
1. 板金加工入門
1.1 定義
板金加工についての完全な定義はまだない。海外の専門誌の定義によると、金属板(通常6mm以下)の剪断、打ち抜き・切断・複合、折り曲げ、溶接、リベット、組立、成形(自動車ボディなど)などの総合的な冷間加工工程と定義できる。同一部品の板厚が一定であることが大きな特徴で、鋼板、アルミ板、銅板などの金属板を加工する。
1.2 板金加工のプロセスフロー:
どのような板金部品であっても、一定の加工工程があり、それは工程フローと呼ばれる。構造が異なる板金部品では、工程の流れも異なることがある。当社の状況に照らし合わせると、一般的な工程は次のようになる:
顧客からの注文 → 図面の準備 → 図面作成 展開 (数値制御プログラミング)→切断(数値パンチング)→一般的なパンチング→曲げ→プレスリベット→溶接。
関連記事 板金加工用トップ機器:ガイド
2. 板金製図の基礎知識
2.1 機械製図入門
板金加工のための技術製図は、機械製図の範疇に属する。機械製図は、機械の構造形状、サイズ、動作原理、技術的要件を正確に表現するためにパターンを使用する学問分野です。
パターンは図形、記号、文字、数字などで構成される。設計意図、製造要件、経験の交換を表現する技術文書であり、一般にエンジニアリング業界の言語と呼ばれる。
機械製図規格に規定されている項目には、図面形式・書式、縮尺、字体、線などがある。図面形式と書式は、標準図面の書式とそれに対応する図面の枠の大きさを規定する。縮尺とは、機械部品の実際の大きさに対する図案の寸法の長さの比率をいう。
1:1の縮尺で描く以外は、規格で定められた縮小率、拡大率しか認められていない。中国では、漢字は長体模写宋体、文字・数字は所定の構成で書くことが定められている。
太い実線は可視輪郭線、点線は不可視輪郭線、細い点破線は軸線や対称中心線、細い実線は寸法線や断面線など、8種類の線が指定されている。
機械図面には主に部品図と組立図がある。部品図には部品の形状、寸法、製造、検査などの技術的要求が表現され、組立図には機械に属する部品と部品の組立関係や動作原理が表現される。部品の構造や形状を図式化したもので、一般的には正面図、断面図、断面図などが用いられる。
ビューとは、正射投影法に従って投影面に部品を投影して得られる図形である。投影方向と投影面の位置によって、メインビュー、トップビュー、レフトビューなどに分けられる。ビューは主に機械部品の外形形状を表現するために使用される。図では見えない輪郭線は点線で表す。
投影平面に部品を投影する場合、観察者、部品、投影平面の間には2つの相対位置がある。部品が投影平面と観察者の間に位置するとき、それは第一角度投影法と呼ばれる。投影平面が部品と観察者の間にある場合は、第3角度投影法と呼ばれる。どちらの投影法も機械部品の形状を同じように表現することができる。中国の国家規格では、第一角投影法の使用が規定されている。
2.2 正射投影入門
正射投影は、物体の輪郭を平面に投影することで、物体の形状、大きさ、形を正確に表現する描画方法です。
オブジェクトには6つのビューがある。正面から投影したときにオブジェクトの正面の形状を反映するフロントビュー、上から投影したときにオブジェクトの上面の形状を反映するトップビュー、左側から投影したときにオブジェクトの左側面の形状を反映するレフトビュー、そして一般的には使用されないその他の3つのビューである。
正面、上面、左側面という3つの主要なビューを合わせて、正射投影または多視点投影と呼ぶ。
それぞれのビューは、対象物の一方向の形状しか示すことができず、対象物の構造的な形状を完全に反映することはできない。三面図とは、同じ物体を3方向から投影した図面である。さらに、断面図や半断面図などの補助的なビューを使用して、対象物の構造を完全に表現します。
正射投影の投影ルールは以下の通り:
- 正面図と上面図- 長さ寸法線が揃っている。
- 正面図と左側面図-高さ寸法線が揃っている。
- 左から見た図と上から見た図-幅寸法線が揃っている。
2.3 描画認識方法
三面図を見るとき、その空間形状をどのように理解できるだろうか。これは二次元から三次元空間へのプロセスである。 板金 図面は比較的単純なものであり、ここではその基本的な見方を紹介する。
形状分析では、物体を構成する基本的な形状を分析し、それぞれの基本的な形状の投影を見つけ、それらの空間形状を視覚化し、次に基本的な形状とそれらの相対的な位置を組み合わせて、全体的な空間形状を視覚化する。
それぞれのビューは物体の一方向の形状しか示せないため、物体の構造を完全に理解するには複数のビューを組み合わせる必要がある。より複雑な物体の場合、3つのビューだけではその形状を明確に表現できないことがある。
右側面図、上面背面図、背面図、あるいは断面図、断面図、局所拡大図などの補助的な投影図が追加で必要になる場合もある。
2.4 サードアングルプロジェクション入門
三面図の描き方には、ISO国際規格に準拠した第三角投影と第一角投影がある。
現在、中国やドイツなどでは第一角投影法、アメリカや日本などでは第三角投影法が採用されている。実際の生産現場でも、第三角投影法による図面をよく見かける。
この2つの投影法の違いは、次のようなものだ:
第一角投影法は、観察者と投影面の間に物体を置く。
