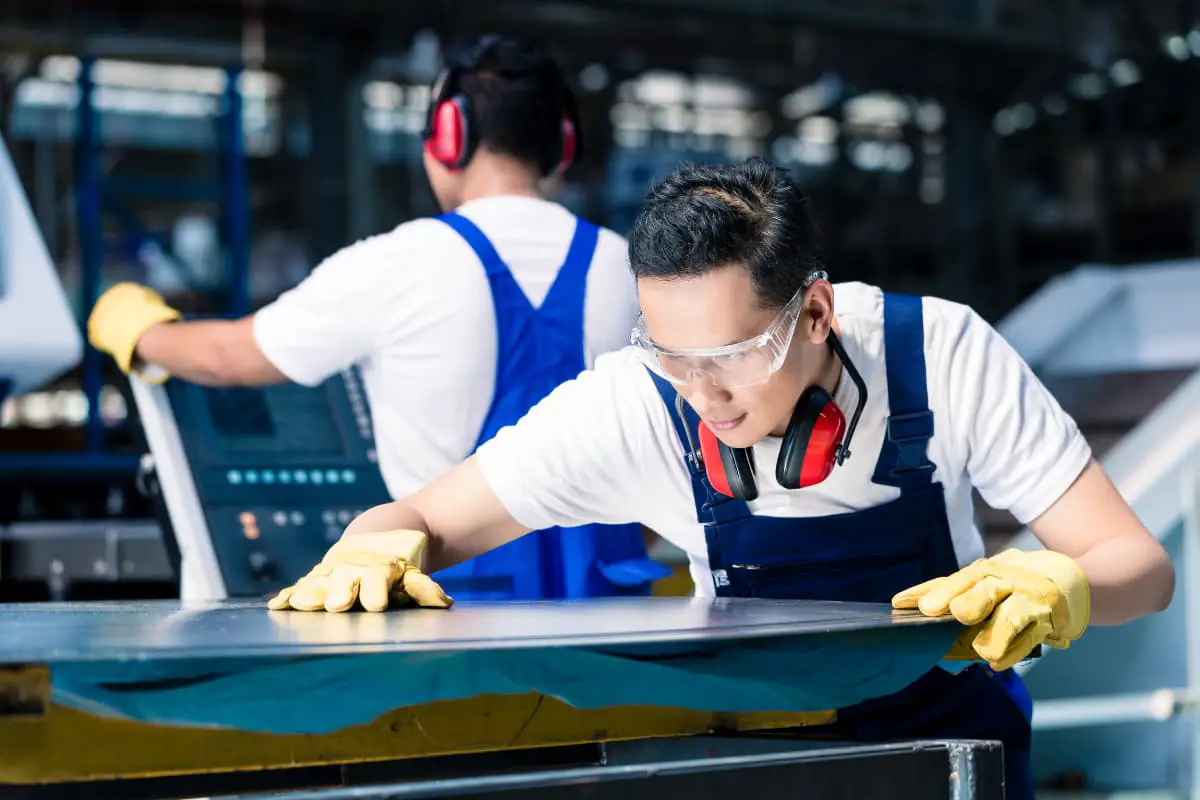
Заготовки, полученные обычной штамповкой, имеют фаски, зоны разрушения и заусенцы на поверхности среза, а также явную конусность, с шероховатостью поверхности Ra 6,3~.
12,5 мкм, и в то же время, точность размеров пробитых деталей относительно низкая, обычно T10~T11, что обычно может удовлетворить технические требования к деталям.
Однако если поверхность среза штампованных деталей используется в качестве опорной поверхности, сопрягаемой поверхности, поверхности сборочного соединения или подвижной поверхности, необходимы более высокие требования к качеству сечения и точности размеров штампованных деталей. В это время необходимо применять технологические методы повышения качества и точности штампованных деталей (см. табл. 1), чтобы соответствовать предъявляемым требованиям.
Таблица 1 Несколько технологических методов повышения качества и точности штампованных деталей
Категория | Имя процесса | Схема | Ключевые моменты метода | Ключевые моменты метода |
Отделка | Капитальный ремонт | ![]() | Удалите нечистые поверхности, односторонний зазор 0,006~0,01 мм или отрицательный зазор, определите объем и частоту капитального ремонта в зависимости от толщины и формы материала | Высокая точность, низкая шероховатость поверхности, малые углы разрушения и заусенцы. Высокие требования к позиционированию, нелегко удалить стружку. Эффективность ниже, чем при прецизионной штамповке |
Полировка экструзии | ![]() | Коническая вогнутая матрица экструзионной полировки, припуск на одной стороне менее 0.04~0.06mm. Зазор между выпуклыми и вогнутыми штампами обычно составляет (0.1~0.2)t (t - толщина материала). | Качество ниже, чем при капитальном ремонте и точной штамповке, подходит только для мягких материалов, эффективность ниже, чем при точной штамповке | |
Полупрецизионная штамповка | Штамповка с отрицательным зазором | ![]() | Размер выпуклой матрицы больше размера вогнутой (0.05~0.3)t, радиус вогнутой матрицы (0.05~0.1)t | Низкая шероховатость поверхности, подходит для мягких цветных металлов металлы и сплавы, мягкая сталь и т.д. |
Пробивка лезвия с малым зазором и закругленным углом | ![]() | Зазор менее 0,02 мм Заготовка: Радиус закругленного угла лезвия штампа составляет 0,1t Перфорирование: радиус закругленного угла лезвия перфоратора составляет 0,1 т. | Меньшее значение шероховатости поверхности, больший угол развала и заусенцы | |
Пробивание вверх и вниз | ![]() | Первый шаг пресса выпуклый, глубина пуансона в (0.15~0.30)t, второй шаг обратный пуансон вниз заготовки | Нет заусенцев на верхней и нижней сторонах, сохранились углы разрушения и поверхности излома, сложные действия | |
Пробивание вверх и вниз | ![]() | Пуансон врезается в материал плиты (0.15~0.35)t, поверхность пуансона ab затем сжимает материал плиты, односторонний зазор между пуансоном и матрицей 0.01~0.05mm, радиус закругленного угла лезвия составляет 0.05~0.2mm | Поверхность реза гладкая, а шероховатость поверхности небольшая. Он отлично адаптируется к характеристикам и толщине материала, не требуя специализированного оборудования для точной штамповки. | |
Прецизионная штамповка | Нажимной диск с зубчатым венцом Прецизионная штамповка | ![]() | / | |
Противоположный вогнутый штамп Прецизионная штамповка | ![]() | / | ||
Противоположный вогнутый штамп Прецизионная штамповка | ![]() | / |
Ниже кратко описаны несколько методов чистовой и полуточной штамповки.
I. Refinishing
Доработка включает в себя использование доводочного штампа для снятия тонкого слоя стружки вдоль внешнего края или стенки отверстия пробитых деталей, удаление разрушений, заусенцев и зон разрушения, оставшихся на поперечном сечении при обычной штамповке, что позволяет получить гладкие и перпендикулярные поперечные сечения и детали точного размера. Как правило, детали после доработки могут достигать допусков IT6 - IT7, а шероховатость поверхности Ra может достигать 0,4 - 0,8 мкм.
Метод рафинирования показан на рисунке 1. Внешняя форма обрезанных деталей называется обрезкой кромок (см. рис. 1a); внутренняя форма пробитых деталей называется обрезкой внутренних кромок (см. рис. 1b), а механизм доработки полностью отличается от пробивки, аналогично обработке резанием.
