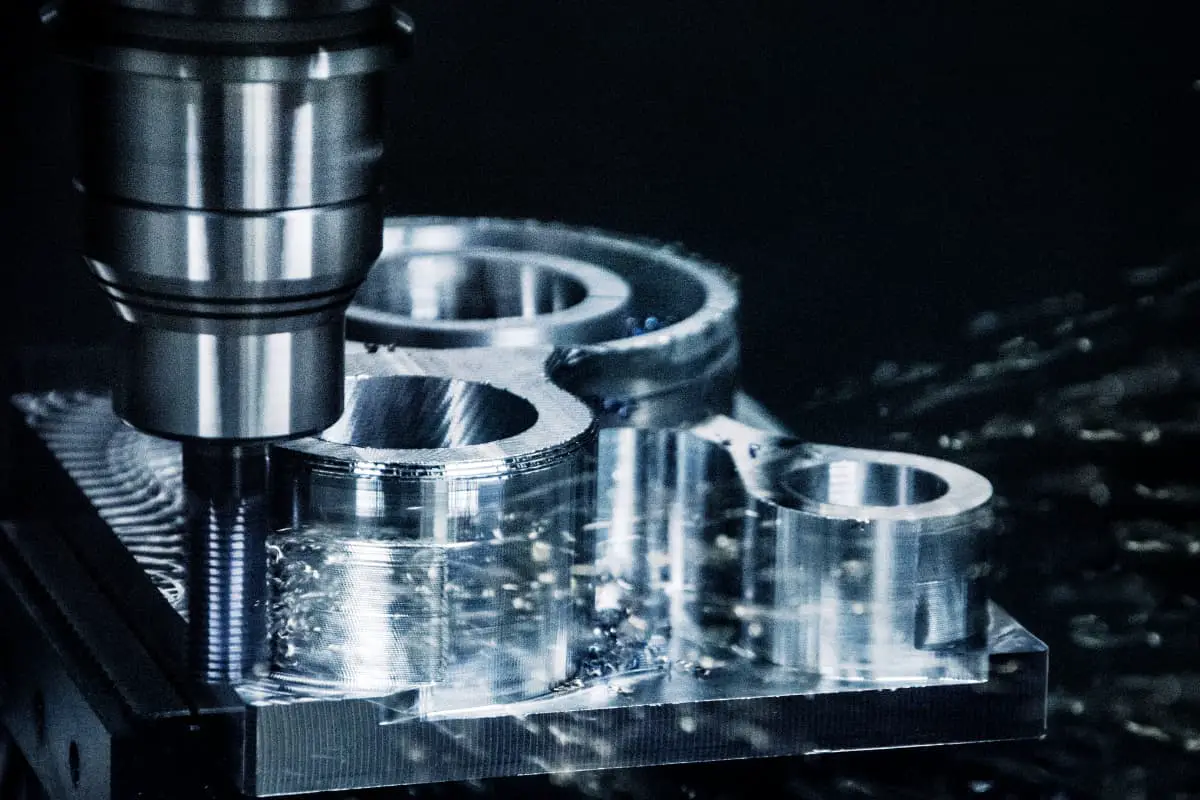
分析によると、冷間押出成形用ダイスの使用条件は非常に厳しく、耐用年数の短さにつながっていることは明らかです。これは特に、鉄鋼材料の冷間押出成形に使用されるダイスに当てはまります。したがって、冷間押出技術の発展を促進するためには、冷間押出ダイスの寿命に関する詳細な研究が重要な課題である。
冷間押出ダイスの寿命を延ばすには、主に2つの側面がある:
単位押出力の低減
a) 適切な変形方法の選択
異なる押し出し方法で成形できる部品は、下部ユニットを使用する方法で成形する。 押し出し力 を選択すべきである。例えば、単純な直接押出しや間接押出しを複合押出しに変換するためにプロセスシャフトを使用することは、単位押出し力を低減し、ダイスの寿命を延ばすための効果的な対策である。
押出し成形では、摩擦抵抗の方向は常に金属の流れ方向と反対である。そのため、図9-15に示すような押し出し方法を用いると、単位押し出し力を小さくすることができます。
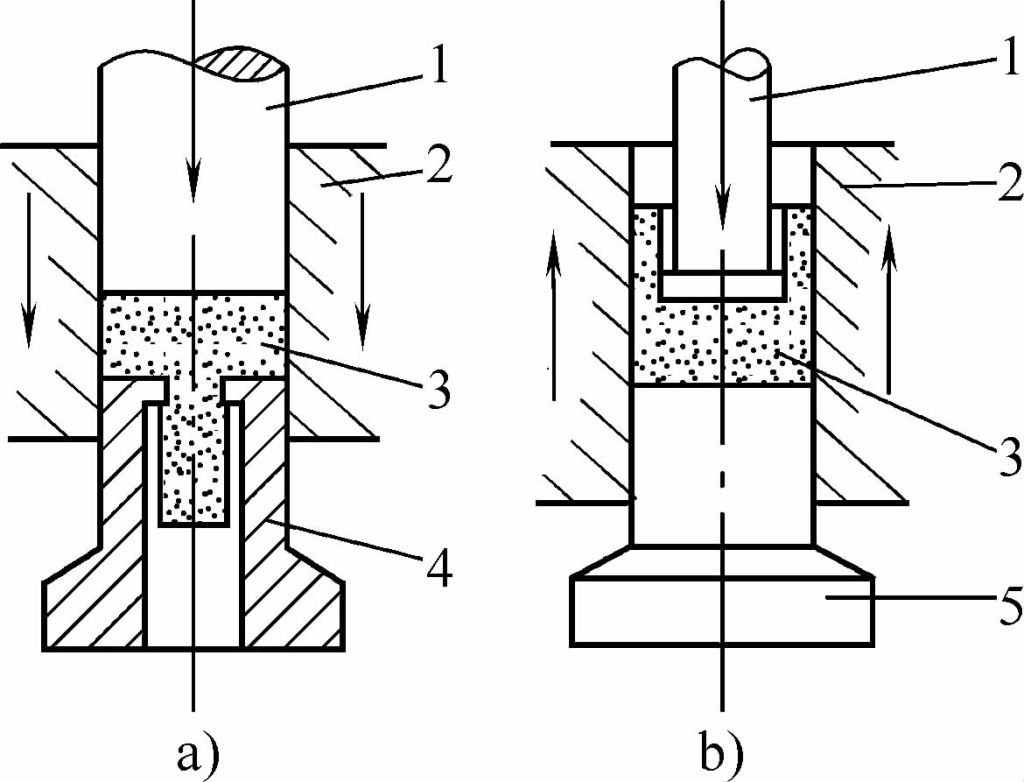
a) 直接押し出し、b) 間接押し出し。
コンポーネントの番号は以下の通り:
1 - パンチ
2 - 押出シリンダー
3 - 押出成形品
4 - 死ぬ
5 - エジェクターロッド
b) 適切な変形度合いの選択
実際の生産現場では、生産性を向上させ、変形操作の回数を減らすために、変形度を大きくする方法がしばしば採用されるが、これは不適切である。これは必然的に単位押出力を増加させ、ダイの早期破損につながる。したがって、工程設計の際には、許容される変形度を厳密に管理する必要がある。
c) 最適な金型形状の使用
直接押出しダイス、間接押出しダイスを問わず、単位押出し力を最小にする最適な形状が必要である。従って、実際の生産では、メタルフローの数値シミュレーションを行い、単位押出力を小さくし、ダイス寿命を延ばす最適なダイス形状を見つける必要がある。
d) 正しいブランク形状の選択
入手可能なデータによると、合理的なブランク形状を使用することで、単位押出力を低減できる。したがって、冷間押出成形に使用されるブランクは、切断された原材料から直接取り出されるのではなく、プリフォーム加工によって加工される。
e) ブランクの厳格な前処理
冷間押出し前のブランクに適度なアニールと表面潤滑処理を施すことで、単位押出し力を大幅に低減することができる。例えば 鋼材の冷間押出押出前にリン酸塩処理を行うかどうかで、押出力は約半分になる。