第3角度の投影法は、観察者と対象物の間に投影面を置く。したがって、2つの投影法によって得られるビューは、対象物の前後関係を表現する上で正反対となる:
第1角度の投影法の場合、左側のビューは右側に、右側のビューは左側に、上側のビューは下側に配置される。
サードアングル投影法の場合:左側のビューは左側に配置され、右側のビューは右側に配置され、トップビューは上側に配置される。
この2つの投影法を区別するために、国際規格では図のようにそれぞれ異なる記号を定めている。

3.板金展開計算
3.1 展開計算の原理:
その間に 板金の曲げ加工外層は引張応力を受け、内層は圧縮応力を受け、その間に引張でも圧縮でもない中立層がある。
中立層の長さは曲げ加工中も変化しないため、曲げ加工の基準となる。 展開の計算 曲げられた部分の長さ。中立層の位置は、変形の程度に依存する。
そのとき 曲げ半径 曲げ半径が大きく、曲げ角度が小さい場合、変形の程度は小さく、中立層は板厚の中心付近に位置する。曲げ半径が小さくなり、曲げ角度が大きくなると、変形の度合いが大きくなり、中立層の位置は徐々に曲げ中心の内側に移動する。
3.2 計算方法
板金の展開寸法を計算する方法はたくさんあり、各板金工場の計算方法は同じとは限りません。当社では、シンプルで実用的な推算方法で展開寸法を算出しています。
展開の基本式は展開長=外寸+外寸-展開係数(K値)。
曲げタイプ | 模式図 | 計算式 |
直角曲げ | ![]() | 展開寸法=A+B-K |
非直角曲げ | ![]() | 展開寸法=A+B-(q/90°)*K |
アーク・ベンディング(R/T>5) | ![]() | 展開寸法=A+B-0.43T |
ストレートフランジ(Zベンド) | ![]() | 1.H≧5Tの場合、2段階で形成され、2つの直角ベンドに従って計算されるべきである; 2.H<5Tの場合、1ステップで形成する必要があり、L=A+B+K(Kの値は表3.2.4を参照)。 |
アングルドフランジ(Zベンド) | ![]() | 1.H<2Tのとき a. q≦70°のとき、L=A+B+C+0.2 b. q>70°のとき、L=A+B+K (Kの値は表3.2.4を参照。すなわち、直線の辺の差によって拡大される) 2.H≧2Tの場合、2段階で形成し、2つの非直角度ベンドに従って計算する。 |
表3-1 鋼板の展開係数表(単位:mm)
板厚 T | 0.8 | 1.0 | 1.2 | 1.5 | 2.0 | 2.5 | 3.0 |
K(コールドプレート) | 1.5 | 1.8 | 2.1 | 2.6 | 3.4 | 4.5 | 5.4 |
K(ステンレス鋼) | 1.4 | 1.9 | 2.3 | 2.87 | 3.75 |
表3-2 アルミ板の展開係数表(単位:mm)
板厚 T | 0.5 | 1.0 | 1.2 | 1.5 | 2.0 | 2.5 | 3.0 |
K | 0.8 | 1.5 | 1.7 | 2.3 | 3.2 | 4.0 | 5.0 |
表3-3 銅板の展開係数表(単位:mm)
板厚 T | 1.0 | 1.5 | 2.0 | 2.5 | 3.0 | 4.0 | 5.0 | 6.0 | 8.0 | 10.0 |
K | 1.8 | 2.6 | 3.5 | 4.4 | 4.8 | 6.5 | 8.0 | 9.5 | 12.5 | 16 |
表3-4 ストレートエッジ差の展開係数表(単位:mm)
H T | 0.5 | 0.8 | 1.0 | 1.2 | 1.5 | 1.6 | 2.0 | 3.2 |
0.5 | 0.1 | |||||||
0.8 | 0.2 | 0.1 | 0.1 | |||||
1.0 | 0.5 | 0.2 | 0.2 | 0.2 | 0.2 | 0.2 | ||
1.5 | 1.0 | 0.7 | 0.5 | 0.3 | 0.3 | 0.3 | 0.3 | 0.2 |
2.0 | 1.5 | 1.2 | 1.0 | 0.8 | 0.5 | 0.4 | 0.4 | 0.3 |
2.5 | 2.0 | 1.7 | 1.5 | 1.3 | 1.0 | 0.9 | 0.5 | 0.4 |
3.0 | 2.5 | 2.2 | 2.0 | 1.8 | 1.5 | 1.4 | 1.0 | 0.5 |
3.5 | 2.7 | 2.5 | 2.3 | 2.0 | 1.9 | 1.5 | 0.6 | |
4.0 | 3.2 | 3.0 | 2.8 | 2.5 | 2.4 | 2.0 | 0.8 | |
4.5 | 3.7 | 3.5 | 3.3 | 3.0 | 2.9 | 2.5 | 1.3 | |
5.0 | 4.0 | 3.8 | 3.5 | 3.4 | 3.0 | 1.8 |
3.3 計算によく使われる数学的知識の展開
3.3.1 寸法単位
中国の長さの基本単位はメートル(m)であり、換算関係は次の通りである:
- 1メートル(m)=100センチメートル(cm)
- 1センチメートル(cm)=10ミリメートル(mm)
- 1ミリメートル(mm)=1000マイクロメートル(μm)
イギリスやアメリカなどでは、英語の長さの単位が使われており、以下のような流れになっている:
- 1ヤード=3フィート
- 1フィート(1フィート)=12インチ(12インチ)
インチとミリメートルの換算関係:1インチ(1″) = 25.4mm