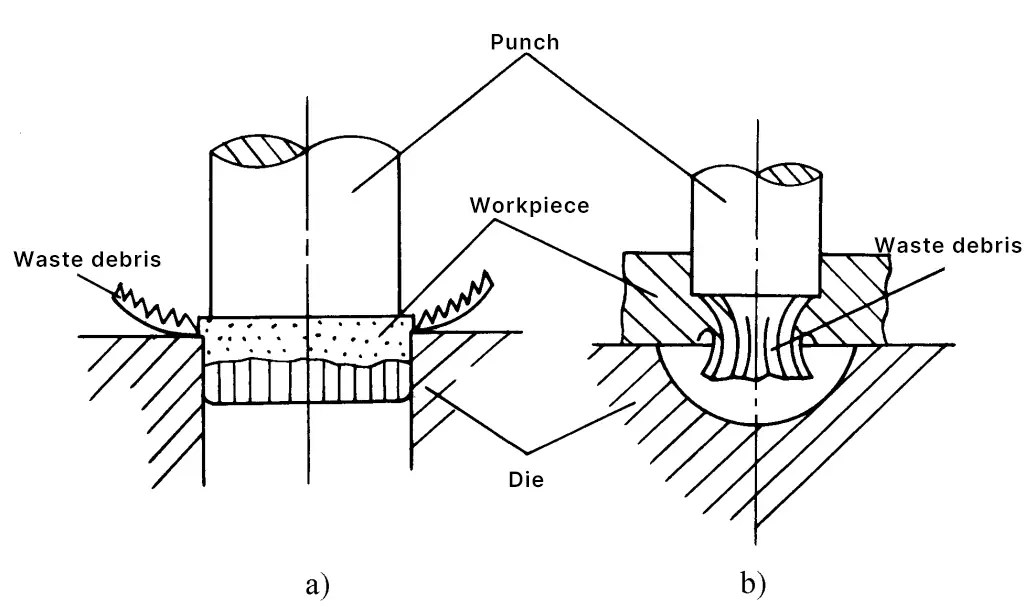
1. Надбавка на доработку
Припуск на рафинирование должен быть выбран правильно; слишком большой или слишком маленький припуск снизит качество рафинированных деталей. Припуск на доработку зависит от материала, толщины и формы деталей, а также от условий обработки перед доработкой. Например, если перед облагораживанием используется штамповка с большим зазором, необходим больший припуск на облагораживание, чтобы срезать большую коническую зону разрушения на поперечном сечении; в то время как при штамповке с малым зазором для срезания средней шероховатой полосы и возможных трещин, образующихся при вторичном сдвиге, большой припуск на облагораживание не требуется.
При доработке внутренней кромки, если требуется сверление, припуск на доработку может быть меньше, чем при перфорации. Если при доработке отверстий также требуется точность расстояния между отверстиями, то припуск на доработку должен быть увеличен. Припуск на доработку для перфорирования с большим зазором приведен в таблице 2, а для перфорирования с малым зазором припуск на доработку приведен на рисунке 2.
Таблица 2 Двунаправленный припуск на доработку y (единицы измерения: мм)
Толщина материала | Латунь, низкоуглеродистая сталь | Сталь средней твердости | Твердая сталь | |||
Мин | Макс | Мин | Макс | Мин | Макс | |
0.5~1.6 | 0.1 | 0.15 | 0.15 | 0.2 | 0.15 | 0.25 |
>1.6 ~3.0 | 0.15 | 0.2 | 0.2 | 0.25 | 0.2 | 0.3 |
>3.0~4.0 | 0.2 | 0.25 | 0.25 | 0.3 | 0.25 | 0.35 |
>4.0~5.2 | 0.25 | 0.3 | 0.3 | 0.35 | 0.3 | 0.4 |
>5.2~7.0 | 0.3 | 0.35 | 0.4 | 0.45 | 0.45 | 0.5 |
>7.0~10.0 | 0.35 | 0.4 | 0.45 | 0.5 | 0.55 | 0.6 |
Примечание:
1. Наименьший припуск используется для заготовок простой формы, а наибольший - для заготовок сложной формы или с острыми углами.
2. При многократном ремонте для второго и последующих ремонтов используется наименьшее значение в таблице.
3. Припуск на ремонт для титановых сплавов составляет (0,2 ~ 0,3) т.
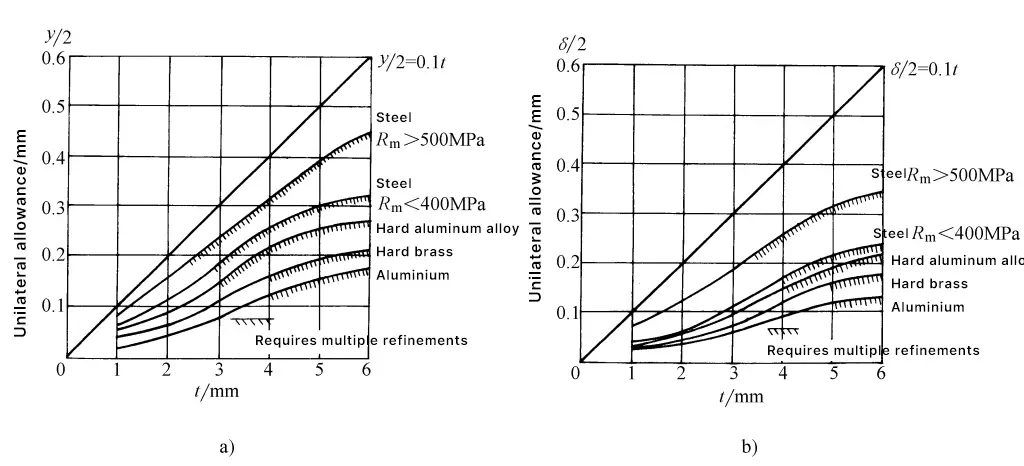
a) Бланкирование
б) Удар
В зависимости от размера зазор между штампами При заготовке метод расчета размеров рабочей части штампа делится на два типа. Расчет размеров заготовительного штампа приведен в таблице 3, а штампа для вырубки - в таблице 4.
Таблица 3 Расчет размеров рабочей части заготовительного штампа до ремонта
Размеры штампов и припуски на ремонт | Первый тип метода ремонта Используйте заглушки с большими зазорами | Первый тип метода ремонта Используйте заглушки с большими зазорами |
![]() | ![]() | |
Размер заготовительного штампа Размер заглушки Односторонний зазор Надбавка за капитальный ремонт Общее пособие на удаление | ![]() y см. таблицу 2 δ равно 2c плюс y | ![]() δ, см. рис. 2a |
Примечание:
- c- односторонний зазор для перфорации;
- y-надбавка на ремонт, см. таблицу 7;
- D - основные размеры ремонтной детали;
- t- толщина ремонтной детали;
- δ p , δ d - производственные отклонения выпуклых и вогнутых штампов, δ p , δ d = (0.8~1.2) (c max -c min );
Таблица 4 Расчет размеров рабочей части пуансон-формы до ремонта
Размеры пресс-формы и припуск на ремонт | Первый метод ремонта Использование перфорации с большими зазорами | Второй метод ремонта Применяйте перфорацию с малым зазором |
![]() | ![]() | |
Размер вырубного штампа Размер пуансона Односторонний зазор Пособие на ремонт Общее пособие на удаление | ![]() y см. таблицу 2 δ равно 2c плюс y | ![]() δ, см. рис. 2b δ |
Примечание: d - базовый размер ремонтного отверстия;
2. Количество ремонтов
Количество ремонтов зависит от толщины материала и формы заготовки. Для заготовок толщиной менее 3 мм и простой, гладкой формы, как правило, требуется только один ремонт; для заготовок толщиной более 3 мм или с острыми углами необходимо два или более ремонтов для предотвращения разрыва. Распределение припусков на второй ремонт показано на рисунке 3. Количество ремонтов можно определить по таблице 5 в зависимости от толщины материала и сложности формы заготовки.