カビの耐性を高める
(1) 金型素材の品質向上と新素材の開発
既存の金型材料の品質を向上させ、新しい金型材料を開発することは、金型の寿命を延ばすための基本的な方法である。
1) 金型材料の品質を向上させる第一の方法は、冶金工場に冶金品質の向上を要求することである。これは鋼の化学成分だけでなく、金型鋼の純度と均一性を保証する必要がある。メーカーにとっては、原材料の検査を強化し、金型材料の品質を向上させるために、いくつかの効果的な工程措置を適時に採用することが不可欠である。
2) 近年、新しい金型材料の開発が国内外で大きく進展している。新高速度鋼、鋼結合硬質合金、母材鋼、セラミックス材料など、数多くの革新的な金型材料が開発され、金型強度の向上や金型寿命の延長に有利な条件が整ってきている。
しかし、これらの新素材の特性を十分に理解し、特定の使用条件に基づいて正しく選択することが極めて重要である。
(2) 金型材料の正しい選択
冷間押出成形用金型の使用条件に基づいて適切な金型材料を正しく選択することは、金型の寿命を延ばし、コストを削減するための重要な方策である。そのため、金型材料の選定にあたっては、次の2点を考慮する必要がある。
1) 金型材料の選択は、金型の使用条件に基づいて行う。冷間押出成形金型の実際の使用条件はさまざまであることが多く、破損のモードも完全に同じではありません。金型が主に摩耗によって破損する場合は、高強度の金型材料を選択する必要はなく、代わりに耐摩耗性の高い金型材料を選択する必要があります。
金型に大きな偏心力がかかり、主に破壊によって破損する場合(パンチ金型など)には、靭性の高い金型材料を選択する必要があります。経験上、選択した金型材料が使用条件を満たせない面があると、金型の寿命が短くなり、早期故障を引き起こす可能性がある。
2)金型材料の選択は、経済的利益も十分に考慮しなければならない。よく知られているように、金型材料の価格は一般的にかなり高く、特に一部の先進的な金型材料は高い。したがって、金型材料を選択する場合、使用条件を満たしながら、できるだけ手頃な金型材料を選択する必要があり、先進的な金型材料の恣意的な誤用は絶対に避けなければならない。
(3) 合理的な金型構造の設計
合理的な金型構造は、金型の耐荷重性を高め、寿命を延ばすための重要な対策である。まとめると、次のような点に注意する必要がある。
1) 金型が十分な強度、剛性、信頼性、良好なガイド性能を持つことを確認する。
2) 応力集中の大きい金型構造はできるだけ避ける。例えば、トランジションパーツはフィレット半径を十分に大きく設計し、割れやすい金型キャビティパーツは分割構造を採用する等である。
