
1. Sac Metal İmalatına Giriş
1.1 Tanım:
Sac metal imalatı için henüz tam bir tanım bulunmamaktadır. Yurtdışındaki profesyonel bir dergiden alınan bir tanıma göre, metal levhalar (genellikle 6 mm'nin altında) için kesme, delme / kesme / birleştirme, katlama, kaynak, perçinleme, montaj, şekillendirme (otomobil gövdeleri gibi) vb. dahil olmak üzere kapsamlı bir soğuk işleme süreci olarak tanımlanabilir. Önemli özelliği, aynı parçanın kalınlığının tutarlı olması ve çelik levhalar, alüminyum levhalar, bakır levhalar vb. gibi metal levhaları işlemesidir.
1.2 Sac Metal İmalatının Süreç Akışı:
Herhangi bir sac metal parça için, proses akışı olarak adlandırılan belirli bir işleme süreci vardır. Farklı yapılara sahip sac metal parçalar için işlem akışı da farklı olabilir. Şirketimizin durumu ile birleştirildiğinde, genel süreç aşağıdaki gibidir:
Müşteri Siparişi → Çizimlerin Hazırlanması → Çizim Açılım (Sayısal Kontrol Programlama) → Kesme (Sayısal Delme) → Ortak Delme → Bükme → Pres Perçinleme → Kaynak.
İlgili okuma: Sac Metal İmalatı için En İyi Ekipmanlar: Bir Kılavuz
2. Temel Sac Metal Mühendisliği Çizim Bilgisi
2.1 Mekanik Çizime Giriş:
Sac metal imalatı için mühendislik çizimi, mekanik çizim kategorisine aittir. Mekanik çizim, makinelerin yapısal şeklini, boyutunu, çalışma prensibini ve teknik gereksinimlerini doğru bir şekilde temsil etmek için kalıpları kullanan bir disiplindir.
Kalıplar grafikler, semboller, metinler, sayılar vb. unsurlardan oluşur. Tasarım amacını, üretim gereksinimlerini ve deneyim alışverişini ifade eden teknik belgelerdir ve genellikle mühendislik endüstrisinin dili olarak adlandırılırlar.
Mekanik çizim standartlarında öngörülen öğeler şunları içerir: çizim formatı ve biçimi, ölçek, yazı tipi ve çizgiler vb. Çizim formatı ve biçimi, standart çizim formatının boyutunu ve çizimdeki çerçevenin karşılık gelen boyutunu belirtir. Ölçek, desendeki boyutun uzunluğunun makine parçasının gerçek boyutuna oranını ifade eder.
1:1 ölçekte çizim dışında, yalnızca standartlarda belirtilen küçültme ve büyütme oranlarına izin verilir. Çin'de, Çince karakterlerin uzun taklit Song yazı karakteri ile yazılması ve harf ve rakamların öngörülen yapıda yazılması şart koşulmuştur.
Görünür kontur çizgileri için kalın düz çizgiler, görünmez kontur çizgileri için noktalı çizgiler, eksen ve simetri merkezi çizgileri için ince noktalı kesik çizgiler ve boyut ve kesit çizgileri için ince düz çizgiler gibi çizim için sekiz tür çizgi belirtilmiştir.
Mekanik çizimler temel olarak parça çizimleri ve montaj çizimlerini içerir. Parça çizimleri, parçaların şekil, boyut, imalat ve muayene teknik gereksinimlerini ifade eder; montaj çizimleri, makineye ait parçalar ve bileşenler arasındaki montaj ilişkilerini ve çalışma prensiplerini ifade eder; ve parçaların yapısını ve şeklini grafiksel olarak ifade eder, yaygın olarak kullanılan görünümler önden görünüm, kesit görünümü ve kesit görünümü vb. içerir.
Görünüşler, ortografik projeksiyon yöntemine göre parçaların projeksiyon düzlemi üzerine yansıtılmasıyla elde edilen grafik şekillerdir. İzdüşüm yönüne ve ilgili izdüşüm düzleminin konumuna bağlı olarak, görünümler ana görünümler, üst görünümler ve sol görünümler vb. olarak ayrılır. Görünüşler esas olarak makine parçalarının dış şeklini ifade etmek için kullanılır. Şekilde görülemeyen kontur çizgileri noktalı çizgilerle temsil edilir.
Bir parçayı bir projeksiyon düzlemine yansıtırken, gözlemci, parça ve projeksiyon düzlemi arasında iki göreceli konum vardır. Parça projeksiyon düzlemi ile gözlemci arasında yer aldığında, buna birinci açı projeksiyon yöntemi denir. Projeksiyon düzlemi parça ile gözlemci arasında yer aldığında, buna üçüncü açılı projeksiyon yöntemi denir. Her iki projeksiyon yöntemi de makine parçalarının şeklini eşit derecede iyi ifade edebilir. Çin ulusal standartları birinci açılı projeksiyon yönteminin kullanılmasını şart koşmaktadır.
2.2 Ortografik Projeksiyona Giriş
Ortografik projeksiyon, bir nesnenin dış hatlarını bir düzlem üzerine yansıtarak geometrisini, boyutunu ve şeklini doğru bir şekilde temsil eden bir çizim yöntemidir.
Bir nesnenin altı görünümü vardır: önden yansıtıldığında nesnenin önünün şeklini yansıtan bir ön görünüm; yukarıdan yansıtıldığında nesnenin üstünün şeklini yansıtan bir üst görünüm; sol taraftan yansıtıldığında nesnenin sol tarafının şeklini yansıtan bir sol görünüm ve yaygın olarak kullanılmayan diğer üç görünüm.
Üç ana görünüm - ön, üst ve sol - birlikte ortografik projeksiyon veya çoklu görünüm projeksiyonu olarak adlandırılır.
Her bir görünüm nesnenin sadece bir yönünün şeklini gösterebilir ve nesnenin yapısal şeklini tam olarak yansıtamaz. Üç görünüşlü çizimler, aynı nesnenin üç farklı yönden yansıtılmasının sonucudur. Ayrıca, kesit görünüşler ve yarım kesit görünüşler gibi yardımcı görünüşler de nesnenin yapısını tam olarak ifade etmek için kullanılır.
Ortografik projeksiyon için projeksiyon kuralları şunlardır:
- Önden görünüm ve üstten görünüm - Uzunluk boyut çizgisi hizalanmıştır.
- Önden görünüm ve soldan görünüm - Yükseklik boyut çizgisi hizalanmıştır.
- Sol görünüm ve üst görünüm- Genişlik boyut çizgisi hizalanır.
2.3 Çizim Tanıma Yöntemi
Üç görünüşlü bir çizime bakarken, onun uzamsal şeklini nasıl anlayabiliriz? Bu, iki boyutludan üç boyutlu uzaya doğru bir süreçtir. Sac metal Çizimler nispeten basittir ve burada temel bir görüntüleme yöntemi tanıtılmaktadır - form analizi.
Biçim analizi, nesneyi hangi temel şekillerin oluşturduğunu analiz etmeyi, her bir temel şeklin izdüşümünü bulmayı, uzamsal şekillerini görselleştirmeyi ve ardından genel uzamsal şekli görselleştirmek için temel şekilleri ve göreceli konumlarını birleştirmeyi içerir.
Her bir görünüm nesnenin yalnızca bir yönünün şeklini gösterebildiğinden, nesnenin yapısını tam olarak anlamak için birden fazla görünümün birleştirilmesi gerekir. Daha karmaşık nesneler için, şekillerini açıkça ifade etmek için tek başına üç görünüm yeterli olmayabilir.
Sağdan görünüm, üstten görünüm, arkadan görünüm gibi ek projeksiyon görünümleri veya kesit görünümleri, kesit görünümleri ve yerel büyütme görünümleri gibi yardımcı görünümler gerekebilir.
2.4 Üçüncü Açı Projeksiyonuna Giriş
Üç görünümlü bir çizim yapmanın iki yolu vardır: üçüncü açı projeksiyonu ve birinci açı projeksiyonu, her ikisi de ISO uluslararası standardına uygundur.
Şu anda Çin, Almanya ve diğer ülkeler birinci açı projeksiyon yöntemini kullanırken, Amerika Birleşik Devletleri, Japonya ve diğer ülkeler üçüncü açı projeksiyon yöntemini kullanmaktadır. Gerçek üretim sürecinde, üçüncü açı projeksiyon yöntemini kullanan çizimleri de sıklıkla görüyoruz.
İki projeksiyon yöntemi arasındaki fark şudur:
Birinci açı projeksiyon yöntemi, nesneyi gözlemci ile projeksiyon düzlemi arasına yerleştirir.