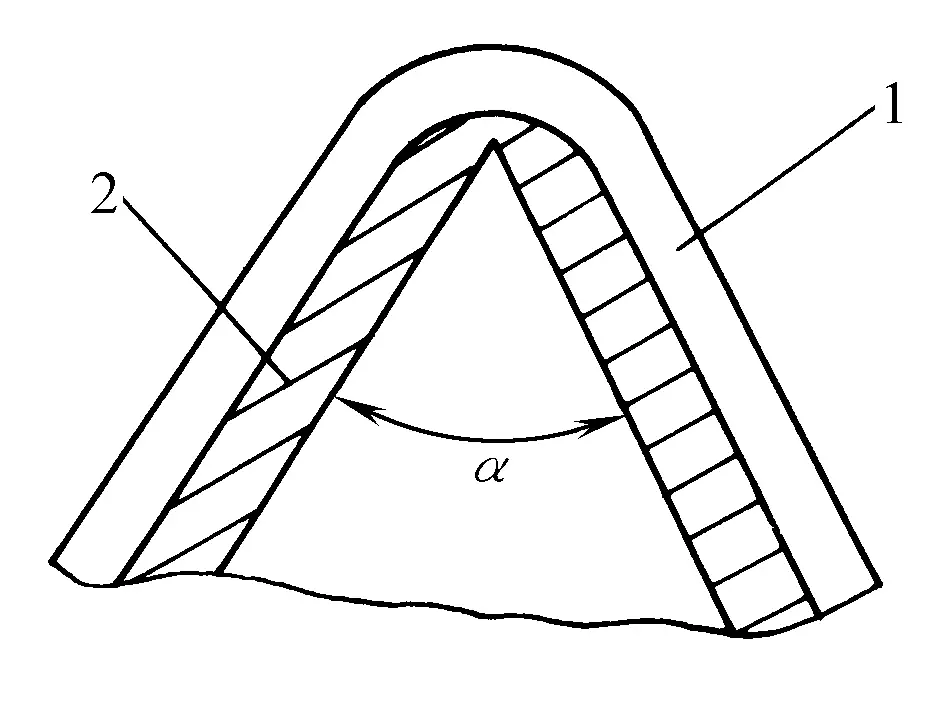
1-Первый ремонт
Двухсекундный ремонт
Таблица 5 Периодичность процесса ремонта
Сложность контура заготовки | Материал Толщина / мм | |
<3 | <3 | |
Плавный контур без острых углов | 1 | 2 |
Сложный контур с острыми углами | 2 | 3~4 |
3. Ремонтные силы
Усилие, необходимое для капитального ремонта, можно приблизительно рассчитать по следующей формуле
Pz=L(δ+0.1tn)τb
где
- L - длина периметра капитального ремонта (мм);
- δ - общий припуск на удаление (мм);
- n - количество деталей, одновременно зажатых в штампе:
- t - толщина материала (мм);
- τ b - Прочность материала на сдвиг (МПа).
4. Расчет размеров рабочей части ремонтной пресс-формы
Формула для расчета размеров рабочей части ремонтной пресс-формы приведена в таблице 6.
Таблица 6 Расчет размеров рабочей части ремонтной пресс-формы
Размеры рабочей части | Восстановление внешнего края (процесс) | Восстановление внутренней кромки (процесс) |
Размеры матрицы для восстановления | ![]() | Штамп, как правило, поддерживает только заготовку, а форма и размеры полости не должны быть строго определены |
Размеры пуансонов для восстановления | ![]() | ![]() |
Примечание:
- D max максимальный предельный размер восстановленной детали (мм);
- d мин минимальный предельный размер восстановленной детали (мм);
- Δ - допуск на восстановленную деталь (мм);
- c′- односторонний зазор пресс-формы для восстановления, 2c'=0.01~0.025 мм;
- δ p , δ d допуски на изготовление выпуклых и вогнутых форм (мм), δ p =0,2Δ, δ d =0.25Δ;
- ε y - усадка отверстия после реконструкции
- Для алюминия: ε y =0.005~0.01mm;
- Латунь: ε y =0.007~0.012mm;
- Мягкая сталь: ε y =0.008~0.015mm.
5. Другие методы восстановления
(1) Восстановление горения
Восстановление кромки обжигом включает в себя принудительное вдавливание заготовки, полученной обычной штамповкой, в отверстие с округлой или конической вогнутой формой (см. рис. 4), используя поверхностную пластическую деформацию для достижения аккуратного и гладкого сечения. Припуск на одностороннее обжигание составляет менее 0,04~0,06 мм. Этот процесс, как правило, подходит только для мягких материалов, и его качество немного ниже, чем у процессов восстановления резанием.
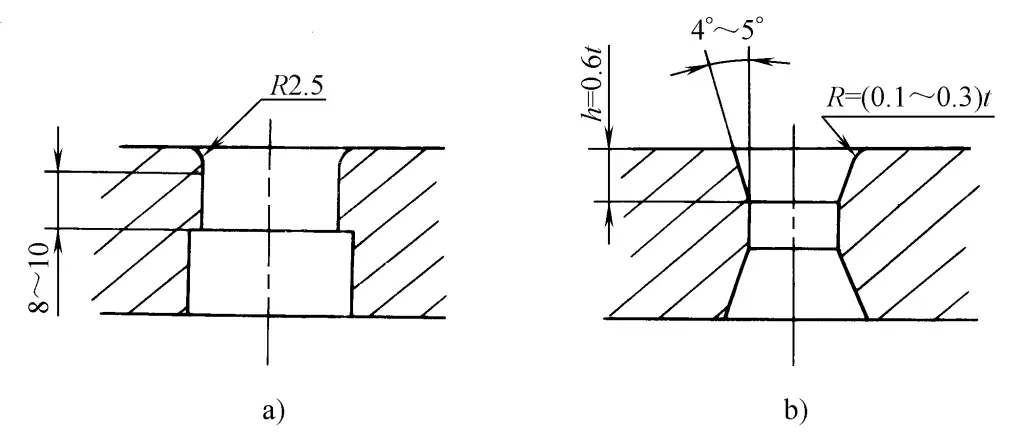
a) Закругленная вогнутая форма
б) Коническая вогнутая форма
Определение размера рабочей части вогнутой пресс-формы аналогично определению размера восстановленной пресс-формы, но так как этот метод предполагает большую упругую деформацию заготовки (для заготовок в пределах 30 мм упругая деформация может достигать 0,01~0,025 мм) и увеличивается с толщиной восстановленной заготовки, размер вогнутой пресс-формы должен быть рассмотрен соответствующим образом. Размер выпуклой формы больше размера вогнутой формы на (0.1~0.2)t.
Обработка внутренних кромок с помощью оправки или прецизионного прессованного шарика (см. рис. 5). Этот процесс предполагает использование давления выпуклой пресс-формы для проталкивания стального шарика (или оправки) с высокой твердостью (63-66 HRC) через отверстие на заготовке, которое немного меньше требуемого размера, сплющивая поверхность отверстия. Он может обрабатывать не только круглые отверстия с помощью шарика, но и некруглые отверстия с выемками с помощью оправки.