3) 使用する金型材料の種類に応じて、異なる最適化設計方法を選択すべきである。例えば、金型に硬質合金または鋼結合硬質合金を使用する場合、最適化設計は金型内壁の引張応力ゼロを目標とすべきである。
金型に工具鋼を使用する場合、最適化設計の目標関数として、金型とプレストレスリング材の両方が同時に降伏する必要があります。こうすることで、金型材のポテンシャルを十分に活かすことができる。
4) 実績のある新しい金型構造を採用する。例えば、鋼帯巻きダイスまたはワイヤー巻きダイスを使用すると、金型のサイズと重量を減らしながら、金型に高い強度を確保することができます。階段状複合ダイスを使用すると、同じサイズの平口複合ダイスよりも大きな半径方向内圧に耐えることができます。
(4) 合理的な鍛造プロセスの採用
金型鋼中の炭化物の分布と形態は、その機械的性質に決定的な影響を与える。鍛造変形は、鋼中のブロック状や帯状の炭化物を破壊し、微粒子として均一に分布させ、材料の異方性をなくし、内部品質を向上させる主な方法である。
製鉄所から供給される金型素材は、ある程度の加圧加工が施されているが、使用条件を満たすことができず、再鍛造を受けなければならない。金型用鋼を再鍛造する場合、次の点に注意する必要がある。
1) 金型材料を再鍛造する主な目的は機械的特性を向上させることであり、形状を変更するのはその次であることを十分に理解すること。
2)鍛造用金型材料と鍛造用一般材料の違いに特に注意し、金型材料の鍛造工程仕様を厳守する。
3) 炭化物を完全に分解し、均一に分散させるためには、鍛造比を高くし、多方向押出し法を採用する。
(5) 合理的な熱処理工程の採用
国内外の金型初期不良に関する統計によると、金型初期不良の最大の原因は、無理な熱処理工程によるものである。経験上、金型の熱処理工程は金型材料の機械的特性を向上させる重要な手段の一つである。
金型の高強度、高硬度、耐摩耗性、耐熱硬度を確保するためには、焼入れ・焼戻し熱処理に加えて、表面強化熱処理工程を加える必要がある。これにより、金型加工面の硬度、耐摩耗性、耐疲労性を大幅に向上させることができる。現在、冷間押出用金型鋼には、次のような表面強化熱処理工程が用いられている。
1) 炭窒化
鋼の表面に炭素と窒素を同時に浸透させることを炭窒化という。多元素共浸透化学熱処理の一種に属する。
浸炭と比較して、浸炭窒化にはいくつかの利点がある。
浸潤層表面は浸炭鋼よりも高い硬度と耐摩耗性を有し、一定の熱硬度と耐食性を有する。