Üçüncü açı projeksiyon yöntemi, projeksiyon düzlemini gözlemci ile nesne arasına yerleştirir. Bu nedenle, iki projeksiyon yöntemiyle elde edilen görünümler nesnenin ön-arka ilişkisini temsil etmede zıttır:
Birinci açı projeksiyon yöntemi için: sol görünüm sağ tarafa yerleştirilir, sağ görünüm sol tarafa yerleştirilir ve üst görünüm alt tarafa yerleştirilir vb.
Üçüncü açı projeksiyon yöntemi için: sol görünüm sol tarafa yerleştirilir, sağ görünüm sağ tarafa yerleştirilir ve üst görünüm üste yerleştirilir vb.
İki projeksiyon yöntemini birbirinden ayırmak için uluslararası standart, şekilde gösterildiği gibi her biri için farklı semboller öngörmektedir.

3. Sac Metal Açma Hesaplaması
3.1 Açılım Hesaplama Prensibi:
sırasında sac metal bükme i̇şlemi̇dış katman çekme gerilimine, iç katman basınç gerilimine maruz kalır ve aralarında ne gerilimde ne de sıkıştırmada olmayan nötr bir katman vardır.
Nötr tabakanın uzunluğu bükme sırasında değişmeden kalır, bu nedenle açılımın hesaplanması bükülmüş parçanın uzunluğu. Nötr tabakanın konumu deformasyon derecesine bağlıdır.
Ne zaman bükülme yarıçapı büyük ve bükme açısı küçük olduğunda, deformasyon derecesi küçüktür ve nötr tabaka sac metal kalınlığının merkezine yakın bir yerde bulunur. Bükme yarıçapı küçüldüğünde ve bükme açısı arttığında, deformasyon derecesi artar ve nötr tabakanın konumu kademeli olarak bükme merkezinin içine doğru hareket eder.
3.2 Hesaplama Yöntemi:
Sac metalin açılmasını hesaplamanın birçok yolu vardır ve her sac metal fabrikası tarafından kullanılan hesaplama yöntemleri aynı olmayabilir. Firmamız açılım boyutunu hesaplamak için basit ve pratik bir kesinti yöntemi kullanmaktadır.
Açma için temel formül şöyledir: Açma Uzunluğu = Dış Boyut + Dış Boyut - Açma Katsayısı (K Değeri).
Bükme Tipleri | şematik diyagram | hesaplama formülü |
Dik Açılı Bükme | ![]() | katlanmamış boyutlar=A+B-K |
Dik Açılı Olmayan Bükme | ![]() | katlanmamış boyutlar=A+B-(q/90°)*K |
Ark Bükme (R/T>5) | ![]() | katlanmamış boyutlar=A+B-0.43T |
Düz Flanş (Z-Bend) | ![]() | 1. H≧5T olduğunda, iki adımda oluşturulmalı ve iki dik açılı dirseğe göre hesaplanmalıdır; 2. H<5T olduğunda, tek adımda oluşturulmalıdır ve L=A+B+K (K değeri için Tablo 3.2.4'e bakınız). |
Açılı Flanş (Z-Bend) | ![]() | 1. H<2T olduğunda, a. q≤70° olduğunda, L=A+B+C+0,2 b. q>70° olduğunda, L=A+B+K (K değeri için Tablo 3.2.4'e bakınız, yani düz kenarların farkına göre genişletilmiştir) 2. H≧2T olduğunda, iki adımda oluşturulmalı ve iki dik açılı olmayan kıvrıma göre hesaplanmalıdır. |
Tablo 3-1 Çelik Plakalar için Açılma Katsayısı Tablosu (Birim: mm)
plaka kalınlığı T | 0.8 | 1.0 | 1.2 | 1.5 | 2.0 | 2.5 | 3.0 |
K(soğuk plaka) | 1.5 | 1.8 | 2.1 | 2.6 | 3.4 | 4.5 | 5.4 |
K(paslanmaz çelik) | 1.4 | 1.9 | 2.3 | 2.87 | 3.75 |
Tablo 3-2 Alüminyum Plakalar için Açılma Katsayısı Tablosu (Birim: mm)
plaka kalınlığı T | 0.5 | 1.0 | 1.2 | 1.5 | 2.0 | 2.5 | 3.0 |
K | 0.8 | 1.5 | 1.7 | 2.3 | 3.2 | 4.0 | 5.0 |
Tablo 3-3 Bakır Plakalar için Açılma Katsayısı Tablosu (Birim: mm)
plaka kalınlığı T | 1.0 | 1.5 | 2.0 | 2.5 | 3.0 | 4.0 | 5.0 | 6.0 | 8.0 | 10.0 |
K | 1.8 | 2.6 | 3.5 | 4.4 | 4.8 | 6.5 | 8.0 | 9.5 | 12.5 | 16 |
Tablo 3-4 Düz Kenar Farkı için Açılma Katsayısı Tablosu (Birim: mm)
H T | 0.5 | 0.8 | 1.0 | 1.2 | 1.5 | 1.6 | 2.0 | 3.2 |
0.5 | 0.1 | |||||||
0.8 | 0.2 | 0.1 | 0.1 | |||||
1.0 | 0.5 | 0.2 | 0.2 | 0.2 | 0.2 | 0.2 | ||
1.5 | 1.0 | 0.7 | 0.5 | 0.3 | 0.3 | 0.3 | 0.3 | 0.2 |
2.0 | 1.5 | 1.2 | 1.0 | 0.8 | 0.5 | 0.4 | 0.4 | 0.3 |
2.5 | 2.0 | 1.7 | 1.5 | 1.3 | 1.0 | 0.9 | 0.5 | 0.4 |
3.0 | 2.5 | 2.2 | 2.0 | 1.8 | 1.5 | 1.4 | 1.0 | 0.5 |
3.5 | 2.7 | 2.5 | 2.3 | 2.0 | 1.9 | 1.5 | 0.6 | |
4.0 | 3.2 | 3.0 | 2.8 | 2.5 | 2.4 | 2.0 | 0.8 | |
4.5 | 3.7 | 3.5 | 3.3 | 3.0 | 2.9 | 2.5 | 1.3 | |
5.0 | 4.0 | 3.8 | 3.5 | 3.4 | 3.0 | 1.8 |
3.3 Yaygın olarak kullanılan matematiksel bilginin hesaplanmasının açılması
3.3.1 Boyut Birimleri
Çin'de temel uzunluk birimi metredir (m) ve dönüştürme ilişkisi şöyledir:
- 1 metre (m) = 100 santimetre (cm)
- 1 santimetre (cm) = 10 milimetre (mm)
- 1 milimetre (mm) = 1000 mikrometre (μm)
İngilizce uzunluk birimleri, Birleşik Krallık ve Amerika Birleşik Devletleri gibi ülkelerde aşağıdaki ilerleme ile kullanılır:
- 1 yarda = 3 fit
- 1 ayak (1′) = 12 inç (12″)
İnç ve milimetre arasındaki dönüşüm ilişkisi: 1 inç (1″) = 25,4 mm
3.3.2 Yaygın Olarak Kullanılan Hesaplama Formülleri
Kosinüs Yasası | ![]() | ![]() |
kemer boyutu hesaplama | ![]() | ![]() |
Dik üçgenlerin trigonometrik fonksiyonları için hesaplama formülleri | sinA=a/c cosA=b/c tanA=a/b cotA=b/a | ![]() |
4. Yaygın olarak kullanılanlara giriş sac metal malzemeler
4.1 Yaygın olarak kullanılan plakalara giriş
4.1.1 Soğuk levha olarak da bilinen soğuk haddelenmiş normal ince çelik levha, normal karbon yapısal çelik soğuk haddelenmiş levha için kısaltılmış bir isimdir. Sıradan karbon yapısal çeliğin sıcak haddelenmiş çelik levhasından yapılır ve ayrıca 4 mm'den daha az bir kalınlığa soğuk haddelenir.
Oda sıcaklığında haddelendiği ve tufal üretmediği için yüzey kalitesi iyidir, boyutsal doğruluğu yüksektir ve tavlama işlemi ile mekanik ve proses özellikleri iyidir. Sac metal işlemede en yaygın kullanılan metal malzemedir.
Yaygın kaliteler: Ulusal Standart GB (Q195, Q215, Q235, Q275), Japon Standardı JIS (SPCC, SPCD, SPCE)
4.1.2 Yaygın olarak elektrolitik plaka olarak bilinen sürekli elektrolizle galvanizlenmiş ince çelik plaka, elektrokaplama çinko üretim hattındaki bir elektrik alanının etkisi altında önceden hazırlanmış bir soğuk plaka yüzeyine derin bir su çinko tuzu çözeltisinden çinko biriktirilmesini ifade eder ve çelik plakanın yüzeyinde iyi bir korozyon direnci sağlayan bir galvanizli tabaka tabakası ile sonuçlanır.
