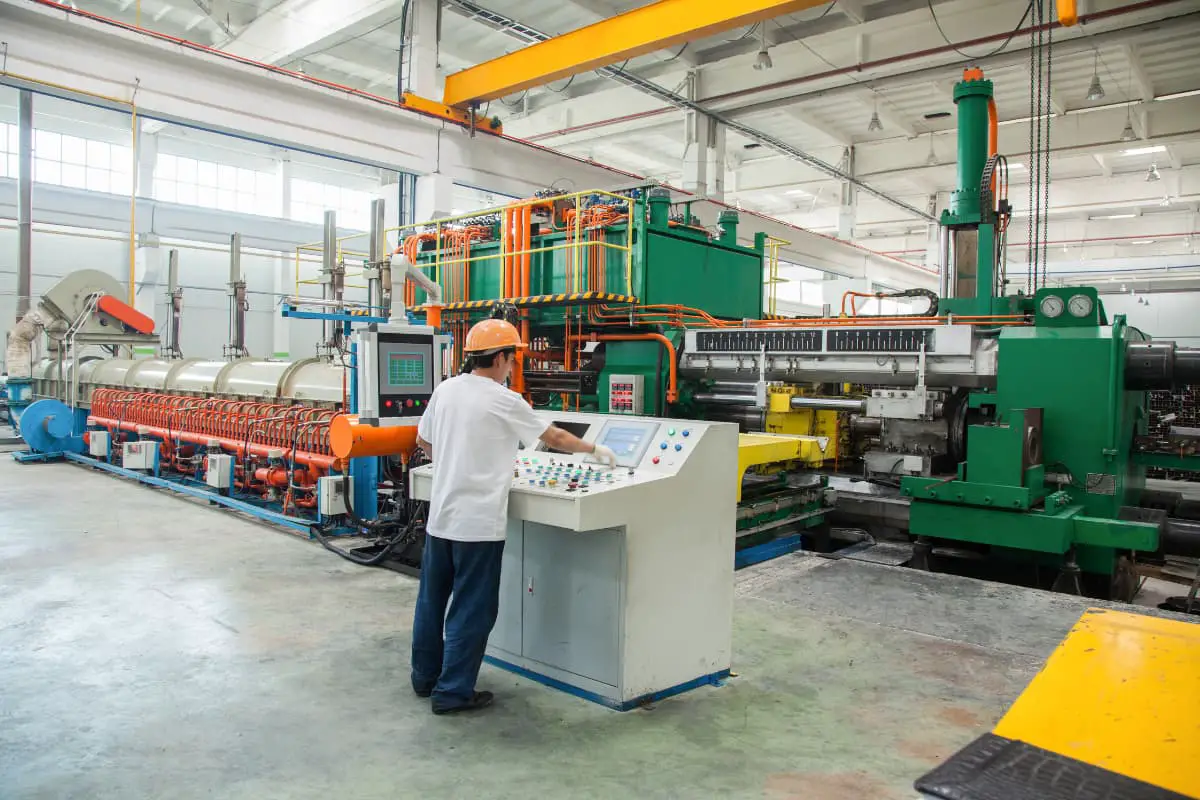
冷間押出工程では、一連の技術的要因により、押出力を正確に計算することが困難です。特に複雑な形状の部品の場合、確立された計算方法や実用的で信頼できる公式や図表がありません。
現在、冷間押出し時の押出し力を計算する一般的な方法には、単純計算、グラフ計算、グラフ解析法などがある。
簡単な計算方法
様々な異なる材料の単位押出力のおおよその値は、表3-13で調べることができ、次に押出の実際の作業面積を乗じておおよその押出力を得ることができる。計算式は
P = pA (3-9)
どこでだ:
- Aは押し出しの加工面積(mm²)です。複雑な形状の部品の場合は、投影面積に基づいて計算します。
- pは単位押出力(MPa)であり、表3-13に示す。
上記の経験則に基づく推定が実際の状況に近く、基本的に要件を満たすことができることは、実践によって証明されている。
グラフィカルな計算方法
ノモグラム法としても知られるこの方法では、冷間押出工程における金属の変形状態が均一であると仮定します。押出断面の減少率、ブランクの大きさ、材料の機械的特性、ダイスの加工部分の形状などの要因を考慮します。
図解計算法を使用するためのもう一つの条件は、押出成形前にブランクが軟化、表面処理、潤滑処理を受けることである。
(1)鋼材の単位押出力のグラフ計算法
図3-9にソリッド押出の単位押出力のグラフ計算を示します。中空押出の単位押出力のグラフ計算を図 3-10 に示す。