オーステナイトに溶解した窒素は、過冷却オーステナイトの安定性を高め、浸透層の焼入れ性を向上させる。
窒素の導入は、オーステナイトが形成される温度を下げ、結晶粒の粗大化を防ぐことができる。
浸炭窒化より変形が小さい。
上記のような一連の利点から、浸炭に代わって金型の表面強化熱処理工程に浸炭窒化が採用される傾向にある。
炭窒化プロセスは、使用する材料の状態によって、固体、液体、気体の炭窒化に分けられる。シアン炭窒化は毒性が強いため、近年は廃止されつつある。一方、気体炭窒化は毒性がなく、作業条件が良く、操作が簡単で、制御も容易である。そのため、気体炭窒化は現在広く使用されている。
2) ガス軟窒化
ガス浸炭窒化の一種で、主にFe-C-N三元系の共晶温度以下で窒素を浸透させる。ガス軟窒化処理後の金型表面は、強度、耐摩耗性、疲労強度が向上する。現在、この表面強化熱処理プロセスは冷間押出成形金型に使用され始めており、良好な結果を得ている。
例えば、ある工場が15個の鋼製計器用シートの冷間押出成形に使用しているパンチ金型は、ガス軟窒化処理なしのCG-2母材鋼の場合、金型寿命は14,500個であったが、軟窒化処理後の平均寿命は27,500個に達し、最高は45,600個に達した。
加熱温度は530~570℃、保持時間は通常1~16時間である。
さらに、イオン窒化、硬質クロムめっき、TiC蒸着、塩浴バナジウム浸透、ホウ素浸透、レアアース表面工学、ナノ表面工学技術も冷間押出金型鋼の表面強化熱処理に応用されている。これらはすべて、金型表面の強度をさまざまな程度まで向上させ、金型の寿命を延ばすことができる。
(6) 加工品質の確保と新しい加工方法の採用
1)機械加工の品質を厳しく保証する。
加工品質が高ければ、金型の寿命を延ばすことができる。従って、指定された技術要件を確実に満たすために、効果的な工程対策を講じる必要がある。経験上、冷間押出ダイスの機械加工でより高い加工品質を達成するためには、以下の点を重視すべきである:
i) パンチ・ダイの最終加工後、すべての移行部分は滑らかで継ぎ目がないこと。加工部分はクランプ部分と同軸でなければならず、その形状は厳密に対称でなければならない。そうでないと、押出成形品の厚みが不均一になるだけでなく、パンチ・ダイ自体も片側応力によって曲がる可能性がある。
ii) パンチ・ダイの高い強度を確保し、応力集中によるクラックの発生を避けるため、パンチ・ダイの両端にセンター・ホールを残してはならない。したがって、パンチ・ダイを加工する際には、上面にセンター・ホールを開けるための "バンプ "を確保しなければならない。