3.3.2 よく使われる計算式
コサインの法則 | ![]() | ![]() |
アーチサイズ計算 | ![]() | ![]() |
直角三角関数の計算公式 | sinA=a/c cosA=b/c tanA=a/b cotA=b/a | ![]() |
4.一般的に使用される 板金材料
4.1 よく使われるプレートの紹介
4.1.1 冷間圧延普通薄鋼板は、コールドプレートとも呼ばれ、普通炭素構造用鋼冷間圧延鋼板の略称である。普通炭素構造用鋼の熱間圧延鋼板をさらに冷間圧延して厚さを4mm未満にしたもの。
常温で圧延され、スケールが発生しないため、表面品質が良く、寸法精度が高く、焼鈍処理により機械的特性、加工特性も良好である。板金加工で最もよく使われる金属材料である。
一般的な等級国家標準GB(Q195、Q215、Q235、Q275)、日本標準JIS(SPCC、SPCD、SPCE)
4.1.2 連続電気亜鉛メッキ薄鋼板、通称電解鋼板とは、電気メッキ亜鉛製造ラインの電界の作用の下で、亜鉛塩の深層水溶液から亜鉛を予め準備した冷鋼板表面に析出させることを指し、その結果、鋼板表面に亜鉛メッキ層が形成され、良好な耐食性が得られる。
等級国家標準GB(DX1、DX2、DX3、DX4)、日本標準JIS(SECC、SECD、SECE)
4.1.3 連続溶融亜鉛メッキ薄鋼板は、一般に亜鉛メッキ鋼板または 白鉄板と呼ばれ、ブロック状またはリーフ状の結晶模様のある美 しい表面を持ち、塗膜は堅固で、耐大気腐食性に優れている。
同時に、鋼板は良好な溶接性能と冷間成形性能を持っています。電気亜鉛メッキ鋼板の表面と比較すると、そのコーティングは厚く、主に強い耐食性を必要とする板金部品に使用されます。
グレード国家標準 GB (Zn100-PT、Zn200-SC、Zn275-JY)、日本標準 JIS (SGCC、SGCD1、SGCD2、SGCD3)
4.1.4 ステンレス鋼板は、空気、蒸気、水などの弱腐食媒体と酸、アルカリ、塩などの化学腐食媒体に耐性を持つ鋼の一種である。ステンレス耐酸鋼とも呼ばれる。実際の使用では、弱い腐食媒体に耐える鋼をステンレス鋼、化学媒体に耐える鋼を耐酸鋼と呼ぶことが多い。
ステンレス鋼は通常、マトリックス構造によって分類される:
1.フェライト系ステンレス鋼。
12%~30%のクロムを含有。クロム含有量の増加とともに耐食性、延性、溶接性が向上し、塩化物応力腐食に対する耐性は他のステンレス鋼よりも優れている。
2.オーステナイト系ステンレス鋼。
クロム含有量は18%以上、ニッケル含有量は約8%、モリブデン、チタン、窒素、その他の元素は少量である。優れた総合特性を持ち、様々な媒体による腐食に耐えることができる。
3.オーステナイト・フェライト二相鋼。
オーステナイト系ステンレス鋼とフェライト系ステンレス鋼の長所を併せ持ち、超塑性を有する。
マルテンサイト系ステンレス鋼。強度は高いが、塑性と溶接性が悪い。ステンレス鋼板は強度が高いため、溶接時に工具の摩耗が大きくなる。 CNCパンチプレス.一般的に、数値制御による打ち抜き加工には適さない。
鋼種ステンレス鋼には多くの種類がありますが、板金加工で一般的に使用されるのはオーステナイト系ステンレス鋼(1Cr18Ni9Ti)の一種です。日本規格 JIS (SUS)
4.1.5 アルミニウム板 アルミニウムは銀白色の軽量金属で、熱伝導性、電気伝導 性、延性に優れている。純アルミニウムは強度が低く、構造材料としては使用できない。板金加工に一般的に使用されるアルミニウム合金板は、合金元素の含有量によって、1000系、2000系~8000系の8つのシリーズに分けられる。
一般的に使用されているのは、2000シリーズ、3000シリーズ、5000シリーズである。2000系は銅とアルミニウムの合金で、硬度が高いのが特徴で、硬質アルミニウムとも呼ばれ、様々な中強度の部品やコンポーネントに使用できます。3000系はマンガンアルミニウム合金で、防錆性能に優れているため、防錆アルミニウムとも呼ばれています。5000シリーズはマグネシウムとアルミニウムの合金で、密度が低く、引張強度が高く、伸びが大きいのが特徴です。
アルミニウム・マグネシウム合金の重量は、同じ面積の他のシリーズよりも軽い。
一般的な等級3A21(旧品種LF21)、5A02(旧品種LF2)、2A06(旧品種LY6)
4.1.6 黄銅板 黄銅は純銅の通称で、紫色の外観を持ち、電気伝導性、熱伝導性、延性、耐食性に優れている。しかし高価であり、主に導電材料、熱伝導材 料として使用され、一般に電源の大電流を流す部品に使 われる。真鍮は強度が低く、一般に構造部品としては使用できない。
グレードT1、T2、T3
4.1.7 銅合金板、黄銅は銅と亜鉛の合金で、強度が高く、冷間および熱間加工性に優れるが、腐食割れを起こしやすく、比較的安価であるため、広く使用されている。
一般的なグレードH59、H62、H70
4.2 一般的に使用されるプレートの重量の計算
基本的な計算式材料重量 = 長さ (m) * 幅 (m) * 厚さ (mm) * 材料密度
材料名 | 鋼板 | ステンレス鋼板 | アルミプレート | パープル・カッパー・プレート | 真鍮プレート |
密度 | 7.85 | 7.93 | 2.71 | 8.89 | 8.5 |
