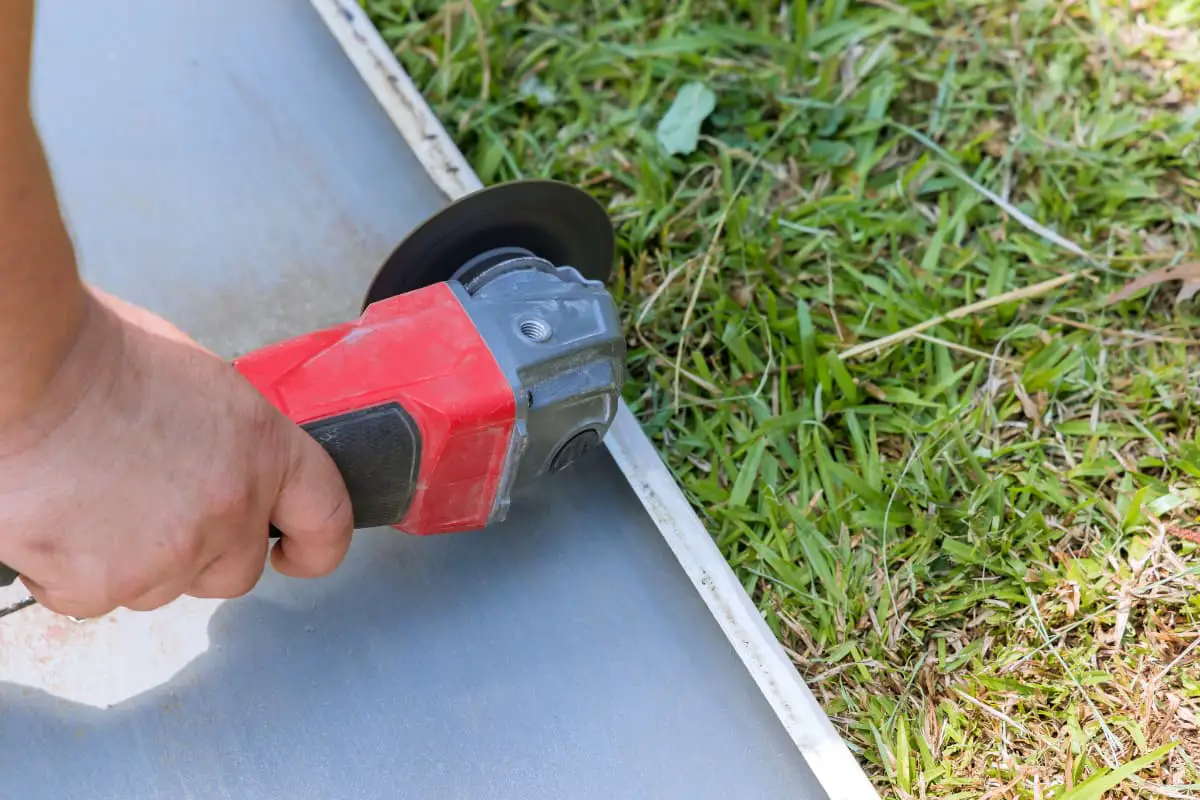
I. Обработка бурения
Сверление - это метод обработки отверстий в заготовке с помощью сверла. При обработке заготовки на сверлильном станке, как правило, заготовка фиксируется на месте, а инструмент вращается (главное движение), перемещаясь при этом в осевом направлении (движение подачи).
1. Характеристики и применение бурения
(1) Характеристики процесса
- Сверло режет в полузакрытом состоянии, с большим съемом металла, что затрудняет удаление стружки.
- При трении выделяется большое количество тепла, что затрудняет отвод тепла и повышает температуру резки.
- Непросто заточить сверло до симметричных режущих кромок, и диаметр обрабатываемого отверстия часто расширяется.
- Экструзия очень сильная, сила резания большая, что легко приводит к холодной закалке стенок отверстия.
- Сверло тонкое, с длинным выступом, плохой жесткостью и склонно к отклонениям при обработке.
- Точность сверления низкая, с классом допуска IT13~IT12, и шероховатость поверхности значение Ra12,5~6,3 мкм.
(2) Диапазон процессов
Технологический диапазон сверления широк. Используя различные инструменты на сверлильном станке, можно выполнить сверление центровых отверстий, сверление, развертывание, развертывание, нарезание резьбы, растачивание и торцевание, как показано на рис. 1. Точность сверления на сверлильном станке невысока, но возможно обрабатывать отверстия с высокими требованиями к точности (IT8~IT6, шероховатость поверхности Ra1,6~0,4 мкм) посредством сверления-расточки-расточки, а также обрабатывать отверстия с позиционными требованиями с помощью приспособлений.
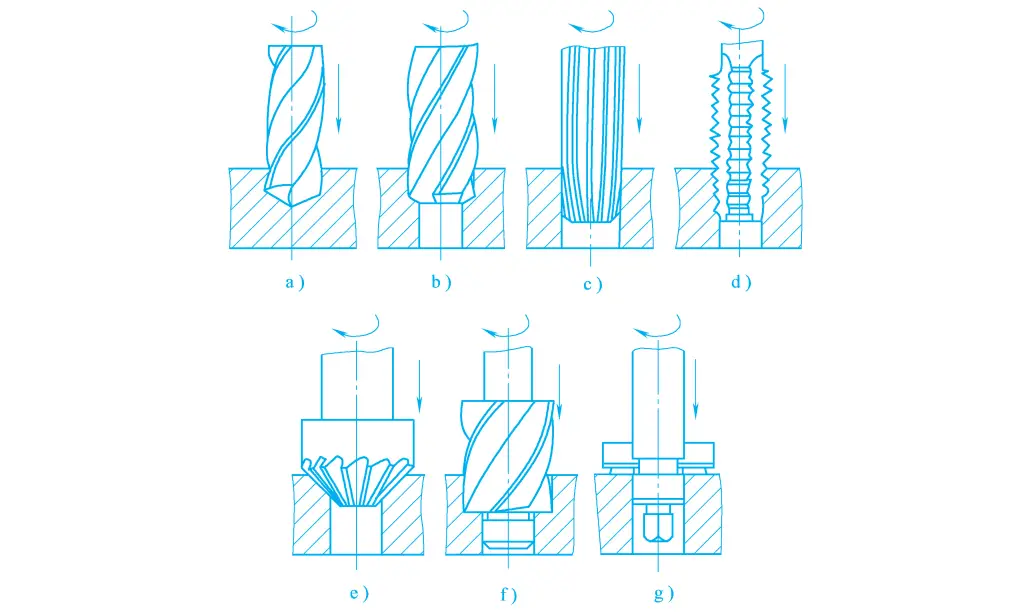
a) Бурение
б) Развертывание
в) Развертывание
г) Резьба
e)、f) Отверстие с заглубленной головкой из гафния
g) Плоскость из гафния
2. Сверлильный станок
К основным типам сверлильных станков относятся настольные, вертикальные, радиальные, специализированные и т.д. Ниже представлены два наиболее широко используемых типа сверлильных станков.
(1) Вертикальная сверлильная машина
Вертикально-сверлильные станки делятся на три серии: цилиндрические вертикально-сверлильные станки, вертикально-сверлильные станки с квадратной колонной и регулируемые многоосевые вертикально-сверлильные станки. На рис. 2 показан вертикально-сверлильный станок с квадратной колонной, шпиндель которого расположен вертикально, его положение фиксировано в горизонтальном направлении, и положение обрабатываемого отверстия должно быть найдено путем перемещения заготовки.
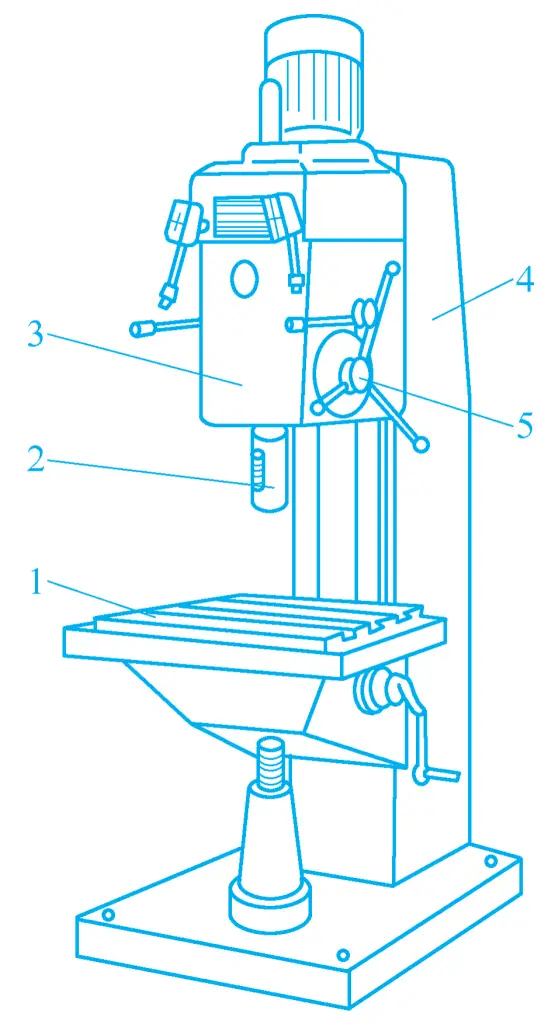
1-рабочий стол
2-Главный шпиндель
3-Головной убор
4-колонна
5-Операционный механизм
Шпиндельная коробка 3 и рабочий стол 1 установлены на вертикальных направляющих квадратной колонны 4 и могут быть отрегулированы по положению для размещения заготовок разной высоты. После регулировки их взаимное положение не изменяется в процессе обработки. Помимо основного вращательного движения, шпиндель также перемещается в осевом направлении для подачи.
С помощью механизма управления 5, установленного на шпиндельной коробке 3, можно быстро поднимать и подавать шпиндель вручную, а также включать и выключать моторизованную подачу. Изменение направления вращения шпинделя происходит за счет прямого и обратного вращения двигателя. Данный тип сверлильного станка имеет низкую производительность и в основном используется для штучной и мелкосерийной обработки средних и мелких заготовок.
(2) Радиально-сверлильный станок
При сверлении отверстий в больших заготовках желательно, чтобы заготовка оставалась неподвижной, а шпиндель сверлильного станка мог быть установлен в любое положение. Для этого необходимо использовать радиальный сверлильный станок, на рисунке 3a показана внешняя форма радиального сверлильного станка. Основание 1 оснащено колонной, которая разделена на два слоя: внутренняя колонна 2 закреплена на основании 1, а внешняя колонна 3 опирается на подшипники качения и может вращаться вокруг внутреннего слоя, как показано на рисунке 3b. Рычаг 4 может перемещаться вверх и вниз вдоль внешней колонны 3, а шпиндельная коробка 5 может перемещаться горизонтально вдоль направляющей рычага.