表 3-13 押出時の単位押出力の概算値
素材 | 変形状態 | |||||
直接押出 | 間接押出 | クローズド・ダイ・フォーミング | ||||
断面削減率 εA (%) | 単位押出力 ρ/MPa | 断面削減率 εA (%) | 単位押出力 ρ/MPa | 断面削減率 εA (%) | 単位押出力 ρ/MPa | |
純アルミニウム | 97 ~ 99 | 600 ~ 800 | 97 ~99 | ≈800 | 30 ~ 50 | / |
アルミニウム合金 | 92 ~ 95 | 800 ~ 1000 | 75 ~82 | 800 ~ 1200 | 30 ~ 50 | 1000 ~ 1600 |
真鍮 | 75 ~87 | 800 ~ 1200 | 75 ~ 78 | 800 ~ 1200 | 30 ~ 50 | 1000 ~ 1600 |
10スチール | 50 ~ 80 | 1400 ~ 2000 | 40 ~75 | 1600 ~ 2200 | 30 ~ 50 | 1000 ~ 1600 |
30 スチール | 50 ~ 70 | 1600 ~ 2500 | 40 ~ 70 | 1800 ~ 2500 | 30 ~ 50 | 1600 ~ 2000 |
50スチール | 40 ~ 60 | 2000 ~ 2500 | 30 ~ 60 | 2000 ~ 2500 | 30 ~ 50 | 1800 ~ 2500 |
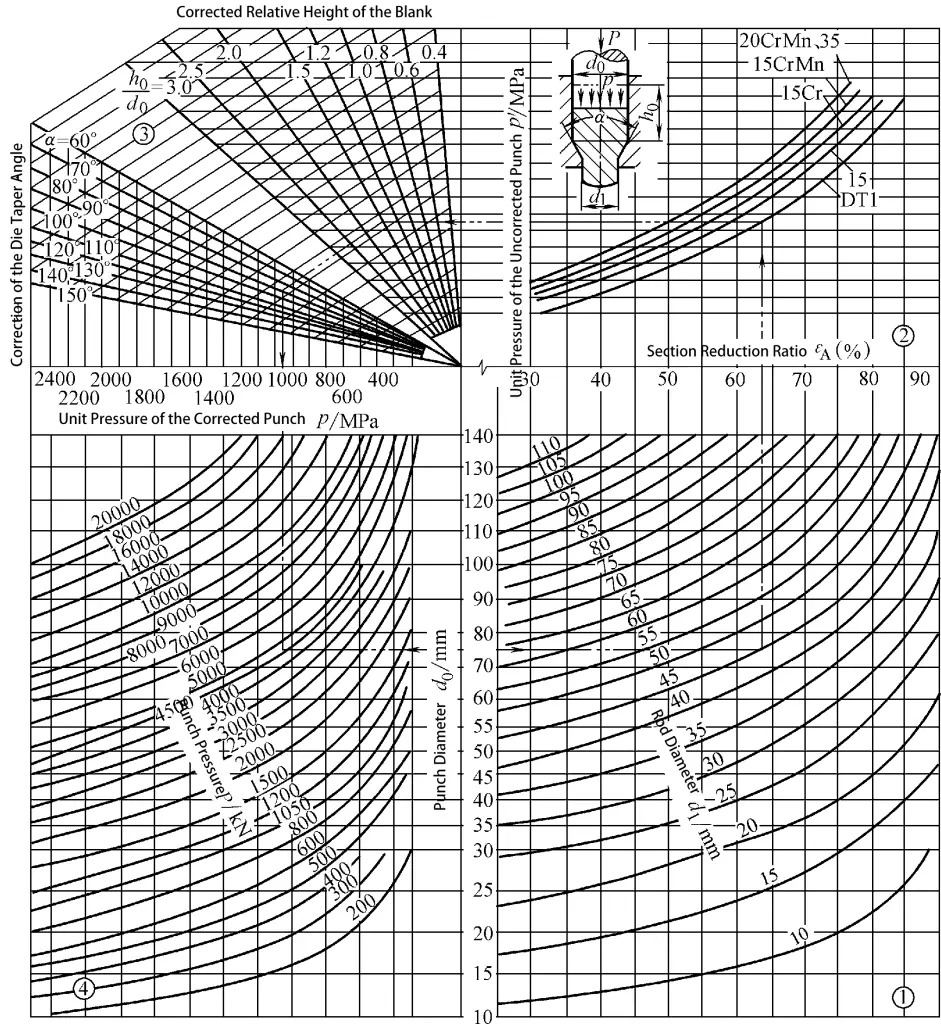