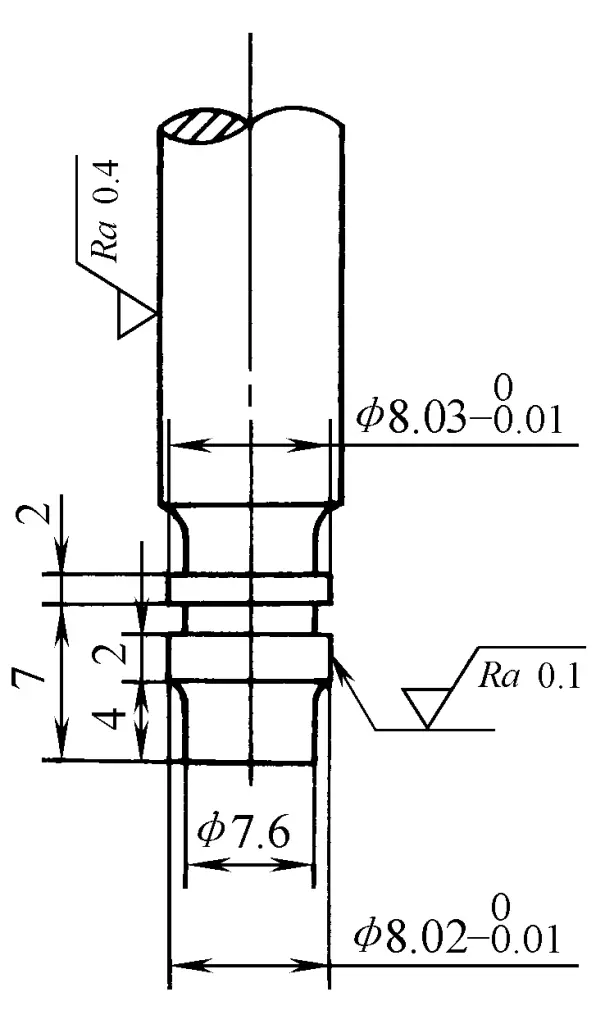
(2) Ламинированная отделка
При использовании общих методов отделки из-за очень малого зазора требуется высокая точность изготовления пресс-формы, а также проблема выбора оптимального припуска на отделку. Поэтому гладкая поверхность не может быть достигнута за один проход отделки, а многослойная отделка позволяет избежать вышеупомянутых проблем.
При ламинированной отделке две заготовки укладываются друг на друга, при этом диаметр выпуклой формы больше диаметра вогнутой формы, и выпуклая форма давит на отделываемую заготовку через одну из заготовок. Когда отделка достигает 2/3 - 3/4 толщины листа заготовки, вторая заготовка подается для следующего хода отделки (см. рис. 6).
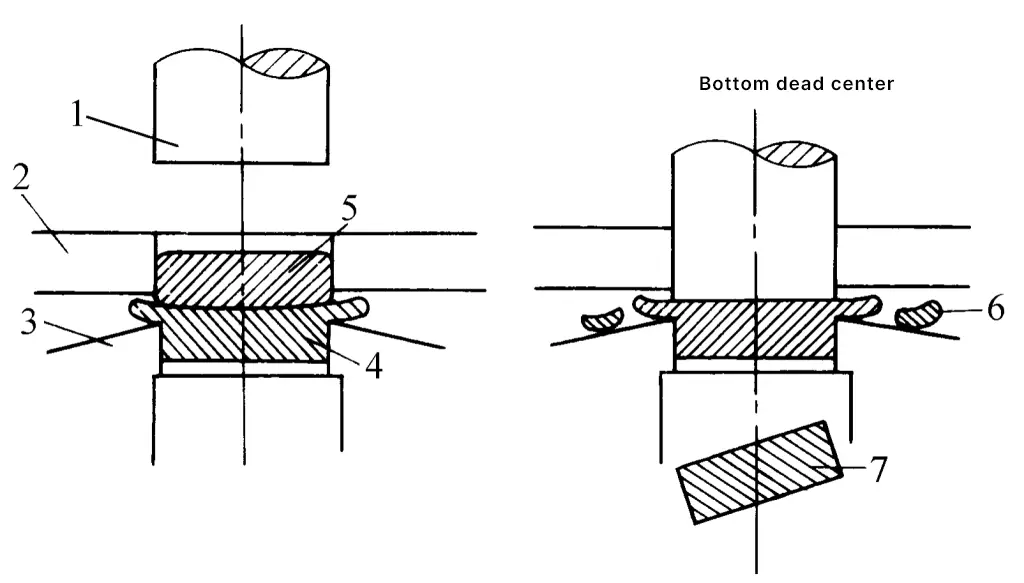
1-Выпуклая форма
2-Направляющая пластина
3-Вогнутая форма (с передним углом)
4-Первичная обработка заготовок до 2/3 - 3/4 толщины листа
5-Совпадающие заготовки для следующей корректировки
6 чипсов
7-Заготовки
Поскольку при восстановлении пуансон не входит в матрицу, изготовление пресс-формы не представляет сложности. Материалы, пригодные для восстановления, и диапазон припусков на обработку шире, чем при общих методах восстановления. Недостатком является то, что после ввода заготовки в следующий ход необходимо удалить стружку, поэтому требуются соответствующие меры, например, обработка угла опережения 10°~15° или стружкоотбойной канавки на торцевой поверхности штампа, а также использование сжатого воздуха высокого давления для удаления стружки. Еще одна проблема - крупные заусенцы.
(3) Вибрационное восстановление
Для небольших высокоточных деталей сложной формы, таких как кулачки и шестерни, вибрационное восстановление может быть выполнено на специальном вибрационном прессе, оснащенном вибрирующим ползуном, который имеет второй двигатель для обеспечения вибрации пуансона, соединенного с этим ползуном. Детали, помещенные в матрицу для восстановления, при продвижении пресса на 0,05~0,06 мм за ход, выдерживают 1200~2000 кратковременных ударов в минуту.
Деформация при вибровосстановлении ограничивается меньшим объемом обрабатываемого металла, что позволяет избежать расширения свинцовых трещин и возникновения разрывов. Кроме того, благодаря вибрационному воздействию скребка кромок штампа поверхность среза становится гладкой, а деформация деталей сводится к минимуму. После восстановления точность размеров деталей может достигать 0,05~0,01 мм, а шероховатость поверхности Ra - 0,4~0,8 мкм.
II. Перфорация с отрицательным зазором
Как показано на рисунке 7, штамповка с отрицательным зазором - это, по сути, комбинированный процесс штамповки и восстановления. Поскольку размер пуансона больше, чем размер штампа, направление трещин, возникающих в процессе штамповки, противоположно направлению трещин при обычной штамповке, образуя заготовку в форме перевернутого конуса. Пуансон продолжает давить вниз, вдавливая заготовку в матрицу, отрезая излишки материала и получая более качественное сечение, что эквивалентно процессу восстановления.