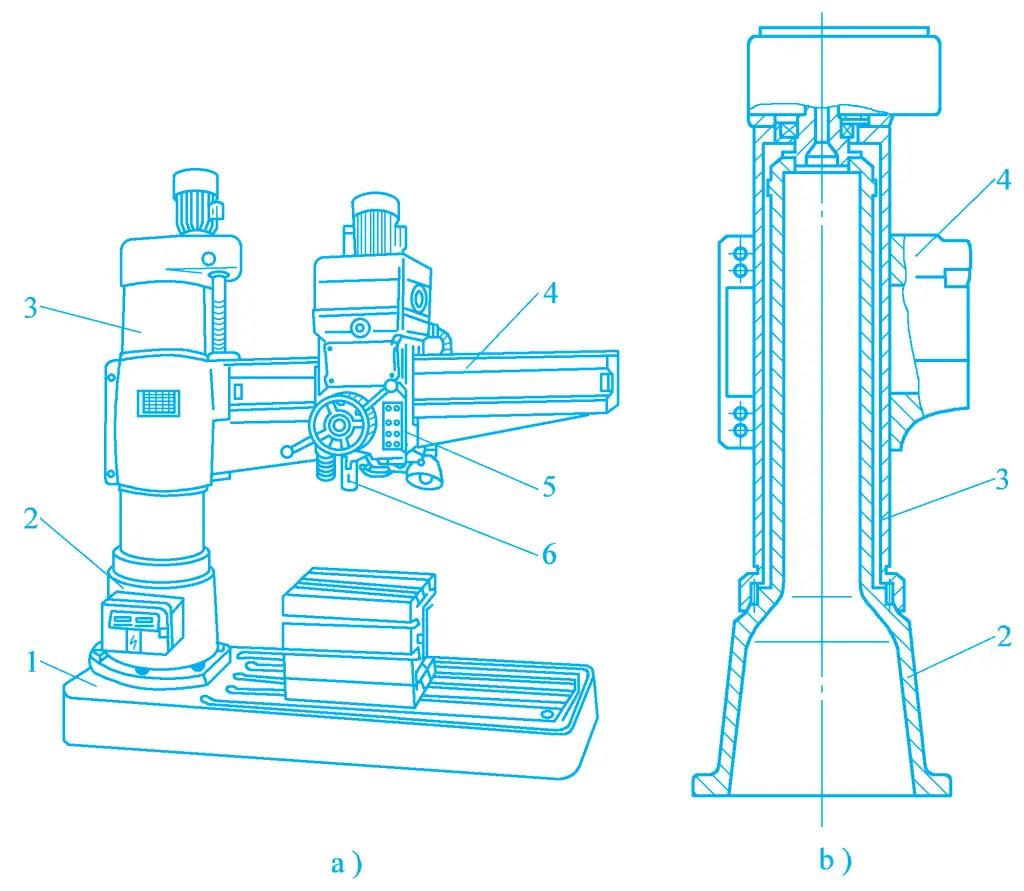
a) Внешняя форма
б) Структура колонн
1-База
2-Внутренняя колонка
3-Внешняя колонна
4-арм
5-шпиндельная коробка
6-шпиндель
Таким образом, положение шпинделя 6 может быть удобно отрегулировано. Чтобы предотвратить горизонтальное перемещение шпинделя во время обработки, радиально-сверлильный станок оснащен зажимными механизмами между шпиндельной коробкой и рычагом, внешней колонной и внутренней колонной, а также рычагом и внешней колонной. Заготовка может быть зажата на рабочем столе, или, если заготовка большая, рабочий стол может быть снят, а заготовка непосредственно установлена на станине. Радиально-сверлильные станки широко используются для обработки крупных и средних заготовок.
3. Бурение
Сверла, используемые в сверлильных операциях, представляют собой режущие инструменты фиксированного размера, которые по конструктивным особенностям и назначению можно разделить на плоские, спиральные, глубокие и центровые, с диаметром сверления от 0,1 до 100 мм и широким диапазоном глубин сверления. Сверлильные операции широко используются для черновой обработки отверстий, а также могут применяться для окончательной обработки некритичных отверстий.
Спиральное сверло - самое распространенное сверло в производстве, его применение описано ниже.
(1) Состав спирального сверла
Стандартное спиральное сверло, как показано на рисунке 4, состоит из хвостовика, шейки и рабочей части.
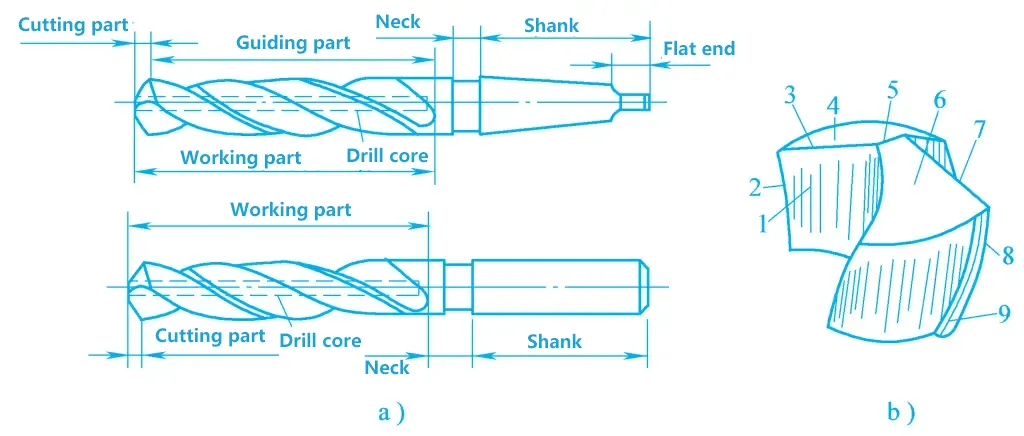
a) Общая конструкция сверла
b) Режущая часть сверла
1-Фронт
2, 8 - вторичная режущая кромка (скошенная кромка)
3, 7 - главная режущая кромка
4, 6 - главная задняя часть
5-Крестовая кромка
9-Вторичный тыл
1) Хвостовик.
Хвостовик - это удерживающая часть спиральной дрели, которая может быть прямой или конической и используется для передачи крутящего момента при сверлении. Прямые хвостовики используются в основном для небольших спиральных сверл диаметром менее 12 мм, которые обычно крепятся на шпинделе с помощью сверлильного патрона.
Конические хвостовики используются для спиральных сверл большего диаметра, которые могут быть вставлены непосредственно в коническое отверстие шпинделя или через коническую втулку в коническое отверстие шпинделя. Плоский хвостовик сверла с коническим хвостовиком может использоваться для передачи крутящего момента и удобного извлечения сверла.
2) Шея.
Паз шейки - это паз для втягивания при заточке хвостовика сверла, на дне которого выгравированы технические характеристики и заводская маркировка спирального сверла.
3) Рабочая часть.
Рабочая часть спиральной дрели состоит из режущей и направляющей частей.
Режущая часть выполняет работу по резанию и состоит из двух передних частей, главной задней части, вспомогательной задней части, главной режущей кромки, вспомогательной режущей кромки и поперечной кромки. Поперечная кромка - это кромка, образованная пересечением двух главных задних кромок, а вспомогательная задняя - это две кромочные полосы спирального сверла, которые работают напротив стенки отверстия (обрабатываемой поверхности) заготовки.
Направляющая часть служит в качестве направляющей при врезании режущей части в заготовку, а также является запасной шлифовальной частью режущей части. Чтобы уменьшить трение между направляющей частью и стенкой отверстия, ее внешний диаметр шлифуется с обратным конусом. В то же время для поддержания достаточной прочности спирального сверла необходимо наличие коронки, выполненной в виде положительного конуса в направлении хвостовика сверла.
(2) Методы сверления спиральным сверлом
Существует шесть способов сверления с помощью спиральной дрели:
1) Сверление в отмеченном месте.
В начале бурения необходимо провести пробное бурение, которое заключается в сверлении неглубокого отверстия (около 1/4 диаметра отверстия) с кончиком сверла на центральной отметке отверстия, затем проверить, правильно ли расположен центр отверстия, и своевременно внести коррективы, если обнаружены отклонения.
При сверлении сквозных отверстий уменьшайте скорость подачи, когда отверстие вот-вот прорвется, чтобы улучшить качество сверления и предотвратить поломку сверл малого диаметра. При сверлении глухих отверстий уделяйте внимание контролю глубины сверления, как правило, путем регулировки ограничителя глубины на сверлильном станке или нанесения меток и т. д.
2) Сверление глубоких отверстий.
Когда глубина отверстия превышает в три раза его диаметр, часто втягивайте сверло, чтобы своевременно удалять стружку и охлаждать его, иначе это может привести к забиванию стружкой, чрезмерному износу или даже поломке сверла, что повлияет на качество отверстия.
3) Сверление твердых материалов.
Скорость сверления не должна быть слишком высокой, ручная подача должна быть равномерной, особенно когда отверстие вот-вот прорвется, обратите внимание на соответствующее снижение скорости и подачи.
4) Сверление отверстий большего диаметра.
Если диаметр отверстия большой (обычно более 30 мм), его следует сверлить в два этапа. Сначала просверлите отверстие сверлом, диаметр которого в 0,6~0,8 раза больше диаметра отверстия, а затем просверлите до нужного диаметра. Это не только поможет уменьшить осевое сопротивление сверла, но и улучшит качество сверления.
5) Сверление отверстий в высокоэластичных пластиковых материалах.
При сверлении материалов с хорошей пластичностью и высокой вязкостью разрушение стружки часто становится серьезной проблемой, влияющей на процесс обработки, например, стружка забивает сверло, влияет на качество заготовки; не способствует проникновению смазочно-охлаждающая жидкость в зону резания, что сокращает срок службы бурового долота, влияет на безопасность операторов и технологической системы и т.д.
При возникновении таких проблем их можно устранить путем изменения геометрического угла сверла, уменьшения скорость резкиувеличение скорости подачи, своевременное втягивание сверла для удаления стружки и охлаждения и т.д.
6) Сверление на наклонной поверхности.
При бурении на склоне радиальная сила, возникающая под действием склона, часто вызывает отклонение бурового долота, что приводит к перекосу оси отверстия (см. Рисунок 5a) или даже к поломке бурового долота. Чтобы предотвратить отклонение сверла, на склоне перед сверлением можно рассверлить плоскость (см. Рисунок 5b) или использовать специальную втулку для направления сверла, чтобы повысить жесткость сверла и точность работы (см. Рисунок 5c).