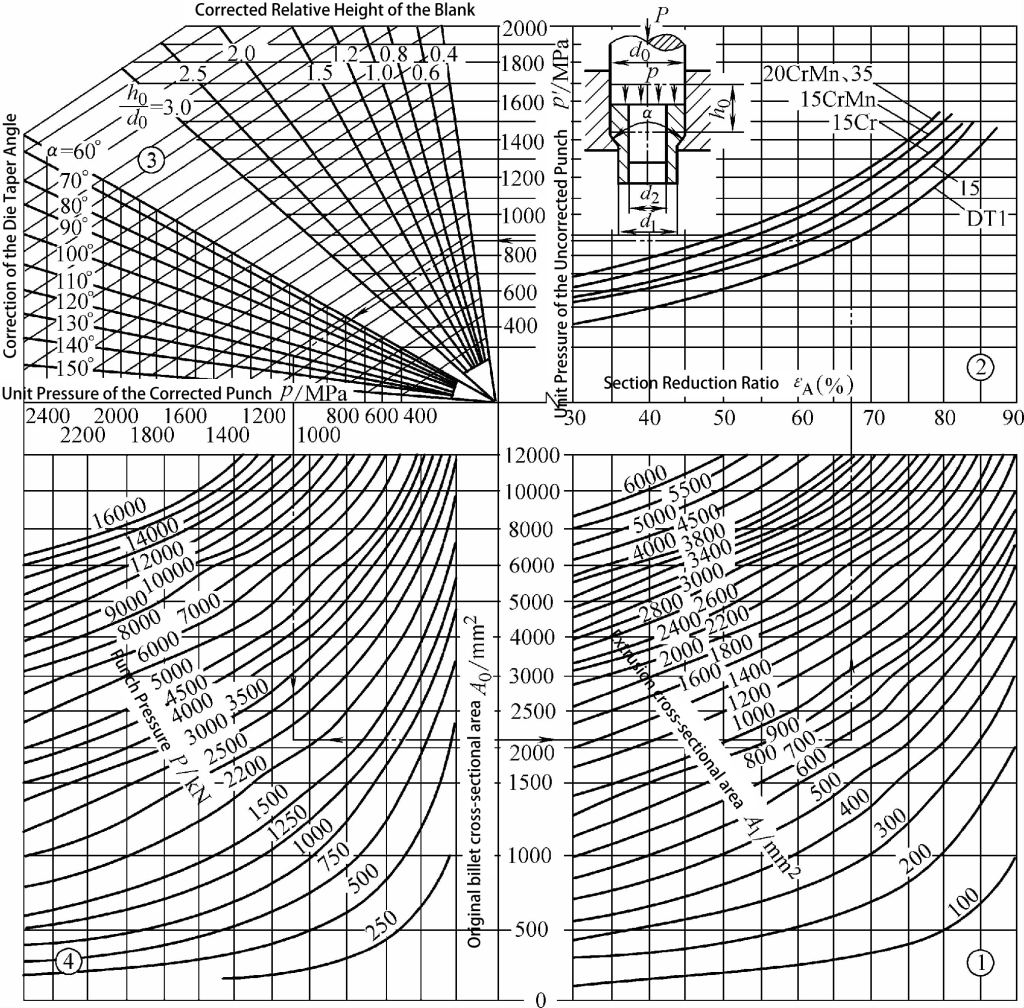
グラフィカルな方法: 図中の矢印の方向に進み、必要な単位押出力と総押出力を求める。
例えば、ソリッド材の直接押出し時の単位押出し力と全押出し力を求める場合:ビレットの直径d1 は75mm、押出棒径d0 は45mm、ビレット高さhは110mm、ダイスコーン角度αは90度。材料は純鉄DT1である。図3-9を参照すると、単位押出力pは1050MPa、全押出力Pは4600kNである。
同様に、中空材の直接押出し時の単位押出し力と全押出し力を求めます:ビレットの直径d0を95mmとし、押出材の外径d1 は85mm、内径d2 は80mm、ビレット高さh0は50mm、ダイスコーン角度αは120度。材料は純鉄DT1である。図3-10を参照すると、単位押出力pは1080MPa、全押出力Pは2230kNである。
(2) 鋼材の後方押出しにおける単位押出し力のグラフ計算
鋼製カップ状部品の後方押出しにおける単位押出し力と総押出し力は、図3-11に示すようにグラフで計算することができる。
チャートの使い方 画像の矢印の方向に従って、必要な単位押出力と総押出力を求めます。
例えば、ビレットの直径(d0)70mm、パンチ直径(d1)は58mm、ビレット高さ(h0)が35mm、材質が純鉄(DT1)の場合、図3-11から、単位押出力(p)は1660MPa、全押出力(P)は4400kNであることがわかります。
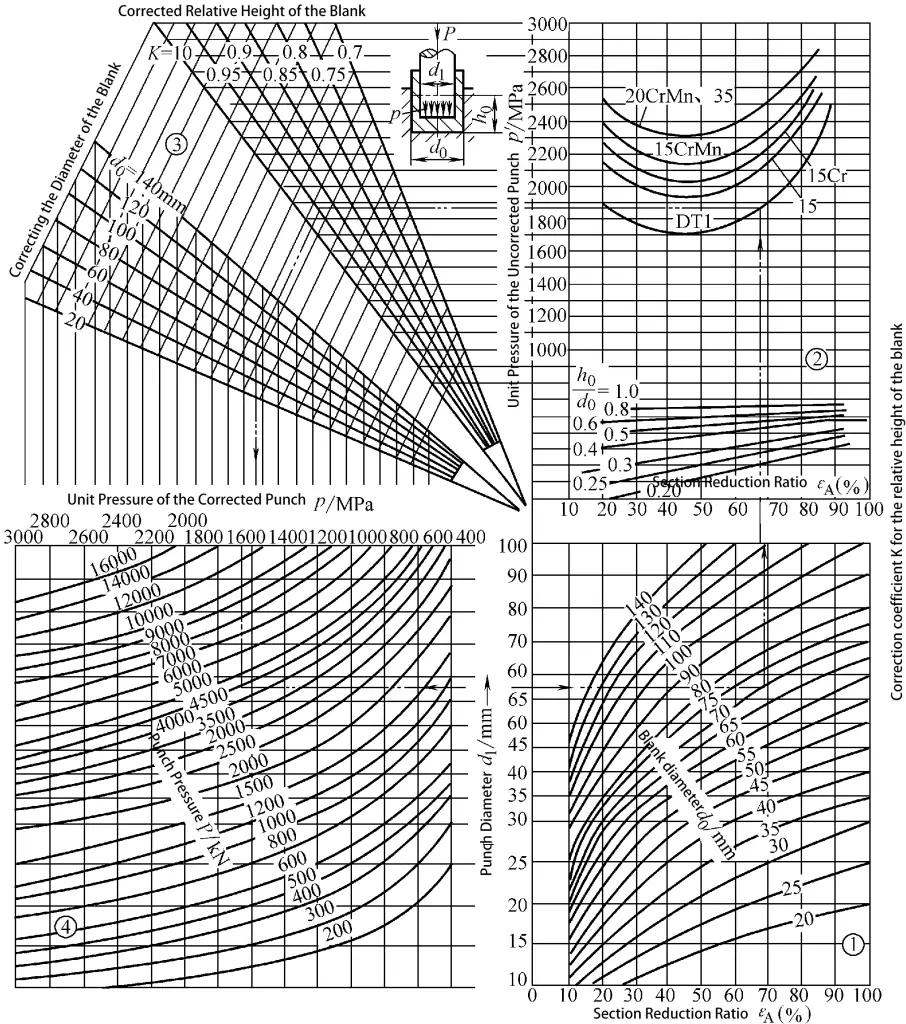