iii) パンチ金型の表面粗さは、一般に、押出成形品の原材料の種類に基づく一定の要件に従うべきである。鋼の逆押し出しパンチダイスの場合、表面粗さRaは0.2μm未満であるべきであり、非鉄の場合、表面粗さRaは0.2μm未満であるべきである。 金属 純アルミニウムと同様、表面粗さRaは0.8μmで十分である。
しかし、作業バンド部については、押出される材料が鋼鉄であるか非鉄金属であるかにかかわらず、表面粗さRaを0.2μm未満に維持する必要がある。
iv)前方または後方押出ダイスキャビティの表面粗さは低いほどよく、一般的にはRa<0.2μmであるべきである。研磨されたダイスキャビティは、単位押出力を減少させることができ、ダイスの寿命を大幅に延ばすことができる。
v) 金型の加工部分の研削または研磨は、最終熱処理後に行う。研削前に残す加工代は0.1mm以下とし、表面粗さRaは1.6μm以下とする。研削後の残留応力を除去するには、研削終了後に応力除去焼鈍処理を行うのがよい。
2)新しい加工方法の採用
冷間押出しダイスの加工には、一般的な機械的加工法の他に、放電加工、電解加工、ダイスキャビティの冷間押出しなどの方法や、超精密機械加工、高速ミーリングなどの新しい加工法もある。ここでは、ダイスキャビティの冷間押出し加工法について簡単に紹介する。
ダイキャビティの冷間押出し加工の本質は、金属の塑性加工原理に基づく冷間押出し加工を用いてダイキャビティを直接加工することである。通常、まず工具鋼からダイキャビティの形状に合わせて高硬度のパンチ金型を加工します。
その後、キャビティ押出機(または大トネージ押出機)の作用により、押出成形される。 油圧プレス)、パンチ金型をブランクに押し込むことにより、パンチ金型加工部の形状、外周、サイズに合致した凹凸反転した金型キャビティが形成される。
ダイ・キャビティの冷間押出しには多くの方法があるが、その中で最も一般的なのは、図9-16に示すようなダイ・フレーム内でのキャビティ押出しである。作業工程は次のとおりである。焼鈍軟化したブランクをあらかじめダイ・フレーム内に配置し、油圧プレスの作用でパンチ・ダイをブランクに押し込む。
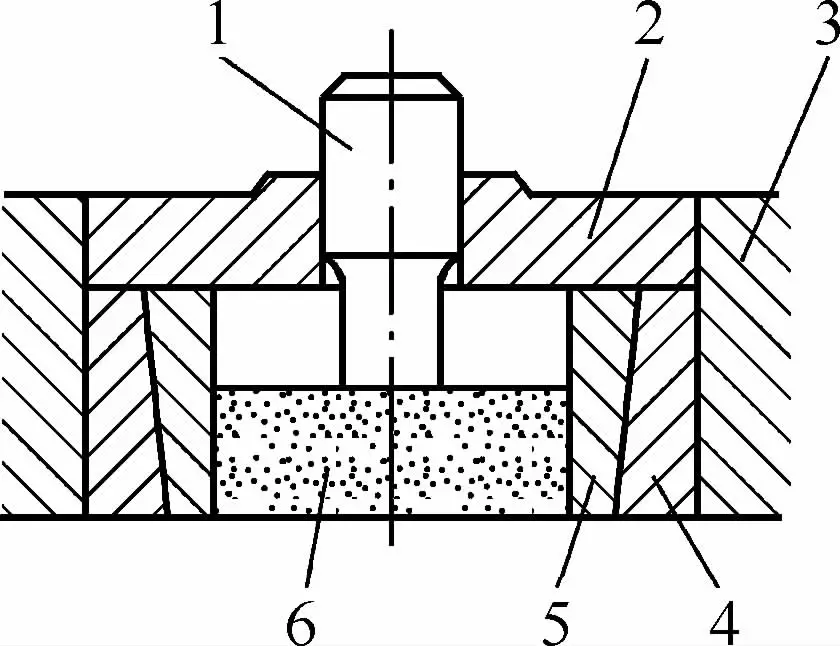
1.パンチ
2.ガイドプレート
3.アウターリング
4.インナーリング
5.コニカルフィットブロック
6.ブランク