4.3 一般的なファスナー情報
ファスナーは、2つ以上の部品(またはコンポーネント)を1つの全体に固定するために使用される機械部品の総称です。一般的に使用されるファスナーには、ボルト、ネジ、ナット、ワッシャー、ピンなどがある。
4.3.1 スレッド処理
共通の糸の表現:
並目ねじは、アルファベット "M "と呼び径で表される。例えば、呼び径24mmの並目ねじのコードはM24です。
細目ねじは、M24*1.5のように、アルファベット "M"、呼び径、ピッチで表される。
タッピング前の下穴径の計算式は、下穴径=ねじ山の外径-ピッチである。
これは直接調べることもできる:
表4-1.
スレッド仕様 | M2 | M3 | M4 | M5 | M6 | M8 | M10 | M12 | M14 |
底穴径 | Φ1.6 | Φ2.4 | Φ3.3 | Φ4.2 | Φ5 | Φ6.8 | Φ8.5 | Φ10 | Φ12 |
4.3.2 ねじ用皿穴の構造寸法
表4-2 ネジ用皿穴の寸法
![]() | d1 | M2 | M2.5 | M3 | M4 | M5 |
d2 | Φ2.2 | Φ2.8 | Φ3.5 | Φ4.5 | Φ5.5 | |
D | Φ4.0 | Φ5.0 | Φ6.0 | Φ8.0 | Φ9.5 | |
h | 1.2 | 1.5 | 1.65 | 2.7 | 2.7 | |
最低希望シート厚 | 1.2 | 1.5 | 1.5 | 2.0 | 2.0 | |
α | 90° |
4.3.3 リベット・ナット、ルーズ・プルーフ付きリベット・ナット及びリベット・スクリューの作業原理は、ワークピース上の対応するサイズの穴を予備加工し、パンチ・プレス又はリベット・マシンのような装置を通して圧力を加えることであり、その結果、リベット・ナット及びリベット・スクリューの歯がプレートに圧入され、穴の周囲に塑性変形を引き起こす。変形した材料はガイド溝に押し出され、それによってロック効果が生じる。
表4-3 弊社で一般的に使用しているリベットナット、リベットねじ、溶接ナットの下穴の加工寸法の問合せ表。
仕様 タイプ | M2.5 | M3 | M4 | M5 | M6 | M8 | M10 |
プレス・リベット・ナット・コラム | Φ5.4 | Φ6.1 | Φ7.2 | スルーホールΦ8 | |||
ブラインドホールΦ8.5 | |||||||
プレスリベットネジ | Φ2.5 | Φ3 | Φ4 | Φ5 | Φ6 | Φ8 | |
エキスパンション・リベット・ナット | Φ5 | Φ6 | Φ8 | Φ9 | Φ11 | Φ14 | |
緩み防止機能付きスクリュー | Φ5.8 | Φ6.4 | Φ8 | Φ9.5 | |||
溶接ナット | Φ5 | Φ6 | Φ7 | Φ9 |
5.一般的な測定工具の基礎知識
直径や角度など、機械部品の要素を測定するための器具を測定器という。機械部品には多くの要素があり、その精度に対する要求も多岐にわたります。そのため、要素を測定するための測定工具には多くの種類があります。当社で一般的に使用されている測定工具には、スチールテープ、ノギス、マイクロメーター、万能角度定規などがあります。
一般に、これらの測定器の仕様は、レンジと目盛値で表される。レンジは測定範囲であり、目盛値は測定器の最小目盛の値である。目盛りが小さいほど精密な測定器ということになる。
測定工具が正しく使用されているかどうかは、測定工具自体の精度に影響するだけでなく、ワークサイズの測定精度に直接影響し、さらには品質事故を引き起こし、企業に不必要な損失をもたらします。したがって、測定工具を正しく使用することを重視し、優れた測定技術に努め、正確な測定結果を得て、製品の品質を確保しなければならない。
ここでは、私たちが頻繁に使用する測定ツールを簡単にご紹介します:
5.1 スチールテープ
スチールテープは日常生活や仕事でよく使われ、使い方も比較的簡単です。主にワークの長さ寸法を測るのに使います。精度によってI種とII種に分けられ、目盛りは1mmです。精度は比較的低く、測定可能な長さ範囲は3m、5m、10m以上で、寸法精度の要求が低い大型ワークの長さ寸法測定に適しています。
5.2 キャリパー
ノギスは、シンプルな構造、便利な使用、中程度の精度、および測定サイズの広い範囲の特性を持つ一般的に使用される測定ツールです。用途は広く、ワークの外径、内径、長さ、幅、厚さ、深さ、穴の間隔などを測定することができる。読み取り方法や原理の違いにより、バーニヤキャリパー、ダイヤルキャリパー、デジタルキャリパーなどがあります。当社では、ノギスが一般的に使用されています。ノギスは私たちの仕事で最もよく使われる測定工具なので、ここではノギスの原理と使い方を中心に説明しましょう:
5.2.1 バーニヤキャリパーは、その構造によって片面ノギス、両面ノギス、三面ノギスなどに分けられる。
(1) 片面ノギスは、内側と外側の測定ジョーを持ち、内側と外側の寸法を測定できます(図1-1)。

(2) 両面ノギスは、上顎にナイフ状の外径測定爪、下顎に内径測定爪と外径測定爪があり、内外径寸法を測定できる(図1-2)。

(3)三方ノギスは、内寸測定用のナイフ形状の内爪、外寸測定用の平らな測定面とナイフ形状の測定面を持つ外爪、深さと高さを測定するための定規裏のデプスゲージを持つ(図1-3)。