なお、この表は金属材料の一部のみを掲載している。掲載されていない 金属炭素含有量が同程度の金属を表から見つけ、引張強さの比(Rm)を、チャートで求めた押出し力で割って、押出し材の押出し力を求める。
例えば、GCr15軸受鋼の前方押出しにおける単位押出し力を求める場合、GCr15と35鋼の炭素含有量は似て非なるものであり、焼鈍後のGCr15のRmは650~750MPaであるのに対し、焼鈍後の35鋼のRmは530~550MPaであることが分かっている。
図3-9から、対応するサイズの35鋼部品の単位押出力(p)は2000MPaなので、GCr15の単位押出力は約2000×(750/550)MPaで約3000MPaとなる。
(3)非鉄金属の単位押出力のグラフ計算法
図3-12〜図3-14に非鉄金属の中実、中空材の直接押出しとカップ状材の逆押出しの単位押出し力グラフを示します。これらのグラフにおいて、σは材料の平均変形抵抗を表し、変形効率はブランクの高さと断面減少率によって変化します。
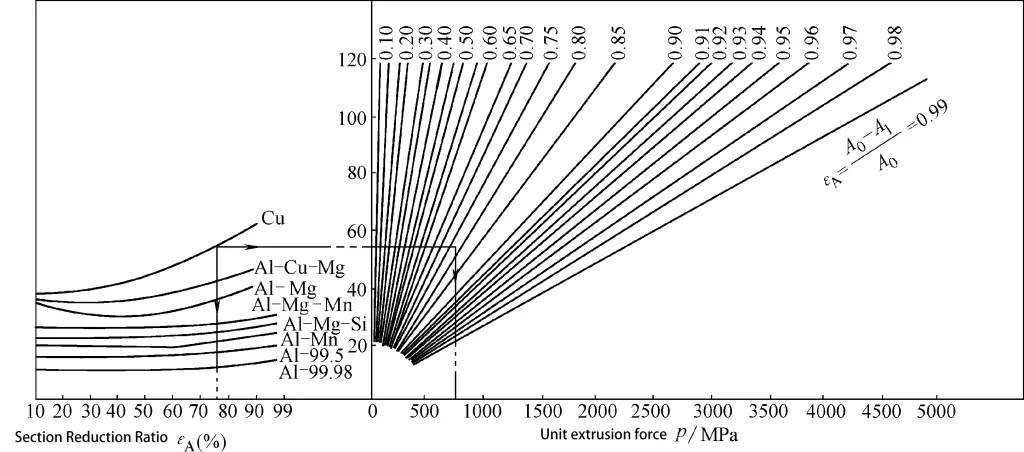
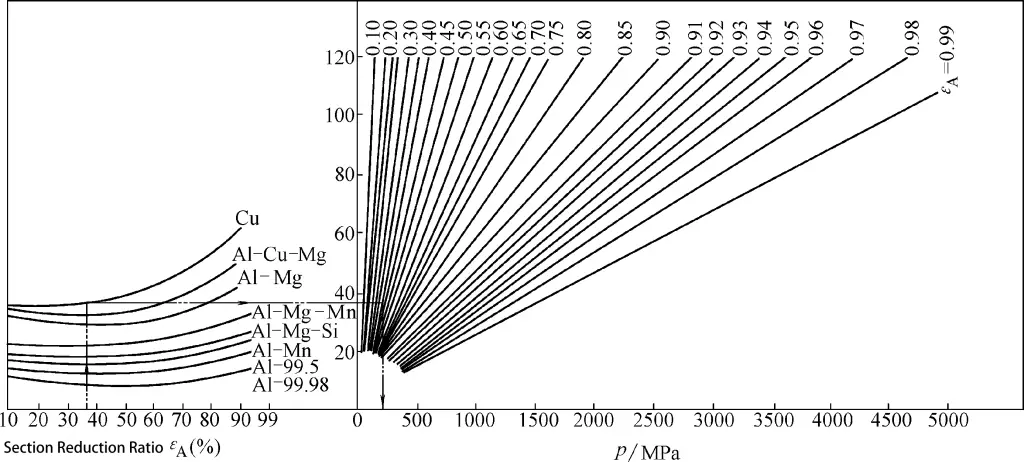
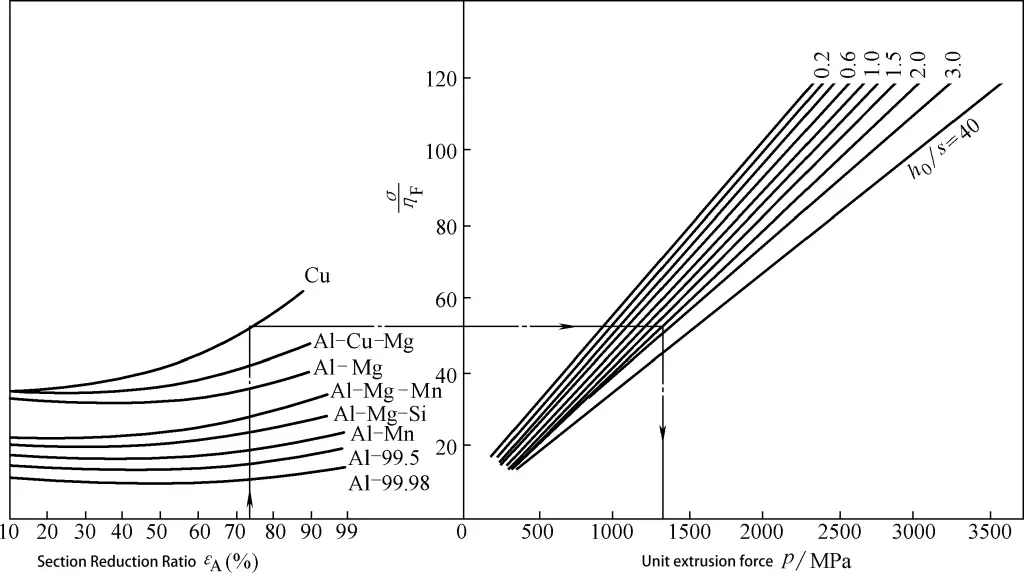
グラフの見方必要な単位押出力は、グラフの矢印の方向に従って求めることができる。
例えば、銅素材から直接押し出されるソリッドピースの単位押し出し力を計算する場合。ブランクの直径(d0)50mm、押出棒径(d1)が24mmであることから、図3-12を参照すると、単位押出力(p)は760MPaであることがわかる。