この時、ブランクメタルは上方にしか流れず、ブランクとパンチダイの密着が確保される。その結果、ダイキャビティの精度はIT6-IT7に達することができ、幾何学的形状は正しく、表面粗さRaは0.1~0.2μmである。
ダイキャビティの冷間押出し用のパンチダイは、成形の成否に関わる重要な部品である。このパンチ・ダイの製造には注意を払わなければならない。一般的には、次のような事項を考慮する必要がある:
i) 応力集中を軽減するため、パンチ・ダイの移行部は急激な変化を避け、最小曲率半径0.2mmとする。
ii) パンチ金型の高強度・高硬度を確保するために、パンチ金型の原材料として超高強度鋼を選択し、厳格な鍛造変形・熱処理工程を実施する。
iii) 熱処理後、パンチ・ダイの加工部分を再度研削し、表面粗さRa≦0.1μmとする。
iv) パンチ・ダイのガイド精度を確保するため、パンチ・ダイ・ガイド部の長さは、一般にダイ・キャビティの最大半径寸法の1.2倍を下回ってはならない。
冷間押出しによるダイスキャビティの製造率は、切削加工よりもはるかに高いことに留意すべきである。さらに重要なことは、冷間押出しによってダイスキャビティが形成された後、ダイスの内部構造が密になり、その強度と耐摩耗性が高くなるため、ダイスの耐用年数が延びることである。
しかし、押し出しで成形されたダイス素材は強度が高く、塑性加工性に劣るため、この加工法は単純な形状や浅いダイスキャビティ加工にしか用いられない。
(7) 金型の合理的な使用とメンテナンス
冷間押出成形の特性を理解し、ダイスの合理的な使用と入念なメンテナンスを行うことも、ダイスの寿命を延ばすための重要な対策である。
冬季の低温時には、使用前にダイスを予熱し、割れを防止するのがよい。冷間押出しの生産中、熱の影響によりダイスの温度上昇が速いので、ダイスを定期的に冷却する必要があります。
大きな力がかかる金型では、数千回押し出した後、160~180℃で2時間の応力除去アニール処理を行う。
繰り返し使用される外側と中間のプレストレス・リングは、複数回押し出した後、180℃で2時間の応力除去焼鈍処理を行う必要がある。そうしないと、中間のプレストレス・リングと外側のプレストレス・リングに突然亀裂が入り、金型に損傷を与えるだけでなく、人身事故を引き起こす可能性がある。
金型の耐用年数を延ばすためには、完全なメンテナンス・ケア・システムを確立しなければならない。金型の修理、調整、保管作業だけでなく、プレスの調整を迅速に行うために、指定された担当者を配置する必要があります。金型の保管や輸送の際には、防錆対策を講じるとともに、上下のダイベースの間にリミットブロックを設置し、損傷を防止する。