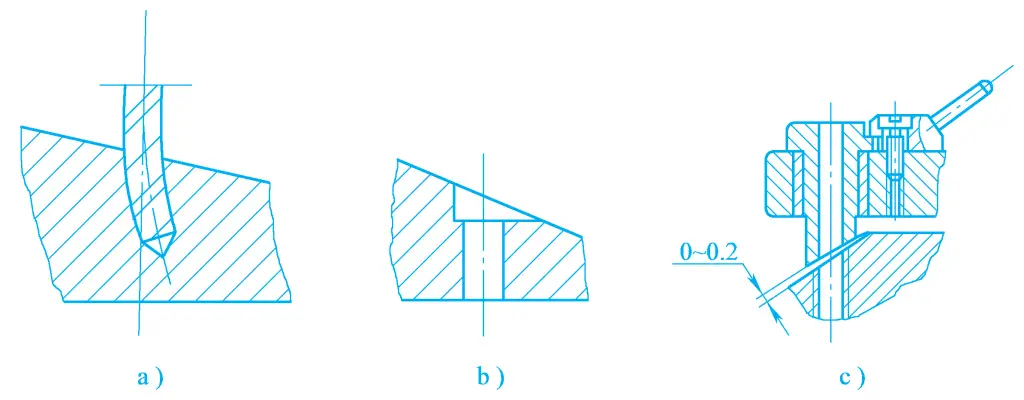
При сверлении сверло необходимо охлаждать и смазывать, при этом для стальных деталей часто используется эмульсия или машинное масло, для чугунных - керосин, а для цветных металлы часто с использованием эмульсии или керосина.
4. Развертывание и растачивание
(1) Развертывание
Развертывание обычно используется для увеличения отверстий, которые были отлиты, выкованы или просверлены. Развертывание может использоваться как предварительный процесс обработки перед развертыванием или шлифованием отверстий, или как окончательный процесс обработки отверстий с низкими требованиями к точности, обычно используемый для отверстий диаметром 10~100 мм. Припуск на обработку при развертывании составляет 0,5~4 мм.
К распространенным инструментам для развертывания относятся спиральные сверла и развертки. Спиральные сверла обычно используются для развертывания заготовок, а развертки - для полуфинишной обработки отверстий при больших объемах производства.
Структура развертки показана на рисунке 6. Развертка похожа на спиральное сверло, но основное отличие заключается в том, что главная режущая кромка часто имеет 3 или 4 лезвия, поэтому лучше направляется; главная режущая кромка не проходит через центр, без поперечного лезвия, что позволяет избежать негативного влияния поперечного лезвия на резание; спиральная канавка мельче, а диаметр сердечника сверла больше, поэтому прочность корпуса инструмента выше, а жесткость лучше, что позволяет увеличить объем резки при развертывании.
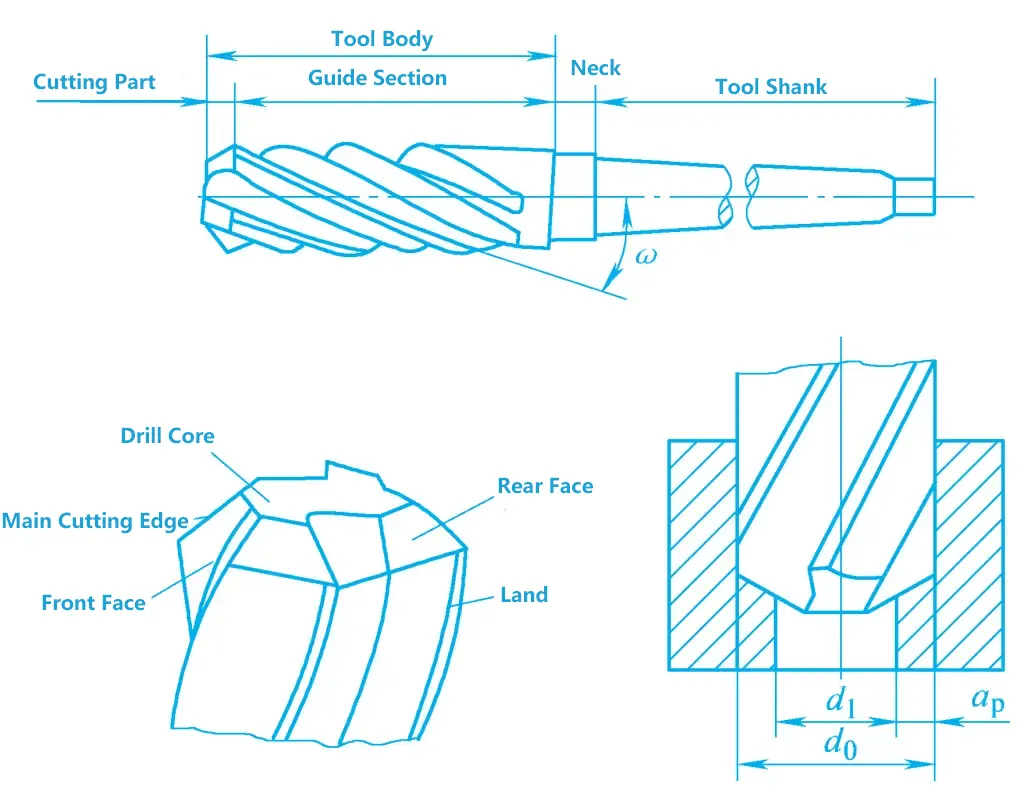
Благодаря вышеперечисленным характеристикам развертки качество обработки при развертывании выше, чем при сверлении, а производительность выше. Развертка оказывает определенное корректирующее воздействие на отклонение оси литых отверстий, просверленных отверстий и других предварительно обработанных отверстий. Класс допуска размеров при развертывании обычно составляет около IT10, а значение шероховатости поверхности может достигать Ra6.3~3.2μm.
При развертывании других материалов, за исключением чугуна и бронзы, следует использовать смазочно-охлаждающую жидкость, причем чаще всего применяется эмульсия.
(2) Скука
Под растачиванием понимается обработка цилиндрических потайных отверстий, конических потайных отверстий и торцевых поверхностей бобышек в предварительно обработанных отверстиях. Инструменты, используемые для растачивания, называются расточными сверлами и обычно изготавливаются из быстрорежущей инструментальной стали.
В расточных сверлах для обработки торцов бобышек большого диаметра могут использоваться перетачиваемые или сменные вставки из твердых сплавов, закрепляемые на корпусе инструмента пайкой или механическим зажимом. Направляющая стойка расточного сверла обеспечивает соосность расточенного потайного отверстия с исходным отверстием.
5. Развертка
Развертывание - это процесс использования развертки для снятия небольшого слоя металла со стенки отверстия в заготовке с целью повышения точности размеров и уменьшения шероховатости поверхности. Она подходит для полуфинишной и финишной обработки отверстий, а также может использоваться в качестве предварительного процесса обработки перед шлифованием или хонингованием.
Поскольку припуск на резание при развертывании невелик, класс допуска размеров после развертывания обычно составляет IT9~IT7, а шероховатость поверхности - Ra3.2~1.6μm, при тонком развертывании класс допуска размеров достигает IT6, а шероховатость поверхности - Ra1.6~0.4μm.
Развертки не подходят для обработки закаленной стали и материалов со слишком высокой твердостью. Развертки - это инструменты фиксированного размера, подходящие для обработки отверстий среднего и малого диаметра. Перед развертыванием заготовка должна пройти такие процессы, как сверление и растачивание (развертывание).
(1) Расширители
В зависимости от способа использования развертки делятся на ручные и машинные, как показано на рисунке 7. Ручные развертки имеют прямой хвостовик с более длинной рабочей частью, обеспечивающей хорошее ведение, что может предотвратить перекос развертки при ручном развертывании. Машинные развертки часто имеют конический хвостовик, который может быть установлен на сверлильных, токарных и расточных станках для развертывания.
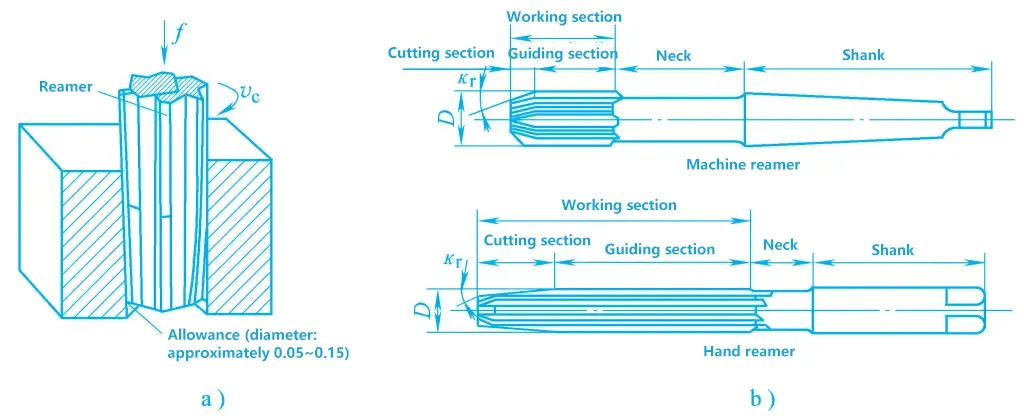
a) Развертка
б) Расширители
Рабочая часть развертки включает в себя режущую и калибрующую части. Режущая часть имеет коническую форму и выполняет основную работу по резанию. Калибровочная часть используется для калибровки диаметра отверстия, сглаживания стенки отверстия и направления, с очень маленьким обратным конусом в задней части калибровочной части для уменьшения трения со стенкой отверстия и предотвращения расширения диаметра отверстия после развертывания.
Расширители имеют режущие зубья 6~12, относительно неглубокие стружечные канавки и большой диаметр коронки сверла, поэтому жесткость и направление расширителей даже лучше, чем у расширительных сверл.
(2) Вопросы, на которые следует обратить внимание при развертывании
- Припуск на развертывание должен быть умеренным. Слишком большой припуск на развертывание может привести к увеличению диаметра развертки из-за большого количества тепла резания, увеличивая диаметр отверстия; стружка легко забивается, режущая жидкость не может легко попасть в зону резания, поверхность отверстия становится более шероховатой, и развертка легко изнашивается; слишком маленький припуск не может удалить следы инструмента, оставленные в нижнем отверстии, и шероховатость поверхности не соответствует требованиям. Припуск на грубое развертывание обычно составляет 0,15~0,35 мм, а припуск на тонкое развертывание - 0,05~0,15 мм.