(4) 鋼材の既知のビッカース硬度に基づく単位押出力のグラフ計算法
金属材料の種類を考慮して作られたグラフは、すべての材料を列挙することはできない。記載されていない材料については、炭素含有量から換算するのは不便です。図3-15、図3-16は鉄鋼材料の焼鈍後のビッカース硬さ(HV)をパラメータとして作成したグラフです。これらのグラフの硬度値が変化するにつれて、得られる単位押出力も変化するはずです。
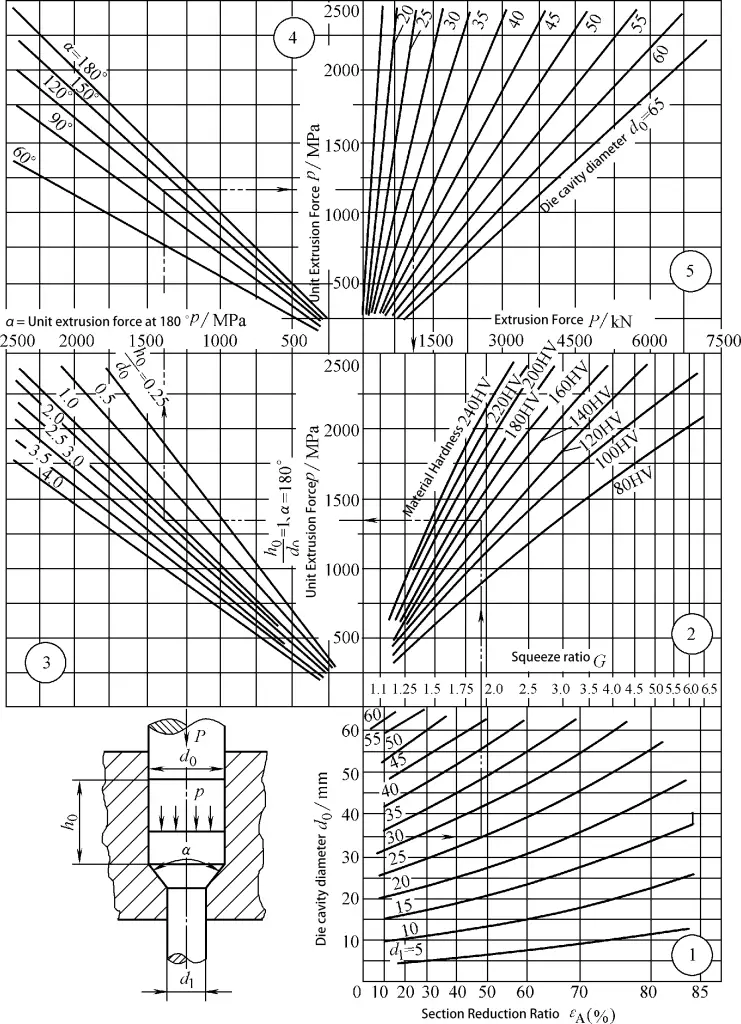
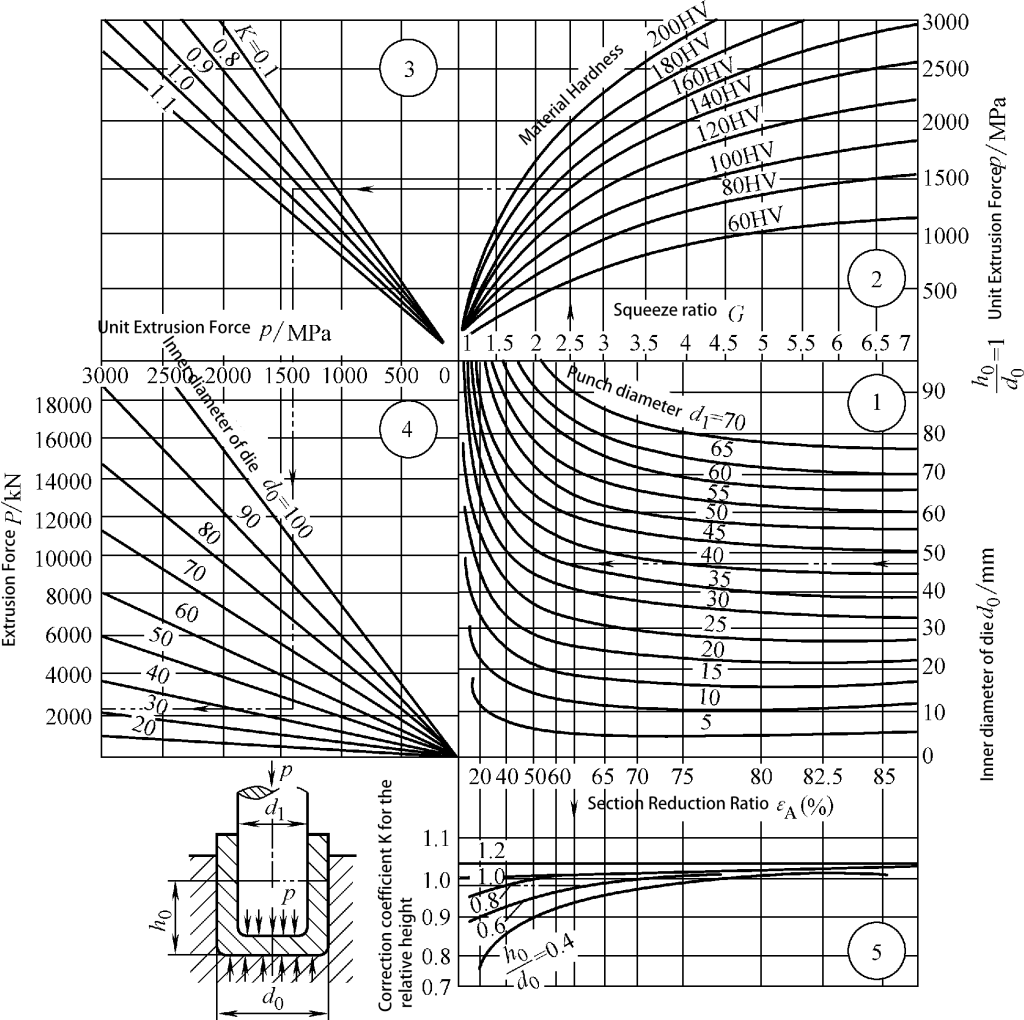
チャートの参照方法:チャートの矢印の方向に従って、必要な単位押出圧力と合計押出圧力を求めます。
例えば、ソリッド材を直接押出成形する際の単位押出圧力と全押出圧力を求める場合。
ブランクの直径d0 は35mm、高さh0 は35mm、押し出し部品の直径d1 図3-15を参照すると、単位押出圧力pは1220MPaであり、全押出圧力Pは1180kNである。
グラフ分析法
単純な棒状やカップ状のワークの押出し圧力は、既存の経験式やチャートを用いて推定することができる。しかし、複雑な形状のワークピースの押出圧力については、包括的な計算方法や実用的で信頼性の高いカラムチャートはありません。
例えば、図3-17に示す部品の直接押出し時の押出し圧力を計算するために直接採用できる既製の公式や図表はありません。したがって、図3-18に示すように、具体的に解析して単純なカップ状の部品に分解して計算する必要がある。