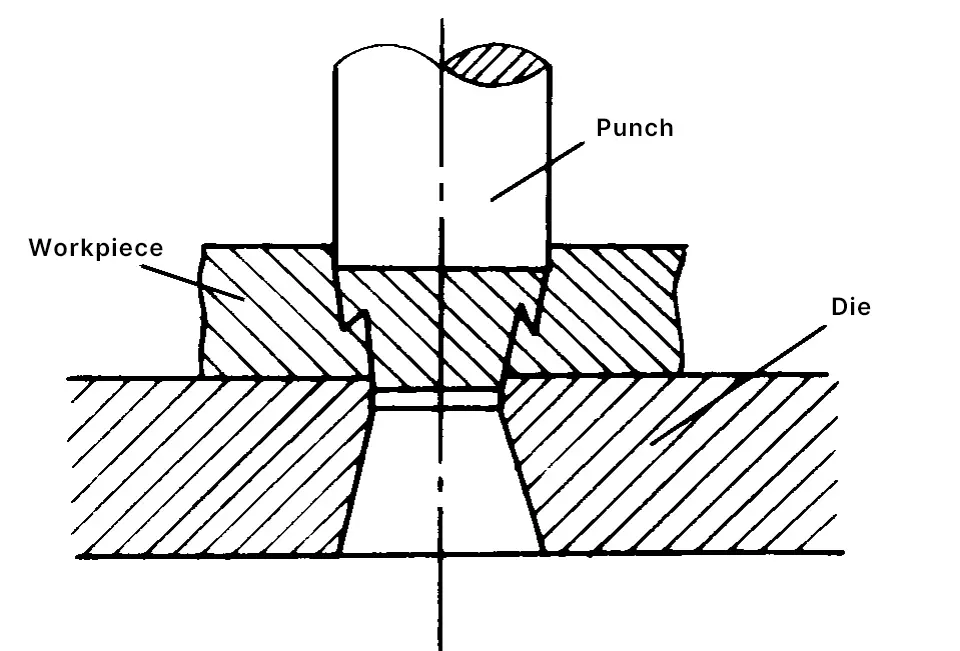
Как правило, размер пуансона больше размера матрицы на (0,1~0,2)t. Для круглых заготовок периметр, на который пуансон больше матрицы, является равномерным. Для заготовок с углублениями и выступами, выступающие углы должны быть в два раза больше остальных, т.е. (0.2~0.4)t, а углубленные части должны быть уменьшены в два раза, т.е. (0.05~0.1)t, как показано на рисунке 8.
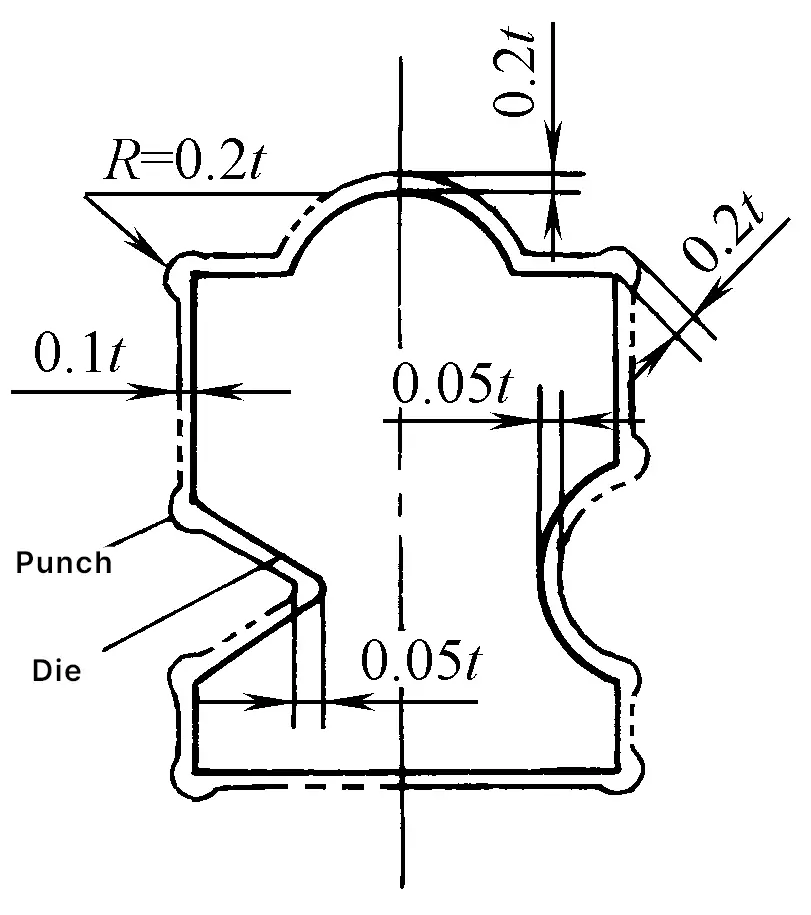
Для достижения более низкого значения шероховатости поверхности на срезанной поверхности, на краю штампа можно сделать радиус 0,1~0,3 мм. Поскольку пуансон больше штампа, пуансон не должен входить в отверстие штампа после завершения штамповки, а должен находиться на расстоянии 0,1~0,2 мм от верхней поверхности штампа.
В это время заготовка еще не полностью впрессована в штамп, и ее необходимо полностью впрессовать во время штамповки следующей детали. После того, как заготовка выпадет из отверстия штампа, ее размер увеличится на 0,02~0,06 мм из-за упругой деформации. Поэтому при проектировании рабочей части штампа необходимо уменьшить эту деформацию.
При использовании этого метода шероховатость поверхности Ra пробитых заготовок может достигать 0,4~0,8 мкм, а точность размеров - IT9 - IT11. Однако для тонких пластин большого размера с толщиной t≤1,5 мм может возникнуть значительная дугообразность. Кроме того, штамповка с отрицательным зазором подходит только для мягких материалов с хорошей пластичностью, таких как мягкий алюминий, медь, мягкая сталь и т. д. В основном она используется для точной заготовки холоднопрессованных листовых заготовок и некоторых простых плоских деталей.
Усилие, необходимое для штамповки с отрицательным зазором, намного больше, чем при обычной штамповке, и штамп испытывает большее давление, что делает его склонным к растрескиванию. Использование хорошей смазки может предотвратить прилипание материала к пресс-форме и продлить срок ее службы.
Усилие для пробивки с отрицательным зазором P можно определить по следующей формуле
Pf=CP
В формуле
- P - Нормальный усилие пробивки (N);
- C - коэффициент, выбирается в зависимости от различных материалов: Алюминий: C=1.3~1.6; Латунь: C=2.25~2.8; Мягкая сталь: C=2.3~2.5.
III. Пробивка закругленных углов с малым зазором
При заготовке край штампа имеет небольшой закругленный или эллиптический угол (см. рис. 9), а пуансон имеет стандартную форму. При перфорации кромка пуансона имеет закругленный угол, а штамп - стандартную форму. Двусторонний зазор между пуансоном и матрицей составляет менее 0,01-0,02 мм и не зависит от толщины материала.