5.2.2 バーニヤキャリパーの読み取り原理と読み取り方法
ノギスの正しい使い方をマスターするには、正確な読み方と正しい操作方法を学ぶ必要がある。バーニヤキャリパーの読み取り装置は、定規枠とバーニヤで構成されています。定規枠の可動測定ジョーと定規本体の固定測定ジョーが接触すると、定規枠の「0」線(バーニアゼロラインと呼ばれる)と定規本体の「0」線が一致し、測定ジョー間の距離がゼロになります。測定の際には、定規枠を目盛り上のある位置まで移動させる必要があり、図1-4に示すように、可動測定ジョーと固定測定ジョーとの間の距離が測定サイズとなります。
定規本体の30mmを示す目盛りにバーニアゼロラインがぴったり合っている場合、定規本体のバーニアゼロラインが示す値が30mmより少し大きい場合はどうすればよいのでしょうか。この場合、バーニアゼロラインの左側にある定規本体の目盛線(図中矢印で示す)から測定サイズの整数部(30mm)を読み取り、バーニアの力を借りて1mmより小さい小数部(図中●線で示す0.7mm)を読み取ればよい。両者の和が30.7mmであることは、バーニア付き測定器の共通の特徴である。したがって、ノギスの読み方のポイントは、小数部の読み方にあることがわかる。

バーニアの小数点部分の読み取り方法は、まず、バーニア上のどの線が定規本体上の線と一致しているかを識別する。次に、このバーニア上の線の次数とバーニアの読み取り値を掛け合わせ、その結果をバーニアの読み取り値とする。すなわち、バーニアの読み取り値 = バーニアの読み取り値 * バーニア上のアライメントラインのオーダー番号。
ノギスを読む場合、3つのステップに分けることができる:
- まず整数部を読みます:定規本体のバーニア・ゼロ・ラインの最も左にある目盛り線の値を見て、測定されたサイズの整数部を読み取ります。
- 次に小数部を読む:バーニアのゼロ線の右側を見て、バーニア上のどの線が定規本体上の線と一致しているかを数えます。バーニアの読み取り値に、バーニア上のアライメントラインのオーダー番号を乗じることで、測定サイズの小数部を読み取ります。
- 測定サイズを計算する:前の2つのステップで得た整数部と小数部を加算し、その合計がノギスの測定サイズとなる。
5.2.3 ノギスの使い方
ノギスを使用してワークのサイズを測定する場合、以下の点に注意する必要がある:
(1) 測定の前に、ノギスをきれいに拭き、ノギスの2つの測定面と測定エッジが平らで損傷していないことを確認します。2つの測定ジョーがしっかりと取り付けられている場合、明らかな隙間がなく、バーニヤとメインスケールのゼロ線が一致していなければなりません。この作業をノギスのゼロ位置の確認といいます。
(2) 定規枠を動かすときは、ゆるすぎず、きつすぎず、揺れのない滑らかな動きであること。定規枠を固定ネジで固定する際、ノギスの読みが変化しないこと。定規枠を移動させるときは、固定ネジを緩めることを忘れず、また、落下しないように緩めすぎないこと。
(3) 被測定物の外径寸法を測定する場合:ノギスの2つの測定面の接続線は、被測定物の測定面に対して垂直でなければならず、傾いてはならない。測定中、図1-5に示すように、ノギスを軽く振って垂直位置を修正することができる。そうしないと、図1-5のように測定ジョーが間違った位置にある場合、測定結果 "a "は実際のサイズ "b "よりも大きくなってしまいます。まず、ノギスの可動式測定ジョーを開き、測定ジョーがワークピースに自由に挿入できるようにします。
次に固定測定爪にワークを当て、定規枠を動かして可動測定爪に少し圧力をかけてワークに接触させます。ノギスにマイクロメータ装置が付いている場合は、この時点でマイクロメータ装置の固定ネジを締め、調整ナットを回して測定ジョーをワークに接触させ、サイズを読み取ります。ノギスの2つの測定ジョーを測定サイズに近づけるか、あるいはそれよりも小さくなるように調整し、ノギスをワークピースに無理にクランプすることは絶対にしないでください。測定ジョーが変形したり、早期に摩耗したりして、ノギスが要求される精度を失う原因になります。
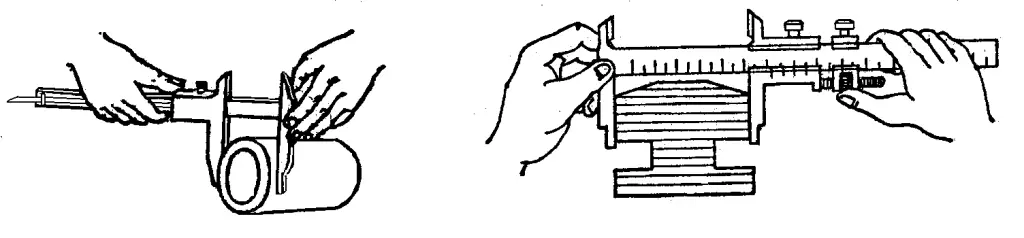

図1-5:外形寸法測定の正しい位置と正しくない位置
溝を測定する場合は、ノギスの測定面を刃先にして測定し、先端の測定刃やナイフ状の測定爪で外形寸法を測定することは避けた方がよい。円形溝の寸法は、1-6に示すように、ナイフ状の測定爪を使用して測定し、平らな測定刃は測定に使用すべきではない。

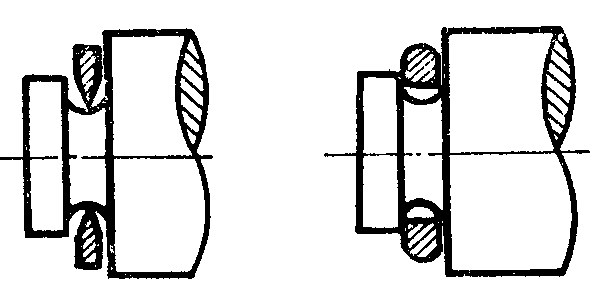
図1-6:溝を測定するための正しい位置と正しくない位置
溝の幅を測定する場合は、ノギスの位置も適切に調整する。ノギスの2つの測定端を結ぶ線は、溝に対して垂直でなければならず、傾いてはならない。そうしないと、図1-7に示すように測定爪の位置が正しくない場合、測定結果が不正確になります(大きすぎたり小さすぎたりする可能性があります)。
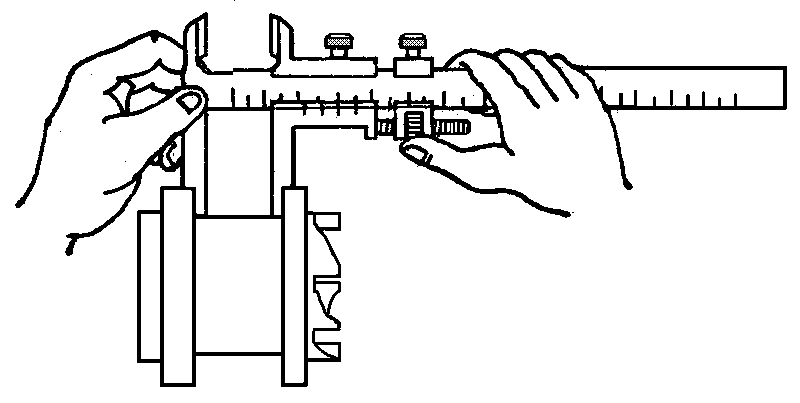


図1-7:溝幅測定の正しい位置と正しくない位置