- При развертывании следует использовать более низкую скорость резания и меньшую подачу.
- Разумно используйте смазочно-охлаждающую жидкость.
- Чтобы предотвратить отклонение оси развертки от оси главного шпинделя, вызывающее перекос оси отверстия, увеличение диаметра отверстия и другие явления, между разверткой и главным шпинделем следует использовать плавающее соединение. При использовании плавающего соединения развертка не может исправить отклонение оси нижнего отверстия, поэтому точность позиционирования отверстия должна быть обеспечена предыдущим процессом.
- В процессе развертывания нельзя поворачивать развертку, чтобы избежать застревания стружки в развертке и царапания стенок отверстия, что может привести к сколу развертки.
- После затупления развертку следует своевременно затачивать. Как правило, затачивается только задняя часть резца, а шлифовальный камень используется для шлифовки стыка режущей и калибровочной частей развертки на небольшой радиус, чтобы сформировать переходное лезвие, чтобы повысить срок службы развертки и качество поверхности при обработке.
II. Расточная обработка
Расточная обработка - это метод обработки существующих отверстий с помощью расточного инструмента.
1. Характеристики и технологический диапазон расточки
(1) Характеристики расточки
- Расточная обработка отличается высокой гибкостью и адаптивностью. Помимо обработки отверстий и систем отверстий на расточном станке можно обрабатывать внешние окружности, торцы и т. д. Размер обработки может быть большим или маленьким, что подходит для различных типов производства и требований к точности.
- Расточная обработка требует высокой технической квалификации оператора. Обеспечение точности размеров и шероховатости поверхности заготовки зависит не только от используемого оборудования, но и главным образом от технического уровня рабочих. В то же время время наладки станков и инструментов также увеличивается. При растачивании в работе участвует меньшее количество режущих кромок, поэтому производительность расточной обработки в целом ниже.
- Конструкция расточного инструмента проста, легко затачивается и имеет низкую стоимость.
- Растачивание позволяет исправить погрешность положения оси отверстия, полученную в предыдущем процессе, обеспечивая точность позиционирования отверстия.
(2) Технологический диапазон расточки
Технологический диапазон расточной обработки широк. На станке можно растачивать отдельные отверстия или системы отверстий, выполнять протяжку, фрезеровать плоскости, растачивать глухие отверстия и растачивать торцы, как показано на рис. 8. Крупные заготовки сложной формы, такие как основания, коробки и кронштейны, особенно системы отверстий с требованиями к точности позиционирования, часто обрабатываются на расточных станках с использованием координатных устройств или расточных шаблонов.
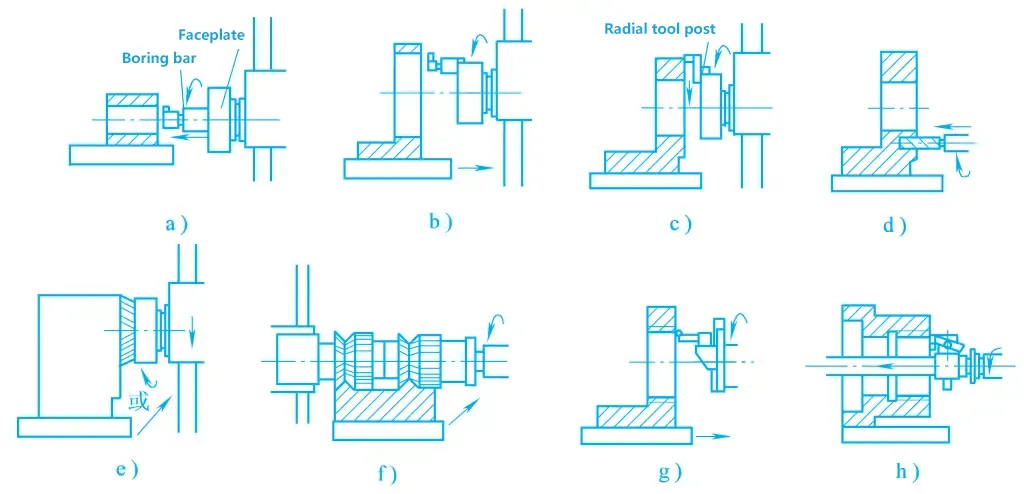
a) Сверление небольших отверстий
б) Сверление больших отверстий
c) Расточка торцевых поверхностей
г) Бурение
e) Фрезерные плоскости
f) Фрезерование комбинированных поверхностей
g) Расточные резьбы
h) Расточка глубоких отверстий под резьбу
При растачивании уровень допуска размеров составляет IT7~IT6, точность расстояния между отверстиями может достигать 0,015 мм, а шероховатость поверхности - Ra1,6~0,8 мкм. При оснащении различными приспособлениями, специальными расточными линейками и другими устройствами, расточной станок может также обрабатывать канавки, резьбу, конические отверстия и сферические поверхности.
2. Расточные станки
Расточные станки предназначены для обработки имеющихся отверстий на заготовках больших и средних размеров, особенно подходят для обработки систем отверстий с жесткими требованиями к расстоянию между отверстиями и точности позиционирования, распределенных по одной или разным поверхностям. Главное движение рабочего времени инструмента - вращение, а движение подачи может осуществляться инструментом или заготовкой, в зависимости от типа станка и условий обработки.
Расточные станки можно разделить на горизонтально-расточные станки, координатно-расточные станки, прецизионные расточные станки и т.д.
(1) Горизонтально-расточной станок
Горизонтально-расточной станок состоит из станины, шпиндельной коробки, рабочего стола, поворотного стола, передней и задней колонн, как показано на рис. 9. Шпиндельная коробка установлена на вертикальной направляющей передней колонны и может перемещаться вверх и вниз по направляющей. Шпиндельная коробка содержит компоненты шпинделя, поворотный стол, механизмы передачи главного движения и движения подачи, а также рабочие механизмы. Основным движением станка является вращение шпинделя или поворотного стола.
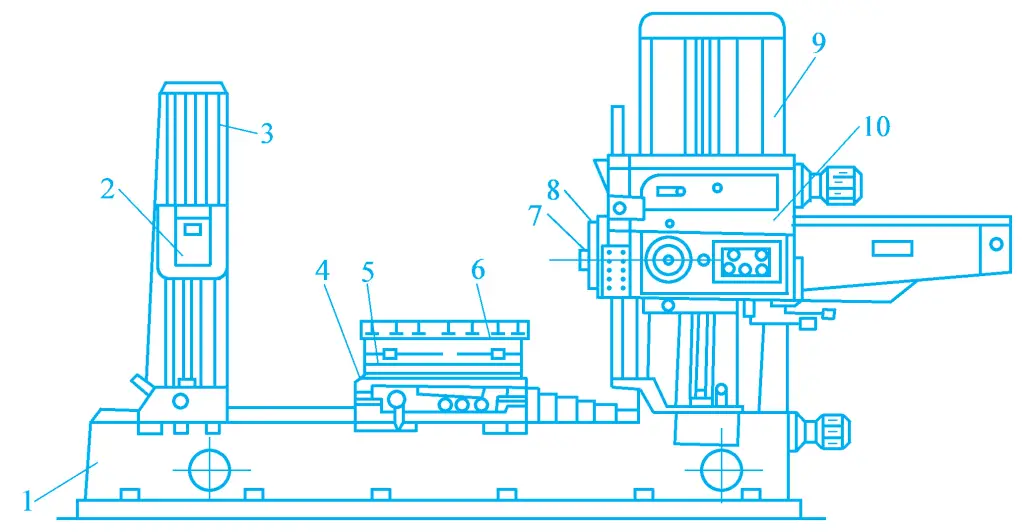
1-Bed
2-Опорная рама
3-Задняя колонка
4-Нижнее скользящее основание
5 Верхнее основание салазок
6-Рабочий стол
7-шпиндель
8-Поворотный стол
9-Фронтальная колонка
10-шпиндельная коробка
В зависимости от требований к обработке, расточной вал может совершать осевое движение подачи или радиальный суппорт инструмента на поворотном столе может совершать радиальное движение подачи, вращаясь вместе с поворотным столом. Устройство рабочего стола состоит из нижнего основания суппорта, верхнего основания суппорта и рабочего стола. Рабочий стол может перемещаться в продольном направлении вдоль направляющей станины с нижним скользящим основанием, или может перемещаться в поперечном направлении вдоль верхней направляющей нижнего скользящего основания с верхним скользящим основанием.
Рабочий стол также может вращаться вокруг вертикальной оси по круговой направляющей верхнего основания суппорта, что облегчает обработку отверстий, расположенных на разных поверхностях. На вертикальной направляющей задней стойки расположена опорная рама для поддержки более длинного расточного прутка, чтобы увеличить жесткость расточного прутка. Опорная рама может перемещаться вверх и вниз по направляющей задней стойки для сохранения соосности с расточным валом, а задняя стойка может регулироваться в продольном направлении в зависимости от длины расточного прутка.
Технологический диапазон горизонтально-расточных станков очень широк, а типичные методы обработки показаны на рисунке 10.
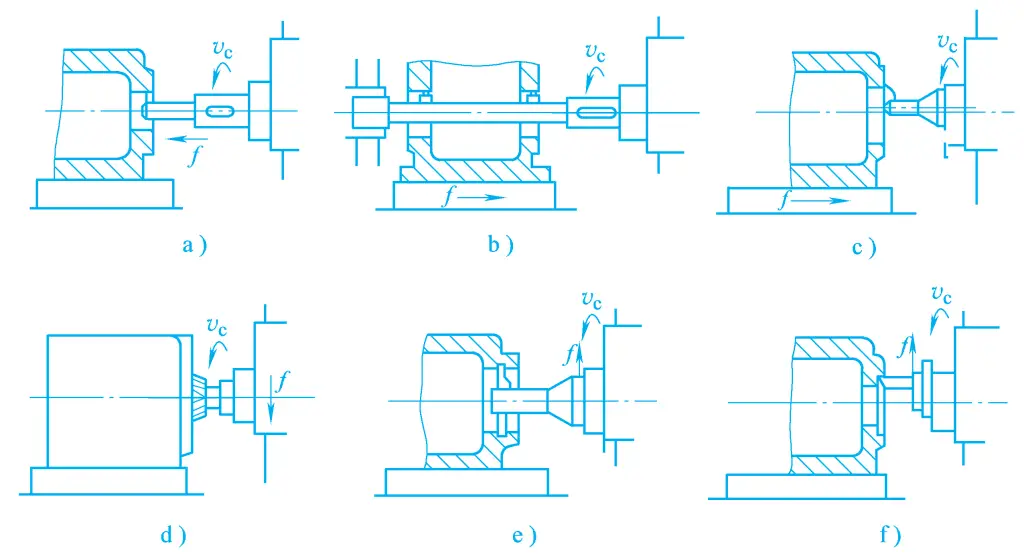
(2) Сверлильный станок
Расточной станок - это высокоточный расточной станок, обладающий хорошей жесткостью и виброустойчивостью, а также оснащенный прецизионным координатно-измерительным устройством для подвижных частей, таких как рабочий стол и шпиндельная коробка, что позволяет точно позиционировать заготовки и инструменты. Поэтому точность размеров и геометрическая точность обработки на расточном станке очень высоки.