Sınıflar: Ulusal Standart GB (DX1, DX2, DX3, DX4), Japon Standardı JIS (SECC, SECD, SECE)
4.1.3 Genellikle galvanizli sac veya beyaz demir sac olarak adlandırılan sürekli sıcak daldırma galvanizli ince çelik levha, blok veya yaprak benzeri kristal desenlere sahip güzel bir yüzeye sahiptir ve kaplama sağlamdır, mükemmel atmosferik korozyon direncine sahiptir.
Aynı zamanda, çelik levha iyi kaynak performansına ve soğuk şekillendirme performansına sahiptir. Elektro galvanizli sacın yüzeyi ile karşılaştırıldığında, kaplaması daha kalındır ve esas olarak güçlü korozyon direnci gerektiren sac metal parçalar için kullanılır.
Sınıflar: Ulusal Standart GB (Zn100-PT, Zn200-SC, Zn275-JY), Japon Standardı JIS (SGCC, SGCD1, SGCD2, SGCD3)
4.1.4 Paslanmaz çelik levha, hava, buhar, su gibi zayıf korozif ortamlara ve asit, alkali ve tuz gibi kimyasal korozyon ortamlarına dayanıklı bir çelik türüdür. Paslanmaz aside dayanıklı çelik olarak da adlandırılır. Gerçek kullanımda, zayıf korozif ortama dayanıklı çelik genellikle paslanmaz çelik olarak adlandırılırken, kimyasal ortama dayanıklı çelik aside dayanıklı çelik olarak adlandırılır.
Paslanmaz çelik genellikle matris yapısına göre sınıflandırılır:
1. Ferritik paslanmaz çelik.
12% ila 30% krom içerir. Korozyon direnci, sünekliği ve kaynaklanabilirliği artan krom içeriği ile artar ve klorür stres korozyonuna karşı direnci diğer paslanmaz çelik türlerinden daha iyidir.
2. Östenitik paslanmaz çelik.
Krom içeriği 18%'den fazladır, yaklaşık 8% nikel ve az miktarda molibden, titanyum, nitrojen ve diğer elementler içerir. İyi kapsamlı özelliklere sahiptir ve çeşitli ortamlar tarafından korozyona dayanabilir.
3. Östenitik-ferritik dubleks paslanmaz çelik.
Östenitik ve ferritik paslanmaz çeliğin avantajlarına sahiptir ve süper plastisiteye sahiptir.
Martensitik paslanmaz çelik. Yüksek mukavemetli, ancak zayıf plastisite ve kaynaklanabilirlik. Paslanmaz çelik levhanın mukavemetinin yüksek olduğu ve daha fazla takım aşınmasına neden olduğu unutulmamalıdır. CNC zımba presleri. Genellikle nümerik kontrollü delme işlemi için uygun değildir.
Sınıflar: Birçok paslanmaz çelik türü vardır ve sac metal işlemede yaygın olarak kullanılanı bir tür östenitik paslanmaz çeliktir (1Cr18Ni9Ti). Japon Standardı JIS (SUS)
4.1.5 Alüminyum levha, alüminyum iyi termal iletkenliğe, elektrik iletkenliğine ve sünekliğe sahip gümüş-beyaz hafif bir metaldir. Saf alüminyum düşük mukavemete sahiptir ve yapısal bir malzeme olarak kullanılamaz. Sac metal işlemede yaygın olarak kullanılan alüminyum alaşımlı levha, alaşım elementlerinin içeriğine göre 1000 serisi, 2000 serisi ~ 8000 serisi olmak üzere sekiz seriye ayrılabilir.
Yaygın olarak kullanılanlar 2000 serisi, 3000 serisi ve 5000 serisidir. 2000 serisi, sert alüminyum olarak da bilinen yüksek sertlik ile karakterize edilen bir bakır-alüminyum alaşımıdır; çeşitli orta mukavemetli parçalar ve bileşenler için kullanılabilir. 3000 serisi, iyi pas önleme performansına sahip bir manganez-alüminyum alaşımıdır, bu nedenle pas önleyici alüminyum olarak da adlandırılır. 5000 serisi, düşük yoğunluk, yüksek gerilme mukavemeti ve yüksek uzama ile karakterize edilen bir magnezyum-alüminyum alaşımıdır.
Alüminyum-magnezyum alaşımının ağırlığı, aynı alandaki diğer serilere göre daha düşüktür.
Yaygın kaliteler: 3A21 (eski sınıf LF21), 5A02 (eski sınıf LF2), 2A06 (eski sınıf LY6)
4.1.6 Pirinç levha, pirinç, mor bir görünüme ve mükemmel elektrik iletkenliğine, termal iletkenliğe, sünekliğe ve korozyon direncine sahip olan saf bakırın ortak adıdır. Bununla birlikte, pahalıdır ve genellikle güç kaynaklarında büyük akımlar taşıyan parçalar için kullanılan iletken ve termal malzemeler olarak kullanılır. Pirinç düşük mukavemete sahiptir ve genellikle yapısal parçalar olarak kullanılamaz.
Sınıflar: T1, T2, T3
4.1.7 Bakır alaşımlı levha, pirinç yüksek mukavemetli ve mükemmel soğuk ve sıcak çalışma özelliklerine sahip bir bakır-çinko alaşımıdır, ancak korozyon çatlamasına eğilimlidir ve nispeten ucuzdur ve yaygın olarak kullanılmaktadır.
Yaygın sınıflar: H59, H62, H70
4.2 Yaygın olarak kullanılan plakaların ağırlığının hesaplanması
Temel hesaplama formülü: Malzeme ağırlığı = Uzunluk (m) * Genişlik (m) * Kalınlık (mm) * Malzeme yoğunluğu
Malzeme Adı | Çelik Levha | Paslanmaz Çelik Levha | Alüminyum Levha | Mor Bakır Tabak | Pirinç Levha |
Yoğunluk | 7.85 | 7.93 | 2.71 | 8.89 | 8.5 |
4.3 Yaygın Bağlantı Elemanı Bilgileri
Bağlantı elemanları, iki veya daha fazla parçayı (veya bileşeni) bir bütün halinde tutturmak için kullanılan mekanik parçalar için kullanılan genel bir terimdir. Yaygın olarak kullanılan bağlantı elemanları arasında cıvatalar, vidalar, somunlar, pullar, pimler vb. bulunur.
4.3.1 İplik İşleme
Ortak konuların temsili:
Kaba diş "M" harfi ve nominal çap ile temsil edilir. Örneğin, nominal çapı 24 mm olan kaba diş için kod M24'tür.
İnce diş "M" harfi, nominal çap ve M24*1.5 gibi hatve ile temsil edilir.
Kılavuz çekmeden önce alt delik çapını hesaplamak için formül şöyledir: Alt delik çapı = diş dış çapı - hatve.
Bu doğrudan yukarıdan da bakılabilir:
Tablo 4-1.
İplik Özellikleri | M2 | M3 | M4 | M5 | M6 | M8 | M10 | M12 | M14 |
Alt Delik Çapı | Φ1.6 | Φ2.4 | Φ3.3 | Φ4.2 | Φ5 | Φ6.8 | Φ8.5 | Φ10 | Φ12 |
4.3.2 Vidalar için Havşa Deliğinin Yapısal Boyutları
Tablo 4-2 Vidalar için Havşa Deliği Boyutları
![]() | d1 | M2 | M2.5 | M3 | M4 | M5 |
d2 | Φ2.2 | Φ2.8 | Φ3.5 | Φ4.5 | Φ5.5 | |
D | Φ4.0 | Φ5.0 | Φ6.0 | Φ8.0 | Φ9.5 | |
h | 1.2 | 1.5 | 1.65 | 2.7 | 2.7 | |
Tercih Edilen Minimum Sac Kalınlığı | 1.2 | 1.5 | 1.5 | 2.0 | 2.0 | |
α | 90° |
4.3.3 Perçin somunu, gevşek perçin somunu ve perçin vidasının çalışma prensibi, iş parçası üzerindeki ilgili boyuttaki delikleri önceden işlemek ve ardından zımba presi veya perçinleme makinesi gibi ekipmanlar aracılığıyla basınç uygulamaktır, böylece perçin somunu ve perçin vidasının dişleri plakaya sıkıştırılarak delik çevresinde plastik deformasyona neden olur. Deforme olan malzeme kılavuz oluğa ekstrüde edilir ve böylece bir kilitleme etkisi yaratılır.
Tablo 4-3 Şirketimiz tarafından yaygın olarak kullanılan Perçin Somunları, Perçin Vidaları ve Kaynak Somunu Alt Deliklerinin İşleme Boyutları için Sorgu Tablosu.