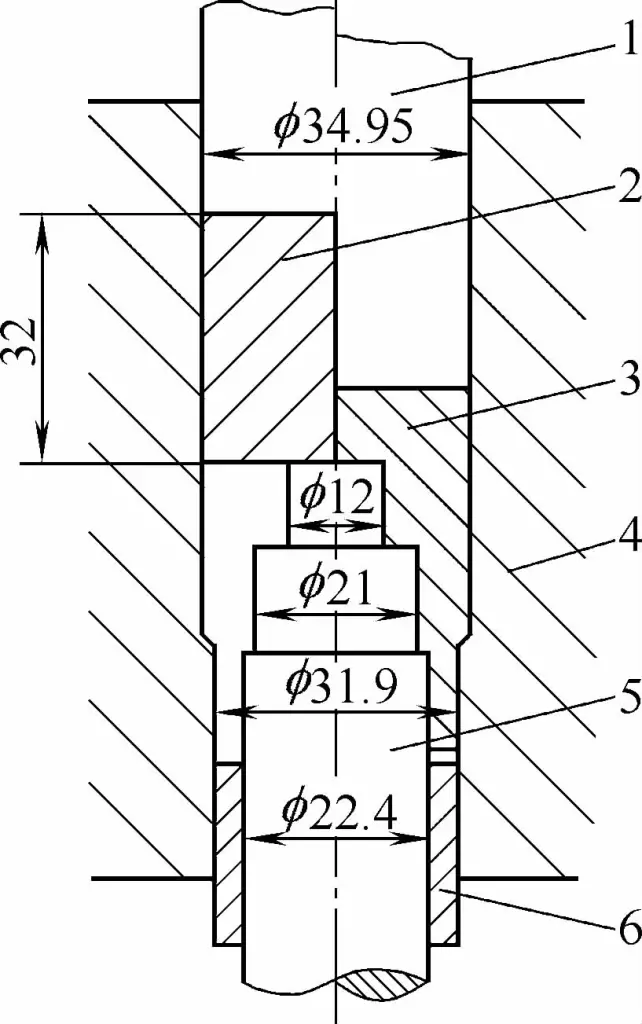
1パンチ
2-ブランク
3押し出し部品
4-ダイ
5-下パンチ
6-アンギュラーエジェクタースリーブ
計算の際、図 3-18a に示す押し出し部品の外側の段差 4 は、まず、直壁の円筒形部品に単純化されます(図 3-18b 参照)。穴 2 と穴 3 の大きさは比較的類似しているため、2 つの穴は 1 つの大きな穴と見なすことができ、図 3-18c に示す形状になります。
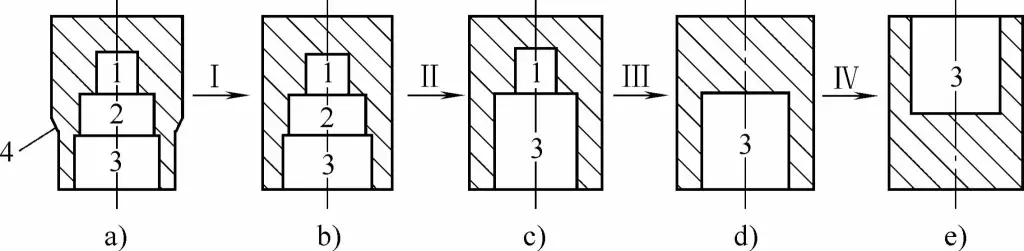
1、2、3-穴、4-ステップ
小孔 1 も別途考慮する場合、3 回目の簡略化後の形状は、簡略化された直接押出しカップ状片となる(図 3-18d 参照)。あるいは、逆押し出しのカップ状ピースから計算を開始することもできます(図3-18e参照)。
この時点で、最終的な単純化プロセスが完了します。このようにして、具体的な解析と単純化を行った後、内部と外部の段差のような形状を持つ複雑な部品を、典型的な逆押し出しカップ形状の部品として扱い、必要な押し出し圧力を計算することができます。
計算では、最終的に簡略化された形状から遡る必要があります。計算の過程では、各形状が押出し力に与える影響を考慮し、必要な押出し力を徐々に決定していく必要があります。逆押し出しカップ形状品(図3-18e参照)の押し出し力をPとし、その値は既存の計算式やチャートから求めることができますが、ここでは詳しく説明しません。