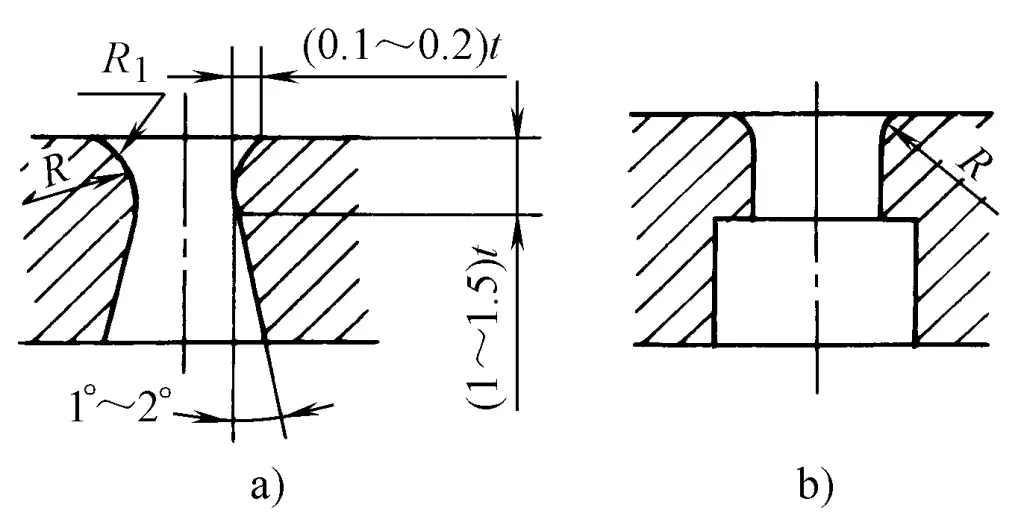
a) С эллиптическим углом
б) С закругленными углами
Поскольку кромка штампа закруглена и использует очень маленький зазор, это увеличивает гидростатическое давление в зоне штамповки, снижает растягивающее напряжение, а закругленная кромка также уменьшает концентрацию напряжения, тем самым препятствуя образованию трещин и обеспечивая яркую поверхность среза.
На рисунке 9 показаны две формы штампов с эллиптическими или закругленными углами. На рис. 9a показан штамп с эллиптическим углом, где соединение дуги и прямой линии должно быть плавным и равномерным, без острых краев.
Радиус закругленного угла R1 приведен в таблице 7, это результат, полученный для заготовки диаметром 25 мм. При других размерах можно выбрать 2/3 из значений, приведенных в таблице, и увеличивать скругленный угол по мере необходимости в процессе пробной штамповки. Для удобства изготовления можно также использовать штамп, показанный на рисунке 9b, где радиус закругленного угла обычно равен R=0,1t (t - толщина материала) или выбирается в соответствии с таблицей 8.
Таблица 7 Радиус закругления эллиптического угла R 1 Значение (диаметр заготовки ϕ = 25 мм) (Единицы измерения: мм)
Материал | Состояние материала | Толщина материала | Радиус филе R 1 |
Мягкая сталь | горячий прокат | 4 | 0.5 |
6.4 | 0.8 | ||
9.6 | 1.4 | ||
Холодный прокат | 4 | 0.25 | |
6.4 | 0.8 | ||
9.6 | 1.1 | ||
Алюминиевый сплав | Мягкий | 4 | 0.25 |
6.4 | 0.25 | ||
9.6 | 0.4 | ||
Hard | 4 | 0.25 | |
6.4 | 0.25 | ||
9.6 | 0.4 | ||
Медь | Мягкий | 4 | 0.25 |
6.4 | 0.25 | ||
9.6 | 0.4 | ||
Hard | 4 | 0.25 | |
6.4 | 0.25 | ||
9.6 | 0.4 |
Таблица 8 Значения круглого углового вогнутого штампа R (единицы измерения: мм)
Материал | Толщина материала 1 | Толщина материала 2 | Толщина материала 3 | Толщина материала 4 |
Алюминий | 0.25 | - | 0.25 | 0. 50 |
Медь (T2) | 0.25 | - | 0.5 | (1.00) |
Мягкая сталь | 0.25 | (0.5) | (1.00) | - |
Латунь (H70) | (0.25) | - | (1.00) | - |
Нержавеющая сталь (0Cr18Ni9) | (0.25) | (0.5) | (1.00) | - |
Примечание: Данные в скобках - это справочные значения.
Пробивка закругленных кромок с небольшим зазором подходит для материалов с хорошей пластичностью, таких как мягкий алюминий, чистая медь, латунь, мягкая сталь (05F, 08F) и т. д. Заготовка в идеале должна иметь равномерный гладкий контур, а закругленные углы следует использовать при прямых или острых углах, чтобы предотвратить разрыв. При расчете усилия пробивки оно должно быть увеличено на 50%, исходя из обычного усилия пробивки.
Точность обработки деталей может достигать IT9 - IT11, а шероховатость поверхности Ra - 0,4 - 1,6 мм. После выталкивания детали из отверстия штампа, вследствие упругой деформации, ее размер увеличится на 0,02-0,05 мм, что необходимо компенсировать при проектировании пресс-формы.
IV. Пробивание вверх и вниз
Процесс штамповки вверх и вниз (также называемый возвратно-поступательной штамповкой) показан на рис. 10. В нем используются две выпуклые пресс-формы для пробивки заготовки сверху и снизу, сначала пробивка идет сверху вниз (как показано на a), и останавливается, когда верхняя выпуклая пресс-форма врезается в материал на 15% - 30% толщины материала. Затем нижняя выпуклая пресс-форма используется для пробивки в обратном направлении (как показано на рисунках b, c, d).
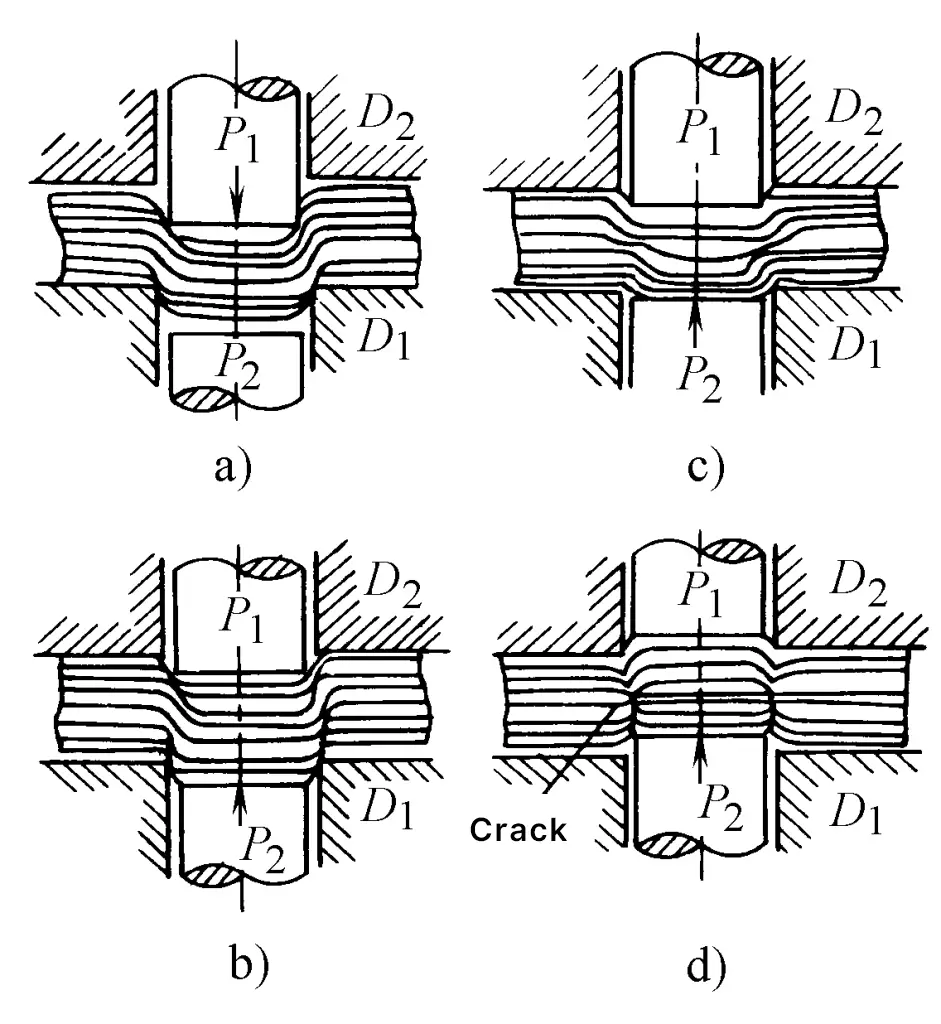
Механизм деформации при этом методе похож на обычную штамповку, по-прежнему образуются трещины сдвига и зоны разрушения, но поскольку штамп проходит через два пробития, вверх и вниз, он может получить две яркие полосы, тем самым увеличивая долю ярких полос во всем сечении, и может устранить заусенцы, тем самым значительно улучшая качество поперечного сечения штампованных деталей (см. рис. 11).