(4) 被測定物の内径寸法を測定する場合:図1-8に示す。測定爪の間隔は、測定した内径寸法より小さくします。ワークの内孔に入った後、ゆっくりと開き、ワークの内面に軽く触れる。固定ネジでノギスを固定した後、静かにノギスを取り外して測定値を読み取ります。
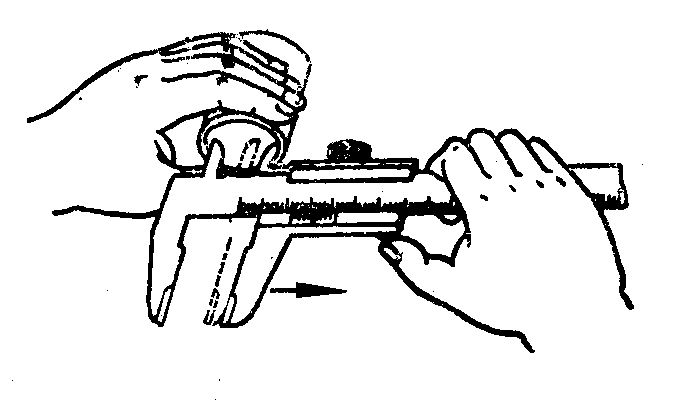
測定爪を取り出す際、力は均一であるべきで、ノギスは傾くことなく穴の中心線方向に沿ってスライドさせ、ねじれや変形、測定爪の不必要な摩耗や破損を避ける必要があります。そうすれば、ねじれ、変形、測定爪の不必要な磨耗、破損を避けることができます。同時に、スケールフレームを移動させ、測定精度に影響を与えます。ノギスの2つの測定端は、穴の直径上にあり、斜めにならないようにしてください。
図1-9は、ナイフ状の測定爪と円筒状の表面測定爪を備えたノギスで内孔を測定する際の正しい位置と正しくない位置を示しています。測定爪の位置が正しくない場合、測定結果は実際の開口部Dよりも小さくなります。

(5) 下部測定爪の外側測定面で内寸法を測定する場合は、測定結果を読み取る際に測定爪の厚さを加えなければならない。つまり、ノギスの読みに測定爪の厚みを加えたものが、測定したワークの内寸法となります。測定範囲が500mm以下のノギスの測定爪の厚さは、一般的に10mmです。ただし、測定爪が摩耗したり、修理した場合は、測定爪の厚みが10mm以下になるので、測定結果を読み取る際には、この補正値も考慮する必要があります。
(6) ワークを測定するためにノギスを使用する場合、過度の圧力は禁物です。使用する圧力は、2つの測定爪がちょうどワークの表面に接触する程度にしてください。測定圧力が高すぎると、測定爪が曲がったり磨耗したりするだけでなく、圧力を受けて測定爪が弾性変形し、不正確な測定結果(外寸が実寸より小さく、内寸が実寸より大きい)になります。
(7) ノギスで測定結果を読み取るときは、視線の傾きによる読み取り誤差を避けるため、ノギスを水平に持ち、明るい光の方向に向け、目盛面に対して視線をできるだけ垂直にする。
(8) 正確な測定結果を得るために、複数の測定を行うことができる。つまり、ワークピースの同じ部分について、異なる方向から測定を行う。長いワークピースの場合は、比較的正確な測定結果を得るために、全長のさまざまな部分で測定を行う必要があります。
5.3.デプスゲージ
図1-10に示すデプスゲージは、ワークの深さ、段差の高さ、溝の深さなどを測定するためのものである。その構造上の特徴は、目盛り枠3の2つの測定爪を連結してバーニア付きの測定ベース1を形成し、ベースの端面と目盛り本体4の端面がその2つの測定面となることである。内孔の深さを測定する場合、ベースの端面を測定孔の端面に密着させ、目盛本体を測定孔の中心線と平行に挿入する。スケール本体の端面とベースの端面との間の距離が、被測定物の深さ寸法となります。
読み取り方法はノギスとまったく同じ。
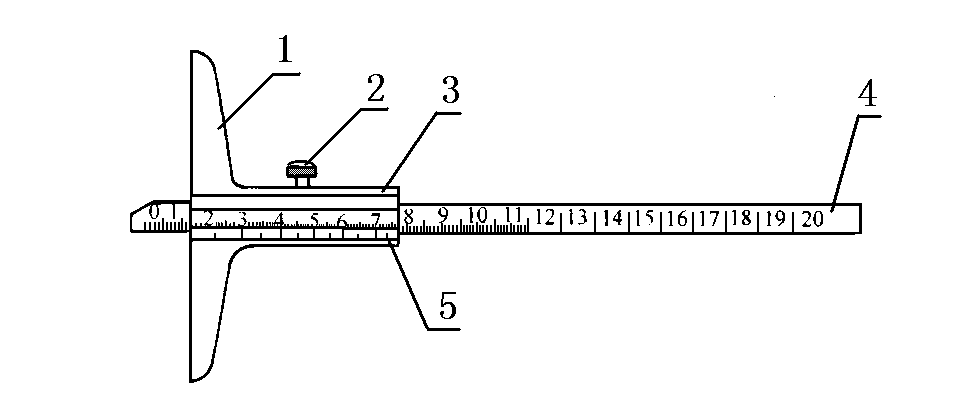
- 1- 測定ベース;
- 2- 固定ネジ;
- 3- スケールフレーム;
- 4- スケールボディ;
- 5- バーニア
5.4.マイクロメーター:
スクリューマイクロメーターとも呼ばれ、スクリューによる微小測定の原理を応用した測定器。測定精度はノギスよりも高く、測定に柔軟性がある。そのため、高い加工精度が要求される場合に使用されることが多い。
読み取り分解能により、100目盛と1000目盛に分けられる。百目盛りの読み取り値は0.01mm、千目盛りの読み取り値は0.001mmです。工場では、百目盛と千目盛を一般にバーニヤキャリパーやミリノギスと呼んでいる。板金加工では、読み取り値が0.01mmの百目盛ノギスが多く使われています。

5.4.1 1000分の1スケールマイクロメーターの使用方法:
- ステップ1: 必要に応じて、適切なノギスの範囲を選択します。
- ステップ2:マイクロメーターの目盛り本体と測定面をきれいにします。
- ステップ3:マイクロメーターをマイクロメータースタンドに取り付け、固定し、ゼロ調整を行う。
- ステップ4:2つの作業面の間にワークを置き、作業面がワークと素早く接触するまでシンブルを調整し、「カチッ」と3回音がするまで測定力装置を調整します。
5.4.2 1000分の1スケールマイクロメーターの読み取り方法:
- ステップ1:固定スリーブに露出した目盛線の大きさを読み、読み取るべき0.5mmの目盛線の値を見逃さないように注意する。
- ステップ2:シンブルのサイズを読み取り、シンブルの円周上のどのグリッドが固定スリーブの中心線ベンチマークと一致しているかを確認し、グリッドの数に0.001mmを掛けてシンブルのサイズを求めます。
- ステップ3:上記の2つの数値を足し、ノギスで測定した寸法を求める。
例下図のように、スリーブの上の目盛りを3とし、3の後の下の目盛りを読むと、3+0.5=3.5となる。次にスリーブの目盛りを25に揃えて読むと、25×0.001=0.025となる。これを足すと3.525となる。
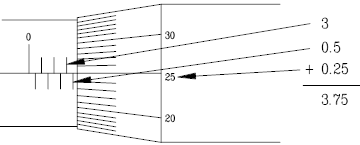
5.5.万能角度定規:
精密部品の内角・外角の測定や、角度のマーキングなどに使用される角度測定器です。
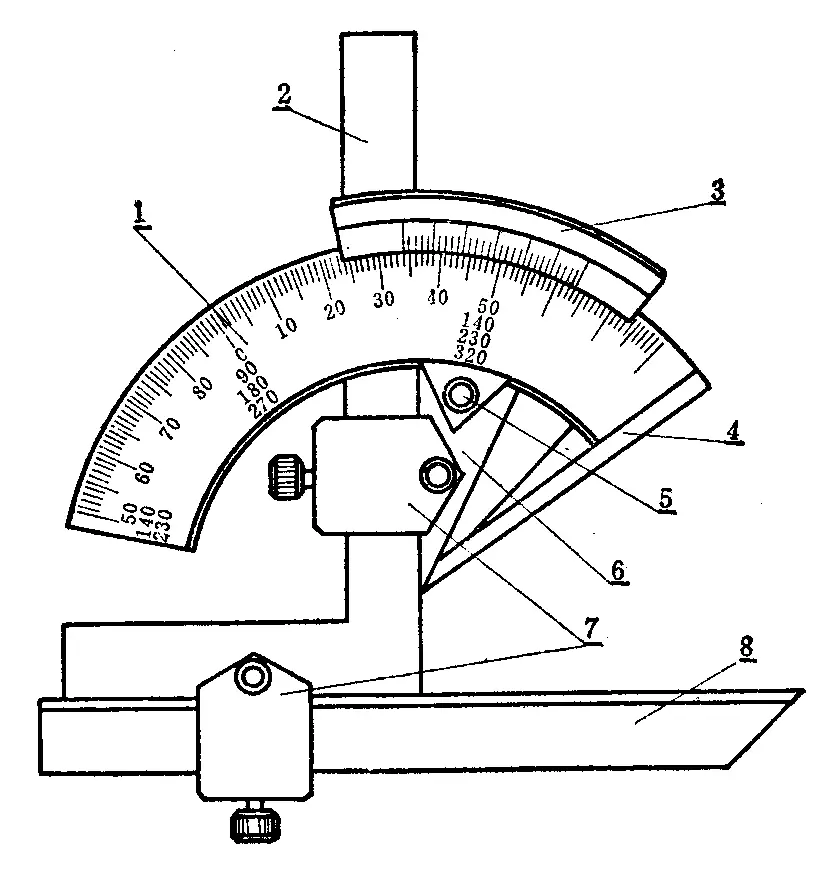