В основном используется для обработки точных отверстий, систем отверстий и деталей пресс-форм в условиях единичного и мелкосерийного производства, а также может применяться для точной обработки различных типов коробок, корпусов цилиндров и корпусов машин в серийном производстве. По своей структуре расточные станки делятся на одностоечные, двухстоечные и горизонтальные.
1) Одноколонный сверлильный станок
Как показано на рис. 11, шпиндельная коробка установлена на вертикальной направляющей колонны и может регулироваться вверх и вниз для размещения заготовок различной высоты. Координатное положение расточного отверстия определяется продольным перемещением рабочего стола по направляющей седла станины и поперечным перемещением седла станины по направляющей станины. Во время растачивания движение подачи завершается продольным или поперечным перемещением рабочего стола.
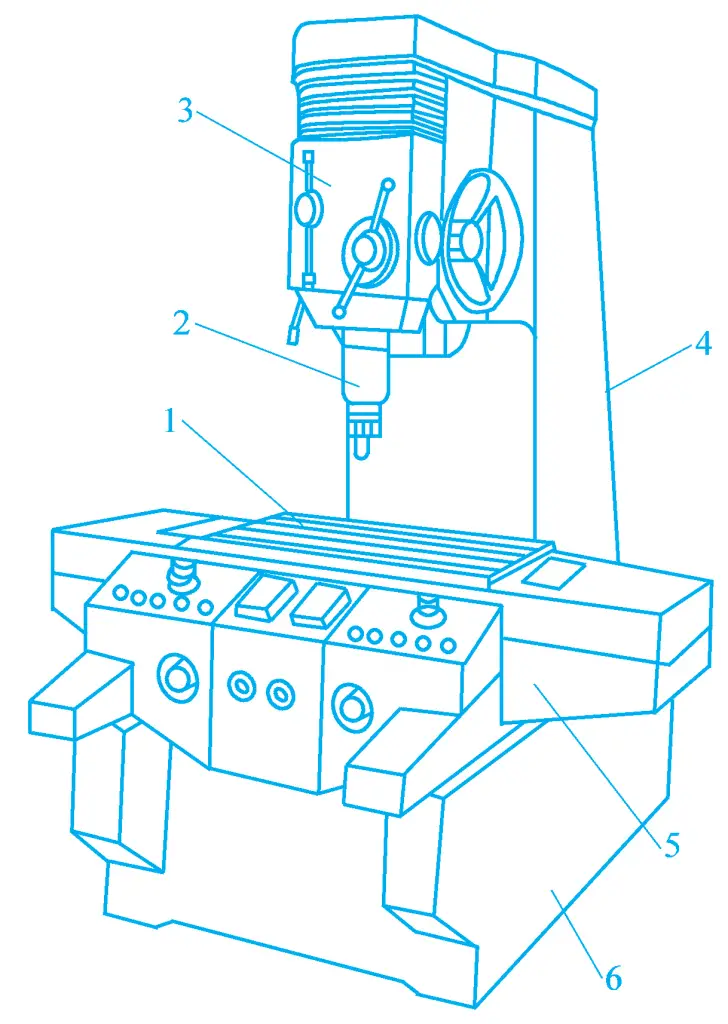
1-рабочий стол
2-Главный шпиндель
3-Головной убор
4-колонна
5-Bed saddle
6-местный
Этот тип станков имеет три открытые стороны рабочего стола, что удобно для работы, но шпиндельная коробка консольно закреплена на колонне. Чем больше размер рабочего стола, тем дальше осевая линия шпинделя от колонны, что влияет на жесткость и точность обработки станка. Поэтому станки этого типа обычно имеют средние или малые размеры (ширина рабочего стола менее 630 мм).
2) Двухколонный расточной станок
Как показано на рис. 12, расточной станок состоит из двух колонн, верхней балки и станины, образующих портальную раму с хорошей жесткостью. Шпиндельная коробка установлена на поперечной балке, которая может регулироваться вверх и вниз по направляющим колонн, а координатное положение расточного отверстия определяется перемещением шпиндельной коробки по направляющим поперечной балки и перемещением рабочего стола по направляющим станины. Двухстоечные расточные станки обычно относятся к крупным или средним станкам.
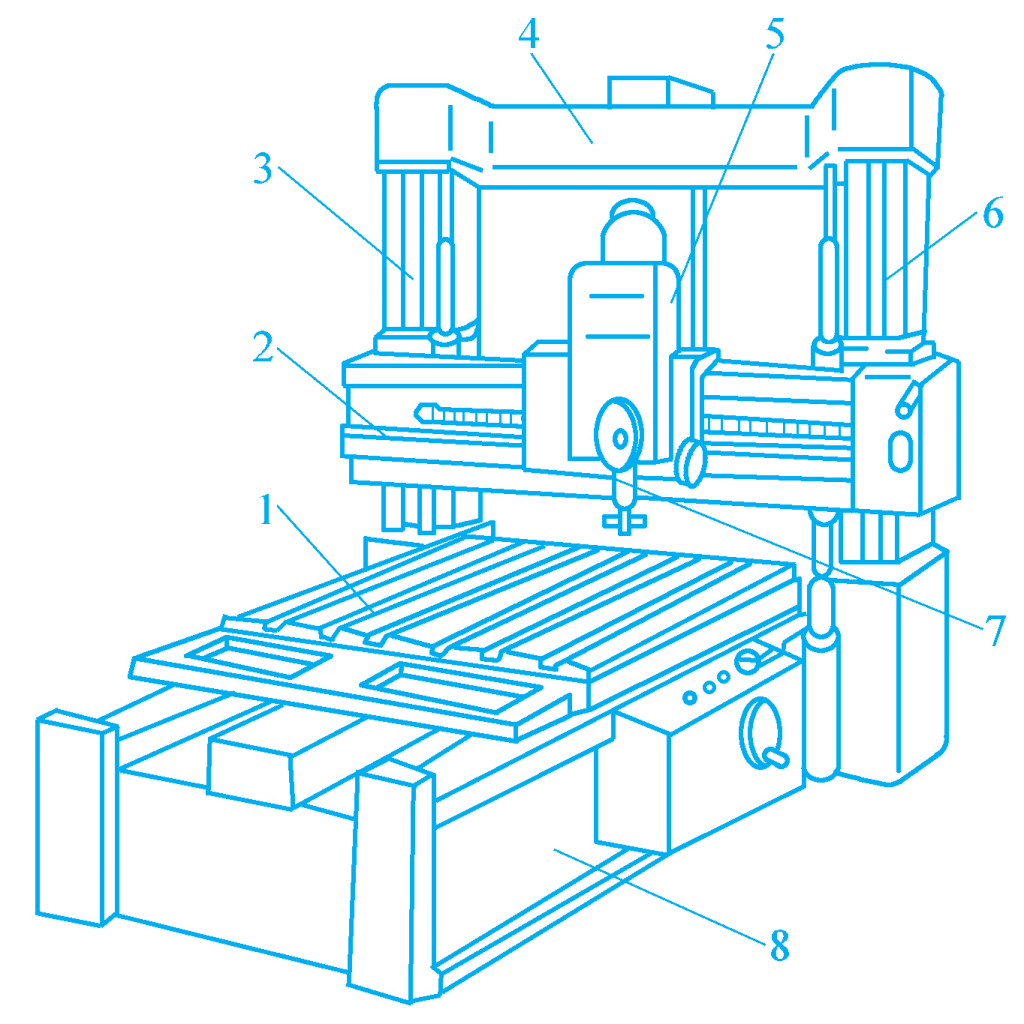
1-рабочий стол
2-поперечная балка
3, 6-колонна
4-Топочная балка
5-шпиндельная коробка
7-шпиндель
8-местный
3) Горизонтальный расточной станок
Как показано на рис. 13, конструктивная особенность этого типа расточного станка заключается в горизонтальном расположении шпинделя. Рабочий стол состоит из нижнего основания суппорта, верхнего основания суппорта и поворотного рабочего стола, который может точно индексироваться. Координаты растачивания определяются продольным перемещением нижнего основания суппорта по направляющей станины и вертикальным перемещением шпиндельной коробки по направляющей колонны.
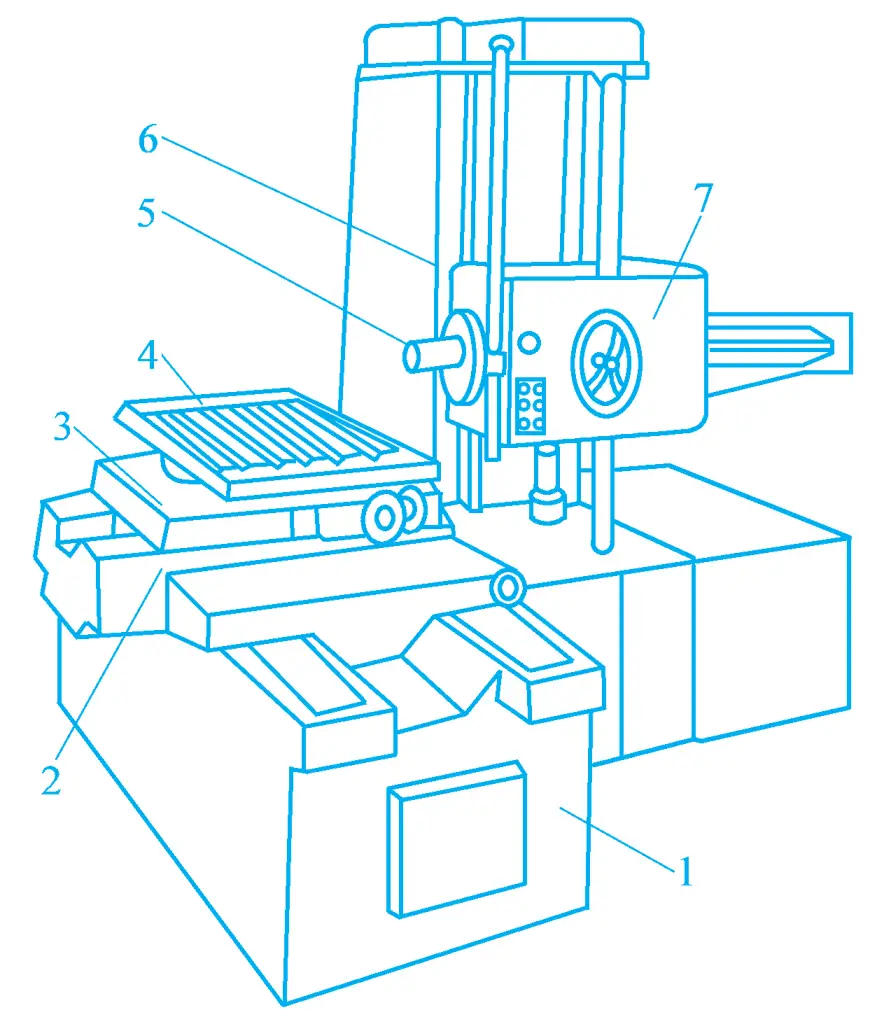
1-Bed
2-Нижняя скользящая база
3 Верхнее основание горки
4-поворотный рабочий стол
5 Главный шпиндель
6-колонна
7-шпиндельная коробка
При обработке отверстий движение подачи может осуществляться за счет осевого перемещения шпинделя или движения верхнего основания суппорта. Горизонтальный координатно-расточной станок имеет хорошую производительность, высота заготовки обычно не ограничена, и ее удобно зажимать. Используя индексирующее движение рабочего стола, можно выполнять разнонаправленную обработку отверстий и плоскостей за один зажим заготовки.