カップ状ピースを直接押出法で加工した場合(図3-18d参照)、図3-19に示すように、押出力は15%~20%高くなる。したがって、この時点での押出し力は1.2Pとなる。一般に、段付き穴があると、図3-20に見られるように、押出力は約20%増加する。したがって、図3-18cに示す形状の押出力は1.44P(1.2P×1.2)となる。
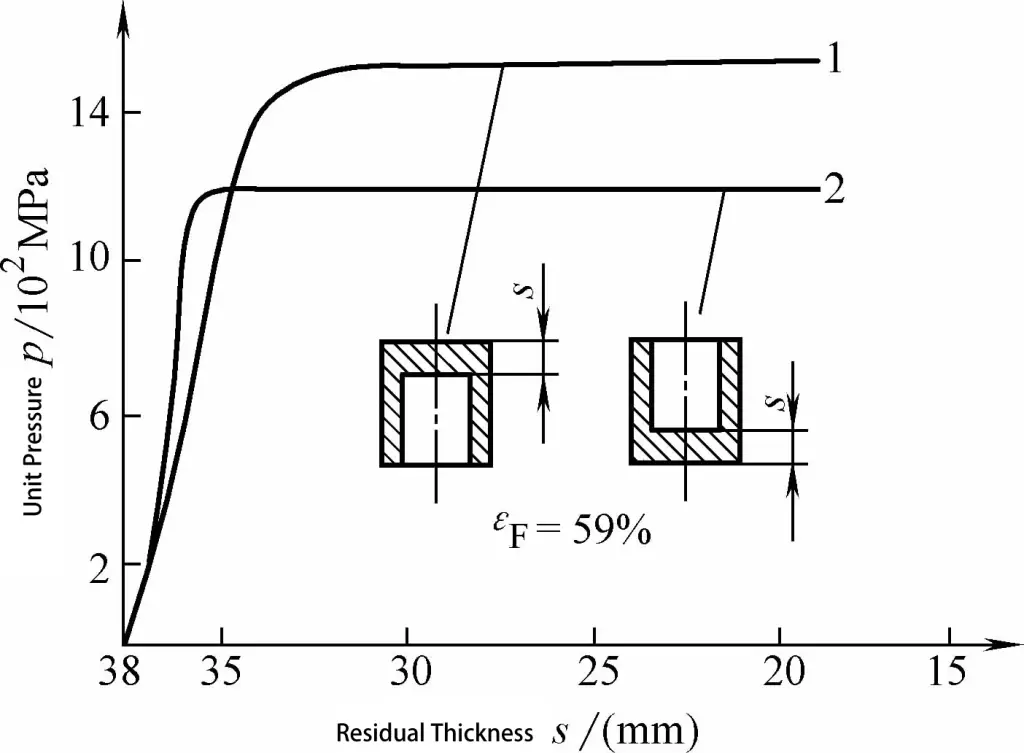
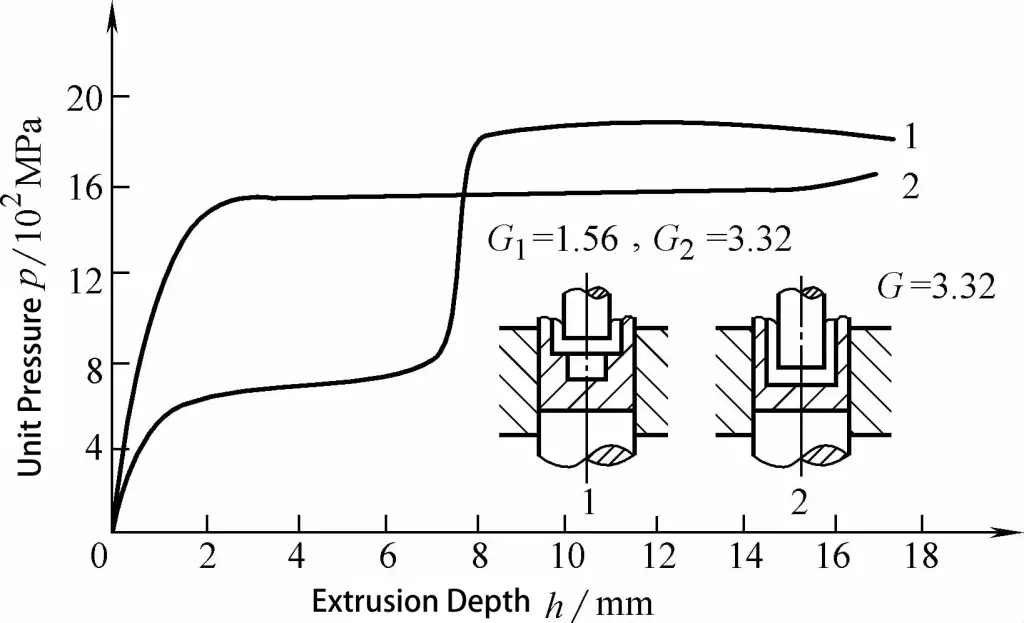
1.段付き穴による間接押し出し
2.ストレートホールによる間接押し出し
段付き穴(穴2と穴3)の大きさはわずかに異なるため、その影響は無視できる。そのため、図3-18bに示す形状の押し出し力は1.44Pのままです。外部段差4(図3-18a参照)の影響は、押出し力の10%増加として考慮されるため、図3-18aに示す形状の押出し力は1.58P(1.44P×1.1)となります。
この部品のブランクサイズを34.94mm×32mm、変形度を40%とすると(図3-18e)、一般的なチャートから得られる押出し力は約800kNとなります。従って、図3-17に示す直接押出し段付き部品の必要押出し力は1264kN(800kN×1.58)となります。
したがって、複雑な形状の部品の押し出し力を計算する式は次のようになる:
P = P1C1C2 (3-10)
どこだ?