Teknik Özellikler Tip | M2.5 | M3 | M4 | M5 | M6 | M8 | M10 |
Pres Perçinleme Somunu Kolonu | Φ5.4 | Φ6.1 | Φ7.2 | Delikten Φ8 | |||
Kör DelikΦ8.5 | |||||||
Pres Perçinleme Vidası | Φ2.5 | Φ3 | Φ4 | Φ5 | Φ6 | Φ8 | |
Genleşme Perçinleme Somunu | Φ5 | Φ6 | Φ8 | Φ9 | Φ11 | Φ14 | |
Gevşemez özellikli vida | Φ5.8 | Φ6.4 | Φ8 | Φ9.5 | |||
Kaynak Somunu | Φ5 | Φ6 | Φ7 | Φ9 |
5. Yaygın Ölçme Araçları Hakkında Temel Bilgi
Mekanik parçaların çap ve açı gibi elemanlarını ölçmek için kullanılan aletlere ölçüm aletleri denir. Mekanik parçaların birçok elemanı vardır ve bu elemanların hassasiyeti için de birçok gereksinim vardır. Bu nedenle, elemanları ölçmek için birçok ölçüm aleti türü vardır. Firmamız tarafından yaygın olarak kullanılan ölçüm aletleri arasında çelik bant, kumpas, mikrometre, üniversal açı cetveli vb. bulunmaktadır.
Genel olarak, bu ölçüm aletlerinin özellikleri aralık ve mezuniyet değeri ile temsil edilir. Aralık, ölçüm aralığıdır ve mezuniyet değeri, alet üzerindeki en küçük ölçeğin değeridir. Mezuniyet değeri ne kadar küçükse, ölçüm aleti o kadar hassastır.
Ölçüm aletinin doğru kullanılıp kullanılmadığı yalnızca ölçüm aletinin doğruluğunu etkilemekle kalmaz, aynı zamanda iş parçası boyutunun ölçüm doğruluğunu da doğrudan etkiler ve hatta kalite kazalarına neden olarak şirket için gereksiz kayıplara yol açar. Bu nedenle, ölçüm aletlerinin doğru kullanımına büyük önem vermeli, ölçüm teknolojisinde mükemmellik için çaba göstermeli, doğru ölçüm sonuçlarının elde edilmesini sağlamalı ve ürün kalitesini güvence altına almalıyız.
Burada sık kullandığımız bazı ölçüm araçlarına kısa bir giriş yapıyoruz:
5.1 Çelik Bant:
Çelik bant günlük hayatta ve işte sıklıkla kullanılır ve kullanımı nispeten kolaydır. Esas olarak iş parçalarının uzunluk boyutlarını ölçmek için kullanırız. Doğruluğa göre Sınıf I ve Sınıf II olarak ayrılır ve mezuniyet değeri 1 mm'dir. Doğruluğu nispeten düşüktür ve uzunluk aralığı 3m, 5m, 10m veya daha uzundur; düşük boyut doğruluğu gereksinimleri olan daha büyük boyutlu iş parçalarının uzunluk boyutlarını ölçmek için uygundur.
5.2 Kaliper:
Kumpas, basit yapı, rahat kullanım, orta doğruluk ve geniş ölçülen boyut aralığı özelliklerine sahip yaygın olarak kullanılan bir ölçüm aracıdır. Geniş bir uygulama alanına sahiptir ve iş parçalarının dış çapını, iç çapını, uzunluğunu, genişliğini, kalınlığını, derinliğini ve delik aralığını ölçmek için kullanılabilir. Farklı okuma yöntemlerine ve ilkelerine göre, vernier kumpaslar, kadranlı kumpaslar, dijital kumpaslar vb. vardır. Verniyer kumpas şirketimiz tarafından yaygın olarak kullanılmaktadır. Kumpas işimizde en sık kullanılan ölçüm aracı olduğundan, verniyer kumpasın prensibine ve kullanımına odaklanalım:
5.2.1 Vernier kumpaslar yapılarına göre tek taraflı kumpaslar, çift taraflı kumpaslar, üç kullanımlı kumpaslar vb. olarak ayrılabilir.
(1) Tek taraflı kumpaslar iç ve dış ölçüm çenelerine sahiptir ve iç ve dış boyutları ölçebilir (Şekil 1-1).

(2) Çift taraflı kumpaslar, üst çenede bıçak şeklinde bir dış ölçüm çenesine ve alt çenede iç ve dış boyutları ölçebilen iç ve dış ölçüm çenelerine sahiptir (Şekil 1-2).

(3) Üç kullanımlı kumpaslarda iç boyutları ölçmek için kullanılan bıçak şeklinde bir iç ölçüm çenesi, dış boyutları ölçmek için kullanılan düz ve bıçak şeklinde ölçüm yüzeylerine sahip dış ölçüm çeneleri ve derinlik ve yüksekliği ölçmek için kullanılan cetvelin arkasında bir derinlik göstergesi bulunur (Şekil 1-3).

5.2.2 Vernier Kumpasın okuma prensibi ve okuma yöntemi
Verniyer kumpasların doğru kullanımında ustalaşmak için, doğru okumayı ve doğru çalıştırmayı öğrenmek gerekir. Verniyer kumpasın okuma cihazı cetvel gövdesi ve verniyerden oluşur. Cetvel çerçevesi üzerindeki hareketli ölçüm çenesi cetvel gövdesi üzerindeki sabit ölçüm çenesi ile temas ettiğinde, cetvel çerçevesi üzerindeki "0" çizgisi (verniyer sıfır çizgisi olarak adlandırılır) cetvel gövdesi üzerindeki "0" çizgisi ile hizalanır ve ölçüm çeneleri arasındaki mesafe sıfır olur. Ölçüm sırasında, cetvel çerçevesinin ölçek üzerinde belirli bir konuma hareket ettirilmesi gerekir ve hareketli ölçüm çenesi ile sabit ölçüm çenesi arasındaki mesafe, Şekil 1-4'te gösterildiği gibi ölçülen boyuttur.
Verniyer sıfır çizgisi cetvel gövdesi üzerinde 30 mm'yi gösteren ölçek ile tam olarak hizalanmışsa, cetvel gövdesi üzerindeki verniyer sıfır çizgisinin gösterdiği değer 30 mm'den biraz daha büyükse ne yapmalıyız? Bu durumda, ölçülen boyutun tam sayı kısmı (30mm) cetvel gövdesi üzerinde verniyer sıfır çizgisinin solundaki ölçek çizgisinden okunabilir (şekilde ok ile gösterilmiştir) ve 1mm'den küçük ondalık kısım verniyer yardımıyla okunabilir (şekilde ● çizgisi ile gösterilmiştir, bu 0,7mm'dir). İkisinin toplamı 30,7 mm'dir, bu da verniyer ölçüm cihazlarının ortak özelliğidir. Bu nedenle, bir sürmeli kumpası okumanın anahtarının ondalık kısmın okunmasında yattığı görülebilir.

Verniyerin ondalık kısmının okuma yöntemi, öncelikle verniyer üzerindeki hangi çizginin cetvel gövdesi üzerindeki bir çizgi ile hizalandığını belirlemektir. Daha sonra, verniyer üzerindeki bu çizginin sıra numarasını verniyerin okuma değeri ile çarpın ve sonuç verniyerin okumasıdır. Yani, Verniyer okuması = Verniyer okuma değeri * Verniyer üzerindeki hizalama çizgisinin sıra numarası.
Bir sürmeli kumpas okunurken üç adıma ayrılabilir:
- Önce tam sayı kısmını okuyun: Cetvel gövdesindeki vernier sıfır çizgisinin soluna en yakın ölçek çizgisinin değerine bakın ve ölçülen boyutun tam sayı kısmını okuyun.
- Ardından ondalık kısmı okuyun: Verniyer sıfır çizgisinin sağına bakın ve verniyerdeki hangi çizginin cetvel gövdesindeki bir çizgiyle hizalandığını sayın. Verniyer okuma değerini verniyer üzerindeki hizalama çizgisinin sıra numarası ile çarparak ölçülen boyutun ondalık kısmını okuyun.
- Ölçülen boyutu hesaplayın: Önceki iki adımdan elde edilen tam sayı ve ondalık kısımları toplayın ve toplam, kumpasın ölçülen boyutudur.
5.2.3 Verniyer kumpas nasıl kullanılır
İş parçasının boyutunu ölçmek için sürmeli kumpas kullanırken aşağıdaki noktalara dikkat edilmelidir:
(1) Ölçümden önce kumpası silerek temizleyin ve kumpasın iki ölçüm yüzeyinin ve ölçüm kenarlarının düz ve hasarsız olup olmadığını kontrol edin. İki ölçüm çenesi sıkıca takıldığında, belirgin bir boşluk olmamalı ve verniyer ve ana ölçek üzerindeki sıfır çizgileri birbiriyle hizalanmalıdır. Bu işleme sürmeli kumpasın sıfır konumunun kontrol edilmesi denir.