(3) Прецизионный расточной станок
Прецизионный расточной станок - это высокоскоростной расточной станок, который в прошлом назывался алмазным расточным станком, поскольку в качестве инструментального материала использовался алмаз. Как показано на рис. 14, сейчас в качестве инструментального материала используется твердый сплав, обычно используются более высокие скорости, меньшая величина обратного резания и величина подачи для резания, что приводит к более высокой точности обработки, поэтому он называется прецизионным расточным станком. В основном он используется для обработки отверстий средней и малой точности в серийном или массовом производстве.
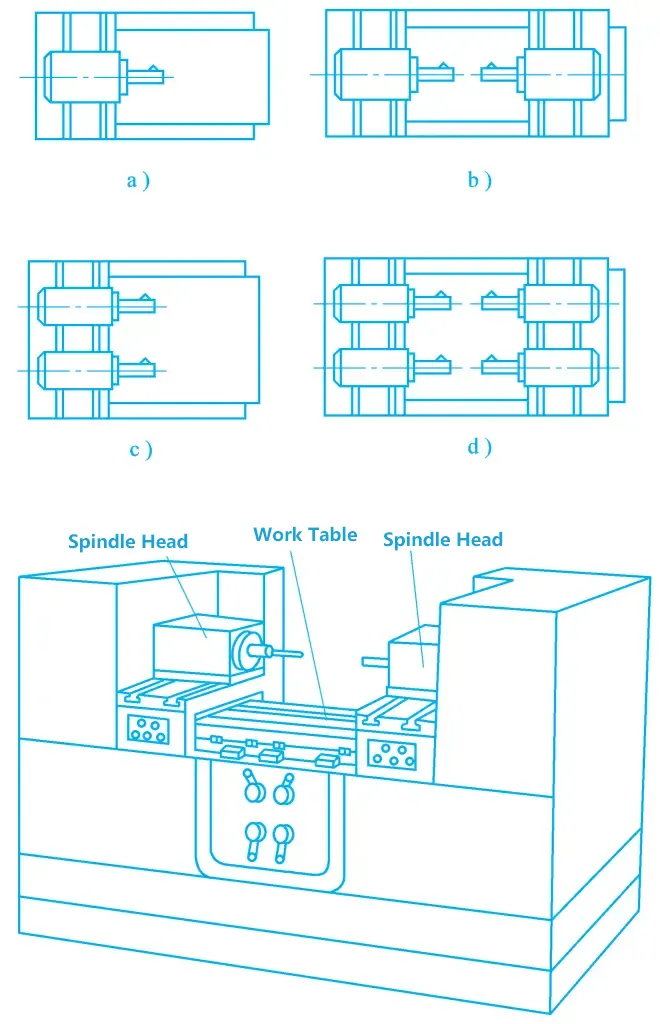
a) Односторонняя одноосная
b) Односторонняя двойная ось
c) Односторонняя двойная ось
г) Двухсторонняя четырехосевая
3. Расточной инструмент
Распространенные расточные инструменты делятся на однолезвийные, двухлезвийные и многолезвийные, а их строение и характеристики представлены ниже.
(1) Однолезвийный расточной инструмент
Большинство однолезвийных расточных инструментов имеют регулируемую конструкцию, показанную на рис. 15, где винт 3 используется для регулировки размера, а винт 2 - для фиксации. У однолезвийных расточных инструментов, используемых на токарных станках, головка расточного инструмента и стержень инструмента часто выполнены как единое целое. Размер поперечного сечения (круглое или квадратное) и длина расточного стержня зависят от диаметра и длины отверстия, которые могут быть выбраны в соответствии с соответствующими книгами по инструментам или техническими стандартами.

a) Инструмент для растачивания несквозных отверстий
b) Инструмент для растачивания сквозных отверстий
1-насадка
2-Затяжной винт
3 - Регулировочный винт
4-Расточной стержень
Регулируемая структура однолезвийного расточного инструмента позволяет перемещать головку инструмента только в одном направлении. Если головка инструмента слишком сильно выдвигается во время регулировки, ее необходимо вручную втягивать, что иногда требует многократного повторения для настройки на требуемый размер. Таким образом, эффективность низкая, а точность регулировки не очень высокая, что подходит только для производства единичных деталей и небольших партий.
(2) Двухлезвийный расточной инструмент
Простой двухлезвийный расточной инструмент имеет пару симметричных режущих кромок на обоих концах инструмента, которые участвуют в резании одновременно, что позволяет исключить влияние радиальной силы резания на расточной стержень. Точность размеров отверстия в заготовке обеспечивается размером расточного инструмента.
Двухлезвийные расточные инструменты делятся на фиксированные и плавающие. Фиксированный блок расточного инструмента и его установка показаны на рис. 16. Блок расточного инструмента может быть паяным с лезвиями из твердых сплавов или полностью изготовленным из быстрорежущей инструментальной стали. Этот тип расточного инструмента из-за ограничений по точности установки и конструктивным размерам блока расточного инструмента подходит только для черновой и получистовой расточки отверстий диаметром более 40 мм.
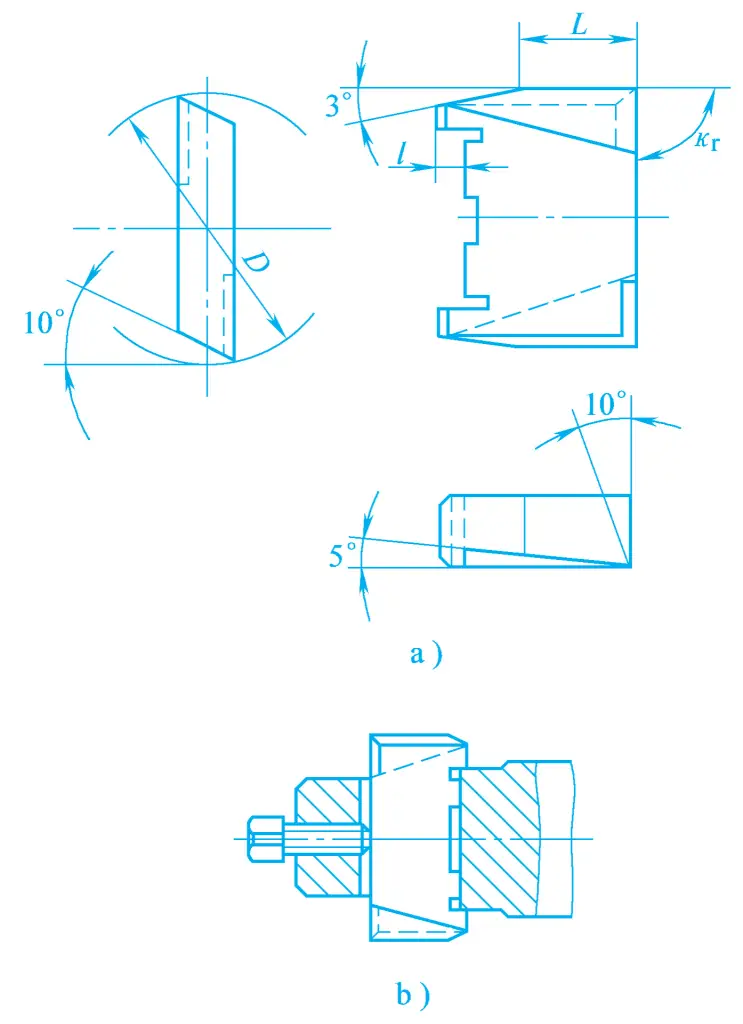
a) Блок расточного бруса
b) Установка
В настоящее время большинство обоюдоострых расточных штанг имеют плавающую конструкцию, как показано на рис. 17, где представлена широко используемая плавающая расточная штанга монтажного типа. Блок расточного прутка устанавливается в квадратное отверстие расточного прутка с зазором, без необходимости зажима. Во время резания он балансируется и позиционируется под действием силы резания, действующей на режущие кромки с обеих сторон, что позволяет автоматически компенсировать погрешности обработки, вызванные ошибками установки блока расточного прутка и погрешностями радиального биения расточного прутка.