万能角度定規の使用方法と読み方:
ユニバーサル角度定規の読み取り機構は、右図に示すように、基本角度目盛線を持つスケールベース1と、セクタープレート6上に固定されたバーニヤ3から構成されています。セクタープレートはベース上を回転移動(ブレーキ5付き)することができ、バーニヤキャリパーのような読み取り機構を形成します。
ユニバーサル角度定規の目盛線の各グリッドの度数は1度です。バーニアには30個のグリッドがあり、合計29°の角度を占めるので、各グリッド間の度数の差は
したがって、万能角度定規の精度は2′である。
万能角度定規の読み取り方法は、バーニアキャリパーと同じです。まず、バーニアのゼロラインの手前の角度を読み取り、次にバーニアから角度の「分」値を読み取ります。この2つの値を足すことで、測定部分の角度値が得られます。
万能角度定規は、ベース定規4がベース上に固定され、角度定規2がクランプブロック7によってセクタープレート上に固定されています。可動定規8はクランプブロックによって角度定規上に固定されています。角度定規2を取り外せば、直線定規8もセクタープレート上に固定できる。角度定規2と直線定規8は移動および交換が可能であるため、万能角度定規は、図1-11に示すように、0°から320°までのあらゆる角度を測定することができます。
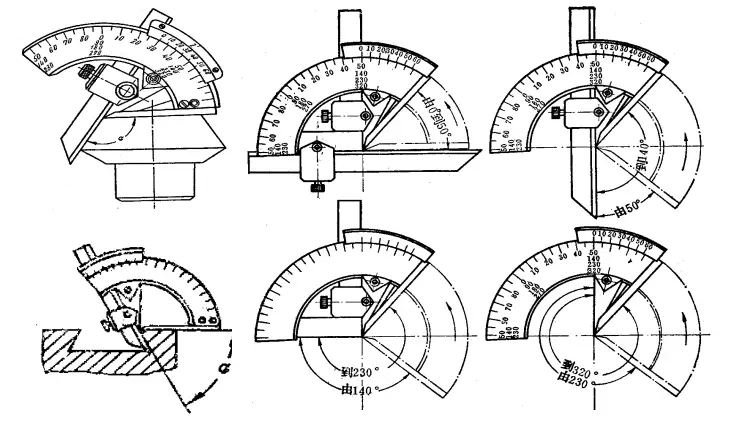
図 1-11 に示すように、角度定規と直定規を完全に取り付けると、0º から 50º までの外角を測定することができます。直定規のみを取り付けた場合、50°から140°までの角度を測定することができます。角度定規のみを取り付けた場合、140°から230°までの角度を測定できます。角度定規と直定規の両方を取り外すと、230ºから320ºまでの角度を測定することができます(つまり、40ºから130ºまでの内角を測定することができます)。
万能角度定規のスケールベース上の基本角度目盛線は、0°から90°の範囲のみです。測定された部品の角度が90°を超える場合は、基本値(90°、180°、270°)を読み取りに追加する必要があります。部品の角度が>90º~180ºを超える場合は、測定角度=90º+万能角度定規の読み取り値、180º~270ºを超える場合は、測定角度=180º+万能角度定規の読み取り値、270º~320ºを超える場合は、測定角度=270º+万能角度定規の読み取り値。
万能角度定規を使用して部品の角度を測定する場合、測定誤差を避けるために、ベース定規を部品の角度方向のベースラインに合わせ、部品が角度ゲージの2つの測定面に完全に接触するようにします。
6.主なプロセス技術の紹介
6.1 プレス加工
6.1.1 穴あけサイズの最小要件 穴あけ金型の強度制限のため、開口部をあまり小さくすることはできない。打ち抜き穴の最小サイズは、穴の形状、材料の機械的特性、材料の厚さによって決まります。
表6-1にパンチングの最小穴サイズを示す。
材料 | 打ち抜きの最小直径または最小辺の長さ(tは材料の厚さ)。 | ||
丸穴D(Dは直径) | 正方形の穴L(Lは各辺の長さ) | ウエスト丸穴、長方形穴a(aは最小辺の長さ) | |
高炭素鋼および中炭素鋼 | ≥1.3t | ≥1.2t | ≥1t |
低炭素鋼と真鍮 | ≥1t | ≥0.8t | ≥0.8t |
アルミニウムと亜鉛 | ≥0.8t | ≥0.6t | ≥0.6t |
6.1.2 最小打ち抜きピッチ
図1-12に示すように、打ち抜かれた部品の端と外形との間の最小距離には、部品と穴の形状によって一定の制限がある。

6.1.3 重ね打ちの要件
複合ダイスで加工する穴と穴、穴と穴の精度は比較的確保しやすく、加工効率も高い。しかし、図1-13に示すように、穴と穴の間隔、穴と外形の間隔は、複合ダイスの最小肉厚要求を満足できるものでなければならない。
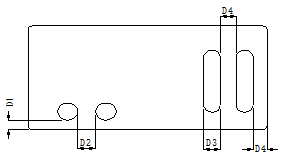
表6-2:パンチング部品とブランキング部品の複合金型加工におけるオーバーラップの最小サイズ。
t (0.8以下) | t (0.8~1.59) | t (1.59~3.18) | t (3.2以上) | |
D1 | 3mm | 2t | ||
D2 | 3mm | 2t | ||
D3 | 1.6mm | 2t | 2.5t | |
D4 | 1.6mm | 2t | 2.5t |
6.1.4 穴が変形しないように、曲げる前にパンチをする。穴と曲げ端の間の最小距離を図1-14に示す。この距離の公式はX≧2t+Rである。

図1-15に示すように、深絞り部品に穴を開ける場合、穴の形状と位置の正確さ、および金型の強度を確保するために、穴の壁と部品の直線壁との間に一定の距離を保つ必要がある。この距離a1、a2は次の要件を満たす必要がある:
- a1 ≧ R1 + 0.5t
- a2 ≧ R2 + 0.5t
ここで、R1とR2は丸みの半径、tは板厚である。
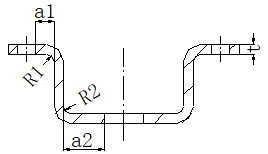
6.1.6 数値打抜き時に注意すべき問題と要件
厚みが0.6mm以下の材料は変形しやすく、金型やクランプによって加工範囲が制限されるため、一般的に数値打ち抜き加工は適さない。