(2) Cetvel çerçevesini hareket ettirirken, hareket çok gevşek veya çok sıkı olmadan düzgün olmalı ve sallanma olmamalıdır. Cetvel çerçevesini bir sabitleme vidası ile sabitlerken, kumpasın okuması değişmemelidir. Cetvel çerçevesini hareket ettirirken, sabitleme vidasını gevşetmeyi unutmayın veya düşmeyi önlemek için çok gevşek olmamalıdır.
(3) İş parçasının dış boyutlarını ölçerken: kumpasın iki ölçüm yüzeyinin bağlantı çizgisi iş parçasının ölçülen yüzeyine dik olmalı ve eğri olmamalıdır. Ölçüm sırasında kumpas, Şekil 1-5'te gösterildiği gibi dikey konumu düzeltmek için hafifçe sallanabilir. Aksi takdirde, ölçüm çeneleri Şekil 1-5'te gösterildiği gibi yanlış konumdaysa, ölçüm sonucu "a" gerçek boyut "b "den daha büyük olacaktır. İlk olarak, ölçüm çenelerinin iş parçasına serbestçe yerleştirilebilmesi için kumpasın hareketli ölçüm çenesini açın.
Ardından iş parçasını sabit ölçüm çenesine yerleştirin ve hareketli ölçüm çenesinin iş parçasına hafif bir basınçla temas etmesini sağlamak için cetvel çerçevesini hareket ettirin. Kumpasın bir mikrometre cihazı varsa, bu sırada mikrometre cihazındaki sabitleme vidasını sıkabilir ve ardından ölçüm çenelerinin iş parçasına temas etmesini sağlamak ve boyutu okumak için ayar somununu çevirebilirsiniz. Kumpasın iki ölçüm çenesini asla ölçülen boyuta yakın veya daha küçük olacak şekilde ayarlamayın ve kumpası iş parçasına kenetlenmeye zorlamayın. Bu, ölçüm çenelerinin deforme olmasına veya zamanından önce aşınmasına neden olarak kumpasın gerekli hassasiyetini kaybetmesine yol açacaktır.
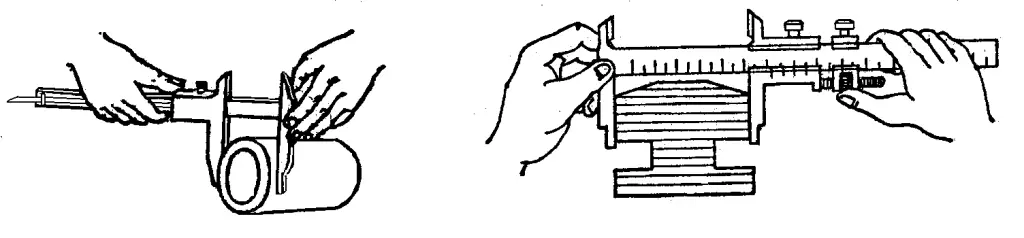

Şekil 1-5: Dış Boyutları Ölçmek için Doğru ve Yanlış Konumlar
Olukları ölçerken, kumpasın ölçüm yüzeyi bıçak kenarı ile ölçüm yapmak için kullanılmalıdır ve dış boyutları uç ölçüm bıçağı ve bıçak şeklindeki ölçüm pençeleri ile ölçmekten kaçınmak en iyisidir. Dairesel olukların boyutu için, ölçüm için bıçak şeklindeki ölçüm pençeleri kullanılmalı ve 1-6'da gösterildiği gibi düz ölçüm bıçağı ölçüm için kullanılmamalıdır.

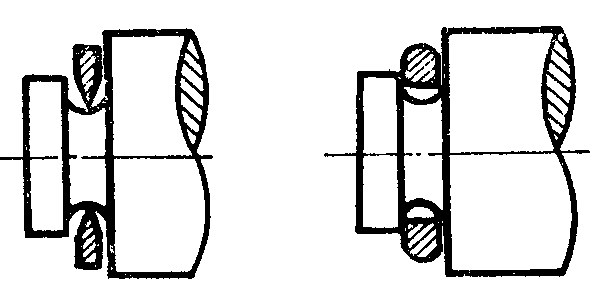
Şekil 1-6: Yivleri Ölçmek için Doğru ve Yanlış Konumlar
Oluk genişliğini ölçerken, sürmeli kumpasın konumu da uygun şekilde ayarlanmalıdır. Kumpasın iki ölçüm kenarı arasındaki bağlantı çizgisi oluğa dik olmalı ve eğimli olmamalıdır. Aksi takdirde, ölçüm tırnağı Şekil 1-7'de gösterildiği gibi yanlış konumdaysa, ölçüm sonucu hatalı olacaktır (muhtemelen çok büyük veya çok küçük).
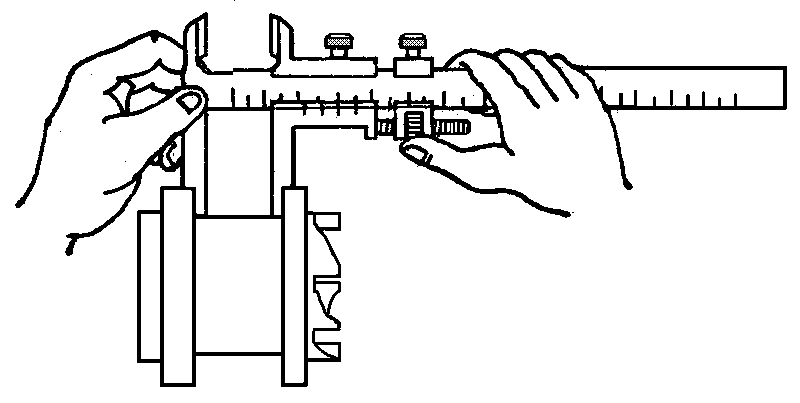


Şekil 1-7: Yiv Genişliğini Ölçmek için Doğru ve Yanlış Konumlar
(4) İş parçasının iç boyutlarını ölçerken: Şekil 1-8'de gösterildiği gibi. Ölçüm tırnakları arasındaki mesafe ölçülen iç boyuttan daha küçük olmalıdır. İş parçasının iç deliğine girdikten sonra, yavaşça açın ve iş parçasının iç yüzeyine hafifçe dokunun. Kumpası bir sabitleme vidası ile sabitledikten sonra, ölçümü okumak için kumpası yavaşça çıkarın.
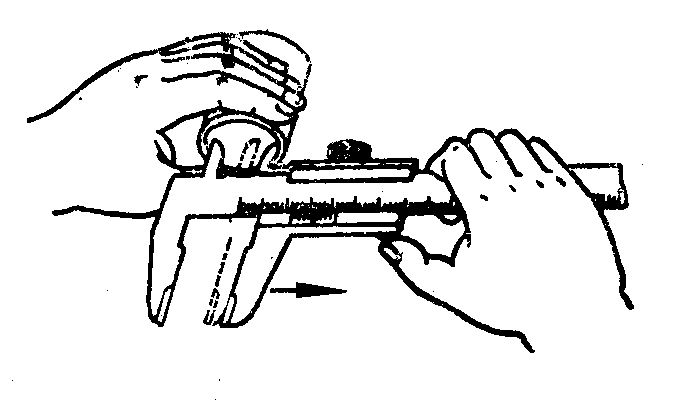
Ölçüm pençesini çıkarırken, kuvvet eşit olmalı ve kumpas, ölçüm pençelerinin bükülmesini, deformasyonunu ve gereksiz aşınma ve yıpranmasını önlemek için eğilmeden deliğin merkez hattı yönünde kaymalıdır. Aynı zamanda, ölçek çerçevesinin hareket etmesine neden olacak ve ölçüm doğruluğunu etkileyecektir. Kumpasın iki ölçüm kenarı deliğin çapı üzerinde olmalı ve eğik olmamalıdır.
Şekil 1-9, bıçak şeklindeki ölçüm pençeleri ve silindirik yüzey ölçüm pençeleri ile donatılmış kumpaslarla iç delikleri ölçmek için doğru ve yanlış konumları göstermektedir. Ölçüm tırnağı yanlış konumda olduğunda, ölçülen sonuç gerçek açıklık D'den daha küçük olacaktır.