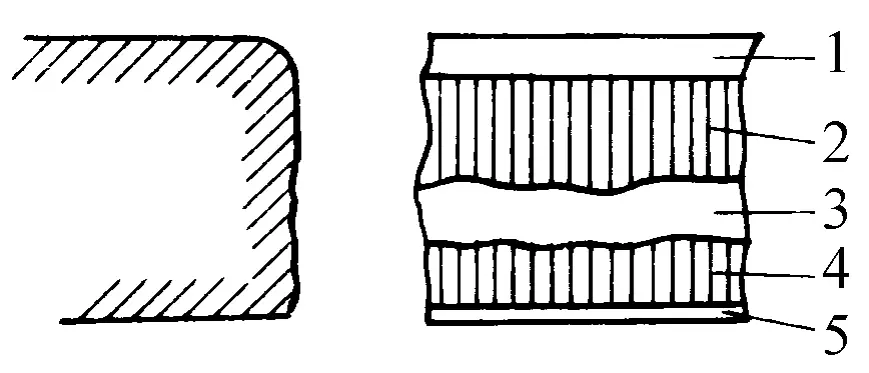
- 1, 5 Угол коллапса
- 2, 4 - Яркая полоса
- 3 - Зона разлома
Однако, поскольку этот метод предполагает более сложную конструкцию пресс-формы, он увеличивает время штамповки и предъявляет особые требования к штамповочному оборудованию, поэтому в настоящее время он применяется в производстве реже. Чтобы избежать использования специализированного пресса, этот метод также можно реализовать с помощью трехпозиционного прогрессивного штампа на прессе одинарного действия в три этапа (см. рис. 12).
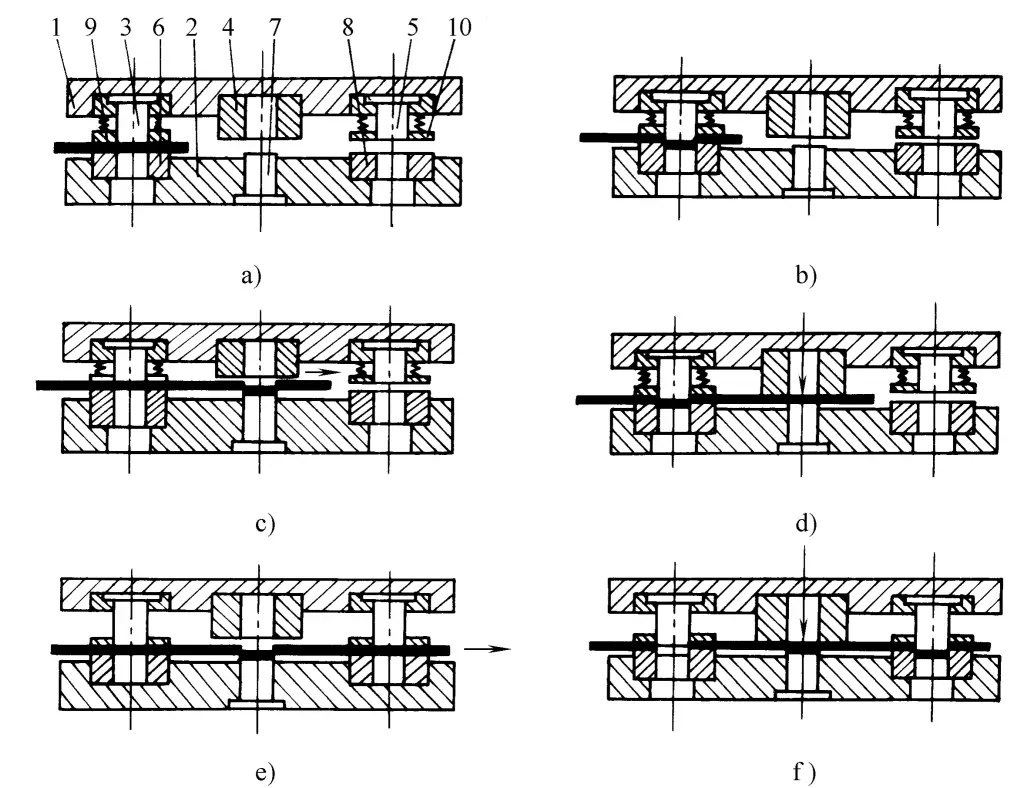
1-Верхний держатель штампа
2-Нижний держатель штампа
3-Штамп для тиснения
4-Материал для считывания
5-Сепарационный вырубной выпуклый штамп
6-Тиснение вогнутым штампом
7-Реверсивный выпуклый штамп
8-Сепарационный вырубной вогнутый штамп
9Нажимная плита для тиснения
10- Разделительная вырубная прижимная плита
1. На первом этапе тиснения материал не режется, а только вдавливается в углубление в зоне перфорации (см. рис. 12b).
2. На втором этапе тисненую заготовку возвращают в еще не разрушенное состояние в зоне перфорации с направления, противоположного первому этапу (см. рис. 12d).
3. На третьем этапе перфорация выполняется в том же направлении, что и на первом этапе, полностью разделяя заготовку (см. рис. 12f).
Глубина проникновения штампа на этапах тиснения и обратной перфорации в основном зависит от толщины и характеристик материала. Глубина проникновения штампа, как при тиснении, так и при обратной перфорации, должна быть ограничена до уровня, при котором зона перфорации еще не разрывается.
V. Синхронная стрижка и отжимная штамповка
Рабочий процесс метода синхронного сдвига и выдавливания пуансона (т. е. ступенчатой штамповки) показан на рис. 13. Когда пуансон врезается в металлический лист, материал подвергается сдвиговой деформации на основе собственной пластичности до тех пор, пока поверхность ab пуансона не соприкоснется с поверхностью листа (см. рис. 13a, b). В этот момент в листе не образуются трещины сдвига, а продолжительность этой фазы зависит в основном от пластичности материала и состояния кромки штампа.