- P1 は単純な棒状またはカップ状のピースの押し出し力(N)である;
- C1 は形状の複雑さ係数である;
- C2 は変形法のインパクト・ファクターである。
複雑さ係数は、主に段差形状が押出し力に与える影響を考慮し、押出しピース形状の複雑さによって決定される。これは、関連する設計材料と実験曲線に基づいておおよそ選択することができる。複雑さ係数C1の正確な選択は、設計者の経験と密接に関係しています。
変形法影響係数は、主に直接押出し、逆押出し、および2つの組み合わせの変形力の差を考慮します。通常、20%の増加、すなわちC2≈1.2程度になるように選択されます。
したがって、複雑な形状の部品の押出し力を計算するための図解分析プロセスは次のとおりである:
1) 複雑な形状の押出成形品を徐々に単純化し、単純な棒状またはカップ状の成形品にする。
2)各ボディの違いを分析し、独立した要因として考える。
3) 図形の分解と簡略化プロセスを総合的に分析し、実際の押出ピースの冷間押出力を計算する技術モデルとして使用する。
グラフ解析を使って押し出し力を求める方法は、シンプルで実用的、かつ効果的な工学的計算方法である。この方法の推定精度は、要求を満たすのに十分である。
複合押出しの押出し力の計算方法は、図3-21、図3-22に見られるように、複合押出しに必要な押出し力は、変形の程度が小さい一方向押出しに必要な押出し力の値と同じか、やや小さい値となります。つまり、複合押出しの圧力を計算する際には、変形の程度が小さい方向の押出し力の値を解けばよいことになります。
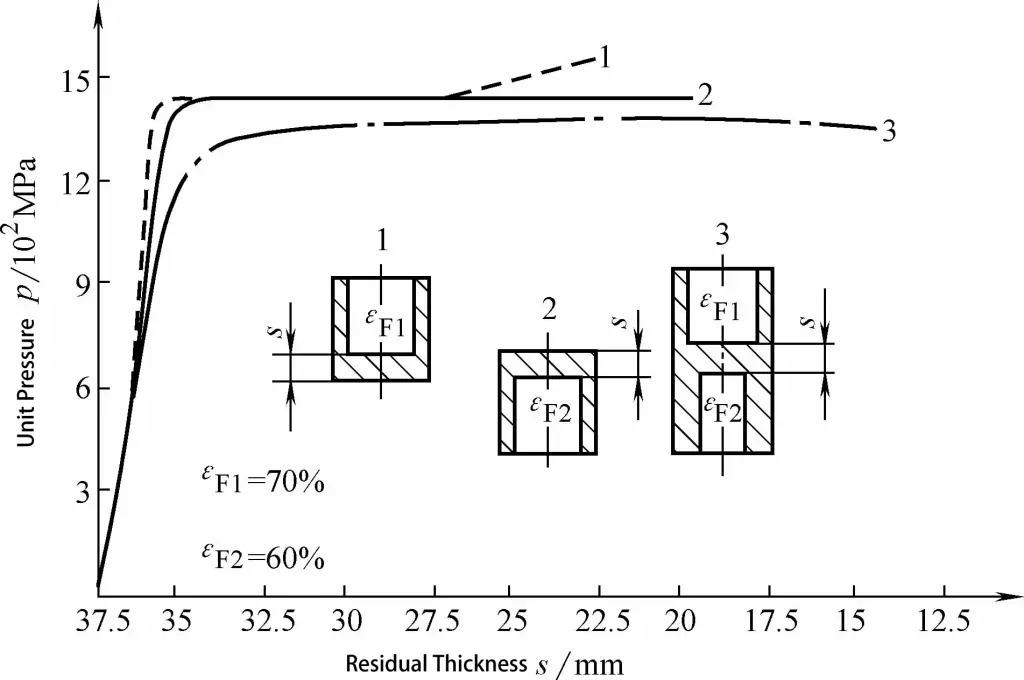
1.間接押出
2.直接押出
3.複合材押出成形
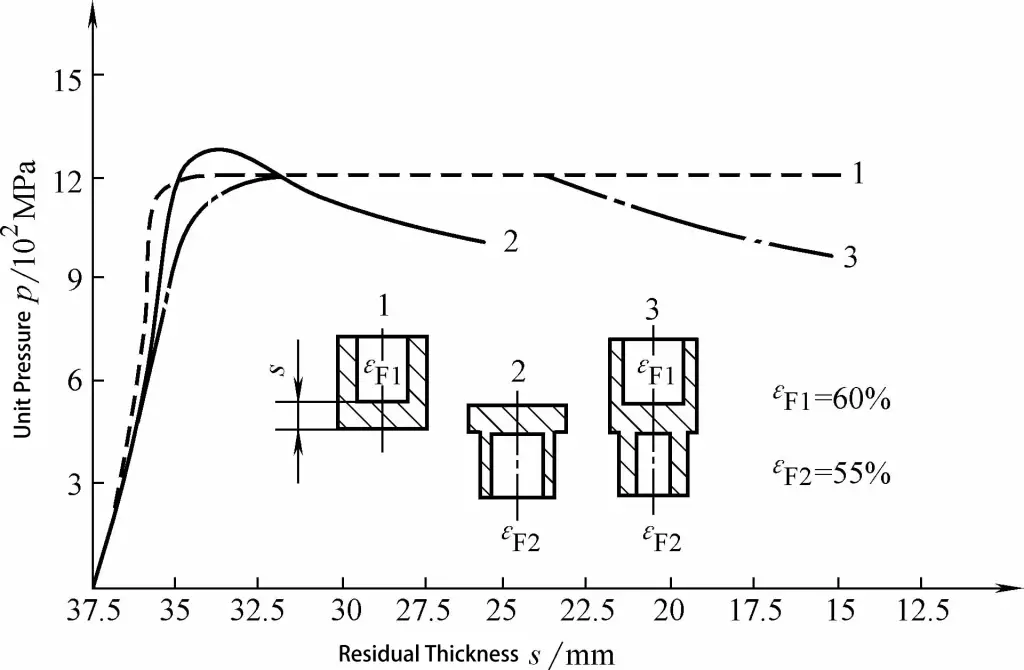
1.間接押出
2.直接押出
3.複合材押出成形
複合押出が特定の方向のサイズを制限しない場合、すなわち、ダイスの両端が開いている状態で金属が両方向に自由に流れる場合、圧力は次のように定義される:
Pコンプ=Pダイレクト (Pダイレクト<P間接的) (3-11)
Pコンプ=P間接的(P間接的<Pダイレクト (3-12)
どこでだ:
- Pダイレクト は、同じビレットサイズと変形度(N)の一方向間接押出しに必要な圧力である。
- P間接的 は、同じビレットサイズと変形度(N)の一方向直接押出しに必要な圧力である。
複合押出が特定の方向のサイズを制限する場合、すなわち、押出工程が終了しようとしているときに、一端で閉鎖押出が必要な場合、圧力は次のように定義される:
- Pコンプ=Pダイレクト 間接押し出し方向にサイズが制限されている場合 (3-13)
- Pコンプ=P間接的 直接押し出し方向にサイズが制限されている場合 (3-14)