(5) Alt ölçüm tırnağının dış ölçüm yüzeyi ile iç boyutları ölçerken, ölçüm tırnağının kalınlığı okunurken ölçüm sonucuna eklenmelidir. Yani, sürmeli kumpas üzerindeki okuma artı ölçüm tırnağının kalınlığı, ölçülen iş parçasının iç boyutudur. Ölçüm aralığı 500 mm'nin altında olan sürmeli kumpasın ölçüm tırnağının kalınlığı genellikle 10 mm'dir. Bununla birlikte, ölçüm tırnağı aşındığında veya onarıldığında, ölçüm tırnağının kalınlığı 10 mm'den az olacaktır ve ölçüm sonucu okunurken bu düzeltme değeri de dikkate alınmalıdır.
(6) Bir iş parçasını ölçmek için sürmeli kumpas kullanılırken aşırı basınca izin verilmez ve kullanılan basınç iki ölçüm tırnağının iş parçasının yüzeyine temas etmesini sağlamalıdır. Ölçüm basıncı çok yüksekse, sadece ölçüm tırnaklarının bükülmesine veya aşınmasına neden olmakla kalmaz, aynı zamanda ölçüm tırnaklarının basınç altında elastik deformasyonuna neden olarak yanlış ölçüm sonuçlarına (dış boyutlar gerçek boyuttan daha küçük ve iç boyutlar gerçek boyuttan daha büyük) neden olur.
(7) Ölçüm sonucunu sürmeli kumpas üzerinde okurken, kumpası yatay olarak tutun ve parlak ışık yönüne doğru çevirin, görüş hattının eğriliğinden kaynaklanan okuma hatalarını önlemek için görüş hattını ölçek yüzeyine mümkün olduğunca dik hale getirin.
(8) Doğru ölçüm sonuçları elde etmek için birden fazla ölçüm alınabilir. Yani, iş parçasının aynı bölümünde farklı yönlerde ölçümler yapılır. Daha uzun iş parçalarında, nispeten doğru bir ölçüm sonucu elde etmek için tüm uzunluğun çeşitli kısımlarında ölçümler yapılmalıdır.
5.3. Derinlik Ölçer:
Şekil 1-10'da gösterilen derinlik ölçer, bir iş parçasının derinliğini, bir basamağın yüksekliğini veya bir oluğun derinliğini ölçmek için kullanılır. Yapısal özelliği, ölçek çerçevesinin 3 iki ölçüm tırnağının bir verniyerli ölçüm tabanı 1 oluşturmak üzere birbirine bağlanması ve tabanın uç yüzü ile ölçek gövdesinin 4 uç yüzünün iki ölçüm yüzeyi olmasıdır. Bir iç deliğin derinliğini ölçerken, tabanın uç yüzü ölçülen deliğin uç yüzüne sıkıca tutturulmalı ve terazi gövdesi ölçülen deliğin merkez çizgisine paralel olarak yerleştirilmelidir. Terazi gövdesinin uç yüzü ile tabanın uç yüzü arasındaki mesafe, ölçülen iş parçasının derinlik boyutudur.
Okuma yöntemi verniyer kumpas ile tamamen aynıdır.
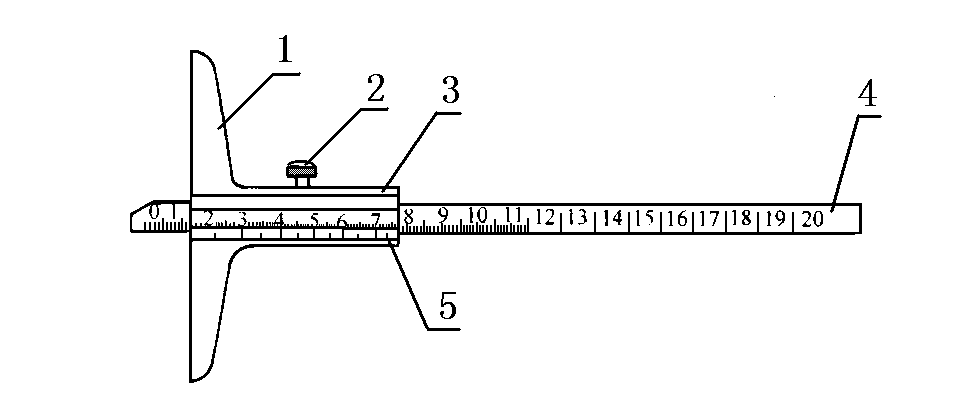
- 1- Ölçüm Tabanı;
- 2- Sabitleme Vidası;
- 3- Ölçek Çerçevesi;
- 4- Ölçekli Gövde;
- 5- Vernier
5.4. Mikrometre:
Vidalı mikrometre olarak da bilinir, vidalı mikro ölçüm prensibi kullanılarak yapılan bir ölçüm aletidir. Ölçüm hassasiyeti bir sürmeli kumpastan daha yüksektir ve ölçümde daha esnektir. Bu nedenle, genellikle yüksek işleme hassasiyeti gerektiğinde kullanılır.
Okuma çözünürlüğüne göre, yüzüncü ölçek ve bininci ölçek olarak ikiye ayrılır. Yüzüncü ölçeğin okuma değeri 0,01 mm ve bininci ölçeğin okuma değeri 0,001 mm'dir. Fabrikalarda, yüzlük ölçek ve bindelik ölçek genellikle sürmeli kumpas veya milimetre kumpas olarak adlandırılır. Sac metal imalatında çoğunlukla 0,01 mm okuma değerine sahip yüzüncü ölçekli sürmeli kumpaslar kullanılır.

5.4.1 Binde bir ölçekli mikrometre kullanma yöntemi:
- Adım 1: Gereksinimlere göre uygun sürmeli kumpas aralığını seçin.
- Adım 2: Mikrometrenin ölçek gövdesini ve ölçüm yüzeylerini temizleyin.
- Adım 3: Mikrometreyi mikrometre standına takın, sabitleyin ve ardından sıfırlayın.
- Adım 4: İş parçasını iki çalışma yüzeyi arasına yerleştirin, yüksüğü çalışma yüzeyi iş parçasına hızla temas edene kadar ayarlayın, ardından ölçüm kuvveti cihazını üç "klik" sesi duyana kadar ayarlayın.
5.4.2 Binde bir ölçekli mikrometrenin okuma yöntemi:
- Adım 1: Okunması gereken 0,5 mm'lik mezuniyet çizgisinin değerini kaçırmamaya dikkat ederek, sabit manşon üzerinde açıkta kalan mezuniyet çizgisinin boyutunu okuyun.
- Adım 2: Yüksük üzerindeki ölçüyü okuyun ve yüksüğün çevresindeki hangi ızgaranın sabit manşonun merkez çizgisi ölçütü ile hizalandığına bakın, ardından yüksük üzerindeki ölçüyü elde etmek için ızgara sayısını 0,001 mm ile çarpın.
- Adım 3: Verniyer kumpas üzerinde ölçülen boyutu elde etmek için yukarıdaki iki sayıyı toplayın.
Örnek: Aşağıdaki şekilde gösterildiği gibi, manşonun üst ölçeğini 3 olarak ve alt ölçeği 3'ten sonra okuyun, bu da 3+0,5=3,5 anlamına gelir. Ardından manşon ölçeğini 25 ile hizalı olarak okuyun, bu da 25×0,001=0,025 anlamına gelir. Bunların toplanması 3,525 sonucunu verir.
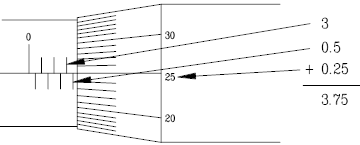
5.5. Evrensel Açı Cetveli:
Hassas parçaların iç ve dış açılarını ölçmek veya açıları işaretlemek için kullanılan bir açı ölçüm aletidir.