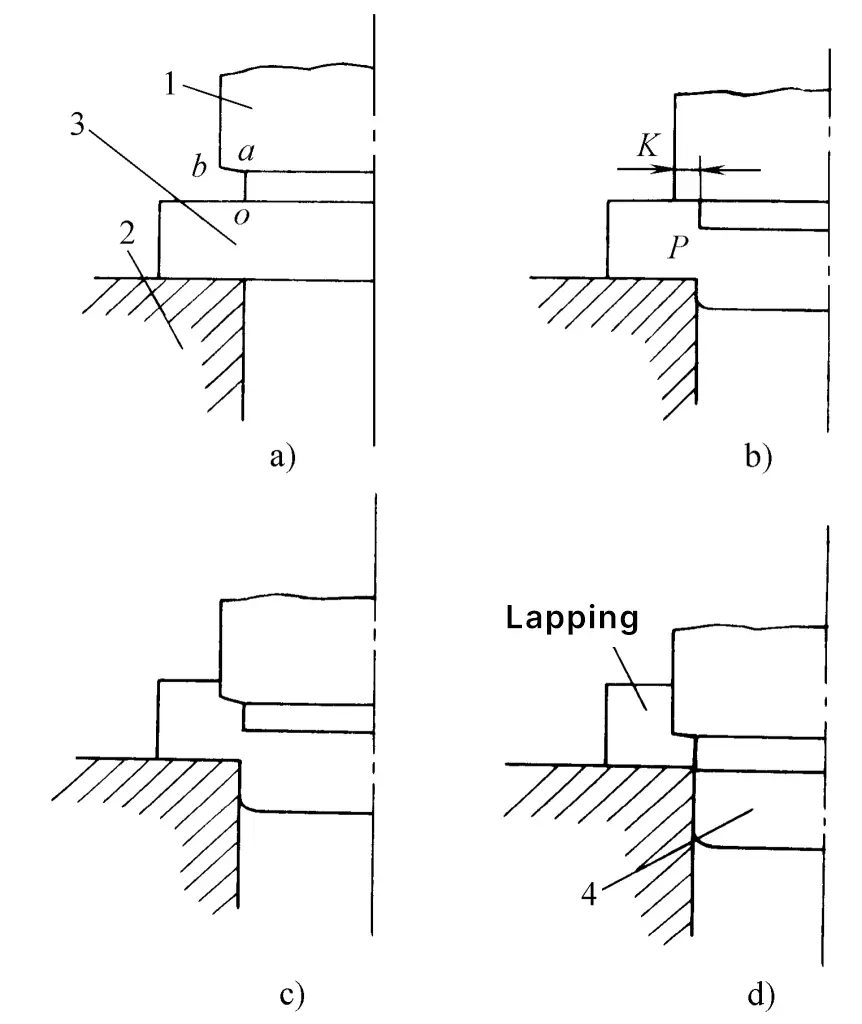
1-Панч
2-Die
3-листовой металл
4-Workpiece
Когда пуансон продолжает вдавливаться, поверхность ab пуансона вдавливается в металлический лист, и сжатый материал создает достаточно большое гидростатическое давление в зоне сдвига P, чтобы повысить пластичность материала, подавить образование трещин сдвига и позволить пластической деформации сдвига продолжаться на протяжении всего изделия. процесс стрижки. Когда торцевая поверхность пуансона входит в отверстие матрицы, точное разделение металлического листа завершается (см. рис. 13c, d).
В вышеупомянутом процессе сдвига соответствующим образом используется присущая материалу пластичность, а затем своевременно прикладывается достаточно большое гидростатическое давление для подавления образования трещин сдвига.
По мере того как поверхность ab пуансона постепенно вдавливается, гидростатическое давление становится все более значительным, компенсируя постепенное снижение пластичности металлического листа в процессе резки. В рабочей части пуансона основная функция секции ao заключается в контроле времени начального увеличения гидростатического давления, в то время как основная функция поверхности ab заключается в контроле величины гидростатического давления. Изменяя свои размеры, они могут адаптироваться к листовым металлам различных характеристик и толщины.
Используя тот же принцип, можно добиться точности штамповки, как показано на рис. 14. В это время отходы штамповки должны выгружаться сверху штампа.
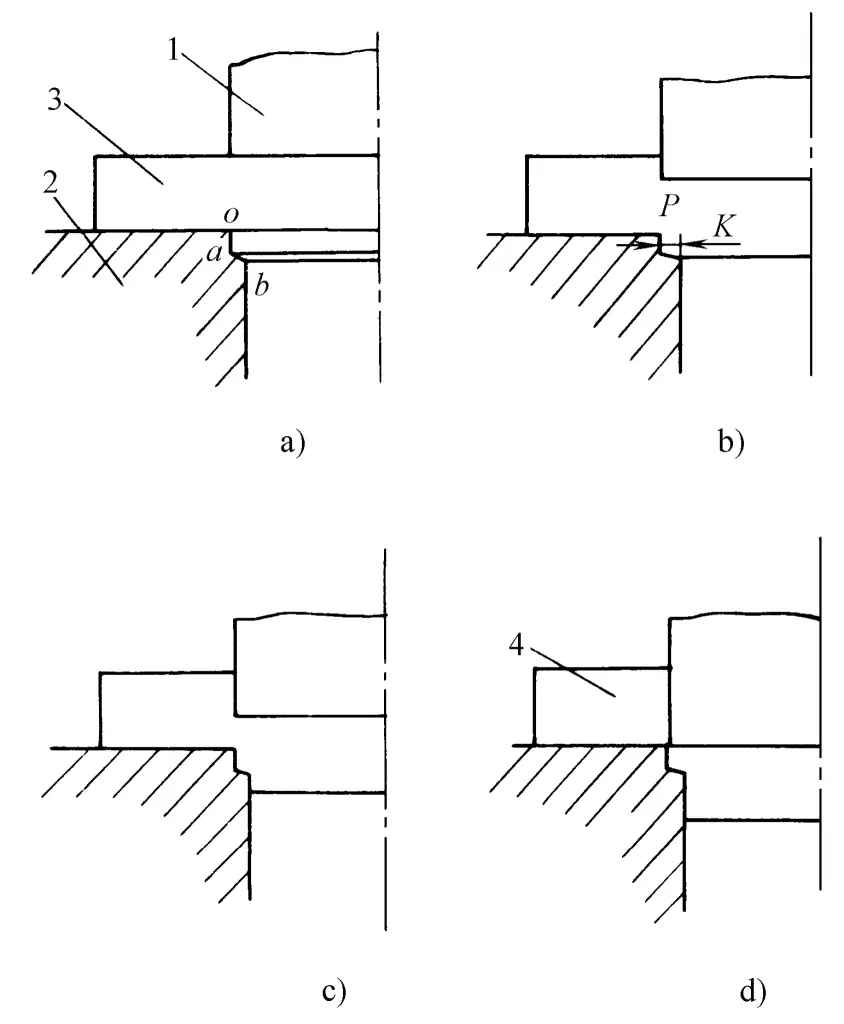
1-Панч
2-Die
3-листовой материал
4-Workpiece
Технический ключ к этому методу заключается в разумном определении формы и размера рабочей части заготовительного пуансона (или вырубного штампа) и выборе рекомендуемых значений в зависимости от различной пластичности материала.
- Длина секции ао составляет (0,15~0,35)т;
- Горизонтальная ширина поверхности ab K=(0.1~0.4)t;
- Угол между поверхностью ab и горизонтальной плоскостью составляет 0°~20°;
- Односторонний зазор между секцией ao пуансона (или матрицы) и матрицей (или пуансоном) составляет 0,01~0,05 мм;
- Радиус кромки заготовительного штампа (или пуансона) составляет 0,05~0,2 мм.
С помощью этого метода были проведены эксперименты с чистой медью, алюминиевым сплавом, латунью, сталью 08, сталью 25 (горячекатаная сталь) и цинковым сплавом с использованием пресс-формы с направляющей пластиной на обычном прессе, и все они позволили получить абсолютно гладкие поверхности среза. Кроме того, для свинцовой латуни, которую трудно точно пробить, этот метод позволяет достичь поверхности среза заготовки почти 0,9t (t - толщина материала).