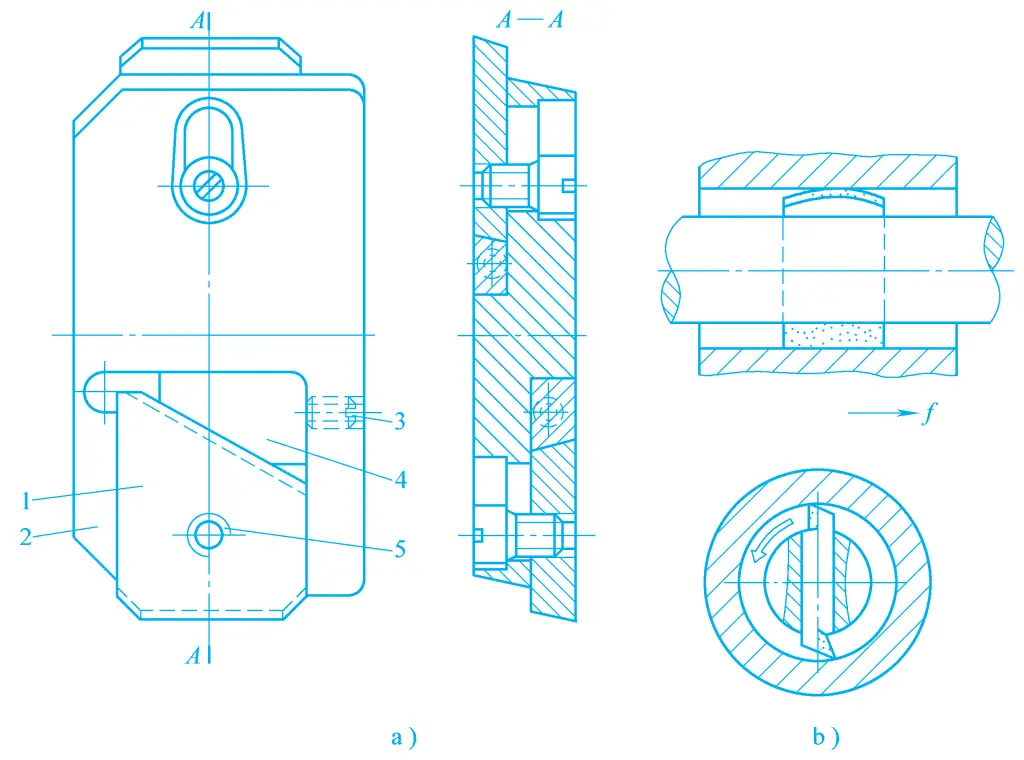
a) Плавающая расточная штанга
б) Использование
1-Расточная вставка
Корпус с 2 инструментами
3 - Регулировочный винт
4-уровневая шайба
5-Затяжной винт
Класс допуска отверстия, который может быть достигнут с помощью этой расточной линейки, достигает IT7~IT6, а шероховатость поверхности составляет Ra1,6~0,4 мкм. Недостатком плавающего расточного блока в расточном станке является то, что он не может исправить погрешность прямолинейности и погрешность взаимного расположения отверстий.
(3) Многогранный расточной брусок
В массовом производстве, особенно при обработке цветных металлов с малым износом инструмента, часто используются комбинированные многокромочные расточные головки, то есть расположение нескольких расточных пластин для обработки радиальных и осевых размеров на одной расточной головке и одной резцовой головке. Хотя изготовление и перешлифовка такой комбинированной расточной головки несколько затруднительны, она все же имеет преимущество с точки зрения общей эффективности обработки.
Чтобы повысить точность и эффективность растачивания отверстий и избежать необходимости перешлифовки вышеупомянутых многокромочных расточных брусков, при растачивании можно использовать комбинированный многокромочный расточной брусок, то есть устанавливать две или более режущих головок на один корпус инструмента или расточной брусок, причем каждая режущая головка регулируется независимо. Расточной брусок с двумя или более режущими кромками, работающими одновременно, называется комбинированным многокромочным расточным бруском.
На рис. 18a показан комбинированный расточной брусок с двумя кромками, используемый для сквозных и глухих отверстий, а на рис. 18b - комбинированный расточной брусок с несколькими кромками, используемый для грубого и тонкого растачивания двойных отверстий.
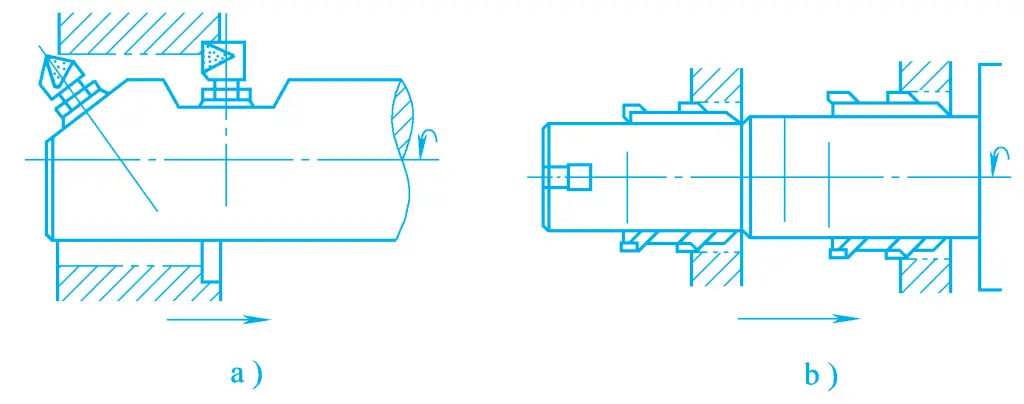
4. Методы расточной обработки
(1) Обработка одной поверхности
1) Расточка отверстий малого диаметра
Расточная линейка может быть установлена на шпинделе для вращения, при этом рабочий стол не перемещается, что позволяет шпинделю также выполнять осевое перемещение подачи, как показано на рис. 8a. После каждой подачи шпиндель возвращается в исходное положение, затем регулируется величина обратного резания, чтобы продолжить обработку до завершения.
2) Сверление неглубоких больших отверстий
Установите держатель инструмента и расточную планку на плоский поворотный суппорт, дайте плоской поворотной плите вращаться, доводя расточную планку до необходимой глубины, затем дайте рабочему столу привести заготовку в движение для выполнения продольной подачи, как показано на рис. 8b.
3) Обработка торцевой поверхности отверстия
Установите инструмент на держатель плоской поворотной пластины, приводимой во вращение плоской поворотной пластиной, в то время как держатель инструмента подается радиально вдоль плоской поворотной пластины с помощью ползуна держателя инструмента, как показано на рис. 8c.
4) Сверление, развертывание и рассверливание отверстий
Для обработки небольших отверстий сверла, развертки и инструменты для развертывания могут последовательно устанавливаться на шпиндель, который вращается и совершает осевое движение подачи, чтобы завершить процессы сверления, развертывания и другой резки небольших отверстий, как показано на рис. 8d.
5) Расточные резьбы
Установите резьбонарезной брусок на специально изготовленный держатель, который приводится во вращение расточным шпинделем, в то время как рабочий стол перемещается вдоль станины на один ход за оборот инструмента, тем самым растачивая резьбу.
Чтобы контролировать величину обратного резания при каждом ходе, можно при необходимости перемещать специальный держатель инструмента на определенное расстояние вдоль направления его скольжения в конце каждого хода, как показано на рис. 8g. Этот метод также можно использовать для обработки коротких наружных резьб. Для растачивания внутренней резьбы на расточной линейке можно установить еще один специальный держатель, который вращается и подается в осевом направлении по мере необходимости, как показано на рис. 8h.
(2) Обработка системы отверстий
Под системой отверстий понимаются два или более отверстий в пространстве, к которым предъявляются определенные требования по точности взаимного расположения. Системы отверстий подразделяются на системы коаксиальных отверстий, системы вертикальных отверстий и системы параллельных отверстий.
1) Системы расточки коаксиальных отверстий
Основным техническим требованием к системам коаксиальных отверстий является точность соосности каждого отверстия на коаксиальной линии. В производстве для обработки обычно используются следующие методы:
① Метод руководства.
При обработке систем отверстий в корпусе в единичном и мелкосерийном производстве деформация расточного стержня под действием силы может повлиять на точность соосности отверстий. В этом случае для обработки соосных отверстий можно использовать направляющую втулку.
Используйте направляющую втулку на задней стойке расточного станка для поддержки и направления. Вставьте расточной стержень в коническое отверстие расточного шпинделя, а другой конец поддерживается направляющей втулкой на задней стойке, установите расточной инструмент и отрегулируйте размер. Расточной шпиндель вращается, а рабочий стол приводит заготовку в движение с продольной подачей, таким образом, растачивая два соосных отверстия.
Если два отверстия имеют разные диаметры, два расточных инструмента могут быть установлены в разных положениях на расточной линейке для последовательной или одновременной расточки двух отверстий, как показано на рис. 10b. Недостатком этого метода является то, что регулировка положения направляющей втулки на задней стойке требует много времени и усилий, а для выравнивания требуется центрирующий блок, который обычно подходит для обработки больших корпусов.
Используйте уже обработанное отверстие для поддержки и направления. После того как отверстие на передней стенке корпуса обработано, в него можно установить направляющую втулку, которая будет поддерживать и направлять расточной стержень для обработки отверстия позади, чтобы обеспечить соосность двух отверстий. Этот метод подходит для обработки соосных отверстий с относительно близкими стенками корпуса, как показано на рис. 19.
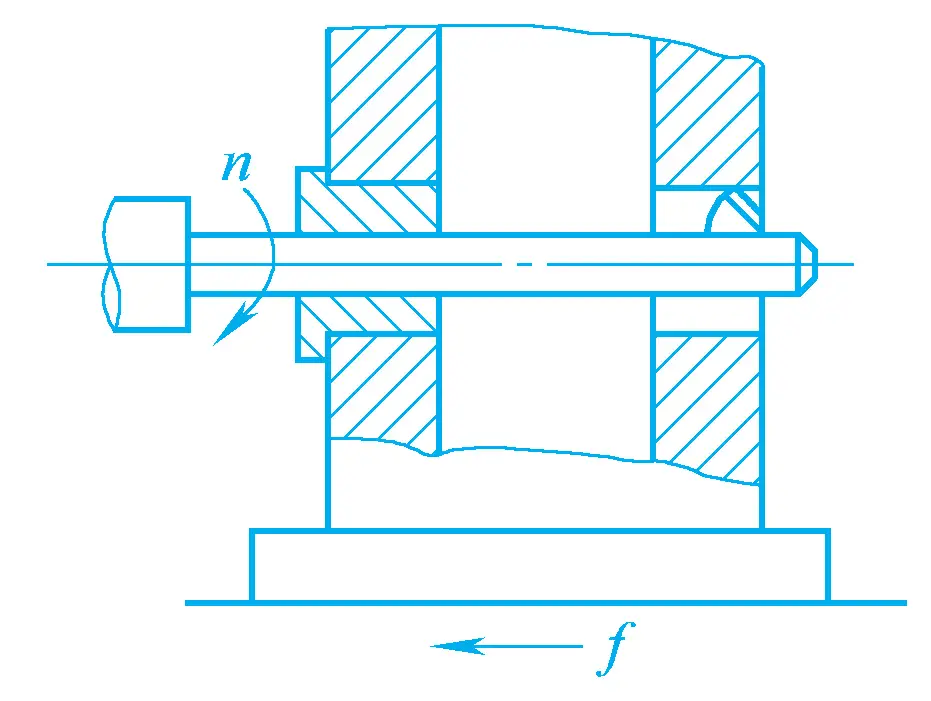
② Метод выравнивания.