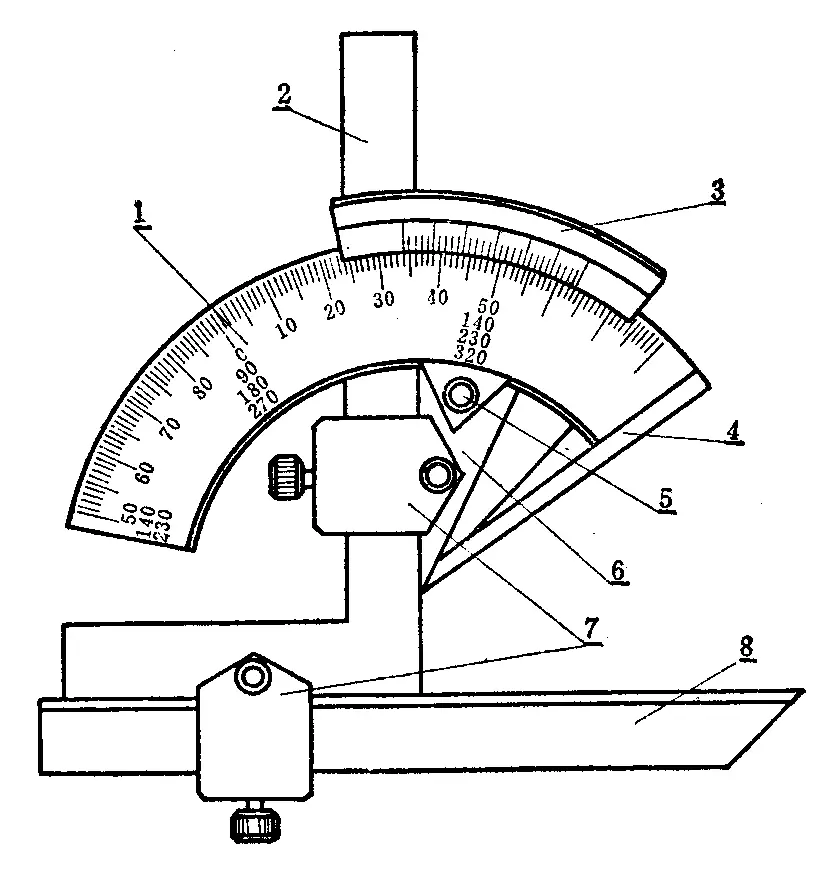
Evrensel Açı Cetvelini kullanma ve okuma yöntemi:
Evrensel Açı Cetvelinin okuma mekanizması, sağdaki şekilde gösterildiği gibi, temel açı derecelendirme çizgilerine sahip bir ölçek tabanı 1 ve sektör plakası 6 üzerine sabitlenmiş bir verniyer 3'ten oluşur. Sektör plakası, verniyer kumpasına benzer bir verniyer okuma mekanizması oluşturmak için taban üzerinde (bir fren 5 ile) dönebilir ve hareket edebilir.
Evrensel Açı Cetveli üzerindeki dereceli çizgilerin her bir ızgarası 1º'lik bir dereceye sahiptir. Verniyerde toplam 29º'lik bir açıyı kaplayan 30 ızgara olduğundan, her ızgara çizgisi arasındaki derece farkı
Bu nedenle, Evrensel Açı Cetvelinin doğruluğu 2′dir.
Evrensel Açı Cetvelinin okuma yöntemi Verniyer Kumpas ile aynıdır. İlk olarak, verniyerdeki sıfır çizgisinden önceki açıyı okuyun ve ardından verniyerden açının "dakika" değerini okuyun. İki değerin toplanması ölçülen parçanın açı değerini verir.
Evrensel Açı Cetvelinde, taban cetveli 4 tabana sabitlenir ve açı cetveli 2 bir kelepçe bloğu 7 ile sektör plakasına sabitlenir. Hareketli cetvel 8, bir kelepçe bloğu ile açı cetveline sabitlenmiştir. Açı cetveli 2 çıkarılırsa, düz cetvel 8 de sektör plakasına sabitlenebilir. Açı cetveli 2 ve düz cetvel 8 hareket ettirilebildiğinden ve değiştirilebildiğinden, Evrensel Açı Cetveli Şekil 1-11'de gösterildiği gibi 0º ila 320º arasındaki herhangi bir açıyı ölçebilir.
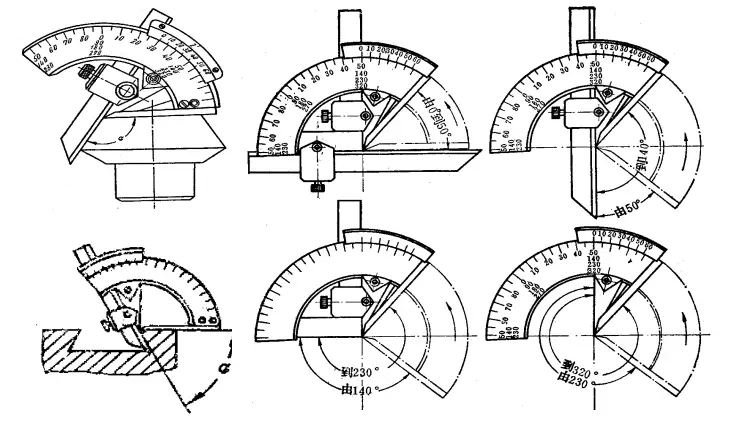
Şekil 1-11'de gösterildiği gibi, açı cetveli ve düz cetvel tamamen takıldığında, 0º ila 50º arasındaki dış açılar ölçülebilir. Yalnızca düz cetvel takıldığında, 50º ila 140º arasındaki açılar ölçülebilir. Yalnızca açı cetveli takıldığında, 140º ila 230º arasındaki açılar ölçülebilir. Hem açı cetveli hem de düz cetvel çıkarıldığında, 230º ila 320º arasındaki açılar ölçülebilir (yani, 40º ila 130º arasındaki iç açılar).
Evrensel Açı Cetvelinin ölçek tabanındaki temel açı derecelendirme çizgileri yalnızca 0º ila 90º arasında değişir. Parçanın ölçülen açısı 90º'den büyükse, okumaya bir temel değer (90º, 180º, 270º) eklenmelidir. Parçanın açısı şu şekilde olduğunda: >90º ila 180º arasında ise, ölçülen açı = 90º + Evrensel Açı Cetvelinin okuması; 180º ila 270º arasında ise, ölçülen açı = 180º + Evrensel Açı Cetvelinin okuması; 270º ila 320º arasında ise, ölçülen açı = 270º + Evrensel Açı Cetvelinin okuması.
Bir parçanın açısını ölçmek için Evrensel Açı Cetvelini kullanırken, ölçüm hatalarını önlemek için taban cetveli parçanın açı yönünün taban çizgisiyle hizalanmalı ve parça açı ölçerin iki ölçüm yüzeyine tam olarak temas etmelidir.
6. Ana Süreç Teknolojilerine Giriş
6.1 Damgalama Süreci
6.1.1 Delme boyutu için minimum gereksinim Delme kalıbının mukavemet sınırlaması nedeniyle, açıklık çok küçük olamaz. Delinen deliğin minimum boyutu deliğin şekline, malzemenin mekanik özelliklerine ve malzeme kalınlığına bağlıdır.
Tablo 6-1 zımbalama için minimum delik boyutlarını listeler.
malzemeler | Zımbalama için minimum çap veya minimum kenar uzunluğu (t malzeme kalınlığıdır) | ||
Dairesel delik D (burada D çaptır) | Kare delik L (burada L her bir kenarın uzunluğudur) | Bel yuvarlak delik, dikdörtgen delik a (burada a minimum kenar uzunluğudur) | |
yüksek ve orta karbonlu çelik | ≥1.3t | ≥1.2t | ≥1t |
düşük karbonlu çelik ve pirinç | ≥1t | ≥0.8t | ≥0.8t |
alüminyum ve çinko | ≥0.8t | ≥0.6t | ≥0.6t |
6.1.2 Minimum delme aralığı
Delinmiş parçanın kenarı ile anahat arasındaki minimum mesafe, Şekil 1-12'de gösterildiği gibi parçanın ve deliğin şekline bağlı olarak belirli sınırlamalara sahiptir

6.1.3 Üst üste zımbalama için gereklilikler
Bileşik kalıplar tarafından işlenen deliklerin ve anahatların ve deliklerin ve deliklerin doğruluğunu sağlamak nispeten kolaydır ve işleme verimliliği yüksektir. Bununla birlikte, delikler ve delikler arasındaki ve delikler ve anahatlar arasındaki mesafe, Şekil 1-13'te gösterildiği gibi bileşik kalıbın minimum duvar kalınlığı gereksinimlerini karşılayabilmelidir
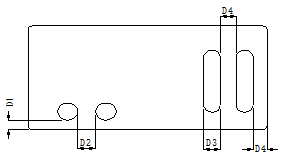
Tablo 6-2: Delme ve kesme parçalarının bileşik kalıpla işlenmesi için minimum örtüşme boyutu.
t (0,8'in altında) | t (0.8~1.59) | t (1.59~3.18) | t (3,2以上) | |
D1 | 3mm | 2t | ||
D2 | 3mm | 2t | ||
D3 | 1.6mm | 2t | 2.5t | |
D4 | 1.6mm | 2t | 2.5t |
6.1.4 Deliklerin deforme olmadığından emin olmak için bükmeden önce zımbalayın. Delikler ve bükülmüş kenarlar arasındaki minimum mesafe Şekil 1-14'te gösterilmiştir. Bu mesafe için formül X≥2t+R'dir.