適度な硬度と靭性を持つ材料は、打ち抜きや切断に適している。硬度が高すぎると パンチ力 が大きくなり、パンチヘッドや精度に悪影響を及ぼします。硬度が低すぎると、打ち抜き時の変形が激しくなり、精度が大きく制限されます。
材料の可塑性が高いことは、成形加工には有利であるが、ニブリングや連続打ち抜きには適さない場合があり、打ち抜きやトリミングにはあまり適していない。適切な靭性は、打ち抜き時の変形の程度を抑えることができるため、打ち抜き加工に有利である。しかし、靭性が高いと、打ち抜き後の反発が大きくなり、精度に影響することがある。
通常の低炭素鋼板をプレスする場合、金型の直径と幅は材料の厚さより大きくなければならない。例えば、直径Φ1.4の金型では1.5mmの材料は打抜けない。アルミニウム合金や銅合金の板を打ち抜く金型は小さくてもよいが、ステンレス鋼や高炭素鋼の板を打ち抜く金型は大きくなければならない。そうでないと、金型が割れたり破損したりしやすいからだ。
ステンレス鋼板は一般的に数値打ち抜き加工には適しません。もちろん、板厚0.8mm~2.5mmのステンレス板は数値打ち抜きで加工できますが、一般鋼板に比べ金型の摩耗が大きく、スクラップ率も高くなります。
6.2 曲げ加工
板金における曲げ加工とは、板金をV字型やU字型などに曲げるなど、板金や部品の角度を変える加工を指す。一般的に板金の曲げ加工には、複雑な構造、少量生産、大量生産の板金構造物に使用される金型曲げ加工と、比較的寸法が大きい板金構造物や生産量の少ない板金構造物の加工に使用されるベンディングマシン曲げ加工の2つの方法があります。現在、当社の製品は主にベンディングマシンを使用して加工しています。
6.2.1 曲げ加工シーケンスの基本原則
- 内側から外側に曲げる;
- 小さなものから大きなものまで曲がる;
- まず特殊な形を曲げ、次に一般的な形を曲げる;
- 前工程の成形が後工程の邪魔にならないようにする。
6.2.2 曲げ半径
材料が曲げられると、外側の層は引き伸ばされ、内側の層は角の丸い部分で圧縮される。材料の厚さが一定の場合、内半径rが小さいほど、材料の伸びと圧縮が激しくなる。外角部の引張応力が材料の極限強度を超えると、亀裂や破損が発生する可能性がある。したがって、曲げ部品の構造設計では、小さな曲げ半径は避けるべきである。その 最小曲げ 一般的な材料の半径を下表に示す。
表6-1:一般的に使用される金属材料の最小曲げ半径リスト
いや。 | 素材 | 最小曲げ半径 |
1 | 08、08F、10、10F、DX2、SPCC、E1-T52、0Cr18Ni9、1Cr18Ni9、1Cr18Ni9Ti、1100-H24、T2 | 0.4t |
2 | 15、20、q235、q235a、15f | 0.5t |
3 | 25、30、Q255 | 0.6t |
4 | 1Cr13、H62(M、Y、Y2、冷延) | 0.8t |
5 | 45、50 | 1.0t |
6 | 55、60 | 1.5t |
7 | 65Mn、60SiMn、1Cr17Ni7、1Cr17Ni7-Y、1Cr17Ni7-DY、SUS3010Cr18Ni9、SUS302 | 2.0t |
- 曲げ半径は、曲げられた部品の内半径を指し、"t "は材料の厚さである。
- t "は材料の厚さ、"M "は焼鈍状態、"Y "は硬化状態、"Y2 "は半硬化状態を示す。
6.2.3 鋼板折り曲げ最小曲げ端寸法の参考表
材料の厚さ | 0.8 | 1.0 | 1.2 | 1.5 | 2.0 | 2.5 | 3 |
最小曲げエッジ | 5 | 6.5(5) | 6.5(6) | 7(6.5) | 9 | 11 | 13 |
上記の仕様より小さい曲げ寸法を要求される部品については、別の金型を使用して加工する必要があります。
6.2.4 穴および楕円穴から曲げ端までの最小距離:
図1-16に示すように、曲げ部の穴端が曲げ線に近すぎると、曲げ時に材料が浮き上がらず、穴形状が変形する。従って、孔縁と曲げ線との距離は、孔縁最小距離X≧t+R以上でなければならない。
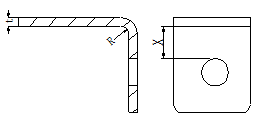
表6-2:丸穴から曲げ端までの最小距離。
材料の厚さ | 0.6~0.8 | 1.0 | 1.2 | 1.5 | 2.0 | 2.5 |
最短距離 X | 1.3 | 1.5 | 1.7 | 2.0 | 3 | 3.5 |
図1-17に示すように、楕円孔が曲げ線に近すぎると、曲げ時に材料が浮き上がり、孔形状が変形する。したがって、穴の縁と曲げ線との間の距離は、表1-14による穴の縁の最小距離より大きくなければならない。

表6-3:楕円穴から曲げ端までの最小距離。
L | <26 | 26~50 | >50 |
最短距離 X | 2t+R | 2.5t+R | 3t+R |
6.2.5 穴、スロット、切り欠きの加工 曲げ部品:
曲げ加工の際、曲げられた部品の端がブランクの内側 の端まで曲げられる必要がある場合は、図1-18に示すように、破れ や歪みを防ぐために、加工穴、スロット、またはノッチを追加す ることを推奨する。
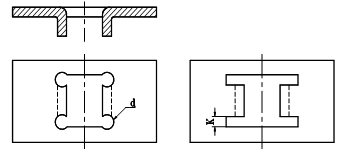
- 加工穴の直径は≧tでなければならない。
- プロセスノッチの幅は≧t、深さは≧1.5tとする。