Метод выравнивания предполагает обработку отверстия на одном конце корпуса после однократного зажима, затем поворот рабочего стола расточного станка на 180° и выравнивание отверстия на другом конце корпуса по коаксиальной линии.
На рис. 20a показано выравнивание технологической базовой поверхности параллельно оси растачиваемого отверстия на корпусе с помощью циферблатного индикатора, установленного на расточной линейке перед растачиванием, придание ей параллельности оси расточной линейки, а затем регулировка положения шпинделя для обработки отверстия на стенке A корпуса.
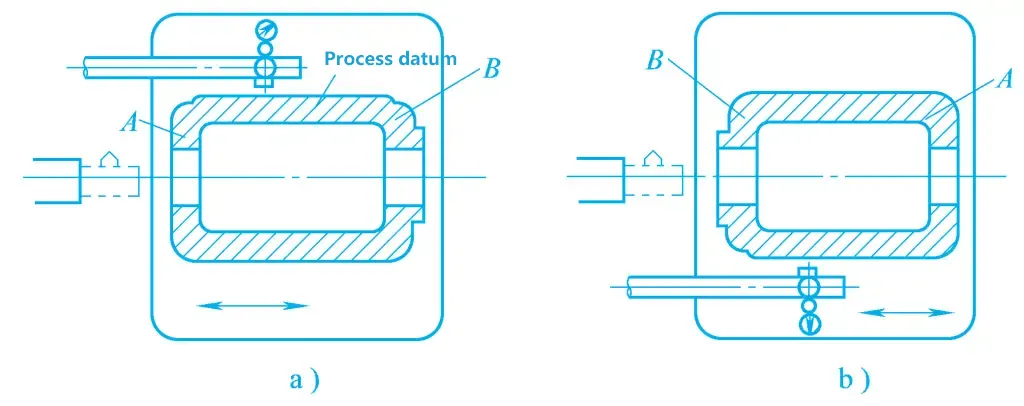
На рис. 20b показано, что после расточки рабочий стол поворачивается на 180°, технологическая базовая поверхность выравнивается в соответствии с требованиями параллельности оси расточного прутка, затем, используя технологическую базовую поверхность как единый измерительный эталон, регулируется положение шпинделя таким образом, чтобы ось расточного прутка совпала с осью отверстия на стенке A, и таким образом обрабатывается отверстие на стенке B корпуса.
③ Метод расточного станка.
При серийном производстве для обработки обычно используются расточные приспособления, при этом точность соосности гарантируется расточным приспособлением. Как показано на рис. 21, заготовка зажимается на расточной оснастке, а расточная линейка упирается в направляющие отверстия передней и задней расточных втулок и направляется расточными втулками для сверления отверстий в нужном положении на заготовке.
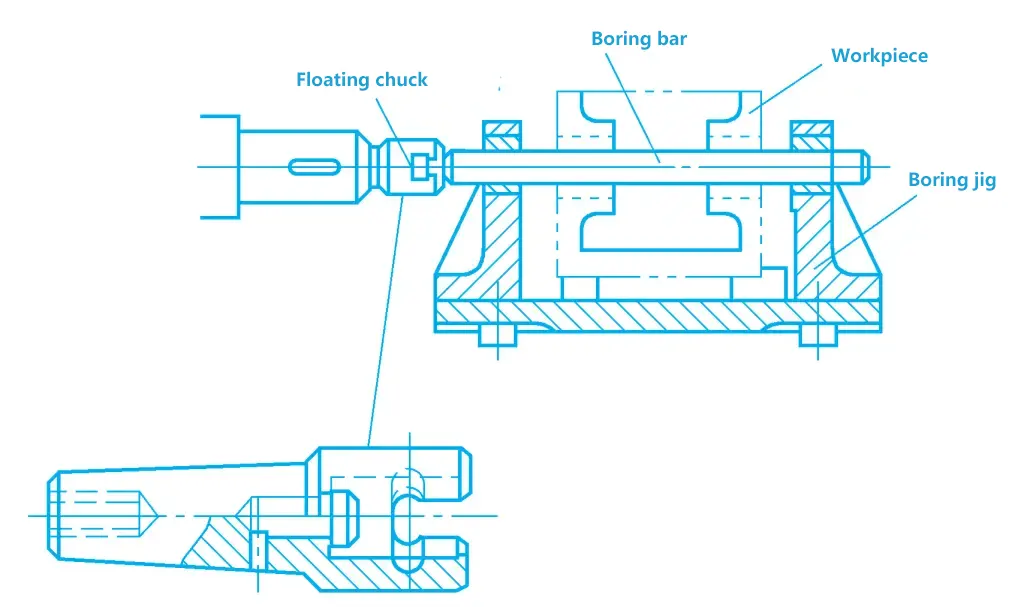
При растачивании отверстий с помощью расточной оснастки расточная линейка плавно соединяется со шпинделем станка через плавающий патрон, что позволяет не влиять на точность обработки системы отверстий на станке. На рис. 21 точность соосности отверстий зависит в основном от точности расточной оснастки, что позволяет обрабатывать высокоточные системы отверстий на менее точных станках.
Он также облегчает одновременное резание несколькими инструментами, а позиционирование и зажим осуществляются быстро и с высокой производительностью. Однако требования к точности расточного станка высоки, производственный цикл длителен, а стоимость производства высока, поэтому метод расточного станка для обработки систем отверстий применяется в основном в серийном производстве, которое может осуществляться как на станках общего назначения, так и на специализированных станках или обрабатывающих центрах.
2) Системы параллельного сверления отверстий
Основными техническими требованиями к системам параллельных отверстий являются точность размеров и позиционная точность расстояний между осями параллельных отверстий и между осями отверстий и базовой плоскостью. В производстве обычно используются следующие методы:
① Метод координат.
Координатный метод растачивания отверстий предусматривает преобразование размеров расстояния между отверстиями в системе отверстий в два взаимно перпендикулярных координатных размера, а затем точную настройку относительных положений шпинделя станка и заготовки в горизонтальном и вертикальном направлениях в соответствии с этими координатными размерами, чтобы обеспечить точность размеров расстояния между отверстиями путем контроля координатных размеров смещения и допусков станка.
② Метод выравнивания.
Метод центровки при растачивании предполагает использование некоторых вспомогательных устройств для точного определения правильного положения каждого обрабатываемого отверстия на станке общего назначения. К распространенным методам выравнивания относятся:
Метод выравнивания по линейной разметке.
Перед обработкой отметьте положение каждого отверстия на заготовке в соответствии с требованиями чертежа, а во время обработки выровняйте инструмент и заготовку по отмеченным линиям, совмещая их с методом пробного резания.
Линейная разметка требует ручного управления, сложна, а точность обработки сильно зависит от уровня квалификации рабочего, что приводит к низкой точности расстояния до отверстия и низкой производительности. Поэтому он обычно подходит для обработки систем отверстий с низкими требованиями к точности расстояния между отверстиями и небольшими партиями.
Метод выравнивания оси сердца калибровочного блока.
Как показано на рис. 22, вставьте прецизионную сердечную ось в отверстие шпинделя расточного станка и обрабатываемое отверстие соответственно, а затем соедините калибровочные блоки определенных размеров для выравнивания положения шпинделя.
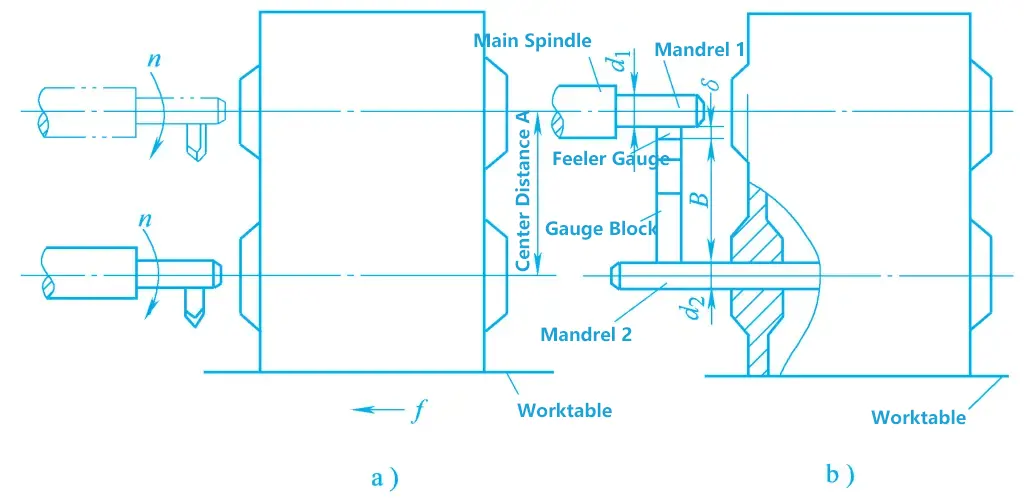
a) Расточка параллельных отверстий
b) Выравнивание с блоком измерительных приборов по оси сердца
При выравнивании необходимо использовать щуп для измерения зазора между калибровочным блоком и осью сердцевины, чтобы предотвратить деформацию от прямого контакта калибровочного блока с осью сердцевины. Этот метод позволяет достичь более высокой точности расстояния между отверстиями, но имеет низкую производительность и подходит для единичного и мелкосерийного производства. На рисунке d₁ и d₂ - диаметры оси сердцевины, δ - размер щупа, A - межосевое расстояние отверстия, B - размер блока манометров в сборе.
③ Метод расточного станка.
В массовом производстве, как правило, используется обработка на расточном станке, а требования к параллельности обеспечиваются расточным станком.
3) Система расточки вертикальных отверстий
Основными техническими требованиями к системе вертикальных отверстий являются требования к перпендикулярности между осями отверстий, и в производстве обычно используются следующие два метода:
① Метод выравнивания.
При единичном и мелкосерийном производстве она обычно обрабатывается на универсальном станке. При расточке вертикальной системы отверстий после обработки отверстия в одном направлении рабочий стол поворачивается на 90° для расточки отверстия в перпендикулярном направлении. Точность перпендикулярности системы отверстий обеспечивается устройством выравнивания 90° рабочего стола расточного станка. Если точность устройства выравнивания на 90° обычного рабочего стола расточного станка невысока, выравнивание можно выполнить с помощью сердечной оси и циферблатного индикатора, то есть вставить сердечную ось в обрабатываемое отверстие, затем повернуть рабочий стол назад и использовать циферблатный индикатор для выравнивания путем встряхивания рабочего стола.
② Метод расточного станка.
При серийном производстве, как правило, используется метод расточного станка, точность перпендикулярности которого гарантируется расточным станком.