Şekil 1-15'te gösterildiği gibi derin çekilmiş parçalara delik açarken, deliklerin şekil ve konum doğruluğunu ve kalıbın mukavemetini sağlamak için, delik duvarı ile parçanın düz duvarı arasında belirli bir mesafe korunmalıdır. a1 ve a2 mesafeleri aşağıdaki gereklilikleri karşılamalıdır:
- a1 ≥ R1 + 0,5t
- a2 ≥ R2 + 0,5t
Burada R1 ve R2 yuvarlama yarıçapı ve t plakanın kalınlığıdır.
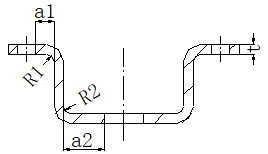
6.1.6 Sayısal delme sırasında dikkat edilmesi gereken hususlar ve gereklilikler:
Kalınlığı 0,6 mm'den az olan malzemelerin deforme olması kolaydır ve işleme aralığı kalıp ve kelepçe ile sınırlıdır, bu nedenle sayısal delme genellikle kullanım için uygun değildir.
Orta sertlik ve tokluğa sahip malzemeler iyi delme ve kesme özelliklerine sahiptir. Sertlik çok yüksekse delme kuvveti artacaktır, bu da zımba kafası ve doğruluk üzerinde olumsuz bir etkiye sahip olabilir. Sertlik çok düşükse, zımbalama sırasında deformasyon şiddetli olur ve bu da doğruluğu büyük ölçüde sınırlar.
Malzemelerde yüksek plastisite, şekillendirme işlemleri için avantajlıdır, ancak nibbling veya sürekli delme için uygun olmayabilir ve delme ve düzeltme için çok uygun değildir. Uygun tokluk, zımbalama sırasında deformasyon derecesini bastırabileceğinden zımbalama için faydalıdır. Ancak, yüksek tokluk zımbalama sonrasında ciddi geri tepmelere neden olabilir ve bu da hassasiyeti etkileyebilir.
Sıradan düşük karbonlu çelik plakaları damgalarken, kalıp çapı ve genişliği malzeme kalınlığından daha büyük olmalıdır. Örneğin, Φ1,4 çapındaki bir kalıp 1,5 mm'lik bir malzemeyi delemez. Alüminyum alaşımlı ve bakır alaşımlı plakaları delmek için kalıplar daha küçük olabilir, ancak paslanmaz çelik ve yüksek karbonlu çelik plakaları delmek için kalıplar daha büyük olmalıdır. Aksi takdirde kalıp kırılmaya ve hasar görmeye meyillidir.
Paslanmaz çelik plakalar genellikle sayısal zımbalama için uygun değildir. Elbette, 0,8 mm ila 2,5 mm kalınlıktaki paslanmaz çelik plakalar sayısal delme kullanılarak işlenebilir, ancak bu, kalıpta daha fazla aşınmaya yol açar ve sıradan çelik plakalara kıyasla daha yüksek bir hurda oranıyla sonuçlanır.
6.2 Bükme İşlemi
Sac metalde bükme, bir sac metali V şekline, U şekline vb. bükmek gibi sacın veya bileşenin açısını değiştirme işlemini ifade eder. Genel olarak, sac metal bükme için iki yöntem vardır: biri karmaşık yapılar, küçük hacimli ve büyük ölçekli sac metal yapı üretimi için kullanılan kalıp bükme; diğeri ise nispeten büyük boyutlara veya düşük üretim hacimlerine sahip sac metal yapıları işlemek için kullanılan bükme makinesi bükme. Şu anda, şirketimizin ürünleri ağırlıklı olarak işleme için bükme makineleri kullanmaktadır.
6.2.1 Bükme işlemi sırasının temel ilkeleri:
- İçten dışa doğru bükün;
- Küçükten büyüğe doğru bükün;
- Önce özel şekilleri bükün, sonra genel şekilleri bükün;
- Önceki sürecin şekillendirilmesi sonraki süreçlere müdahale etmemelidir.
6.2.2 Bükme yarıçapı
Malzeme büküldüğünde, dış katman gerilirken iç katman yuvarlatılmış köşe bölgesinde sıkıştırılır. Malzemenin kalınlığı sabit olduğunda, iç yarıçap r ne kadar küçükse, malzemenin gerilmesi ve sıkışması o kadar şiddetli olur. Dış köşedeki çekme gerilmesi malzemenin nihai mukavemetini aştığında, çatlaklar ve kırılmalar meydana gelebilir. Bu nedenle, bükülmüş parçaların yapısal tasarımı küçük bükülme yarıçaplarından kaçınmalıdır. Bükülme minimum bükülme Yaygın malzemeler için yarıçap aşağıdaki tabloda gösterilmiştir.
Tablo 6-1: Yaygın olarak kullanılan metalik malzemeler için minimum bükülme yarıçaplarının listesi
Hayır. | Malzeme | Minimum bükülme yarıçapı |
1 | 08、08F、10、10F、DX2、SPCC、E1-T52、0Cr18Ni9、1Cr18Ni9、1Cr18Ni9Ti、1100-H24、T2 | 0.4t |
2 | 15、20、Q235、Q235A、15F | 0.5t |
3 | 25、30、Q255 | 0.6t |
4 | 1Cr13、H62 (M、Y、Y2、Soğuk haddelenmiş) | 0.8t |
5 | 45、50 | 1.0t |
6 | 55、60 | 1.5t |
7 | 65Mn、60SiMn、1Cr17Ni7、1Cr17Ni7-Y、1Cr17Ni7-DY、SUS301、0Cr18Ni9、SUS302 | 2.0t |
- Bükme yarıçapı, bükülen parçanın iç yarıçapını ifade eder ve "t" malzeme kalınlığıdır.
- "t" malzemenin kalınlığını, "M" tavlanmış durumu, "Y" sertleştirilmiş durumu ve "Y2" yarı sertleştirilmiş durumu ifade eder.
6.2.3 Çelik Levha Katlamasının Minimum Bükme Kenarı Boyutları için Referans Tablosu
Malzeme kalınlığı | 0.8 | 1.0 | 1.2 | 1.5 | 2.0 | 2.5 | 3 |
Minimum bükülme kenarı | 5 | 6.5(5) | 6.5(6) | 7(6.5) | 9 | 11 | 13 |
Yukarıda belirtilen özelliklerden daha küçük bir bükme boyutu gereksinimi olan parçalar için, işleme için ayrı bir kalıp kullanılmalıdır.
6.2.4 Deliklerden ve Eliptik Deliklerden Bükme Kenarlarına Minimum Mesafe:
Şekil 1-16'da gösterildiği gibi, bükme alanının delik kenarı bükme çizgisine çok yakınsa, malzeme bükme sırasında yukarı kaldırılamaz ve bu da delik şeklinin deforme olmasına neden olur. Bu nedenle, delik kenarı ile bükme çizgisi arasındaki mesafe minimum delik kenarı mesafesi X≥t+R'den büyük olmalıdır.
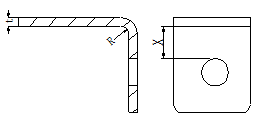
Tablo 6-2: Yuvarlak Deliklerden Bükme Kenarlarına Minimum Mesafe.
Malzeme kalınlığı | 0.6~0.8 | 1.0 | 1.2 | 1.5 | 2.0 | 2.5 |
Minimum mesafe X | 1.3 | 1.5 | 1.7 | 2.0 | 3 | 3.5 |
Şekil 1-17'de gösterildiği gibi, eliptik delik bükme hattına çok yakınsa, malzeme bükme sırasında kalkacak ve bu da delik şeklinin deforme olmasına neden olacaktır. Bu nedenle, delik kenarı ile bükme çizgisi arasındaki mesafe Tablo 1-14'e göre minimum delik kenarı mesafesinden daha büyük olmalıdır.

Tablo 6-3: Eliptik Deliklerden Bükme Kenarlarına Minimum Mesafe.
L | <26 | 26~50 | >50 |
Minimum mesafe X | 2t+R | 2.5t+R | 3t+R |
6.2.5 Proses Delikleri, Yuvalar ve Çentikler için Bükme Parçaları:
Bükme işlemi sırasında, parçanın bükülmüş kenarının işlenmemiş parçanın iç kenarına doğru bükülmesi gerekiyorsa, Şekil 1-18'de gösterildiği gibi yırtılmayı ve bozulmayı önlemek için işlem delikleri, yuvalar veya çentikler eklenmesi önerilir.
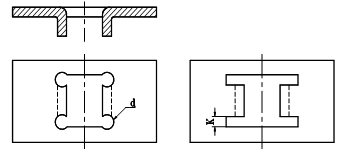
- İşlem deliğinin çapı ≥t olmalıdır.
- İşlem çentiğinin genişliği ≥t ve derinliği ≥1,5t olmalıdır.